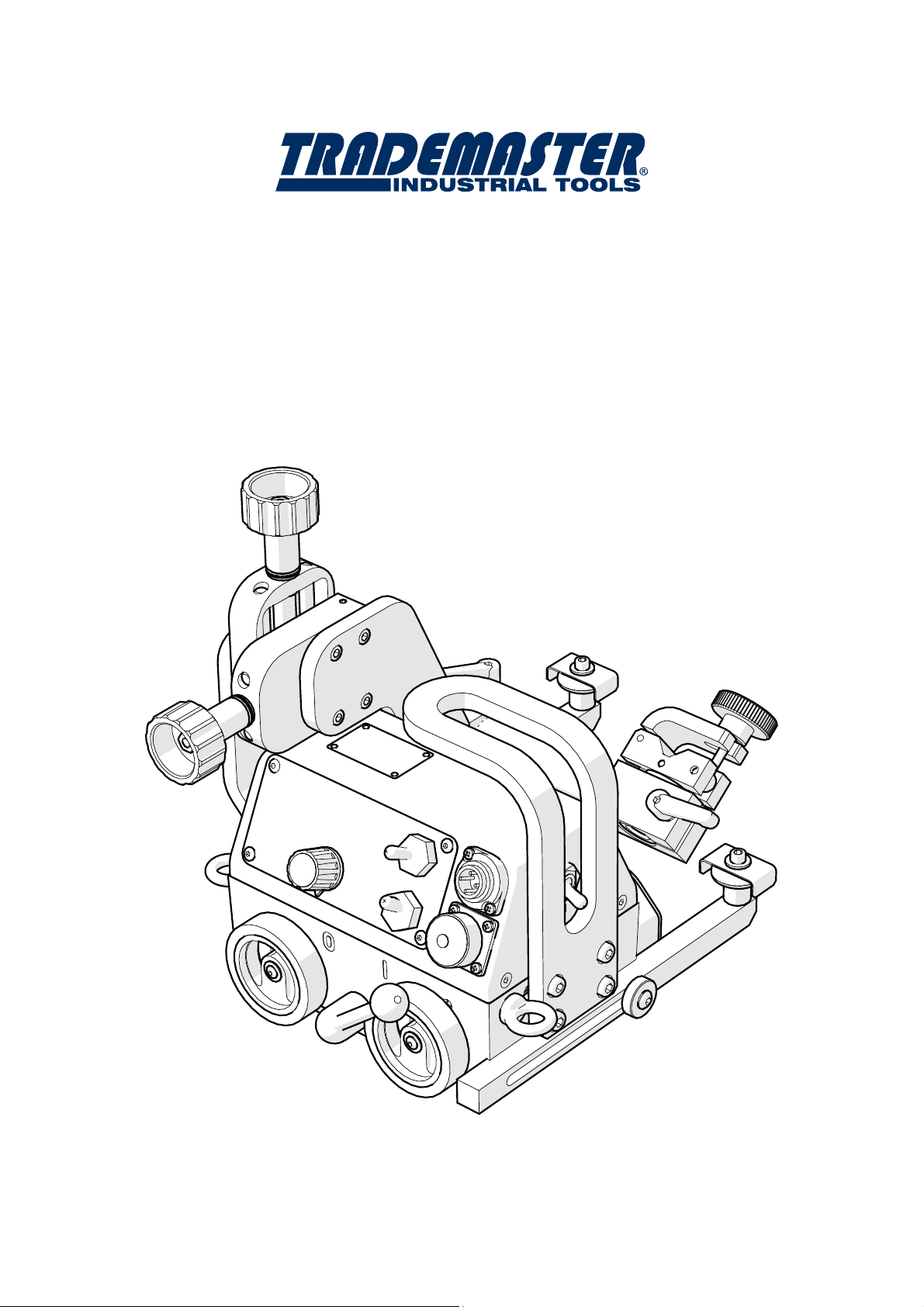
GECKO
WELDING CARRIAGE
OPERATOR’S MANUAL
BEFORE USE, ENSURE EVERYONE USING THIS MACHINE READS AND UNDERSTANDS
ALL SAFETY AND OPERATING INSTRUCTIONS IN THIS MANUAL .
Serial #............................................ Date of Purchase............................
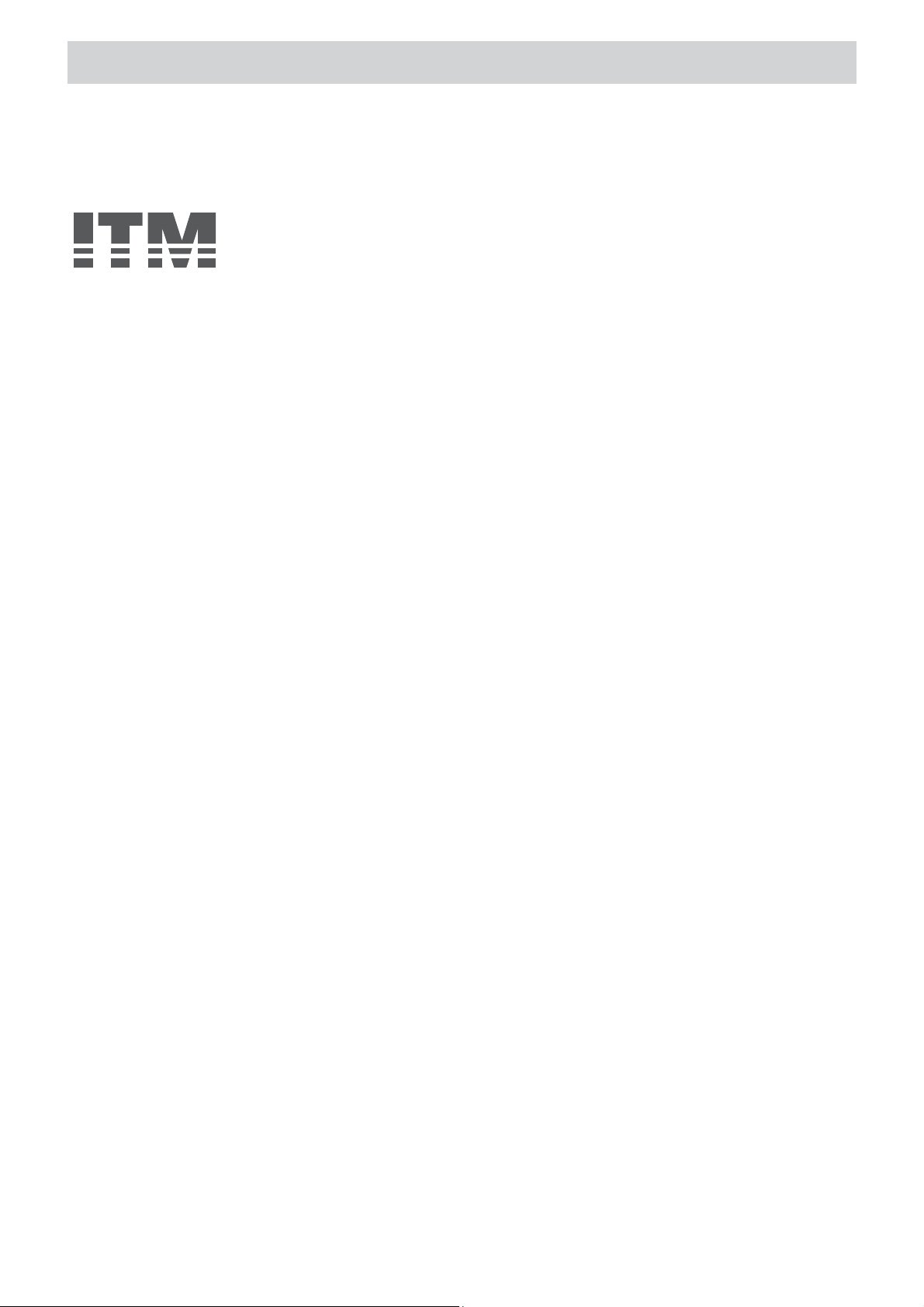
TRADEMASTER GECKO WELDING CARRIAGE
IMPORTED & DISTRIBUTED BY
18 BUSINESS ST
YATALA QLD 4207 AUSTRALIA
07 3287 1114
T
07 3287 1115
F
sales@industrialtool.com.au
E
www.industrialtool.com.au
W
INDUSTRIAL TOOL & MACHINERY SALES
WARRANTY TERMS
In addition to any warranties or conditions implied by applicable Statute or Regulations, Industrial Tool & Machinery
Sales warrants all of it’s products against defective workmanship and faulty materials for a period of twelve (12)
months from the date of purchase, unless otherwise stated. At our option we will repair or replace, free of charge,
any item on the condition that:
• The complete machine or tool is returned, freight prepaid to ITM or one of it’s authorised service agents as
directed by ITM, and is found to have a material or constructional defect.
• The machine or tool has not been subject to misuse, neglect or damage by accident.
• The fault is not a result of normal “wear and tear”.
• Written permission has been received from ITM prior to commencement of repair.
• Repairs, tampering or modification carried out by unauthorised personnel will void all warranty.
• Consumable items such as cutting tools, pilot pins, saw blades, grinding wheels etc. are NOT covered by
warranty.
Our goods come with guarantees which cannot be excluded under the Australian Consumer Law. You are entitled
to replacement or refund for a major failure and to compensation for other reasonably foreseeable loss or damage.
You are also entitled to have the goods repaired or replaced if the goods fail to be of acceptable quality and the
failure does not amount to a major failure.
TABLE OF CONTENTS
General Information 2
Technical Data 3
Design 4 - 5
Saftey Precautions 6 - 7
Startup and Operation 8 - 11
Wiring Diagram 12
Parts Lists & Exploded Views
General Assembly 13 - 14
Drive System Assembly 15
Drive System 16 - 17
Controller Housing Complete 18
Panel Assembly 19
Torch Holding & Low Torch Holding Assembly 20
1
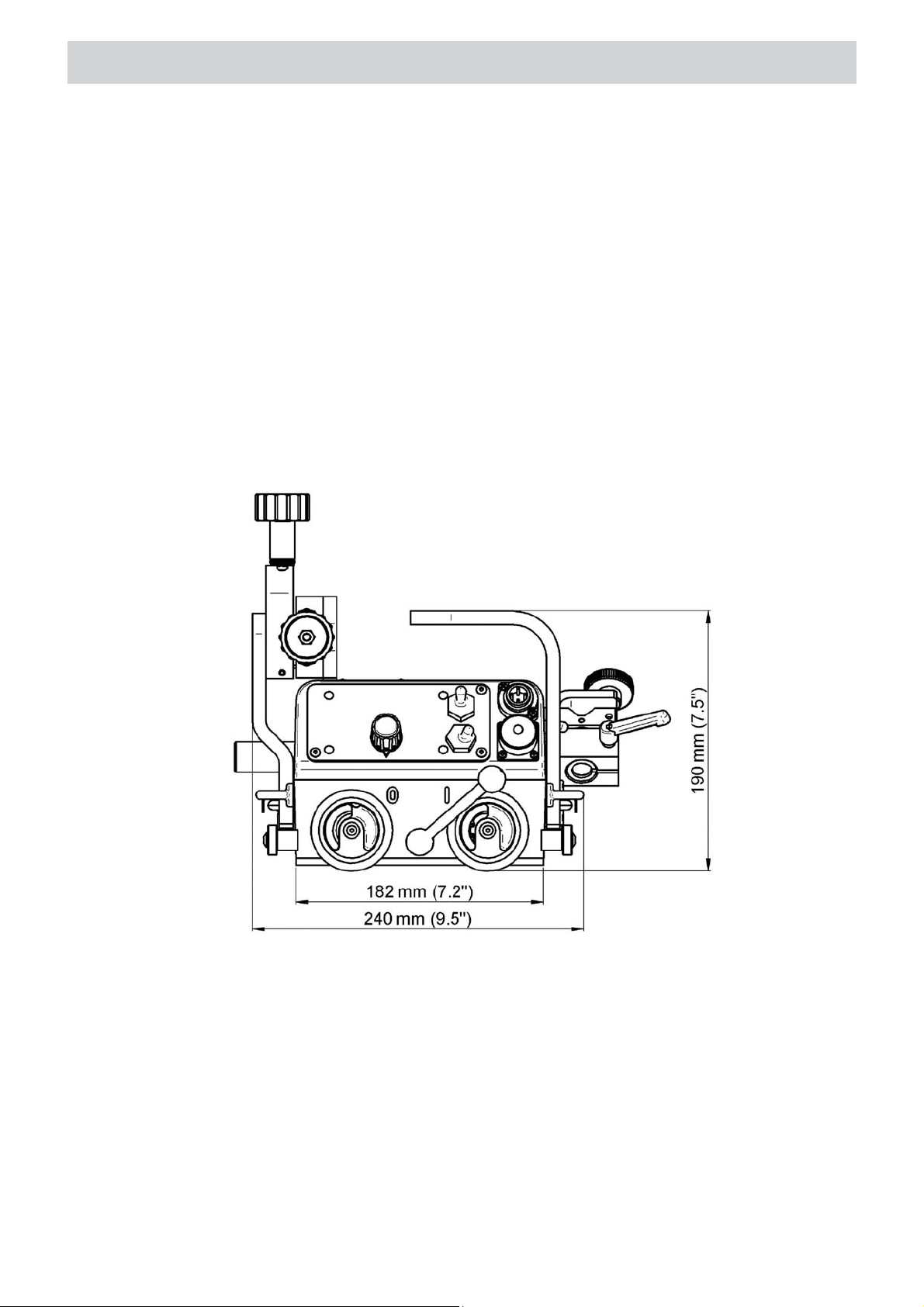
GENERAL INFORMATION
1. GENERAL INFORMATION
1.1. Application
The GECKO Welding Carriage produces continuous welds using MIG/MAG welding torches with
handle diameter in 16–22 mm range (0.63–0.87’’). The machine can work in PA, PB, PC, and PF
welding positions. It is fixed by permanent magnets and contains a four wheel drive with speed
adjustment.
1.2. Technical data
2
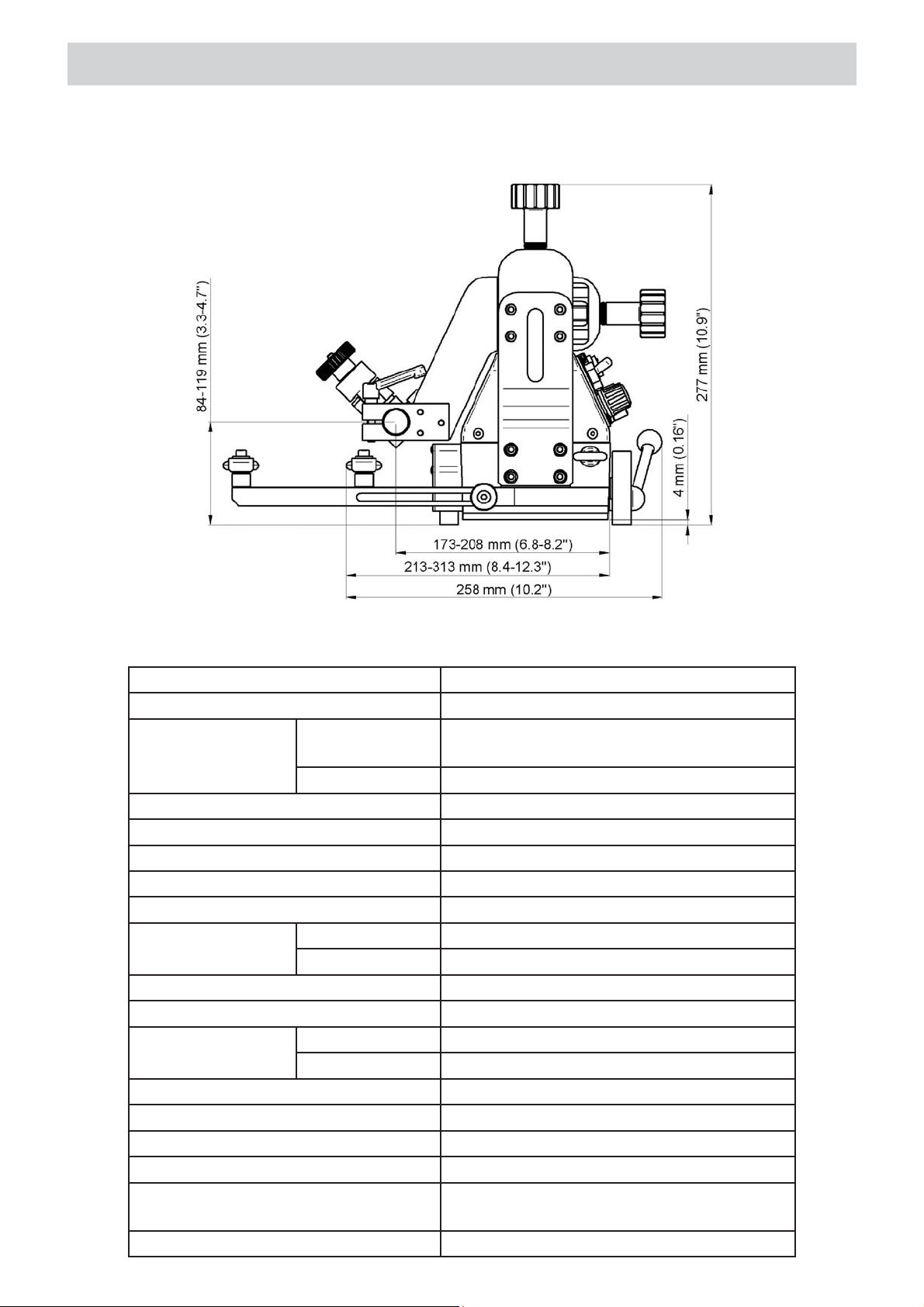
TECHNICAL DATA
Welding position ~ 115–230 V, 50–60 Hz
Power 20 W
Welding position horizontal PA (flat), PB (horizontal vertical), PC
(horizontal)
vertical PF (vertical up)
Minimum path convex radius 1000 mm (40’’)
Minimum path concave radius 1250 mm (50’’)
Torch type MIG/MAG
Torch diameter 16–22 mm (0.63–0.87’’)
Maximum torch reach 70 mm (2.76’’)
Maximum weight
of cables
Welding material thickness minimum 4 mm (0.16’’)
Ground clearance 4 mm (0.16’’)
Pulling force horizontal work 150 N
Torch adjustment range 35 mm (1.38’’, up-down, left-right)
Follower arm adjustment range 100 mm (3.93’’)
Horizontal speed 0–110 cm/min (0–43.3’’/min)
Vertical speed 0–100 cm/min (0–39.4’’/min)
Dimensions 240 mm (L) × 258 mm (W) × 277 mm (H)
3
Weight 8 kg (17.7 lbs)
horizontal work 8 kg (17.7 lbs)
vertical work 13.3 lbs)
vertical work 100 N
9.5’’ (L) × 10.2’’ (W) × 10.9’’ (H)
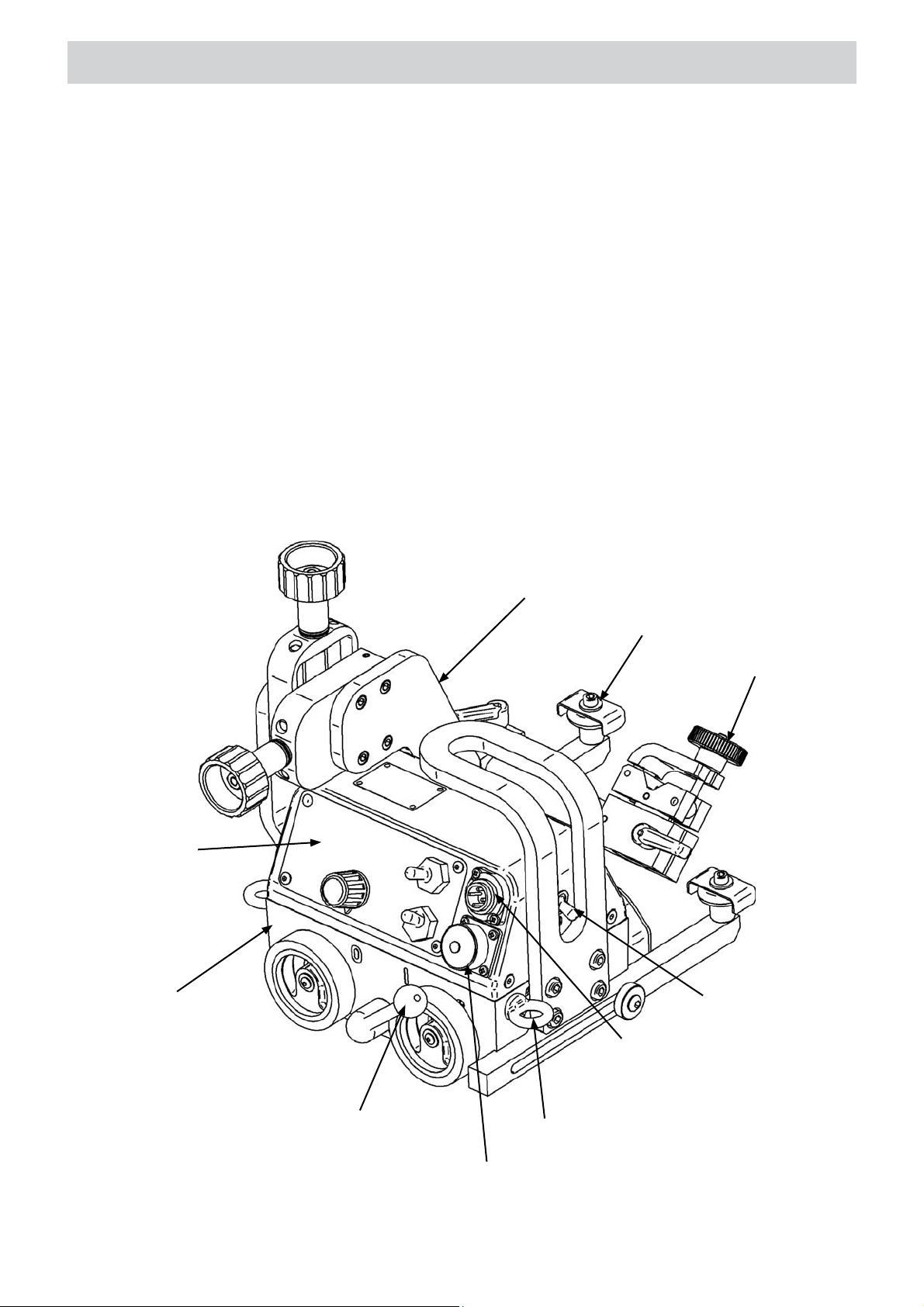
DESIGN
1.3. Design
The GECKO Welding Carriage contains a drive system with controller, cross slides, two follower
arms, and torch holder. The drive system comprises a gear motor that drives four rubber wheels
of high thermal resistance.
The magnetic unit with powerful permanent magnets fitted at the carriage bottom ensures
proper adhesion to ferromagnetic surfaces. Toggling the magnetic unit lever (Figure 1) to position
“0” reduces the intensity of the magnetic field, what helps moving the welding carriage during
positioning. The cross slides enable precise control of the torch holder position in both horizontal
and vertical axis. Additionally, the machine can ignite an arc through the arc ignition socket when
choosing a travel direction.
Control Panel
Drive System
Cross Slides
Follower Arm
Torch Holder
Power Switch
Magnetic Unit Lever
Arc Ignition Socket
Figure 1. GECKO Operator’s Manual
Saftey Line Lug
Power Supply Socket
4
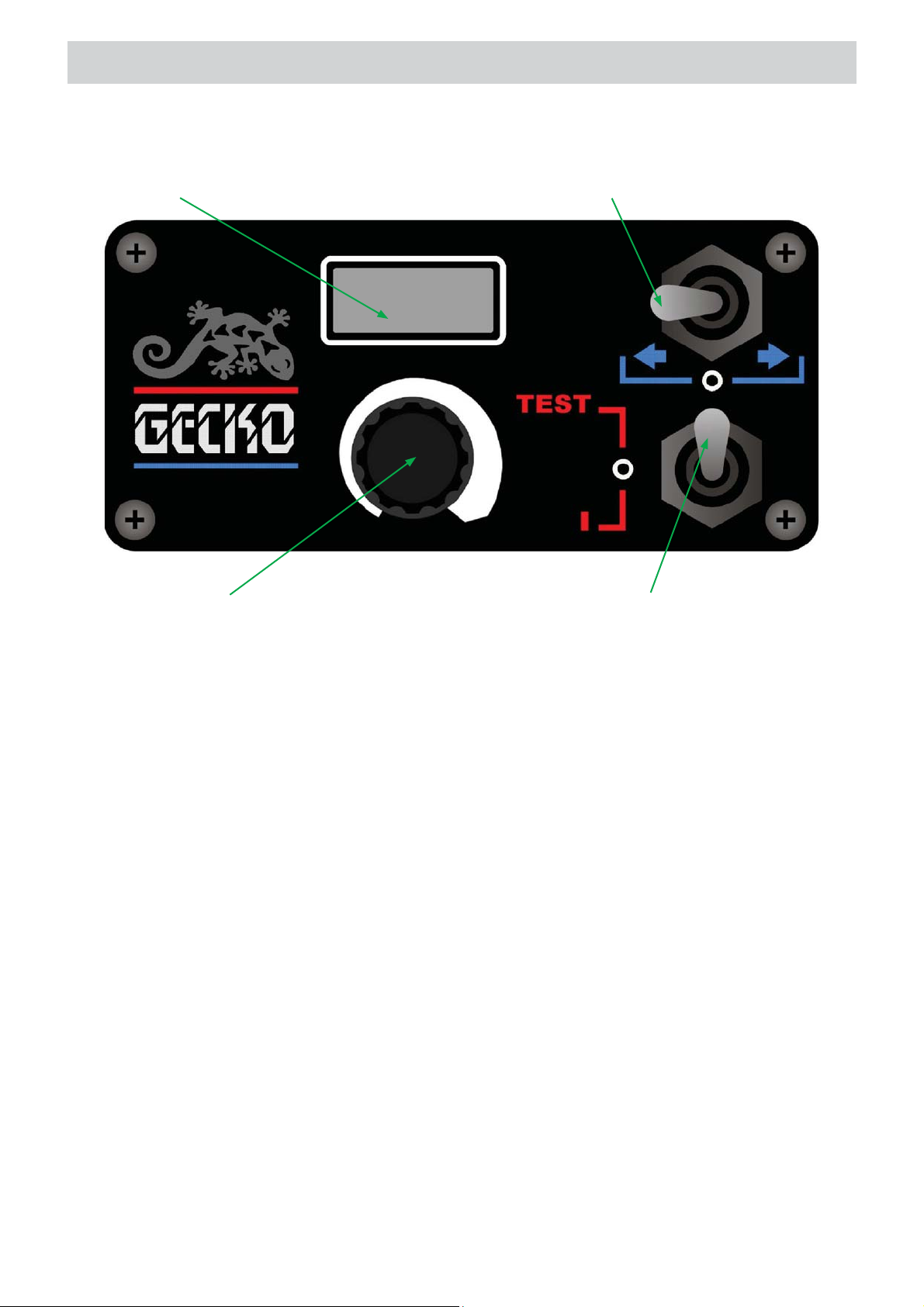
DESIGN
LED Display
Speed Adjusting Knob Arc Ignition Switch (TEST / 0 / 1)
Travel Direction Switch (left / 0 / right)
Figure 2. Control Panel Design
1.4. Equipment included
The GECKO Welding Carriage is supplied with complete standard equipment in a foam filled
cardboard box. The included equipment consists of:
• welding carriage – 1 unit
• foam filled cardboard box – 1 unit
• power cord – 1 unit
• arc ignition cable – 1 unit
• torch holder – 1 unit
• 4 mm Allen key – 1 unit
• Operator’s Manual – 1 unit
5
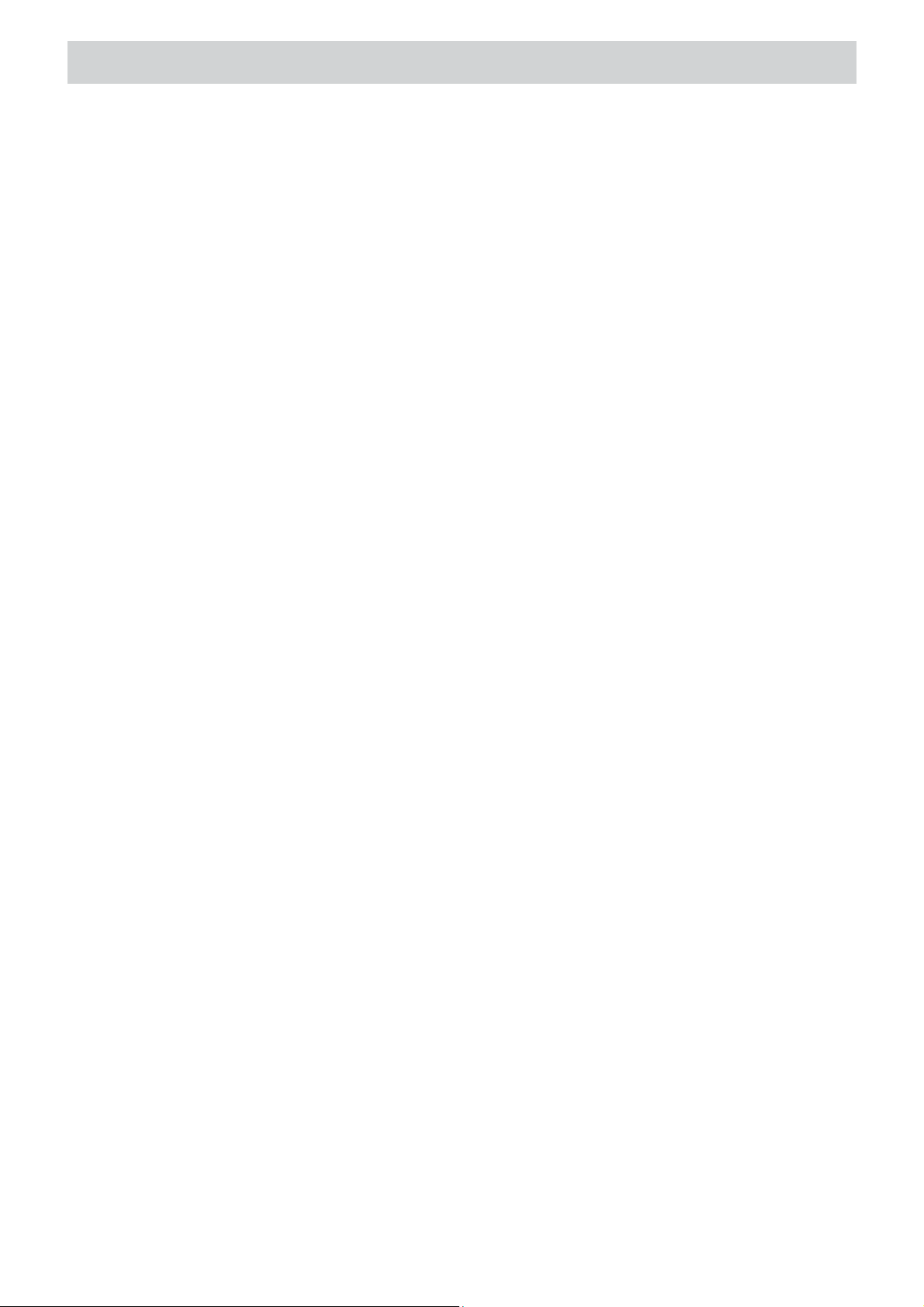
SAFTEY PRECAUTIONS
2. SAFETY PRECAUTIONS
1. Before start, read Operator’s Manual and complete proper occupational safety and
health training.
2. Machine must be used only in applications stated in Operator’s Manual.
3. Machine must be complete and all parts must be genuine.
4. Power supply specifications must conform to those stated on rating plate.
5. Power supply socket must be equipped with grounding pin.
6. Never carry machine by cord or yank it to disconnect plug from socket. It may cause
power cord to break and result in electric shock.
7. Bystanders must not be present in immediate vicinity of machine.
8. Before start, check condition of machine and electrical installation, including power
cord, plug, control panel, and wheels.
9. Keep machine dry. Exposing it to rain, snow, or frost is prohibited.
10. Ensure proper lighting at worksite.
11. Never use machine in vicinity of flammable fluids or gases, or in explosive environments.
12. Make sure that rubber of driving wheels is clean and not damaged.
13. Never disassemble driving wheels cover.
14. Remove objects attracted to chassis by magnetic unit.
15. Transport and position machine using carrying handle, with magnetic unit lever set to
position “0”.
16. Place machine on ferromagnetic material in such a way that wheels always touch
surface and there is no contact between surface and chassis.
17. Do not stay underneath machine placed at heights.
18. Plug power cord into mains only when power switch is set to position “0”.
19. Keep power socket clean. Do not use compressed air for cleaning purposes.
20. Mounting torches other than MIG/MAG type or torches with handle diameter outside
16–22 mm range (0.63–0.87’’) is prohibited.
21. Maximum torch reach must not exceed 70 mm (2.76’’).
22. Keep torch cables from touching surface (they must be suspended to reduce carriage
load). Use only cables which maximum weight is 8 kg (17.7 lbs) for horizontal work
and 6 kg (13.3 lbs) for vertical work.
23. Operating in welding positions: PD (horizontal overhead), PE (overhead), and PG
(vertical down), as well as on curvatures with convex (concave) radius lower than
1000 mm (1250 mm) is prohibited.
24. When operating at heights, use safety line to protect machine from falling down.
25. Always use eye protection (welding helmet, shield, and screen), hearing protection,
gloves, and protective clothing during operation. Do not wear loose clothing.
26. Before every use, inspect machine to ensure it is not damaged. Check whether any
part is cracked or improperly fitted. Make sure to maintain proper conditions that may
affect machine operation.
27. Never try to manually stop motion of machine. For this purpose set travel direction
switch to position “0”.
6