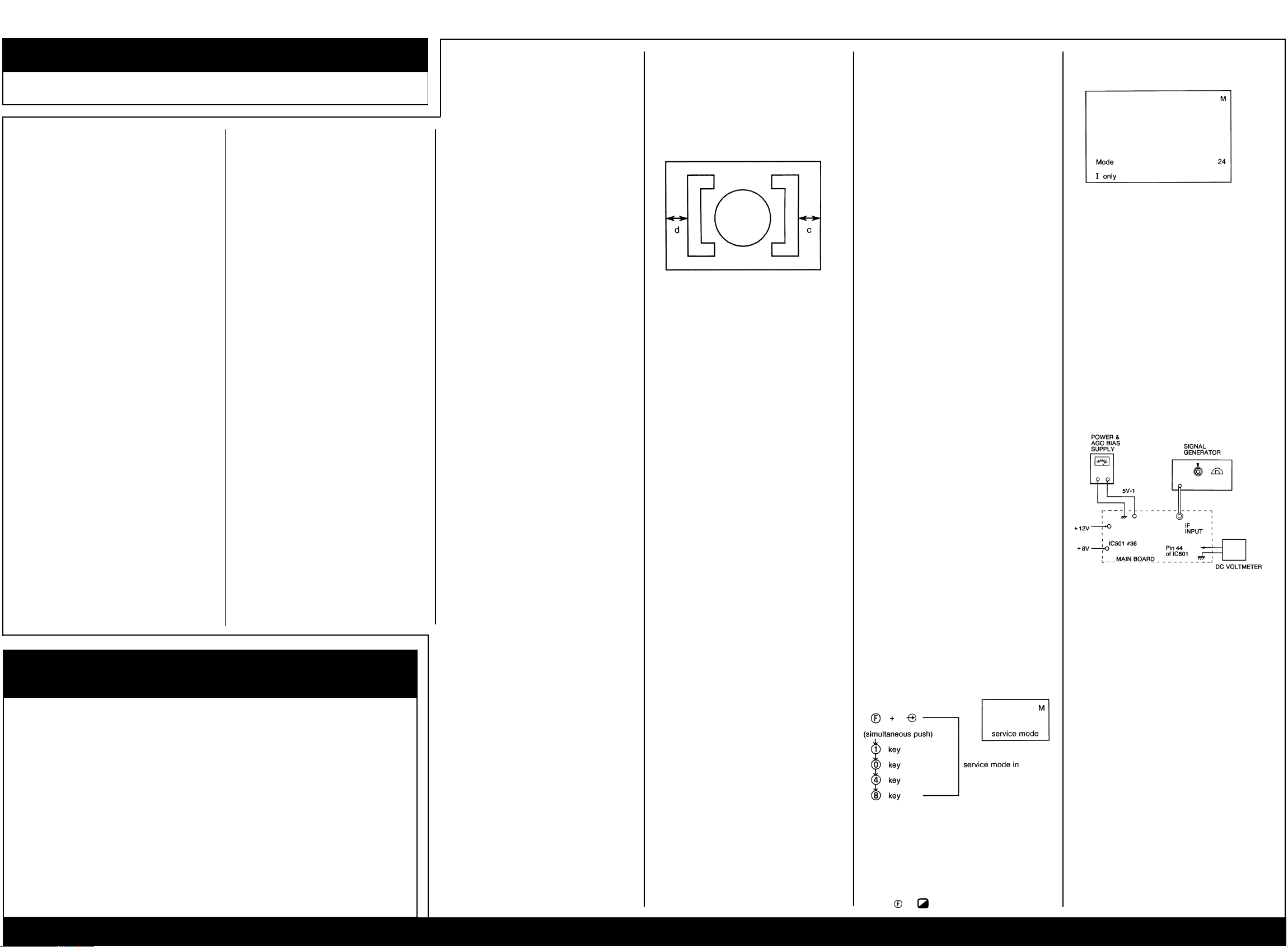
TOSHIBA 1752 TB
1
General Information
Chassis : C4E-R
Safety Instructions
X-RAY RADIATION PRECAUTION
1. The E.H.T. must be checked every time the
receiver is serviced to ensure that the C.R.T.
does not emit X-ray radiation as result of
excessive E.H.T. voltage. The nominal E.H.T.
for this receiver is 27.1 kV at zero beam
current (minimum brightness) operating at
220V a.c. The maximum E.H.T. voltage
permissible in any operating circumstances
must not exceed 27.5 kV. When checking the
E.H.T., use the ‘High Voltage Check’ procedure using an accurate E.H.T. voltmeter.
2. The only source of X-RAY radiation in this
receiver is the C.R.T. To prevent X-ray
radiation, the replacement C.R.T. must be
identical to the original fitted as specified in
the Parts List.
3. Some components used in this receiver have
safety related characteristics preventing the
C.R.T. from emitting X-ray radiation.
For continued safety, replacement component
should only be made after referring to the
Product Safety Notice
SAFETY PRECAUTION
1. This receiver has a nominal working E.H.T.
voltage of 23.0 kV. Extreme caution should be
exercised when working on the receiver with
the back removed.
Do not attempt to service this receiver if you
are not conversant with the precautions and
procedures for working on high voltage
equipment.
When handling or working on the C.R.T.,
always discharge the anode to the receiver
chassis before removing the anode cap.
The C.R.T., if broken, will violently expel glass
.
fragments. Use shatter proof goggles and
take extreme care while handling. Do not hold
the C.R.T. by the neck as this is a very
dangerous practice.
2. It is essential that to maintain the safety of the
customer all cable forms be replaced exactly
as supplied from factory.
3. A small part of the chassis used in this
receiver is, when operating, at approximately
half mains potential at all times. It is therefore
essential in the interest of safety that when
serving or connecting any test equipment the
receiver should be supplied via a suitable
isolating transformer of adequate rating.
4. Replace blown fuses within the receiver with
the fuse specified in the parts list.
5. When replacing wires or components to
terminals or tags, wind the leads around the
terminal before soldering. When replacing
safety components identified by the international hazard symbols on the circuit diagram
and parts list, it must be a Toshiba approved
type and must be mounted as the original.
6. Keep wires away from high temperature
components.
PRODUCT SAFETY NOTICE
Many electrical and mechanical components in
this chassis have special safety-related
characteristics. These characteristics are often
passed unnoticed by a visual inspection and the
X-ray radiation protection afforded by them
cannot necessarily be obtained by using
replacements rated at higher voltages or
wattage, etc. Components which have these
special safety characteristics in this manual and
its supplements are identified by the international hazard symbols on the schematic diagram
and parts list. Before replacing any of these
components read the parts list carefully.
Recommended Safety Parts
Item Part No. Description
A401 23426340 Back Cover
C440 24082348 PF, 6800pF, ±3%, 1500V
C463 24212222 CD, 2200pF, ±10%
C801 24082363 PF, 0.22pF, ±20%, AC250V
C802 24094656 CD, 2200pF, ±20%, AC400V
C803 24094656 CD, 2200pF, ±20%, AC400V
R327 24339569 ME, 5.6 ohm, 2W
R444 24338398 MF, 0.39 ohm, 1W
R801 24009954 Metal-Glazed Resistor, 2.2M ohm, 1/2W
R844 24005007 Metal-Glazed Resistor, 8.2M ohm, 1W
R890 24000918 PTC Thermistor, 18 ohm, ±20%, 290V
R920 24000884 FR, 3 ohm, 1W
L462 ------------- DY, Supplied with V901
L901 23200696 Coil, Degaussing, TSB-2293AT
T401 23224983 Transformer, Horiz. Drive, TLN1039
T461 23236501 Transformer, Flyback, TFB4124AE
T801 23211929 Line Filter, TRF3130
T803 23217274 Transformer, Converter, TPW3322AR
Q404 A6871242 Transistor, 2SD1554
Q826 A8643108 Photo Coupler, TLP621(GR-LF
F801 23144898 Fuse, 3.15A
F803 23144876 Fuse, 0.5A
P801 23372012 Power Cord
S801 23145434 Switch, Power, 2C2P
V901A 23902022 Socket, CRT, 8P
V901 23312611 Picture Tube, A41EAM40X50
Substitute replacement components which do
not have the same safety characteristics as
specified in the parts list may create X-ray
radiation
Service Adjustments
GENERAL INFORMATION
All adjustments are thoroughly checked and
corrected when the receiver leaves the factory.
Therefore the receiver should operate normally
and produce proper colour and B/W pictures
upon installation. However, several minor
adjustments may be required depending on the
particular location in which the receiver is
operated.
This receiver is shipped completely in cardboard
carton. Carefully draw out the receiver from the
carton and remove all packing materials.
Plug the power cord into a convenient 220 volts
50 Hz AC two pin power outlet. Turn the receiver
ON. Check and adjust all the customer controls
such as BRIGHTNESS, CONTRAST and
COLOUR Controls to obtain natural colour or B/
W picture.
AUTOMATIC DEGAUSSING
A degaussing coil is mounted around the picture
tube so that external degaussing after moving
the receiver is normally unnecessary, providing
the receiver is properly degaussed upon
installation. The degaussing coil operates for
about 1 second after the power to the receiver is
switched ON. If the set is moved or faced in a
different direction, the power switch must be
switched off at least 30 minutes in order that the
automatic degaussing circuit operates properly.
Should the chassis or parts of the cabinet
become magnetized to cause poor colour purity,
use an external degaussing coil. Slowly move
the degaussing coil around the faceplate of the
picture tube, the sides and front of the receiver
and slowly withdraw the coil to a distance of
about 2 m before disconnecting it from AC
source. If colour shading still persists, perform
the COLOUR PURITY ADJUSTMENT and
CONVERGENCE ADJUSTMENTS procedures.
HIGH VOLTAGE CHECK
CAUTION: There is no HIGH VOLTAGE
ADJUSTMENT on this chassis.
1. Connect an accurate high voltage meter to
the second anode of the picture tube.
2. Turn on the receiver. Set the BRIGHTNESS
and CONTRAST Controls to minimum (zero
beam current).
3. High voltage will be measured below 26.0 kV.
4. Change the BRIGHTNESS Control to both
extremes to be sure the high voltage does not
exceed the limit of 26.0 kV under any
conditions.
HEIGHT ADJUSTMENT
1. Receive the WG PHILIPS pattern, and set the
contrast and colour to minimum, and the
brightness to centre.
2. Ajust HEIGHT Control (R351) so that white
blocks at top and bottom of the picture are are
just masked.
HORIZONTAL CENTRE ADJUSTMENT
1. Receive the UK PHILIPS pattern.
2. Set the contrast and colour to centre, and the
brightness to centre.
3. Adjust H. CENTER USER Control (R451) so
the pattern can be located for d-c to be +
4.0 mm.
Figure 1
FOCUS ADJUSTMENT
Adjust FOCUS Control on FLYBACK TRANS.
(T461) for well defined scanning lines in the
centre area on the screen.
DELAYED R-F AGC ADJUSTMENT
1. Tune the set to the strongest station in your
area.
2. Turn AGC DELAY Control (R151) on PIF
Board to fully counterclockwise position.
3. Adjust AGC DELAY Control clockwise until
noise (snow) disappears on the screen.
CRT GREY SCALE ADJUSTMENT
1. Press VIDEO INPUT button on Remote
Control unit to turn TV to video input mode.
(Video input should have no signal). Next
press PICTURE SELECT button to select
function and set CONTRAST to minimum,
BRIGHTNESS to maximum, COLOUR to
minimum.
2. Turn the SCREEN Control (on T461) fully
counterclockwise.
3. Set the RED, GREEN and BLUE CUT OFF
Controls (R557, R558, R559)
counterclockwise to the centre position.
4. Set the GREEN and BLUE DRIVE controls
(R252, R253) to the centre position.
5. Set the CUT OFF SW. (S202) in the H. line
position.
6. Set the SUB BRIGHTNESS Control to
minimum.
7. Rotate the SCREEN Control gradually
clockwise until the first horizontal line of a
colour (RED, GREEN or BLUE) appears
slightly on the screen. Set the SCREEN
Control to this position.
8. Adjust the CUT OFF Controls to obtain the
slightly lighted horizontal lines in the same
levels of three colours (RED, GREEN and
BLUE). The lines may look like white if the
CUT OFF Controls are adjusted properly.
9. Return the CUT OFF SW. (S202) in the
receiving position. Press VIDEO INPUT button
to turn TV to the TV mode.
10.Set the BRIGHTNESS Control to the
maximum and COLOUR Control to the centre.
11.Adjust the BLUE and GREEN DRIVE controls
(R252/R253) to obtain proper white-balance
picture in highlight areas.
12.Set the BRIGHTNESS and CONTRAST
Controls to obtain dark grey raster. Then
check the white balance in low brightness. If
the white balance is not proper, retouch the
CUT OFF Controls to obtain a good white
balance in both low and high light areas.
SUB-BRIGHTNESS ADJUSTMENT
1.Tune in a colour programme of Philips pattern.
2. Set the CONTRAST Control to the minimum
and the BRIGHTNESS Control to the centre.
3. Set the COLOUR Control to the minimum.
4. Set the SUB-BRIGHT. Control (R551) so that
the voltage across terminals Y-Z can be 0.2 ±
0.05V with voltmeter and leave the receiver
for five minutes in this state.
5. Watching the picture well, adjust the SUBBRIGHT. Control in the position where the
picture does not show evidence of blooming
in high bright area and not appear too dark in
low bright portion.
6. Check the proper picture variation by rotating
the CONTRAST and BRIGHTNESS Controls
to both extremes.
7. If the picture does not appear dark with the
CONTRAST and BRIGHTNESS Controls
turned to the minimum, or not appear bright
with the controls turned to the maximum,
adjust the SUB-BRIGHT. Control again for the
acceptable picture.
BUS DATA SETTING
1. In the TV set of initial lot of production,
SAA5290ZP/024 is used for QA01. But
replace with SAA5290ZP/032 for servicing.
2. When QA01 only is replaced, it is not
necessary to change the mode data.
3. When memory IC (QA02) is replaced, change
the mode data in the manner below.
ADJUSTMENT METHOD FOR SERVICING
1.OUTLINE
In the service mode, MODE DATA adjustments can be made easily with user remote
control unit. (CT-9689 only)
2.SERVICE MODE OPERATION
2-1. How to Enter the Service Mode
Figure 2
2-2. How to Exit from the ServIce Mode
Exit the service mode by turning the power on/
off with the remote control.
3. ADJUSTMENT IN THE SERVICE MODE
Service Mode Level Adjustments
1) Push + key (simultaneous push) to
appear Mode Data to be adjusted.
2) Adjust with the level UP/DOWN (VOL UP/
DOWN) key.
Example of screen display in level adjustment.
Figure 3
PICTURE I-F ALIGNMENT
GENERAL
Refer to figure 4 for test equipment connection.
PRELIMINARY STEPS
Supply +5 volts to the 5V-1 line.
SIGNAL GENERATOR
Connect to both leads of R101 with signal level
of 75 dBµ, and open the solder-link at IF OUT of
tuner on the Main Board. (See figure 4.)
DVM
Connect to pin #44 of 1C501 on the Main Board
through the detector.
Figure 4. Picture IF Alignment
STEP
Detector Coil
SIGNAL GENERATOR
39.5 MHz CARRIER WAVE (Level 75 dBµ)
ADJUST
T103
REMARKS
1. Supply external DC power (+ 5V) to 5V-1 line.
2. Supply + 8V to pin 36 of IC501.
3. Supply external DC power to + 12V line.
4. Apply test signal to IF input.
5. Adjust T103 so that DC voltage at pin 44 of
IC501 becomes 3.2V ± 0.5V.
After completing the above steps, disconnect
the equipment and re-solder the links on the
Main Board, and adjust the AGC Delay control
(R151) following DELAYED RF AGC ADJUSTMENTS.
Safety Instructions / Service Adjustments / Safety Parts / Main Diagram / Main Diagram Cont’d