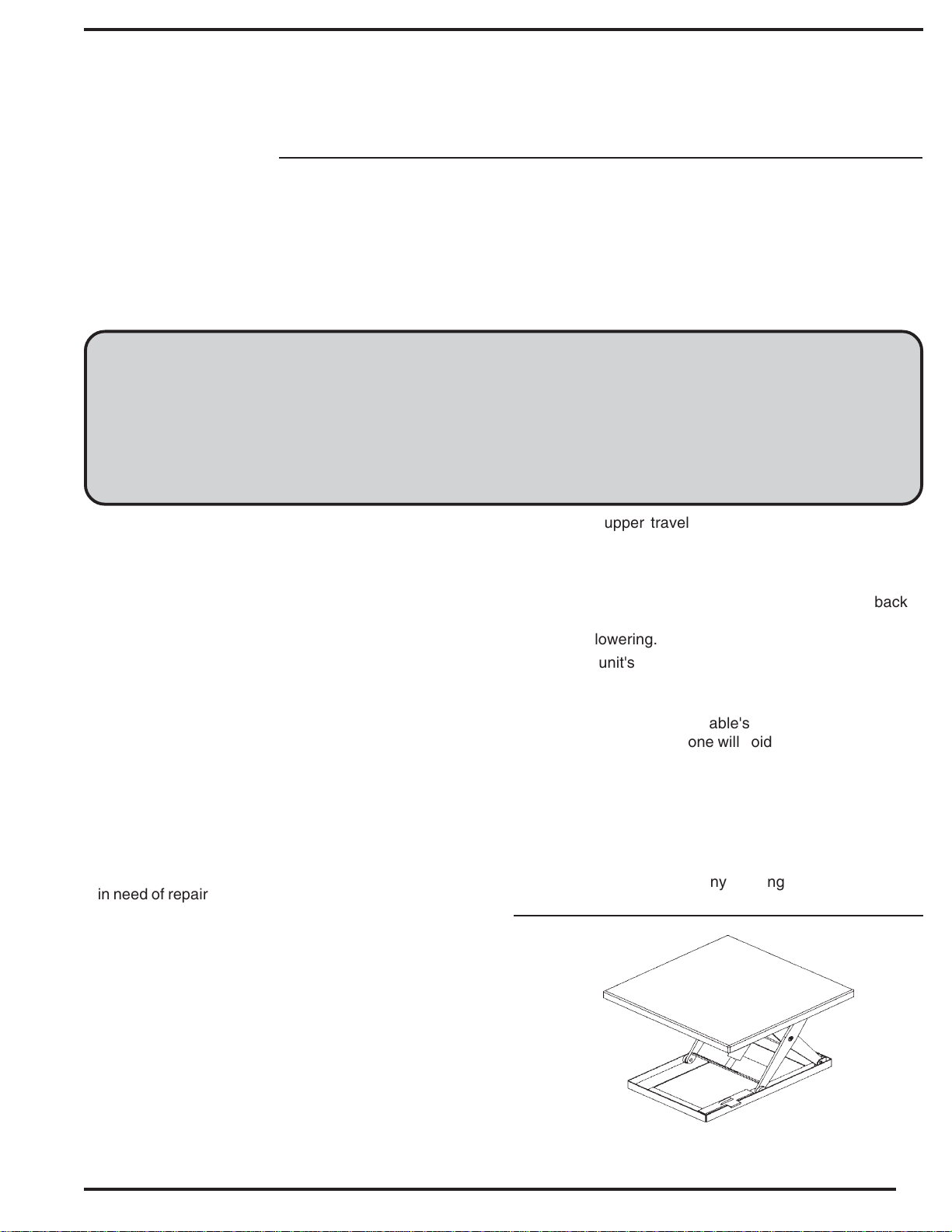
VESTIL MANUFACTURING CORP.
2999 North Wayne St., Angola, IN 46703
Ph: 260-665-9521 Fax: 260-665-1339
Website: www.vestil.com
Ergonomic Solutions
Contents
Safety Precautions .......................................... 1
Operation .................................................. 1 & 4
Installation Instructions.................................... 2
Hydaulic Circuit ............................................... 3
Loading Instructions ........................................ 4
Pneumatic/Hydraulic Diagram ......................... 5
Revised 03-00
A company dedicated to solving ergonomic and material
handling problems since 1955
.
OWNER'S
MANUAL
AIR HYDRAULIC SCISSOR TABLE
MODEL AHLT
Exploded Parts Drawing ............................... 6
Parts List....................................................... 7
Troubleshooting Guide ........................... 8 & 9
Maintenance & Safety ................................ 10
Warning Label Identification ....................... 11
Warranty ..................................................... 12
SAFETY PRECAUTIONS
Read owner's manual completely before operating unit! The
model number and capacity of the table is incribed on its
(green or red) nameplate. Please remember to include these
numbers with any correspondence with your dealer or factory.
Have only qualified personnel perform maintenance and repairs
on this unit.
• The lifting capacity of your unit is based on a uniformly
centered load. This capacity should never be exceeded,
as permanent damage and/or personnel injury could result.
Consult the factory for side or end loading capacities.
• Never lower the unit onto the safety maintenance prop
while the table is loaded. Never go under the platform
unless the maintenance prop is in position.
• Use AW-32 hydraulic oil (or equivalent), or Dexron II
transmission fluid in the tables reservoir. Do not use brake
fluids or jack oils.
• Check the setting and conditions of all safety switches and
stickers frequently.
• Never operate the table if it or any of its components are
in need of repair. Notify the appropriate personnel in the
event of any unusual noises, movements, or noticeable
damage to the table's understructure of controls, or if the
table doesn't respond normally to its controls.
upper travel upper travel setpoint, and air valve is closed
which in turn disables the pilot-operated motor air supply valve
and causes the unit to stop.
The "LOWER" control opens a hydraulic "dump"
valve to allow that same oil in the cylinder(s) to return back to
the reservoir. When the unit has completely lowered it will
simply stop lowering.
• The power unit's air motor requires a minimum air supply
of 70 CFM at 70 PSI.
• A good quality air filter/lubricator is required for proper,
long-term operation of the table's power unit. Operation
of this machine without one will void the warranty!
• Refer to the hydraulic troubleshooting guide if problems
arise with the table's operation.
• Regular inspections should be performed on all
pneumatic and hydraulic hoses, as will as a visual
inspection of all structural members, hinges and
components. Check for cracking or scraped paint, oil
leaks, noticeable wear at any pivoting points, loose or
missing fastners and components, etc.
OPERATION
The table is furnished with a remote "deadman" style
control. This type of operation, also called "push to run", allows
the operator to move the unit as much or as little as necessary.
Each press of the air control valves opens a seperate pilotoperated valve to initaiate the desired movement, and
movement is creased when the valve is released.
The "RAISE" control opens the motor air supply valve
to run the power unit and thereby pump hydraulic fluid to the
cylinder(s). When the table raises to the previously determined
AIR HYDRAULIC SCISSOR TABLE
MODEL AHLT
1
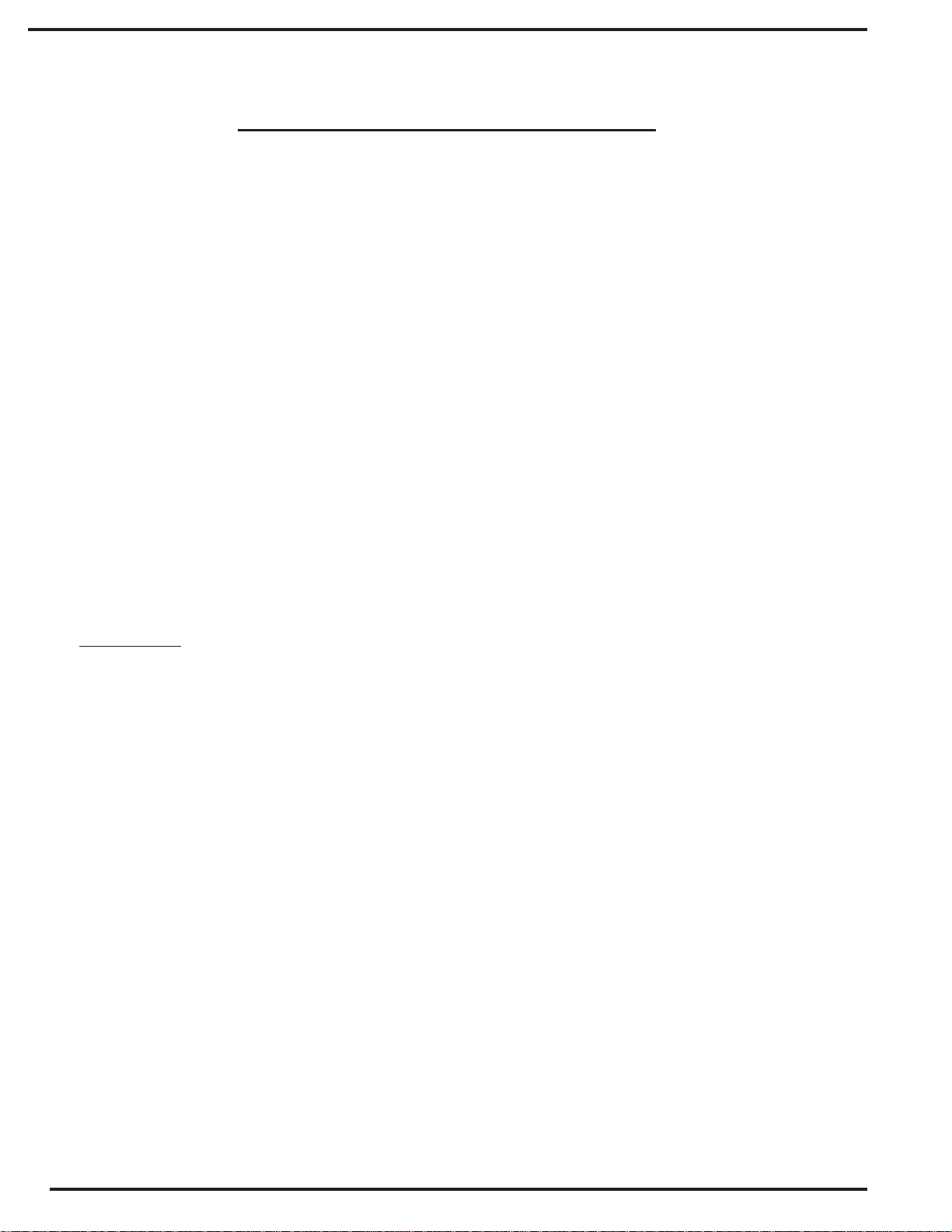
INSTALLATION INSTRUCTIONS
Review Complete Owner's Manual Before Commencing Installation.
For installation you will need the following:
1.) A fork truck or hoisting means.
2.) Lag bolts, masonry drill, masonry bit, wrench for lag bolt, grout, and steel shims.
Move the lift with straps or forks under frame.
Read all the warning labels on the lift and be sure all of the labels are on the lift.
Check local codes pertaining to your application.
If the power unit is to be mounted externally, be sure to blow out the connecting hydraulic line with
compressed air.
Be sure maintenance prop is in place before getting under platform.
After anchoring to floor, shim or grout the full length on the frame sides.
The entire length of the frame sides must be supported.
Operate lift through a few cycles. Check and add oil if necessary. See oil specification elsewhere
in this manual.
Clean up any debris or spilled oil.
2
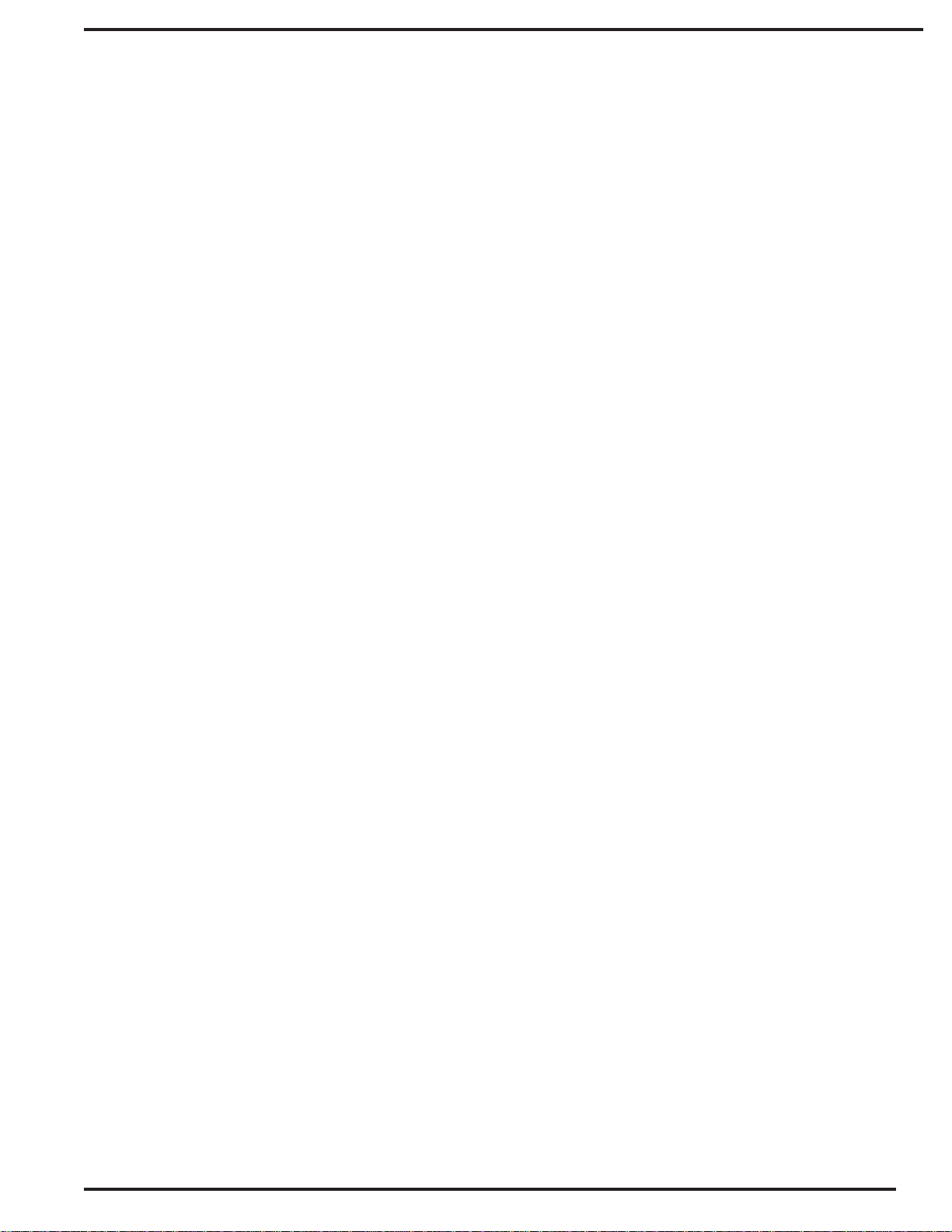
HYDRAULIC CIRCUIT
When the operator wants to raise the unit, he/she presses the "RAISE" button. This opens the
air motor supply valve which turns the hydraulic pump. Oil from the reservoir is drawn in through the
suction filter and into the pump. The pump delivers the pressurized oil through the check valve before
entering the cylinders.
The function of the check valve is to allow the oil to flow in one direction, i.e. towards the
cylinders. It also prevents the flow of oil back into the pump circuit when the pump stops running. This
holds the oil in the cylinders and maintains the desired elevation.
If the load is excessive, and the "RAISE" button is still depressed, pressure will build up in the
circuit between the pump and the cylinders. This forces the "ball" or "poppet" in the relief valve to
unseat allowing the pump out put returns into the reservoir through the return pipe.
When the operator wants to lower the unit, he presses the "LOWER" button. This opens a
hydraulic "DUMP" valve. The poppet in the solenoid valve is unseated and oil now returns from the
cylinders through the flow control valve, return filter, the solenoid valve, oil return pipe, and in the
reservoir.
The flow control valve controls the down speed of the table. It is preset and cannot be
changed.
Releasing the "LOWER" control will de-energize the solenoid, closing the valve poppet. This
prevents the oil from returning to the reservoir and the cylinders will stop retracting. The unit will
maintain that particular elevation.
Cartridge Valves
The lowering valve, as discussed above, is of cartridge construction and is virtually
maintenance free. If there is a faulty operation, check trouble shooting section. To clean the cartridge
valve, follow this procedure:
1.) Use a sharp object and push poppet in from the bottom to open the valve.
2.) Repeat several times while valve is immersed in kerosene or mineral spirits. Blow dry.
3.) Inspect "O" rings and the teflon extrusion washer.
4.) Reinstall. The valve should be tightened to approximately 30 ft. lbs.
Velocity Fuse
There is a brass velocity fuse with a stainless steel spring in the base of each cylinder. In the
event of a hydraulic pump failure, the platform starts to lower at a fast rate. As soon as the descent
speed exceeds the preset speed, the velocity fuse will shut off the oil flow and the platform will remain
stationary until pressure is reapplied. This safety feature reduces the possibility of accidental personal
injury or damage to the table or contents. To reset the velocity fuse just briefly activate pump by
depressing the "RAISE" button.
3
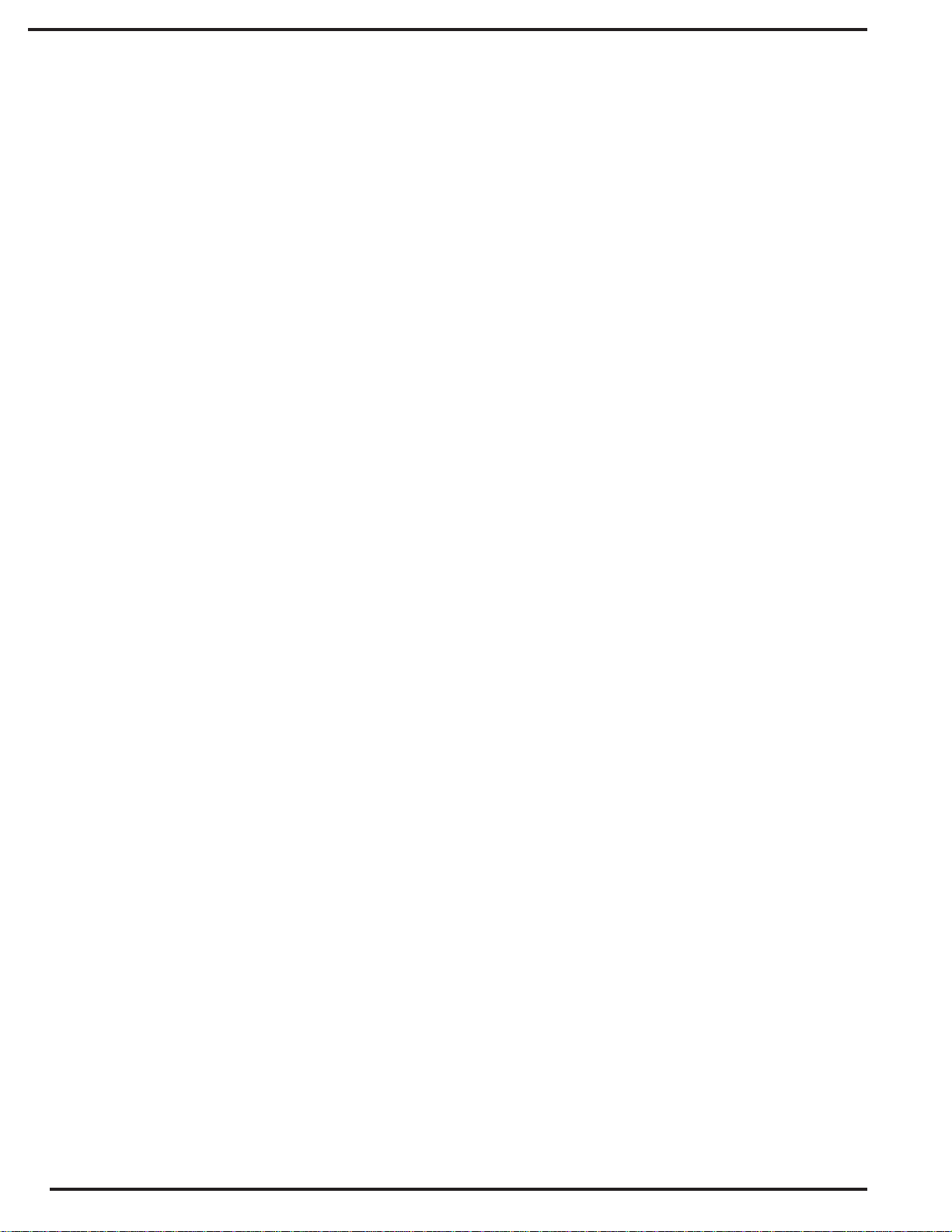
LOADING INSTRUCTIONS
The load capacity rating as inscribed on the
nameplate of your unit designates the net capacity,
assuming the load is centered. This capacity must
never be exceeded, as permanent damage or injury
may result.
SAFETY INSTRUCTIONS TO THE OPERATOR
1.) Always load the unit properly.
2.) Never use the Lift if it is in need of
repairs or in the case of malfunction.
OPERATING INSTRUCTIONS
This unit is furnished with constant pressure
("deadman" type) push button controls. Depressing
the "RAISE" control opens ths motor air supply
valve. The cylinder begins to extend and the deck
starts to raise. Stand to the side when operating.
Stay clear of moving parts. The platform will rise as
long as the "RAISE" control is pressed.
On releasing the control, the unit will cease
to rise and will remain at that particular elevation.
This is because the pushbutton valve will close
which in turn closes the pilot-operated motor air
supply valve.
On pressing the "LOWER" control, the
lowering solenoid valve is energized. The cylinders
retract as the oil returns to the reservoir and, upon
releasing the control, the unit will cease to lower,
remaining at that particular elevation. Be certain no
person or object is in the way when the unit is
descending.
3.) Notify your maintenance personnel in case
you notice anything out of the ordinary,
such as binding, odd pump noises, etc.
4.) Do not continue to depress the "UP" control
if the unit is not raising. You can
permanently damage the motor or pump
by doing so.
ORDERING REPLACEMENT OR EXTRA PARTS
Our company takes pride in using the finest
available parts for our equipment. We are not
responsible for equipment failure resulting from the
use of unapproved replacement parts. To order
replacement or extra parts for your equipment
contact Customer Service at the factory. In any
correspondence with the factory please include the
serial number which is inscribed on the nameplate
of the piece of equipment. Use only the part numbers
provided in this Owner's Manual.
In the event the unit is overloaded, it will not
raise the relief valve will open due to excessive
pressure buildup, an oil will bypass into the reservoir.
Always remember that the motor runs only when the
"RAISE" button is depressed and the lowering
solenoid valve is energized only when the "LOWER"
button is pressed.
4