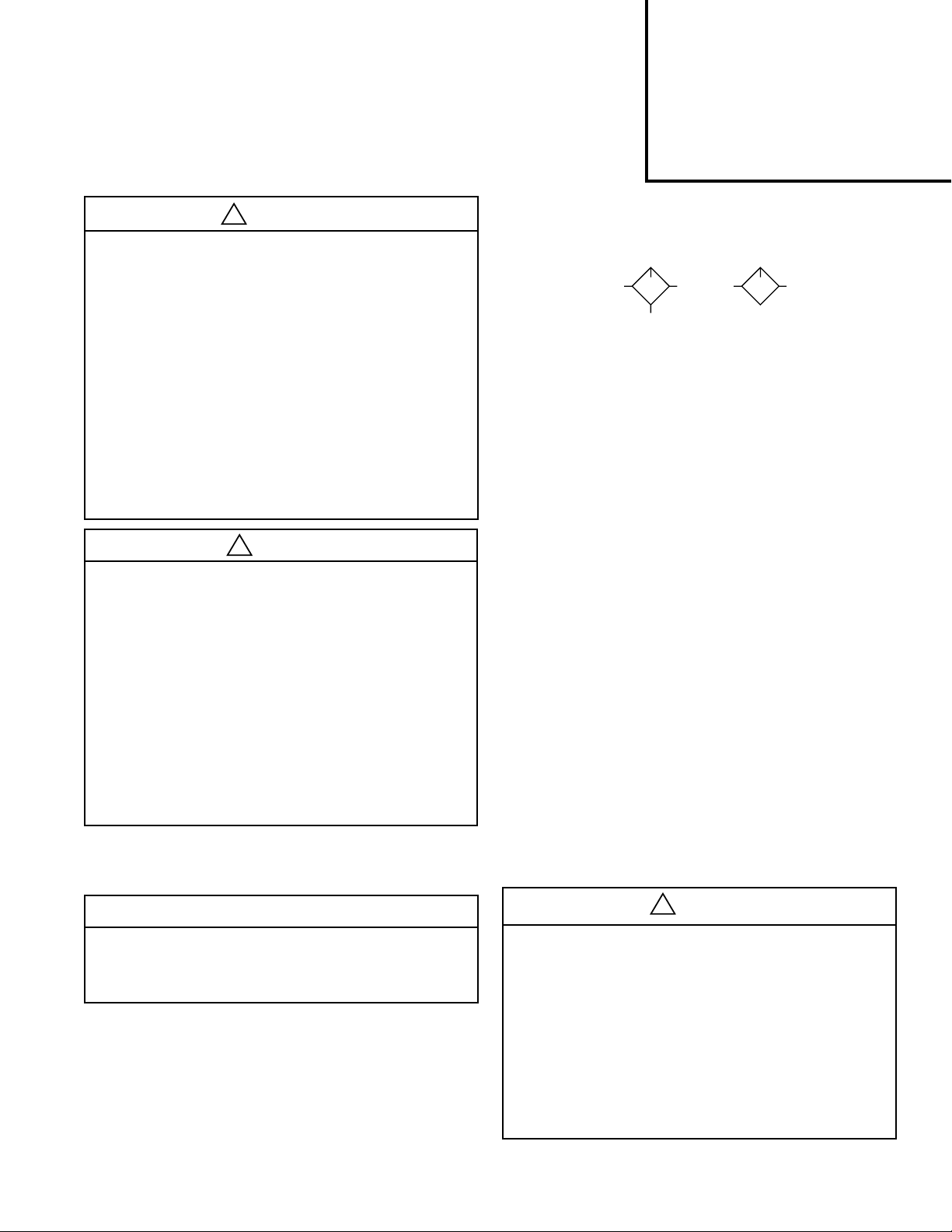
Pneumatic Division
Lubricator
w/ Manual Drain
Lubricator
Less Drain
Richland, Michigan 49083
269-629-5000
Installation & Service Instructions:
2L300C
1" Lubricator Series
ISSUED: August, 2006
Supersedes: November, 2003
Doc.# 2L300, ECN# 060900, Rev. 7
WARNING
To avoid unpredictable system behavior that can cause personal injury
and property damage:
• Disconnect electrical supply (when necessary) before installation,
servicing, or conversion.
• Disconnect air supply and depressurize all air lines connected to this
product before installation, servicing, or conversion.
• Operate within the manufacturer’s specified pressure, temperature,
and other conditions listed in these instructions.
• Medium must be moisture-free if ambient temperature is below
freezing.
• Service according to procedures listed in these instructions.
• Installation, service, and conversion of these products must be
performed by knowledgeable personnel wh o understand how
pneumatic products are to be applied.
• After installation, servicing, or conversion, air and electrical supplies
(when necessary) should be connected and the product tested for
proper function and leakage. If audible leakage is present, or the
product does not operate properly, do not put into use.
• Warnings and specifications on the product should not be covered by
paint, etc. If masking is not possible, contact your local representative
for replacement labels.
CAUTION
Polycarbonate bowls, being transparent and tough, are ideal for use with
Filters and Lubricators. They are suitable for use in normal industrial
environments, but should not be located in areas where they could be
subjected to an impact blow, nor temperatures outside of the rated range.
As with most plastics, some chemicals can cause damage. Polycarbonate
bowls should not be exposed to chlorinated hydro-carbons, ketones,
esters, and certain alcohols. They should not be used in air systems where
compressors are lubricated with fire resistant fluids such as phosphate
esters and di-esters types. In areas where polycarbonate bowls are
exposed to high temperatures or atmospheres containing vapors or fluids,
which are damaging to plastic, use metal bowls.
Metal bowls resist the action of most such solvents but should not be used
where strong acids or bases are present or in salt laden atmospheres.
Consult the factory for specific recommendations where these conditions
exist.
TO CLEAN POLYCARBONATE BOWLS USE MILD SOAP AND WATER
ONLY! DO NOT use cleaning agents such as acetone, benzene, carbon
tetrachloride, gasoline, toluene, etc., which are damaging to this plastic.
Bowl gua rds are recommended for add ed protection of
polycarbonate bowls where chemical attack may occasionally
occur.
Operating Temperature Maximum 80°C (175°F)
Operating Temperature Minimum
0°C (32°F)
ANSI Symbol
Installation
1. The lubricator should be installed with reasonable accessibility
for service whenever possible. Keep pipe or tubing lengths to a
minimum with inside clean and free of dirt and chips. Pipe joint
compound should be used sparingly and applied only to the
male pipe – never into the female port. Do not use PTFE tape
to seal pipe joints – pieces have a tendency to break off and
lodge inside the unit, possibly causing malfunction.
2. Install lubricator so air flows in the direction of arrow on body.
3. Installation should be upstream of the device it is to lubricate
(valve, cylinders, tool, etc.).
Operation and Service
(Refer to Pictorial on Following Page)
1. Filling — The Mist lubricator can be filled without turning off
the upstream pressure. Slowly remove the fill plug by turning
counterclockwise. This allows the bowl pressure to vent.
Suggested lubricant: F442
Petroleum based oil of 100 to 200 SUS viscosity at 100°F and
an aniline point greater than 200°F. (Mobil DTE24 and Sun
Company Sunvis 932 are good examples). Do not use oils
with adhesives, compound oils containing solvents, graphite,
detergents or synthetic oils.
2. Replace the fill plug (by turning clockwise) and seat firmly.
Excessive torque is not required. If leakage occurs, DO NOT
OPERATE — conduct repairs again.The lubricator is now
ready for setting.
3. Oil delivery adjustment — To adjust oil delivery, turn adjustment
knob on top of the lubricator.
Safety Guide
For more complete information on recommended application
guidelines, see the Safety Guide section of Pneumatic Division
catalogs or you can download the Pneumatic Division Safety
Guide at: www.parker.com/safety
Introduction
Follow these instructions when installing, operating, or servicing
the product.
Application Limits
These products are intended for use in general pur pose
compressed air systems only.
kPa PSIG bar
Operating Pressure Maximum 1700 250 17.0
WARNING
FAILURE OR IMPROPER SELECTION OR IMPROPER USE OF THE
PRODUCTS AND/OR SYSTEMS DESCRIBED HEREIN OR RELATED ITEMS
CAN CAUSE DEATH, PERSONAL INJURY AND PROPERTY DAMAGE.
This document and other information from Parker Hannifin Corporation, its
subsidiaries and authorized distributors provide product and/or system options
for further investigation by users having technical expertise. It is impor tant
that you analyze all aspects of your application, including consequences of
any failure and review the information concerning the product or systems
in the current product catalog. Due to the variety of operating conditions
and applications for these products or systems, the user, through its own
analysis and testing, is solely responsible for making the final selection of the
products and systems and assuring that all performance, safety and warning
requirements of the application are met.
The products described herein, including without limitation, product features,
specifications, designs, availability and pricing, are subject to change by Parker
Hannifin Corporation and its subsidiaries at any time without notice.
EXTRA COPIES OF THESE INSTRUCTIONS ARE AVAILABLE FOR INCLUSION
IN EQUIPMENT / MAINTENANCE MANUALS THAT UTILIZE THESE PRODUCTS.
CONTACT YOUR LOCAL REPRESENTATIVE.
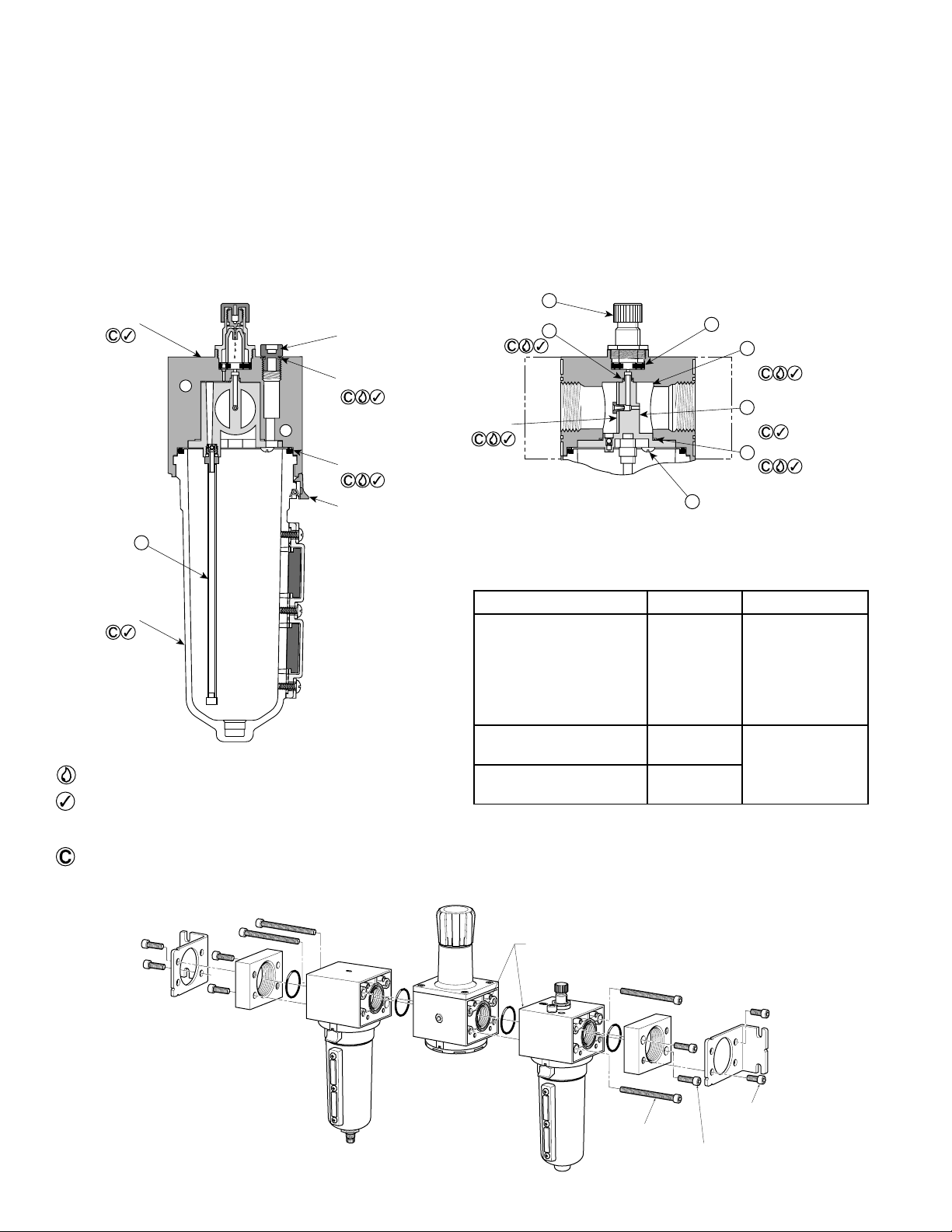
O
I
L
Torque value for assembling
units together, port blocks,
and mounting brackets:
5 to 6 Nm (48 to 52 in.lb.)
M8 x 90 Bolt
(4 Places)
Note: If both mating faces have
an o-ring groove, units may need
to be assembled with two seals.
( One square and one round seal.)
M8 x 15 Bolt
(4 Places)
M8 x 20 Bolt
(4 Places)
Bowl Seal
O Ring
Fill Plug
Hand Tighten
Drip Control
Torque:
Flapper
Insert
Assembly
Body
O Ring
Seal Plate
Bowl
Screws
Torque:
1.5 to 2 Nm
(13 to 18 in.lb.)
Snap Fit Tab
Detent must snap
in groove for proper
assembly
(To remove bowl
depress tab, turn
& pull bowl down)
Tube
6
7
8
5
2
Seal
(Not Shown)
3
Seal
1
4
1" Lubricator Series 2L300C
Leaner — Clockwise
Richer — Counterclockwise
By counting the number of drops per minute in the sight dome,
you can adjust to your requirements.
Mist lubricator — Every drop visible in the sight dome goes
downstream.
Generally, one drop per minute downstream for every
10 - 15 SCFM flow is satisfactory.
25 drops per minute equals one (1) ounce per hour - volume
of oil passing through the sight dome.
NOTE: This is a constant density type lubricator which
delivers a constant ratio of oil air flow. Therefore, if
air flow incr eases o r decreases, o il deli very will be
adju s t e d propor tionately. ONLY IF A DI F FERENT
RATIO IS DESIRED SHOULD YOUR ADJUSTMENT KNOB
SETTING BE CHANGED AFTER YOUR INITIAL SETTING.
4. To replace fill plug, drip control, & service lubricator:
A. Turn off air supply and depressurize the unit.
B. Refer to pictorial for servicing and torque values.
C. Turn on air supply and check lubricator for leakage. If
leakage occurs, DO NOT OPERATE — conduct repairs
again.
Lightly grease with provided lubricant.
In spe c t for ni ck s, scratc hes , a nd sur fa ce imp erfect ion s.
If present, reduced service life is probable and future replacement
should be planned.
Clean with lint-free cloth.
Service Kits Available
Description Kit Number Contains Items
Lubricator Repair Kit P3NKA00RL
Sight Dome / Drip Control
(Polycarbonate)
Sight Dome / Drip Control
(Polyamide / Nylon)
PS740
PS740N
(1) Seal,
(2) O-Ring,
(3) Seal (Not Shown),
(4) Screws,
(5) Insert Assembly
(Including Flapper),
and (6) Tube
(7) Drip Control,
(8) Seal Plate