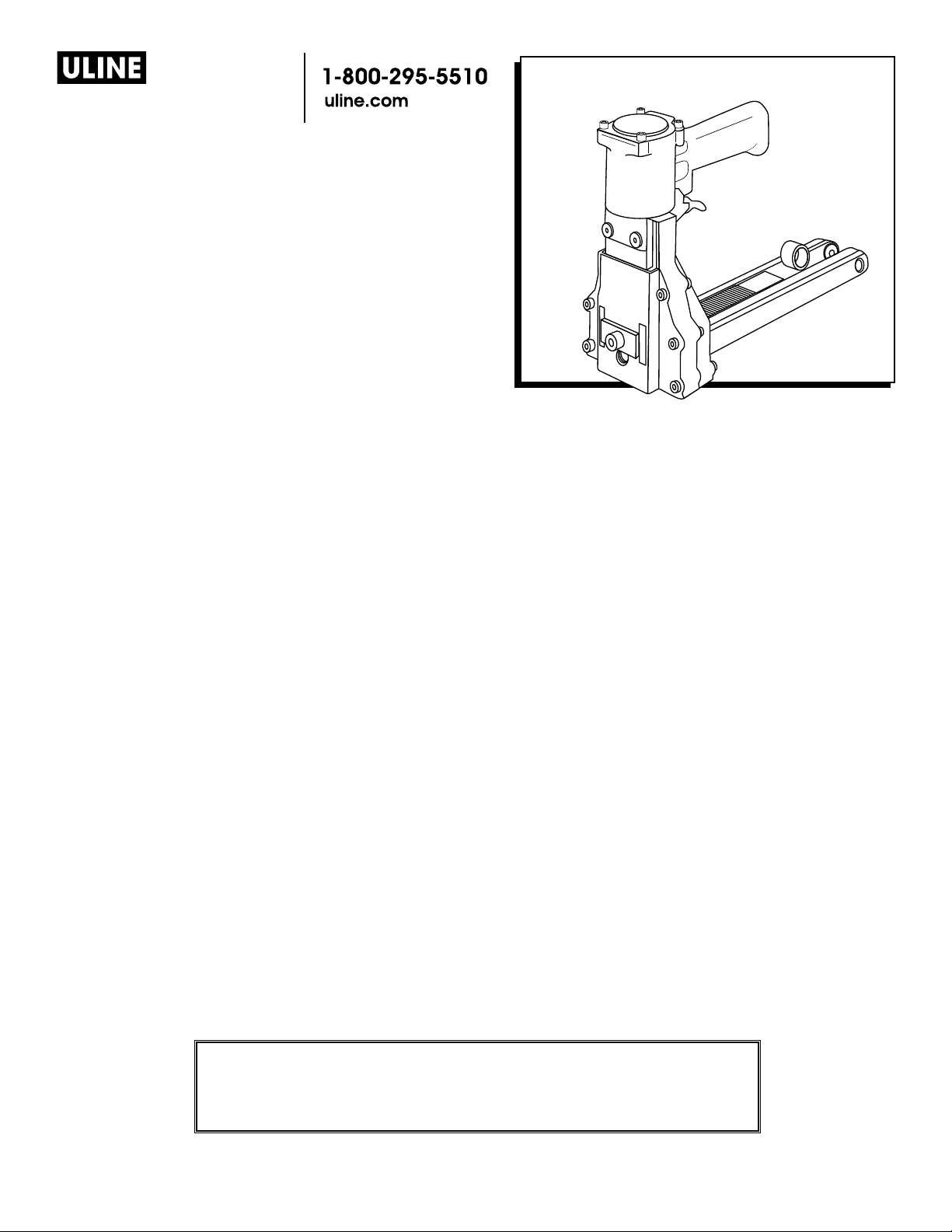
H-1027, H-1028
H-3064
PNEUMATIC STICK
STAPLER
STAPLER SPECIFICATIONS
Dimensions: L x H x W 13.5 x 8.75 x 6"
Weight (Without Fasteners) 6 lb.
Compressed Air:
Ma ximum psi: 110 psi
Recommended
O perating Pressu re: 71–100 psi
A ir Consumption: 2.4 CFM
Staple Specification: S-1397 A58 Stick
Staple Specification: S-1396 C34 Stick
Staple Specification: S-289 C58 Stick
Staple Capacity: 100 Staples
Noise Levels: 89 dBa
WARNING
Before operating this stapler familiarize yourself with the safety
warnings and instructions in this manual. Keep these instructions with
the stapler for future reference. If you have any questions, contact
Uline at 1-800-295-5510.
0513 IH-1027PAGE 1 OF 11
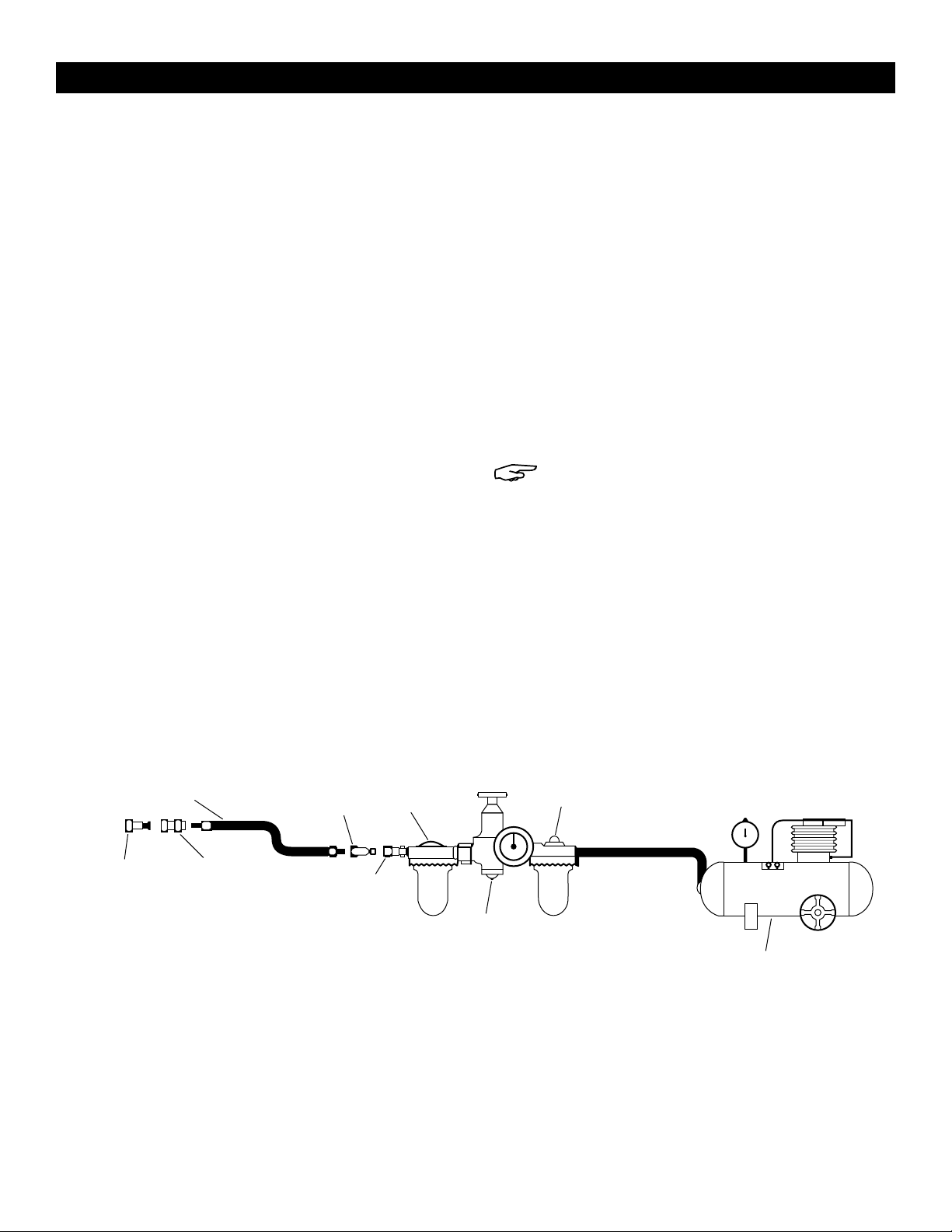
SAFETY INSTRUCTIONS
GENERAL SAFETY
1. Read the manual and understand all safety
instructions before operating the stapler. If you have
questions, contact Uline at 1-800-295-5510.
2. Never use flammable gases as a power source for
the stapler. Only use filtered, compressed air.
3. Never use gasoline or other flammable liquids to
clean the stapler. Vapors left on the stapler could
ignite and cause the stapler to explode.
4. Do not exceed 110psi of air pressure when
operating the stapler.
5. Disconnect the stapler from the air supply before
making adjustments, cleaning or clearing jams and
when not in use.
6. Do not pull the trigger when carrying or holding the
stapler.
7. Never carry the stapler by the hose or pull on the
hose to move the stapler.
8. Always wear protective equipment; i.e., safety
glasses, hearing protection and head protection.
9. Do not use a check valve or any other fitting which
allows air to remain in the stapler.
10. Do not place your hand or any other body part in
the staple clinching area or adjustment window
when connecting or disconnecting the air supply.
LUBRICATION & MAINTENANCE
1. Lubricate the stapler prior to initial operation.
2. Disconnect the stapler from the air supply prior to
servicing.
3. Turn the stapler so that the inlet is facing up and put
one drop of high-speed spindle oil, UNOCOL RX22,
or 3-in-1 oil, into air inlet. Never use detergent oil or
additives.
4. Operate the stapler briefly after adding oil.
5. Wipe off excessive oil at the exhaust. Excessive
oil will damage the O-rings. If inline oiler is used,
manual lubrication through the air inlet is not
required on a daily basis.
AIR SUPPLY AND CONNECTIONS
NOTE: The following illustration shows the
correct mode of connection to the air supply
system which will increase the efficiency and
life of the stapler.
1. Many air stapler users find it convenient to use an
inline oiler to provide oil circulation through their
stapler. Check oil level in the oiler daily.
2. A filter is recommended on your air compressor.
Check the filter and drain on a daily basis.
11. Never point the stapler at yourself or anyone else
Quick
Connector
Air Hose
Quick
Coupler
Connector Oiler
Quick
Coupler
Filter
Regulator
Compressor
0513 IH-1027PAGE 2 OF 11
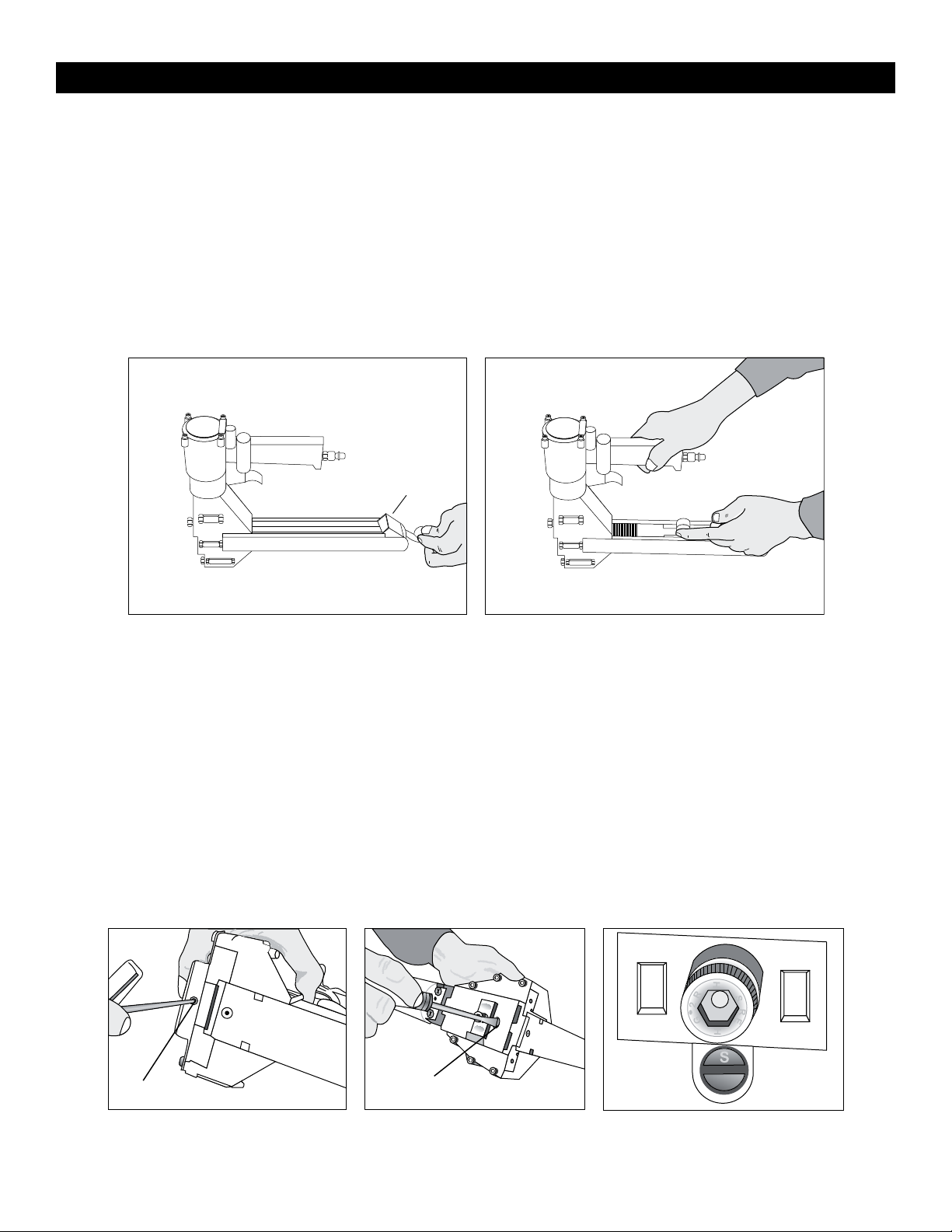
SAFETY INSTRUCTIONS CONTINUED
LOADING THE STAPLER
1. Disconnect the air supply.
2. Pull the pusher back until it stops on pusher pivots.
Rotate pusher to position. (See Figure 1)
3. Insert 2 sticks of appropriate staples into the
magazine. Let the sticks slide forward to the front of
the magazine. (See Figure 2)
Pusher
4. Pull the pusher back to an upright position and
gently let the pusher slide forward against the
staples. Do not let the pusher slide forward and strike
the staples at high speed as this may deform the
staples and damage the stapler.
Figure 1
STAPLE LEG LENGTH
1. Loosen the set screw on the bottom with a 3 mm
Allen wrench. (See Figure 3)
2. Adjust L/S screw with a screwdriver to the desired
setting. (See Figure 4)
a. If you are using ¾" staples set L up.
b. If you are using ⁄" staples set S up.
(See Figure 5)
Set Screw
L /S Screw
Figure 2
3. Tighten the set screw on the bottom.
L
Figure 3 Figure 4 Figure 5
0513 IH-1027PAGE 3 OF 11

SAFETY INSTRUCTIONS CONTINUED
CLINCH ADJUSTMENT
Use 2.5 mm Allen wrench and turn collar through window
clockwise to tighten clinch. (See Figure 6)
Tight
Medium
Loosen
Loose
Figure 6
DEPTH ADJUSTMENT
1. Loosen front screw with a 6 mm Allen wrench.
(See Figure 7)
2. Push the body up and adjust to the desired depth.
(See Figure 8)
Tighten
3. When the top edge of the adjustment plate is at
its highest setting the teeth are at their shallowest
penetration. (See Figure 9)
4. If set at No. 1 the teeth are at their deepest
penetration. (See Figure 10)
Figure 7
Adjustment Plate
Figure 9
Figure 8
No. 1
No. 2 & 3
No. 4
Figure 10
0513 IH-1027PAGE 4 OF 11