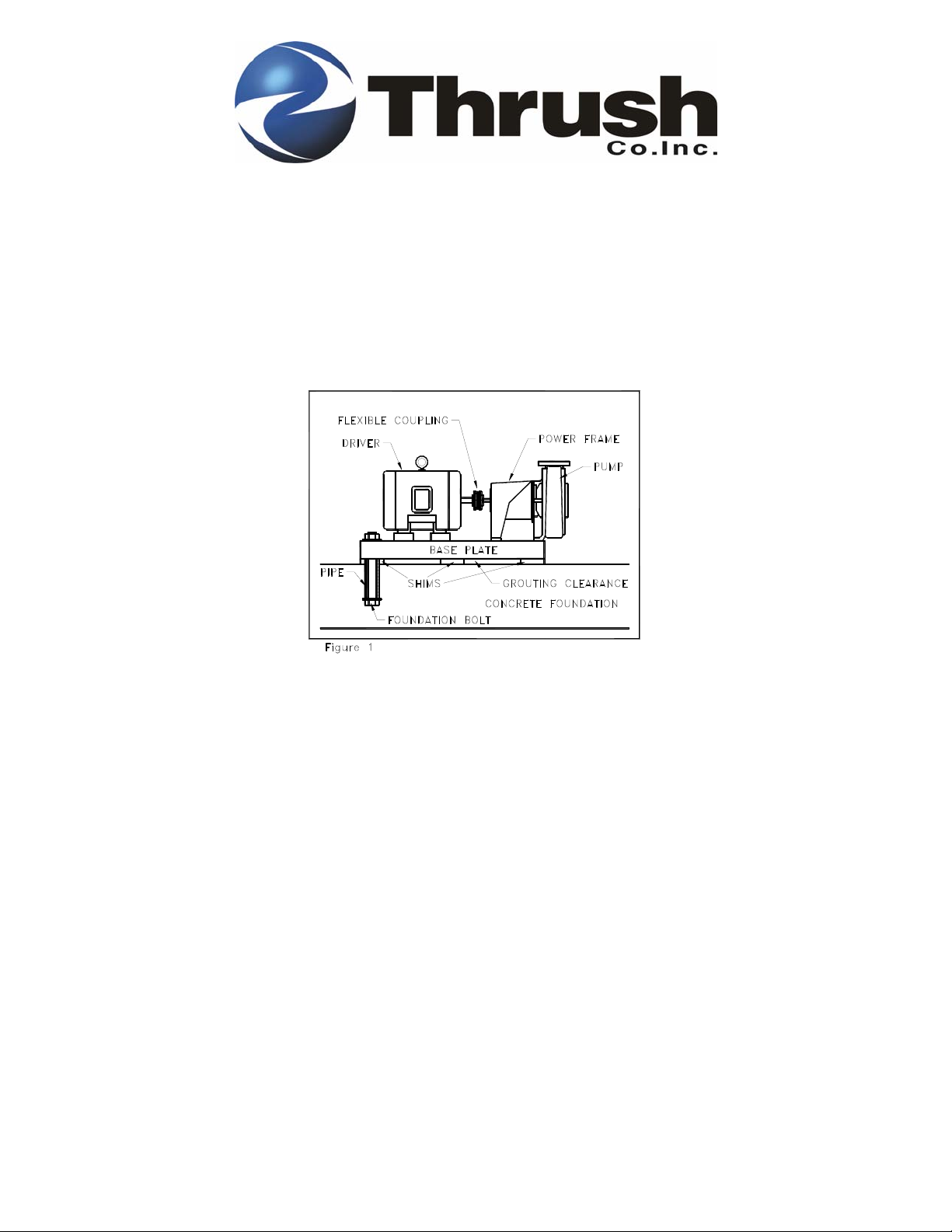
OPERATING AND MAINTENANCE INSTRUCTIONS
FOR BASE MOUNTED END SUCTION
CENTRIFUGAL PUMPS
The THRUSH End Suction Centrifugal Pump has been carefully assembled and factory tested to
provide years of trouble free service. In order to insure the service intended, the following
information is provided to enable proper installation, operation and maintenance of this product.
9636-0400 8/08
INSTALLATION
LOCATION
The pump should be located as close to the liquid source as possible so that the suction line can
be short and direct. It should be located in a clean, open area, where it is easily accessible for
inspection, lubrication and repair. Pumps installed in dark, dirty areas or cramped locations are
often neglected which can result in premature failure of both the pump and the driver.
Adequate provisions should be made for electrical wiring to the pump motor. A switch and
overload protection should be installed near the pump unless it is impractical. The electrical
conduit should be positioned in such a way as to preclude the possibility of moisture entering the
conduit or the motor and causing short circuit.
FOUNDATION
The foundation must be sufficiently rigid to absorb any vibration and stress encountered during
pump operation. A raised foundation of concrete is preferable for most floor-mounted pumps.
The raised foundation assures a satisfactory base, protects against flooding, simplifies moisture
drainage and facilitates keeping the area clean.
The pump should be firmly bolted to the foundation, whether it is a raised concrete base,
steelwork wall, or structural member. The mounting bolts or studs should be accurately located
per the applicable THRUSH dimension sheet. Foundation bolts should be enclosed by a slee ve 2
to 4 diameter larger than the bolt to allow movement for proper alignment with the pump mounting
holes. Refer to Figure 1. If the pump is to be mounted on steelwork or other structure, adequate
support should be provided to prevent distortion of the base plate or the structure, which could
produce excessive strain on the pump casing and piping and seriously affect alignment of the
pump and driver.
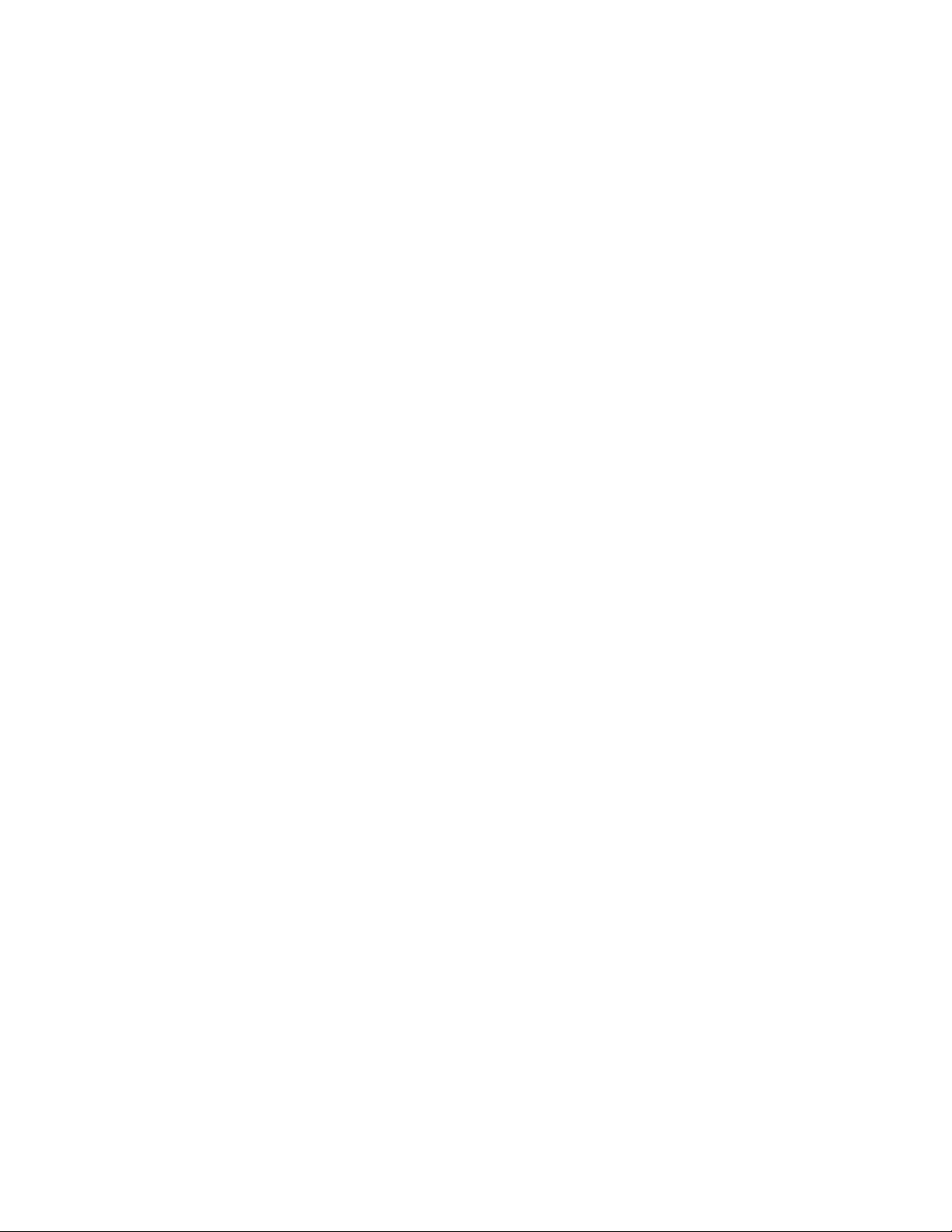
MOUNTING
The pump unit should be set on the foundation, being careful not to damage the threads on the
foundation bolts. The flexible coupling halves should be disconnected. Shims could be inserted
and the pump leveled. A spirit level should be used on the faces of the flexible coupling halves
and on the suction and discharge flanges. If the pump has threaded nozzles, a short piece of
pipe inserted in the nozzles will serve as a smooth surface for a leveling reference point. The
shims should be adjusted until the pump is leveled horizontally and vertically. Tighten the
foundation bolts finger tight.
GROUTING
Grouting the base plate prevents lateral movement of the base plate and improves the vibration
absorbing characteristics of the foundation by increasing its mass. A wooden dam should be
constructed around the base plate to contain the grout while it is being poured. The entire base
plate should be filled with grout, allow 48 to 72 hours for grout to dry. After grout is thoroughly
dried, firmly tighten foundation bolts.
PIPING
The piping practices followed will directly affect the efficiency and power consumption of the
pump. Pay particular attention to the seemingly insignificant details involved in piping for they
make the difference between a good and bad installation. BOTH THE SUCTION AND THE
DISCHARGE PIPING SHOULD BE INDEPENDENTLY SUPPORTED NEAR THE PUMP.
LIBERAL USE OF PIPE HANGERS AND SUPPORT BLOCKS WILL PREVENT EXCESSIVE
STRAIN ON THE PUMP CASING AND ON THE PIPE JOINTS. The suction diameter should be
at least the same diameter as the suction nozzle on the pump and preferably larger. Use of a
smaller diameter pipe will result in loss of head due to friction. All joints must be tight to maintain
prime on the pump.
SUCTION PIPING
Long radius elbows should be used in place of standard elbows wherever possible, beca use of
their superior flow characteristics. Elbows should not be used at suction nozzle, but if it is
unavoidable, long radius elbows should be used. Elbows installed in any position at the suction
nozzle have a tendency to distribute the liquid unevenly in the impeller eye and may cause a
reduction in capacity, create an undesirable thrust condition, or create noisy operation. Eccentric
reducers should be installed directly at the suction nozzle, with the taper at the bottom to prevent
air pockets from forming. Straight taper reducers should never be used in a horizontal suction
line because of the air pocket that is formed at the leg of the reducer and the pipe.
DISCHARGE PIPING
The discharge pipe diameter should be the same as or larger than the discharge nozzle diameter.
The size of the discharge pipe to be used is dependent upon its application.
Long radius elbows should be used in the discharge piping as well as in the suction piping to
prevent excessive head loss due to friction. Whenever possible, elbows should not be installed
directly at the discharge nozzle as the turbulence created by the elbow will affect pressure gauge
readings.
An increaser should be installed at the discharge nozzle if larger diameter discharge piping is
used. Straight taper increasers and/or reducers are satisfactory in discharge applications.
Expansion joints are used primarily to prevent the transmission of piping strain, caused by
thermal expansion and contraction, piping misalignment, pressure cha nges, or other causes, to
the pump casing. They are also used to suppress any noise that may be transmitted through the
piping.
PROPER PIPING ALIGNMENT IS ESSENTIAL BEFORE CONNECTION IS MADE. PIPING
ALIGNMENT SHOULD NEVER BE ACHIEVED BY FORCE. THIS COULD PRODUCE STRAIN
ON THE PIPING AND THE PUMP CASING. PROPER SUPPORTS SHOULD BE INSTALLED
FOR THE PIPING TO KEEP ITS WEIGHT OFF THE PUMP CASING.
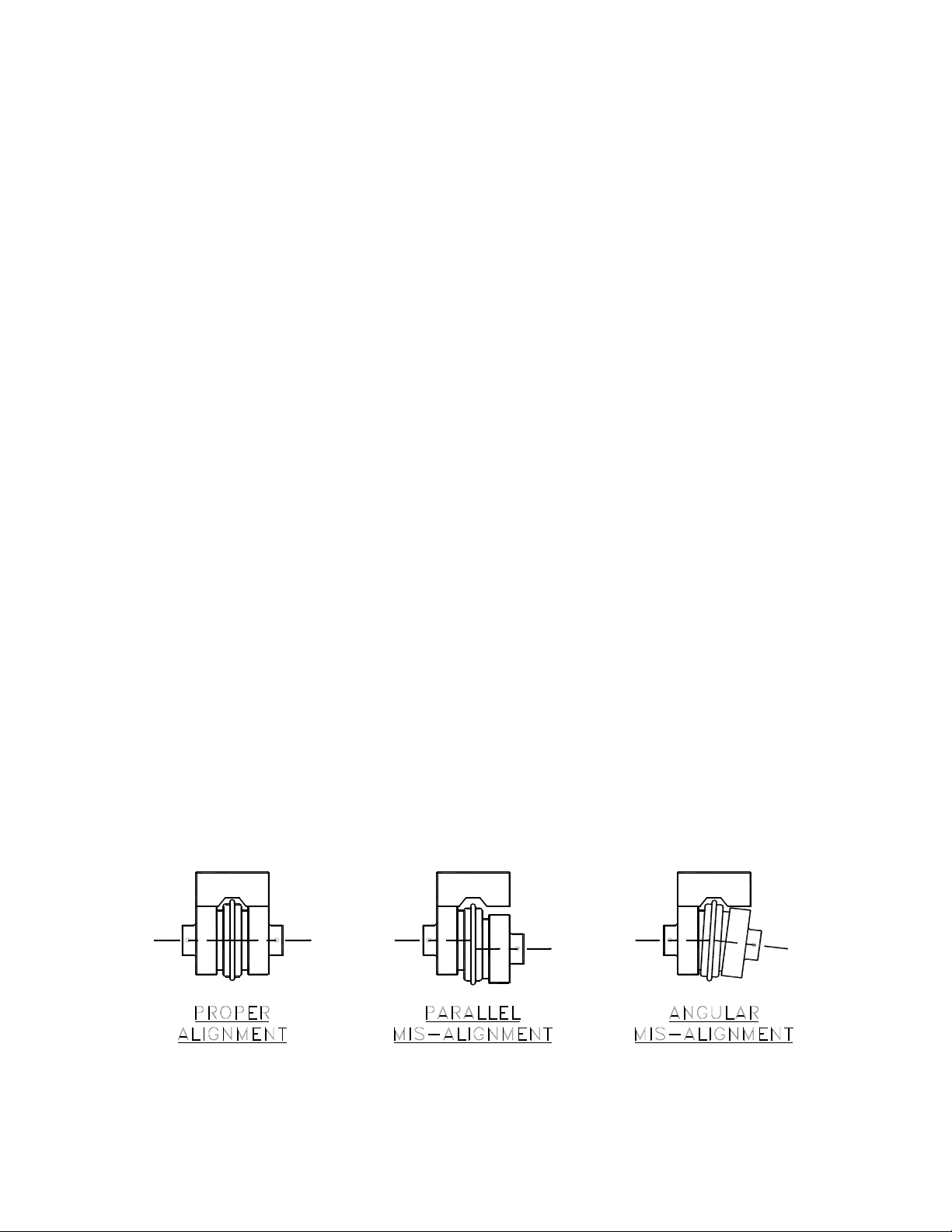
ALIGNMENT
The pump and driver were accurately aligned at the factory. However, it is impossible to maintain
this alignment during shipping and handling. Therefore, it will be necessary to realign the pump
and driver. Flexible couplings are not universal joints and should not be used to compensate for
misalignment of the pump and motor shafts. Their function is to transmit power from the driver to
the pump while compensating for thermal expansion and shaft end movement. The coupling
faces should be far enough apart so that they do not make contact when the motor shaft is forced
to the limit of the bearing clearance toward the pump.
There are two types of misalignment encountered with flexible couplings: ANGULAR
MISALIGNMENT in which the shafts are not parallel and PARALLEL MISALIGNMENT where the
shafts are parallel but not on the same axis.
STRAIGHT EDGE ALIGNMENT
All THRUSH base mounted end suction pumps are furnished with flexible couplings. To check
alignment, simply place the alignment gauge furnished with the pump across the coupling
flanges, making sure the edge is firmly against the coupling halves. If parallel misalignment
exists, there will be a gap under the gauge. To correct this, loosen the motor, hold down bolts
and realign or shim motor until the alignment gauge rests firmly on both coupling halves as in
Figure 2. Check alignment at 90° increments around the circumference of the coupling. (Do not
rotate shaft for this check.) If alignment is correct, retighten motor bolts. After the bolts have
been tightened, recheck alignment. Angular misalignment can be checked with a caliper by
checking the spacing between coupling halves at 90° intervals. If misalignment exists, realign as
previously described.
DIAL INDICATOR ALIGNMENT
To check angular alignment with a dial indicator, remove coupling insert, clamp the dial indicator
to the pump coupling half so that the ball on the indicator just rests on the face of the motor
coupling half. A chalk mark should be made at the point where the ball contacts the coupling half.
Both the pump shaft and the motor shaft should be rotated an equal amount so that the reading is
taken at all check points with the ball on the chalk mark. Insert shims as required. To check
parallel alignment with the dial indicator, the ball should rest on periphery of the motor coupling
half. A chalk mark should be made at the point of contact, and the shafts rotated equally so that
the reading is taken with the ball on the chalk mark at all check points. Insert shims as required.
NOTE: ANY ADJUSTMENT TO CORRECT ONE DIRECTION OF ALIGNMENT MAY AFFECT
THE OTHER DIRECTION. THEREFORE, IT IS NECESSARY TO RECHECK BOTH ANGUALR
AND PARALLEL ALIGNMENT AFTER EACH ADJUSTMENT.
THRUSH STANDARD COUPLINGS (TB WOODS) WILL OPERATE SATISFACTORILY WITH
1/16” PARALLEL MISALIGNMENT OR 1 Deg. ANGULAR MISALIGNMENT MAXIMUM. ON
OTHER COUPLINGS CONSULT MANUFACTURE’S DATA.
Figure 2