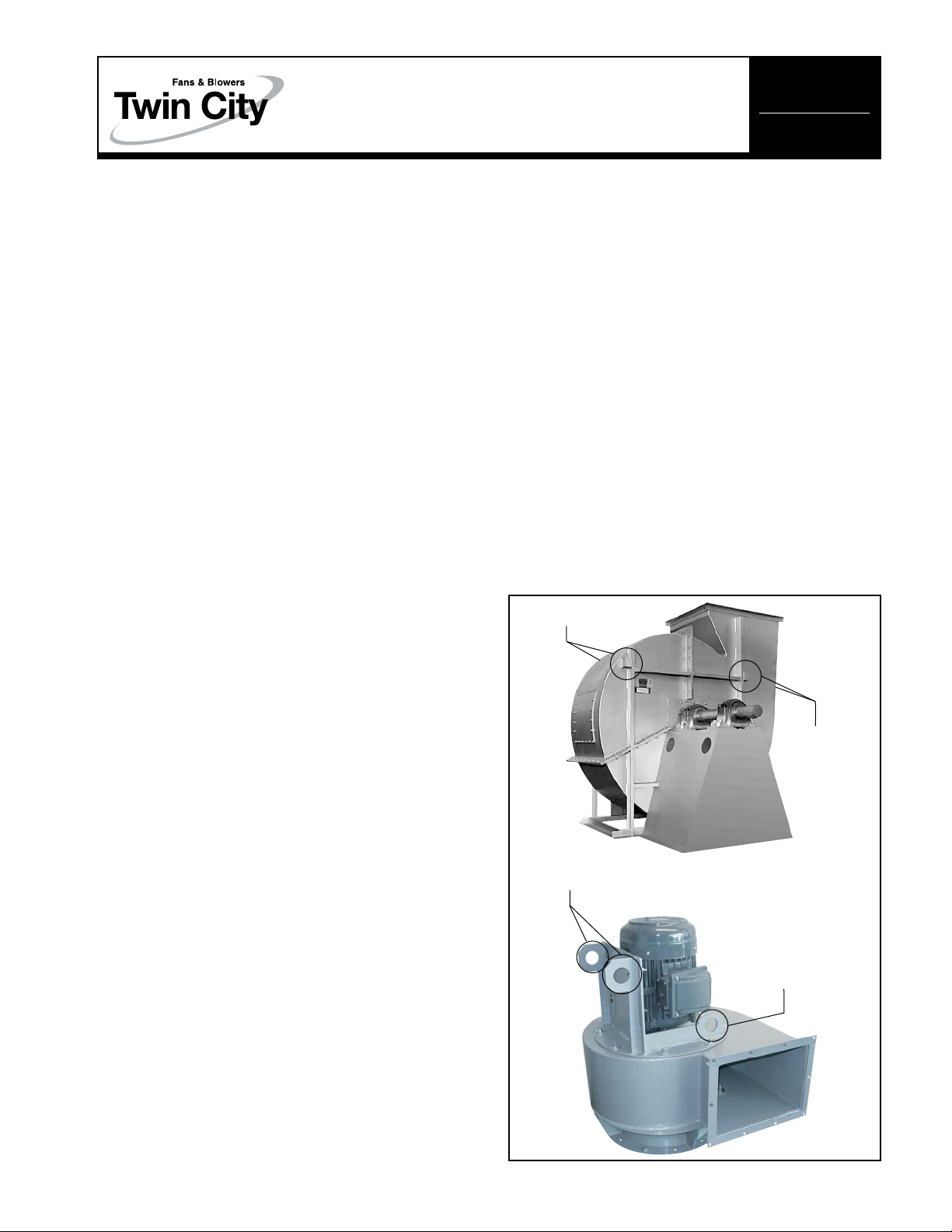
Centrifugal Fans
INSTALLATION, OPERATION & MAINTENANCE MANUAL
ES-52
August 2014
Contents
Introduction .........................................................................1
Shipping and Receiving .....................................................1
Handling .............................................................................. 1
Short Term Storage ...........................................................2
Long Term Storage............................................................2
Foundations and Supporting Structures .......................... 2
Fan Installation ...................................................................2
Factory Assembled Units ............................................. 2
Disassembled Units .......................................................3
Fan Operation – Safety .....................................................4
Operation Checklist ............................................................ 5
Maintenance of Fans ......................................................... 5
General Motor Maintenance ......................................... 5
Drive Maintenance ......................................................... 5
Bearing Maintenance .....................................................5
Lubrication ...................................................................... 6
Wheel and Shaft Maintenance ..................................... 7
Structural Maintenance ................................................. 7
Troubleshooting Guidelines................................................ 7
Troubleshooting Performance Problems
Air Capacity Problems ..................................................7
Noise Problems .............................................................7
Vibration Problems ........................................................ 7
Motor Problems ............................................................. 7
Drive Problems .............................................................. 7
Bearing Problems .......................................................... 8
Limitation of Warranties and Claims ............................... 8
immediately to the carrier and the necessary damage
report filed.
Handling
Handling of all air moving equipment should be conducted by trained personnel and be consistent with safe
handling practices. Verify the lift capacity and operating condition of handling equipment. Maintain handling
equipment to avoid serious personal injury.
Units shipped completely assembled may be lifted with
slings and spreader bars. Use well-padded chains, cables
or nylon straps. On most units, lifting lugs are provided
for attaching chains (see Figure 1). Lift the fan in a fashion that protects the fan and fan coating from damage.
Never lift a fan by the inlet or discharge flange, shafting
or drives, wheel or impeller, motor or motor base, or in
any other manner that may bend or distort parts.
Partial or disassembled units require special handling.
All parts should be handled in a fashion which protects the coatings and parts from damage. Components
should be handled such that forces are not concentrated
and bending or distortion cannot occur.
Figure 1. Lifting Lug Locations
Lifting Lugs
Introduction
The purpose of this manual is to provide instructions
that complement good general practices when installing or operating fans manufactured by Twin City Fan &
Blower. It is the responsibility of the purchaser to provide qualified personnel experienced in the installation,
operation, and maintenance of air moving equipment.
Instructions given in the body of this manual are
general in nature and apply to a variety of models
manufactured by Twin City Fan & Blower. Most units
can be installed and maintained with the instructions
given. Additional product and engineering information is
available at www.tcf.com.
Special applications may require additional information.
These instructions are supplied in the form of attached
appendices. Use the instructions in the appendix if the directions in this manual differ from instructions in the appendix.
As always, follow good safety practices when installing, maintaining and operating your air moving equipment. A variety of safety devices are available. It is
the user’s responsibility to determine adequate safety
measures and to obtain the required safety equipment.
Shipping and Receiving
All Twin City Fan & Blower products are carefully constructed and inspected before shipment to insure the
highest standards of quality and performance.
Compare all components with the bill of lading or
packing list to verify that the proper unit was received.
Check each unit for any damage that may have
occurred in transit. Any damage should be reported
Lifting Lugs
Lifting Lugs
Lifting Lugs
©2014 Twin City Fan Companies, Ltd.
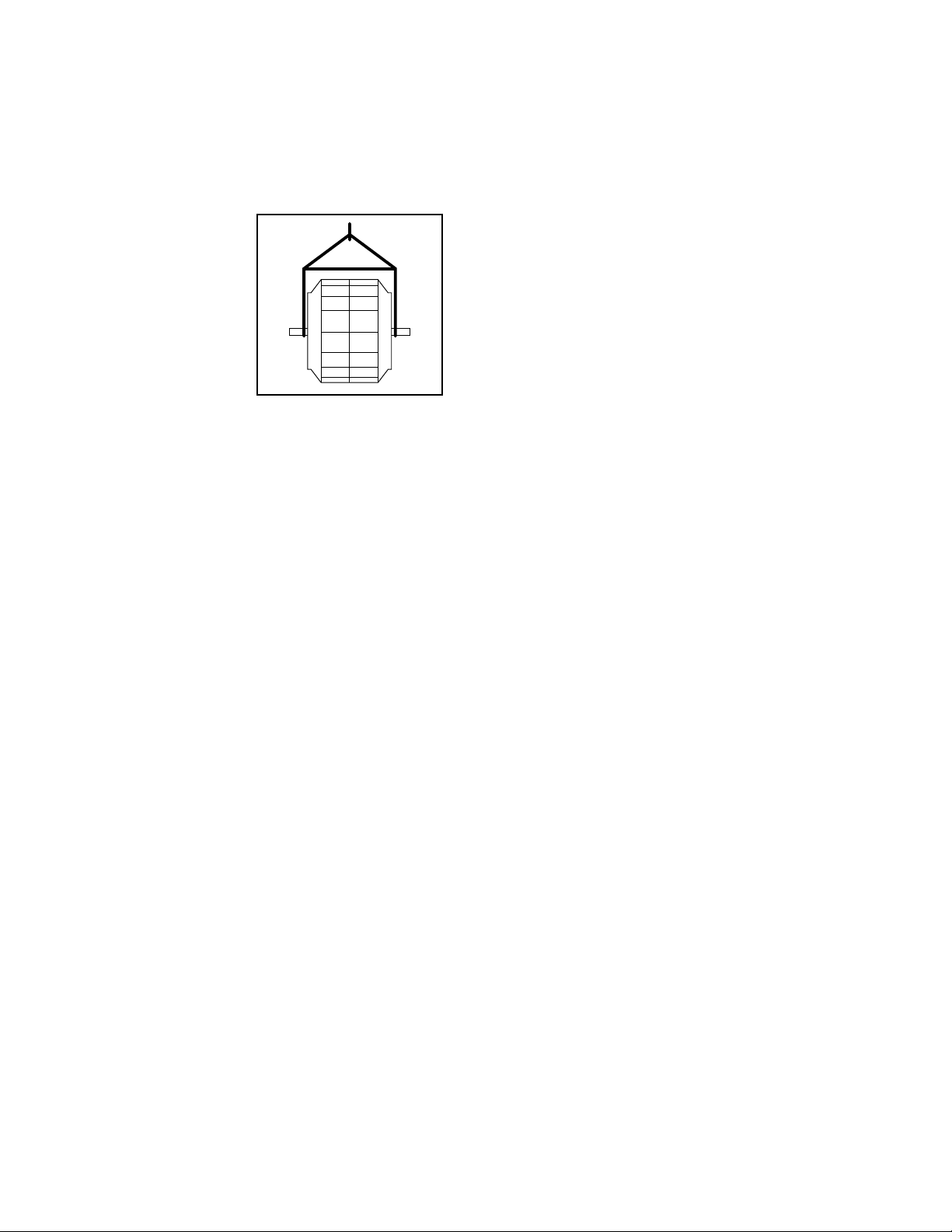
Housing should be lifted using straps and spreaders. Do
not distort housing or side plates when lifting.
Bearing pedestals should be lifted using straps or padded chains. Under no circumstances should an attached or
separated bearing pedestal be lifted by the shaft, bearings,
drives, motor or wheel.
The shaft and wheel assembly may be lifted using
a hoist and a spreader
with a sling around the
shaft at points nearest the
wheel (see Figure 2). Take
care not to scratch the
shaft where the wheel or
bearings will be mounted.
Never lift or support the
assembly by the wheel.
Always support the assembly by the shaft when lifting
or storing. Do not support
the shaft or the wheel on
housing sides. Use only the
key provided with the shaft
and wheel.
Wheels shipped separately can be lifted by slings running through the blades and around the hub. Never lift the
wheel by blades or flanges. Always transport wheels by
lifting. Do not roll the wheel as this can damage coatings
and change the balance of the wheel.
Bent shafting is a source of vibration and bearing failure,
so handle the shaft with care. Any scratches on the shaft
may be removed with fine emery cloth or a stone.
Figure 2. Moving Shaft and
Wheel with Spreader Bar
Short Term Storage
If fan installation is to be delayed, store the unit in a
protected area. Protect the fan and motor bearings from
moisture and vibration (or shock loading).
Long Term Storage
Prior to Storage – Fan bearings (and motor bearings per
the motor manufacturer’s specifications) are to be greased
at the time of going into extended storage. On belt drive
units the belt tension should be reduced to less than half
the specified value for the fan’s design to prevent a sag/
set from forming in the shafts and belts.
If the unit was supplied with a motor, the motor windings
should be measured at this time and recorded for
comparison prior to placing in service. If the fan housing
was supplied with a drain connection, this plug should
be removed to prevent any moisture from accumulating in
this portion of the unit during storage.
Storage Procedure – Fans should be stored indoors whenever possible where control over temperature, shock and
dust is reasonably maintained. If units are to be stored
outside in the elements, they should be covered with a
water-resistant material. The bearings should be shielded
individually from water and dirt; however, do not tightly
seal to avoid trapping condensation. Stored equipment
should be stored on a clean, dry floor or blocked up off
the ground on blocks to prevent unit from setting in any
water or directly on the ground. If shock or vibration will
be present during storage, the unit may need to be placed
on some type of vibration dampening material to aid in
preventing brinelling of the bearing surfaces.
Periodic Check – On a monthly interval, the equipment
should be checked to ensure that it has remained in an
acceptable stored condition. The fan (and motor if supplied) should be rotated several times by hand while adding enough grease to replenish the bearing surfaces with
fresh grease and to maintain a full bearing cavity. Grease
2
used must be compatible with that already supplied in the
motor and fan bearings. The fan impeller should be left
at approximately 180 degrees from that of the previous
month to prevent the shaft and impeller from taking a
set in one position. Storage records should be maintained
which indicate the above requirements have been followed.
Consult the motor manufacturer for proper storage, space
heater connection and lubrication if the unit was supplied
with one.
Start-Up – When the unit is removed from storage, all fan
bearing grease should be purged and replenished with fresh
grease as per the lubrication decal. The motor should be
measured to verify that the resistance is still at a satisfactory level compared to the value recorded prior to storage.
Spherical roller bearings with split pillow block housings
should be recharged with grease. The bottom half of the
housing should be 1/3 full.
Foundations and Supporting Structures
Floor mounted fans should be installed on a flat, level, rigid
concrete foundation with a mass at least three to five times
that of the assembly supported as a guide, depending on
the size and speed of the fan. Foundation shall be suitable
for static and dynamic loads and foundation frequencies
be separated at least 20% from the rotational speed/speed
ranges. The plan area should be no more than twice that
required by the equipment. Foundations with larger areas
should have correspondingly larger mass. Anchor bolts
should be “L” or “T” shaped with sufficient length for nuts,
washers, shims, and threads for draw-down. Each bolt
should be placed in a sleeve or pipe with a diameter larger
than the bolt to allow for adjustment.
If the fans are mounted on a sub-structure, an inertia
base with spring isolator system should be considered.
Fans mounted to or within a structure should be placed
as close as possible to a rigid member such as a wall or
column. The structure must be designed for rotating equipment; static design for strength is not sufficient to insure
proper operation. Supports for suspended fans must be
cross-braced to prevent side sway. Structural resonance
should be at least 20% from fan operating speed. Vibration
isolators should be used where applicable.
Any ducting should have independent support; do not
use the fan to support ducting. Isolating the fan from
ductwork with flex connections eliminates transmission of
vibration. Fans handling hot gases require expansion joints
at both the inlet and discharge to prevent excessive loads
caused by thermal growth.
For fans requiring concrete filled bases or pedestals,
please refer to Twin City Fan's installation and maintenance manual "Heavy Duty Centrifugal Fans - ES-995"
for instructions.
Fan Installation – Factory Assembled Units
Follow proper handling instructions given earlier.
1. Move the fan to the final mounting position.
2. Remove skid, crates, and packing materials carefully.
3. If supplied, place vibration pads or isolation base on
mounting bolts. Line up holes in fan base with bolts.
4. Place fan on mounting structure. Carefully level unit
using shims as required at all mounting hole locations.
Bolt down the unit. Be careful not to force the fan to
conform to the mounting structure/foundation. This may
cause the bearings to become misaligned or pinched
causing vibration and premature failure.
5. Any grout may now be used. Bolt the fan in position
before applying grout. Do not depend upon grout to
support rotating equipment.
6. Continue with Operations Checklist.
Twin City Engineering Supplement ES-52
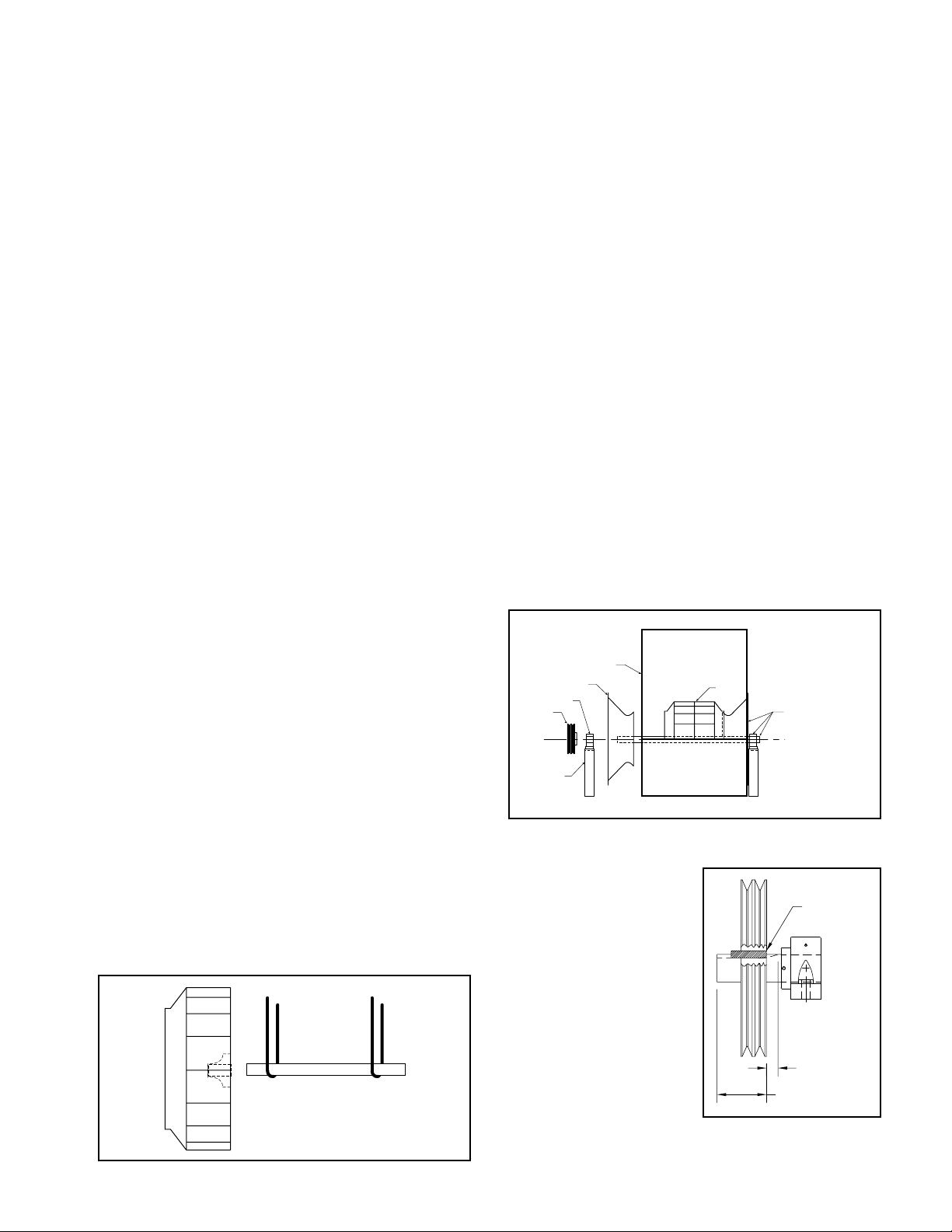
Additional instructions may be given for some fan models,
components and accessories in the appendix.
Fan Installation – Disassembled Units
A unit is considered “disassembled” if any component
required for proper operation is shipped or supplied separately or in pieces. Reference earlier instructions concerning
proper handling of fan components.
Instructions for Mounting and Assembly of Unit:
1. Move lower housing/framework to mounting location.
2. If vibration pads or bases are used, place on bolts first.
Place lower housing assembly onto bolts.
3. Level and shim if required. Bolt into place.
4. If separated pedestal or bearing pedestal:
a. Bring bearing pedestal to desired location.
b. Place any vibration base or pads into place. Set
bearing pedestal on bolts.
c. Never distort bearing pedestal by forcing it to align
with a non-level surface. Shim beneath the pedestal
as required.
d. Check bearing centerline height. Change centerline
height to match centerline height of housing. High
temperature units may require the housing centerline
to be lower when cold so that it will be centered
when hot.
e. Measure from housing to bearing pedestal to bring
bearing pedestal into square with housing (a large
square may also suffice).
f. Bolt into position.
5. Shaft and wheel assembly preparation:
a. Clean protective coating off shaft with solvent. Do
not touch clean areas of shaft with hands. Perspiration
can cause rust or pitting over time.
b. Remove keys from shaft.
c. Clean inside of wheel bore with solvent. Make sure
setscrews will not interfere when inserting shaft into
wheel bore.
6. Arrangement 1, 9 or 10: Drive Component Assembly
(See Figure 3):
a. Insert shaft into wheel from back side of wheel.
b. When shaft is flush with wheel hub, put key into
keyway and tighten wheel setscrews.
c. Insert shaft through opening in drive side. (If split
housed unit, lower into position.)
d. Install bearings onto shaft. Do not tighten bearing
setscrews at this time. The bearing housing should
be perpendicular and the bearing base parallel to the
axis of the shaft to prevent loads caused by misalignment.
e. Mount assembly, bolt bearings to drive stand. Shaft
Figure 3. Drive Component Assembly
must be parallel with side of bearing pedestal.
Precision shim bearings as required. After aligning
and bolting bearings to pedestal, lock bearings. Be
sure expansion bearing (if supplied) is set to allow
for growth. Continue with step 8.
7. Arrangement 3 (Split-housed) units (See Figure 4):
a. Parts on DWDI units are assembled in the following
order as viewed from opposite drive side: Bearing
bar assembly and opposite bearing, funnel, (housing side), wheel, (housing side), funnel, drive side
bearing bar assembly, drive bearing and sheaves.
Mount bearing bar assembly to housing. Center
wheel in funnels.
b. Parts on SWSI units are assembled in the following
order as viewed from opposite drive side: Bearing
bar assembly and opposite bearing, funnel, (housing
side), wheel, (housing side), drive side bearing bar
assembly, drive bearing and sheaves. Mount bearing
bar assembly to housing. (See Figure 7 for wheel-
funnel overlap.)
c. Assemble parts in above order on shaft.
d. Move assembly into position. Lightly bolt bearings
into place.
e. Shaft should be parallel with discharge of housing.
Move bearings to accommodate.
f. Level shaft; shim bearings if required. Lock bearings.
Be sure expansion bearing (if supplied) is set to allow
for shaft growth.
8. Install motor on base. Carefully align shafts for drive
installation.
Figure 4. Split-housed Drive Component Assembly
Housing Side
Inlet Funnel
Bearing
Sheave
Shaft
Centerline
Bearing
Pedestal
9. Mount drives as follows:
Wheel
Shaft, Funnel, and
Housing. Frame
Angles Not Shown.
Figure 5. Sheave Position
a. Slip (do not pound)
proper sheave
onto corresponding shaft. CAUTION:
SHEAVE LINED
UP WITH END
OF KEYWAY
RUN OUT
PLACING FAN
SHEAVE ON MOTOR
CAN OVERSPEED
WHEEL AND CAUSE
STRUCTURAL
FAILURE.
b. Position sheaves
so they are placed
on motor shaft and
fan shaft as close
as possible to the
RUN OUT OF
KEYWAY
KEYWAY LENGTH
motor and/or bearing. Sheave must be
placed so that it does not rub on the bearing,
motor guard or other structures. On keyed shafts,
Twin City Engineering Supplement ES-52 3