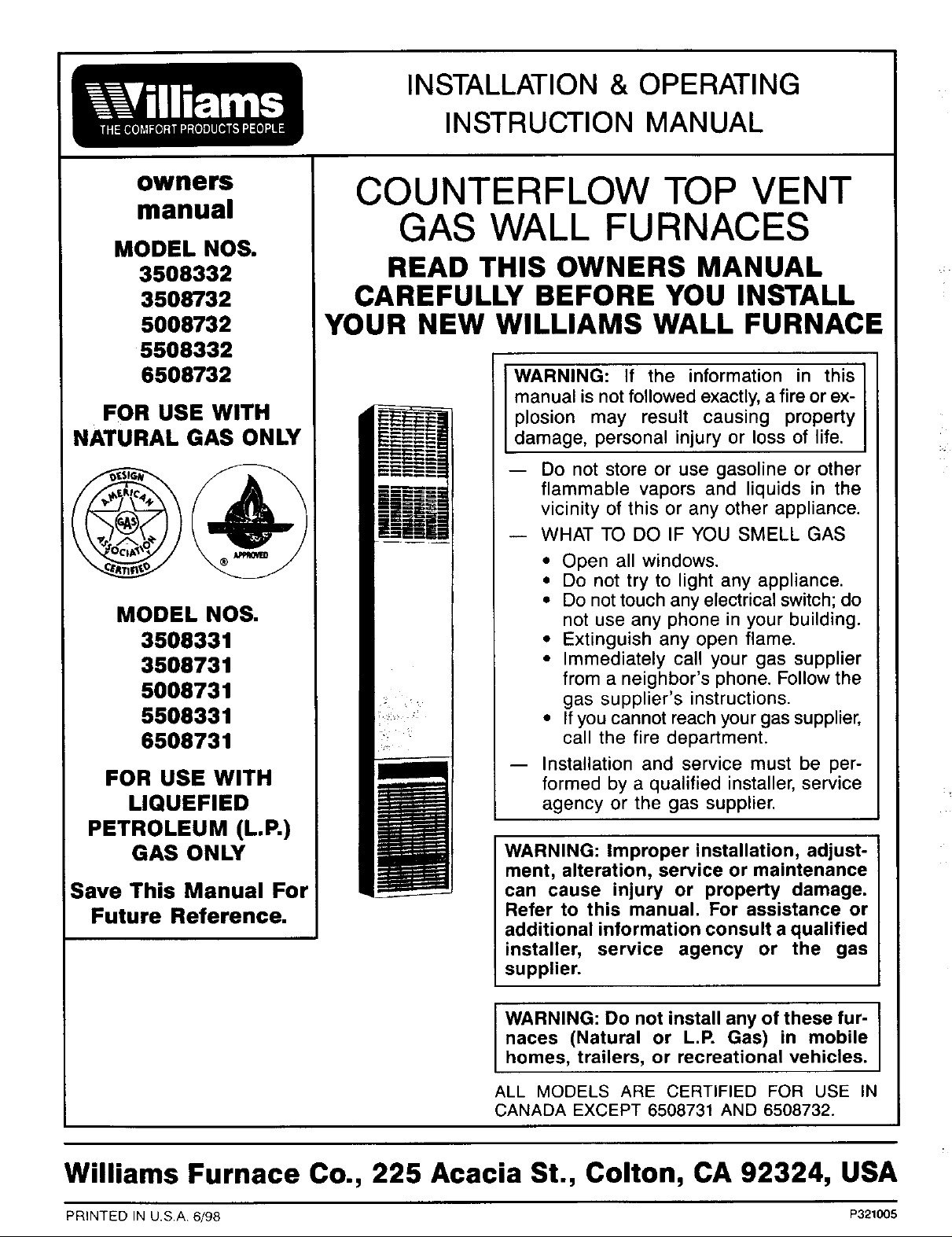
INSTALLATION & OPERATING
INSTRUCTION MANUAL
owners
manual
MODEL NOS.
3508332
3508732
5008732
5508332
6508732
FOR USE WITH
NATURAL GAS ONLY
MODEL NOS.
3508331
3508731
5008731
5508331
6508731
FOR USE WITH
LIQUEFIED
PETROLEUM (L.P.)
GAS ONLY
Save This Manual For
Future Reference.
COUNTERFLOW TOP VENT
GAS WALL FURNACES
READ THIS OWNERS MANUAL
CAREFULLY BEFORE YOU INSTALL
YOUR NEW WILLIAMS WALL FURNACE
WARNING: If the information in this
manual is not followed exactly, a fire or ex-
plosion may result causing property
damage, personal injury or loss of life.
-- Do not store or use gasoline or other
flammable vapors and liquids in the
vicinity of this or any other appliance.
WHAT TO DO IF YOU SMELL GAS
• Open all windows.
• Do not try to light any appliance.
• Do not touch any electrical switch; do
not use any phone in your building.
• Extinguish any open flame.
• Immediately call your gas supplier
from a neighbor's phone. Follow the
gas supplier's instructions.
• If you cannot reach your gas supplier,
call the fire department.
Installation and service must be per-
formed by a qualified installer, service
agency or the gas supplier.
WARNING: Improper installation, adjust-
ment, alteration, service or maintenance
can cause injury or property damage.
Refer to this manual. For assistance or
additional information consult a qualified
installer, service agency or the gas
supplier.
WARNING: Do not install any of these fur- I
naces (Natural or L.R Gas) in mobile
Ihomes, trailers, or recreational vehicles.
ALL MODELS ARE CERTIFIED FOR USE IN
CANADA EXCEPT 6508731 AND 6508732.
Williams Furnace Co., 225 Acacia St., Colton, CA 92324, USA
PRINTED IN U.S.A 6/98 P321005
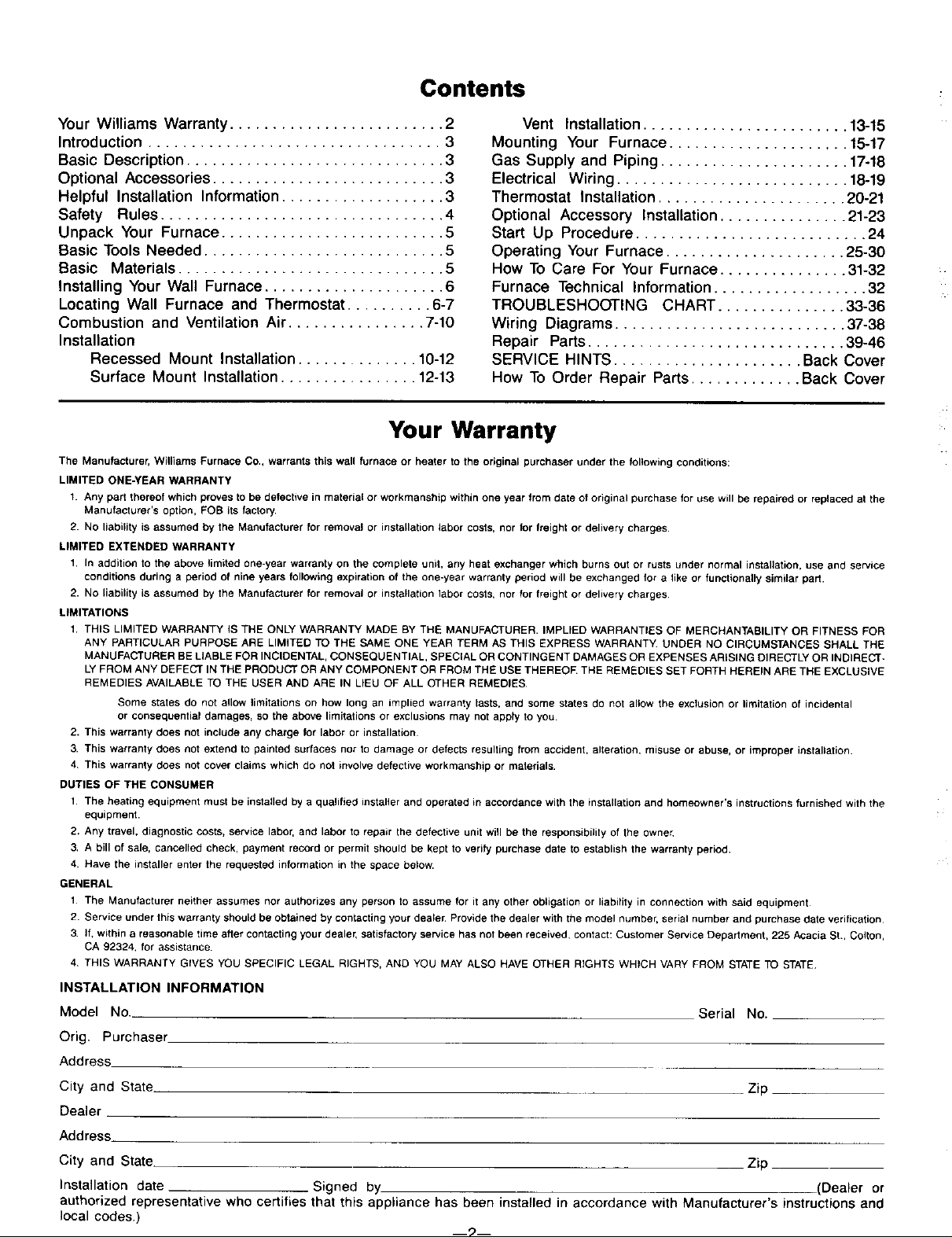
Contents
Your Williams Warranty ......................... 2
Introduction .................................. 3
Basic Description .............................. 3
Optional Accessories ........................... 3
Helpful Installation Information ................... 3
Safety Rules ................................. 4
Unpack Your Furnace .......................... 5
Basic Tools Needed ............................ 5
Basic Materials ............................... 5
Installing Your Wall Furnace ..................... 6
Locating Wall Furnace and Thermostat .......... 6-7
Combustion and Ventilation Air ................ 7-10
Installation
Recessed Mount Installation ............. 10-12
Surface Mount Installation ................ 12-13
Vent Installation ........................ 13-15
Mounting Your Furnace ..................... 15-17
Gas Supply and Piping ...................... 17-18
Electrical Wiring ........................... 18-19
Thermostat Installation ...................... 20-21
Optional Accessory Installation ............... 21-23
Start Up Procedure ........................... 24
Operating Your Furnace ..................... 25-30
How To Care For Your Furnace ............... 31-32
Furnace Technical Information .................. 32
TROUBLESHOOTING CHART ............... 33-36
Wiring Diagrams ........................... 37-38
Repair Parts .............................. 39-46
SERVICE HINTS ...................... Back Cover
How To Order Repair Parts ............. Back Cover
Your Warranty
The Manufacturer, Williams Furnace Co., warrants this wall furnace or heater to the original purchaser under the following conditions:
LIMITED ONE-YEAR WARRANTY
1. Any part thereof which proves to be defective in material or workmanship within one year from date of original purchase for use will be repaired or replaced al the
Manufacturer's option, FOB its factory,
2. No liability is assumed by the Manufacturer for removal or installation labor costs, nor for freight or delivery charges.
LIMITED EXTENDED WARRANTY
1, In addition to the above limited one-year warranty on the complete unit, any heat exchanger which burns out or rusts under normal installation, use and service
conditions during a period of nine years following expiration of the one-year warranty period will be exchanged for a like or functionally similar part.
2. No liability is assumed by the Manufacturer for removal or installation labor costs, nor for freight or delivery charges
LIMITATIONS
1. THIS LIMITED WARRANTY IS THE ONLY WARRANTY MADE BY THE MANUFACTURER. IMPLIED WARRANTIES OF MERCHANTABILITY OR FITNESS FOR
ANY PARTICULAR PURPOSE ARE LIMITED TO THE SAME ONE YEAR TERM AS THIS EXPRESS WARRANTY. UNDER NO CIRCUMSTANCES SHALL THE
MANUFACTURER BE LIABLE FOR INCIOENTAL, CONSEQUENTIAL, SPECIAL OR CONTINGENT DAMAGES OR EXPENSES ARISING DIRECTLY OR INDIRECT-
LY FROM ANY DEFECT IN THE PRODUCT OR ANY COMPONENT OR FROM THE USE THEREOF THE REMEDIES SET FORTH HEREIN ARE THE EXCLUSIVE
REMEDIES AVAILABLE TO THE USER AND ARE IN LIEU OF ALL OTHER REMEDIES
Some states do not allow limitations on how long an implied warranty lasts, and some states do not allow the exclusion or limitation of incidental
or consequential damages, so the above limitations or exclusions may not appty to you
2. This warranty does not include any charge for labor or installation
3. This warranty does not extend to painted surfaces nor to damage or defects resulting from accident, alleration, misuse or abuse, or improper installation.
4 This warranty does not cover claims which do not involve defective workmanship or materials.
DUTIES OF THE CONSUMER
1. The heating equipment must be installed by a qualified installer and operated in accordance with the installation and homeowner's instructions furnished with the
equipment.
2, Any travel, diagnostic costs, service labor, and labor to repair the defective unit will be the responsibility of the owne_
3, A bill of sale, cancelled check, payment record or permit should be kept to verify purchase date to establish the warranty period.
4. Have the installer enter the requested information in the space below.
GENERAL
1 The Manufacturer neither assumes nor authorizes any person to assume for it any other obligation or liability in connection with said equipment
2. Service under this warranty should be obtained by contacting your dealer Provide the dealer with the model number, serial number and purchase date verification
3. If. within a reasonable time after contacting your deale_ satisfactory service has not been received, contact: Customer Service Department, 225 Acacia St., Colton,
CA 92324_ for assistance
4 THIS WARRANTY GIVES YOU SPECIFIC LEGAL RIGHTS, AND YOU MAY ALSO HAVE OTHER RIGHTS WHICH VARY FROM STATE TO STATE
INSTALLATION INFORMATION
Model No.
Orig. Purchaser
Address
Serial No
City and State Zip
Dealer
Address.
City and State Zip
Installation date Signed by (Dealer or
authorized representative who certifies that this appliance has been installed in accordance with Manufacturer's instructions and
local codes.)
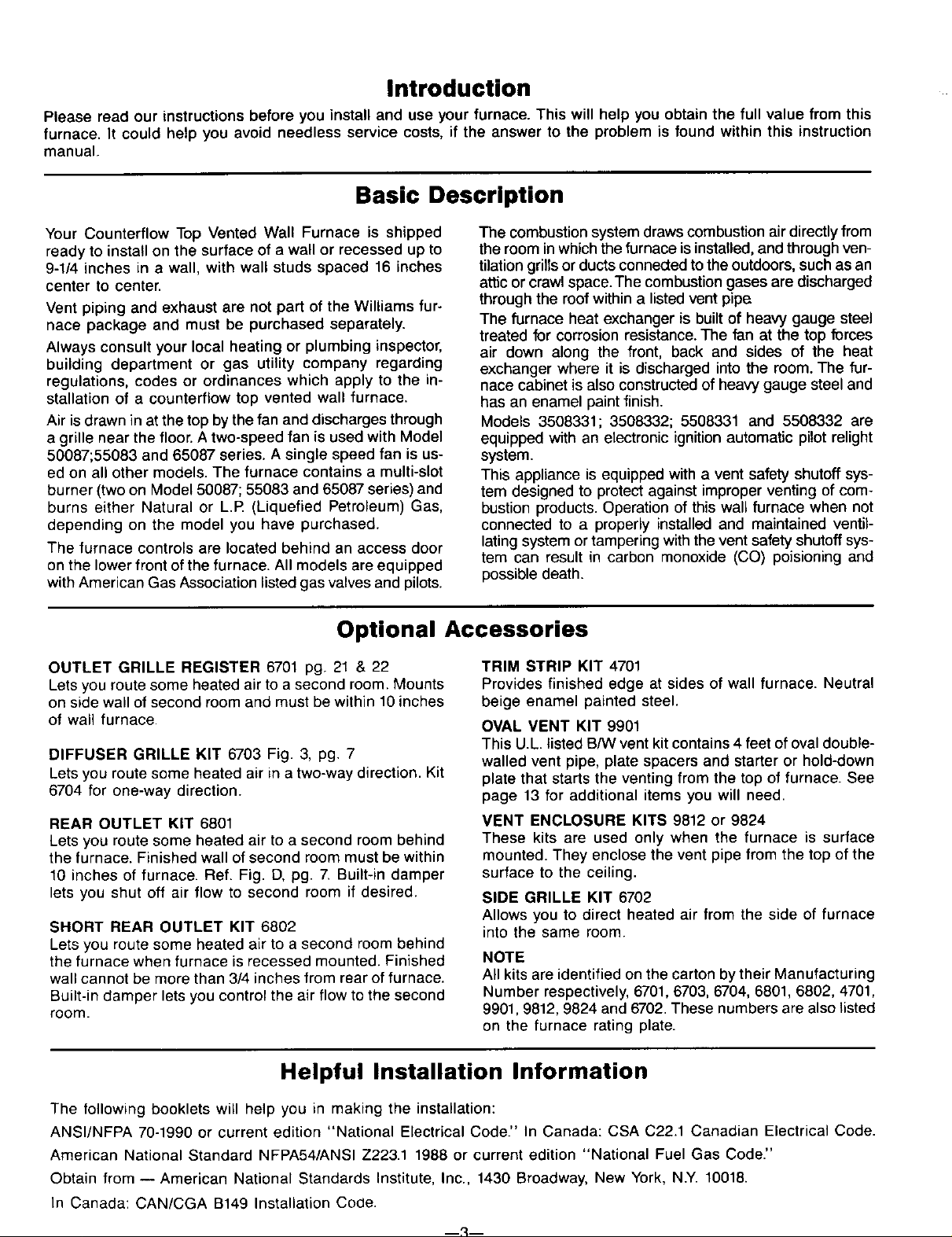
introduction
Please read our instructions before you install and use your furnace. This will help you obtain the full value from this
furnace. It could help you avoid needless service costs, if the answer to the problem is found within this instruction
manual.
Basic Description
Your Counterflow Top Vented Wall Furnace is shipped
ready to install on the surface of a wall or recessed up to
9-1/4 inches in a wall, with wall studs spaced 16 inches
center to center.
Vent piping and exhaust are not part of the Williams fur-
nace package and must be purchased separately.
Always consult your local heating or plumbing inspector,
building department or gas utility company regarding
regulations, codes or ordinances which apply to the in-
stallation of a counterflow top vented wall furnace.
Air is drawn in at the top by the fan and discharges through
a grille near the floor. A two-speed fan is used with Model
50087;55083 and 65087 series. A single speed fan is us-
ed on all other models. The furnace contains a multi-slot
burner (two on Model 50087; 55083 and 65087 series) and
burns either Natural or L.P (Liquefied Petroleum) Gas,
depending on the model you have purchased.
The furnace controls are located behind an access door
on the lower front of the furnace. All models are equipped
with American Gas Association listed gas valves and pilots.
Optional Accessories
OUTLET GRILLE REGISTER 6701 pg. 21 & 22
Lets you route some heated air to a second room. Mounts
on side wall of second room and must be within 10 inches
of wall furnace.
DIFFUSER GRILLE KIT 6703 Fig. 3, pg. 7
Lets you route some heated air in a two-way direction. Kit
6704 for one-way direction.
REAR OUTLET KIT 6801
Lets you route some heated air to a second room behind
the furnace. Finished wall of second room must be within
10 inches of furnace. Ref. Fig. D, pg. 7. Built-in damper
lets you shut off air flow to second room if desired.
SHORT REAR OUTLET KIT 6802
Letsyou route some heated air to a second room behind
the furnace when furnace is recessed mounted. Finished
wall cannot be more than 3/4 inches from rear offurnace.
Built-in damper lets you control the air flow to the second
room.
The combustion system draws combustion air directly from
the room in which the furnace is installed, and through ven-
tilation grills or ducts connected to the outdoors, such as an
attic or crawl space. The combustion gases are discharged
through the roof within a listed vent pipe
The furnace heat exchanger is built of heavy gauge steel
treated for corrosion resistance. The fan at the top forces
air down along the front, back and sides of the heat
exchanger where it is discharged into the room. The fur-
nace cabinet is also constructed of heavy gauge steel and
has an enamel paint finish.
Models 3508331; 3508332; 5508331 and 5508332 are
equipped with an electronic ignitionautomatic pilot relight
system.
This appliance is equipped with a vent safety shutoff sys-
tem designed to protect against improper venting of com-
bustion products. Operation of this wall furnace when not
connected to a properly installed and maintained ventil-
lating system or tampering with the vent safety shutoff sys-
tem can result in carbon monoxide (CO) poisioning and
possible death.
TRIM STRIP KIT 4701
Provides finished edge at sides of wall furnace. Neutral
beige enamel painted steel.
OVAL VENT KIT 9901
This U.L. listed B/W vent kit contains 4 feet of oval double-
walled vent pipe, plate spacers and starter or hold-down
plate that starts the venting from the top of furnace. See
page 13 for additional items you will need.
VENT ENCLOSURE KITS 9812 or 9824
These kits are used only when the furnace is surface
mounted. They enclose the vent pipe from the top ofthe
surface to the ceiling.
SIDE GRILLE KIT 6702
Allows you to direct heated air from the side of furnace
into the same room.
NOTE
All kits are identified on the carton by their Manufacturing
Number respectively, 6701, 6703, 6704, 6801, 6802, 4701,
9901, 9812, 9824 and 6702. These numbers are also listed
on the furnace rating plate.
Helpful Installation Information
The following booklets will help you in making the installation:
ANSI/NFPA 70-1990 or current edition "National Electrical Code." In Canada: CSA C22.1 Canadian Electrical Code.
American National Standard NFPA54/ANSI Z223.1 1988 or current edition "National Fuel Gas Code."
Obtain from -- American National Standards Institute, Inc., 1430 Broadway, New York, N.Y. 10018.
In Canada: CAN/CGA B149 Installation Code.
m:_m
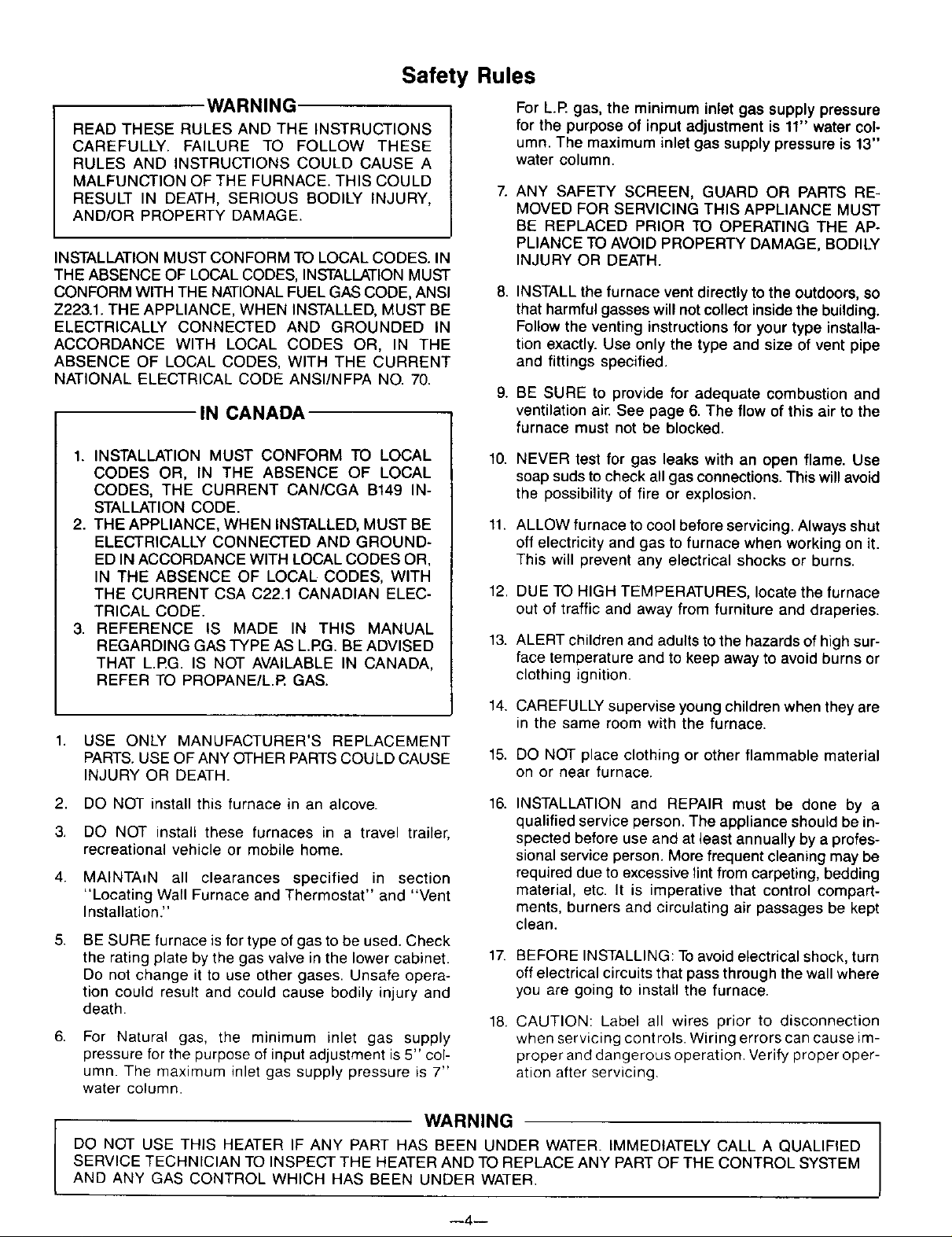
Safety Rules
WARNING
READ THESE RULES AND THE INSTRUCTIONS
CAREFULLY. FAILURE TO FOLLOW THESE
RULES AND INSTRUCTIONS COULD CAUSE A
MALFUNCTION OF THE FURNACE. THIS COULD
RESULT IN DEATH, SERIOUS BODILY INJURY,
AND/OR PROPERTY DAMAGE.
INSTALLATION MUST CONFORM TO LOCAL CODES. IN
THE ABSENCE OF LOCAL CODES, INSTALLATION MUST
CONFORM WITH THE NATIONAL FUEL GAS CODE, ANSI
Z223.1. THE APPLIANCE, WHEN INSTALLED, MUST BE
ELECTRICALLY CONNECTED AND GROUNDED IN
ACCORDANCE WITH LOCAL CODES OR, IN THE
ABSENCE OF LOCAL CODES, WITH THE CURRENT
NATIONAL ELECTRICAL CODE ANSI/NFPA NO. 70.
IN CANADA
1. INSTALLATION MUST CONFORM TO LOCAL
CODES OR, IN THE ABSENCE OF LOCAL
CODES, THE CURRENT CAN/CGA B149 IN-
STALLATION CODE.
2. THE APPLIANCE, WHEN INSTALLED, MUST BE
ELECTRICALLY CONNECTED AND GROUND-
ED IN ACCORDANCE WITH LOCAL CODES OR,
IN THE ABSENCE OF LOCAL CODES, WITH
THE CURRENT CSA C22.1 CANADIAN ELEC-
TRICAL CODE.
3. REFERENCE IS MADE IN THIS MANUAL
REGARDING GAS TYPE AS L.P.G. BE ADVISED
THAT L.RG. IS NOT AVAILABLE IN CANADA,
REFER TO PROPANE/L.P. GAS.
1. USE ONLY MANUFACTURER'S REPLACEMENT
PARTS. USE OF ANY OTHER PARTS COULD CAUSE
INJURY OR DEATH.
2,
DO NOT install this furnace in an alcove.
3_
DO NOT install these furnaces in a travel trailer,
recreational vehicle or mobile home.
4.
MAINTAIN all clearances specified in section
"Locating Wall Furnace and Thermostat" and "Vent
Installation."
5.
BE SURE furnace is for type of gas to be used. Check
the rating plate by the gas valve in the lower cabinet.
Do not change it to use other gases. Unsafe opera-
tion could result and could cause bodily injury and
death.
6.
For Natural gas, the minimum inlet gas supply
pressure for the purpose of input adjustment is 5" col-
umn. The maximum inlet gas supply pressure is T'
water column.
For L.IR gas, the minimum inlet gas supply pressure
for the purpose of input adjustment is 11" water col-
umn. The maximum inlet gas supply pressure is 13"
water column.
7.
ANY SAFETY SCREEN, GUARD OR PARTS RE-
MOVED FOR SERVICING THIS APPLIANCE MUST
BE REPLACED PRIOR TO OPERATING THE AP-
PLIANCE TO AVOID PROPERTY DAMAGE, BODILY
INJURY OR DEATH.
8.
INSTALL the furnace vent directly to the outdoors, so
that harmful gasses will not collect inside the building.
Follow the venting instructions for your type installa-
tion exactly. Use only the type and size of vent pipe
and fittings specified.
9.
BE SURE to provide for adequate combustion and
ventilation air. See page 6. The flow of this air to the
furnace must not be blocked.
10.
NEVER test for gas leaks with an open flame. Use
soap suds to check all gas connections. This will avoid
the possibility of fire or explosion.
11.
ALLOW furnace to cool before servicing. Always shut
off electricity and gas to furnace when working on it.
This will prevent any electrical shocks or burns.
12.
DUE TO HIGH TEMPERATURES, locate the furnace
out of traffic and away from furniture and draperies.
13.
ALERT children and adults to the hazards of high sur-
face temperature and to keep away to avoid burns or
clothing ignition.
14.
CAREFULLY supervise young children when they are
in the same room with the furnace.
15. DO NOT place clothing or other flammable material
on or near furnace.
16.
INSTALLATION and REPAIR must be done by a
qualified service person. The appliance should be in-
spected before use and at least annually by a profes-
sional service person. More frequent cleaning may be
required due to excessive lint from carpeting, bedding
material, etc. It is imperative that control compart-
ments, burners and circulating air passages be kept
clean.
17.
BEFORE INSTALLING: Toavoid electrical shock, turn
off electrical circuits that pass through the wall where
you are going to install the furnace.
18.
CAUTION: Label all wires prior to disconnection
when servicing controls. Wiring errors can cause im-
proper and dangerous operation. Verify proper oper-
ation after servicing
WARNING
DO NOT USE THJS HEATER IF ANY PART HAS BEEN UNDER WATER. IMMEDIATELY CALL A QUALIFIED
SERVICE TECHNICIAN TO INSPECT THE HEATER AND TO REPLACE ANY PART OF THE CONTROL SYSTEM
I
AND ANY GAS CONTROL WHICH HAS BEEN UNDER WATER.
--4--
I
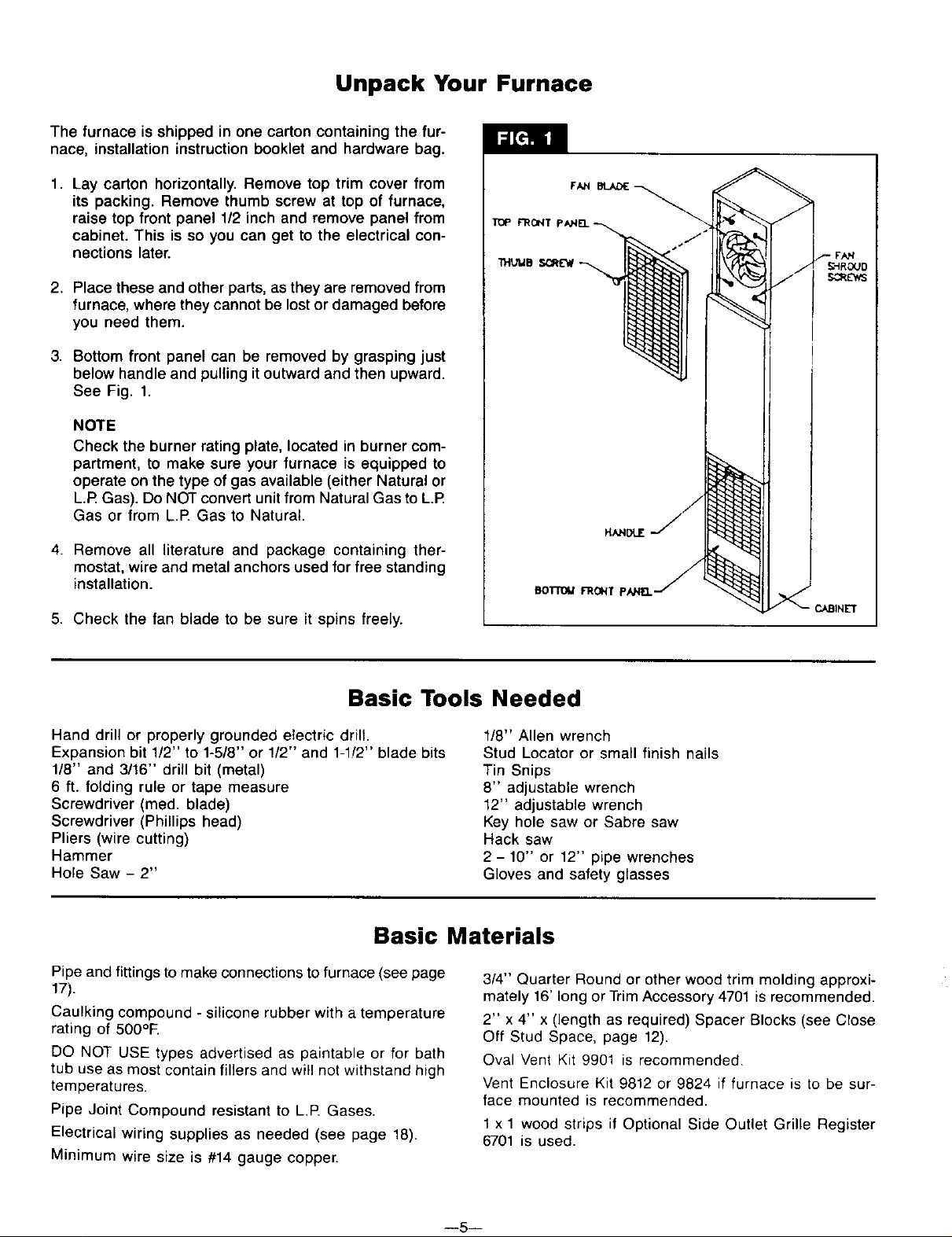
Unpack Your Furnace
The furnace is shipped in one carton containing the fur-
nace, installation instruction booklet and hardware bag.
1. Lay carton horizontally. Remove top trim cover from
its packing. Remove thumb screw at top of furnace,
raise top front panel 1/2 inch and remove panel from
cabinet. This is so you can get to the electrical con-
nections later.
2. Place these and other parts, as they are removed from
furnace, where they cannot be lost or damaged before
you need them.
3. Bottom front panel can be removed by grasping just
below handle and pulling it outward and then upward.
See Fig. 1.
NOTE
Check the burner rating plate, located in burner com-
partment, to make sure your furnace is equipped to
operate on the type of gas available (either Natural or
L.IRGas). Do NOT convert unit from Natural Gas to L.IR
Gas or from L.F_ Gas to Natural.
4. Remove all literature and package containing ther-
mostat, wire and metal anchors used for free standing
installation.
5. Check the fan blade to be sure it spins freely.
Basic Tools Needed
Hand drill or properly grounded electric drill.
Expansion bit 1/2" to 1-5/8" or 1/2" and 1-1/2" blade bits
1/8" and 3/16" drill bit (metal)
6 ft. folding rule or tape measure
Screwdriver (med. blade)
Screwdriver (Phillips head)
Pliers (wire cutting)
Hammer
Hole Saw - 2"
Basic Materials
Pipe and fittings tomake connections to furnace (see page
17).
Caulking compound - silicone rubber with a temperature
rating of 500°tE
DO NOT USE types advertised as paintable or for bath
tub use as most contain fillers and will not withstand high
temperatures.
Pipe Joint Compound resistant to L.P. Gases.
Electrical wiring supplies as needed (see page 18).
Minimum wire size is #14 gauge copper.
1/8" Allen wrench
Stud Locator or small finish nails
Tin Snips
8" adjustable wrench
12" adjustable wrench
Key hole saw or Sabre saw
Hack saw
2- 10" or 12" pipe wrenches
Gloves and safety glasses
3/4" Quarter Round or other wood trim molding approxi-
mately 16' long or Trim Accessory 4701 is recommended.
2" x 4" x (length as required) Spacer Blocks (see Close
Off Stud Space, page 12).
Oval Vent Kit 9901 is recommended.
Vent Enclosure Kit 9812 or 9824 if furnace is to be sur-
face mounted is recommended.
1 x 1 wood strips if Optional Side Outlet Grille Register
6701 is used.
--5--
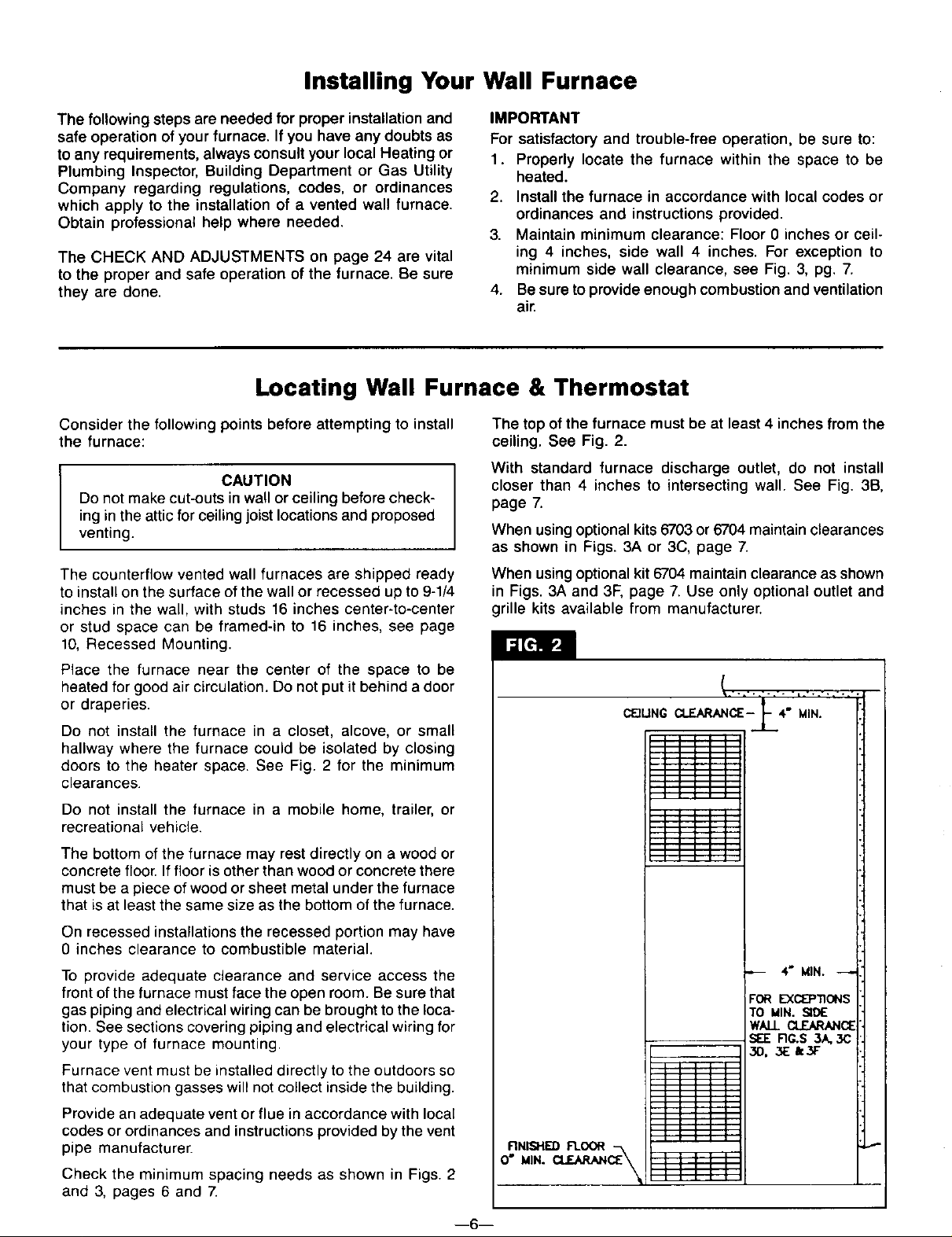
Installing Your Wall Furnace
The following steps are needed for proper installation and
safe operation of your furnace. If you have any doubts as
to any requirements, always consult your local Heating or
Plumbing Inspector, Building Department or Gas Utility
Company regarding regulations, codes, or ordinances
which apply to the installation of a vented wall furnace.
Obtain professional help where needed.
The CHECK AND ADJUSTMENTS on page 24 are vital
to the proper and safe operation of the furnace. Be sure
they are done.
IMPORTANT
For satisfactory and trouble-free operation, be sure to:
1. Properly locate the furnace within the space to be
heated.
2. Install the furnace in accordance with local codes or
ordinances and instructions provided.
3. Maintain minimum clearance: Floor 0 inches or ceil-
ing 4 inches, side wall 4 inches. For exception to
minimum side wall clearance, see Fig. 3, pg. 7.
4. Besure to provide enough combustion and ventilation
air.
Locating Wall Furnace & Thermostat
Consider the following points before attempting to install
the furnace:
CAUTION
Do not make cut-outs in wall or ceiling before check-
ing in the attic for ceiling joist locations and proposed
venting.
The counterflow vented wall furnaces are shipped ready
to install on the surface of the wall or recessed up to 9-1/4
inches in the wall, with studs 16 inches center-to-center
or stud space can be framed-in to 16 inches, see page
10, Recessed Mounting. I_[{'kIP_ll
Place the furnace near the center of the space to be
heated for good air circulation. Do not put it behind a door
or draperies.
Do not install the furnace in a closet, alcove, or small
hallway where the furnace could be isolated by closing
doors to the heater space. See Fig. 2 for the minimum
clearances.
The top of the furnace must be at least 4 inches from the
ceiling. See Fig. 2.
With standard furnace discharge outlet, do not install
closer than 4 inches to intersecting wall. See Fig. 3B,
page 7.
When using optional kits 6703or 6704 maintain clearances
as shown in Figs. 3A or 3C, page 7.
When using optional kit 6704 maintain clearance as shown
in Figs. 3A and 3F, page 7. Use only optional outlet and
grille kits available from manufacturer.
Do not install the furnace in a mobile home, trailer, or
recreational vehicle.
The bottom of the furnace may rest directly on a wood or
concrete floor. If floor is other than wood or concrete there
must be a piece of wood or sheet metal under the furnace
that is at least the same size as the bottom of the furnace.
On recessed installations the recessed portion may have
0 inches clearance to combustible material.
To provide adequate clearance and service access the
front of the furnace must face the open room. Be sure that
gas piping and electrical wiring can be brought to the loca-
tion. See sections covering piping and electrical wiring for
your type of furnace mounting.
Furnace vent must be installed directly to the outdoors so
that combustion gasses will not collect inside the building.
Provide an adequate vent or flue in accordance with local
codes or ordinances and instructions provided by the vent
pipe manufacturer.
Check the minimum spacing needs as shown in Figs. 2
and 3, pages 6 and 7.
--6--
RNISHED FLOOR
O" MIN.
FOR EXCEPllONS
TO MIN. SIDE
WALL CLF_CE
_RG.S 3A. ,.3C
,'.'_ k 3F
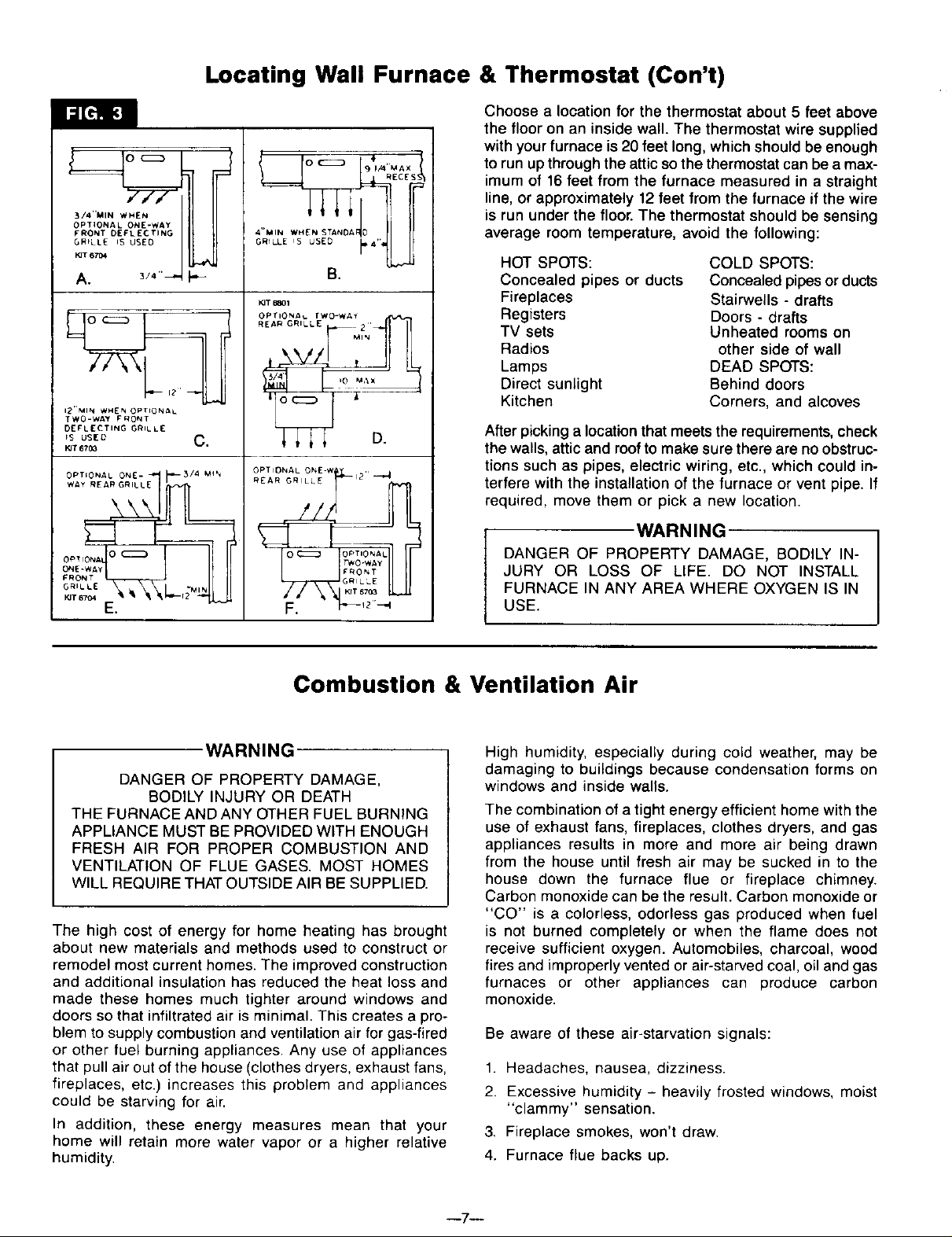
_/4"MIN WHEN
OPTIONAL ONE-WAY
FRONT DEFLECTING
GRILLE IS USED
A. 3/4 "_- _
12 ¸' _
12"MIN WHEN OPTIONAL
T W0 -WAY F_ONT
DEFL [CTING GRILLE
rS USED C.
FJT 67_
OPTIONAL ON[- _'_ I,_- 3/4 MI%
WAY f_EAR GRILLE
_IE-WAy
FRONT
0PTIONAo__
GRILL[ -MI N
r2
E.
Locating Wall Furnace & Thermostat (Con't)
Choose a location for the thermostat about 5 feet above
the floor on an inside wall. The thermostat wire supplied
with your furnace is 20 feet long, which should be enough
....,%
0 _ I_llM A X
GRIU-E IS US[D 1_4" _
B.
KIT I_01
OP_IONA_ rWO-WA_ _.
REAR GRILLE 2 ¸'_ I
D.
;_
to run up through the attic so the thermostat can be a max-
imum of 16 feet from the furnace measured in a straight
line, or approximately 12feet from the furnace if the wire
is run under the floor. The thermostat should be sensing
average room temperature, avoid the following:
HOT SPOTS:
Concealed pipes or ducts
Fireplaces
Registers
TV sets
Radios
Lamps
Direct sunlight
Kitchen
After picking a location that meets the requirements, check
the walls, attic and roof to make sure there are no obstruc-
tions such as pipes, electric wiring, etc., which could in-
terfere with the installation of the furnace or vent pipe. If
required, move them or pick a new location.
WARNING
DANGER OF PROPERTY DAMAGE, BODILY IN-
JURY OR LOSS OF LIFE. DO NOT INSTALL
FURNACE IN ANY AREA WHERE OXYGEN IS IN
USE.
COLD SPOTS:
Concealed pipes or ducts
Stairwells - drafts
Doors - drafts
Unheated rooms on
other side of wall
DEAD SPOTS:
Behind doors
Corners, and alcoves
Combustion & Ventilation Air
WARNING
DANGER OF PROPERTY DAMAGE,
BODILY INJURY OR DEATH
THE FURNACE AND ANY OTHER FUEL BURNING
APPLIANCE MUST BE PROVIDED WITH ENOUGH
FRESH AIR FOR PROPER COMBUSTION AND
VENTILATION OF FLUE GASES. MOST HOMES
WILL REQUIRE THAT OUTSIDE AIR BE SUPPLIED.
The high cost of energy for home heating has brought
about new materials and methods used to construct or
remodel most current homes. The improved construction
and additional insulation has reduced the heat loss and
made these homes much tighter around windows and
doors so that infiltrated air is minimal. This creates a pro-
blem to supply combustion and ventilation air for gas-fired
or other fuel burning appliances. Any use of appliances
that pull air out of the house (clothes dryers, exhaust fans,
fireplaces, etc.) increases this problem and appliances
could be starving for air.
In addition, these energy measures mean that your
home will retain more water vapor or a higher relative
humidity.
High humidity, especially during cold weather, may be
damaging to buildings because condensation forms on
windows and inside walls.
The combination of a tight energy efficient home with the
use of exhaust fans, fireplaces, clothes dryers, and gas
appliances results in more and more air being drawn
from the house until fresh air may be sucked in to the
house down the furnace flue or fireplace chimney.
Carbon monoxide can be the result. Carbon monoxide or
"CO" is a colorless, odorless gas produced when fuel
is not burned completely or when the flame does not
receive sufficient oxygen. Automobiles, charcoal, wood
fires and improperly vented or air-starved coal, oil and gas
furnaces or other appliances can produce carbon
monoxide.
Be aware of these air-starvation signals:
1. Headaches, nausea, dizziness.
2. Excessive humidity - heavily frosted windows, moist
"clammy" sensation.
3. Fireplace smokes, won't draw.
4. Furnace flue backs up.
--7--
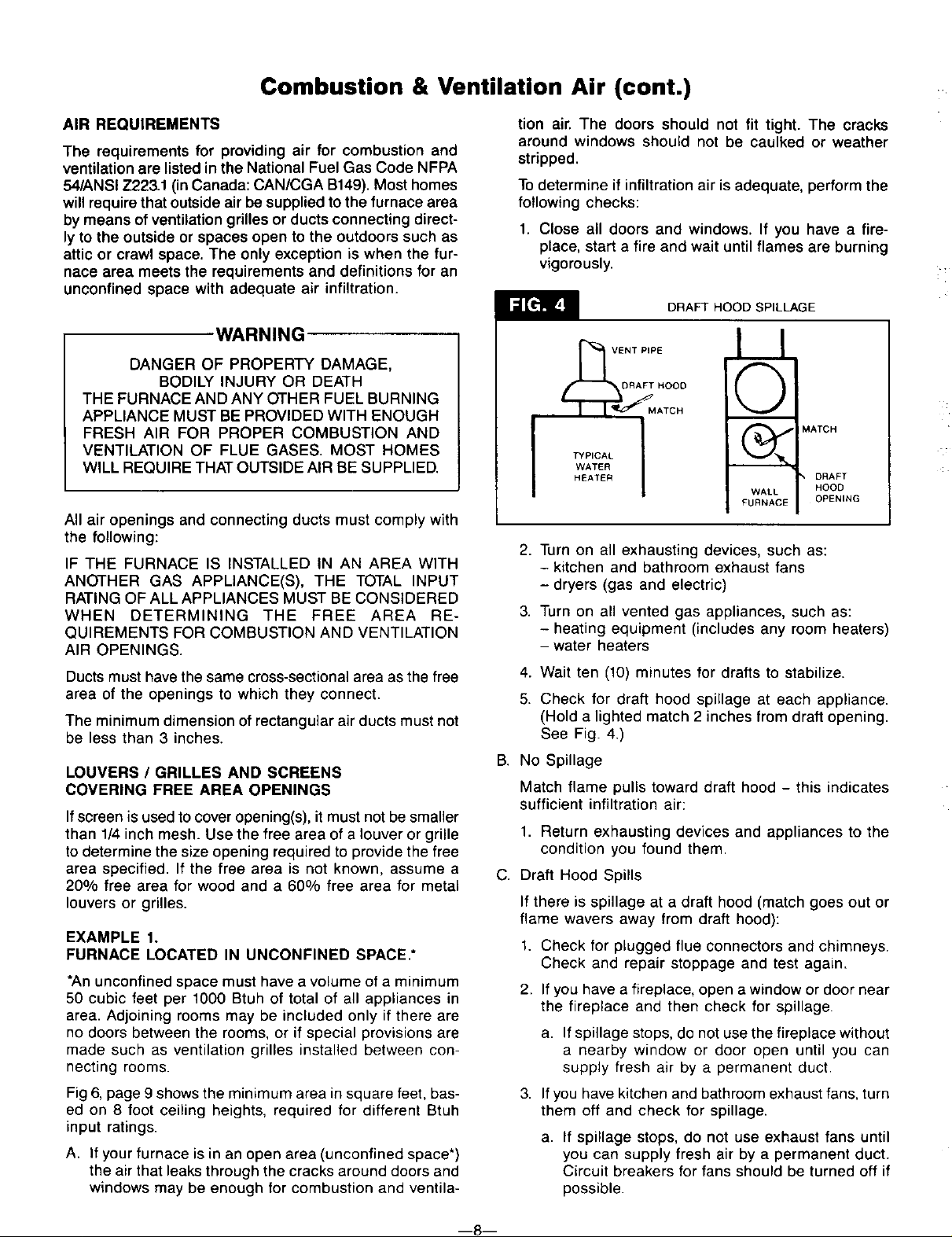
Combustion & Ventilation Air (cont.)
AIR REQUIREMENTS
The requirements for providing air for combustion and
ventilation are listed in the National Fuel Gas Code NFPA
54/ANSI Z223.1 (in Canada: CAN/CGA B149). Most homes
will require that outside air be supplied to the furnace area
by means of ventilation grilles or ducts connecting direct-
ly to the outside or spaces open to the outdoors such as
attic or crawl space. The only exception is when the fur-
nace area meets the requirements and definitions for an
unconfined space with adequate air infiltration.
WARNING
DANGER OF PROPERTY DAMAGE,
BODILY INJURY OR DEATH
THE FURNACE AND ANY OTHER FUEL BURNING
APPLIANCE MUST BE PROVIDED WITH ENOUGH
FRESH AIR FOR PROPER COMBUSTION AND
VENTILATION OF FLUE GASES. MOST HOMES
WILL REQUIRE THAT OUTSIDE AIR BE SUPPLIED.
All air openings and connecting ducts must comply with
the following:
IF THE FURNACE IS INSTALLED IN AN AREA WITH
ANOTHER GAS APPLIANCE(S), THE TOTAL INPUT
RATING OF ALL APPLIANCES MUST BE CONSIDERED
WHEN DETERMINING THE FREE AREA RE-
QUIREMENTS FOR COMBUSTION AND VENTILATION
AIR OPENINGS.
Ducts must have the same cross-sectional area as the free
area of the openings to which they connect.
The minimum dimension of rectangular air ducts must not
be less than 3 inches.
LOUVERS / GRILLES AND SCREENS
COVERING FREE AREA OPENINGS
If screen is used to cover opening(s), it must not be smaller
than 1/4 inch mesh. Use the free area of a louver or grille
to determine the size opening required to provide the free
area specified. If the free area is not known, assume a
20% free area for wood and a 60% free area for metal
louvers or grilles.
EXAMPLE 1.
FURNACE LOCATED IN UNCONFINED SPACE.*
*An unconfined space must have a volume of a minimum
50 cubic feet per 1000 Btuh of total of all appliances in
area. Adjoining rooms may be included only if there are
no doors between the rooms, or if special provisions are
made such as ventilation grilles installed between con-
necting rooms.
Fig 6, page 9 shows the minimum area in square feet, bas-
ed on 8 foot ceiling heights, required for different Btuh
input ratings.
A. If your furnace is in an open area (unconfined space*)
the air that leaks through the cracks around doors and
windows may be enough for combustion and ventila-
tion air. The doors should not fit tight. The cracks
around windows should not be caulked or weather
stripped.
To determine if infiltration air is adequate, perform the
following checks:
1. Close all doors and windows. If you have a fire-
place, start a fire and wait until flames are burning
vigorously.
DRAFT HOOD SPILLAGE
VENT PIPE
WATER
HEATER
DRAFT HOOD
__MATCH
2,
Turn on all exhausting devices, such as:
__L
I
WALL
FURNACE
MATCH
DRAFT
HOOD
OPENING
- kitchen and bathroom exhaust fans
- dryers (gas and electric)
3,
Turn on all vented gas appliances, such as:
- heating equipment (includes any room heaters)
- water heaters
4. Wait ten (10) minutes for drafts to stabilize.
5. Check for draft hood spillage at each appliance.
(Hold a lighted match 2 inches from draft opening.
See Fig. 4.)
B. No Spillage
Match flame pulls toward draft hood - this indicates
sufficient infiltration air:
1. Return exhausting devices and appliances to the
condition you found them.
C. Draft Hood Spills
If there is spillage at a draft hood (match goes out or
flame wavers away from draft hood):
1. Check for plugged flue connectors and chimneys.
Check and repair stoppage and test again.
2. If you have a fireplace, open a window or door near
the fireplace and then check for spillage.
a. If spillage stops, do not use the fireplace without
a nearby window or door open until you can
supply fresh air by a permanent duct.
3. Ifyou have kitchen and bathroom exhaust fans, turn
them off and check for spillage.
a. If spillage stops, do not use exhaust fans until
you can supply fresh air by a permanent duct.
Circuit breakers for fans should be turned off if
possible.
m8--
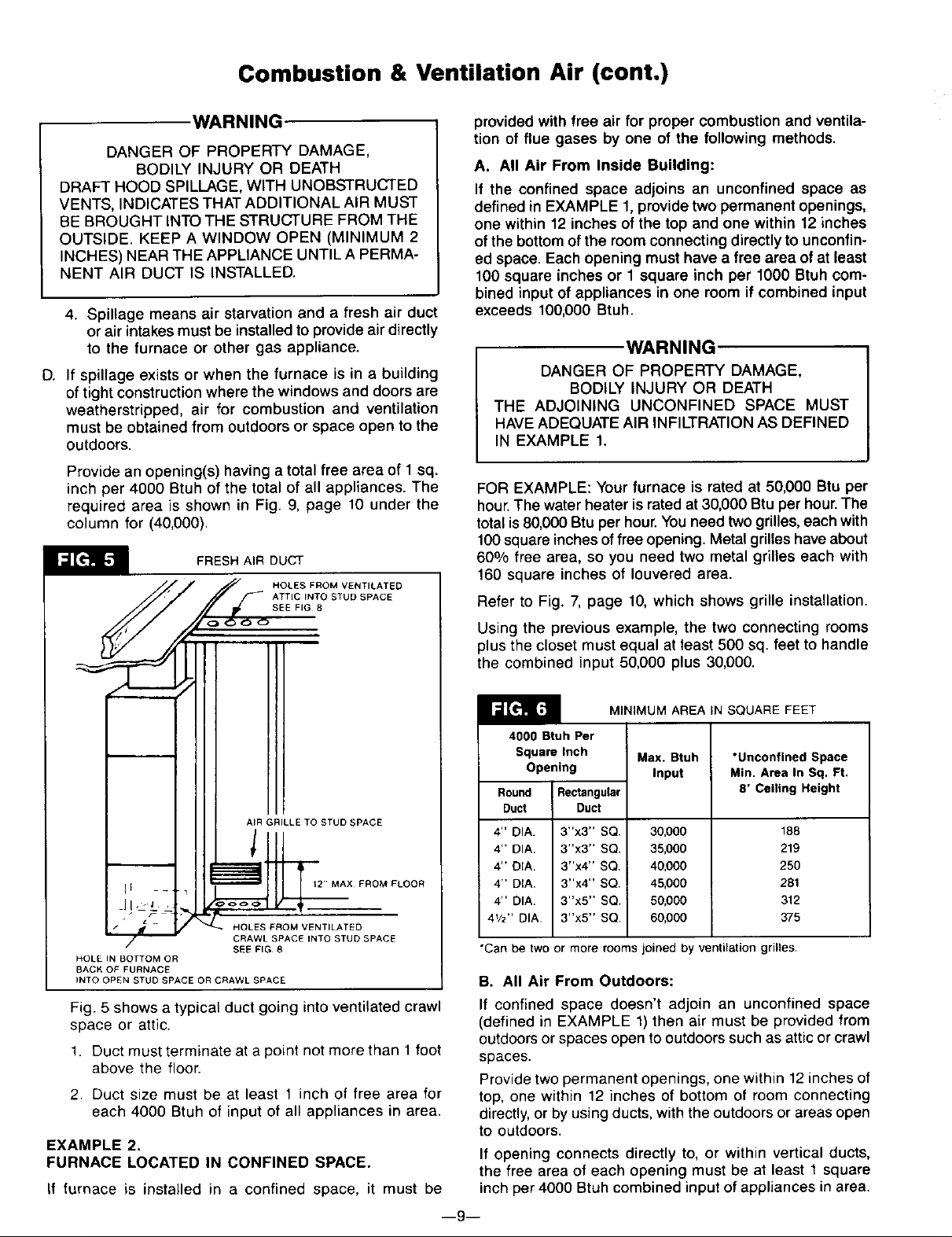
Combustion & Ventilation Air (cont.)
WARNING,
DANGER OF PROPERTY DAMAGE,
BODILY INJURY OR DEATH
DRAFT HOOD SPILLAGE, WITH UNOBSTRUCTED
VENTS, INDICATES THAT ADDITIONAL AIR MUST
BE BROUGHT iNTO THE STRUCTURE FROM THE
OUTSIDE. KEEP A WINDOW OPEN (MINIMUM 2
INCHES) NEAR THE APPLIANCE UNTIL A PERMA-
NENT AIR DUCT iS INSTALLED.
4. Spillage means air starvation and a fresh air duct
or air intakes must be installed to provide air directly
to the furnace or other gas appliance.
D. If spillage exists or when the furnace is in a building
of tight construction where the windows and doors are
weatherstripped, air for combustion and ventilation
must be obtained from outdoors or space open to the
outdoors.
Provide an opening(s) having a total free area of 1 sq.
inch per 4000 Btuh of the total of all appliances. The
required area is shown in Fig. 9, page 10 under the
column for (40,000).
FRESH AIR DUCT
HOLES FROM VENTILATED
ATTIC INTO STUD SPACE
SEE FIG 8
provided with free air for proper combustion and ventila-
tion of flue gases by one of the following methods.
A. All Air From Inside Building:
If the confined space adjoins an unconfined space as
defined in EXAMPLE 1,provide two permanent openings,
one within 12 inches of the top and one within 12 inches
of the bottom of the room connecting directly to unconfin-
ed space. Each opening must have a free area of at least
100 square inches or 1 square inch per 1000 Btuh com-
bined input of appliances in one room if combined input
exceeds 100,000 Btuh.
WARNING
DANGER OF PROPERTY DAMAGE,
BODILY INJURY OR DEATH
THE ADJOINING UNCONFINED SPACE MUST
HAVEADEQUATE AIR INFILTRATION AS DEFINED
IN EXAMPLE 1.
FOR EXAMPLE: Your furnace is rated at 50,000 Btu per
hour.The water heater israted at 30,000 Btu per hour.The
totalis80,000 Btu per hour.Youneed two grilles,each with
100 square inchesof free opening. Metal grilles haveabout
60% free area, so you need two metal grilles each with
160 square inches of Iouvered area.
Refer to Fig. 7, page 10, which shows grille installation.
Using the previous example, the two connecting rooms
plus the closet must equal at least 500 sq. feet to handle
the combined input 50,000 plus 30,000.
AIR GRILLE TO STUD SPACE
12" MAXFROM FLOOR
HOLES FROM VENTILATED
CRAWL SPACE INTO STUD SPACE
HOLE IN BOTTOM OR
BACK OF FURNACE
INTO OPEN STUD SPACE OR CRAWL SPACE
SEE FIG 8
Fig. 5 shows a typical duct going into ventilated crawl
space or attic.
1. Duct must terminate at a point not more than 1 foot
above the floor.
2. Duct size must be at least 1 inch of free area for
each 4000 Btuh of input of all appliances in area.
EXAMPLE 2.
FURNACE LOCATED IN CONFINED SPACE.
If furnace is installed in a confined space, it must be
MINIMUM AREA IN SQUARE FEET
4000 Btuh Per
Square lnch
Opening
Round Rectangular
Duct
4" DIA.
4" DIA.
4" D[A.
4" DIA,
4" DIA.
4_ '' DIA
*Can be two or more rooms joined by ventilation grilles.
Duct
3"x3" SQ.
3"x3" SQ.
3"x4" SQ.
3"x4" SQ.
3"x5" SQ.
3"x5" SQ.
Max. Btuh
Input
30,000
35,000
40,000
45,000
50_00
60_00
*Unconfined Space
Min. Area In Sq. Ft.
8' Ceiling Height
250
B. All Air From Outdoors:
If confined space doesn't adjoin an unconfined space
(defined in EXAMPLE 1) then air must be provided from
outdoors or spaces open to outdoors such as attic or crawl
spaces.
Provide two permanent openings, one within 12 inches of
top, one within 12 inches of bottom of room connecting
directly, or by using ducts, with the outdoors or areas open
to outdoors.
If opening connects directly to, or within vertical duets,
the free area of each opening must be at least 1 square
inch per 4000 Btuh combined input of appliances in area.
m9--
188
219
281
312
375
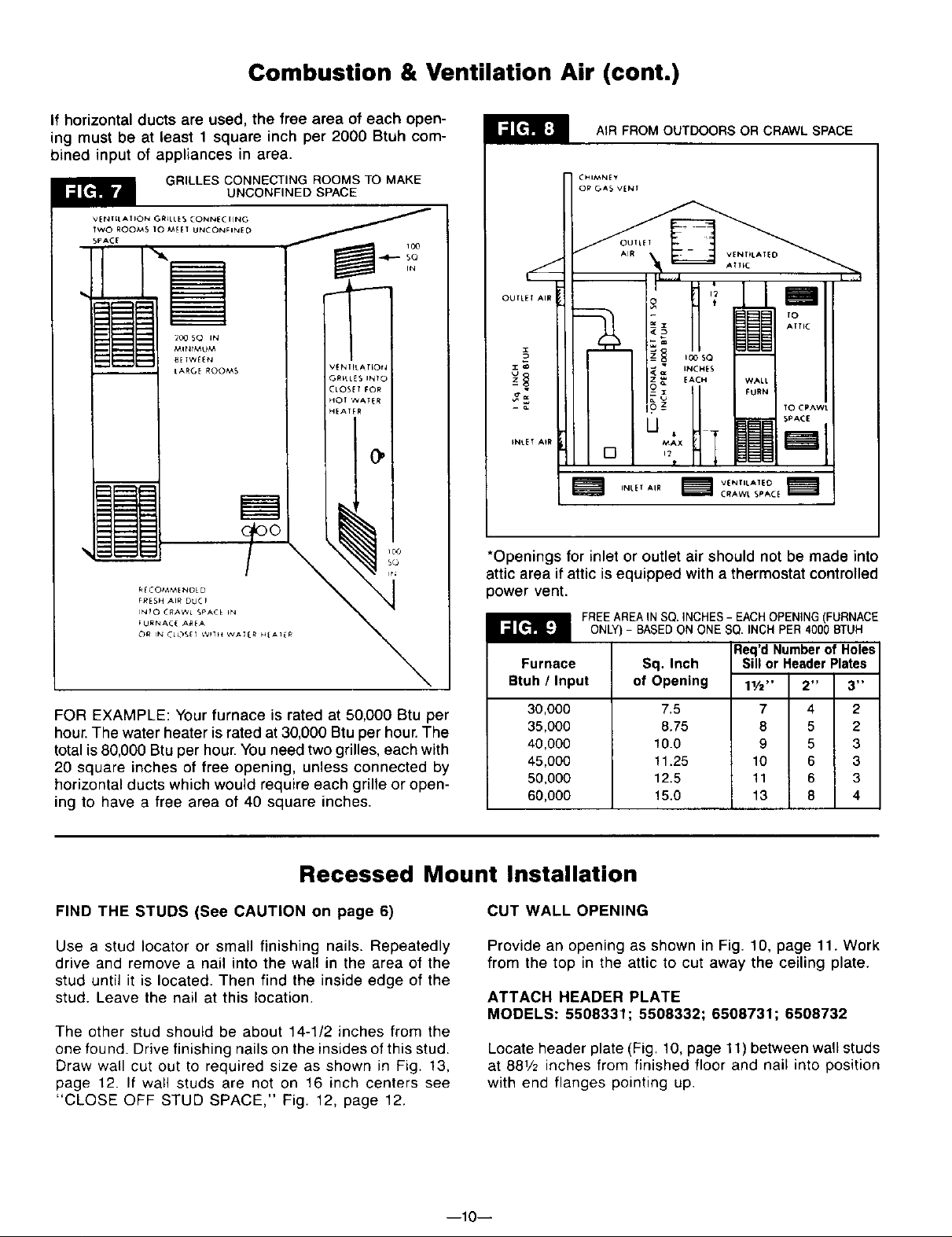
Combustion & Ventilation Air (cont.)
If horizontal ducts are used, the free area of each open-
ing must be at least 1 square inch per 2000 Btuh com-
bined input of appliances in area.
GRILLES CONNECTING ROOMS TO MAKE
UNCONFINED SPACE
FOR EXAMPLE: Your furnace is rated at 80,000 Btu per
hour. The water heater is rated at 30,000 Btu per hour. The
total is 80,000 Btu per hour. You need two grilles, each with
20 square inches of free opening, unless connected by
horizontal ducts which would require each grille or open-
ing to have a free area of 40 square inches.
Recessed Mount Installation
FIND THE STUDS (See CAUTION on page 6)
Use a stud Iocator or small finishing nails. Repeatedly
drive and remove a nail into the wall in the area of the
stud until it is located. Then find the inside edge of the
stud. Leave the nail at this location.
The other stud should be about 14-1/2 inches from the
one found. Drive finishing nails on the insides of this stud.
Draw wall cut out to required size as shown in Fig. 13,
page 12. If wall studs are not on 16 inch centers see
"CLOSE OFF STUD SPACE," Fig. 12, page 12.
*Openings for inlet or outlet air should not be made into
attic area if attic is equipped with a thermostat controlled
power vent.
FREEAREA IN SQ.INCHES - EACHOPENING (FURNACE
ONLY) - BASEDON ONE SQ. INCH PER 4000 8TUH
Furnace
Btuh / Input
30,000
35,000
40,000
45,000
50,000
60,O00
Sq, Inch Sill or Header Plates
of Opening 1_/2'' 2" 3"
7.5 7 4 2
8.75 8 5 2
10.0 9 5 3
11.25 10 6 3
12.5 11 6 3
15.0 13 8 4
Req'd Number of Holes
CUT WALL OPENING
Provide an opening as shown in Fig. 10, page 11. Work
from the top in the attic to cut away the ceiling plate.
ATTACH HEADER PLATE
MODELS: 5508331; 5508332; 6508731; 6508732
Locate header plate (Fig. 10, page 11) between wall studs
at 88V2 inches from finished floor and nail into position
with end flanges pointing up.
--10--
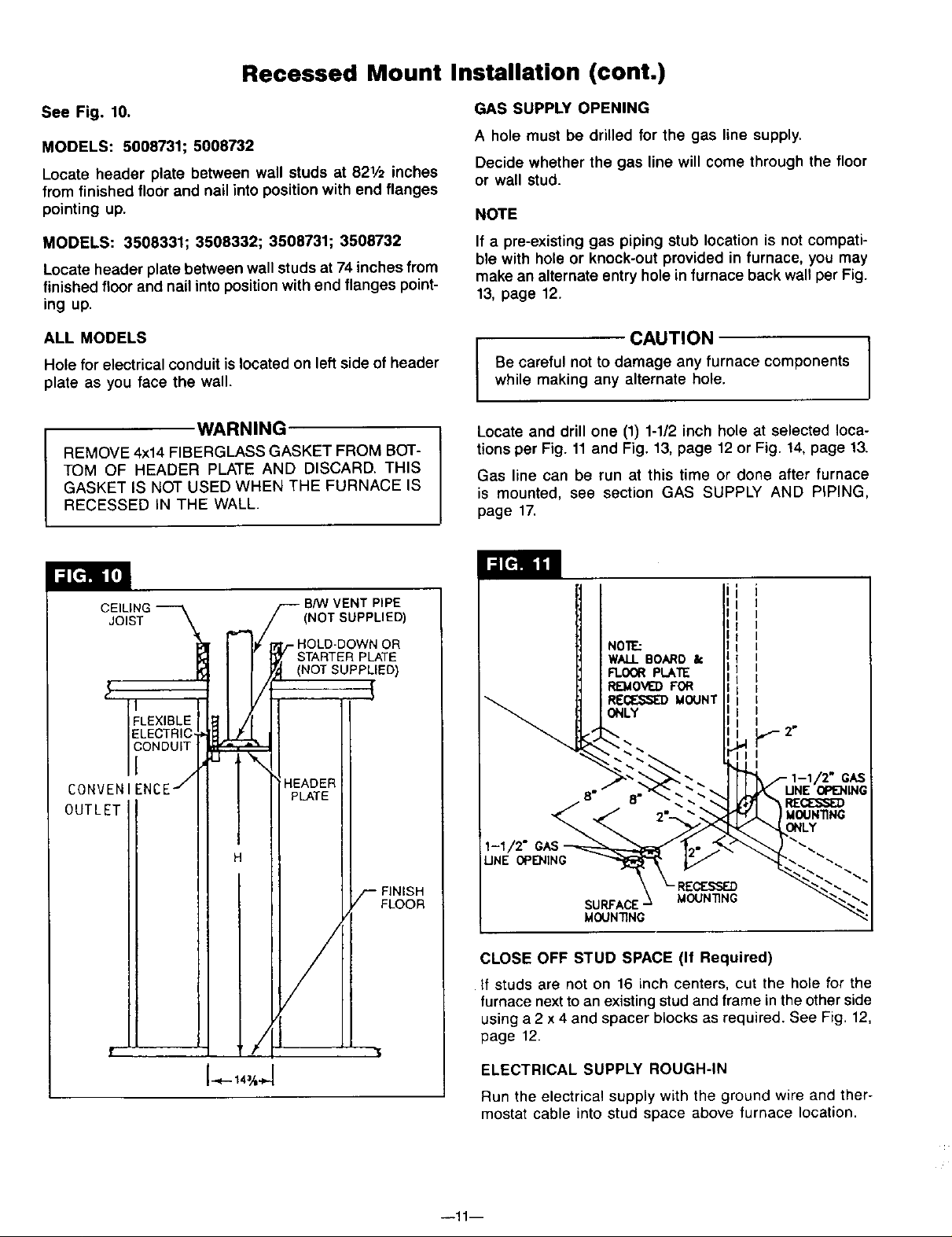
Recessed Mount Installation (cont.)
See Fig. 10.
MODELS: 5008731; 5008732
Locate header plate between wall studs at 821/2 inches
from finished floor and nail into position with end flanges
pointing up.
MODELS: 3508331; 3508332; 3508731; 3508732
Locate header plate between wall studs at 74 inches from
finished floor and nail intoposition with end flanges point-
ing up,
ALL MODELS
Hole for electrical conduit is located on left side of header
plate as you face the wall.
WARNING
REMOVE 4x14 FIBERGLASS GASKET FROM BOT-
TOM OF HEADER PLATE AND DISCARD. THIS
GASKET IS NOT USED WHEN THE FURNACE IS
RECESSED IN THE WALL.
GAS SUPPLY OPENING
A hole must be drilled for the gas line supply.
Decide whether the gas line will come through the floor
or wall stud.
NOTE
If a pre-existing gas piping stub location is not compati-
ble with hole or knock-out provided in furnace, you may
make an alternate entry hole in furnace back wall per Fig.
13, page 12.
CAUTION
Be careful not to damage any furnace components
while making any alternate hole.
Locate and drill one (1) 1-1/2 inch hole at selected loca-
tions per Fig. 11and Fig. 13, page 12 or Fig. 14, page !3.
Gas line can be run at this time or done after furnace
is mounted, see section GAS SUPPLY AND PIPING,
page 17.
F-
_LEXIBLE
ELECTRIC,
ONDUIT
CONVENI ENCE-_
OUTLET
f -- . j
B/W VENT PIPE
(NOT SUPPLIED)
7_r HOLD-DOWN OR
STARTER PLATE
_(NOT SUPPLIED)
/
N
HEADER
PLATE
/
/
,'- FINISH
FLOOR
N01_:
WALL BOARD &
FLOOR PLAI_
REMOVEDFOR
RECIE_ MOUNT
ONLY
2"
SURFACE _ MOUNTING
MOUNTING
CLOSE OFF STUD SPACE (If Required)
If studs are not on 16 inch centers, cut the hole for the
furnace next to an existing stud and frame in the other side
using a 2 x 4 and spacer blocks as required. See Fig. 12,
page 12.
ELECTRICAL SUPPLY ROUGH-IN
Run the electrical supply with the ground wire and ther-
mostat cable into stud space above furnace location.
--11 m
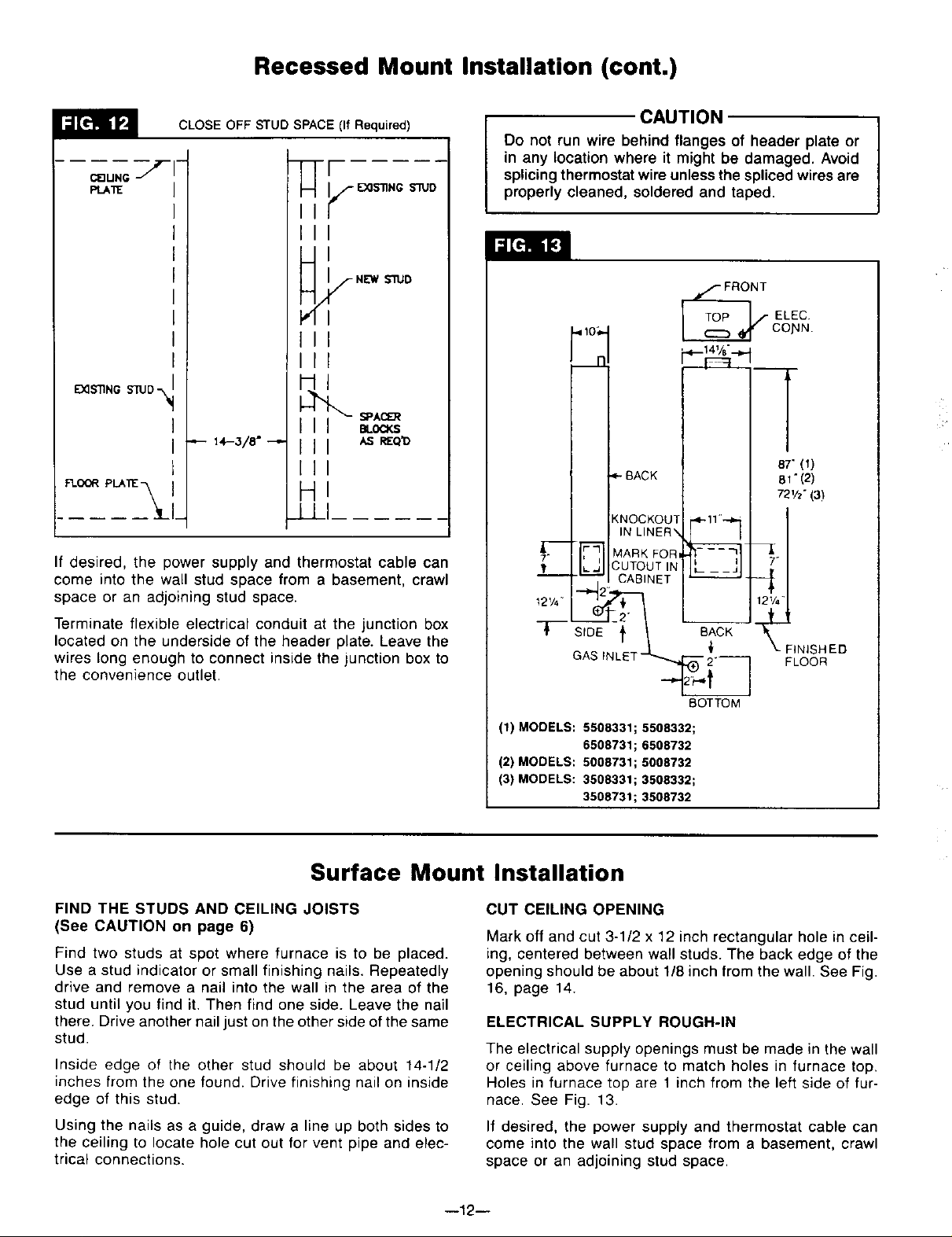
Recessed Mount Installation (cont.)
CLOSE OFF STUD SPACE (If Required)
7
PLA'I_
F I_]b-I1NG b-lUD
Ill
II NEW S'IUD
111
III
E_S71NG S31JDt
]
I -- 14-_/8"_-
1
..... LI-1 r-!U-I......
If desired, the power supply and thermostat cable can
come into the wall stud space from a basement, crawl
space or an adjoining stud space.
Terminate flexible electrical conduit at the junction box
located on the underside of the header plate. Leave the
wires long enough to connect inside the junction box to
the convenience outlet.
%
SPACER
III
H I
CAUTION
Do not run wire behind flanges of header plate or
in any location where it might be damaged. Avoid
splicing thermostat wire unlessthe spliced wires are
properly cleaned, soldered and taped.
.,_,- FRONT
TOP ELEC
_,/" CONN.
[41C ",+--141/6"-_-
BOTTOM
(1) MODELS: 5508331; 5508332;
6508731 ; 6508732
(2) MODELS: 5005731; 5008732
(3) MODELS: 3508331; 3508332;
3508731; 3508732
Surface Mount Installation
FIND THE STUDS AND CEILING JOISTS
(See CAUTION on page 6)
Find two studs at spot where furnace is to be placed.
Use a stud indicator or small finishing nails. Repeatedly
drive and remove a nail into the wall in the area of the
stud until you find it. Then find one side. Leave the nail
there. Drive another nail just on the other side of the same
stud.
Inside edge of the other stud should be about 14-1/2
inches from the one found. Drive finishing nail on inside
edge of this stud.
Using the nails as a guide, draw a line up both sides to
the ceiling to locate hole cut out for vent pipe and elec-
trical connections.
CUT CEILING OPENING
Mark off and cut 3-1/2 x 12 inch rectangular hole in ceil-
ing, centered between wall studs. The back edge of the
opening should be about 1/8 inch from the wall. See Fig.
16, page 14.
ELECTRICAL SUPPLY ROUGH-IN
The electrical supply openings must be made in the wall
or ceiling above furnace to match holes in furnace top.
Holes in furnace top are 1 inch from the left side of fur-
nace. See Fig. 13.
If desired, the power supply and thermostat cable can
come into the wall stud space from a basement, crawl
space or an adjoining stud space.
--12--
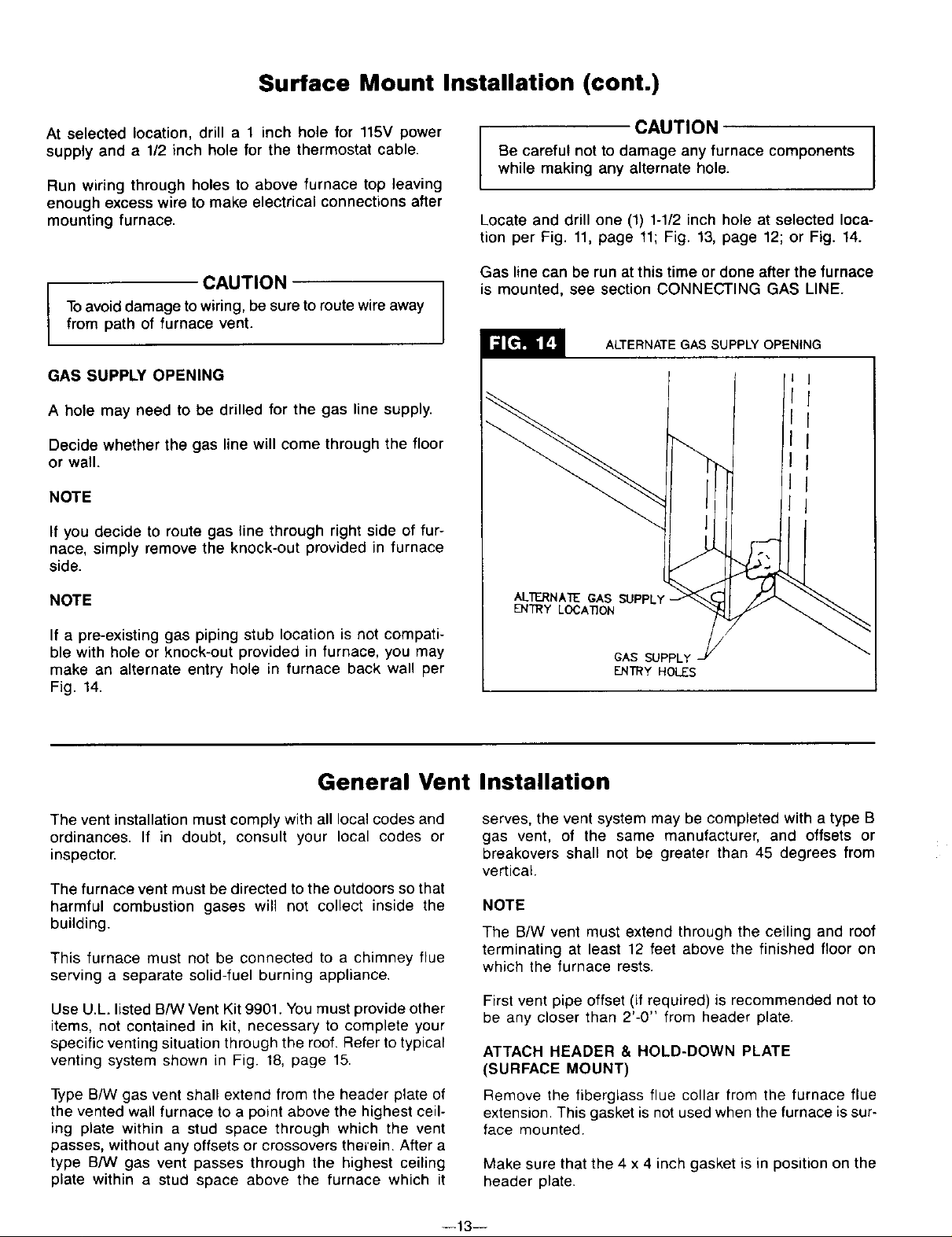
Surface Mount Installation (cont.)
At selected location, drill a 1 inch hole for 115V power
supply and a 1/2 inch hole for the thermostat cable.
Run wiring through holes to above furnace top leaving
enough excess wire to make electrical connections after
mounting furnace.
CAUTION
Toavoiddamage towiring, be sure to route wire away
from path of furnace vent.
GAS SUPPLY OPENING
A hole may need to be drilled for the gas line supply.
Decide whether the gas line will come through the floor
or wall.
NOTE
If you decide to route gas line through right side of fur-
nace, simply remove the knock-out provided in furnace
side.
CAUTION
while making any alternate hole.
I e careful not to damage any furnace components
Locate and drill one (1) 1-1/2 inch hole at selected loca-
tion per Fig. 11, page 11; Fig. 13, page 12; or Fig. 14.
Gas line can be run at this time or done after the furnace
is mounted, see section CONNECTING GAS LINE.
ALTERNATE GAS SUPPLY OPENING
r;
NOTE
If a pre-existing gas piping stub location is not compati-
ble with hole or knock-out provided in furnace, you may
make an alternate entry hole in furnace back wall per
Fig. 14.
General Vent Installation
The vent installation must comply with all local codes and
ordinances. If in doubt, consult your local codes or
inspector.
The furnace vent must be directed to the outdoors so that
harmful combustion gases will not collect inside the
building.
This furnace must not be connected to a chimney flue
serving a separate solid-fuel burning appliance.
Use U.L. listed B/W Vent Kit 9901. You must provide other
items, not contained in kit, necessary to complete your
specific venting situation through the roof. Refer to typical
venting system shown in Fig. 18, page 15.
Type B/W gas vent shall extend from the header plate of
the vented wall furnace to a point above the highest ceil-
ing plate within a stud space through which the vent
passes, without any offsets or crossovers thei'ein. After a
type B/W gas vent passes through the highest ceiling
plate within a stud space above the furnace which it
ALTERNATE GAS SUPPLy---"%._I )--'t
ENTRy LOCA]10N
?
GAS SUPPL_
ENTRy HOLES
serves, the vent system may be completed with a type B
gas vent, of the same manufacturer, and offsets or
breakovers shall not be greater than 45 degrees from
vertical.
NOTE
The B/W vent must extend through the ceiling and roof
terminating at least 12 feet above the finished floor on
which the furnace rests.
First vent pipe offset (if required) is recommended not to
be any closer than 2'-0" from header plate.
ATTACH HEADER & HOLD-DOWN PLATE
(SURFACE MOUNT)
Remove the fiberglass flue collar from the furnace flue
extension. This gasket is not used when the furnace is sur-
face mounted.
Make sure that the 4 x 4 inch gasket is in position on the
header plate.
--13--
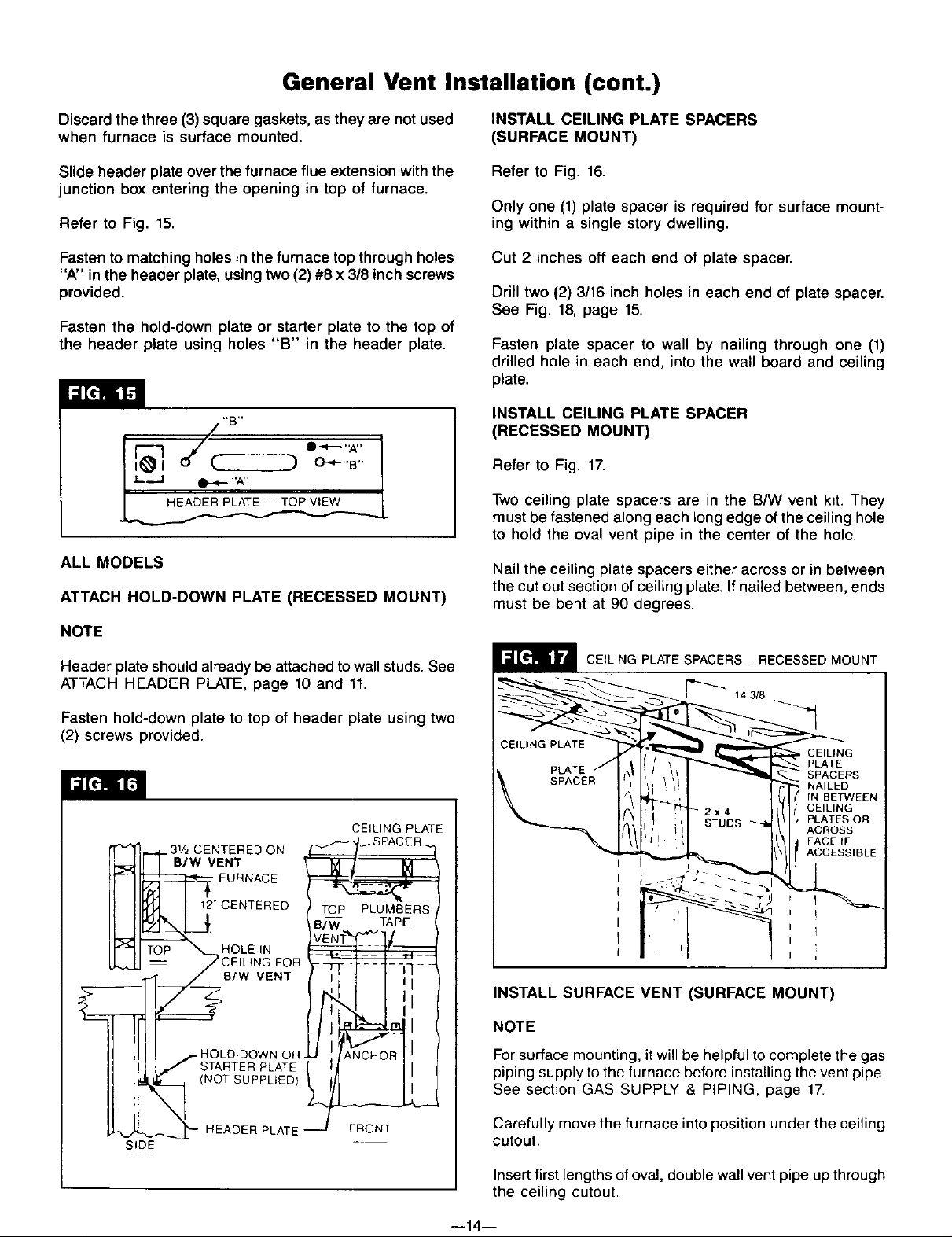
General Vent Installation (cont.)
Discard the three (3) square gaskets, as they are not used
when furnace is surface mounted.
Slide header plate over the furnace flue extension with the
junction box entering the opening in top of furnace.
Refer to Fig. 15.
Fasten to matching holes in the furnace top through holes
"A" in the header plate, using two (2) #8 x 3/8 inch screws
provided.
Fasten the hold-down plate or starter plate to the top of
the header plate using holes "B" in the header plate.
j ,,g,,
ALL MODELS
ATTACH HOLD-DOWN PLATE (RECESSED MOUNT)
NOTE
INSTALL CEILING PLATE SPACERS
(SURFACE MOUNT)
Refer to Fig. 16.
Only one (1) plate spacer is required for surface mount-
ing within a single story dwelling.
Cut 2 inches off each end of plate spacer.
Drill two (2) 3/16 inch holes in each end of plate spacer.
See Fig. 18, page 15.
Fasten plate spacer to wall by nailing through one (1)
drilled hole in each end, into the wall board and ceiling
plate.
INSTALL CEILING PLATE SPACER
(RECESSED MOUNT)
Refer to Fig. 17.
Two ceiling plate spacers are in the B/W vent kit. They
mustbe fastened along each longedge of the ceiling hole
to hold the oval vent pipe in the center of the hole.
Nail the ceiling plate spacers either across or in between
the cut out section of ceiling plate. If nailed between, ends
must be bent at 90 degrees.
Header plate should already be attached to wall studs. See
ATTACH HEADER PLATE, page 10 and 11.
Fasten hold-down plate to top of header plate using two
(2) screws provided.
CEILING PLATE
"_" r,_4_3V2 CENTERED ON
!1 a/w VENT
TOP ___ HOLE IN
HOLD-DOWN OR
RTER PLATE
r_ (NOT SUPPLIED)
FRONT
SIDE
HEADER PLATE
CEILING PLATE SPACERS - RECESSED MOUNT
_ 14 318
INSTALL SURFACE VENT (SURFACE MOUNT)
NOTE
For surface mounting, it willbe helpful to complete the gas
piping supply to the furnace before installing the vent pipe.
See section GAS SUPPLY & PiPiNG, page 17.
Carefully move the furnace into position under the ceiling
cutout.
Insert first lengths of oval, double wall vent pipe up through
the ceiling cutout.
--14 m
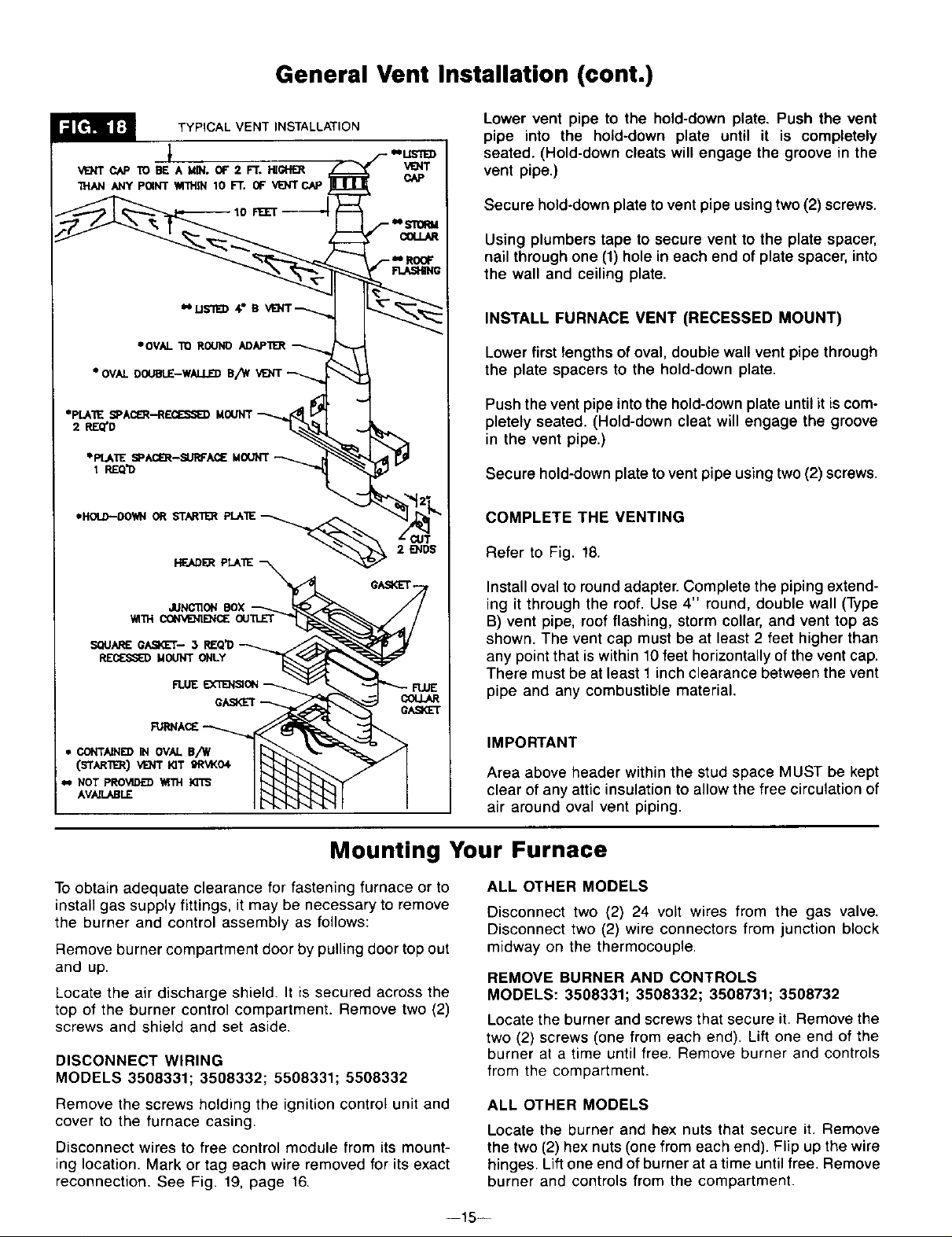
General Vent Installation (cont.)
TYPICAL VENT INSTALLATION
1
Vl_IT CAP "rOBE AMINo OF2 FT. HIGHER
THANANYpOINT_ 10 FT. OF _rr C_
HEADER PLA1E
2 E_DS
FLUE
COLLAR
QAS_£T
Lower vent pipe to the hold-down plate. Push the vent
pipe into the hold-down plate until it is completely
seated. (Hold-down cleats will engage the groove in the
vent pipe.)
Secure hold-down plate to vent pipe using two (2) screws.
Using plumbers tape to secure vent to the plate spacer,
nail through one (1)hole in each end of plate spacer, into
the wall and ceiling plate.
INSTALL FURNACE VENT (RECESSED MOUNT)
Lower first lengths of oval, double wall vent pipe through
the plate spacers to the hold-down plate.
Push the vent pipe into the hold-down plate until it is com-
pletely seated. (Hold-down cleat will engage the groove
in the vent pipe.)
Secure hold-down plate to vent pipe using two (2) screws.
COMPLETE THE VENTING
Refer to Fig. 18.
Install oval to round adapter. Complete the piping extend-
ing it through the roof. Use 4" round, double wall (Type
B) vent pipe, roof flashing, storm collar, and vent top as
shown. The vent cap must be at least 2 feet higher than
any point that is within 10 feet horizontally of the vent cap.
There must be at least 1 inch clearance between the vent
pipe and any combustible material.
Mounting Your Furnace
To obtain adequate clearance for fastening furnace or to
install gas supply fittings, it may be necessary to remove
the burner and control assembly as follows:
Remove burner compartment door by pulling door top out
and up.
Locate the air discharge shield. It is secured across the
top of the burner control compartment. Remove two (2)
screws and shield and set aside.
DISCONNECT WIRING
MODELS 3508331; 3508332; 5508331; 5508332
Remove the screws holding the ignition control unit and
cover to the furnace casing.
Disconnect wires to free control module from its mount-
ing location. Mark or tag each wire removed for its exact
reconnection. See Fig, 19, page 16,
IMPORTANT
Area above header within the stud space MUST be kept
clear of any attic insulation to allow the free circulation of
air around oval vent piping.
ALL OTHER MODELS
Disconnect two (2) 24 volt wires from the gas valve.
Disconnect two (2) wire connectors from junction block
midway on the thermocouple.
REMOVE BURNER AND CONTROLS
MODELS: 3508331; 3508332; 3508731; 3508732
Locate the burner and screwsthat secure it. Remove the
two (2) screws (one from each end). Lift one end of the
burner at a time until free. Remove burner and controls
from the compartment.
ALL OTHER MODELS
Locate the burner and hex nuts that secure it. Remove
the two (2) hex nuts (one from each end). Flip up the wire
hinges. Lift one end of burner at a time until free. Remove
burner and controls from the compartment.
--15--

Mounting Your Furnace (cont.)
Straighten the furnace by pushing furnace bottom intothe
stud space.
IMPORTANT
AFTER FURNACE HAS BEEN PLACED IN POSITION,
MAKE SURE THE GASKETS ARE PRESSING AGAINST
THE FURNACE TOP TO ELIMINATE AIR LEAKS.
FASTEN FURNACE BOTTOM
(SURFACE AND RECESSED MOUNT)
24V
PV
SEt6
24V
GND
lnV
GND
WILLIAMS IGNITION CONTROL
PART NUMBER P321910
LA707-01 .DWG
POSITION FURNACE (RECESSED MOUNT ONLY)
NOTE
If your furnace is surface mounted, your mounting was
started during VENT INSTALLATION, page 13.To complete
furnace mounting, go on to FASTEN FURNACE BOTTOM
on this page.
ALL MODELS
Make sure that the flue collar gasket, Fig. 18, page 15, is
in place over the flue extension. Check to see if header
plate gaskets are in place.
NOTE
Fasteners are not furnished because of different require-
ments of various types of wall construction.
Fasten furnace to floor through holes provided in furnace
bottom. If you have concrete flooring, use an alternate
fastening method. See Fig. 20.
If burner and control assembly were removed, replace
them by reversing "DISCONNECT WIRING" and
"REMOVE BURNER AND CONTROLS" sections on
page 15.
FURNACE MOUNTING
- METAL ANOH(_
TOP FASTENING
II
I
I
Hold the furnace at a slight angle (top closer to the wall
than bottom) with the flue extension centered under the
oval hole in the header plate.
NOTE
Electrical wiring should already be routed to the header
plate. If not, see sections on ELECTRICAL SUPPLY
ROUGH-IN, page 12.
Place three (3) square gaskets over the junction box. See
Fig. 18, page 15.
ALL MODELS
Lift furnace up so that the flue extension enters the oval
hole in the header plate.
NOTE: DO NOT U_ BOTTOM DOOR _ FOR MOUNTING
--16--

Mounting Your Furnace (cont.)
IMPORTANT
TO PREVENT DAMAGE TO WIRING, MAKE SURE
NOT TO PINCH THE WIRES BETWEEN FURNACE
COMPONENTS. KEEP THEM ROUTED AWAY FROM
THE BURNER.
Resecure the air discharge shield across the top of the
burner and controls compartment, Small leg of "L" shape
must be positioned toward floor, pointing away from front
of furnace.
over the back flange of furnace top and screwing to wall.
See Fig. 20, page 16.
FASTEN FURNACE TOP (RECESSED MOUNTING)
Fasten furnace top by drilling two (2) holes through the
side flanges of furnace top and securing with two (2)
screws or nails into the wall studs. See Fig. 20, page 16.
FASTEN FURNACE TOP (SURFACE MOUNTING)
Fasten furnace top to wall using two (2) metal anchors
(packed in plastic bag with thermostat) by placing them
Gas Supply and Piping
Gas control valve, within the furnace, is shipped with a
seal over gas inlet tapping. Do not remove seal until ready
to connect piping.
WARNING
DANGER OF PROPERTY DAMAGE,
BODILY INJURY OR DEATH.
MAKE SURE THE FURNACE IS EQUIPPED TO
OPERATE ON THE TYPE OF GAS AVAILABLE.
MODELS DESIGNATED AS NATURAL GAS ARE TO
BE USED WITH NATURAL GAS ONLY, FURNACE
DESIGNATED FOR USE WITH LIQUIFIED
PETROLEUM (L.P) GAS HAVE ORIFICES SIZED
FOR COMMERCIALLY PURE PROPANE GAS,
THEY CAN NOT BE USED WITH BUTANE OR A
MIXTURE OF BUTANE AND PROPANE.
CAUTION
Becareful notto damage furnace components or wir-
ing when drilling holes,
GAS PIPING
The gas supply line must be of adequate size to handle
the BTU/HR requirements and length of the run for the
unit being installed.
Determine the minimum pipe size from Fig. 23, page 18,
basing the length of the run from the gas meter or source
to the unit.
DROP
I PIPED CR0UN0 JOINT
SUPPLy
i_ I GAS aN,0N
GAS SUPPLY
For Natural gas, the minimum inlet gas supply pressure
for the purpose of input adjustment is 5" water column.
The Maximum inlet gas supply pressure is T' water
column.
For L.E gas, the minimum inlet gas supply pressure for
the purpose of input adjustment is 11" water column. The
maximum inlet gas supply pressure is 13" water column.
Gas pressure and input to the burners must not exceed
the rated input and pressure shown on the rating plate. On
Naturel Gas the manifold pressure should be 4 inches
water column. The manifold pressure should be 10.5 inch-
es water column for L.P. Gas. See page 32 for operation
above 2000 feet altitude Office change may be required to
suit gas supplied. Check with your local gas supplier.
ORIFICE SIZES
Furnace Technical Information, page 32, shows the
correct orifice sizes for the different input ratings when
using Natural or L.P Gas.
tlANUAL SHUT OFF
VALVE
DF(Op
--17--

Gas Supply and Piping (cont.)
CHECKING THE GAS PIPING
PROPER PIPING PRACTICE
2 IMPERFECT CONTRO L USE MODERATE AMOUNT OF DOPE
THREADS _
THREAD PIPE RIGHT LENGTH LEAVE 2 END THREADS [IARE "
All piping must comply with local codes and ordinances
or with the National Fuel Gas Code (ANSI Z223.1),
whichever applies. In Canada: Follow CAN 1-B149 Installa-
tion Code.
Refer to Fig. 21, page 17,for the general layout at the unit.
It shows the basic fittings needed.
The following rules apply:
1. Use new, properly reamed pipe free from chips such
as steel or black iron pipe and fittings or other
approved by local codes.
2. Do not thread pipe too far. Valve distortion or mal-
function may result from excess pipe within control.
Apply moderate amount of good quality dope to pipe
only, leaving 2 end threads bare. If LP Gas installation,
use compound resistant to action of liquified petroleum
gases.
3. Use ground joint unions.
4. Install a drip leg to trap dirt and moisture before it can
enter the gas valve. Drip leg must be a minimum of 3
inches long.
5. Install a manual shut-off valve.
6. Provide a 1/8 NPT test gauge connection immediately
before the gas supply connection to the furnace.
GAS CONNECTION
If installation is for L.R Gas, have L.R installer use two-
stage regulation and make all connections from storage
tank to furnace.
Use two pipe wrenches when making the connection to
the valve to prevent turning or damage to gas valve.
Connection between manual shutoff valve and burner con-
trol assembly can be made with an A.G.A./C.G.A. design
certified flexible connector if allowed by local codes. Drip
leg and ground joint union are still required.
Tighten all joints securely.
Test all piping for leaks. When checking gas piping to the
furnace with gas pressure less than 1/2 PSI, shut off
manual gas valve for the furnace. If gas piping is to be
checked with the pressure at or above 1/2 PSI, the fur-
nace and manual shut off valve must be disconnected dur-
ing testing. (SEE WARNING BELOW.) Apply soapsuds (or
a liquid detergent) to each joint. Bubbles forming indicates
a leak. Correct even the slightest leak at once.
GAS PIPE SIZES
NATURAL GAS
PIPE CAPACITY - BTU PER HOUR
(INCLUDES FITTINGS)
PIPE SIZE
LENGTH OF
PIPE - FEET 1/2 inch 3/4 inch 1 inch
20 92,000 190,000 350,000
40 63,000 130,000 245,000
60 50,000 105,000 195,000
L.P. GAS
PIPE CAPACITY - BTU PER HOUR
(INCLUDES FITTINGS)
LENGTH OF
PIPE - FEET 1/2 inch 3/4 inch 1 inch
20 189,000 393,000 732,000
40 129,000 267,000 504,000
60 103,000 217,000 409,000
WARNING
DANGER OF PROPERTY DAMAGE,
BODILY INJURY OR DEATH.
NEVER USE A MATCH OR OPEN FLAME TO TEST
FOR LEAKS. NEVER EXCEED SPECIFIED
PRESSURES FOR TESTING. HIGH PRESSURES
MAY DAMAGE THE GAS VALVE AND CAUSE
OVER-FIRING WHICH MAY RESULT IN HEAT
EXCHANGER FAILURE. LIQUID PETROLEUM
(L.P.) IS HEAVIER THAN AIR AND IT WILL SETTLE
IN ANY LOW AREA, INCLUDING OPEN DEPRES-
SIONS AND IT WILL REMAIN THERE UNLESS
AREA IS VENTILATED.
NEVER ATTEMPT STARTUP OF UNIT BEFORE
THOROUGHLY VENTILATING AREA.
Electrical Wiring
All electrical work must conform to your local codes and
ordinances or in their absence, with National Electrical
Code, ANSI/NFPA 70. If you are not familiar with wiring
codes, in general, have a competent electrician do this
job. In Canada: Follow C22.1, Canadian Electrical Code.
ELECTRICAL CONNECTION
REMOVE FAN SHROUD
Take out four screws holding fan shroud to side flanges
of cabinet and remove shroud. See Fig. 1, page 5.
m18m

WARNING
DANGER OF PROPERTY DAMAGE,
BODILY INJURY OR DEATH.
TURN OFF ELECTRIC POWER AT FUSE BOX
OR SERVICE PANEL BEFORE MAKING ANY
ELECTRICAL CONNECTIONS.
INSULATE WHERE NECESSARY.
ALL LINE VOLTAGE AND GROUND CONNEC-
TIONS MUST BE COMPLETED BEFORE
ELECTRICAL POWER IS RESTORED.
LOW VOLTAGE CONNECTIONS
CAUTION
The Heat Anticipator WILL BURN OUT if 24 voltsare
applied directly to thermostat by shorting out the gas
valve or primary control during testing or by incorrect
wiring.
WALL THERMOSTAT WIRING
ELECTRICAL POWER SUPPLY
A branch circuit including this furnace must not exceed
15 Amperes, or run a separate 115V, 60 Hz, 15 Ampere
circuit from a separate circuit breaker or fuse in your ser-
vice entrance panel to the furnace junction box. Do not
run supply wires inside the furnace cabinet, except from
the top of cabinet down to junction box.
JUNCTION BOX
CAUTION
Be careful not to damage the fan blade when mak- 1
ing the 115V connection to the convenience outlet.
115V supply wiring connection is made within the upper
left corner of the furnace cabinet.
Locate 115V plug and push into the convenience outlet
attached to the bottom of header plate. (It protrudes
through the rectangular opening in the furnace top.)
Run thermostat wire to the furnace.
Avoidsplicingthermostat wire unlessthe spliced wires are
properly cleaned, soldered and taped.
Connect thermostat to two wires marked "Thermostat"
extending from top of furnace, using two wire nuts pro-
vided. See Wiring Diagrams, pages 37 or 38.
CAUTION
Do not connect 115V service line to the gas control
valve or the wall thermostat.
]
I
ALL MODELS
Reinstall fan shroud to furnace front. Slots in fan shroud
allow up/down adjustment. Make sure the fan blade spins
freely. Tighten screws securely.
Replace top front panel and secure with thumbscrew.
Refer to paragraph covering GAS AND ELECTRICAL
SUPPLY OPENINGS, page 13. Follow Wiring Diagrams,
pages 37 or 38.
If you have any doubt regarding electrical hookup, or com-
pliance with code or ordinance, consult your electrical in-
spector or a licensed electrician.
GROUNDING
A ground lug is installed for the ground connection. Use
a copper conductor (#14 AWG) from the unit to a ground-
ed connection in the electric service panel or a properly
driven and electrically grounded ground rod.
COMPLETE WIRING DIAGRAMS ON PAGES 37 AND 38.
I19--

Thermostat Installation
1. If an old thermostat is being replaced and is in a
satisfactory location and the wiring appears to be
in good condition, use existing wiring. If in doubt, use
new wire.
2. If a new location is chosen or if this is a new installa-
tion, thermostat cable must first be run to the location
selected. All wiring must agree with local codes and
ordinances. These instructions cover bringing the wire
down from the attic but it can be run from a basement
or crawl space using similar methods. Refer to Fig. 24.
3. Before drilling hole in wall at selected location, drive
a small finishing nail through the ceiling in the corner
of the wall and ceiling above the thermostat location.
Pull the nail out and push a small stiff wire through the
hole so it can be found in the attic. Drill a 1/2 inch hole
through the ceiling wall plate.
4. Probe for obstructions in the partition. Then drill a 1/2
inch hole through wall at selected location for
thermostat.
5. From the attic, feed the thermostat cable or a stiff wire
through wall until even with thermostat location.
6. Snag thermostat cable through hole and pull cable
through hole in wall so that 6 inches of cable protrudes.
7. Route cable to wall furnace.
ROUTE THERMOSTAT CABLE
Ske,AL t
FINISH
NAIL TO
LOCATE
HEADER
THERMOSIAT
CABLE
STIFF WIRE
TO SNAG
CABLE
MOUNTING THE THERMOSTAT
1. To remove thermostat cover, squeeze both sides and
lift. See Fig. 25.
2. 'Connect thermostat wires to the terminal screws on the
thermostat base.
3. Push any excess wire back through hole in wall and
plug hole with insulation to prevent drafts from affect-
ing thermostat operation.
4. Being sure to level thermostat for best appearance,
fasten thermostat base to wall through mounting holes
with screws provided.
5. Replace the thermostat cover.
THERMOSTAT HEAT ANTICIPATOR
SET THE THERMOSTAT HEAT ANTICIPATOR
A simple method of setting the heat anticipator in a 24-volt
thermostat (without an A.C. ammeter) is to first read the
label on the gas control valve and match its rating.
Example: If the ampere draw for the valve is .5 amps,
set thermostat heat anticipator at the same
setting (.5). (Fig. 26, page 21.)
ADJUST THERMOSTAT ANTICIPATOR
Many factors affect this setting -- room size, length of ther-
mostat wire, thermostat location, etc. Additional small
adjustments to increase or decrease heating cycles (4-6
per hour typical) may be required. If an amp meter is
available, see instructions supplied with thermostat.
SQUEEZE RR_4LY
SOl1"1SIDES
AND UFT 110
R£_IO_,_COVER
t,/_r/...oa.l=t_
NOTE
Use heavier wire size if more than 20 ft. of wire is required.
--20--

Thermostat Installation (ton't)
MV"--X.-_J_ -LONGER
HEATAN 0,P TOR
SETTING '_ u_.-_,._m
For longer "ON" time, move anticipator clockwise.
For shorter "ON" time, move anticipator counterclockwise.
.---,.- 1.0 .-'-- CYCLE
Optional Accessory Installation
NOTE
Refer to installation instructions packed in the thermostat
carton if you have any doubt about the above procedures.
When all is adjusted properly, the furnace burner should
shut off slightly before the desired room temperature is
reached. The stored heat in the appliance is enough to
bring room temperature up to desired level. The heat
anticipator thus makes it possible to maintain very close
temperature control.
SIDE OUTLET NO. 6701
REAR OUTLET NO. 6801
SHORT REAR OUTLET NO. 6802
CAUTION
Use only Boots and Grilles provided by the
manufacturer.
CLEARANCES
IMPORTANT
Carefully follow all measurements and clearances given
to ensure proper installation.
When SiDE OUTLET 6701 is used, the furnace casing
must be exactly 4 inches from an adjacent side wall
(except may be 3/4" minimum when 1-WAY FRONT
DIFFUSING GRILLE is used). See Figs. 28 and 29,
page 22.
CUT WALL OPENING(S)
Make an opening(s) in the wall(s) for a Side and/or a Rear
Outlet Register. See Fig. 27.
CUT WALL OPENING
SIDE OUTLET REAR OUTLET
II . II
FURNACE "BACK"
AGAINST WALL _
°IIs'_os/ II
a-1/4" L_
ll-s/8"
Ill I IR,-v,-
.-s/s'! I II
l II 11
F1NI_tlE9FLOOR,-J_
RNISHED FL_
When REAR OUTLET 6801 or SHORT REAR OUTLET
6802 are used, the furnace casing must be a minimum
of 12 inches from an adjacent side wall. See Figs. 3D and
3F, page 7.
CUT CASING OPENING(S)
Before setting the furnace into position, cut a 5 x 7 inch
rectangular opening for Side Register, or 7 x 11 inch open-
ing for a Rear Outlet Register where marked on the fur-
nace casing. Cut carefully as edges must be straight and
smooth. See Fig. 13, page 12.
--21--
/1/1 m '"
3/4" MIN WHEN OPTIONAl, "J_ -
6704 ONE-WAY 3/4"
FRONT DIFFUSING
GRILLE IS USED

Optional Accessory Installation (cont.)
INSTALL PLASTERGROUNDS
Install Plastergrounds as shown in Figs. 29 and 30.
Flanges of Plastergrounds extend the normal thickness
of plaster. If "DRYWALL" or other thin material, flanges
must be trimmed off flush with wall surface.
REAR PLASTER GROUND CENTERS EXACTLY
ON THE BACK OF THE HEATER
- PLASTER GROUND
t
1/4 ROUND METAL
TRiM FILLER
Press Inner Boot against furnace Inner Liner, mark and
cut off flush with the wall surface.
Fasten Outer Bootsecurely to furnace casing with screws
provided.
EXACTLY 41/2 FROM BACK OF THE HEATER
" GROUND
._ ._ PLASTER
15_/4"
FLOOR
MOUNTING
Refer to Fig. 31.
BEFORE placing the furnace into position, place Out Boot
against the furnace casing with inside of flanges exactly
on edges of hole in casing. Mark hole locations on cas-
ing through the holes in Out Boot flanges
Drill #33 holes in casing at marked locations.
Remove knockout plate and knockouts for screws from
Inner Liner.
SIDE REGISTER ONLY
Secure a 1 x 1 wood strip (not included in this kit) to wall
surface next to side outlet as a backup for metal filler strips.
Fasten metal filler strips to side of furnace casing with front
surface exactly opposite front of wood backup strip.
SIDE AND REAR OUTLET REGISTERS
Place furnace in position.
With furnace in position, pass Outer Boot through Plaster-
grounds, holding it firmly against furnace casing. Mark and
cut off the end of the Outer Boot flush with the wall surface.
SIDE OUTLET ONLY
Positioninner Bootagainst furnace Inner Liner and fasten
securely through all holes with screws provided.
REAR OUTLET ONLY
Ptace Inner Boot in position and fasten with screws along
the top and bottom edges only. Place Damper Assembly
inside Inner Boot and fasten with one (1)screw on each
side. Thread chain through key hole in clip on Outer Grille
and attach the Bell end.
SIDE AND REAR OUTLETS
Place Outlet Grille into position, drill through the wall
material and Plasterground with a #33 drill bit, using
the holes in grille as a template and secure with screws
provided.
VENT ENCLOSURE KIT INSTALLATION
(SURFACE MOUNT ONLY)
Refer to Fig. 32, page 23.
Cut Side Panels to fit between the top of furnace casing
and ceiling.
Fasten Side Panels to wall parallel to furnace casing sides.
Cut Front Panel height to fit. Note that the bottom edge of
Front Panel is notched to fit into the furnace casing recess.
Fasten Front Panel to Side Panels with screws provided.
SIDE CASING GRILLE KIT NO. 6702
See clearances Fig. 33, page 23.
Locate marked opening(s) on furnace casing. Mark
and cut an opening 1 inch wider than opening already
marked (1/2 inch larger on all four sides). See Fig. 13,
page 12.
Remove knockout plate and knockouts for screws from fur-
nace inner liner.
--22--

Optional Accessory Installation (cont.)
Fasten Boot to Inner Liner with screws provided. NOTE
Using holes in grille as a template, drill two (2) #33 holes Quarter-round wood molding may be used for trim if
in out casing and fasten securely with screws provided, desired, which may be painted to match the wall.
CEILING
C
VENT
ENCLOSURE
FRONT
OPTIONA _L_I h_OPTIONAL
OUTLET _ II_ 0UTLET
KIT 6702 _I _'" KIT 6702
o(Nill
JOIST
B/W
VENT
:VENT
ENCLOSURE
!ILING
LOWER DOOR CASING
OPTIONAL TWO-WAY DIFFUSING GRILLE 6703
_OPTIONAL REAR
i
DISCHARGE
o
T W O -WAY
OIFFU SING--_
GRILLE KIT 6703
'll \\k-,2
--4
2-WAY FRONT DIFFUSING GRILLE KIT NO. 6703
Refer to Fig. 34.
CAUTION
For use only in conjunction with a front outlet when
the furnace is spaced at least 12 inches from an in-
tersection wall (see Fig. 35).
Metal clips on backside of grille snap into side louvers of
front warm air outlet. Adjust clips with pliers if necessary.
Grille may also be attached with sheet metal screws.
1-WAY FRONT DIFFUSING GRILLE KIT NO. 6704
Follow instructions for 2-WAY FRONT DIFFUSING GRILLE
6703 above, except furnace clearance to an adjacent wall
must be 3/4 inch minimum. See Fig. 28, page 21.
TRIM STRIP KIT NO. 4701
When desired, optional Trim Strip Kit may be used to cover
the crack between furnace and wall. See Figs. 36 and 37.
Place strips tight against furnace with other edge against
wall surface and fasten to wall with escutcheon pins pro-
vided. Cut off trim strips to fit each furnace as required.
KIT 470R_
OPTIONAL TRIM ST
WALL WITH FASTENERS PROVIDED
VENT COVER j
,==..
]
TRIM
MOULDING
(OPTIONAL}
INSTALL VENT COVER (PROVIDED)
(RECESSED MOUNT ONLY)
Place Vent Cover on top of furnace, see Fig. 37.Press snug
against wall and secure through bottom to top of furnace
with screw provided.
--23--

Start-Up Procedure
Start the furnace using the procedures in section
OPERATING YOUR FURNACE.
WARNING
DANGER OF BODILY INJURY OR DEATH.
LIQUIFIED PETROLEUM L.P. GAS IS HEAVIER
THAN AIR AND IT WILL SETTLE IN ANY LOW
AREA, INCLUDING OPEN DEPRESSIONS AND
IT WILL REMAIN THERE UNLESS AREA IS
VENTILATED.
NEVER ATTEMPT START-UP OF UNIT BEFORE
THOROUGHLY VENTILATING AREA.
Check the furnace operation as outlined in the following
instructions. If any sparking, odors or unusual noises are
encountered, shut off electric power immediately. Recheck
for wiring errors, or obstructions in or near fan motor.
WARNING
NATURAL GAS HEATING VALUE (BTU PER CUBIC
FOOT) CAN VARY SIGNIFICANTLY, THEREFORE,
IT IS THE INSTALLER'S RESPONSIBILITY TO SEE
THAT BTU INPUT TO THE FURNACE IS ADJUSTED
PROPERLY. FAILURE TO DO SO COULD CAUSE
HEAT EXCHANGER FAILURE, ASPHYXIATION, FIRE
OR EXPLOSION, RESULTING iN DAMAGE, BODILY
INJURY OR DEATH. REFER TO THE NATIONAL
FUEL GAS CODE (NFPA-54)TO BE SURE THE FUR-
NACE IS BURNING FUEL AT THE PROPER RATE.
manometer having a scale range from 0 to 12 inches of
water should be used for this measurement. The manifold
pressure must be measured with the burner and pilot
operating. Any major changes in flow must be made by
changing the size of the burner orifice. Check with your
local gas supplier for proper orifice sizing.
CHECK THE GAS INPUT (NATURAL GAS ONLY)
To measure the input using the gas meter, proceed as
follows:
1. Turn off gas supply to all other appliances except the
furnace.
2,
With the furnace operating, time the smallest dial on
the meter for one complete revolution. If this is a 2 cubic
foot dial, divide the seconds by 2; if it is a 1 cubic foot
dial, use the time in seconds as is. This gives the
seconds per cubic foot of gas being delivered to the
furnace.
3. Assuming natural gas with aheating value of 1000 Btu
per cubic foot and 34 seconds per cubic foot used as
determined by step (2), then:
Second per hour = 3,600
Input = 1,000 x 3,600 + 34 =106,000 BTU Per Hour
This measured input must not be greater than the in-
put indicated on the rating plate of the furnace.
4. Relight all other appliances turned off in step 1above.
Be sure all pilot burners are operating.
Underfiring could cause inadequate heat, excessive conden-
sation or ignition problems. Overfiring could cause soot-
ing flame impingement or overheating of heat exchanger.
Before starting natural gas input check, obtain heating
value of gas (BTU per cubic foot) at standard conditions
from your local supplier. This factor is used in "Check the
Gas Input" section and procedure.
CHECK GAS INPUT AND PRESSURES
For furnace located at elevations between sea level and
2000 feet, the measured input must not be greater than
the input shown on the rating plate of the furnace. For
elevations above 2000 feet, the measured input must not
exceed the input of the rating plate reduced by 4 percent
for each 1000 feet that the furnace is above sea level.
Gas supply pressure and manifold pressure with the burners
operating must also be as specified on the rating plate.
Type of Gas Manifold Pressure, In. W.C.
Natural 4
LP. 10.5
Rated input will be obtained on 2500 Btu propane at 10.5
inch manifold pressure with factory-sized orfices. If LP gas
having a different heating value is supplied, offices must
be changed by a qualified service technician before the
furnace is operated.
ADJUST PILOT BURNER
(STANDING PILOT MODELS ONLY)
Pilotflame should surround 3/8 inch to 1/2 inch of the ther-
mocouple tip. Toadjust, remove pilot adjustment screw on
gas valve. Turnscrew counterclockwise to increase flame,
clockwise to decrease. Replace cap.
CHECK THERMOSTAT
Check thermostat operation. When set above temperature
shown on the thermostat, the main burner should light.
Make certain the thermostat turns off the furnace when
room temperature reaches the selected setting and starts
the furnace when room temperature falls a few degrees.
MAKE SURE THERMOSTAT ANTICIPATOR IS SET
PROPERLY, SEE PAGE 20.
THERMOSTAT (TYPICAL)
CHECK THE MANIFOLD GAS PRESSURE
A tapped opening is provided in the gas valve to facilitate
measuring the manifold gas pressure. A "U Tube"
SEI"_G
--24 m

Operating Your Furnace
STANDING PILOT MODELS*
3508731; 3508732
5008731; 5008732
6508731; 6508732
NOTE:
For models equipped with WILLIAMS gas valve P322041
or P322042 refer to this sheet and sheet 26 for "SAFETY
& LIGHTING INSTRUCTION" and "TURN GAS OFF TO
APPLIANCE."
For models equipped with WILLIAMS gas valve P321704
or P321705 refer to this sheet and sheet 27 for "SAFETY
& LIGHTING INSTRUCTIONS" and "TURN GAS OFF TO
APPLIANCE."
(All other models refer to sheet 28, 29 & 30.)
On new installations, the gas lines will be filled with air
and it may take several minutes to establish the pilot flame.
Keep all access doors and panels in place except for in-
spection and maintenance.
WARNING
THE SURFACE OF THE FURNACE IS HOT DUR-
ING OPERATION. KEEP CHILDREN, CLOTHING,
FURNITURE, AND FLAMMABLE MATERIAL AWAY
FROM IT.
DO NOT STORE OR USE GASOLINE OR OTHER
FLAMMABLE LIQUIDS OR VAPORS NEAR THE
FURNACE.
WARNING
DANGER OF IGNITION FLASH
AND EYE INJURY OR BLINDNESS
PROTECT YOUR EYES. NEVER ATTEMPT TO
LIGHT PILOT WITH GAS CONTROL VALVE KNOB
IN "ON" POSITION. FLASHBACK COULD OCCUR.
NOTE: Models 3508731; 3508732 are equipped with a
single speed fan.
TWO-SPEED FAN OPERATION
MODELS: 5008731; 5998732; 6508731; 6508732
For models equipped with WILLIAMS gas valve P322041
or P322042.
Blower will first operate at low speed then shift to high
speed as the furnace heats up.
For models equipped with WILLIAMS gas valve P321704
or P321705.
Models areequipped with a two-rate control valve. The rate
knob on the gas valve is marked "LO" and "HI." Turn the
rate knob to the "LO" position and the room thermostat
will operate the main burner at about 70% of maximum
capacity, blower will operate at low speed. Turn the rate
knob to the "HI" position only when a fast heat-up is
desired during extremely cold weather. High operation
develops maximum capacity of the furnace, blower will first
operate at low speed then shift to high speed as the fur-
nace heats up.
SAFETY LIMIT CONTROL
These furnaces are protected against unsafe operation by
five automatic safety controls: (1)A safety pilot acts to shut
OFF the gas valve in case of pilot failure; (2) A redundant
gas valve; (3) A limit switch shuts down the main burner
to prevent overheating the furnace cabinet; (4) A vent safe-
ty shutoff device shuts down the main burner to protect
against improper venting of combustion products. These
limit switchs will reset when furnace cools; and (5) A ther-
mal overload protects the motor against burnout caused
by current surges or if anything should block the flow of
air through the furnace. This switch will reset itself when
the motor cools down and it cannot be adjusted.
IMPORTANT
KEEP BURNER AND CONTROL COMPARTMENT
CLEAN.
WARNING
DANGER OF PROPERTY DAMAGE
BODILY INJURY OR DEATH.
IF THE FURNACE OVERHEATS OR FAILS TO
SHUT OFF, CLOSE MANUAL GAS VALVE FOR THE
FURNACE BEFORE TURNING OFF ELECTRIC
POWER.
--25--

FOR YOUR SAFETY, READ BEFORE LIGHTING
I WARNING: If you do not follow these instructions exactly, a fire or explosion
A,
This appliance has a pilot which must be lighted by
hand. When lighting the pilot, follow these instructions
exactly.
B.
BEFORE LIGHTING smell around the appliance area
for gas. Be sure to smell next to the floor because some
gas is heavier than air and will settle on the floor.
WHAT TO DO IF YOU SMELL GAS
• Do not try to light any appliance or strike a match.
• Do not touch any electric switch; do not use any
phone in your building.
• Immediately call your gas supplier from a neighbor's
phone. Follow the gas supplier's instructions.
NOTES: FOR ADDITIONAL INFORMATION REFER TO THE INSTALLATION AND OPERATION INSTRUCTION MANUAL SUPPLIED
WITH THIS APPLIANCE OR CONTACT THE MANUFACTURER IDENTIFYING THE PRODUCT BY ITS MODEL NUMBER LOCATED ON
THE RATING PLATE, FOUND NEAR THE GAS VALVE.
may result causing property damage, personal injury or loss of life,
• If you cannot reach your gas supplier, call the fire
department.
C.
Use only your hand to push in or turn the gas control
knob. Never use tools. If the knob will not push in or
turn by hand, don't try to repair it, call a qualified serv-
ice technician. Force or attempted repair may result in a
fire or explosion.
D_
Do not use this appliance if any part has been under
water. Immediately call a qualified service technician to
inspect the appliance and to replace any part of the
control system and any gas control which has been
under water.
LIGHTING INSTRUCTIONS
1. STOP! Read the safety information above.
2. Set the thermostat to lowest setting.
3. Turn off all electric power to the appliance.
4. Remove control access panel.
5. Turn gas control knob clockwise( _l_to "OFF".
POSITION --_ RESET
6. Wait five (5) minutes to clear out any gas, then smell for
gas, including near the floor. If you then smell gas, stop!
Follow "B" in the safety information above. If you don't
smell gas, go to next step.
7. Loosen wingnut and open pilot observation door (if
equipped).
8. Find pilot--follow metal tube from gas control. The pilot
is mounted on side of burner.
9. Turn knob on gas control counterclockwise
J_to "PILOT."
10. Push in red reset button THERMO- JJ
Immediately light the
all the way and hold in, COUPIF _ _.._
pilot. Continue to hold
the red reset button in for about PILOT
(1) minute after the pilot is lit. Release BURNER
button and it will pop back up. Pilot should
remain lit. If it goes out, repeat steps 5 through 10.
• If button does not pop up when released, stop and
immediately call your service technician or gas
supplier.
• If the pilot will not stay lit after several tries, turn
the gas control knob to "OFF" and call your service
technician or gas supplier.
11. Close pilot observation door, tighten wingnut
(if equipped).
12. Turn gas control knob counterclockwise _"_to "ON".
Knob can be turned to "ON" only if red reset button is
up.
13. Replace control access panel.
14. Turn on all electric power to the appliance.
15. Set thermostat to desired setting.
n
TO TURN OFF GAS TO APPLIANCE
1. Set the thermostat to lowest setting.
2. Turn off all electric power to the appliance if service is to be performed (if applicable).
3. Remove control access panel.
4. Push in gas control knob slightly and turn clockwise _ to "OFF'. Do not Force.
5. Replace control access panel.
WARNING: DUE TO HIGH SURFACE TEMPERATURES -- KEEP CHILDREN, CLOTHING,
FURNITURE OR ANY COMBUSTIBLE MATERIAL AWAY FROM FURNACE.
IMPORTANT: KEEP BURNER AND CONTROL COMPARTMENT CLEAN.
--26--

FOR YOUR SAFETY, READ BEFORE LIGHTING
I WARNING: If you do not follow these instructions exactly, a fire or explosion
A.
This appliance has a pilot which must be lighted by
hand. When lighting the pilot, follow these instructions
exactly.
B.
BEFORE LIGHTING smell around the appliance area
for gas. Be sure to smell next to the floor because some
gas is heavier than air and will settle on the floor.
WHAT TO DO IF YOU SMELL GAS
• Do not try to light any appliance or strike a match.
• Do not touch any electric switch; do not use any
phone in your building.
• Immediately call your gas supplier from a neighbor's
phone. Follow the gas supplier'a instructions,
NOTES: FOR ADDITIONAL INFORMATION REFER TO THE INSTALLATION AND OPERATION INSTRUCTION MANUAL SUPPLIED
WITH THIS APPLIANCE OR CONTACT THE MANUFACTURER IDENTIFYING THE PRODUCT BY ITS MODEL NUMBER LOCATED ON
THE RATING PLATE, FOUND NEAR THE GAS VALVE.
may result causing property damage, personal injury or loss of life.
• If you cannot reach your gas supplier, call the fire
department.
C.
Use only your hand to push in or move the selector
arm, Never use tools. If the arm will not push in or
move by hand, don't try to repair it, call a qualified
service technician. Force or attempted repair may result
in a fire or explosion,
D.
Do not use this appliance if any part has been under
water. Immediately call a qualified service technician to
inspect the appliance and to replace any part of the
control system and any gas control which has been
under water.
LIGHTING INSTRUCTIONS
8.
1. STOPT Read the safety information above.
2. Set the thermostat to lowest setting.
3. Turn off all electric power to the appliance.
4. Remove control access panel.
5. From "ON" position, depress and move selector
arm on gas control to "OFF" position. Do not force.
GAS CONTROL
SELECTOR
ARM SHOWN
IN *OFF"
POSI'nON
6. Wait five minutes to clear out any gas, then smell for gas,
including near the floor. If you then smell gas, stop! Follow
"B" in the safety information above. If you don't smell
gas, go to next step.
7. Loosen wingnut and open pilot observation door (if
equipped).
Find pilot--follow metal tube from gas control. The pilot
is mounted on side of burner.
9.
Hold lighted match at pilot
burner.
10.
Move selector arm to
"SET" position and light
pilot. Hold in "SET" position
for 1/2 minute after pilot is lit.
NOTE: Sufficient time must be allowed BURNER
for pilot flame to heat thermocouple
and hold safety magnet in locked-up position.
Also, time must be allowed for air to be purged
from gas lines during first starting operation.
11. Release selector arm, and if pilot remains lit, move
selector arm to "ON" position.
• If the pilot will not stay lit after several tries, move
the selector arm to "OFF" and call your service
technician or gas supplier.
12. Close pilot observation door and tighten wingnut
(if equipped).
13. Replace control access panel.
14. Turn on all electric power to the appliance.
15. Set thermostat to desired setting.
THERMO-_
COUPLE _
PILOT
TO TURN OFF GAS TO APPLIANCE
1. Set the thermostat to lowest setting.
2. Turn off all electric power to the appliance if service is to be performed (if applicable).
3. Remove control access panel.
4. From "ON" position, depress and move selector arm on gas control to "OFF" position. Do not force.
5. Replace control access panel.
WARNING: DUE TO HIGH SURFACE TEMPERATURES -- KEEP CHILDREN, CLOTHING, I
FURNITURE OR ANY COMBUSTIBLE MATERIAL AWAY FROM FURNACE.
IMPORTANT: KEEP BURNER AND CONTROL COMPARTMENT CLEAN.
--27--
I
I

Operating Your Furnace
ELECTRONIC IGNITION MODELS*
3508331; 3508332
5508331, 5508332
NOTE:
For models equipped with WILLIAMS gas valve P322043
or P322044 refer to this sheet and sheet 29 for "SAFETY
& LIGHTING INSTRUCTION" and "TURN GAS OFF TO
APPLIANCE."
For models equipped with WILLIAMS gas valve P321897
or P321898 refer to this sheet and sheet 30 for "SAFETY
& LIGHTING INSTRUCTIONS" and "TURN GAS OFF TO
APPLIANCE."
(All other models refer to sheet 25, 26 & 27.)
THE FURNACE WORKS LIKE THIS:
1. Thermostat turns on the control module.
2. Automatic relight system (in module) opens gas valve
and electronically ignites pilot. After pilot flame has
been established and proven by the control module,
main gas valve circuit opens and pilot lights main
burners.
3. Heat builds up in the furnace and starts the fan. The
heated air comes out the front bottom Iouvered panel
at floor level.
4. When the thermostat setting is reached, it shuts off the
main burner.
5. The fan runs until the heat is removed from furnace,
then it turns off.
WARNING
DANGER OF IGNITION FLASH
AND EYE INJURY OR BLINDNESS
PROTECT YOUR EYES. NEVER ATTEMPT TO
LIGHT PILOT WITH GAS CONTROL VALVE KNOB
IN "ON" POSITION. FLASHBACK COULD OCCUR.
NOTE: Models 3508331; 3508332 are equipped with a
single speed fan.
TWO-SPEED FAN OPERATION
MODELS: 5508331; 5508332
Formodels equipped with WILLIAMS gas valve P322043
or P322044.
Blower will first operate at low speed then shift to high
speed as the furnace heats up.
For models equipped with WILLIAMS gas valve P321897
or P321898.
Models are equipped with a two-rate control valve. The rate
knob on the gas valve is marked "LO" and "HI." Turn the
rate knob to the "LO" position and the room thermostat
will operate the main burner at about 70% of maximum
capacity, blower will operate at low speed. Turn the rate
knob to the "HI" position only when a fast heat-up is
desired during extremely cold weather. High operation
develops maximum capacity of the furnace, blower will first
operate at low speed then shift to high speed as the fur-
nace heats up.
IMPORTANT
KEEP BURNER AND CONTROL COMPARTMENT
CLEAN.
SAFETY LIMIT CONTROL
These furnaces are protected against unsafe operation by
three automatic safety controls: (1)The electronic ignition
system; (2) A limit switch shuts down the main burner to
prevent overheating the furnace cabinet; this limit switch
will reset when furnace cools; (3) A thermal overload pro-
tects the motor against burnout caused by current surges
or if anything should block the flow of air through the fur-
nace, the switch will turn the main burner off. When motor
cools down, this switch will reset itself. This switch can-
not be adjusted.
WARNING
THE SURFACE OF THE FURNACE IS HOT DUR-
ING OPERATION. KEEP CHILDREN, CLOTHING,
FURNITURE, AND FLAMMABLE MATERIAL AWAY
FROM IT.
On new installations the gas lines will be filled with air and
it may take several minutes to establish the pilot flame.
Keep all access doors and panels in place except for in-
spection and maintenance.
WARNING
DANGER OF PROPERTY DAMAGE,
BODILY INJURY OR DEATH
IF THE FURNACE OVERHEATS OR FAILS TO
SHUT OFF, CLOSE MANUAL GAS VALVE FOR THE
FURNACE BEFORE TURNING OFF ELECTRIC
POWER.
--28--

FOR YOUR SAFETY, READ BEFORE LIGHTING
WARNING: If you do not follow these instructions exactly, a fire or explosion I
may result causing property damage, personal injury or loss of life.
I
A. This appliance is equipped with an ignition device which
automatically lights the pilot. Do not try to light the pilot
by hand.
B. BEFORE LIGHTING smell around the appliance area
for gas. Be sure to smell next to the floor because some
gas is heavier than air and will settle on the floor.
WHAT TO DO IF YOU SMELL GAS
• Do not try to light any appliance or strike a match.
• Do not touch any electric switch; do not use any
phone in your building.
• Immediately call your gas supplier from a neighbor's
phone. Follow the gas supplier's instructions.
NOTES: FOR ADDITIONAL INFORMATION REFER TO THE INSTALLATION AND OPERATION INSTRUCTION MANUAL SUPPLIED
WITH THIS APPLIANCE OR CONTACT THE MANUFACTURER IDENTIFYING THE PRODUCT BY ITS MODEL NUMBER LOCATED ON
THE RATING PLATE, FOUND NEAR THE GAS VALVE.
• If you cannot reach your gas supplier, call the fire
department.
C.
Use only your hand to push in or turn the gas control
knob. Never use tools. If the knob will not push in or
turn by hand, don't try to repair it, call a qualified serv-
ice technician. Force or attempted repair may result in a
fire or explosion.
O.
Do not use this appliance if any part has been under
water. Immediately call a qualified service technician to
inspect the appliance and to replace any part of the
control system and any gas control which has been
under water.
LIGHTING INSTRUCTIONS
t. STOP! Read the safety information above,
2. Set the thermostat to lowest setting.
3. Turn oft all electric power to the appliance.
4. This appliance is equipped with an ignition device which
automatically lights the pilot. Do not try to light the pilot
by hand.
5. Remove control access panel.
6, Turn gas control knob clockwise( _!_to "OFF",
GAS CONTROL _
KNOBSHOWN !> F _ .
7. Wait five (5) minutes to clear out any gas, then smell for
gas, including near the floor. It you then smell gas, stop!
Follow "B" in the safety information above. If you don't
smell gas, go to next step,
8,
Turn the gas control knob counterclockwise _' I
to "ON".
9. Replace control access panel.
10. Turn on all electric power to the appliance.
11. Turn thermostat to on (HEAT) position. Set thermostat
higher than room temperature. Pilot will automatically
light and main burner(s) will light in approximately 45
seconds.
NOTE: On initial start-up or after prolonged shot down,
several ignition cycles may be required to purge gas
lines. To accomplish the recycle - repeat steps 6
through 11 until pilot is established.
12.
Set thermostat to desired setting.
13.
After the room thermostat turns the system off, a delay
of approximately one minute is required before the
system can be turned on again.
14.
If the appliance will not operate, follow the instructions
"To Turn Off Gas To Appliance" and call your service
technician or gas supplier.
TO TURN OFF GAS TO APPLIANCE
1. Set the thermostat to lowest setting.
2. Turn off all electric power to the appliance if service is to be performed.
3. Remove control access panel.
4. Push in gas control knob slightly and turn clockwise [ _, to "OFF". Do not Force.
5. Replace control access panel.
WARNING: DUE TO HIGH SURFACE TEMPERATURES -- KEEP CHILDREN, CLOTHING,
FURNITURE OR ANY COMBUSTIBLE MATERIAL AWAY FROM FURNACE.
IMPORTANT: KEEP BURNER AND CONTROL COMPARTMENT CLEAN.
--29--

FOR YOUR SAFETY, READ BEFORE LIGHTING
I WARNING: If you do not follow these instructions exactly, a fire or explosion
A. This appliance is equipped with an ignition device which
automatically lights the pilot. Do not try to light the pilot
by hand.
B. BEFORE LIGHTING smell around the appliance area
for gas. Be sure to smell next to the floor because some
gas is heavier than sir and will settle on the floor.
WHAT TO DO IF YOU SMELL GAS
• Do not try to light any appliance or strike e match.
• Do not touch any electric switch; do not use any
phone in your building.
• Immediately call your gas supplier from a neighbor's
phone, Follow the gas supplier's instructions.
NOTES: FOR ADDITIONAL INFORMATION REFER TO THE INSTALLATION AND OPERATION INSTRUCTION MANUAL SUPPLIED
WITH THIS APPLIANCE OR CONTACT THE MANUFACTURER IDENTIFYING THE PRODUCT BY ITS MODEL NUMBER LOCATED ON
THE RATING PLATE, FOUND NEAR THE GAS VALVE,
may result causing property damage, personal injury or loss of life.
• If you cannot reach your gas supplier, call the fire
department.
C.
Use only your hand to push in or move the selector
arm. Never use tools. If the arm will not push in or
move by hand, don't try to repair it, call a qualified
service technician. Force or attempted repair may result
in a fire or explosion.
D.
Do not use this appliance if any part has been under
water. Immediately call a qualified service technician to
inspect the appliance and to replace any part of the
control system and any gas control which has been
under water.
LIGHTING INSTRUCTIONS
1, STOP! Read the safety information above,
2. Set the thermostat to lowest setting.
3, Turn off all electric power to the appliance.
4. This appliance is equipped with an ignition device which
automatically lights the pilot. Do not try to light the pilot
by hand.
5. Remove control access panel.
6. From "ON" position, depress and move selector arm on
gas control to "OFF" position, Do not force.
GAS CON'n_OL
SELECTOR
ARM SHOWN
IN "OFF"
POSI'NON
8. Move selector arm to "ON" position.
9, Replace control access panel.
10, Turn on all electric power to the appliance.
11. Turn thermostat to "ON" (HEAT) position. Set thermostat
higher than room temperature. Pilot will automatically
light and main burner(s) will light in approximately 45
seconds,
NOTE: On initial start-up or after prolonged shut down,
several ignition cycles may be required to purge gas
lines. To accomplish the recycle - repeat steps 6
through 11 until pilot is established.
12.
Set thermostat to desired setting.
13.
After the room thermostat turns the system off, a delay
of approximately one minute is required before the
system can be turned on again.
14.
If the appliance will not operate, follow the instructions
"To Turn Off Gas To Appliance" and call your service
technician or gas supplier.
Wait five (5) minutes to clear out any gas, then smell for
gas, including near the floor. If you then smell gas, stop!
Follow "B" in the safety information above. If you don't
smell gas, go to next step.
TO TURN OFF GAS TO APPLIANCE
1. Set the thermostat to lowest setting.
2. Turn off all electric power to the appliance if service is to be performed.
3. Remove control access panel.
4. From "ON" position, depress and move selector arm on gas control to "OFF" position. Do not Force.
5. Replace control access panel.
WARNING: DUE TO HIGH SURFACE TEMPERATURES -- KEEP CHILDREN, CLOTHING,
FURNITURE OR ANY COMBUSTIBLE MATERIAL AWAY FROM FURNACE.
IMPORTANT: KEEP BURNER AND CONTROL COMPARTMENT CLEAN.
--30--

How To Care For Your Furnace
WARNING
DANGER OF BODILY INJURY OR DEATH
TURN OFF ELECTRIC POWER SUPPLY AT
DISCONNECT SWITCH, FUSE BOX OR SERVICE
PANEL BEFORE REMOVING ANY DOORS OR
ACCESS OR SERVICE PANELS FROM UNIT.
CABINET FINISH
Clean cabinet with damp rag. Never use abrasive cleaners.
Cabinets are finished in heat resistant baked enamel - DO
NOT refinish with wall paint.
COMBUSTION AND VENTILATION AIR
The combustion and ventilation air supply must not be
blocked.
Do not put anything in or on the furnace cabinet.
For better circulation and more effective heating, do not
place obstructive furniture closer than four feet to the front
of the cabinet or two feet to the side of the cabinet.
PILOT BURNER
Light pilot using instructions in OPERATING YOUR
FURNACE (on pages 25 through 30, depending on your
model). Leave thermostat at lowest setting.
Pilot flame should surround 3/8 to 1/2 inch of the thermo-
couple tip. Refer to Fig. 42, Page 32. If flame needs
adjusting, do it as follows:
ADJUST PILOT BURNER (see Fig. 42, page 32)
1. Remove screw cover over pilot adjusting screw.
2. Insert small screwdriver, Adjust flame as needed. Turn
screw counterclockwise ( _ ) to increase flame,
clockwise ( _ ) to decrease.
3. Turnthermostat to highest setting. Main burnersshould
light quickly and smoothly. Turn thermostat to lowest
setting. Main burners should go out. Pilot should re-
main lit except for electronic ignition models.
4. Replace screw cover over pilot adjusting screw.
BURNER FLAME
Start the furnace and let it operate about 10 minutes then
look at the burner flame. Flames should be soft and blue,
see Fig. 40. If flames appear abnormal, contact the gas
company or a qualified service technician immediately.
FURNACE AREA
Keep the area near the furnace clear and free from com-
bustible materials, gasoline, and other flammable liquids
and vapors.
ANNUAL UPKEEP NEEDED
It is recommended that a qualified service technician per-
form these checks at the beginning of each heating
season.
CLEANING AND OILING
Shut off electricity, then remove cabinet door and front
panel. Clean any lint or dirt from fan blades, fan motor,
and exposed air passages. Use a brush.
Put 5 drops of SAE 20 oil in each of the two cups or oil
tubes on the fan motor, See Fig. 39, below.
MOTOR OIL HOLES
OIL 1UBES
OR
OIL CUPS
ON EACH
_ND OF
MOTOR
FAN
MOTOR
VENTING SYSTEM
Make sure that no parts of the vent air system are block-
ed or rusted. Clean or replace before using furnace.
MAIN BURNER FLAME PATTERN
CORRECT
le4SUFflCiENE AIR LONG OPEN
ENI) (_ONES YELtOW IN COLOR
INNER CONES LIGHT BLUE POINTED TOP
OUTER MANTLE LIGHT BLUE
PROPER FLAME I/2 Io 3/4 HIGH
--31--

How To Care For Your Furnace (Con't)
BURNER CLEANING
Check burner. If cleaning is required, contact a qualified
service technician to clean and service burner.
WARNING
DANGER OF BODILY INJURY OR DEATH
MAKE SURE ELECTRIC POWER AND GAS
SUPPLY ARE OFF BEFORE REMOVING PANELS
OR DOORS, ETC.
CLEANING BURNER COMPARTMENT
Because cold air is attracted to the flame during furnace
operation, a build up of lint from bedding and dust, etc.,
in the burner area will occur each heating season. It is
necessary to clean this area regularly. Use a vacuum
cleaner with a narrow attachment to reach small areas.
Be careful in and around the pilot. A change in its adjust-
ment could be made if struck during cleaning.
TO REMOVE BURNER(S)
Refer to "Mounting Your Furnace" section (pages 15, 16
and 17).
Check the spark gap. It must be carefully adjusted to
specifications as illustrated (Fig. 42) for ignition device to
function properly.
PILOT FLAME AND SPARK GAP
PILOT • 3/8 TO 112
HOOD
SENSOR
SLIGHT
ORANGE TIP
ELECTRODE TYPICAL
TYPICAL BLUE CONE BLUE CONE
--LP GAS NATURAL
BURNER GAS
CASTING
N_TURAL GAS
NATURAL
Disconnect gas line inside cabinet.
MODEL
NUMBER
3508732
3508731
3508332
35O8331
5008732
50O8731
5508332
5508331
6508732
6508731
**For elevations above 2000 feet reduce ratings 4% for each 1000 feet above sea level
Furnace Technical Information
TYPE
GAS
NAT
L.F:
NAT
L.I_
NAT
L.P
NAT
L.R
NAT
L.P
INPUT** RATING
HI-FIRE LO-FIRE
35,000 24,500
35,000 24,500
35,000 24,500
35,000 24,500
50,000 35,000
50,000 35,000
55,000 38,500
55,000 38,500
65,000 45,500
65,000 45,500
MAIN BURNER ORIFICE
DRILL DEC.
#38 .1015
#52 .0635
#38 .1015
#52 .0635
#43 .089O
#54 .0550
#42 .0935
#54 .O550
#38 .1015
#52 .0635
QTY.
1
1
1
1
2
2
2
2
2
2
The efficiency rating of these appliances is a product thermal efficiency rating system determined under continuous
operating conditions and was determined independently of any installed system.
m32--

Troubleshooting Chart
FOR MODELS: 3508731; 3508732; 5008731; 5008732; 6508731; 6508732
SYMPTOM
1. Pilot will not stay lit after
following lighting
instructions.
2. Main burner will not come
ON -- pilot burning and
thermostat set for heat.
POSSIBLE CAUSE(S)
a. Thermocouple producing insuffi-
cient millivoltage.
b. Loose or dirty thermocouple
connection at gas valve.
c. Thermocouple defective.
d. Thermomagnet pilot safety
defective.
e. Vent safety shutoff device.
a. Gas valve not turned ON.
b. Electric power to furnaceturned
OFE
c. Low voltage transformeror limit
switch defective.
CORRECTIVE ACTION
a. Check pilotflame -- mustimpinge onthermocouple.Pilotflame
maybeloworblowing(high)causing safetytodropout. Pilo_orifice
or aeratinghole maybe plugged (checkfor spiders,websor other
organic material). Be sure the thermocouple is fully insertedin
bracket.
b. Clean and/ortightenthermocouplefitting atconnectiontovalve.
C. Check thermocouplewithmillivoltmeter-- shouldgenerateap-
proximately30 millivolts when not connected to load. When con-
nectedtoload,should generateapproximately14millivolts.If below
7 miilivolts, replace.
d. Replacegas valve after above is checked out.
e. Checkwiringconnectionsfrom valve to vent safetyshutoffdevice.
Be sure all connections are tight. Check for blocked vent.
a.
Turngasvalve knob to "ON" position -- if no main gas flow, pro-
ceed to Step. "b".
b.
Checkforline voltage atfurnace-- if okayandno main gasflow,
proceed to Step "c".
C.
Checkfor24 volts at the lowvoltage terminals ofthetransformer.
If novoltage,turn OFFelectric powerto furnace.Removeone wire
from limit switch and check for continuity across both terminals.
No continuity-- replacelimit switch.With a good limitswitchback
in the circuitand the electric powerturned ON -- if no voltage,
replace transformer. NOTE: Before replacing the transformer or
limit switch, check wiring for loose connections or broken wires
and repair as needed. If voltage is present at transformer, pro-
ceed to Step "d".
d. Wall thermostat defective.
d.
With thermostat set for heat (contacts closed) checkfor voltage
at terminals on gas valve. If no voltage is present replacedefec-
tive thermostat. NOTE: Before replacing thermostat, be sureto
checkwiring from furnace to thermostat for loose connectionsor
broken wiresand replace as needed.
Ifvoltageis presentat terminals on gas valveand still nogas flow
to main burners, proceed to Step "e".
e. Burner orifice plugged.
e.
Clean or replace orifice -- if okay and still nogas flow to main
burners, proceed to Step "f".
"3. Burner comes "ON" but
goes OFFbefore blower
turns ON.
f. Gas valve defective.
a. Defective wiring.
f.
Replace defective gas valve.
a.
TurnOFF electric power to furnace. Removetop front panel, fan
shroudand blower wheel. Refer to Wiring Diagram and check all
wiring inside junction box. Removecenter front paneland check
all wiring inside switch box containing fan, limit and selectorswit-
ches.Correctif necessary. If correct, proceed to Step "b". NOTE:
Selectorswitch used onlyon Models5008731;5008732;6508731:
6508732.
b. Defective limit switch.
b.
If burner goes OFF in less than five minutes from room
temperaturestart, check limit control switch. Ifdefective,replace.
NOTE:Blower shouldturn "ON" within three minutesafter burner
is "ON" froma room temperaturestart.Ifnot,proceedtoStep"c".
*Also applicabLeto Models equipped with an electric intermittent pilot system. (continued next page)
--33--

Troubleshooting Chart
FOR MODELS: 3508731; 3508732; 5008731; 5008732; 6508731; 6508732
SYMPTOM
3. Burner comes "ON" but
goesOFF before blower
turns ON. (cont.)
*4. Burnercomes "ON", blowe
comes "ON", but cycles
"ON" and "OFF" while
burner remains "ON".
*5. Burner comes "ON",
blower comes "ON", but
burner cycles "OFF" and
"ON" with blower "ON".
POSSIBLE CAUSE(S)
c, Defectivemotor(2-speed).
d. Defective motor (1-speed).
e. Defectivefan switch.
a. Furnace not operating at full
rate.
a. Furnace operating over-rate.
b. Line voltage too low.
c. Recirculation.
d. Loss of circulating air due to
leakage.
CORRECTIVE ACTION
C.
Jumperacrossfan switch,turnelectric powerON, motor should
rotate.A2-speedmotorisused-- jumperfrom "brown" terminal
onfanswitchto #2(red)terminalonselectorswitch, motorshould
rotateon "LOW" speed. Jumperfrom same"brown" terminalon
fan switchto#3 (black) terminalonselectorswitch, motorshould
rotateon "HIGH" speed.Replacemotor if defective.
d.
Jumper across fan switch, turn electric power ON, motorshould
rotate. Replace motor if defective.
e.
If, after checkingabove possibilities, problem still exists, replace
fan switch.
a.
Check for low gas pressure atgas valve -- should be 4" W.C.for
NaturalGas, 11" W.C.for L.R Gas. Check burner orifice.
a.
Check for high gas pressure at gas valve -- correctif necessary.
See correct pressure above.
b.
Check line voltage to motor, if below 115volts motor will run too
s_ow.
C,
Heated air discharging against an object causing recirculation,
such as a hall installation or a large piece of furniture within 4'
of discharge.
d,
Checkheaderplateinstallation and proper use of gaskets.Repair
as necessary.
"6. Furnace operates but turns
"OFF" before room tem-
perature is attained.
*7. Furnace operatesbut will not
shut "OFF" when room
temperature is attained.
*8. Abnormal operation.
a. Thermostat location.
b. Defective thermostat.
a. Thermostat wiring defective.
b. Thermostat location,
c Improper thermostat anticipator
setting.
a. Blower noise.
b. Expansion noise ticking,
c. Burnerresonance.
d. Seleclor switch defective.
(2-speed).
a.
Checklocationof thermostat. It should not be in the path of warm
air discharge from furnace, near a lamp,or above a TV set or
stereo.
b.
Check thermostatcalibration or replace.
a.
Check thermostat wiringfrom furnace to thermostat -- may be
shorted together by a nail or staple.
b.
Check thermostat location -- if an outside wall or a hole in wall
behind thermostatcausingcold air to contactthermostat, relocate.
C.
Set anticipator per THERMOSTATANTICIPATOR,page 20.
Check motor mounts -- they may be loose. Blower wheelcould
be out of balance Setscrew may be looseon motor shaft. Blower
may be rubbing on fan shroud. Motor may need oiling. Correct
as needed.
Check installation -- casing may be twisted or not level at time
of installation causing combustion chamber to bind on its locating
pros
Usually associated with L.R Gas operation. Adjust primary air
screw =nthroatof each cast iron burner after about 10 minutes
of operation.Adjust toobtain a soft blue flame without streaming
yellow tips,
During normal furnace operation motorwill be on "LOW" speed
when operatingon minimum inputcapacityand on"HIGH" speed
whenoperating on maximum input capacity. Ifthere isno change
in motor speed, replace selector switch.
"Alsoapplicableto Models with an electric intermittent pilot system.
--34--

Troubleshooting Chart
FOR MODELS: 3508331; 3508332; 5508331; 5508332
SYMPTOM
1. Nospark-- nopilotgas.
2. Spark -- but no pilot gas,
POSSIBLE CAUSE(S)
a. No main powe_
b. Faulty transformer.
c. Faulty thermostat.
d. Faulty limit switch.
e. Faulty ignitioncontrol.
f. Faulty wiring.
g. Vent safety shutoffdevice.
a. Faulty ignition.
b. No gas supplied to pilot valve.
c. Manual valves in OFF position.
CORRECTIVE ACTION
a.-e. Perform normalsystemchecks of mainpower,transformer,ther-
mostat, limit switch, and replace faulty component.
With power ON, turnthermostatto the lowestsetting, wait 10
seconds and return to HIGH setting. With power ON and ther-
mostatset at its highest position, set voltmeterto24Vscale and
attach probesto terminals "TR" and "TH" on the ignition con-
trol unit.
If you read 24V and there still is no sparkor pilot gas, the igni-
tion controlis defective and must be replaced.
f. Testwiring. Repair or replace.
g. Check wiring connectionsfromvalvetoventsafetyshutoffdevice,
be sure all connectionsare tight. Check for blocked vent.
a. See le.
b. Check for availabilityofgas atgascontrol. Makesurethe manual
valve (gas cock) on the gas control are in the full ON position.
No pilot gas could be caused by a plugged pilot tubing. Also
check the pilot adjustment at the gas control.
c. See 2b.
3. Pil_gas--but no spark.
d. Faulty pilot valve.
e. Faulty wiring.
f. Restricted pilot line or clogged
pilot orifice.
a. Faulty ignitioncontrol.
b. Broken or shorted electrode
assembly.
d. See2b.
e. See lf.
f. See2b.
a.
With power ON, turn thermostat to the lowestsetting, wait 10
secondsand return1ohighsetting WithpowerONandthermostat
set atits highest position, set voltmeter to 24V scale and attach
probesto terminals"24V" (*TH) and "GRD" ('TR) on the igni-
tion control unit. If you read 24V and there is still no spark or
pilotgas, the ignition control is detective and must be replaced.
With thermostat turned to its highest setting, set test meter to
24Vscale.Touchprobesto "PV/MV" and"PV" terminalson Gas
Valve. If you do not get a 24V reading, check wiring. If wiring
tests okay, check ignition control.
Connectprobesto "PV/MV" AND"PV" terminalsonignitioncon-
trol.If youdo not read24V,the ignition control mustbe replaced.
Remove wire at "PV/MV" terminal at the ignition control, being
careful not to touch any metal parts; disconnect the electrode
wire at the ignition control. Connect one end of a jumper wire
to terminal "GND" (DO NOT REMOVE EXISTING WIRE.) At-
tach the other end of the jumper wire to the metal blade of a smal!
screwdriver. Position end of metal blade approx. 1/8" from ter-
minal. Reconnect "PV/MV" terminal Sparking should occur be-
tween screwdriver blade and terminal
If no sparking occurs, the ignition control must be replaced.
Checkthe pilot and electrode assembly for proper electrodegap
(3/32" to 1/8") or any possible shorting of electrode 1osurroun-
ding metal surfaces. Make surethe spark ignitor and electrode
connectionsto the ignition control are tight. The ignition control
and pilot burner musl both be chassis ground. If there is still no
spark, the pilot and electrode assembly must be replaced.
--35--
(continuednextpage)

Troubleshooting Chart
FOR MODELS: 3508331; 3508332; 5508331; 5508332
SYMPTOM
4. Pilotlit,butmainburner
won'tcome ON.
POSSIBLE CAUSE(S)
a. Faultyignitioncontrol.
b. Faultywiring.
c. Low pilot flame.
d. Improper alignment of sensor in
pilot flame.
e. Faulty flame sensor.
CORRECTIVE ACTION
a,
See 3a.
b.
See if.
C.
NOTE:Waitat least90 secondsafter pilotlightsbeforedoing the
check out procedures for problem number 4.
With thermostatON,be surethat the pilot and sensor are prop-
erly aligned so that the pilot flame impinges the top 3/4 inch of
the sensoi_Be surethat the sensor is pushed allthe way into pilot
bracket.Adjustpilotflamewithpilotadjustment, if necessary.Also
check inlet supply pressure and pilot orifice, if pilot hOOdor sen-
sor is bent, the defective unit should be replaced.
If main burner still won't comeON, make sure the main burner
orifices are clear:.If orifices are clear, set voltmeter to 24V scale
andtouch probes to the terminals of the main gas operator:on
the gas valve.Attach to terminal "MV", "PV/MV" on Gas Valve.
Ifyou read24Vand theburner won't turn ON, replace entire gas
valve.
d,
WhenmainburnercomesON,ensurethatthepilotflameisstrong,
sensor is properly aligned,and pilot flame impingesthe top 3/4
inchofthe sensor:(Seeproceduresforcheck for proper pilot flame
and alignment in problem 4c.) Check the pilot and electrode
assembly for proper electrode gap (3/32" to 1/8") or any possi-
bleshortingofelectrodetosurrounding metal surfaces.Makesure
the spark ignitor and electrode connections to the ignition con-
trol aretight. The ignition control and pilot burner must both be
chassis ground. _fthere is still no spark, the pilot and electrode
assembly must be replaced.
e.
BE SURE POWER IS "OFF", BEFORE PERFORMING THIS
TEST!! Settest meterto "ohm" scale or use continuity checker.
Touch one end of probes to top of flame sensor, the other to
"SENSE" terminal onthe ignitioncontrol. Ohmmetershould read
"0", continuity should be evident. If you don't obtain a reading,
removewiring from sensor and test both individually, If continui-
ty is not evident, replace wiring and/or sensor.
There should be NOcontinuity between sensor and "GND" ter-
minalonthe ignition control,Testingwiringand sensorindividually,
determine which is shorted on ground. Replace or repair. Turn
ON power.
PiJotcycles OFF and ON
by itself,
Main burner shuts down
before thermostat is
satisfied.
a. Faulty pilot valve.
b. Faulty wiring.
a. Lowpilotflame.
b. Improperalignmentof sensor in
pilotflame.
c. Pilot flame being drawn away
from sensor
d. Improper heat anticipator
setting.
e. Faultylimit.
--36--
a. See 2b.
b. See lf.
a. See 4c.
b. See 4d.
C,
Whenmainburner comesON,ensurethat the pilot flame is strong,
sensor is properly aligned and pilot flame impingesthe top 3/4
inch of the sensor. (Seeprocedures for checking forproper pilot
flame and alignment in problem 4d.) If the pilot flame is drawn
awayfrom the sensor when the main burner comes "ON", the
cause could be the manual valve is notin the full ON position
or the inlet gas pressure with the main burner ON.
NOTE:Low inlet gas pressure to the gas controlcan be caused
byseveralproblemsandis notwithin the scope of the procedures
outlined in this service guide Consult your local utility or gas
supplier:
d.
See 6c.
Check the setting of the heat anticipator in the wall thermostat.
Set it to setting specified on the gas control.
e.
The system may be cycling on a faulty limit. Using a test meter
set to the 110volt scale, check for a voltage reading across the
limitwhen the main burner shuts OFF.If you get a 24volt or 110
volt reading on shutdown, replace defeclive limit switch.

Wiring Diagrams
FOR MODEL_
3508331 ond 3508332
FOR 35M B.T.U.
FAN TYPE VENTED WALL FURNACE
WITH INTERMITTENT IGNITION CONTROL SYSTEM
L1 1.2
HOT 115V 80HZ NEUT
FAN SWITCH
115V
SENSOR•
@
THERMOSTAT IGN
TO + II
.v/Pv O _--r-_ O
Z4V/GNDO,
PV O- 0
24V O"
MV O-
s_s O__ 0
IGNO-
IN1T-,RMI3'TENTIGN.
CONTROL MODULE
_FACTORy _ L_ VOLTAGE. 1 ffanyoftheoriginaJwireassupplied
-- FA_ WM_£D LOW VOLTAGE. with the appliance has to be replac-
1//4 QUICK CONNECT "I_RMINAL ed, useonly 18Ga.,4/64insulation,
FACTORY WIRING. 105° C. AWM copper wire or its
V4RE CONNECTOR FOR FAC'F(_Y equivalent 115V-60Hz.-lessthan
_R_O LINE VOf.TA_- 3amps.
(_ SCREW "J_E_NAL LOW _31.TAGF-
"n-IERMOSTAT r_] cONV-oUR-ET
PV (P) 7
PVA=V(c)
_(_0
GAS
VALVE
NOTES:
2. MOTOR IS THERMALLY OVER-
LOAD
115V. 60Hz - LESS THAN 3 AMPS
VENT
SAFETY
SHUT OFF
DE'V1CE
PROTECTED.
FOR MODELS:
5508331 and 5508332
FOR 55M B.T.U.
FAN TYPE VENTED WALL FURNACE
WITH INTERMITTENT IGNITION CONTROL SYSTEM
L1 • 115V BOHZ _ 19
FAN _TCH _TGPI 'v' 3 _ w _L COM
UMIT SWITCH r'mor_ • SENSOR
i I_10 O i
TR_S. FLAME
+1
z4v/mD 0 , ,
SENS 0 -- _; PV/_IV (C)
PV 0 MV (M)
24V 0 _ GAS
Mv0 L VALVE
IGN0 ---
IN'W.RMITW.NT IGN.
CONTROL MODULE
LE_ NOTES:
m FACTORY _ LINE VOLTA_-. 1. Ifanyoftheoriginalwireassupplisd
-- FACTORY _ LOW VOLTAGE. withtheappliancehastobereplac-
I/4. QUICK CONNECT "I_UNAL ed, useonly 18 Ga., 4/64 insulation,
FOR FACTORY V_RtNG. 105° C. AWM copper wire or its
_RE CONNECTOR FOR FACTORY equivalent115V-60Hz.-lessthen
'_4RINQ LINE VOLTAGE* 3 amps
SCREW/ _ LOW _OLTAGE, LOAD PROTECTED.
"THERMOSTAT _ CONV.OU'I1..ET
2. MOTOR IS THERMALLY OVER-
115V 60Hz - LESS THAN 3 AMPS.
VENT
SAFETY
SHUT OFF
DE_CE
D
SPNtK GAP
7/'G:2- oTR
-- ARK
uv (_)
-- 2"-'ff49-
T
'= "l
_1 VENT SAFETY
NTERMIT_T IGNITION CONTROL MODULE SHUT OFT"DEVICE
D
_1 / ELECTRODE
__ 7/a,r --FSPA_K S_TCH
@
-- "_R-- BLACK 't/
--_ I'_ -uv(M) ._=i_
w--Qg- .,
_QN "1, VENT SAFETY
Z]N'R_MIT'Jl_T IGNITIONCON_I_OLMODULESHUT OFF DEVICE
--37--

{:'OR MODELS:
3508731 and 3508732
Wiring Diagrams
FOR MODELS:
5008731 and 5008732
6508731 ond 6508732
FOR 35M B.T.U.
FAN TYPE VENTED WALL FURNACE
WITH CONTINUOUS PILOT CONTROL SYSTEM
u / /_
.oq- ,sv.,z
I _ r _ _ .oTo. I
TO THE3_MOSTAT
"IN_MOe_UPI.E
SHUTOFFDE_ _ _
LE_ NOTES:
I FACTORY _ UN =' VOLTAGE. 1. Ifanyoftheorigina/wireassupplied
-- FACTORY _R_ LOW _3LTAGF-.. wi(h the appliance hasto be replac-
1/'4 QI_C_ C_CT "i_AL ed, useonly 18Ga.,4/64insula5on,
EZ]
F_-_ORy _ 105 ° C, AWM copper wire or its
WIRE CQNNECTOR FOR FACTORy equivalent 115V-60Hz.-lessthan
_P_NG lINE VOLTAGE. 3 amps,
_ERMJNAL LOW VIO_TAG_. LOAD PROTECTED.
2 MOTOR IS THERMALLY OVER-
115V 60Hz - LESS THAN 3 AMPS.
FOR 50M AND 65M B.T.U.
FAN TYPE VENTED WALL FURNACE
WITH CONTINUOUS PILOT CONTROL SYSTEM
.z "I. T
UMIT SWITCH (_TRANS.
I
TO "IHE_OSTAT l
VENT __
SHUT OFF D
LIEG_qD NOTES:
-_, FAC'R_Y _ L_IE VOLTAGE.1. Itanyof theoriginalwireassupp_ied
-- FACTORY t_RIED LOW VOLTAGE. with the appliance has to be replac-
1/'4 QU]C_ C_NNECT "RE_MINAL ed, useonly 18 Ga., 4/64 insulation,
FACTORY '/_RJN P_ 105= C AWM copper wire or its
_RE CONNECTOR FOR FACTORY equivalent 115V- 60Hz,- less lha_
• IRSNG LINE VOLTAGE. 3 amps
SCREW "I]B_.MINAL LOW VOLTAGE. 2 LOAD PROTECTED.
T=,,T
J - BLOCK
THERMOCOUPLE
MOTOR IS THERMALLY OVER-
115V. 60Hz LESS THAN 3 AMPS.
THERMOSTAT
1 2
11t 11t
[_ CONV.OU_
ON HEADER
BROWN
BLUE
BLOCK "I'HERMOCOUPLE
VENT SAFELY
SHUT oFF DEVICE
THERMOSTAT
1 2
TR TH
GAS VALVE
_._] CONV,OU1LEr
ON HEADER
-(:)
R_.-_
UMIT SWITSH
-- BLOCKTHERMOCOUPLE
8LAOK./YELLOW('_ VENT SAF'E--W
et.Aa<./"Y_EU.OW_ SHUT OFF DEVlC£
--38--

Williams Top Vent Gas-Fired Wall Furnace
REPAIR PARTS FOR MODELS
3508331; 3508332; 3508731 and 3508732
CABINET and BODY
ASSEMBLY
16
28
17 18 19
20
3O
5
33
32
35
_4
28
USE ONLY MANUFACTURER'S AUTHORIZED PARTS
FOR PARTS LIST SEE PAGES 41 AND 42.
--39--

Williams Top Vent Gas-Fired Wall Furnace
CONTROL ASSEMBLY
FOR MODELS
3508731 and 3508732
FOR PARTS LISTING SEE PAGE 42
1
USE ONLY MANUFACTURER'S
AUTHORIZED PARTS
--40--
CONTROL ASSEMBLY FOR MODELS-
3508331 and 3508332
FOR PARTS LISTING SEE PAGE 42

Williams Top Vent Gas-Fired Wall Furnace
REPLACEMENT PARTS LIST FOR MODELS 3508331; 3508332; 3508731 and 3508732
REF.
NO.
DESCRIPTION
1
Outer Casing, Less Front Panel
2
tnner Liner
3
Heating Element
4
Bottom Front Panel
5
Top Front Panel
6
Fan Shroud
7
Vent Cover
8
Draft Hood
9
Switch Box
10
Center Front Panel
11
Internal Wires (All Except Ign. Control)
12
Header Plate
13
Junction Box
14
Gasket-Element Base
15
Draft Hood Gasket
18
Flue Collar Gasket
17
Fan Blade
18
Motor
19
Motor Support (2 Req,)
20
Vibration Isolators (4 Req.)
21
Transformer, 116V-24V
22
Limit Switch
23
Fan Switch
24
Switch Box Cover
28
Limit Switch
25
Deflector Baffle Handte
27
Header Gasket (3 Req.)
27A
Lower Element Base Angle
28
* Vent Enclosure Bide (2 Req.)
29
_r Vent Enclosure Front
28
-* Vent Enclosure Side (2 Req.)
29
* Vent Enclosure Front
30
* Rear Grille, Two-Way
31
* Plaster Ground
32
* Rear inner Boot, 10-3/4 Inches Long
33
* Damper
34
* Rear Outer Boot, 10 Inches Long
3O
Jr Rear Grille, Two-Way
31
J, Plaster Ground
32
* Rear Inner Boot, 1-5/8 Inches Long
33
* Damper
34
_, Rear Outer Boot, 7/8 Inches Long
36
* Diffusing Grille Kit Two-Way
35
* Diffusing Grilte Kil - One-Way
* Trip Strip Kit (Not Shown)
* Oval B/W Vent Kit (Not Shown)
PART NO. FOR
35O8331
12C10
12B15
12C18
12B49
12B50
12B03-1
7B12
12B12
tlB05
12C21
3508331
7B57
12B05
P026500
P107900
P027100
P300500
P322544
7B46
P022800
P024200
P309600
P200200
11C68
P321127
11C63
7A68
7Al17
9812 9812 9812 9812
9824 9824 9824 9824
6801 6801 6801 6801
6802 6802 6802 6802
6703 6703 6703 6703
6704 8704 8704 8704
4701 4701 470! 4701
9901 9901 9901 9901
3508332
12C10
12B15
12C18
12B49
12B50
12B03-1
7B12
12B12
tlB05
12C21
3508332
7B67
12B05
P020500
P107900
P027100
P300500
P322544
7B46
P022800
P024200
P309600
P200200
11C68
P321127
11C63
7A68
7Al17
MODEL:
3508731
12C10
12B15
12C18
12B49
12B50
12B03-1
7B12
12B12
11B05
12C21
3508731
7B57
12B05
P026500
P107900
P027100
P300500
P322544
7S46
P022800
P024200
P309600
P200200
11C68
P321127
11C63
7A68
7A117
3508732
12C10
12B15
12C18
12B49
12B50
12B0_1
7B12
12B12
11B05
12C21
3508732
7B57
12B05
P026500
P107900
P027100
P300500
P322544
7B40
P022800
P024200
P309600
P200200
11C68
P321127
11C63
7A68
7Al17
"_ Not available separately, in kit form only. For part illustration see pages 39 and 40
Note: Screws and bolts are standard hardware items, available locally
(continued on next page)
--41--

Williams Top Vent Gas-Fired Wall Furnace
REPLACEMENT PARTS FOR MODELS 3508531; 3508332; 3508731 AND 5508752
REF.
NO.
36
37
38
39
40
41
41
42
43
44
45
46
47
48
49
NOTE:
PART NO. FOR MODEL:
DESCRIPTION
Valve, WILLIAMS Nat. -- P322043
Valve, WILLIAMS L.P.G. P322044 --
Manifold 12A01 12A01
Orifce Fitting, Specify Model & Gas P090500 P090500
Locknut P026200 P026200
Pilot, Cast Iron Burner, Robertshaw LP.G. P229200 --
Pilot, Cost Iron Burner, Robertshow Net. -- P229100
Pilot, Formed Steel Burner, Robertshaw Nat. -- P229300
Junction Block Thermocouple
Flame Sensor
Burner, Cast Iron, Nat. or L.P.G.
Burner, Formed Steel, Net. Gas Only
Thermostat
Ignition Control
Wire Assembly
Wire Assembly
Manifold Adopter
Ignition Control Shield
Wire Assembly (2 Required)
Ignition Control WIres (Not Shown)
Screws ond bolts are standard hardware items, available locally.
3508331 3508332 3508731 3508732
-- P321828 P321828
P271100 P271100 -- --
P025600 P025600 P025600 P025600
-- 7C52 -- 7C52
P322017 P322017 P322017 P322017
P321910 P321910 -- --
P321522 P321522 -- --
P321935 P321935 -- --
P321887 P321887 P321888 P321888
7C79 7C79 -- --
-- -- P321935 P321935
31B036 31B036 -- --
-- P322041
P322042
12A01 12A01
P090500 P090500
P026200 P026200
P179800
-- P179700
-- P321837
For ports illustration see page 40.
--42--

Williams Top Vent Gas-Fired Wall Furnace
REPAIR PARTS FOR MODELS
5008731; 5008732; 5508331; 5508332; 6508731 and 6508732
CABINET and BODY
ASSEMBLY
16
28 26
1 •
33
34
32
5
8
39
37
36
40
41
USE ONLY MANUFACTURER'S AUTHORIZED PARTS
FOR PARTS LIST SEE PAGES 45 AND 46.
--43--

Williams Top Vent Gas-Fired Wall Furnace
CONTROL ASSEMBLY
FOR MODELS
5008731 and 5008732
6508731 and 6508732
FOR PARTS LISTING SEE PAGE 46
USE ONLY MANUFACTURER'S
AUTHORIZED PARTS
--441
CONTROL ASSEMBLY FOR MODELS-
5508331 and 5508332
FOR PARTS LISTING SEE PAGE 46

Williams Top Vent Gas-Fired Wail Furnace
REPLACEMENTPARTSFORMODELS5008731 5008732; 5508331; 5508332; 6508731 AND 6508732
REF. PART NO. FOR MODEL:
NO. DESCRIPTION
1 Outer Casing, Less Front Panel
2 Inner Liner
3 Heating Element
€ Relief Opening Pan
5 Top Front Panel
6 Center Front Panel
7 Switch Box
8 Limit Switch
9 Selector Switch
10 Fan Switch
11 Bottom Front Panel
12 Element Base Gasket
13 Fan Shroud
14 Relief Pan Gasket
15 Vent Cover
16 Header Gasket (3 Req.)
17 Flue Collar Gasket
18 Header
19 Limit Switch
20 Switch Box Cover
21 Lower Element Base Angle
22 Transformer, 115V/24V
23 Junction Box
2¢ Internal Wires (All Except Ign. ControI
25 Vibration Isolators (4 Req.)
26 Motor Support (2 Req.)
27 Motor
28 Fan Blade
29 Deflector Baffle Handle
30 _ Vent Enclosure Side (2 Req.)
31 _ Vent Enclosure Front
30 _r Vent Enclosure Side (2 Req.)
31 "JrVent Enclosure Front
32 • Rear Grille, Two-Way
33 _r Rear Outer Boot, 10" Long
3¢ _Plaster Ground
35 _Rear Inner Boot, 10-3/4" Long
36 _" Damper
32 _" Rear Grille, Two-Way
33 _'Rear Outer Boot, 7/8" Long
34 _Plaster Ground
35 .kRear Inner Boot, 1-5/8" Long
36 11rDamper
37 _Diffusing Gril]e Kit (Two-Way)
37 _Diffusing Grille Kit (One-Way)
NOTE: Screws and bolts are standard hardware items, available locally.
"k Not available separately, in kit form only.
5008731
7055-4
11B46
7069
7D10
7B126
11060
11B05
P200300
P213400
P200200
11B103
P026500
78106
=028300
7812
7A68
P027100
7811€
P321127
11068
7Al17
P024200
7829
5008731
P022800
7B€6
P062101
P200600
11063
9812
9824
6801
6802
6705
6704
5008732
7055_t
11B46
7C69
7D10
7B126
11060
11B05
P200300
P213400
P200200
11B103
P026500
78106
P028300
7B12
7A68
P027100
78114
P32t127
11068
7Al17
P02€200
7829
5008732
P022800
7846
P062101
P200600
11063
9812
9824
6801
6802
6705
6704 i
5508331 5508332
7C55-3 7C55-3
7879 7B79
7C68 7C68
7D10 7D10
7B126 78126
11059 11C59
11B05 118O5
P296001 P296001
P296201 P296201
P200200 P2O020O
11B103 11B103
P026500 P026500
7B106 78106
P028300 P028300:
7812 7812
7A68 7A68
P027100 P027100
7B57 7B57
P321127 P321127
11068 11068
7Al17 7Al17
P024200 P024200
7B29 7829
5508331 5508332
P022800 P022800
7B46 7846
P062101 P062101
P200600 P200600
11063 11063
9812 9812
9824 9824
6801 6801
6802 6802
6703 6703
6704 6704
6508731 6508732
7C55-3 7C55-3
7879 7B79
7C54-3 7054-3
7D09 7D09
7B126 7B126
11059 11059
11805 11805
P200300 P200300
P296201 P296201
P200200 P200200
11B103 118103
>026500P02650C
78106 78106
P028300 P02830C
7B12 7812
7A68 7A68
P027100 P027100
7857 7B57
P321127 P321127
11068 11068
7Al17 7Al17
P024200 P024200
7B29 7B29
6508731 6508732
P022800 P022800
7846 7B46
P321601 P321601
P014300 P014300
11063 11063
9812 9812
9824 9824
6801 6801
6802 6802
6703 6703
6704 6704
For parts illustration see pages 4.3 and 44.
m45--

Williams Top Vent Gas-Fired Wall Furnace
REPLACEMENT PARTS FOR MODELS 5008731; 5008732; 5508531; 5508332; 6508751 AND 6508732
REF.
NO. DESCRIPTION
38 _ Side Inner Boot, 10-3/4" Long
39 _rSide Outer Boot, 10" Long
40 ,k Side Plaster Ground
41 • Side Grille
38 _r Side Inner Boot, 1" Long
41 _r Side Grille
_" _" Trim Strip Kit (Not Shown)
_" _ Oval B/W Vent Kit (Not Shown)
42 Manifold
4-5 Orifice Fitting, Specify Model& Gas (2 Req.)
44 Locknut (2 Req.)
45 Valve, _LLIAMS Nat.
Valve, WILLIAMS L.P.O.
46 Thermostat
47 Junction Block Thermocouple
47 Flame Sensor
48 Pilot, Cast Iron Burner, Robertshow LP.G.
Pilot, Cast Iron Burner, Robertshaw Net.
Pilot, Formed Steel Burner, Robertshaw Not.
4-9 Burner Spacer, Cast Iron Burner (2 Req.)
Burner Spacer, Formed Steel Burner (2 Req.)
50 Burner, Cost Iron, Nat. or L.P.G. (2 Req.)
Burner,Formed Steel, Nat. Gas Only(2 Req.)
51 Ignition Control
52 Wire Assembly
53 Wire Assembly
54- Wire Assembly (2 Req.)
55 Manifold Adapter
56 Ignition Contro; Shield
57 Ignition Control Wires (Not Shown)
PART NO. FOR MODEL:
5008731
6701
6702
4-701
9901
7B80
P090500
P026200
P32204-2
P322017
P321828
P179800
P018!00
P025600
P322048
P321888
5008732 5508331
6701 6701
6702 6702
4701 4-701
9901 9901
7B80 7B80
P090500 P090500
P026200 P026200
P32204-1 --
-- P322044-
P322017 P322017
P321828 --
-- P271100
-- P229200
P179700 --
P321837 --
P018100 P018100
P230500 --
P025600 P025600
7C52
-- P321910
-- P321524-
-- P32204-8
P32204-8 --
P321888 P321887
-- 7C79
-- 31B036
5508332
6701
6702
4-701
9901
7B80
P090500
P026200
P322043
P322017
P271100
P229100
P229300
P018100
P230500
P025600
7C52
P321910
P321524
P32204-8
P321887
7C79
31B036
6508731
6701
67O2
4-701
9901
7B80
P090500
P026200
P32204-2
P322017
P321828
P179800
P018100
P025600
P322048
P321888
6508732
6701
67O2
4701
9901
7B80
P09050C
P02620C
P322041
P322017
P321828
P179700
P018100
iP025600
P32204-8
P321888
NOTE: Screws and bolts are standard hardware items, available locally.
• " Not available separately, in kit form only.
For parts illustration see pages 4,3 and 44.

Notes

Service Hints
If your furnace fails to work right, you may avoid inconvenience and the cost
of a service call by checking the following points before you call for service.
FOR YOUR SAFETY FOR YOUR SAFETY
owners
manual
SERVICE
MODEL NOS.
3508331
3508332
3508731
3508732
5008731
5008732
5508331
5508332
6508731
6508732
Do not store or use gasoline If you smell gas:
or other flammable vapors and 1. Open windows.
liquids in the vicinity of this or any 2. Don't touch electrical.
other appliance. 4. Immediately call your gas
POSSIBLE CAUSE WHAT TO DO
If fan motor is noisy --
Housing rattling.
Fan dirty.
Fan blade bent.
Motor bearings need oiling.
If fan does not run --
Fuse blown or tripped circuit
breaker.
Motor bearings need oiling.
If your furnace is not heating or
not giving enough heat --
Fuse blown or tripped circuit
breaker.
Thermostat is not set correctly.
Air flow restricted.
3. Extinguish any open flame.
supplier.
Tighten screws.
Clean fan blade.
Replace fan blade.
Oil motor.
Replace fuse or reset breaker.
Oil motor.
Replace fuse or reset breaker.
Reset thermostat to desired
setting.
Check that doors, drapes or
furniture are not blocking
furnace louvers.
If your furnace short cycles --
Thermostat anticipator not set
correctly.
If your furnace pops and cracks --
Heat exchanger expansion and Normal condition, especially
contraction, with newer furnaces.
See troubleshooting section for more detailed information.
How to Order Repair Parts
When ordering repair parts, always give the following
information:
1. MODEL NUMBER
2 MFG. DATE CODE
3 PART NUMBER
4 PART DESCRIPTION
WILLIAMS FURNACE COMPANY
All parts listed herein may be ordered from your equip-
ment supplier.
The Model Number of your Williams wall furnace will be
found on the rating plate near gas valve, inside control
compartment.
225 Acacia Street
Colton, CA 92324 USA
(909) 825-0993
Set anticipator (See Page 20).
MANUFACTURED
IN THE U.S.A.
Established 1916
FAX: (909) 824-8009
©1998 The Williams Furnace Company Rev 6/98 Printed in U.S.A. P321005