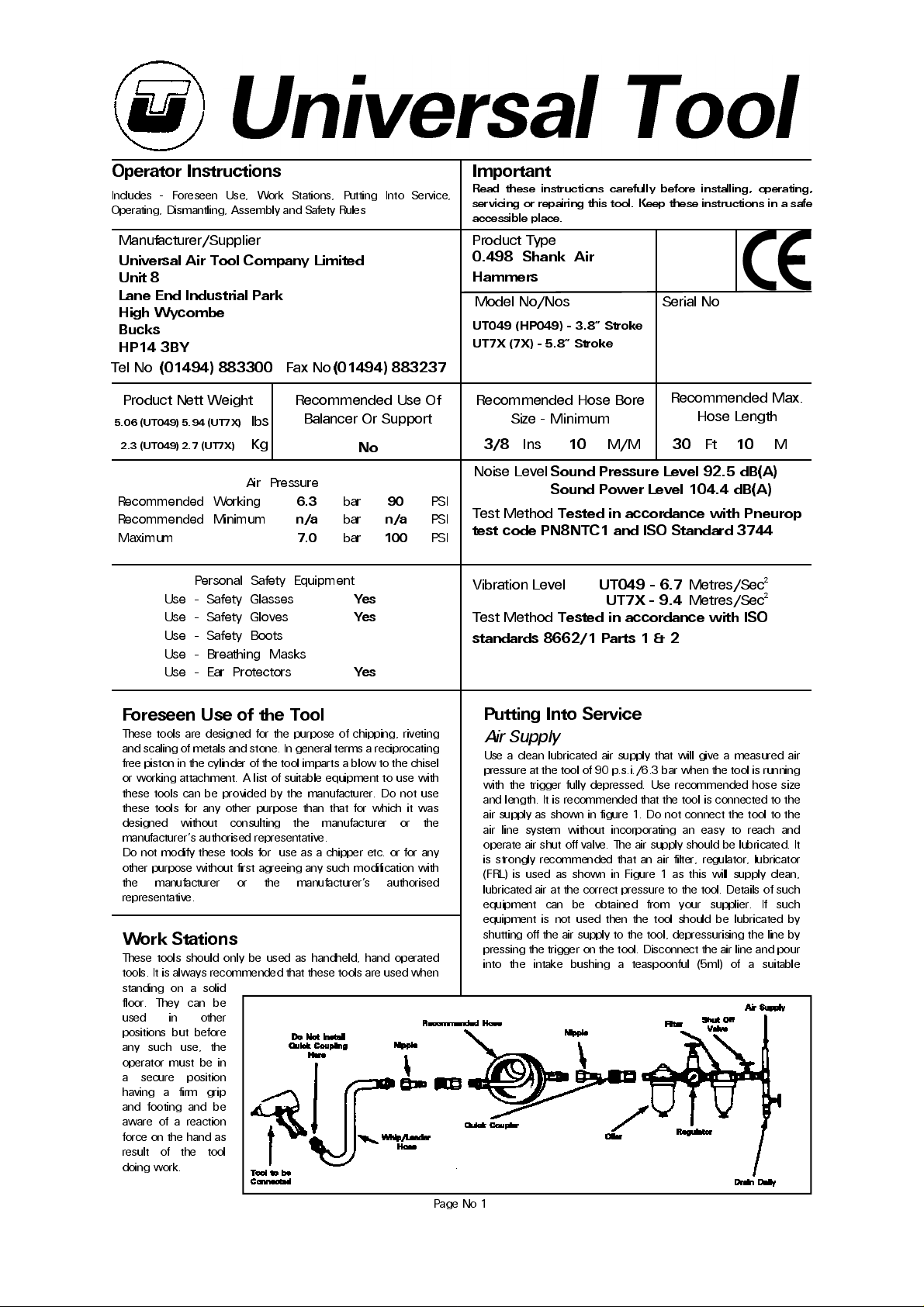
Operator Instructions Important
Includes - Foreseen Use, Work Stations, Putting Into Service,
Operating, Dismantling, Assembly and Safety Rules
Manufacturer/Supplier Product Type
Universal Air Tool Company Limited
Unit 8
Lane End Industrial Park
High Wycombe
Bucks
HP14 3BY
Tel No Fax No
(01494) 883300 (01494) 883237
Read these instructions carefully before insta lling, operating,
servicing or repairing this tool. Keep these instructions in a safe
accessible place.
0.498 Shank Air
Hammers
Model No/Nos Serial No
UT049 (HP049) - 3.8” Stroke
UT7X (7X) - 5.8” Stroke
Product Nett Weight
5.06 (UT049) 5.94 (UT7X)
2.3 (UT049) 2.7 (UT7X)
Recommended Use Of
lbs
Balancer Or Support
Kg
No
Air Pressure
Recommended Working
Recommended Minimum
Maximum
6.3
n/a
7.0
bar
bar
bar
90
n/a
100
Personal Safety Equipment
Use - Safety Glasses
Use - Safety Gloves
Yes
Yes
Use - Safety Boots
Use - Breathing Masks
Use - Ear Protectors
Yes
Foreseen Use of the Tool
These tools are designed for the purpose of chipping, riveting
and scaling of metals and stone. In general terms a reciprocating
free piston in the cylinder of the tool imparts a blow to the chisel
or working attachment. A list of suitable equipment to use with
these tools can be provided by the manufacturer. Do not use
these tools for any other purpose th an that for which it was
designed without consulting the manufacturer or the
manufacturer’s authorised representative.
Do not modify these tools for use as a chipper etc. or for any
other purpose without first agreeing any such modification with
the manufacturer or the manufacturer’s authorised
representative.
Work Stations
These tools should only be used as handheld, hand operated
tools. It is always recommended that these tools are used when
standing on a solid
flo or . T hey c an b e
used in other
positions but before
any such u se, the
operator mu st be in
a secure position
having a firm gri p
and footing a nd be
aware of a reaction
force on the hand as
result of the tool
doing work.
Recommended Hose Bore
Size - Minimum
3/8 10 30 10
Ins M/M Ft M
Noise Level
PSI
Test Method
PSI
est code PN8NTC1 and ISO Standard 3744
PSI
Vibration Level
Sound Pressure Level 92.5 dB(A)
Sound Power Level 104.4 dB(A)
Tested in accordance with Pneurop
UT049 - 6.7
UT7X - 9.4
Test Method
ested in accordance with ISO
standards 8662/1 Parts 1 & 2
Putting Into Service
Air Supply
Use a clean lubricated air supply that will give a measured air
pressure at the tool of 90 p.s.i./6.3 bar when the tool is running
with the trigger fully depressed. Use recommended hose size
and length. It is recommended that the tool is connected to the
air supply as shown in figure 1. Do not connect the tool to the
air line sys tem withou t incorporating an easy to reach a nd
operate air shut off valve. The air supply should be lubricated. It
is strongly recommended that an air filter, regulator, lubricator
(FRL) is used as shown in Figure 1 as this will supply clean ,
lubricated air at the correct pressure to the tool. Details of such
equipment can be obtained from your supplier. If such
equipment is not used then the tool should be lubricated by
shutting off the air supply to the tool, depressurising the line by
pressing the trigger on the tool. Disconnect the air line and pour
into the intake bushing a teaspoonful (5ml) of a suitable
Recommended Max.
Hose Length
Metres/Sec²
Metres/Sec²
Page No 1
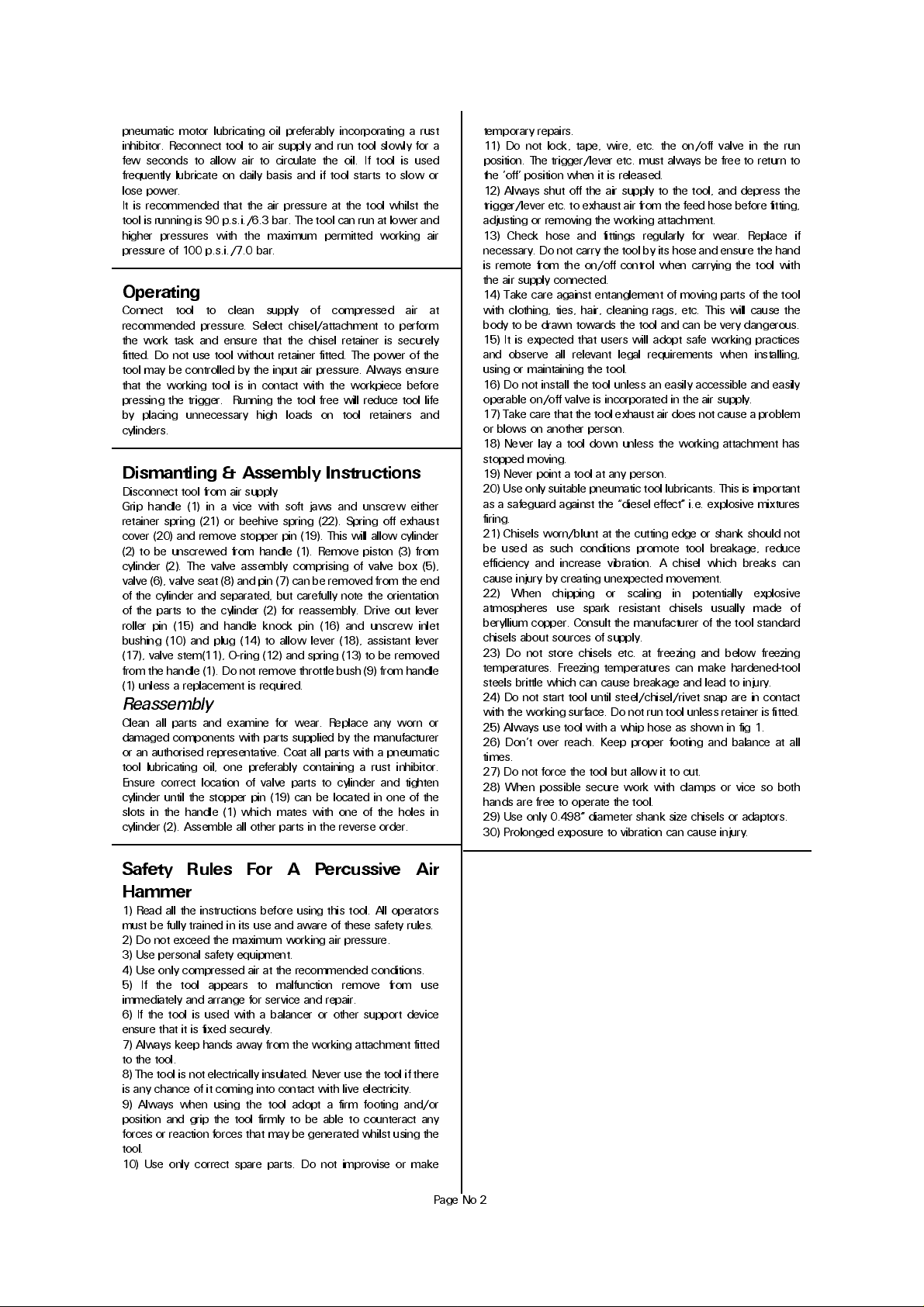
pneumatic motor lubricating oil preferably incorporating a rust
inhibitor. Reconnect tool to air supply and run tool slowly for a
few sec onds to allow air to circulate the oil. If tool is used
frequently lubricate on daily basis and if tool starts to slow or
lose power.
It is recommended that the air pressure at the tool whilst the
tool is running is 90 p.s.i./6.3 bar. The tool can run at lower and
higher pressures with the maximum permitted working air
pressure of 100 p.s.i./7.0 bar.
Operating
Connect tool to clean supply of compressed air at
recommended pressure. Select chisel/attachment to perform
the work task and ensure that the chisel retainer is securely
fitted. Do not use tool without retainer fitted. The power of the
tool may be controlled by the input air pressure. Alwa ys ensure
that the working tool is in contact with the workpiece before
pressing the trigger. Running the tool free will reduce tool life
by p laci ng unn ecessar y hi gh l oads on t ool ret ainer s and
cylinders.
Dismantling & Assembly Instructions
Disconnect tool from air supply
Grip handle (1) in a vice with soft jaws and unscrew either
retainer spring (21) or beehive spring (22). Spring off exhaust
cover (20) and remove stopper pin (19). This will allow cylinder
(2) to be unscrewed from handle (1). Remove piston (3) from
cylinder (2). The valve asse mbly comprising of valve box (5),
valve (6), valve seat (8) and pin (7) can be removed from the end
of the cylinder and separated, but carefully note the orientation
of the parts to the cylinder (2) for reassembly. Drive out lever
roller pin (15) and handle knock pin (16) and unscrew inlet
bushing (10) and plug (14) to allow lever (18), assistant lever
(17), valve stem(11), O-ring (12) and spring (13) to be removed
from the handle (1). Do not remove throttle bush (9) from handle
(1) unless a replacement is required.
Reassembly
Clean all parts and examine for wear. Replace any worn or
damaged components with parts supplied by the manufacturer
or an authorised representative. Coat all parts with a pneumatic
tool lubricating oil, one preferably containing a rust inhibitor.
Ensu re correct loc ation of valve parts to cylinder and tighten
cylinder until the stopper pin (19) can be located in one of the
slots in the handle (1) which mates with one of the holes in
cylinder (2). Assemble all other parts in the reverse order.
temporary repairs.
11) Do not lock, tape, w ire, etc. the on/off va lve in the run
position. The trigger/lever etc. must always be free to return to
the 'off' position when it is released.
12) Always shut off the air supply to the tool, and depress the
trigger/lever etc. to exhaust air from the feed hose before fitting,
adjusting or removing the working attachment.
13) Check hose and fittings regularly for wear. Replace if
necessary. Do not carry the tool by its hose and ensure the hand
is remote from the on/off control when carrying the tool with
the air supply connected.
14) Take care against entanglement of moving parts of the tool
with clothing, ties, hair, cleaning rags, etc. This will cause the
body to be drawn towards the tool and can be very dangerous.
15) It is expected that users will adopt safe working practices
and observ e all r ele va nt lega l requ irem ents wh e n in st alling,
using or maintaining the tool.
16) Do not install the tool unless an easily accessible and easily
operable on/off valve is incorporated in the air supply.
17) Take care that the tool exhaust air does not cause a problem
or blows on another person.
18) Never lay a tool down unless the working attachment has
stopped moving.
19) Never point a tool at any person.
20) Use only suitable pneumatic tool lubricants. This is important
as a safeguard against the “diesel effect” i.e. explosive mixtures
firing.
21) Chisels worn/blunt at the cutting edge or shank should not
be used a s such c onditions promote tool breakage , reduce
efficiency and increase vibration. A chisel which breaks can
cause injury by creating unexpected movement.
22) When chipping or scaling in potentially explosive
atmo spheres use spar k resist ant chi sels usua lly mad e of
beryllium copper. Consult the manufacturer of the tool standard
chisels about sources of supply.
23) Do not store chisels etc. at freezing and below freezing
temperatures. Freezing temperatures can make hardened-tool
steels brittle which can cause breakage and lead to injury.
24) Do not start tool until steel/chisel/rivet snap are in contact
with the working surface. Do not run tool unless retainer is fitted.
25) Always use tool with a whip hose as shown in fig 1.
26) Don’t over reach. Keep proper footing and balance at all
times.
27) Do not force the tool but allow it to cut.
28) When possible secure work with clamps or vice so both
hands are free to operate the tool.
29) Use only 0.498” diameter shank size chisels or adaptors.
30) Prolonged exposure to vibration can cause injury.
Safety Rules For A Percussive Air
Hammer
1) Read all the instructions before using this tool. All operators
must be fully trained in its use and aware of these safety rules.
2) Do not exceed the maximum working air pressure.
3) Use personal safety equipment.
4) Use only compressed air at the recommended conditions.
5) I f the too l appea rs to mal functio n remove f rom use
immediately and arrange for service and repair.
6) If the tool is used with a balancer or other support device
ensure that it is fixed securely.
7) Always keep hands away from the working attachment fitted
to the tool.
8) The tool is not electrically insulated. Never use the tool if there
is any chance of it coming into contact with live electricity.
9) Always when u sing the tool a dopt a firm footing and/or
position and grip the tool firmly to be able to counteract any
forces or reaction forces that may be generated whilst using the
tool.
10) Use only correct spare parts . Do not improvise or make
Page No 2

UT049 & UT7X (HP049 & 7X) 0.498” Diameter Shank Air Hammers
Ref No Part No Description
1 853001 Handle
2
3 853003 Piston
4 853004 Bush
5 85300 5 V al ve B ox
6 853006 Valve
7 853007 Pin
8 85300 8 V al ve Se al
9 853009 Throttle Bush
10 853010 Inlet Bushing
11 853011 Valve Stem
12 853012 O-Ring
13 853013 Spring
14 853014 Plug
15 853015 Lever Roller Pin
16 853016 Handle Knock Pin
17 853017 Assistant Lever
18 853018 Lever
19 853019 Stopper Pin
20 853020 Exhaust Cover
21 853021 Reatiner Spring
22 853022 Bee Hive Spring
853002 Cylinder (3.8" Stroke)
853002A Cylinder (5.8" Stroke)
Rivet capacity (steel) - UT049 (1/4-6mm) UT7X (5/16 - 8mm)
Jun 2005 Ver 1.5
Page No 3

Declaration of Conformity
Universal Air Tool Company Limited
Unit 8, Lane End Industrial Park, High Wycombe, Bucks, HP14 3BY, England
declare under our sole responsibility that the product
Model UT049 & UT7X Air Hammers, Serial Number
to which this declaration relates is in conformity with the following standard(s) or other normative document(s)
EN792 (Draft), EN292 Parts 1 & 2, ISO 8662 Parts 1 & 2, Pneurop PN8NTC1
following the provisions of
89/392/EEC as amended by 91/368/EEC & 93/44/EEC Directives
Lane End D.H.Moppett (Man. Director)
Place and date of issue Name and signature or equivalent marking of authorised person
Accessories
Notes
Distributor
This document may not be copied wholly or in part by anyone without the consent of the Directors of Universal Air Tool Company Limited
Designed & Written in the U.K.
©Copyright of Universal Air Tool Company Limited, established in the Un ited Kingdom, 1994
Page No 4