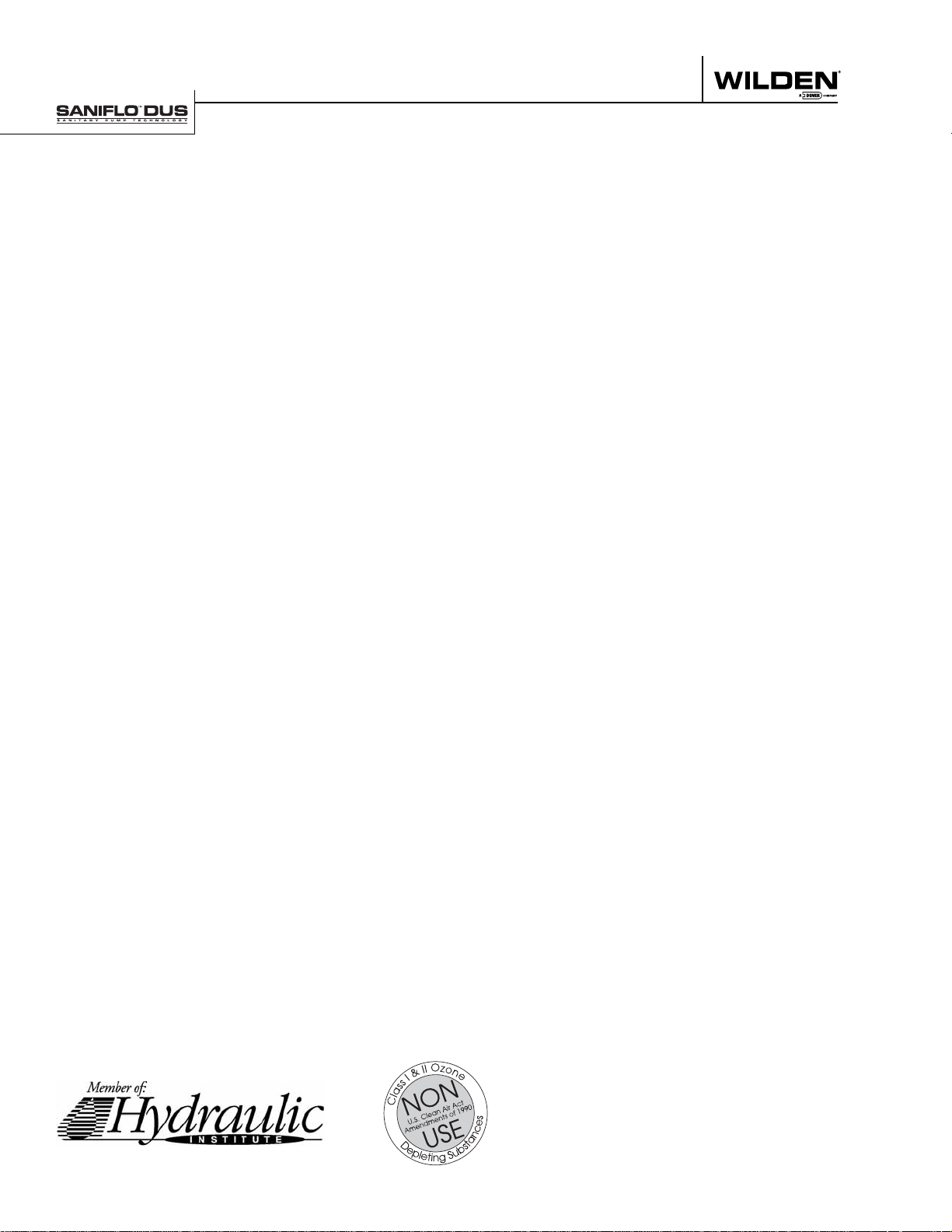
TABLE OF CONTENTS
SECTION 1 CAUTIONS—READ FIRST! . . . . . . . . . . . . . . . . . . . . . . . . . . . . . . . . . . . . . . . . . . . . . .1
SECTION 2 DESIGNATION SYSTEM. . . . . . . . . . . . . . . . . . . . . . . . . . . . . . . . . . . . . . . . . . . . . . . . .2
SECTION 3 DIMENSIONAL DRAWINGS . . . . . . . . . . . . . . . . . . . . . . . . . . . . . . . . . . . . . . . . . . . . .3
SECTION 4 TROUBLESHOOTING . . . . . . . . . . . . . . . . . . . . . . . . . . . . . . . . . . . . . . . . . . . . . . . . . . . .4
SECTION 5 ASSEMBLY . . . . . . . . . . . . . . . . . . . . . . . . . . . . . . . . . . . . . . . . . . . . . . . . . . . . . . . . . . . . . 5
SECTION 6 OPERATION . . . . . . . . . . . . . . . . . . . . . . . . . . . . . . . . . . . . . . . . . . . . . . . . . . . . . . . . . . .13
SECTION 7 CLEANING . . . . . . . . . . . . . . . . . . . . . . . . . . . . . . . . . . . . . . . . . . . . . . . . . . . . . . . . . . . .17
SECTION 8 SCHEMATICS
A. Control Box . . . . . . . . . . . . . . . . . . . . . . . . . . . . . . . . . . . . . . . . . . . . . . . . . . . . . . . . . .20
B. Hoses . . . . . . . . . . . . . . . . . . . . . . . . . . . . . . . . . . . . . . . . . . . . . . . . . . . . . . . . . . . . . . .21
SECTION 9 EXPLODED VIEW & PARTS LISTING . . . . . . . . . . . . . . . . . . . . . . . . . . . . . . . . . . . .22
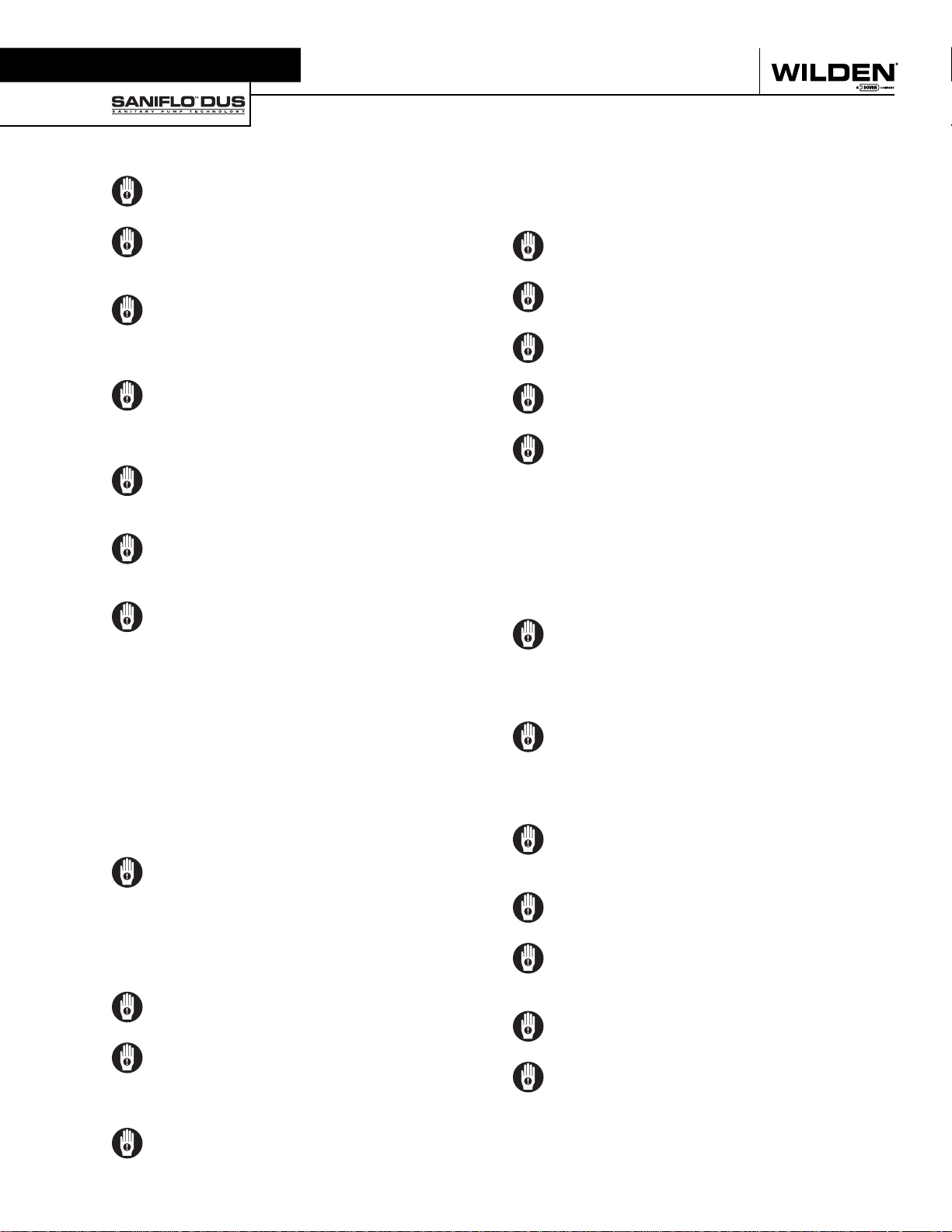
Section 1
CAUTIONS—READ FIRST!
Drum Unloader System
CAUTION : Always wear safety glasses and appropriate safety
gear when operating the Sanifl o™ DUS unit.
CAUTION : Always perform an inspection of the entire system
before each use. Ensure that all parts are in good working
condition and do not show signs of wear.
WARNING: Prior to installing a Sanifl o™ DUS in to an
application, you must fi rst ensure that the DUS components
are compatible with the process media and any cleaning or
sanitation products.
WARNING: Never attempt to modify the Sanifl o™ DUS unit.
Modifi cation will change the dynamics of the DUS and could
damage the unit, result in failure of the unit, or cause harm to
anyone in the area.
CAUTION : Always disconnect the main air supply to the
Sanifl o™ DUS before service or repairs are attempted. Failure
to do so could result in harm to anyone in the area.
CAUTION : The Sanifl o™ DUS unit must be properly secured
while in use. Failure to properly secure the system while in use
could result in harm to anyone in the area.
CAUTION : When using the Sanifl o™ DUS unit, it is extremely
important to note that the retracting downward movement can
cause a pinch point at two areas of the unit.
1. A pinch point is located at the bottom of the structure when
the ram plate is lowered to the base assembly. To avoid injury
to anybody operating this equipment or to anyone in the area
of the equipment, keep hands, arms and head clear of plate
and drum edge.
2. Another pinch point is located at the area where the ram
support bar comes in the vicinity of the header plate. To avoid
injury t o anyb ody operating this e quipment or to anyone in th e
area of the equipment when it is in operation, a safe distance
must be kept from the ram support bar/header plate area.
CAUTION : Do not exceed 8.6 bar (125 psig) air pressure to the
Sanifl o™ DUS unit .
Do not exceed 1.7 bar (25 psig) air pressure to the RAM DOWN.
For normal operation, 1.0 bar (15 psig) is suggested.
Do not exceed 5.5 bar (80 psig) air pressure to the RAM UP. For
normal operation, 4.1 bar (60 psig) is suggested.
CAUTION : Before attaching an air source to the DUS unit,
inspect all hose connections to ensure they are secure.
CAUTION : Before operating Sanifl o™ DU S unit, a t t ach d rum
retention hooks to secure drum during operation. Failure to
do so will result in drum being moved and/or lifted when ram
assembly is moved upward.
WARNING: It is important to follow the assembly instructions
provided when building the Sanifl o™ DUS unit. Altering the
steps or changing the process may result in operation
issues including improper rise and fall of the follower plate
assembly.
Pump
NOTE: Pump not included with Sanifl o™ DUS. Pump sold
separately.
CAUTION : Do not apply compressed air to the exhaust port
– pump will not operate.
CAUTION : Do not exceed 8.6 bar (125 psig) air supply
pressure.
CAUTION : Do not over-lubricate air supply. Excessive
lubrication will reduce pump performance.
TEMPERATURE LIMITS:
Neoprene –17.7°C to 93.3°C 0°F to 200°F
Buna-N –12.2°C to 82.2°C 10°F to 180°F
EPDM –51.1°C to 137.8°C –60°F to 280°F
Viton
Sanifl ex™ –28.9°C to 104.4°C –20°F to 220°F
Polytetrafl uoroethylene (PTFE)
4.4°C to 104.4°C 40°F to 220°F
Polyurethane –12.2°C to 65.6°C 10°F to 150°F
®
–40.0°C to 176.7°C –40°F to 350°F
CAUTION: Maximum temperature limits are based upon
mechanical stress only. Certain chemicals will signifi cantly
reduce maximum safe operating temperatures. Consult
Chemical Resistance Guide (E4) for chemical compatibility and
temperature limits.
WARNING: Prevention of static sparking – if static sparking
occurs, fi re or explosion could result. Pump, valves, and
containers must be grounded to a proper grounding point
when handling fl ammable fl uids and whenever discharge of
static electricity is a hazard.
CAUTION : The process fl uid and cleaning fl uids must be
chemically compatible with all wetted pump components.
Consult Chemical Resistance Guide (E4).
CAUTION : Do not exceed 82.2°C (180.0°F) air inlet temperature
for Pro-Flo V™ models.
CAUTION : Pumps should be thoroughly fl ushed before
installing into process lines. FDA and USDA approved pumps
should be cleaned and /or sanitized before use.
CAUTION : If diaphragm rupture occurs, material being pumped
may be forced out air exhaust.
CAUTION : Before any maintenance or repair is attempted, the
compressed air line to the pump should be disconnected and
all air pressure allowed to bleed from pump. Disconnect all
intake, discharge and air lines. Drain pump by turning it upside
down and allowing any fl uid to fl ow into a suitable container.
WIL-12070-E-03 1 WILDEN PUMP & ENGINEERING, LLC

Section 2
WILDEN DESIGNATION SYSTEM
DRUM UNLOADER
SYSTEM
LEGEND
SANIFLO
MODEL
DUS = DRUM UNLOADER
SYSTEM
PUMP SIZE
4 = 38 mm (1-1/2”) ORIGINAL
SERIES
PUMP TYPE
S = SIMPLEX SINGLE ACTING
D = DUPLEX DOUBLE ACTING
TM
DUS MATERIAL CODES
DUSXX/ XXXX / XXX/ XXXX
MODEL
DRUM SIZE
PUMP SIZE GASKET MATERIAL
PUMP TYPE FRAME MATERIAL
FOLLOW PLATE MATERIAL
CYLINDER MATERIAL
BASE TYPE
BASE TYPE
F = FLOOR MOUNTED
B = BASE PLATE MOUNTED
CYLINDER MATERIAL
S = STAINLESS STEEL
FOLLOW PLATE MATERIAL
S = STAINLESS STEEL
SPECIALTY CODE
FRAME MATERIAL
S = STAINLESS STEEL
GASKET MATERIAL
FB = SANITARY BUNA-N
DRUM SIZE (DIA.)
K = 533 - 557 mm (21.0”-21.9”)
L = 558 - 582 mm (22.0”-22.9”)
SPECIALTY CODES
0070 Saniflo™
WILDEN PUMP & ENGINEERING, LLC 2 WIL-12070-E-03
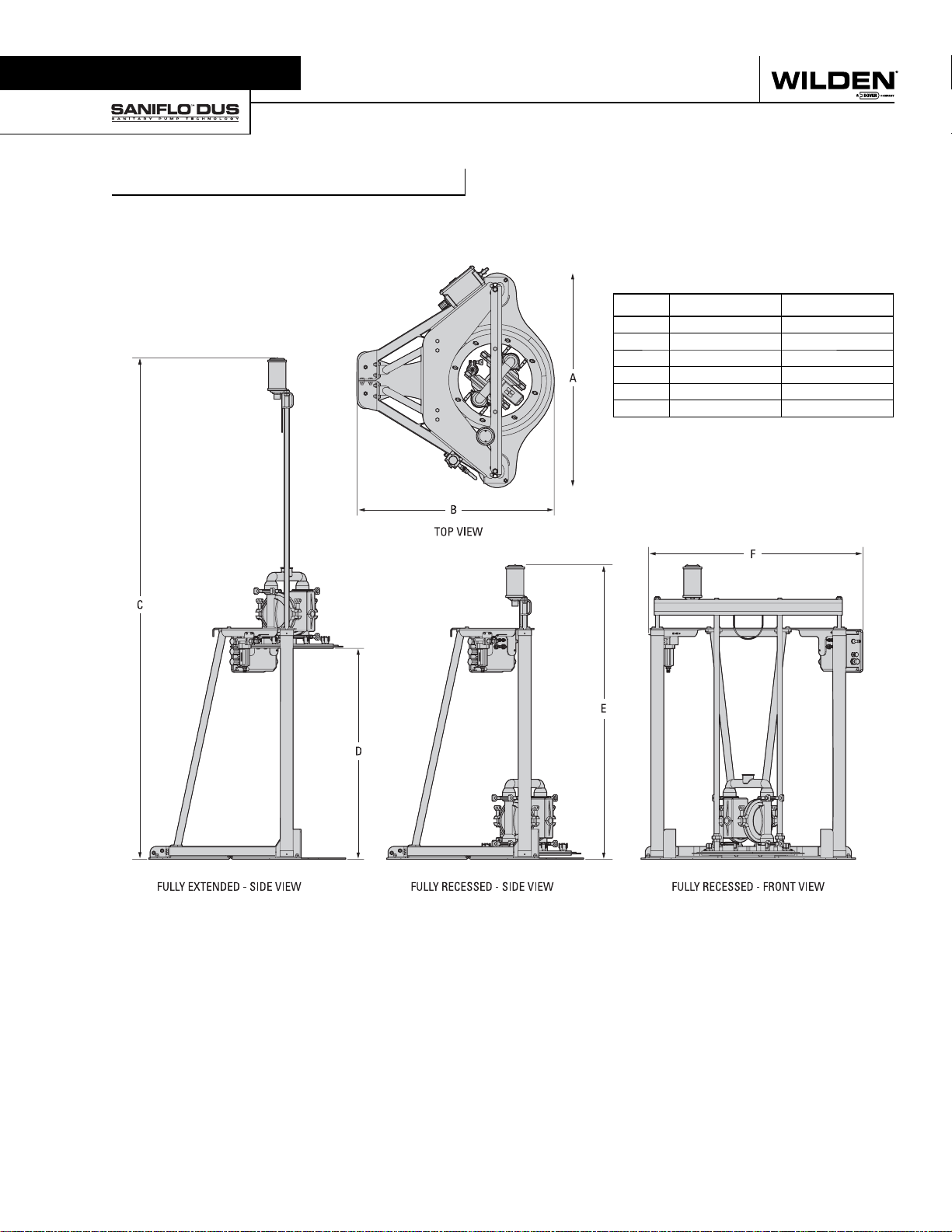
Section 3
DIMENSIONAL DRAWING
DRUM UNLOADER SYSTEM
DIMENSIONS
ITEM METRIC (mm) STANDARD (inch)
A 1143 45.0
B 1049 41.3
C 2667 105.0
D 1123 44.2
E 1567 61.7
F 1140 44.9
WIL-12070-E-03 3 WILDEN PUMP & ENGINEERING, LLC
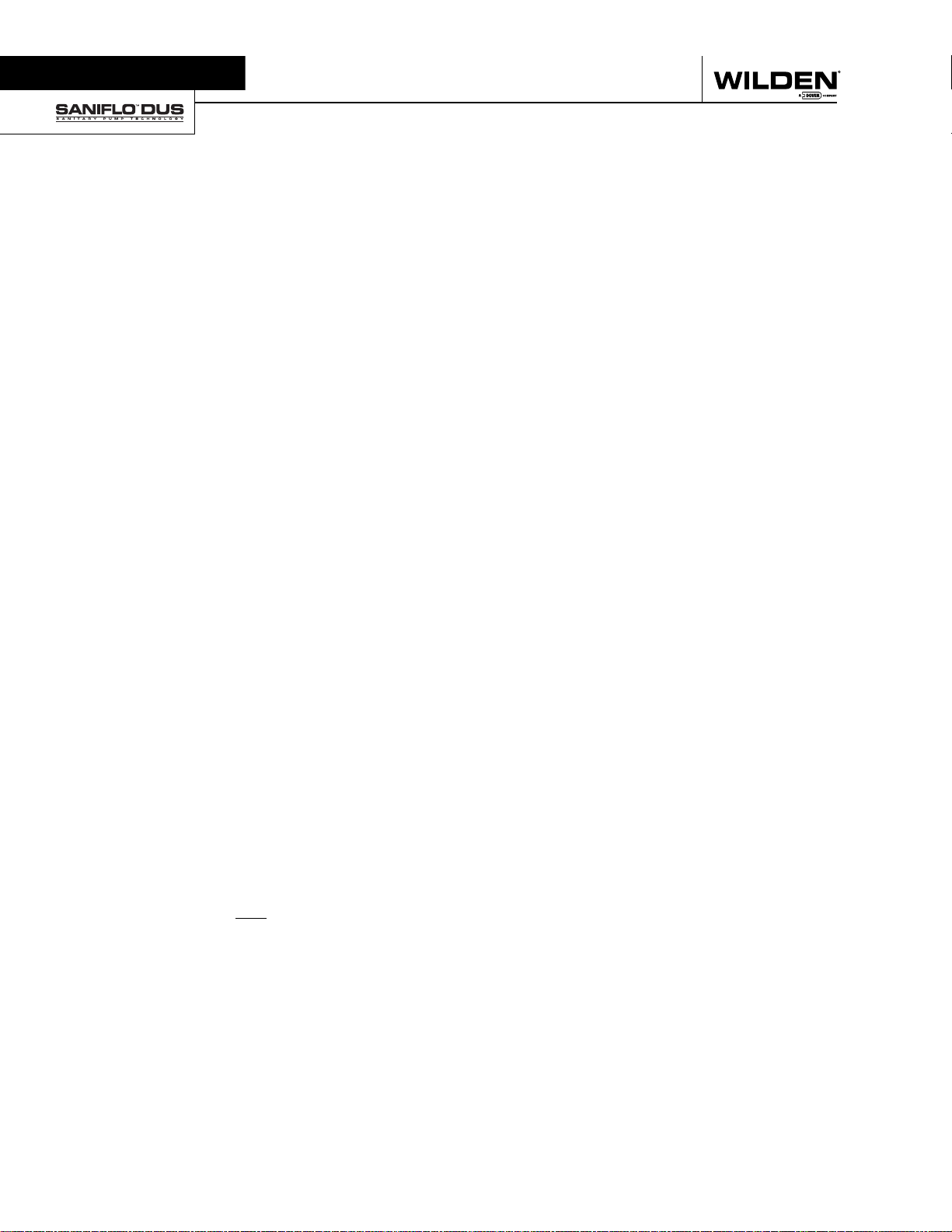
Section 4
TROUBLESHOOTING
Uneven ram cylinder movement.
1. Ensure that the ram cylinder down pressure is not
excessive. Generally, no more than 1.0 bar (15 psig) is
required to move the ram cylinders in the downward
direction.
2. Check to determine whether or not the ram
cylinder air hoses are connected properly. The
ram down cylinder air hoses consist of two longer
air hoses that are equal in length and one shorter
air hose. The ram up cylinder air hoses consist of
two shorter hoses that are equal in length and one
longer air hose. If the ram cylinder air hoses are
not connected properly, the ram cylinders will fi ll
unevenly, causing the ram cylinder movement to
be inconsistent.
3. It is important to follow the assembly process
(section 5). Altering the steps or changing the
process may result in operation issues including
improper rise and fall of the ram cylinders. Steps 1
through 10 of the assembly process are extremely
critical. Following these steps will ensure that the
ram cylinder movement is unrestricted.
Pump runs but little or no product fl ows.
1. Check for pump cavitation; slow pump speed to
allow thick material to fl ow into liquid chambers.
2. Chec k for sticking b all check valves . If material being
pumped is not compatible with pump elastomers,
swelling may occur. Replace ball check valves and
seats with proper elastomers. Also, as the check
valve balls wear out, they become smaller and can
become stuck in the seats. In this case, replace
balls and seats.
3. Check to ensure that there is suffi cient air pressure
supplied by the ram down regulator on the control
panel.
After evacuating drum contents, ram cylinders are
struggling with upward movement.
1. Check to determine whether or not drum vent
button is activated. This will inject air under the
ram plate and break the vacuum caused when
removing the ram plate from the drum.
Pump air valve freezes.
1. Check for excessive moisture in compressed
air. Either install a dryer or hot air generator
for compressed air. Alternatively, a coalescing
fi lter may be used to remove the water from the
compressed air in some applications.
Air bubbles in pump discharge.
1. Check for ruptured diaphragm.
2. Check tightness of outer pistons.
3. Check tightness of fasteners and integrity of
o-rings and seats, especially at intake manifold.
4. Ensure pipe connections are airtight.
Product comes out air exhaust.
1. Check for diaphragm rupture.
2. Check tightness of outer pistons to shaft.
Excessive drum contents leaking past gaskets.
1. Ensure that the correct gasket size is being used in
accordance with the drum size.
NOTE: The gaskets are NOT designed to completely
seal against sides of drum. Under normal operating
conditions, there will be some slight weeping of
drum contents.
WILDEN PUMP & ENGINEERING, LLC 4 WIL-12070-E-03
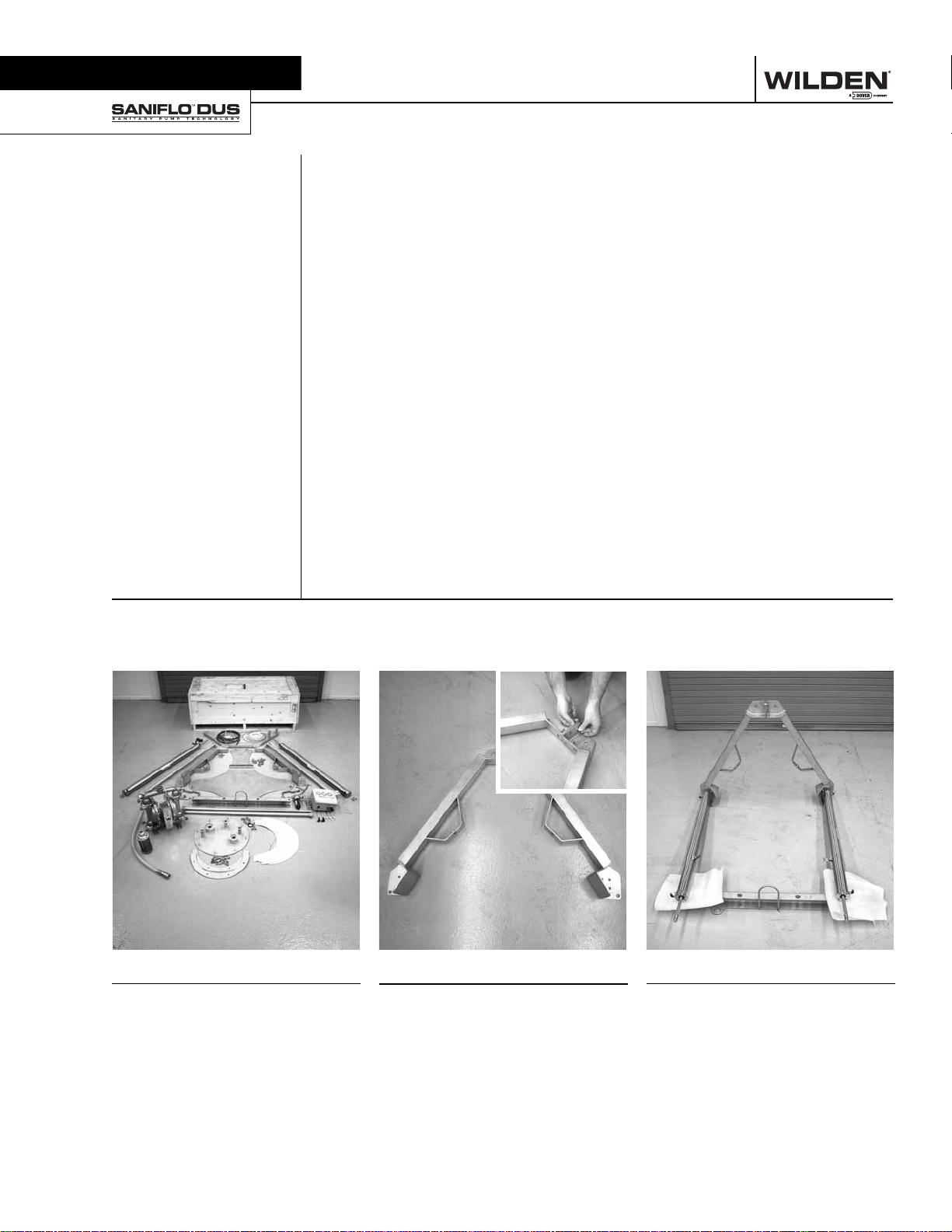
Section 7 Assembly / disassembly
Section 5
ASSEMBLY
Tools Required :
• 10 mm Hex Head
Wrench
• 12 mm Wrench
• 18 mm Wrench
• Adjustable Wrench
CAUTION: During assembly it is important not to tighten any bolts completely
until specifi cally instructed. This will ensure system alignment and allow for
proper operation. It is also recommended that an appropriate anti-s eize is us ed on
all stainless steel fasteners during assembly.
Although some air fi ttings may come with a pipe sealant already applied, it is
recommended that a pipe sealant be used with all additional air fi ttings during
assembly.
NOTE: It is important to follow the assembly instructions provided when building
the Sanifl o™ DUS unit. Altering the steps or changing the process may result in
operation issues including improper rise and fall of the follower plate assembly.
Step 1
Remove all parts from shipping
container and compare with Bill of
Materials listing in Section 9 before
beginning assembly of unit.
WIL-12070-E-03 5 WILDEN PUMP & ENGINEERING, LLC
Step 2
Assemble the left and right base
sections as shown, using two (2) 12
mm bolts, nuts and lock washers.
Leave fasteners hand tight.
Step 3
Raise two connected base pieces
on their side as shown and align
the two pneumatic cylinders. Use
the top support beam to raise the
opposite end of the cylinders for
proper alignment.
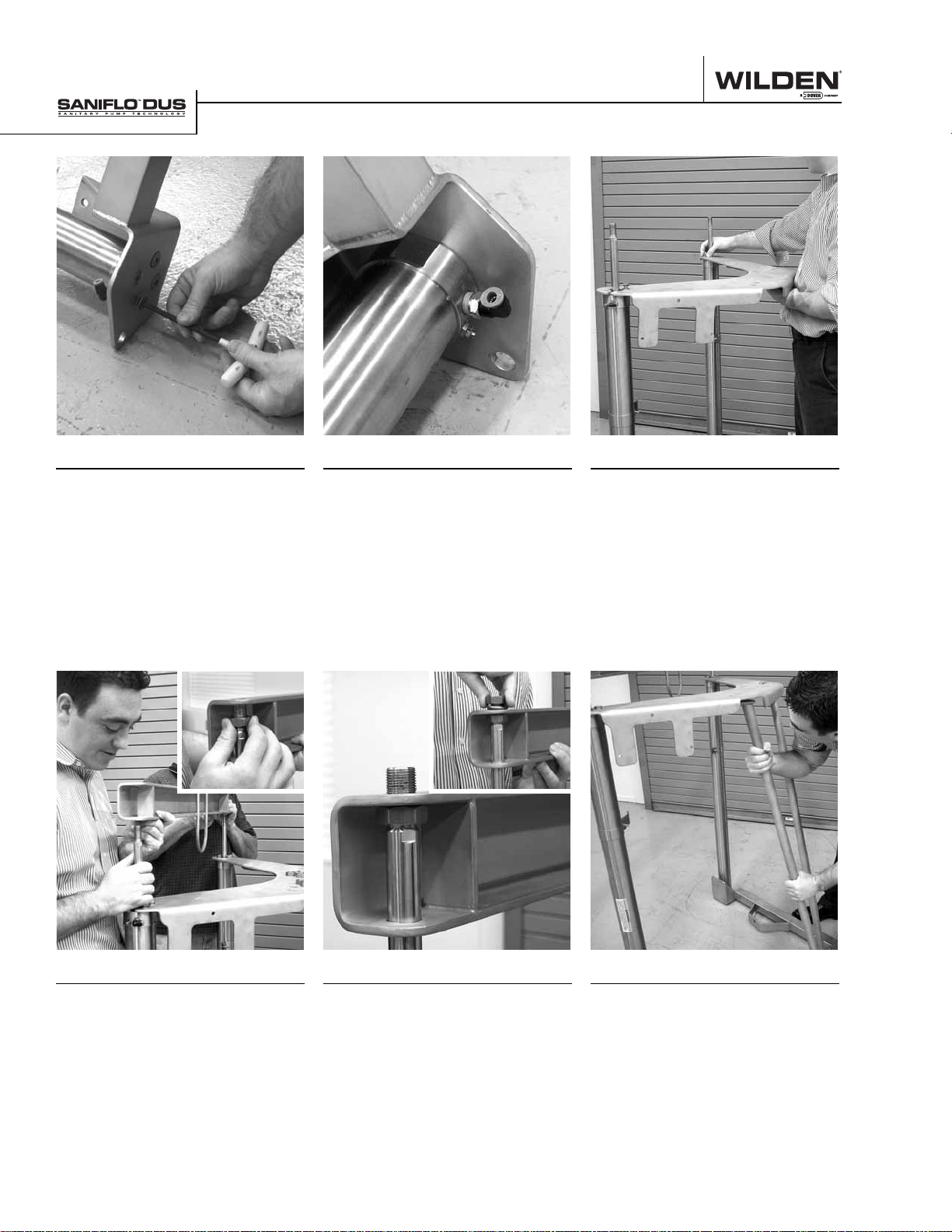
ASSEMBLY
Step 4
Install four (4) 10 mm countersunk
screws in the bottom of the base
frame and end of the cylinders.
NOTE: Once screws are snug, back
off one full turn.
Step 5
When cylinders are installed on
the base frame, ensure that the air
connections are facing away from
the center of the frame assembly.
Step 6
Install the fl at header plate on
the top end of the pneumatic
cylinders. Ensure that the header
plate is positioned as shown when
compared to the base frame.
Step 7
Slide ram support bar over threaded
ends of pneumatic cylinders and
install one (1) 18 mm nut on end of
threaded end until it stops at the rod
shoulder then tighten. NOTE: Nut
should be between upper and lower
support bar holes.
WILDEN PUMP & ENGINEERING, LLC 6 WIL-12070-E-03
Step 8
Slide ram support bar farther down
on the cylinder rod until it bottoms
out on the previously installed nut.
Then add a second 18 mm nut and
lock washer on the end of the rod
and hand tighten.
Step 9
Install braces between base frame
header plate. Triangle end goes up
and rectangular end goes down.
Use 12 mm bolts, nuts and lock
washers and leave hand tight.