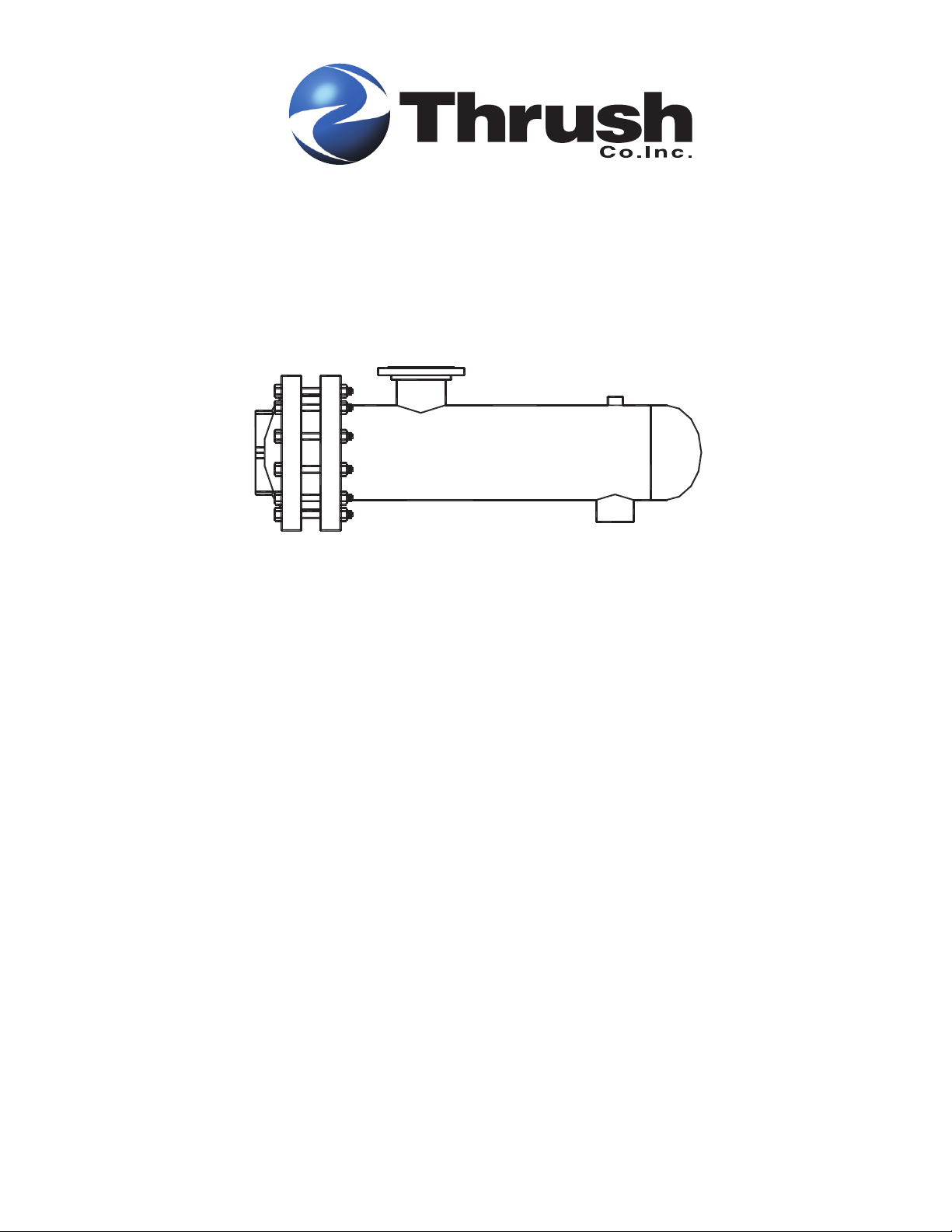
9636-0760
The THRUSH Heat Exchanger has been carefully assembled and factory tested to provide years of
trouble-free service. In order to assure the service intended, the following information is provided to
enable proper installation, operation and maintenance of the Thrush Heat Exchanger.
LOCATION
The heat exchanger should be located in a clean, open area, where it is easily accessible for
inspection, service and repair. Allowance should be made for the clearance required to remove the
tube bundle.
PIPING
Long radius elbows should be used in place of standard elbows wherever possible, because of their
superior flow characteristics. Liberal use of shut off valves is recommended to enable inspection
and service.
INSTALLATION
1. To move or lift the heat exchanger, place a sling around the unit's inlet and outlet
connections. Verify that all equipment, including the sling, is certified to handle the total
weight of the heat exchanger. Carefully lift to piping site. Av oid slinging at the bolted gasket
head joint area.
2. Install unit level and square so pipe connections can be made without force. During
installation and operation, unit should be adequately supported to prevent settling that could
cause piping strains.
3. Provide sufficient clearance at channel end for removal and replacement of tube bundle.
(Minimum clearance = one length of the shell)
4. Provide positive shutoff valves and by-pass to permit both shell and tubeside to be shut off for
inspection and service.
5. After installation and prior to startup all head flange bolts should be re-tightened.
OPERATING & MAINTENANCE INFORMATION
FOR
HEAT EXCHANGERS
8/08
Shell and Tube Heat Exchanger - U-tube style
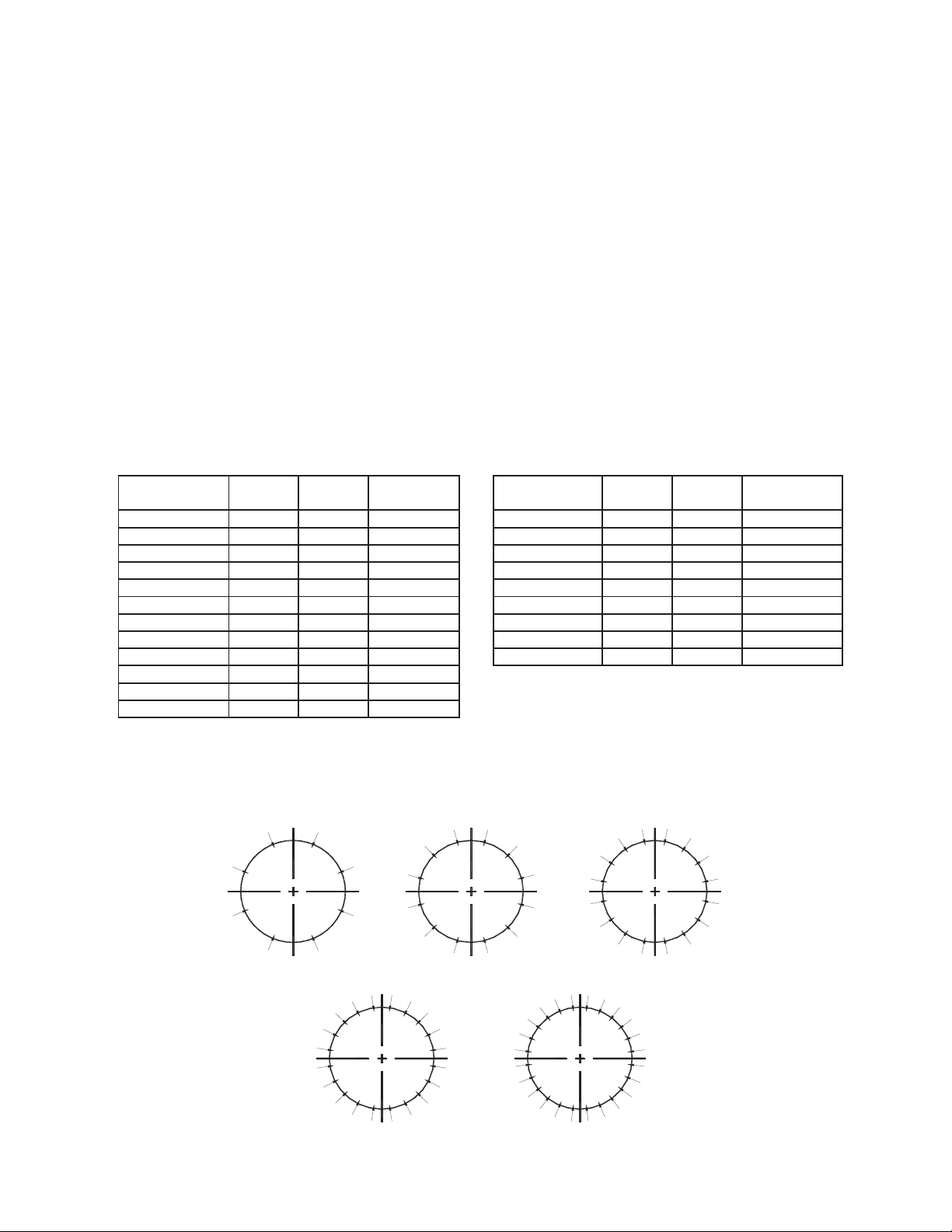
OPERATION
Start up - Open cold side first; then start hot side fluid slowly to gradually bring unit to operating
condition. Bring unit from ambient temperature up to operating temperature gradually. Do not
introduce hot or cold fluids suddenly. This could damage the unit and void the warranty.
Shut down - Always close off flow of hot fluid first.
Important - Never admit hot fluid suddenly when unit is empty or cold. Do not shock with cold water
when unit is hot.
Gasket Creep is inherent to most gasket joints, and retorquing is required. The greater the operating
temperature and pressure the greater the problem can become. It is imperative that the head bolts
be torqued after installation, after initial startup, and inspected seasonally to be sure the bolts are
torqued correctly.
The bolts should be torqued incrementally to 30%, 60%, and then to 100% of the appropriate value
in Figure 1. They should be torqued in the sequential order of the appropriate pattern in Figure 2.
Figure 1: Bolt size and Torque requirements
Heat Exchanger
Size
Bolt
Size
Number
of Bolts
Torque Ft/Lb.
150# Flgs.
Heat Exchanger
Size
Bolt
Size
Number
of Bolts
Torque Ft./Lb.
300# Flgs.
4" .62 8 30 4" .75 8 100
6" .75 8 50 6" .75 12 100
8" .75 8 50 8" .87 12 160
10" .87 12 80 10" 1.00 16 245
12" .87 12 80 12" 1.12 16 390
14" 1.00 12 123 14" 1.12 20 390
16" 1.00 16 123 16" 1.25 20 545
18" 1.12 16 195 18" 1.25 24 545
20" 1.12 20 195 20" 1.25 24 545
22" 1.25 20 273
24" 1.25 20 273
26" 1.25 24 273
Figure 2: Sequential Order for Torquing Flange Bolts
12
10
5
11
17
19
1 5
6
9
3
15
7
9
11
2
16
8
20
12
4
22
14
6
3
7
24
18
24 BOLT
12
4
14
1
10
16
4
10
5
3
8
4
7
2
1
13
12
20
8
18
6
2
14
20 BOLT
1
8
4
6
8 BOLT 12 BOLT 16 BOLT
8
6
10
9
17
23
2
16
15
2
5
13
21
3
11
19
7
15
1
9
5
13
3
11
7

MAINTENANCE
Thrush Co., Inc. recommends regular cleaning of the heat exchanger tube bundles. The bundle
should be removed periodically and any scale or deposits should be cleaned from the tube bundle
surface. Frequency of cleaning is dependent upon water quality and is the responsibility of the
Owner. Please note that new gaskets are required for start up each time the unit is disassembled.
Thrush Co., Inc.
P.O. Box 228 - 340 West 8th St.
Peru, IN 46970 (765) 472-3351