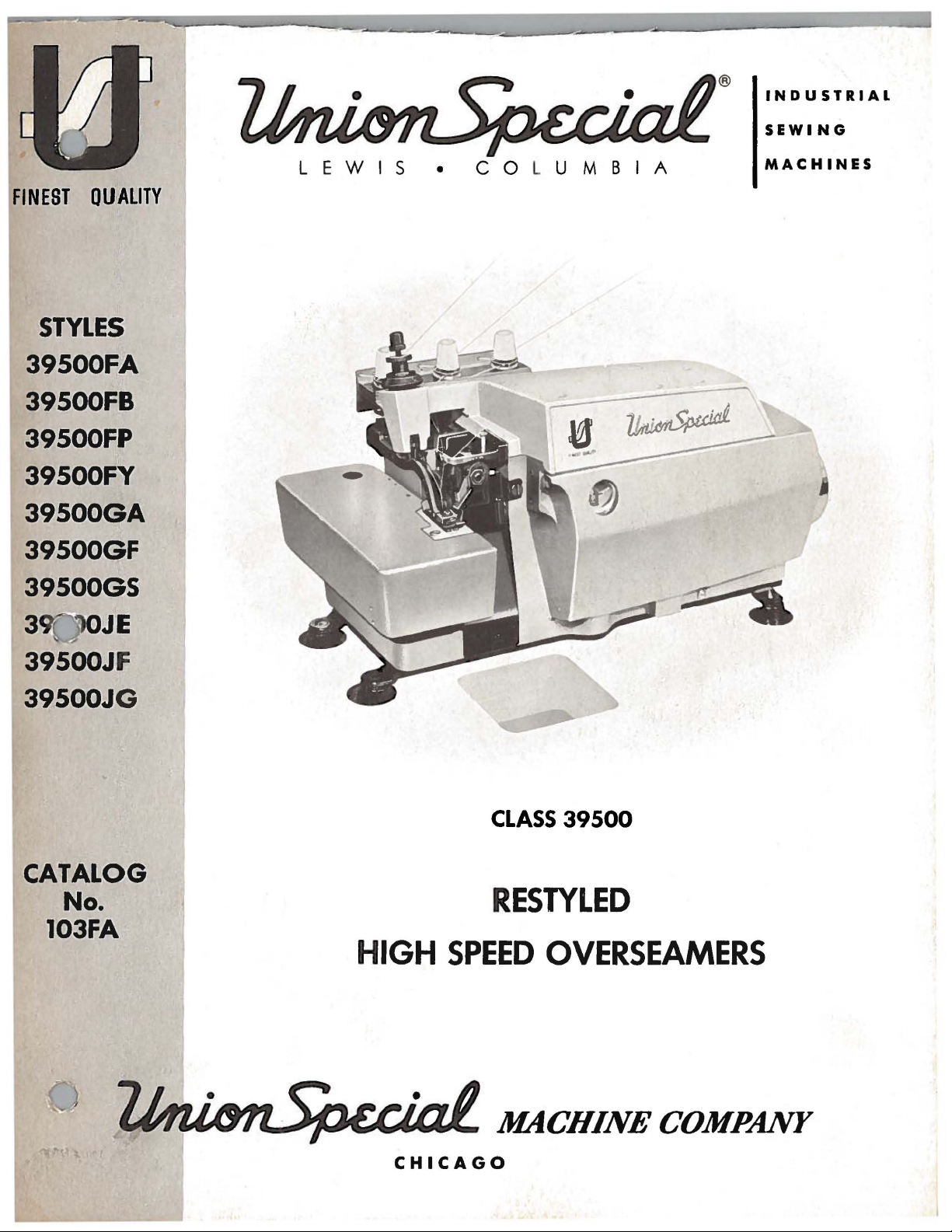
®
INDUSTRIAl
SEWING
FINEST
QUALITY
STYLES
39500FA
39500FB
39500FP
39500FY
39500GA
39500GF
39500GS
LEWIS
•
CO
L
UMBIA
MACHINES
3
39500JF
39500JG
CATALOG
No.
103FA
HIGH
CLASS
39500
RESTYLED
SPEED
OVERSEAMERS
CHICAGO
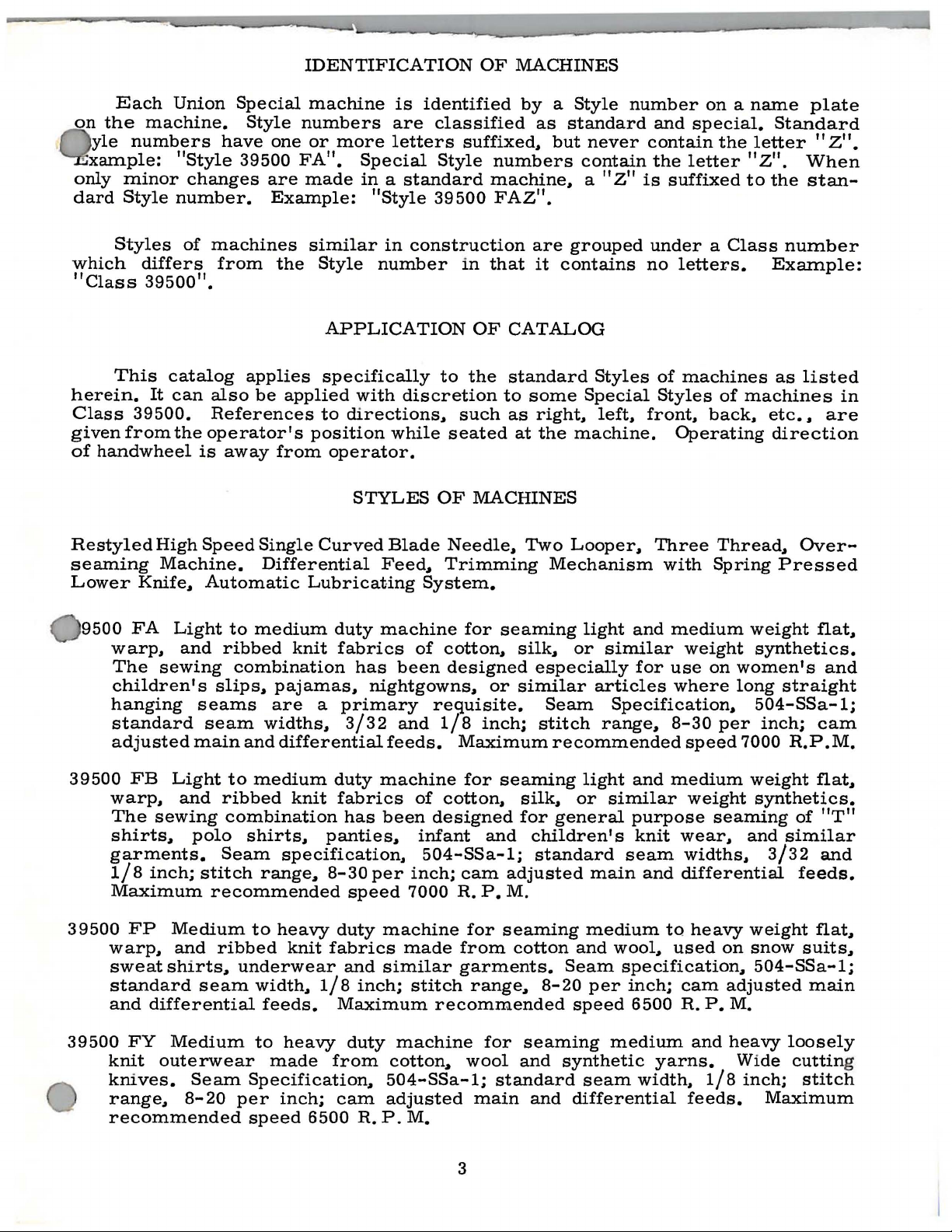
IDENTIFICATION
OF
MACHINES
Each
on
the
yle
numbers
xa.m.ple:
only
dard
which
"Class
herein.
Class
given
of
Restyled
seaming
Lower
minor
Style
Styles
This
39500.
from
handwheel
Union
machine.
"Style
changes
number.
of
differs
39500".
catalog
It
can
the
High
Machine.
Knife..
Special
Style
have
39500
are
machines
from
applies
also
be
References
operator's
is
away
Speed
Automatic
Single
Differential
machine
numbers
one
or
more
FA".
made
Example:
similar
the
Style
APPLICATION
specifically
applied
to
position
from
operator.
Curved
Lubricating
is
identified
are
classified
letters
Special
in a standard
"Style
in
number
with
directions
STYLES
Blade
Feed
39500
construction
discretion
while
..
System.
suffixed..
Style
to
..
OF
Trimming
numbers
machine.. a "Z"
FAZ".
in
that
OF
the
to
such
seated
MACHINES
Needle.
by a Style
as
standard
but
never
contain
are
grouped
it
contains
CATALOG
standard
as
at
some
right
Two
Special
..
the
machine.
Looper
Mechanism
number
Styles
left
..
..
on a name
and
special.
contain
the
is
suffixed
under a Class
no
of
Styles
front
Three
with
the
letter
letters.
machines
..
Operating
"Z".
to
of
machines
back
Thread
Spring
Standard
letter
the
number
Example:
as
..
etc..
direction
..
Pressed
plate
"Z".
When
stan-
listed
in
are
Over-
9500
39500
39500
39500
FA
warp..
The
children's
hanging
standard
adjusted
FB
warp..
The
shirts..
garments.
1/8
Maximum
FP
warp.,
sweat
standard
and
FY
knit
knives.
range.,
recommended
Light
and
sewing
Light
and
sewing
inch;
Medium
and
shirts.,
differential
Medium
outerwear
to
ribbed
combination
slips,
seams
seam
main
to
ribbed
combination
polo
Seam
stitch
recommended
ribbed
seam
Seam
8-20
medium
pajamas
are
widths.
and
differential
medium
shirts.
specification.
range,
to
heavy
knit
underwear
width
feeds.
to
heavy
made
Specification.,
per
inch;
speed 6 500
knit
knit
..
duty
a
duty
panties,
8-30
fabrics
1/8
from
machine
fabrics
has
been
..
nightgowns.
primary
3/32
fabrics
has
speed
duty
and
Maximum
duty
cam
and
feeds.
machine
been
per
inch;
7000
machine
made
similar
inch;
R.
stitch
machine
cotton
504-SSa-1;
adjusted
P.
M.
for
seaming
of
cotton
designed
requisite.
1/8
of
cotton.
designed
infant
504-SSa-1;
recommended
..
..
or
inch;
Maximum
for
seaming
and
cam
R.
P.
for
from
garments.
range.,
for
wool
standard
main
silk,
especially
similar
Seam
stitch
recommended
silk,
for
general
children's
standard
adjusted
M.
seaming
cotton
8-20
seaming
and
synthetic
and
light
or
light
or
medium
and
Seam
speed
seam
differential
and
similar
for
articles
Specification.
range.
and
similar
purpose
knit
seam
main
wool
specification.,
per
inch;
6500
medium
width.
medium
weight
use
where
8-30
speed
medium
weight
wear
widths.
and
differential
to
heavy
..
used
cam
R.
and
yarns.
feeds.
weight
synthetics.
on
women's
long
504-SSa-1;
per
7000
weight
synthetics.
seaming
..
and
weight
on
snow
504-SSa-1;
adjusted
P.M.
heavy
Wide
1/8
inch;
flat,
and
straight
inch;
3/32
Maximum
cam
R.P
.M.
flat
of
"T"
similar
and
feeds.
flat,
suits,
main
loosely
cuttin
stitch
..
g
3
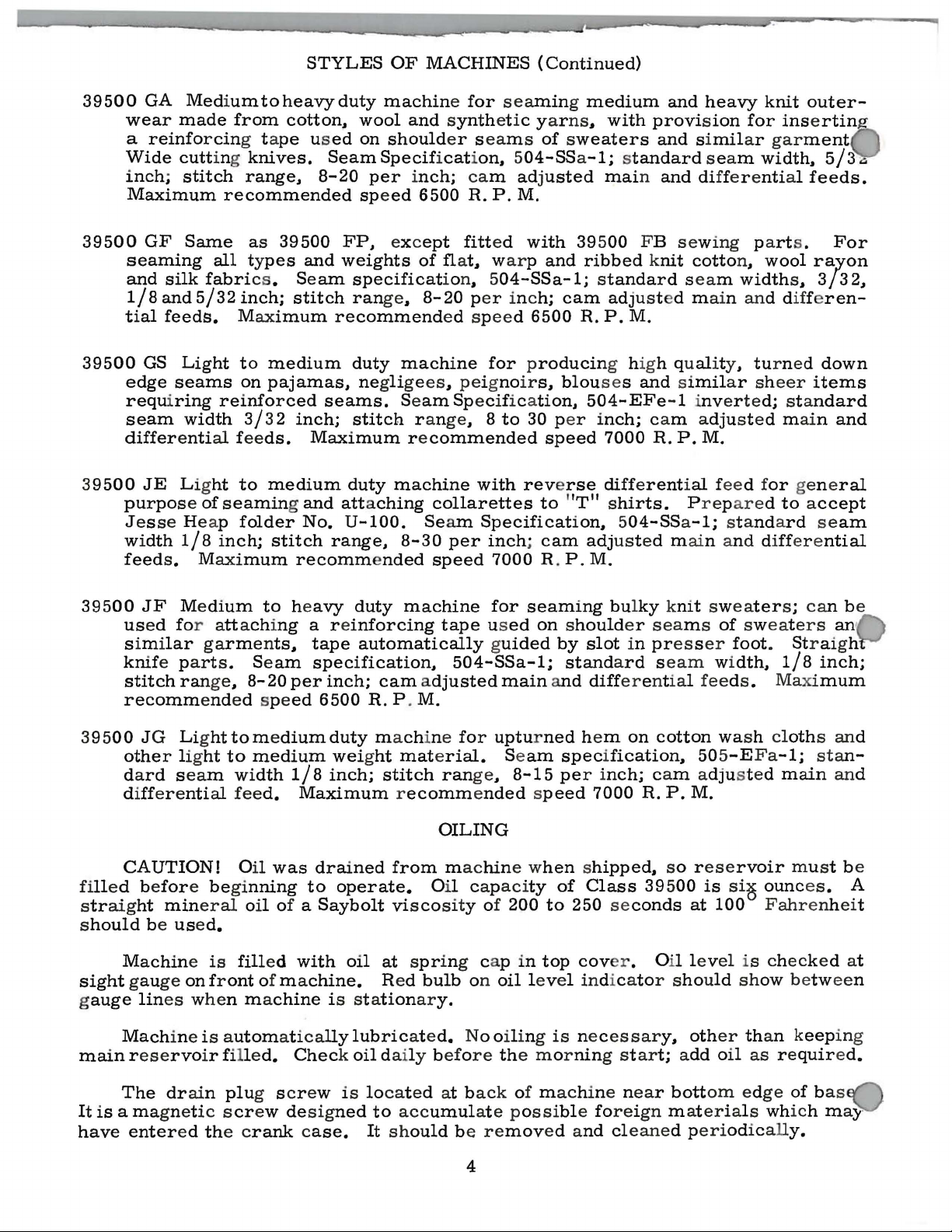
STYLES
OF
MACHINES
(Continued)
39500
GA
wear
a
Wide
i
nch; stitch
Maximum
39500
GF
seaming
and
1/8
tial
39500
GS
edge
requiring rei
seam
differenti
3
9500
JE Lig
purpo
J es
wi
dth
feed
Mediumtoheavyduty
made
reinforcin
cutt
ing
from
g ta
knives.
range,
recommended
Same
as
all types
silk
fabri
cs.
and
5/32
inch;
feeds.
Light
seams
Maximum
to
medium
on
pajamas,
nforced
width 3/3 2
al fee
ht
se
of seaming and
ds.
to
medium
se Heap folder
1/8 inch;
s. M
axi
stitch
mum
cotton,
pe used
wool
on
Seam
8-20
per inch; cam adj
speed
39500
stitch
and
Seam
FP,
weights
specification, 504-SSa-1; standard seam width
range,
recommend
duty
negligees, peignoirs,
seams.
inch;
stitch
Maximum
duty
attaching
No.
U-100.
range,
recommended
mach
ine
and synth
should
for
seaming
et ic y arns,
er seam s
medium
with
of sweaters
and
provision
and simil
Specification, 504-SSa-1; standard
6500
ex c
ept fitt
of
fl a
8-20
ed speed
machine
Se
am Specifi ca
r ange, 8
r e
commended
machine
collarettes
Se
am
8-30
per
speed
usted
R.
P.M.
ed
with
t, warp and
per in ch;
6500
for producin
tion,
to
30 per i
speed
with
reverse
to "T" shirts.
Specification, 504-SSa-1;
inch; cam
7000
R.
main and differ e
39500 FB sew
ribbed knit
cam adjust ed main and diffe
R.
P.
M.
g high quality, turned
blouses
504-EFe
and simil
- 1 inverted; st a
nch;
cam adjust ed main
7000
R.
P.
differential fee
adjusted main and differ e
P.
M.
heavy
knit
for
ar
s eam
width,
nti
ing part
cotto
n,
wool
ar sh
M.
d f
Prepared
standa
outer-
insertin
gar
ment
5/3
al
feeds.
s.
ra~:on
s,
3j32,
ren-
down
eer
items
ndard
or
gene
to accept
rd
se
ntial
,a
.:.
For
and
ral
am
395
00
JF
Medi
us
ed for attachi
s imilar garments,
knif
e parts. Se
stitch
range,
recommend
395
00
JG Lig
other lig
da
rd seam
ff
er e
di
nti
CAUTION! Oil
filled be
tr
aig
s
s
hould
sight gau
g
auge
main rese
fore beginning
ht
min
eral oil
be use
Mach
Mach
ge
lin
ine i s
on front
es whe
ine is a
rvo
um
to heavy
ng
a r e
tape
am
specification,
8-20
per
inch;
ed spe
ed
6500
httomediumduty
ht
to
medium
al
width
fee
1/8
inch;
d.
Maximum recommended speed
was
drained
to
of a
Saybolt viscosit
d.
fill
ed
with
n m a
utomatica
ir f
ille
of m a
chine.
chine
is st a
lly
d.
Check oil daily before the m or
duty
inforcing
machine
tape used
automatically guided
504-SSa-1;
cam adjusted
R. P .
weight
M.
m achine
material.
stitch
range,
for
OILING
from mac
operate.
O
il
hin
cap
y of 200
oil
at spr
Red
ing cap in
bulb
on
tionary.
lubric
at e
d.
No o
for
seaming bul
on should
by
er
slot
standard seam
main and
upturned
Se
am
8-15 per i
differential
hem
specification,
nch;
7000
e w
hen
shi
pped,
aci
ty
of
Class
to
250 seconds
top
cover. O
oil
level indicator shou
ili
ng is nec
essar
nin
g start; add oil
ky
knit sweater
sea
m s
of sweaters
in presser
foot
wi
fee
ds .
on
cotton wash cloths an
505-EFa
cam adjusted
R.
P.M.
so r
ese
39500
il
at
lev
is
100
sia
el
s;
. Str aigh
dth,
1/8
Maxi
-1;
main and
rvoir
ounces. A
Fahrenheit
is chec
ld show between
y,
oth
er than k
as
r e
can
be
an
inch;
mum
stan
must be
ked at
eep
ing
quired.
d
-
The drain plu
It
is a magnet
have
enter
ic scr
ed the c
g s cr ew
ew desig
ned
rank case.
is loca
to
It should
ted at b
acc
umul
ack
of machine near
at e po
be remov
ssible foreign
ed a
4
nd cleane
bott
om edge
of bas
m aterials whic
d p
eriodic
all
y.
h m
ay
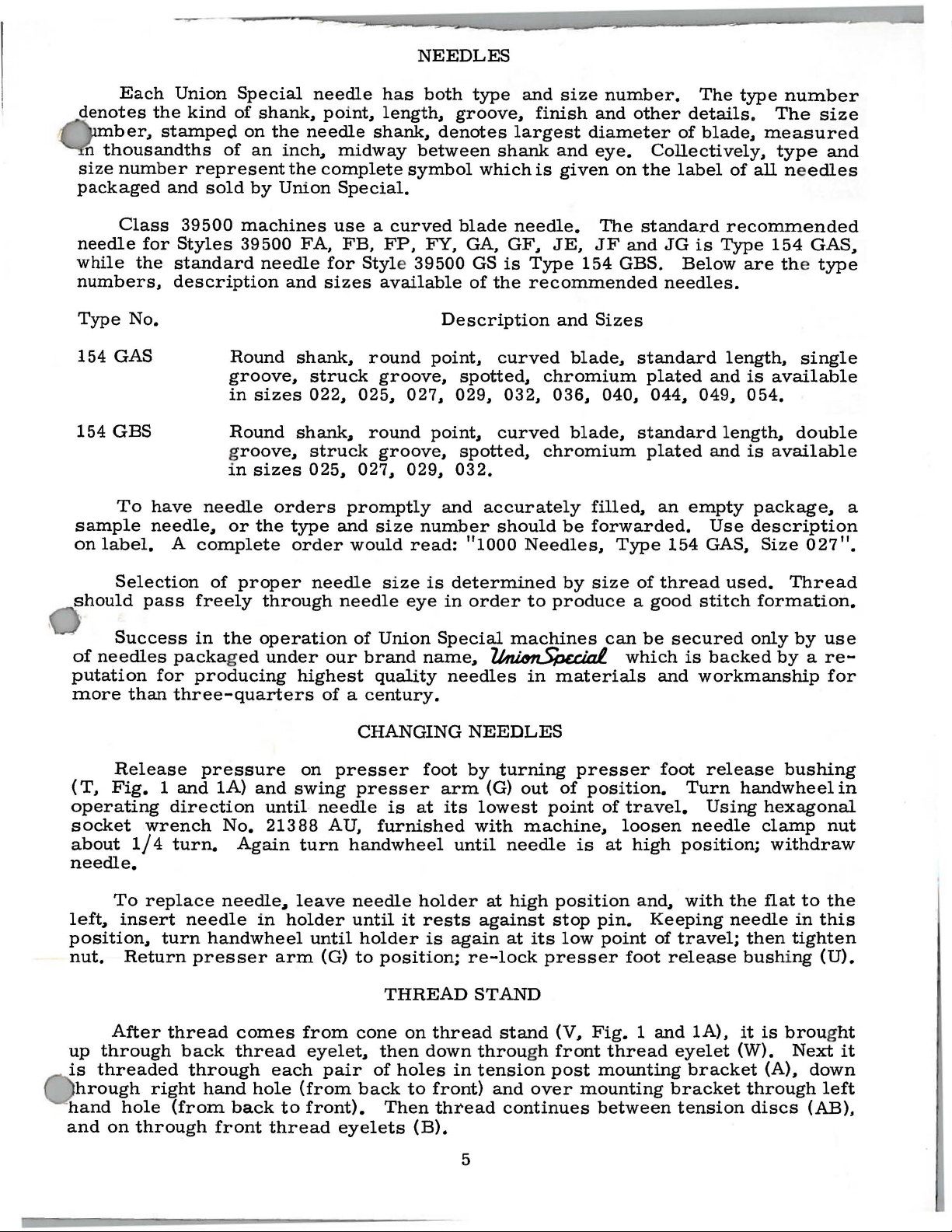
NEEDLES
Each
denotes
mber,
n
thousandths
size
number
packaged
Class
needle
while
numbers,
Type
154 GAS
154
sample
on
the
No.
GBS
To
label.
Union
the
kind
stamped
represent
and
39500
for
Styles
standard
description
have
needle,
A
complete
Special
of
on
of
sold
machines
39500
Round
groove,
in
Round
g
roove,
in
needle
or
shank,
the
an
inch,
by
Union
needle
and
sizes
sizes
orders
the
needle
point,
needle
the
complete
use a curved
FA,
for
sizes
shank,
struck
022, 025, 027, 029, 032, 036,
shank,
struck
025,
type
order
has
length,
shank,
midway
symbol
Special.
FB,
FP,
Style 39500
available
round
groove,
round
groove,
027,
promptly
and
would
029,
size
both
groove,
denotes
between
blade
FY,
Description
point,
spotted,
point,
spotted,
032.
and
number
read:
type
GA,
GS
of
"1000
and
largest
shank
which
needle.
GF,
is
the
curved
curved
accurately
should
Needles,
finish
is
Type
recommended
size
number.
and
diameter
and
eye.
given
JE,
and
chromium
chromium
be
on
The
JF
154
Sizes
blade,
040,
blade,
filled,
forwarded.
Type
other
of
Collectively,
the
label
standard
and
JG
GBS.
Below
needles.
standard
plated
044,
standard
plated
an
154
The
type
details.
blade,
of
all needles
recommended
is
Type
are the
length,
and
is
049,
empty
length
and
Use
GAS,
054.
is
package,
description
number
The
size
measured
type
154
GAS
type
single
available
..
double
available
Size
027".
and
..
a
Selection
should
Success
of
needles
putation
more
(T,
operating
socket
about
needle.
left,
position,
nut.
up
is
hrough
hand
and
than
Release
Fig. 1 and
1/4
To
insert
Return
After
through
threaded
hole
on
pass
wrench
replace
through
freely
in
packaged
for
producing
three-quarters
pressure
direction
turn.
needle
turn
presser
thread
back
through
right
hand
(from
of
proper
through
the
operation
under
1A)
and
until
No.
21388
Again
needle,
in
holder
handwheel
arm
comes
thread
each
hole
back
front
to
thread
needle
needle
of
our
brand
highest
of a century.
CHANGING
on
presser
swing
turn
leave
from
eyelet,
(from
front).
needle
AU,
handwheel
needle
until
until
(G)
pair
eyelets
presser
holder
to
cone
back
size
is
eye
Union
quality
is
furnished
position;
THREAD
then
of
Then
name,
foot
at
holder
it
rests
is
on
thread
down
holes
to
(B).
Special
front)
thread
determined
in
order
machines
~
needles
NEEDLES
by
turning
arm
(G)
its
lowest
with
until
again
in
needle
at
high
against
at
re-lock
STAND
stand
throu
tension
and
continues
by
size
to
produce a good
can
in
materials
presser
out
of
position.
point
machine,
stop
its
presser
gh
post
over
of
is
at
position
pin.
low
point
(V,
Fig. 1 and
front
thread
mounting
mounting
between
of
thread
be
which
and
foot
travel.
loosen
high
and,
Keeping
of
foot
used.
stitch
secured
is
backed
workmanship
release
Turn
Using
needle
position;
with
the
needle
travel;
release
1A),
eyelet
bracket
bracket
tension
(W).
Thread
formation.
only
by
by a re-
bushing
handwheel
hexagonal
clamp
withdraw
flat
to
in
this
then
tighten
bushing
it
is
(A),
through
discs
(U).
brought
Next
down
(AB),
use
for
in
nut
the
it
left
5
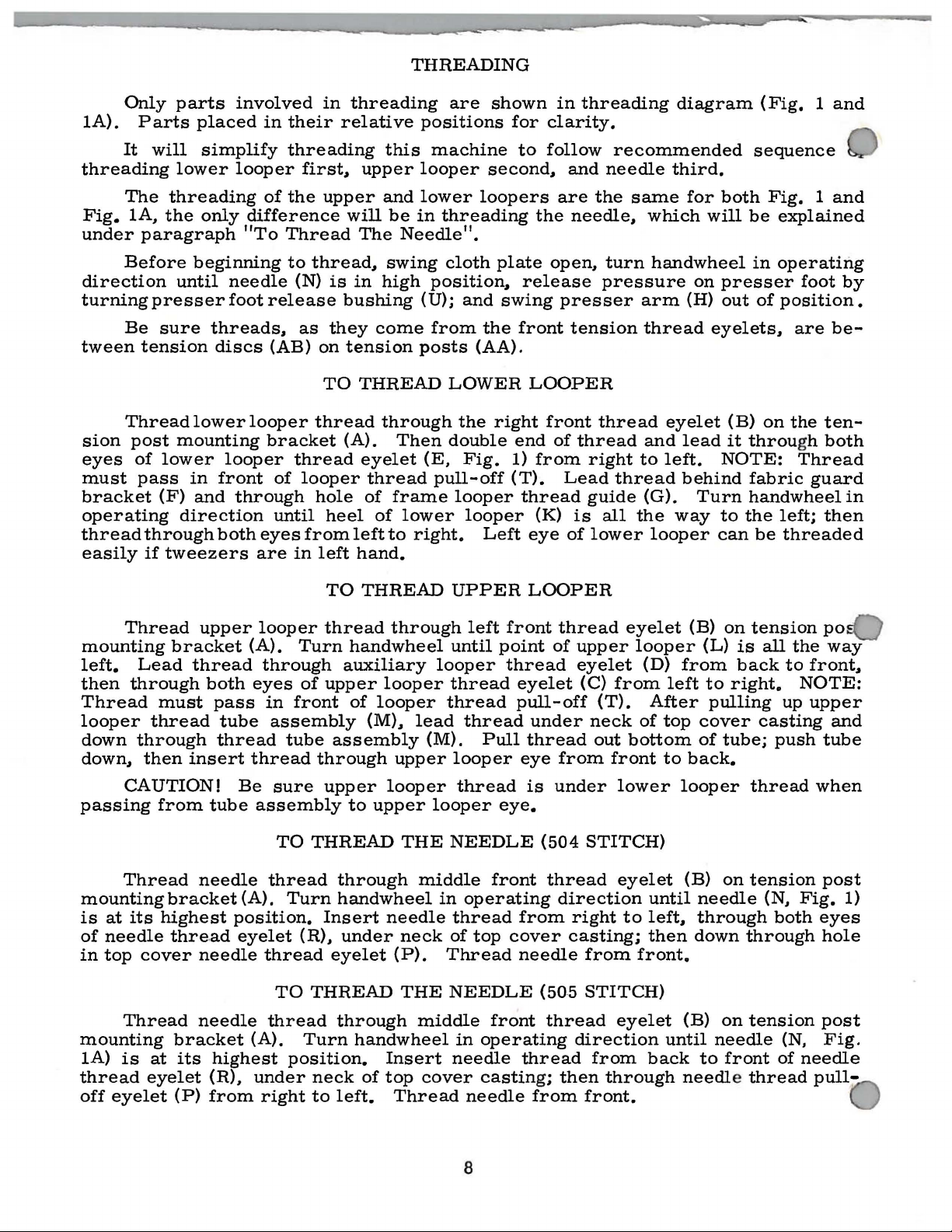
THREADING
Only
1A).
threading
Fig.
under
direction
turning
tween
sion
eyes
must
bracket
operating
thread
easily
Parts
It
The
1A,
paragraph
Before
Be
tension
Thread
post
of
pass
through
if
parts
placed
will
presser
simplify
lower
threading
the
only
beginning
until
sure
lower
mounting
lower
in
(F)
and
direction
tweezers
involved
in
looper
of
difference
"To
needle
foot
release
threads.,
discs
front
both
(AB)
looper
bracket
looper
through
until
eyes
are
in
their
threading
first,
the
upper
Thread
to
thread,
(N)
is
as
they
on
TO
thread
thread
of
looper
hole
heel
from
in
left
threading
relative
this
upper
and
will
be
The
swing
in
high
bushing
come
tension
THREAD
through
(A).
eyelet
thread
of
of
left
hand.
Then
frame
to
are
positions
machine
looper
lower
in
threading
Needle".
cloth
position,
(U);
and
from
posts
LOWER
the
double
(E,
Fig.
pull-off
looper
lower
right.
shown
second,
loopers
plate
swing
the
(AA).
right
looper
Left
in
for
clarity.
to
follow
are
the
open,
release
presser
front
LOOPER
front
end
of
1)
from
(T).
thread
(K)
eye
threading
recommended
and
needle
the
needle,
turn
pressure
tension
thread
thread
right
Lead
of
guide
is
lower
thread
all
diagram
third.
same
to
the
for
which
handwheel
arm
(H)
thread
eyelet
and
lead
left.
behind
(G).
way
looper
both
will
on
presser
out
eyelets,
(B)
it
NOTE:
Turn
to
can
(Fig. 1 and
sequence
Fig. 1 and
be
explained
in
operating
foot
of
position.
are
on
the
ten-
throu
fabric
handwheel
the
left;
be
threaded
gh
both
Thread
guard
then
by
be-
in
Thread
mounting
left.
then
Thread
looper
down
down,
passing
mounting
is
of
in
mounting
1A)
thread
off
Lead
through
through
then
CAUTION!
Thread
at
its
needle
top
cover
Thread
is
eyelet
eyelet
bracket
thread
must
thread
insert
from
bracket
highest
thread
bracket
at
its
(P)
upper
both
pass
tube
thread
Be
tube
needle
(A).
position.
eyelet
needle
needle
highest
(R),
from
looper
(A).
thread
(A).
Turn
through
eyes
under
of
in
front
assembly
tube
sure
assembly
TO
thread
Turn
(R),
thread
TO
thread
Turn
position.
right
TO
THREAD
thread
handwheel
auxiliary
upper
of
looper
(M),
assembly
through
upper
to
upper
THREAD
through
handwheel
Insert
under
eyelet
THREAD
through
handwheel
neck
to
of
left.
through
looper
lead
(M).
upper
looper
looper
THE
middle
needle
neck
(P).
THE
middle
Insert
top
cover
Thread
UPPER
left
until
looper
thread
thread
thread
Pull
looper
thread
NEEDLE
front
in
operating
thread
of
top
Thread
NEEDLE
front
in
operating
needle
casting;
needle
LOOPER
front
point
thread
eyelet
pull-off
under
thread
eye
is
eye.
from
cover
needle
thread
from
thread
of
upper
eyelet
(C)
from
under
(504
STITCH)
thread
direction
right
casting;
from
(50-5
STITCH)
thread
direction
then
front.
eyelet
from
(T).
neck
out
bottom
front
lower
eyelet
to
eyelet
from
through
looper
(D)
left
After
of
top
to
until
left,
then
front.
until
back
(B)
on
tension
(L)
is
all
from
back.
looper
(B)
(B)
needle thread
back
to
right.
pulling
cover
of
tube;
thread
on
tension
needle
through
down
to
through
on
tension
needle
front
to
up
casting
push
(N,
both
(N,
of
po
the
way
front,
NOTE:
upper
and
tube
when
post
Fig.
eyes
hole
post
Fig.
needle
pull-
1)
8
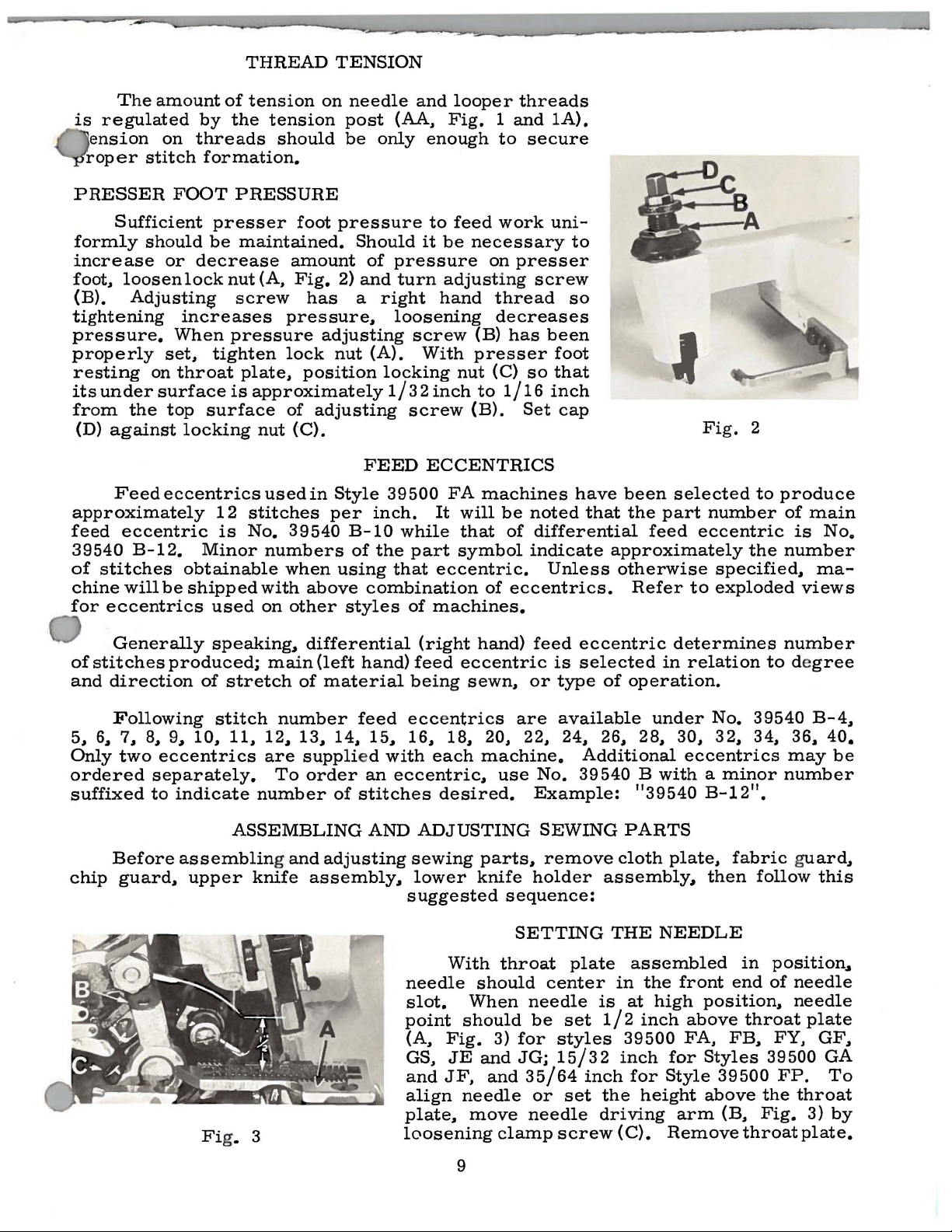
is
regulated
ension
roper
The
amount
on
stitch
THREAD
of
tension
by
the
threads
formation.
tension
should
TENSION
on
needle
post
be
only
and
(AA~
Fig. 1 and
enough
looper
threads
to
secure
1A).
PRESSER
Sufficient
formly
increase
foot~
(B).
tightening
pressure.
properly
resting
its
from
(D)
approximately
feed
39540
of
chine
for
of
and
loosen
under
against
Feed
eccentric
stitches
will
eccentrics
Generally
stitches
direction
FOOT
should
or
Adjusting
When
set,
on
surface
the
top
eccentrics
B-12.
be
produced;
PRESSURE
presser
be
maintained.
decrease
lock
nut
screw
increases
pressure
tighten
throat
locking
obtainable
shipped
plate,
is
surface
12
is
Minor
used
speaking,
of
stretch
foot
pressure
amount
(A,
Fig.
2)
has
pressure~
adjusting
lock
approximately
of
nut
used
stitches
No.
numbers
when
with
on
main
nut
position
adjusting
(C).
in
Style
per
39540
other
of
B-10
using
above
styles
differential
(left
material
to
Should
of
and
a
(A).
FEED
inch.
of
the
combination
hand)
it
pressure
turn
right
loosening
screw
With
locking
1/3 2 inch
screw
ECCENTRICS
39500
while
part
that
of
(right
feed
being
feed
work
be
necessary
on
adjusting
hand
It
eccentric.
machines.
thread
decreases
(B)
presser
nut
(C)
to
(B).
FA
machines
will
that
symbol
of
hand)
eccentric
sewn,
1/16
be
uni-
to
presser
screw
so
has
been
foot
so
that
inch
Set
cap
have
noted
of
differential
indicate
Unless
eccentrics.
feed
or
eccentric
is
selected
type
been
that
the
part
feed
approximately
otherwise
Refer
in
of
operation.
I
Fig.
selected
eccentric
to
determines
relation
2
number
the
specified~
exploded
to
produce
of
main
is
number
ma-
views
number
to degree
No.
Following
5~
6,
7,
Only
ordered
suffixed
chip
two
Before
guard..
stitch
8,
9,
10,
11,
eccentrics
separately.
to
indicate
ASSEMBLING
assembling and
upper
Fi
g. 3
number
12, 13,
are
To
number
knife
feed
14,
suppli
order
assembly,
ed
an
of
stitches
adjusting
15,
with
eccentric
AND
needle
slot.
point
(A,
GS~
and
align
plate,
loosening
eccentrics
16,
18,
20,
each
ADJUSTING
sewing
lower
suggested
machine.
..
desired.
parts,
knife
With
should
When
should
Fig.
JF,
JE
needle
move
9
3)
and
and
are
available
22, 24,
use
No.
Example:
SEWING
remove
holder
sequence:
SETTING
throat
center
needle
be
for
styles
JG;
15/32
35/64
or
needle
clamp
screw
under
26,
28,
Additional
39540 B with a minor
"39540
PARTS
cloth
assembly,
plate
set
inch
set
THE
is
1/2
the
driving
NEEDLE
assembled
in
the
at
high
inch
39500
inch
for
height
(C).
No.
30,
32,
eccentrics
B-12".
plate,
then
front
position,
above
FA,
for
Styles
Style
Remove
39500
above
arm
FB~
(B,
39540
34,
fabric
follow
in
position-a
end
of
throat
39500
the
Fig.
throat
B-4,
36
..
may
number
gu
needle
needle
plate
FY,
FP.
throat
3)
plate.
40.
be
ard,
this
GF~
GA
To
by
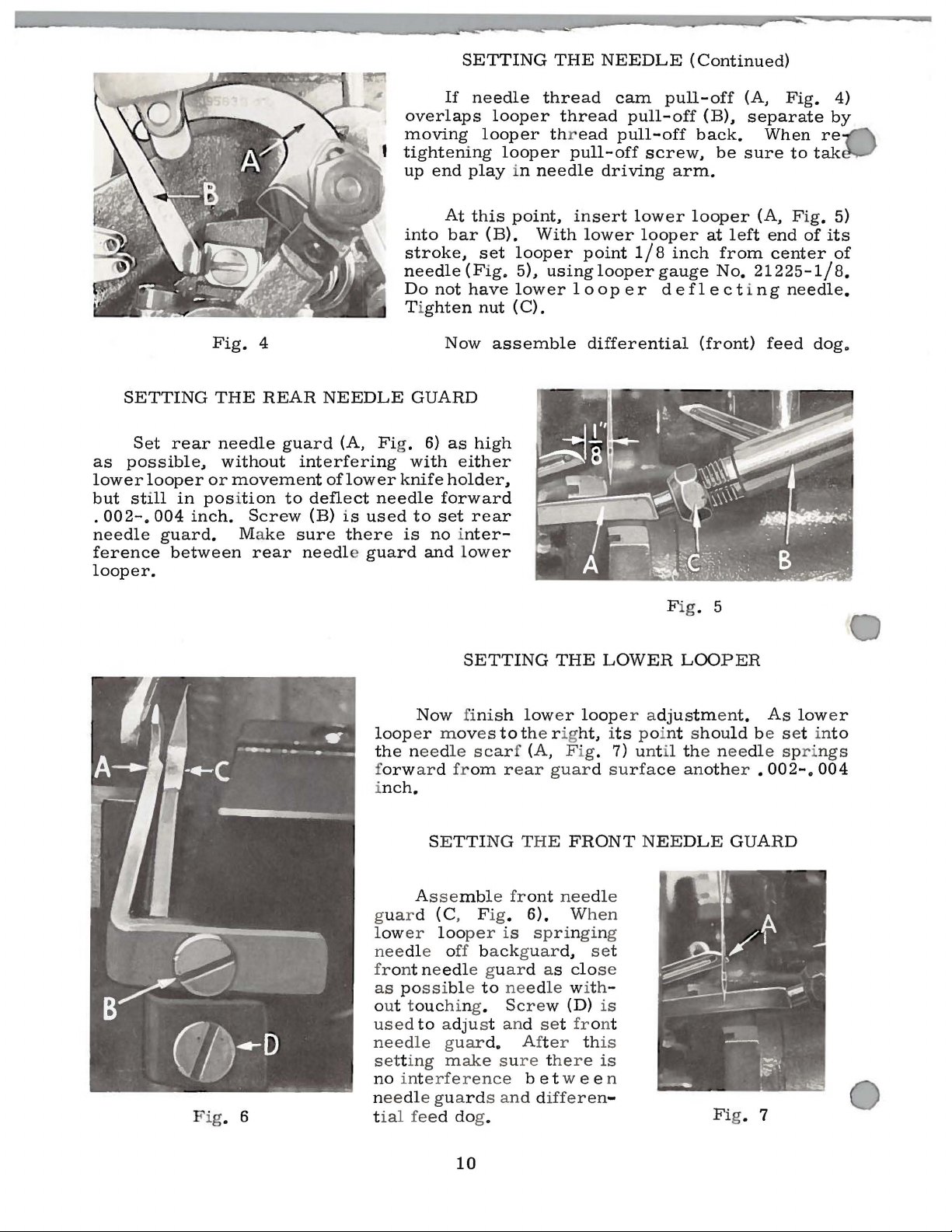
Fig.
4
SETTING
If
needle
overlaps
moving
tightening
up
end
play
At
this
into
bar
stroke,
needle
Do
Ti
not
ghten
(Fig.
have
Now
looper
looper
looper
in
point,
(B).
set
looper
5),
lower
nut
(C).
assemble
THE
thread
thread
thread
pull-off
needle
insert
With
using
1 o
NEEDLE
cam
pull-off
pull-off
screw,
driving
lower
lower
point
looper
1/8
looper
ope
r
differential
(Continued)
pull-off
(B),
back.
arm.
looper
at
inch
gauge
deflect
(front)
be
left
from
No.
(A,
separate
sure
i
Fig.
by
When
(A, Fi
end
to
g.
of
re
tak
its
center
21225-1/8.
ng
needle.
feed
dog.
4)
5)
of
SETTING
Set
as
possible~
lower
but
.
needle
still
002-.
looper
004
guard.
ference
looper.
THE
rear
needle
without
or
in
position
inch.
between
REAR
guard
interfering
movement
to
Screw
Ma
ke
sure
rear
needle guard
NEEDLE
(A,
oflower
deflect
(B)
is
there
GUARD
Fi
g. 6)
knife
needle
used
with
to
is
no inter-
as
high
either
holder,
forward
set
rear
and lower
SETTING
loop
Now
er moves
fini
the needle scar
f
orward fr
i
nch.
om
SETTING
sh
low
THE
er
LOWER
loope
to the right. its
f
(A,
Fig .
r e ar
guard su
THE
FRONT
r a
poi
7)
unt
r f
ace anoth
NEEDLE
Fig. 5
LOOPER
djustment.
nt should
il the needl
er • 002-.004
GUARD
As
low
er
be set into
e springs
As s e
Fig. 6
mble fr
gua r d ( C, F
lower
n
eedle off backguard,
fr ont ne
loo
per
edl
e guard as
as possible to need
out t
ouc
hing.
used
to adju
need
le g
setting
no
int erfer
eedle gu ards and d
n
tia
l feed dog.
st and set front
uar
make sure the
ence
ont
needle
ig
.
6).
is
sp
r inging
le
Screw (D) is
d.
Aft er
bet
w
iffe
10
W
hen
se
clo
se
wit h-
th
r e
ee
ren-
is
is
n
t
Fi
g. 7
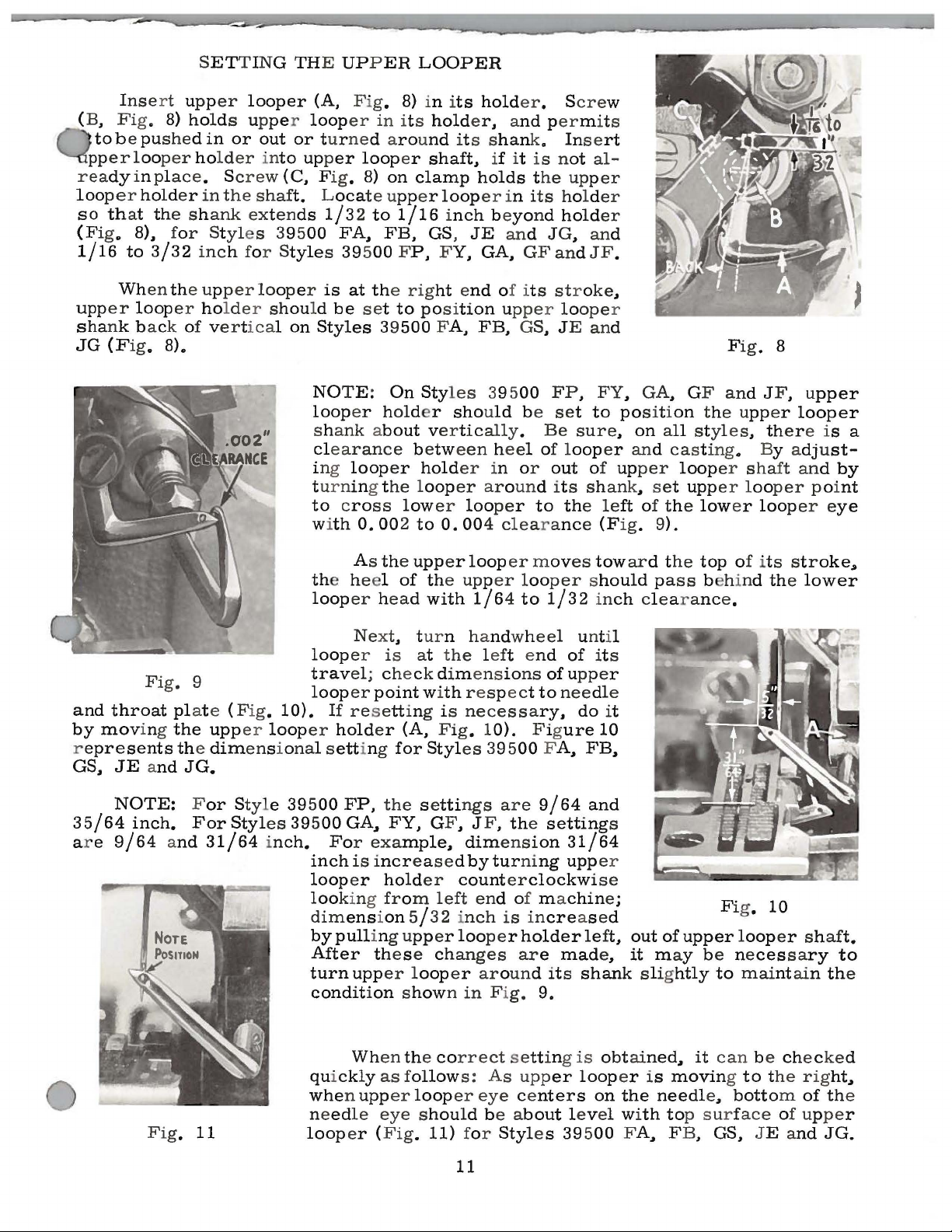
SETTING
I
nse
rt upp
(B, Fig.
to
b e pushed in
pp
er
rea
dy
loo
per holder
8) holds upper
loo
per holder into upp
in pl
so that the sh
er
or
ace
. S
in
the
ank extends
looper
out
crew
shaf
(C, Fig. 8)
(Fig. 8), for Styles 395
1/16
upp
sha
JG {Fig
to
Wh
er
3/32
en the up
loop
inc
h for S
per looper
er holder s
nk back of vert
. 8).
hou
ical on
THE UPPER
(A, Fig.
loop
er
or
turned arou
er
in
loop
8)
it s
er
on
t. Loca
00
tyle
ld
te upp
1/32 to
FA,
s 395
is
00 FP,
at the
be set
1/16 inch beyo
FB,
to posi
Styles 39500 FA,
NO
TE :
loop
sh
ank about ver
cl
earance
i
ng
t
urning t
to cro
wi
th
On
er holder
loop
er
he loop
ss
low
0. 002
LOOPER
in i
ts
holder. S
holder. and per
nd
it s s
han
shaft.
clamp
er
loop
GS,
F Y,
rig
ht end
if it
holds the upp
er
in i
JE
an
GA.
of its str oke,
tion uppe
FB,
Sty
les
39 5
should
ti c
ally. Be
between hee
hold
er
in or
er around its shank, set
er
looper
to
0. 004
clea
cre
w
m its
k.
Insert
is not
al-
er
ts
hol d
er
nd
hold
er
d J G, and
GF and JF.
r l o
ope
GS, J E and
00
FP, FY, GA
be set
to positi
sure. on all
l of l
oop
out
er and
of upper
to the le
r ance (Fig. 9
r
ft of t he
).
Fi
g. 8
, GF and J F , u
on
the upper
looper
styles. ther e is a
casting
loop
upp
. By adju
er
er loo
low
er
shaft and
per
loop
er eye
pper
st-
p oi
by
nt
Fig.
and
throat plat e (Fig.
by
mov
ing
the
r
epresents the
GS,
JE and
JG.
NOTE: For Styl
35/64
a r e
inch.
9/64 and
9
10).
upp
er
loop
dimensi onal s
e 39 5
For
Styl
es
31/64 inch.
er
39 5
th
loop
loop
trav
loop
00
00
inch
loop
loo
dim
by
After
turn
As the
e heel
er head with
Next
er
el; check dim
er
If
re
hold
ett
ing
FP,
GA,
For exa
is increased by
er
king from
ension 5/32 inch
pull
upp
upp
er
of the upp
, turn
is
at
the lef
point with
s etting is
er
(A,
Fig. 1
for
Styl
the
s e
tti
FY,
GF , J F, the
mple,
hold
er
left end of m a
ing upper
th
es e changes
er loop
loop
1/64 to
handwheel unt
ensions
respect to
necessa
es
ngs
dim
counterclockwi
looper
er around its
condition shown in Fig.
er mov
er loo
t e
nd
ry.
0).
F ig
395
00 FA,
are
9/64
ensi
on
turning
is incre
holder
are mad
9.
es
toward t
per should pass
he
top
behind the
1/32 inch clear ance.
il
of
it s
of
upper
needle
do
it
ure
10
FB,
and
setting
s
31/64
upp
er
se
chin
e; F
as ed ig .
left,
shank slightly
e,
out
of
upper loop
it
m ay b e ne
to
of it s
str
lower
10
er shaft.
cessary
m aintain th
oke~
to
e
Wh
Fig. 11
quickly
when upp
ed
le
ne
loop
er (
en the correct sett
as follow
er
loop
eye should
Fig. 11)
s:
As
er
eye centers
be a
for
Styl
ing
upp
er
bout
e s 395
11
is
obtained,
loop
er is
on
the
level wi
00 FA,
it
can
moving to the
needl
th top
e,
surface
F B, GS. J E a
be checked
rig
ht,
bottom of the
of upper
nd
JG.
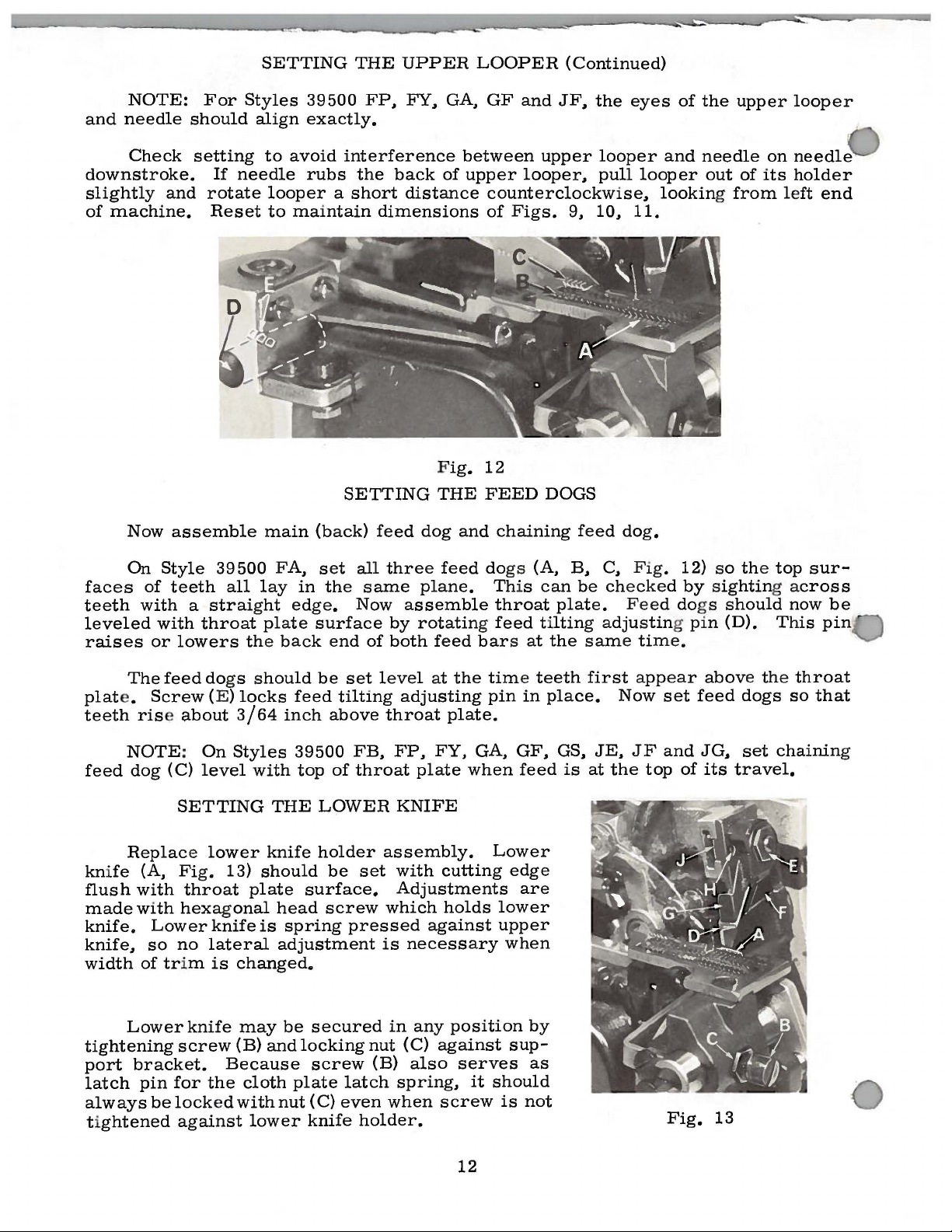
SETTING
THE
UPPER
LOOPER
(Continued)
NOTE:
and
needle
Check
downstroke.
slightly
of
machine.
Now
and
assemble
For
should
setting
If
rotate
Reset
Styles
align
needle
39500
exactly.
to
avoid
rubs
looper a short
to
maintain
main
(back)
FP,
FY,
interference
the
back
distance
dimensions
SETTING
feed
dog
GA
between
of
upper
Fig.
THE
and
..
GF
and
JF,
upper
looper,
counterclockwise,
of
Figs.
12
FEED
chaining
9,
DOGS
feed
the
eyes
looper
pull
10,
11.
dog.
of
and
looper
looking
the
upper
needle
out
of
from
on
its
looper
needle
holder
left
end
On
faces
teeth
leveled
raises
The
plat
e.
teeth
NOTE:
feed
dog
Replace
knife
flush
made
knife.
knife,
width
Style
of
with a straight
with
or
feed
Screw
rise
(C)
(A,
with
with
Lower
so
of trim
39500
teeth
lowers
SETTING
Fig.
hexagonal
no
throat
dogs
(E)
about
On
level
lower
throat
knife
lateral
is
all
Styles
13)
the
locks
3/64
with
plate
changed.
FA,
lay
in
edge.
plate
back
should
feed
inch
39500
top
THE
knife
should
surface.
head
is
spring
adjustment
set
all
the
same
Now
surface
end
of
be
set
tilting
above
FB,
of
throat
LOWER
holder
be
set
screw
pressed
three
by
both
level
throat
FP,
assembly.
which
is
feed
plane.
assemble
rotating
feed
at
adjusting
plate.
FY,
plate
KNIFE
with
cutting
Adjustments
holds
against
necessary
the
when
dogs
This
throat
feed
bars
time
pin
GA,
Lower
lower
upper
(A,
tilting
at
teeth
in
GF,
feed
edge
are
when
B,
can
plate.
the
place.
GS,
is
c
..
Fig.
be
checked
Feed dogs
adjusting pin
same
first
at
JE,
the
time.
appear
Now
JF
top
12)
by
set
and
of
so
the
top
sighting across
should
(D).
above
feed
JG,
its
dogs
travel.
the
set
now
This
throat
so
chaining
sur-
be
pin
that
Lower
tightening
port
latch
always
ti
ghtened
bracket.
pin
be
knife
screw
for
the
locked
against
may
(B)
and
Because
cloth
with
nut
lower
be
secured
locking
screw
plate
(C)
knife
nut
latch
even
holder.
in
(B)
when
any
(C)
against
also
spring,
screw
position
serves
it
should
is
12
by
sup-
as
not
Fig.
13