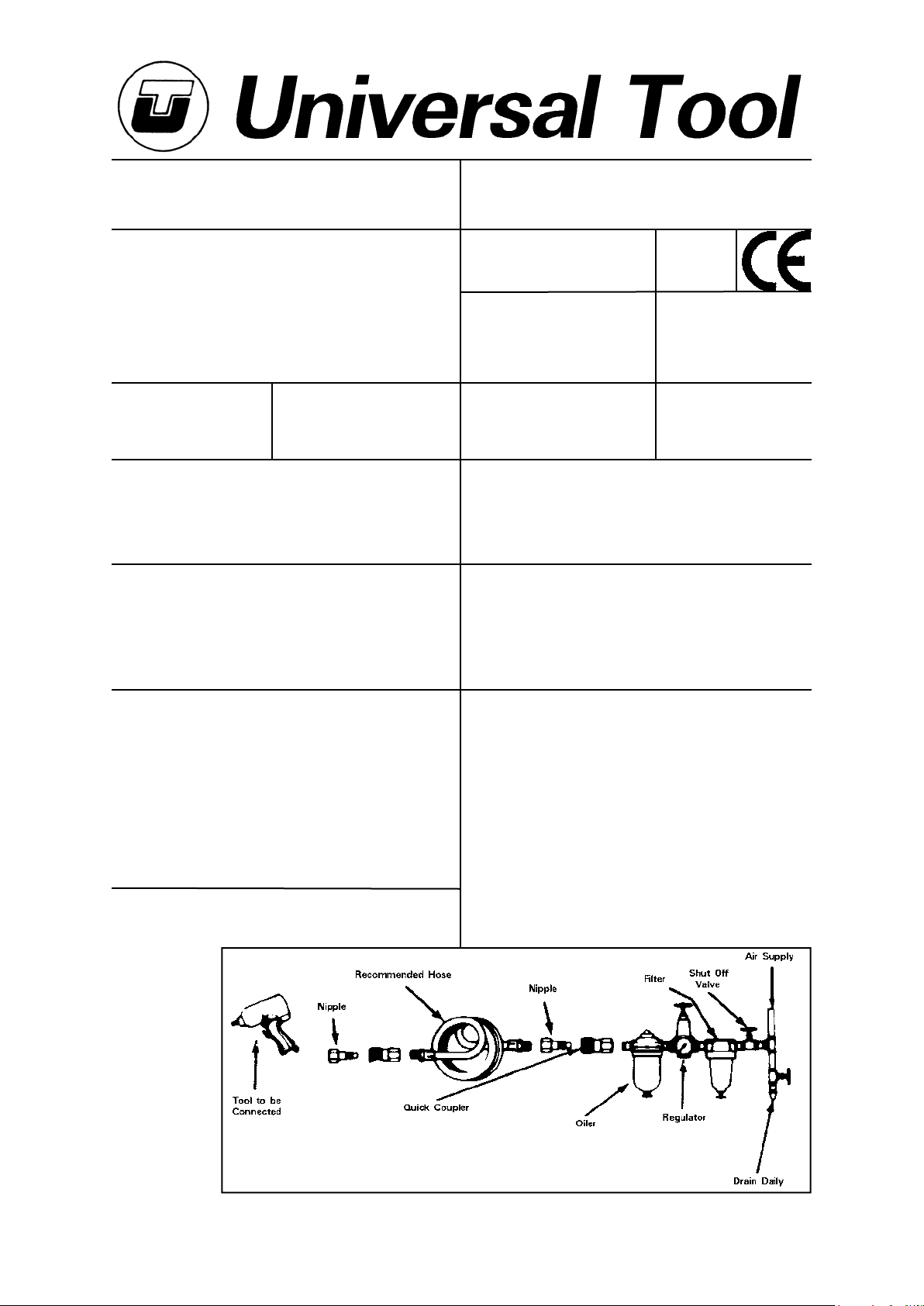
Includes - Foreseen Use, Work Stations, Putting Into Service, Operating,
Operator Instructions Important
Read these instructions carefully before installing, operating,
servicing or repairing this tool. Keep these instructions in a safe
Test Method
Tested in accordance with Pneurop
test code PN8NTC1 and ISO Standard 3744
Test Method
Tested in accordance with ISO
Dismantling, Assembly and Safety Rules
accessible place.
Manufacturer/Supplier Product Type
Universal Air Tool Company Limited
Unit 8
Lane End Industrial Park
High Wycombe
Bucks
5/8” Reversible Straight
Drill
Model No/Nos Serial No (if any)
HP17RD
HP14 3BY
(01494) 883300 (01494) 883237
Product Nett Weight Recommended Use Of
10.14
4.6
Recommended Working
Recommended Minimum
Maximum
Personal Safety Equipment
Use - Safety Glasses
Use - Safety Gloves
Use - Safety Boots
Use - Breathing Masks
Use - Ear Protectors
Fax No
lbs
Kg
Air Pressure
6.3
n/a
7.0
Balancer Or Support
No
bar
90
bar
n/a
bar
10.0
Yes
Yes
Yes
Recommended Hose Bore
Size - Minimum
3/8 10 30 10
Noise Level
PSI
PSI
PSI
standard 8662/1
RPM
1,000
Cycles Per Min
Recommended Max.
Hose Length
Ins M/M Ft M
Sound Pressure Level 90.0 dB(A)
Metres / Sec²
Foreseen Use Of Tool
This drill is designed for the purpose of drilling holes in all types of
materials, i.e. metals, wood, stone, plastics etc. using drilling bits
designed for this purpose. It may be used with other forms of cutting
tools, polishing devices or for sanding using coated abrasive products.
Before using any such products first check with the manufacturer their
suitability for use with this type of drill. Do not use bonded abrasive
products (i.e. grinding wheels) or saw blades or any device which has a
permitted safe working speed less than the free speed of the drill.
Do not use this drill for any other purpose than that specified without
consulting the manufacturer or the manufacturer's authorised supplier.
Work Stations
The tool should only be used as a handheld hand operated tool. It is
always recommended that the
tool is used when
standing on the solid
floor. It can be used
in other positions
but before any such
use, the operator
must be in a secure
position having a
firm grip and footing
and be aware that
the drill can develop
a torque reaction
see section
"Operating".
Putting Into Service
Air Supply
Use a clean lubricated air supply that will give a measured air pressure
at the tool of 90 p.s.i./6.3 bar when the tool is running with the trigger
fully depressed. Use recommended hose size and length. It is
recommended that the tool is connected to the air supply as shown in
figure 1. Do not connect the tool to the air line system without
incorporating an easy to reach and operate air shut off valve. The air
supply should be lubricated. It is strongly recommended that an air filter,
regulator, lubricator (FRL) is used as shown in Figure 1 as this will supply
clean, lubricated air at the correct pressure to the tool. Details of such
equipment can be obtained from your supplier. If such equipment is not
used then the tool should be lubricated by shutting off the air supply to
the tool, depressurising the line by pressing the trigger on the tool.
Disconnect the air line and pour into the intake bushing a teaspoonful
Page No 1
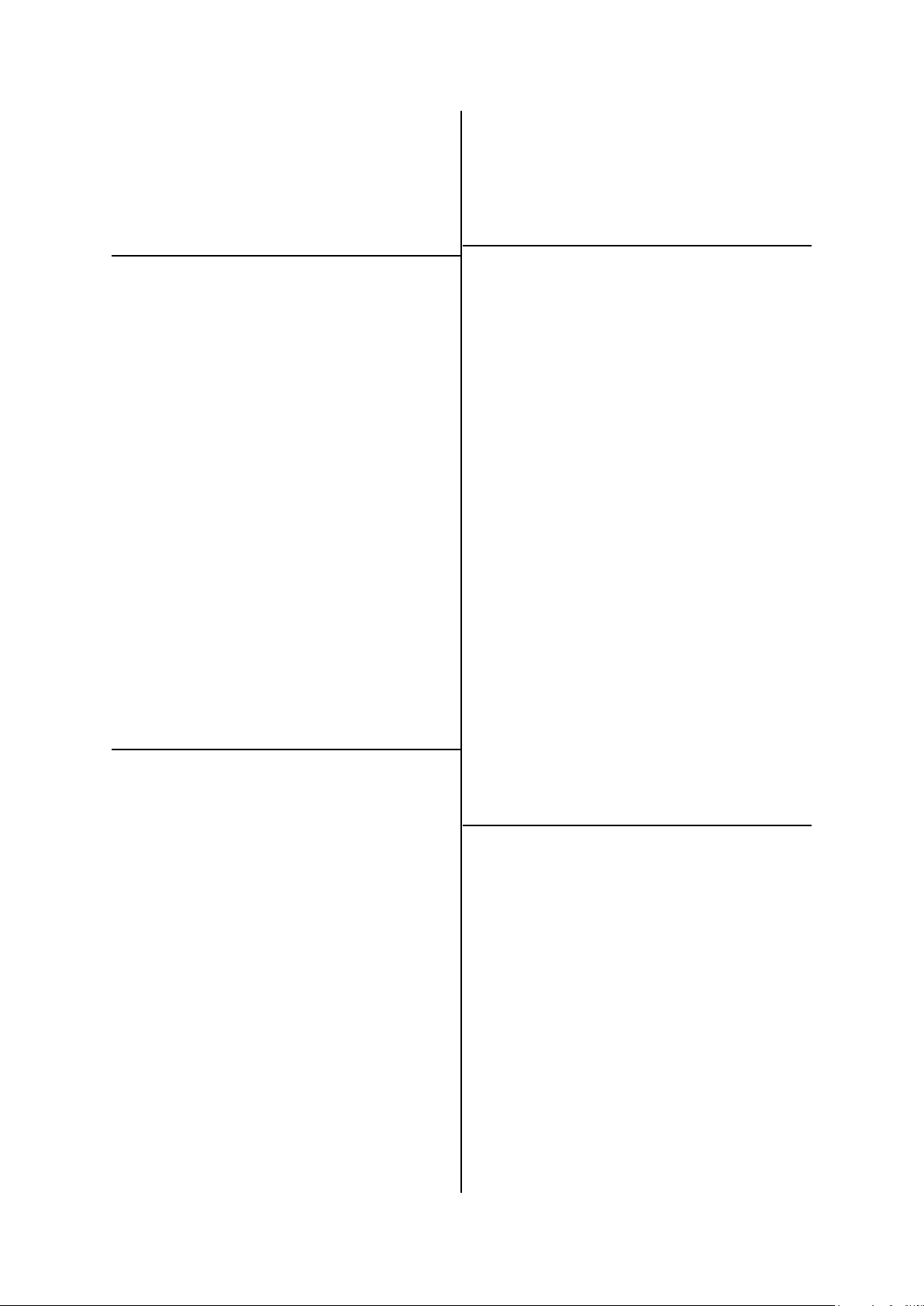
(5ml) of a suitable pneumatic motor lubricating oil preferably
incorporating a rust inhibitor. Reconnect tool to air supply and run tool
slowly for a few seconds to allow air to circulate the oil. If tool is used
frequently lubricate on daily basis and if tool starts to slow or lose power.
It is recommended that the air pressure at the tool whilst the tool is
running is 90 p.s.i./6.3 bar. The tool can run at lower and higher
pressures with the maximum permitted working air pressure of 100
p.s.i./7.0 bar.
all parts with suitable pneumatic tool lubrication oil and reassemble in
the reverse order.
On completing assembly, ensure that all parts are locked tight
and the spindle rotates and the lever throttle. Connect tool to
suitable air supply and operate tool slowly for a few seconds
and reset for operation required. Refer to section on
Operation Instructions.
Operating
Select suitable drill bit, insert the shank into the drill chuck as far as
possible and tighten chuck with key supplied making sure that the
shank of the device is securely clamped centrally between the three
chuck jaws. Remove chuck key.
When drilling holes of all sizes it is advised to use a pointed punch to
mark the centre at which the hole is to be drilled as this will provide a
starting point for the drill tip. This procedure will prevent the drill bit from
skidding, ensure that the hole is drilled where intended and help to
prevent drill breakage when using small drills. When drilling, particularly
with small diameter drills, always try to ensure that load applied to the
drill is such that the drill bit is always at right angles to the hole being
drilled. Do not force the drill but allow it to cut.
When drilling always adopt a firm posture to be able to counteract any
sudden movement of the drill due to torque reaction. Such torque
reaction can occur when the drill stalls due to a too heavy load being
applied or the material being too hard or tough. The torque reaction can
occur when the drill breaks through the material being drilled,
particularly on sheet metal. Always use eye protection and hand
protection is advised, particularly when drilling holes in metals where
the material being removed from the hole is in the form of long sharp
strips. Do not tie the drill chuck key to the drill as the attaching device i.e.
string or chain could become entangled with the rotating chuck and bit
etc.
If using an abrasive device, drilling stone or performing any operation
where dust is created, it is recommended to use a breathing mask.
Always ensure that the material to be drilled is firmly fixed to prevent its
movement.
It is also recommended that when drilling holes of large diameter to first
pre drill a hole of smaller diameter as this will reduce effort required to
drill the hole and minimise torque reaction.
Dismantling & Assembly Instructions
Disconnect the tool from the air supply,
To remove the chuck (53) use a fork chisel, place the fork between the
body of the drill and the chuck and give the fork a tap with a hammer the
chuck will then slide off (JT3 taper chuck).
Use a spanner to undo 8 bolts (37) and 8 screws (19) then you can
divide the tool into three parts.
From the front cap (49) take out 4 pins (9) and 4 gears (24) pull out the
driving rod (48) and bearing (23).
Remove the rotor (33) from the handle (51) by tapping the spline end of
the rotor (33) take off the rear plate (35) and remove the bearing (21)
then take out the 6 rotor blades (1).
To remove the cylinder (36) you must heat the handle (51) this will then
allow you to remove the front plate (34) oil seal (20) and bearing (22) To
remove the speed switch (39) first remove pins (12) (13) remove the
switch lever (26) first remove 2 pins (14).
Remove 4 screws (18) and washers (45) and take off the air inlet (29)
this will then allow you to take out the valve rod assembly parts (5) (16)
(6) (2) (28) .
Reassembly
Clean all parts and examine for wear and cracks, etc. and replace as
necessary. Look in particular for wear and cuts on O-rings, wear on
rotor blades, gears and wear on bearing (21) (22) and (23). Make sure
that the faces of the end plates (34) and (34) and the cylinder (36) are
flat and free from burrs.
Lap on a flat fine grade of abrasive paper if necessary. Use only
manufacturer or authorized distributor supplied spare parts. Lightly coat
Safety Rules When Using A Drill
1) Read all the instructions before using this tool. All operators must be
fully trained in its use and aware of these safety rules. All service and
repair must be carried out by trained personnel.
2) Always select a suitable cutting, abrasive device suitable for use with
this drill.
3) Always shut off the air supply to the drill and depress the trigger to
exhaust air from the feed hose before fitting, adjusting or removing the
device. Remove drill chuck.
4) Always adopt a firm footing and/or position and be aware of torque
reaction developed by the drill.
5) Use only correct spare parts.
6) Check hose and fittings regularly for wear. Do not carry the tool by its
hose and ensure that the hand is remote from the on/off valve (trigger)
when carrying the tool with air supply connected.
7) Do not exceed maximum recommended air pressure. Avoid low air
pressures as this will allow the drill to stall more easily and develop
torque reaction.
8) Use safety equipment as recommended.
9) The tool is not electrically insulated. Do not use where there is a
possibility of coming into contact with live electricity, gas pipes, water
pipes, etc. Check the area of operation before performing the
operation.
10) Take care against entanglement of moving parts of the tool with
clothing, ties, hair, cleaning rags, etc. This will cause the body to be
moved towards the work process and can be very dangerous.
11) Do not attempt to hold or guide the drill chuck when the tool is
running. Keep hands clear of the drilling process.
12) Use only compressed air at recommended conditions.
13) Do not attempt to fit attachments, i.e. for sawing, hedge cutting,
grinding, chain sawing, etc.
14) If the tool appears to malfunction remove from use immediately
and arrange for service and repair.
15) If an additional side handle is fitted to the tool ensure that it is
correctly positioned and fixed securely.
16) If the drill is used with a balancer or other suspension device ensure
that it is fixed securely.
Page No 2

HP17RD 5/8” Reversible Straight Drill
Ref No Part No Description
1 01-105-02 Rotor Blade (6)
2 02-200-01 O-Ring
3 02-200-10 O-Ring
4 02-201-05 O-Ring
5 02-201-09 O-Ring
6 03-301-01 Plastic Ball
7 03-700-04 Steel Ball (2)
8 04-701-09 Pin
9 04-702-09 Pin (4)
10 05-700-01 Pin
11 05-701-03 Pin (2)
12 05-702-01 Pin
13 05-702-04 Pin
14 05-702-05 Pin (2)
15 06-701-21 Spring (2)
16 06-702-15 Pring
17 13-701-11 Screw
18 13-702-02 Screw (4)
19 13-703-03 Screw (8)
20 14-702-05 Oil Seal
21 15-703-02 Ball Bearing
22 15-704-03 Ball Bearing
23 15-706-02 Ball Bearing
24 16-702-02 Gear (4)
25 17-705-01 Switch Lever
26 18-705-01 Reverse Valve
27 22-701-01 Filter
Mar 2007 Ver 1.00
Ref No Part No Description
28 24-706-02 Valve Rod
29 25-704-03 Air Inlet
30 30-308-03 Packing
31 30-308-04 Packing
32 31-703-01 Hook
33 35-710-05 Rotor
34 36-607-02 Front Plate
35 37-607-02 Rear Plate
36 38-507-01 Cylinder
37 39-701-01 Bolt (8)
38 39-702-01 Bolt
39 45-704-02 Speed Switch
40 48-707-01 Gear Ring
41 51-403-08 Bushing
42 51-404-03 Bushing
43 51-607-01 Bushing
44 51-702-13 Bushing
45 52-700-04 Washer (4)
46 52-701-04 Washer (8)
47 52-701-14 Washer
48 74-711-03 Driving Rod
49 75-610-02 Front Cap
50 78-311-01 Handle
51 78-608-02 Handle
52 79-612-01 Handle
53 H0122 Chuck
Page No 3
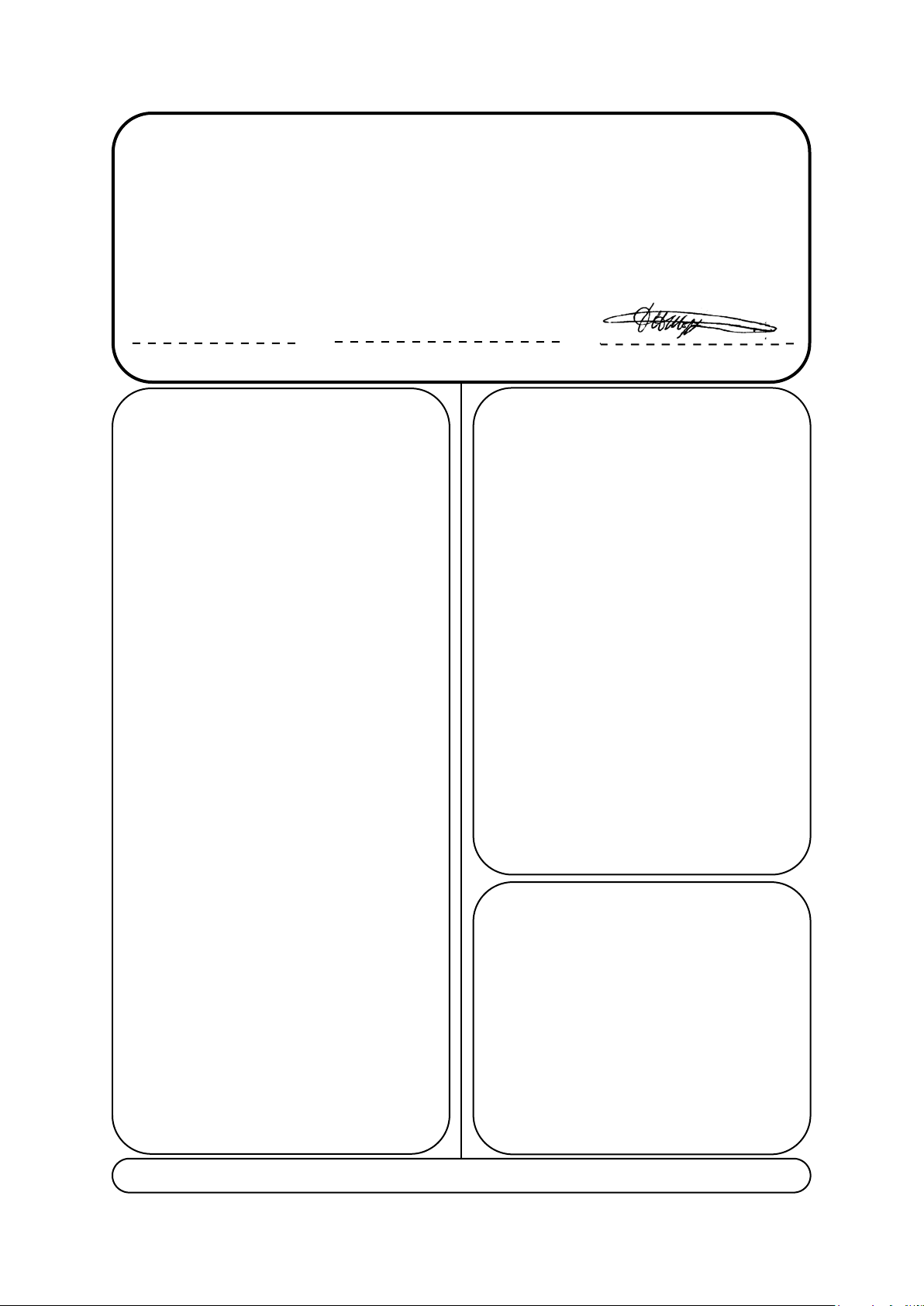
Declaration of Conformity
Universal Air Tool Company Limited
Unit 8, Lane End Industrial Park, High Wycombe, Bucks, HP14 3BY, England
declare under our sole responsibility that the product
Model HP17RD 5/8” Reversible Straight Drill, Serial No
to which this declaration relates is in conformity with the following standard(s) or other normative document(s)
EN792 (Draft), EN292 Parts 1 & 2, ISO 8662 Part 1, Pneurop PN8NTC1
following the provisions of
89/392/EEC as amended by 91/368/EEC & 93/44/EEC
Lane End D.H.Moppett (Man Director)
Place and date of issue Name and signature or equivalent marking of authorised person
Notes
Distributor
This document may not be copied wholly or in part by anyone without the consent of the Directors of Universal Air Tool Company Limited
Designed & Written in the U.K.
©Copyright of Universal Air Tool Company Limited, established in the United Kingdom, 1994
Page No 4