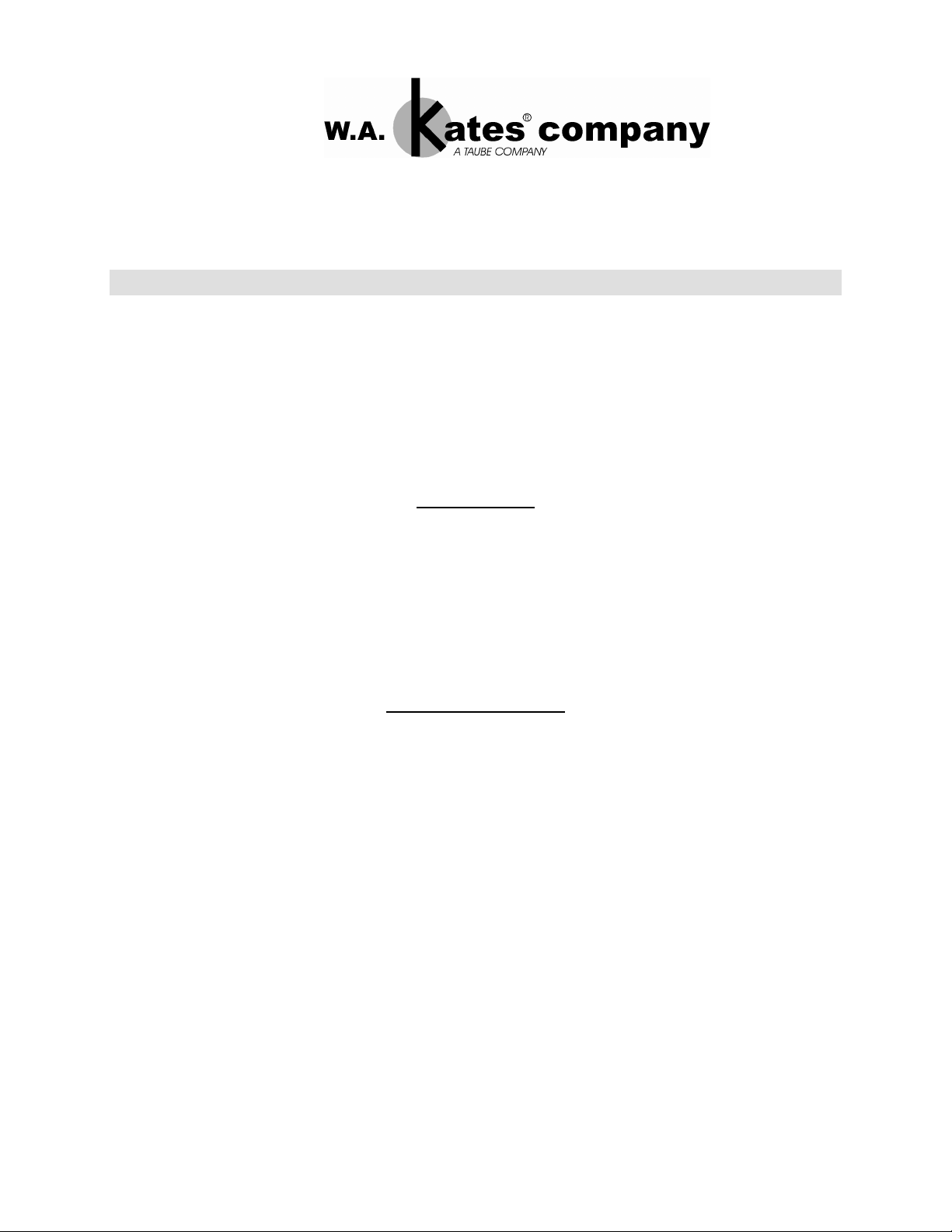
INSTALLATION & SERVICE INSTRUCTION MANUAL FOR KATES
5050 & 5160 ADJUSTABLE FLOW RATE CONTROLLERS
IMPORTANT
THE KATES FLOW RATE CONTROLLER IS DESIGNED TO ACCURATELY REGULATE FLOW RATES AND IS PRECISION BUILT
WITH EXACTING TOLERANCES AND FINISHES. TO INSURE SATISFACTORY PERFORMANCE, THE REGULATED FLUID MUST
BE CLEAN AND FREE OF DIRT OR SOLIDS. THE INSTALLATION OF A 10 MICRON FILTER IS RECOMMENDED JUST UPSTREAM
OF THE CONTROLLER.
EQUALLY IMPORTANT: WHEN DIS-ASSEMBLING, SERVICING, OR CLEANING THE CONTROLLER, THE INTERNAL PARTS
MUST BE HANDLED WITH CARE TO PREVENT DAMAGING THE SURFACE FINISH IN ANY WAY.
OPERATION OF A KATES ADJUSTABLE FLOW RATE CONTROLLER THAT IS SUPPLIED BY A POSITIVE DISPLACEMENT PUMP,
WILL BE SATISFACTORY ONLY IF A PRESSURE-RELIEVING VALVE IS CONNECTED BETWEEN THE PUMP AND THE
CONTROLLER. THIS IS TO BYPASS EXCESS FLUID BACK TO THE FLUID SOURCE, OR TO THE INTAKE OF THE PUMP.
INSTALLATION
1. The Kates Controller is shipped fully assembled, ready for operation, with all parts in place. It is completely self-contained,
requires no outside source of power, no straight piping runs, and is as simple to install as an ordinary angle valve.
2. Upstream and downstream shutoff valves and a bypass valve should be installed so that the controller may be opened for inspection
and cleaning without requiring complete system shutdown.
3. Before installing the controller be sure to flush out the piping system to remove any foreign material such as dirt, scale, chips, etc.
4. The Kates Controller is constructed substantially, but pipe supports should be located so that the controller is not subject to
mechanical load due to piping, or expansion or contraction of piping. Proper provisions for pipe expansion should always be made.
5. The controller should be installed at a point in the pipe where it will be completely filled with liquid under all conditions or
operation. The preferred axis of the controller is vertical, with the bonnet up. On threaded connections, apply pipe thread
compound sparingly to male threads only so that surplus will not get inside the controller and cause “sticking” or prevent operation.
START UP PRODEDURE
1. The pointer on the stainless steel nameplate should be at front, readily visible to operator. If not, proceed as follows:
a) Loosen and remove the bonnet bolts.
b) Lift the bonnet straight up and turn until the pointer faces front.
c) Make sure the body O-ring is in good condition and is in place.
d) Lower the bonnet slowly, at the same time turning the flow rate setting knob until the key on the end of the adjuster shaft
fits into the slots in the orifice sleeve, and the shoulder on the lower face of the bonnet fits into the body. When properly
assembled, bonnet will seat squarely on the body all the way around. (See diagram).
e) Replace and tighten the bonnet bolts in a “star” pattern.
2. By hand, turn the flow rate setting knob in both directions until the stop pin inside the controller prevents further rotation. If it does
not turn easily without sticking, or if it does not hit the stop pin in both directions, follow directions below “To Clean Controller”.
CAUTION: Never use a wrench or attempt to force the knob to turn.
3. Turn the flow rate setting knob clockwise until it hits the internal stop pin. The minimum setting at right hand end of dial should
now line up with the pointer. If not, loosen the three screws on the top of the knob, turn the dial until the minimum setting on the
dial lines up with pointer and retighten the screws.
4. Turn the flow rate setting knob until the desired flow rate mark on the dial lines up with the pointer on the nameplate.
5. Place controller “on stream” by opening upstream and downstream shutoff valves and closing the bypass valve around the controller.
Controller will now regulate the flow rate at the set value.
6. When normal fluid temperature is above room temperature, especially with viscous fluids, there may be a “warming up” period until
the controller reaches the same temperature as the fluid. During this warming up period, the controller may be somewhat sluggish in
action. If desired, this warming up period may be eliminated by the use of a heating coil or jacket.
7. During the first few days of operation, gasketed joints should be observed and tightened if necessary.
BLT 303 - 01
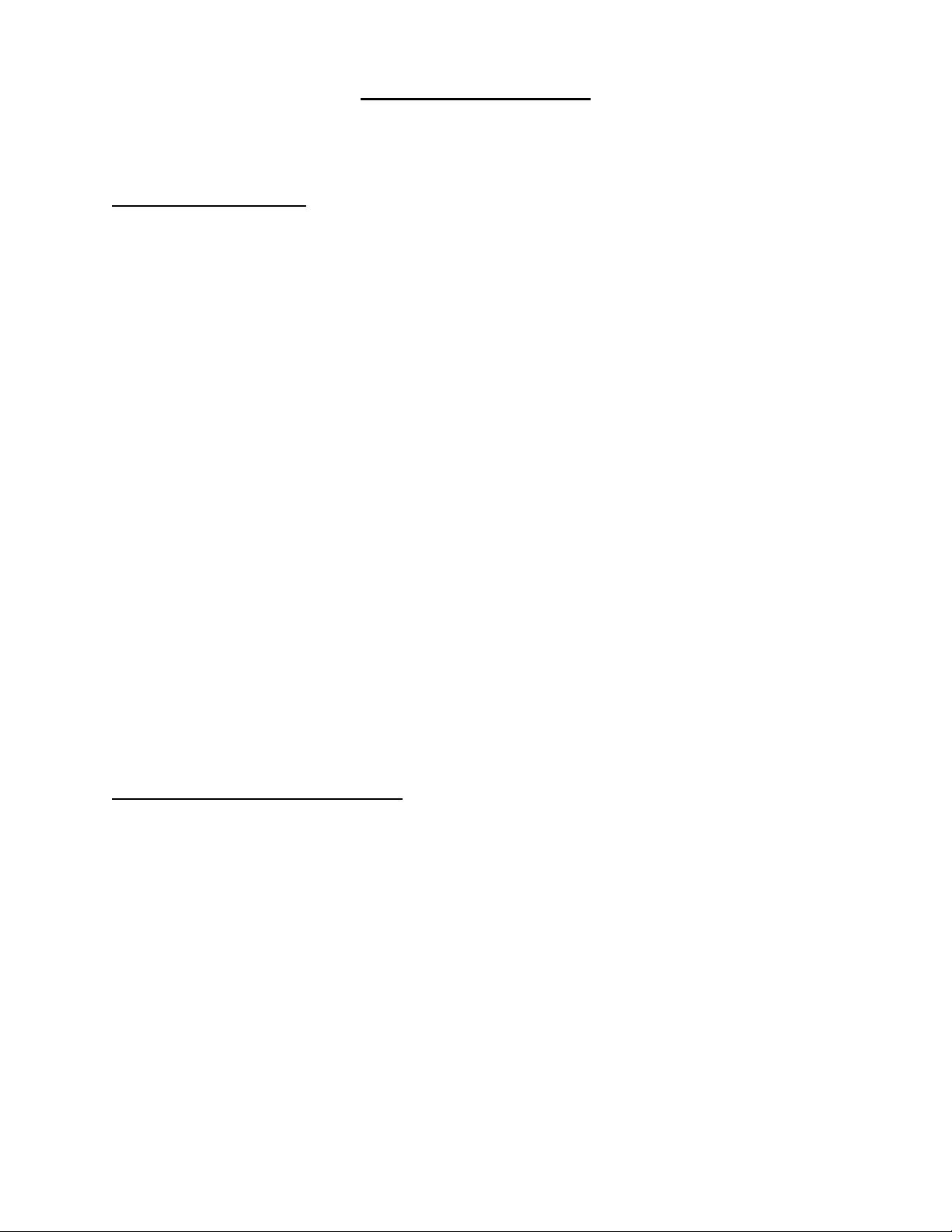
SERVICE INSTRUCTIONS
The Kates Flow Rate Controller has only one moving element, and is designed so that there are no complex linkages, delicate bearings, or any
failure-prone components. Therefore, occasional cleaning may be the only servicing the controller will require.
CAUTION: MAKE SURE THAT THE CONTROLLER IS RELIEVED OF PRESSURE BEFORE ATTEMPTING TO SERVICE OR CLEAN.
TO CLEAN CONTROLLER
CAUTION: in all cleaning operations, be very careful not to scratch, nick or mark any surfaces or edges.
1. It is not necessary to remove the controller from the line to clean. If installation includes proper shutoff and bypass valves, operate these
and take controller off stream or control.
2. Arrange a clean area where internal trim parts can be placed and kept free of lint or grit.
3. Remove bonnet bolts, lift bonnet assembly straight up, and set it in the clean area.
4. Lift out the orifice sleeve and put it in the clean area.
5. Remove the orifice cylinder clamp screws, lift out the orifice cylinder and put it in the clean area.
6. Remove the spring and piston and set them in the clean area.
7. Valve sleeve is now exposed and can usually be cleaned in place.
8. Thoroughly clean all the parts which have been removed from the controller by immersing them in a suitable solvent. Thoroughly clean
and flush inside of controller body with the solvent, and drain. Because of the small size of orifice opening and the closely fitted parts, it is
VERY IMPORTANT that all parts and surfaces, including the orifice opening and valve ports, be COMPLETELY CLEAN. Any dirt,
sediment, coating or gummy residue must be completely removed. Wipe all parts and surfaces dry with a clean, lint-free cloth.
CAUTION: in all cleaning operations, be very careful not to scratch, nick or mark any surfaces or edges.
9. Replace piston carefully into valve sleeve.
10. Install spring. Insure that it is clean and that it seats properly.
11. Replace orifice cylinder insuring that it seats firmly on the valve sleeve. Opening should face away from the inlet pipe.
12. See that the orifice sleeve is clean and that the orifice slot is clean and open. Place it on the orifice cylinder, check for free rotation, and see
that it does not ride on top of the stop pin.
13. Replace body o-ring if necessary, then replace bonnet. See that the pointer is in front where set point can be read. When replacing bonnet,
revolve dial and knob assembly and thus fit the cross bar into the slots in the upper end of the orifice sleeve. Tighten bonnet bolts
uniformly.
14. Place controller in service as specified under steps 2-7, “TO PLACE CONTROLLER IN SERVICE”.
TO REPLACE ADJUSTER SHAFT SEAL:
1. The only packing required is between the adjuster shaft and the bonnet. This consists of a Teflon thrust washer and a simple O-ring of
standard size. Material is suitable for use with the liquid flowing through the controller.
2. To replace the thrust washer and O-ring, remove bonnet, remove flow rate setting knob by removing knob clamp screw and lifting dial and
knob assembly upwards. Adjuster shaft can now be removed by pulling it through the bonnet to the inside.
3. Remove the existing O-ring by prying it out of the groove in the shaft, using a blunt-ended hook. (With a Teflon O-ring, first immerse the
adjuster shaft in warm water to slightly soften the O-ring).
CAUTION: Be careful not to scratch the groove or the shaft.
4. Remove the existing thrust washer, and replace with a new thrust washer. Run the washer down the shaft until it rests on the shoulder.
5. Slide a new O-ring down the adjuster shaft until it fits properly in the groove. (With a Teflon O-ring, first immerse it in warm water to
soften it slightly.)
6. Carefully push the adjuster shaft through the bonnet from the inside until the thrust washer is held tightly between the shoulder on the shaft
and the shoulder on the bonnet. Observe that there are flats at the top of the shaft and the bottom of the hole in the knob. Place knob on
shaft with both sets of flats aligned so the shaft will key into the knob. Support shaft from below, then press or tap knob down on shaft. If
flats on shaft do not fit into those in knob, turn knob slightly, then tap or press it down into place. Replace knob clamp screw to hold knob
in place.
7. Replace regulator bonnet, and put the regulator “on stream” by following Steps 2-7 listed under the heading “START UP PROCEDURE”.
BLT 303 - 01