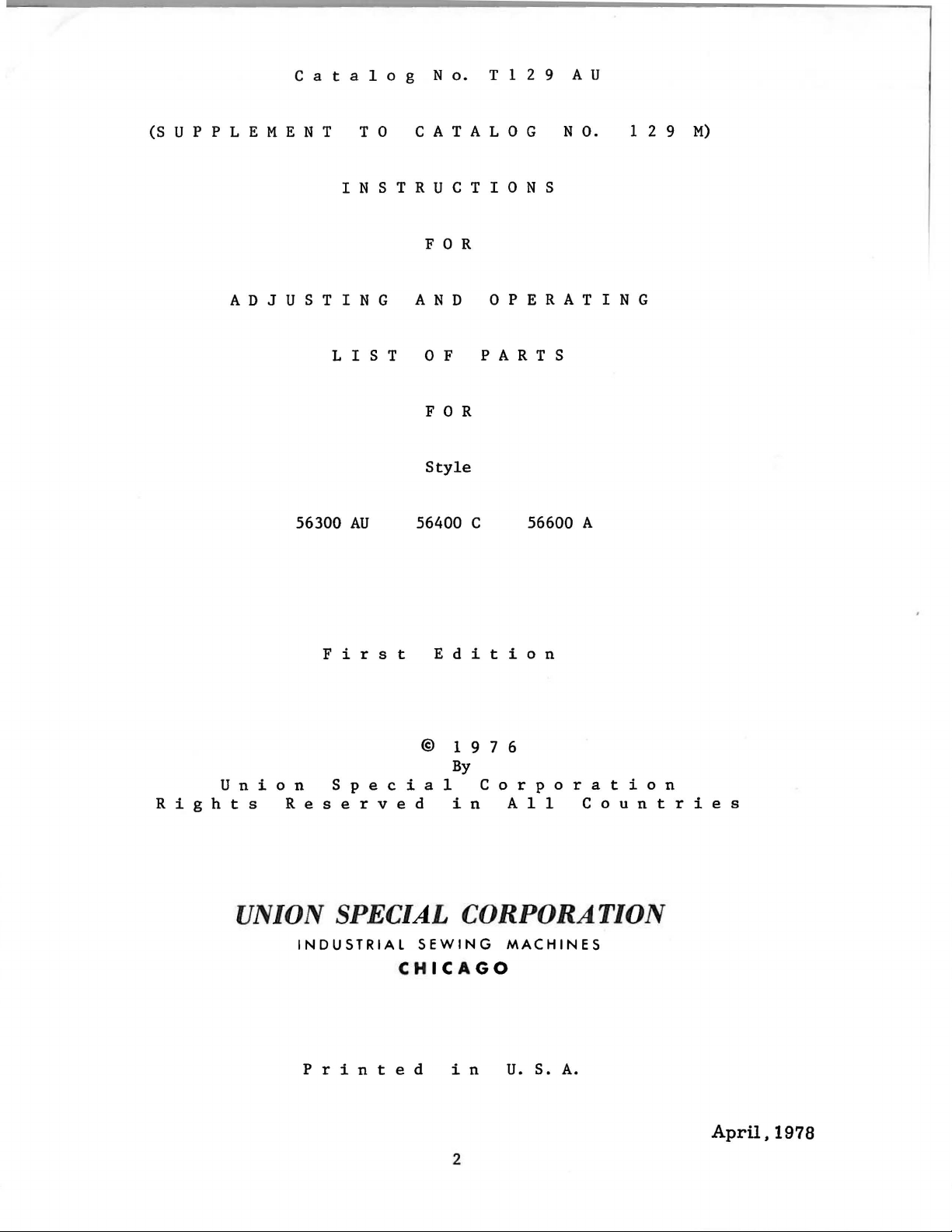
C a t a 1 o g N
o.
T 1 2 9 A U
(S U P P
L E M E N T T 0 C A T A L 0 G N
0.
1 2 9
I N S T R U C T I 0 N S
F 0 R
A D J U S T I N G A N D 0 P E R A T I N G
L I S T 0 F P A R T S
F 0 R
Style
56300
AU
56400 c 56600 A
M)
F i r s t E d i t i o n
@ 1 9 7 6
By
U n i o n S p e c i a 1 C o r p o r a t i o n
R i g h t s R e s e r v e d i n A 1 1 C o u n t r i e s
UNION SPECIAL CORPORATION
INDUSTRIAL
P r i n t e d i n
SEWING
CHICAGO
MACHINES
U.
S.
A.
2
April.1978
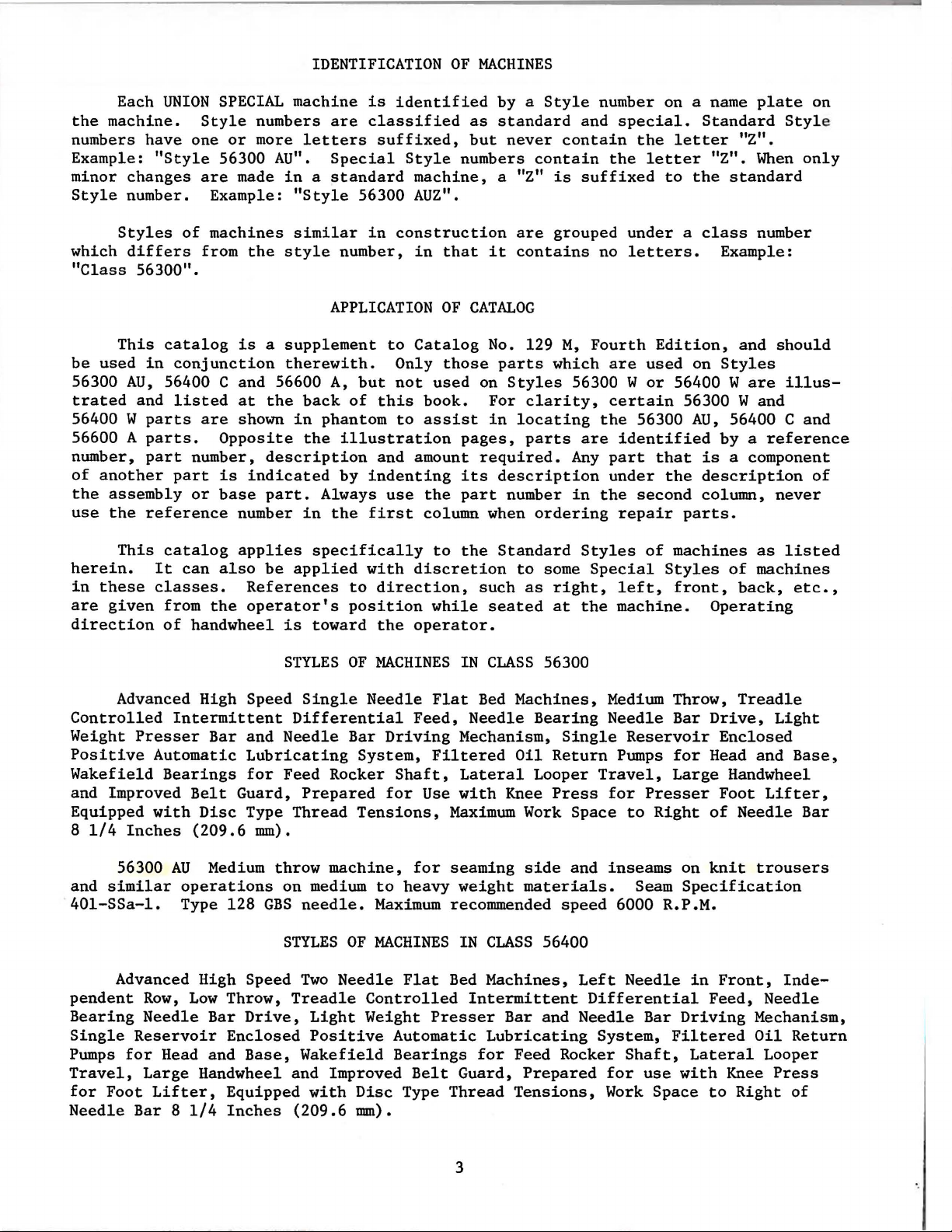
Each
the
machine.
numbers
Example:
minor
Style
changes
number. Example:
UNION
have
"Style
SPECIAL
Style
one
56300
are
numbers
or
more
made
IDENTIFICATION
machine
letters
AU".
in a standard
"Style
is
are
classified
Special
56300
identified
suffixed,
Style
machine,
AUZ".
OF
MACHINES
by a
as
standard
but
numbers
a "Z"
never
contain
Style
contain
is
number on a name
and
special.
the
letter
the
letter
suffixed
to
the
plate
Standard
"Z".
"Z".
When
standard
Styl
only
on
e
Styles
which
"Class
be
56300
trated
56400 W
56600 A
number,
of
the
use
herein.
in
are
direction
differs
This
used
AU,
another
assembly
the
This
these
given
of
machines
from
56300".
catalog
in
conjunction
56400 C and 56600 A,
and
listed
parts
parts.
part
reference
are
number,
part
or
catalog
It
can
classes.
from
of
handwheel
the
is a supplement
at
the
shown
Opposite
description
is
indicated
base
also
the
part.
number
applies
be
References
operator's
similar
style
therewith.
applied
is
STYLES
number,
APPLICATION
back
of
in
phantom
the
illustration
by
Always
in
the
specifically
to
position
toward
OF
in
construction
in
to
Catalog
Only
but
not
this
book.
to
assist
and amount
indenting
use
first
with
MACHINES
column when
discretion
direction,
the
operator.
that
OF
those
used
the
to
while
are
it
contains
CATALOG
No.
parts
on
Styles
For
in
locating
pages,
required.
its
description
part
number
the
Standard
to
such
seated
IN
CLASS
grouped
129
M,
which
56300 W
clarity,
parts
Any
in
ordering
some
as
right,
at
56300
under a class
no
letters.
Fourth
are
certain
the
56300
are
identified
part
under
the
second
repair
Styles
Special
left,
the
machine.
Edition,
used
or
of
on
56400 W
56300 W and
AU,
that
is
the
description
column,
parts.
machines
Styles
front,
number
Example:
and
should
Styles
are
illus-
56400 C and
by a reference
a component
of
never
as
listed
of
machines
back,
Operating
etc.,
Advanced High Speed
Controlled
Weight
Positive
Wakefield
and Improved
Equipped
1/4
8
56300
and
similar
401-SSa-1.
Advanced High Speed
pendent
Bearing
Single
Pumps
Travel,
for
Needle
for
Foot
Intermittent
Presser
Automatic
Bearings
with
Inches
AU
operations
Type 128
Row,
Low
Needle
Reservoir
Head and
Large
Lifter,
Bar 8
1/4
Belt
Single
Differential
Bar
and
Needle
Lubricating
for
Feed Rocker
Guard,
Disc
(209.6
Handwheel and Improved
Type
Medium
Throw,
Bar
Drive,
Enclosed
Base,
Equipped
Inches
Prepared
Thread
mm).
throw
on medium
GBS
needle.
STYLES
Two
Treadle
Wakefield
(209.6
Light
Positive
with
Needle
Bar
System,
Tensions,
machine,
to
Maximum
OF
MACHINES
Needle
Controlled
Weight
Disc
mm).
Flat
Feed,
Driving
Filtered
Shaft,
for
Use
Maximum
for
seaming
heavy
recommended
Flat
Automatic
Bearings
Type
Bed
Presser
Belt
Thread
Bed
Machines,
Needle
Mechanism,
Lateral
with
weight
IN
CLASS
Machines,
Intermittent
Lubricating
for
Guard,
Bearing
Oil
Looper
Knee
Work
side
materials.
Bar and
Feed Rocker
Prepared
Tensions,
Single
Return
Press
Space
and
speed
56400
Left
Needle
Medium
Needle
Pumps
Travel,
for
inseams
6000 R.P.M.
Needle
Differential
System,
Shaft,
for
Work
Throw,
Bar
Reservoir
for
Large
Presser
to
Right
Seam
Bar
Filtered
use
Space
Treadle
Drive,
Enclosed
Head and
Handwheel
Foot
Lifter,
of
Needle
on
knit
Specification
in
Feed,
Driving
Lateral
with
to
trousers
Front,
Needle
Mechanism,
Oil
Looper
Knee
Right
Press
Light
Base,
Bar
Inde-
Return
of
3

STYLES
OF
MACHINES
IN
CLASS
56400
(Continued)
5640 0 C
pajamas,
modified.
speed
6000 R.P.M.
Low
etc.,
made from
Type 108
Advanced Hi gh Speed
p ·
ndent
Row,
Low
Throw,
Bearing Needle Bar
Singl
Pumps
Travel,
Needle
garments
ification
Maximum
number
The
measured
ively,
given
for
Foot Lif t e
size
e Rese
56600 A
rvoir
for Head
Larg
e Handwheel and Improved
Bar 8
1/4
Enclosed
and
r,
Equipped
Low
made from light wei
401-LSc-2
recommended
Each
UNION
denotes
number,
in
the
on
the
SPECIAL
the
stamped
thousandths
type
number and
label
throw
machine,
light
GS
needle.
STYLES
Two
Treadle
Drive,
Base,
Inch
throw
Wakefield
es (209.6mm).
machine,
modified.
speed
needle
kind
of
on
of
of
all
for
weight
Standard
OF
MACHINES
Needle
Controlled
Light
Positive
Weight
Automatic
Bearings
with
Disc
for gathering
ght
wov
en fabri
Type 108
6000 R.P.M.
has
both a type
shank,
the
an
the
needles
point,
needle
inch,
size
packaged
setting
woven
gauges
IN
Flat
Bed
Presser
Belt
Type
Thread
GS
NEEDLES
length,
shank,
midway
number
puff
sleeves
fabrics.
nos.
CLASS
56600
Machines,
Intermittent
Bar
Lubricating
for
Feed Rocker
Guard,
Prepared
Tensions,
and
cs and
needle.
similar
Standard
number and a
groove,
denotes
between
represent
and
sold
Seam
12,
16.
Right
Differential
and
Needle
System,
attaching
finish
the
the
shank
the
complete
by
Union
in
house
dresses,
Specification
Maximum
Needle
Bar
Driving
Filtered
Shaft,
for
Work
use
Space
Lateral
with
ruffles
operations.
gauges
size
nos.
number. The
and
largest
and
diameter
the
symbol,
Special.
waists,
401-LSc-2
recommended
in
Front,
Feed,
Ind
Needle
Mechanism,
Oil
Return
Looper
Knee
Press
to
to
Right
body
Seam
8,
12,
of
of
Spec-
16.
type
other
eye.
details.
of
blade,
Collect-
which
e-
is
Standard
shank,
point,
125/049,
round
chromium
140/054,
Standard
has a round
spotted,
needle,
complete
To
have
or
chromium
order
Selection
Thread
should
mation.
Success
UNION
its
approved
and
SPECIAL
subsidiaries
scientific
durability
Genuine
parts
your
are
guarantee
recommended
point,
recommended
shank,
needle
the
type
would
of
pass
in
Needles
are
needles
stamped
of
short,
plated
and
060.
round
plated
orders
and
read:
the
proper
freely
USE
the
operation
and
and
~uthorized
principles,
assured.
are
with
the
the
highest
needle
~ouble
is
available
needle
point,
and
is
promptly
size
number
"1000
needle
through
GENUINE
of
Repair
packaged
Union
quality
for
Style
groove,
for
Styles
extra
short,
available
and
should
Needles,
size
needle
NEEDLES
these
Parts
machines
as
distributors.
. and
are
with
Special
in
56300
struck
in
sizes
56400 C and 56600 A
double
in
sizes
accurately
be
Type 128
should
eye
in
AND
REPAIR
furnished
made
with
labels
trademark,
materials
AU
is
groove,
032,
groove,
036,
filled,
forwarded.
GBS,
be
determined
order
PARTS
can
be
by
They
are
utmost
marked
~
U S Emblem. Each
and
Type 128
ball
90/036,
GBS.
eye,
100/040,
is
struck
040.
an
empty
Use
description
Size
032".
by
to
produce
secured
the
designed
only
Union
according
precision.
workmanship.
It
has a round
spotted,
ball
110/044,
Type 108
groove,
GS.
ball
package, a sample
on
label.
size
of
thread
a good
Special
• Genuine
stitch
with
genuine
Corporation,
to
Maximum
the
efficiency
repair
trademark
It
eye,
A
used.
for-
most
is
. 4

-
FILL
MAIN
RESERVOIR
HERE
FOR
CORRECT
OIL
LEVEL
NEEDLE
SHOULD
OPERATE
OF
GAUGE
BE
IN
POSITION
Thread
clarity.
Note:
it
has
The
must
be
screw
black
mineral
oil
level
to
the
and no
THREADING
machine
Style
only
one
oil
has
filled
(A,
line,
oil
left
oiling
before
Fig.
1)
located
of a Saybolt
in
"OPERATE"
of
"OPERATE"
other
AND
OILING
as
56300
needle
been
in
to
than
DIAGRAM
indicated
AU
threads
and
one
drained
starting
top
cover
the
right
viscosity
position
zone marked
keeping
above.
looper
from
to
and
of
and
the
CAUTION!
FILL ALL
BEFORE
MACHINE
BEFORE
FOR
STYLES
exactly
thread.
the
machine
operate.
add
oil
"OPERATE"
of
90
add
oil
"LOW".
main
OIL
RESERVOIRS
STARTING.
HAS
BEEN
SHIPPING.
56300
The
looper
the
same
To
fill
until
zone marked "FULL". Use a
to
125
when
The
reservoir
AU,
threading
as
before
machine
needle
seconds
needle
machine
filled
DRAINED
56400 C and 56600 A
the
other
shipping
with
of
oil
at
100°
is
to
is
automatically
is
has
been
machines
and
the
oil,
gauge
Fahrenheit.
the
necessary.
remove
(B)
black
Fig.
enlarged
except
reservoir
plug
is
on
straight
Maintain
line
located
lubricated
1
for
that
the
in
Excessive
the
main
oil
frame
to
in
the
the
main
left
reservoir
of
the
oil
may
be
gauge.
6
drained
at
the
plug
screw
(C,
Fig.
1)
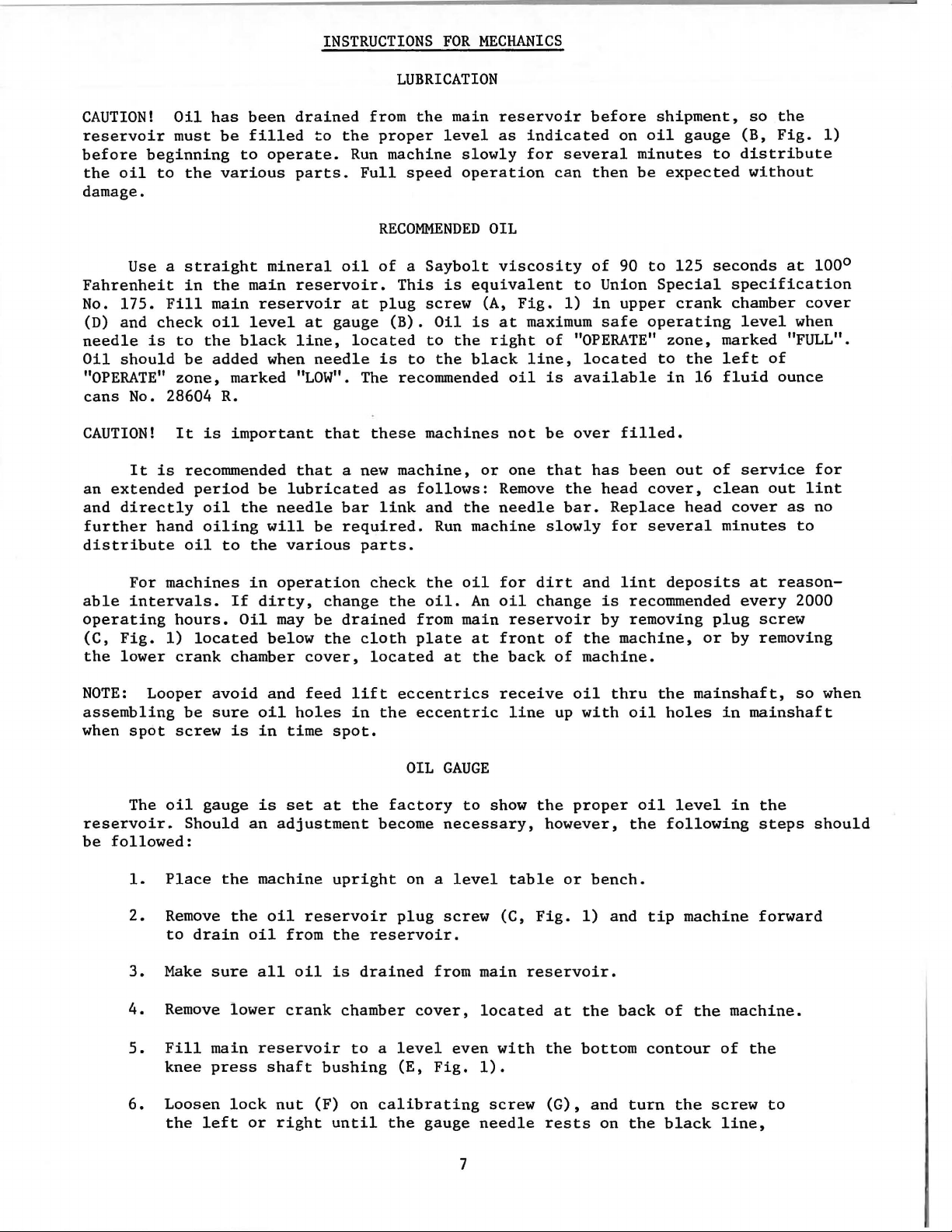
INSTRUCTIONS
LUBRICATION
FOR
MECHANICS
CAUTION!
reservoir
before
the
damage.
Fahrenheit
No.
(D)
needle
Oil
"OPERATE"
cans
CAUTION!
an
and
further
distribute
beginning
oil
to
Use a
175.
and
check
is
should
No. 28604 R.
It
is
extended
directly
hand
Oil
has
must
Fill
be
to
the
various
straight
in
the
main
oil
to
the
black
be
added
zone,
It
marked
is
important
recommended
period
oil
the
oiling
oil
to
been
drained
filled
operate.
parts.
mineral
main
reservoir.
reservoir
level
line,
when
"LOW".
that
be
lubricated
needle
will
the
various
to
at
gauge
needle
that
be
from
the
Run
Full
oil
at
located
The recommended
a new
bar
required.
parts.
the
main
proper
machine
RECOMMENDED
of a Saybolt
plug
(B).
is
these
as
link
level
speed
This
is
screw
Oil
to
the
to
the
machines
machine,
follows:
and
Run
reservoir
as
slowly
operation
equivalent
is
black
the
machine
OIL
viscosity
(A,
Fig.
at
right
oil
not
or
one
Remove
needle
for
maximum
before
indicated
several
can
of
to
1)
of
"OPERATE"
line,
located
is
available
be
over
that
the
bar.
slowly
has
on
then
90
Union
in
upper
safe
filled.
been
head
Replace
for
shipment,
oil
gauge
minutes
be
expected
to
125
Special
crank
operating
zone,
to
the
in
out
cover,
head
several
so
the
(B,
Fig.
to
distribute
without
seconds
specification
chamber
marked "FULL".
left
16
fluid
of
clean
cover
minutes
at
level
of
ounce
service
out
as
1)
100°
cover
when
for
lint
no
to
For
able
operating
NOTE:
assembling
when
be
intervals.
(C,
Fig.
the
lower
Looper
spot
The
reservoir.
followed:
1.
2.
3.
4.
machines
hours.
1)
located
crank
avoid
be
sure
screw
oil
gauge
Should
Place
Remove
to
Make
Remove
the
drain
sure
in
operation
If
dirty,
Oil
may
below
chamber
and
oil
is
in
is
an
adjustment
machine
the
oil
oil
all
lower
change
be
the
cover,
feed
holes
time
set
at
reservoir
from
oil
crank
check
drained
cloth
located
lift
in
the
spot.
the
become
upright
the
reservoir.
is
drained
chamber
the
the
oil.
from main
plate
at
eccentrics
eccentric
OIL
GAUGE
factory
necessary,
on a
plug
screw
from main
cover,
oil
An
at
the
to
level
located
for
oil
reservoir
front
back
receive
line
show
table
(C,
reservoir.
dirt
and
change
of
the
of
machine.
oil
up
with
the
proper
however,
or
Fig.
at
1)
the
lint
is
recommended
by
removing
machine,
thru
oil
oil
the
bench.
and
back
deposits
the
mainshaft,
holes
level
following
tip
machine
of
the
every
plug
or
by
in
in
machine.
at
reason-
2000
screw
removing
so
mainshaft
the
steps
forward
should
when
5.
Fill
6.
main
knee
press
Loosen
the
left
reservoir
lock
or
shaft
nut
right
to a level
bushing
(F) on
until
even
(E,
Fig.
calibrating
the
gauge
1).
needle
7
with
screw
the
(G),
rests
bottom
and
on
contour
turn
the
the
black
of
screw
line,
the
to

OIL
GAUGE
(Continued)
7.
8.
Remove
chamber
needle
inside
chamber
lever
stud
wardly
the
inside
just
above
stop
collar.
on
the
clearance
located
Tighten
cover.
Add
right
NEEDLE
cover
lever
the
arm
cover,
(B).
and
that
wall
the
needle
as
to
lock
oil
so
of
"OPERATE"
LEVER
the
head
(D,
Fig.
bearing
casting,
which
Make
its
of
notch
(Do
not
lever).
in
Figure
the
left
nut
that
BEARING
cover
1).
oiler
below
lubricates
sure
delivery
the
bed
of
the
allow
Allow
2.
of
(F) and
gauge
zone,
Check
(A,
it
end (C)
casting
needle
the
1/64
ALIGNING
"OPERATE"
replace
needle
rests
marked "FULL".
OILER
and
upper
position
Fig.
2)
the
upper
the
needle
is
tilted
contacts
at
the
lever
oiler
to
inch
THE
(TWO
NEEDLE
zone,
plug
on
crank
of
located
crank
down-
back,
shaft
rest
(.40mm)
NEEDLE
MACHINES)
marked
screw
the
black
BAR
"LOW".
(C) and
line,
lower
located
Fig.
crank
2
chamber
to
the
Align
PI40
A.
See
set
of
needles
correspond
needle
bar
Fig.
the
chart
with
clamp
3
needle
bar
below.
(Type and
the
vertical
screw
(A,
Fig.
3)
with
the
proper
If
test
Size
faces
(B,
Fig.
Machine
56400 C-12
plate
as
required)
3)
of
the
and
Styles
and
turn
test
and
needle
bar
Test
pins
align
guard.
as
698 AP-12
56400 C-16 698 AP-16
56600 A-8 698 H-2
56600 A-12 698
56600 A-16
698
SYNCHRONIZING
Insert
wheel
(A,
Fig.
of
the
with
respect
the
reverse
the
left,
the
motions
with
tion
from
respect
of
the
greatest
tion
move
the
rear.
in
needle
the
operating
4),
moving
(B).
to
direction
and
is
synchronize,
to
.005
inch
eye
of
when
the
the
looper
Moving
looper
direction
to
Note
the
looper
even
the
looper
(.127mm)
the
needle
pulley
it
in
the
until
with
drive
in
reverse.
test
are
the
required.
Plate
H-4
H-4~
LOOPER
the
until
left
the
height
point,
the
the
the
height
point
is
allowable.
to
is
turned
shaft
the
opposite
plate,
not
available,
needle
To
bar
align
Tighten
No.
AND
NEEDLE
looper
rocker
the
is
even
of
the
then
looper
left
side
of
will
be
the
point
in
the
synchronizing
direction
using
so
needle
Test
PI40
PI40
PI40
PI40
PI40
MOTIONS
point
with
eye
turn
point
of
the
eye
the
If
of
the
operating
test
insert
that
needles
bar,
clamp
Pin
screw.
No.
A
A
A
A
A
and
turn
of
the
the
left
of
the
handwheel
again
the
needle.
of
the
same. A
the
distance
looper
stud
acts
pins
a
loosen
hand-
looper
side
needle
in
moves
needle
varia-
is
direct-
(C)
the
No.
new
to
If
to
8