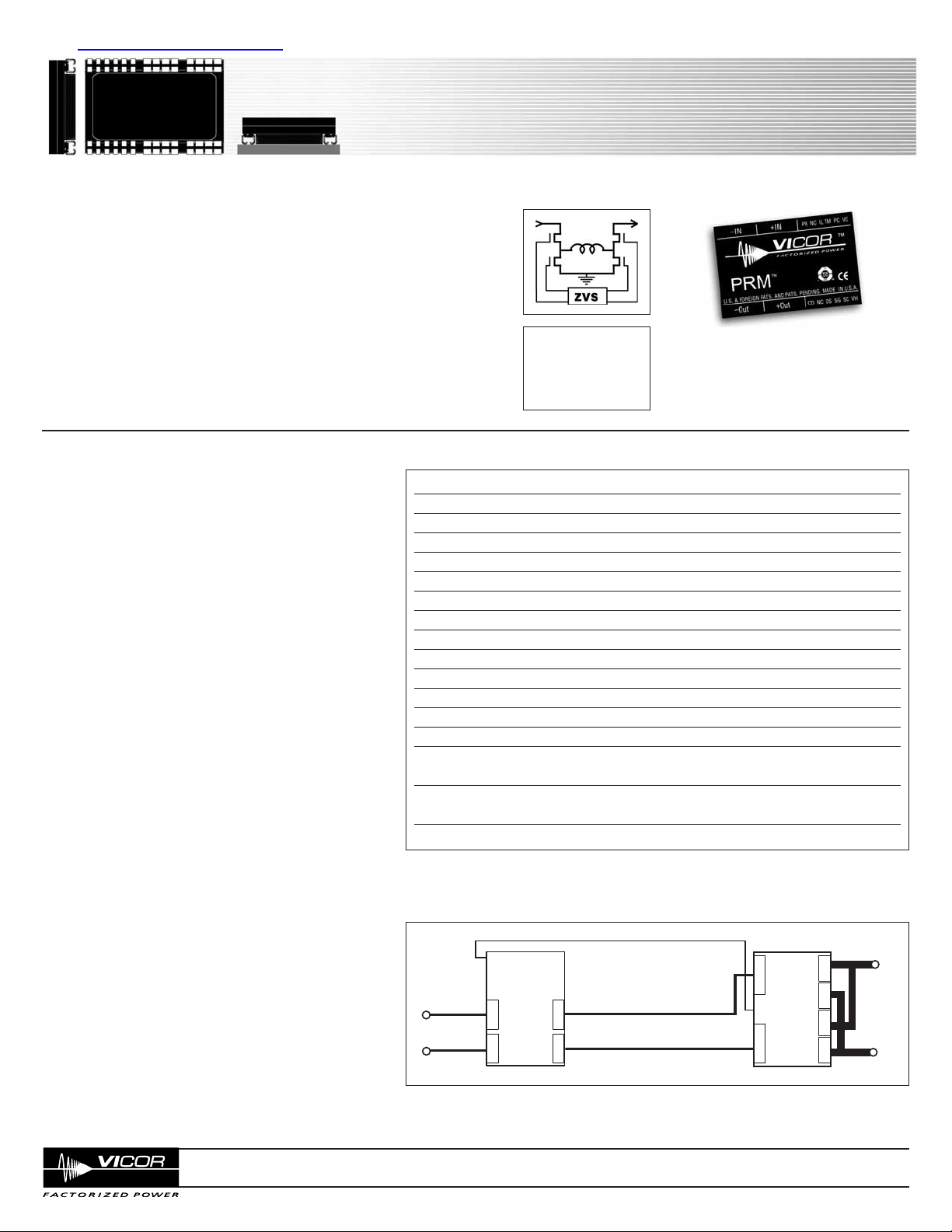
vicorpower.com 800-735-6200 V•I Chip Pre-Regulator Module P048F048T24AL Rev. 1.7
Page 1 of 14
PRELIMINARY
• 48 V input V•I Chip PRM
• Vin range 36 – 75 Vdc
• High density – 875 W/in
3
• Small footprint – 220 W/in
2
• Low weight – 0.5 oz (14 g)
• Adaptive Loop feedback
• ZVS buck-boost regulator
• 1.5 MHz switching frequency
• 96% Efficiency
• 125˚C operation
P048F048T24AL
Vin = 36 – 75 V
V
f = 26 – 55 V
Pf = 240 W
If = 5 A
©
V•I ChipTM– PRM-AL
Pre-Regulator Module
Product Description
The V•I Chip Pre-Regulator Module (PRM) is a very
efficient non-isolated regulator capable of both
boosting and bucking a wide range input voltage. It is
specifically designed to provide a controlled Factorized
Bus distribution voltage for powering downstream
V•I Chip Voltage Transformation Modules (VTMs) —
fast, efficient, isolated, low noise Point-of-Load (POL)
converters. In combination, PRMs and VTMs form a
complete DC-DC converter subsystem offering all of
the unique benefits of Vicor’s Factorized Power
Architecture (FPA): high density and efficiency; low
noise operation; architectural flexibility; extremely fast
transient response; and elimination of bulk capacitance
at the Point-of-Load (POL).
In FPA systems, the POL voltage is the product of the
Factorized Bus voltage delivered by the PRM and the
"K-factor" (the fixed voltage transformation ratio) of a
downstream VTM. The PRM controls the Factorized Bus
voltage to provide regulation at the POL. Because VTMs
perform true voltage division and current multiplication,
the Factorized Bus voltage may be set to a value that is
substantially higher than the bus voltages typically
found in "intermediate bus" systems, reducing
distribution losses and enabling use of narrower
distribution bus traces. A PRM-VTM chip set can
provide up to 100 A or 230 W at a FPA system density
of 200 A/in
3
or 460 W/in3— and because the PRM can
be located, or "factorized," remotely from the POL,
these power densities can be effectively doubled.
The PRM described in this data sheet features a unique
"Adaptive Loop" compensation feedback: a single wire
alternative to traditional remote sensing and feedback
loops that enables precise control of an isolated POL
voltage without the need for either a direct connection
to the load or for noise sensitive, bandwidth limiting,
isolation devices in the feedback path.
Actual size
Parameter Values Unit
+In to -In -1.0 to 85.0 Vdc
PC to -In -0.3 to 6.0 Vdc
PR to -In -0.3 to 9.0 Vdc
IL to -In -0.3 to 6.0 Vdc
VC to -In -0.3 to 18.0 Vdc
+Out to -Out -0.3 to 59 Vdc
SC to -Out -0.3 to 3.0 Vdc
VH to -Out -0.3 to 9.5 Vdc
OS to -Out -0.3 to 9.0 Vdc
CD to -Out -0.3 to 9.0 Vdc
SG to -Out 100 mA
Continuous output current 5 Adc
Continuous output power 240 W
Operating junction temperature (M-Grade) -55 to 125 °C
(T-Grade) -40 to 125 °C
Storage temperature (M-Grade) -65 to 150 °C
(T-Grade) -40 to 150 °C
Case temperature during reflow: 208 °C
The P048F048T24AL is used with any 048 input series VTM to provide a regulated and
isolated output.
DC-DC Converter
Absolute Maximum Ratings
PRM
查询V040F033T060供应商
+In
-In
VTM
K
Ro
+Out
-Out
+Out
-Out
+Out
–Out
VH
SC
SG
OS
NC
CD
Factorized
Bus (Vf)
TM
VC
PC
VC
PC
TM
IL
NC
PR
PRM-AL
+In
Vin
–In
Vout
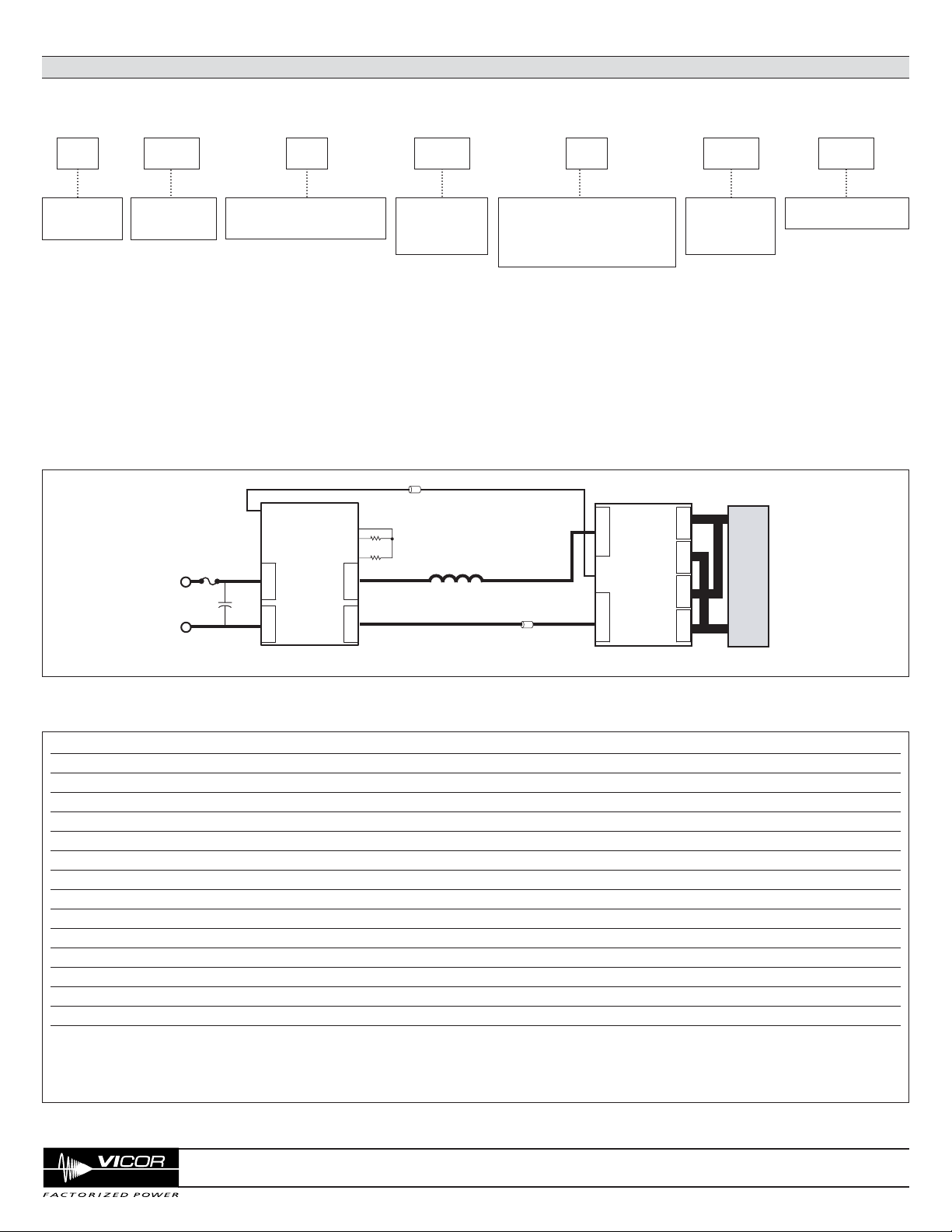
vicorpower.com 800-735-6200 V•I Chip Pre-Regulator Module P048F048T24AL Rev. 1.7
Page 2 of 14
PRELIMINARY
Overview of Adaptive Loop Compensation
Adaptive Loop compensation, illustrated in Figure 1, contributes to
the bandwidth and speed advantage of Factorized Power. The PRM
monitors its output current and automatically adjusts its output
voltage to compensate for the voltage drop in the output
resistance of the VTM. R
OS sets the desired value of the VTM
output voltage, Vout; R
CD is set to a value that compensates for
the output resistance of the VTM (which, ideally, is located at the
point of load). For selection of R
OS and RCD, refer to Table 1 below
or Page 9.
The V•I Chip’s bi-directional VC port :
1. Provides a wake up signal from the PRM to the VTM that
synchronizes the rise of the VTM output voltage to that of the PRM.
2. Provides feedback from the VTM to the PRM to enable the PRM
to compensate for the voltage drop in VTM output resistance, R
O.
Output Power
Designator
(=Pf /10)
P 048 F 048 T 24 AL
Pre-Regulator
Module
Input Voltage
Designator
Product Grade Temperatures (°C)
Grade Storage Operating
T -40 to150 -40 to125
M -65 to150 -55 to125
Configuration
(Fig.21)
Nominal
Factorized Bus
Voltage
AL = Adaptive Loop
Desired Load Voltage (Vdc) VTM P/N
(1)
Max VTM Output Current (A)
(2)
ROS (kΩ)
(3)
RCD (Ω)
(3)
1.0 V048F015T100 100 3.57 26.1
1.2 V048F015T100 100 2.94 32.4
1.5 V048F015T100 100 2.37 39.2
1.8 V048F020T080 80 2.61 35.7
2.0 V048F020T080 80 2.37 39.2
3.3 V040F033T060 60 2.89 32.6
5.0 V048F060T040 40 2.87 33.2
10 V048F120T025 25 2.86 32.9
12 V048F120T025 25 2.37 39.2
15 V048F160T019 18.8 2.49 37.4
24 V048F240T012 12.5 2.37 39.2
28 V048F320T009 9.4 2.74 35.7
36 V048F480T006 6.3 3.16 30.1
48 V048F480T006 6.3 2.37 39.2
Table 1 — Configure your Chip Set using the PRM-AL
Note:
(1) See Table 2 on page 9 for nominal Vout range and K factors.
(2) See “PRM output power vs. VTM output power” on Page 10
(3) 1% precision resistors recommended
Figure 1 — With Adaptive Loop control, the output of the VTM is regulated over the load current range with only a single interconnect between the PRM and
VTM and without the need for isolation in the feedback path.
General Specifications
V•I Chip Pre-Regulator Module
Part Numbering
+Out
–Out
VH
SC
SG
OS
ROS
NC
CD
RCD
Vf =
Vin
VC
PC
TM
IL
NC
PR
PRM-AL
+In
–In
Factorized
Bus (Vf)
(
V
L
Io•Ro
+
K
K
Vo = VL ± 1.0%
+Out
+In
L
O
A
D
VTM
K
Ro
-Out
+Out
-Out
TM
VC
)
PC
-In
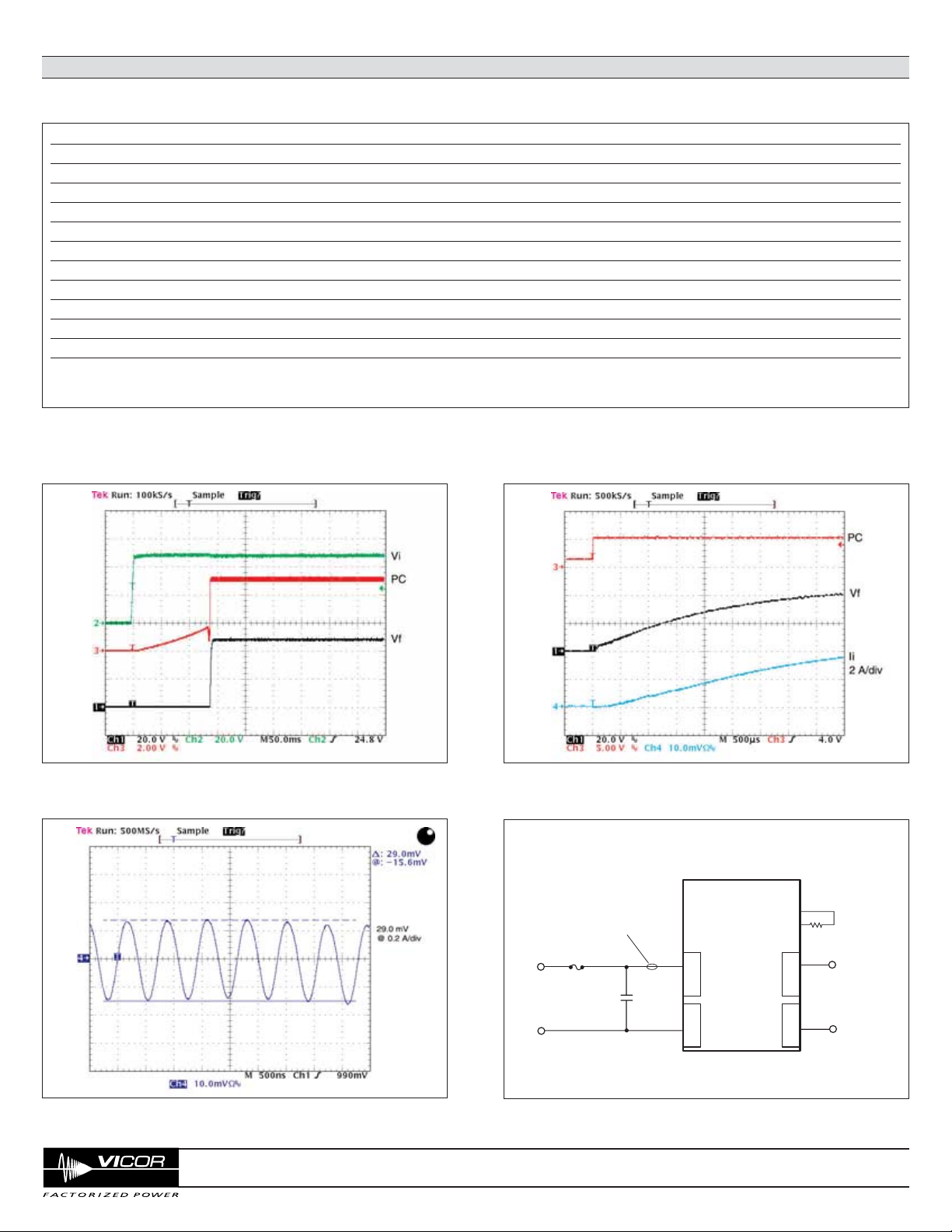
vicorpower.com 800-735-6200 V•I Chip Pre-Regulator Module P048F048T24AL Rev. 1.7
Page 3 of 14
PRELIMINARY
Parameter Min Typ Max Unit Note
Input voltage range 36 48 75 Vdc
Input dV/dt 1 V/µs
Input undervoltage turn-on 33.8 35.3 Vdc
Input undervoltage turn-off 30.5 31.8 Vdc
Input overvoltage turn-on 75.8 77.3 Vdc
Input overvoltage turn-off 78.8 81.0 Vdc
Input quiescent current 0.5 1 mA PC low
Input current 5.2 Adc
Input reflected ripple current 580 mA p-p See Figures 4 & 5
No load power dissipation 3.0 W
Internal input capacitance 5 µF Ceramic
Recommended external input capacitance 100 µF See Figure 5 for input filter circuit.
Source impedance dependent
Input Specs (Conditions are at 48 Vin, 48 Vf, full load, and 25°C ambient unless otherwise specified)
Figure 3 — Vf turn-on waveform with inrush current – PC enabled at
full load, 48 Vin
Figure 2 — Vf and PC response from power up
Figure 4 — Input reflected ripple current at full load and 48 Vin
Input Waveforms
Figure 5 — Input filter capacitor recommendation
Electrical Specifications
V•I Chip Pre-Regulator Module
+IN
–IN
Reflected
Measurement
10 A
100 μF
Al-Electrolytic
Ripple
VC
PC
TM
IL
NC
PR
PRM-AL
+In
–In
+Out
–Out
VH
SC
SG
OS
NC
CD
2.37 kΩ
+ OUT
– OUT
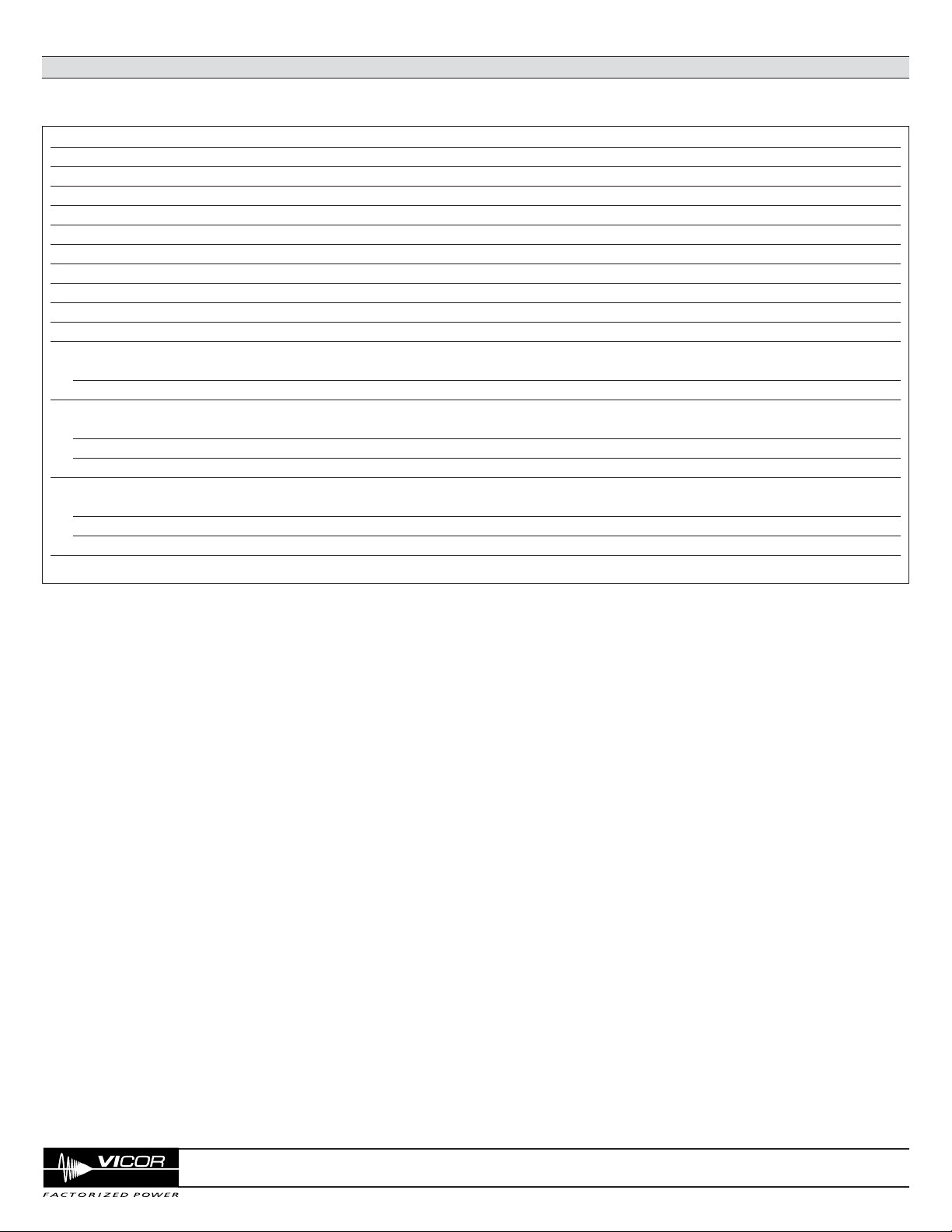
vicorpower.com 800-735-6200 V•I Chip Pre-Regulator Module P048F048T24AL Rev. 1.7
Page 4 of 14
PRELIMINARY
Parameter Min Typ Max Unit Note
Output voltage range 26 48 55 Vdc Factorized Bus voltage (Vf) set by ROS
Output power 0 240 W
Output current 0 5 Adc
DC current limit 5.25 6.0 6.6 Adc IL pin floating
Average short circuit current 0.5 A Auto recovery
Set point accuracy 1.5 %
Line regulation 0.1 0.2 % Low line to high line
Load regulation 0.1 0.2 % No CD resistor
Load regulation (at VTM output) 1.0 2.0 % Adaptive Loop
Current share accuracy 5 10 %
Efficiency
Full load 96 % See Figure 6,7 & 8
Output overvoltage set point 56 59.4 Vdc
Output ripple voltage
No external bypass 2.3 2.5 % Factorized Bus, see figure 13
With 10 µF capacitor 1.0 1.1 % Factorized Bus, see figure 14
Switching frequency 1.35 1.45 1.55 MHz Fixed frequency
Output turn-on delay
From application of power 200 300 ms See Figure 2
From PC pin high 100 µs See Figure 3
Internal output capacitance 5 µF Ceramic
Factorized Bus capacitance 47 µF
Output Specs (Conditions are at 48 Vin, 48 Vf, full load, and 25°C ambient unless otherwise specified)
Electrical Specifications
(continued) V•I Chip Pre-Regulator Module
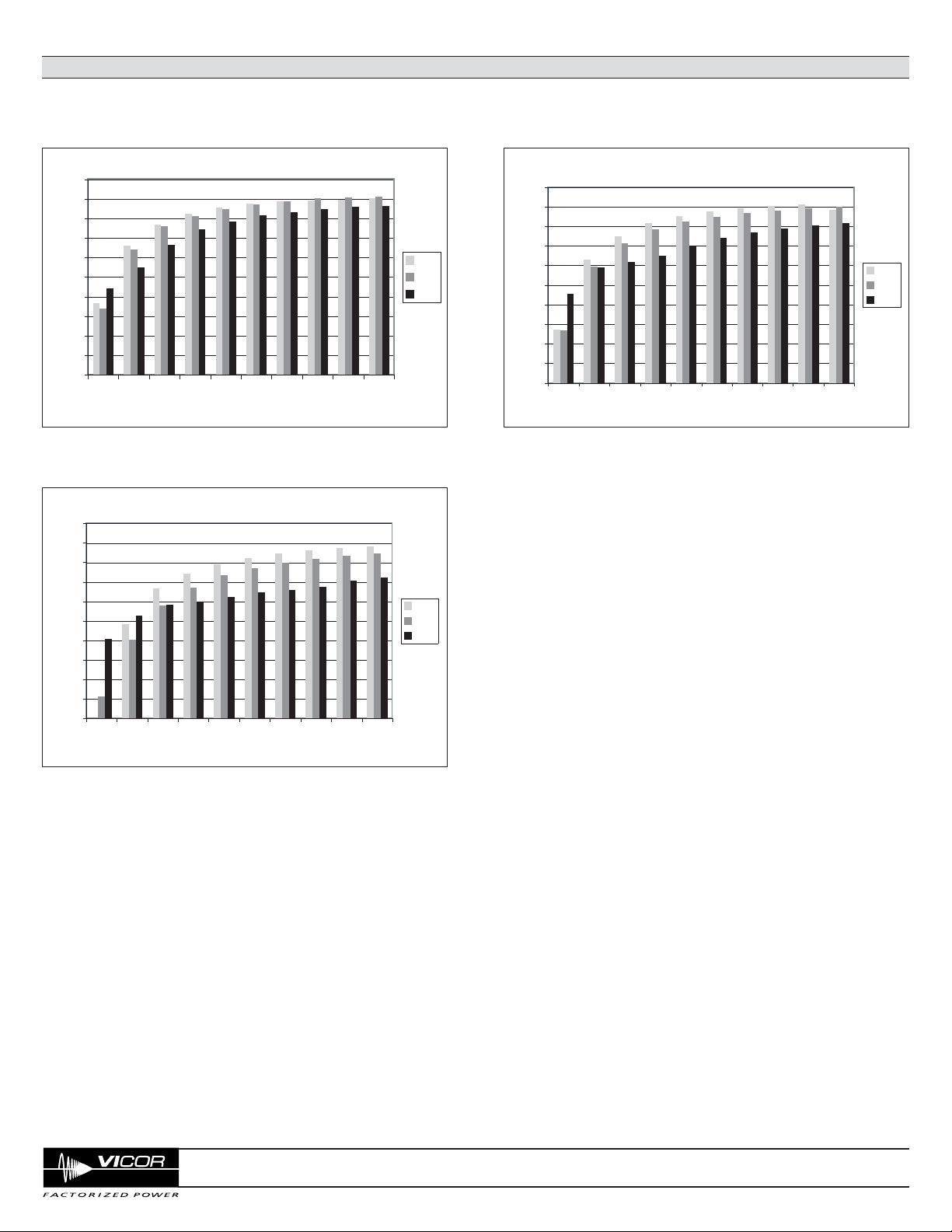
vicorpower.com 800-735-6200 V•I Chip Pre-Regulator Module P048F048T24AL Rev. 1.7
Page 5 of 14
PRELIMINARY
Electrical Specifications
(continued) V•I Chip Pre-Regulator Module
Figure 7 — Efficiency vs. output current at 36 Vf
Figure 8 — Efficiency vs. output current at 26 Vf
Efficiency Graphs
Figure 6 — Efficiency vs. output current at 48 Vf
Efficiency vs. Output Current
98
96
94
92
90
88
86
Efficiency (%)
84
82
80
78
0.5 1.1 1.5 2.0 2.5 3.0 3.5 4.0 4.6 5.0
Output Current (A)
Efficiency vs. Output Current
98
96
94
92
90
88
86
Efficiency (%)
84
82
80
78
0.5 1.0 1.6 2.0 2.5 3.0 3.5 4.0 4.6 5.0
Output Current (A)
Vin
Vin
36V
48V
75V
36V
48V
75V
Efficiency vs. Output Current
98
96
94
92
90
88
86
Efficiency (%)
84
82
80
78
0.5 1.0 1.5 2.0 2.5 3.0 3.5 4.0 4.5 5.0
Output Current (A)
Vin
36V
48V
75V