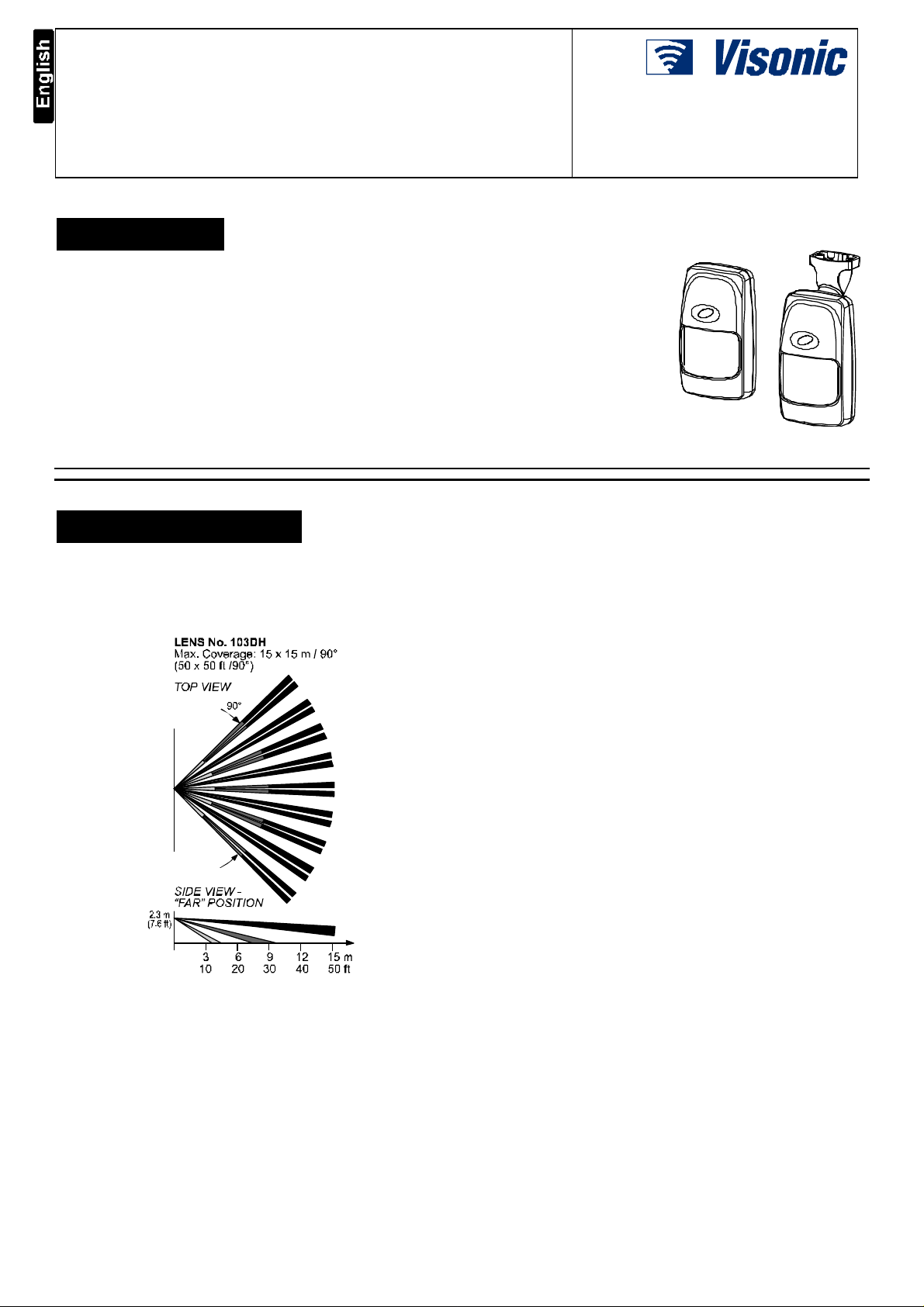
DISCOVERY QUAD
MCW
Wireless PowerCode Quad PIR Detector
1. FEATURES
• Employs a real quad element low-noise pyroelectric sensor
• Includes a fully supervised PowerCode transmitter
• Patented sophisticated motion analysis algorithm - True Motion
Recognition (TMR™)
• Two-position vertical adjustment for coverage pattern
• Integral swivel bracket for wall or ceiling installation
• Programmable motion event counter - ON or OFF (default)
• Front and back tamper switches for improved tamper protection
• Full stabilization achieved 30 seconds after power up
• After detection, the detector disables itself to save battery
power. It reverts to the ready state if there is no subsequent
detection throughout the following 2-minute period
2. SPECIFICATIONS
OPTICAL
Detector Type: Quad element low-noise pyroelectric sensor.
Detection Pattern: 90° wide angle lens with 19 quad zones in 3
detection layers. Max. coverage is 15 x 15 m (50 x 50 ft).
Adjustment: 2-position vertical adjustment scale: FAR and NEAR.
Figure 2. Coverage Pattern
ELECTRICAL
Internal Battery: 3 V Lithium battery, Panasonic CR-2 or
equivalent
Nominal Battery Capacity: 750 mAh
Standby Current Drain: 0.015 mA
Transmit Current Drain: 20 mA (including LED)
Battery Life Expectancy: 3 years (for typical use)
Battery Supervision: Automatic reporting of battery status with
each alarm and with periodic supervision message.
FUNCTIONAL
True Motion Event Verification: 2 position selector - 1 (OFF) or
2 (ON) motion events.
Alarm Period: 3 seconds.
Installation Instructions
• Automatic termination of
walk-test after 15 minutes
• Low current consumption
• Microprocessor-controlled
temperature compensation
• Sealed chamber protects the
optical system
• White light protection
• Elegantly styled, sturdy case
• Keyhole-shaped slot for
easy removal of PCB
Visual Indications:
LED lights for about 3 seconds upon transmission of alarm &
tamper messages and upon each motion detection in the walk
test mode.
LED flashes during the power-up stabilization period, or after
restoring (pressing) the tamper switch.
LED does not light upon transmission of supervision
messages.
Rearm Timer: Rearms the detector 2 minutes after the last alarm.
Timer disabled in the walk test mode.
WIRELESS
Frequency (MHz): 315, 433.92, 868.95, 869.2625 or other
frequencies according to local requirements.
Transmission Sequence: 3 data bursts at variable intervals
within 3 seconds.
Encoding: 24-bit ID, over 16 million possible combinations.
Total Message Length: 36 bits.
Tamper Alert: Reported when a tamper event occurs and in any
subsequent message, until the tamper switch is restored.
Supervision Message: Once per 15 minutes, 60 minutes or
according to local standards.
MOUNTING
Height:
With bracket : Up to 3.6 m (12 ft)
Without bracket: 2 - 2.6 m (6.5 - 8.5 ft)
Installation Options:
With bracket: Surface or ceiling
Without bracket: Surface or corner
Bracket Adjustment: 20° downward, 20° left and right.
ENVIRONMENTAL
RFI Protection: >30 V/m up to 1000 MHz.
Operating Temperatures: -10°C to 50°C (14°F to 122°F).
Storage Temperatures: -20°C to 60°C (-4°F to 140°F).
Compliance with Standards: Designed to meet FCC Part 15
and Directive 1999/5/EC of the European Parliament.
PHYSICAL
Dimensions (H x W x D): 117 x 65 x 47 mm.
(4-5/8 x 2-9/16 x 1-7/8 in.).
Weight: 92 g (3.25 oz) without bracket, 107 g (3.75 oz) with
bracket.
Color: White
PATENTS: U.S. Patent No. 5,693,943
Figure 1. External View
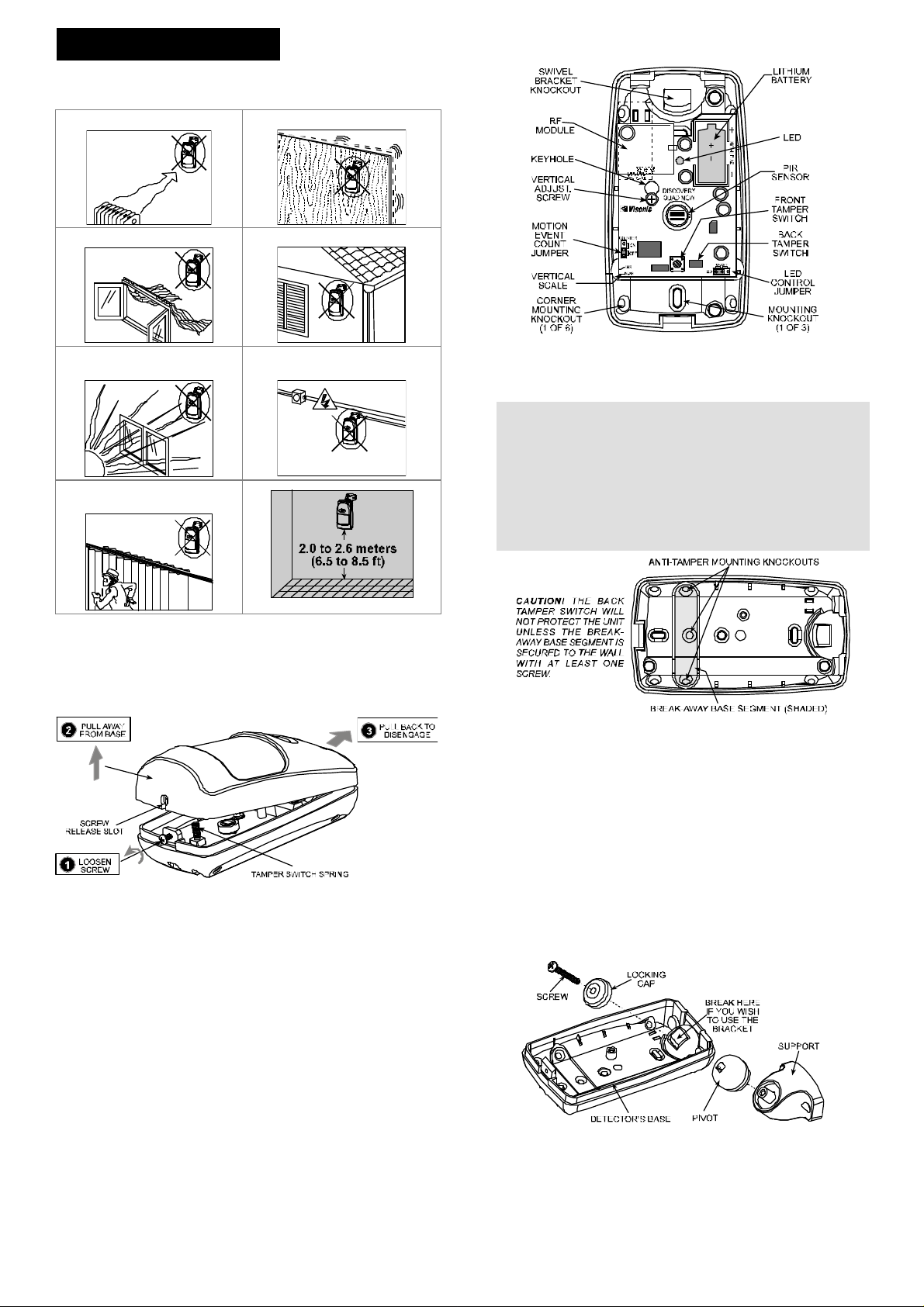
3. INSTALLATION
3.1 Installation Hints
To minimize false alarms:
Do not aim at heat sources Mount on solid, stable surfaces
Do not expose to air draughts
Do not install outdoors
Prevent direct sunlight from
reaching the detector
Do not install behind
partitions
Keep wiring away from electrical
power cables
3.2 Battery Insertion
It is recommended to power up the detector and let the target
receiver “learn” the transmitter’s ID before actual installation. This
can be done only after battery installation.
1st.Remove the front cover as shown in Figure 3.
Figure 3. Cover Removal
B. Insert the battery into the battery clip - observe polarity (see
Figure 4).
3rd. Press the tamper switch once and release it. This will perform
the reset necessary for smooth power up.
4th. Put the cover on and observe the LED. It will flash until the
detector stabilizes (within about 30 seconds).
Figure 4. Inside View
3rd.Punch out the mounting knockouts at the base (for surface
mounting) or mounting knockouts at the angled sides of the
base (for corner mounting).
Attention! The unit has a special tamper switch under the PCB. As
long as the PCB is seated firmly within the base, the switch lever will
be pressed against a special break-away base segment that is
loosely connected to the base (Figure 5). Be sure to fasten the
break-away segment to the wall. If the detector unit is forcibly
removed from the wall, this segment will break away from the base,
causing the tamper switch to open. It is advisable to pierce the
anti-tamper knockouts from within the base outward, while
pressing the rear surface of the break-away segment against a
piece of wood.
Figure 5. Anti-Tamper Break-Away Base Segment
4th.Hold the base against the wall at the selected location, mark
the drilling points, drill the holes and attach the base to the
wall.
5th.Return the PCB to its place: align the ”keyhole” with the head
of the vertical adjustment screw, press the PCB against the
base, slide the PCB up and temporarily tighten the screw.
3.5 Mounting with Swivel Bracket
1st.Remove the front cover as shown in Figure 3.
2nd.Loosen the vertical adjustment screw, slide the PCB down
and remove it via the “keyhole” (see Figure 4).
3rd.Punch out the large knockout in the round bulge at the top
part of the base (see Figure 6).
4th.Assemble the bracket as shown in Figure 6.
3.3 Enrolling the Transmitter ID
Refer to the target receiver’s installation instructions and follow
the procedure given there for “teaching” the transmitter's ID. It is
much easier to carry out this operation in close proximity to the
receiver.
3.4 Mounting without Swivel Bracket
1st.Remove the front cover as shown in Figure 3.
2nd.Loosen the vertical adjustment screw, slide the PCB down
and remove it via the “keyhole” (see Figure 4).
5th.Rotate the bracket to the desired position (see Figure 7) but
do not yet tighten the screw fully.
Figure 6. Attaching the Bracket