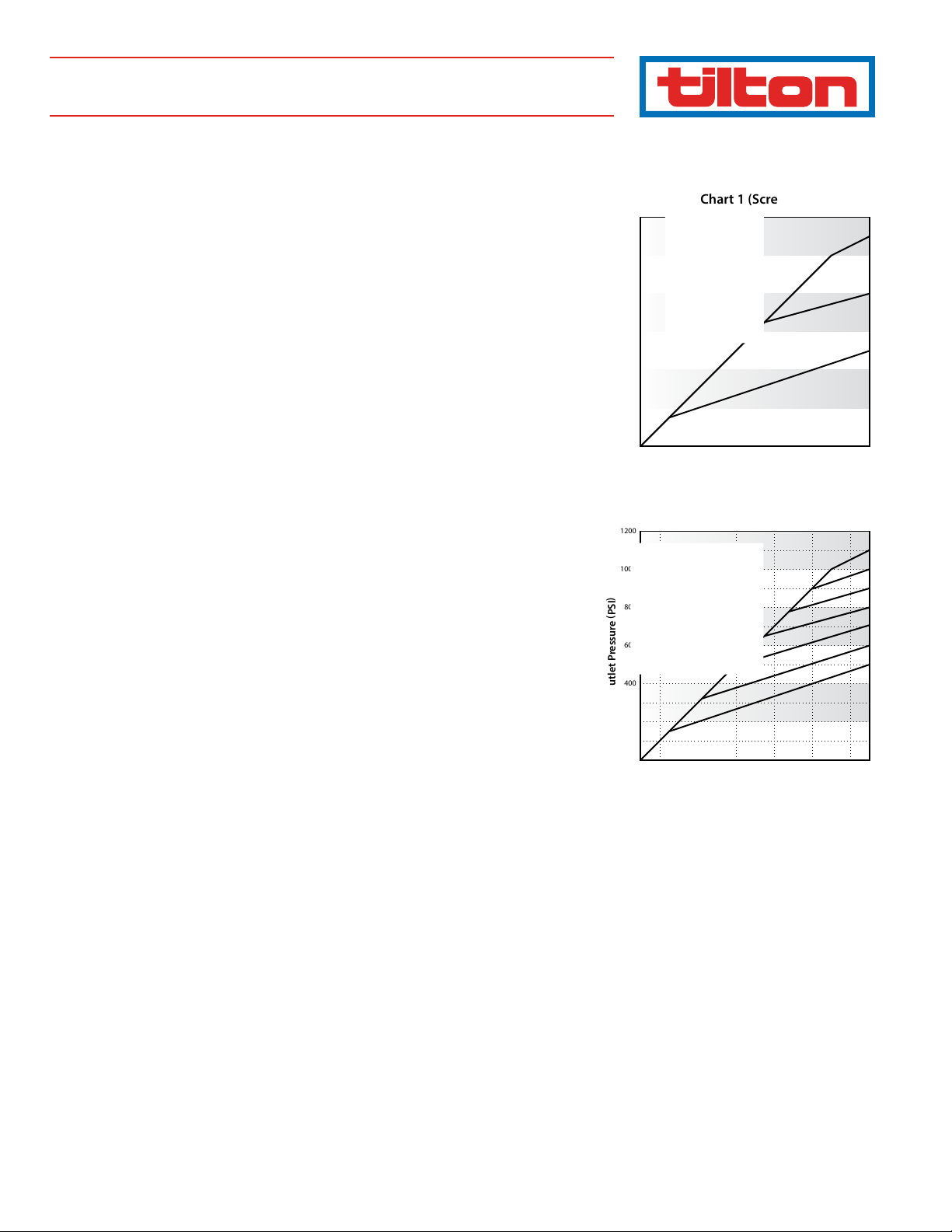
Position 7
Position 6
Position 5
Position 4
Position 3
Position 2
Position 1
1000 1200800600400200
200
400
600
800
1000
1200
Inlet Pressure (PSI
)
Outlet Pressure
(
PSI
)
Maximum
Compression
Midpoint o f
Compression
Minimum
Compression
1000 1200800600400200
200
400
600
800
1000
1200
Inlet Pressure (PSI
)
Outlet Pressure
(
PSI
)
INSTALLATION INSTRUCTIONS
Brake Proportioning Valve
How It works
Tilton Engineering’s patented, adjustable hydraulic brake proportioning valve enables the driver,
or a crew member, to adjust the brake-force to a particular wheel (or wheels). The light, rugged
valve may be bulkhead or panel-mounted. The proportioning valve can also be used eectively
with dual master cylinder systems.
The proportioning valve is often one of the less understood devices bolted onto a racecar.
Understanding how it works from a functional standpoint will allow the driver and crew chief to
take advantage of its properties for a better racecar setup.
At lower pressures, the Tilton proportioning valve acts as a simple hydraulic connector.
The pressure going into the proportioning valve is equal to the pressure going out. There is a 1:1
ratio between inlet and outlet pressure. The 45º line shown in Chart 1 and Chart 2 indicates this
pressure range. Once a certain pressure limit is reached, a further increase in line pressure occurs
at a reduced rate of 3:1 from inlet to outlet.
The adjustment control alters the point at which the inlet/outlet pressure ratio changes from 1:1
to 3:1. For example, look at the proportioning valve Midpoint Position of Chart 1 for Screw-type
proportioning valves and Position 4 of Chart 2 for Lever-type proportioning valves. When the
master cylinder line (inlet) pressure is above 650 PSI, the caliper line (outlet) pressure is below
the pressure in the master cylinder line. The sloping line o to the right (shown in Chart 1 & 2)
demonstrates this. Below 650 PSI they are equal.
The dual-slope line gives the proportioning valve one advantage over the balance bar system. It
can be tuned for a better front-to-rear brake balance under both light and heavy braking. A par-
ticular setting of the balance bar gives you a set front-to-rear brake balance, such as 70/30 (70%
front/30% rear). Under both light and heavy braking, this balance remains the same. However, the
loading on the front and rear axles does not remain the same under dierent braking conditions.
During heavy braking, there is a large load transfer from the rear to the front axle. As the load
increases on the front axle you want a higher percentage of the braking force on the front axle.
The bend in the graph for the proportioning valve allows this to happen when the proportioning
valve is placed in the line for the rear calipers. During heavier braking, a higher percentage of the
braking force is distributed to the front calipers.
98 -1261
Chart 1 (Screw Type)
Chart 2 (Lever Type)
InstallatIon notes
There are a few items to remember concerning the proportioning valve:
• Standard Proportioning Valves (P/N 90-1000 & 90-2000)
AN-3 port with 3/8"-24 threads. Fittings (supplied): AN-3 male to AN-3 male
(P/N 73-820); AN-3 male to 3/16" inverted are (P/N TE2089-188).
• Metric Proportioning Valve (P/N 90-1003 & 90-2003)
Threads: M10 x 1.0-6H with 74º included angle at base. No ttings supplied.
• Lever-type portioning valves:
A typical setup has the valve oriented in such a way that when the handle
is pushed towards the front of the vehicle it reduces the rear brake pres-
sure. When the handle is moved toward the rear of the vehicle it increases
the rear brake pressure. Handle can be re-oriented by loosening the jam
nut and rotating the handle. To determine which direction to move the
handle, refer to Chart 2 and Diagram 4.
• Screw-type portioning valves:
Rotating the adjustment knob in a clockwise direction will allow more
brake pressure to be applied to the rear brakes, counter-clockwise will
reduce the pressure (when installed on the rear calipers line).
• At higher pressures, a piston separates the uid at the inlet and outlet
sides. No uid ows through the valve. Therefore, you cannot bleed the
system at high pressure. Use light pedal pressure, and as an extra precau-
tion, move the lever to Position 7 (lever-type), or rotate adjusting knob in a
clockwise direction (screw-type), to reduce internal pressure.
• The proportioning valve can be used to reduce brake line pressure, but will
not increase it.
• Hooking it up backwards will not work.
• It can be used very eectively with a balance bar. Set the lever to Position 7
(lever-type) or set adjustment knob to the fully clockwise position (screw-
type). Adjust the balance bar until the rear brakes lock on the track with
slightly less pedal eort than the front brakes. The proportioning valve
is connected to the rear brakes in this case. Then, adjust the valve one
position at a time (lever-type) or rotate the knob counter-clockwise (screw-
type) until the proper balance is achieved.
• The proportioning valve is ideal for cars that must retain the stock calipers
and master cylinder, yet have too much rear brake when running soft tires.
A prime example is SCCA A Sedan (AS).
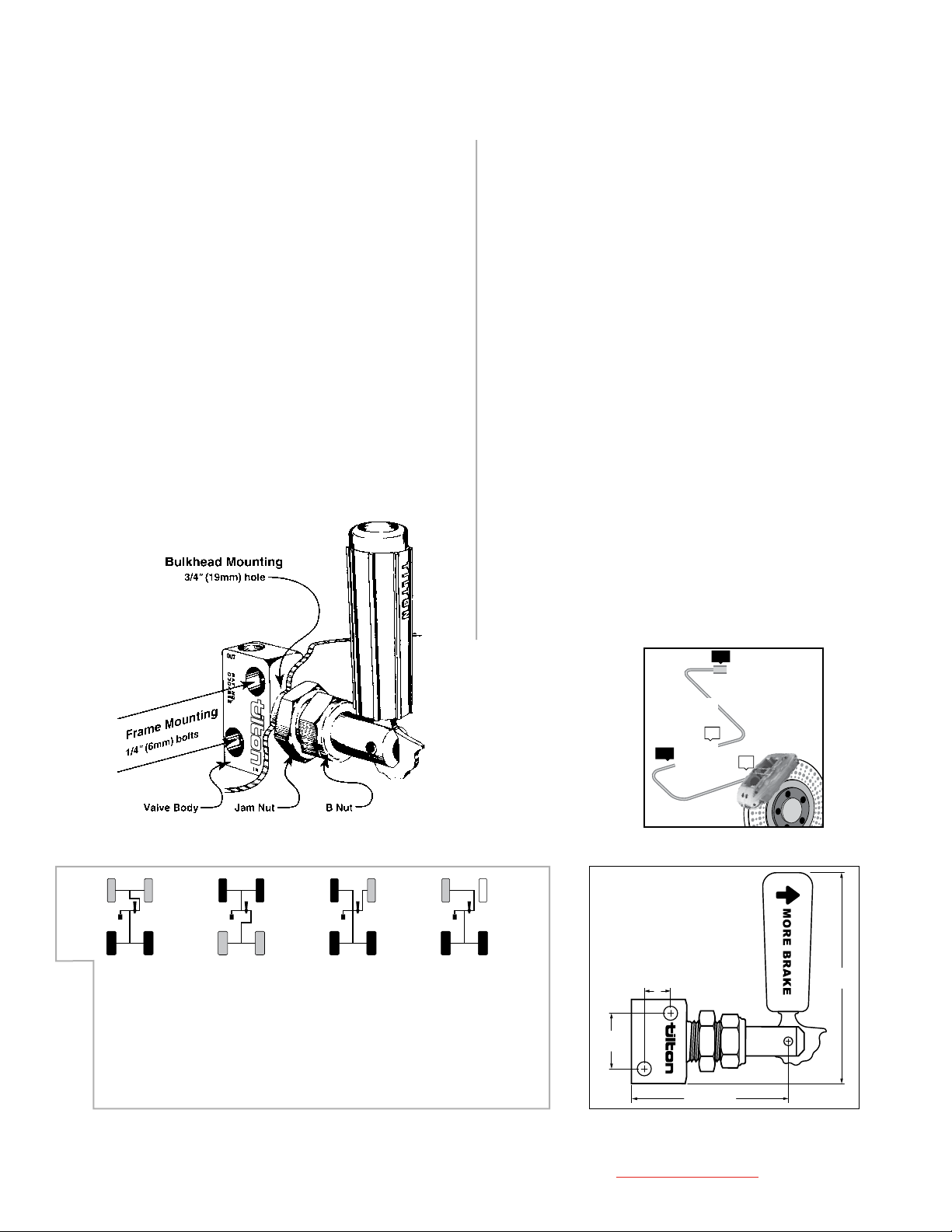
InstallatIon
Select either the frame or bulkhead mounting style and follow the steps below:
Frame mountIng
1. Select a location for frame mounting the proportioning valve that allows
easy access to the adjusting handle/knob.
2. Make sure that the location allows room for the hydraulic lines and access
for servicing.
3. Locate and mark the location of the mounting holes on the frame refer-
ring to Diagram 4.
4. Drill two 9/32" (7mm) diameter holes in the marked locations. Debur both
of the drilled holes.
5. Test t the valve in the prepared location and select the proper mounting
hardware. Use two 1/4" (6mm)
diameter socket head cap screws with locknuts. The length will be deter-
mined by your application.
6. Select the routing of the hydraulic lines carefully and avoid any heat
sources such as the exhaust pipes and
manifolds.
7. Refer to Diagram 2 and connect the outlet of the master cylinder to the
inlet of the proportioning valve. The outlet of the proportioning valve is
connected to the line leading to the caliper(s).
BulkHead mountIng
1. Select the location for bulkhead mounting the proportioning valve that
allows easy access to the adjusting handle (knob).
2. Make sure that the location allows room for the hydraulic lines and access
for servicing.
3. Locate and mark the location of the mounting hole on the frame referring
to Diagram 1.
4. Cut, drill or punch a 3/4" (19mm) diameter hole in the marked location.
Debur the hole.
5. Refer to Diagram 1 and loosen the B-nut on the valve body and carefully
remove the handle assembly (adjusting knob) from the valve body.
6. Refer to Diagram 1 and loosen and remove the jam nut.
7. Test t the valve in the prepared location by sliding the valve body
through the hole in the bulkhead.
8. Secure the jam nut and insert the handle assembly (adjusting knob) into
the valve body.
9. Rotate the handle assembly into the desired position (Lever-type). Tighten
the B-nut and verify the location is suitable for ease of adjustment and
servicing. Make sure that the B-nut does not touch the jam nut. Other-
wise, the valve handle may not be held in its proper position in the valve
body.
10. Select the routing of the hydraulic lines carefully and avoid any heat
sources such as the exhaust pipes and manifolds.
11. Refer to Diagram 2 and connect the outlet of the master cylinder to the
inlet of the proportioning valve. The outlet of the proportioning valve is
connected to the line leading to the caliper(s).
Front
Rear
Reduced front
• Rally
• Dirt
• O road
• Stadium rac ing
Used when th e front tire
needs more adhesion for
steering , as well as in loose
gravel conditions.
Diagram 1 - Mounting Diagram
Reduced rear
• Road racin g
• Street rod s
• Tru cks
• Oval Track
Used to compe nsate for fuel
load or weight changes, deteriorating rear tire adhesion,
and brake systems with only
one master cylinder
Reduced right front
• Dirt
• Asphalt
Used to decr ease out- side
front corner braking, which
increases t urn in and reduces
underste er. Used to compensate for track conditions or
deteriorating chassis setup.
Reduce d left, no ri ght
front
• Dirt raci ng
• Midget
• Sprint
Used to decr ease in- side
front corner braking, which
decrease s turn in and reduces
overstee r. Usually used on the
inside fro nt with twin calip ers
on the rear.
1.00"
(25.4m m)
OUT
IN
OUT
IN
Diagram 2 - Flow Diagram
.50" (12.8mm)
OUT
IN
3.00" (122mm)
3.98"
(102mm)
Diagram 3 - Typical Applications
Diagram 4 - Overall Dimensions
(Handle shown in Position 1, referring to Chart 1)
Tilton Engineering, Inc. 25 Easy Street • PO Box 1787 • Buellton, CA 93427 • www.tiltonracing.com