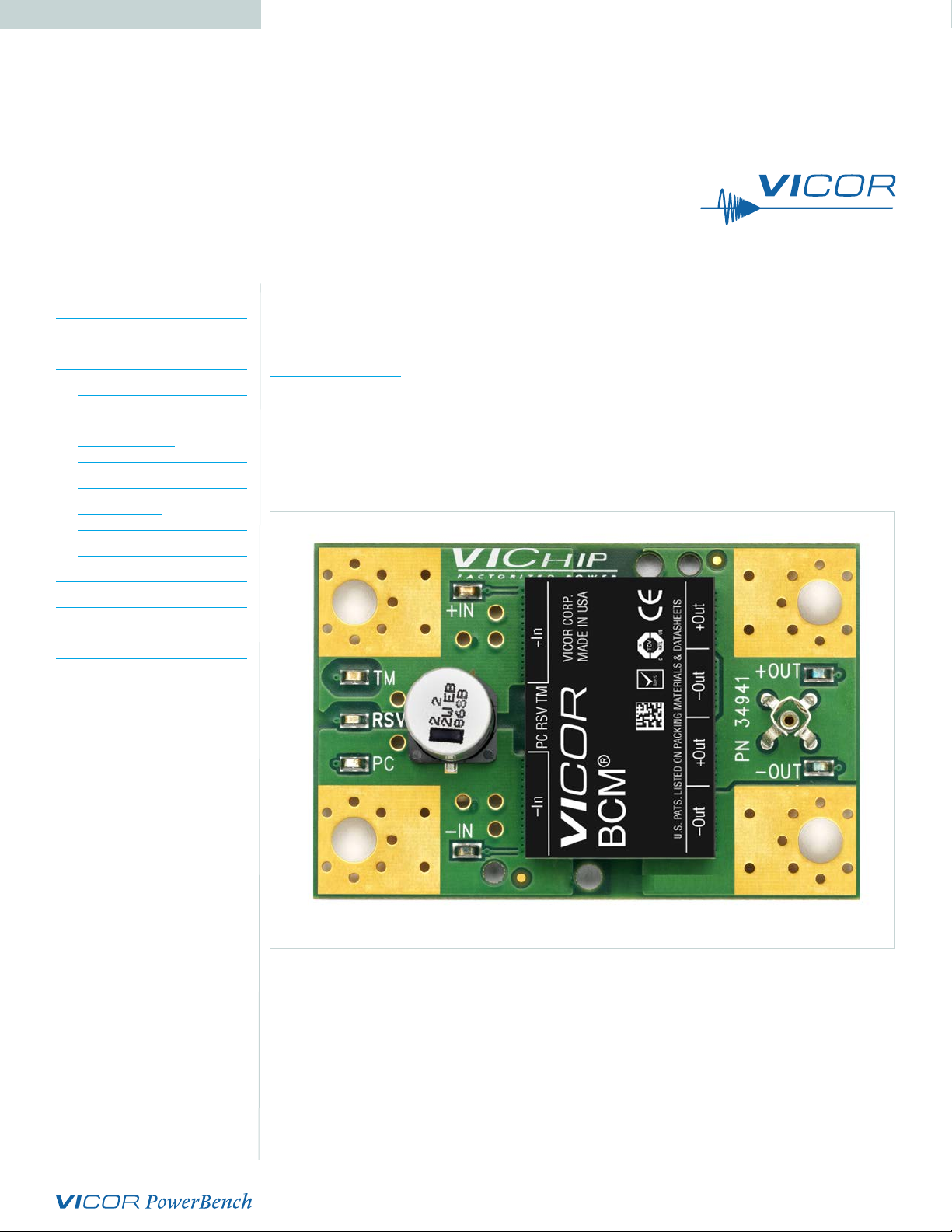
USER GUIDE | UG:001
VI Chip® BCM® Evaluation Board
Contents Page
Introduction 1
Features 1
Set Up 3
+IN, –IN 3
+ OUT, –OUT 3
Output Voltage
Measurement Jack (J1) 3
Paralleling 3
Input Current
Measurement 4
Efficiency Measurement 4
Recommended Hardware 5
Thermal 5
Caution 5
Ordering Information 5
Introduction
The evaluation board offers a convenient means to evaluate the performance of the Vicor BCM bus
converter and has been optimized for user convenience. Refer to the appropriate BCM data sheet for
performance and operating limits. The data sheets are available for downloading at:
www.vicorpower.com.
It is important to remember the fast response of most BCMs can readily show the limitations of the
source, load and associated wiring connected to the evaluation board. Care should be exercised to
minimize stray source and load impedances in order to fully exercise the BCM.
Please refer to Figure 1 for locations of the input and output connections as viewed from the
component side. Wires may be soldered directly to the pads instead of ring lugs if desired to minimize
circuit impedances.
Features
Oscilloscope probe jack for output voltage and ripple measurements
Simple to use
Ring lug or solder connections
Parallelable
UG:001 Page 1
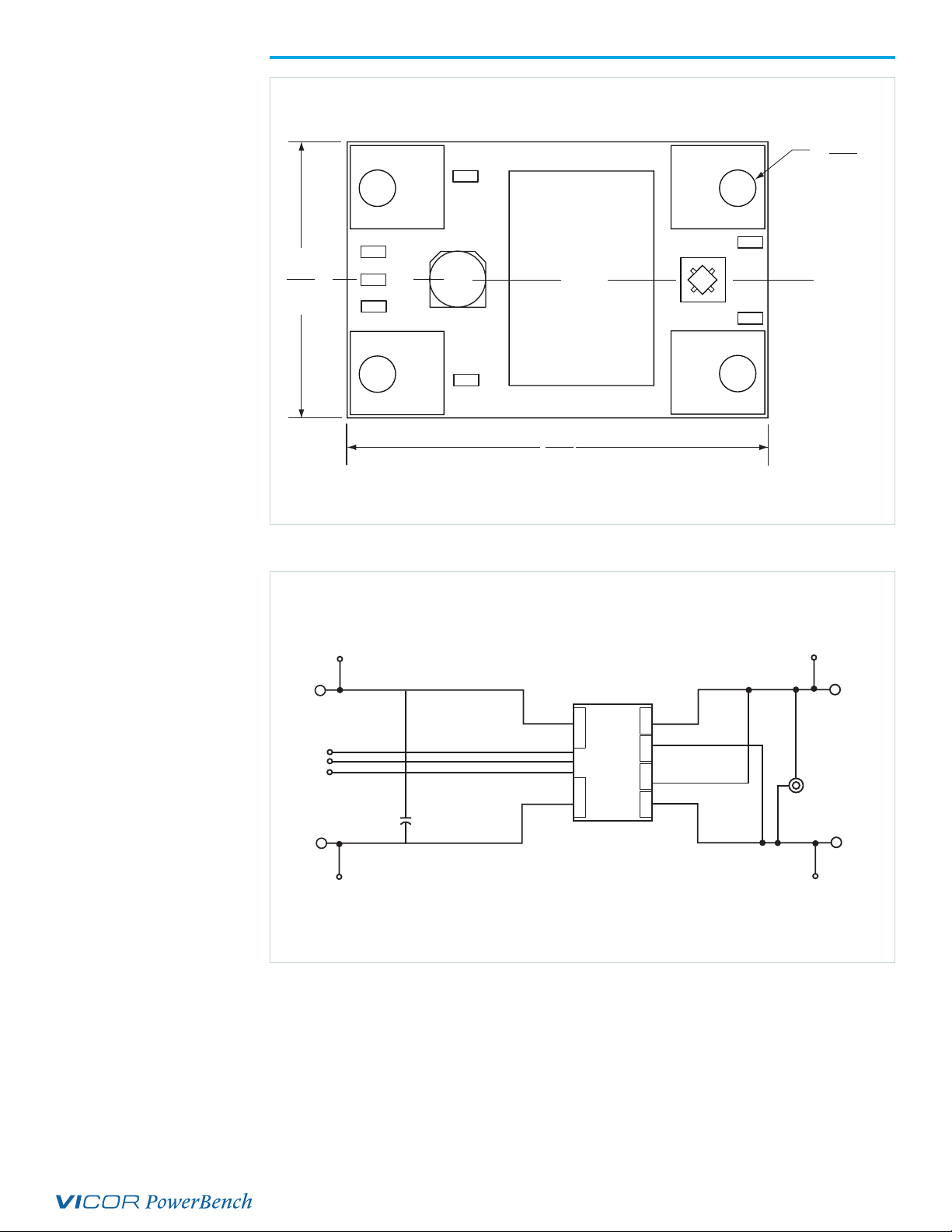
Figure 1
BCM® evaluation board
demo layout and dimensional
drawing, component side
1.65
41.9
TP2
TP1
TM
RSV
PC
+IN
C1
–IN
TP5
TP4
2.52
64,0
BCM
+OUT
J1
– OUT
TP7
TP6
Ø 0.20 Typ
5.08
C
L
Figure 2
BCM evaluation
board schematic
+IN
IN
TM
RSV
PC
C1
2.2 µF
450 V
+OUT
TP5
+In
TM
BCM
RSV
TP2
PC
TP1
TP4
-In
+Out
-Out
+Out
-Out
TP7
TP6
J1
–OUT
UG:001 Page 2
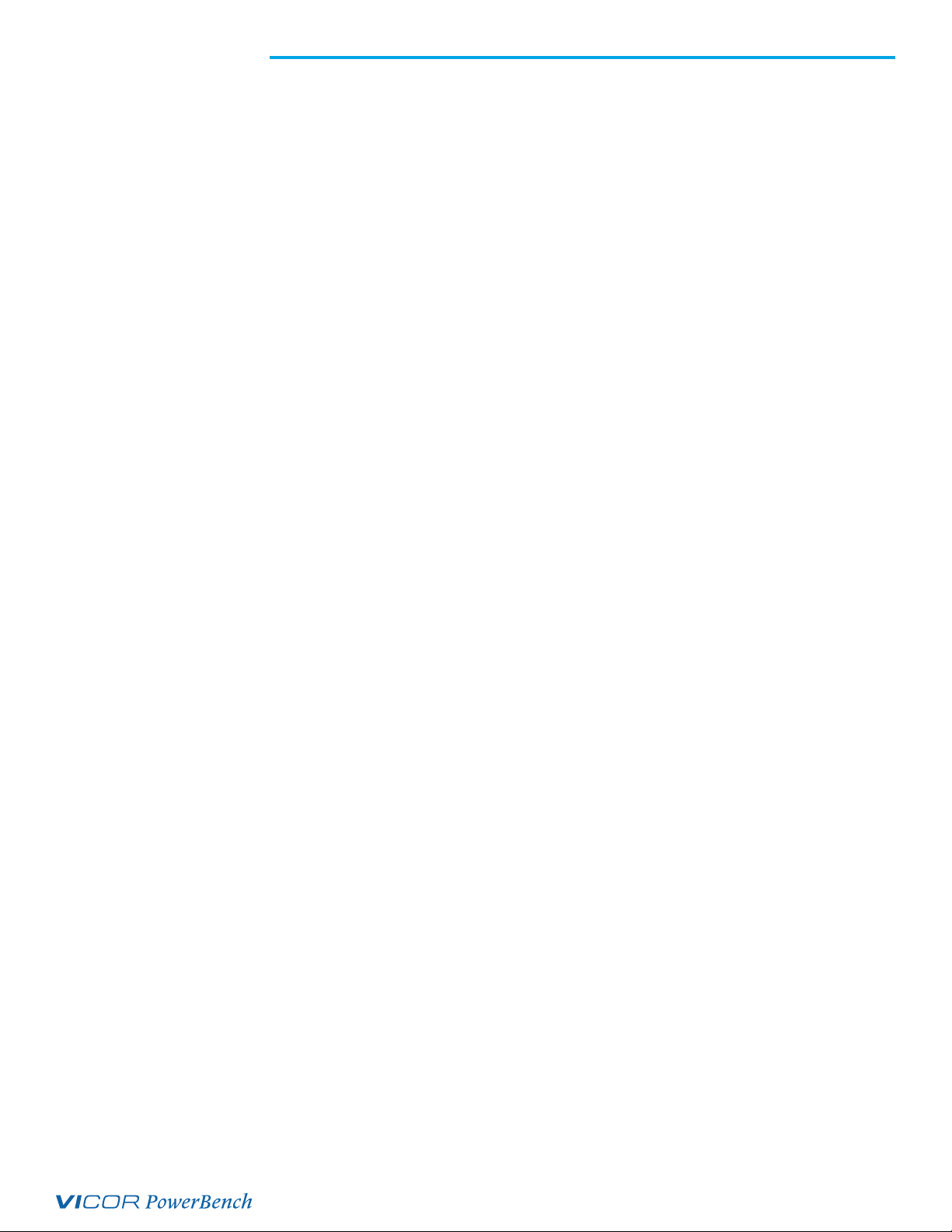
Set Up
The evaluation board should be set up as follows.
Note: Care should be taken to avoid reversing polarities if connecting to the opposite (solder) side of the board.
+IN, –IN
Connect a high-quality, low-noise power supply to the +IN and –IN terminals of the evaluation board.
The interconnect leads should be heavy gauge and as short as possible. Additional capacitance may
have to be added on the evaluation board to make up for impedances in the interconnect leads as
well as deficiencies in the source. It is important to remember that noise from the source, as well as
any input source voltage drops, will appear at the output of the BCM® multiplied by its K factor. Test
points 4 (–IN) and 5 (+IN) can be used to monitor the input and are located on the PCB adjacent to the
input terminals.
+ OUT, –OUT
An electronic or passive load should be connected to +OUT and –OUT terminals of the evaluation
board with short heavy-gauge leads. Most commercially available electronic loads do not have current
slew rates capable of fully exercising the BCM. The evaluation board can be connected directly to
the application for which the BCM is intended. However, the interconnect impedances between
the evaluation board and the application can greatly affect the transient response. For applications
where transient response is critical, the user should consider mounting the BCM directly to the target
application PCB. Test points 6 (–OUT) and 7 (+OUT) can be used to monitor the output and are located
on the PCB adjacent to the output terminals.
Output Voltage Measurement Jack (J1)
This connector is provided to make accurate measurements of the output voltage of the BCM. Many
types of scope probes may be directly connected to this point if the probe is equipped with a removable
plastic sheath. To avoid creating ground loops when making measurements of the output or input
voltage, these measurements should be made separately.
Paralleling
The paralleling and current sharing capability of the devices can be demonstrated by stacking multiple
evaluation boards and interconnecting the inputs and outputs with standoffs of sufficient current
handling capability to create a 3-dimensional array. See Figure 3. When paralleling BCMs, the PC ports
should be connected together to ensure the outputs turn on simultaneously.
UG:001 Page 3