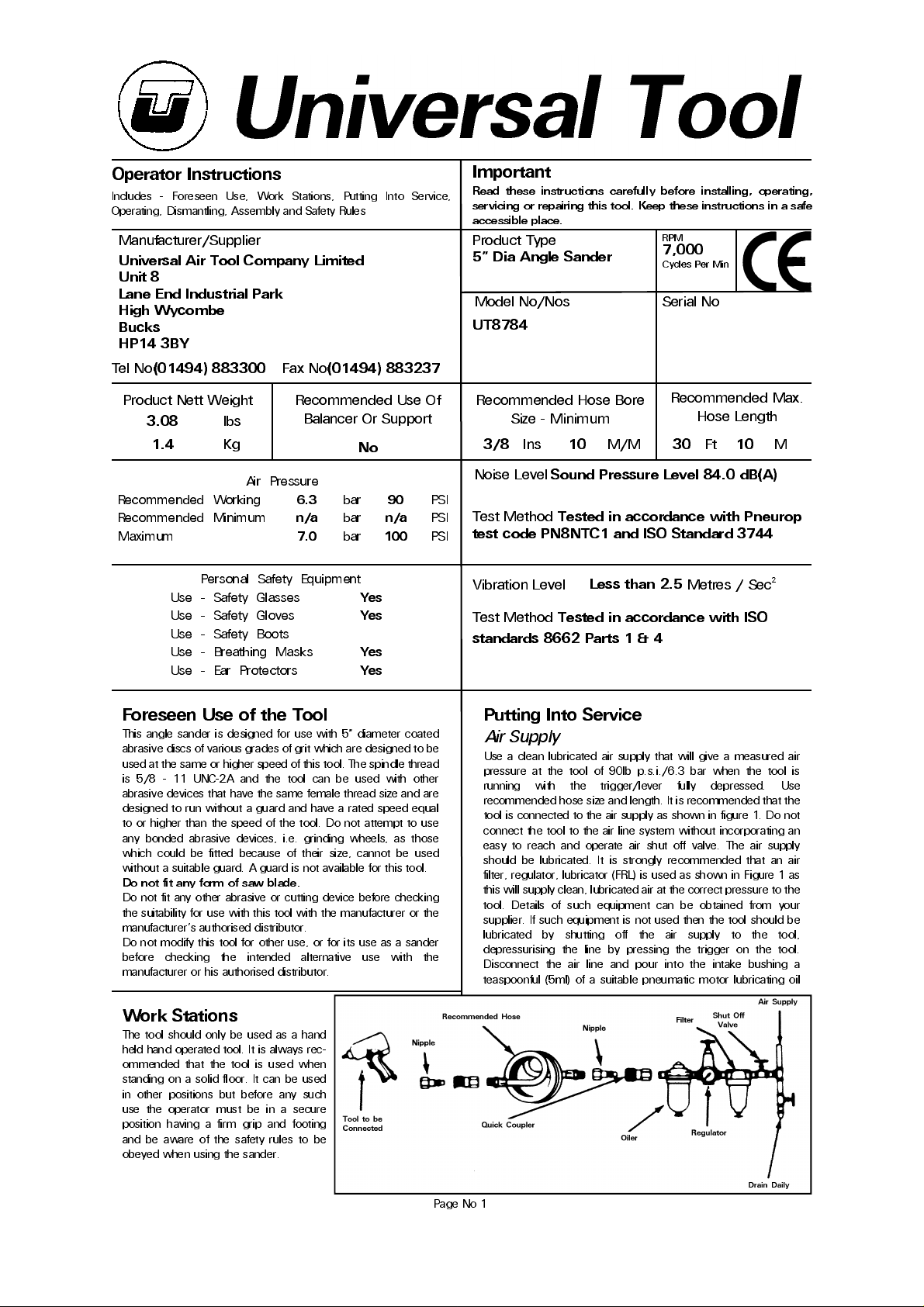
Operator Instructions
Includes - Foreseen Use, Work Stations, Putting Into Service,
Operating, Dismantling, Assembly and Safety Rules
Important
Read these instructions carefully before insta lling, operating,
servicing or repairing this tool. Keep these instructions in a safe
accessible place.
Manufacturer/Supplier Product Type
Universal Air Tool Company Limited
5" Dia Angle Sander
Unit 8
Lane End Industrial Park
High Wycombe
Bucks
Model No/Nos Serial No
UT8784
HP14 3BY
Tel No Fax No
(01494) 883300 (01494) 883237
RPM
7,000
Cycles Per Min
Product Nett Weight
3.08
1.4 3/8 10 30 10
Recommended Working
Recommended Minimum
Maximum
Use - Safety Glasses
Use - Safety Gloves
Use - Safety Boots
Use - Breathing Masks
Use - Ear Protectors
lbs
Kg
Air Pressure
Perso n a l Sa fe t y E q ui pm en t
Foreseen Use of the Tool
This angle sander is designed for use with 5" diameter coated
abrasive discs of various grades of grit which are designed to be
used at the same or higher speed of this tool. The spindle thread
is 5/8 - 11 UNC-2A and the tool can be used with other
abrasive devices that have the same female thread size and are
designed to run without a guard and have a rated speed equal
to or higher than the speed of the tool. Do not attempt to use
any bonded a brasive devices , i.e. grinding wheels, as those
which could be fitted becau se of their size, cannot be us ed
without a suitable guard. A guard is not available for this tool.
Do not fit any form of saw blade.
Do not fit any other abrasive or cutting device before checking
the suitability for use with this tool with the manufacturer or the
manufacturer's authorised distributor.
Do not modify this tool for other use, or for its use as a sander
before checking the intended alternative use with the
manufacturer or his authorised distributor.
Recommended Use Of
Balancer Or Support
No
6.3
bar
90
PSI
n/a
7.0
bar
bar
Yes
Yes
Yes
Yes
n/a
100
PSI
PSI
Recommended Hose Bore
Size - Minimum
Ins M/M Ft M
Noise Level
Test Method
Sound Pressure Level 84.0 dB(A)
Tested in accordance with Pneurop
test code PN8NTC1 and ISO Standard 3744
Vibration Level
Test Method
Less than 2.5
Tested in accordance with ISO
standards 8662 Parts 1 & 4
Putting Into Service
Air Supply
Use a clean lubricated air supply that will give a measured air
pressu re at the tool of 90lb p.s.i./6.3 bar when the tool is
running with the trigger/lever fully depressed. Use
recommended hose size and length. It is recommended that the
tool is connected to the air supply as shown in figure 1. Do not
connect the tool to the air line system without incorporating an
easy to reach and opera te air shut off va lve. The air s upply
should be lubricated. It is strongly recommended that an air
filter, regulator, lubricator (FRL) is used as shown in Figure 1 as
this will supply clean, lubricated air at the correct pressure to the
tool. Details of such equ ipment can be obtaine d from your
supplier. If such equipment is not used then the tool should be
lubricated by shutting off the air supply to the tool,
depressu rising the line by pressing th e trigger on the tool.
Disconne c t th e a ir line an d pour into the in ta ke bu sh ing a
teaspoonful (5ml) of a suitable pneumatic motor lubricating oil
Recommended Max.
Hose Length
Metres / Sec²
Work Stations
The tool should only be used as a hand
held hand operated tool. It is always rec-
ommende d that the tool is used when
standing on a solid floor. It can be used
in other positions but before an y such
use th e operator must be in a secu re
position havin g a firm grip and footing
and be aware of the safety rules to be
obeyed when using the sander.
Page No 1
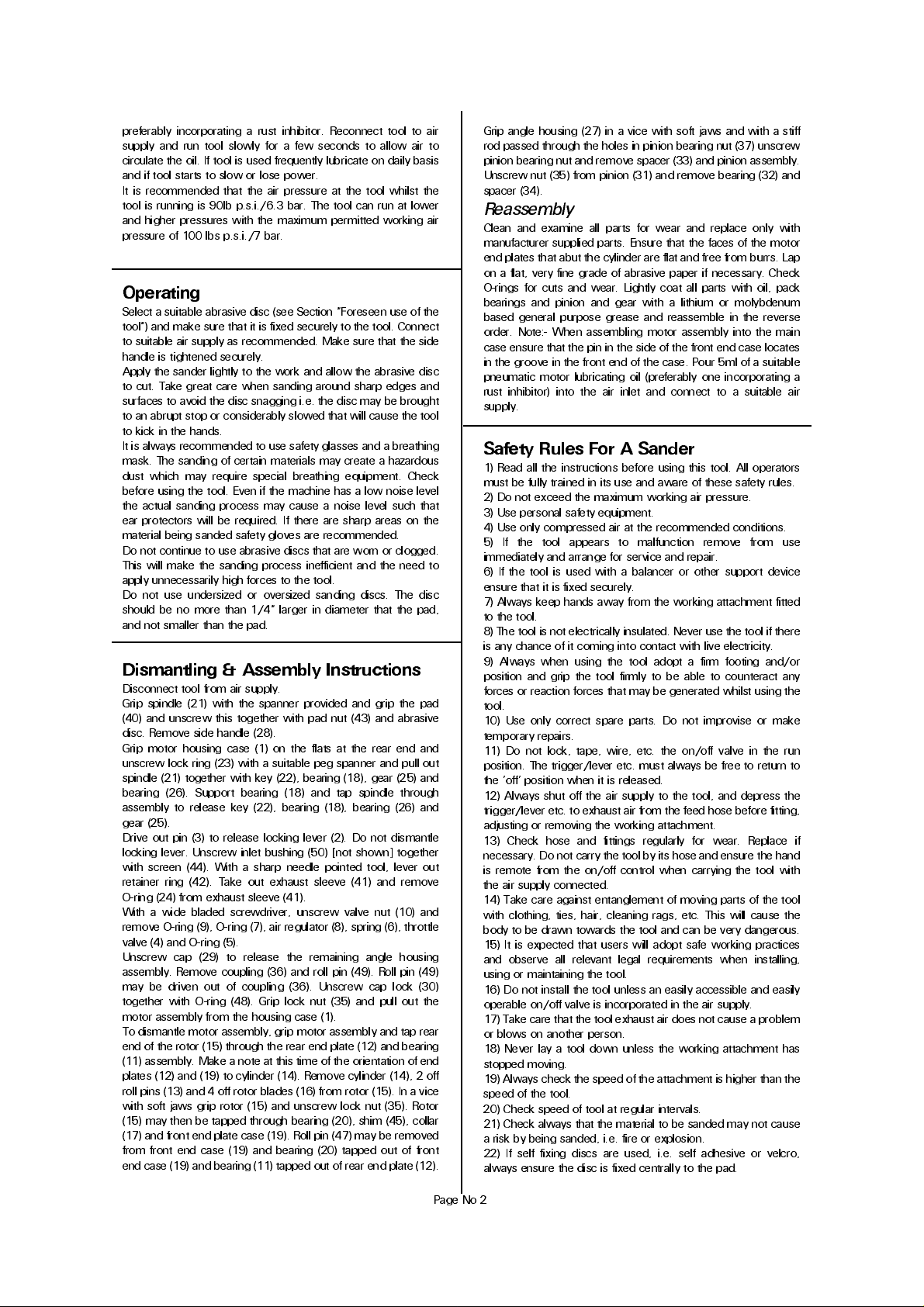
preferably incorporating a rust inhibitor. Reconnect tool to air
supply an d run tool slowly for a fe w seconds to allow a ir to
circulate the oil. If tool is used frequently lubricate on daily basis
and if tool starts to slow or lose power.
It is recommended that the air pressure at the tool whilst the
tool is running is 90lb p.s.i./6.3 bar. The tool can run at lower
and higher pressures with the maximum permitted working air
pressure of 100 lbs p.s.i./7 bar.
Operating
Select a suitable abrasive disc (see Section "Foreseen use of the
tool") and make sure that it is fixed securely to the tool. Connect
to suitable air supply as recomm ended. Make sure that the side
handle is tightened securely.
Apply the sander lightly to the work and allow the abrasive disc
to cut. Take great care when sanding around sharp edges and
surfaces to avoid the disc snagging i.e. the disc may be brought
to an abrupt stop or considerably slowed that will cause the tool
to kick in the hands.
It is always recommended to use safety glasses and a breathing
mask. The sanding of certain materials may create a hazardous
dust wh ich may require s pecial brea thing equipmen t. Check
before using the tool. Even if the machine has a low noise level
the actual sanding process may cause a noise level such that
ear protectors will be required. If there are sharp areas on the
material being sanded safety gloves are recommended.
Do not continue to use abrasive discs that are worn or clogged.
This will make the sanding process inefficient and the need to
apply unnecessarily high forces to the tool.
Do not use undersized or overs ized sanding discs. T he disc
should be no more than 1/4" larger in diameter that the pad,
and not smaller than the pad.
Dismantling & Assembly Instructions
Disconnect tool from air supply.
Grip spindle (21) with the spanner provided and grip the pad
(40) and unscrew this together with pad nut (43) and abrasive
disc. Remove side handle (28).
Grip motor housing case (1) on the flats at the rear end and
unscrew lock ring (23) with a suitable peg spanner and pull out
spindle (21) together with key (22), bearing (18), gear (25) and
bearing (26). Su pport bea ring (18) an d ta p s pindle thr ough
assembly to release key (22), bearing (18), bearing (26) and
gear (25).
Drive out pin (3) to release locking lever (2). Do not dismantle
locking lever. Unscrew inlet bushing (50) [not shown] together
with screen (44). With a sharp needle pointed tool, lever out
retainer ring (42). Take out exhaust sleeve (41) and remove
O-ring (24) from exhaust sleeve (41).
With a wide bladed screwdriver, unscrew valve nut (10) and
remove O-ring (9), O-ring (7), air regulator (8), spring (6), throttle
valve (4) and O-ring (5).
Unscrew cap (29) to release the remaining angle housing
assembly. Remove coupling (36) and roll pin (49). Roll pin (49)
may be driven ou t of coupling (36). Uns crew c ap lock (30)
together with O-ring (48). Grip lock nut (35) and pull out the
motor assembly from the housing case (1).
To dismantle motor assembly, grip motor assembly and tap rear
end of the rotor (15) through the rear end plate (12) and bearing
(11) assembly. Make a note at this time of the orientation of end
plates (12) and (19) to cylinder (14). Remove cylinder (14), 2 off
roll pins (13) and 4 off rotor blades (16) from rotor (15). In a vice
with soft jaws grip rotor (15) and unscrew lock nut (35). Rotor
(15) may then be tapped through bearing (20), shim (45), collar
(17) and front end plate case (19). Roll pin (47) may be removed
from front end case (19) and bearing (20) tapped out of front
end case (19) and bearing (11) tapped out of rear end plate (12).
Grip angle housing (27) in a vice with soft jaws and with a stiff
rod passed through the holes in pinion bearing nut (37) unscrew
pinion bearing nut and remove spacer (33) and pinion assembly.
Unscrew nut (35) from pinion (31) and remove bearing (32) and
spacer (34).
Reassembly
Clean and examine all parts for wear and replace only with
manufacturer supplied parts. Ensure that the faces of the motor
end plates that abut the cylinder are flat and free from burrs. Lap
on a flat, very fine grade of abrasive paper if necessary. Check
O-rings for cuts and wear. Lightly coat all parts with oil, pack
bearings an d pinion and gear with a lithium or molybdenu m
based general purpose grease and reassemble in the reverse
order. Note:- When assembling motor assembly into the main
case ensure that the pin in the side of the front end case locates
in the groove in the front end of the case. Pour 5ml of a suitable
pneumatic motor lubricating oil (preferably one incorporating a
rust inhibitor) into the air inlet and connect to a suitable air
supply.
Safety Rules For A Sander
1) Read all the instructions before using this tool. All operators
must be fully trained in its use and aware of these safety rules.
2) Do not exceed the maximum working air pressure.
3) Use personal safety equipment.
4) Use only compressed air at the recommended conditions.
5) I f the too l appea rs to mal functio n remove f rom use
immediately and arrange for service and repair.
6) If the tool is used with a balancer or other support device
ensure that it is fixed securely.
7) Always keep hands away from the working attachment fitted
to the tool.
8) The tool is not electrically insulated. Never use the tool if there
is any chance of it coming into contact with live electricity.
9) Always when u sing the tool a dopt a firm footing and/or
position and grip the tool firmly to be able to counteract any
forces or reaction forces that may be generated whilst using the
tool.
10) Use only correct spare parts . Do not improvise or make
temporary repairs.
11) Do not lock, tape, w ire, etc. the on/off va lve in the run
position. The trigger/lever etc. must always be free to return to
the 'off' position when it is released.
12) Always shut off the air supply to the tool, and depress the
trigger/lever etc. to exhaust air from the feed hose before fitting,
adjusting or removing the working attachment.
13) Check hose and fittings regularly for wear. Replace if
necessary. Do not carry the tool by its hose and ensure the hand
is remote from the on/off control when carrying the tool with
the air supply connected.
14) Take care against entanglement of moving parts of the tool
with clothing, ties, hair, cleaning rags, etc. This will cause the
body to be drawn towards the tool and can be very dangerous.
15) It is expected that users will adopt safe working practices
and observ e all r ele va nt lega l requ irem ents wh e n in st alling,
using or maintaining the tool.
16) Do not install the tool unless an easily accessible and easily
operable on/off valve is incorporated in the air supply.
17) Take care that the tool exhaust air does not cause a problem
or blows on another person.
18) Never lay a tool down unless the working attachment has
stopped moving.
19) Always check the speed of the attachment is higher than the
speed of the tool.
20) Check speed of tool at regular intervals.
21) Check always that the material to be sanded may not cause
a risk by being sanded, i.e. fire or explosion.
22) If self fixing discs are used, i.e. self adhesive or velcro,
always ensure the disc is fixed centrally to the pad.
Page No 2

UT8784 5" Dia Angle Sand er
Ref No Part No Descripti on
1 731752 Case
2 900382 Locking Lever
3 731754 Pin
4 731755 Throttle Valve
5 1012370 O Ring
6 729258 Spring
7 729088 O Ring
8 729282 Air Regulatopr
9 729073 O Ring
10 729262 Valve Nut
11 731756 Ball Bearing
12 731757 Rear End Plate
13 731758 Roll Pin (2)
14 731759 Cylinder
15 731760 Rotor
16 731761 Rotor Blade (4)
17 731762 Collar
18 731763 Ball Bearing
19 731764 Front Case
20 731782 Ball Bearing
21 731765 Spindle
22 731766 Key
23 731767 Lock Ring
23 732420 O Ring
23 731769 Gear
Dec 2004 Ver 1.11
Ref No Part No Description
26 731770 Bearing
27 731772 Angle Housing
28 731773 Handle
29 731774 Cap
30 731775 Cap Lock
31 731776 Pinion
32 731777 Ball Bearing (2)
33 731779 Spacer
34 731778 Spacer
35 731781 Lock Nut (2)
36 731771 Coupling
37 731780 Pinion Bearing Nut
39 731788 Spanner Wrench
40 731783 5" Pad
41 731786 Exhaust Sleeve
42 731787 Retainer Ring
43 731784 Pad Nut
44 731785 Screen
45 731768 Shim
47 731758 Roll Pin
48 732238 O Ring
49 729296 Roll Pin
50 730120 Inlet Bushing
Page No 3

Declaration of Conformity
Universal Air Tool Company Limited
Unit 8, Lane End Industrial Park, High Wycombe, Bucks, HP14 3BY, England
declare under our sole responsibility that the product
Model UT8784 5” Dia Angle Sander, Serial Number
to which this declaration relates is in conformity with the following standard(s) or other normative document(s)
EN792 (Draft), EN292 Parts 1 & 2, ISO 8662 Parts 1 & 4, Pneurop PN8NTC1
following the provisions of
89/392/EEC as amended by 91/368/EEC & 93/44/EEC Directives
Lane End D.H.Moppett (Man. Director)
Place an d date of issue Name and signature or equivalent marking of authorised person
Accessories
Notes
Distributor
This document may not be copied wholly or in part by anyone without the consent of the Directors of Universal Air Tool Company Limited
Designed & Written in the U.K.
©Copyright of Universal Air Tool Company Limited, established in the United Kingdom, 1994
Page No 4