
®
Mylar
polyester film
Electrical Properties
Product Information
Mylar® offers unique design capabilities to the
electrical industry due to the excellent balance of
its electrical properties with its chemical, thermal,
and physical properties. Detailed descriptions of
these latter properties are included in other available bulletins. Table 1 is a summary of some
typical electrical properties; further details on these
and other electrical properties are included in the
remaining pages of the bulletin.
Dielectric Strength
The short-term dielectric strength test (ASTM
D149) is primarily used to measure the quality of a
film. This test method allows considerable freedom
in the choice of electrode size, environmental
conditions, etc. The following discussion of these
variables is based on tests run with brass electrodes
of the dimensions prescribed in ASTM D2305. In
limited testing, stainless steel electrodes gave
results similar to those obtained with the standard
brass electrodes. The data were obtained at a
frequency of 60 Hz, using a 500 V/sec rate of rise,
unless otherwise noted.
Film Thickness
As with most materials, the AC Dielectric Strength
of Mylar
thickness increases (see Figure 1). At 500 V/sec
rate of rise, corona occurs within a few seconds,
and the film begins to melt before the actual
breakdown occurs. The greater the film thickness,
the more the failure is due to melting and, thus, the
lower the V/mil as thickness increases.
®
polyester film in V/mil decreases as film
Electrode Size
Differences in dielectric strength values may result
when comparing
electrodes. Because of the larger film area between
the electrodes, the potential for lower dielectric
strength values is greater with 2-in electrodes.
Figure 1. Dielectric Strength vs. Thickness
Dielectric Strength, V/mil
(2 in Electrode in air at 25°C [77°F])
40,000
30,000
20,000
10,000
8,000
6,000
4,000
3,000
2,000
1,000
1
4 /12
1
/4 in and 2 in diameter brass
1 2 4 6 8 10 14 20/
Thickness, mil
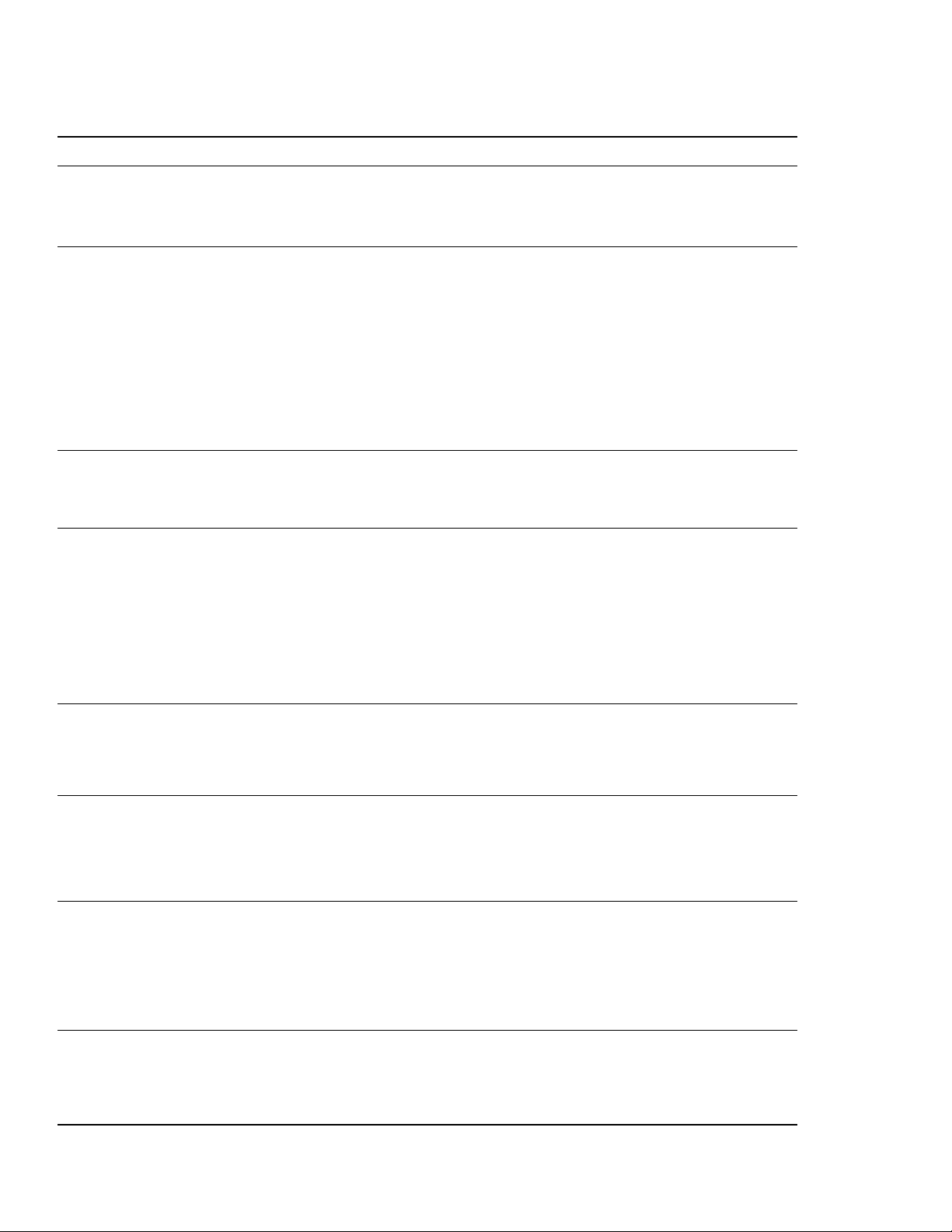
Table 1
Typical Electrical Properties of Mylar Polyester Film
Property Value Test Method
DC Dielectric Strength Typical Value for Mylar 92 EL/C*
25°C (77°F) 11.0 kV/mil
Gauge and Type at 25°C (77°F) Minimum Values for Mylar C Film
6C 0.225 kV Minimum average
7C 0.300 kV voltage of 20 film-foil
8C 0.320 kV capacitors, 0.5 µF each
10C 0.490 kV
12C 0.650 kV
14C 0.825 kV
20C 1.500 kV
24C 2.000 kV
32C 3.100 kV 100 V/sec rate of rise
40C 4.100 kV
48C 4.900 kV
75C 5.500 kV
92C 6.000 kV
AC Dielectric Strength Typical Value for Mylar 92 EL/C*
25°C (77°F) 7.0 kV/mil ASTM D149 and
Gauge and Type at 25°C (77°F) Minimum Values for Mylar EL Film
48EL 2.8 kV ASTM D149 and D2305,
75EL 3.5 kV Minimum average
92EL 4.0 kV voltage of 10 sheet
142EL 5.5 kV samples
200EL 7.7 kV
300EL 10.0 kV 60 Hz
500EL 13.5 kV 500 V/sec rate of rise
750EL 17.5 kV
900EL 18.4 kV
1000EL 19.0 kV
1400EL 20.0 kV
Dielectric Constant Typical Value for Mylar 92 EL/C*
25°C (77°F)—60 Hz 3.3 ASTM D150
25°C (77°F)—1 kHz 3.25
25°C (77°F)—1 MHz 3.0
25°C (77°F)—1 GHz 2.8
150°C (302°F)—60 Hz 3.7
Dissipation Factor Typical Value for Mylar 92 EL/C
25°C (77°F)—60 Hz 0.0025 ASTM D150
25°C (77°F)—1 kHz 0.0050
25°C (77°F)—1 MHz 0.016
25°C (77°F)—1 GHz 0.008
150°C (302°F)—60 Hz 0.004
–269°C (–452°F)—1 kHz (in Helium) 0.0002
Volume Resistivity Typical Value for Mylar 92 EL/C
25°C (77°F) 1018 ohm⋅cm ASTM D257 and D2305
150°C (302°F) (Type C Film) 1013 ohm⋅cm
Surface Resistivity
23°C (73°F)—30% RH 1016 ohm/sq
23°C (73°F)—80% RH 1012 ohm/sq
Insulation Resistance
35°C (95°F)—90% RH 1012 ohm
Capacitor Insulation Typical Value for Mylar 92 C
Resistance
100°C (212°F) 30,000 MΩ-µF Based on 0.5 µF film125°C (257°F) 1,000 MΩ-µF foil capacitor sections,
150°C (302°F) 100 MΩ-µF using single layer, 92
*Data relevant for other types of Mylar
1
/4 in upper electrode
and flat plate lower
electrode. 500 V/sec
rate of rise
ASTM D2305
60 Hz
500 V/sec rate of rise
Mylar C
2
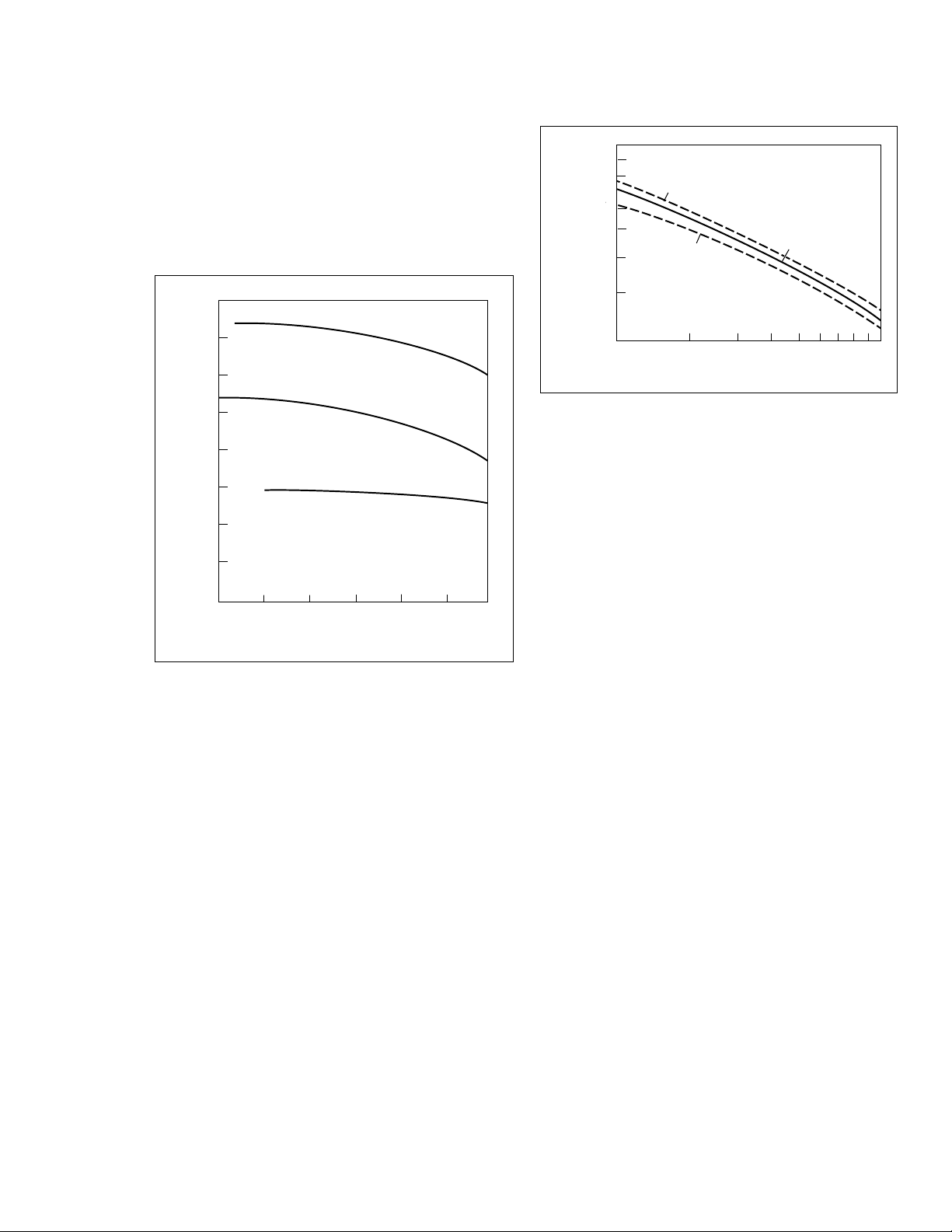
Temperature
The effect of film temperature on the dielectric
strength of Mylar
Figure 2; there is a slight decrease in dielectric
strength from room temperature up to 150°C
(302°F).
®
polyester film is shown in
Figure 3. Dielectric Strength at Various Humidities
10,000
8,000
6,000
20% RH
Figure 2. Dielectric Strength vs. Temperature
8,000
7,000
6,000
5,000
4,000
3,000
Dielectric Strength, V/mil
2,000
1,000
0
0
25
(32)
(77)
50
(122)
Temperature,
0.92 mil
75
(167)
2 mil
7.5 mil
100
(212)
°C (°F)
125
(257)
150
(302)
Humidity
While the dielectric strength of Mylar® is much less
sensitive to the humidity of the surrounding air than
cellulosic materials, there is a slight effect as shown
in Figure 3. For films above 2 mil thick, the effect
of varying the relative humidity from 20 to 80%
causes a maximum change in the dielectric strength
of less than ±10% from the value obtained at 35%
RH. The absolute differences in dielectric strength
as a result of humidity changes appear to be independent of electrode size.
4,000
Dielectric Strength, V/mil
2,000
12345678910
80% RH
Thickness, mil
35% RH
Frequency and Wave Form
The DC dielectric strength of Mylar® 92 EL varied
from 14,000 V at 25°C (77°F) to 12,000 V at 90°C
(194°F), 8,000 V at 150°C (302°F), and 5,500 V
at 200°C (392°F). These data were obtained with a
1
/4 in upper electrode and a flat plate lower elec-
trode using a 500 V/sec rise.
Deviations from a sinusoidal wave form can have
marked effects on the measured dielectric strength
at power frequencies. To simulate the effect of
transients, impulse strength tests were run using
1.5 × 40 µsec square wave forms and subjecting
specimens to five pulses at each voltage. (The
voltage was increased by several hundred volts
between each set of pulses.) The average impulse
strengths were 22 kV for Mylar
film and 26 kV for Mylar
samples were tested in air.
®
®
300 EL polyester
1000 EL when the
3