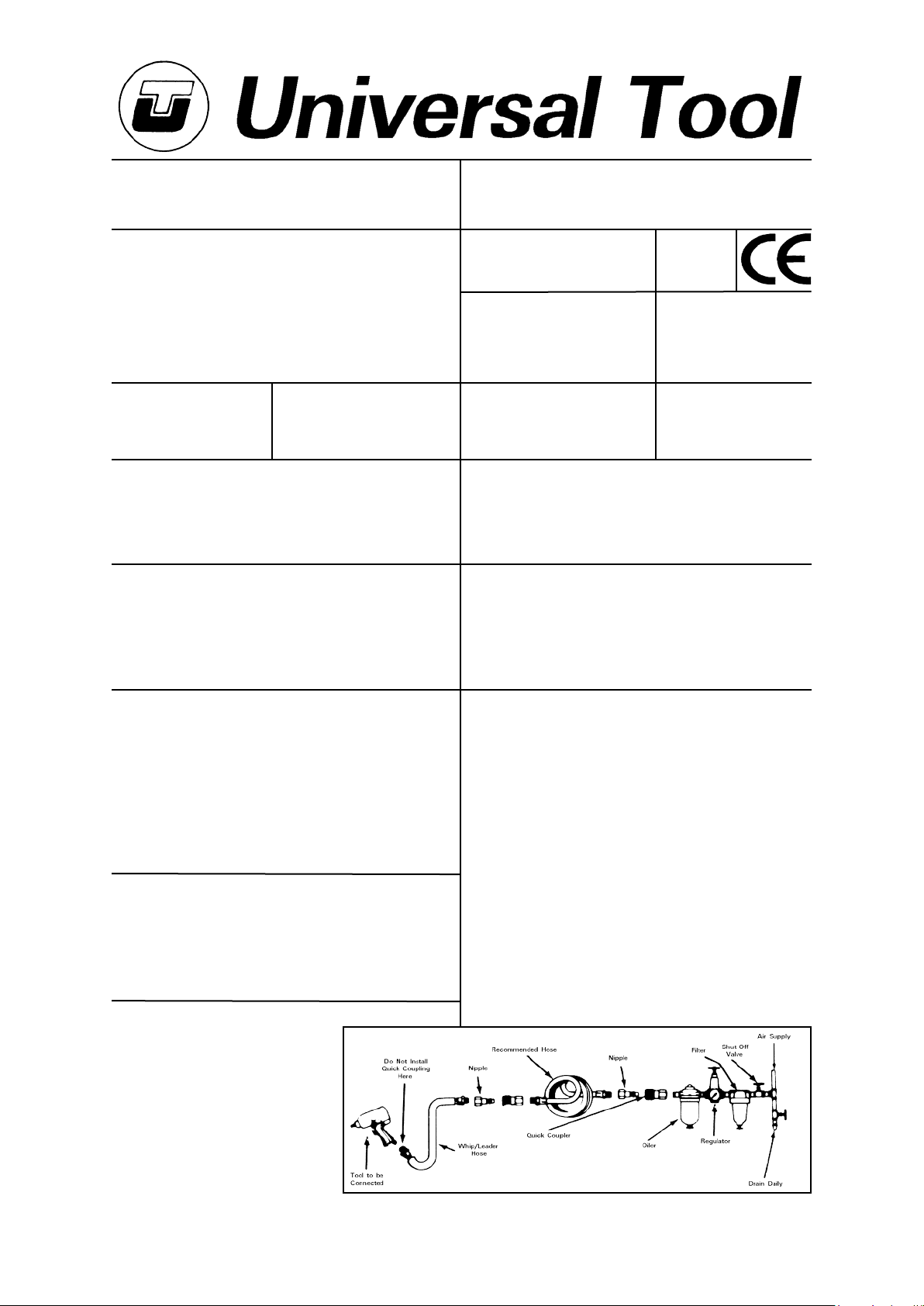
Personal Safety Equipment
Use - Safety Glasses
Yes
Use - Safety Gloves
Use - Safety Boots
Use - Breathing Masks
Use - Ear Protectors
Operator Instructions
Air Pressure
Recommended Working
6.3
bar
90
PSI
Recommended Minimum
n/a
bar
n/a
PSI
Maximum
7.0
bar
100
PSI
Includes - Foreseen Use, Work Stations, Putting Into Service, Operating,
Dismantling, Assembly and Safety Rules
Important
Read these instructions carefully before installing, operating,
servicing or repairing this tool. Keep these instructions in a safe
accessible place.
Manufacturer/Supplier Product Type
Universal Air Tool Company Limited
Unit 8
Lane End Industrial Park
High Wycombe
Bucks
Windscreen Cutter
(Air Knife)
Model No/Nos Serial No
UT616BN
HP14 3BY
Tel No Fax No(01494) 883300 (01494) 883237
RPM
20,000
Cycles Per Min
Product Nett Weight
2.14
0.97
lbs
Kg
Recommended Use Of
Balancer Or Support
No
Foreseen Use of Tool
This tool is designed to be used to assist in the removal of automobile
windscreens by cutting the rubber/rubber bonding that holds the
windscreen in place. It can also be used for the removal of body
protection mouldings and emblems on automobiles. Do not use the
tool for any other purpose than that specified unless first checking
with the manufacturer or an authorised distributor. Unless first
approved by the manufacturer or an authorised distributor, never
modify the tool for any other use or for its use as a windscreen
removal tool.
Work Stations
The tool should only be used as a handheld hand operated tool. It is
always recommended that the tool is used when standing on the
solid floor. It can be used in other positions but before any such use,
the operator must be in a secure position having a firm grip and
footing.
Recommended Hose Bore
Size - Minimum
Ins M/M Ft M
3/8 10 30 10
Recommended Max.
Hose Length
Noise Level Sound Pressure Level 86.0 dB(A)
Test Method Tested in accordance with Pneurop
test code PN8NTC1
Vibration Level
3.8
Metres / Sec²
Test Method Tested in accordance with ISO
standard 8662
incorporating an easy to reach and operate air shut off valve. The air
supply should be lubricated. It is strongly recommended that an air
filter, regulator, lubricator (FRL) is used as shown in Figure 1 as this
will supply clean, lubricated air at the correct pressure to the tool.
Details of such equipment can be obtained from your supplier. If such
equipment is not used then the tool should be lubricated by shutting
off the air supply to the tool, depressurising the line by pressing the
trigger on the tool. Disconnect the air line and pour into the intake
bushing a teaspoonful (5ml) of a suitable pneumatic motor lubricating
oil preferably incorporating a rust inhibitor. Reconnect tool to air
supply and run tool slowly for a few seconds to allow air to circulate
the oil. If tool is used frequently lubricate on daily basis and if tool
starts to slow or lose power.
It is recommended that the air pressure at the tool whilst the tool is
running is 90 p.s.i./6.3 bar. The tool can run at lower and higher
pressures with the maximum permitted working air pressure of 100
p.s.i./7.0 bar.
Putting Into Service
Air Supply
Use a clean lubricated air supply that will give
a measured air pressure at the tool of 90
p.s.i./6.3 bar when the tool is running with
the trigger fully depressed. Use
recommended hose size and length. It is
recommended that the tool is connected to
the air supply as shown in figure 1. Do not
connect the tool to the air line system without
Page No 1
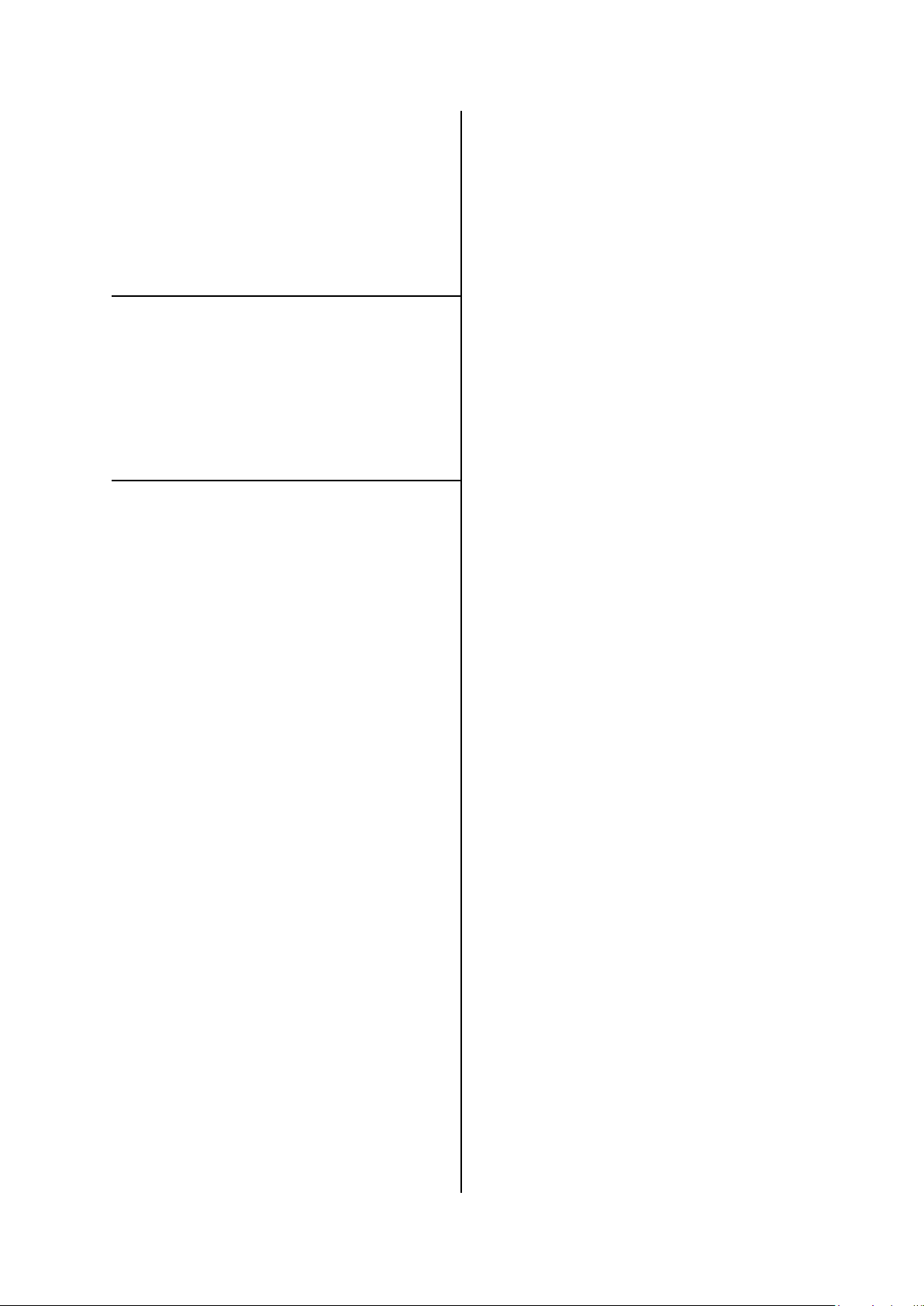
Operating
Fit cutter as required. Cutter blades are covered with a plastic tube.
It is recommended to avoid cutting the hands and/or parts of the
body that this plastic tube is in place when fitting or removing the
cutter and when the tool is not in use.
When using the tool apply firm pressure and allow the tool to cut do not force the cutter. A spray of a diluted “washing up” liquid will
reduce friction and assist the cutting action by reducing friction.
The speed of the tool can be varied by installing an air regulator on
the airline.
Tool Maintenance
It shall be the tool owner’s and/or employer’s responsibility to assure
that tools are maintained in a safe operating condition. Tool
maintenance and repair shall be performed by authorised, trained,
competent personnel. Tools shall be disconnected from their
compressed air supply before repairs are attempted. Repairs shall be
consistent with the manufacturer’s recommended procedures. Tool,
hoses and fittings shall be replaced if unsuitable for safe operation. It
shall be the tool owner’s and/or employer’s responsibility to keep
required rating markings and warnings on the tool in legible condition.
Safety Rules for an Air Knife
1) Prolonged exposures to vibration can cause injury.
2) As this tool has a high vibration level, try to hold the tool when
running free for the shortest time period possible.
3) Read all instructions before using this tool. All operators must be
fully trained in its use and aware of these safety rules.
4) Do not exceed the maximum working air pressure.
5) Use personal protection equipment as recommended.
6) Use only compressed air at the recommended conditions.
7) If the tool appears to malfunction, remove from use immediately
and arrange for service and repair. If it is not practical to remove the
tool from service, then shut off the air supply to the tool and write or
have written a warning note and attach it to the tool.
8) If the tool is to be used with a balancer or other suspension device,
ensure that the tool is firmly attached to the suspension/support
device.
9) When operating the tool, always keep the body and particularly
the hands away from the working attachment fixed to the tool.
10) The tool is not electrically insulated. Never use the tool if there is
any chance of coming into contact with live electricity.
11) Always when using the tool, adopt a firm footing and/or position
and grip the tool sufficiently only to overcome any reaction forces
that may result from the tool doing work. Do not over grip.
12) Use only approved spare parts for maintenance and repair. Do
not modify or make temporary repairs. Major servicing and repairs
should only be carried out by persons trained to do so.
13) Do not lock, tape, wire, etc. the ‘On/Off’ valve in ‘On’ position.
The trigger lever, etc. must always be free to return to the ‘Off’
position when released.
14) Always shut off the air supply to the tool and press the ‘On/Off’
valve to exhaust the air from the feed hose before fitting, removing
or adjusting the working attachment fitted to the tool.
15) Before using the tool make sure that a shut off device has been
fitted to the supply line and the position is known and easily accessible
so that the supply to the tool can be shut off in an emergency.
16) Check hose and fittings regularly for wear.
17) Take care against entanglement of the moving parts of the tool
with clothing, hair, ties, cleaning rags, rings, jewellery, watches,
bracelets, etc. This could cause the body or parts of the body to be
drawn towards and in contact with the moving parts of the tool and
could be very dangerous.
18) It is expected that users will adopt safe working practices and
observe all local, regional or country legal requirements when
installing, using or maintaining the tool.
19) Take care that the exhaust air does not point towards any other
person or material or substance that could be contaminated by oil
droplets. When first lubricating a tool or if the tool exhaust has a high
oil content, do not allow the exhaust air to come near very hot
surfaces or flames.
20) Never lay the tool down until the working attachment has stopped
moving.
21) When the tool is not in use, shut off the air supply and press
trigger/lever to drain the supply line. If the tool is not to be used for
a period of time, first lubricate, disconnect from air supply and store
in a dry average room temperature environment.
22) If the tool is passed from one user to a new or inexperienced
user, make sure these instructions are available to be passed with
the tool.
23) Do not remove any manufacturer fitted safety devices where
fitted, i.e. wheel guards, safety trigger, speed governors, etc.
24) Where ever possible, secure workpiece with clamps, a vice, etc.
to make it rigid so it does not move during the work operation. Keep
good balance at all times. Do not stretch or overreach.
25) Try to match the tool to the work operation. Do not use a tool
that is too light or heavy for the work operation. If in doubt, seek
advice.
26) In general terms this tool is not suitable for underwater use or
use in explosive environments ) seek advice from manufacturer.
27) Try to make sure that the work area is clear to enable the work
task to be performed safely. If practical and possible, try to clear
unnecessary obstructions before starting work.
28) Always use air hose and couplings with minimum working
pressure ratings at least 11/2 times the maximum working pressure
rating of the tool.
Page No 2

UT616BN Windscreen Cutter
Ref No Part No Description
1 616BN-01 Screw
2 616BN-02 Retainer
3 616BN-03 Blade 57mm
4 616BN-04 Packing
5 616BN-05 Spindle Drive
6 616BN-06 Nut Clamp
7 616BN-07 Seal Oil
8 616BN-08 Ball Bearing
9 616BN-09 Head
10 616BN-10 Ball Bearing
10A 616BN-10A Ball Bearing
11 616BN-11 O-Ring
12 616BN-12 Plug
13 616BN-13 O-Ring
14 616BN-14 Screw
15 616BN-15 Fork Drive
16 616BN-16 Shaft Crank
17 616BN-17 Coupling Nut
18 616BN-18 Internal Gear
19 616BN-19 Ball Bearing
20 616BN-20 Front End Plate
21 616BN-21 Spring Pin
22 616BN-22 Spring Pin
Ref No Part No Description
23 616BN-23 Washer
24 616BN-24 Rotor
25 616BN-25 Rotor Blade (4)
26 616BN-26 Cylinder
27 616BN-27 Rear End Plate
28 616BN-28 Ball Bearing
29 616BN-29 Motor Housing
30 616BN-30 Spring Pin
31 616BN-31 Safety Lever Assembly
32 616BN-32 Valve Shaft
33 616BN-33 O-Ring
34 616BN-34 Throttle Valve
35 616BN-35 Valve Spring
36 616BN-36 O-Ring
37 616BN-37 Valve Screw
38 616BN-38 Spring Pin
39 616BN-39 O-Ring
40 616BN-40 Exhaust Sleeve
41 616BN-41 Inlet Bushing
42 616BN-42 "O" Rubber Band
43 616BN-43 Housing Cover
44 616BN-44 Key
Apr 2012 Ver 1.00
Page No 3

Declaration of Conformity
Universal Air Tool Company Limited
Unit 8, Lane End Industrial Park, High Wycombe, Bucks, HP14 3BY, England
declare under our sole responsibility that the product
Model UT616BN Windscreen Cutter, Serial Number
to which this declaration relates is in conformity with the following standard(s) or other normative document(s)
EN792 (Draft), EN292 Parts 1 & 2, ISO 8662 Parts 1, 2 & 14, Pneurop PN8NTC1
following the provisions of
Directive 2006/42/EC
Lane End C. Moppett, Managing Director
Place of issue For and on behalf of the company
Accessories
Distributor
Notes
This document may not be copied wholly or in part by anyone without the consent of the Directors of Universal Air Tool Company Limited
Designed & Written in the U.K.
©Copyright of Universal Air Tool Company Limited, established in the United Kingdom, 1994
Page No 4