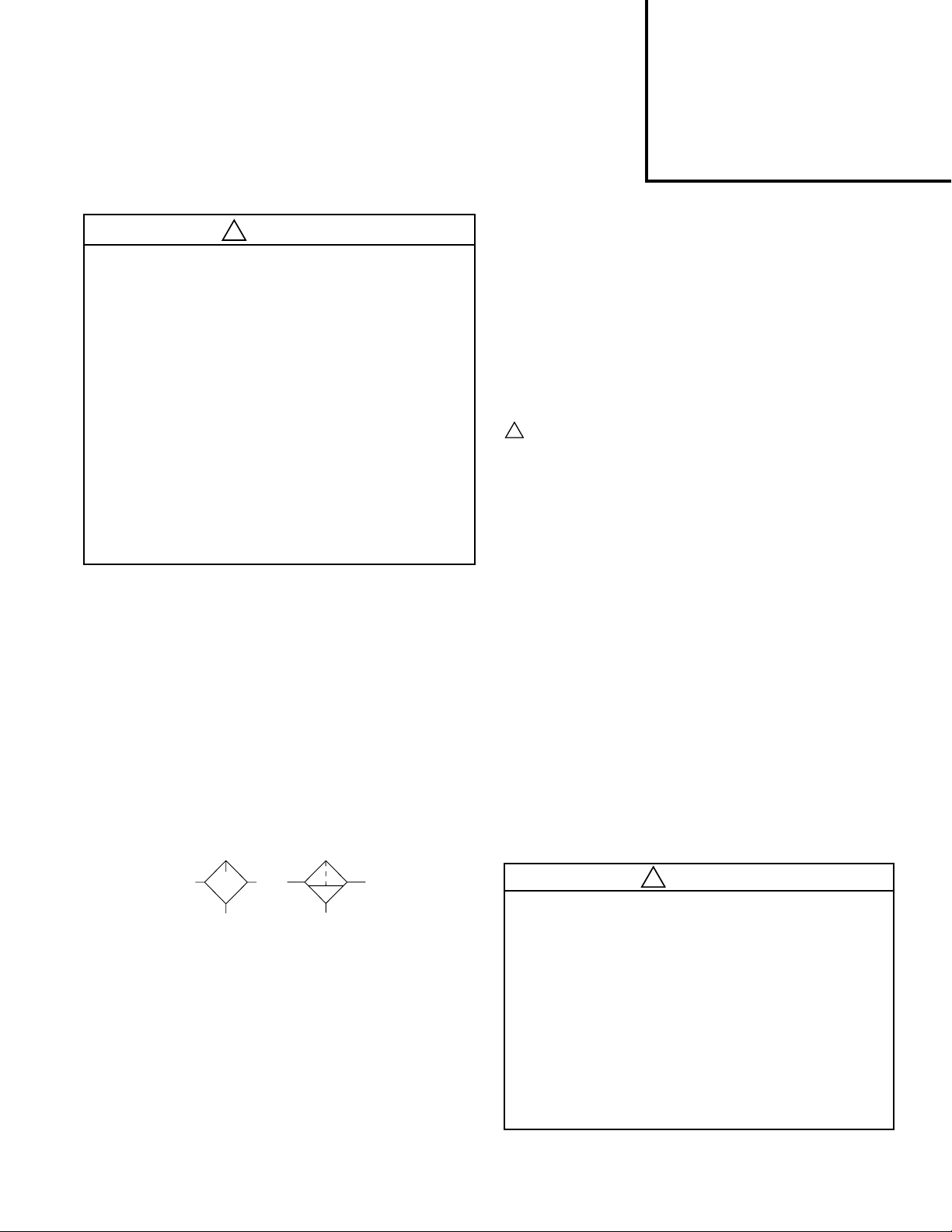
Particulate FilterLubricator
Pneumatic Division
Richland, Michigan 49083
269-629-5000
Installation & Service Instructions:
1M301
Miniature Series Mist Lubricators
& Particulate Filters
ISSUED: April, 2013
Supersedes: November, 2003
Doc# 1M301, EN# 130068, Rev. 3
!
WARNING
To avoid unpredictable system behavior that can cause personal
injury and property damage:
• Di sco nnect el ectri cal supp ly (w hen n ece ssary ) before
installation, servicing, or conversion.
• Disconnect air supply and depressurize all air lines connected
to this product before installation, servicing, or conversion.
• Op era te withi n t he manufact ure r’s speci fie d press ure ,
temperature, and other conditions listed in these instructions.
• Medium must be moisture-free if ambient temperature is below
freezing.
• Service according to procedures listed in these instructions.
• Installation, service, and conversion of these products must be
performed by knowledgeable personnel who understand how
pneumatic products are to be applied.
• After installation, servicing, or conversion, air and electrical
supplies (when necessary) should be connected and the product
tested for proper function and leakage. If audible leakage is
present, or the product does not operate properly, do not put
into use.
• Warnings and specifications on the product should not be
covered by paint, etc. If masking is not possible, contact your
local representative for replacement labels.
Introduction
Follow these instructions when installing, operating, or servicing the
product.
Application Limits
These products are intended for use in general purpose compressed
air systems only.
Operating Inlet Pressure:
kPa PSIG bar
with Polycarbonate Bowl 1000 150 10.3
with Metal Bowl 1700 250 17.0
NOTE: The maximum recommended pressure drop for a particulate
filter is 70 kPa (10 psig, 0.7 bar)
Ambient Temperature Range:
with Polycarbonate Bowl 0°C to 52°C (32°F to 125°F)
with Metal Bowl 0°C to 80°C (32°F to 175°F)
Symbols
2. Install lubricator so that air flow is in the direction of arrow on body.
3. Installation should be upstream from, and as close as possible, to
the device it is to lubricate (valve, cylinder, tool, etc.). Whenever
possible, avoid locations that require air-borne oil to move in an
upward direction to reach the device to be lubricated.
4. The installation of an individual lubricator for each air consuming
device provides best assurances of proper lubrication.
5. In new installations, it is good practice to “wet down” the inside
diameter of piping and/hose with oil before making final connections.
Although your lubricator delivers oil to the line, pre-coating the inside
diameter with oil helps insure that proper amounts of oil are delivered
to the point of application.
Operation & Service of Lubricator
Warning: Before filling, inlet pressure must be eliminated
!
and then de-pressurize system pressure.
1. FILLING - After de-pressurizing system, remove bowl to refill
lubricator. Fill bowl to fill line indicated on the bowl with oil of 150 to
200 SSU at 100°F viscosity - same as SAE No. 10 (petroleum based
hydraulic oils or spindle oils are good examples). DO NOT USE
OILS WITH TACKY ADDITIVES, COMPOUND OILS CONTAINING
SOLVENTS, GRAPHITE, SOAPS OR DETERGENTS. (Automotive
oils generally contain detergents and are not recommended.
2. Replace the bowl and seat firmly. Excessive torque is not necessary.
The lubricator is now ready for setting.
3. OIL DELIVERY ADJUSTMENT - To adjust oil delivery, turn the
adjusting needle on top of the lubricator.
Leaner - Clockwise Richer - Counterclockwise
By counting the number of drops per minute in the sight dome, you can
adjust lubricator to your required setting.
Generally, one drop per minute downstream for every 10-15 SCFM flow
is satisfactory. 25 drops per minute equals one ounce per hour - volume
of oil passing through the sight dome.
NOTE: This is a constant density type lubricator which delivers a
constant ratio of oil to air flow. Therefore, if air flow increases
or decreases, oil delivery will be effected propor tionately.
ONLY IF DIFFERENT RATIO IS DESIRED SHOULD YOUR
ADJUSTMENT KNOB SETTING BE CHANGED AFTER YOUR
INITIAL SETTING.
Mist Lubricators (Figure 1)
Description
These mist lubricators are designed to deliver an atomized oil mist to
air operated tools, motors, and other pneumatic equipment. Units are
equipped with full-view sight glass for visual indication of oil drop rate,
needle valve feed adjustment to regulate oil drop rate, and a venturi
bypass disc to compensate for changes in air flow demands.
Installation of Lubricator
1. Lubricator should be installed with reasonable accessibility for
service whenever possible - repair service kits are available. Keep
pipe and tubing lengths to a minimum with inside clean and free of
dirt and chips. Pipe joint compounds should be used sparingly and
applied only to the male pipe – never into the female port. Do not
use PTFE tape to seal pipe joints - pieces have a tendency to break
off and lodge inside the unit, possibly causing malfunction.
WARNING
!
FAILURE OR IMPROPER SELECTION OR IMPROPER USE OF
THE PRODUCTS AND/OR SYSTEMS DESCRIBED HEREIN OR
RELATED ITEMS CAN CAUSE DEATH, PERSONAL INJURY AND
PROPERTY DAMAGE.
This document and other information from The Company, its subsidiaries
and authorized distributors provide product and/or system options for
further investigation by users having technical expertise. It is important
that you analyze all aspects of your application, including consequences
of any failure and review the information concerning the product or
systems in the current product catalog. Due to the variety of operating
conditions and applications for these products or systems, the user,
through its own analysis and testing, is solely responsible for making
the final selection of the products and systems and assuring that all
performance, safety and warning requirements of the application are met.
The products described herein, including without limitation, product
features, specifications, designs, availability and pricing, are subject to
change by The Company and its subsidiaries at any time without notice.
EXTRA COPIES OF THESE INSTRUCTIONS ARE AVAILABLE FOR
INCLUSION IN EQUIPMENT / MAINTENANCE MANUALS THAT UTILIZE
THESE PRODUCTS. CONTACT YOUR LOCAL REPRESENTATIVE.
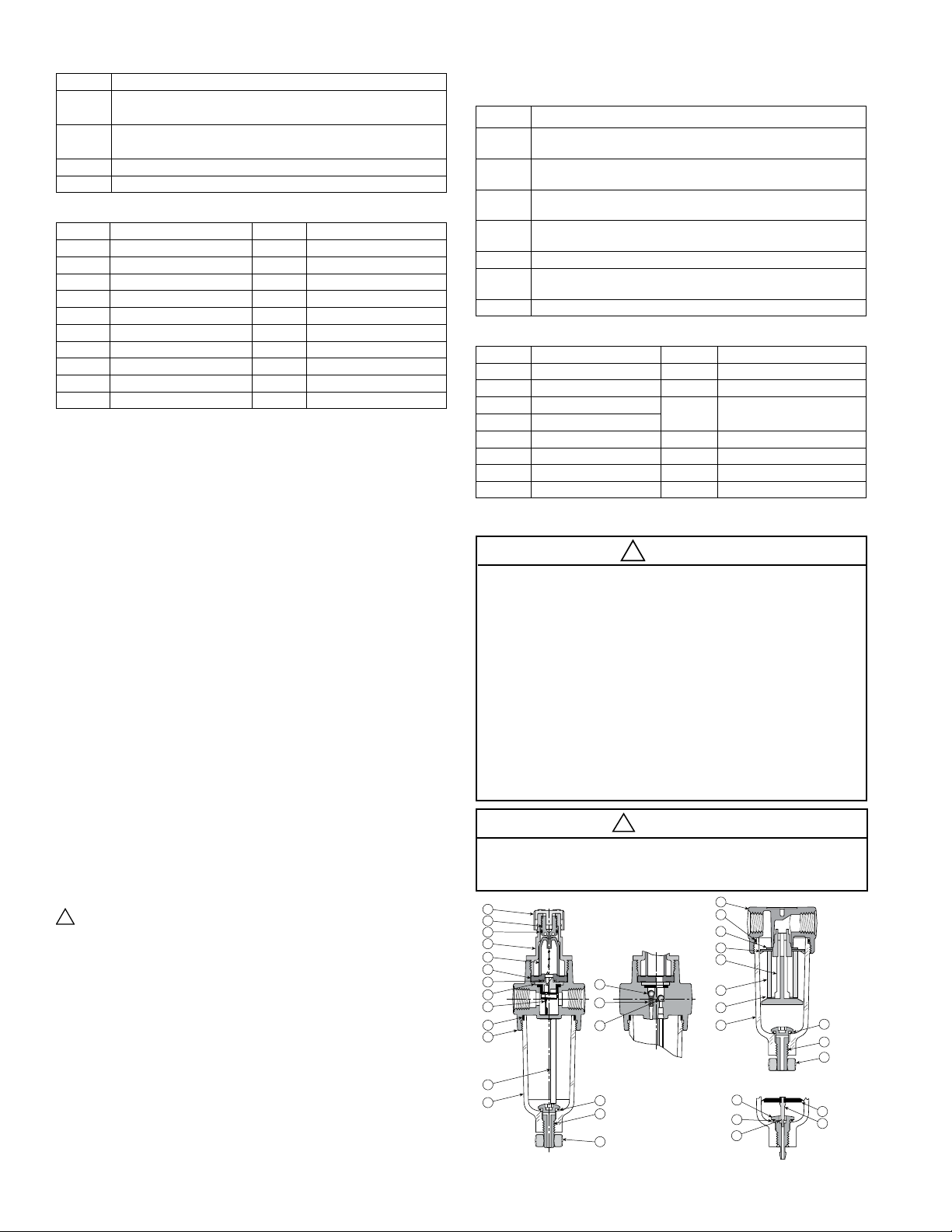
Mist Lubricator & Particulate Filters Series 1M301
Service Kits - Lubricator
Kit# Description
PS420
PS421
Polycarbonate Bowl with Manual Drain - consists of items:
18 (open bottom), 15, 16, 17 & 32
Polycarbonate Bowl without Drain - consists of items:
18 (closed bottom) & 15
PS740 Drip Control (Polycarbonate)
PS740N Drip Control (Nylon)
Parts Identification List - Lubricator
Item# Description Item# Description
1 Knob 11 Spring
2 Drip Control Body 12 Ball, Check
3 Needle 13 Body
4 O-ring 14 Tube
5 Drip Tube 15 O-ring (Body to Bowl)
6 Seal Plate 16 Twist Drain
7 O-ring 17 O-ring (Drain)
8 By-pass Plate 18 Bowl
9 By-pass 32
Twist Drain Knob
10 Ball, Check
Particulate Filter (Figure 2)
Description
These air line filters are heavy-duty units used to remove airborne
impurities from air supply lines by means of centrifugal force and
filter element. Units are equipped with vane-type deflectors and drain
valves. Deflector plate creates swirling action to the air stream assuring
entrainments separation at all flow rates. Filter element with extra large
surface assures fine filtration with low pressure drop. Turn manual drain
clockwise to open and counterclockwise to close.
Installation of Filter
1. Filter should be installed with reasonable accessibility for service
whenever possible - repair service kits are available. Keep pipe and
tubing lengths to a minimum with inside clean and free of dirt and
chips. Pipe joint compounds should be used sparingly and applied
only to the male pipe - never into the female port. Do not use PTFE
tape to seal pipe joints - pieces have a tendency to break off and
lodge inside the unit, possibly causing malfunction.
2. Install unit so that air flow is in the direction of arrow. Installation must
be upstream of and close to devices it is to service (valve, cylinder,
tool, etc.). Position unit vertically with the bowl drain mechanism at
the bottom. Free moisture will thus drain into the sump (“quiet zone”)
at the bottom of the bowl.
Operation of the Filter
1. Both free moisture and solids are removed automatically by
the filter.
2. Manual drain filters must be drained regularly before the separated
moisture and oil reaches the bottom of the element holder. Automatic
drain models (pulse drain) will collect and dump liquids automatically.
They are actuated when a pressure drop occurs within the filter.
3. The filter element should be removed and replaced when the
pressure differential across the filter exceeds 70 kPa (10 psig, 0.7
bar).
Service
Caution: SHUT OFF AIR SUPPLY and exhaust the primary and
!
secondary pressure before dis-assembling unit. (Units may be
serviced without removing them from the air line.)
Servicing Filter Element
1. Unscrew threaded bowl and element holder. Then remove filter
element, deflector, and gaskets.
2. Clean all internal parts, bowl, and body before re-assembling unit.
See Polycarbonate bowl cleaning section.
3. Install deflector, filter element, and gaskets.
4. Attach element holder. Torque from 0.9 to 1.4 Nm (8 to 12 in-lbs).
5. To assist with retaining bowl’s o-ring while installing bowl, lubricate
the o-ring (with a mineral based oil or grease). Then place on
the bowl.
6. Screw bowl into the body until it is stopped by body; then back off
bowl 1/8 turn.
7. Apply pressure to the system and check for leaks. If leaks occur, shut
off the air supply, de-pressurize the system and make necessary
adjustments to eliminate leakage.
If you have questions concerning how to service this unit, contact your
local dealer or your customer service representative.
Service Kits- Filter
Kit# Description
PS404
PS408
PS447B
PS451
Polycarbonate Bowl with Manual Drain - consists of items:
19, 24, 26 & 27
Polycarbonate Bowl with Automatic Drain - consists of items:
19, 24, 26, 28, 29, 30 & 31
Metal Bowl with Manual Drain - consists of items:
19, 24, 26 & 27
Metal Bowl with Automatic Drain - consists of items:
19, 24, 26, 28, 29, 30 & 31
PS403 5 Micrometer Element Kit - consists of items: 20, 21 & 24
PS407
5 Micrometer Element Car tridge Kit - consists of items:
20, 21, 22, 23 & 24
PS401 40 Micrometer Element Kit - consists of items: 20, 21 & 24
Parts Identification List - Filter Units
Item# Description Item# Description
19 Bowl 27 Manual Drain (twist style)
20 Gasket 28 O-ring - pulse drain
21 Filter Element
22 Filter Holder
Drain (body of pulse
29
drain shown)
23 Deflector 30 Diaphragm
24 O-ring (body to bowl) 31 Pin
25 Body 32 Twist Drain Knob
26 O-ring (drain to bowl)
Safety: Transparent Bowls
CAUTION
!
Polycarbonate bowls, being transparent and tough, are ideal for use with
Filters and Lubricators. They are suitable for use in normal industrial
environments, but should not be located in areas where they could be
subjected to direct sunlight, an impact blow, nor temperatures outside of
the rated range. As with most plastics, some chemicals can cause damage.
Polycarbonate bowls should not be exposed to chlorinated hydrocarbons,
ketones, esters and certain alcohols. They should not be used in air systems
where compressors are lubricated with fire-resistant fluids such as phosphate
ester and diester types.
Metal bowls are recommended where ambient and/or media conditions are
not compatible with polycarbonate bowls. Metal bowls resist the action of
most such solvents, but should not be used where strong acids or bases
are present or in salt laden atmospheres. Consult the factory for specific
recommendations where these conditions exist.
TO CLEAN POLYCARBONATE BOWLS USE MILD SOAP AND WATER
ONLY! DO NOT use cleansing agents such as acetone, benzene, carbon
tetrachloride, gasoline, toluene, etc., which are damaging to this plastic.
WARNING
To avoid polycarbonate bowl rupture that can cause personal injury or
property damage, do not exceed bowl pressure or temperature ratings.
Polycarbonate bowls have a 150 PSIG pressure rating and a maximum
temperature rating of 125°F.
1
3
4
2
5
6
7
8
9
15
13
14
18
Torque Bowl
to bottom stop,
then back off
Bowl 22 to 45
Figure 1: Mist Lubricator Figure 2: Particulate Filter
10
11
12
17
16
TORQUE:
finger tight
32
25
24
20
23
22
TORQUE:
8 - 12 in-lbs
21
20
19
Torque bowl to
bottom stop,
then back off
bowl 22 to 45
TORQUE:
1 - 3 in-lbs
26
TORQUE:
27
finger tight
32
29
26
28
30
31