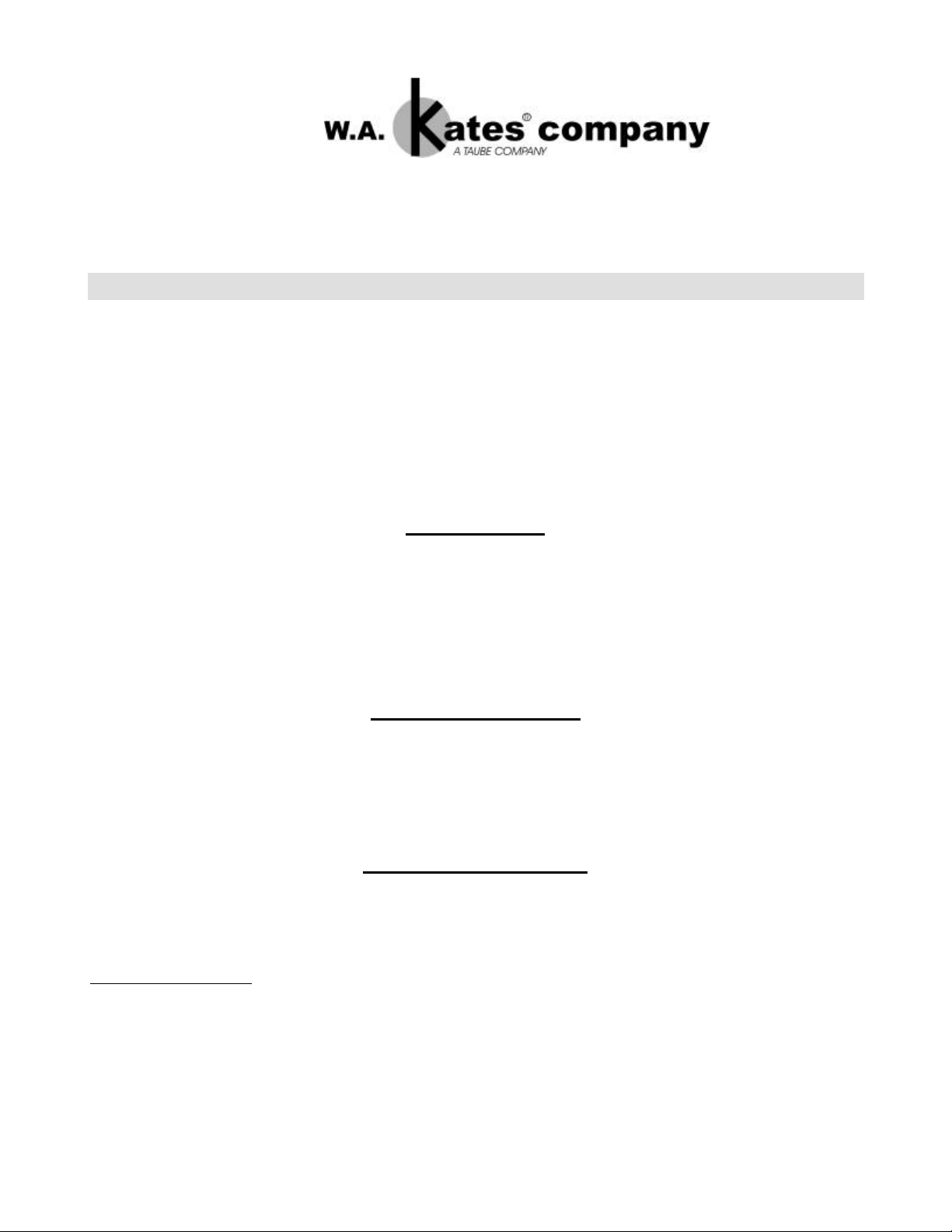
INSTALLATION & SERVICE INSTRUCTIONS FOR KATES FLOW
CONTROLLER MODELS 50FB, 50FB-UHRA
IMPORTANT
THE KATES FLOW RATE CONTROLLER IS DESIGNED TO ACCURATELY REGULATE FLOW RATES AND IS PRECISION BUILT
WITH EXACTING TOLERANCES AND FINISHES. TO INSURE SATISFACTORY PERFORMANCE, THE REGULATED FLUID MUST
BE CLEAN AND FREE OF DIRT OR SOLIDS. THE INSTALLATION OF A 20 MICRON FILTER IS RECOMMENDED JUST UPSTREAM
OF THE CONTROLLER.
EQUALLY IMPORTANT: WHEN DIS-ASSEMBLING, SERVICING, OR CLEANING THE CONTROLLER, THE INTERNAL PARTS
MUST BE HANDLED WITH CARE TO PREVENT DAMAGING THE SURFACE FINISH IN ANY WAY.
OPERATION OF A KATES ADJUSTABLE FLOW RATE CONTROLLER THAT IS SUPPLIED BY A POSITIVE DISPLACEMENT PUMP,
WILL BE SATISFACTORY ONLY IF A PRESSURE -RELIEVING VALVE IS CONNECTED BETWEEN THE PUMP AND THE
CONTROLLER. THIS IS TO BYPASS EXCESS FLUID BACK TO THE FLUID SOURCE, OR TO THE INTAKE OF THE PUMP.
INSTALLATION
1. The Kates flow controller is sh ipped fully assembled, ready for operation, with all parts in place. It is completely self-contained, requires
no outside source of power, no straight piping runs, and is as simple to install as an ordinary ball valve.
2. Upstream and downstream shutoff valv es and a bypass valve should be installed (see Fig. 1) so that the controller may be opened for
inspection and cleaning without requiring complete system shutdown.
3. Before installing the controller be sure to flush out the piping system to remove any foreign material such as dirt, scale, chips, etc.
4. The controller should be installed at a point in the pipe where it will be completely filled with liquid under all conditions of
operation. On threaded connections, apply pipe thread compound sparingly to male threads only so that surplus will not get inside the
controller and cause “sticking” or prevent operation.
START UP PRODEDURE
1. Place controller “on stream” by opening upstream and downstream shutoff valves and slowly closing the bypass valve around the
controller.
The controller will now regulate the flow rate at the set value.
2. When normal fluid temperature is above room temperature, especially with viscous fluids, there may be a “warming up” period until the
controller reaches the same temperature as the fluid. During this warming up period, the controller may be somewhat sluggish in action. If
desired, this warming up period may be eliminated by the use of a heating coil or jacket.
SERVICE INSTRUCTIONS
The Kates Flow Rate Controller has only one moving element, and is designed so that there are no complex linkages, delicate bearings, or any
failure-prone components. Therefore, occasional cleaning may be the only servicing the controller will require.
CAUTION: MAKE SURE THAT THE CONTROLLER IS RELIEVED OF PRESSURE BEFORE ATTEMPTING TO SERVICE OR CLEAN.
TO CLEAN CONTROLLER
CAUTION: in all cleaning operations, be very careful not to scratch, nick or mark any surfaces or edges.
1. It is necessary to remove the controller from the line to clean. If installation includes proper shutoff and bypass valves, operate these
and take the controller off stream or control. (See fig. 1)
2. Arrange a clean area where internal trim parts can be placed and kept free of lint or grit.
3. Do not remove the hex nut and the socket head cap screw in the center of the adjuster orifice assembly. By moving this rotationally, the
flow rate will be altered. Remove the screws holding the adjuster orifice assembly in the body, pull the assembly out of the body, and place
in the clean area.
4. Remove end plug, spring, piston, and place all in the clean area.
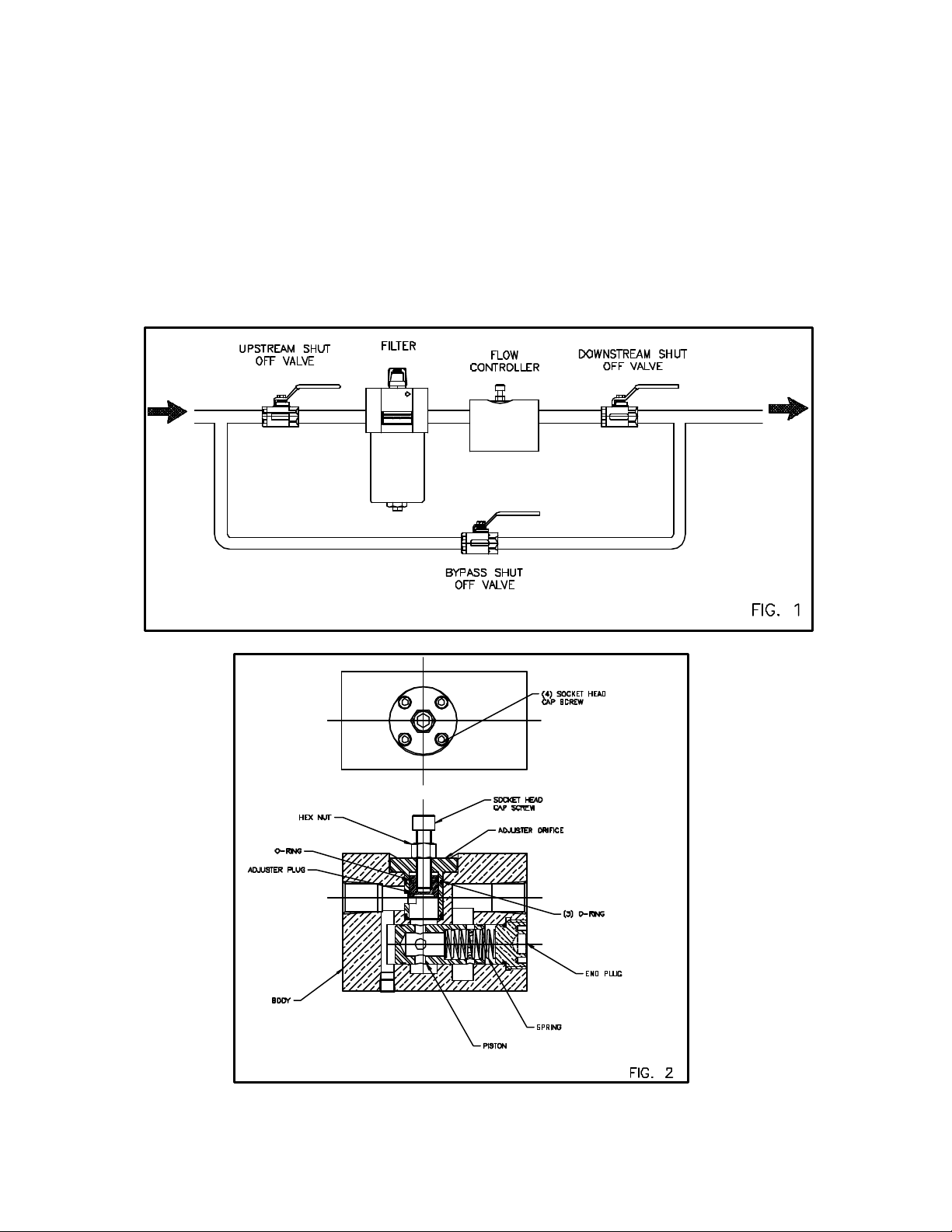
5. Thoroughly clean all the parts that have been removed from the controller by immersing them in a suitable solvent. Thoroughly clean
and flush inside of controller body with the solvent, and drain. Because of the closely fitted parts, it is VERY IMPORTANT that all parts
and surfaces, including valve ports, be COMPLETELY CLEAN. Any dirt, sediment, coating or gummy residue must be completely
removed. Wipe all parts and surfaces dry with a clean, lint-free cloth. CAUTION: in all cleaning operations, be very careful not to
scratch, nick or mark any surfaces or edges.
6. Check all O-rings for damage, and replace if necessary.
7. Insert the piston, the spring, the end cap, and tighten.
8. Insert the adjuster orifice assembly, with the slot facing the inlet port, and install the screws until tight
9. Reinstall controller in system and place in service by following Steps 1-2 listed under the heading “START UP PROCEDURE”.
PRODUCT WARRANTY