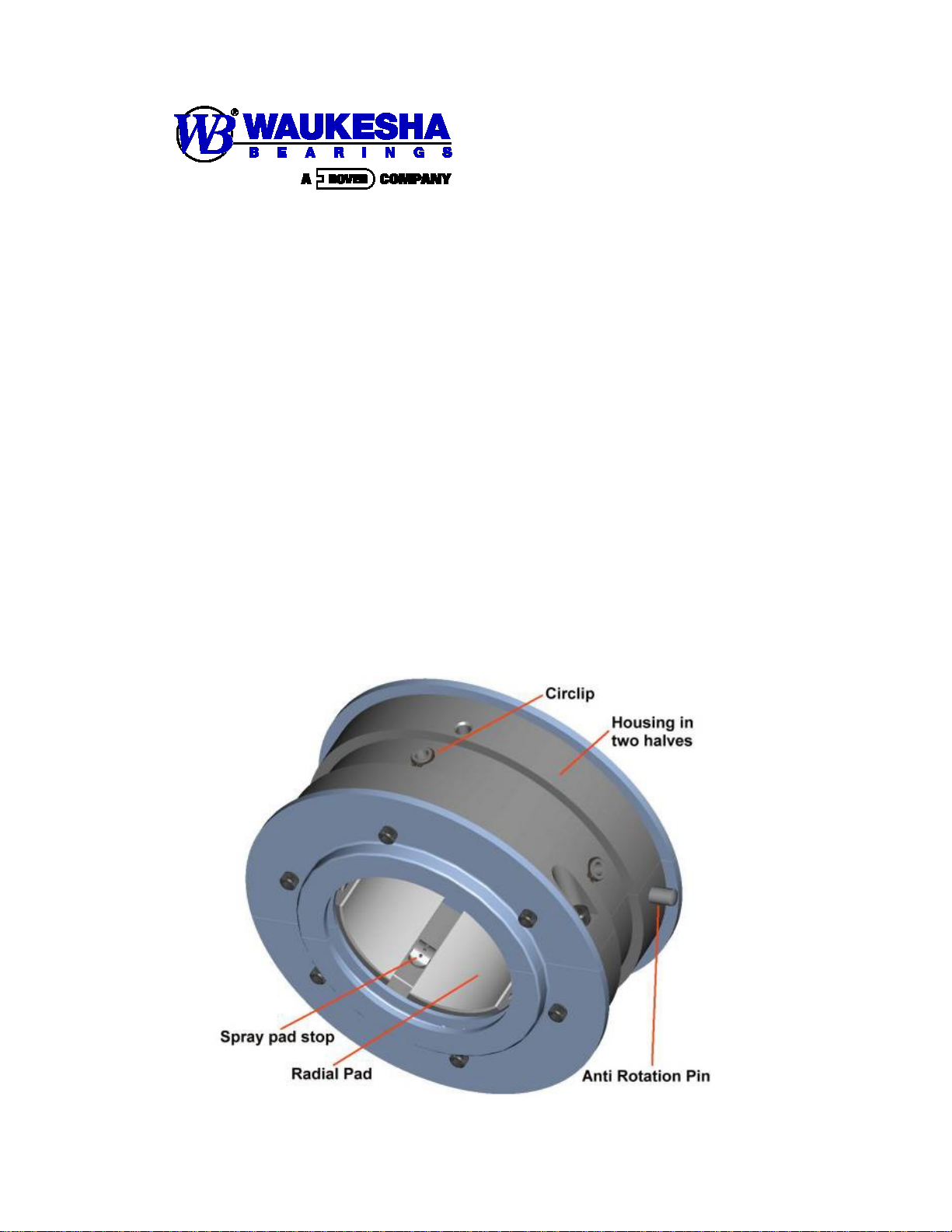
Tilting Pad Radial Bearings
Installation and Maintenance Instructions
1 Introduction
The following notes provide installation and assembly instructions for RPB tilting pad
radial bearings which are now provided with Directed Lubrication as standard, with a
simple and trouble free construction and no end seals. Reference should be made to
the specific contract drawing for operational information and any special features
which may be provided.
2 General Description
The standard RPB tilting pad radial bearing consists of a housing with 5 radial pads
located both circumferentially and radially by combined pad stops/oil sprays and
axially by an end plate or an integral housing flange. The standard radial pads are
centre pivoted and are suitable for either direction of rotation. The general
construction of the bearing is shown in Fig 1 and reference to this figure is made in
the following comments.
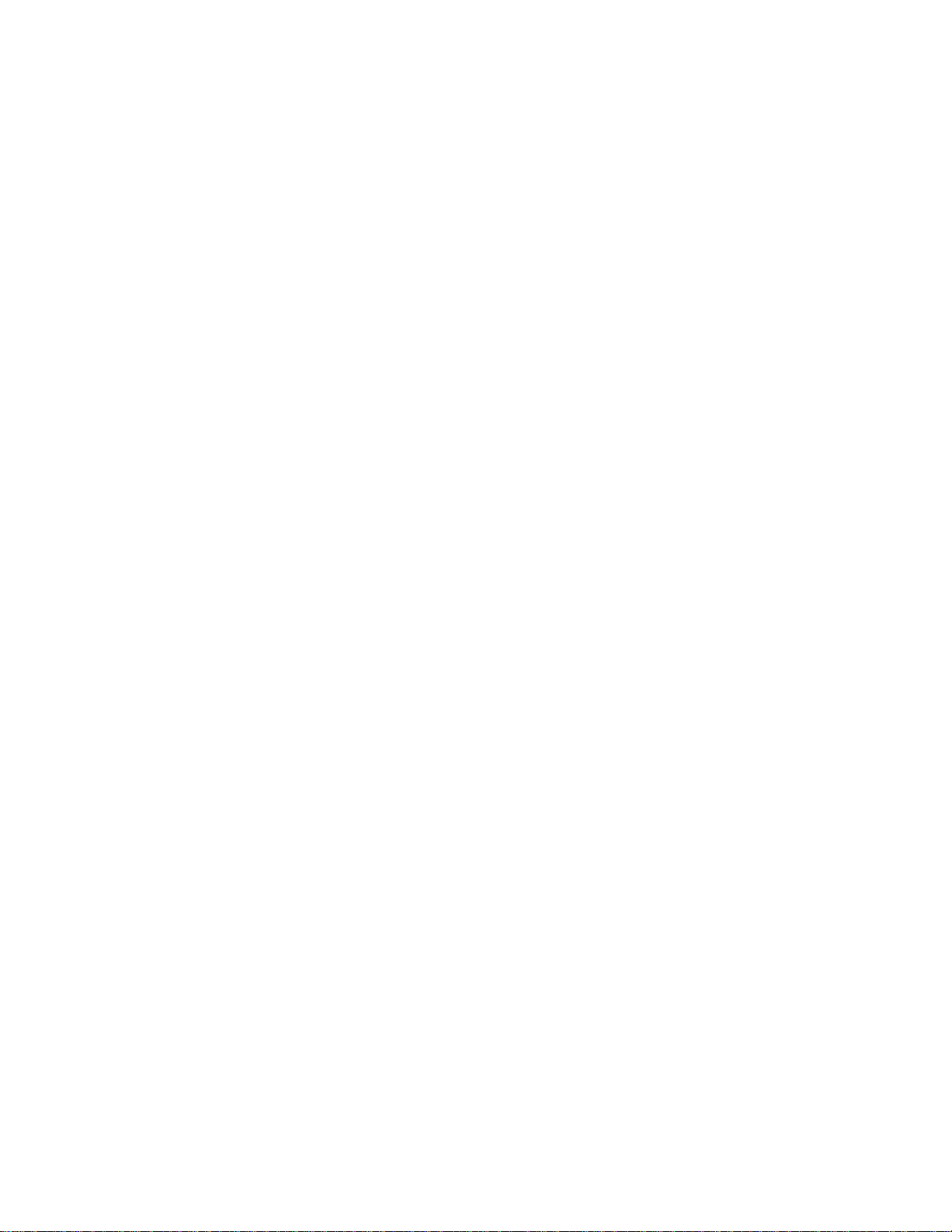
The bearings are designed to be lubricated by a pressurised oil system with oil
reaching the pads via the spray pad stops. The oil exits from the bearing through the
end baffles. The radial pads are manufactured from steel lined with tin based
whitemetal. They can tilt in the direction of shaft movement to generate a
hydrodynamic film. They are also capable of movement in the axial direction to
accommodate limited shaft misalignment.
The radial pads and spray pad stops are located in a housing which may be supplied
either in halves or as a one piece ring. The spray pad stops are held by circlips on the
outside which can be removed to allow inward, radial withdrawal of the stops.
Rotation of the housing is prevented by the anti-rotation pin. In the case of split
housings the two halves are fastened together by dowels and bolts.
3. Installation
3.1 Cleanliness
To obtain the most reliable performance from these bearings it is necessary to observe
high engineering cleanliness standards. The interior of the casing and all oil passages
and pipes, especially on the supply side, must be perfectly clean and free from
foundry sand, scale, welding spatter etc. Any unmachined surfaces should be shot
blasted down to a clean metal surface.
3.2 Alignment
It is most important that the bearings should be accurately aligned to their journal and
this alignment should be carefully checked during assembly. The required alignment
should be achieved by shimming the housing pedestals; the bearing bore must not be
scraped.
3.3 Assembly
In the following instructions it is assumed that the bearings will be assembled when the
rest of the machine is already in a partially assembled state with the shaft in position.
If this is the case, the shaft should be suitably supported over the bearing housings,
leaving sufficient room to rotate each bearing half between the shaft and the bearing
support housing.
3.3.1 Bearings in halves (Code /2D and /2DF)
This type of bearing is normally installed by wheeling it into position around the shaft
which is assumed to be in a horizontal position. Before installation it is necessary to
separate the two bearing halves by removing the screws which hold the halves
together. It should be noted that the two outer radial pads at the bearing housing joint
are loose when the bearing is split and they should be removed before assembly
commences.
Installation of the bearing commences by wheeling the bottom bearing half between
the shaft and the bearing support housing until the anti-rotation pin is located in the
recess which should be provided in this housing. The joint face of the bearing should
now be horizontal and facing up. The two loose radial pads should now be placed in
position in the lower bearing half. Finally, the top bearing half is placed on the bottom
bearing half and the retaining screws fitted and tightened to keep the halves together.
The machine housing top cover may now be placed in position.