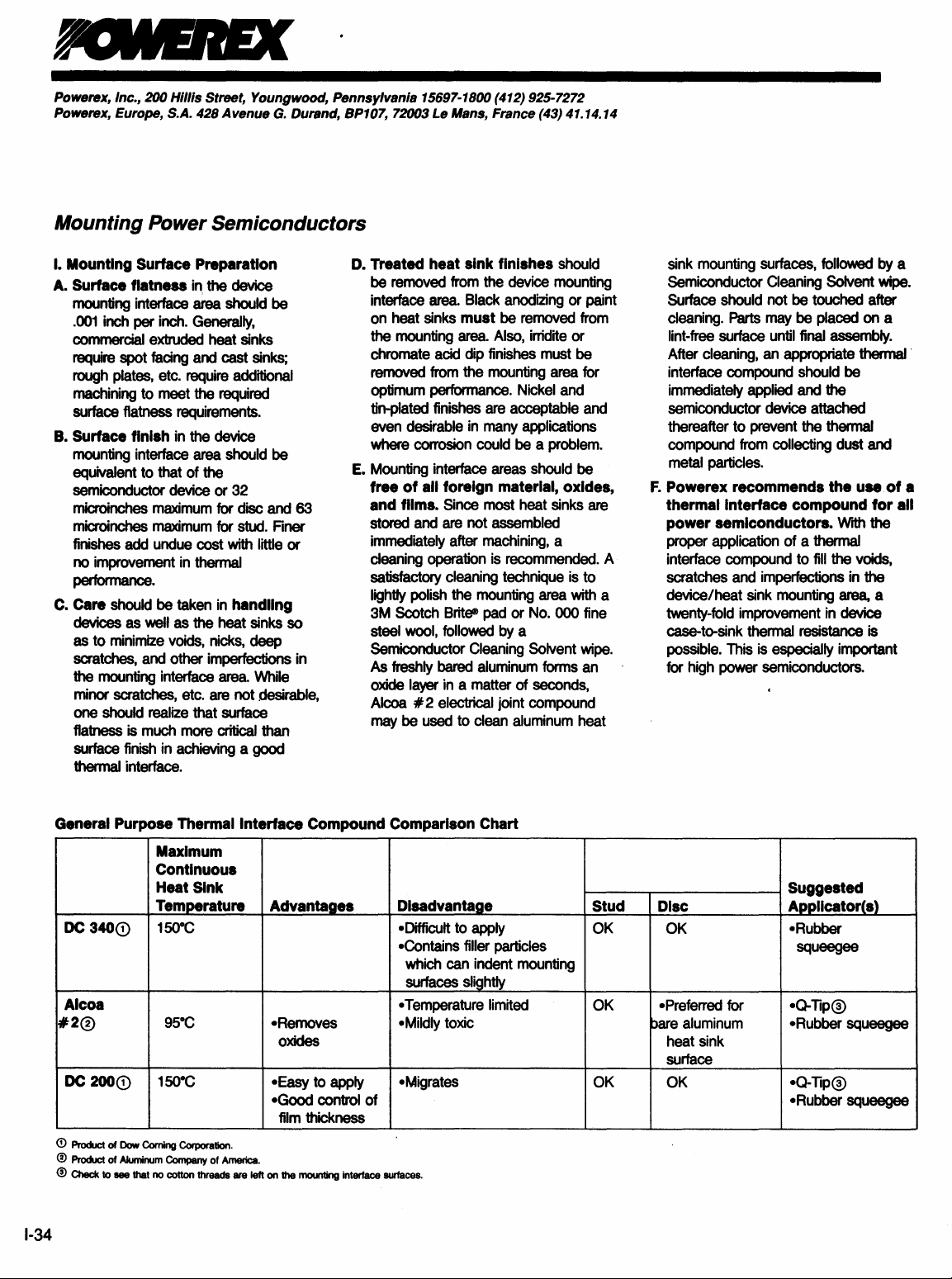
Powerex, Inc., 200 Hillis Street, Youngwood, Pennsylvania 15697-1800 (412) 925-7272
Powerex, Europe, S.A. 428 Avenue
G.
Durand, BP107, 72003
Le
Mans, France (43) 41.14.14
Mounting Power Semiconductors
D.
I. Mounting Surface Preparation
in
the
A. Surface flatness
mounting
.001
commercial
require
rough
machining
surface
B.
Surface finish
mounting
equivalent
semiconductor
microinches
microinches
finishes
no
performance.
C.
Care
devices
as
scratches,
the
minor
one
flatness is
surface
thermal
interface
inch
per
inch.
extruded
spot
facing
plates,
etc.
to
meet
flatness
interface
to that of the
maximum
maximum
add
undue
improvement
should
be
as
well
to
minimize
and
mounting
interface
scratches,
should
realize
much
finish
in
interface.
requirements.
in
device
taken
as
voids,
other
achieving
in
etc.
more
device
area
should
Generally,
heat
sinks
and
cast
sinks;
require
additional
the
required
the
device
area
should
or
32
for
disc
and
for
stud.
cost with little or
thermal
in
handling
the
heat
sinks
nicks,
deep
imperfections
area.
While
are
not
desirable,
that
surface
critical
than
a good
be
be
Finer
so
63
in
Treated heat sink finishes
be
removed
interface
on
heat
the
mounting
chromate
removed
optimum
tin-plated
even
where
E.
Mounting
free
and films.
stored
immediately
cleaning
satisfactory
lightly
3M
Scotch
steel
Semiconductor
As
freshly
oxide
from
the
device
area.
Black
anodizing
sinks
must
be
area.
Also,
acid
dip
finishes
from
the
mounting
performance.
finishes
desirable
corrosion
interface
of
all foreign material, oxides,
and
operation
polish
wool,
in
many
could
Since
most
are
not
after
machining,
cleaning
the
mounting
Britst
pad
followed
are
areas
assembled
is
recommended.
technique
by
Cleaning
bared
aluminum
layer
in
a matter
Alcoa :# 2 electrical joint
may
be
used
to
clean
should
mounting
or paint
removed
irridite
or
must
area
Nickel
and
acceptable
applications
be a problem.
should
heat
sinks
a
is
area
with
or
No.
000
a
Solvent
forms
of
seconds,
compound
aluminum
from
be
for
and
be
are
to
fine
wipe.
an
heat
sink
mounting
Semiconductor
Surface
cleaning.
lint-free
After
cleaning,
interface
immediately
semiconductor
thereafter to
compound
metal
particles.
F.
Powerex recommends the use.
thermal Interface compound
power semiconductors.
proper
A
interface
scratches
a
device/heat
twenty-fold
case-to-sink
possible.
for
high
surfaces,
Cleaning
should
not
Parts
may
surface
an
compound
applied
device
prevent
from
application
compound
and
imperfections
sink
improvement
thermal
This
is
power
semiconductors.
followed
Solvent
be
touched
be
placed
until
final
appropriate thermal .
should
and
after
on
assembly.
be
the
attached
the
thermal
collecting dust
and
for
With
the
of a
thermal
to
fill
the
voids,
in
the
mounting
especially
area,
in
device
resistance
important
a
is
by
a
wipe.
a
of
all
a
General Purpose Thermal Interface Compound Comparison Chart
Maximum
Continuous
Heat Sink
DC340Q)
Temperature
1500C
Advantages
Disadvantage
-Difficult
-Contains filler particles
which
can
surfaces
Alcoa
#2®
95°C
-Removes
-Temperature
-Mildly
toxic
oxides
DC
2OOQ)
150°C
-Easy
to
apply
-Migrates
-Good control of
film
thickness
<D
Product of
Dow
® Product of
@)
Check
Coming Corporation.
Aluminum
to
see
that
Company of America.
no
cotton threads
are
left
on
the mounting interface
surfaces.
1-34
to
apply
indent
slightly
mounting
limited
Stud
OK
OK
OK
Disc
OK
-Preferred
~ealuminum
heat
surface
for
sink
OK
Suggested
Appllcator(s)
-Rubber
squeegee
-Q-Tip@
-Rubber
squeegee
-Q-Tip@
-Rubber
squeegee
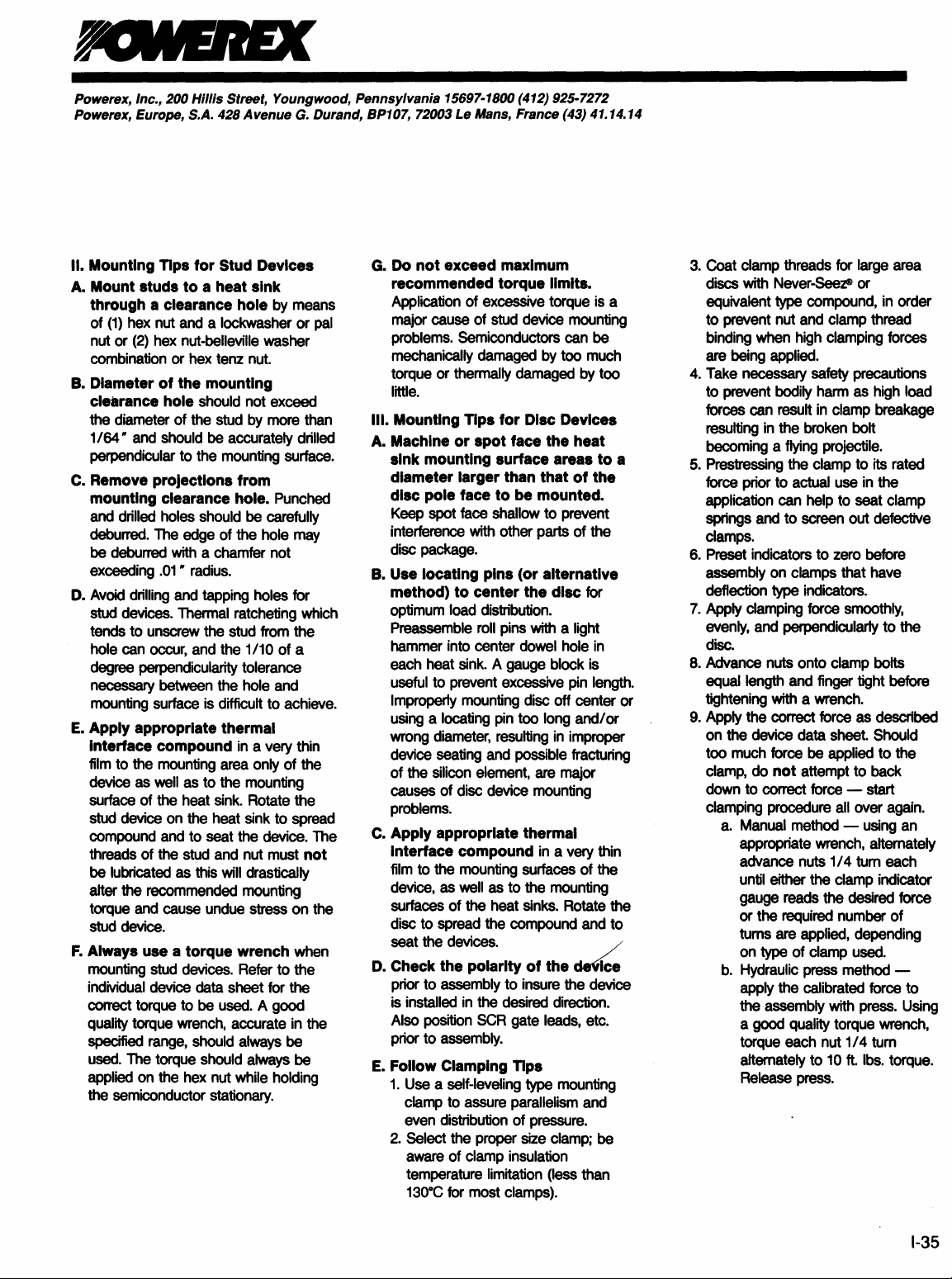
Powerex, Inc., 200 Hillis Street, Youngwood, Pennsylvania 15697-1800 (412) 925-7272
Powerex, Europe, S.A. 428 Avenue
G.
Durand, BP107, 72003 Le Mans, France (43) 41.14.14
II. Mounting TIps
A.
Mount studs
for
Stud Devices
to
a heat sink
through a clearance hole
of
(1)
hex
nut
and
a lockwasher or
nut or
(2)
hex
nut-belleville washer
hex
tenz
combination or
B.
Diameter
of
the mounting
clearance hole
the diameter of
1/64"
and
perpendicular to the
C.
Remove proJections from
the
should
nut.
should
not exceed
stud
by
be
accurately drilled
mounting
mounting clearance hole.
and drilled holes
deburred.
be
deburred
exceeding
D.
Avoid
drilling
stud
devices.
tends to
hole
degree perpendicularity tolerance
necessary
mounting
E.
Apply appropriate thermal
unscrew
can
Interface compound
film
to the
as
device
surface
stud
compound
threads of the
be
alter
torque
stud device.
F.
Always use a torque wrench
mounting
individual
correct
quality torque
specified
used.
applied
the semiconductor
of the heat
device
lubricated as
the
recommended
and
torque to
range,
The
on
should
The
edge
with
a chamfer not
.01
"
radius.
and
tapping holes for
Thermal
the
occur,
and
between
surface
mounting
well
on
and
cause
stud
device
torque
the
the hole
is
as
to the mounting
sink.
the heat sink to
to seat the device.
stud
and
this
undue
devices.
data
be
wrench,
should
should
hex
nut while holding
stationary.
be
of the hole
ratcheting
stud
the 1/10 of a
difficult to
in
a very thin
area
only of the
Rotate the
nut
will
drastically
mounting
stress on the
Refer
sheet for the
used.
accurate
always
always
by
more
surface.
Punched
carefully
from
and
achieve.
must
to the
A
good
in
be
means
pal
than
may
which
the
spread
The
not
when
the
be
G.
Do
not
exceed maximum
recommended torque limits.
Application of excessive torque
major
cause
of
stud
device
problems.
mechanically
torque or thermally
little.
III. Mounting Tips
A.
Machine
Semiconductors
damaged
or
spot face the heat
by
damaged
for
Disc Devices
can
too
sink mounting surface areas
diameter larger than that
to
disc pole face
Keep
spot
face
interference
disc
package.
B.
Use locating pins (or alternative
method)
optimum
Preassemble
hammer
each
useful
Improperly
using
wrong
device
of
causes
problems.
C.
Apply appropriate thermal
to
load
into center
heat
sink. A gauge
to prevent excessive
mounting
a locating
diameter,
seating
the silicon
of disc device mounting
Interface compound
film
to
the
mounting
device,
surfaces of the heat
disc to
seat the
D.
Check the polarity
prior to assembly to
is
Also
prior to
E.
Follow Clamping TIps
1.
2.
as
well
spread
devices.
installed
Use
clamp
even
Select the proper
aware
temperature limitation (less than
130°C for most
in
position
assembly.
a self-leveling type mounting
to
assure
distribution of
of
clamp
be mounted.
shallow to prevent
with
other parts of the
center the disc for
distribution.
roll
pins
with
a light
dowel
hole
block
disc off center or
pin
too
long
resulting
and
element,
as
the compound and to
the
desired
SCR
in
possible fracturing
are
major
in
a very thin
surfaces of the
to the
mounting
sinks.
Rotate the
of
the deVIce
insure
the device
direction.
gate
leads,
parallelism
pressure.
size
clamp;
insulation
clamps).
is
a
mounting
be
much
by
too
to
of
the
in
is
pin
length.
andlor
improper
/
etc.
and
be
3.
Coat
clamp
threads for
discs
with
Never-Seez®
equivalent
to prevent nut
binding
are
4.
Take
to prevent bodily
forces
resulting
a
becoming a flying
5.
Prestressing
force prior to actual
application
springs
clamps.
6.
Preset
assembly
deflection type indicators.
7.
Apply
evenly,
disc.
8.
Advance
equal
tightening
9.
Apply the
on
too
clamp,
down to correct force - start
clamping
a.
b.
type
and
when
high
being
applied.
necessary
can
result
in
the
broken
the
can
and
to
screen
indicators to
on
clamps that
clamping
and
perpendicularly to the
nuts onto clamp bolts
length
and
with
a
correct
the device data
much
force be
do
not
attempt to
procedure allover
Manual
appropriate
advance
until
gauge
or the
turns
on
HydrauliC
apply
the assembly
a
torque each nut
alternately to
Release
method -
nuts
either the
reads
required
are
applied,
type of
press method -
the calibrated force to
good
quality torque
press.
large
area
or
compound,
clamp
clamping
safety
harm
in
clamp breakage
projectile.
clamp
help
force
finger tight before
wrench.
force as described
sheet.
applied
wrench,
1/4
the
clamp
with
10ft.
in
order
thread
forces
precautions
as
high
bolt
to its
rated
use
in
the
to seat clamp
out defective
zero
before
have
smoothly,
Should
to the
back
again.
using
an
alternately
tum each
clamp
indicator
desired
force
number of
depending
used.
press.
Using
wrench,
1/4
tum
Ibs.
torque.
load
1-35

Powerex, Inc., 200 Hillis Street, Youngwood, Pennsylvania 15697-1800 (412) 925-7272
Powerex, Europe, S.A.
F.
Install
disc
assemblies
way
that
the
always
semiconductor
affected by electrical connections or
supports. Only one of the
may
mounting bracket; cable and bus
connections that
sinks must
relief built
G.
IV.
Powerex recommends the use of a thermal
interface compound for all power
semiconductors. With the proper
application of a thermal interface
compound to fill the air voids, scratches,
and imperfections
mounting interface area, one can achieve
up to a twenty-fold improvement in device
case-to-sink thermal resistance as well as
retard oxidation or corrosion. The General
Purpose Thermal Interface Compound
Comparison Chart included in this
application information presents a
comparison of three different types of
thermal interface compounds. These
compounds are typical of those that are
commercially available; they have been
evaluated and tested by Powerex and have
been found to exhibit good field
performance. When property applied and
mounted per the recommendations
included herein, the use of these
compounds will allow the user to meet the
case-to-sink thermal resistance values
published on the Powerex device data
sheet
be
centered
be rigidly attached to a bus bar
be flexible or have stress
in.
Develop a thorough
procedure
every detail in mounting a disc is much
more critical than
device. Successful and reliable device
operation depends on itl
Application
428
Avenue
clamping
on
so as not to be
In
such
force
the
G.
Durand, BP107, 72003 Le Mans, France (43) 41.14.14
a
will
two heat sinks
bar
tie
to the other heat
disc
mounting
as attention to each and
in
mounting a stud
of
Thermal
in
the device/heat sink
Compounds
or
V.
Tips
For
Applying
Interface
A.
Always
mounting
to application of the thermal interface
a
compound.
Select
B.
Interface
application.
limitations, advantages, disadvantages,
etc. to see that they are compatible
with your needs.
Apply
C.
Interface
film
(s)
mounting surface(s). Rotate the device
on the heat sink(s) to spread
compound and to seat the device.
Thermal interface compound may
applied to the device mounting
interface(s)
sink flatness, finish, and surface
cleaning have been property
performed. Compound should still
applied in a very thin film and then
device rotated on heat sink per
previous directions.
Wipe
D.
from
with a Semiconductor Cleaning
Solvent and a lint-free towel after
mounting the device. Otherwise,
thermal compound on the insulator
(glass or ceramic) housing could
collect dust and metal particles and
cause arc-over.
E.
Use
sparingly.
compound is a major cause of device
mounting problems. The thermal
interface compound should appear
only as a thin, moist film when
properly applied
Compounds
perform
surface
the
appropriate
compound
appropriate
compound
to the device mounting interface
as well as to the heat sink
only
away
edges
thermal
Applying too much
Thermal
the
necessary
preparation
thermal
for
your
Note the temperature
thermal
In a
very
provided device/heat
excess
compound
of
the
contact
interface
to
compound
a mounting surface.
area
prior
thin
be
be
1-36