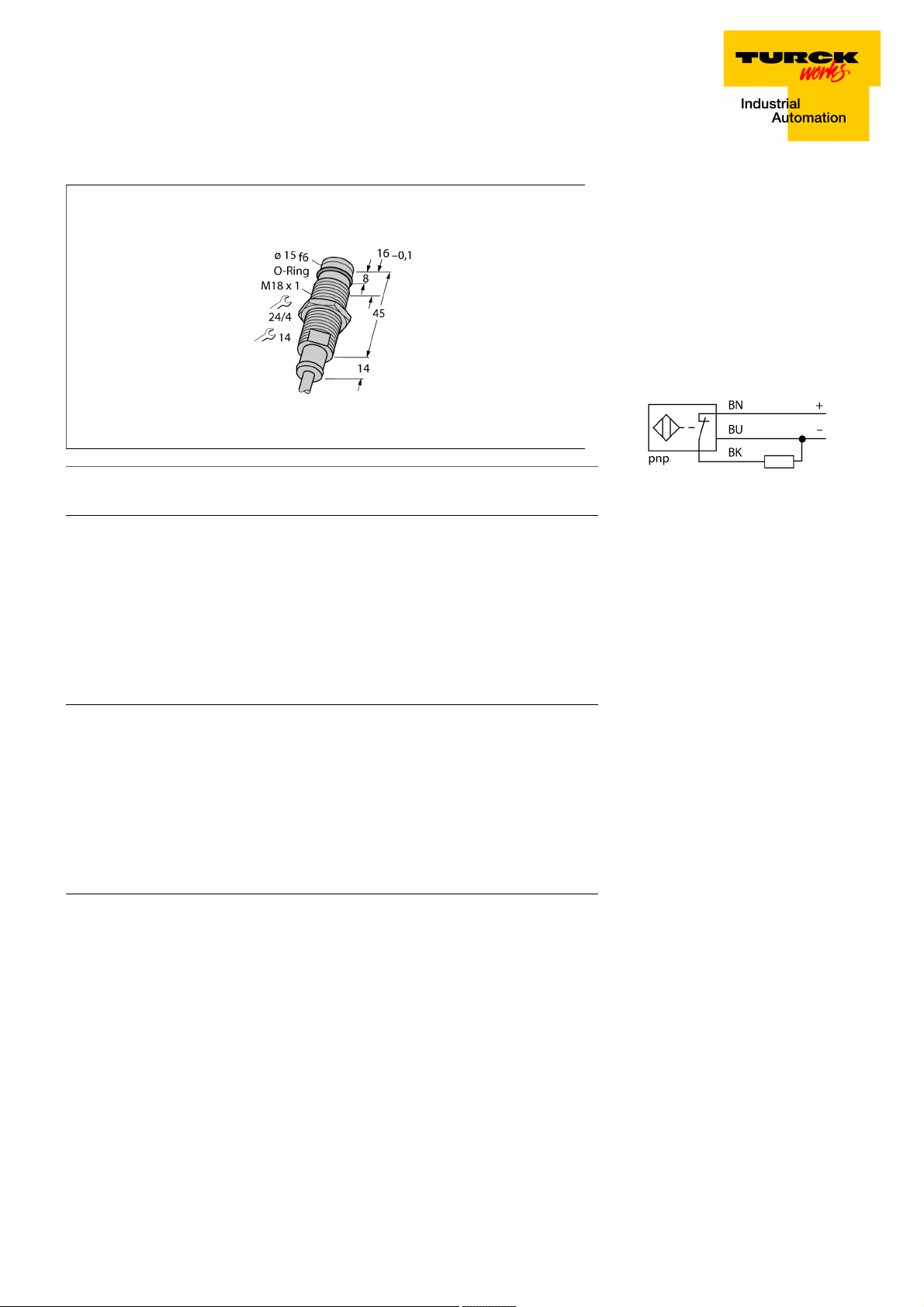
Inductive sensor
For high pressures
BID2-G180-RP6/S212
Type designation BID2-G180-RP6/S212
Ident-No. 1688010
Rated switching distance Sn 2 mm
Mounting conditions Flush
Secured operating distance
Correction factors St37 = 1; Al = 0.3; stainless steel = 0.7; Ms = 0.4
Repeat accuracy
Static pressure
Dynamic pressure
Admissible contact medium electrically non-conductive
Temperature drift
Hysteresis 3…15 %
Ambient temperature -25…+85 °C
Operating voltage 10…30 VDC
Residual ripple
DC rated operational current
No-load current I
Residual current
Isolation test voltage
Short-circuit protection yes/ Cyclic
Voltage drop at I
Wire breakage/Reverse polarity protection yes/ Complete
Output function 3-wire, NC contact, PNP
Switching frequency 2 kHz
0
e
ð (0,81 x Sn) mm
ð 2 % of full scale
ð 500 bar
ð 350 bar
ð ± 10 %
ð 10 % U
ss
ð 200 mA
ð 15 mA
ð 0.1 mA
ð 0.5 kV
ð 1.8 V
■ Threaded barrel, M18 x 1
■ Stainless steel, 1.4305
■ Admissible pressure static/dynamic
500/350 bar
■ DC 3-wire, 10…30 VDC
■ NC contact, PNP output
■ Cable connection
Wiring Diagram
Functional principle
Inductive sensors detect metal objects contactless and wear-free. For this purpose they
use a high-frequency electromagnetic AC
field that interacts with the target. The sensors
hosting a ferrite core coil generate the AC field
through an LC resonant circuit.
Pressure resistant inductive sensors withstand pressures of up to 500 bar which makes
them perfectly suited for position control in hydraulic cylinders.
Design Threaded barrel,M18 × 1
Dimensions 58 mm
Housing material Metal, V2A (1.4305)
Active area material Plastic, PA12-GF30
Max. tightening torque housing nut 25 Nm
Electrical connection Cable
Cable quality 6.3mm, LiÖlflex, Ölflex®, 2
Cable cross section
Vibration resistance 55 Hz (1 mm)
Shock resistance 30 g (11 ms)
Protection class IP67
Edition • 2018-04-23T15:46:52+02:00
1 / 2 TURCK Inc.
3 x 0.5 mm
2
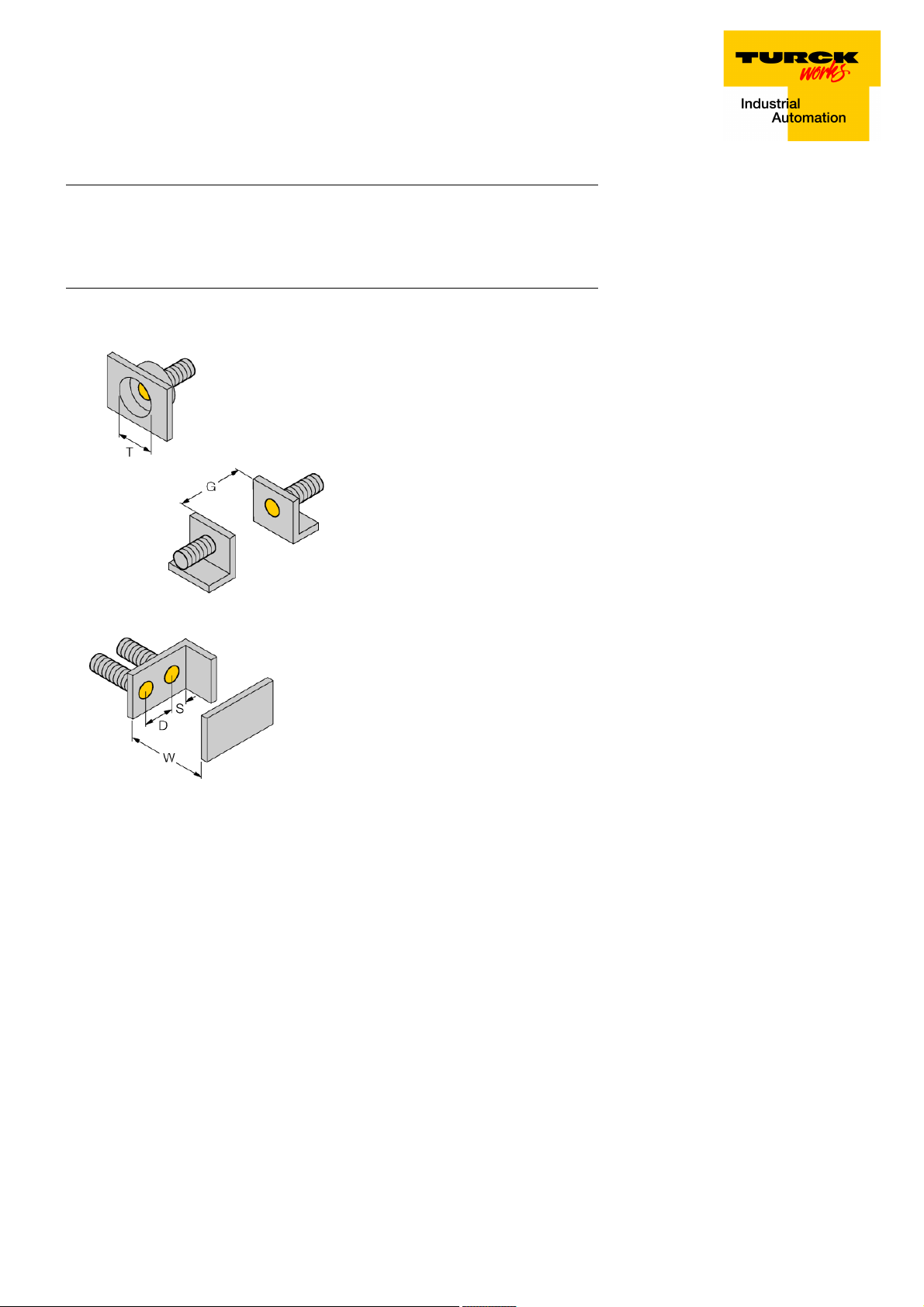
Inductive sensor
For high pressures
BID2-G180-RP6/S212
Distance D 2 x B
Distance W 3 x Sn
Distance T 3 x B
Distance S 1.5 x B
Distance G 6 x Sn
Diameter active area B Ø 18 mm
In order to protect the coil connections integrated in
■
the sensor head, it is required to ventilate the chamber of the oscillator coil.
For this the employed non-conductive and neutral
■
medium is filled into the cavity via the middle hole of
the sensor's active face, using a thin cannula.
Edition • 2018-04-23T15:46:52+02:00
2 / 2 TURCK Inc.