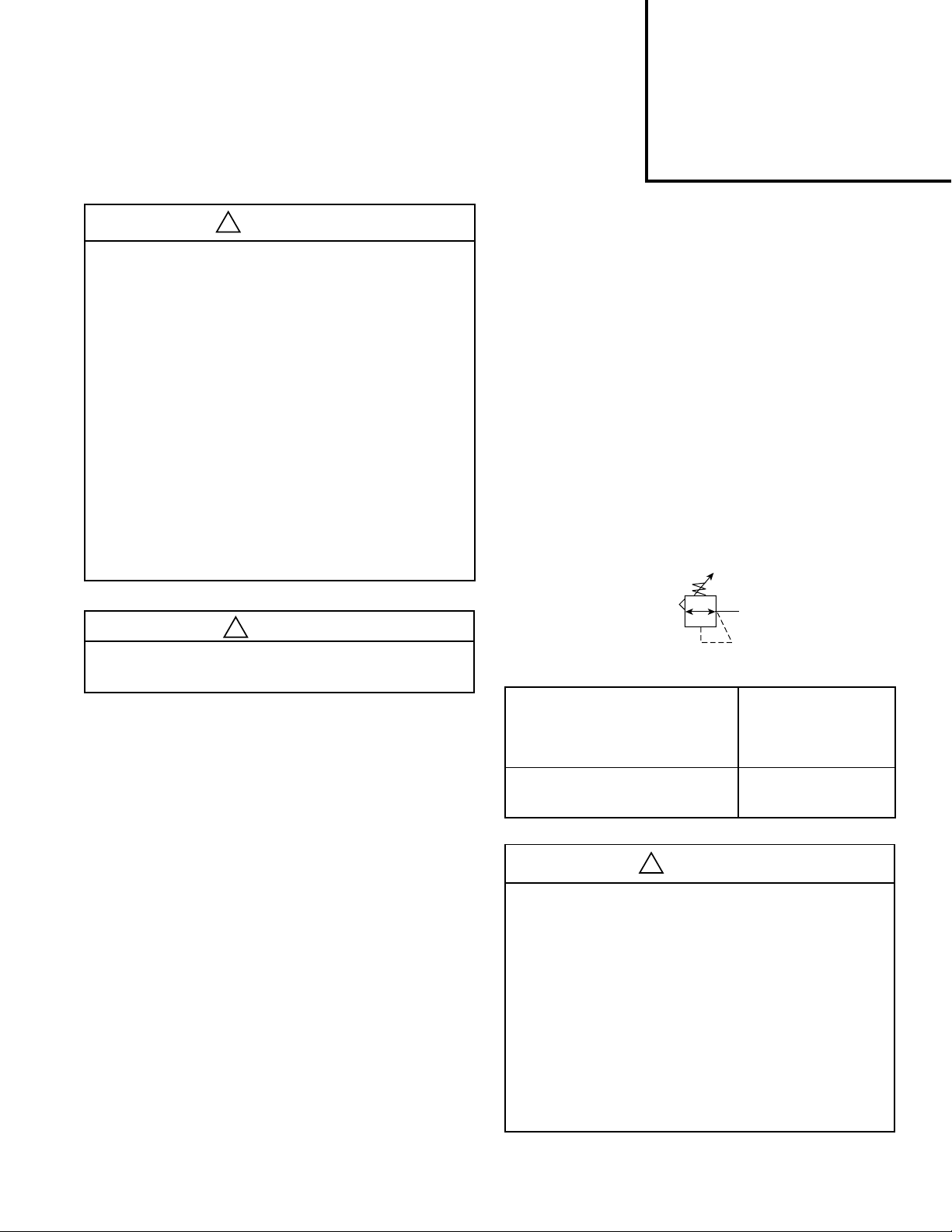
Pneumatic Division
Richland, Michigan 49083
269-629-5000
Installation & Service Instructions:
IS-2R206
High Flow Precision Regulators
ISSUED: July, 2004
Supersedes: April, 2004
Doc.# 2R206, ECN# 040593, Rev. 2
WARNING
!
To avoid unpredictable system behavior that can cause personal
injury and property damage:
• Disconnect electrical supply (when necessary) before
installation, servicing, or conversion.
• Disconnect air supply and depressurize all air lines connected
to this product before installation, servicing, or conversion.
• Operate within the manufacturer’s specified pressure,
temperature, and other conditions listed in these instructions.
• Medium must be moisture-free if ambient temperature is below
freezing.
• Service according to procedures listed in these instructions.
• Installation, service, and conversion of these products must be
performed by knowledgeable personnel who understand how
pneumatic products are to be applied.
• After installation, servicing, or conversion, air and electrical
supplies (when necessary) should be connected and the product
tested for proper function and leakage. If audible leakage is
present, or the product does not operate properly, do not put
into use.
• Warnings and specifications on the product should not be
covered by paint, etc. If masking is not possible, contact your
local representative for replacement labels.
! WARNING
Product rupture can cause serious injury.
Do not connect regulator to bottled gas.
Do not exceed maximum primary pressure rating.
Introduction
Follow these instructions when installing, operating, or servicing
the product.
Application Limits
These products are intended for use in general purpose compressed
air systems only.
Operating Pressure Range: PSIG bar
PRIMARY – Maximum 250 17.24
SECONDARY – Spring Pressure
2 PSIG Minimum 00
Maximum 2 0.14
30 PSIG Minimum 0.5 0.03
Maximum 30 20.70
60 PSIG Minimum 1 0.07
Maximum 60 4.14
150 PSIG Minimum 2 0.14
Maximum 150 10.34
Operating Temperature Range:
-40°C † to 71°C (-40°F to 160°F)
† Temperatures below 0°C (32°F) require moisture free air.
Installation:
1. Regulator should be installed with reasonable accessibility for
service whenever possible — repair service kits are available.
Keep pipe or tubing lengths to a minimum with inside clean
and free of dirt and chips. Pipe joint compound should be
used sparingly and applied only to the male pipe — never into
the female port. Do not use PTFE tape to seal pipe joints —
pieces have a tendency to break off and lodge inside the unit,
possibly causing malfunction.
2. Install regulator so that air flows from “IN” to “OUT” as marked
on the regulator. Installation must be upstream from devices it
is to service (lubricator, valve, cylinder or tool), and mounted
closely to these devices. Mounting may be in any position.
3. Gauge ports are located on both sides of the regulator body
for your convenience. It is necessary to install a gauge or pipe
plug into each port during installation.
4. Remove plastic plug from vent hole in bonnet.
5. For protection against rust, pipe scale and other foreign matter,
install a filter on the upstream (high pressure) side as closely
to the regulator as possible.
ANSI Symbols
Relieving
Service Kits / Accessories:
Relieving Service Kit
0-2 PSIG RKR230E*
0-30 PSIG RKR230B*
1-60 PSIG RKR230C*
2-150 PSIG RKR230D*
Mounting Brackets
Pipe Mounting SA200XW57
Right Angle Mounting 446-707-025
* Parts in Kit.
WARNING
!
FAILURE OR IMPROPER SELECTION OR IMPROPER USE OF THE
PRODUCTS AND/OR SYSTEMS DESCRIBED HEREIN OR RELATED
ITEMS CAN CAUSE DEATH, PERSONAL INJURY AND PROPERTY
DAMAGE.
This document and other information from The Company, its subsidiaries
and authorized distributors provide product and/or system options for
further investigation by users having technical expertise. It is important
that you analyze all aspects of your application, including consequences
of any failure and review the information concerning the product or
systems in the current product catalog. Due to the variety of operating
conditions and applications for these products or systems, the user,
through its own analysis and testing, is solely responsible for making
the final selection of the products and systems and assuring that all
performance, safety and warning requirements of the application are
met.
The products described herein, including without limitation, product
features, specifications, designs, availability and pricing, are subject to
change by The Company and its subsidiaries at any time without notice.
EXTRA COPIES OF THESE INSTRUCTIONS ARE AVAILABLE FOR
INCLUSION IN EQUIPMENT / MAINTENANCE MANUALS THAT UTILIZE
THESE PRODUCTS. CONTACT YOUR LOCAL REPRESENTATIVE.
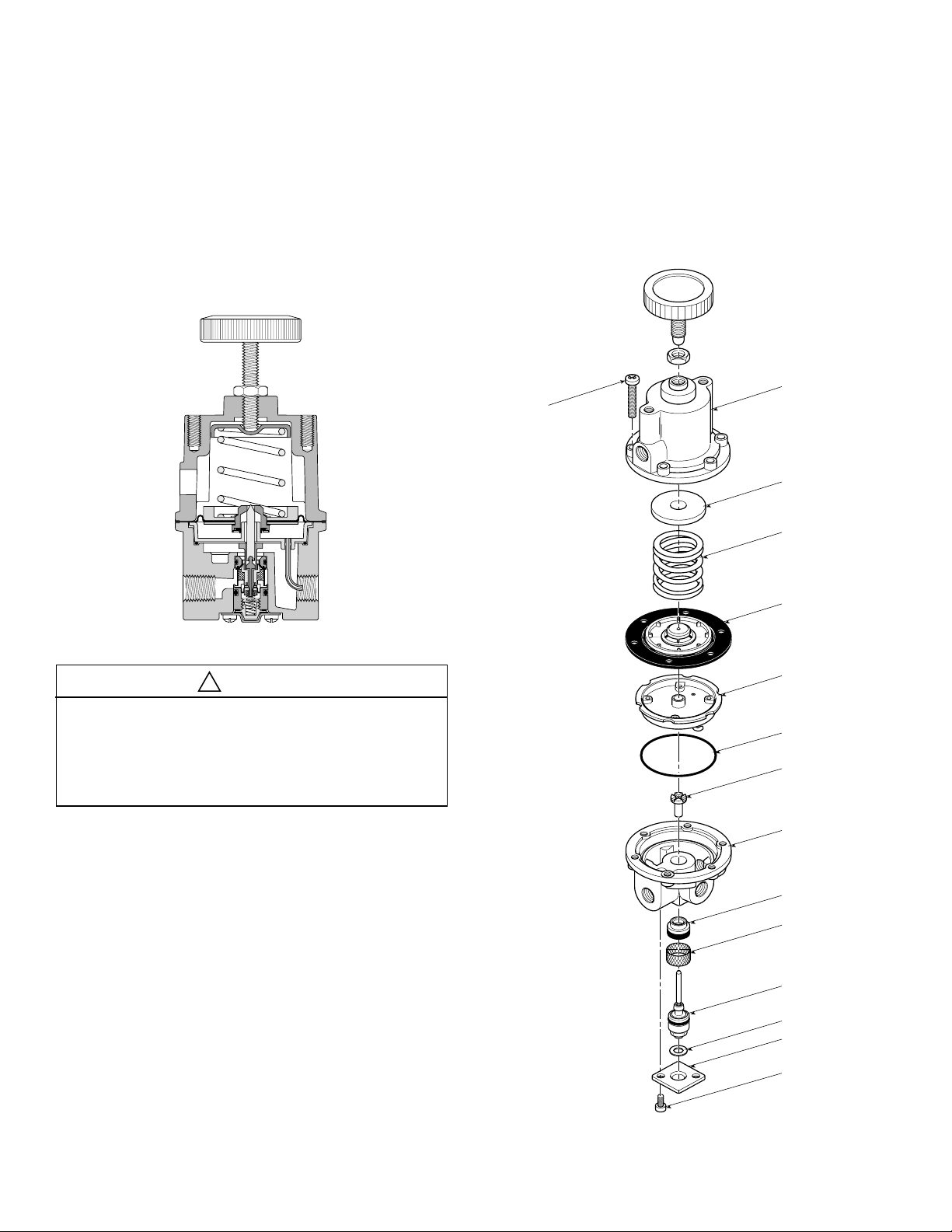
High Flow Precision Regulator IS2R206
Operation
1. Before turning on the air supply, turn the adjusting knob
counterclockwise until compression is released from the control
spring. Then tur n on air supply and adjust regulator to desired
secondary pressure by turning adjusting knob clockwise. This
permits pressure to build up slowly, preventing any unexpected
operation of the valve, cylinders, tools, etc., attached to the line.
Adjustment to desired secondary pressure can be made only
with primary pressure applied to the regulator.
2. To decrease regulator pressure setting, always reset from a
pressure lower than the final setting desired. For example,
lowering the secondary pressure from 5.5 to 4.1 bar (80 to 60
PSIG) is best accomplished by dropping the secondary pressure
to 3.5 bar (50 PSIG), then adjusting upward to 4.1 bar
(60 PSIG).
8. Insert the new inner valve assembly (N) making sure the screen
(M) is centrally located in the groove on the top side of the
valve body. Replace the seal (P) and cap (Q), and securely
tighten using the two #10-32 screws (R) torque 3.2 to 3.6 Nm
(28 to 32 in-lbs).
9. Place the bonnet (C) into position over the spring cap (D) and
reassemble the (6) screws (B). Tighten screws 3.2 to 3.6 Nm
(28 to 32 in-lbs) in progressive steps using a crisscross pattern.
10. Admit inlet pressure and turn the adjusting knob (A) to obtain
the desired pressure.
NOTE:A slight flow of air through the bonnet vent hole is necessary
for proper operation of the regulator.
A
}
C
B
D
IN OUT
Figure 1
CAUTION
!
REGULATOR PRESSURE ADJUSTMENT - The working range
of the knob adjustment is designed to permit outlet pressures
within their full range. Pressure adjustment beyond this
range is also possible because the knob is not a limiting
device. This is a common characteristic of most industrial
regulators, and limiting devices may be obtained only by
special design.
Service: (Always vent all air pressure
before servicing)
1. Turn the control knob (A) fully counterclockwise. Remove
upstream air supply.
2. Remove two # 10-32 screws (R) on the bottom of the regulator
body (K) releasing the seal (P) and cap (Q). Pull out the inner
valve assembly (N) and screen (M). Discard inner valve
assembly and clean screen with mild soap and water.
3. Remove six screws (B) holding the bonnet (C) in place. Remove
bonnet, spring cap (D), spring (E) and diaphragm assembly
(F). Discard diaphragm assembly.
4. Remove the seal plate and jet tube assembly (G) and carefully
lift out the assembly taking precautions not to bend the jet
tube. Remove o-ring (H) and inner valve guide (J).
5. Clean all retained parts with mild soap and water.
6. Assemble the o-ring (H) and inner valve guide (J).
7. Place the new diaphragm assembly (F) over the valve stem
and pilot bushing. Align the screw holes in the diaphragm with
those In the regulator body (K). Place the main spring (E) and
spring cap (D) into position on top of the diaphragm assembly.
E
F*
G
H*
J
K
L
M
N*
P
Q
R
* Parts in Kit
Figure 2