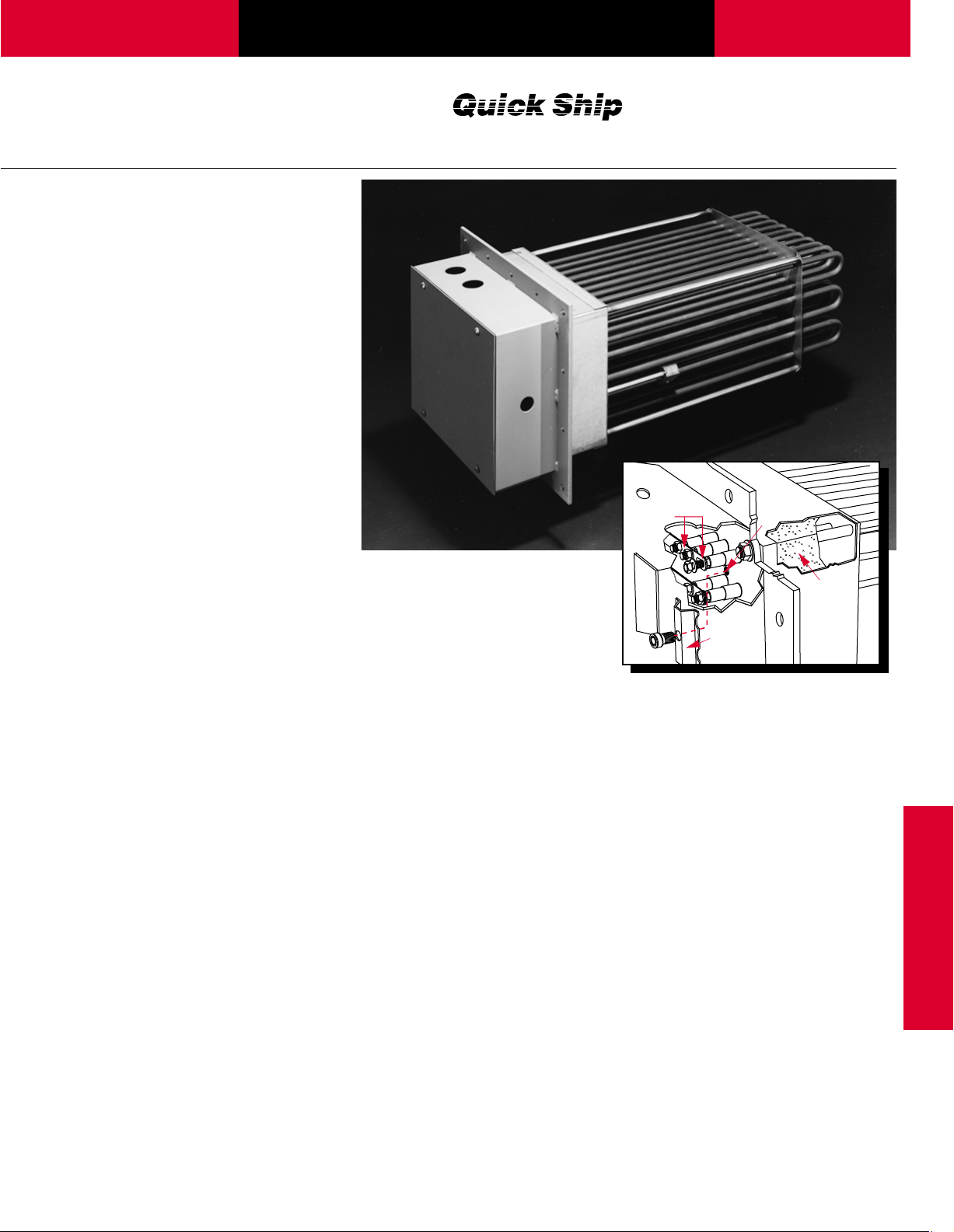
W A T L O W
Tubular and
Process Assemblies
Duct Heaters
Constructed of sturdy 0.430 inch
(11 mm) diameter WATROD heating
elements mounted to a 1⁄4 inch
(6 mm) thick steel flange, duct
heaters are easily adapted to many
non-pressurized, air-heating
systems.
They are easily installed in
applications requiring a wide range
of temperature vs. air flow
combinations.
Watlow duct heaters offer
advantages over gas or oil fired and
open coil electric units with:
• Installation flexibility—
no flues or fuel lines.
• 100 percent energy efficient—
no energy loss up the flue.
• Universal availability of electricity.
• Resistance coil in Incoloy
sheath is protected from corrosive environments.
Performance Capabilities
• Watt densities to 40 W/in
(6.2 W/cm2)
• Recommended process
temperatures from -20 to 1200°F
(-7 to 650°C)
• Wattages to 2.2 megawatts
• Voltages to 600VÅ(ac)
Features and Benefits
• Long life Incoloy®sheath
resists corrosion/oxidation while
protecting resistance coils
against contamination.
• MgO insulation filled elements,
compacted to rock hard density
maximize dielectric strength, heat
transfer and life.
• Field replaceable heating
elements permit easy service
and reduce downtime. Element
change-out is made simple by a
single screw clamp.
Incoloy®is a registered trademark of
Special Metals Corporation.
®
2
1
⁄2 inches (90 mm) thick
• 3
mineral insulation keeps wiring
cooler and reduces heat loss.
• Vented general purpose
(NEMA 1) terminal enclosure
ensures cooler terminations.
• A 1⁄4
inch (6 mm) inside
diameter thermowell accepts
an optional Type J or K
thermocouple for accurate
sheath temperature sensing.
• Rigid stainless steel suppor ts
prevent element sagging or
deformation in various mounting
positions.
1
• A
⁄4 inch (6 mm) thick steel
flange, with 3⁄8 inch (10 mm)
diameter mounting holes, easily
bolts to the duct wall.
®
is a registered trademark of
UL
Underwriter's Laboratories, Inc.
On stock chart units:
• Three to five working days on most heaters
• 10 working days on special voltages and/or
wattages
• 15 working days on special element lengths
Bussing
Single
Screw
Clamp
Threaded
Hole
Mineral
Insulation
• WATROD hairpins are
repressed (recompacted) after
bending to assure MgO density
that eliminates hot spots and
electrical insulation voids.
• Stock heaters feature 6, 12, 18,
24, 30, 36, 42, 48, 54, and 60
elements to meet a wide variety
of kW demands.
• One or three phase voltages to
meet local power supplies.
• Maximum 48 amps per circuit
complies with National Electrical
Code (NEC).
• Duct heaters with general
purpose enclosures meet UL
and CSA component recognition to 480 and 600VÅ(ac)
maximum respectively—UL
and CSA file numbers are
E52951 and 31388.
Duct Heaters
®
®
411
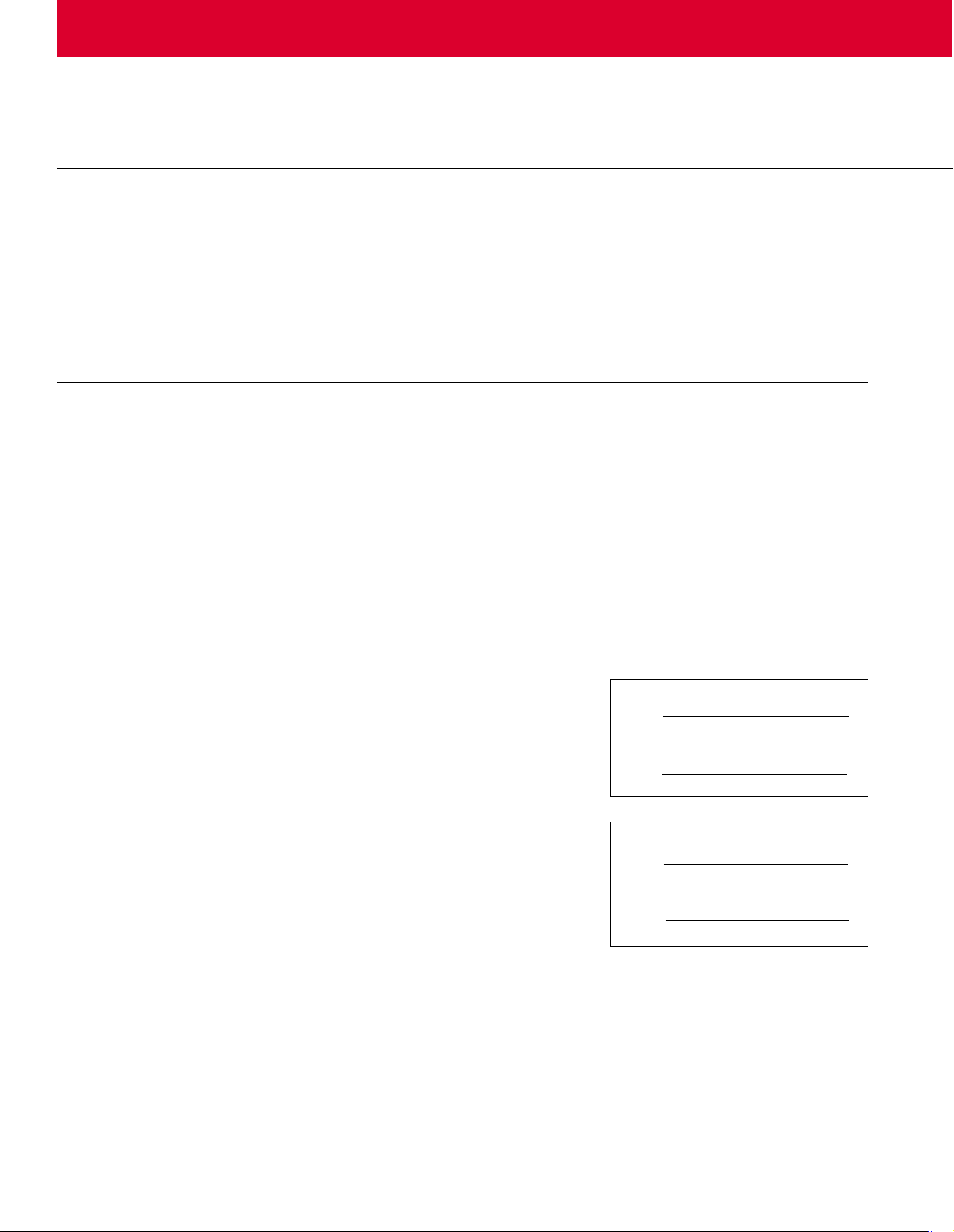
Tubular and
Process Assemblies
Duct Heaters
Applications
• Dr ying ovens
• Autoclaves
• Furnaces
• Load banks
• Heat treating
• Reheating
•HVAC
• Paint dr ying
Choosing a Duct Heater
The following English and metric
graphs, shown on pages 413 to
414, will help you to select the
correct duct heater. These graphs
include: Watt Density vs. Air
Temperature/Velocity, Watt Density
vs. Sheath Temperature and
Pressure Drop vs. Air Velocity.
These graphs, with the quick
formulas on this page, along with
information specific to your
application, will determine the
correct duct heater specifications.
However, if engineering assistance
is needed, contact your Watlow
representative.
Required Application Information
• Desired outlet air temperature
• Inlet air temperature
• Delta T—the temperature
difference between inlet and
desired outlet temperature
• Air volume (CFM/CMM)
measured at both inlet
temperature and pressure
• Air velocity in feet per minute
(FPM); meters per minute (MPM)
which equals:
• Minimum duct heater wattage
(kW). This can be determined by:
English
CFM measured at standard conditions
FPM =
Duct cross section area at heater in ft
Metric
MPM =
kW =
kW =
CMM measured at normal conditions
Duct cross section area at heater in m
English
CFM x Delta T (°F) x 1.1(safety factor)
3000
Metric
CMM x Delta T (°C) x 1.1(safety factor)
48
2
2
412
Note: The duct heater, or
combination of duct heaters, used
for the process should be equal to
or exceed the minimum wattage
calculation.
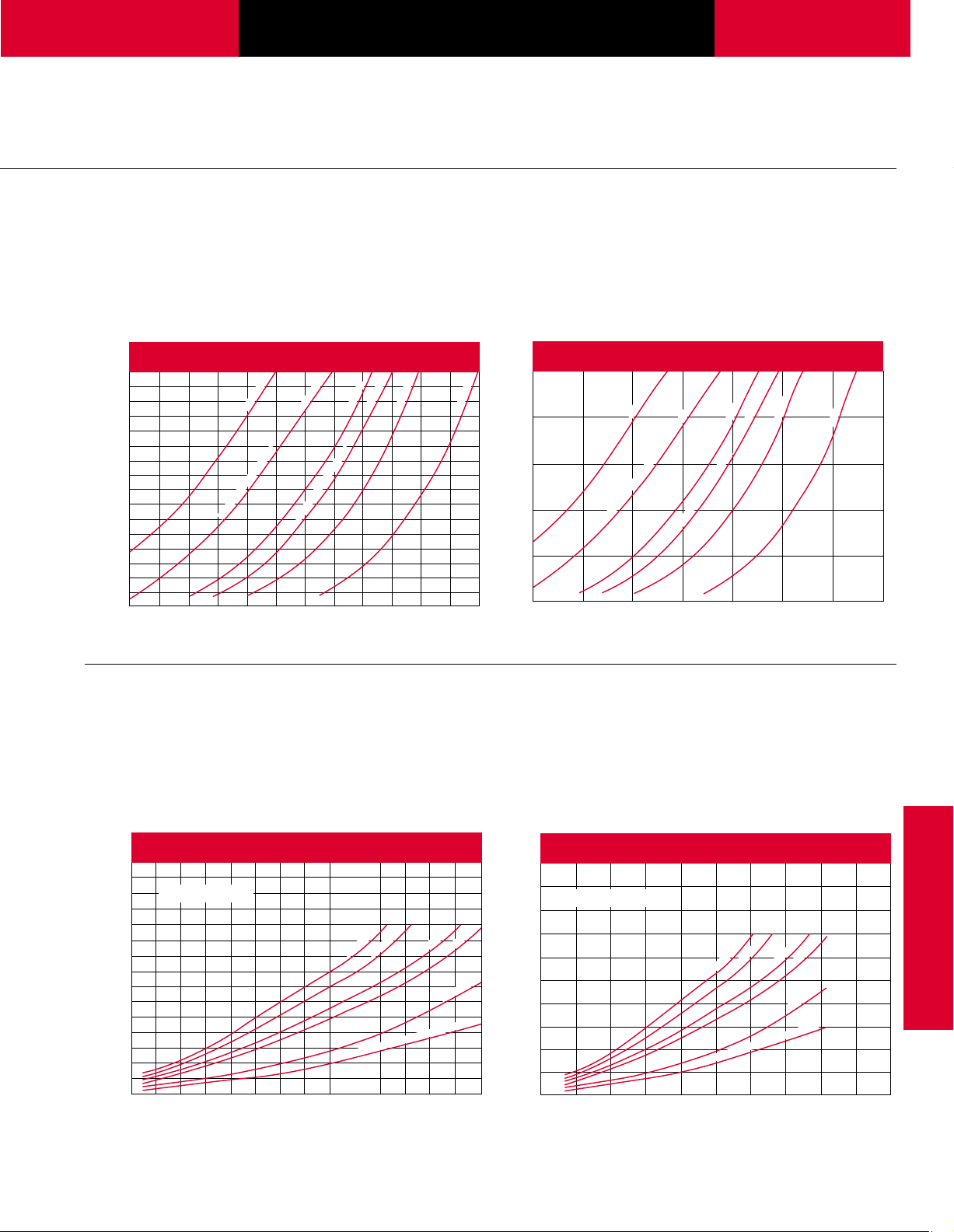
W A T L O W
WATROD Duct Heater
Watt Density vs. Air Temperature/Velocity
Process Temperature—°F
Air Velocity—FPM
100
100
200
300
400
500
600
700
800
900
1000
1100
1200
1300
1400
1500
1600
200 300 400 500 600 700 800 900 1000 1100 1200
40 W/in230 W/in
2
23 W/in
2
20
W/in
2
16 W/in
2
8 W
/in
2
Catalog Duct Heaters
Catalog Duct Heaters
Estimated Sheath Temperature = 1400°F
Process Temperature—°C
Air Velocity—MPM
100
500
Estimated Sheath Temperature = 760°C
WATROD Duct Heater
Watt Density vs. Air Temperature/Velocity
400
300
200
100
200 300 400 500 600 700
4.65 W
/cm
2
3.5 W/cm
2
3.1 W/cm
2
2.5 W/cm
2
1.25 W
/cm
2
Catalog Duct Heaters
6.2 W
/cm
2
Catalog Duct Heaters
Sheath Temperature—°F
Watt Density—W/in
2
100
4
WATROD Duct Heater
Watt Density vs. Sheath Temperature
8
12
16
20
24
28
32
36
40
44
48
52
56
60
0
200 300 400 500 600 700 800 900 1000 1100 1200 1300 1400 1500
Inlet Temperature at
75 Degrees Fahrenheit
1200 FPM
760 FPM
680 FPM
300 FPM
60 FPM or Natural Convection
1550 FPM
Sheath Temperature—°C
100
WATROD Duct Heater
Watt Density vs. Sheath Temperature
Watt Density—W/cm
2
5
4
3
2
1
6
7
8
9
10
200 300 400 500 600 700 800 900 1000
365 MPM
235 MPM
180 MPM
90 MPM
18 MPM or Natural Convection
475 MPM
Inlet Temperature at
25 Degrees Celsius
Tubular and
Process Assemblies
Duct Heaters
Watt Density vs. Air
Temperature/Velocity
To decide watt density
requirements, first determine the
desired outlet air temperature and
velocity in feet per minute. Then
follow the lines on the graph for
velocity and process temperature to
the watt density curve’s intersecting
point. This shows the recommended
watt density based on a maximum
sheath temperature of 1400°F
(760°C). For longer heater life,
lower watt densities should be
chosen.
Watt Density vs. Sheath
Temperature
The Watt Density vs. Sheath
Temperature graph shows the air
velocity (FPM or MPM) required to
operate a WATROD duct heater at
specific watt densities or sheath
temperatures. Also depicted is the
appropriate watt density vs. sheath
temperature at a specified air flow.
Duct Heaters
413