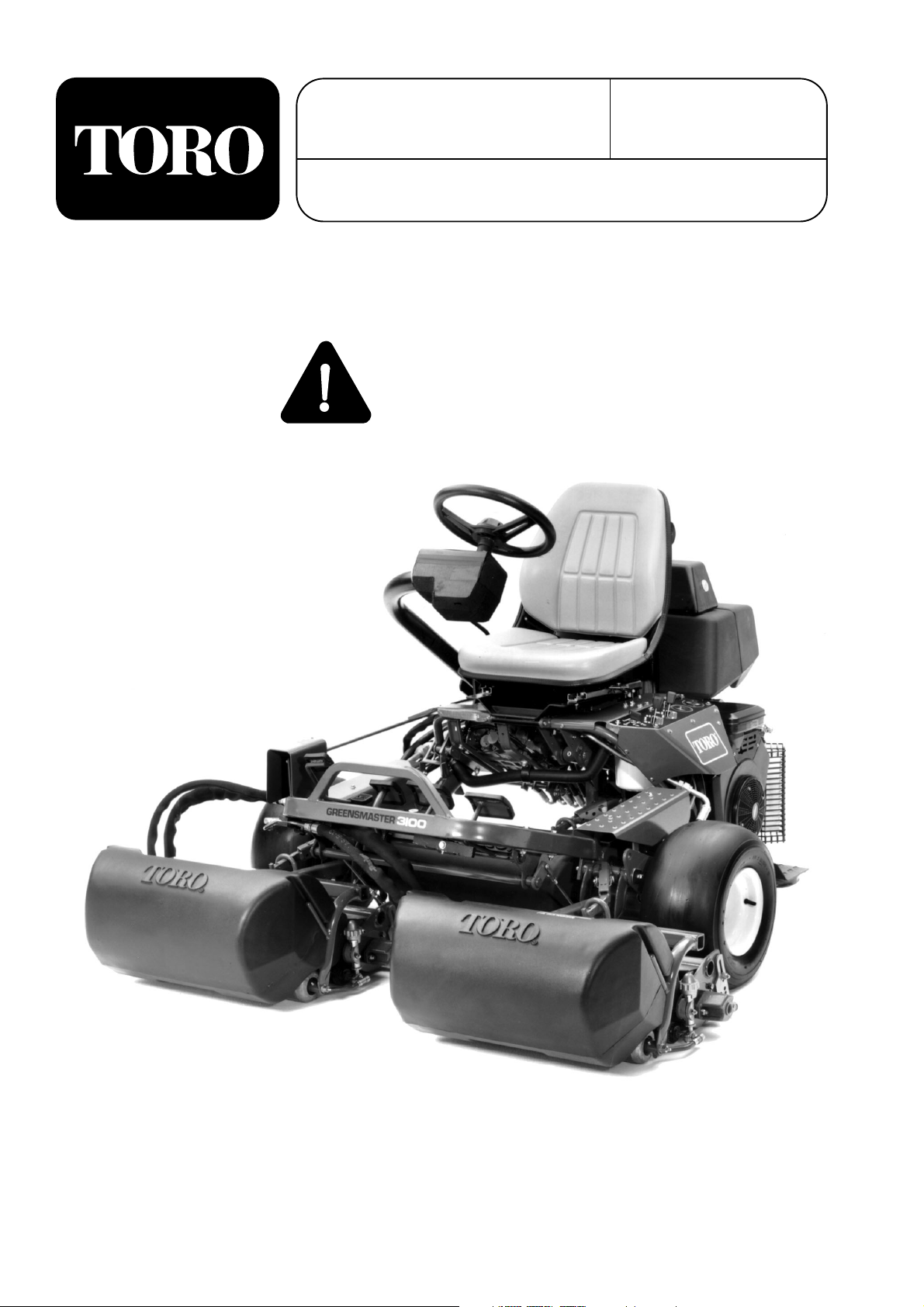
FORM NO. 3324-858
© The Toro Company—2000
To understand this product, and for
safety and optimum performance,
read this manual before starting
operation. Pay special attention to
SAFETY INSTRUCTIONS
highlighted by this symbol.
The safety alert symbol means CAUTION,
WARNING or DANGER—personal safety
instruction. Failure to comply with the
instruction may result in personal injury.
MODEL NO. 04356—200000001 AND UP
®
GREENSMASTER
OPERATOR’S
MANUAL
®
3100
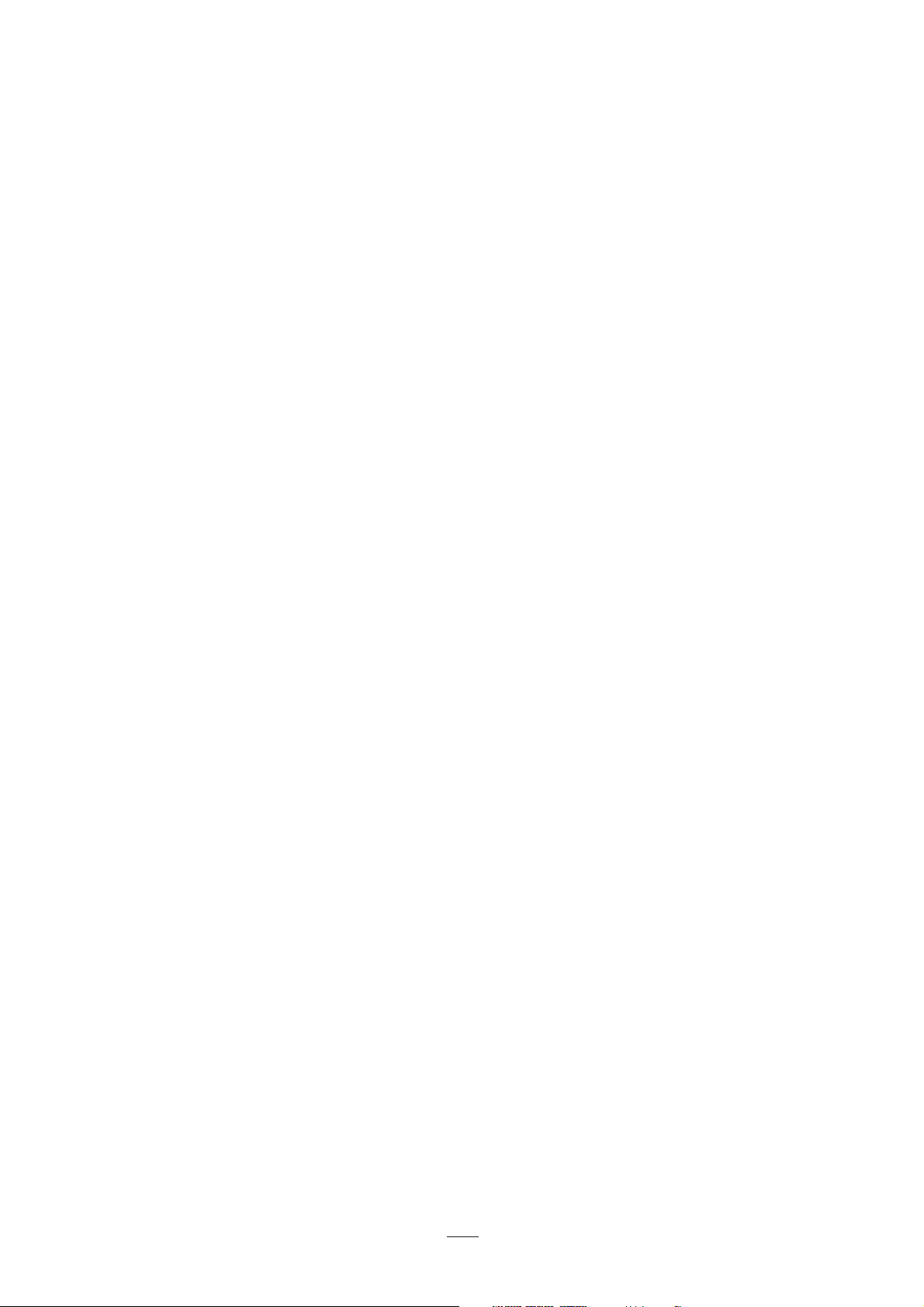
Forward
Table of Contents
2
Forward 2
Table of Contents 2
Safety 3
Sound & Vibration Levels 5
Symbol Glossary 6
Specifications 9
Set-Up 10
Install the Cutting Units 10
Installing Cutting Units 11
Rear Ballast 12
Before Operating 13
Check the Engine Oil 13
Fill the Gas Tank 13
Check the Hydraulic System 14
Tire Pressure 15
Check Wheel Nut Torque 15
Controls 16
Operating Instructions 18
Break-In Period 18
Starting Instructions 18
Check the Interlock System Operation 18
Check the Leak Detector Operation 20
Preparing the Machine for Mowing 21
Training Period 21
Before Mowing 21
Mowing Procedures 21
Leak Detector Operation 22
Transport Operation 23
Inspection and Clean-Up After Mowing 23
Maintenance 24
Maintenance Schedule 24
Lubrication 26
Changing the Engine Oil and Filter 28
Servicing the Air Cleaner 28
Adjusting the Throttle Control 29
Adjusting the Choke Control 29
Adjusting Carburetor and Speed Control 29
Replacing Spark Plugs 30
Fuel Filter Replacement 30
Changing the Hydraulic Oil and Filter 31
Checking Hydraulic Hoses and Lines 31
Brake Adjustment 32
Rear Camshaft Adjustment 32
Adjusting the Lift and Mow Pedal Height 33
Leveling the Lift and Mow Pedals 33
Adjusting the Traction Pedal 33
Adjusting the Cutting Unit Lift/Drop 34
Adjusting the Lift Cylinders 35
Seat Switch Maintenance 35
Traction Switch Maintenance 35
Mow/Lift Switch Maintenance 36
Adjusting the Traction Return Linkage 36
Battery Care 36
Troubleshooting 38
Storage 44
Identification and Ordering 44
The Greensmaster 3100 was developed to provide an efficient, trouble-free and time-saving method of mowing
high-quality turf on the finest greens. The latest concepts in engineering, design and safety have been
incorporated into this machine, along with the highest quality parts and workmanship. This product will provide
excellent service if you follow proper operation and maintenance practices.
We know, because you have purchased the industry leader in mowing excellence, that future performance and
dependability are of prime importance. Therefore, this manual should be read by you and all others involved
with the Greensmaster 3100 to make sure that safety, operation and maintenance procedures are followed.
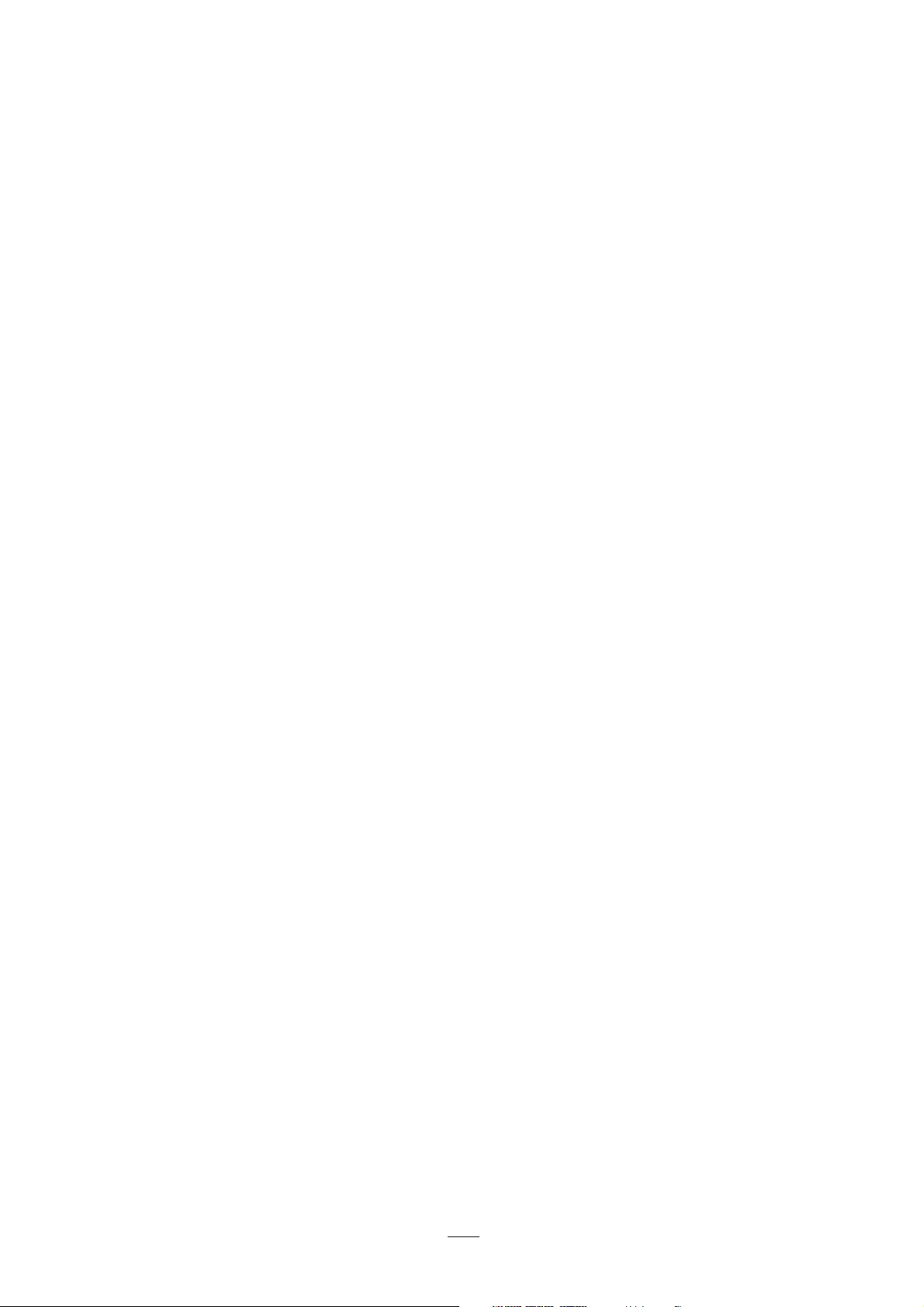
Safety
Training
1. Read the instructions carefully. Be familiar with
the controls and the proper use of the equipment.
2. Never allow children or people unfamiliar with
these instructions to use the lawn mower. Local
regulations may restrict the age of the operator.
3. Never mow while people, especially children, or
pets are nearby.
4. Keep in mind that the operator or user is
responsible for accidents or hazards occurring to
other people or their property.
5. Do not carry passengers.
6. All drivers should seek and obtain professional
and practical instruction. Such instruction should
emphasize:
• the need for care and concentration when
working with ride-on machines;
• control of a ride-on machine sliding on a
slope will not be regained by the application
of the brake. The main reasons for loss of
control are:
– insufficient wheel grip;
– being driven too fast;
– inadequate braking;
– the type of machine is unsuitable for its
task;
– lack of awareness of the effects of
ground conditions, especially slopes;
– incorrect hitching and load distribution.
Preparation
1. While mowing, always wear substantial footwear
and long trousers. Do not operate the equipment
when barefoot or wearing open sandals.
2. Thoroughly inspect the area where the equipment
is to be used and remove all objects which may
be thrown by the machine.
3. WARNING—Petrol is highly flammable.
• Store fuel in containers specifically
designed for this purpose.
• Refuel outdoors only and do not smoke
while refueling.
• Add fuel before starting the engine. Never
remove the cap of the fuel tank or add petrol
while the engine is running or when the
engine is hot.
• If petrol is spilled, do not attempt to start the
engine but move the machine away from the
are of spillage and avoid creating any source
of ignition until petrol vapors have
dissipated.
• Replace all fuel tanks and container caps
securely.
4. Replace faulty silencers.
Operation
1. Do not operate the engine in a confined space
where dangerous carbon monoxide fumes can
collect.
2. Mow only in daylight or in good artificial light.
3. Before attempting to start the engine, disengage
all blade attachment clutches and shift into
neutral.
4. Do not use on slopes of more than:
• Never mow side hills over 5°
• Never mow uphill over 10°
• Never mow downhill over 15°
5. Remember there is no such thing as a “safe”
slope. Travel on grass slopes requires particular
care. To guard against overturning:
• do not stop or start suddenly when going up
or downhill;
• engage the clutch slowly, and always keep
the machine in gear, especially when
travailing downhill;
• machine speeds should be kept low on
slopes and during tight turns;
3
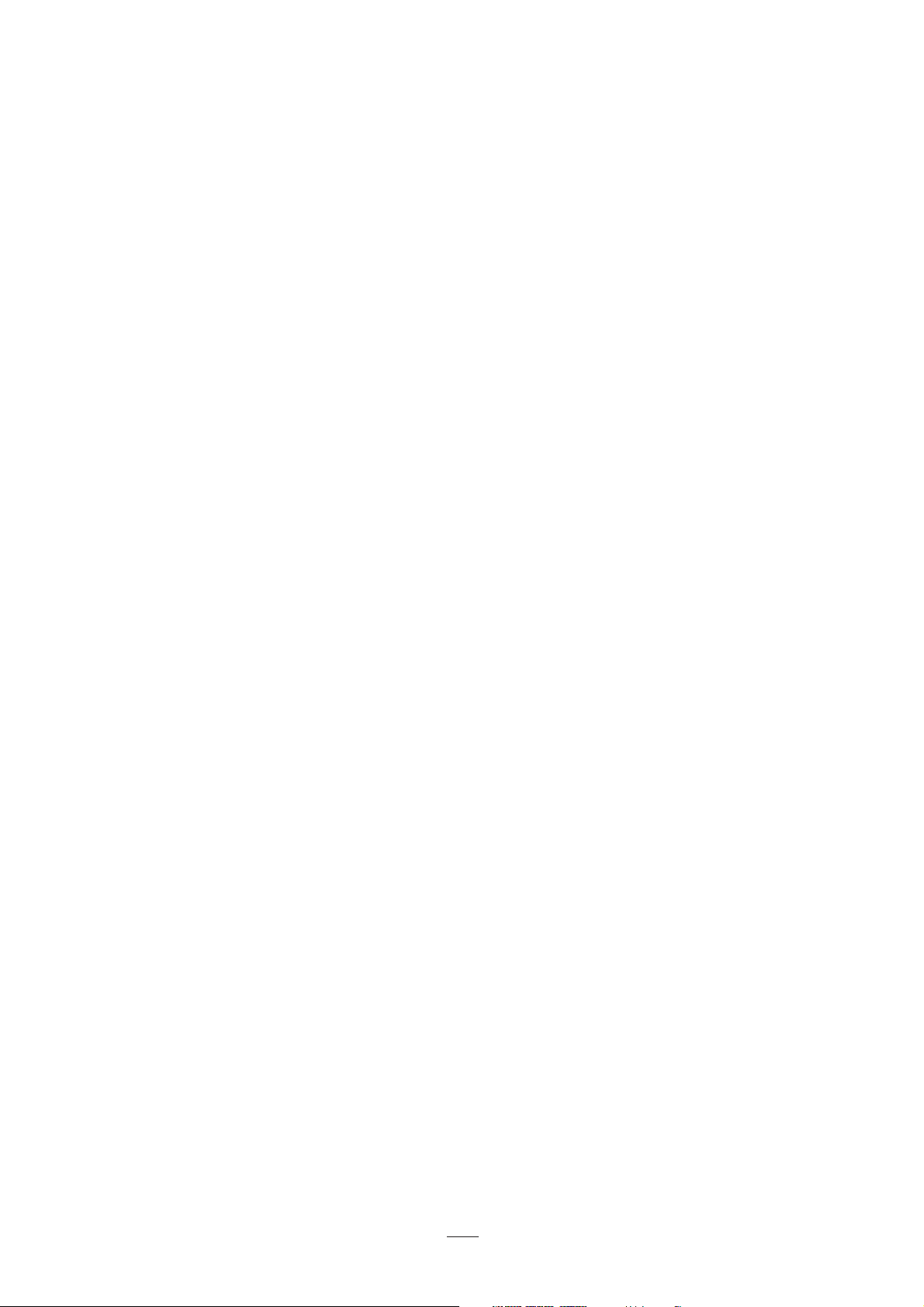
4
• stay alert for bumps and hollows and other
hidden hazards;
• never mow across the face of the slope,
unless the lawn mower is designed for this
purpose.
6. Use care when pulling loads or using heavy
equipment.
• Use only approved drawbar hitch points.
• Limit loads to those you can safely control.
• Do not turn sharply. Use care when
reversing.
• Use counterweight(s) or wheel weights
when suggested in the instruction handbook.
7. Watch out for traffic when crossing or near
roadways.
8. Stop the blades rotating before crossing surfaces
other than grass.
9. When using any attachments, never direct
discharge of material toward bystanders nor
allow anyone near the machine while in
operation .
10. Never operate the lawn mower with defective
guards, shields or without safety protective
devices in place.
11. Do not change the engine governor settings or
overspeed the engine. Operating the engine at
excessive speeds may increase the hazard of
personal injury.
12. Before leaving the operator’s position:
• Disengage the power take-off and lower the
attachments;
• Change into neutral and set the parking
brake;
• Stop the engine and remove the key.
13. Disengage the drive to attachments when
transporting or not in use.
14. Stop the engine and disengage the drive to the
attachment
• Before refueling;
• Before removing the grass catcher;
• Before making height adjustments unless
the adjustment can be made from the
operator’s position.
• Before clearing blockages;
• Before checking, cleaning or working on the
lawnmower;
• After striking a foreign object. Inspect the
lawnmower for damage and make repairs
before restarting and operating the
equipment.
15. Reduce the throttle setting during engine runout
and, if the engine is provided with a shutoff
valve, turn the fuel off at the conclusion of
mowing.
Maintenance and Storage
1. Keep all nuts, bolts and screws tight to be sure
the equipment is in safe working condition.
2. Never store the equipment with petrol in the tank
inside a building where fumes may reach an open
flame or spark.
3. Allow the engine to cool before storing in any
enclosure.
4. To reduce the fire hazard, keep the engine,
silencer, battery compartment and petrol storage
area free of grass, leaves, or excessive grease.
5. Check the grass catcher frequently for wear or
deterioration.
6. Replace worn or damaged parts for safety.
7. If the fuel tank has to be drained, this should be
done outdoors.
8. Be careful during adjustment of the machine to
prevent entrapment of the fingers between
moving blades and fixed parts of the machine.
9. On multi-bladed machines, take care as rotating
one blade can cause other blades to rotate.
10. When the machine is to be parked, stored or left
unattended, lower the cutting means unless a
positive mechanical lock is used.
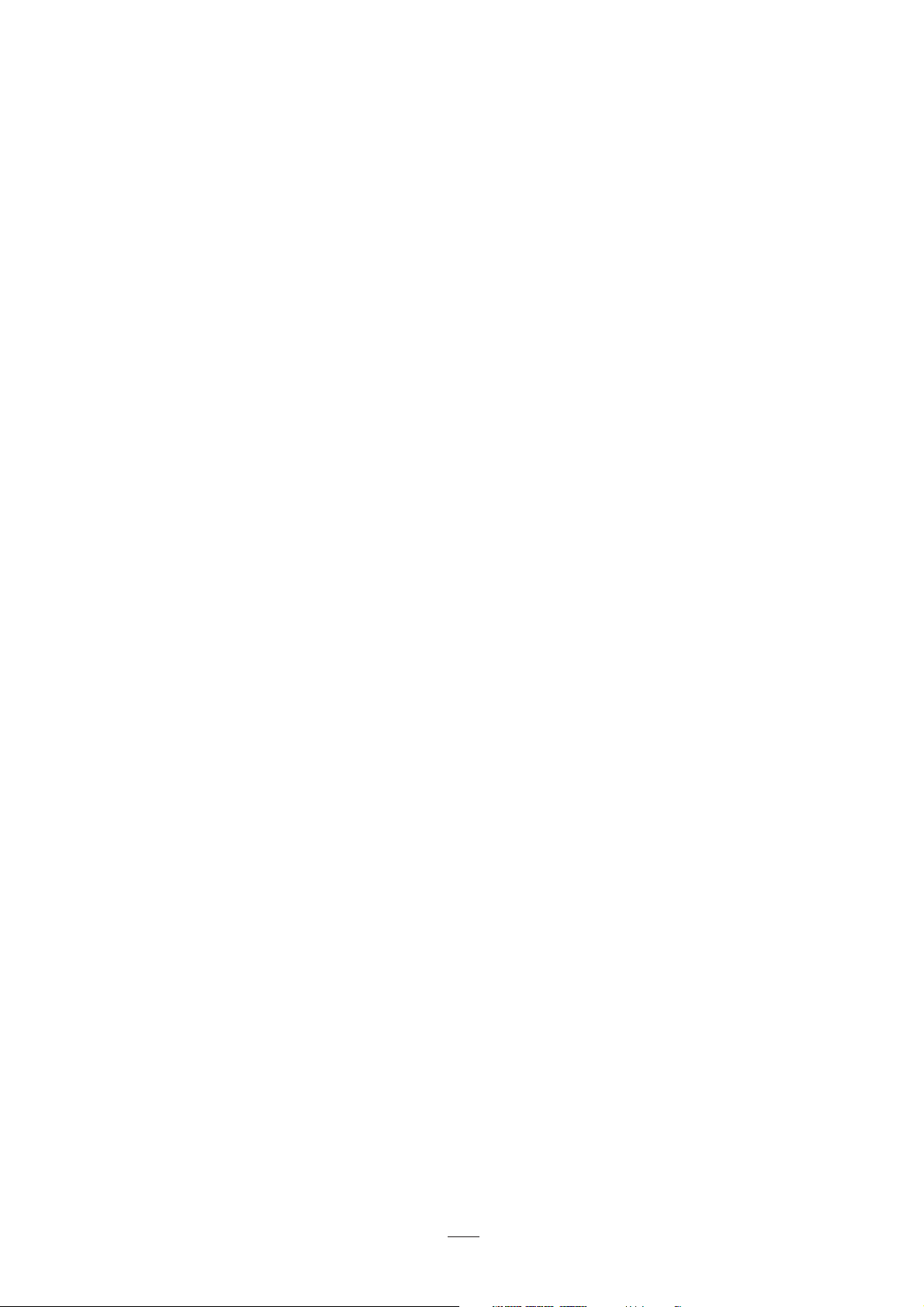
Sound & Vibration Levels
Sound Levels
This unit has an equivalent continuous A-weighted
sound pressure at the operator ear of: 86 dB(A), based
on measurements of identical machines per
84/538/EEC.
This unit has a sound power level of 100 dB(A)/1pW,
based on measurements of identical machines per
procedures outlined in Directive 79/113/EEC and
amendments.
Vibration Levels
This unit has a vibration level of 2.5 m/s2at the
posterior, based on measurements of identical
machines per ISO 2631 procedures.
This unit does not exceed a vibration level of 0.5 m/s
2
at the posterior based on measurements of identical
machines per ISO 2631 procedures.
5
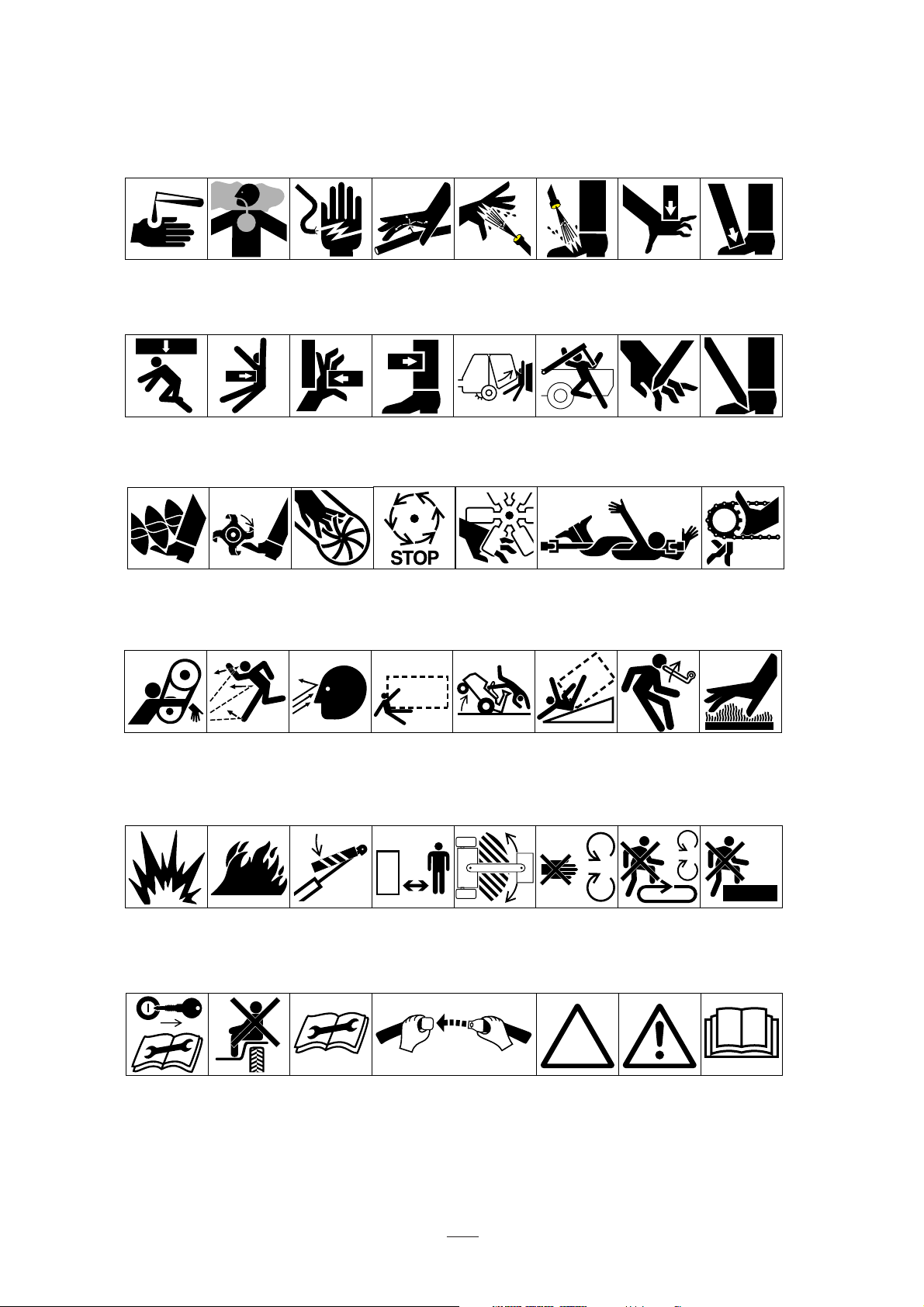
Caustic liquids,
chemical burns to
fingers or hand
Crushing of
whole body,
applied from
above
Cutting or
entanglement of
foot, rotating auger
Poisonous
fumes or toxic
gases, asphyxiation
Crushing of
torso, force
applied from side
Severing of
foot, rotating
knives
Electrical shock,
electrocution
Crushing of fingers
or hand/, force
applied from side
Severing of
fingers or hand,
impeller blade
High pressure
fluid, injection
into body
force applied
from side
Wait until all
machine
components have
completely stopped
before touching them
High pressure
spray, erosion of
flesh
Crushing of
whole body
Severing of
fingers or hand,
engine fan
High pressure
spray, erosion of
flesh
Crushing of
head, torso and
arms
Whole body entanglement,
implement input drive line
Crushing of
fingers
or hand,
force
applied from
above
Cutting of
fingers or hand
Crushing of
toes or foot, force
applied from above
Cutting of footCrushing of leg,
Fingers or
hand entanglement, chain drive
Hand & arm
entanglement,
belt drive
Explosion Fire or open
Shut off engine
& remove key before
performing maintenance or repair work
Thrown or flying objects, whole
body exposure
flame
Riding on this
machine is allowed
only on a passenger seat & only if the
driver’s view is not
hindered
Thrown or
flying objects,
face exposure
Secure lifting
cylinder with locking
device before getting
in hazardous area
Consult
technical manual
for proper service
procedures
Runover/backover, (relevant
machine to appear
in dashed box)
Stay a safe
distance from
the machine
Fasten seat belts Safety alert
Machine tipping,
riding mower
Stay clear of
articulation area
while engine is
running
Machine rollover,
ROPS (relevant
machine to appear
in dashed box)
Stored energy
hazard, kickback
or upward motion
Do not open
or remove safety
shields while
engine is
running
triangle
Do not step on
loading platform if
PTO is connected to tractor
& engine is running
outline safety
alert symbol
Hot surfaces,
burns to fingers
or hands
Do not step
Read operator’s
manual
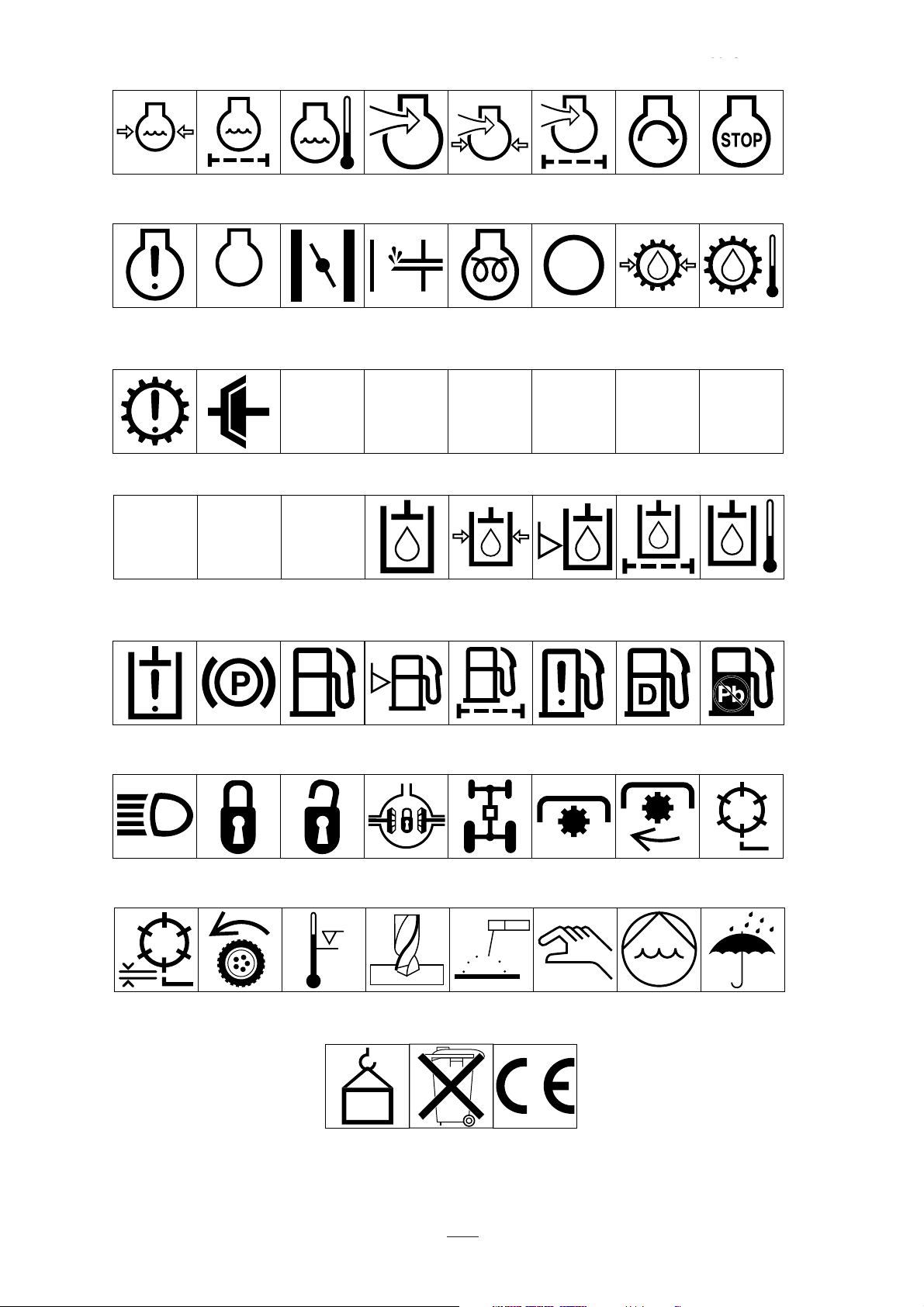
Engine coolant
pressure
Engine coolant f
ilter
n/min
Engine failure/
malfunction
Transmission
failure/malfunction
Engine rotational
speed/frequency
Clutch Neutral High Low Forward Reverse Park
231
First gear Second gear
Engine
lubricating oil
pressure
Choke Primer (start aid) Electrical preheat
Engine intake/
combustion air
Engine intake/
combustion air
pressure
(low temperature
start aid)
Engine intake/
air filter
Transmission oil Transmission oil
Engine start Engine stop
pressure
Transmission oil
temperature
NHLFRP
Third gear (other #'s
may be used until
the maximum # of forward gears is reached.)
Hydraulic oil Hydraulic oil
Hydraulic oil
pressure
Hydraulic oil level Hydraulic oil filter
temperature
Hydraulic oil
failure/malfunction
Headlights Lock Unlock Differential lock 4-Wheel drive Pow er Take-Off Power Take-Off,
Reel cutting
element, height
adjustment
Parking brake Fuel
Traction Above working
temperature range
0430 weight Do not dispose
Fuel level Fuel filter Fuel system
Drilling Manual metal arc
welding
in the garbage
failure/malfunction
Manual 0356 Water pump
CE logo
Diesel fuel Unleaded fuel
rotational speed
Reel cutting
element
0626 Keep dry
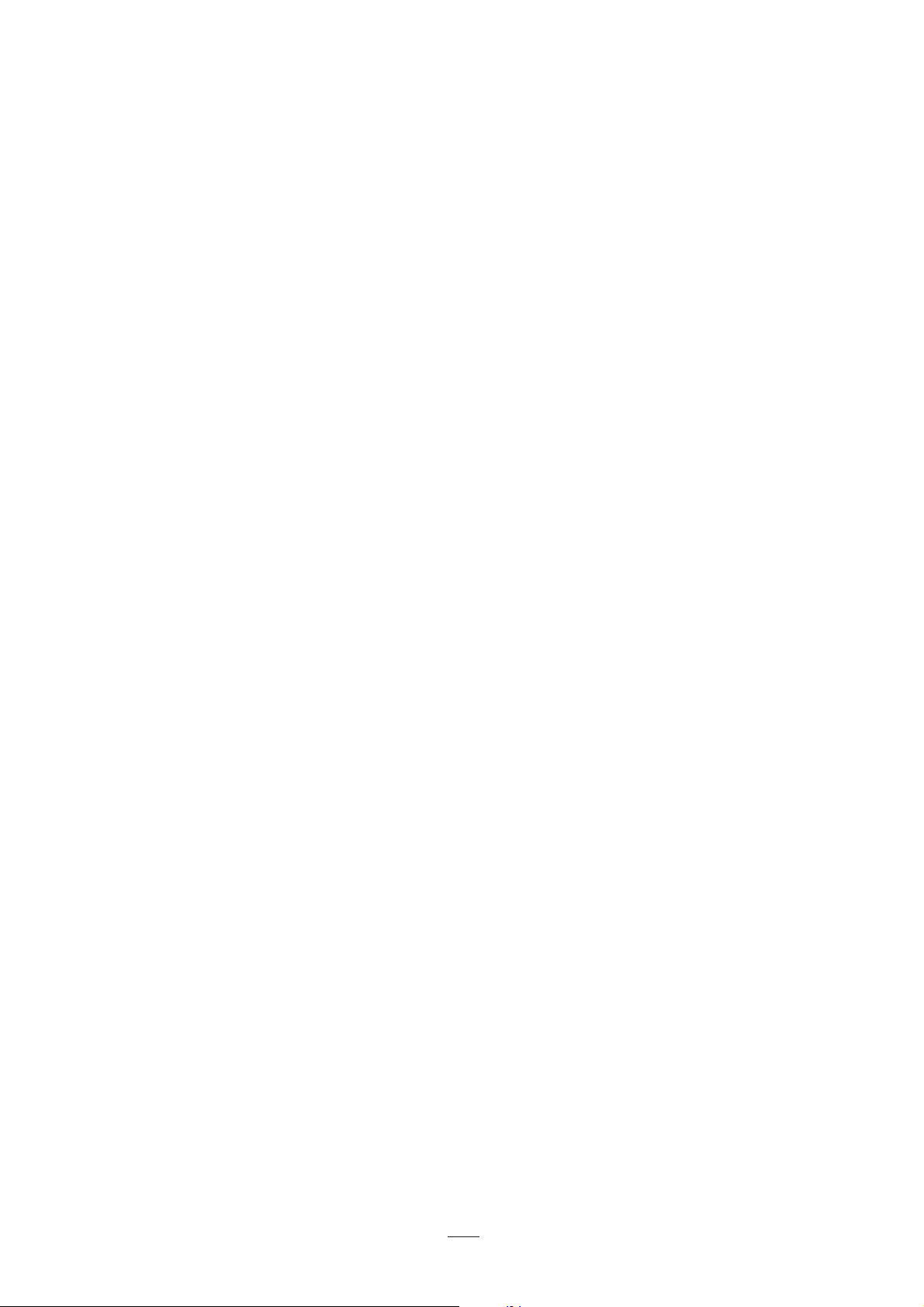
9
Configuration: Tricycle vehicle with the front two
wheels providing drive and the rear wheel providing
steering. The operator sits in the center over the No. 1
cutting unit with the No. 2 & 3 cutting units in front
of the vehicle.
Power: 4-cycle gasoline engine, electric start, with
output of 13.4 kW @3,600 rpm. Maximum no-load
governed engine speed is 2,900 rpm.
Traction: All-hydraulic drive, consisting of multiple
stack pump valve, valve, and two orbital gear motors
to drive the front wheels.
Cutting Units: All-hydraulic drive, consisting of
three gear pump sections, three valve sections and
three gear motors that drive the reels.
Hydraulic Valve: Five spool sections: the first 3
spool sections control the lowering, mowing and lift
functions of the cutting units. The spools moved out
provide lowering and MOW operation; moved in they
provide LIFT operation. The number 4 spool section
controls the traction functions, N (Neutral), 1 (Mow),
and 2 (transport). The number 5 spool section
controls forward and reverse traction.
Tire Pressure :
• 55–83 kPa—front
• 55–103 kPa—rear
Brakes: 15 cm drum-type mechanical with rack and
pawl lock for parking.
Hydraulic Filter: 10-micron, cartridge type.
Hydraulic Oil Reservoir: 32.2 liter capacity with
internal baffle. Type fluid: Mobil 15M. Red dye is
added at the factory.
Gas Tank: 28.4 liter capacity.
Fuel Filter: In-line type.
Fuel Pump: Vacuum pulse type.
Seat Adjustment: 17.8 cm (forward and rearward).
Wheel Bearings:
Drive Wheels: Needle provided in wheel motors.
Rear Caster Wheels: Timken tapered roller
Electrical & Instrumentation: The engine contains a
18-amp alternator; the circuit is fused at 20 amps.
Instruments include ammeter and hour meter. An
accessory terminal is available at the leak detector test
switch if attachment of headlights is desired.
Battery: 12-Volt, lead acid, 32-amp. hour. Size:
Length—18.4cm, Width—12.4cm, height—15.2cm.
General Specifications:
Width of Cut: 149.9 cm
Wheel Tread: 123.3 cm
Wheel Base: 119 cm
Overall Length: 229 cm
Overall Width: 177 cm
Overall Height: 123 cm
Net Weight (Wet): 381 kg
Shipping Weight (In carton): 471 kg
Speeds:
1st —6.1 kmh
2nd—13 kmh
Rev.—3.1 kmh
Reels: 1,975 rpm (approximately)
Clip:
0.46 cm (11-Blade Cutting Unit)
0.64 cm (8-Blade Cutting Unit)
1.0 cm (5-Blade Cutting Unit)
Specifications and design subject to change
without notice
.
Specifications
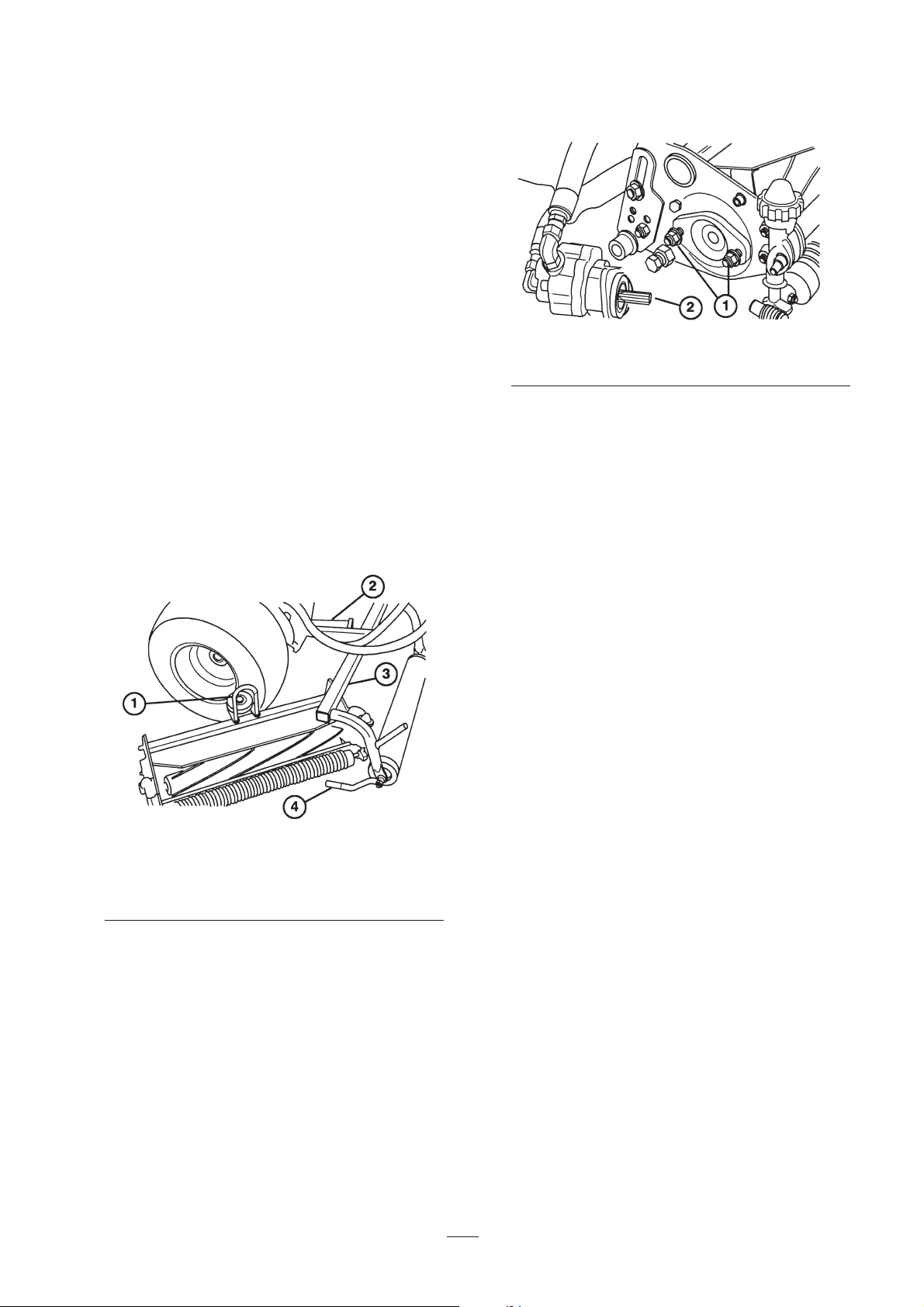
10
Install the Cutting Units
For Cutting Unit Models 04404, 04406, 04408
04450 and 04468.
Note: When sharpening, setting height of cut, or
performing other maintenance procedures on the
cutting units, store the cutting unit reel motors in
support tubes on the front of the frame to prevent
damage to the hoses.
1. Remove the cutting units from their cartons.
Assemble and adjust according to the operator’s
manual for the cutting units. Use the height
gauge bar from the loose parts kit to adjust height
of cut.
2. Slide the cutting units under the pull frames and
position the hoop on the top of cutting units over
the lift arms (Fig. 1).
Figure 1
1. Hoop
2. Lift arm
3. Pull frame
4. Pull arm
3. Assemble the mount nuts for the reel drive motor
to each cutting unit. Leave approximately 1.2cm
of threads exposed on each mount stud (Fig. 2).
Figure 2
1. Motor mount nuts
2. Coat with grease
4. Remove the protective covers from the cutting
units and the reel drive motor shafts. Coat the
spline shaft of the motor with clean grease and
install the motor by turning the motor clockwise
so the motor flanges clear the studs. Rotate the
motor counterclockwise until the flanges encircle
the studs, then tighten the mounting nuts (Fig. 2).
Note: Retain the protective covers for the cutting
units. Install them whenever the reel drive
motors are removed to protect the cutting unit
bearings from contamination.
5. Slide the sleeve back on the ball joint and rotate
the pull arm down so the socket fits over the ball
stud. Release the sleeve so it slides over the stud
and locks the assemblies together (Fig. 4).
6. Mount the baskets on the pull frames, loosen the
jam nuts on the pull arms and adjust the ball
sockets until there is 6–11mm clearance between
the lip of the basket and the reel blades (Fig. 3).
Note: This prevents the basket from tipping the
cutting unit forward, causing the hoop to come
off the lift arm while mowing.
Be sure the basket lips are equidistant from the
reel blades all across each reel. If the basket is
too close to the reel, it is possible for the reel to
contact the basket when the cutting unit is raised
off the ground.
Set-Up
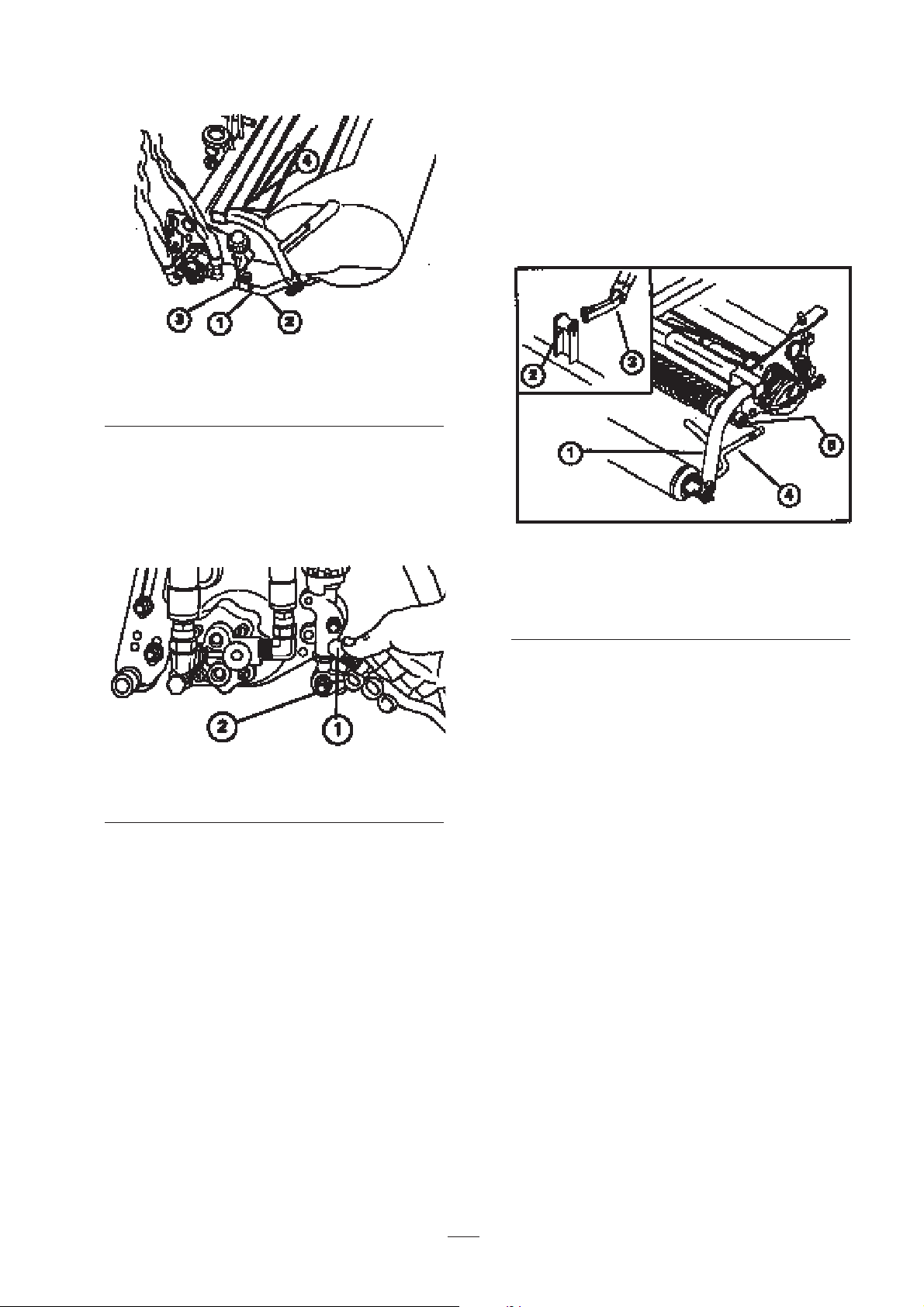
11
Figure 3
1. Jam nut
2. Pull arm
3. Ball joint-adjust for clearance
4. 6–11mm clearance
7. Align the sockets in the ball joints so the open
side of the socket is centered toward the ball
stud. Tighten the jam nuts to secure the sockets
in position (Fig. 3).
Figure 4
1. Slide back to mount
2. Ball stud
Installing Cutting Units
For Cutting Unit Models 04480, 04481, 04482, and
04483.
Note: When sharpening, setting height of cut or
performing other maintenance procedures on the
cutting units, store the cutting unit reel motors in
support tubes on the front of the frame to prevent
damage to the hoses.
1. Remove the cutting units from their cartons.
Assemble and adjust according to the operator’s
manual for the cutting units. Use the height
gauge bar from the loose parts kit to adjust height
of cut.
2. Mount a washer and ball stud to each end of the
front roller on the cutting units (Fig. 5).
3. Slide the cutting unit under the pull frame while
hooking the lift roller onto the lift arm (Fig. 5).
Figure 5
1. Pull frame
2. Lift roller
3. Lift arm
4. Pull arm
5. Ball stud
4. Slide the sleeve back on the ball joint and rotate
the pull arm down so the socket fits over the ball
stud. Release the sleeve so that it slides over the
stud and locks the assemblies together (Fig. 6).
5. Mount the baskets on the pull frames, loosen the
jam nuts on the pull arms and adjust the ball
sockets until there is 6–11mm clearance between
the lip of the basket and the reel blades or front
shield.
Note: This prevents the basket from tipping the
cutting unit forward causing the lift roller to
come off the lift arm while mowing.
Be sure the basket lips are equidistant from the
reel blades all across each reel. If the basket is
too close to the reel, it’s possible for the reel to
contact the basket when the cutting unit is raised
off the ground.
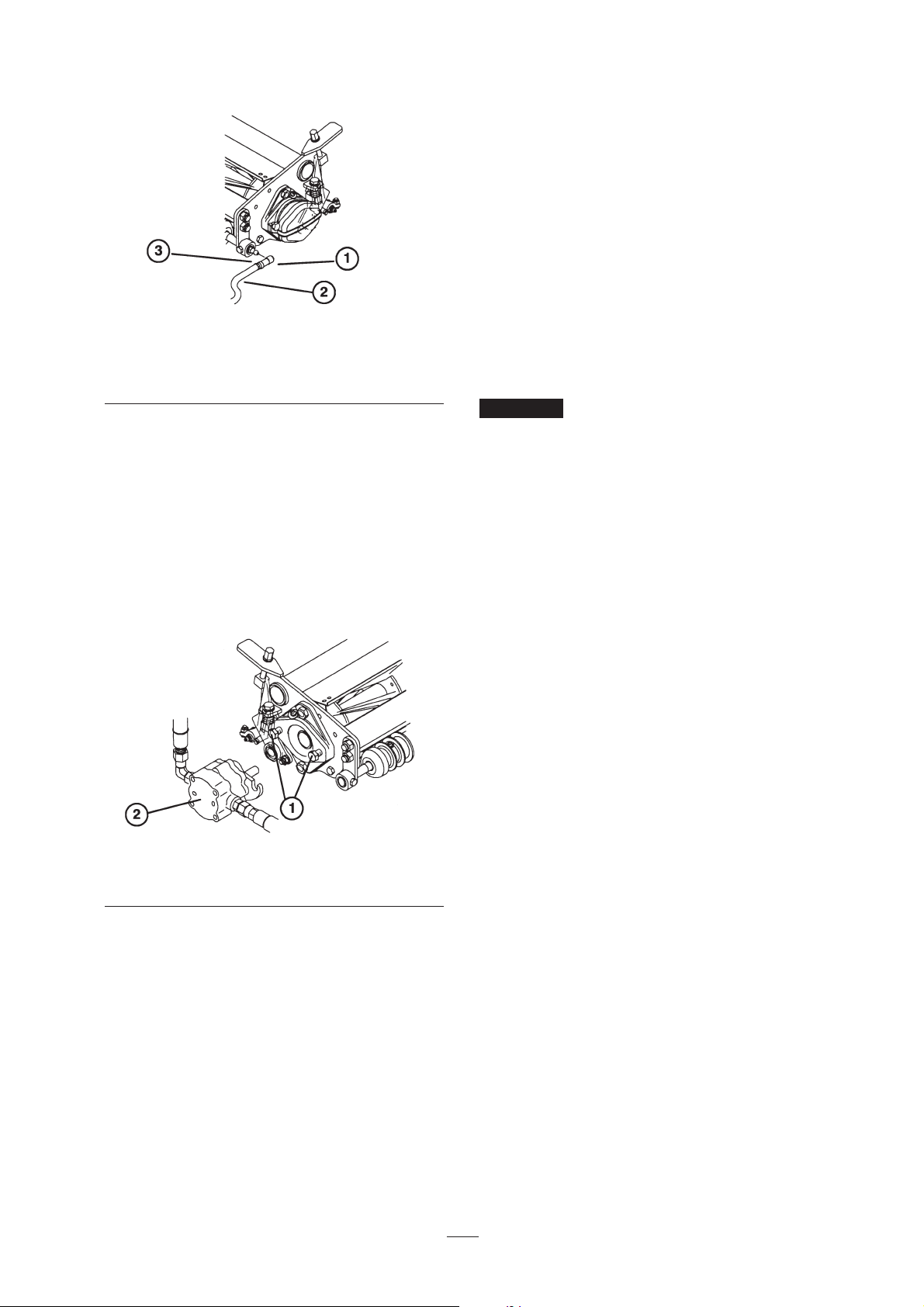
12
Figure 6
1. Ball joint
2. Pull arm
3. Jam nut
6. Align the sockets in the ball joints so the open
side of the socket is centered toward the ball
stud. Tighten the jam nuts to secure the sockets
in position (Fig. 6).
7. Assemble the mounting capscrews for the reel
drive motor to each cutting unit. Leave
approximately 1.2cm of thread exposed on each
mounting capscrew (Fig. 7).
Figure 7
1. Capscrews
2. Drive motor
8. Remove the protective covers from the cutting
units and the reel drive motor shafts.
Note: Retain the protective covers for the cutting
units. Install them whenever the reel drive
motors are removed to protect the cutting unit
bearings from contamination.
9. Using a hand pump grease gun, fill the cavity at
the end of the cutting unit with #2 general
purpose grease.
10. Coat the spline shaft of the motor with clean
grease and install the motor by rotating the motor
clockwise so that the motor flanges clear the
studs. Rotate the motor counterclockwise until
the flanges encircle the studs, then tighten the
mounting capscrews (Fig. 7).
Rear Ballast
This unit complies with the ANSI B71.4-1999
Standard when 40 lbs. of calcium chloride ballast is
added to the rear wheel.
If a puncture occurs in a tire with
calcium chloride, remove the unit from the turf area as
quickly as possible. To prevent possible damage to
turf, immediately soak the affected area with water.
Important
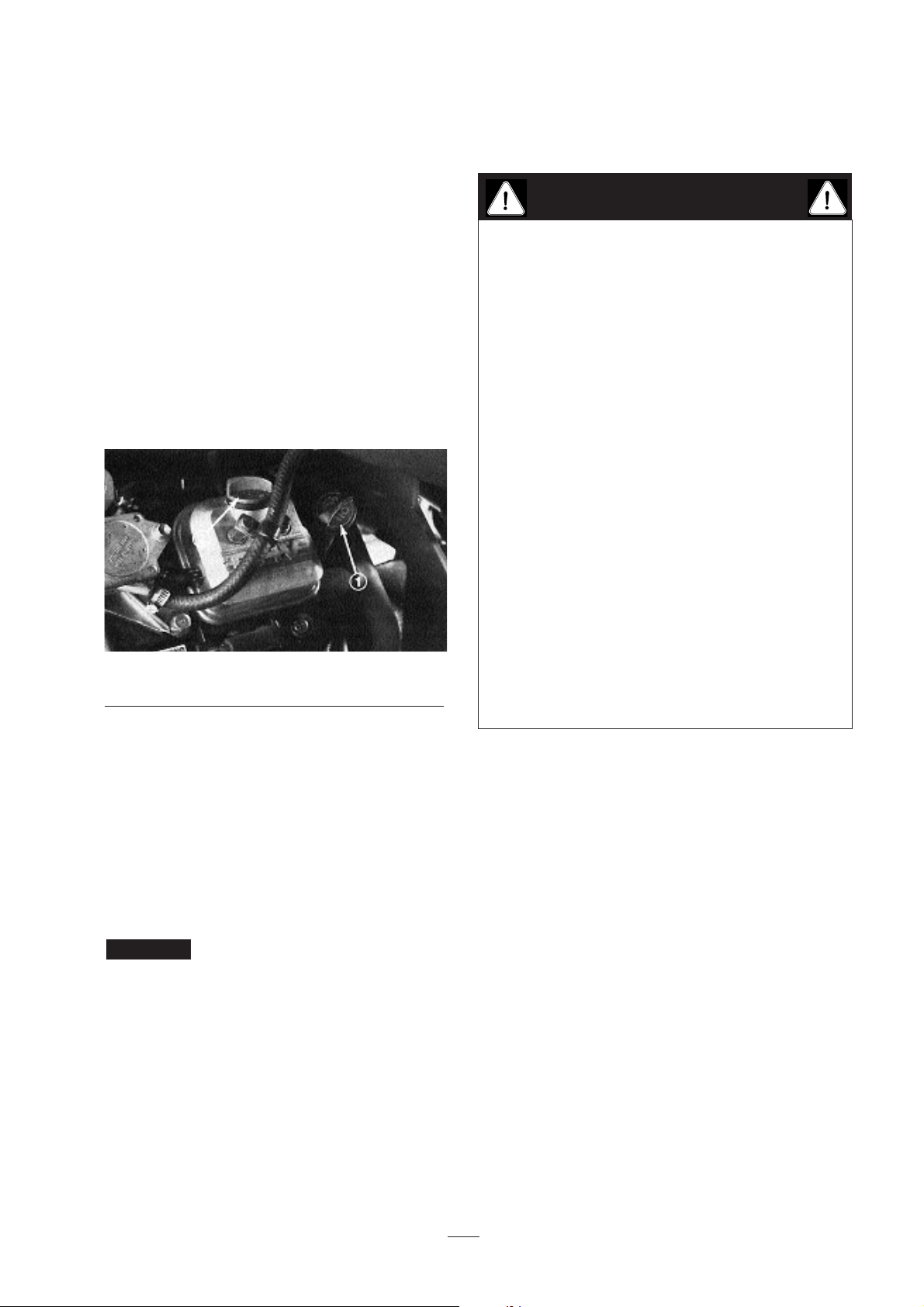
13
Check the Engine Oil
The engine is shipped with 1.7 liter (with filter) of oil
in the crankcase; however, the level of oil must be
checked before and after you first start the engine.
1. Position the machine on a level surface.
2. Unscrew the dipstick and wipe it with a clean
cloth. Screw the dipstick into the tube and make
sure it is seated fully. Unscrew the dipstick and
check the oil level. If it is low, remove the filler
cap from the valve cover and add enough oil to
raise the level to the FULL mark on the dipstick.
Figure 8
1. Dipstick
2. Fill Cap
3. The engine uses any high-quality detergent oil
having the American Petroleum Institute —
API—service classification SC, SD, SE, SF or
SG. Recommended viscosity (weight) is SAE
30.
4. Pour the oil into the opening in the valve cover
until the oil level is up to the FULL mark on the
dipstick. Add the oil slowly and check the level
often during this process. DO NOT OVERFILL.
Check the oil level every 8
operating hours or daily. Initially change the oil
and filter after the first 8 hours of operation; after
that—under normal conditions—change the oil
after every 50 hours and the filter after every 100
hours. However, change the oil more often when
you operate the engine in extremely dusty or
dirty conditions.
5. Install the dipstick firmly in place.
Fill the Gas Tank
THE TORO COMPANY STRONGLY
RECOMMENDS THE USE OF CLEAN, FRESH
UNLEADED REGULAR GASOLINE IN TORO
GASOLINE-POWERED PRODUCTS. UNLEADED
GASOLINE BURNS CLEANER, EXTENDS
ENGINE LIFE, AND PROMOTES GOOD
STARTING BY REDUCING THE BUILD-UP OF
COMBUSTION CHAMBER DEPOSITS. LEADED
GASOLINE CAN BE USED IF UNLEADED IS
NOT AVAILABLE.
NOTE: Never use methanol, gasoline containing
methanol, gasohol containing more than 10% ethanol,
gasoline additives, premium gasoline, or white gas
because the engine fuel system damage could result.
1. Fill the gasoline tank to the bottom of the filler
neck. DO NOT OVERFILL. Install the cap and
tighten it securely in place.
Important
Before Operating
Because gasoline is flammable, use caution when
storing or handling lt. Do not fill the fuel tank
while the engine is running, or hot, or when the
machine is in an enclosed area. Vapors may
build up and be ignited by a spark or flame
source many feet away. DO NOT SMOKE while
filling the fuel tank to prevent the possibility of
an explosion. Always fill the fuel tank outside
and wipe up any spilled gasoline before starting
the engine. Use a funnel or spout to prevent
spilling gasoline before starting the engine and
fill the tank to about 1 inch from the top of the
tank, not the filler neck. Store gasoline in a clean
safety-approved container and keep the cap in
place on the container. Keep gasoline in a cool,
well-ventilated place—never in an enclosed area
such as a hot storage shed. To assure volatility,
do not buy more than a 30-day supply of
gasoline. Gasoline is a fuel for internal
combustion engines; therefore, do not use it for
any other purpose. Since many children like the
smell of gas, keep it out of their reach because the
fumes are explosive and dangerous to inhale.
DANGER
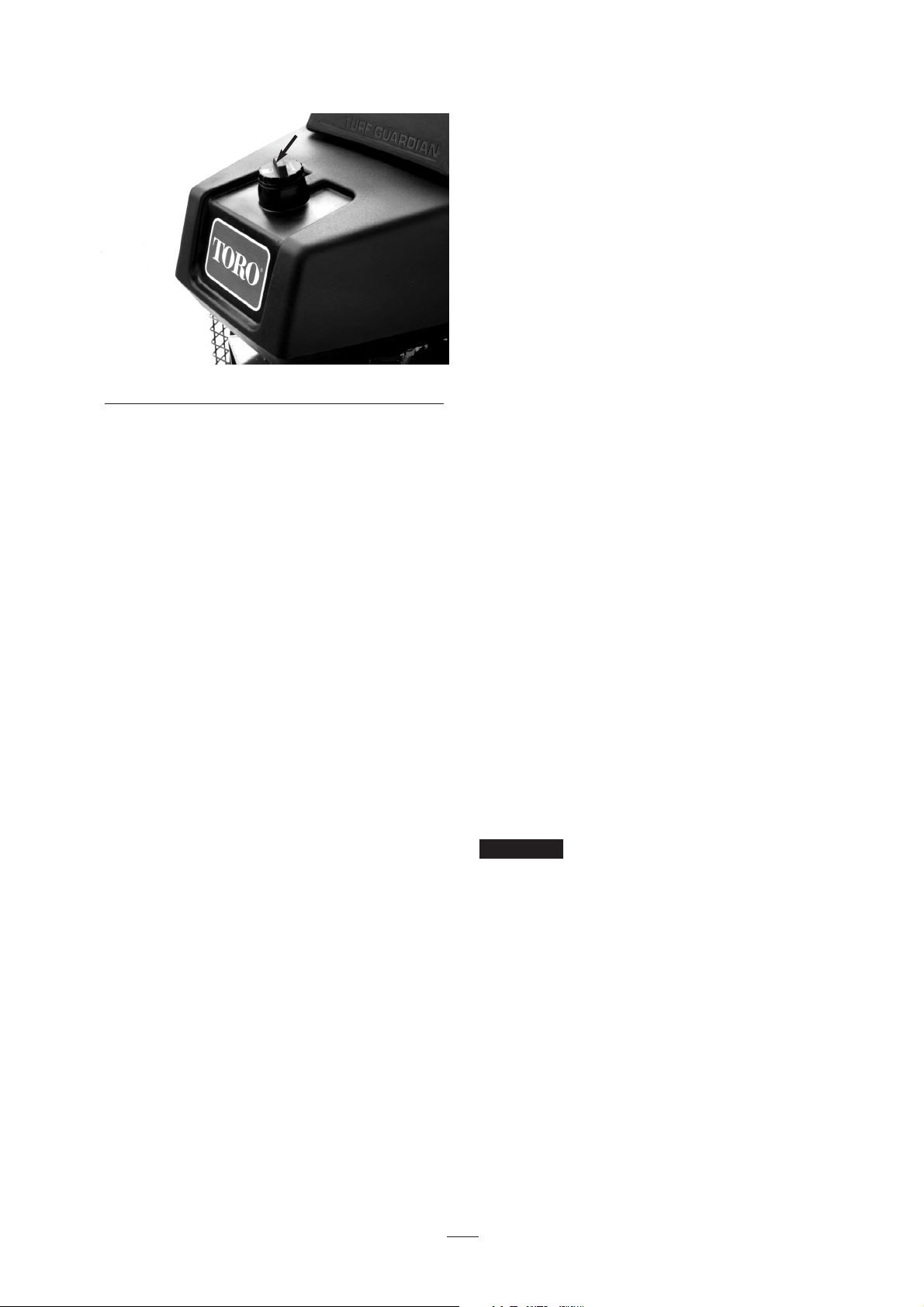
14
Figure 9
1. Fuel tank cap
Check the Hydraulic System
The hydraulic system is designed to operate on antiwear hydraulic fluid. The machine’s reservoir is filled
at the factory with 8.5 gallons (32.2 l) of Mobil 15M
hydraulic fluid. Check the level of hydraulic fluid
before the engine is first started and daily
thereafter.
Group 1 Hydraulic Fluid (Moderate climate—
average duty)
Note: The fluids within this group are
interchangeable.
ISO VG 46/48 multi-viscosity anti-wear hydraulic
fluid
Mobil DTE 15M
Amoco Rycon Premium ISO 46
Castrol AWH 46
Conoco Hydroclear AW MV68
Gulf Harmony HVI 46 AW
Kendall Hyken Golden MV SAE 5W-20
Pennzbell AWX MV46
Phillips Magnus A KV 5W-20
Shell Tellus T 46
Sunoco Sun Hyd. Oil 2105
Texaco Rando HDZ 46
Universal Tractor Hydraulic Fluid
Mobil Mobilfluid 424
Amoco 1000 Fluid
Chevron Tractor Hydraulic Fluid
Conoco Hydroclear Powertran
Esso Hydraul
Gulf Universal Tractor Fluid
Kendall Hyken 052
Marathon Marafluid Super HT
Pennzoil Hydra-trans
Phillips HG Fluid
Shell Donax TD
76 Lubricants Hydraulic/Tractor Fluid
Sunoco TH Fluid
Texaco TDH
Group 2 Hydraulic Fluid (Hot Climate—Heavy
Duty)
Note: The fluids within this group are
interchangeable.
ISO VG 68 anti-wear hydraulic fluid
Mobil DTE 26
Amoco Rykon AW No. 68
Castrol AWS 68
Chevron Hydraulic Oil AW ISO 68
Conoco Hydroclear AW 68
Exxon Nuto H 68
Gulf Harmony 68AW
Kendall Four Seasons AW68
Marathon ISO 68
Pennzoil IAW Hydraulic Oil 68
Phillips Magnus A ISO 68
Shell Tellus 68
76 Lubricants AW 68
Sunoco SunVis 868
Texaco Rando HD 68
Group 1 fluids are recommended for use
at typical ambient temperatures of 0°C to 41°C. The
ISO type 46/68 fluid has been found to offer optimal
performance in a wide range of temperature
conditions for the average user. The Universal Tractor
Fluids offer similar performance for those who prefer
them, with perhaps some slight loss of efficiency at
high ambient temperatures compared with the Type
46/48 fluids
Group 2 fluids are recommended for heavy-duty
use in hot climates where ambient temperatures
range from about 20°C to 49°C. Use at lower
ambient temperatures may result in hard starting,
increased engine laboring while cold, sluggish or
non-operating spool valves while cold and high
Important
1