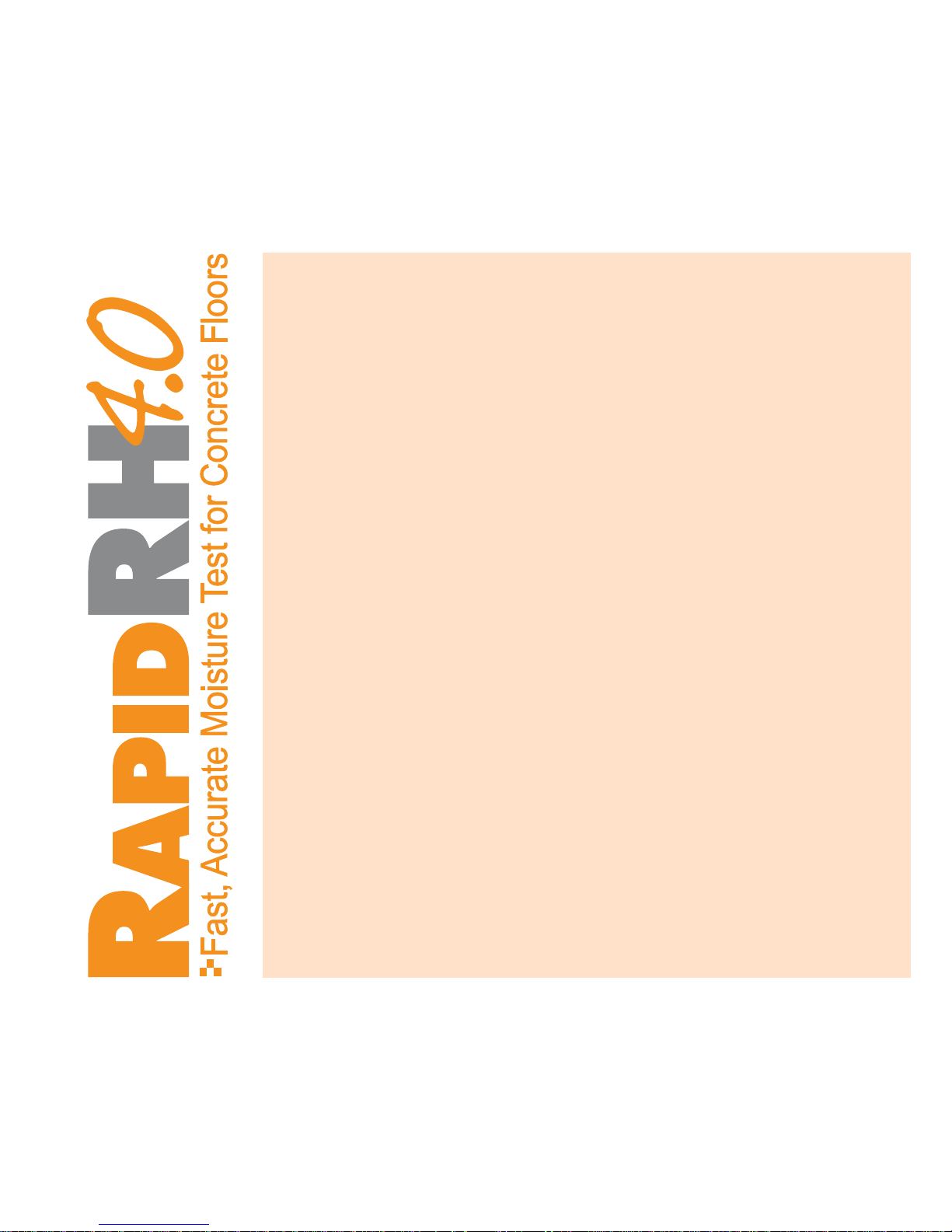
X
E
®
T
he Rapid RH
®
moisture testing system
should be used on any project where
moisture-sensitive floor coverings or coatings
are to be applied over concrete slabs. Owners,
General Contractors, Flooring Contractors/
Installers and Testing Companies need to
be sure the tests they perform are accurate,
repeatable and available to all who need
to know the current moisture condition of
concrete slabs.
R
apid RH
®
significantly improves your
project team’s ability to instantly test and/
or monitor the drying progress of a concrete
slab without adding substantial cost to the
project. The Rapid RH® enables you to take
fast, accurate periodic readings that fully
comply with industry standards. The Rapid
RH® “Smart Sensors” are factory-calibrated
and use CMOS Sens
®
technology, to ensure
the sensor’s accuracy and fast equilibration.
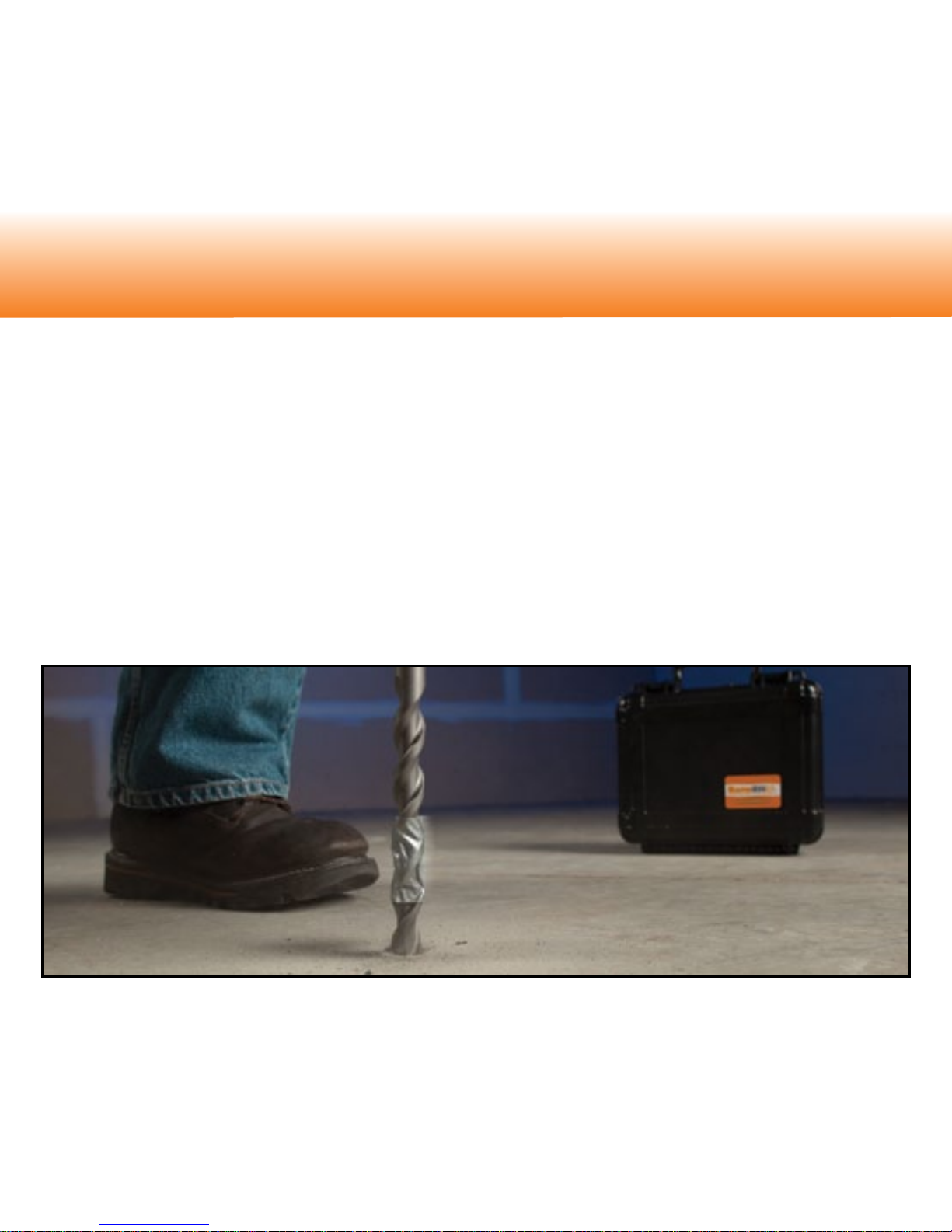
Correct hole-depth is important in complying with the ASTM F2170 standard. Drill
a hole in the concrete slab to the required depth using a rotary-hammer drill and a
¾” (19mm)-diameter masonry drill bit. Per the ASTM F2170 standard, drill the hole
to a depth equaling 40% of the slab’s thickness for slabs that are drying from one
side, or 20% depth for a slab drying from two sides. For proper Rapid RH® 4.0 EX
installation, be sure to position the drill perpendicular (90˚) to the surface being tested.
TIP: If you do not have a depth-gauge for your drill, mark or tape-off your drill bit
to the correct depth setting. Vacuum around, and periodically in the hole as you
drill to better see your progress and use the depth ruler supplied with your Rapid
RH kit to check your depth progress to keep from over-drilling.
Step 1: Drill the Hole
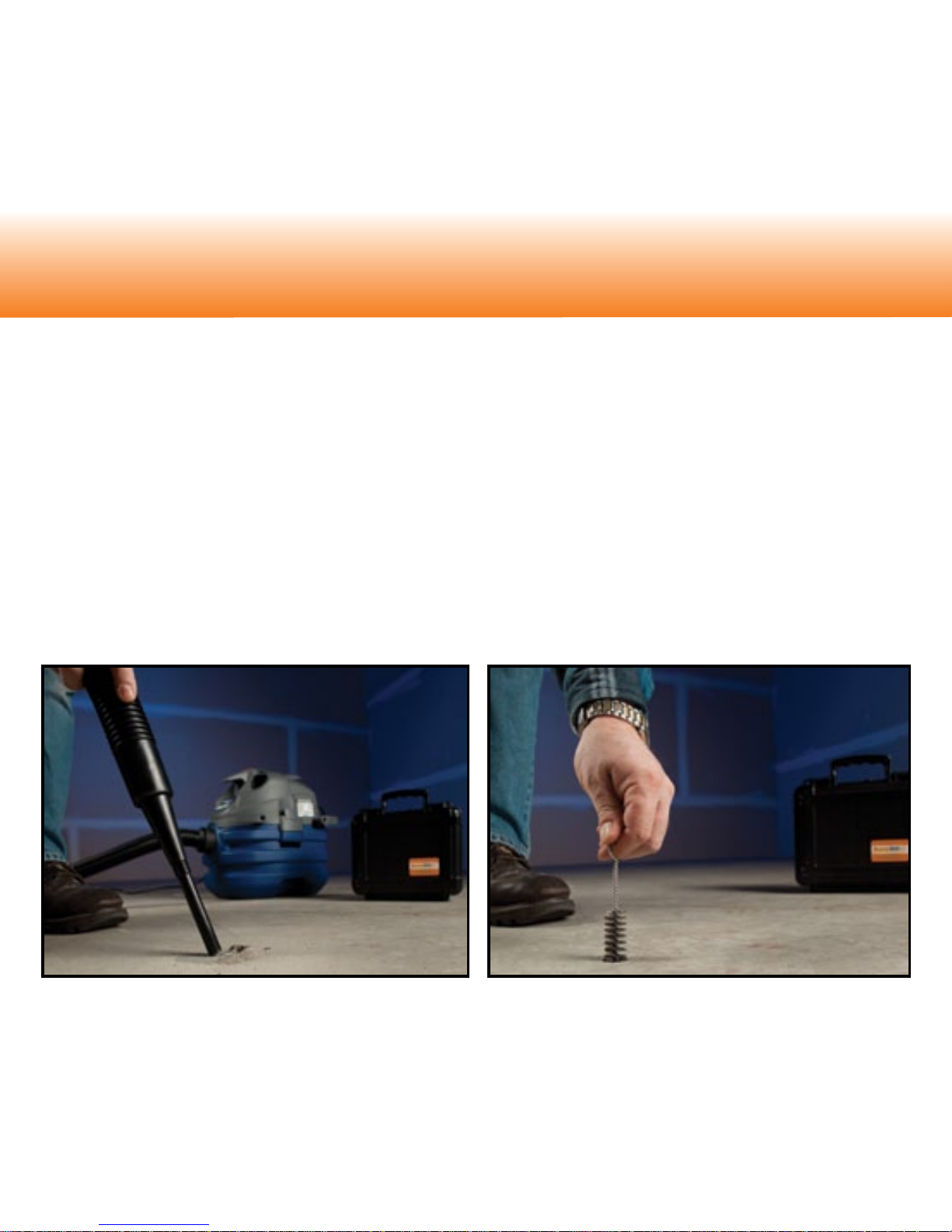
Attach the vacuum attachment to the straight extension of a shop vacuum cleaner
hose* and thoroughly vacuum up the dust in and around the hole.
Next, insert the wire bristle brush into the hole. Turn the brush several times to loosen
pulverized concrete from the walls of the hole. Vacuum again. Repeat this step twice
to ensure no loose concrete particles remain in the hole.
Step 2: Clean the Hole
*The vacuum attachment may require an adapter depending on vacuum model.
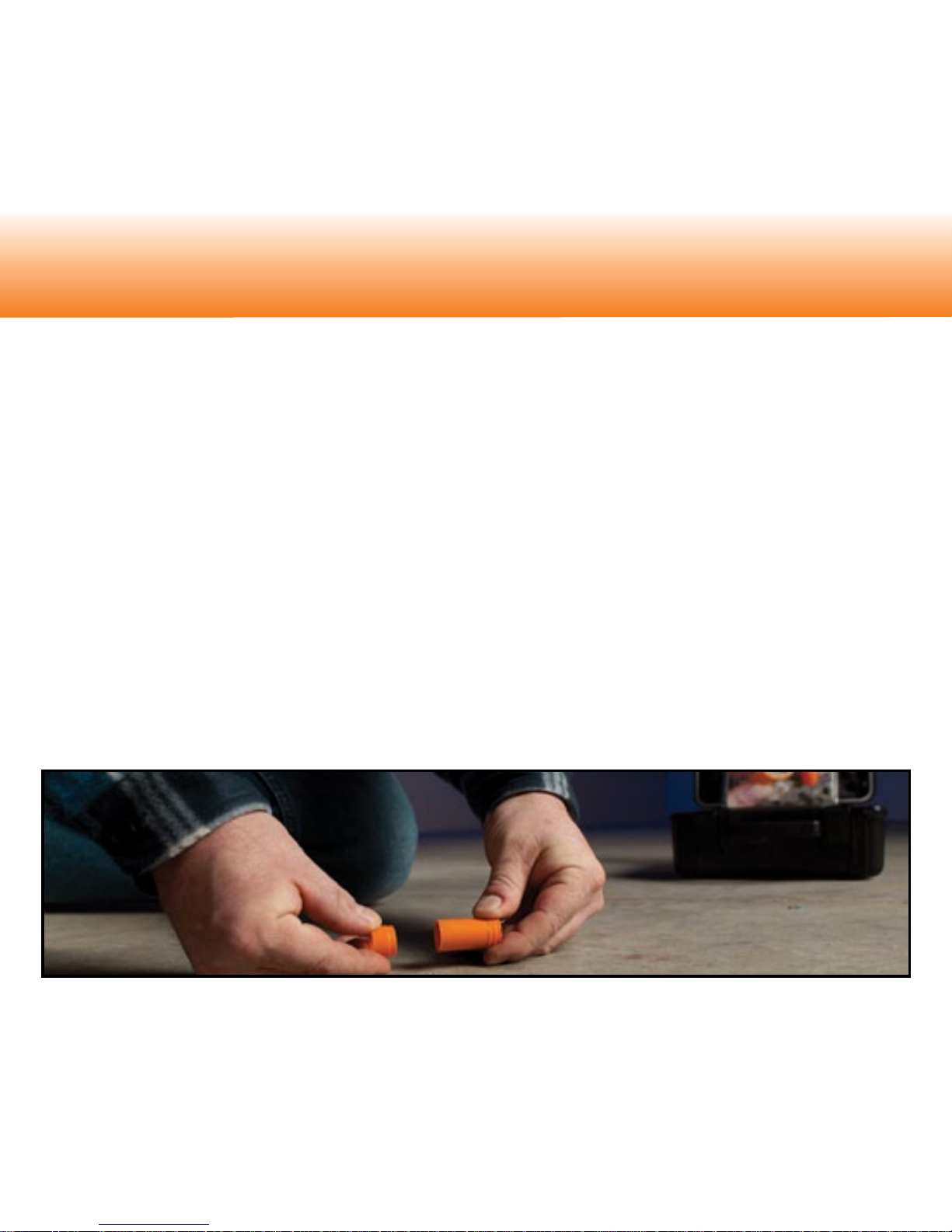
NOTE: The newest ASTM F2170 standard (F2170-11) has a revision (from the previous -09
version) calling for the ‘sleeve’ (liner) to go from the top to the bottom of the hole. The new
Rapid RH
®
extension insert approach allows you to easily adhere to this new revision of
the ASTM test method. Additionally, the main, smooth sleeve section of the Smart Sensor
barrel is now detachable, allowing for even more convenient use of only the bottom ‘nned’
section of the barrel in shallow-hole applications such as thin topping slabs, etc.
Directly out of the package, the Smart sensor is 1.6” or 40% of a 4” slab. ASTM F217011, Section 10.2 states: “Slab drying from top only (Example: slab on ground with vapor
retarder below, or slab on metal deck): 40% depth. Slab drying from top and bottom
(Example: elevated structural slab not in metal deck): 20% depth)”. Each Smart Sensor
pack includes ten (10) short (0.4”) extensions that can be inserted into the Smart Sensor
barrel to enable use in thicker slabs. Adding one insert extends the Smart Sensor barrel
length to 2” for testing 5”-thick slabs to the 40% depth. Keep any unused extensions for
future jobs. If need be, you can use additional extensions to increase the length of the
sensor barrel for thicker slab applications.
Step 3: Insert the Smart Sensor
Adding an extension