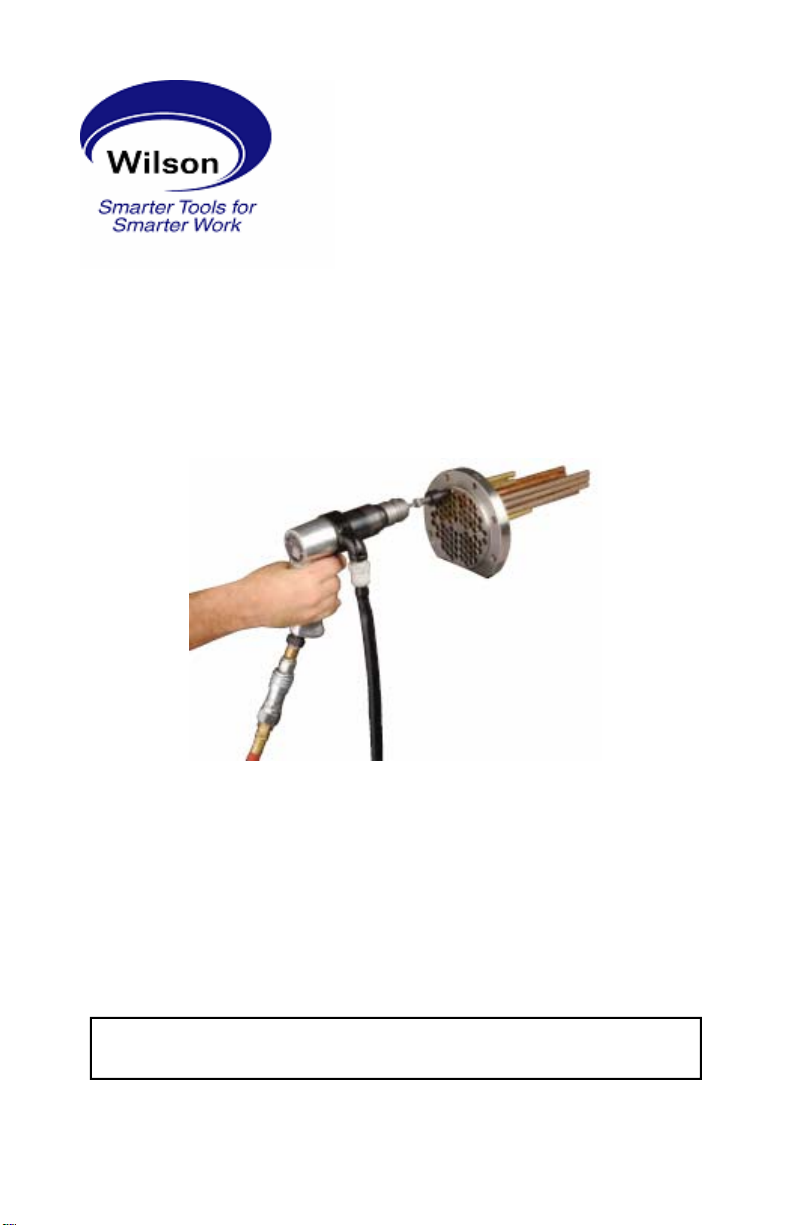
930-450
930-750
930-1000
MODEL 930 TUBE ROLLER
SM-79D
OPERATING INSTRUCTIONS
&
SERVICE MANUAL
Rev: A, 10/1/2007
TO REDUCE THE RISK OF INJURY AND EQUIPMENT DAMAGE
USER MUST READ AND UNDERSTAND OPERATOR’S MANUAL.
Thomas C. Wilson, Inc.
21-11 44th Avenue, Long Island City, New York 11101
Tel: (718)729-3360 Fax: (718)361-2872 http://www.tcwilson.com
E-mail: tcwilson@tcwilson.com
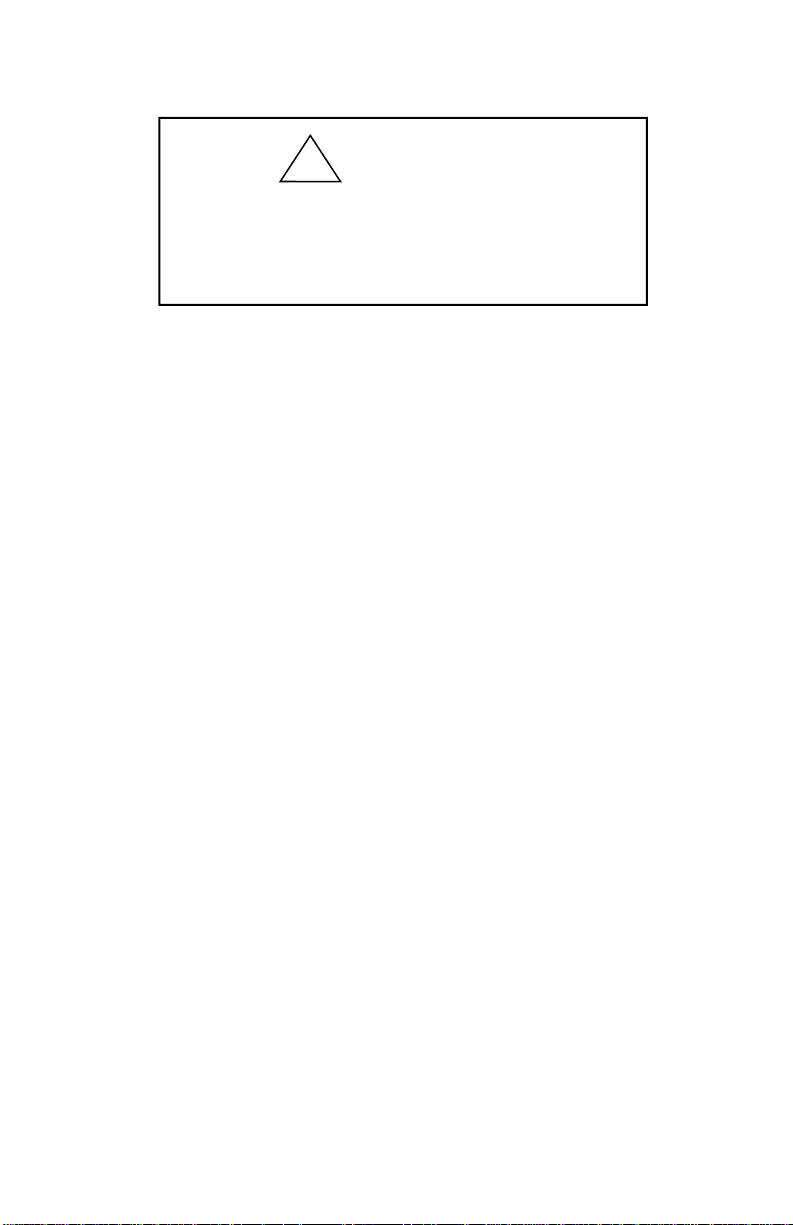
SAFETY INSTRUCTIONS
SM-79D
READ AND UNDERSTAND ALL INSTRUCTIONS
Failure to follow all instructions listed below, may result
!
in accident, fire and/or personal injury.
WARNING!
SAVE THESE INSTRUCTIONS
1. Do not allow corrosive gases or foreign material to enter the unit. Moisture, oilbased contaminants, or other liquids must be filtered out.
2. Eye protection is always required when running motor.
3. Hearing protection is recommended when in close proximity to all operating air
motors.
4. Dust mask, non-skid safety shoes, hard hat, gloves and other personal safety equipment must be used.
5. Stay alert, watch what you are doing, and use common sense when operating a
power tool.
6. Dress properly. Do not wear loose clothing or jewelry.
7. Keep your work area clean and well lit.
8. Do not operate power tools in explosive atmospheres, such as in the presence of
flammable liquids, gases, or dust.
9. Disconnect the tool from the air supply before installing, making any adjustment,
changing accessories, servicing or storing tool.
2
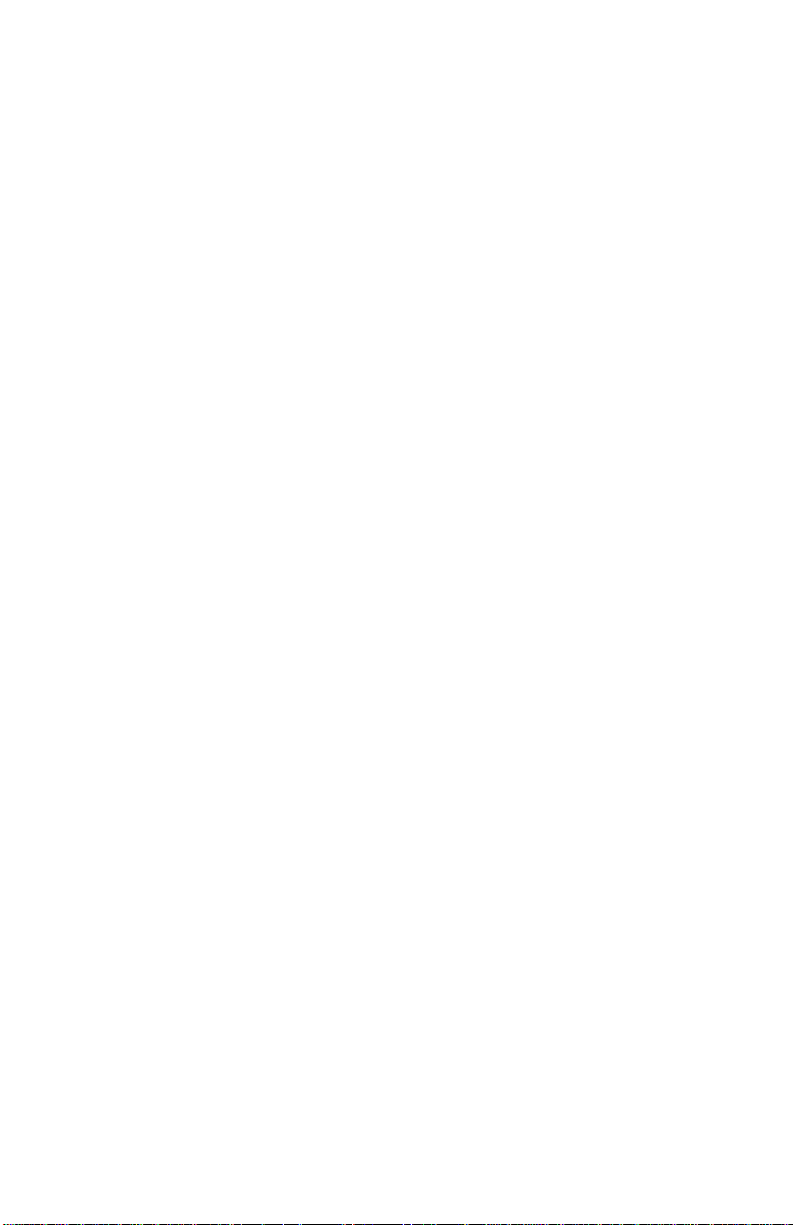
SM-79D
LUBRICATION
Amount of oil used will vary with tool usage but daily filling of handle oil reservoir
should normally be adequate. Check that a fine mist of oil is always present in the air
which passes out through exhaust deflector holes. For continuous and heavy tool usage, it is preferable to use an automatic air line lubri-cator. For this purpose, the Wilson Air Filter-Lubricator Unit (Cat. #8596 for 3/8” lines) is recommended. This unit
combines an automatic lubricator with an efficient air filter.
Caution: To inhibit rust during tool storage be sure a liberal amount of oil has been
introduced into valve and air motor. Also be sure operat-ing air moisture content is
kept at a minimum. Compressor after coolers, air line traps, water separators and use
of rust-inhibiting lubricat-ing oil all help. Thoroughly clean or replace any rusted
parts found during service checks.
OPERATION
1. Make sure there is an adequate supply of clean air of 90 psi lubricated with light
machine oil of SAE 10 viscosity. This should be done before all long runs of
tube expanding and after every four hours of continuous use unless an air line
lubricator of ample capacity is used. SEE ’LUBRICATION’ SECTION BELOW.
2. Always blow out air hose thoroughly before attaching it to throttle valve cap
which takes the 3/8” pipe coupling of 3/8” hose assembly supplied (No. 50007).
Always use a 3/8” I.D. or larger air line when maximum power is desired and be
sure that air pressure at the tool is at least 90 psi gauge.
3. Select required snap-on mandrel drive and attach it to tool spindle nose. Be sure
to align detents within it with drilled spots on spindle nose. (Instructions for releasing detents are stamped on mandrel drive sleeves.)
4. Adjust Thrust Collar on expander and attach mandrel to snap-on mandrel drive
by engag-ing detent and circular groove on mandrel’s square shank.
5. Insert expander in tube as required.
6. Completely depress throttle valve trigger lever to find forward speed. When desired expansion has been attained, release throttle valve lever .
7. Fully squeeze reverse valve trigger into reverse position (depressed). Depress
throttle valve trigger lever to reverse drive and back expander out of tube.
3