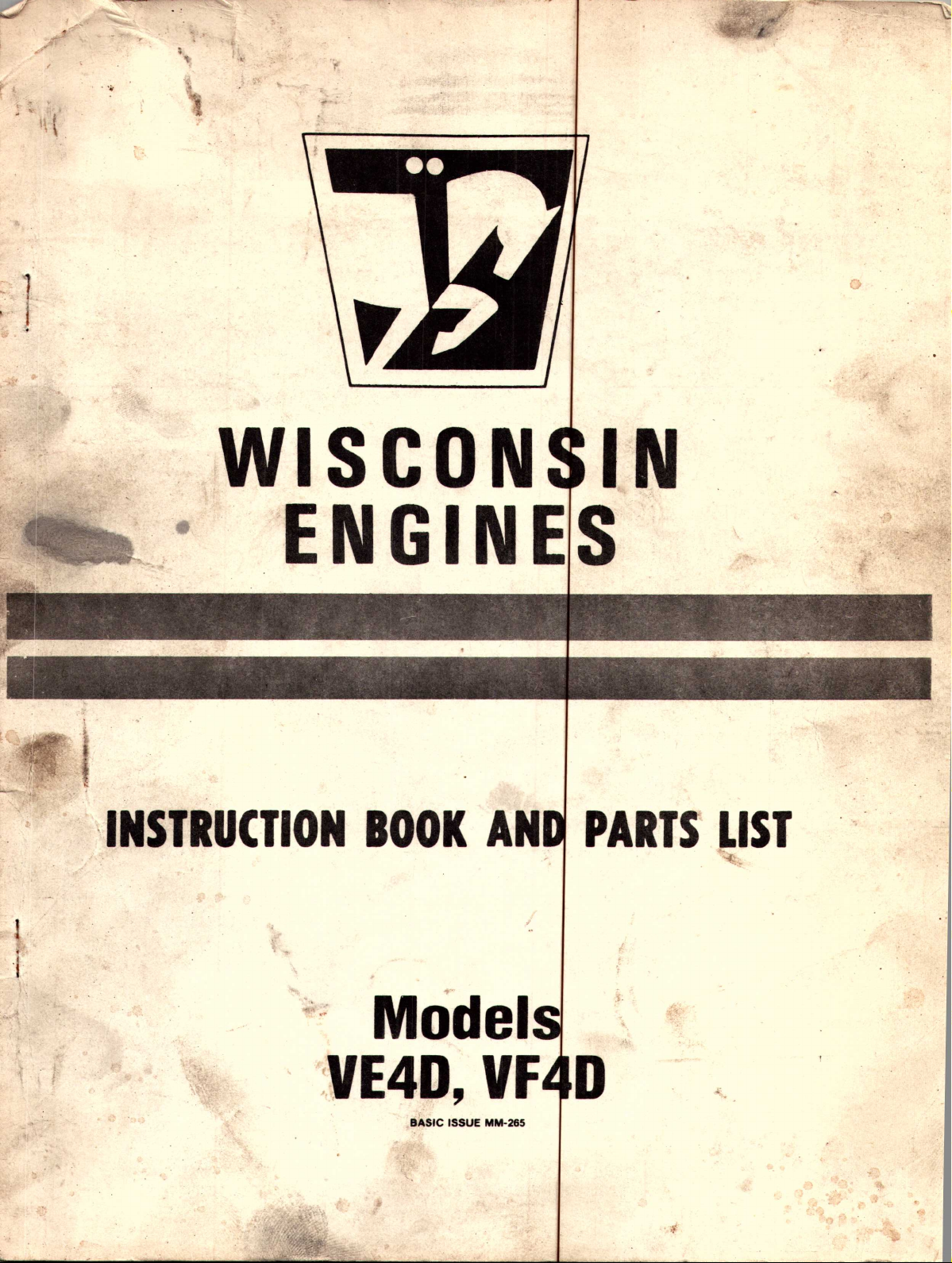
( t •
• ,t • ";' , • .: ~ -
:.", t .
Ii ' •
,
_-
"
.
1'" •
I
t"
o .
.
'
,.
y .
'. WISCON IN .
....ENGINES'
.. t}
.'~ . ,INSTRUCTION BOOK AN PARTS:
..
~
.
,,'........ . '; Model
,
'1'
't.,.
":VE4D,
BASIC ISSUE MM-265
,
.
l(
VF
,
I"
.),
,
0 . '.
~IST
.
,
.
.....~
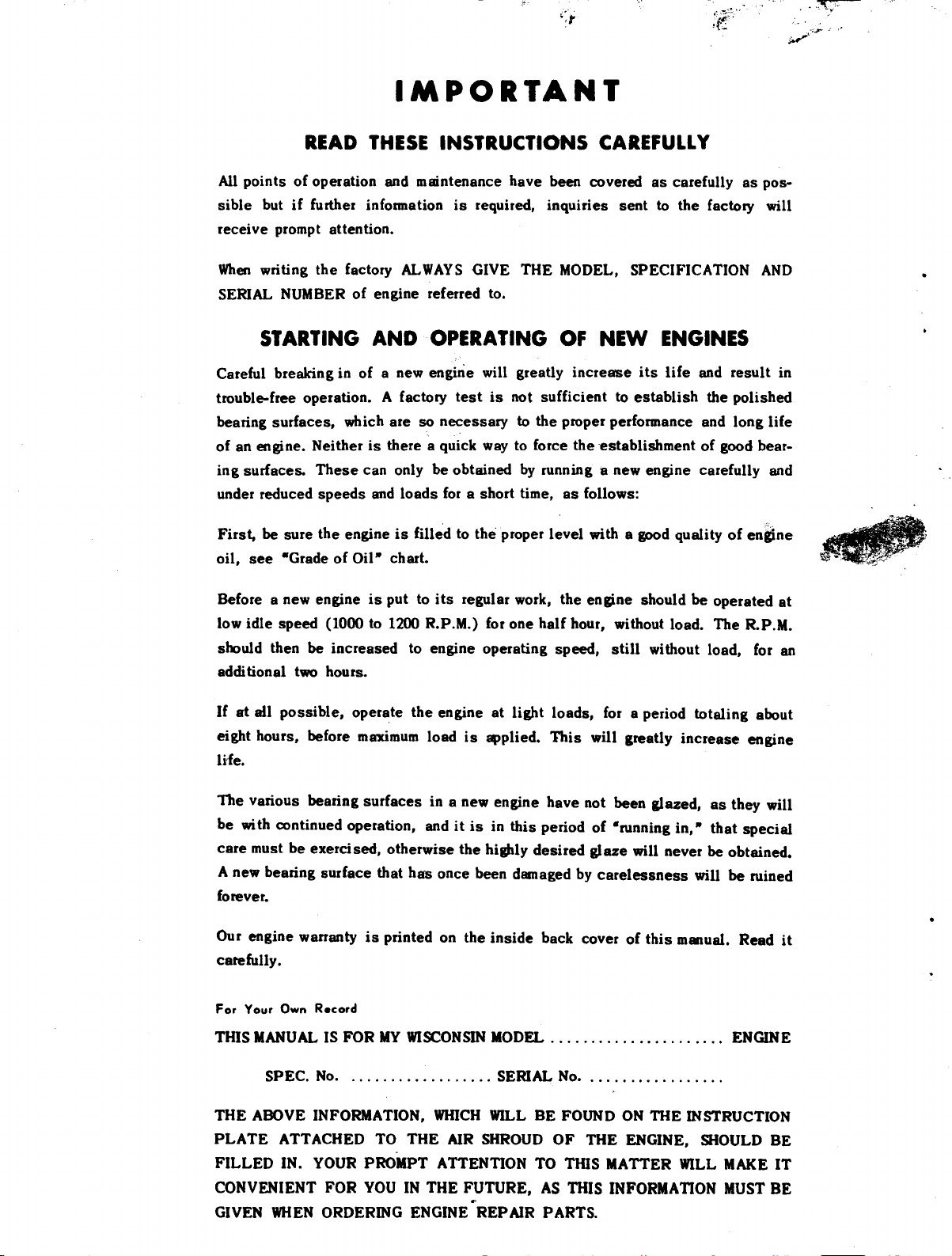
IMPORTANT
READ THESE INSTRUCTIONS CAREFULLY
All points of operation and maintenance have been covered as carefully as pos-
sible but if further information is required, inquiries sent to the factory will
receive prompt attention.
When writing the factory ALWAYS GIVE THE MODEL, SPECIFICATION AND
SERIAL NUMBERof engine referred to.
STARTING AND OPERATING OF NEW ENGINES
Careful breaking in of a new engine will greatly increase its life and result in
trouble-free operation. A factory test is not sufficient to establish the polished
bearing surfaces, which aresonecessary to the proper performance and long life
of an engine. Neither is there a quick way to force the establishment of good bear-
ing surfaces. These can only be obtained by running'anew engine carefully and
under reduced speeds and loads for a short time, as follows:
,
..
~
First, be sure the engine is filled to the proper level with a good quality of entine
oil, see -Grade of Oil- chart.
Before a new engine is put to its regular work, the engine should be operated at
low idle speed (1000 to 1200 R.P.M.) for one half hour, without load. The R.P.M.
should then be increased to engine operating speed, still without load, for an
additional two hours.
If
at all possible, operate the engine at light loads, for a period totaling about
eight hours, before maximum load is applied. This will greatly increase engine
life.
The various bearing surfaces in a new engine have not been glazed, as they will
be with continued operation, and it is in this period of -running in, - that special
care must be exercised, otherwise the highly desired glaze will never be obtained.
A new bearing surface that has once been damaged by carelessness will be ruined
forever.
Our engine warranty is printed on the inside back cover of this manual. Read it
carefully.
For Your Own Record
THIS MANUALIS FOR MYWISCONSINMODEL ENGINE
SPEC. No. . SERIAL No. . .
THE ABOVE INFORMATION, WHICHWILL BE FOUND ON THE INSTRUCTION
PLATE ATTACHED TO THE AIR SHROUD OF THE ENGINE, SHOULD BE
FILLED IN. YOUR PROMPT ATTENTION TO THIS MATTER WILL MAKE IT
CONVENIENT FOR YOU IN THE FUTURE, AS THIS INFORMATION MUST BE
GIVEN WHENORDERING ENGINE REPAIR PARTS.
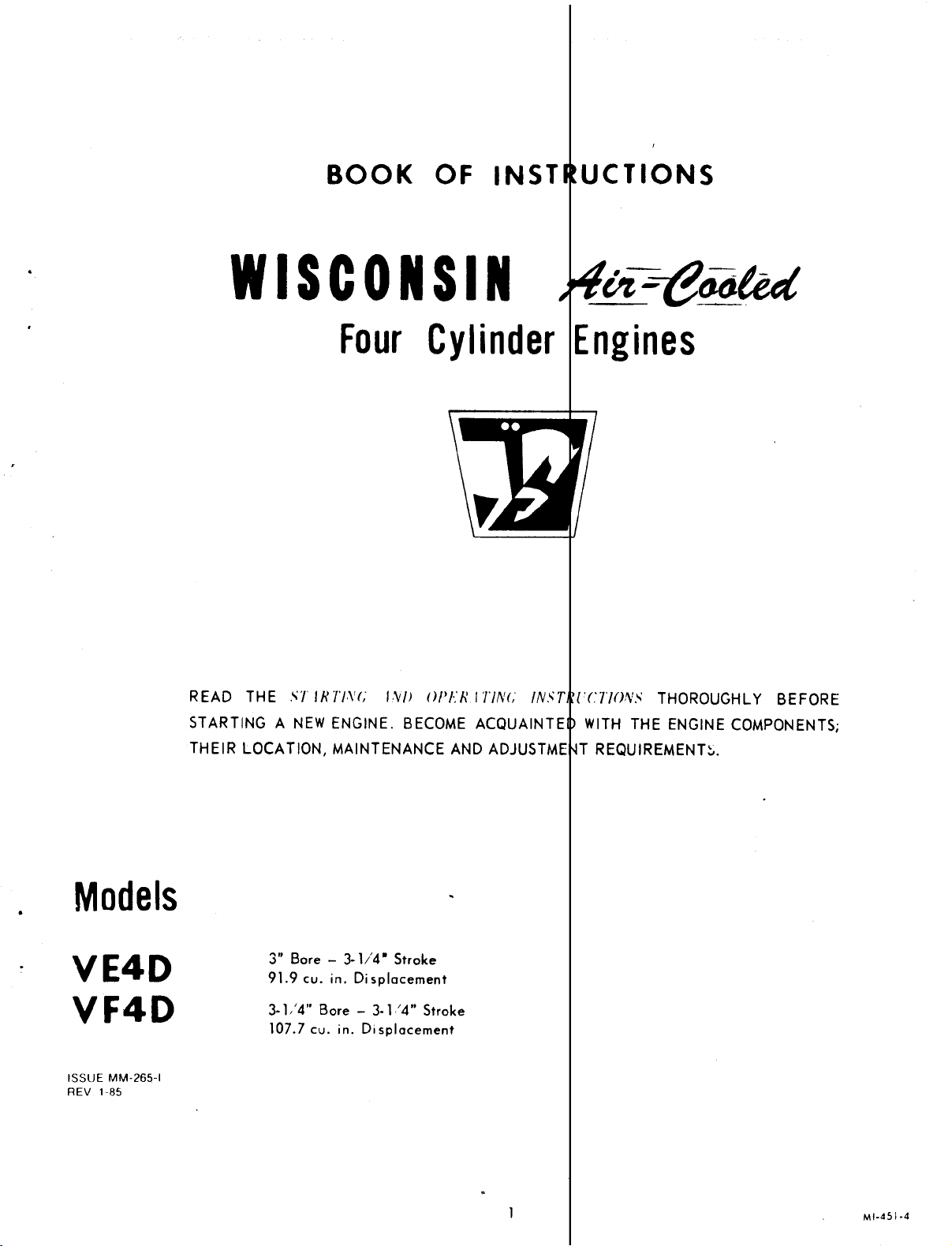
BOOK OF INST UCTIONS
WISCONSIN
Four Cylinder Engines
Models
VE4D
VF4D
ISSUE MM-265-1
REV
1-85
READ THE ....tI
STARTING A NEW ENGINE. BECOME ACQUAINTE WITH THE ENGINE COMPONENTS;
THEIR LOCATION, MAINTENANCE AND ADJUSTM T REQUIREMENT~.
3" Bore - 3-1/4- Stroke
91.9 cu. in. Displacement
3-1,'4" Bore -
107.7 cu. in. Displacement
RT!W;
isn
3-1/4"
OI'FRITINe INST {'('T/ONS
Stroke
THOROUGHLY BEFORE
MI-451.4
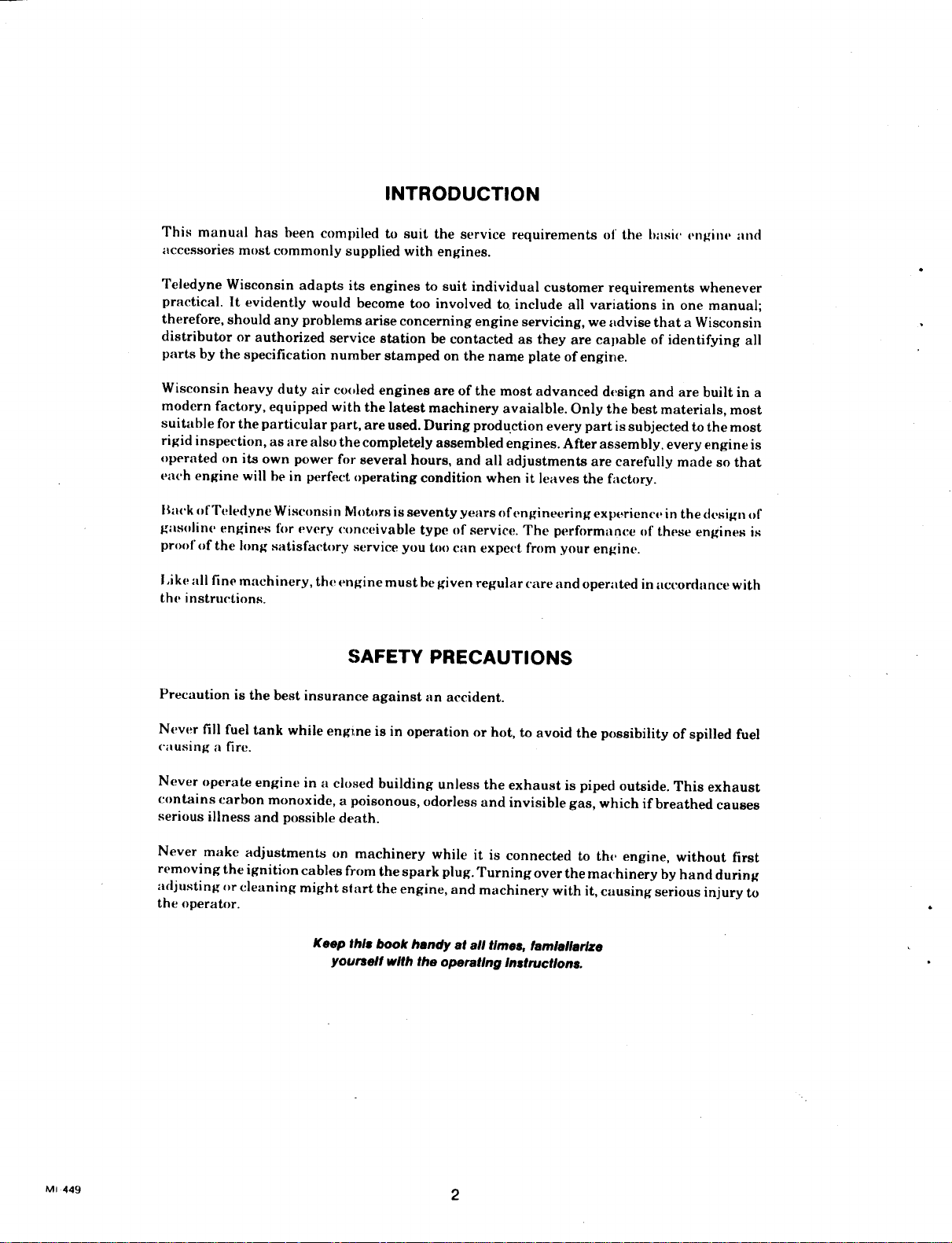
INTRODUCTION
This manual has been compiled to suit the service requirements of the hnsu- t'ngint· and
accessories most commonly supplied with engines.
Teledyne Wisconsin adapts its engines to suit individual customer requirements whenever
practical.Itevidently would become too involved to. include all variations in one manual;
therefore. should any problems arise concerning engine servicing. we advise that a Wisconsin
distributor or authorized service station be contacted as they are capable of identifying all
parts by the specification number stamped on the name plate of engine.
Wisconsin heavy duty air cooled engines are of the most advanced design and are built in a
modern factory, equipped with the latest machinery avaialble. Only the best materials, most
suitable for the particular part, are used. During production every part is subjected to the most
rigid inspection, as are also the completely assembled engines. After assembly, every engine is
operated on its own power for several hours, and all adjustments are carefully made so that
each
engine will be in perfect operating condition when it leaves the factory.
HackofTeledyne
gasolillt' engines for every conceivable type of service. The performance of these engines is
proof of the long satisfactory service you too can expect from your engine.
I.ike
all fine machinery, the engine must begiven regular care and operated in
the instructions,
Wiseonsi n Motors is seventy years of engi neering
experience
in the dt'sign of
accordance
with
SAFETY PRECAUTIONS
Precaution is the best insurance against an accident.
Never fill fuel tank while engine is in operation or hot,toavoid the possibility of spilled fuel
causing a fire.
Never operate engine in a closed building unless the exhaust is piped outside. This exhaust
contains carbon monoxide, a poisonous, odorless and invisible gas, which if breathed causes
serious illness and possible death.
Never make adjustments on machinery while it is connected to the engine, without first
removing the ignition cables from the spark plug. Turning over the machinery by hand during
adjusting or cleaning might start the engine, and machinery with it, causing serious injury to
the operator.
Keep thl. book handy at all time., 'am/allar/ze
yourself with the operating In.truct/on •.
MI449
2
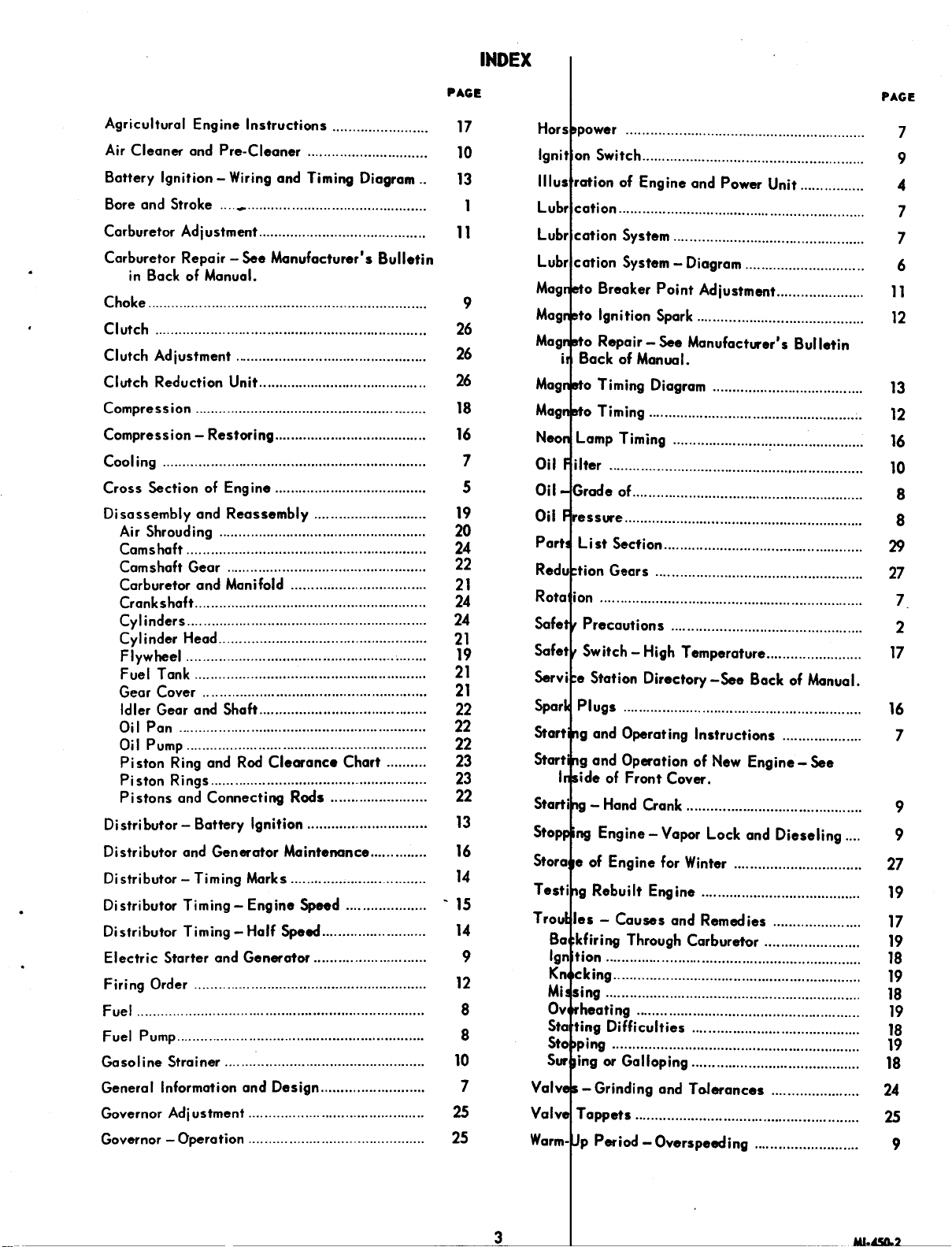
INDEX
Agricultural Engine Instructions .
Air Cleaner and Pre-Cleaner .
Battery Ignition - Wiring and Timing Diagram ..
Bore and Stroke _ .
Carburetor Adj ustment ..
Carburetor Repair - See Manufacturer's Bulletin
in Bock of Manual.
Choke ..
Clutch ..
Clutch Adjustment ..
Clutch Reduction Unit ..
Compression ..
Compression - Restoring ..
Cooling ..
Cross Section of Engine .
Disassembly and Reassembly .
Air Shrouding ..
Camshaft ..
Camshaft Gear .
Carburetor and Manifold .
Crankshaft ..
Cylinders ..
Cylinder Head .
Flywheel ; .
Fuel Tank .
Gear Cover ..
Idler Gear and Shaft .
Oil Pan .
Oil Pump ..
Piston Ring and Rod Clearance Chart .
Piston Rings ..
Pistons and Connecting Rods .
Distributor - Battery Ignition .
Distributor and Generator Maintenance ..
Distributor - Timing Marks .
Distributor Timing - Engine Speed .
Distributor Timing - Half Speed ..
Electric Starter and Generator ..
Firing Order .
Fuel .
Fuel Pump ..
Gasol ine Strainer .
General Information and Design ..
Governor Adjustment .
Governor - Operation .
PAGE
17
10
13
11
26
26
26
18
16
19
20
24
22
21
24
24
21
19
21
21
22
22
22
23
23
22
13
16
14
- lS
14
12
10
2S
2S
PAGE
Hors power .
Ignit on Switch ..
IIlus ration of Engine and Power Unit .
1
9
Lubr cation .
Lubr cation System .
Lubr cation System - Diagram ..
Mag
0
Breaker Point Adjustment.. .
to Ignition Spark ..
Mag
0
Repair - See Manufacturer's Bulletin
Back of Manual.
o Timing Diagram .
o Timing ..
Lamp Timing : .
7
S
Oil
Oil
Part List Secfion .
7
9
4
7
7
6
11
12
13
12
16
10
8
8
29
27
7
Precautions ..
Switch - High Temperature .
Servi e Station Directory -See Back of Manual.
Spar Plugs ..
g and Operating Instructions ..
g and Operation of New Engine - See
ide of Front Cover.
g - Hand Crank ..
Stop ng Engine- Vapor Lock and Dieseling ..
Stora e of Engine for Winter .
Testi g Rebuilt Engine .
Tro les - Causes and Remedies ..
Ba kfiring Through Carburetor .
9
8
8
7
Ign tion ..
Kn cking .
Mi sing .
Ov heating ..
Sta ting Difficulties .
Sto ping ..
Sur ing or Galloping .
- Grinding and Toferances ..
Valve Tappets ..
Warm- p Period - Overspeeding ..
2
17
16
7
9
9
27
19
17
19
18
19
18
19
18
19
18
24
2S
9
3
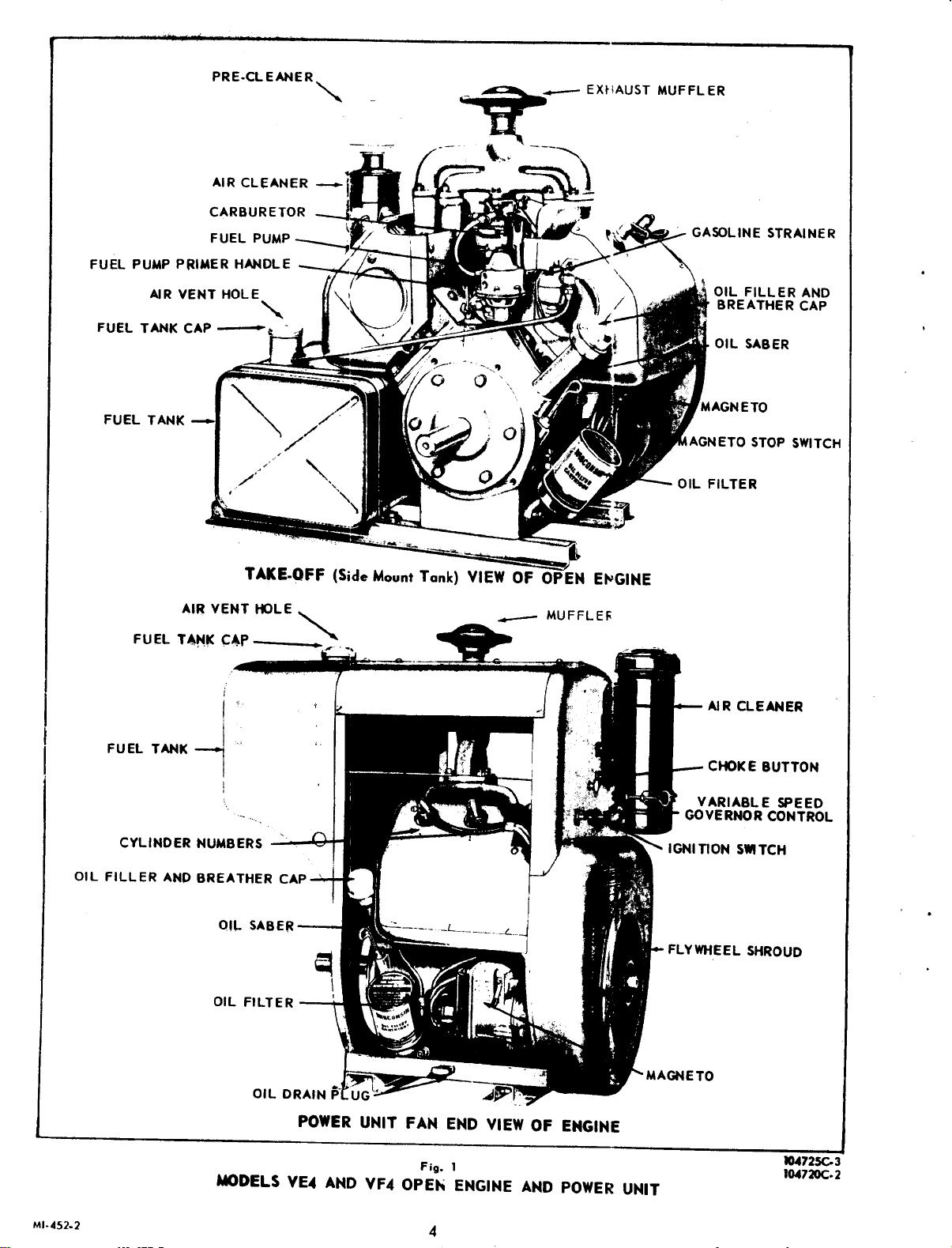
PRE.CLEANER"'"
AIR CLEANER _
CARBUR ETOR
FUEL PUMP_~
FUEL PUMP P~IMER HANDLE
AIR VENT HOLE,
FUEL TANK CAP - -
FUEL TANK
TAKE·OFF (Side MountTank) VIEW OF
AI~ VENT HOLE
FUEL T4~f(
~4P "" .•,
-\ir:--~.:JL.)
77"'~_J.._
--;:''_'i?;.c~..l__J}
II!.
OIL FILLER AND
BREATHER CAP
OIL SABER
_ MUFFLfF:
FUEL TANK~
OIL FILLER AND BREATHER CAP
ou,
SABER
OIL FILTER
MODELS VE~ AND VF4 OPE... ENGINE AND POWERUNIT
POWERUNIT FAN END VIEW OF ENGINE
Fig. 1
AIR CLEANER
CHOK E BUTTON
VARIABLE SPEED
GOVERNOR CONTROL
FLYWHEEL SHROUD
lO472sc.3
10472OC.2
MI-452.2
4
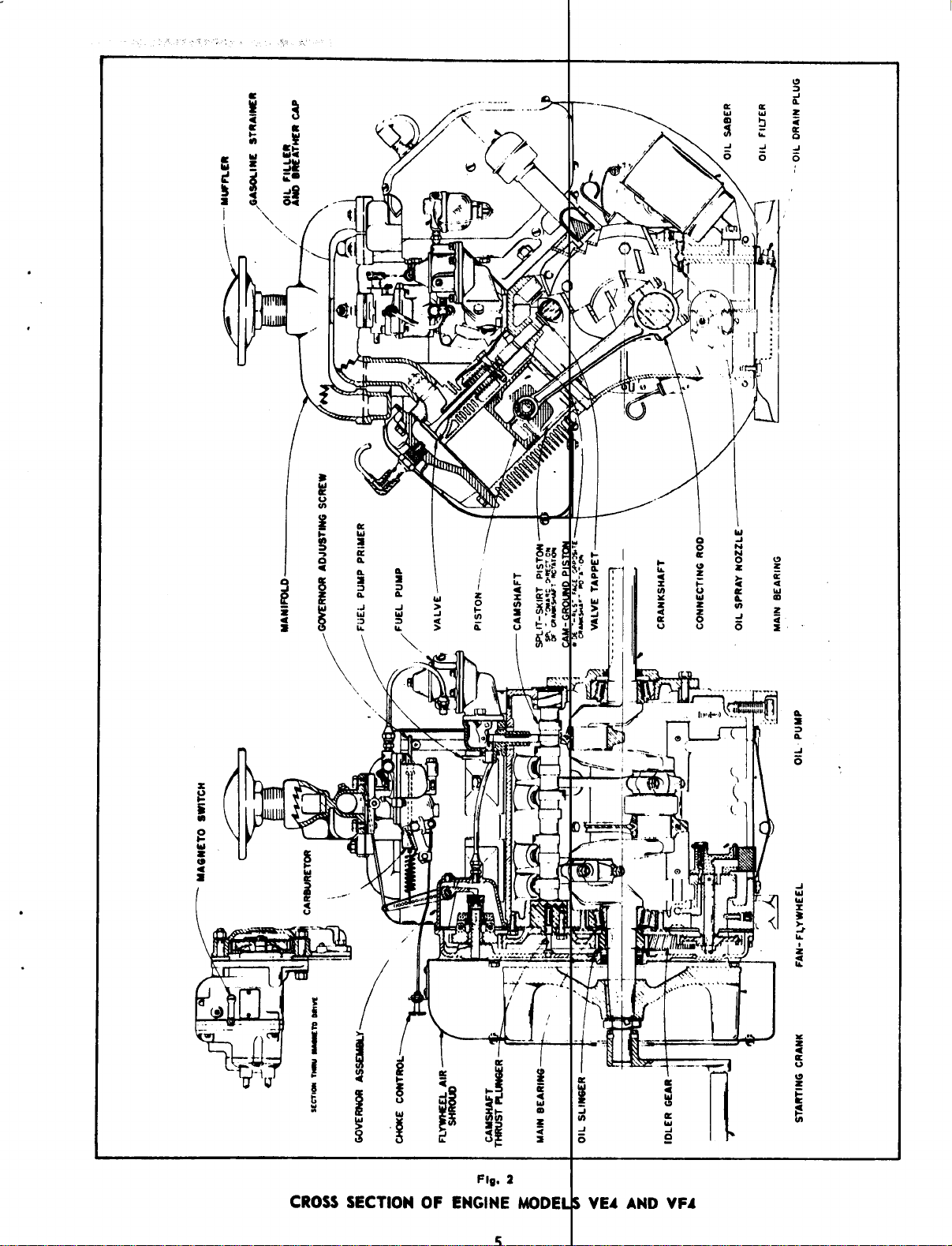
C>
::J
II:
W
3
C
II:
II:
I-
til
II:~
..,
Z
i
c
"'-
",
..,Ii
:jW
i::.
..Ji
04
-,
•
r
u
en
II:
III
rt
~
a
I
at:
... ...
CD
~
at:
!:J
;:;:
..J
0
..J
CL
z
C
at:
Q
..J
(5
%
~
i
..
e
..,
z
III
c
a
...
>
..J
~
C>
;
I
z
o
I-
en
~
z
ii
c
...
III
Z
Ci
::IE
Fig. 2
CROSS SECTION OF ENGINE
..J
s
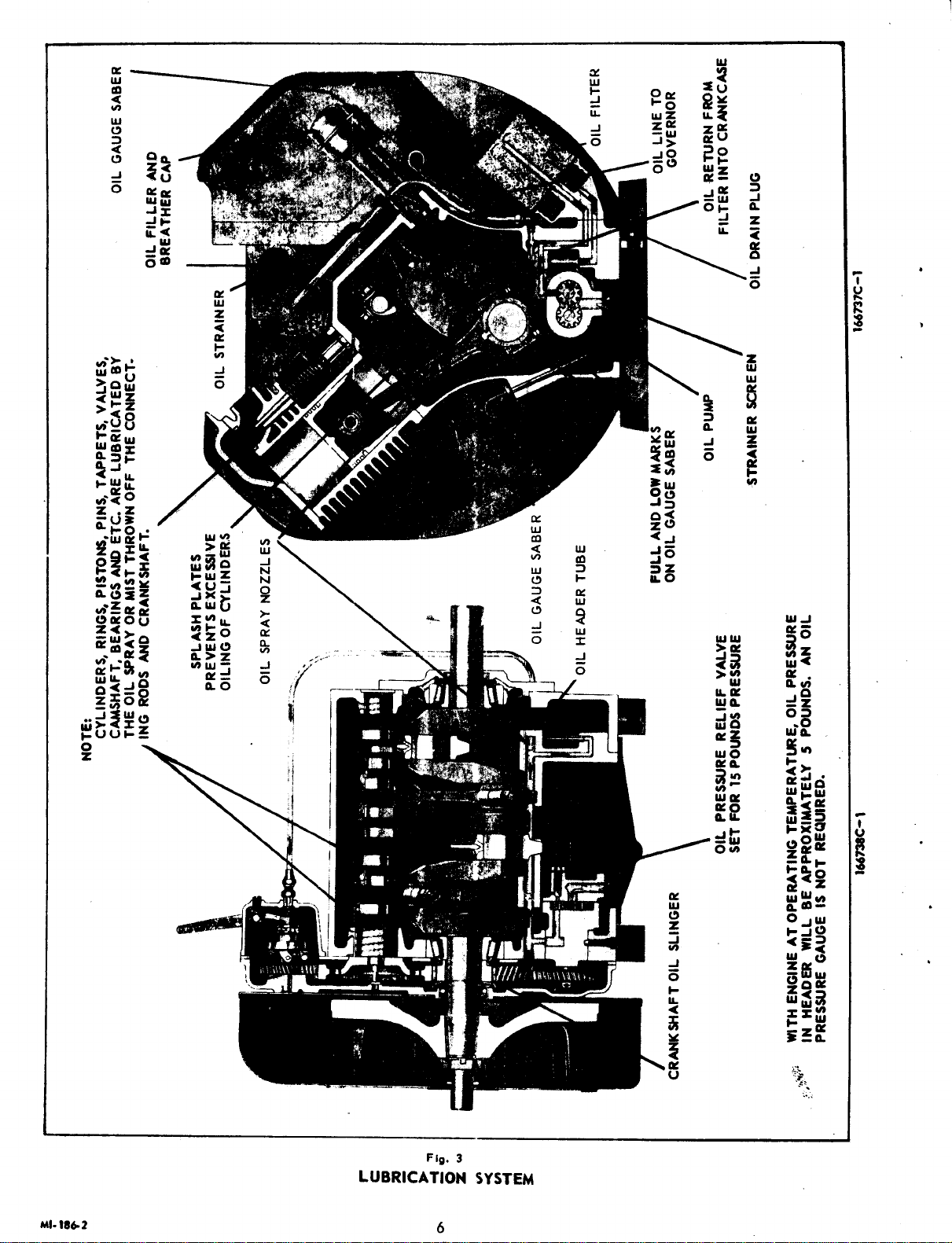
:-------
co
...:
'"
W
(.)
;:)
-e
o
..J
o
w
-c
V)
-c
CO
W
e
::::l
o
w
CO
;:)
I-
0:
w
~
W
J:
~
W
I-
..J
w
~3
i:w:
IL~
Zlll:
IlI:U
~~
Wz
q:-
... 1lI:
-W
O'_
IL
=
e
;:)
...
~
Z
~
~
...
(5
-
~
I:!
I
!
z
W
W
III:
~
III:
"'Ill:
:W:
w
~CO
~~
·W
0"
...
;:)
0"':
z"
...:
...
...
-
....0
:::tZ
ILO
W
Z
-
III:
._
lit
WW
~III:
-c5J
>."
w
ILIII:
W~
:::;~
~~
WO
III:~
51'"
.,,-
Will:
::2
-c
W ...
111:-
51
0
."Z
w-C
III:
~.,;
... 0
_Z
0;:)
_0
W~
!'"
...
-c~ .
III:WO
W'_W
'-c!!
w
2;:)
._;;CO
"o~
!f ...
...~o
~ Z
wW."
~co-
O ...W
......
-c-;:)
.-c
w "
!8i
"0111:
z-C5J
Ww
:2::2:'"
... W
-zlII:
.-~
"
,
-
U
i
w
MI. 186-2
Fig. 3
LUBRICATION SYSTEM
6
~~
·.t~..
...•
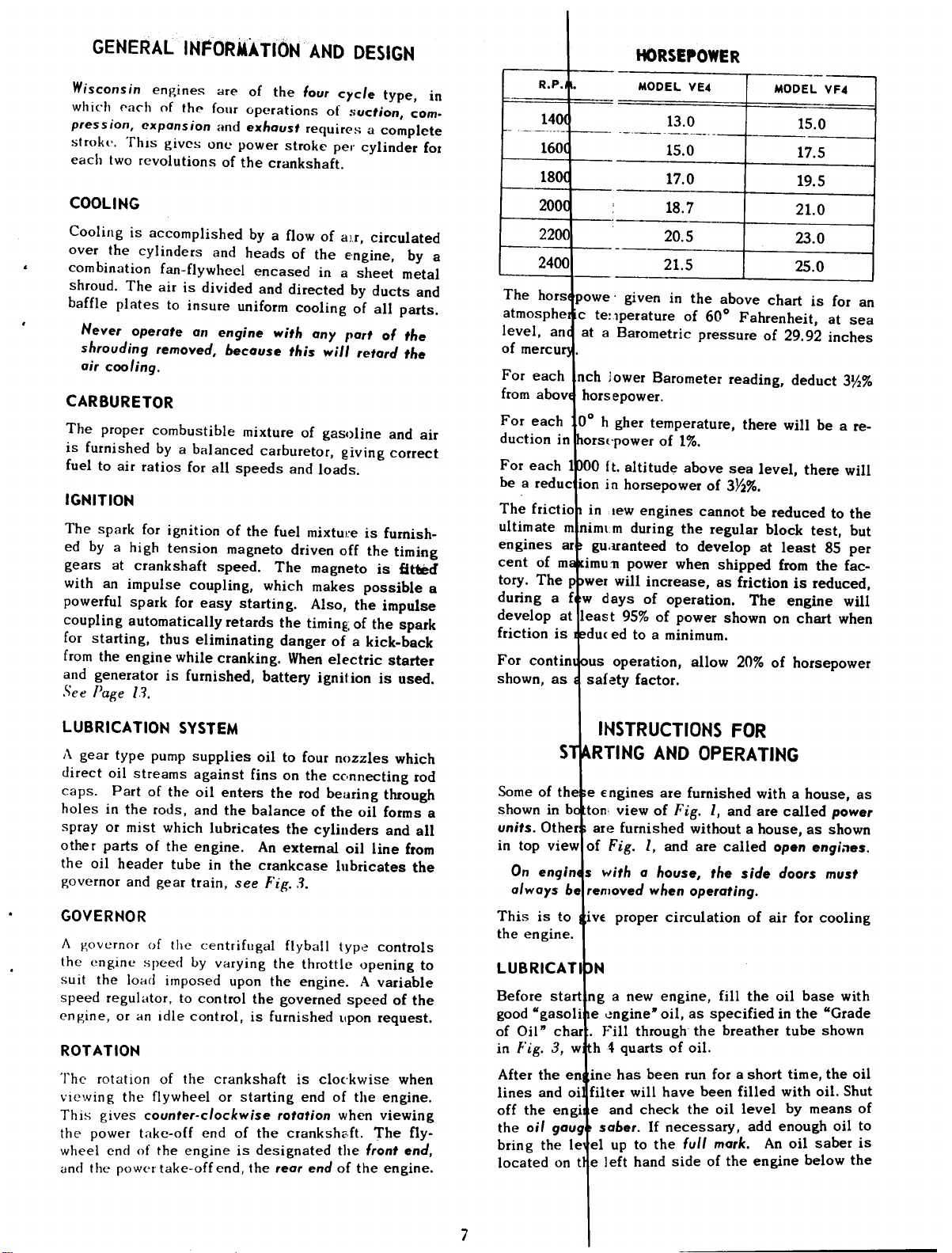
GENERAL ··INFORMATION·AND DESIGN
Wisconsin engines are of the four cycle type, in
which each of the four operations of suction, com.
pressio~, expansion and exhaust requires a complete
stroke, I'hrs grves one power stroke per cylinder for
each two revolutions of the crankshaft.
COOLING
Cooling is accomplished by a flow of au, circulated
over. the. cylinders and heads of the engine, by a
combination fan-flywheel encased in a sheet metal
shroud. The air is divided and directed by ducts and
baffle plates to insure uniform cooling of all parts.
Never operate an engine with any I'art 01 the
shrouding removed, because this will retard the
air cooling.
CARBURETOR
The proper combustible mixture of gasoline and air
is furnished by a balanced carburetor, giving correct
fuel to air ratios for all speeds and loads.
IGNITION
The spark for ignition of the fuel mixture is furnish.
ed by a high tension magneto driven off the timing
gears at crankshaft speed. The magneto is fitted
with an impulse coupling, which makes possible a
powerful spark for easy starting. Also, the impulse
coupling automatically retards the timing;of the spark
for starting, thus eliminating danger of a kick-back
from the engine while cranking. When electric starter
and generator is furnished, battery ignition is used.
See Page
n.
R.P.
140(
-
.
~----.~---
160(
180(
200(]
2200
2400
The
hors
atmosphe
level, ant
of mercurjt,
For each
from above
For each
duction in
For each 1
be a reduc
The frictio
ultimate m
engines ar
cent of rna
tory. The p
during a f
develop at
friction is
For contim
shown, as
HORSEPOWER
I.
r----
MODEL VE4
-_
..
_-----_._---
13,0
15.0
17.0
,
18.7
20,S
21.5
powe'
horse
pOO
given in the above chart is for an
c te:
rperature of 60° Fahrenheit, at sea
at a
Barometric pressure of 29.92 inches
nch
j
ower Barometer reading, deduct 3~%
hors
epower.
0° h
gher temperature, there will be a re-
power of 1%.
ft
. altitude above sea level, there will
ion
i
n horsepower of
in
I
ew engines cannot be reduced to the
nirm,
m during the regular block test, but
e gu.
aranteed to develop at least 85 per
~imu.
:n
power when shipped from the fac-
pwer
will increase, as friction is reduced,
w d
ays of operation. The engine will
least
95% of power shown on chart when
educ
ed to a minimum.
~us
operation, allow 20% of horsepower
safe
ty factor.
-----
3Y2%.
MODEL VF4
15.0
17.5
19.5
21.0
23.0
25.0
LUBRICATION SYSTEM
A gear type pump supplies oil to four nozzles which
direct oil streams against fins on the connecting rod
caps, Part of the oil enters the rod bearing through
holes in the rods, and the balance of the oil forms a
spray or mist which lubricates the cylinders and all
other parts of the engine. An external oil line from
the oil header tube in the crankcase lubricates the
governor and gear train, see Fig.
.1.
GOVERNOR
1\
governor of the centrifugal flyball type controls
the engine speed by varying the throttle opening to
suit the load imposed upon the engine. A variable
speed regulator, to control the governed speed of the
engine, or an idle control, is furnished upon request.
ROTATION
The rotation of the crankshaft is clockwise when
viewing the flywheel or starting end of the engine.
This gives counter-clockwise rotation when viewing
the power take-off end of the crankshaft. The fly-
wheel end of the engine is designated the front end,
and the power take-off end, the rear end of the engine.
IN
ST
~RT
Some of the
shown in bo
units. Other
in top view
On
engin
always be
This is to
the engine.
LUBRICAT IlN
Before start
good "gasol
of Oil" cha
in
Fig.
After the enine
lines and
off the engi e a
the oil gaug
bring the Ie el
located on
e En
ton,
are
of
s
WI
rem
ivt
ng
i e e
r. F'
3, w h 4
i filt
0
sa
t e le
STRUCTIONS FOR
ING AND OPERATING
gines are furnished with a house, as
view of
furnished without a house, as shown
Fig. 1, and are called open engi01es.
'thahouse, the side doors must
oved when operating.
proper circulation of air for cooling
a new engine, fill the oil base with
ngine" oil, as specified in the "Grade
III through the breather tube shown
quarts of oil.
has been run for a short time, the oil
er will have been filled with oil. Shut
nd check the oil level by means of
ber.Ifnecessary, add enough oil to
up to the full mark. An oil saber is
ft hand side of the engine below the
Fig.
1, and are called power
7
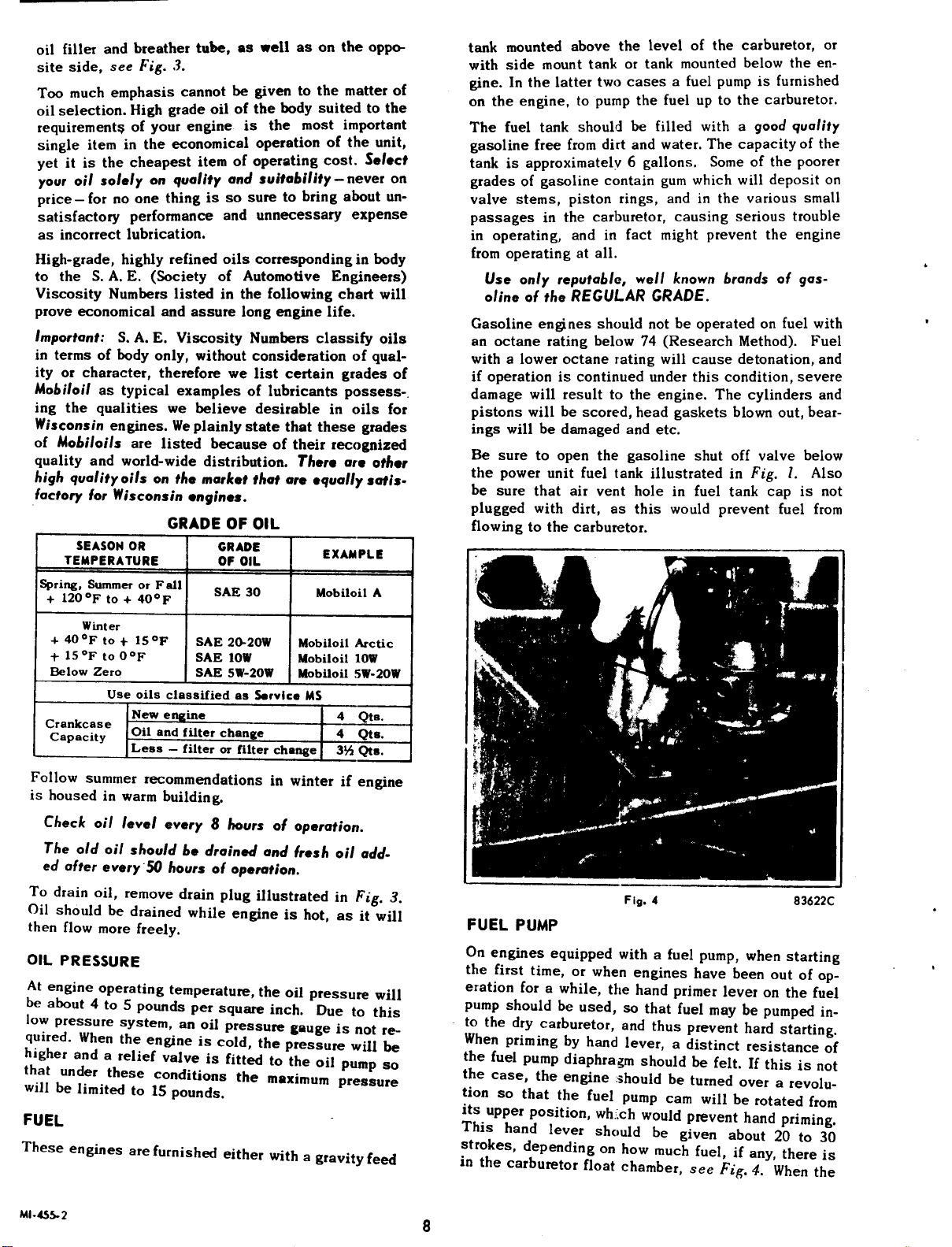
oil filler and breather tube, as well as on the oppo-
site side,
see
Fig. 3.
Too much emphasis cannot be given to the matter of
oil selection. High grade oil of the body suited to the
requirements
of your engine is the most important
single item in the economical operation of the unit,
yet it is the cheapest item of operating cost. Se'ect
your oi' so'.'y on
quality
and suitabi'ity-never on
price - for no one thing is so sure to bring about un-
satisfactory performance and unnecessary expense
as incorrect lubrication.
High-grade, highly refined oils corresponding in body
to theS.A.E. (Society of Automotive Engineers)
Viscosity Numbers listed in the following chart will
prove economical and assure long engine life.
Important:
S.A.E. Viscosity Numbers classify oils
in terms of body only, without consideration of qual-
ity or character, therefore we list certain grades of
Mobi'oi' as typical examples of lubricants possess-.
ing the qualities we believe desirable in oils for
Wisconsin engines. Weplainly state that these grades
of Mobi'oi's are listed because of their recognized
quality and world-wide distribution. There are other
high
qualityoi's on
the
marle.t
that
are
equally
soti.-
lactory lor Wisconsin eng;n••.
GRADE OF OIL
SEASON OR
TEMPERATURE
Spring,
Summeror Fall
+
120OF to ... 40°F
GRADE
OF OIL
SAE 30
EXAMPLE
Mobiloil A
tank mounted above the level of the carburetor, or
with side mount tank or tank mounted below the en-
gine. In the latter two cases a fuel pumpis furnished
on the engine, to pumpthe fuel up to the carburetor.
The fuel tank should be filled with a
good quality
gasoline free from dirt and water. The capacity of the
tank is approximately6gallons. Someof the poorer
grades of gasoline contain gumwhich will deposit on
valve stems, piston rings, and in the various small
passages in the carburetor, causing serious trouble
in operating, and in fact might prevent the engine
fromoperating at all.
Use
only reputable, well known brands
o'ine of
the REGULAR GRADE.
of
gas-
Gasoline engines should not be operated on fuel with
an octane rating below 74 (Research Method). Fuel
with a lower octane rating will cause detonation, and
if operation is continued under this condition, severe
damage will result to the engine. The cylinders and
pistons will be scored, head gaskets blown out, bear-
ings will be damaged and etc.
Be sure to open the gasoline shut off valve below
the power unit fuel tank illustrated in
Fig.
1.
Also
be sure that air vent hole in fuel tank cap is not
plugged with dirt, as this would prevent fuel from
flowing to the carburetor.
Winter
... 40°F to+15°F
+
15°F to OOF
Below Zero
Use oils classified as Service MS
Crankcase
Capacity
Newell2ine
Oil and filter change
Less - filter or filter change
SAE 2~20W
SAE lOW
SAE 5W-20W
Mobiloil Arctic
Mobiloil lOW
Mobiloil 5W-20W
4 Qts.
4 Qts.
3Y.1Qts.
Follow summer recommendations in winter if engine
is housed in warm building.
Check oil
The old oil
ed after every'SO
T~ drain oil, remove drain plug illustrated in
011
should be drained while engine is hot, asitwill
'eve' every 8 hours 01 operation.
shou'd be drained and Iresh oil
hours of operation.
add-
Fig. 3.
then flow more freely.
OIL PRESSURE
At engine operating temperature, the oil pressure will
be about 4 to 5 pounds per square inch. Due to this
lo~ pressure system, an oil pressure gauge is not re-
q~lred. Whenthe engine is cold, the pressure will be
higher and a relief valve is fitted to the oil pump so
th.at und~r. these conditions the maximum pressure
Willbe Iimited to15pounds.
FUEL
These engines are furnished either with a gravity feed
Fig. 4
83622C
FUEL PUMP
On engines equipped with a fuel pump, when starting
the first time, or when engines have been out of op-
eration for a while, the hand primer lever on the fuel
pump should be used, so that fuel may be pumped in-
to the d~y.carburetor, and thus prevent hard starting.
When
pnmmg
by hand lever, a distinct resistance of
the fuel pump diaphragm should be felt.Ifthis is not
the case, the engine should be turned over a revolu-
!ion so that the fuel pump cam will be rotated from
ItS.upper posttton, which would prevent hand priming.
ThIS hand lever should be given about
20to30
~trokes, depending on how much fuel, if any, there is
In the carburetor
float
chamber,
see
Fig.
4. Whenthe
MI·4S5-2
8
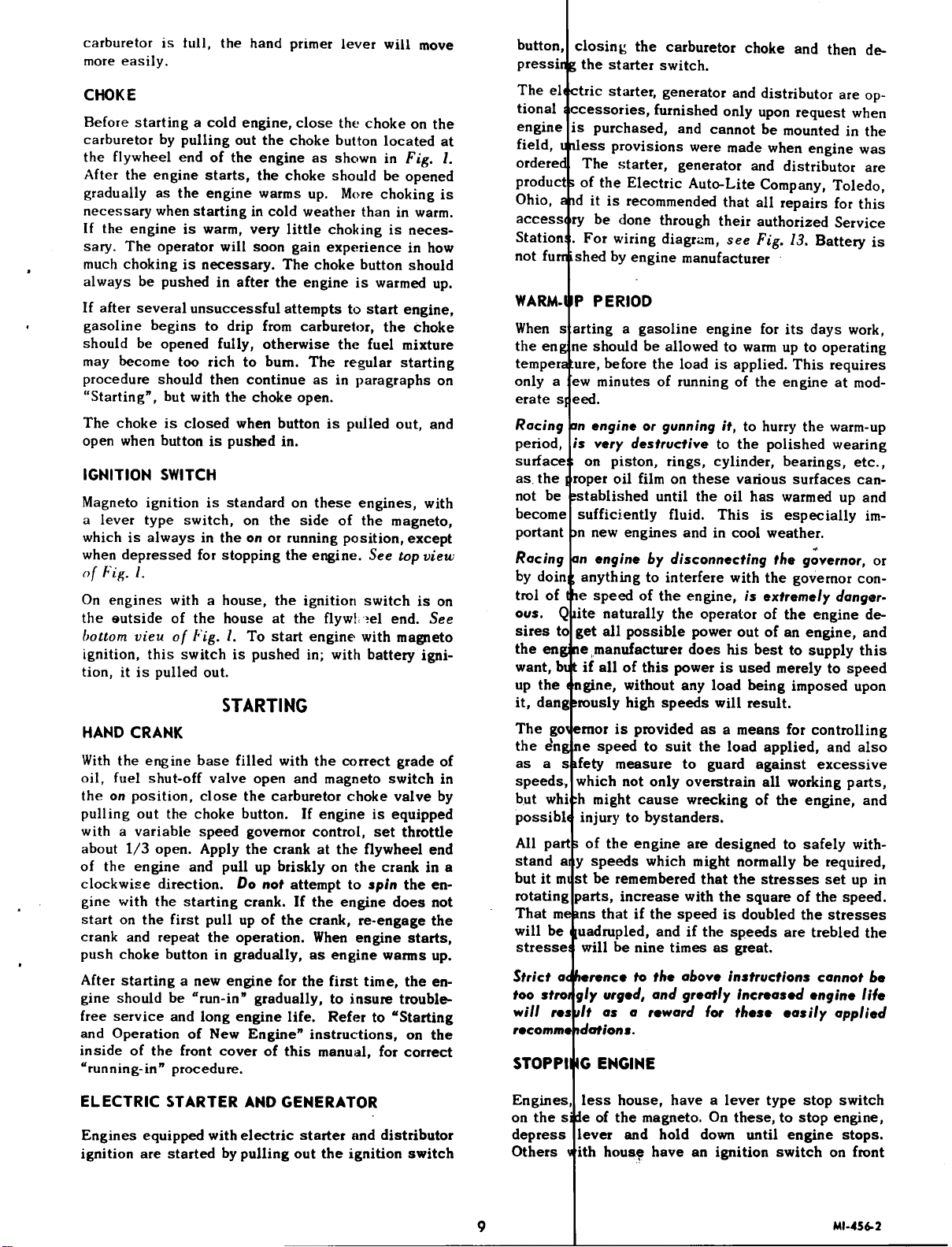
carburetor is tull, the hand primer lever will move
more easily.
CHOKE
Before starting a cold engine, close the choke on the
carburetor by pulling out the choke button located at
the flywheel end of the engine as shown in
Fig. 1.
After the engine starts, the choke should be opened
gradually as the engine warms up. Morechoking is
necessary whenstarting in cold weather than in warm.
If
the engine is warm, very little choking is neces-
sary. The operator will soon gain experience in how
muchchoking is necessary. The choke button should
always be pushed in after the engine is warmedup.
H
after several unsuccessful attempts to start engine,
gasoline begins to drip from carburetor, the choke
should be opened fully, otherwise the fuel mixture
may become too rich to bum. The regular starting
procedure should then continue as in paragraphs on
"Starting", but with the choke open.
The choke is closed when button is pulled out, and
open when button is pushed in.
IGNITION SWITCH
Magneto ignition is standard on these engines, with
a
lever type switch, on the side of the magneto,
which is always in the on or running position, except
whendepressed for stopping the engine.
of
Fig. I.
See top view
On engines with a house, the ignition switch is on
the eutside of the house at the
bottom vieu of
Fig.
1. To start engine with magneto
flywl:
-el end.
See
ignition, this switch is pushed in; with battery igni-
tion, it is pulled out.
STARTING
HAND CRANK
Withthe engine base filled with the correct grade of
oil, fuel shut-off valve open and magneto switch in
the on position, close the carburetor choke valve by
pulling out the choke button.
with a variable speed governor control, set throttle
about 1/3 open. Apply the crank at the flywheel end
of the engine and pull up briskly on the crank in a
clockwise direction.
Do
gine with the starting crank.Ifthe engine does not
start on the first pull up of the crank, re-engage the
crank and repeat the operation. Whenengine starts,
push choke button in gradually, as engine warms up.
After starting a new engine for the first time, the en-
gine should be "run-in" gradually, to insure trouble-
free service and long engine life. Refer to "Starting
and Operation of New Engine" instructions, on the
inside of the front cover of this manual, for correct
"running-in" procedure.
If
engine is equipped
not attempt to
spin
the en-
button, closing the carburetor choke and then de-
the starter switch.
tric
starter, generator and distributor are op-
tional ccessories, furnished only upon request when
is purchased, and cannot be mounted in the
less provisions were made when engine was
The starter, generator and distributor are
of the Electric Auto-Lite Company,Toledo,
d it is recommendedthat all repairs for this
ry be done through their authorized Service
. For wiring
diagram, see
Fig.
13.
Battery is
shed by engine manufacturer
When s arting a gasoline engine for its days work,
the en ne should be allowed to warmup to operating
temper ure, before the load is applied. This requires
only a ew minutes of running of the engine at mod-
eed.
Racing n engine or gunning it, to hurry the warm-up
period, is very destructive to the polished wearing
surface on piston, rings, cylinder, bearings, etc.,
as, the roper oil film on these various surfaces can-
not be stablished until the oil has warmed up and
become sufficiently fluid. This is especially im-
portant n new engines and in cool weather.
Racing
n engine
by
disconnecting the g~vernor, or
by doin anything to interfere with the governorcon-
trol of e speed of the engine, is extremely danger.
ous.
Q
ite naturally the operator of the engine de-
sires to get all possible power out of an engine, and
the en e ,manufacturerdoes his best to supply this
if all of this power is used merely to speed
up the ngine, without any load being imposed upon
it, dang rously high speeds will result.
The go emor is provided as a means for controlling
the ~n ne speed to suit the load applied, and also
as a s fety measure to guard against excessive
speeds, which not only overstrain all working parts,
but
whi h might cause wrecking of the engine, and
possibl injury to bystanders.
All part of the engine are designed to safely with-
stand a y speeds which might normally be required,
but it m st be rememberedthat the stresses set up in
rotating parts, increase with the square of the speed.
That m. ns that if the speed is doubled the stresses
will be uadrupled, andifthe speeds are trebled the
will be nine times as great.
too stro
will
res
erence
gly
It
to
tlte above instructions cannot be
urged,
and
greatly
Increased engine
as a rewarel lor tltes.
easily
lile
applieel
elations.
ELECTRIC STARTER AND GENERATOR
Engines equipped withelectric starter and distributor
ignition are started bypulling out the ignition switch
Engines, less house, have a lever type stop switch
on the si e of the magneto. On these, to stop engine,
depress lever and hold down until engine stops.
Others ith hous~ have an ignition switch on front
9
MI·"5~2
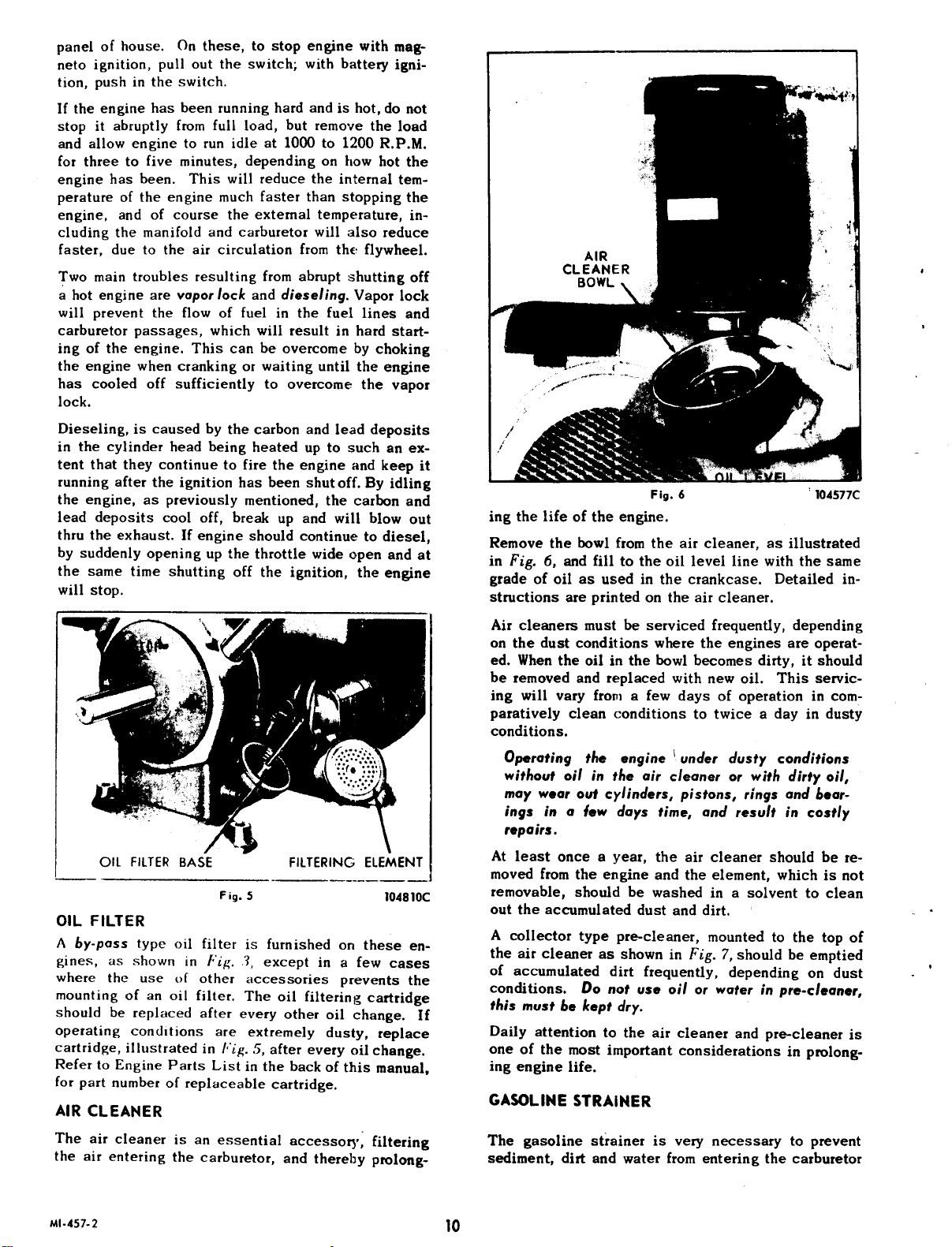
panel of house. On these, to stop engine with mag-
neto ignition, pull out the switch; with battery igni-
tion, push in the switch.
If
the engine has been running hard and is hot, do not
stop it abruptly from full load, but remove the load
and allow engine to run idle at 1000 to 1200 R.P.M.
for three to five minutes, depending on how hot the
engine has been. This will reduce the internal tem-
perature of the engine much faster than stopping the
engine, and of course the external temperature, in-
cluding the manifold and carburetor will also reduce
faster, due to the air circulation from the flywheel.
Two main troubles resulting from abrupt shutting off
a hot engine are
vapor lock
and
dieseling.
Vapor lock
will prevent the flow of fuel in the fuel lines and
carburetor passages, which will result in hard start-
ing of the engine. This can be overcome by choking
the engine when cranking or waiting until the engine
has cooled off sufficiently to overcome the vapor
lock.
Dieseling, is caused by the carbon and lead deposits
in the cylinder head being heated up to such an ex-
tent that they continue to fire the engine and keep it
running after the ignition has been shut off. By idling
the engine, as previously mentioned, the carbon and
lead deposits cool off, break up and will blowout
thru the exhaust.Ifengine should continue to diesel,
by suddenly opening up the throttle wide open and at
the same time shutting off the ignition, the engine
will stop.
Fig. 6
, 104577C
ing the life of the engine.
Remove the bowl fromthe air cleaner, as illustrated
in
Fig.
6, and fill to the oil level line with the same
grade of oil as used in the crankcase. Detailed in-
structions are printed on the air cleaner.
Oil FilTER BASE
---------
Fig.
FilTERING ElEMENT
._--------_
S
104810C
OIL FILTER
A
by-pass
gines, as shown in
type oil filter is furnished on these en-
Fi,; .. '(
except in a few cases
where the use of other accessories prevents the
mounting of an oil filter. The oil filtering cartridge
should be replaced after every other oil change.
operating conditions are extremely dusty, replace
cartridge, illustrated in
Fil!..
5, after every oil change.
Refer to Engine Parts List in the back of this manual,
for part numberof replaceable cartridge.
AIR CLEANER
Air cleaners mustbeserviced frequently, depending
on the dust conditions where the engines are operat-
ed. Whenthe oil in the bowl becomes dirty, it should
be removed and replaced with new oil. This servic-
ing will vary from a few days of operation in com-
paratively clean conditions to twice a day in dusty
conditions.
Operating the
without oil in
may wear out
ings
in a lew
engine \ under dusty
the
air
cleaner or
conditions
with dirty oil,
cylinders, pistons, rings and
days
time, and result
in
bear-
costly
repairs.
At least once a year, the air cleaner should be re-
moved fromthe engine and the element, which is not
removable, should be washed in a solvent to clean
out the accumulated dust and dirt.
A collector type pre-cleaner, mounted to the top of
the air cleaner as shown in
Fig.
7,should be emptied
of accumulated dirt frequently, depending on dust
conditions.
this
If
must be
Do
not use
leept dry.
oilorwater
in pr&-cleaner,
Daily attention to the air cleaner and pre-cleaner is
one of the most important considerations in prolong-
ing engine life.
GASOLINE STRAINER
The air cleaner is an essential accessory, filtering
the air entering the carburetor, and thereby prolong-
MI·4S7.2
The gasoline strainer is very necessary to prevent
sediment, dirt and water fromentering the carburetor
10
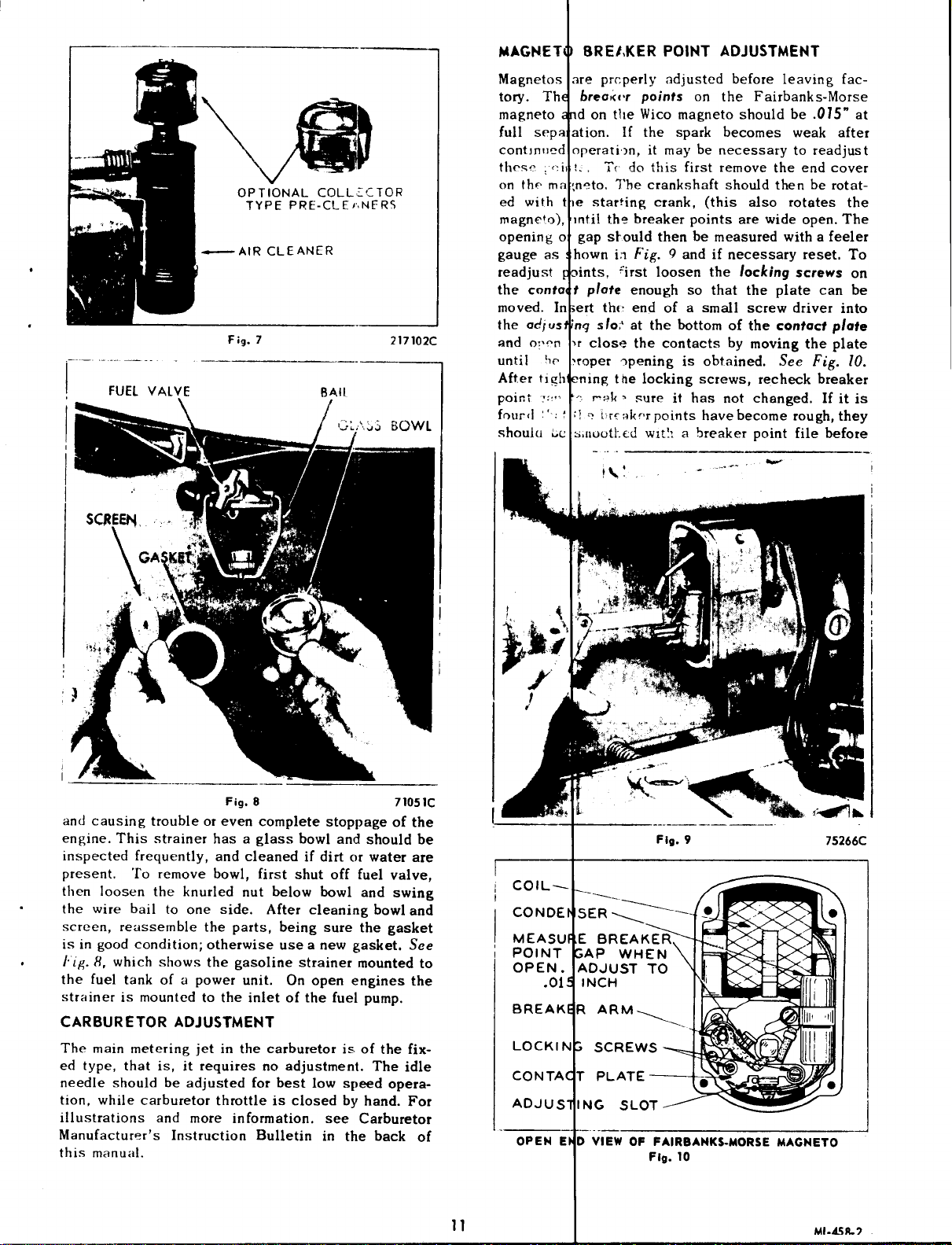
FUEl VALVE
Fig. 7
BAli
217102C
BREJ,KER POINT ADJUSTMENT
are properly adjusted before leaving fac-
breaKI'r points on the Fairbanks-Morse
on the Wico magneto should be
full
sep
ation.
continued operat
to.
If
the spark becomes weak after
ion, it may be necessary to readjus t
Tr do this first remove the end cover
.015"
to. The crankshaft should then be rot at-
starting crank, (this also rotates the
magneto), mtil the breaker points are wide open. The
opening
0
gap sbould then be measured with a feeler
hown in Fig. 9 andifnecessary reset. To
s. first
loosen the locking screws on
plate enough so that the plate can be
moved. I
the ad;
the end of a small screw driver into
s
10;'
at the bottom of the
contact
plate
close the contacts by moving the plate
until
After
ti
point ";'''
four
d :'., ~
shoulu cc
opening is obtained. See Fig. 10.
ning the locking screws, recheck breaker
r"k>sure
:) ~ i.rr
akr-r
it
has not changed.
If
it is
points have become rough, they
s.nootl.cd with a breaker point file before
at
Fig. 8 71051C
and causing trouble or even complete stoppage of the
engine. This strainer has a glass bowl and should be
inspected frequently, and cleanedifdirt or water are
present. To remove bowl, first shut off fuel valve,
then loosen the knurled nut below bowl and swing
the wire bail to one side. After cleaning bowl and
screen, reassemble the parts, being sure the gasket
is in good condition; otherwise use a new gasket. See
Fil!..8, which shows the gasoline strainer mounted to
the fuel tank of a power unit. On open engines the
strainer is mounted to the inlet of the fuel pump.
CARBURETOR ADJUSTMENT
The main metering jet in the carburetor is of the fix-
ed type, that is,itrequires no adjustment. The idle
needle should be adjusted for best low speed opera-
tion, while carburetor throttle is closed by hand. For
illustrations and more information. see Carburetor
Manufacturer's Instruction Bulletin in the back of
this manual.
11
75266C
VIEW OF FAIRBANKS.MORSE MAGNETO
Fig. 10
MI.45R..?
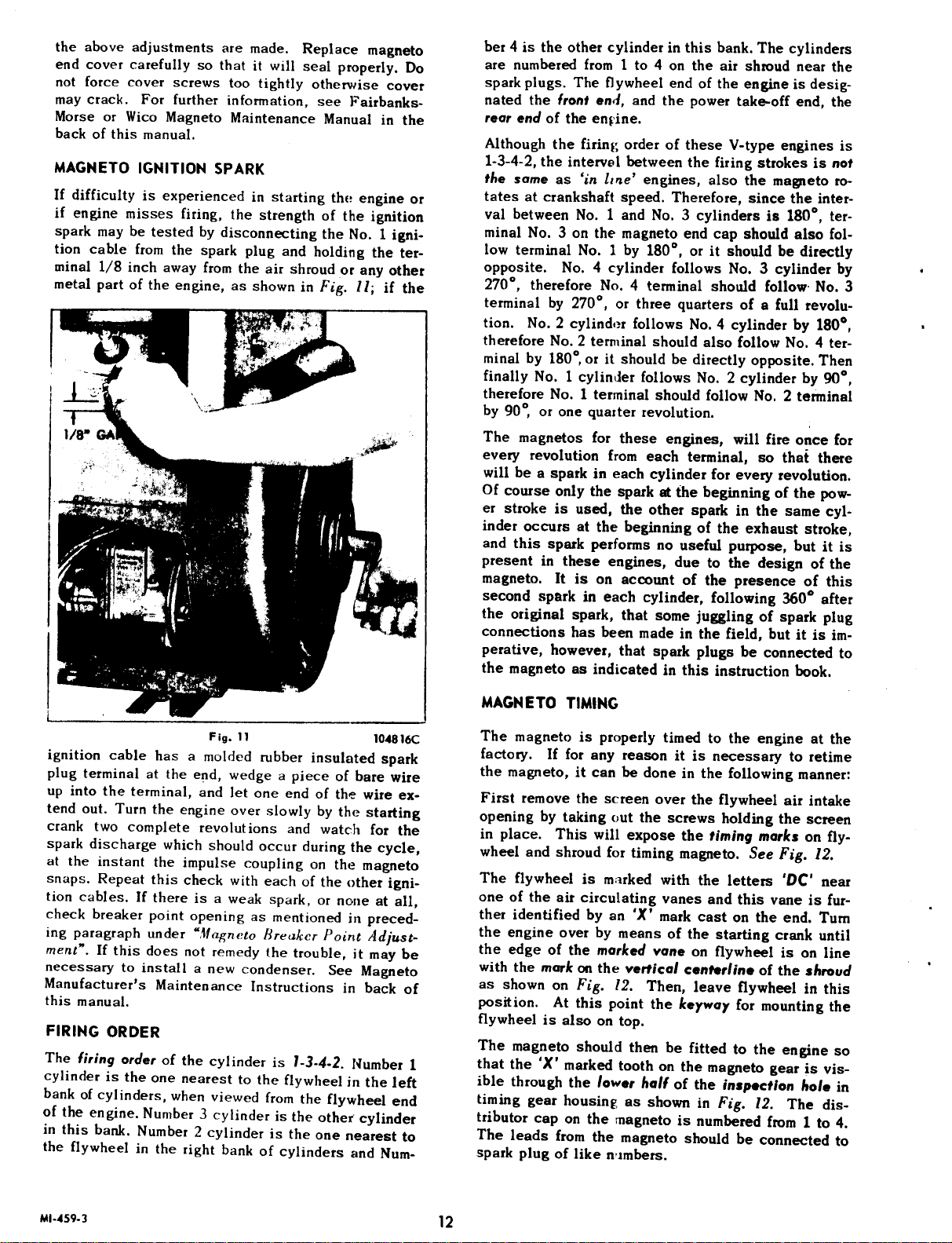
the above adjustments are made. Replace magneto
end cover carefully so that it will seal properly. Do
not force cover screws too tightly otherwise cover
may crack. For further information, see Fairbanks-
Morse or Wico Magneto Maintenance Manual in the
back of this manual.
MAGNETO IGNITION SPARK
If
difficulty is experienced in starting the engine or
if
engine misses firing, the strength of the ignition
spark maybe tested by disconnecting the No. 1 igni-
tion cable from the spark plug and holding the ter-
minal 1/8 inch away from the air shroudor any other
metal part of the engine, as shown in
Fig.
11; if the
ber 4 is the other cylinder in this bank.The cylinders
are numbered from 1 to 4 on the air shroud near the
spark plugs. The flywheel end of the engine is desig-
nated the
rear end
Iront
en,l, and the power take-off end, the
of the engine.
Although the firing order of these V-type engines is
1-3-4-2,the interval between the firing strokes is not
the
same as
'in
line'
engines, also the magneto ro-
tates at crankshaft speed. Therefore, since the inter-
val between No.1 and No.3 cylinders is 180°, ter-
minal No. 3 on the magneto end cap should also fol-
low terminal No.1 by 180°, or it should be directly
opposite. No. 4 cylinder follows No. 3 cylinder by
270°, therefore No.4 terminal should follow·No.3
terminal by 270°, or three quarters of a full revolu-
tion. No.2 cylinder follows No.4 cylinder by 180°,
therefore No.2 terminal should also follow No.4 ter-
minal by 180°,or it should be directly opposite. Then
finally No.1 cylinder follows No.2 cylinder by 90°,
therefore No.1 terminal should follow No.2 terminal
by 90°, or one quarter revolution.
The magnetos for these engines, will fire once for
every revolution from each terminal, so that there
will be a spark in each cylinder for every revolution.
Of course only the sparkatthe beginning of the pow-
er stroke is used, the other spark in the same cyl-
inder occurs at the beginning of the exhaust stroke,
and this spark performs no useful purpose, but it is
present in these engines, due to the design of the
magneto. It is on account of the presence of this
second spark in each cylinder, following 3600after
the original spark, that some juggling of spark plug
connections has been made in the field, but it is im-
perative, however, that spark plugs be connected to
the magneto as indicated in this instruction book.
Fig. 11 10..S16C
ignition cable has a molded rubber insulated spark
plug terminal at the end, wedge a piece of bare wire
up into the terminal, and let one end of the wire ex-
tend out. Turn the engine over slowly by the starting
crank two complete revolutions and watch for the
spark discharge which should occur during the cycle,
at the instant the impulse coupling on the magneto
snaps. Repeat this check with each of the other igni-
tion cables.
If
there is a weak spark, or none at all,
check breaker point opening as mentioned in preced-
ing paragraph under
ment".
If
this does not remedy the trouble, it may be
"Ma~n(!to Breaker Point Adjust-
necessary to install a new condenser. See Magneto
Manufacturer's Maintenance Instructions in back of
this manual.
FIRING ORDER
The
liring order
of the cylinder is 1-3-4-2. Number 1
cylinder is the one nearest to the flywheel in the left
bank of cylinders, when viewed from the flywheel end
of the engine. Number3 cylinder is the other cylinder
in this bank. Number2 cylinder is the one nearest to
the flywheel in the right bank of cylinders and Num-
MAGNETO TIMING
The magneto is properly timed to the engine at the
factory.
If
for any reason it is necessary to retime
the magneto, it canbedone in the following manner:
First remove the screen over the flywheel air intake
opening by taking out the screws holding the screen
in place. This will expose the
wheel and shroud for timing magneto.
The flywheel is marked with the letters
timing
marieson fly-
See Fig. 12.
'DC'
near
one of the air circulating vanes and this vane is fur-
ther identified by an
'X'
mark cast on the end. Tum
the engine over by means of the starting crank until
the edge of the
with the
marie
as shown on
position. At this point the
marleed
on the
Fig.
vane on flywheel is on line
vertical
centerline of the sltroud
12. Then, leave flywheel in this
leeyway
for mounting the
flywheel is also on top.
The magneto should then be fitted to the engine so
that the
ible through the
timing gear housing as shown in
'X'
marked tooth on the magneto gear is vis-
lower Itoll
of the inspection
Fig.
12. The dis-
Itole
tributor cap on the magneto is numbered from 1 to 4.
The leads from the magneto should be connected to
spark plug of like numbers,
in
1011·459.3
12
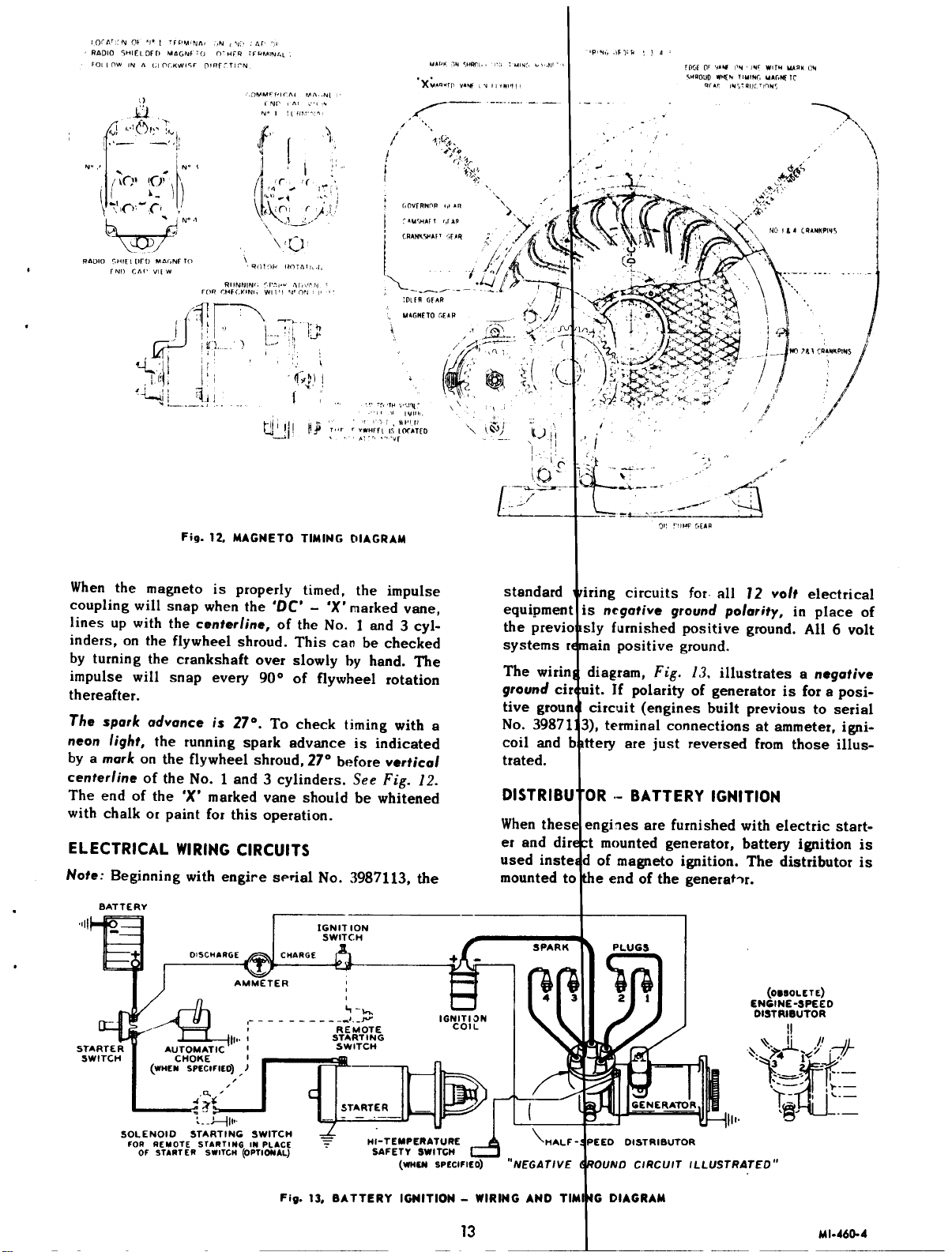
I_O((IT;:'N
or ')-
I
-rF~lM1Ntl.1
;-;1\1::
~c':
I'l.r'
, RAOIO SHIElOHI MAGNf;() ()~HfR iF~M1Nt~l ~
FOI lOW IN
I'l.
CIO(.KWIt;f OIRf:':T:('N
')1
',OMMU~ICI\I MA,.Nt
r Nr~
,..,,31flm,~'~,:
fO('f
('1f
'1."
!'''4 .
l"4
r
WIT ...
~?I(
<,"AOUO
1IfH[I<t
'X~"'Ql(r['1
VA"If
i ~
flVWI'!jl
l'/\!
v'
j ' ..
1\
,~-
./
"
._
...._..
_.
_.
Qr ..n
TlutN(, UA[.Nf rc
i"'~,
'1'
QlJ(,
/
I
I
,
,
0101
1'In".~.
~,
'\
1
j
RADIO SHIH
[If
0 MM,NF
fNO eM' VI! W
Tn
RIIN~J!Nr;
fOR
(;HfCl(lNt; W11'1
;,","'.1'"
''''',,'~.r'J,
<
·,J'n~J I'
. ~~~I
!
'
.....
,
T"r r VWHfrt IS IOCAT£O
'~. ~:".,.,~ ''-''.111. ~
"I! ,11
'!
I'l,r •
.4;'"
"l,'vf
;OlfR GfA,R
U"GNETO (.EAP
IVIIII,
..,d'Ui
Fig. 12, MAGNETO TIMING DIAGRAM
When the magneto is properly timed, the impulse
coupling will snap when the
lines up with the
centerline,
'DC' -
'X' marked vane,
of the No. 1 and 3 cyl-
inders. on the flywheel shroud. This can be checked
by turning the crankshaft over slowly by hand. The
impulse will snap every 900of flywheel rotation
thereafter.
rhe
spark
advance
neon
light,
the running spark advance is indicated
by a mark on the flywheel shroud, 270before
centerline
of the No.1 and 3 cylinders.
The end of the
is 27°. To check timing with a
See Fig. 12.
'X'
marked vane should be whitened
vertical
with chalk or paint for this operation.
ELECTRICAL WIRING CIRCUITS
Note: Beginning with engire serial No. 3987113, the
BATTERY
IGNITION
SWITCH
standard
equipment
the previo
systems r
The wirin diagram,
mng circuits for all 12
is
negative
grou"d
polarity,
volt
electrical
in place of
sly furnished positive ground. All 6 volt
ain positive ground.
Fig.
13. illustrates a
negative
ground cir uit.Ifpolarity of generator is for a posi-
tive groun circuit (engines built previous to serial
No. 39871 3), te-rminalconnections at ammeter, igni-
coil and b ttery are just reversed from those illus-
trated.
DISTRIBU OR·- BATTERY IGNITION
Whenthese engines are furnished with electric start-
er and dir t mounted generator, battery ignition is
used inste d of magneto ignition. The distributor is
mounted to e end of the generahr.
STARTER
SWITCH
----.:1:'.J-...!It.·
SOLENOID STARTING SWITCH
FOR REMOTE STARTING IN PLACE
or STARTER SWITCH(OPTIONAL)
.0, ,
04~':~ __
IGNITION
COil
Fig. 13, BATTERY IGNITION - WIRING AND TIM
13
DISTRIBUTOR
ENC;INE-SPEED
~:~ i~:;t
,LLUSTRATED"
(OI.OlUE)
DISTRIBUTOR
II
~ JL
~: 1]: -[-
• - 't-.-
1:.:
,~-
/.'-If
.i,.v-
I 1\._-
_.-
MI.46O-4
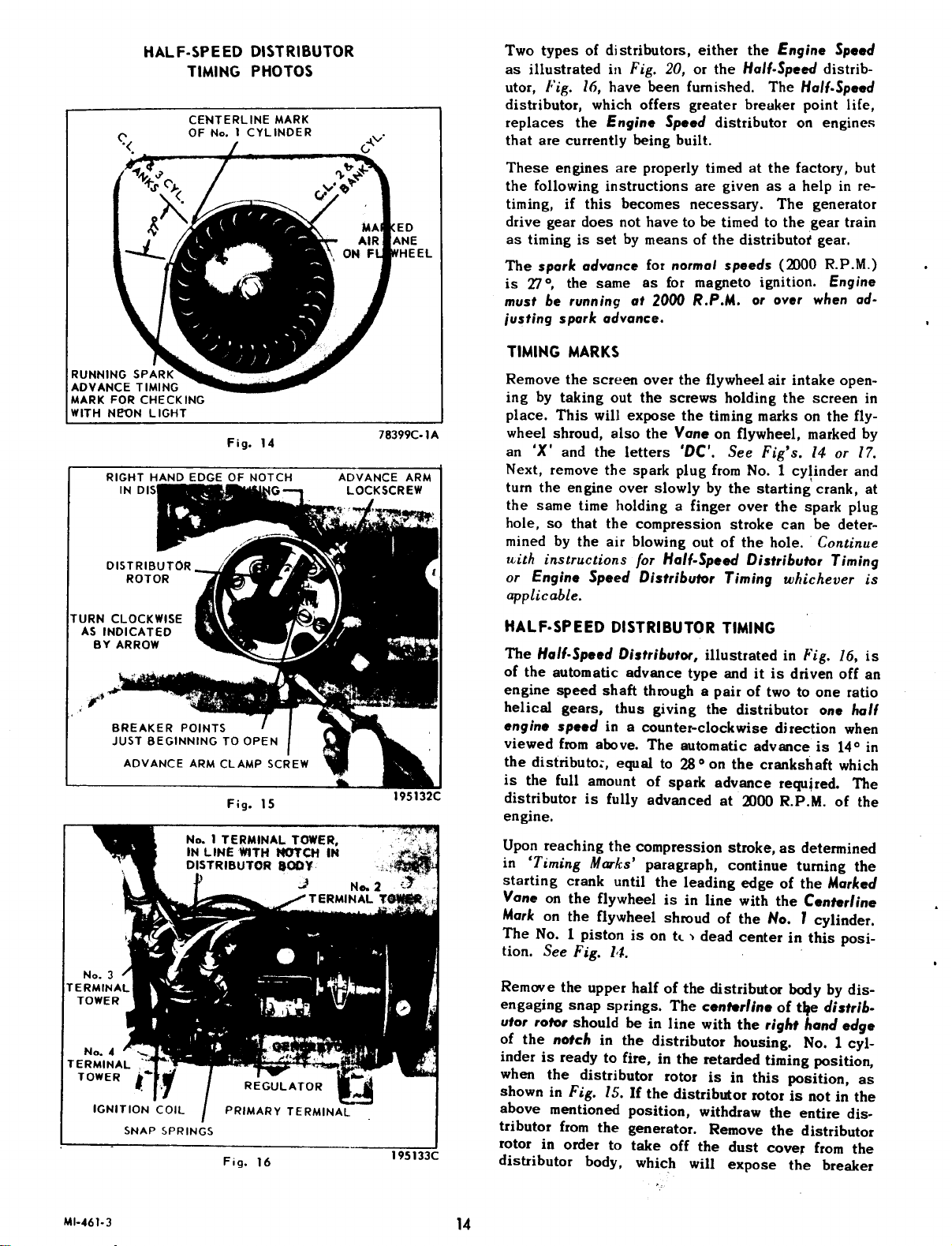
HALF-SPEED DISTRIBUTOR
TIMING PHOTOS
CENTERLINE MARK
OF No. I CYLINDER
RUNNING SPAR
ADVANCE TIMING
MARK FOR CHECKING
WITH NE'ON LIGHT
URN CLOCKWISE
AS INDICATED
BY
ARROW
,.
ADVANCE ARM CLAMP SCREW
No.1 TERMINAL TOWER,
IN LINE WITH I«JTCH IN
DISTRIBUTOR
Fig. 14
Fig. 15
80DY
78399C-1A
Two types of distributors, either the
as illustrated in
utor,
Fig.
Fig. 20,
or the
16, have been furnished. The
Engine
HaU-SpeeJ
HaU-Speed
Speed
distrib-
distributor, which offers greater breaker point life,
replaces the
Engine
Speed distributor on engines
that are currently being built.
These engines are properly timed at the factory, but
the following instructions are given as a help in re-
timing, if this becomes necessary. The generator
drive gear does not have to be timed to the gear train
as timing is set by means of the distributot gear.
The
sparle advance
is
Zl0,the same as for magneto ignition.
must be
running
for
normal
at
2000 R.P.M.
speeds (2000 R.P.M.)
Engine
or over
when ad-
;usting sparle advance.
TIMING MARKS
Remove the screen over the flywheel air intake open-
ing by taking out the screws holding the screen in
place. This will expose the timing marks on the fly-
wheel shroud, also the Vane on flywheel, marked by
an
'X'
and the letters
'DC'. See Fig's. 14 or 17.
Next, remove the spark plug fromNo.1cylinder and
tum the engine over slowly by the starting' crank, at
the same time holding a finger over the spark plug
hole, so that the compression stroke can be deter-
mined by the air blowing out of the hole.
u.ith.
instructions for HaU-SpeeJ Distributor Timing
or Engine
Speed
Distributor Timing whichever is
Continue
applicable.
HALF-SPEED DISTRIBUTOR TIMING
The
Hall-Speed Distributor,
illustrated in
Pig. 16,
of the automatic advance type and it is driven off an
engine speed shaft through a pair of two to one ratio
helical gears, thus giving the distributor one
hall
engine speed in a counter-clockwise direction when
viewed from above. The automatic advance is
thedistributor, equal to
is the full amount of spark advance
distributor is fully advanced at
280on the crankshaft which
required,
:!lOO
R.P.M. of the
140in
The
engine.
Upon reaching the compression stroke, as determined
in
'Timing
starting crank until the leading edge of the
Vane
Marie
The No.1piston is on
tion.
Marks'
paragraph, continue turning the
on the flywheel is in line with the
on the flywheel shroud of the
tc )
dead center in this posi-
No.Jcylinder.
See Fig. U. ..
Marleed
Centerline
is
. I
MI-461-3
SNAP SPRINGS
Fig. 16
195133C
Remove the upper half of the distributor body by dis-
engaging snap springs. The
utor rotor
of the
should be in line with the
notd
in the distributor housing. No.1cyl-
centerline
r;gltt "and edge
inder is ready to fire, in the retarded timing position,
when the distributor rotor is in this position, as
shown in
Fig. 15.Ifthe distributor rotor is not in the
above mentioned position, withdraw the entire dis-
tributor from the generator. Remove the distributor
rotor in order to take off the dust cove, from the
distributor body. which will expose the breaker
14
of tlfe
distrib-
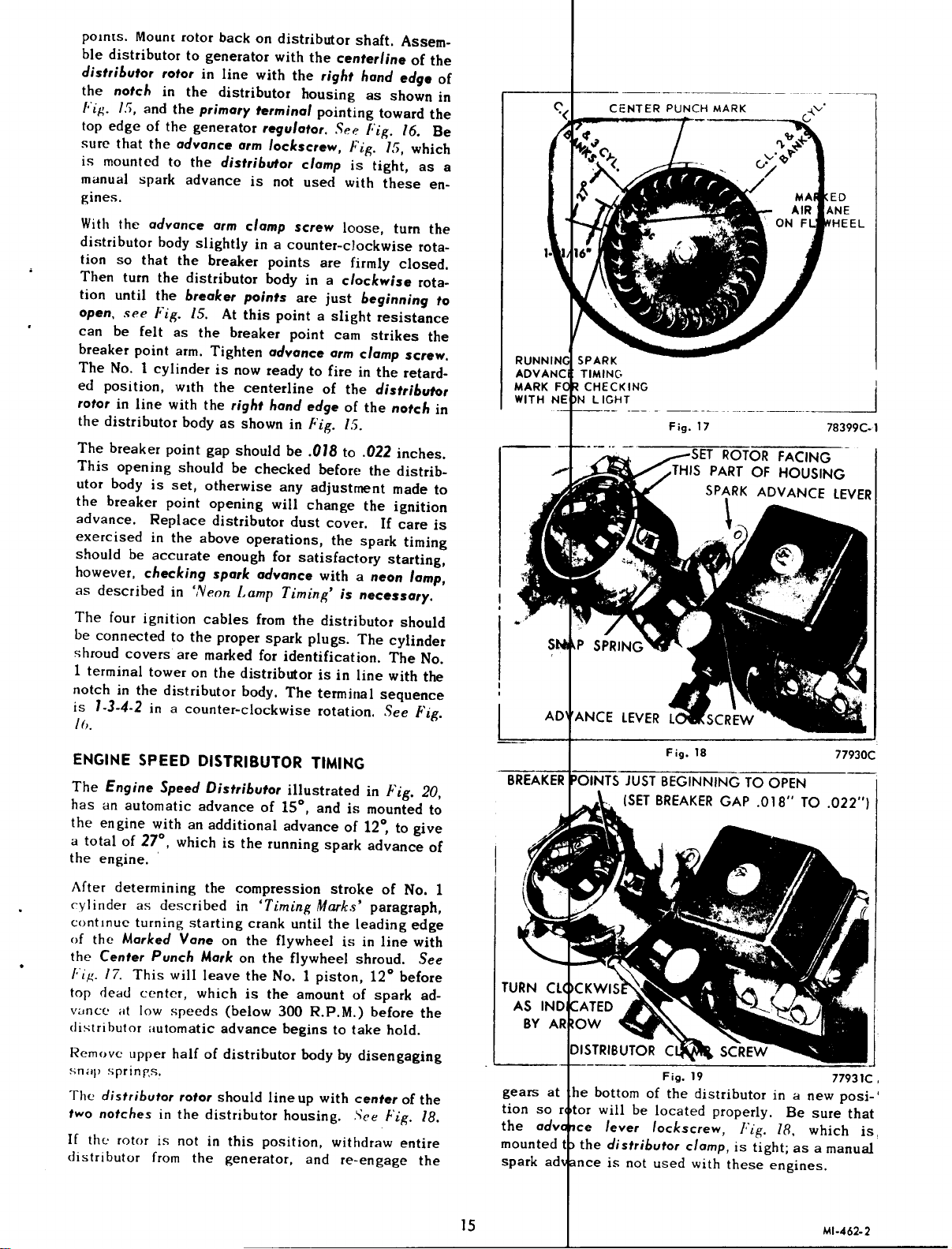
POInlS.
ble distributor to generator with the
distributor rotor
the
Fip,.
top edge of the generator
sure that the
is mounted to the
manual spark advance is not used with these en-
gines.
Moum
notch
15,
rotor back on distributor shaft. Assem-
centerline
in line with the
in the distributor housing as shown in
and the
primary terminal
right hand edge
pointing toward the
regulator. See Fig.
advance arm locks
distributor clomp
crew,
Fig.
15,
is tight, as a
of the
16. Be
which
of
With the
distributor body slightly in a counter-clockwise rota-
tion so that the breaker points are firmly closed.
Then turn the distributor body in a
tion until the
open, see Fig. 15.
can be felt as the breaker point cam strikes the
breaker point arm. Tighten advance
The No.1cylinder is now ready to fire in the retard-
ed position, WIth the centerline of the
rotor
the distributor body as shown in
The breaker point gap should be
This opening should be checked before the distrib-
utor body is set, otherwise any adjustment made to
the breaker point opening will change the ignition
advance. Replace distributor dust cover.
exercised in the above operations, the spark timing
should be accurate enough for satisfactory starting,
however,
as described in
The four ignition cables from the distributor should
be connected to the proper spark plugs. The cylinder
shroud covers are marked for identification. The No.
1 terminal tower on the distributor is in line with the
notch in the distributor body. The terminal sequence
is
1.3.4·2
I
fl.
advance arm clomp
breaker points
At this point a slight resistance
in line with the
right hand edge
checking spark advance
'/Veon Lamp Timing' is
in a counter-clockwise rotation.
screw loose, turn the
are just
arm clomp
clockwise
beginning
rota-
screw.
distributor
of the
notch
Fig. 15.
.018to.022
with a neon
inches.
If
care is
necessary.
See Fig.
lamp,
to
in
78399C.l
SET ROTOR FACING
S PART OF HOUSING
ENGINE SPEED DISTRIBUTOR TIMING
The
Engine Speed Distributor
has an automatic advance of 15°, and is mounted to
the engine with an additional advance of 12°, to give
a total of 27°, which is the running spark advance of
the engine ..
After determining the compression stroke of No.
cylinder as described in
cont
mue turning starting crank until the leading edge
of the
the Center
Fig.
top dead center, which is the amount of spark ad-
vance
distributor automatic advance begins to take hold.
Remove upper half of distributor body by disengaging
snap spr ings.
The
two notches
lf
distributor from the generator, and re-engage the
Marked -Vane
Punch Mark
17.
This will leave the No.1 piston, 12° before
at
low speeds (below
distributor rotor
in the distributor housing.
the rotor is not in this position, withdraw entire
on the flywheel is in line with
on the flywheel shroud.
should line up with center of the
illustrated in
'Timing
300 R.P.M.)
Marks'
Fig. 20,
paragraph,
See
before the
See Fig. 18.
1
Fig. 19
he bottom of the distributor in a new posi-'
will be located properly. Be sure that
ce
lever locks
the
distributor clamp,
ce is not used with these engines.
crew,
Fig.
is tight; as a manual
18, which is,
15
MI·462·2
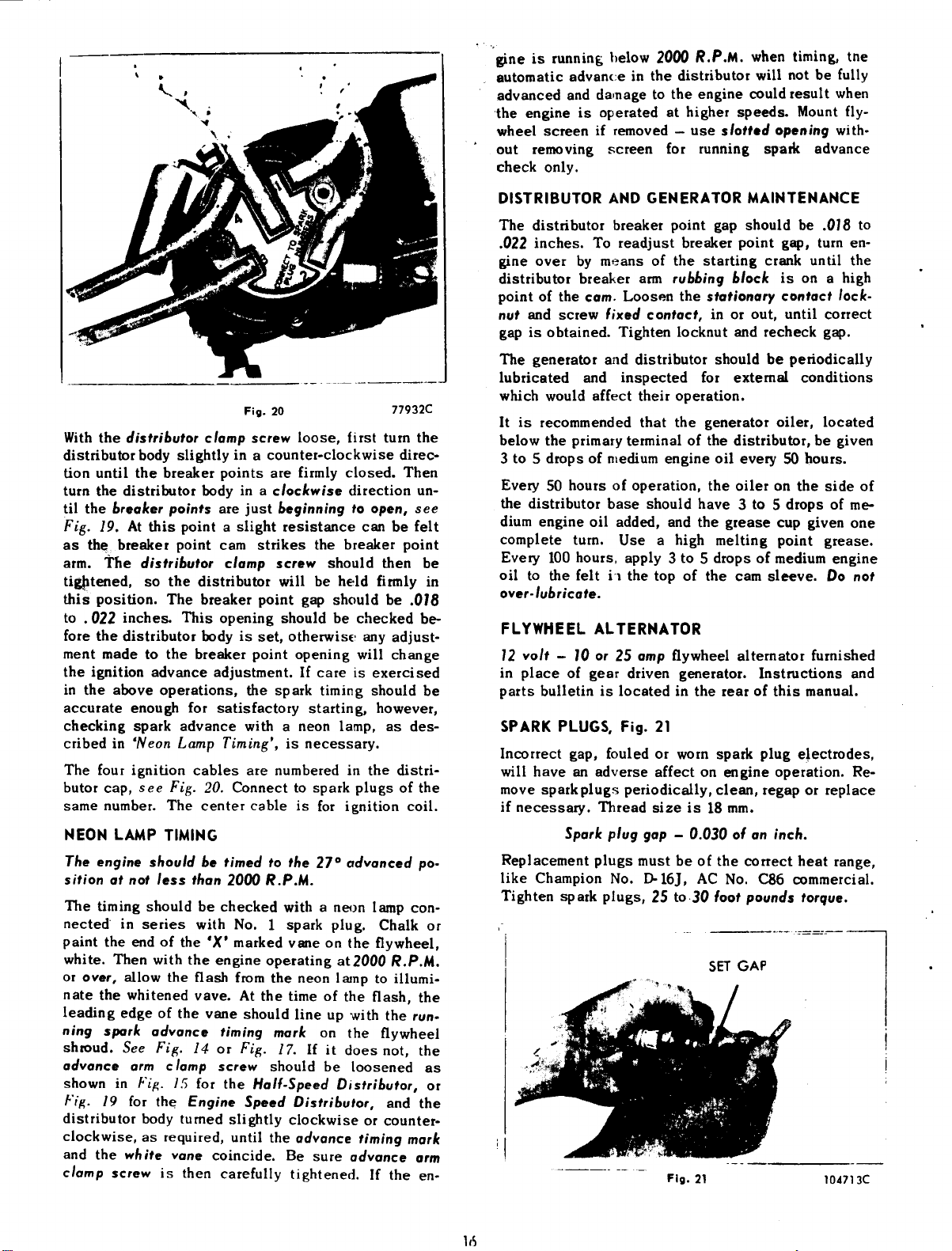
•
",
",
.
~
"""
\.
Fig. 20
Withthe distributor
distributor body slightly in a counter-clockwise direc-
tion until the breaker points are firmly closed. Then
turn the distributor body in a cloclewise direction un-
til the brealeer
Fig.
19. At this point a slight resistance can be felt
as the breaker point cam strikes the breaker point
arm. the
tiglttened, so the distributor will be held firmly in
this position. The breaker point gap should be
to
.022
fore the distributor body is set, otherwise any adjust-
ment made to the breaker point opening will change
the ignition advance adjustment.Ifcare is exercised
in the above operations, the spark timing should be
accurate enough for satisfactory starting, however,
checking spark advance with a neon lamp, as des-
cribed in
The four ignition cables are numbered in the distri-
butor cap,
same number. The center cable is for ignition coil.
distributor
inches. This opening should be checked be-
'Neon Lamp Timing',
see Fig. 20.
points
clamp
screw loose, first turn the
are just beginning to open,
clamp screw should then be
Connect to spark plugs of the
.
,
is necessary.
77932C
see
.018
gine is running helow
automatic advance in the distributor will not be fully
advanced and damage to the engine could result when
the engine is operated at higher speeds. Mount fly-
wheel screen if removed - use
out removing screen for running spark advance
check only.
DISTRIBUTOR AND GENERATOR MAINTENANCE
The distributor breaker point gap should be
.022
inches. To readjust breaker point gap, turn en-
gine over by means of the starting crank until the
distributor breaker arm
point of the cam. Loosen the stationary contact
nut and screw lixed contact, in or out, until correct
gap is obtained. Tighten locknut and recheck gap.
The generator and distributor should be periodically
lubricated and inspected for external conditions
which would affect their operation.
It
is recommended that the generator oiler, located
below the primaryterminal of the distributor, be given
3 to 5 drops of medium engine oil every 50 hours.
Every 50 hours of operation, the oiler on the side of
the distributor base should have 3 to 5 drops of me-
dium engine oil added, and the grease cup given one
complete turn. Use a high melting point grease.
Every 100hours. apply 3 to 5 drops of mediumengine
oil to the feltitthe top of the cam sleeve.
over-lubricate.
FLYWHEEL ALTERNATOR
12 volt -
in place of gear driven generator. Instructions and
parts bulletin is located in the rear of this manual.
SPARK PLUGS, Fig. 21
Incorrect gap, fouled or worn spark plug electrodes,
will have an adverse affect on engine operation. Re-
move spark plugs periodically, clean, regap or replace
if necessary. Thread size is 18 mm.
10
or 25 amp flywheel alternator furnished
2000 R.P.M.
slotted
rubbing blocle
when timing, the
opening with-
.018
is on a high
lock-
Do
not
to
NEON LAMP TIMING
The
engine
sition
The timing should be checked with a neon lamp con-
nected" in series with No. 1 spark plug. Chalk or
paint the end of the
white. Then with the engine operating at
or over, allow the flash from the neon lamp to illumi-
nate the whitened vave. At the time of the flash, the
leading edge of the vane should line up with the run-
ning
shroud.
advance arm c
shown in
Fig. 19
distributor body turned slightly clockwise or counter-
clockwise, as required, until the advance
and the
clamp
should
at not
sparle advance
See Fig.
Fig.
for the
white vane
screw is then carefully tightened. If the en-
be
timed
to
the
less than 2000 R.P.M.
'X'
marked vane on the flywheel,
timing
14 or
lamp
screw should be loosened as
15 for the
Engine
coincide. Be sure
marie on the flywheel
Fig.
17.Ifit does not, the
Half-Speed Distributor,
Speed
27° advanced po·
2000 R.P.M.
Distributor,
timing marie
advance
and the
arm
or
Sparle plug gop - 0.030
Replacement plugs must be of the correct heat range,
like Champion No. 0-16J, AC No. C86 commercial.
Tighten spark plugs, 25 to 30
Fig. 21
01
on
inch.
loot pounds
--"--"===~l
SET GAP
torque.
104713C
I
I
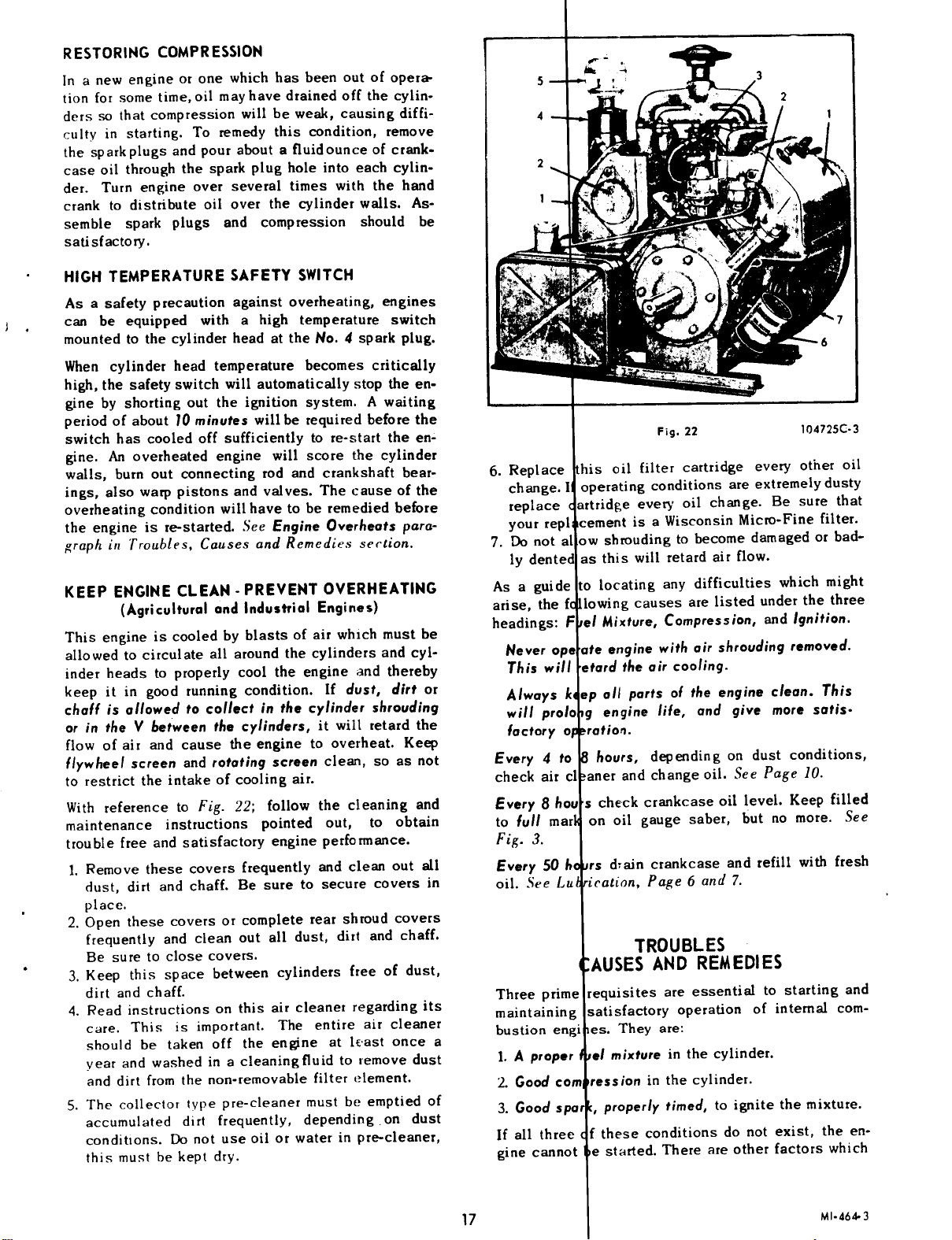
RESTORING COMPRESSION
In a new engine or one which has been out of opera-
tion for some time, oil may have drained off the cylin-
ders so that compression will be weak, causing diffi-
eu
lty
in starting. To remedy this condition, remove
the sp ark plugs and pour about a fluid ounce of crank-
case oil through the spark plug hole into each cylin-
der. Turn engine over several times with the hand
crank to distribute oil over the cylinder walls. As-
semble spark plugs and compression should be
satisfactory.
HIGH TEMPERATURE SAFETY SWITCH
As a safety precaution against overheating, engines
can be equipped with a high temperature switch
mounted to the cylinder head at the
When cylinder head temperature becomes critically
high, the safety switch will automatically stop the en-
gine by shorting out the ignition system. A waiting
period of about 10 minutes will be required before the
switch has cooled off sufficiently to re-start the en-
gine.
An
overheated engine will score the cylinder
walls, burn out connecting rod and crankshaft bear-
ings, also warp pistons and valves. The cause of the
overheating condition will have to be remedied before
the engine is re-started.
f!,raph
in Troubles, Causes and Remedies
See Engine
No.4
Overheats
spark plug.
para-
section:
KEEP ENGINE CLEAN - PREVENT OVERHEATING
(Agricultural and Industrial Engines)
This engine is cooled by blasts of air which must be
allowed to circulate all around the cylinders and cyl-
inder heads to properly cool the engine and thereby
keep it in good running condition.
chaUisallowee/
or
in the
flow of air and cause the engine to overheat. Keep
flywheel
to restrict the intake of cooling air.
With reference to
maintenance instructions pointed out, to obtain
trouble free and satisfactory engine performance.
1.
Remove these covers frequently and clean out all
dust, dirt and chaff. Be sure to secure covers in
place.
2. Open these covers or complete rear shroud covers
frequently and clean out all dust, dirt and chaff.
Be su re to close covers.
3. Keep this space between cylinders free of dust,
dirt and chaff.
4. Read instructions on this air cleaner regarding its
care. This is important. The entire air cleaner
year and washed in a cleaning fluid to remove dust
5. The collector type pre-cleaner must be emptied of
accumulated dirt frequently, depending. on dust
conditions. 00 not use oil or water in pre-cleaner,
this must be kept dry.
V between
screen and
should be taken off the engine at
and dirt from the non-removable filter element.
to
collect
the cyline/ers,
rotating
Fig.
in
screen clean, so as not
22; follow the cleaning and
If
dust, e/irt
the
cylinder
it will retard the
shroue/ing
le-ast
once a
Fig. 22
6. Replace
change. I
replace
your repl
7.
Do
not
ly dent
or
is oil filter cartridge every other oil
operating conditions are extremely dusty
ridge every oil change. Be sure that
is a Wisconsin Micro-Fine filter.
w shrouding to become damaged or bad-
as this will retard air flow.
locating any difficulties which might
lowing causes are listed under the three
I
Mixture, Compression, and
te
engine with air shroue/ing
the
air
cooling.
hours,
s check crankcase oil level. Keep filled
on oil gauge saber, but no more.
rs drain crankcase and refill with fresh
depending on dust conditions,
er and change oil.
See Page 10.
l04725C·3
Ignition.
removed.
clean. This
more satis·
See
'cation, Page 6 and 7.
TROUBLES
AUSES AND REMEDIES
Three prime requisites are essential to starting and
.sfactory operation of internal com-
es. They are:
sion
in the cylinder.
properly timed,
If all three f these conditions do not exist, the en-
started. There are other factors which
to ignite the mixture.
17
MI·464-3
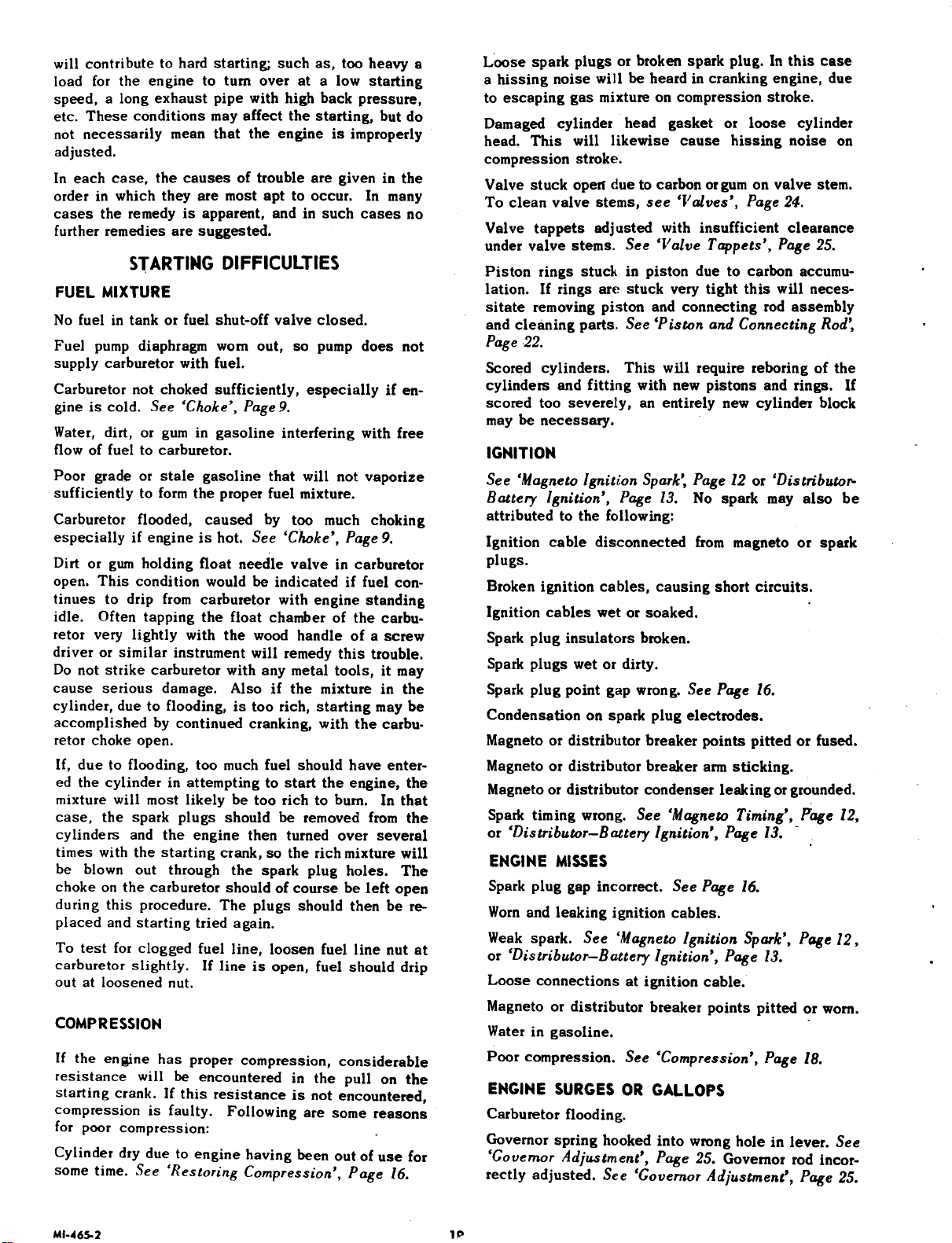
will contribute to hard starting; such as, too heavy a
load for the engine to tum over at a low starting
speed, a long exhaust pipe with high back pressure,
etc. These conditions may affect the starting, but do
not necessarily mean that the engine is improperly
adjusted.
In each case, the causes of trouble are given in the
order in which they are most apt to occur. In many
cases the remedy is apparent, and in such cases no
further remedies are suggested.
STARTING DIFFICULTIES
FUEL MIXTURE
No fuel in tank or fuel shut-off valve closed.
Fuel pump diaphragm worn out, so pump does not
supply carburetor with fuel.
Carburetor not choked sufficiently, especially if en-
gine is cold.
Water, dirt, or gumin gasoline interfering with free
flow of fuel to carburetor.
Poor grade or stale gasoline that will not vaporize
sufficiently to formthe proper fuel mixture.
Carburetor flooded, caused by too much choking
especially if engine is hot.
Dirt or gumholding float needle valve in carburetor
open. This condition wouldbeindicated if fuel con-
tinues to drip from carburetor with engine standing
idle. Often tapping the float chamber of the carbu-
retor very lightly with the wood handle of a screw
driver or similar instrument will remedy this trouble.
Do not strike carburetor with any metal tools, it may
cause serious damage. Alsoifthe mixture in the
cylinder, due to flooding, is too rich, starting may be
accomplished by continued cranking, with the
retor choke open.
If,
due to flooding, too much fuel should have enter-
ed the cylinder in attempting to start the engine, the
mixture will most likely be too rich to bum. In that
case, the spark plugs should
cylinders and the engine then turned over several
times with the starting crank, so the rich mixture will
be blown out through the spark plug holes. The
choke on the carburetor should of course be left open
during this procedure. The plugs should then be re-
placed and starting tried again.
To test for clogged fuel line, loosen fuel line nut at
carburetor slightly.
out at loosened nut.
COMPRESSION
If
the engine has proper compression, considerable
resistance will be encountered in the pull on the
starting crank.Ifthis resistance is not encountered,
compression is faulty. Following are some reasons
for poor compression:
Cylinder dry due to engine having been out of use for
some time.
See 'Choke', Page 9.
See 'Choke', Page 9.
carbu-
be
removed from the
If
line is open, fuel should drip
See 'Restoring Compression', Page 16.
Loose spark plugs or broken spark plug. In this case
a hissing noise willbeheardincranking engine, due
to escaping gas mixture on compression stroke.
Damaged cylinder head gasket or loose cylinder
head. This will likewise cause hissing noise on
compression stroke.
Valve stuck open due to carbon orgumon valve stem.
To clean valve stems,
see 'Valves', Page 24.
Valve tappets adjusted with insufficient clearance
under valve stems.
See 'Valve Tappets', Page 25.
Piston rings stuck in piston due to carbon accumu-
lation.
If
rings are stuck very tight this will neces-
sitate removing piston and connecting rod assembly
and cleaning parts.
See 'Piston and Connecting Rod',
Page ·22.
Scored cylinders. This will require reboring of the
cylinders and fitting with new pistons and rings.
scored too severely, an entirely new cylinder block
maybenecessary.
IGNITION
See 'Magneto Ignition Spark', Page 12or'Distributor-
Battery Ignition', Page 13.
attributed to the
following:
No spark may also be
Ignition cable disconnected from magneto or spark
plugs.
Broken ignition cables, causing short circuits.
Ignition cables wet or soaked.
Sparkplug insulators broken.
Sparkplugs wet or dirty.
Spark plug point gap wrong.
See Page 16.
Condensation on spark plug electrodes.
Magnetoor distributor breaker points pitted or fused.
Magnetoor distributor breaker arm sticking.
Magnetoor distributor condenser leaking orgrounded.
Spark timing wrong.
or
'Distributor-Battery Ignition', Page 13. -
ENGINE MISSES
Spark plug gap incorrect.
See 'Magneto Timing', Page 12,
See Page 16.
Wornand leaking ignition cables.
Weakspark.
or
'Distributor-Battery Ignition', Page 13.
See 'Magneto Ignition Spark', Page
12,
Loose connections at ignition cable.
Magnetoor distributor breaker points pitted or worn.
Waterin gasoline.
Poor compression.
ENGINE SURGES OR GALLOPS
See 'Compression', Page 18.
Carburetor flooding.
Governorspring hooked into wronghole in lever.
'Governor Adjustment', Page
rectly adjusted.
See 'Governor Adjustment', Page 25.
25. Governor rod incor-
See
If
lP
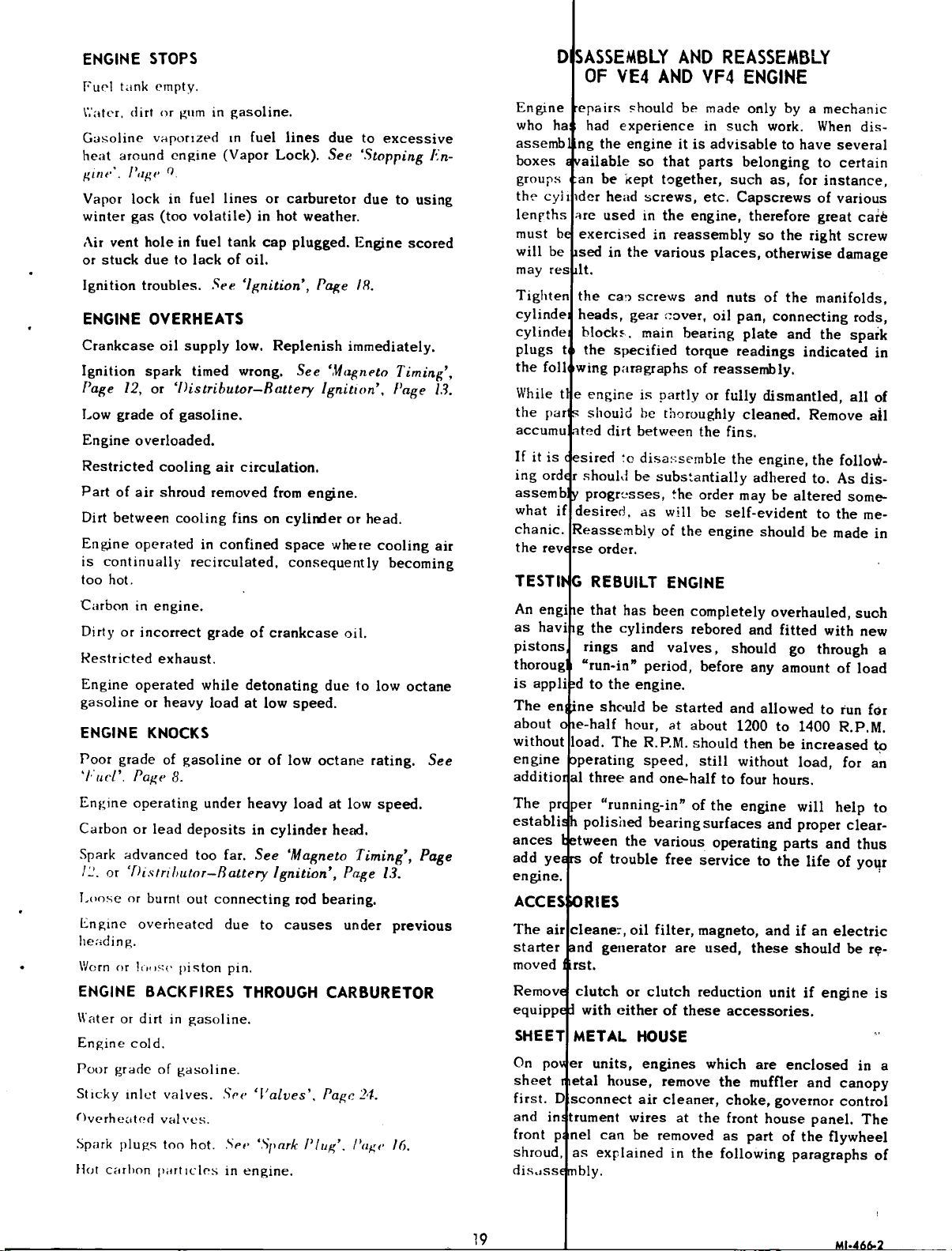
ENGINE STOPS
Fur-l tank empty.
r,'akr. dirt or
Gasol
ine
heat around engine (Vapor Lock).
/!,1Tlf'·.
"'I/!,
gllm
in gasoline.
vapor
i
zed In fuel lines due to excessive
See
I'
(J_
'Stopping
Vapor lock in fuel lines or carburetor due to using
winter gas (too volatile) in hot weather.
Air vent hole in fuel tank cap plugged. Engine scored
or stuck due to lack of oil.
Ignition troubles.
ENGINE OVERHEATS
See 'Ignition",
PG(!.e
/R.
Crankcase oil supply low. Replenish immediately.
Ignition spark timed wrong.
Page
12,
or
'Distributor-Bouery
See
'Mllgnt>to Timinr,',
lgniuon", Page 13.
Low grade of gasoline.
Engine overloaded.
Restricted cooling air circulation.
Part of air shroud removed fromengine.
Dirt between cooling fins on cylird er or head.
Engine operated in confined space where cooling air
is continually recirculated. consequently becoming
too hot.
Carbon in engine.
Dirty or incorrect grade of crankcase
oil.
Restricted exhaust.
Engine operated while detonating due to low octane
gasoline or heavy load at low speed.
ENGINE KNOCKS
Poor grade of gasoline or of low octane rating.
'Fuel",
PaKe
8.
See
Engine operating under heavy load at low speed.
Carbon or lead deposits in cylinder head.
Spark advanced too far.
I:!.or'{)isfrihufor-Rattt>ry Ignition',
See 'Magneto Timing', Page
Page
13.
Loose or burnt out connecting rod bearing.
Engine overheated due to causes under previous
heading.
Wornor
ENGINE BACKFIRES THROUGH CARBURETOR
l""s('
piston pin.
Wateror dirt in gasoline.
Engine cold.
Poor grade of gasol ine.
StickyInlet valves .
Ovcrhcatr-d val ve s.
Spark plugs too hot.
Hot car
lion
particlr-s in engine.
.'ire 'Volves",
"';1'1' 'Spark "/uf!,'. I
PaKe 2,1.
'(I!!,
I'
/6.
En-
D SASSEMBLY AND REASSEMBLY
OF VE4 AND VF4 ENGINE
Engine epairs
who ha had experience in such work. When dis-
assemb ng the engine it is advisable to have several
boxes ailable so that parts belonging to certain
groups anbekept together, such as, for instance,
the cyliider
lengths are
must b exercised in reassembly so the right screw
will be sed in the various places, otherwise damage
It.
Tighten
cylinde
cylinde
the
heads, gear Gover. oil pan, connecting rods,
bloch. main bearing plate and the spark
plugs t
the foIl
wing paragraphs of reassembly.
While t e engine is partly or fully dismantled, all of
the par should
accumu
H
ated
it is esired'0disas.sernble
ing ord r should be substantially adhered to. As dis-
assemb
whatifdesired. as wi11be self-evident to the me-
chanic. Reassembly of the engine should be made in
the rev rse order.
An engi
as havi
e that has been completely overhauled, suoh
g the cylinders rebored and fitted with new
pistons
thoroug
is appli
"run-in" period, before any amount of load
d to the engine.
The en ine should be started and allowed to run for
about e-half hour, at about
without load. The
perating speed. still without load, for an
al three and one-half to four hours.
The pr
per "running-in" of the engine will help to
establi
ances
tween the various operating parts and thus
add ye
The air cleaner, oil filter, magneto, and if an electric
starter nd generator are used, these should be rli!-
moved rst.
clutch or clutch reduction unit if engine is
with either of these accessories.
On po er units, engines which are enclosed in a
sheet etal house, remove the muffler and canopy
first. D sconnect air cleaner, choke, governor control
and in trument wires at the front house panel. The
front p nel can be removed as part of the flywheel
shroud, as explained in the following paragraphs of
dis••ss bly.
should
be made only by a mechanic
head screws, etc. Capscrews of various
used in the engine, therefore great care
can
screws and nuts of the manifolds.
the specified torque readings indicated in
he thoroughly
cleaned. Remove ail
dirt between the fins.
progresses, the
the engine, the
order may be altered some-
follow-
rings and valves, should go through a
1200to1400 R.P.M.
R.P.M.
should then be increased
polished bearing surfaces and proper clear-
of trouble free service to the life of yoqr
RIES
to
19
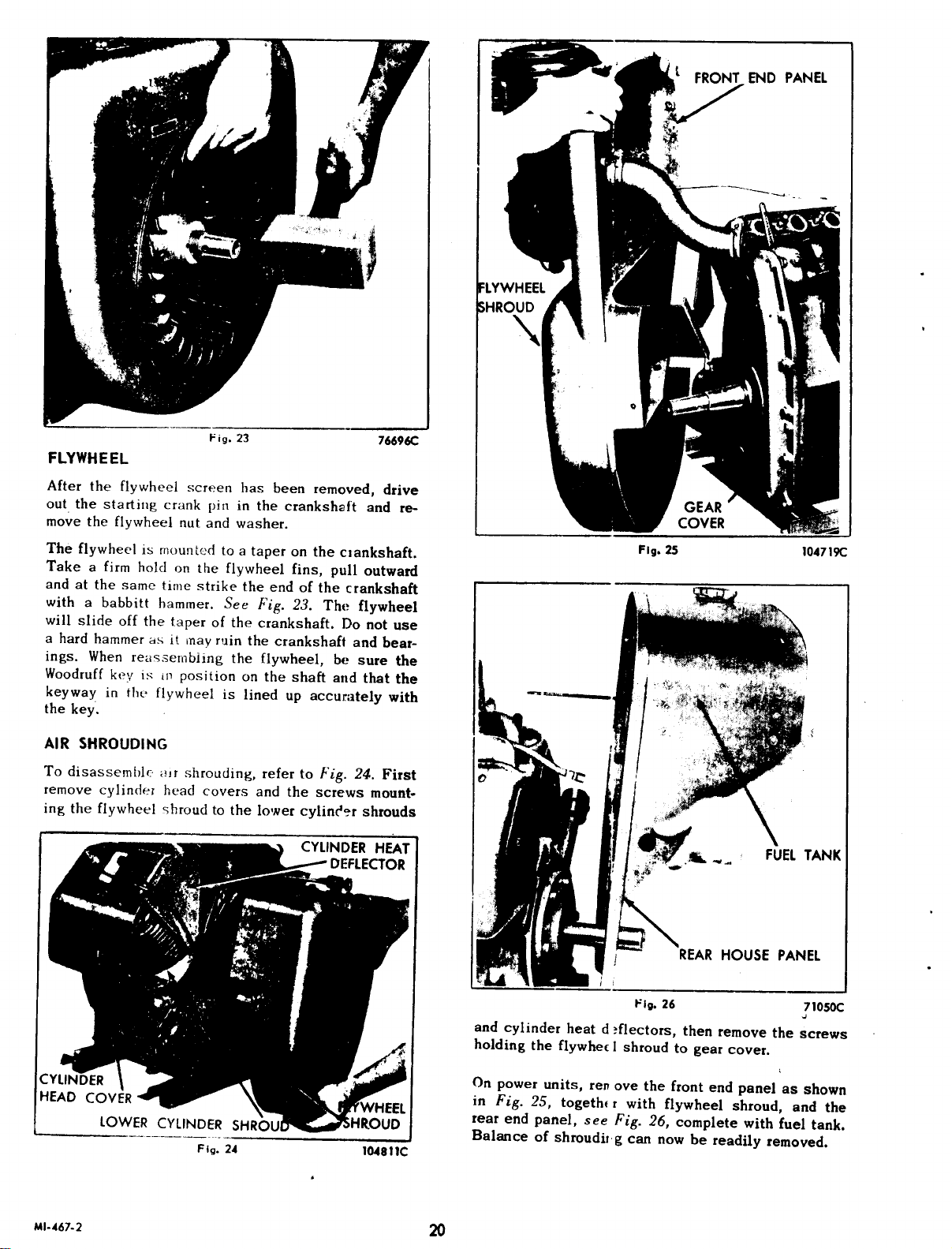
76696C
FLYWHEEL
After the flywheel screen has been removed, drive
out the starting crank pin in the crankshaft and re-
move the flywheel nut and washer.
The flywheel is mounted to a taper on the crankshaft.
Take a firm hold on the flywheel fins, pull outward
and at the same time strike the end of the crankshaft
with a babbitt hammer. See
will slide off the taper of the crankshaft. Do not use
a hard hammer asitmay ruin the crankshaft and bear-
ings. When reassembling the flywheel, be sure the
Woodruff key isinposition on the shaft and that the
keyway in the flywheel is lined up accurately with
the key.
Fig.
23. The flywheel
AIR SHROUDING
To disassemble .ur shrouding, refer to
remove cylinder head covers and the screws mount-
ing the flywheel shroud to the lower cylinder shrouds
Fig.
24. First
Flg.2S
I-'Ig. 26
and cylinder heat d
holding the flywhec I shroud to gear cover.
eflectors,
then remove the screws
104719C
710SOC
'"
MI-467-2
10-4811C
On power units, ren ove the front end panel as shown
in
Fig.
25,
togethe
rear end panel, see
Balance of shroudir g can now be readily removed.
r with flywheel shroud, and the
Fig.
26, complete with fuel tank.
20
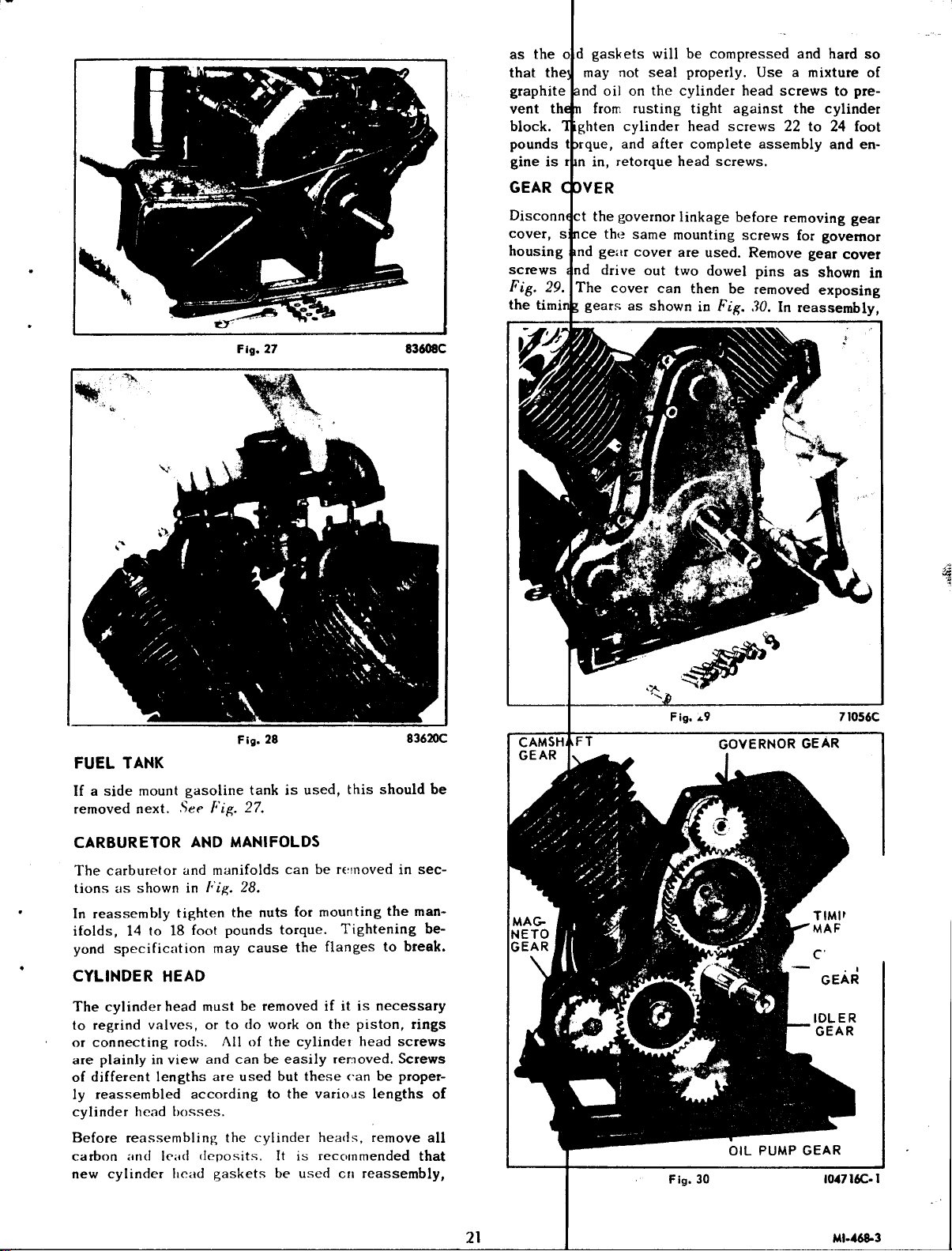
d gaskets will be compressed and hard so
may not seal properly. Use a mixture of
nd oil on the cylinder head screws to pre-
from rusting tight against the cylinder
ghten cylinder head screws 22 to 24 foot
que, and after complete assembly and en-
in, retorque head screws.
the governor linkage before removing gear
the same mounting screws for governor
nd gear cover are used. Remove gear cover
d drive out two dowel pins as shown in
The cover can then be removed exposing
gears as shown in
Fig. 30.
In reassembly,
Fig. 27
Fig.
28
FUEL TANK
If
a side mount gasoline tank is used, this should be
removed next.
Set' Fig. 27.
83608C
710S6C
83620C
CARBURETOR AND MANIFOLDS
The carburetor and manifolds can be removed in sec-
tions as shown in
Fig. 28.
In reassembly tighten the nuts for mounting the man-
ifolds, 14 to 18 foot pounds torque. Tightening be-
yond specification may cause the flanges to break.
CYLINDER HEAD
The cylinder head must be removed ifitis necessary
to regrind valves, or to do work on the piston, rings
or connecting rods. I\ll of the cylinder head screws
are plainly in view and can be easily
of different lengths are used but these can be proper-
ly reassembled according to the various lengths of
cylinder head bosses.
Before reassembling the cylinder heads. remove all
carbon and
I("HI
deposits.
It
new cylinder head gaskets be used
removed,
Screws
is recommended that
Gil
reassembly,
21
Fig. 30
. I
GEAR
104716C.l
MI·468-3
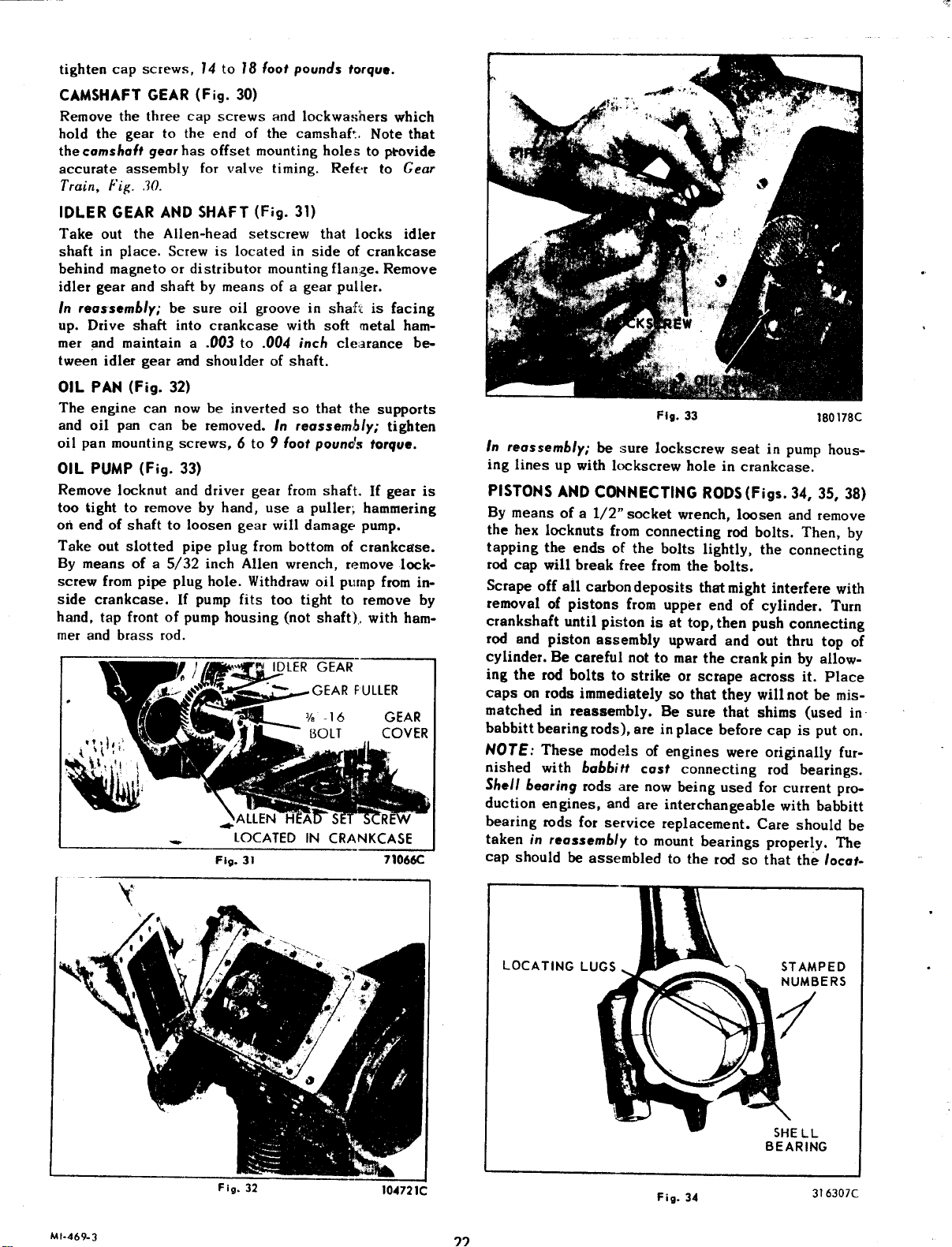
tighten cap screws, 14 to 18
CAMSHAFT GEAR (Fig. 30)
Remove the three cap screws and lockwashers which
hold the gear to the end of the camshaft. Note that
the
camshaft gear
accurate assembly for valve timing. Reft'r to
Train, Fig . .10.
IDLER GEAR AND SHAFT (Fig. 31)
Take out the Allen-head setscrew that locks idler
shaft in place. Screw is located in side of crankcase
behind magneto or distributor mountingflange. Remove
idler gear and shaft by means of a gear puller.
In reassembly;
up. Drive shaft into crankcase with soft metal ham-
mer and maintain a
tween idler gear and shoulder of shaft.
OIL PAN (Fig. 32)
The engine can now be inverted so that the supports
and oil pan can be removed.
oil pan mounting screws, 6 to 9
OIL PUMP (Fig. 33)
Remove locknut and driver gear from shaft.Ifgear is
too tight to remove by hand, use a puller; hammering
on end of shaft to loosen gear will damag€'pump.
Take out slotted pipe plug from bottom of
By means of a 5/32 inch Allen wrench, removelock-
screw from pipe plug hole. Withdrawoil pump from in-
side crankcase.
hand, tap front of pump housing (not shaft). with ham-
mer and brass rod.
has offset mountingholes to provide
be sure oil groove in shaft is facing
.003to.004
If
pump fits too tight to remove by
foot pouncls torque.
inch
clearance be-
In reassem,bly;
foot pounchl torque.
crankcase,
Gear
tighten
GEAR
COVER
Fig. 33
In reassembly; be
ing lines up with lockscrew hole in crankcase.
PISTONS AND CONNECTING RODS(Figs. 34, 35, 38)
By means of a 1/2" socket wrench, loosen and remove
the hex locknuts from connecting rod bolts. Then, by
tapping the ends of the bolts lightly. the connecting
rod cap
Scrape off all carbon deposits
removal of pistons from upper end of cylinder. Turn
crankshaft until piston is at top, then push connecting
rod and piston assembly upward and out thru top of
cylinder. Be careful not to mar the crank pin by allow-
ing the rod bolts to strike or scrape across it. Place
caps on rods immediately so that they will not be mis-
matched in reassembly. Be sure that shims (used in'
babbitt bearing rods), are inplace before cap is put on.
NOTE:
nished with
Sh.1I bearing
duction engines, and are interchangeable with babbitt
bearing rods for service replacement. Care should be
taken in
cap shouldbeassembled to the rod so that the
will
These models of engines were originally fur-
reassembly
sure lockscrew seat in pump hous-
break free fromthe bolts.
that
might interfere with
babbitt
rods are now being used for current pro-
cast connecting rod bearings.
to mount bearings properly. The
lB017BC
locat-
MI.469-3
Fig. 34
STAMPED
NUMBERS
/
316307C
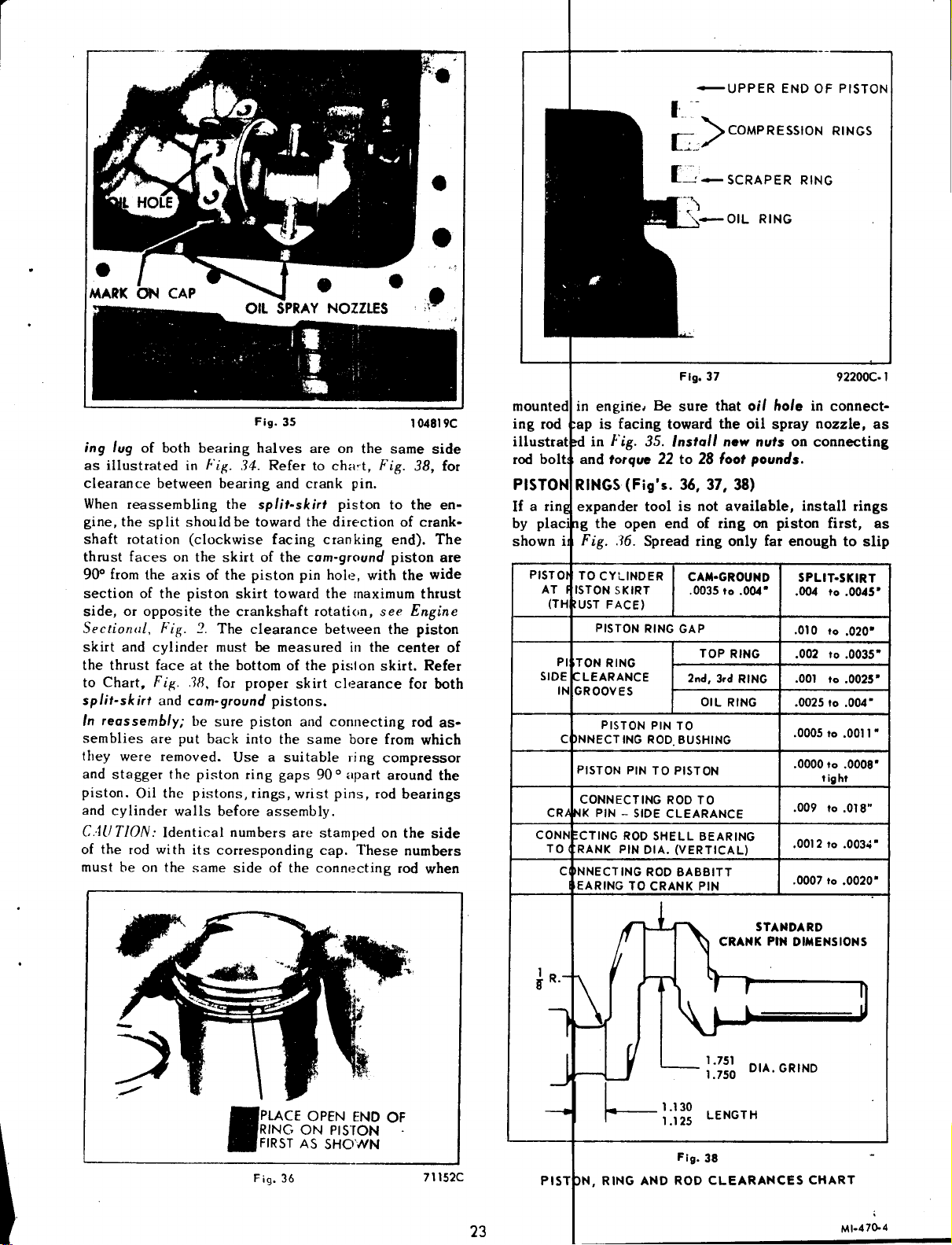
-UPPER ENDOF PISTON
I· --
E..:)COMPRESSION RINGS
[~-SCRAPER RING
Fig.
37
9220OC·l
Fig.
ing lug
of both bearing halves are on the same side
as illustrated in
Fig.
34. Refer to chart,
35
Fig.
104819C
38, for
clearance between bearing and crank pin.
When reassembling the
split-skirt
piston to the en-
gine, the split should be toward the direction of crank-
shaft rotation (clockwise facing cranking end). The
thrust faces on the skirt of the
com-ground
piston are
900from the axis of the piston pin hole, with the wide
section of the piston skirt toward the maximum thrust
side, or opposite the crankshaft rotation,
Sectional, Fig.
skirt and cylinder must
2. The clearance between the piston
be
measured in the center of
see Engine
the thrust face at the bottom of the piston skirt. Refer
to Chart,
split-skirt
In reassembly;
Fig ..
1ll,
for proper skirt clearance for both
and
cam·ground
pistons.
be sure piston and connecting rod as-
semblies are put back into the same bore from which
they were removed. Use a suitable ring compressor
and stagger the piston ring gaps 900apart around the
piston. Oil the pistons, rings, wrist pins, rod bearings
and cylinder walls before assembly.
CAU T/oN:
Identical numbers are stamped on the side
of the rod with its corresponding cap. These numbers
must be on the same side of the connecting rod when
mvu.".....,
u"'"'.... 'LFu
~1",,","",,,,
in engine. Be sure that
oil Itole
in connect-
is facing toward the oil spray nozzle, as
in
Fig.
35.
Install
new nuts on connecting
and torque 22 to 28 foot pounds.
RINGS (Fig's. 36, 37, 38)
expander tool is not available, install rings
the open end of ring on piston first, as
Fig.
J6. Spread ring only far enough to slip
CAM-GROUND SPLIT.SKIRT
.0035to.004· .004to.0045·
PISTON RING GAP .010to.020·
2nd, 3,d RING .001to.0025·
OIL R
PISTON PIN TO
NECT ING ROD.BUSHING
.0005to.0011·
.0000to.0008·
t
illht
.009to.018"
.0012to.003';·
.0007to.0020·
PLACE OPEN END OF
RING ON PISTON .
FIRST AS SHOWN
•
F
;g.
36
71152C
23
STANDARD
CRANK PIN DIMENSIONS
DIA. GRIND
,.. __ 1.130
• RING AND ROD CLEARANCES CHART
1.125 LENGTH
Fig.
38
MI·470-4
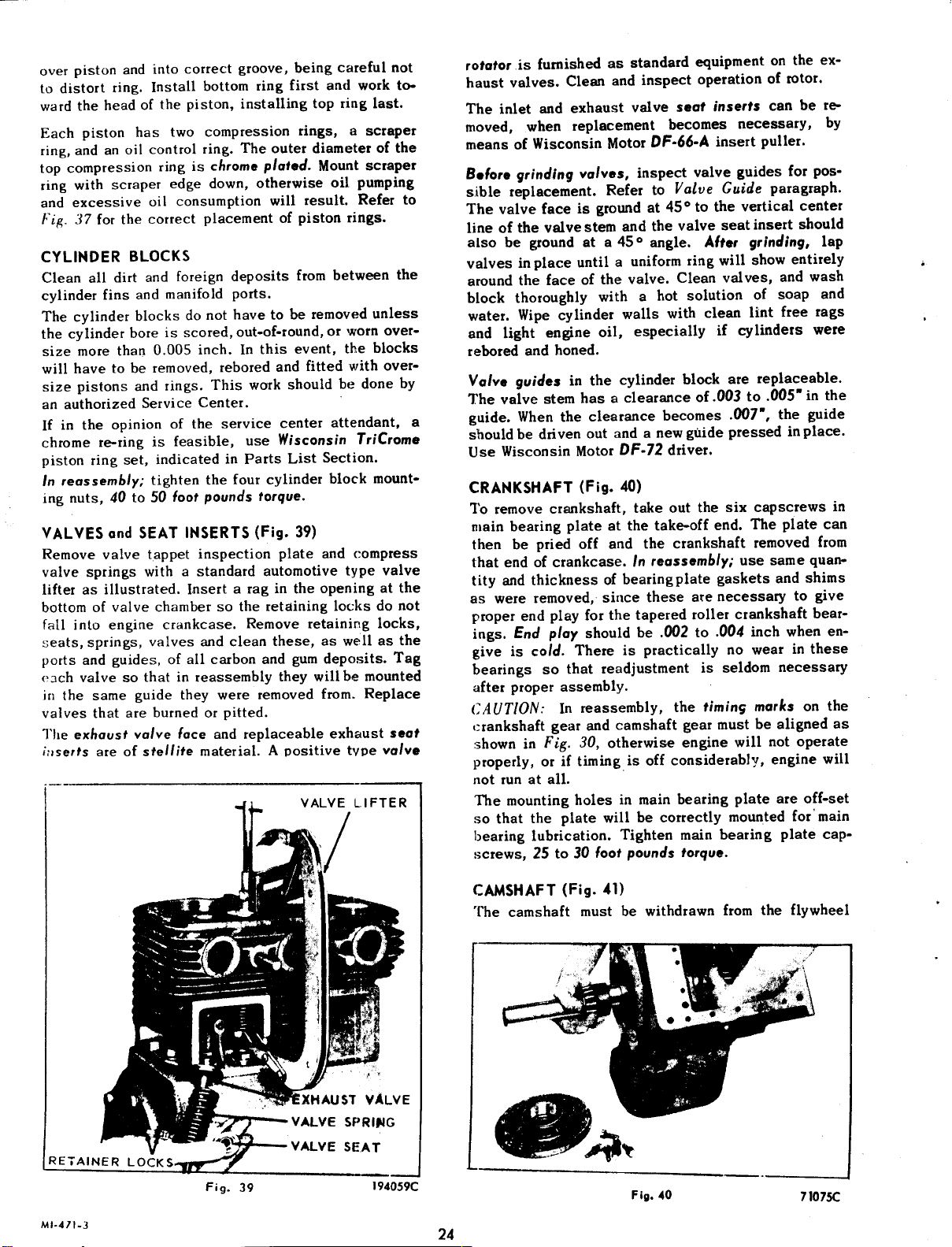
over piston and into correct groove, being careful not
to distort ring. Install bottom ring first and work to-
ward the head of the piston. installing top ring last.
Each piston has two compression rings, a scraper
ring, and an oil control ring. The outer diameter of the
top compression ring is chrome
plated.
Mountscraper
ring with scraper edge down, otherwise oil pumping
and excessive oil consumption will result. Refer to
Fig. 37
for the correct placement of piston rings.
CYLINDER BLOCKS
Clean all dirt and foreign deposits from between the
cylinder fins and manifold ports.
The cylinder blocks do not have to be removed unless
the cylinder bore is scored, out-of-round,or worn over-
size more than 0.005 inch. In this event, the blocks
will have to be removed, rebored and fitted with over-
size pistons and rings. This work should be done by
an authorized Service Center.
If
in the opinion of the service center attendant, a
chrome re-ring is feasible, use Wisconsin TriCrome
piston ring set, indicated in Parts List Section.
In reassembly;
ing nuts,
YALYES
Remove valve tappet inspection plate and compress
valve springs with a standard automotive type valve
lifter as illustrated. Insert a rag in the opening at the
bottom of valve chamber so the retaining locks do not
fall into engine crankcase. Remove retaining locks,
seats, springs, valves and clean these, as well as the
ports and guides. of all carbon and gumdeposits. Tag
oach valve so that in reassembly they willbe mounted
in the same guide they were removed from. Replace
valves that are burned or pitted.
The exhaust
inserts
are of
tighten the four cylinder block mount-
40to50 foot pounds torque.
and
SEAT INSERTS (Fig.
valve
face and replaceable exhaust seat
stellite
material. A positive type
39)
valve
rotator.is furnished as standard equipment on the ex-
haust valves. Clean and inspect operation of rotor.
The inlet and exhaust valve seat inserts can be re-
moved, when replacement becomes necessary, by
means of Wisconsin MotorDF·66·A insert puller.
S.fore
sible replacement. Refer to
grinding
valves, inspect valve guides for pos-
Valve Guide
paragraph.
The valve face is ground at 450to the vertical center
line of the valve stem and the valve seat insert should
also be ground at a
450angle. Alter
grinding,
lap
valves in place until a uniform ring will show entirely
around the face of the valve. Clean valves, and wash
block thoroughly with a hot solution of soap and
water. Wipe cylinder walls with clean lint free rags
and light engine oil, especially if cylinders were
rebored and honed.
Valve
guides in the cylinder block are replaceable.
The valve stem has a clearance of
guide. When the clearance becomes
.003to.OOS·
.007·,
the guide
in the
should be driven out and a new guide pressed in place.
Use Wisconsin MotorDF.72 driver.
CRANKSHAFT (Fig. 40)
To remove crankshaft, take out the six capscrews in
main bearing plate at the take-off end. The plate can
then be pried off and the crankshaft removed from
that end of crankcase.
tity and thickness of bearing plate gaskets and shims
as were removed, since these ate necessary to give
proper end play for the tapered roller crankshaft bear-
ings.
give is
End play
colJ.
should be
There is practically no wear in these
bearings so that readjustment is seldom necessary
after proper assembly.
CAUTION:
In reassembly, the timini maries on the
crankshaft gear and camshaft gear must be aligned as
shown in
Fig. 30,
properly, or if timing is off considerably, engine will
not run at all. .
The mounting holes in main bearing plate are off-set
so that the plate will be correctly mounted for' main
bearing lubrication. Tighten main bearing plate cap-
screws,
2S
to 30
In reassembly;
.002to.004
use same quan-
inch when en-
otherwise engine will not operate
loot pounds
torque.
MI-""-3
Fig. 39
1940S9C
CAMSHAFT (Fig. 41)
The camshaft must be withdrawn from the flywheel
Fig. 40
24
71075C
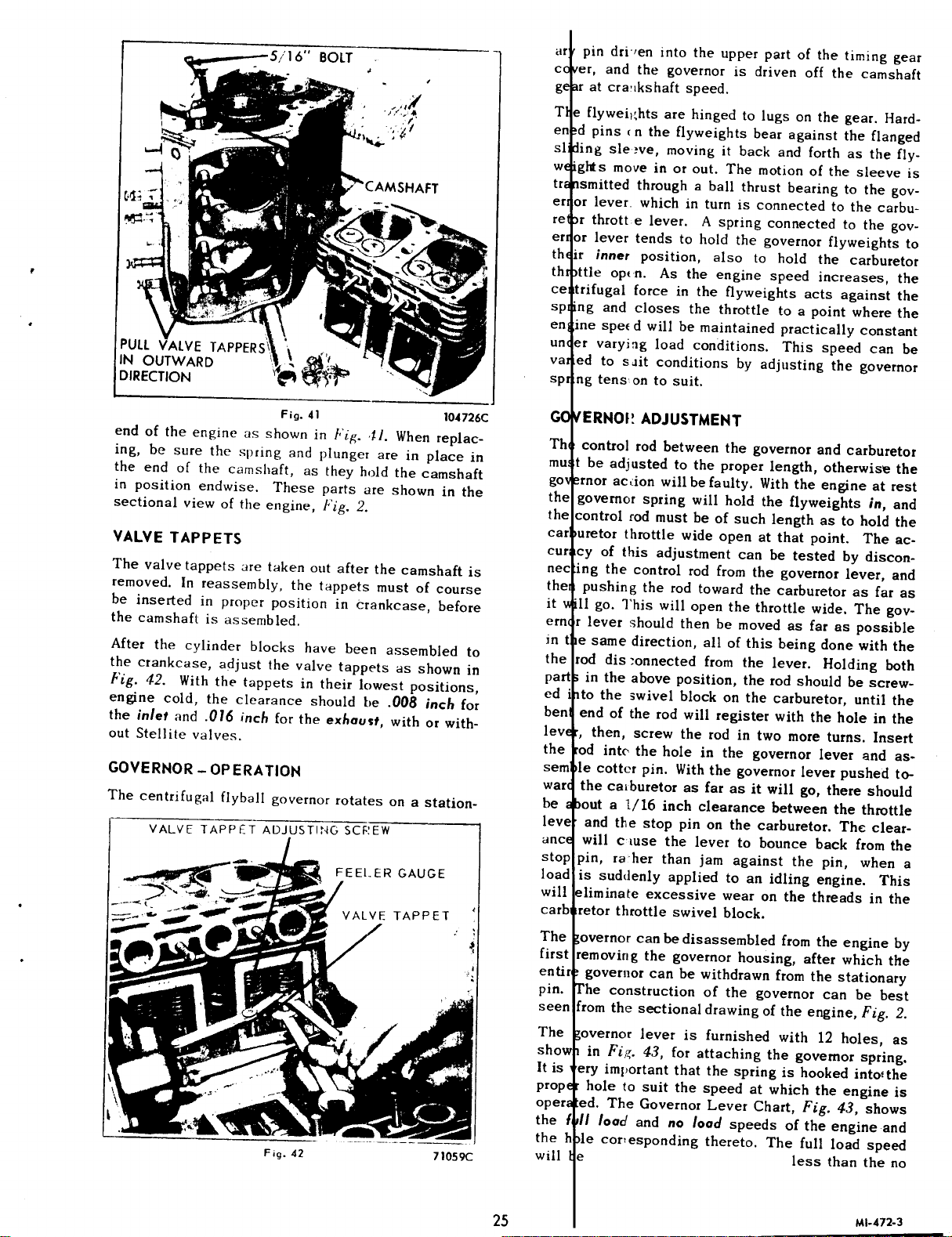
PULL AlVE TAPPERS.
IN OUTWARD
DIRECTION
BOLT
ar pin
c er, and the governor is driven off the camshaft
en d pins ( n the flyweights bear against the flanged
sl ing sle
w 'ghts
tr smitted through a ball thrust bearing to the gov-
er or lever. which in turn is connected to the carbu-
ce trifugal force in the flyweights acts against the
sp0ng and closes the throttle to a point where the
en ine
un er varying load conditions. This speed can be
va ed toSait conditions by adjusting the governor
driven
r at crankshaft speed.
e flyweinhts are hinged to lugs on the gear. Hard-
move
r thrott e lever. A spring connected to the gov-
or lever tends to hold the governor flyweights to
ir
inner
ttle Optn. As the engine speed increases, the
spee
ng tens on to suit.
into the upper part of the timing gear
eve,
movingitback and forth as the fly-
in or out. The motion of the sleeve is
position, also to hold the carburetor
d will be maintained practically constant
Fi9. 41 104726C
end of the engine us shown in
ing, be sure the spring and plunger are in place in
the end of the camshaft, as they hold the camshaft
in position endwise. These parts are shown in the
sectional view of the engine,
VALVE TAPPETS
The valve tappets are taken out after the camshaft is
removed. In reassembly, the tappets must of course
be inserted in proper position in crankcase, before
the camshaft is assembled,
After the cylinder blocks have been assembled to
the crankcase, adjust the valve tappets as shown in
Fig.
42. With the tappets in their lowest positions,
engine cold, the clearance should be
the
inlet
and
.016
inch
out Stellite valves.
GOVERNOR - OP ERATION
The centrifugal flyball governor rotates on a station-
VALVE TAPPET AD
for the exhaust, with or with-
Fig.
Fig. 2.
,t1.
When replac-
.008 inch
for
ERNOJ~ADJUSTMENT
control rod between the governor and carburetor
t be adjusted to the proper length, otherwise the
go rnor accion will be faulty. With the engine at rest
the governor spring will hold the flyweights
the control rod must be of such length as to hold the
car uretor throttle wide open at that point. The ac-
cur cy of this adjustment can be tested by discon-
nee ing the control rod from the governor lever, and
the pushing the rod toward the carburetor as far as
it
OIl
go. This will open the throttle wide. The gov-
ern r lever should then be moved as far as possible
in t e same direction, all of this being done with the
the rod dis ronnected from the lever. Holding both
in the above position, the rod should be screw-
to the swivel block on the carburetor, until the
end of the rod will register with the hole in the
, then, screw the rod in two more turns. Insert
od ink the hole in the governor lever and as-
Ie cotter pin. With the governor lever pushed to-
the carburetor as far as it will go, there should
out a 1/16 inch clearance between the throttle
and the stop pin on the carburetor. ThE: clear-
anc will c ruse the lever to bounce back from the
stop pin, raher than jam against the pin, when a
load is suddenly applied to an idling engine. This
will eliminate excessive wear on the threads in the
carb retor throttle swivel block.
in,
and
Fig.42
71059C
The overnor can be disassembled from the engine by
first removing the governor housing, after which the
entir governor can be withdrawn from the stationary
pin. he construction of the governor can be best
seen from the sectional drawing of the engine,
The overnor lever is furnished with 12 holes, as
show in
It
is ery important that the spring is hooked into! the
oper ed. The Governor Lever Chart,
the
the h Ie
will less than the no
Fig;.
43, for attaching the governor spring.
hole to suit the speed at which the engine is
Fig.
II/load
and no
coresponding
load
speeds of the engine and
thereto. The full load speed
25
Fig. 2.
43, shows
MI-472-3
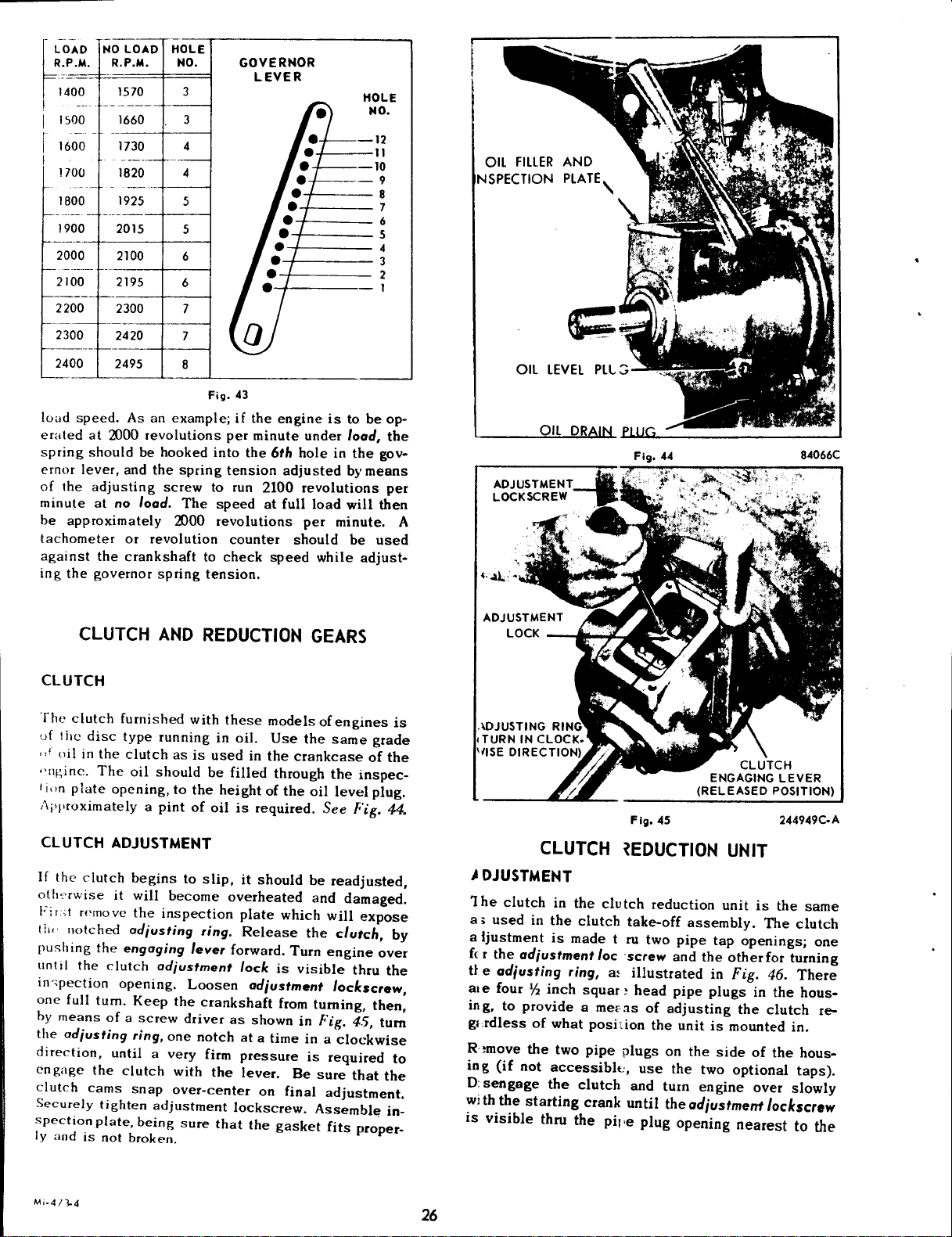
LOAD
;~~~:.
V
!
1500
I
1600
1700
1925
2015
2100
2195
2300
2420
GOVERNOR
LEVER
HOLE
1'10.
-12
II
-10
-9
5
5
6
6
7
7
8
7
6
5
4
3
2
-I
OIL FILLERAND
NSPECTION PLATE,
2495
load speed. As an example; if the engine is to be op-
erated at 2000 revolutions per minute under
spring should be hooked into the
ernor lever, and the spring tension adjusted by means
of the adjusting screw to run 2100 revolutions per
minute at no
be approximately 2000 revolutions per minute. A
tachometer or revolution counter should be used
against the crankshaft to check speed while adjust-
ing the governor spring tension.
8
Fig. 43
6th
hole in the gov-
loael.
The speed at full load will then
loael,
the
CLUTCH AND REDUCTION GEARS
CLUTCH
The clutch furnished with these models of engines is
ofthe disc type running in oil. Use the same grade
"f
oil in the clutch as is used in the crankcase of the
.>nginc. The oil should be filled through the inspec-
t
ion plate opening, to the height of the oil level plug.
Approximately a pint of oil is required.
CLUTCH ADJUSTMENT
If
the clutch begins to slip,itshould be readjusted,
otherwise it will become overheated and damaged.
Fir;t
romove the inspection plate which will expose
til<'
notched
pushing the
until the clutch
in=pection opening. Loosen
one full tum. Keep the crankshaft from turning, then,
by means of a screw driver as shown in
the
acl;usting ling,
direction, until a very firm pressure is required to
engage the clutch with the lever. Be sure that the
clutch cams snap over-center on final adjustment.
Securely tighten adjustment lockscrew. Assemble in-
spection plate, being sure that the gasket fits proper-
ly
and is not broken.
acl;usting ling.
engaging level
Release the
forward. Turn engine over
acl;ustment lock
aeljustment
one notch at a time in a clockwise
See Fig. 44.
clutch,
is visible thru the
locksclew,
Fig.
45, tum
by
CLUTCH
ENGAGING LEVER
(RELEASED POSITION)
Fig. 45
244949C·A
CLUTCH ~EDUCTION UNIT
~DJUSTMENT
1
he clutch in the clutch reduction unit is the same
aiused in the clutch take-off assembly. The clutch
a Ijustment is made t ru two pipe tap openings; one
fc
r the
ael;ustment loc
tl e
ael;usting ring, as
ale four
ing, to provide a mes as of adjusting the clutch re-
gudless of what posi don the unit is mounted in.
R~move the two pipe plugs on the side of the hous-
ing (if not accesaible, use the two optional taps).
0:
with the starting crank until the
is visible thru the pije plug opening nearest to the
Y:z
inch squar ~head pipe plugs in the hous-
sengage the clutch and turn engine over slowly
·screw
and the otherfor turning
illustrated in
acl;ustmerrtloclcscrew
Fig.
46. There
Mi·4!).4
26
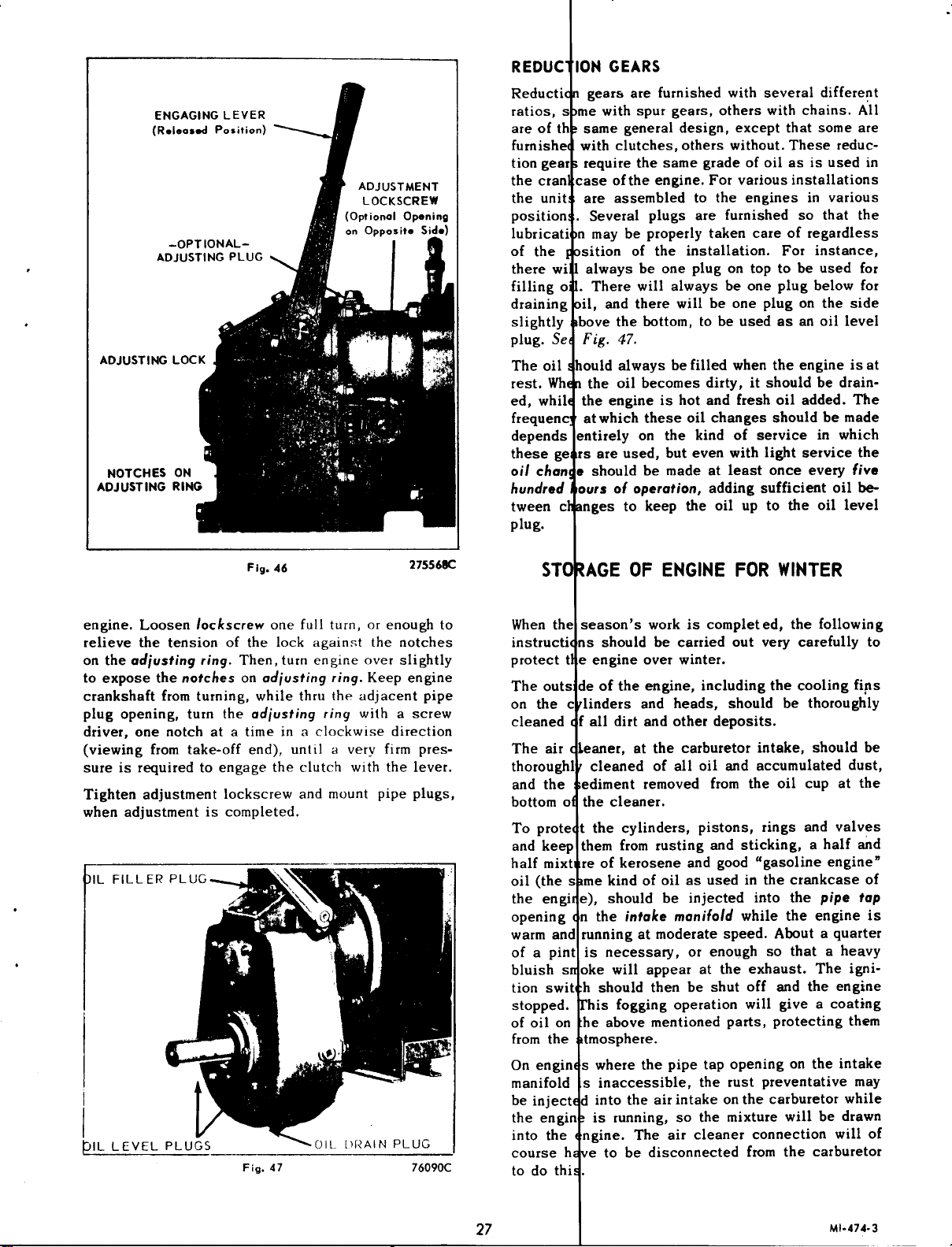
ENGAGING LEVER
(Released Position)
-OPTIONAL-
ADJUSTING PLUG
ADJUSTING LOCK
NOTCHES ON
ADJUSTING RING
ADJUSTMENT
LOCKSCREW
REDUC ION GEARS
Reducti gears are furnished with several different
me with spur gears, others with chains.
same general design, except that some are
with clutches, others without. These reduc-
tion gear require the same grade of oil as is used in
case ofthe engine. For various installations
the unit are assembled to the engines in various
position . Several plugs are furnished so that the
lubricati n may be properly taken care of regardless
of the sition of the installation. For instance,
there wi always be one plug on top tobeused for
filling
0 •
There will always be one plug below for
draining il, and there will be one plug on the side
slightly bove the bottom, to be used as an oil level
plug.
Se Fig. 47.
The oil hould always be filled when the engine is at
rest. Wh the oil becomes dirty, it should be drain-
ed, whil the engine is hot and fresh oil added. The
frequenc at which these oil changes should be made
depends entirely on the kind of service in which
these ge rs are used, but even with light service the
oil chan
hundred
e should be made at least once every five
ours of operation, adding sufficient oil be-
tween c nges to keep the oil up to the oil level
plug.
All
27S568C
engine. Loosen
lockscrew
Fig. 46
one full turn, or enough to
relieve the tension of the lock against the notches
on the
adjusting ring.
to expose the
notches
Then, turn engine over slightly
on
adjusting ring.
Keep engine
crankshaft from turning, while thru the adjacent pipe
plug opening, turn the
adjusting ring
with a screw
driver, one notch at a time in a clockwise direction
(viewing from take-off end), until a very firm pres-
sure is required to engage the clutch with the lever.
Tighten adjustment lockscrew and mount pipe plugs,
when adjustment is completed.
IL FILLER PLUG
I
I
!?IL LEVEL PLUGS
Fig. 47
llf,AIN
PLUG
76090C
Whenthe season's work is completed, the following
instructi ns should be carried out very carefully to
protect t e engine over winter.
The outs de of the engine, including the cooling fins
on the c linders and heads, should be thoroughly
cleaned f all dirt and other deposits.
The air Leaner, at the carburetor intake, should be
thoroughl cleaned of all oil and accumulated dust,
and the ediment removed from the oil cup at the
bottom0the cleaner.
To prote t the cylinders, pistons, rings and valves
and keep them from rusting and sticking, a half and
half mixt re of kerosene and good "gasoline engine"
oil (the s me kind of oil as used in the crankcase of
the engi e), should be injected into the
opening n the
intalce manifold
while the engine is
pipe tap
warm and running at moderate speed. About a quarter
of a pint is necessary, or enough so that a heavy
bluish s oke will appear at the exhaust. The igni-
tion swit h should then be shut off and the engine
stopped. his fogging operation will give a coating
of oil on he above mentioned parts, protecting them
tmosphere.
s where the pipe tap opening on the intake
s inaccessible, the rust preventative may
d into the air intake on the carburetor while
the engin is running, so the mixture will be drawn
ngine. The air cleaner connection will of
e to be disconnected from the carburetor
27
MI.474·3