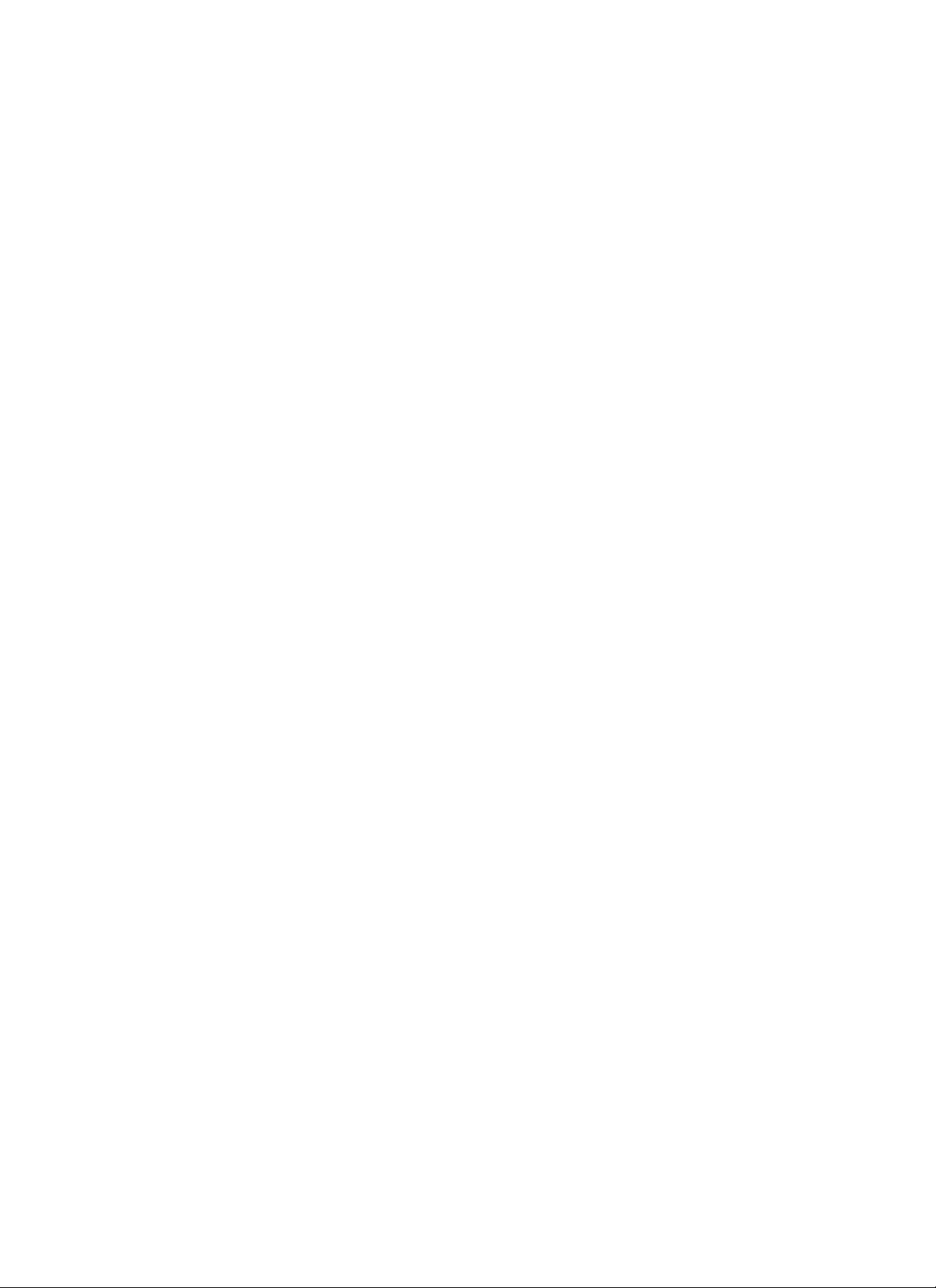
BOSCH
FUEL
INJECTION
SYSTEMS
Forbes Aird
HPBooks
-------- ------

HPBooks
are published by
The Berkley Publishing Group
A division of Penguin Putnam Inc.
375 Hudson Street
New York,New York 10014
First edition: July 2001
ISBN: 1-55788-365-3
@2001 Forbes Aird
10987654321
This book has been catalogued with the Library of Congress
Book design and production by Michael Lutfy
Cover design by Bird Studios
Interior illustrations courtesy of Bosch, Inc. and the author as noted
All rights reserved. No part of this publication may be reproduced, stored in a retrieval system, or transmitted in any form,
by any means electronic, mechanical, photocopying, recording or otherwise, without the prior written permission of the
publisher.
NOTICE: The information in this book is true and complete to the best of our knowledge. All recommendations on parts
and procedures are made without any guarantees on the part of the author or the publisher. Author and publisher disclaim
all liability incurred in connection with the use of this information. Although many of the illustrations in the pages that
follow were supplied by Bosch and used with their permission, this publication is a wholly independent publication of
HPBooks.
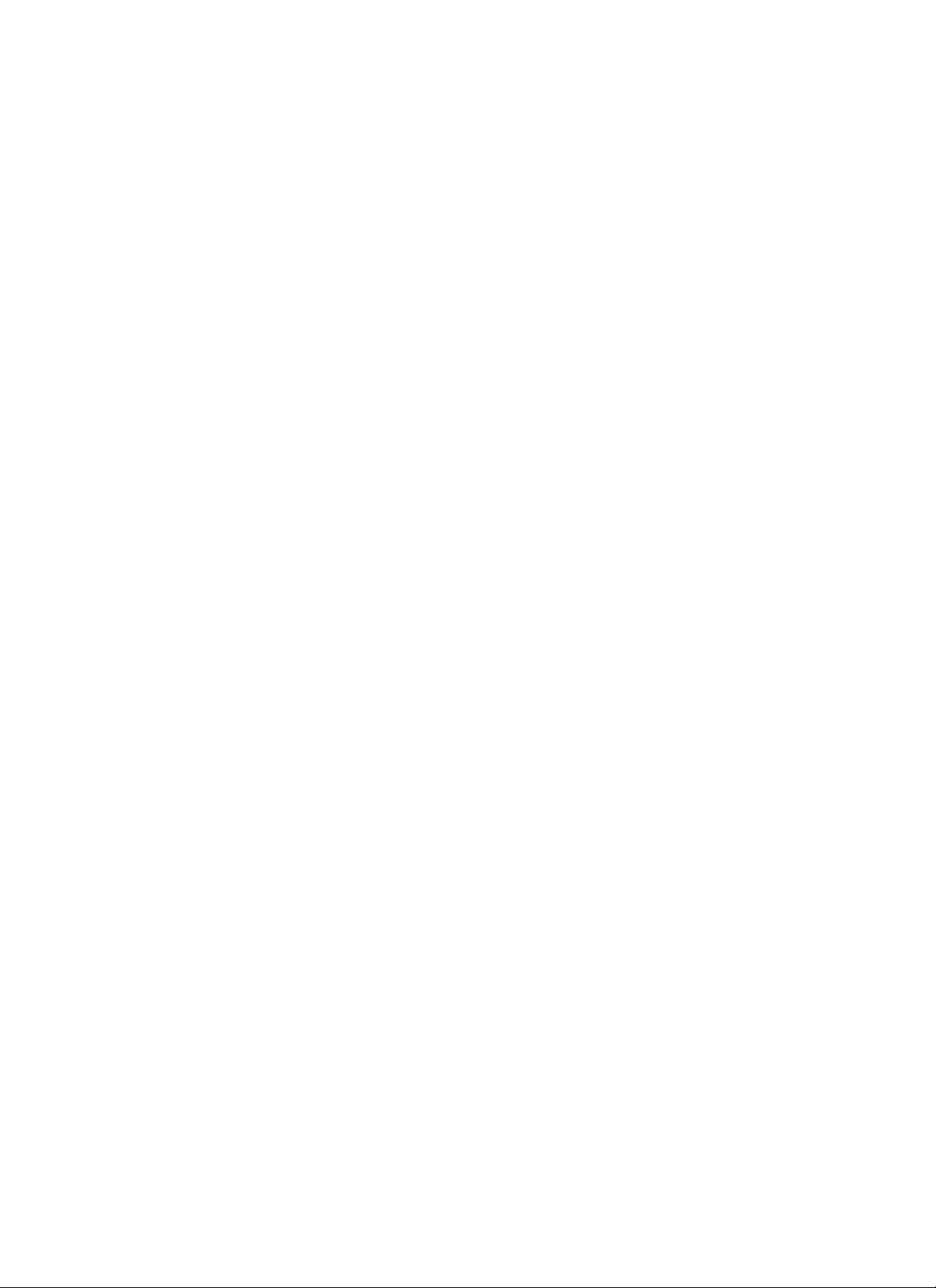
I am grateful to Robert Bosch GmbH in the persons of
Gerhard Kopany, for permission to reproduce copyright
photos and illustrations, and of Wolfgang Boerkel, for
answers to some technical questions. Thanks are also due
to Wolfgang Hustadt of Bosch North America and to Bill
Roth, for further technical information.
~- -

around just about as long as the automobile
A;thOUghgasoline fuel injection (FI) has been
technology. Until about 1970 it was both rare and
expensive, restricted to some aircraft applications, and to
a hand-full of exotic, high performance cars and racers.
Production cars- even high performance sports cars-
made do with carburetors.
Thirty-plus years later, and as a result of the
"electronics revolution," that situation has been very
nearly turned on its head. While cars in many racing
classes wear carburetors, virtually every production car
in the world has FI! Yet it remains a mystery to most.
'tself, it has always been a mysterious
This book is an attempt to de-mystify fuel injection.
While it deals principally with the various electronic fuel
injection systems produced by the Robert Bosch
company, much of what is said in the following pages
also applies to other systems.
No book of this size-indeed, likely no book of any
size-could fully describe the minor variations in FI
installations between one vehicle model and another.
Still, it is hoped that sufficient detail is provided to be of
benefit to mechanics both amateur and professional,
while the general principles described will be useful for
those attempting performance tuning, and informative
for readers who simply seek to understand the mystery.

CONTENTS
CHAPTER 1
Food For Engines, Food For Thought
CHAPTER 2
Fuel Injection: Then and Now
CHAPTER 3
Bosch Intermittent Electronic FI
CHAPTER 4
Motronic Engine Management
CHAPTER 5
Troubleshooting Bosch Intermittent Electronic FI
1
19
37
59
75
CHAPTER 6
Bosch Continuous Injection
CHAPTER 7
Troubleshooting Bosch Continous Injection
CHAPTER 8
Performance Modifications
85
109
123

f a certain fixed quantity of air-or any
other gas- is confined in a closed con-
I
tainer and then heated, the pressure
inside the container will rise. If one of the
walls of the container is moveable, the inter-
nal pressure will push that wall outward
with a certain amount of force, according to
how much heat was put into the trapped gas.
That, in a nutshell, is the working princi-
ple of all internal combustion engines: Each
cylinder is a closed container, and each pis-
ton represents a moveable wall of that con-
tainer; the heat is supplied by the burning of
a fuel, usually gasoline, and the trapped gas
is whatever mixture of gaseous compounds
left over after the burning.
Meanwhile, the other moving parts of an
engine are there for one or the other of just
two supporting functions. The "bottom end"
converts the movement of the pistons into
rotary motion and, by returning them to the
top of their strokes, restores the closed con-
tainers to their original size; the valve gear
and everything else atthe "topend" are there
simply to provide for the emptying out of
the spent gasses and the refilling of the
cylinders with a fresh charge of burnable
mixture.
This may all seem very obvious to anyone
with even the most basic understanding of
how engines work, but lurking within the
simple facts outlined above is a wealth of
detail. Consider the fuel, for example. Some
fuels contain more chemical energy per
pound than others, and so can produce more
heat when burned. Even limiting the discus-
sion to gasoline, the fact is that ordinary
pump gasoline is a mixture of hundreds of
different flammable compounds, and each
of those compounds has a different potential
ability to generate heat when burned. The
exact nature of the mixture of these com-
pounds varies from one pump to another and
from one season to the next, so a pound of
gasoline from one pump on one day might
release somewhat more or less heat when
burned than would a pound from another
pump, or from the same pump on some
other day.
While each is unique, all the hundreds of
compounds that make up gasoline have one
thing in common-they are all hydrocar-
bons. That is, they are all made of just two
kinds of atoms, hydrogen (H) and carbon
(C). The difference between one of these
hydrocarbons and another lies in either the
number of hydrogen and carbon atoms, or in
the way in which these two component ele-
ments are arranged, or both.
Now, burning is a process of oxidation-a
combining with oxygen (O)-so, reduced to
its basics, when a hydrocarbon fuel like
gasoline burns, individual hydrocarbon mol-
ecules from the gasoline combine with indi-
vidual molecules of oxygen from the air.
The hydrogen (H) in the hydrocarbon com-
bines with some of the oxygen (0) in the air
to produce water (H2O), while the carbon
(C) in the hydrocarbon combines with the
rest of the oxygen to form carbon dioxide
(CO2)' In this process, a large amount of
energy gets released, in the form of heat.
This chemical dance amounts basically to a
reversal of the processes that went into cre-
ating the hydrocarbons in the first place. See
the box, "Sunlight by the Gallon."
Air, too, is a mixture of substances,
although all of them are gasses atroom tem-
perature. About 78 percent of our atmos-
phere is nitrogen (N); only about 21 percent
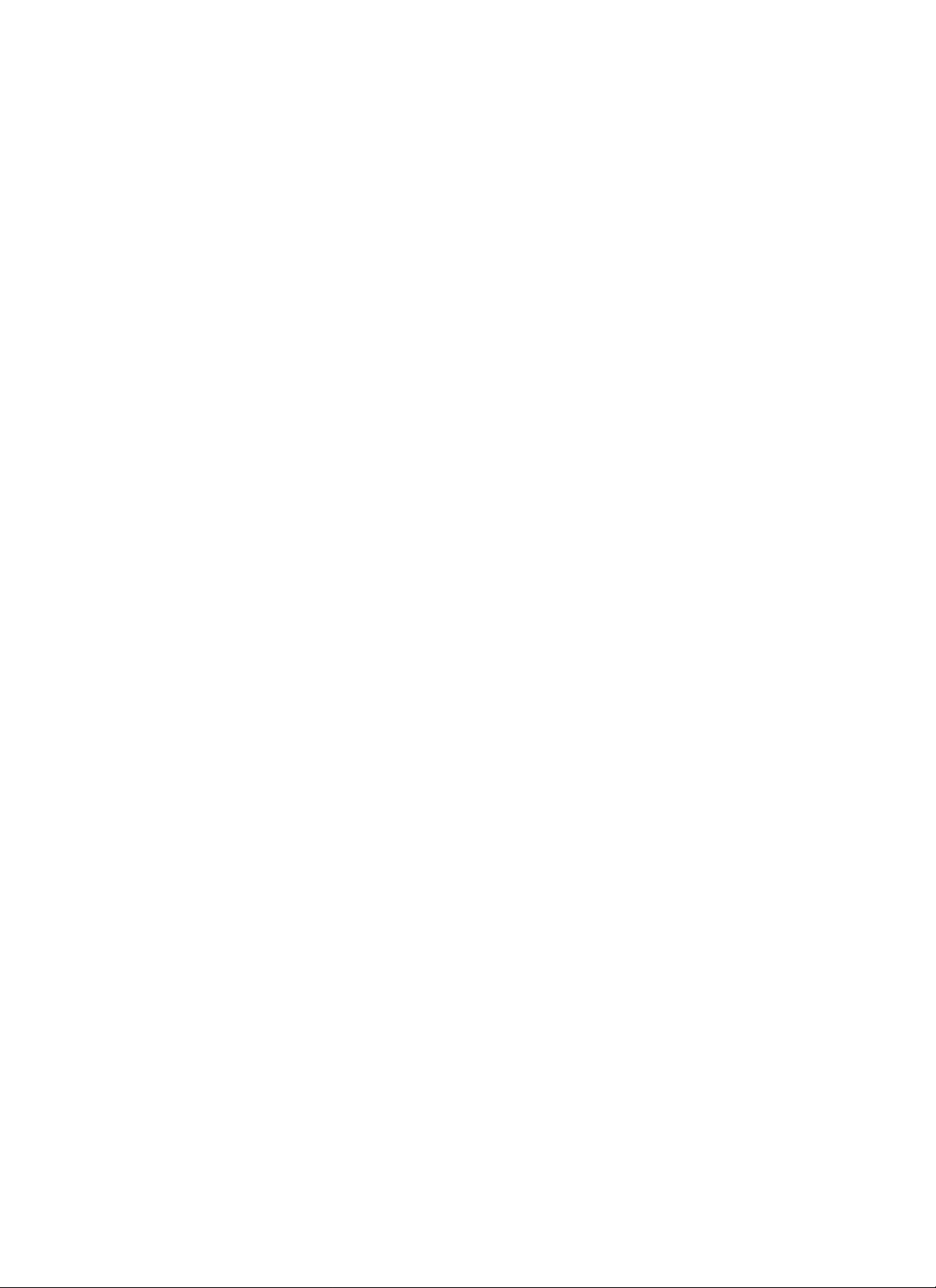
c...E
-~
=> c:
c.. 0
-;;'-'
0Q)
..s:;:""
.8
"E..
LL.
-
V'I
c:
=>
~
~
""
c..
a:Richmixture
b:leanmixture
0-
'-'
-
0
V>
.!!.!><
'i§~
c -
=>'-'
0=
""
.2:
"6
Q)
eo:::
co
a
.
~I.
0.8 1.0 1.2
ExcessAir Factor
Burning fuel with insufficient air results in carbon monoxide (CO) being formed, instead of carbon dioxide (CO2)' Excess fuel also leaves
unburned hydrocarbons (HC) in the exhaust. Paradoxically, a too-lean mixture causes misfires, which also lets unburned fuel escape.
Oxides of nitrogen (NOx) are produced in greatest abundance when the mixture strength is just a bit lean, when combustion is hottest.
(Robert Bosch Corporation)
of it is oxygen. The remaining one percent
or so is made up of several rare gasses, like
neon and argon, plus CO2 and water vapor.
The chemical reaction of burning gaso-
line-especially inside the cylinders of an
operating gasoline engine-is further com-
plicated by the presence of these other ele-
ments, and particularly the nitrogen.
Nitrogen is a comparatively inert sub-
stance-it does not readily react with any-
thing much, so in a simplified description of
b
..
0.6
0.8
ExcessAir Factor
1.0
1.2
1.4
combining with some of the oxygen, form-
ing various oxides of nitrogen- NO2, NO3
and so on-known collectively as NOx.
While for most purposes the minor involve-
ment of the nitrogen does not make much
difference, these nitrogen oxides are air pol-
lutants. Thus, while the idea of "burning" a
fuel seems a simple business, here is just one
factor that begins to reveal that it is some-
what more subtle and complex than it atfIrst
appears.
the burning of gasoline in air,the nitrogen is
ignored, on the assumption that it passes
right through the whole operation
unchanged. In fact, that is not quite true.
Exposed to the enormous temperatures and
pressures in the combustion chamber of an
engine, a little of the nitrogen does end up
(that is, weight) of air contains a certain spe-
cificnumberof oxygenmolecules,and any
givenweightof any specificgasolinelike-
wise contains some definite number of
Stoichiometric Mixture
Within narrow limits, a fixed quantity
2

Vegetables are a lot smarter than you might think. Millions of years ago, they man-
aged to harness the energy of sunlight in order to manufacture themselves from the
simple raw materials available to them, specifically water (H2O)from the ground and
carbon dioxide (CO2) from the atmosphere. A plant-a tree, for instance-grows by
using solar energy to split the CO2 into separate atoms of carbon (C) and oxygen (0),
and then to combine the carbon with the water to make molecules of cellulose
(C6HlOOS)'In effect, a tree uses water and carbon to make more tree.
From the tree's point of view, the oxygen remaining after the carbon is split from the
CO2 is incidental, and so is cast aside, into the air. From our point of view, this aspect
of the process is vital- it is the reason we have a breathable atmosphere. (And you
thought those tree-huggers were as dumb as vegetables!)
Usually, once a plant dies, the cellulose breaks down, but the process is not exactly
a reversal of the original chemistry. In fact, some of the carbon and hydrogen the tree
has spent so much of its sun-energy input combining remain hooked together as mol-
ecules having a certain number (say, "X")of carbon atoms and some number (say, "y")
of hydrogen atoms, (CxHy), of which there are many hundreds of different ones. If
exposed and left to rot, the major product is likely to be a gas-methane (CH4)' other-
wise known as "swamp gas," or "fire damp.IIUnder certain conditions, however, entire
forests can get buried and, over the course of countless millions of years, subject to
enormous pressure from the weight above, the carbon and hydrogen atoms get re-shuf-
fled into more tightly clustered hydrocarbon molecules, many of which are liquids. All
of the world's oil (hydrocarbon) deposits are the age-old remains of this process of
decay and chemical rearrangement of vegetation.
When we subsequently extract, refine and bum some of this liquid sunshine, we are
recombining the hydrogen and carbon with oxygen. When we do so, the swapping of
chemical partners that occurs liberates all of the considerable solar energy that, over
years, went into the original separation processes. And it is that energy, in the form of
heat, that makes the wheels go 'round.
hydrocarbon molecules. Because the burn-
ing process amounts to individual atoms
combining with each other, it follows that
there is only one particular ratio of gasoline-
to-air that can ensure that all of the oxygen
molecules mate up with all of the hydrocar-
bon molecules. This theoretical ideal is
called a stoichiometric mixture.
If there is an excess of oxygen molecules,
some of them will fail to find partners. In
terms of the number of oxygen-hydrocarbon
pairings, and thus the amount of energy
released, the effect is as if we had started
with a smaller quantity of air. At the same
time, if there are too many hydrocarbon
molecules in relation to the amount of air,
then some of the hydrocarbons will emerge
from the combustion process unburned.
3
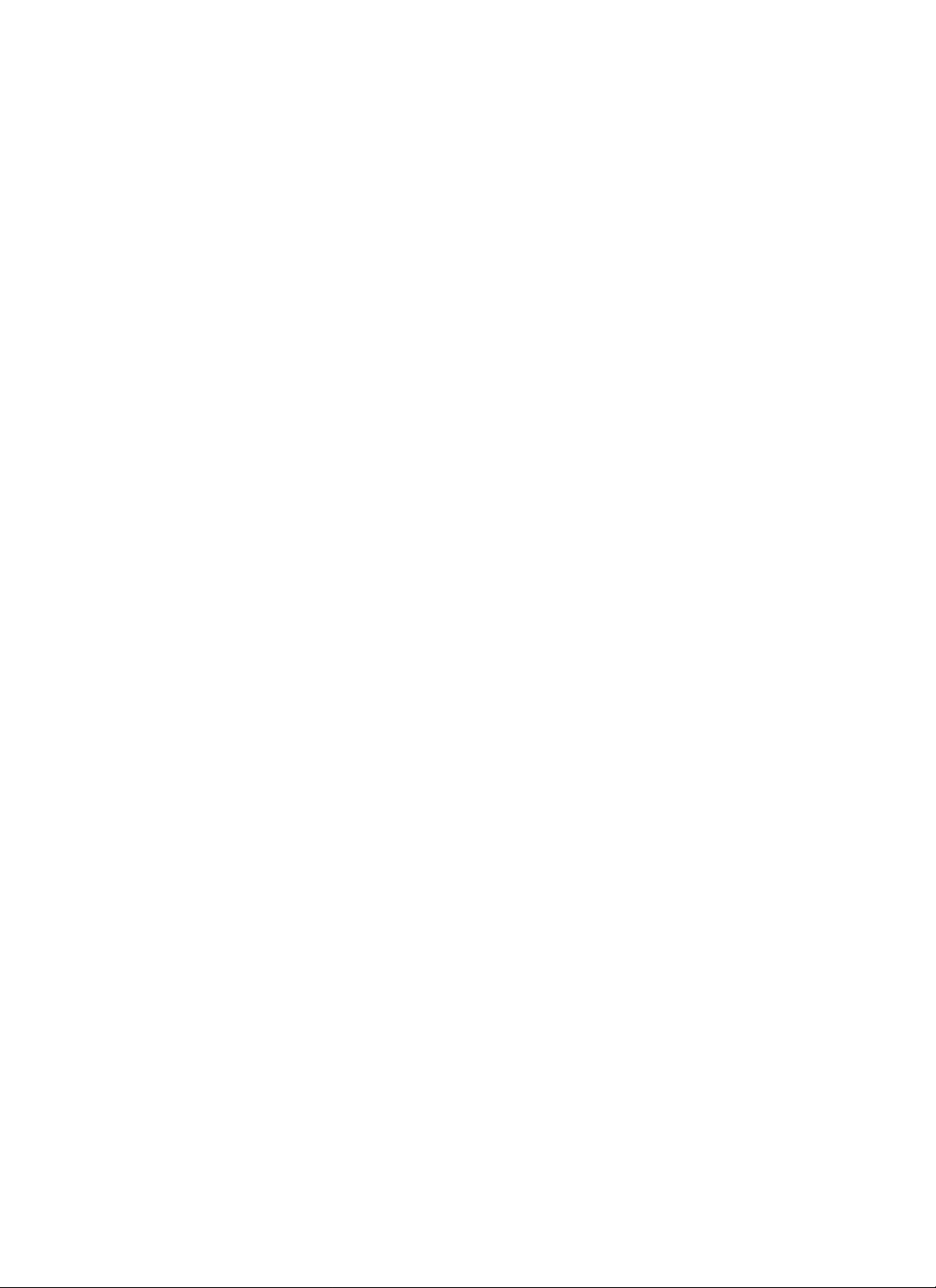
Some of the gasoline is simply wasted. Not
only that, but a shortage of oxygen means
that there is a likelihood of some of the car-
bon atoms in the hydrocarbon fuel to com-
bine with just one oxygen atom, rather than
two, yielding carbon monoxide (CO) rather
than carbon dioxide (CO2)' While CO2 is
one of the" greenhouse gasses" that are part-
1yresponsible for global warming, at least it
is only immediately harmful to animal life
when its concentration grows so large that it
displaces much of the oxygen we need to
breathe. CO, on the other hand, is toxic even
in small doses.
It turns out that about 14.7lbs. of air con-
tains the correct number of oxygen mole-
cules to pair up with the number of hydro-
carbon molecules in 1 lb. of gasoline. The
ratio of air to gasoline to achieve a stoichio-
metric mixture, in other words, is approxi-
mately 14.7:1, by weight. Note we say
approximately- there is no single number
that correctly identifies the stoichiometric
mixture for all gasolines. To explain, recall
that gasoline is a mixture of hydrocarbons.
Each has its own stoichiometric mixture
strength, ranging from less than 13:1 to
more than 15:1, so the stoichiometric ratio
for the entire blend depends on the propor-
tions of the differing hydrocarbons that
make it up. Apart from incidental variations,
the major oil companies deliberately modify
the blend of hydrocarbons in pump gasoline
from season to season and from place to
place, so the stoichiometric mixture may
correspondingly vary slightly, according to
where and when you buy the fuel. (See also
the sidebar "The Oxygen Battery,"page 34.)
As we have said, gasoline, strictly defined,
contains only hydrocarbons, but oil compa-
nies have also begun, fairly recently, to
include certain additives in gasoline that fur-
ther affect the chemically correct mixture.
Among the additives commonly found in
both pump and racing gasolines are ethyl
alcohol (ethanol) and methyl tertiary butyl
ether (MTBE). Both these substances are
4
examples of what are called oxygenates-
like the hydrocarbons we have been speak-
ing of they contain hydrogen and carbon,
but unlike the hydrocarbons they also con-
tain oxygen. A fuel carrying its own oxygen
adds to the amount inhaled by the engine, so
the presence of oxygenates means that a lit-
tle extra fuel is needed in relation to the
quantity of air the engine is breathing in, to
take account of the additional oxygen being
carried within the fuel- the stoichiometric
ratio becomes a little (numerically) smaller.
This is yet another reason why it is not pos-
sible to specify one exact stoichiometric
mixture strength for any and all gasolines.
Note, too, that the stoichiometric mixture
strength is expressed as a ratio of weights-
or more correctly, masses-not volumes.
(The mass of something is, in effect, a
"count" of the number of molecules in it.) A
certain mass of air- that is, a certain number
of molecules- will occupy more or less vol-
ume, according to its temperature. A cubic
foot of hot air contains fewer gas molecules,
including oxygen molecules, than a cubic
foot of cold air. Other factors, like baromet-
ric pressure and altitude also affect the den-
sity of air-the weight of a certain volume,
in other words. For that matter, the density
of gasoline also varies with temperature,
though not nearly as much.
While the ideal of stoichiometry expresses
the chemically correct air-to-fuel ratio for
any particular gasoline blend, gasoline will,
in fact, burn in air over a spread of ratios
from about 6:1 to more than 24:1.Mixtures
that contain more fuel than the theoretical
optimum are said to be "rich," while those
with an excess of air are termed "lean." For
maximum power production, there is some-
thing to be said for mixtures that are some-
what richer than stoichiometric.
To begin to explain, consider a four-cycle
engine turning 6000rpm. At that speed, each
power stroke lasts just 1/400 of a second. To
get an idea of just how short a time that is,
sight through the shutter of an unloaded
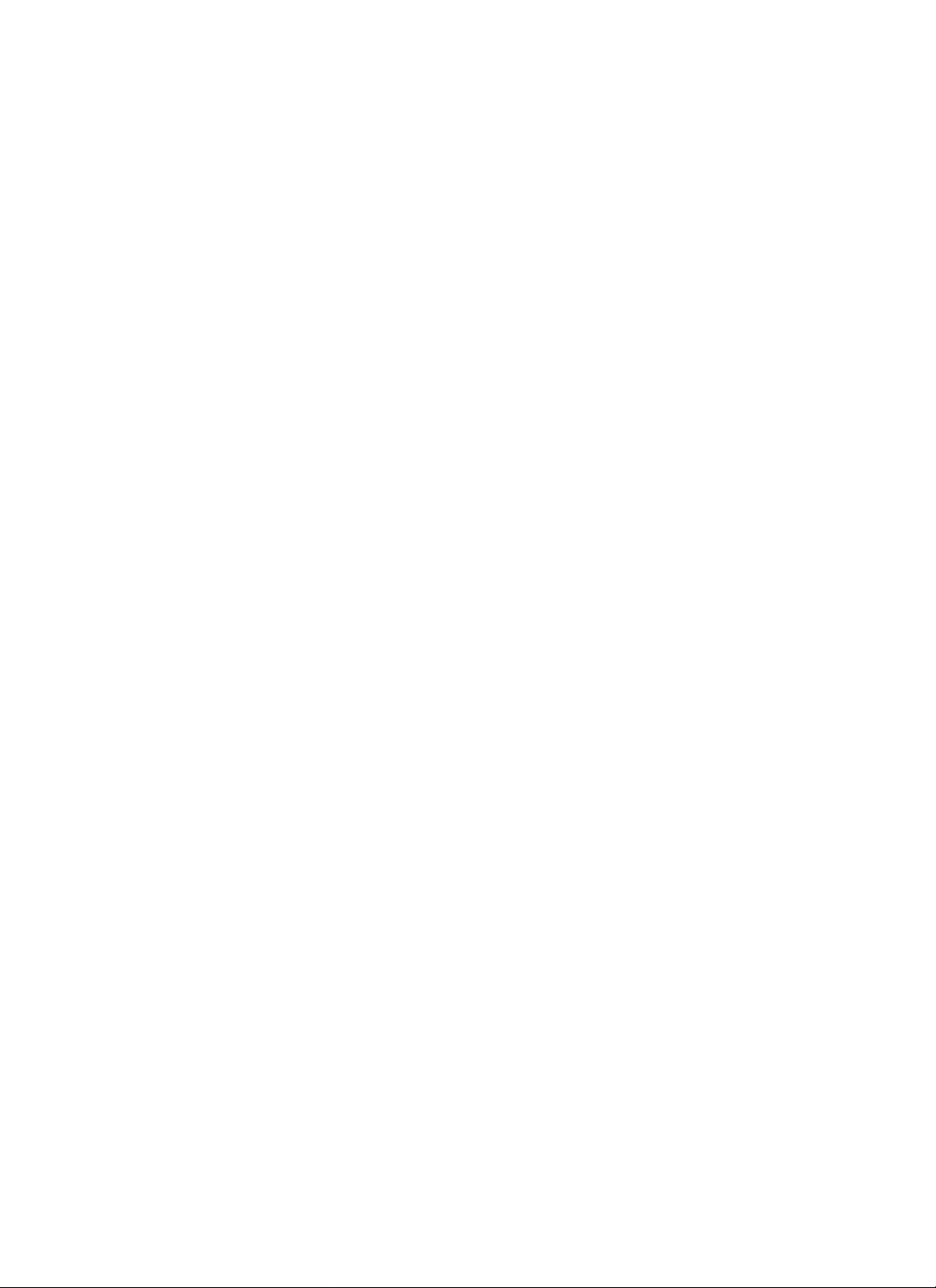
~
Ii:!
~
0
~
Ii:!
rn
~
0
~
0.75
11.0
0.80
11.8
0.85
12.5
0.90
13.2
0.95
14.0
1.00
14.7
1.05
15.5
RICHER ....
Maximum power is produced with a mixture just a bit richer than the chemically "correct" ratio. Power tapers off sharply with increas-
ing richness beyond that point, and more slowly as the mixture is leaned-out.
camera set to that speed, and push the but-
ton. Even though the combustion event
involves extreme turbulence that violently
stirs and mixes the different molecules, it is
extremelyunlikelythateachandeveryoxy-
gen molecule will be able to find a hydro-
carbon molecule to react with in such a brief
flicker of time. Yet for maximum power we
want maximum heat, and the heat comes
from the combining of the hydrocarbon
molecules in the fuel with the oxygen mole-
cules from the air.
An engine'scylindersare of a fixedsize,
however,so the maximumquantityof air,
andsothenumberofoxygenmolecules,that
eachcylindercaninhaleis limited.Formax-
imumpower,we wantto makesurethatall
the oxygenmoleculesavailablein the fixed
amount of air inside the cylinder react with
a hydrocarbon, and the way to do that is to
provide some extra hydrocarbon molecules.
And the way to do that, in turn, is to provide
a mixture that has a little excess fuel- a
slightly rich mixture. As noted, however,
that extra gasoline is wasted; it also adds to
air pollution. Unburned hydrocarbons, or
"HC," are another of the exhaust pollutants
that environmental laws seek to control.
On the other hand, if we are prepared to
sacrifice a little power, we can make maxi-
mum use of the quantity of fuel burned by
providing a slightly lean mixture. In the
same way that a little surplus fuel ensures
that allthe oxygen gets used, a little extra air
helps ensure that every hydrocarbon mole-
cule finds an oxygen molecule to mate with.
1.10
16.2
LEANER
1.15
16.9
A
A/F ratio
5
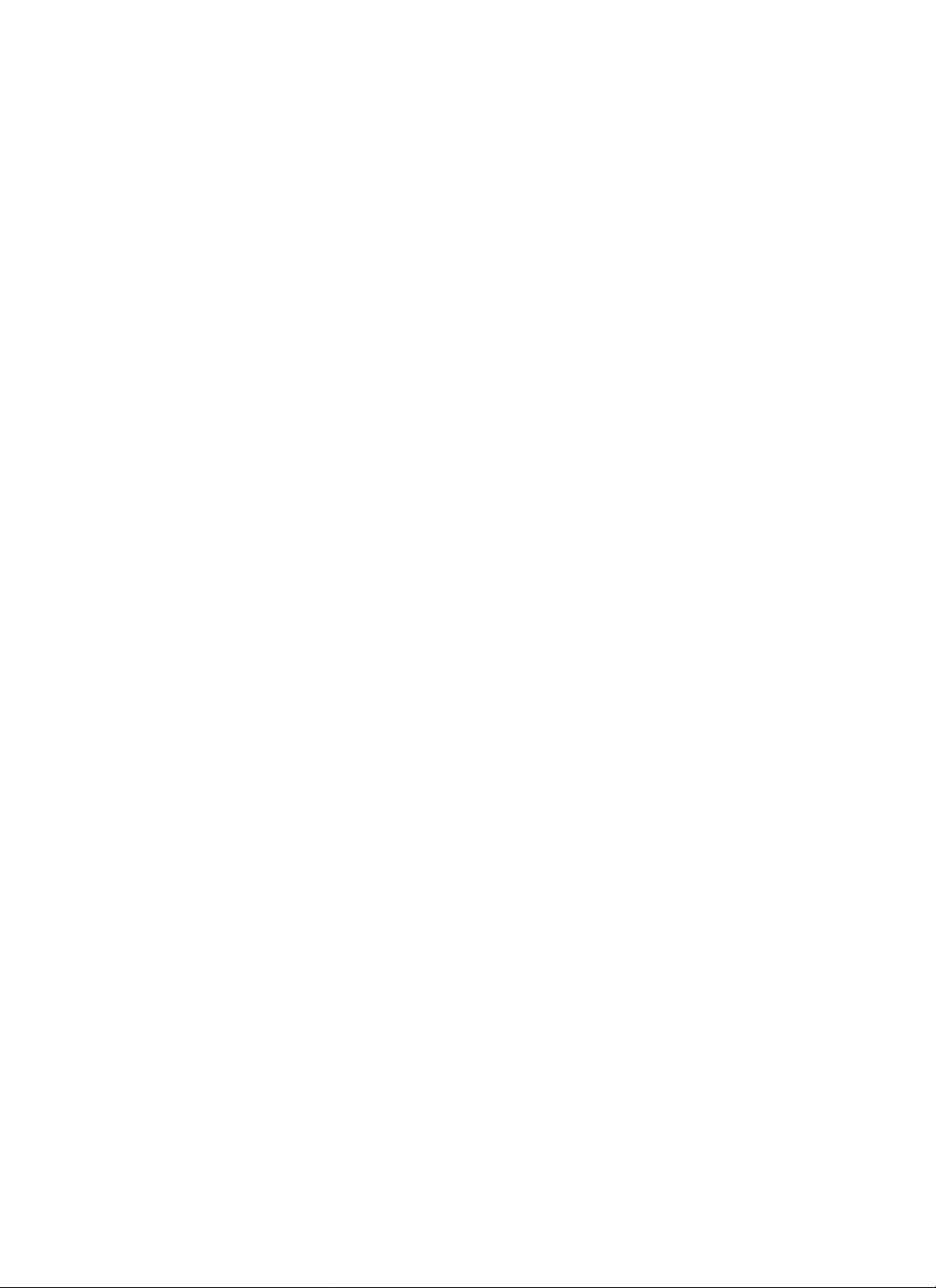
This can reduce, if not eliminate, HC emis-
sions. Within limits, it also leads to lower
fuel consumption for a given power output.
Most fuel injection (PI) systems-and
most carburetors, for that matter- take these
considerations into account in their design
and operation. During light load operation,
such as occurs when cruising at a constant
modest speed with a comparatively small
throttle opening, the system leans the mix-
ture out a bit, to enhance fuel economy and
minimize HC pollution. When the driver
opens the throttle wide, demanding full
power, the system provides a richer mixture,
at some cost to fuel economy and HC levels
in the exhaust.
There are other aspects to the rich-mix-
tures-equal-maximum-power issue. First,
when gasoline evaporates, it soaks up a lot
of heat in the process, as you probably know
from spilling gas on your hands in cold
weather. The internal cooling effect of a
slightly rich mixture reduces internal tem-
peratures somewhat, especially in critical
areas like the piston crowns and the edges of
exhaust valves. While modem street engines
are boringly reliable, the internal cooling
provided by a surplus of fuel can make a
considerable difference to the survival of a
race engine that is running on the ragged
edge of thermal self-destruction.
Also, the heat soaked up in the process of
boiling that excess liquid gasoline into vapor
can reduce the temperature of the air/fuel
mixture entering the engine. As we have
pointed out, cooler air is more dense than
hotter, so a cylinder full of an intake mixture
cooled in this way will weigh more (and
thus contain more oxygen molecules) than
otherwise. This accounts for some slight
potential gain in power output.
Detonation
Another consideration relating to the con-
nection between mixture strength and power
is the issue of the tendency of a gasoline/air
mixture to detonate. To explain, the burning
6
of fuel inside an engine cylinder is often
characterized as an explosion, but although
the combustion event is extremely rapid, it is
not, technically, an explosion. Once initiated
by the spark, the burning begins as a small
bubble of flame around the plug electrodes.
Under normal conditions, the burning
process then spreads rapidly but smoothly
throughout the rest of the mixture as an
expanding ball of fire.
In some circumstances, however, the com-
bustion may start off smoothly enough, but
as the flame-front expands through the com-
bustion chamber, the rapidly rising tempera-
ture and pressure ahead of it causes complex
chemical changes in the unburned mixture
furthest away, called the end-gas. Squeezed
and heated by the approaching fireball, it
changes from a predictable, slow burning
mix into something far more unstable. As a
result, the overheated end-gas ignites spon-
taneously almost all at once, the pressure
inside the cylinder rises sofast it is more like
an explosion than a controlled bum, and the
resulting shock wave rings through the
motor. That is detonation, or "knocking."
The sharp pressure spike that results when
this violent secondary event meets up with
the original flame front can punch holes in
pistons. Even if it does not, the turbulence
created by detonation scours against the sur-
faces of the combustion chamber, allowing
heat to flow out of the swirling gasses and
into the surrounding metal much faster than
normal. As a consequence, the gasses lose
heat, their pressure accordingly falls, and
power drops off immediately. (Although the
peak pressure during detonation is much
higher than during normal combustion, the
average pressure is way down, because of
this heat loss.)
Because the changes preceding detonation
are chemical, the ability of a particular blend
of gasoline to resist detonation depends on
the chemistry of the blend, and thus in turn
on the various hydrocarbons that make it up.
Overall, the knock-resistance of any sample
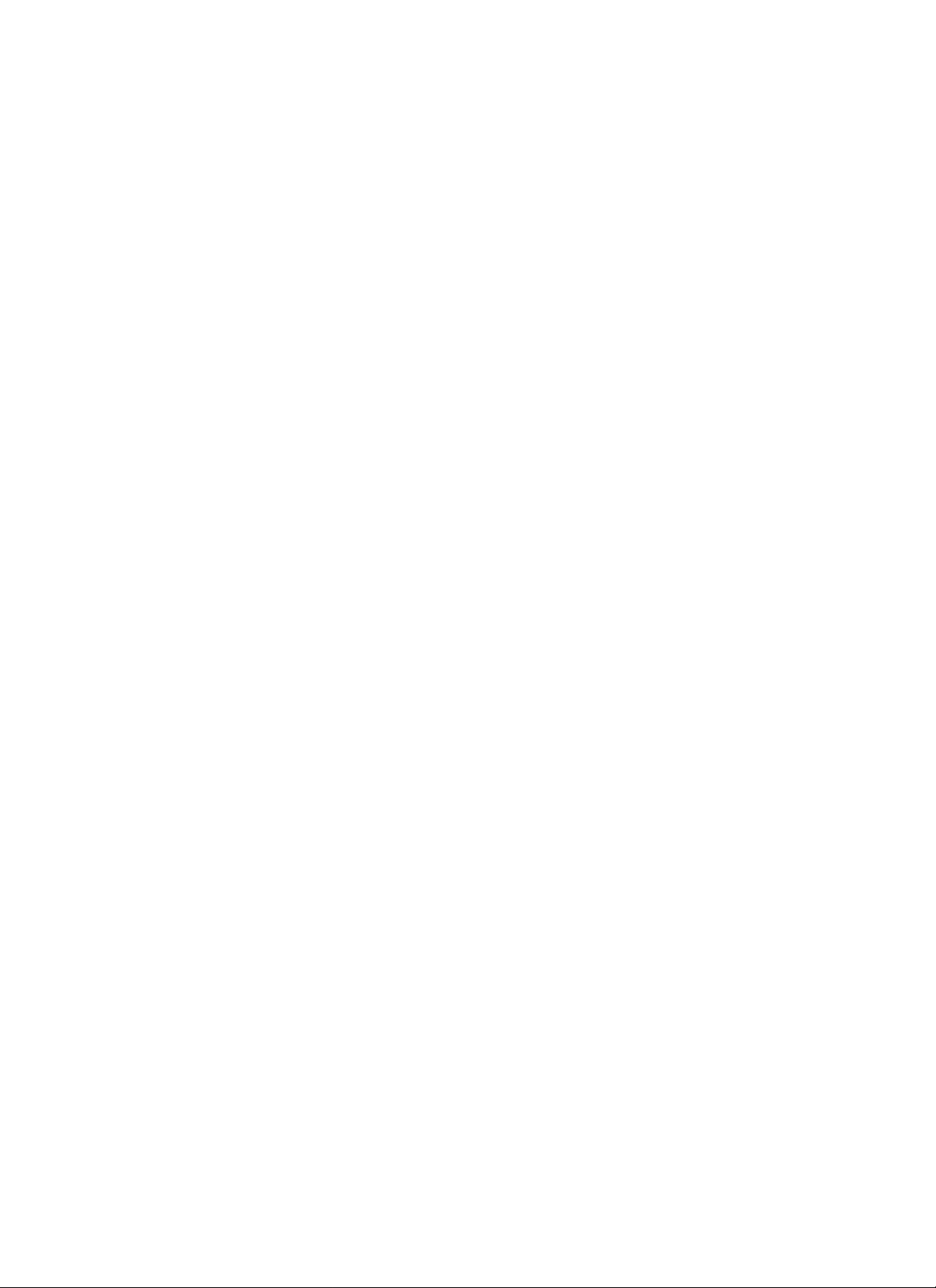
~
0
.r-!
--j-J
~
s
~
IJl
~~
0 H
U~
r--i p...,
Q) ~
~ ~
~~
,D
U ~
.r-! ~
4--1
'F9
U
OJ
~
UJ
maXImum
economy
maXImum
power
stoichiometry
Horsepower
of gasoline is expressed by its octane rating
(see the sidebar "Doing Octane Numbers"),
but the number so obtained also depends to
some extent on the mixture strength. Some
gasoline components knock worst when run
rich; some others increase substantially in
knock-resistance with wholesale enrich-
ment. Predictably, these latter are found in
abundance in race gas.
For typical pump gasoline in a typical
engine, the mixture ratio for peak power is
likely to be in the area of 12:1. Depending
on the particular blend of gasoline, anything
richer than that may exaggerate detonation
problems, and the cooling effect of the sur-
plus fuel, if carried to extremes, may sap
some of the heat that we would rather have
working to raise the gas pressure. For better
..
mileage and lowest HC emissions, some-
thing closer to 16:1 is wanted. Indeed, at
comparatively high engine speeds under
very light load, mixtures as lean as 18:1may
offer even better fuel economy. Such lean
mixtures burn hot, however, and that extra
heat, together with all those extra oxygen
molecules, makes it more likely that the sup-
posedly inert nitrogen will combine with
some oxygen, worsening the NOx emis-
SIons.
Optimizing an Engine's Diet
While the generalizations above are
broadlyapplicableto all engines,establish-
ingthecorrectair:fueldietfor anyparticular
engineover a fullrangeof speedsandloads
canonlybe achievedby a long andtedious
A mixture "fish hook,"
showing the points of
maximum power and of
maximum economy. Fuel
flow is expressed in terms
of the quantity used per
hour per horsepower pro-
duced.
7

0
.,....,
...f-!
.0.9
2,000
6,000
S
U2 ,.-....
I 0.8
0 I 0.7
u
ill I 0.6
'? I 0.5
.--1
u '-'
.,....,
'+--i
.,....,
U
Q)
U)
I 0.4
100 200 300
400
II
Horsepower
A series of fish hooks established at various engine speeds produce, when linked together, a curved band that represents the practical
range of mixture strengths for any given engine. The line forming the upper boundary of this band represents the mixture curve for max-
imum power; the lower one for maximum economy.
process that involves dyno testing. The
engine is run at some fixed throttle opening,
and the load is adjusted to keep the rpm con-
stant. Starting with a very rich air:fuel ratio,
the mixture is adjusted leaner in small steps,
and the fuel flow is measured at each setting
in, say, pounds per hour. As the mixture is
gradually leaned out, power initially
increases until some maximum is reached.
Further leaning results in a reduction in
power but, initially at least, the quantity of
fuel burned for each horsepower produced
actually grows smaller.
This relationship between fuel consump-
tion and power production is described by
8
the expression brake specific fuel consump-
tion, or BSFC. The first word, "brake," sim-
ply refers to the fact that the engine is being
run under load on a dynamometer, or
"brake." (The original dynamometer was
simply a friction brake; modem hydraulic
and electric dynos differ in construction, but
the principle of using a retarding device to
produce an artificialload remains the same.)
"Fuel consumption" is pretty obvious; it is
simply the number of pounds per hour
(lb/hr) of fuel being consumed at some par-
ticular throttle opening and speed.
"Specific" is actually a contraction of
"power-specific," meaning that the fuel con-

sumption at any given setting is divided by
the horsepower produced at that setting. The
results are expressed in units of pounds of
fuel burned per horsepower per hour-
Ib/hp/hr. As a rough rule of thumb, we can
figure that an unsupercharged engine burn-
ing gasoline will have a BSFC of about 0.5
Ibs/hp/hr at peak power. That is, an engine
making 300 hp will need to bum about 150
Ibs. of fuel per hour to do it.
At some mixture strength, the engine will
produce a maximum value of BSFC-a
maximum amount of power from each
pound of fuel, but this will not actually give
the maximum possible power.At somerich-
er setting, the power will likely be some-
what higher, but disproportionately more
fuel will have to be burned to achieve that
slightly higher peak power.As the mixture is
leaned out past the point of peak BSFC, the
power falls off markedly, as you might
expect. What is particularly interesting is
that the amount of fuel burned, in relation to
the power (the BSFC, in other words) actu-
ally increases-although engines can be
made to run on such extremely lean mix-
tures, it is actually wasteful of fuel to do so.
The results of such a test are then plotted on
a graph, with BSFC on the vertical axis and
power output on the horizontal axis. The
resulting curves resemble, and are called,
"fish hooks."
Once one such test has been completed,
the whole thing is repeated allover again at
some other engine speed, until the entire
operating speed range has been covered in,
say, 500rpm steps. Then the entire set of
tests is repeated at different throttle open-
ings. As we said, the operation is tedious.
Special Diets
One specialcircumstancethat requiresa
much richerthan stoichiometricmixtureis
cold starting.It maycomeas no surpriseto
learn that the various hydrocarbons that
makeup gasolinehavewidelydifferentboil-
ing points and so evaporate at differing
rates. At very low temperatures, some of
them may not evaporate at all, so the only
way to ensure there is enough of the ones
that do vaporize to make a burnable mixture
in air is to provide a lot of gasoline overall.
Typical cold start fuel-to-air ratios are
between 2-to-l and I-to-l.
Historically, there are two other situations
that are (or were) thought to demand a rich
mixture-idling and acceleration. Certainly
idle enrichment is needed on typical carbu-
reted engines, and to a lesser extent on those
with throttle body injection (TBI) systems,
but this is mainly a matter of the problems
that arise from trying to distribute from a
central point all the air:fuel mixture needed
by a multi-cylinder engine. Proof that very
little enrichment at idle is necessary in prin-
ciple comes from current emissions-certi-
fied production engines, which get by with
idle mixtures very close to stoichiometric.
The other situation conventionally thought
to demand significant enrichment is acceler-
ation. Every successful carburetor ever
made had either an accelerator pump that
shot in an extra squirt of fuel every time the
throttle was opened, or (more rarely) some
other means to temporarily richen the mix-
ture under sudden throttle opening. It seems
that much (although not all) of this "need,"
too, turns out to be due to secondary fac-
tors- in this case the nature of carbure-
tors- rather than a characteristic of the
needs of engines themselves. In view of that,
this seems as good a time as any to veer off
from our consideration of the kinds of food
that engines prefer and to look at the various
methods for bringing that food to the table.
The Drawbacks of Central
Distribution
For satisfactory engine operation, whatev-
er mixes the fuel and air has to closely
match, in terms of air:fuel ratios, the various
feeding requirements of the engine under
differing conditions, and must be able to
move smoothly and continuously between
9

Ideally, all fuel ingested by the engine would be in the form of vapor. In practice, some droplets remain.
Squirting the fuel through a small orifice under considerable pressure improves atomization, which is one
reason why fuel injection is superior to carburetors. (Robert Bosch Corporation).
10
them as the situation requires. There is more
to it, however, than just keeping the propor-
tions right. Large blobs of fuel haphazardly
distributed throughout the air just will not
do, even if the overall proportions are cor-
rect.
To begin to understand the reasons for
this, imagine setting fire to a tablespoon
measure full of gasoline. Yes,it willbum off
fairly fast, but consider that an engine mak-
ing 225hp goes through about that much gas
every second. Allowing for the fact that each
power stroke occupies at most half of acom-
plete revolution of the crankshaft, and that it
takes two full revolutions for a complete
engine cycle, the combustion event in the
engine obviously occupies, at most, one
quarter of that time. Youcannot bum a table-
spoon full of gasoline in one quarter of a
second.
Vaporization-If you were to divide the
same amount of fuel into, say, three tea-
spoon measures and set them all alight
simultaneously, then the gas will bum more
quickly. If you further divide it into large
droplets, it will bum quicker still. The more
finely you divide the fuel, the more surface
area each particle has in contact with the
oxygen in the air, in relation to the volume
of fuel within the droplet, so the faster the
energy gets released. The ideal would be to
divide the fuel into the smallest possible
units-individual molecules. In that case we
will not see any liquid fuel at all; it will all
exist as a true vapor. In fact, we cannot usu-
ally get quite that close to perfection, so the
intake charge will consist of a mixture of air,
gasoline vapor and fine droplets. One of the
inherent advantages of fuel injection over
carburetors is that the fuel is introduced into
the intake air under comparatively high
pressure. In the same way that a shower
head produces a fine spray when the taps are
cranked all the way open, but gives forth

large drops when the taps are nearly closed,
the pressurized mist issuing from a fuel
injector helps this process of vaporization.
. Intake PortAirflow-But thereismoreto
it than that. Consider one cylinder of a 320
cubic inch (ci) V-8, turning 6000 rpm. That
individual cylinder displaces 40 ci and so
inhales that much air every second engine
revolution (again, assuming it is a four-cycle
engine), for a total of 120,000 ci of air per
minute. That air flows through the intake
ports in the cylinder head and intake mani-
fold which may have a cross-sectional area
of somewhere around 3 square inches (sq
in). The average rate of flow through that
hole is simply the volume divided by the
area of the hole it flows through, so the
speed of flow is:
120,000/3 = 40,000 inches per second, or
about37.8mph. .
Now 38 mph doesn't sound like a particu-
larly high speed, but the air on its way to the
cylinder usually has to negotiate some turns,
and those turns can be mighty sharp-
maybe something like 3" radius. If you both-
er to do the arithmetic,you will discover that
the airflow negotiating a turn with a radius
of 3" experiences an acceleration equivalent
to 382 times the force of gravity (382 g).
Now, if all that is flowing through the
intake ports is air and fuel in vapor form,
those 382 g turns won't bother the gasses at
all. But with any arrangement that mixes the
fuel and air at a central location, those sharp,
high-speed turns really disturb the move-
ment of any fuel droplets that are mixed in
with those gasses. What will happen, in fact,
is that they will get centrifuged to the out-
side of the bend and form puddles of liquid
on the inside surfaces of the ports.
At first it may seem that this does not mat-
ter much; the fuel will get carried along by
the air rushing past and will eventually make
its way into the cylinder and the correct fuel-
to-air ratio will be maintained, at least on
average. But "on average" is not good
enough; the mixture strength in the cylinder
will vary from moment-to-moment, accord-
ing to the whims of the puddles. Of course,
if there is only one cylinder, there is less
need for bends in the intake plumbing, but
things turn really ugly when we are dealing
with more than one cylinder eating from the
same trough, so to speak.
When multiple cylinders are fed from one
common source, as is the case with TBI and
carburetor induction systems, there must
inevitably be bends, and probably lots of
them. Unavoidably, this fuel-drop-out effect
will favor some cylinders and short-change
others. In the days before concern about
emissions (which means in the days of car-
buretors), a variation of four numbers in
mixture strength between cylinders in the
same engine was not uncommon-some
cylinders might be working on 16:1, others
on 12:1.To keep the engine lit at idle, it was
necessary to provide a surplus of fuel over-
all in order to ensure that the leanest running
cylinder got a burnable mixture. With
painstaking development of the manifold
design, it is possible to reduce this cylinder-
to-cylinder variation, and modem manifold
designs for engines fitted with carburetors or
TBI systems do much better than in the bad
old days. Still, the desirability of ensuring as
nearly complete vaporization as possible
should be obvious.
At idle speeds, the speed of the flow of
gasses through the ports is obviously vastly
reduced, so the tendency of droplets to sep-
arate out from the gas flow because of cen-
trifugal forces will be dramatically
decreased. At the same time, the high vacu-
um condition existing in the intake manifold
of an idling engine encourages fuel droplets
to vaporize. In the same way that water boils
at a lower temperature (that is, evaporates
more readily) on a mountaintop than it does
at sea level, gasoline evaporates more readi-
ly in thin air than when it is more dense.
Ironically, the problem of incomplete atom-
ization remains- at least for carbureted
engines-simply because the lower rate of
11
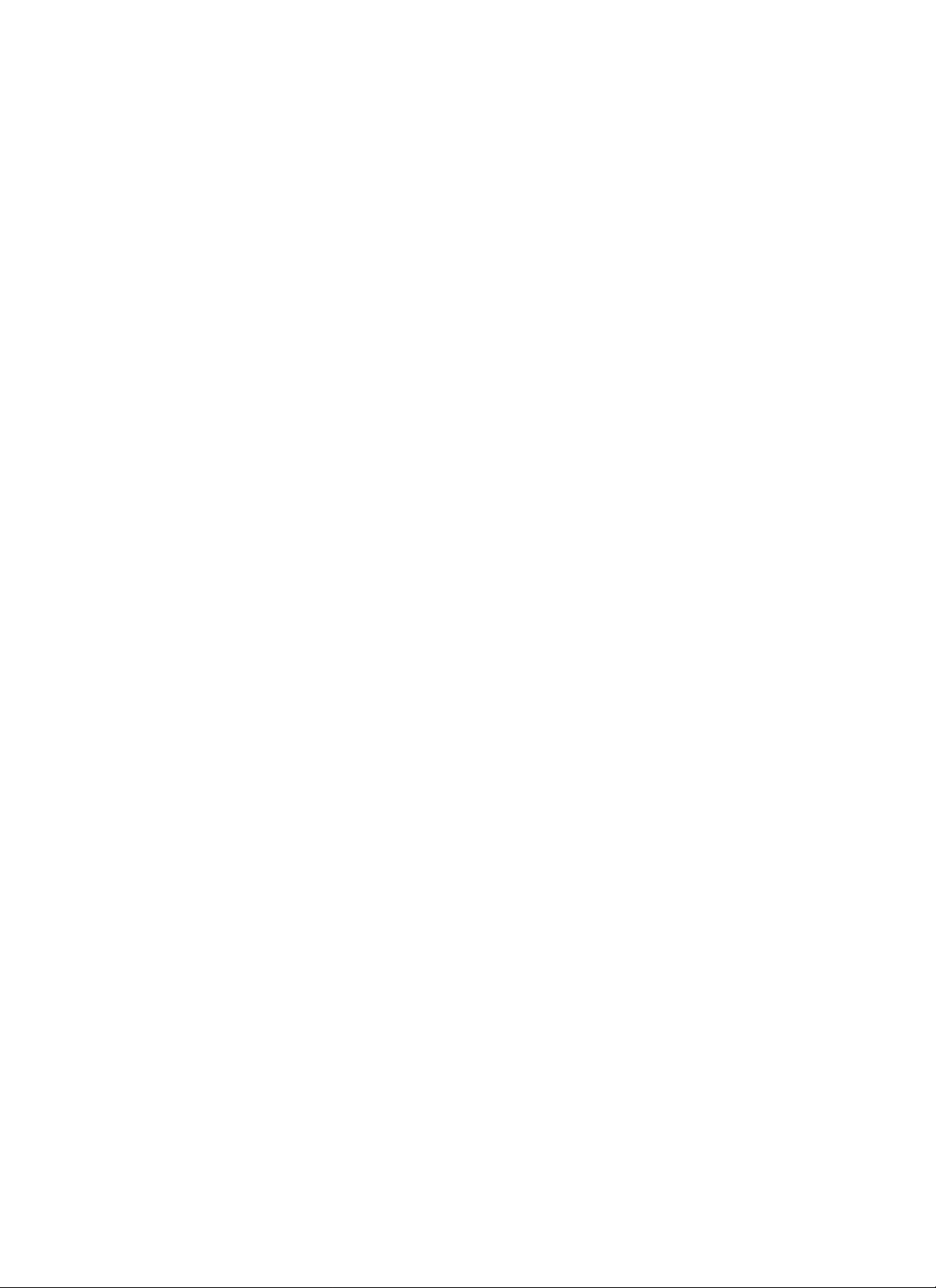
Single Point Fuel Injection (TBI)
!.Fuel
2.Air
3.ThrollieValve
4.IntakeManifold
5.Injector
6.Engine
1
===>
{J/0
W
-
---
~13
5
12
6
Introducing fuel at a single point-whether from a carburetor or a throttle body injector-"wets" a large
area of manifold surface, and gives unevaporated droplets many chances to drop out, forming puddles of
fuel. (Robert Bosch Corporation)
flow meansreducedturbulencewhichmight
otherwise break large droplets up into small-
er ones.
Quite apart from the matter of the rate of
flow, there are other factors at work that
oblige engines with a "central mixer"-and
especially those fitted with a carburetor-to
operate with rich air:fuel ratios at idle. Two
of these are charge dilution and reversion,
terms we shall soon define.
Valve Overlap-To explain, in the kind of
idealized engine that appears in beginner-
level explanations of how piston engines
work, the intake valve opens at top dead
center (TDC) of the intake stroke and closes
at bottom dead center (BDC). Following the
compression and power strokes, the exhaust
valve opens at BDC, and closes again at
TDC. Yet surely anyone reading this book
knows that on all real world engines the cam
timing is arranged to open the valves earlier
and close them later than this.
The reason for this is the inertia of the
intake and exhaust gasses. Although gasses
are very light, they are not weightless-a
cubic foot of air, for example, weighs about
0.08 lbs. Thus, as the valves open and close,
and the columns of gas passing through the
ports on their way to and from the combus-
tion chamber start and stop, the inertia of
those gas columns makes them lag behind
piston movement. Togive sufficient time for
emptying and filling the cylinder, especially
at high engine speeds, the intake valve
opens before TDC and closes after BDC,
while the exhaust valve opens before BDC
of the power stroke and does not close until
after TDC on the exhaust stroke.As a result,
there is a period toward the end of the
exhaust stroke when the intake and exhaust
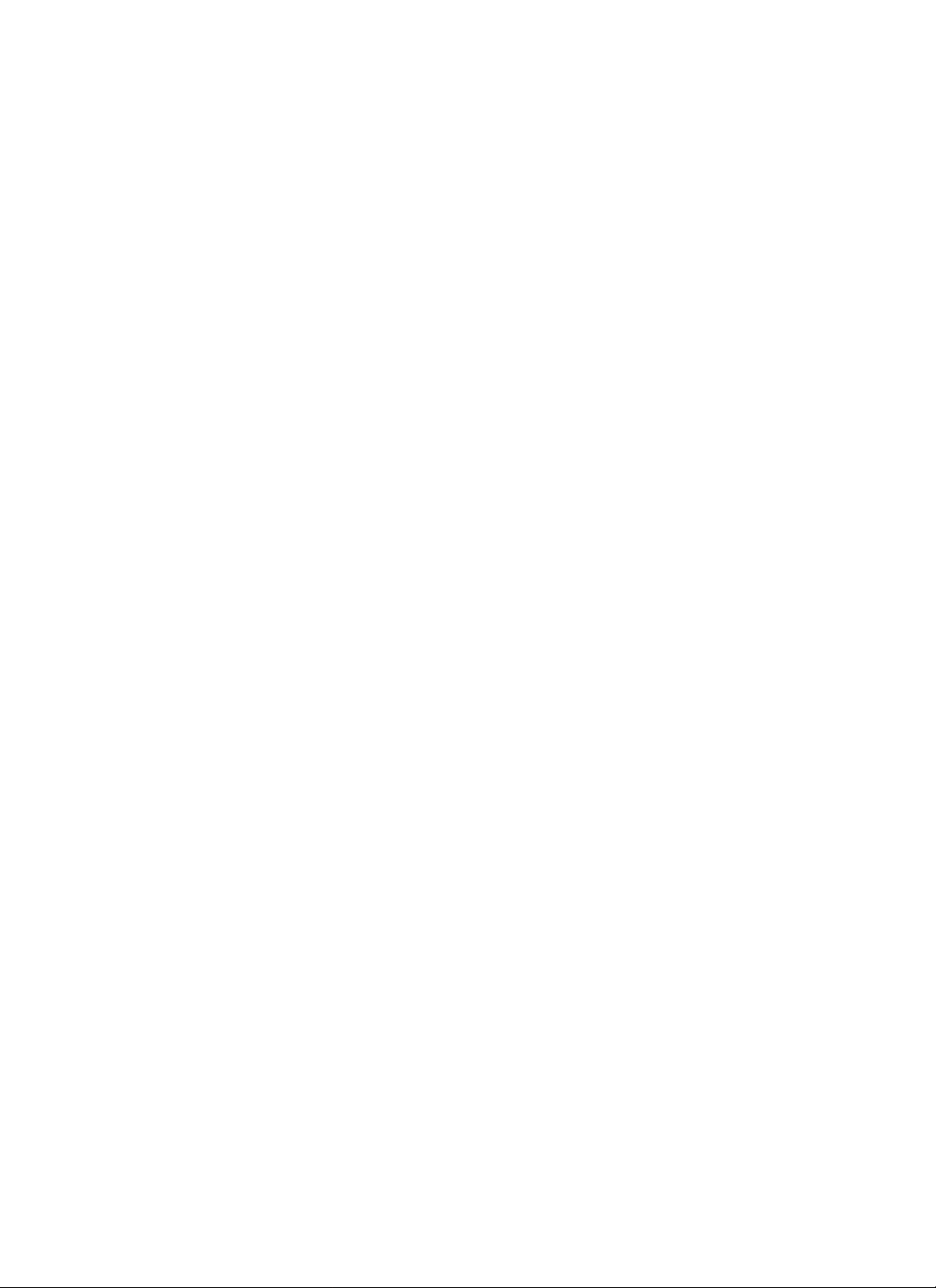
Multi-Point Fuel Injection (MFI)
!.Fuel
2. Air
3.ThrottleValve
4. Intake Manifold
5. Injectors
6. Engine
4
~
-v
I
~m
r r f ,
n
,A, i' 4, !
20
",P' I3
1-'.
!Il
rr
JAi
5
6
Multi-point injection ensures equal mixture strength at each cylinder. (Robert Bosch Corporation)
valves are both open together.
This valve overlap helps an engine to pro-
duce useful power at high speeds, as the
"lead"in the valve timing gets to be in synch
with the "lag" in the movement of the
gasses. But it also leads to problems at very
low speeds, because there is then obviously
an opportunity both for some of the fresh
intake charge to zip right out the exhaust
and/or for some of the exhaust gasses to
make their way backward, upstream, into
the intake manifold.
Charge Dilution-This intermingling of
exhaust gasses with the fresh intake mixture
that occurs at idle because of valve overlap
is termed charge dilution, and for years it
was argued that this demanded a rich idle
mixture, because the dilution tends to keep
the hydrocarbon and oxygen molecules sep-
arate.A hydrocarbon molecule atone side of
the combustion chamber, it was argued,
might be desperately seeking an oxygen
molecule at the other side but they would be
unable to meet, because of the crowd of
exhaust gas molecules in between.
While the above argument appears plausi-
ble, it is apparently at least partly wrong, as
confirmed by the near stoichiometric idle
mixtures of modem fuel injected engines.
The difference between these motors and the
typical rich-idle engines of a few years ago
seems mainly to be the difference between
the degree of variation in mixture strength
between one cylinder and another that exist
when the mixture for all an engine's cylin-
ders is delivered at one central point, such as
in a carbureted or TBI engine, compared to
one with multi-point fuel injection, in which
13
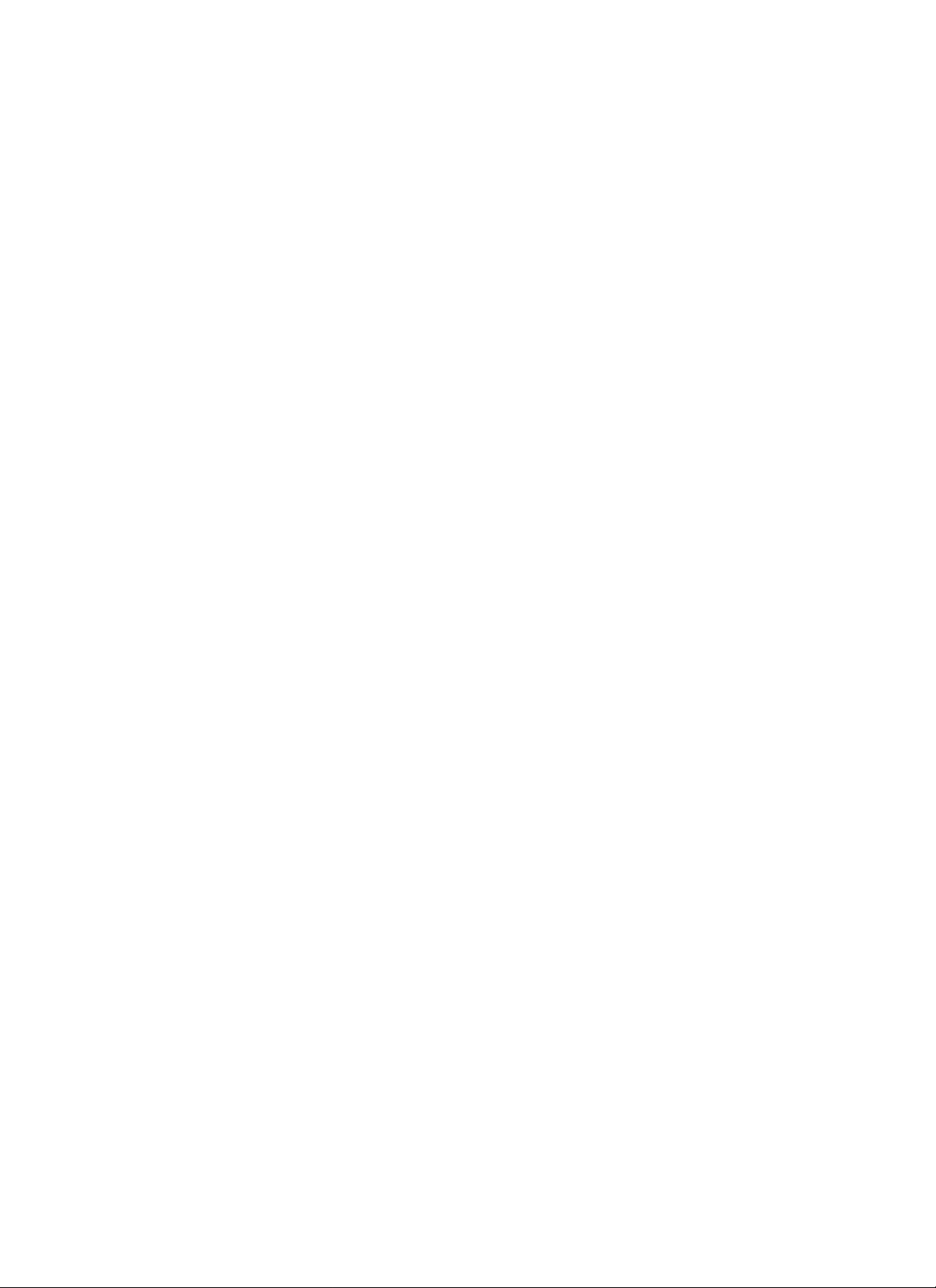
14
each injector is located near the one individ-
ual cylinder that it serves.
TBI engines, at least, are not afflicted by
another complication that affects carbureted
engines at idle, that of charge reversion. The
violent pulsations that occur in the intake
ports and manifold of an engine at idle speed
means that a portion of the flow on its way
to the cylinders sometimes actually reverses
direction- some of the intake air, already
mixed with fuel, actually pops back outside
briefly! This can sometimes be seen as a
pulsating cloud of air:fuel mist hovering
over the intake. Apart from being a potential
fire hazard, a consequence of this in-out-in-
again motion is that some air passes through
the carburetor three times. Because a carbu-
retor adds fuel to gas flowing through it, and
neither knows nor cares which direction the
flow is going, fuel gets added on every trip.
On the face of it, it should be possible to
adjust the basic idle mixture setting to take
account of this triple-dosing. Indeed, a cor-
rectly adjusted carburetor will do so, but the
reversion phenomenon is unpredictable, so
the mixture has to be set somewhat rich to
take account of the instants when it is inef-
fective.
Another area where fuel injectiori- at
least multi-point Fl, with each injector locat-
ed very near the intake valve it serves-has
an inherent advantage over carburetors is the
ability of Fl systems to cope with sudden
increases in engine speed and load. There is
certainly a need to shift from the leaner-
than-stoichiometric, best-BSFC air:fuel
ratio, to the richer-than-stoichiometric best-
power ratio ifthe throttle is suddenly opened
while cruising along at light load, but why
should the actual fact of accelerationitself
that the engine speed is increasing- intro-
duce any greater need for enrichment at any
instant during the acceleration than does any
other situation demanding that same power
output at the same rpm?
The answer to this is that, as previously
noted, some of the mixture supplied by any
-
"central mixer" will wind up as liquid on the
walls and floors of the ports and manifold.
This fuel will eventually flow to the cylin-
ders, but note that the density and viscosity
of this liquid fuel is much greater than that
of the air, gasoline vapor, and very tiny
droplets that make up the remainder of the
mixture, so its motion is much slower than
those gaseous and near gaseous compo-
nents.
Under steady state conditions, this "pool"
of fuel is being consumed and replaced
more or less equally all the time, so under
those conditions there will always be some
more-or-less constant quantity of liquid in
the manifold at any moment. That quantity,
however, will vary according to just what
steady state conditions prevail. Under large
throttle opening/high load conditions, the
density of the air inthe manifold and ports is
higher than otherwise and, as noted above,
gasoline evaporates less readily in air that is
dense than when it is thinner.
An engine operating under a large load
will thus require a larger quantity of liquid
fuel in the manifold in order to maintain
equilibrium between what gets consumed
and what gets supplied. On sudden throttle
opening, additional fuel thus has to be sup-
plied to rapidly build this pool up to the larg-
er size of "store" needed to maintain equi-
librium under the new, higher load condi-
tions.
It is noteworthy, too, that to encourage
vaporization under these and other condi-
tions, carbureted engines for street use are
almost always provided with some means to
heat the mixture in the manifold, whether by
the heat of the exhaust gasses (the familiar
"heat-riser") or of the engine coolant. While
this reduces the problems of having compar-
atively large amounts of liquid fuel washing
about in the manifold, the heating of the
entire intake charge lowers its density. As
we have already seen, hot air is less dense
than cooler air, so a cylinder full of such a
warm mixture will contain fewer oxygen
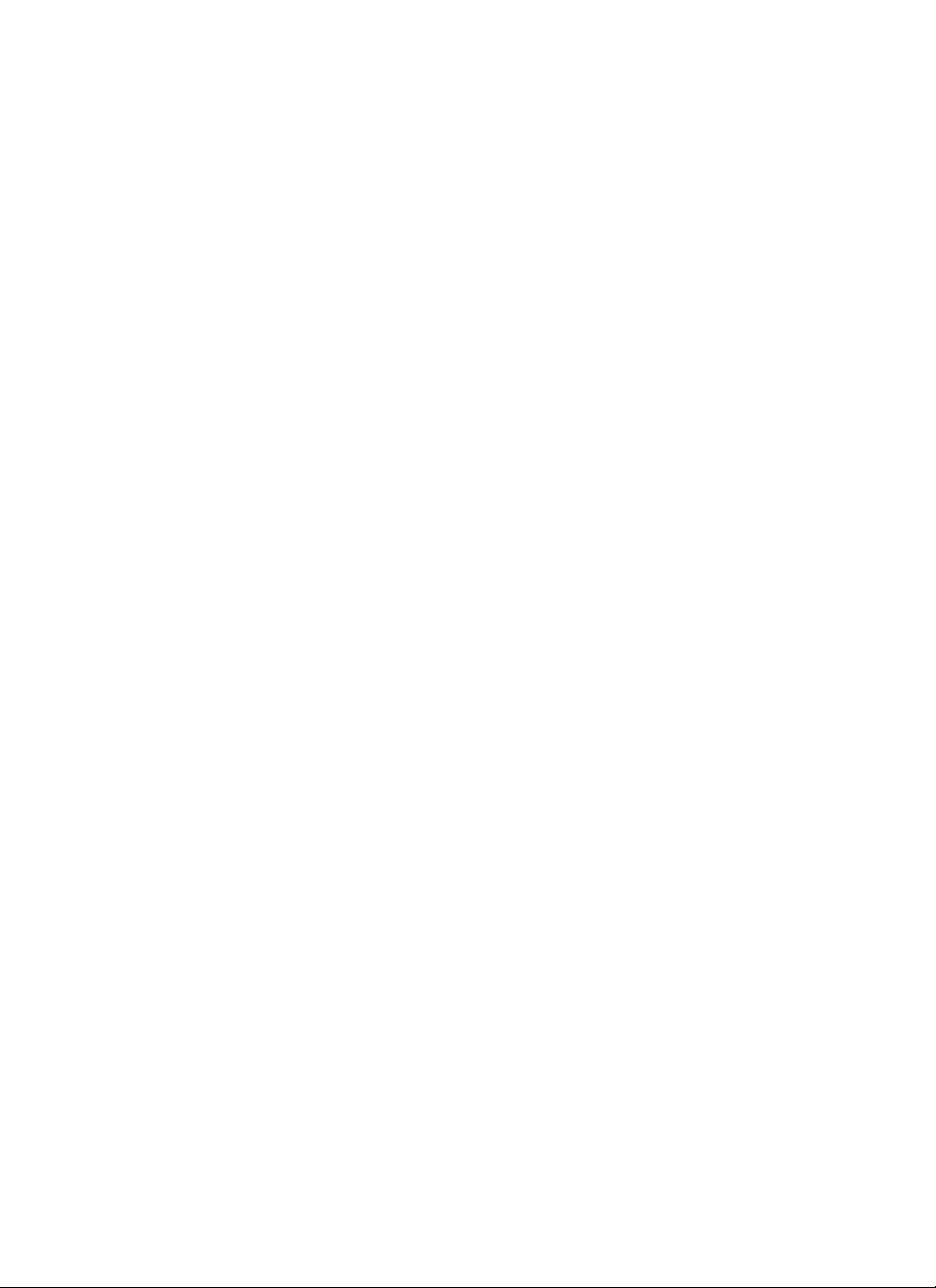
Mixtureformationintermittentinjectionontotheengineintakevalve.
Multi-point injection also provides the opportunity to locate each injector very near the valve it serves.
This reduces port "wetting," and so reduces the amount of enrichment needed for acceleration. (Robert
Bosch Corporation)
molecules- and thus can make less
power-
cool mixture. The vaporization problem is
most severe when the engine is cold, so
many engines provided with such a "hot-
spot" have some means to turn down the
heat once the engine is fully warmed up.
Usually,however, the heat does not getcom-
pletely turned off.
Tosome extent, this problem of wetting of
manifold and port walls also affects multi-
point fuel injection systems, to a degree that
depends on where the injector is located, rel-
ative to the intake valve. On some engines,
the injector is as close to the back of the
intake valve as possible. Here, clearly, the
length of port that is wetted by fuel is
extremely short, so the additional amount of
fuel needed to fatten up the "store" is mini-
mal. However, on other engines
for reasons of packaging, or access for ser-
thanthesamecylinderfilledwitha
- perhaps
vicing- the manufacturer decides to locate
the injectors a considerable distance from
the valves. The more remote the injectors,
and so the greater the length of the wetted
port and manifold, the more the additional
fuel requirements on acceleration resemble
those of a central mixer arrangement, such
as a carburetor.
Carburetors have an accelerator pump to
tide them over this transition, but the amount
of additional fuel supplied by the accelerator
pump of a carburetor considerably exceeds
the amount that should be needed to main-
tainthe "pool."Toseewhythis is so,andto
better understand some of the other short-
comingsof carburetors,we shouldend this
chapter by taking abrief look at their nature,
before moving on to consider the fuel injec-
tion systems that have now almost com-
pletely displaced them.
The Carburetor
The earliest attempts to feed a gasoline
engine hinged on wacky arrangements like a
drip-feed of fuel into the air intake pipe, or
an arrangement of cotton wicks with their
bottom ends immersed in a pool of fuel and
their upper ends exposed in the intake pipe.
These hit-and-miss methods at controlling
mixture strength came to an end soon after
the invention of a basic carburetor, in 1863,
15

VENTURI
DISCHARGE
TUBE
A rudimentary carburetor.
The essential features are a
"pool" of gasoline main-
tained at a constant height
by a float-operated valve; a
restriction (the main jet) to
regulate the flow; a venturi,
with a discharge tube con-
necting the low pressure
area in the venturi to the
fuel supply; and a throttle
plate, to control the total
amount of mixture flowing
through. There is also a cal-
ibrated air bleed, that
meters extra air into the
fuel before the discharge
tube, usually through a per-
forated "emulsion tube,"
that helps to atomize the
fuel.
16
,
'0
°0'
,°0°,
,gogo
°0°0°,
,°0°0°0
'°0°0°0'
***g,
'°0°0°0°0°
,gogogogog,
°0°0°0°0°00
;ggogogo:o:,
Cigggg ggg~g
0'0°0 °0°0 ,
00<5;0 °0'00,
,0gO;? gogo
,0000 00000
,gogo ogog,
'00000 °oooc
'00000 00000
'00000 00000,
'00000 00000,
;ogogo °ogogc
,gogog ogogog
'00000 000000
'00000 000000'
'00000 00000'
'00000 00000'
'000000 oOoooc
'000000 000000
'000000 000000
ogogog 020202,
000000 000000'
000000 °00000(
°o~o~o 0 0 Q
attributed to a Frenchman by the name of
Lenoir. By 1894, the German engineer
Wilhelm Maybach had advanced the devel-
opment of this device by including the now-
familiar float-and-needle-valve arrange-
ment, to maintain a reliable supply of fuel at
a constant height. Arguably, no small part of
the success of Karl Benz's "Patentwagen" of
1897 was attributable to its wearing one of
Maybach's float-equipped carburetors.
The adjacent illustration shows the essen-
tial workings of a simple carburetor. Fuel is
supplied by a pump to the float chamber (or
bowl), where a float and needle-valve
assembly maintains the contents at a fixed
level, very much like the float and valve
arrangement in your toilet tank. The float
chamber connects to a smaller reservoir-
the main well- so the fuel level in the well
will be at the same height as in the float
chamber. A pipe, usually termed the dis-
FLOAT
CHAMBER
-----------
MAIN
WELL
charge tube, leads slightly uphill from the
well to the carburetor's throat-the main air
passage through it. With the engine stopped,
at least, the level of the fuel will reach part
way up the discharge tube, close to- but not
quite-spilling out the end. At the point
where the discharge tube enters it, the car-
buretor throat is fitted with a narrowing
piece, called the venturi. Note, too, that both
the well and the float chamber are open to
the atmosphere at the top.
As the engine draws air through the carb
throat, the restriction created by the venturi
obliges the air to speed up. It is no coinci-
dence that the venturi is named after an
Italian physicist of that name; it was he,
G.B. Venturi, who established, a couple of
hundred years ago, that when a fluid passing
through a pipe or channel is forced to speed
up, its pressure drops. As a result of this phe-
nomenon,the pressurewithinthe venturiis
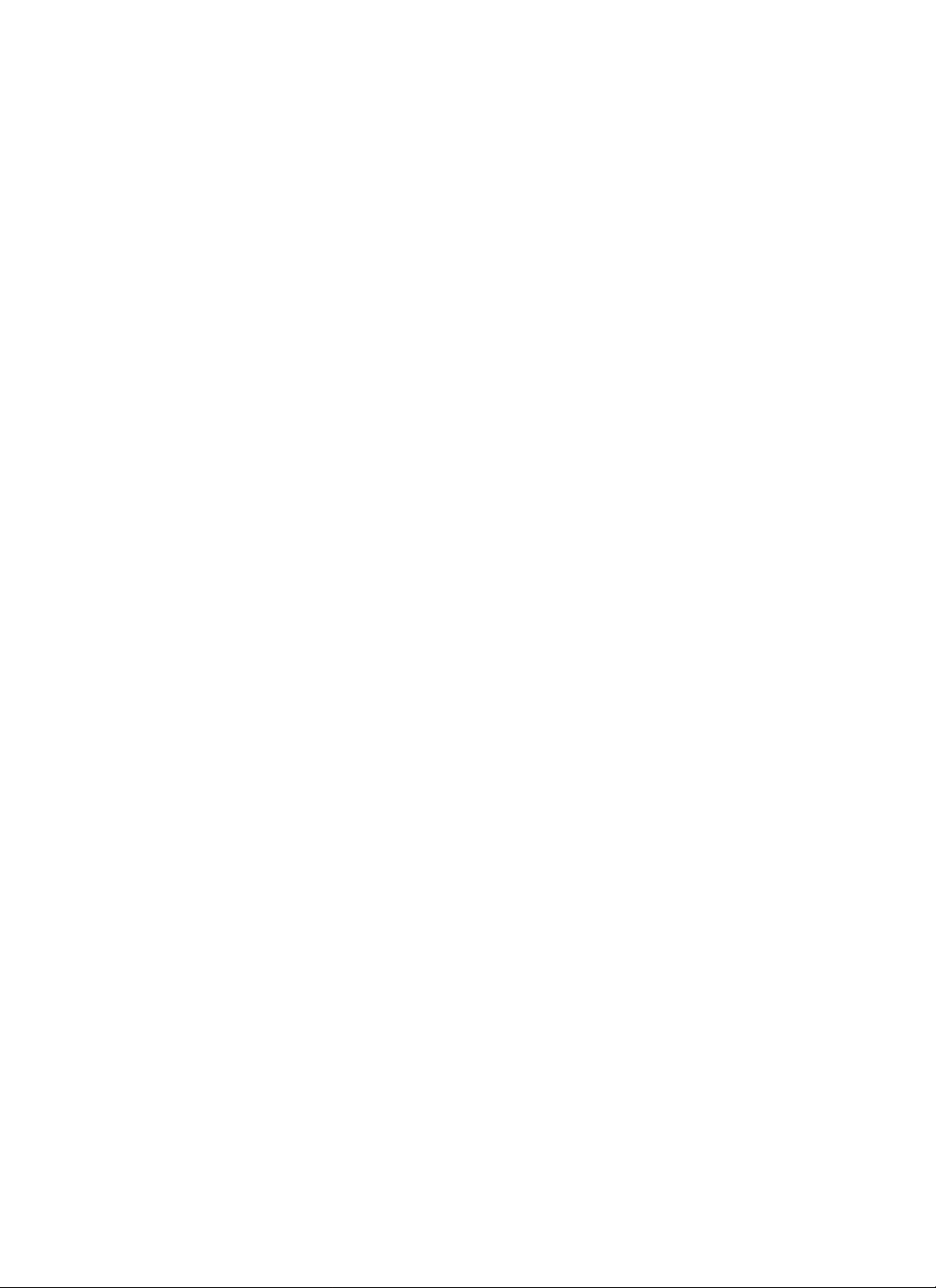
DOING OCTANE NUMBERS I
"Octane" is a measure of a fuel's detonation resistance, compared to two reference
fuels, both of them components found in pump gasoline. One, a particular hydrocarbon
called iso-octane, strongly resists knocking. It defines one end of the scale-lOa octane.
The other reference hydrocarbon, n-heptane, detonates like crazy, so it defines the zero
end of the scale. Mix the two together and you get a tendency to knock that varies from
zero to 100 according to the proportions of the mix. A fuel under test that behaves like a
90:10 mix of iso-octane and n-heptane, then, would be rated at 90 octane.
The actual measurement is performed using a standardized single cylinder test engine
which is specially designed to allow its compression ratio to be varied while the engine
is running. During the test, the compression is raised until the enginejust starts to knock.
From knowing exactly what blend of iso-octane and n-heptane would also just barely
knock at that CR, it is possible to establish the octane number.
Just to keep things baffling, though, there are two octane numbers, "Research" and
"Motor," established under different test conditions. From the chart below it appears that
the Motor method provides a more severe test. In fact, the Research method tallies clos-
er to real world experience in ordinary cars on the road. Toadd to the confusion, the num-
ber printed on a gas pump is the average of the Research and Motor numbers.
TEST CONDITIONS FOR RESEARCH
AND MOTOR METHOD OCTANE RATINGS
Research Method
(RON)
Inlet air temp. 1
Coolant temp.
Engine speed
Spark advance
Air/fuel ratio
25.6
212
600 rpm
13 degrees BTC
Adjusted for
maximum knock
lower than that of the surrounding atmos-
phere, which thus pushes the fuel out of the
discharge tube and into the carb throat.
The rush of air past the end of the dis-
charge tube tends to tear the fuel into
droplets, thus going some way to achieving
atomization. An air bleed at the top of the
main well allows a certain amount of air to
leak into the flow of fuel, via a perforated
sleeve called the emulsion tube, before the
fuel reaches the discharge tube, thus assist-
ing atomization. This is, in fact, almost a
Motor Method
(MON)
300.2
212
900 rpm
19-26 degrees BTC
(varies with CR)
Adjusted for
maximum knock
secondary function of the air bleed. Its pri-
mary reason for existence is to deal with an
odd phenomenon that would otherwise
cause the mixture to become ever richer as
the rate of airflow through the venturi
speeds up, as it does with any increase of
engine speed.
Because the pressure drop within the ven-
turi is a function of the rate of flow through
it, it might seem that the fuel flow would
increase in proportion, maintaining a con-
stant air/fuel ratio over a wide range of flow
17

rates. In fact, the ever-increasing pressure
drop at the venturi as the airflow increases
means that the air within it becomes increas-
ingly rarified. Meanwhile, the fuel flow,pro-
pelled by the pressure difference between
the venturi and the atmosphere, increases as
the volume of air increases, but the density
of the air is dropping at the same time. The
result is that the mixture grows ever richer.
A carburetor venturi, itturns out, is a volume
measuring device, rather than one that mea-
sures mass flow. The air bleed provides a
corresponding "leak" of air that compen-
sates for that phenomenon (indeed, it is
sometimes called a compensating circuit.)
A carburetor as simple as the one just
described would in fact work, and would
supply the engine to which it was fitted with
a reasonably constant mixture strength over
a reasonable range of speeds and loads, but
only if those speeds are constant and moder-
ately high. Under two sets of conditions, it
would fall flat on its face.
At very low flow rates, such as at idle, the
pressure drop through the venturi is so low
that the fuel cannot make it out of the end of
the discharge tube. In these circumstances
the carburetor cannot function at all. To deal
with this, most real world carburetors have
a separate idle circuit, in fact a miniature
carburetor-within-a-carburetor, that com-
pletely bypasses the main throat and ven-
turi. But we needn't bother ourselves with
the details of these.
The other situation that hobbles our simple
carburetor is changing from one speed to
another. (Actually, slowing down probably
would not present much of a problem;
speeding up, however, would.) We have
explained that air weighs about 0.08 lbs. per
cubic foot. While not weightless, this is vast-
ly less dense than gasoline, at about 43 lbs.
per cubic foot. Thus, if an engine should
suddenly begin to draw much more air
through the venturi, the airflow will speed
up almost instantly, but the fuel, because of
its greater inertia, will lag behind. As a
result, the mixture will lean out, to the point
where the engine will, in all probability,
quit.
To deal with this, most carburetors are
equipped with an accelerator pump, that
mechanically squirts an extra shot of fuel
into the venturi whenever the throttle is sud-
denly opened. Note, again, that this tenden-
cy to run lean on sudden throttle opening is
a peculiarity of carburetors. The accelerator
pump exists as much to make up for this
deficiency as it does to build up the larger
quantity of liquid fuel "store" in the mani-
fold, as described above.
18

espite the fact that there were a
thousand and one other problems
D
of the automobile, auto pioneers were quick
to focus attention on the shortcomings of
carburetors. The drawbacks included the
possibility of ice forming within the venturi
in cold, damp air, and a tendency to vapor
lock in hot weather when volatile fuels were
used. Conversely, carburetors were unsuit-
able for use with fuels that did not readily
vaporize (remember, the automobile came
first- gasoline followed, almost anything
that would bum was used as a fuel at one
time or another in the earliest days). Also,
the venturi restricts airflow, and thus power.
Because fuel delivery depends on the level
in the float bowl, a carburetor is sensitive to
the inclination of the car, such as when
climbing hills. In addition, there was some
dawning awareness of the problems of feed-
ing multiple cylinders from a single "central
mixer," as described in the previous chapter.
Accordingly, some of the critics set about
designing an alternative, specifically what
we now call fuel injection.
to be dealt with in the early days
Early Production FI Systems
Although there were even earlier experi-
ments, perhaps the first production applica-
tion of PI was by the German company,
Deutz, who built about 300 fuel-injected sta-
tionary engines around the turn of the centu-
ry. Hampered by a lack of precision manu-
facturing facilities, Deutz abandoned the
scheme soon after. (Deutz is still in the busi-
ness of manufacturing industrial and marine
diesel engines.) Perhaps aware of Deutz's
work, Robert Bosch began experiments with
fuel injection in 1912. In 1927, Bosch
bought the Acro company, and the patent
rights of an Acro employee, Franz Lang,
who had successfully developed the equip-
ment needed for high-pressure fuel injec-
tion. Shortly afterward, Bosch began manu-
facturing diesel injection equipment of a
pattern that has changed little in the 70-odd
years since (see sidebar "TheReal Jerk").
The adaptation of this system to gasoline-
fuelled engines began in the 1930s, initially
for use in aircraft. In this application, three
advantages of fuel injection over carburetors
stand out: freedom from problems of vapor
lock, no risk of icing, and a complete indif-
ference to the attitude of the vehicle. Vapor
lock is a significant problem at high alti-
tudes, because the reduced atmospheric
pressure there makes it so easy for the fuel
to evaporate that it is inclined to boil, form-
ing bubbles of vapor in all sorts of awkward
places that can effectively prevent any fuel
from getting to the engine. Carburetor icing,
while merely an annoyance in an automo-
bile, can be potentially fatal in an aircraft.
And a fuel system that can keep the engine
running no matter what the attitude of the
aircraft becomes a matter of first importance
during extreme maneuvers, such as inverted
flight. Most, if not all, Daimler Benz engines
fitted to German aircraft during World War
II enjoyed this advantage over their Allied
opponents.
Early Racing FI Systems
If we substitute severe cornering for
The straight eight engine of
Mercedes Benz's first post-
war FormulaOne race car-
this streamlined W196-
injected fuel directly into
each cylinder, a system
developed from Diesel injec-
tion principles. (Mercedes
Benz).
19

THE REAL JERK
In a diesel, the cylinder at the end of the compression stroke is filled with nothing but air; combustion cannot
begin until the fuel is injected. Thus, the moment of introduction of the fuel is equivalent to the ignition timing on
a spark-ignition gasoline engine. For that reason, control is needed over not just the quantity of fuel injected, but
alsothe timingof thatinjection. .
Because the fuel has to be kept separate from the air until the correct instant for ignition, the fuel is injected direct-
ly into the combustion chamber- the injector nozzle lies inside the cylinder. As a result of that, the injector is
exposed to full cylinder pressure during the power stroke. To prevent combustion pressure from blowing the fuel
backward through the fuel lines, the injector is fitted with a very stiff spring-loaded check valve. This check valve
also performs a number of other important functions. It prevents fuel from dribbling out of the injectors between
timed squirts, and ensures that the start and end of each injection is clearly defined. Without this valve, the fuel
spray would taper off gradually toward the end of each injection. The check valve, in conjunction with similar
check valves at the pump outlets, also ensures that the fuel lines leading from the injection pump remain filled with
fuel at full pressure, to ensure that the pressure pulse from the pump is transmitted immediately to the injector noz-
zle. To overcome the resistance of these check valves, the entire system has to operate at a very high pressure-as
much as 3000psi!
The design of the classic diesel injection pump, and the gasoline injection pumps directly derived from that
design, follows from the three requirements: to control the quantity of the fuel delivery,and its timing, and to pro-
vide a very high pressure output. In construction, it consists of an approximately rectangular body, bored with a
number of small cylinders-one for each engine cylinder-each of which is lined with a cylindrical sleeve. The
whole thing thus roughly resembles a miniature engine block, a similarity that extends to the "bottom end" of the
pump, which has a shaft running lengthwise through it, analogous to an engine's crankshaft. Instead of crank
throws, however, this shaft has a number of individual carns, one for each cylinder.Each cylinder in the pump con-
tains a piston-likeplunger that is driven up its sleeve by the correspondingcam lobe asthe pump shaft rotates,driven
by the engine at half crank speed, like an ordinary ignition distributor.
The mechanical drive thus provides the timing and the necessary pressure, leaving the problem of control of fuel
quantity.To achieve this, each sleeve has a "spill"port drilled through its side,while the upper edge of each plunger
has its side cut away to form a sort of spiral ramp. The sleeve fits in its bore with a very slight clearance, and so is
free to rotate. Rotation of the sleeve in its bore thus covers or exposes the spill port, according to the angular posi-
tion of the sleeve relative to the spiral cutaway on the plunger.With the sleeve rotated so that the spill port is cov-
ered even when the plunger is at the bottom of its stroke, the only route out of the cylinder is through a hole at the
top, where the fuel lines to the injectors connect. A single stroke of the piston will thus expel the entire volume of
fuel held in the cylinder; this represents the maximum capacity of the pump and thus corresponds to full power.
At anything less than wide-open throttle, a lesser amount of fuel per revolution is obviously needed, and this
reduction is achieved by rotating the sleeve around, relative to the plunger, so that the spill port lies some distance
above the plunger's spirally formed top edge. Upward movement of the plunger thus initially causes fuel to be dis-
charged from this port, from where it is fed back to the tank, until the plunger rises far enough to close off the port,
and injection commences.
The rotation of the sleeve(s) is accomplished by a toothed rack that meshes with gear teeth cut onto the outside
of each sleeve. The rack is connected directly to the throttle linkage, so moving the pedal rotates the sleeves with-
in the pump, thus controlling the quantity of fuel delivered with each stroke of the plunger.
Although such a mechanical injection pump is, in fact, quite a simple device, and contains few parts-just two
per engine cylinder served, plus the camshaft and rack- the quantity of fuel delivered per stroke is very small, so
all those parts have to be made with extreme precision, involving much hardening, grinding and precision gaug-
20

ing. Accordingly, mechanical injection pumps-known widely and for fairly obvious reasons as "jerk"pumps-
are mighty expensive. When adapted for use with gasoline, rather than the kerosene used in diesels, there is the
additional problem that gasoline is a "dry" fuel, lacking the lubricating properties of diesel fuel, thus demanding
the use of extremely hard, wear-resistant alloys, which further adds to the machining difficulty and expense.
The famous Mercedes 300SL "gull-wing" coupe introduced fuel injection to the street. Like the W1.96, a system of direct injection was
used. (Mercedes Benz).
inverted flight, most of the advantages listed
are also highly applicable to race cars.
Accordingly, by 1937 Mercedes Benz had
tested a single cylinder mockup for a racing
engine, using high-pressure injection of fuel
directly into the combustion chamber.In the
meantime, a handful of European makers of
small, two-stroke engined passenger cars
had introduced this "direct"fuel injection, in
an attempt to tame the notorious thirst of
two-strokes that results from something like
one quarter of the air/fuel mixture whistling
straight out the exhaust ports during the
intake/exhaust event, when both inlet
("transfer") and exhaust ports are open
together. Because these engines were two-
strokes, the injection pump had to run at
crank speed, rather than half-speed, as for a
four-stroke. This provided Bosch with valu-
able lessons in running their injection equip-
ment at high pump rpm. Mercedes's first
post-war Formula One race engine made
direct use of the experience so gained, both
their own and that of Bosch.
In both the M196 Formula One engine
that appeared in 1952 and in the engine for
the famous 300SL "gull-wing" sports car,
first exhibited in New York in 1954,
Mercedes retained the direct (into the com-
bustion chamber) injection scheme used in
21
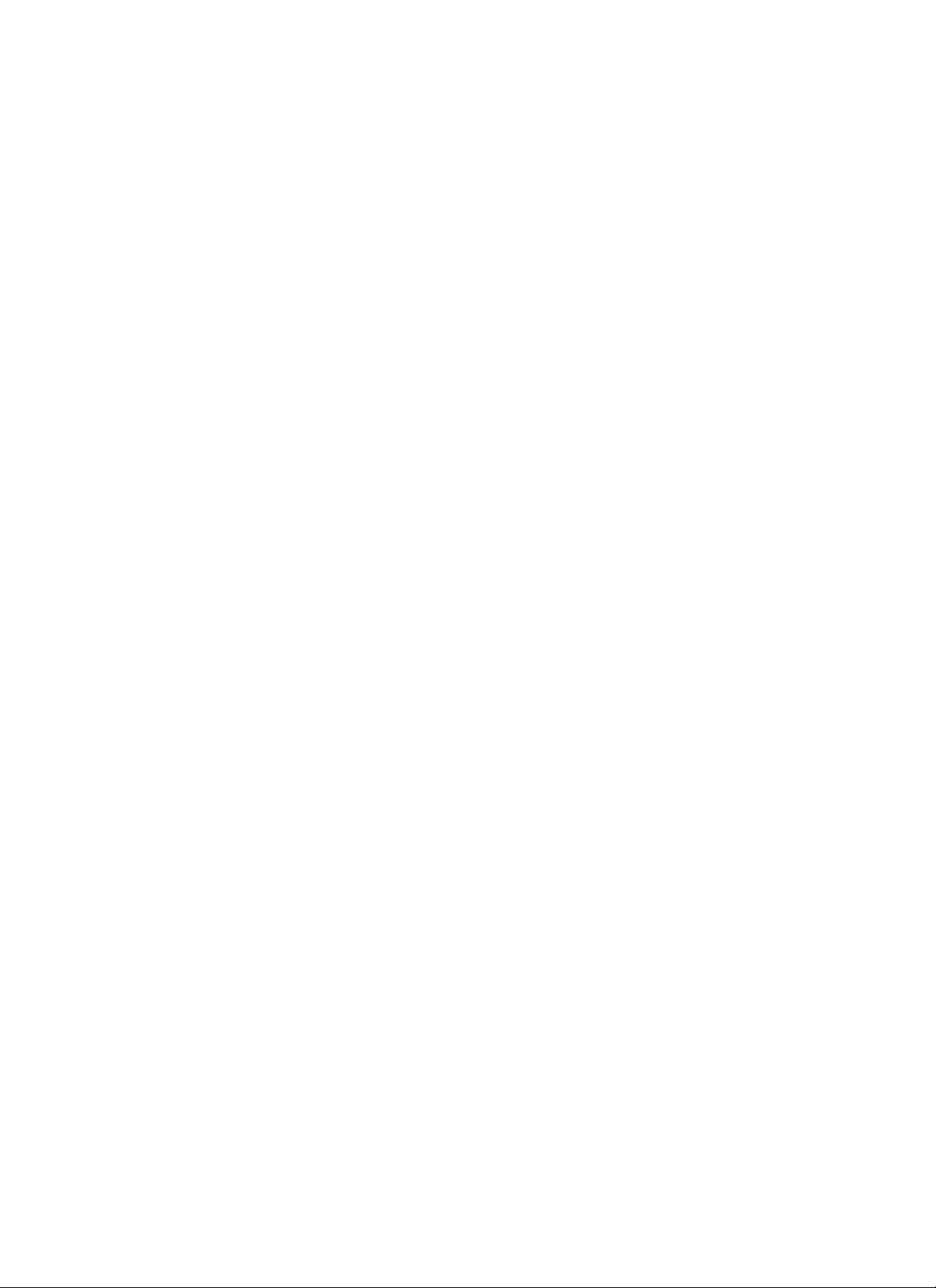
.L~
~
..
~~
~.
r~
.
~-
The location of the injector-screwed right into the cylinder head-is apparent in this cross-section of the 300SL engine. (Daimler-
Chrysler Archive)
22
diesels and in the earlier experiments with
gasoline fuel. Combined with suitable injec-
tion timing, this allowed radical valve tim-
ing and experiments with "tuned" intake
pipes, without introducing the problem of
poor fuel economy from portions of the
intake charge being lost out the exhaust.
Until injection occurred, after the exhaust
valve had closed, the engine was inhaling
only air.
Diesel Jerk Pump
Giventheexistenceof anestablishedtech-
nologyforinjectingfuel,itishardlysurpris-
ing that the diesel "jerk" pump was adapted
in this way for gasoline injection. The adap-
tation, however, required hurdling a major
difficulty- the problem of regulating the
quantity of fuel delivered throughout the full
range of engine operating speeds and loads.
Unlike gasoline engines where power is
controlled by closing off ("throttling") the
air supply,yet where a very narrow range of
air/fuel ratios must be maintained, on a
diesel there is no "throttle" as such. At any
given speed, the engine inhales the same full
load of fresh air no matter what the position
of the gas pedal; varying the power is sim-
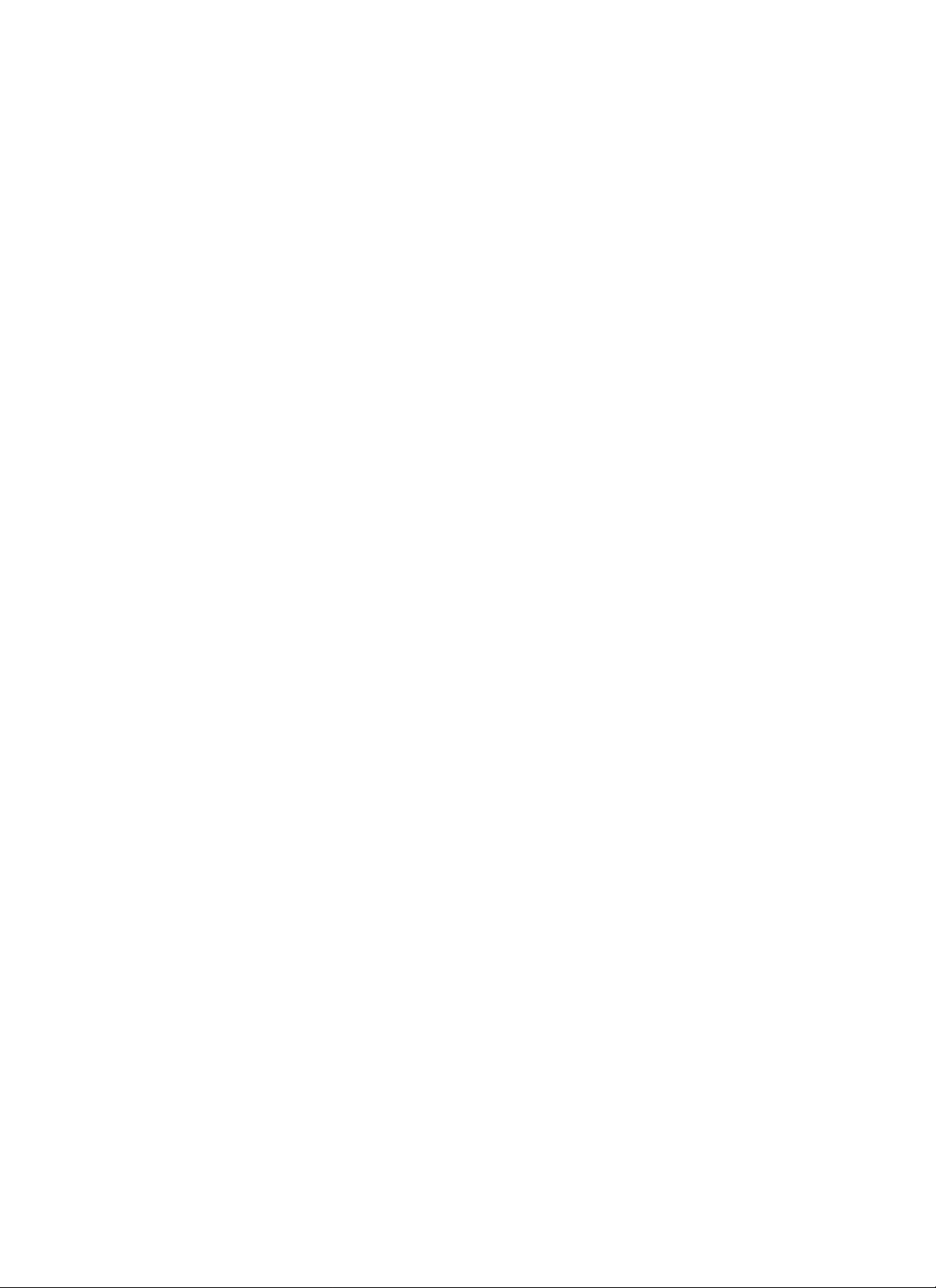
The resemblance to Diesel engine practice is clear in this exterior shot of the 300SL engine. Gasoline's lower lubricity, compared to diesel
fuel, compelled the use of expensive, wear-resistant alloys in the injection pump. (Daimler-Chrysler Archive)
ply a mater of injecting more or less fuel.
Power is regulated, in other words, by
adjusting the mixture strength. In the sim-
pler diesel systems, at least, this is directly
controlled by the driver's right foot-the
engine runs extremely lean at light throttle,
and rich to the point that it visibly smokes
when maximum power is demanded. In fact,
it is the smoky exhaust that sets the limit for
the rated power of a diesel engine; more
power would be available simply by inject-
ing yet more fuel- if we were prepared to
put up with the smoke. (Even at full power,
the amount of fuel injected falls short of a
stoichiometric mixture-diesels are always
running "lean," which is one reason they can
never produce as much power as a gasoline
engine of the same displacement.)
The inefficient breathing of any piston
engine, gas or diesel, at speeds well away
from the rpm at which torque peaks means
that the mass of air inhaled per revolution, at
any given throttle setting, will most definite-
ly not be constant across the speed range.
Because of the gasoline engine's finicky
appetite, the amount of fuel mixed in with
that air also has to be varied on the basis of
the quantity of air inhaled, and not just
23

6 5
7
8
11 12
13 15 16
14
4
3
I
2 12.Controlrockhead
3. Enrichmentsolenoid
4.Thermostat
1
1 5.Barometriccell
6. Checkvalve
7. Plungerunit
8.Toothedsegment
9. Controlrack
10.Rollertappet
11.Camshaft
12.Governorcontrollever
13.Contouredcam
14.Centrifugalgovernor
15.Idleadjustingscrew
16.Shut-offsolenoid
d1.Sensoroncontoure cam
The complexity of the mechanical controls for the Bosch system used on the 300SL is mind-boggling. Fuel delivery of the pump (only the
camshaft is shown, 1.1.)is controlled by the rack (9). The position of the rack is governed by engine speed, via the centrifugal weights
(1.4) acting on a contoured cam (1.3), and by throttle position. Other factors are accounted for by a barometric capsule (5) and a tem-
perature sensitive device (4). (Robert Bosch Corporation)
according to speed and throttle position.
Adapting to Gas Engines-To adapt a
dieseljerk pump to gasoline operation, then,
means that the rack (see sidebar, page 20)
cannot simply be directly hooked up to the
loud pedal; the relationship between the two
has to be modulated by some other con-
troles). The usual way this is done is by
adding a set of centrifugal weights, some-
what like those in a traditional ignition dis-
tributor, to provide a signal proportional to
engine speed, plus a diaphragm that "reads"
manifold vacuum, a fairly close approxima-
tion of engine load. These additional control
devices are connected to the linkage control-
ling the rack via a system of cams and links,
with the shape of the cams tailored accord-
ing to the idiosyncrasies of the engine's
breathing.
The monkey motion of these additional
levels of control added even more to the
substantial cost of the pump itself, demand-
ed meticulous adjustment, and its complexi-
ty mocked the essential simplicity of the
24

basic pump. Indeed, one observer at the time
mused aloud that if all engines had worn
fuel injection all along, then someone
invented the carburetor, he would have been
hailed as a genius.
Injector Location-Apart from the
mechanical complexity of the "add-on"
speed- and load-sensing mechanisms at the
pump, another problem confronted this
adaptation from diesel to gasoline
- that of
shielding the injector nozzles from the heat
and fury of combustion. Surprising as itmay
seem, gasoline combustion chambers see
higher peak temperatures than diesels. On
their Ml96 Formula One engine, Mercedes
dealt with this by fitting the injector into the
side of the cylinder, where it was masked by
the piston at TDC andthus shielded from the
worst of the inferno.
Certainly,timed direct injection deals with
the potential issue of fuel consumption,
especially with radical valve timing, and the
high pressure spray of these systems is
favorable for atomization, but against these
advantages were set the problems noted
above, plus the issue of the power required
to drive a pump that has enough grunt to
blow open the stiff check valves in the injec-
tors and at the pump outlets, used respec-
tively to prevent combustion pressure from
blowing back through the injection lines and
to keep the lines fully charged.
Nevertheless, the fact that engines operate
quite happily on carburetors made it clear
from the outset that there was no absolute
need for precision timing of the fuel delivery
in a spark-ignition engine.
Granted, a carbureted engine would prob-
ably make a little less power than a similar
one with direct injection, but some part of
this might be attributed to the fact that a sep-
arate injector for each cylinder eliminates
the problems of a central mixer, rather than
to the timing. Of course, the same thing can
be achieved with carburetors if a separate
carb is provided for each cylinder. That,
however, would be heavier, probably more
expensive and arguably even more complex,
depending onthe number of cylinders. Thus,
while ahandful of other Formula One teams
and upmarket European sports car manufac-
turers also used Bosch gasoline injection, to
the best of this writer's knowledge, all these
others left the injector just outside the com-
bustion chamber, aimed at, and spraying
against, the head of the intake valve.
But if you decide to locate the injectors
outside the combustion chamber, then you
don't need to fight combustion pressure, so
you don't need a very high pressure pump.
Also, if the injector lies outside the cylinder,
then you don't need to time the injection so
it occurs with both valves closed. In that
case, why bother to time it at all?And if the
timing of discrete squirts is not crucial, then
why does the fuel have to be delivered in
individual pulses?
Early Continuous
Injection Systems
These questions had occurred to a good
many Eeople, and an alternate form of fuel
injection came into being. In these, fuel is
injected continuously, rather than in pulses,
and at very much lower pressure than a
"jerk" pump provides, though still much
higher than the small pressure difference
that exists between a carburetor venturi and
the atmosphere.
The Wright brothers used a primitive form
of this continuous injection, as the arrange-
ment is called, on the engine of their first
successful aircraft. An engine-driven pump
of the "positive displacement" type-one
which supplies a fixed quantity of fuel at
each revolution- was used, to continuously
spray fuel directly into the engine air intake.
It should be clear that while a satisfactory
mixture strength might be arranged at full
throttle-presumably after some tinkering
with the size and/or drive ratio for the
pump- with no means to reduce the pump
output the mixture must have become hope-
lessly rich at anything less than full throttle.
25

Although Stu Hilborn had proved, years earlier, that such a system could work on the track, Rochester were the first to demonstrate the
practicality of the simpler, continuous flow fuel injection system, as on this early "fuelie" Corvette. (Dave Emanuel)
26
But then the Wrights' had no immediate
interest in operation at part throttle!
Winfield's F] System-About the same
time that Bosch and Mercedes were begin-
ning their experiments with timed, high-
pressure, direct gasoline injection in the
mid-l930s, Ed Winfield developed a low
pressure, continuous injection system,
intended for Indy cars. Winfield's design had
provision for varying the fuel flow with
throttle position, but a lack of interest from
potential customers forced him to eventual-
ly abandon the scheme, and he allowed his
patents to lapse. It was not until fifty years
after the Wrights that racers had access to a
continuous injection system that dealt with
the part-throttle problem.
Hilborn ]njection-Stu Hilborn achieved
this by incorporating a controllable spill
valve, connected to the throttle linkage, that
tapped off (and returned to the tank) some
portion of the pump's output, according to
how wide the throttle was opened.
On the face of it, this might appear to fill
the bill, but the assumption built-in here is
that an engine, at any given throttle setting,
needs a fixed quantity of fuel per crank rev-
olution, and we have already seen that this is
mistaken, because of the way an engine's
ability to take a full breath varies across its
speed range.As a result, gasoline PI systems
that use just engine speed and throttle posi-
tion to determine fuel quantity can be
arranged to provide a suitable mixture
strength only under very limited circum-
stances, and must inevitably miss the mark
by a large margin under others.
Still, schemes such as Hilborn's have a
long and honorable history when used with
methanol fuel. As discussed in more detail

in Chapter 8, methanol will tolerate wide
variations in mixture strength with little
effect on power output, which helps mask
the inherent shortcomings of such a simple
system. In this case, rpm and throttle posi-
tion alone provide a sufficiently accurate
measure of fuel flow requirements, so it is
not necessary to measure the rate of airflow
at all. Since there is no need to measure it,
there is no need for the restriction of a ven-
turi or any other airflow sensor stuck in the
airstream. This improves engine breathing
and so promises more power just for that
reason alone.
RochesterFISystern
For a street engine running on gasoline,
however, any purely mechanical system,
whether injecting continuously or in a series
of pulses, needs to somehow measure or
compute the rate of airflow into the engine,
and to use that information to modulate the
delivery of fuel so as to keep the air/fuel
ratio appropriate to the circumstances. We
have discussed how this can be achieved
with a jerk pump, but what about a continu-
ous gasoline injection system?
There have been many such systems
throughout automotive history; one of the
more recent and more widely used of these
is the Bosch K-Jetronic system, described in
Chapter 6. Nevertheless, the example most
of us remember best is likely the Rochester
system used on "fuelie" Corvettes from
1957 to 1965. The heart of the Rochester
system is a spill valve that serves as a regu-
lator of fuel quantity- indeed, it is the only
mixture control element in the whole sys-
tem. Fuel is fed to the spill valve by an
engine-driven gear-type pump that simply
serves as a source of fuel at medium-high
pressure (200psi at maximum), with the
pressure tending to rise with increasing rpm.
The spill valve consists of a sleeve with a
number of ports arranged radially in its side,
plus a plunger that covers or exposes these
ports, according to its position. The position
of the plunger, in turn, depends on a balance
between the fuel pressure and a force
applied to the top of the plunger by a mix-
ture control mechanism.
Increasing fuel pressure tends to raise the
plunger, thus uncovering the sleeve ports
and so bleeding off some of the pressure.
The mixture control device, shown schemat-
ically in the following illustration, amounts
to a simple mechanical computer that
applies a spring force to the top of the
plunger, modified by the forces acting on
two diaphragms
- one connected to the
intake manifold, and one to a venturi
through which all the air entering the engine
has to pass. The eight individual port injec-
tors downstream of the spill valve thus see a
fuel pressure that depends on a balance
between the supply pressure and the forces
acting on the diaphragms, and their output
varies accordingly.
The Rochester system is strikingly simple,
especially when compared to a jerk pump
having the controls needed for street use on
gasoline, and none of its parts require excep-
tional precision or expensive materials for
their manufacture. Although the injectors
themselves had to be individually calibrated
and installed as a matched set, given suffi-
ciently large production numbers it seems
likely that the system overall would have
been little (if any) more expensive to make
than a pair of four barrel carburetors.
Nevertheless, it remained a somewhat rare
and costly performance option, and justified
its price premium by offering more power.
Partly this was because the near-elimination
of cylinder-to-cylinder variations in mixture
strength permitted a higher compression
ratio (CR) than was safe with carburetors,
but an advantage still showed even when the
CR was unchanged. We might attribute this
to three sources: nearly identical air/fuel
ratios at each cylinder, elimination of mani-
fold heating, and areduction in the breathing
restriction imposed by the venturi, com-
pared with a carburetor. Although a venturi
27

IUUI
<::~~
,--.-
--.-
---.
MANIFOLD VACUUM
OUTPUT TO
INJECTORS
\ \\\
I \ \ \
VENTURI
VACUUM
-----.--
The heart of the Rochester system's control unit was a spill valve that returned to the tank a certain fraction of the fuel delivered by the
gear-type pump. The position of the piston in the spill valve was determined by two diaphragms-one hooked to a manifold vacuum, one
to a single large metering venturi that fed the air box. A system of links and rollers linked movement of the diaphragms to the spill valve
piston.
was needed to measure air quantity, the
amount of pressure drop needed to provide a
useful signal to the mixture control unit was
eventually sweep away not only the carbu-
retor, but most other forms of fuel injection
as well.
much less than that required to lift gasoline
out of a carburetor's discharge tube.
In its day, the Rochester FI was regarded
by the auto industry and the public alike as
very much a high-tech piece, and possibly
the final word in fuel delivery. Ironically, at
about the same time that OM was introduc-
ing this system, another completely different
form of fuel injection was being unveiled, to
much less public acclaim, yet this one would
28
The First Use of Solenoid Valves
The basis of this little-hailed breakthrough
was the use of an electrically operated sole-
noid valve as a fuel injector. Supplied with
fuel at a modest constant pressure, it squirts
at a constant rate as long as an electric cur-
rent is applied to the solenoid windings, and
stops when the current is turned off. Thus,
the quantity of fuel injected depends simply

on how long the juice is turned on. If one
electrical pulse is delivered every second
revolution of the crankshaft (for a four-
stroke engine), then the air/fuel ratio of the
mixture delivered to the engine can be con-
trolled simply by varying the length of each
pulse.
The idea of using a solenoid valve as a fuel
injector is a surprisingly old one. Such a
scheme had been developed by an engineer
named Kennedy at the Atlas Imperial diesel
Engine Co, in 1932, and an installation
appeared on a marine engine exhibited at the
New York Motor Boat Show in 1933,
around the same time that Bosch and
Mercedes in Germany, and Winfield in the
U.S. were beginning their experiments.
Given the primitive state of the electrical
sciences back then, it is mildly astonishing
that the thing worked at all, yet in 1934a .
similar but smaller engine was installed in a
truck and driven successfully from Los
Angeles to New York and back.
The "Electrojector"-A quarter century
later, A.H. Winkler and RW. Sutton of the
Eclipse Machine Division, Bendix Aviation
Corporation, announced the fruits of four
years' work atBendix to develop ann FI sys-
tem for gasoline-fuelled automobiles using
such a solenoid-controlled valve as an injec-
tor, in conjunction with an electronic control
unit, or (as they termed it) "brain box." They
described this combination of components
as "electronic fuel injection"-surely the
first time this phrase was ever used. The
resulting "Bendix Electrojector" comprised
a separate port injector for each cylinder,
each supplied with fuel from a common rail
at a regulated 20 psi. Sensors responsive to
manifold pressure, engine speed, atmos-
pheric pressure, and air and coolant temper-
ature fed their various outputs to the "brain
box"- the electronic control unit (ECU)-
which then calculated the instantaneous fuel
requirements of the engine. On the basis of
that calculation, the ECU delivered a pulse
of current to a rotary distributor which fed
that current pulse to each solenoid valve in
turn, causing each successively to open and
supply fuel to the cylinder it served. The
quantity of fuel delivered by each injection
was simply a matter of the duration of the
pulse-as long as it was "on," the injector
would deliver fuel at a constant rate. At idle,
the pulses were of very short duration; at
maximum load, the injectors were open for
as much as 150 crankshaft degrees.
At the beginning of the development of
the Electrojector, about 1951 or 1952, the
triggering signal for the ECU was provided
by a mechanical commutator-a simple
wiper making intermittent contact with a
segmented brass ring, as the engine-driven
ring swept past. That soon gave way to trig-
gering by an extra set of contact points in a
housing sandwiched under the ignition dis-
tributor. In atleast the three earliest versions,
the working bits in the ECU were. . . vacu-
um tubes! One suchunit was installed on the
V8 engine of a 1953 Buick, and used to
demonstrate the system to the auto industry.
By 1957, when it became available to the
public in very limited numbers, the electron-
ics were, thankfully, all transistorized. This
eliminated the need to wait for the tubes to
warm up before the system became func-
tional, shrank the size of the ECU and sub-
stantially reduced the electrical power
required to run it, and doubtless greatly
improved the system reliability
- vacuum
tubes do not take kindly to be rattled around!
The Electrojector was listed by American
Motors as an option for the 1957 Rambler
Rebel, but very few cars so equipped were
ever sold.A year later, Chrysler offered it on
the 300D and DeSoto Adventurer, and sev-
eral hundred with the option were manufac-
tured in 1958 and 1959.
Despite occasional problems from exter-
nal electrical fields causing the brain box to
go haywire, and a degree of unreliability of
the injectors themselves, on the whole the
system worked satisfactorily and matched
Bendix's claims of modest (5 percent)
29
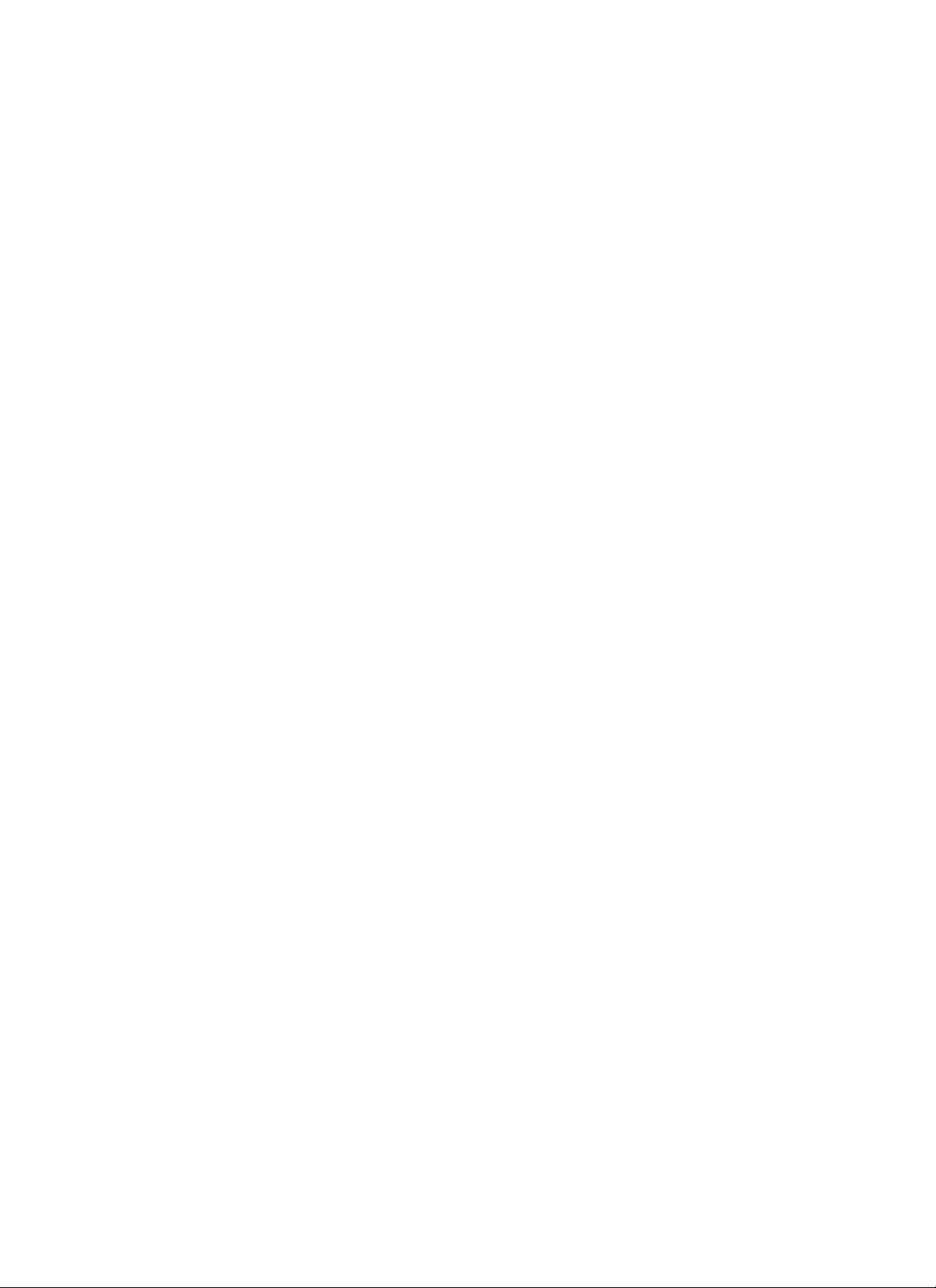
30
improvements in both fuel economy and
power, compared to a similar engine fitted
with a pair of four-barrel carburetors. The
teething troubles were eventually worked
out, and by 1965 Bendix had a fully devel-
oped production version ready to go.
At this point, rather than try to produce
and market the Electrojector themselves,
Bendix decided instead to enter into an
agreement with the Robert Bosch Co.,
which gave Bosch access to the Bendix
patents. From a business point of view, this
made a good deal of sense. In view of their
reputation in the auto industry as an estab-
lished OEM supplier-one with wide expe-
rience both in fuel injection and in electrical
and electronic equipment-Bosch was
clearly in a better position to exploit the
potential market. And fuel prices in Europe
were many times what they were in the U.S.
of the 1950s,justifying a much higher initial
cost there, in exchange for the fuel economy
benefits alone.
Bosch Jetronic FI
In most respects, the Bosch "Jetronic" FI
that first appeared on the 1967 Volkswagen
1600, was functionally identical to the
Electrojector system described by Winkler
and Sutton ten years earlier.Apart from tak-
ing advantage of advances in electronics to
produce a more compact ECU, this sys-
tem-since identified as D-Jetronic, to dis-
tinguish it from later Jetronic versions-dif-
fered from the Bendix prototype in one
respect. In the Electrojector, the housing that
was piggybacked onto the ignition distribu-
tor and which contained the triggering con-
tact points also contained a rotor,just like an
ignition rotor; this distributed the timed
pulse to each injector sequentially. In the D-
Jetronic as applied to the four cylinder VW,
there was no rotor, but there were two sets of
triggering contacts, one for each pair of
cylinders. Each set of contact points drove
two injectors simultaneously, timed so that
one cylinder received its injection while its
intake valve was open; for the other cylin-
der, the injection occurred with valves
closed. Fuel thus accumulated in the port,
awaiting that cylinder's next intake stroke.
We have mentioned earlier that the mere
fact that a carbureted engine will function in
a satisfactory way should make it obvious
that injection timing is, to say the least, not
critical, and the power gains realized with a
few continuous injection systems tended to
confirm this view. The matter was pretty
much clinched in 1959,when Mercedes suc-
cessfully used a Bosch jerk pump with just
two plungers, each feeding three engine
cylinders, on its six cylinder 220SE. This
must all have improved the comfort level of
the Bosch and VW engineers who adopted
the hop-skip timing used on the D-Jetronic,
an arrangement that allowed eliminating the
rotor used in the Electrojector.
The Electrojector-based, intermittent
injection "Jetronic" systems from Bosch
have undergone successive improvements
and refinements over the years since the D-
Jetronic's introduction. Apart from the elec-
tronic innards of the control unit gaining
computing power while shrinking ever fur-
ther in size and weight, and the use of all-
electronic triggering (rather than contact
points), the major differences between one
variant and another have been in the way the
quantity of air supplied to the engine is mea-
sured. These basic differences between sys-
tems are reflected in the nomenclature used:
L-Jetronic, LH-Jetronic, etc. In addition,
most later systems accept inputs from addi-
tional sensors, most notably an oxygen sen-
sor, also called an °2 sensor or lambda sen-
sor. As mentioned in the previous chapter,
this is a device fitted to the exhaust system
that" sniffs" the exhaust gas to gauge its
oxygen content, thereby providing a direct
measure of what the air/fuel ratio actually is
at any given moment, rather than obliging
the system to depend totally on a set of pre-
programmed "maps" or "look-up tables"
that predict what the ratio should be for a

With the rear-mounted "pancake" engine nestled under the apparent floor of the trunk, earlier carburetted versions of the VW 1500/1600
were notorious for vapor lock problems. This is the later 1600 engine with Bosch D-Jetronic injection. The ECU is visible at the far left.
(VW Canada).
given set of operating conditions. (See also
the sidebar "The Oxygen Battery.")
In many cases, control over ignition tim-
ing has been integrated into the ECU of
these systems, in which case they are termed
"Motronic," again with variants according to
the method of air metering. Over time, an
increasing number of functions have been
combined into the Motronic system, includ-
ing integrated control over automatic trans-
mission shift points and torque converter
lockup, the waste-gate on some turbocharg-
er-equipped cars, selection among different
length intake ports on some others, and
authority over the variable valve lift and/or
timing found on a few vehicles. We discuss
these Motronic systems in some detail in
Chapter
4.
K-]etronic-At the start of the new mille-
nium, the principle of intermittent injection
using electronically controlled, electrically
powered solenoid injectors is now universal
on domestic passenger cars, and near-uni-
versal on models imported from Europe and
Asia. Yet not everyone was an immediate
convert to this plan. It seems ironic now that
even after the pulsed (intermittent) Jetronic
system wascommonplace,Bosch feltobliged
tointroducea continuousinjectionsystem,the
K-Jetronic (The "K" stands for kontinuier-
lich, German for continuous). Early versions
of this were purely mechanical; in response
to ever-tightening emissions standards, later
ones-such as KE-Jetronic and correspond-
ing Motronicversions- added a degreeof
electronic control. Inpart this apparent pref-
erence for an all-mechanical system may
have been due to a powerful conservative
31

streakamongsomemanufacturersandtheir
engineers.In part, too, it may have been a
matterof economics-the intermittentsys-
temsmay have beenmoreexpensiveat the
OEM level. Although there were a few hold-
outs until the early 1990s, most of the vari-
ous K-Jetronic systems were history by the
mid 1980s. These now-superseded (not to
say obsolete) systems are dealt with in
Chapter 6.
We will not be dealing with a handful of
sub-variants of Jetronic and Motronic PI that
are used on vehicles not imported into North
America.
To summarize, then, the essential differ-
ence between carburetors and fuel injection
systems is that a carburetor uses the pressure
drop within its venturi both to measure the
airflow and as the means to propel the fuel
into the intake air stream, whereas PI
mechanically forces the fuel into the intake
air in an amount usually determined by a
separate airflow or manifold pressure sen-
sor, acting on an electronic or mechanical
system that actually controls the quantity of
fuel injected.
Intermittent electronic fuel injection allows modern cars to combine high power
with driveability, economy, and low emissions. (VW Canada).
32
Basic Types of Fuel Injection
All fuel injectionsystemscanbe divided
upintotwobasictypes:thosethatinjectfuel

continuously and those that inject intermit-
tently, in a series of pulses. Again, in either
case control over how much fuel is injected
can be achieved either mechanically or elec-
tronically. In the present context, only the
old, diesel-type jerk pump uses mechanical
control over intermittent injection; all Bosch
intermittent systems use electronic control.
Bosch K-Jetronic continuous injection sys-
tems-sometimes called CIS-may use
purely mechanical control, as in the original
K-Jetronic, or may include some degree of
electronic fine-tuning on top of the basic
mechanical computation.
Many FI applications, especially in newer
cars and in older high-performance ones,
use a separate injector for each cylinder.
This greatly reduces the quantity of liquid
fuel laying on the walls of the ports. If the
injectors are located very close to the intake
valves and the intermittent injections are
sequential, the possibility of maldistribution
of the mixture between one cylinder and
another is essentially eliminated.
Many others, though, are of the "throttle
body" type, in which the fuel is sprayed into
and mixed with the air in one centralized
location, then conducted to the cylinders
through a thus "wet" manifold, just like that
of a carbureted engine. This would seem to
put it on the same footing as a single carb in
terms of mixture distribution, but the fact
that the fuel is injected under pressure
means that it emerges from the injector noz-
zles as a very fine spray, with droplets so
small that they have a much better chance of
evaporating than is often the case with the
lumpy soup coming from a carburetor.
While a TBI system is thus likely to be bet-
ter in this regard than a carb, an individual
injector at each intake port can do even bet-
ter.
One of the further advantages sometimes
argued for FI is that it achieves the maxi-
mum possible engine power because it does
away with the venturi. That is not quite true,
because it is a basic principle of science that
you cannot measure something without
affecting the thing you are measuring.
Certainly a venturi measures airflow, and in
the process it also restricts that flow, but
electronic fuel injection (EFI) systems that
use a spring-loaded flap valve or a "hot
wireIIairflow sensor (the current needed to
keep the wire at a constant temperature is
used as the air-quantity signal) both offer at
least some restriction to flow, too, although
a hot wire (or hot film) sensor will impede
airflow much less than any carburetor ven-
turi.
The ultimate sophistication is to provide
an oxygen sensor (°2 sensor, lambda sen-
sor) in the exhaust pipe and to correct the
mixture strength from moment to moment,
based on that information; an excess of °2
calls for a richer mixture, and vice versa. For
all these reasons, EFI with an injector for
each cylinder is unarguably the state-of-the-
art for fuel-air mixing and delivery.
33

Rich mixtures, we explained in Chapter 1, mean that some of the hydrocarbon molecules in the fuel entering
the engine pass out into the exhaust unreacted- there simply aren't enough oxygen molecules available for them
to combine with. These unburned hydrocarbons are a source of air pollution, and legislation severely limits the
quantity of them that is allowed to escape into the atmosphere. The shortage of oxygen also means that the reac-
tion with the hydrocarbons that do bum is chemically incomplete-instead of the hydrocarbon-oxygen pairings
forming CO2 and H2O, many of them wind up as CO-carbon monoxide. Emissions of carbon monoxide are
also strictly controlled by law.
Lean mixtures would keep down the CO levels, and as long as they were just a little lean, the HC levels, too.
Ironically, excessively lean mixtures actually raise HC levels above those found with a stoichiometric mixture,
becauseasthe mixtureapproachesthe"leanlimit"- theair/fuelratioatwhichthemixturesimplywon'tignite-
some cylinders misfire, so all of the HC in that particular cylinderful goes straight out the exhaust unburned.
But even mixtures just lean enough to minimize CO and HC create high combustion temperatures. Too-hot
combustion encourages some of the nitrogen (N) in the air, normally thought of as inert, to combine with some
of the excess oxygen, to form various oxides of nitrogen-NOx. NOx is also a pollutant-it is the principle
source of photochemical" smog"- so the amount of it, too, is limited by law.(Damned if you do; damned if you
don't!) A compromise setting
won't work, either. Anything
lean enough to meet HC and CO
limits would bust the NOx limit,
and anything rich enough to
avoid excessive NOx would
lead to illegal levels of HC and
CO. (Damned even if you sit on
the fence!)
The solution arrived at by auto
makers, beginning about 1975,
has been the "three-way catalyt-
ic converter." In essence, this
device splits the oxygen from
the NOx and helps it combine
with the CO to make CO2, and
with the HC to make H2O, and
more CO2' This works well
enough to satisfy the G-men. . .
provided that the mixture was
neither too rich nor too lean in
the first place. And the three-
way catalytic converter is
mighty fussy indeed about just how Constructionofa three-waycatalyticconvertor.Convertorsareessential
close to the stOIC lOmetnc ldeal the fedto the engineis heldveryclose to the chemicallycorrectratio.Andto achieve
ingoing mixture has to be; mixtures that, a lambda(oxygen)sensor is essential. (RobertBoschCorporation).
that are less than one percent either
.
. .. to meet currentemissionslimits,butcanonlydo theirjObifthe air/fuelmixture
h
1
2
3
1.Ceramicmaterialwithcatalyticallyactivesubstances
2.Steelwaolretainer
3.Housing
34
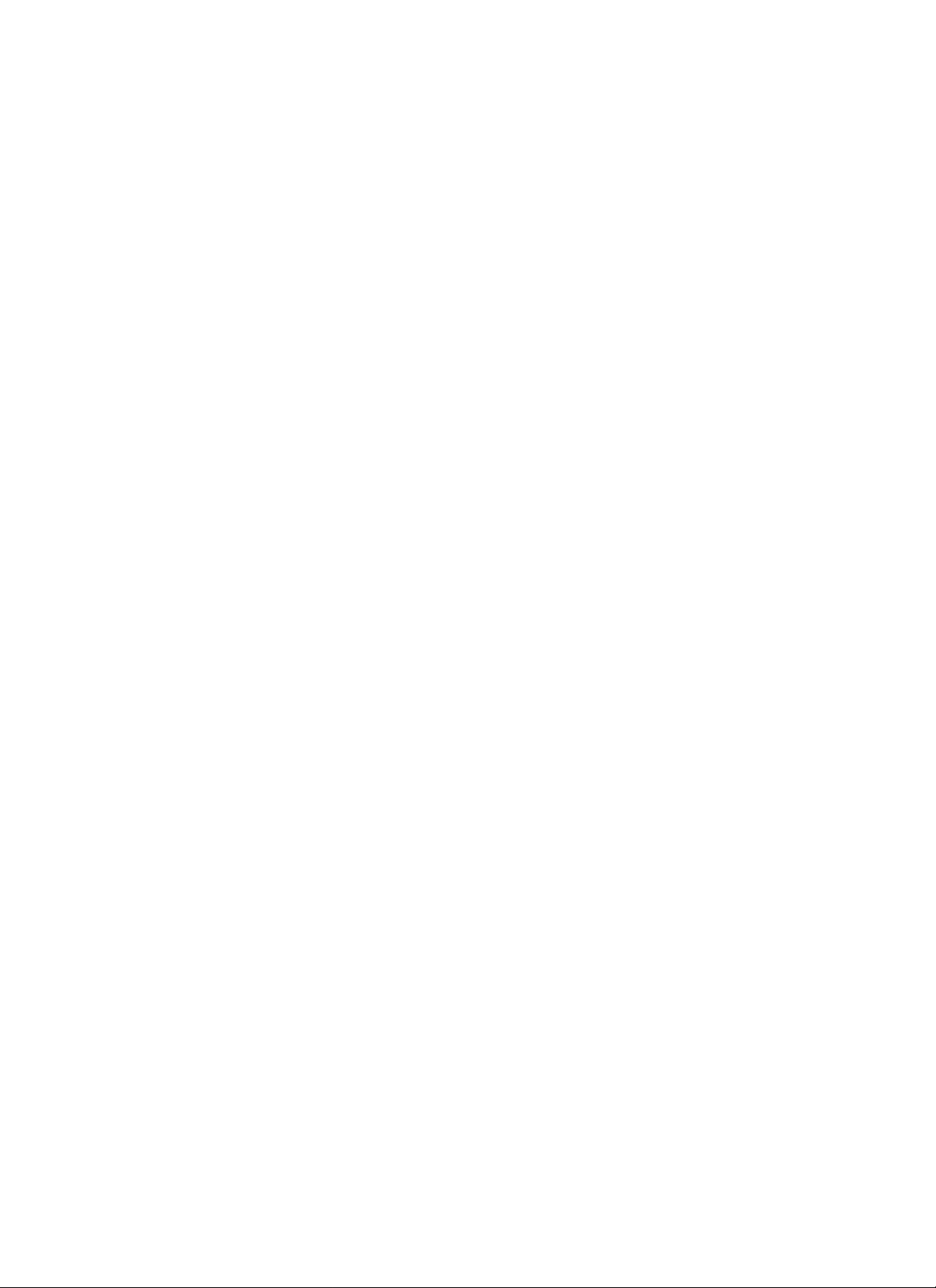
1.Probehousing
2. Ceramicshield
3. Electricalconnections
4.Shieldtubew/slits
5.Activeceramicsensorlayer
6.Contact
7.Shield
1 2
3
5 6 7 9
4
Lambda sensors have a voltage output that rises from near zero in the absence of oxygen in the engine exhaust to
a bit less than one volt when small traces of it are present. This characteristic enables an electronic fuel injection system
to control fuel delivery on the basis of the sensor's reading of the exhaust gas. The sensor only works when hot, however.
To reduce the time between engine start-up from cold and the sensor reaching its operating temperature, some versions are
electrically heated. (Robert Bosch Corporation).
10
side of the chemical ideal render the converter next to useless.
No fuel injection system yet developed (and certainly no carburetor!) can hope to control the mixture strength
that closely,based simply on a set of values derived from the characteristics of some similar engine in a test lab.
The device that enables EFI to "know" just what the mixture strength needs to be at any instant for any particu-
lar engine out in the real world is the "lambda sensor."
In construction, the lambda sensor consists of a hollow ceramic bulb, with both inner and outer surfaces cov-
ered with a microthin layer of platinum. For protection, the outer surface is surrounded by a shield. This bulb is
inserted into the exhaust system so that its exterior surface is washed by the exhaust gas stream, while its hollow
interior is exposed to the atmosphere. In operation, the lambda sensor acts like an oxygen-powered battery: a dif-
ference in the oxygen level of the gasses surrounding the two surfaces of the sensor causes it to generate a small
voltage.
As you might expect, there is very little oxygen in the exhaust of an engine running on a stoichiometric mix-
ture, yet there is some-about 0.5 percent. Surprisingly,even with a mixture that is about five percent rich, there
is still about 0.2 percent oxygen. Equally surprising, a mixture that is five percent lean will only contain about
one percent oxygen. Aparticularly useful feature of the lambda sensor is that its output voltage changes very dra-
matically right around the point of stoichiometry; very small changes (a few tenths of one percent) in oxygen
content lead to large changes in the sensor output. While the sensor will put out about 900 millivolts (0.9v)

when the exhaust oxygen content corresponds to a lambda of about 1.2(that is, the mixture is about twenty per-
cent lean-an air/fuel ratio of a bit less than 12:1), and while its output drops to near zero at about lambda=0.8
(an air/fuel ratio of near 18:1), almost all of that voltage change occurs within one percent of stoichiometry. The
voltage output of the sensor is fed back to the ECD, which slightly reduces or increases the duration of the on
time for the injectors, according to whether the sensor reports the mixture is richer or leaner than stoichiometric.
This "closed-loop" control maintains the air/fuel ratio within 0.1 percent of the chemical ideal, thus allowing the
converter to do its job.
In practice, an output from the sensor of 450mv is used by the ECD as the threshold of the lean limit and 500mv
as the rich limit. This means that the air/fuel ratio actually oscillates back and forth (though always within 0.1
percent of stoichiometry) as the ECD responds to the voltage signal from the sensor.The time required for the
sensor output voltage to vary between these limits depends on its temperature. At idle, when the gas temperatures
are low-say 3000 C (about 5700F)-that time interval might be as much as a couple of seconds; under typical
road loads, the exhaust temperature is more like 6000 C (11000F), and the "cycletime" is reduced to less than 50
milliseconds (1120second).
The sensor is essentially inoperative at temperatures below 3000 C, so during engine startup and initial warm-
up the ECD ignores the sensor voltage and falls back on a set of internal "maps," until such time as the signals it
is getting from the sensor make sense. Accordingly, emissions are inevitably increased during this warm-up peri-
od, so to reduce the wait for the sensor to reach operating temperature, some sensors have an internal heating ele-
ment to bring it on-line as quickly as possible.
36
-

first production application of
A~noted in the previous chapter,the
was the version installed on the Volkswagen
type 3 1600, in 1967, for the 1968 fastback
and Variant (station wagon) models.
Although the prototype for this system- the
Bendix Electrojector
decade earlier, it was a very rarely encoun-
tered option, on just a couple of uncommon
and expensive models. By contrast, that first
Bosch/VW system was standard equipment
on a low-priced, mass production car, and as
such is rightly regarded as something of a
milestone in automotive history.
osch electronic fuel injection
- was introduced a
D-Jetronic
At the time of its introduction, this system
was simply identified by Bosch as
"ECGI"- Electronically Controlled Gas-
oline Injection; it was soon relabeled
"Jetronic."To distinguish it from subsequent
versions, it has since become known as the
"D-Jetronic." Here, the "D" stands for
druck-German for pressure-because the
calculation of the quantity of fuel to be
injected was based on manifold pressure.
After the 1968VW, the D-Jetronic was also
used on the Porsche 914, and a number of
Mercedes, Volvo and Saab models, in some
cases until 1975. The last cars to be fitted
with this system were the 1975 Mercedes
450 and the Volvo 164E of the same year.
Doubtless many thousands remain in use
today.
Mechanical Components
The mechanical parts of the system
includethe fuelpump,filter,pressureregu-
lator,fuellinesandinjectors.An electrically
1
1.Fueltank
2.Electricfuelpump
3.Fuelfilter
4.Fuelrail
5.Fuelpressureregulator
6.Fuelinjectionvalve
7.Coldstart valve
driven roller-type rotary pump draws fuel,
through a filter,from the fuel tank and deliv-
ers it to a "common rail" fuel line supplying
the injectors. Pressure in the fuel rail is
maintained at a constant 28-32psi by a reg-
ulator which functions by bleeding off
excess fuel and allowing it to flow back to
the tank via an essentially unpressurized
return line. The regulator is thus located,
schematically at least, at the opposite end of
the fuel rail from the pump.
The need for tight control of fuel pressure
should be apparent from the system descrip-
tion in the previous chapter: The system
controls fuel quantity by varying the "on-
time," or "pulse time" of the injectors, but
the rate of fuel flow through an injector that
is "on" is a direct function of the supply
4
Schematic layout of the fuel
supply components of a typi-
cal Bosch intermittent injec-
tion system. (Robert Bosch
Corporation)
37
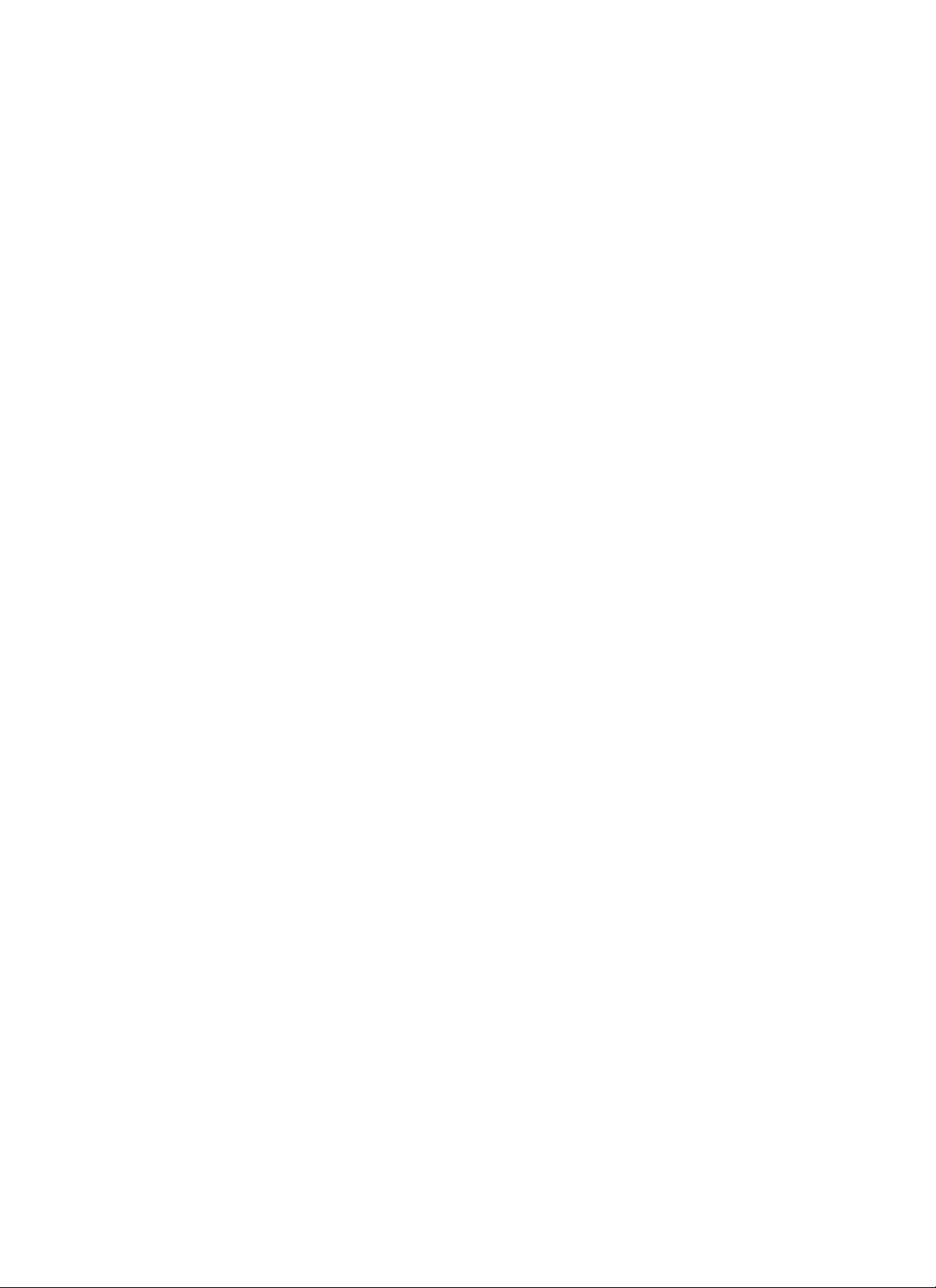
38
pressure. For the on-time to be the control-
ling variable, the supply pressure must be
fixed within narrow limits.
Each injector is installed near the intake
valve it serves.While all D-Jetronic installa-
tions thus employ a number of injectors
equal to the number of engine cylinders, the
injectors do not "fire" individually, but
rather in groups of two, as mentioned in the
previous chapter. Thus, on four-cylinder
engines there are two groups of two, on
sixes two groups of three, and on eights
there are two groups of four.
Each electromagnetic injector consists of a
valve assembly with a needle valve that
opens a single orifice nozzle. The opposite
end of the needle valve is attached to the
core of the solenoid. When no current is sup-
plied, the needle is pressed onto its seat by a
spring. When current is supplied, the needle
is pulled inward very slightly (about 0.006
inch), and fuel flows out through the cali-
brated nozzle opening, past a protruding tip
at the point of the needle that aids atomiza-
tion of the fuel. The action is very much like
that of an ordinary paint spray gun.
Electrical Components
The electronic components of the system
include a pair of contact points, a manifold
pressure sensor, an air temperature sensor
and an engine temperature sensor. There is
also a "throttle position sensor," although in
early versions this consists simply of two
microswitches that detect just full throttle
and closed (idle) throttle. All these compo-
nents feed signals to the electronic control
unit (ECU), which contains a couple of hun-
dred discreet transistors, diodes, and capaci-
tors (condensors) mounted on a circuit
board, and all contained in a metal box about
the size of a large book.
The heart of the ECU is a device known in
electronics as a multivibrator. This is not
actually a single component, but rather a cir-
cuit comprising a number of components,
and having the characteristic that, once trig-
gered, it will turn on an electric current for a
certain length of time. (There is one of these
in your windshield wiper "intermittent"con-
trol). The actual duration of that time inter-
val depends on the value of the components
in the circuit. Thus by arranging for the elec-
trical characteristics of one or more compo-
nents to be variable, the on-time following
each triggering can be altered. (We will
postpone describing the internal logic of the
ECU until we deal with the L-Jetronic sys-
tem, below.)
It seems that the very earliest versions of
D-Jetronic achieved the mixture enrichment
needed for cold starting simply by provid-
ing, in response to information from the
engine temperature sensor, a longer duration
pulse for the injectors. Although the history
has been somewhat difficult to reconstruct,
it also appears that this proved inadequate
for some areas in North America, shortly
after cars fitted with this early equipment
starting arriving on these shores in 1969.
What is certain is that a factory "cold start
kit" was made available, to be retrofitted to
these early units. The heart of this kit was an
extra injector, fitted onto and feeding into
the intake manifold, that opened and stayed
open continuously while the engine was
being cranked. This so-called "fifthinjector"
(the name stuck, even when there were six
or eight injectors, for equally numerous
engine cylinders) subsequently became an
integral part of the system.
Drawbacks
While it was in general an effective and
reliable system, the D-Jetronic was not with-
out its shortcomings. One of these was the
mechanical triggering contacts. Now, a
mechanical device operating in conjunction
with any electronic device often proves to be
a weak spot, but because the triggering con-
tacts for the PI only carried a tiny current,
arcing of these points was not the problem it
is for a traditional ignition distributor.There
nevertheless remained the problem of wear

of the rubbing block on the moveable con-
tact. While these contact points were consid-
ered good for 100,000 miles-essentially
the life of the vehicle- they were an occa-
sional source of grief.
Early versions of D-Jetronic exhibited
another occasional source of complaint
(more an annoyance than a serious defect): a
very brief hesitation on sudden throttle
opening at low rpm. We can speculate that
this resulted from the absence of any direct
provision for acceleration enrichment. Later
versions had a more elaborate throttle posi-
tion sensor that enabled the ECU to detect
sudden throttle opening and to adjust the
pulse time appropriately.
Somewhat surprisingly,the manifold pres-
sure sensing principle itself was also eventu-
ally regarded by Bosch as a shortcoming.
On the face of it, manifold absolute pressure
(MAP) appears to be a valid measure of
engine load, and thus of fuel quantity
requirements, and one having inherent cor-
rection for variations in air temperature and
atmospheric pressure. There are a couple of
points about which we might speculate.
First, to measure manifold absolute pressure
obviously requires that there be a manifold!
Manufacturers wishing to make full use of
acoustic ramming (see Chapter 8) might
prefer to have the intake pipe for each cylin-
der as completely separate as possible from
all the others. And when multiple intake
pipes arejoined together in a common man-
ifold, the pressure fluctuations within those
individual pipes are likely to cause oscilla-
tions in the manifold pressure, especially on
four cylinder engines. Apart from these
design considerations, time revealed that the
D-Jetronic was very sensitive to engine con-
dition. An aging engine with poorly sealing
valves could confound the calculations of
the ECU.
L-Jetronic
Many of the shortcomings of the
D-Jetronic system were answered in
the L-Jetronic, introduced in 1974,and first
appearing on the Porsche 914 of that model
year. Although there have been numerous
subsequent versions of EFI manufactured by
Bosch under the "Jetronic" label, the
L-Jetronic established the principle of cal-
culating the fuel quantity required- and
thus the pulse time of the injectors-on the
basis of airflow, rather than manifold pres-
sure as on the D-Jetronic. This fundamental
difference is reflected in the designation-
the "L" stands for luft, the German word for
aIr.
Components of the L-Jetronic
system. (Robert Bosch
Corporation)
39

1.Throfflevalve
2.Airflowsensor
3. Intakeair temperaturesignaltotheECU
4. ECU
5.Airflowsensorsignalto the ECU
6.Airfilter
4
5
L
3
6
(Q)
~
Airflow sensor in the intake system. (Robert Bosch Corporation)
1
Airflow Sensor
The airflow sensor is a box through which
all of the intake air has to pass. Within the
box is a spring-loaded vane or flap, hinged
at the top, which is deflected from the down
(closed) position by the momentum of the
air passing through the sensor. Attached to
the vane's hinge is a potentiometer-a vari-
able resistor, like a radio volume control.
Movement of the vane causes an electrical
contact in the potentiometer to wipe around
a ring-shaped surface that is wound with a
resistance wire, so that the total resistance of
the potentiometer depends on the position of
the wiper, and thus of the vane. By measur-
ing this resistance value, the ECU is thus
able to "know" the position of the vane and
thus the rate of airflow through the meter.
The internal "floor"of the box is shaped so
that, in combination with the weight of the
vane and the calibration of its return spring,
the angle of the vane is proportional to the
40
I Inductedairquantity
2
logarithm of the airflow rate. That is, a dou-
bling of the flap angle corresponds to a ten-
fold increase in airflow. The sensitivity of
the airflow meter is thus greatest at small
values of airflow, when the greatest meter-
ing precision is needed.
As mentioned in Chapter 1, the opening
and closing of an engine's valves causes
pressure fluctuations in the intake air stream.
To reduce the tendency of these fluctuations
to cause the vane to oscillate or flutter, a sec-
ond flap is arranged at ninety degrees to the
fIrst.Pressure pulsations act on both vanes at
the same time; apulse of pressurethat would
swivel one of the vanes in one direction has
the opposite effect on the other vane, so the
two forces tend to be self-cancelling. This
second balance (or damping) vane also has
another function. As the measuring vane
opens, the balance vane moves into a closely
surrounding space, so the tendency of the
measuring vane to slam open- and perhaps
bounce-is damped by thebalance vane run-
- -

1
w
;::,.
V6543210
.-- Us
QL
2
1.Ringgearforspringpreloading
1
!
2.Returnspring
3.Wipertrack
4. Ceramicsubstratewithresistors
andconductorstraps
1
Q)
30°
60°
90°
~
- <::s
100 150 m3/h50
.
5.Wipertap
6.Wiper
7.Pump contact
The vane-type air meter of an L-Jetronic system, viewed from the electrical con-
nection side. (Robert Bosch Corporation)
7
6
5
i
I
4 3
Interrelationships between intake air quantity,
sensor-flap angle, voltage at the potentiometer
and injected fuel quantity. (Robert Bosch
Corporation)
ning into this dead-end air pocket.
Now, the force that pushes on the measur-
ing vane is a result of the momentum of the
passing air, and momentum is simply the
product (multiple) of mass and velocity. At
first thought, then, it might seem that this
sensor apparatus directly measures mass
flow- the weight of air passing per minute,
which is what matters. In fact, the only way
that the vane could measure the total
momentum of the passing air would be to
bring it all to a complete halt- no air would
flow! Obviously, the vane must obstruct the
airflow as little as possible (the pressure
drop caused by the vane isjust 0.017 psi), so
it only measures a small fraction of the total
momentum, and we have no direct way of
knowing what that fraction is. As a result,
the meter is actually measuring volume
flow. The relationship between the volume
of a certain quantity of air and its mass is a
function of its temperature-cold air is
denser than hot air. Consequently, an air
2
1.Compensationflap
2.Dampingvolume
3.Bypass
4.Sensorflap
5.Idlemixtureadjustingscrew
(bypass)
5
The vane-type air meter of an L-Jetronic system, viewed from the other side. Note
the compensating flap which serves both as a counterweight and as a pulsation
damper. (Robert Bosch Corporation)
4
3
temperature sensor is provided, to allow the
ECU to correct the volume flow information
from the airflow sensor on the basis of the
air's temperature.
Idle Air Bypass
To permit a degree of manual adjustment
of idle mixture strength (mainly to allow
adjustment of idle speed), a small amount of
41

. Signals and controlled variables at the ECU
QL Intake air quantity, 1'}LAir temperature, II Engine speed, P Engine load range,
1'}MEngine temperature, VEInjectionquantity, QLZAuxiliaryair,VEsExcess fuel forstarting,
VB Vehicle-system voltage.
Input variables
QL
~
11M
==8>
~M
~
Control unit
and supply
BOSCH
Output variables
VE
==8>
~
~
Signals and controlled variables at the ECU. (Robert Bosch Corporation)
air is allowed to bypass around the measur-
ing section of the airflow meter through a
separate small passageway. This extra idle
air is thus unmetered; the ECU is "unaware"
of it. The amount of air that is bypassed in
this way can be adjusted by a small needle
valve arranged at the end of the bypass pas-
sage nearest the engine. Turning this screw
in makes the opening smaller, reducing
bypass airflow and so richening the mixture.
Other Sensors
Apart from the main air quantity signal
from the airflow sensor and the density cor-
rection signal from the air temperature sen-
sor, there are additional sensors continuous-
ly providing information to the ECU. Like
the D-Jetronic, there is an engine tempera-
42
ture sensor,the outputof whichis used by
the ECU to enrich the mixtureduringcold
starts and during warm-up.Also like the
earlyD-Jetronic,thereis a throttleposition
sensorthatreportsjust closed(idle)throttle
andfullthrottle.Thisinformationis usedby
theECUto providemixturestrengthcorrec-
tionsfor thosetwooperatingconditions.
Even though some domestic auto mak-
ers retain manifold absolute pressure as
the principle load signal for their EFI sys-
tems, Bosch regards the L-Jetronic's air-
flow meteringas an improvementoverthe
manifold pressure metering used on the
D-Jetronic. Certainlyit makes the system
lesssensitivetochangesin enginecondition
withage,suchas deteriorationof valveand
piston ring sealing, carbon build-up, etc.,

1
2
3
1.Eleclricalconnection
2. Housing
3. NTCresistor
2
3
4
1.Fullloadcontacl
2. Contouredswitchingguide
3.Throttlevalveshaft
4.Idlecontact
5.Electricalconnection
Throttle valve switch. (Robert Bosch Corporation)
Engine temperature sensor. (Robert Bosch
Corporation)
but it has some potential faults of its own.
For one thing, early versions could be
destroyed by a backfire, although later
ones incorporate an "anti-backfire valve"
that opens when exposed to a high pres-
sure on the engine side of the vane. And
like the D-Jetronic, any air leaks down-
stream of the meter allow unmetered air
(sometimes called "false air") into the
engine, causing the mixture to become lean.
The airflow meter is also more expensive to
manufacture than the simple aneroid bel-
lows of the D-Jetronic's pressure measuring
apparatus.
Mechanical Components
The mechanical components of the
L-Jetronic are similar to those of the
D-Jetronic. As there, an electrically
driven roller-type rotary pump draws fuel
from the tank. The L-Jetronic's pump is
equipped with a check valve that keeps the
fuel lines full and pressurized even when the
engine is stopped. This permits quicker
restarts, and helps to prevent vapor lock.The
pump also has arelief valve at its intake end,
which returns fuel to the tank if the internal
pressure rises too high.
Because roller-cell pumps are much better
at pushing than at pulling, the pump is locat-
ed low down, near the tank; indeed, in some
cars it is actually inside the tank, immersed
in fuel! Even in those cases where the pump
is located outside the tank, its internal
electrics are totally submerged in the fuel
carried within the pump; this helps to cool
the pump motor. Although this sounds dan-
gerous, it is a practice that has been used in
aircraft for years, and three decades of
uneventful experience with Bosch systems
using this scheme should dispel any anxiety.
(Although the pump can be damaged by
43

1.Intake
2.Rotorplate
3.Roller
4. Rollerraceplate
5.Outletport
2 3 4
1.Intake
2. Pressurelimiter
3. Rollercellpump
4. Motorarmature
5. Checkvalve
6.Outletport
The roller cell fuel pump. The rollers fit loosely in their lands; centrifugal force
pushes them against the contoured interior of the pump body. (Robert Bosch
Corporation)
2 3 4
5
overheatingif it is rundry for long;bearthis
in mind if you ever run completelyout of
fuel.)A paperelementfilter is provided,but
unliketheD-Jetronicthisis locatedafterthe
ratherthanbeforeit.
pump
As with the D-Jetronic, the regulator is
schematically at the far end of the fuel rail,
maintaining pressure within the rail for the
injectors, and bleeding excess fuel back to
the tank. (A notable side benefit of this con-
stant circulation of fuel is that it helps keep
the fuel cool, thus further reducing the risk
of vapor lock.) The L-Jetronic's regulator
maintains either 36psior 44psi fuel pressure,
according to the vehicle model, somewhat
44
higher than the D-Jetronic's 28-32psi.
Generally, the higher pressure (about 44psi)
is used with more powerful engines; higher
pressure means a greater fuel flow for a
given injector pulse time. Of course, the rate
of flow at a given fuel pressure depends on
the local pressure where the fuel is being
injected. Because manifold pressure varies
according to engine load, the pressure
against which the fuel is working has to be
taken into account. Accordingly, the spring-
loaded diaphragm in the L-Jetronic's regu-
lator has a connection from its back surface
to the manifold. As manifold pressure
varies, the load against the diaphragm
changes, so the regulator maintains a con-
stant pressure difference between the fuel in
the rail and the air in the manifold. The D-
Jetronic did notneed this feature because the
ECU took the manifold pressure into
account in the calculation of the injector
pulse time.
Although all later L-Jetronic systems
used digital electronics, the first version
was analog (see the sidebar "Much or
Many?"). Nevertheless, the principles of
operation that were established with the
first L-Jetronic system have enough in
common with all subsequent versions that it
is now worthwhile to look at the way the
inputs from the various sensors are dealt
withby theintemallogic oftheECU.
Inside the ECU
In contrast to the mechanical contact
points used in the D-Jetronic, L-Jetronic sys-
tems use the firing of the ignition system as
a trigger signal. In a four-cylinder, four-
stroke engine, there will be a spark plug fir-
ing twice per engine revolution. Thus, the
ECU (electronic control unit) receives two
triggering pulses per revolution. If you have
ever seen an oscilloscope trace of an operat-
ing ignition system, you will understand that
these pulses, as received by the ECU, are
"ragged"- the electricaloscillationsin the
coil windings produce a voltage trace with a

46
succession of "wiggles" that rapidly damp
out.
The first operation within the ECU is to
turn these ragged, spikey voltage pulses into
a simple square pulse of fixed duration-
upon triggering by the ignition" spike," the
voltage at the output of these stages rises
nearly instantaneously from zero to some
small positive value, dwells there for a brief
time, then drops back to zero. (In electron-
ics, this "pulse-shaping" circuitry, known as
a "Schmidt trigger," is commonplace. They
are used, for example, to eliminate the
effects of thebouncing that occurs with ordi-
nary mechanical switch contacts, etc.) Thus,
there are now two square-wave pulses
departing from the pulse-shaping circuit
with each revolution of the crankshaft.
These pulses then pass to a frequency
divider, which, in effect, ignores every other
one and passes onjust one of them. The next
stage in the internal electronics thus receives
just one pulse per revolution.
Pulse Time-That next stage is termed by
Bosch the "division control multivibrator."
Here a basic pulse time is generated, on the
basis of engine speed and air mass flow.The
rpm is known from the frequency of the
pulses arriving from the frequency divider;
the air mass flow is known from the position
of the vane in the airflow meter, plus a cor-
rection introduced on the basis of informa-
tion from the air temperature sensor. If all
operating conditions are "normal"-engine
fully warmed up, running at a moderate
speed and load, and battery voltage near
nominal value-that pulse time would give
an appropriate injector pulse time. These
pulses of "basic" duration arethen passed on
to the next batch of circuitry- the "multipli-
er stage."
Multiplier Stage-When circumstances
vary from the optimum that calls for a pulse
of "basic" duration, further internal calcula-
tions are performed by the multiplier stage.
Low battery voltage, for example, will slow
down the opening of the injector valves. The
basic pulse time is calibrated on the assump-
tion that the injector spends a mere one mil-
lisecond opening, stays open for the dura-
tion of the pulse, then closes almost instant-
ly when the pulse ceases. Of course, almost
instantly means that there is some small
amount of fuel injected after the pulse ceas-
es, while the spring within the injector
returns the needle valve fully onto its seat.
As long as the one millisecond delay in
opening can be counted on, this "incidental"
fuel on closing is offset by the opening
delay, so the basic pulse time will deliver an
appropriate amount of fuel. Low voltage
does not affect the closing spring, so the
incidental delivery remains pretty much
constant, but low voltage does extend the
opening delay, so less fuel will be delivered
under these conditions. A connection to the
battery "hot" terminal provides the multipli-
er stage of the ECU with information about
battery voltage, allowing the calculation of
an extension to the basic pulse time, to make
up for the short-changing of fuel that results
from the slow injector opening accompany-
ing a low system voltage, such as occurs
after an extended period of cranking. This
voltage connection is usually made as direct
as possible (no fuse, for example) to reduce
the risk that corrosion at terminals may give
the ECU a false reading of battery voltage.
Inputs from the air temperature and engine
temperature sensors are used by the multi-
plier stage to add more time to the basic
pulse duration to account for cold starting
and warm-up phases. Similarly, the pair of
microswitches that signal idle and full throt-
tle also feed information to the multiplier
stage, which adds the appropriate amount of
pulse duration to provide further enrichment
under these two conditions.
Acceleration Enrichment
Apart from the microswitch that signals
full throttle, there appears to be no provision
for acceleration enrichment on many ver-
sions of L-Jetronic. In fact, this is handled

16
BOSCH
Fueltank
1.
2. Electric fuel pump
1.
3.Fuelfilter
4.ECU
0
4 I-
~
+
5.Fuelinjector
6.Fuelrailandfuelpressureregula-
tor
7.Intakemanifold
8.Cold-startvalve
9.Throllievalveswitch
10.Airflowsensor
11.lambdasensor
12.Thermo-timeswitch
13.Enginetemperaturesensor
14. Ignitiondistributor
15.Auxiliaryair device
16.Ballery
17.Ignitionandstartingswitch
Schematic diagram of an L-Jetronic system with lambda (oxygen sensor) control. (Robert Bosch
Corporation)
mechanically, rather than through the elec-
tronics. When the throttle is openedsudden-
ly, the rapid increase in airflow through the
sensorcausesthevaneto overshoot momen-
tarily. Because the BCD is using the vane
position as a measure of airflow, this exag-
gerated movement
the BCD to briefly increase the pulse time,
thereby providing the enrichment needed to
avoid a "lean stumble" when the throttle is
banged open.
of the vane influences
Some versions of L-Jetronic have afurther
refinement in this regard, in addition to the
enrichment from vane" overshoot." The
same signal from the vane position sensor
that provides the BCD with its basic infor-
mation about air quantity is also analyzed
for the rate-of-change of the vane's position,
so a rapidly moving vane will prompt the
BCD to provide more enrichment than
would a more slowly opening one. In either
case, the BCD will add acceleration enrich-
ment whenever the microswitch that signals
full throttle is closed.
On cars with a lambda sensor-generally,
those built after 1980-the output from that
sensor are also fed to the BCD. The multi-
plier stage processes information from the
lambda sensor, increasing the pulse time
(that is, richening the mixture) when the
oxygenleveldetectedby the sensoris high,
reducing the pulse time (leaning the mixture
out) when the oxygen level drops. This cou-
pling between the lambda sensor and the
BCD is called "closed-loop" control- infor-
mation from the sensor induces the BCD to
47

48
make changes, which are detected by the
sensor which thenprovides a different signal
to the ECU, which adapts again. . . and so
on. (See also the sidebar "The Oxygen
Battery" in Chapter 2.) Whenever the full
throttle microswitch is closed, the ECU
reverts to "open-loop" control-it ignores
data from the lambda sensor, and depends
on its internal "maps."
After all these calculations, the pulse that
emerges from the multiplier stage has the
"basic" on time span, plus some added dura-
tion for enrichment, according to inputs
from all the various sensors. That pulse,
however, is extremely weak; the internal
electronics all operate on just tiny amounts
of voltage and current. Heftier electronic
components are needed to deal with the 12
volts and comparatively large currents that
actuate the injectors. That task is handled in
the final" amplifier stage" of the ECU.
There aretwo points to note here. First, the
pulses are coming once per crank revolu-
tion-on a four-cylinder, four-stroke engine
that means two pulses per cycle-and all the
injectors fire at once. Second, while the
above description of pulses leaving the ECU
to drive the injectors is a fair schematic rep-
resentation of what is going on, the injectors
are actually hot all the time-the ECU in
fact grounds the injectors for the duration of
each pulse.
Cold Starting
As might be expected, cold starting is a
special case that may lie outside the normal
range of calculation of the multiplier stage,
and the total fuel requirement may exceed
the capacity of the injectors, even when they
are "on" almost all the time. Different ver-
sions of L-Jetronics adopt different strategies
for cold starting.A few get by simply by vast
increases (a doubling or tripling) of pulse
time; most use a separate "cold start" injec-
tor, just like the mature version of the D-
Jetronic; a few others use both approaches.
The two temperature sensors on
L-J etronic systems - one for intake air,
the other for engine temperature - are both
based on what is called a "negative temper-
ature coefficient" (NTC) resistor. This refers
to the fact that, unlike many resistors whose
resistance value increases positively with
temperature, the NTC has the opposite char-
acteristic; when the NTC is cold, it has a
high resistance, when hot the resistance
falls. NTC I (or Temp I), in Bosch's termi-
nology, is the airtemperature sensor;NTC II
senses engine temperature. So, while infor-
mation from NTC I is used all the time by
the ECU to correct the airflow information
from the airflow sensorvane, in effectto cal-
culate air mass flow, NTC II is the key com-
ponent in achieving the wholesale enrich-
ment needed for cold start. On water-cooled
engines, NTC II will be found in the same
sort of places- such as the thermostat hous-
ing- where you would expect to find an
ordinary "temperature sender" for the dash
temperature gauge. . . and may be confused
with it! On air cooled engines, NTC II will
be screwed into a cylinder head.
In the comparatively new L-Jetronics that
use just an increased fuel delivery through
the standard injectors for cold starting, a
high resistance value (say 3000 Ohms or
more) detected at NTC II will simply influ-
ence the ECU to increase the pulse time. In
these systems, the required fuel flow for a
"cold-cold" start (engine temperatures much
less than room temperature) may require the
ECU to "double-up" the firing of the injec-
tors as long as the starter is cranking, to pro-
vide two injection cycles per crank revolu-
tion, instead of the usual one cycle. The
ECU makes this decision based on both the
temperature reported by NTC II and by the
cranking rpm. The ECU also keeps track of
the time elapsed during cold cranking, and
will reduce the quantity of fuel injected
under circumstances that seem likely to lead
to flooding.
However, many L-Jetronics (and certainly
most early ones) use a "cold start valve," in

1.Electricalconnection
2.Housing
3.Bimetal
4. Heatingwinding
2
5. Electricalcontact
1
1.Electricalconnection
2.Fuelinlet
3.Valve(solenoidarmature)
4.Solenoidwinding
5.Swirlnozzle
6.Valveseat
3
4
5
The thermo-time switch. The contacts are closed
when the switch is cold, and open when it is hot,
either from a warm engine or because the electric
heating element has had time to warm it. (Robert
Bosch Corporation)
conjunction with a "thermo-time switch."
This cold-cold start circuit, which operates
only as long as the starter is cranking, is
quite independent of the ECU. Power is fed
to the cold start injector (which Bosch terms
a "cold start valve") via the starter terminal
on the ignition switch, but whether or not the
injector is actually energized depends on
whether or not it is grounded. And that
depends on the thermo-time switch.
The thermo-time switch comprises a pair
of electrical contacts, one fixed and one at
the end of a bimetallic strip, which consists
of two layers of different metals bonded
together. The two metals chosen have wide-
ly different thermal expansion characteris-
tics, with the result that the strip bends to a
greater or lesser extent, according to its tem-
perature. When "cold" (less than about 95°
F), the strip is nominally straight, and the
contact on its end touches the fixed contact,
closing the switch so current will flow. The
4 .
6
A cold start injector (cold start valve), shown in the "on" state. (Robert Bosch
Corporation)
3
5
cold start injector is wired in series with this
switch, so when the starter is energized with
the thermo-time switch closed, current flows
through the windings of the cold start injec-
tor, so it opens and passes fuel into the
intake manifold.
To prevent engine flooding, an electrical
heating element surrounds the bimetallic
strip. This heater is fed by the same current
that is passing through the contacts, so after
a brief time (never more than about ten sec-
onds, even in the coldest weather) the strip
will heat up, bend, and so open the switch,
cutting off juice to the cold start injector.
Because its working end is immersed in
engine coolant, or at least attached to the
engine block, the thermo-time switch will
remain open if the engine is much above
room temperature.
Auxiliary Air Bypass
Because Bosch EFI systems have no
mechanism corresponding to the fast-idle
cam on a carburetor equipped with an auto-
49

RPM
3800
,
,
,
,
\
Cut-in
'""d
Q)
Q)
P-<
[f)
"'-;
Q)
0.0
3400
3000
2600
2200
1800
1400
limit
1000
0
-30 -10
To improve economy and
reduce emissions, the fuel is
shut offwhen the throttleis
closed, as signalled by the
throttle switch. To prevent
"hunting," the cut-off and
cut-in limits are separated by
a few hundred rpm. The rpm
at which cut-off occurs is
lowered proportionally as the
engine warms up, to prevent
stalling with a cold engine.
(Robert Bosch Corporation)
50
,
,
,
,
,
,
,
,
'\,
" ~ut-off
\,~ lImit
\
"
"
'-..
"--
----
~
-
50
10
30
70 90
110 Deg C
Coolant temperature
matic choke, the extra internal friction of a
cold engine could pull the idle speed down
so low that the engine may not continue to
run. To provide the equivalent of a slight
throttle opening so as to maintain a reason-
able idle speed, an "auxiliary air bypass" is
provided. This bypass amounts to a small
rotary disc valve; depending on the position
of the disc, more or less air (or none) is
allowed to bleed around the nearly closed
throttle. The position of the disc, in turn, is
governed by a bimetallic coil. When the coil
is warm, the valve is completely closed;
when very cold, it is fully open; at interme-
diate temperatures, it adopts a position
somewhere in between. A smooth and grad-
ual transition from open to closed as the
engine warms up is assured by the profiling
of the valve disc and the calibration of the
bi-metallic coil and of a return spring that
pulls the valve to the closed position. A few
early versions of this valve are heated by
engine coolant; most recent ones are electri-
cally heated, just like the thermo-time
switch.
Note that unlike the idle air bypass, the
auxiliary air valve merely skirts around the
throttle plate; all the air passing through
the auxiliary air valve has already passed
through the airflow meter, and so is
"counted" by the ECU. Note too that,
unlike the functioning of the thermo-time
switch/cold start injector which is never in
operation for more than a few seconds, in
very cold weather the auxiliary air bypass
valve can take several minutes (though
never more than eight or ten) to move from
fully open to fully closed.
Warm-Up
The first 30 seconds after a cold start
represent perhaps the toughest challenge to
auto emissions engineers. On the one
hand, considerable enrichment is needed
to keep a cold engine running and to have
good "driveability;" on the other hand, all
the fuel in excess of stoichiometry just flush-
es out the exhaust, adding to HC emissions.
Once a cold engine has fired, the ECU
immediately cuts back on the wholesale
enrichment that has been provided for start-
ing. A much richer than nominally stoichio-
metric mixture is still needed, however, until
the engine is fully warmed up, so instead of
two to three times normal pulse time (plus
whatever has been added through the cold
start valve), the enrichment drops to, say, 1-
1/2 times the "basic" pulse time. The ECU
gradually tapers off the "post-start" and
warm-up enrichment, on the basis of both
time elapsed and the information from NTC
II. The initial rate of this progressive leaning
of the mixture toward a stoichiometric value
is quite rapid, and is determined mostly on
the basis of time; after about 30 seconds, the
continuing reduction of fuel quantity is
essentially determined by engine tempera-
ture. Even in the coldest weather, the engine
will have warmed up enough for the mixture
to be dialled back to near nominal values
within a couple or three minutes.

Idle/Coasting "Cutoff" Switch
We have mentioned that the microswitch
that signals closed (idle) throttle signals
the ECU to provide a slight enrichment for
idle. There are a couple of other functions
for this switch on some vehicles equipped
with L-Jetronic. To avoid a "stumble" dur-
ing the off-idle transition, the opening of this
switch- indicating that the throttle has just
been opened - is used to trigger a brief addi-
tional enrichment. Also, on later vehicles,
the closing of this switch when engine speed
is well above an idle causes the fuel flow to
be shut off entirely, to eliminate emissions
(and fuel consumption) during this "over-
run" situation. To prevent the engine from
stalling, the fuel is turned back on again as
the idle speed is approached, at an rpm that
depends on engine temperature.
1.Temperaturesensor
2.Sensorringw/hot wire
3.Precisionresistor
Qm =Massairflow
1 2
3
QM
.~
/
Componentsof the hot-wire air mass meter. (Robert Bosch Corporation)
LH -Jetronic
For all that it was an advance on
D-Jetronic, the L-Jetronic system was
not without its own shortcomings. One of
these was the need to make combined use of
two separate signals-one from the airflow
meter and one from NTC I- in order to
compute the airmass flow.The design of the
airflow meter itself might also be regarded
as imperfect, depending as it does on a com-
bination of electronic and mechanical com-
ponents. While modem electronics are about
as reliable as man-made systems get to be,
anytime a mechanical device is intercon-
nected with an electronic one, the mechani-
cal bits are the most likely source of future
problems. Apart from reliability issues, cer-
tain types of road disturbances can poten-
tially "jostle" the metering vane, leading to
momentarily inaccurate information coming
from it. The vane-type airflow meter is also
a somewhat expensive device to make.
To produce a light, compact, simple, all-
electronic sensor with no moving parts that
directly measures air mass, with no need for
calculations relating volume flow, tempera-
ture, and density, Bosch embraced a device
long used in fluid-flow laboratory work-
the hot-wire sensor.Other advantages of this
form of airflow sensor are its more rapid
response (measured in milliseconds), and an
even further reduction of the already near-
trivial resistance to airflow of the vane type
sensor. The adoption of the hot-wire sensor
gave rise to a next-generation form of inter-
mittent EFI called LH-Jetronic, first intro-
duced in 1982 and used on the Volvo 2.3
liter GL model of that year. The "H" stands
Hot-wire air mass meter. The
wire is so fine (less than
0.003 inch) it may only be
visible when it glows red hot
during its "burn-off' cycle.
(Robert Bosch Corporation)
51

4
t
10
0
BOSCH
15
1.Fueltank
2. Electricfuelpump
3.Fuelfilter
4.ECU
5.Fuelinjector
6.Fuelrail
Schematic diagram of an LH-system. The "H" stands for heiss-the German word for hot. Apart from the air meter itself, this is almost
identical to the L-Jetronic. (Robert Bosch Corporation)
for heiss,the Gennanwordforhot.
7. Fuelpressureregulator
8. Intakemanifold
9.Throttlevalveswitch
10.Hot-wireair masssensor
11.lambdasensor
12.Enginetemperaturesensor
Other than the nature of the sensor itself,
many of the operating principles (and a few
of the components) of L-Jetronic and LH-
Jetronic are held in common. The mechani-
cal components-fuel pump, regulator and
injectors-differ only in detail, if at all, and
the computation underlying the fuel quanti-
ty/pulse time calculation is logically identi-
cal to that of the L-Jetronic. Note, however,
that while early versions of L-Jetronic use
analog electronics, all LH-Jetronic systems
are purely digital. Further, all LH-Jetronic
systems include lambda feedback control.
+
13.Ignitiondistributor
14.Rotaryidleactuator
15.Battery
16.Ignitionandstartingswitch
Hot-WIre Sensor
The sensing element is a very fine wire of
platinum alloy, just 0.7 millimeters (less
than 0.003 inches) in diameter, strung across
the interior of a housing through which all
the incoming air stream has to pass. The
wire is heated by an electric current, but
cooled by the passing air stream. An electri-
cal circuit adjusts the current passing
through the wire so as to maintain it at a
temperature that is consistently 180° F
above that of the entering air.Thus, if the air
temperature is 80° F, the wire will be run-
52

ning at 260° F; if the air is at 30° F,the wire
temperature will be at 210°. The current
required to maintain this equilibrium is a
measure of the mass of air passing the wire,
and is used as the principal signal to the
ECU as to air quantity.
You many wonder how the electronics
"know" that the wire is 180°hotter than the
incoming air. The electrical circuit referred
to above is a "Wheatstone bridge," an ele-
gantly simple form of electrical circuit, and
while we will not delve into the actual elec-
tronics, the principles are not particularly
hard to understand, even for the "electroni-
cally challenged." First, note that the electri-
cal resistance of platinum varies very
strongly with its temperature (it is some-
times used as a temperature detecting/con-
trolling device,just for this reason). Second,
note that, like the L-Jetronic, the LH is
equipped with an intake air temperature sen-
sor, which is itself a temperature-sensitive
resistor - a thermistor - but one whose
resistance varies much less with temperature
than the platinum wire.
If an electrical path is divided into two
parallel branches, and each branch contains
a resistor, the voltage difference between the
two branches, measured after the resistors,
will depend on the relative values of the two
resistors. Because one of those resistors-
the wire- has a resistance that varies strong-
ly with temperature, the voltage difference
between the two branches will similarly
depend strongly on the temperature of the
wire. If the current through both resistors is
changed, the wire will either heat up or cool
down.At some levelof current- thatis, at
some temperature of the wire-the two
resistors will have equal values, so the volt-
age between them will be zero. So, by intro-
ducing a detector and amplifier that con-
stantly adjusts the current so as to maintain
the voltage between the two branches of the
circuit at zero, we can be sure that the wire
is some fixed temperature (in this case 180
degrees) higher than the temperature at the
1.Hybridcircuit
1
2 2. Cover
3.Metalinsert
4. Venturi w/hot wire
5. Housing
!
Another view of the hot-wire air mass meter, with integrated electronics. (Robert
Bosch Corporation)
6.Screen
7. Retaining ring
3
4
5
other resistor- the airtemperature sensor.In
this case, the current flowing through the
circuit will be in direct proportion to the heat
lost by the hot wire, which is proportional to
the mass flow of air. The ECU, which sup-
plies the current, thus "knows" what mass of
air per minute is passing through the air
mass sensor.
Like the L-Jetronic, early LH systems had
provision for adjustment of the idle mixture
strength. Unlike the L-Jetronic, however, in
which the adjuster actually varies the size of
the air "leak" around the flow meter, the
adjustment on the LH-Jetronic is electrical
in nature. The small adjuster (located under
a sealed cover on the meter) is actually a
potentiometer that modifies the current sig-
nal received by the ECU. Later LH-Jetronics
53

a.Housing
b.Hotfilmsensor(filledinmiddleof
housing)
1.Heatsink
2. Intermediatemodule
3. Powermodule
4. Hybridcircuit
5.Sensorelement
a
5
b
1
3
4
2
5
The hot-film air mass meter, as used on most later versions of LH-Jetronic. This is
less prone to damage than the fine wire in the earlier meter. (Robert Bosch
Corporation)
omitted this adjustment.
Drawbacks
One potential problem with a hot wire as a
metering element is that if its surface
becomes contaminated, the rate of heat flow
out of it will be reduced, in which case it
would send the BCD a false signal, underes-
timating the amount of air passing. To deal
with this, the BCD's program includes a
"bum-off" cycle that feeds a much larger
than normal current to the wire for about one
second immediately after the engine shuts
off. This brief, large surge of current heats
the wire to about 1800°F, which turns it red-
hot and vaporizesany dirt depositson the
54
wire. (The whole concept is a bit like a self-
cleaning oven!)
Safety Issues-Of course, there are a cou-
ple of safety issues here-anything red-hot
in close proximity to a device that meters
gasoline is a potential hazard. Accordingly,
Bosch provides a couple of safeguards.
First, if the last reported rpm before the igni-
tion was turned off was less than 200 rpm,
then the engine was not idling, it stopped
dead for some reason
- and that reason
might be an accident. In that case, the burn-
off cycle is suppressed. Second, if the engine
has not exceeded 3000 rpm since the last
time the ignition was shut off, then maybe
the driver just started the engine, then
changed his mind. . .and maybe he will
change it back again and refire the engine.
Again, you don't want any chance of the
engine turning over with the wire red-hot, so
again the bum-off is cancelled.
In more recent versions of LH-Jetronic
(and LH-Motronic-see next chapter), the
hot-wire is replaced by a hot-film air mass
sensor. Apart from the rearrangement of
the material that forms the heated surface,
the operating principle is identical to that
of the hot-wire sensor. The hot-film sensor
is used on most modern Audis and
Mercedes, as well as some VW and BMW
models.
Idle Speed Stabilization
While early versions of the LH sys-
tem used the same auxiliary air valve
as the L-J etronic to help maintain a con-
stant idle speed, irrespective of engine tem-
perature, most LH systems use a different
device for the same purpose. Like the auxil-
iary air valve on the L-Jetronic, this "idle
speed stabilizer valve" functions by bypass-
ing a certain amount of air around the closed
(idle) throttle. (Again note that this air has
passed through the hot-wire air sensor, so it
is "measured" air-the functioning of the
idle speed stabilizer does not affect the mix-
ture strength. Functionally, this is exactly the

1
t
911_11<>
L:J
0
+
BOSCH
15
1.Fueltank
2. Electricfuelpump
3.Fuelfilter
4. Fuelinjector
5.Fuelrail
6. Fuelpressureregulator
Schematic diagram of an L3-Jetronic, having the additional control of a lambda (oxygen) sensor. (Robert Bosch Corporation)
same thing as cracking the throttle open
slightly.)
While the L-Jetronic's auxiliary air valve
is a free-standing piece of equipment, with
no connection to the ECD, that determines
for itself the amount of air that should be
allowed to pass based on its own tempera-
ture, the idle speed stabilizer of the later LH
systems is connected to the ECD, and the
amount of air that is bypassed through it is
determined by the ECD.
Instead of the auxiliary air valve's bimetal
7. Intakemanifold
8.Throttlevalveswitch
9.Airflowsensor
10.ECU
11.lambdasensor
12.Enginetemperaturesensor
strip and electric heating element, the LH
system's idle speed stabilizer is opened and
closed by a rotary actuator whose position is
a function of the "on time" to "offtime" of a
series of digital pulses coming from the
ECD. The greater the on/off ratio, the further
the valve opens, passing proportionally
more air. The ECD, of course, "knows" the
engine rpm from the frequency of the igni-
tion triggering pulses it receives. If idle rpm
drops-say, because the driver turned on
something that produces a heavy electrical
13.Ignitiondistributor
14.Auxiliaryairdevice
15.Battery
16.Ignitionandstartingswitch
55

load, such as a rear window defroster-the ECU increases
the on/off ratio of the pulses it is sending out to the idle
speed stabilizer so as to bleed more air past the closed
. throttleto maintainan appropriateidlespeed.
As with the connection with the lambda sensor,this cou-
pling of the actions of the ECU and the idle speed stabiliz-
er produces a closed-loop control. Because this provides
direct, feedback-driven control over idle speed, the idle
rpm can be set lower than when the amount of air bypassed
is based on a fixed, "best guess" program. During cold
starting, the ECU breaks the feedback loop, and directs the
idle speed stabilizer to open a preprogrammed amount,
according to temperature.
An ingenious additional feature of the idle speed stabi-
lizer is found on some LH installations. Arguably the
largest load change that an idling engine experiences is the
engagement of the air conditioner compressor. This load is
sufficiently large, and can commence with such sudden-
ness, that there is a risk of the engine stalling before the
stabilizer has a chance to respond. To conquer this tenden-
cy, the air conditioner controls are fed through the ECU,
and when the alc thermostat "tells" the compressor to cut
in, the ECU briefly delays the actual clutching-in of the
compressor, to give the idle speed stabilizer a chance to
anticipate the additional load. Clever!
MUCH, ORMANY?ANALOGVS. DIGITAL
A dozen eggs, a quart of milk; a hundred bricks, abag of cement. We gauge the quantity of some things by count-
ing, but others we measure by weight or volume. The difference is subtle but basic-the first case involves a dig-
ital operation, the second is an analog process. Now, while one major aspect of the electronic revolution was the
invention of the transistor, the shift from electronic devices that operated on an analog basis to ones that work dig-
itally is at least equally significant.
At its simplest, a transistor can be thought of as an electronic control valve. There are three wires attached; two
"in" and one "out." Youfeed a fixed, comparatively large amount of power to one of the inputs, and a much small-
er, variable amount of juice to the second. What comes out of the third wire may vary from zero up to the full sup-
ply voltage, depending on the size of the signal (the voltage) coming in on wire number two. The special-purpose
computers that comprised the "brain box" of early electronic fuel injection systems used transistors in this way-
as proportional devices. A sensor-say for engine coolant temperature-was hooked (in principle, at least) to the
input of a transistor. Variations in engine temperature would thus directly alter the output, which in turn controlled
the "on time" (pulse time) for the injector(s), adjusting the mixture strength according to whether the engine was
cold, cool, warm, or hot.
But if you fix the "signal" voltage at some comparatively high value, then a transistor will operate more like a
solenoid relay- if the input at the signal terminal is "on," the transistor puts out; if the signal voltage is "off," so is
the output. That makes the transistor function as a digital device. On the face of it, it seems a shame to waste the
ability of a transistor to work proportionally, but this digital way of doing things has the enormous advantage that
now you can use transistors to create an electronic memory. String a few of them- say sixteen- together, and by
having some of them "on" and others "off," you have 256 (16 x 16) possible arrangements. Each arrangement
might then correspond to one of 256 different values along the cold-hot continuum.
Part of the attraction of operating digitally is the unambiguous result you get when you count things. One plus
one always equals exactly two, but when you add "some" and "some," you surely get "more," but you cannot be
sure you have twice as much. Even slight variations in components-whether from production tolerances, or from
aging,or heavenknowswhat- wouldmeancorrespondingvariationsinthe electricaloutputs.Air/fuelratioscon-
trolled by those electronics would then be slightly (or perhaps wildly) in error. Doing things digitally means that a
given sensor input (coolant temperature equals 86° F, say) would correspond to "coolanttemperature value #47,"
56

for example, and "#47" stored in the digital memory would correspond to an injector pulse lasting so many mil-
liseconds.
The opportunity to make use of a memory also means that many more combinations of factors can be taken into
account in the process of determining the pulse time of the injectors, and thus mixture strength. Thus, the appro-
priate amount of fuel for a certain engine speed and load when the coolant is at 86 degrees and the air temperature
is 7SOF is likely to be different from the same situationbut with an air temperature of minus 10°F.And when igni-
tion control gets added in-as with the Motronic systems-the complication becomes unmanageable without a
digital memory.
The air meter of an L3-Jetronic. Use of digital electronics and advances in component miniaturization permit inte-
grating the ECU into the body of the air meter itself. (Robert Bosch Corporation)


n many of the very earliest internal
combustion engines ignition was by
I
means of a "hottube" igniter. The tube,
usually made of porcelain, was located
immediately outside the combustion cham-
ber, and was continuously heated by a small
gas flame that made it glow red hot. As the
piston approached top center on the com-
pression stroke, a timing valve opened,
exposing the contents of the combustion
chamber to the hot tube, which lit (some-
times) the combustible mixture in the cylin-
der. Motoring accounts written around the
turn of the century make frequent reference
to stoppages resulting from the flame blow-
ing out!
By the early 1900s the days of hot tube
ignition were over, and the automotive
world embraced ignition by an electric
spark. As is common with emerging tech-
nologies, there was a bewildering prolifera-
tion of designs at first, but there were really
only two general categories: magnetos of
various types, and systems based on an
induction coil. Magnetos eliminated the
need for a battery- in those days a fragile
device, and even heavier than today's batter-
ies-and so became almost universal on
race cars, motorcycles, and aircraft.
Induction coil systems offeredthe advantage
over magnetos of improved ignition at low
speeds, but required an on-board source of
low voltage-a battery. As electric lighting
(and, later, electric starting) became wide-
spread, the battery was seen as less of a lia-
bility, and design rapidly converged toward
the coil and breaker system designed in
1911 by Charles Kettering. This "Deleo"
system- named after the Dayton Electric
Company, founded by Kettering- rapidly
became almost universal after its introduc-
tion on GM cars in 1922, and remained so
for more than half a century, through the
early 1970s.
Coil and BreakerIgnition
An induction coil consists of a central core
of soft iron surrounded by two separate
windings of copper wire. One of the wind-
ings, called the "primary," consists of a
small number of turns (typically a couple of
hundred) of comparatively thick wire; the
other, called the" secondary," consists of a
much larger number of turns of much finer
wire. At one end, the primary winding is
connected to the "hot" lead of the electrical
source, while the other end is grounded, at
least most of the time. The secondary wind-
ing shares the primary's connection to the
"hot" lead of the battery; the other end is
connected to the spark plug's center elec-
trode, via the distributor cap and rotor.
When current flows through the primary
winding, a magnetic field is created in the
core-the coil is said to be saturated-and
this field is maintained as long as current is
flowing. But if this flow then suddenly stops
for any reason, the magnetic field in the core
collapses, and the stored magnetic energy
"induces" a burst of electricity in the sec-
ondary winding, hence the name "induction
coil." The interruption of the current flow is
accomplished by the breaker points. While
the primary circuit nominally operates at
just twelve volts, the induced secondary
voltage is a thousand or more times higher
thanthat- sufficienttojump the gap in the
spark plug. Notably, the collapse of the
core's field alsoinduces a high voltage in the
primary windings, which thus momentarily
59

60
experiencea surge of perhaps a coupleof
hundredvolts.
Transistorized Ignition
For passenger cars, the "Kettering"system
worked adequately well-though only just.
(At the very least, it was an advance on hot
bulb ignition!) The major catch was the need
for regular maintenance, but there were
other drawbacks as well.
One limitation of the coil and breaker sys-
tem is the current-switching capacity of the
points-a primary current of more than 5 or
6 amps will tendto cause burning and arcing
at the points, shortening their life. This, in
turn, places a restriction on the strength of
the magnetic field that can be stored in the
coil, which limits the amount of power
available to fire the plug.
Dwell
Another problem is the business of dwell.
With the traditional cam and breaker
arrangement, the primary has current flow-
ing through it for a certain fixed number of
degrees of crank rotation, but the corre-
sponding length of time that the current is
flowing thus varies with engine speed. This
leads to a dilemma: If you keep the dwell
angle small, the coil will have insufficient
time to become fully saturated at high
engine speeds, leading to misfiring at high
rpm; but if you arrange for a longer dwell
time, say by using a distributor cam with a
different lobe shape, so the points spend
more time closed and less time open, then at
low speeds the primary becomes saturated
early in the cycle, but then the current keeps
flowing because the points are still closed,
and the coil will tend to overheat.
Finally, the fiber rubbing block on the
moveable half of the point set slowly wears
down, which causes it to contact the cam
ever closer to the peak of the lobe, so the
points open progressively later, and the igni-
tion timing gets more and more retarded. We
will soon discuss the importance of this
issue of spark timing.
These first began to emerge as serious
problems during the 1960s, when manufac-
turers were heavily engaged in a horsepow-
er race. Compression ratios over 12:1, com-
bined with engine speeds over 6000 rpm,
tested the upper limits of coil and breaker
ignition, and it became clear that the days of
the classic KetteringlDeko system were
numbered. Ironically, what finally ensured
the emergence and universal adoption of
modem electronic ignition was not street
hemi's and other monster motors, but rather
the introduction of emissions legislation, in
the 1970s. Though compression ratios tum-
bled and revs dwindled, the need to fire very
lean mixtures, and to do so reliably through-
out the life of the car, became the new fac-
tors that finally eliminated contact points.
When you are scraping to meet standards for
the emission of hydrocarbons you cannot
afford even one misfire in ten thousand, and
when you have to certify the engine's emis-
sions for 50,000 miles without a tune-up,
you need a system that does not depend on
breaker points, and one that can still fire a
spark plug when its gap has eroded open to
50 thou or more.
The solution that was eventually adopted
retained the familiar induction coil, but
eliminated the problems of contact points by
eliminating thepoints themselves. Instead of
a mechanical switch to turn on and off the
current flow in the primary windings of the
coil, the switching is done electronically.
The distributor cam is replaced by a rotating
magnet, having a number of teeth or "poles"
corresponding to the number of cylinders.
As each pole passes a fixed pickup head, a
small pulse of electricity is produced. That
pulse is then used to trigger a transistor-an
electronic relay - that briefly interrupts,
then quickly restores, the current in the pri-
mary winding of the coil.
Compared to a conventional Kettering
system, there are two major advantages to
this scheme. First, the constant wear on the

rubbing block is eliminated, so timing
remains accurate and no adjustment or
replacement is ever needed. Second, when
you remove the concern over the amount of
juice you can put through the points, the cur-
rent in the primary circuit can be dramati-
cally increased, so the coil can be redesigned
to provide a greater secondary voltage out-
put that can fire a plug with a gap that is
larger, whether by design or as a result of
wear, without the risk of frying the points.
As long as there is enough juice to jump the
gap, a wider plug gap provides a bigger
spark that is more likely to light the mixture
in the cylinder. (The beliefthat "themixture
doesn't care if it's lit by a match or by a
blowtorch" is mistaken; the amount of ener-
gy in the spark does matter.) The same
increase in potential output from the coil
also means you can fire a plug that has some
additional insulation, beyond the air gap,
between its electrodes, such as one that is
fouled. The potentially higher energy output
of a modem electronically switched coil will
light the fire in such an engine when a points
type system would not.
The "brains" of an electronic ignition sys-
tem makes this possible without risking
overheating of the coil because it can, in
effect, vary the dwell angle. At low engine
speeds, a timing circuit in the electronics
delays restoring the primary current until it
judges there is just enough time remaining
to saturate the core.At higher speeds, it tries
to keep the dwell time nearly constant,
allowing primary current to flow during a
larger number of crank degrees. This fea-
ture, together with freedom from the current
limitations of breaker points, is what permits
the redesign of the coil to give potentially
more secondary output, without cooking it
through an excessive primary current. But
beyond the potential for greater spark ener-
gy, and near bulletproof reliability, electron-
ic triggering of ignition also makes it possi-
ble to use electronic control for the timing of
the spark.
Ignition Timing
We explained in Chapter 1 that the com-
bustion event, while extremely fast, is not an
instantaneous explosion that takes place the
moment the plug fires; rather, it is an occur-
rence that takes some time. Indeed, as a very
rough first approximation, we can say that at
any given load, the time taken by the com-
bustion event is pretty much constant, over a
considerable range of engine speeds. What
that means, however, is that the combustion
event occurs over a variable range of crank
angle, the variation depending on the rpm.
Now, if the spark was arranged to occur
exactly at TDC, then the engine might run
satisfactorily at very low speeds, but as the
rpm's increase, the combustion would lag
farther and farther behind the piston move-
ment, reaching the point where the fire was
just barely getting started at the moment the
exhaust valve opened, so most of the energy
would just get flushed down the pipe. This,
clearly, is no good for power output, fuel
economy or emissions. Thus, real world
engines incorporate a degree of ignition
advance- the spark occurs before the piston
reaches TDC. And because of the fixed-
combus tion -timelv ariab le-engine-s peed
relationship, that advance is usually
arranged to be variable-less advance at
low speeds; more at high speeds.
Limits and Complications
Of course, there are limits, and there are
complications. As to limits, if the spark
occurs too soon, the pressure will have risen
so high by the time the piston reaches TDC
that the pressure opposing the rising piston
negates much of the power delivered later,
when the piston is on its way back down on
the power stroke. Also, an advanced spark
means that the pressure of the early stages of
combustion add to the pressure rise caused
as the ascending piston squeezes the com-
bustion chamber contents ever smaller, and
we saw in Chapter 1 that the uncontrolled
61

62
combustion called detonation is initiated by
excessively high temperatures and pressures
during these early phases of combustion.
Thus, excessive spark advance leads to det-
onation. Finally, the assumption that com-
bustion takes a fixed length of time, even at
constant load, is only valid at moderate
engine speeds. In fact, at high speeds the
increased degree of turbulence in the com-
bustion chamber, both before ignition and
during the early stages of combustion,
increases the speed of combustion and sothe
requirement for an ever increasing advance
with rising rpm levels out at some point,
beyond which the appropriate amount of
"spark lead," as it is called, is more or less
fixed.
As to complications, all of this discussion
refers to an engine at constant load, and real
engines don't work under those simplified
conditions. A larger load at a given speed
means the throttle is open wider, so a greater
mass of air/fuel mixture will be inhaled, so
the pressure in the cylinder near the end of
the compression stroke will be higher. Thus
to avoid detonation, increased load calls for
less ignition advance.
In the old days of "flintlock" ignitions, the
variation of advance with rpm was handled
by a centrifugal advance mechanism. This
comprised a set of weights spinning within
the distributor body that were flung further
outward as speed increased and so, through
a system of links, rotated the plate on which
the points were mounted, relative to the
position of the cam that opened them.
Vacuum Advance Mechanism
The reduction in advance called for by an
increase in load was provided by a vacuum
advance mechanism. (The name is poten-
tially confusing; while it did in fact increase
advance in response to high manifold vacu-
um, its function was really to retard the
spark when vacuum was low, indicating a
high load.) The vacuum advance generally
took the form of a chamber containing a
diaphragm that had one side exposed to
manifold vacuum and a link connected to
the other surface that, like the centrifugal
weights, swiveled the distributor plate
(although this motion opposed that caused
by the weights).
Asking mechanical devices like these to
balance all the variables that determine opti-
mum spark advance is, of course, asking too
much. Accordingly, soon after the introduc-
tion of electronically triggered ignition-
generallycalledtransistorizedignition- the
task of timing the spark was sometimes also
entrusted to the "black box." Because the
centrifugal and vacuum advance mecha-
nisms were eliminated from the distributor,
leaving simply the rotor and cap to direct the
spark to the appropriate plug, the distribu-
tors on engines equipped with such elec-
tronic ignition have a stumpy, squat appear-
ance. We are terming this as electronic igni-
tion, to distinguish it from transistorized
ignition, described above. Note that this is
not quite the same thing as distributorless
ignition, in which the rotor and cap are elim-
inated and a separate coil provided for each
plug, individually triggered by the ignition
"blackbox." Bosch introduced a true distrib-
utorless system like this in 1990, with the
Motronic M3.1. BMW was the first to use
this on its in-line, 4 valve per cylinder in-line
six, and on 2.0 and 2.5 liter four cylinder
engines, as used in both 3- and 5-series cars.
Apart from eliminating the potentially
troublesome mechanical components, and
beyond the fact that electronics also respond
much faster than the old fly-weights and
vacuum diaphragm arrangement, electronic
control over spark timing meant that these
ignition systems could (at least potentially)
calculate the appropriate amount of spark
advance based on many more factors than
simply rpm and manifold vacuum. These
additional factors include the rate of change
of load and/or speed, coolant temperature,
battery voltage, and speed of starter crank-
ing, among others. Some sophisticated dis-

Motronic ignition advance (top) compared
with map of a conventional mechanical
system (bottom). Electronic control over
ignition timing, based on numerous inputs,
permits finer and much more detailed con-
trol over spark advance, maximizing per-
formance without risking detonation.
(Robert Bosch Corporation).
IgnitionAngle
IgnitionAngle
\.\\i\\\~ 'S'V~~~
63

1.Additionalprogrammemory
1
2.Analogdigitalconverter
3.Microcomputerforstandardpro-
gramanddata
4. Integratedcircuitfor enginespeed
andreference-marksignalprocess-
ing
5.Ignitionoutputstage
6. Fuelinjectionoutputstage
2
3
4
5
6
Because the Ideal ignition advance depends on mixture strength, and vice versa, optimum results can only be achieved with integrated
control over both ignition timing and fuel injection. This is what the inside of the "black-box" that does it looks like. (Robert Bosch
Corporation)
64

tributorless ignitions do, in fact, use these
inputs to tailor the spark advance, and fur-
ther accept signals from a knock sensor, to
retard the spark when detonation is detect-
ed-see the sidebar "Knock, Knock?"
Motronic Engine Management
It may already have occurred to you that
most or all of these sensors already form
parts of the D/L/LH-Jetronic EFI systems.
By'integrating the ignition and fuel injection
"black boxes," we should expect, at the very
least, to wind up with a lighter, simpler and
more compact arrangement than if each sys-
tem were to operate completely indepen-
dently. Merged systems like this are the
basis of Bosch "Motronic" engine manage-
ment. The expected packaging advantages
are realized, but there is much more to it
than that, because the ideal amount of spark
advance also depends on the air/fuel mixture
strength, and vice versa. Only when the igni-
tion and EFI electronics are enabled to talk
to each other can both sparktiming and mix-
ture strength be optimized together to
achieve the best compromise amongst
torque, driveability,economy, and emissions
under all engine operating conditions.
Engines operating at light loads and high
speeds can tolerate a lot of ignition advance
without detonating; indeed they work most
efficiently that way, as the existence of the
vacuum advance unit on traditional distribu-
tors confirms. The reason for this is that the
rate of pressure rise in the combustion
chamber after ignition depends, among
many other things, on the density of the
air/fuel charge. With the small throttle open-
ings that correspond to light load, the mass
of mixture trapped in the cylinder is small-
its density is low.If, at that same high engine
speed, the throttle is opened wider,the man-
ifold pressure will rise (that is, the vacuum
will drop), the density of the charge in the
cylinder will increase, the flame will spread
more rapidly once ignited, soless advance is
called for.
Experiments have shown that the rate of
the chemical reaction during the very earli-
est stages of combustion is fastest when the
air/fuel mixture is near stoichiometric, and
that it slows down quite distinctly with
either leaner or richer mixtures. Because
detonation is very much a time-sensitive
phenomenon, optimum spark advance thus
also depends strongly on mixture strength.
With most pump gasolines, a mixture slight-
ly richer than stoichiometric (around the
air/fuel ratio that gives maximum power)
will generally increase the tendency to deto-
nate, and so would call for less timing
advance. Paradoxically, the same engine is
likely to tolerate more advance without det-
onation if run either very rich or with mix-
tures leaner than stoichiometric.
When a three-way catalytic converter is
used, however, the mixture must be kept
stoichiometric within very close limits for
proper functioning of the converter, and this
tight control is provided by an oxygen sen-
sor (lambda sensor) feeding information
back to the EFI computer in closed-loop
control. All Motronic systems have a lamb-
da sensor, so if this ensures that the mixture
is always stoichiometric within a few tenths
of a percent, there might seem to be no point
in taking mixture strength into account in
calculatingsparktiming.This wouldbe trueif
the system were always operating in closed-
loop mode, but note that both L-Jetronic and
LH-Jetronic revert to open loop operation
during cold starts, warm-up, full throttle
operation and sometimes, transiently, during
acceleration.
Cold Start and Warm-Up
Ignition Timing
While the optimum ignition timing for an
idling engine might be several degrees
advanced from TDC, in a stone-cold engine
being cranked at very low rpm, any advance
at all may cause the piston to be driven back-
ward, possibly damaging the starter drive,
and certainly preventing the engine from
65

INPUT
OUTPUT
-
TDC
Throttle
Boost
rpm
Air temp
Knock
Motrlonic
I
con Irol
I
I
Kn<pck
con trol
I
Timing
Boost control
In early versions of Motronic, the knock sensor/control function was physically separated from the main ignition/injection ECU. The prin-
cipal remains the same.
starting. The very bottom end of the engine's
speed range-cranking and idling-thus
presented an insoluble dilemma to engine
designers in the days of mechanical distrib-
utors, because the speed was so low that the
centrifugal advance mechanism could not
respond to the comparatively slight differ-
ence in rpm between cranking speed and
idle speed.
Faced with these same conditions,
Motronic will retard the spark to approxi-
mately TDC during slow cranking, then
immediately dial in a few degrees of
advance as soon as the engine fires (which
66
the ECU "knows" because the rpm rapidly
builds, and the starter becomes disconnect-
ed). As with L- and LH-Jetronics, a much
richer than normal mixture will be supplied
to a just-fired-from-stone-cold engine; the
Motronic system goes further and provides
more spark advance, which will raise the
otherwise too-low idle speed of a cold, rich-
running engine. On the other hand, an
engine being started at a higher temperature
will be given a small amount of initial
advance during cranking, as this helps start-
ing. Motronic makes this "judgement" based
on both temperature and cranking rpm.

Idle Speed Adjustments
Although all Motronics are equipped with
some form of idle speed stabilization,
whether the thermostatically controlled aux-
iliary air bypass of the L-Jetronic or the
ECU controlled idle speed stabilizer valve
of the LH-Jetronic, these devices are some-
what slow in response. The Motronic system
continuously and almost instantly "fine
tunes" variations in idle speed away from
the ideal by slight adjustments in spark
advance-a little more advance will speed
up the idle; a little less will slow it down.
This ability to tightly control spark advance
at idle reduces the amount of mixture rich-
ness needed.
Mter startup and during the initial warm-
up phase, until the lambda sensor becomes
hot enough to provide meaningful signals to
the ECU, the system will operate open loop
for a certain length of time, according to the
temperature and time elapsed since starting.
During this time, the spark advance and fuel
injector pulse time will be gradually adjust-
ed toward the "nominal" values stored in the
ECU's memory, but always with each taking
account of the other.An added subtlety here
is that the ECU will retard the spark, relative
to the nominal value for the circumstances,
in order to raise the temperature of the
exhaust gasses and so aid a rapid warm-up
of both the lambda sensor and the catalytic
converter.
Once fully warmed up, mixture strength
for most driving is thereafter maintained at
stoichiometry by the ECU, in concert with
the lambda sensor. Ignition advance will be
constantly adjusted according to airflow
(and thus load), rpm, injected fuel quantity,
coolant temperature, air temperature, the
output of the lambda sensor,and, on engines
so equipped, signals from a knock sensor.
The ECU also takes into account how quick-
ly load and speed are changing. When the
rpm and airflow signals from the flow meter
indicate part throttle acceleration, for exam-
pIe, the spark will be retarded slightly, to
avoid the knocking that would otherwise
occur during this transient phase if the tim-
ing advance is just below the detonation
limit for the immediately previous (and
immediately following) steady-state condi-
tions. But note that sudden changes in
engine operating conditions might call for
equally rapid changes in ignition timing, and
the ECU is quite capable of that. Such
abrupt changes in spark advance, however,
would sometimes lead to a jerky response
by the engine, so the ECU, in fact, smoothes
the transition by spreading the adjustment
over a few engine cycles. At the same time,
ignition dwell- the length of time that pri-
mary current flows in the coil- is also con-
tinuously optimized.
The way all this is achieved gives some
idea of the blinding speed at which all these
electronic calculations are carried out within
the ECU. Based on the firing of the immedi-
ately previous cylinder and the rpm, the time
available until the next cylinder reaches
TDC is calculated, and the appropriate
amount of spark advance for the prevailing
conditions is looked up in the internally
stored maps. A suitable time interval for coil
saturation is computed next (with a correc-
tion for the battery voltage-low voltage
will start the process earlier), and the current
to the primary side of the coil is turned on at
a moment that anticipates its interruption an
instant later, when the ECU will open the
primary circuit, causing the spark. It is worth
bearing in mind, here, that in an eight cylin-
der engine turning 6000rpm, the interval
between two consecutive sparks will be just
0.025 seconds! As an added feature to pre-
vent overheating the coil, the primary cur-
rent is shut off if the engine is stopped with
the ignition on.
Knock Sensor Functioning
Use of knock sensing allows the basic,
open-loop spark advance map in the ECU to
be biased toward a bit too much advance.
67

IgnitionAngledegreescrankshaftbeforeTDC
...:~_:'....
-,.
'---" ,~'c-.~
>'. \ r'::"""
..,...",-__,_'-T--r---'1 r-~;~e )\leen ----
0
IgnitionAngledegreescrankshaftbeforeTDC
n./ .~-:~/---<.<...
"~~i~~i~;>,~~;;-~ ~/~
Some Motronic systems have two sets of ignition timing "maps." A typical one for premium fuel is at the top; below is one for regular
fuel. If the knock sensor still reports detonation even though the ignition is retarded as far as "premium" map says it should be, then the
system switches to the map for "regular" fuel. Only performance suffers, not the engine. (Robert Bosch Corporation)
When knock is detected, the spark is retard-
ed a little while the circuitry "listens" again.
If knock is still detected, the timing is retard-
ed a little further. If not, the advance is
cranked up a little, until knock is again
heard. Thus, the engine is always operating
on the brink of detonation, but the knocking
is always held at a point where it is just
detectable to the electronics, but inaudible to
the human ear, and perfectly safe for the
. --
,-. ---'1
.',... ---~-r t"\),,,e
.-" -__,_,-T--r
0
engme.
In some cases, two sets of internal map are
provided. One is programmed for regular
fuel, the other for premium. If the ECU
determines that the reduction of advance
needed lies well off the premium fuel map,
it switches to the other one. Thus, the owner
of a car that calls for premium fuel can buy
a tankful of the nastiest, cheapest sortof reg-
ular and suffer nothing worse than a reduc-
68

1 2
3
, , , , .
1.Permanentmagnet
2. Housing
3. Enginehousing
4. Soft-ironcore
5.Winding
6. Ringgearwithreference
point
~
Engine speed sensor-essential for the kind of precision control offered by Motronic systems. (Robert Bosch Corporation)
tion in perfonnance, resulting from the
knock sensor/ECU backing off the advance
to keep the engine from making buckets-of-
bolts noises.
Again, the speed with which all this
adjustment of spark lead happens is mind-
boggling. There is always one cylinder that
knocks first, but because the ECU "knows"
the crank angle at any instant, it "knows"
which one it is, and can retard the spark for
that cylinder alone, while dialing up more
advance for the next one!And note that even
though many other changes in spark timing
are phased in comparatively gradually by
the ECU, the onset ofknocking will be acted
on instantly.
Triggering
High precision control of ignition timing,
asjust described, demands at least equalpre-
cision in detecting the crank angle. For that
reason, Motronic systems detect crankshaft
angle directly at the crank, rather than from
a camshaft or other half speed shaft, such as
the distributor drive, where gear (or chain or
belt) "backlash" can introduce errors, both
fixed and variable. In many cases, it is the
movement of the flywheel itself that is
gauged, with a magnetic sensor that "reads"
the ring gear teeth going past. This provides
a finely detailed rpm signal- there are a lot
of teeth, and each one provides a little
"blip"-so detailed, in fact, that the ECU is
able to detect a change in speed after just a
few degrees of crank rotation.
69

1 3 5
a
2 4
a.full
b.empty
1.venttoatmosphere.
2.accumulatorhousing
3.spring
4. rubberdiaphragm
5.volumeofstoredfuel.
....
70
.-
b
The fuel accumulator that helps damp out system pressure fluctuations and maintains some residual
pressure when the engine is stopped to ease warm restarts.
To establishTDC on thenumber1 cylin-
der, a separatemagnetic sensor is used
which producesjust a single pulse per
enginerotation by reading,for example,a
single
On installations where this location is
impractical, a separate toothed wheel is pro-
vided, often at the nose of the crank. In these
cases, a single sensor is used for both rpm
and #1 TDC, the TDC signal being provid-
edby a
distinguish between TDC on the compres-
sion stroke and TDC at the end of the
exhaust stroke. This is achieved with a third
bolt head on the flywheelperimeter.
missingtoothon therotatingwheel.
In either case, it is of course necessary to
sensor that reads a timing mark on the
camshaft. Since the carn rotates at half crank
speed, this simply establishes which stroke
the engine is on; the precision timing is left
to the crank sensor.
Fuel Sub-System
It is the integration of ignition and EFI
"black boxes" that characterizes Bosch's
Motronic systems. Since we earlier
explained that the fuel delivery aspect of
these systems is essentially either L-Jetronic
or LH-Jetronic, our attention so far has been
focussed on the ignition aspects.
Nevertheless, there are some points of inter-

RPM
Fuel off
'\j
Q)
Q)
p.,
lfl
Q)
.,...,
QJ)
6000
4500
3000
1500
::t80rpm
0
Time
Another feature of Motronic systems is a built-in rev limiter. Although engine rev limiting can be achieved by interrupting the ignition, this
can cause rough running and backfires and be hard on the machinery. Cutting off fuel is smoother, and reduces emissions, too. Once the
preset rpm limit is reached, the cut-off rapidly oscillates between "fuel on" and "fuel off," with about +j- 80 rpm between the two states.
est in the fuel side of things, too.
For one thing, many later versions of
Motronic inject sequentially, rather than
using the "ganged" firing of the injectors in
D-, L- and LH-Jetronics. Rather than injec-
tors firing in pairs or all together, each cylin-
der receives its dose of fuel at exactly the
same point in the intake stroke. The exact
phasing of the start of injection, however,
varies from one family of engines to anoth-
er-the injection does not necessarily take
place only while the intake valve is open.
While it requires more, (and more rapid)
computations, and thus demands a more
complex ECU, this approach has some
potential advantages. For one thing, the
problem of port wetting, discussed in earlier
chapters, can be minimized or even elimi-
nated. That reduces the amount of accelera-
tion enrichment needed, and so improves
both economy and emissions. For another
thing, the ganged firing of earlier systems
causes both a brief, transient drop in fuel
pressure, and a large momentary electrical
load. Even though the fuel rail on D-, L- and
LH-Jetronics has an internal volume equal
to many times the volume of fuel of one
injection, and so the fuel pressure pulsation
does not drive the mixture strength out of
whack- it could be accommodated in the
.
71

72
internal "maps," anyway- it can cause dis-
agreeable noise. (Motronic systems that do
inject on the "ganged" basis fit a surge sup-
pressor-a kind of hydraulic accumulator-
at the upstream end of the fuel rail, to damp-
en these pulsations.) Reducing the size of
the electrical load "spike" reduces the peak
electrical consumption of the system and
allows some components to be made small-
er and lighter.Further, the system's response
to changes in engine speed and load can be
made more rapid- acceleration enrichment,
for example, can begin with the next cylin-
der, rather than having to wait for a full two
revolutions of the crank before fattening up
the mixture. Finally, each injector can
remain open for much longer than if all were
fired together. Because ganged injectors
open only every other revolution of the
crank, the maximum number of crank
degrees they are open is something less than
360 degrees. Individual, sequential injectors
can stay open for a bit less than 720 degrees.
That permits injectors with a smaller flow
rate to be used which, in turn, simplifies the
problem of metering very small amounts of
fuel at idle.
Injector Pulse
The nature of the pulse that opens the
injectors is also different from that in the
"fuel-only" systems. Rather than a single
"on" pulse that persists for the duration of
the injection, the injectors in LH-Motronic
systems are driven by a "stream-of-blips."
The injector valve is first opened by a com-
paratively large voltage "spike" from the
ECU, then held open by a sequence of fur-
ther on-off blips that cycle rapidly. The
injector never gets a chance to close, how-
ever-it is held open continuously. The volt-
age doesn't drop below 8V, and it will stay
openif thevoltageisabove6Y.Whileit has
been suggested that this is merely an
approach that makes the design of the elec-
tronics more convenient, another reason
may be that it reduces the total electrical
power consumed by an injector during a
cycle. Apart from a miniscule savings in
fuel- the engine doesn't have to work as
hard turning the alternator-this may also
permit smaller and lighter windings in the
injector solenoids, without the risk of over-
heating them, in the same way that dwell
control avoids overheating the ignition coil.
Note that this issue of having to limit the
"duty cycle" (the ratio of on-time to off-
time) is intensified if sequential firing is
used and long periods of time are spent with
the engine at high power and thus demand-
ing that the injectors remain open for long
periods.
Adaptive Control
A final refinement is "adaptive"control, in
which the ECU "learns" changes in the
engine's condition and responds appropri-
ately. Recall that in closed loop mode, the
ECU is continually adjusting the mixture
strength on the basis of signals received
from the lambda sensor. Thus, the tendency
of an aging engine with numerous air leaks
admitting unmetered air to run lean will be
corrected by the ECU detecting this on the
basis of the signals from the lambda sensor,
and make appropriate corrections for it. In
open-loop mode, however, such as during
cold starts, cold engine idling and full throt-
tle acceleration, the ECU reverts to its inter-
nal maps. If these maps were fixed for all
time, the engine would consistently run lean
whenever it operated in open loop. Given a
sufficiently large and subtle memory, the
ECU can "remember" that the engine
always needs a richer mixture than its maps
call for. With adaptive control, the ECU
adjusts the values in the maps, for use in
open loop mode, on the basis of the amount
of enrichment beyond the map values when
running closed loop. So much for regular
tune-ups!

KNOCK,KNOCK?
In broad tenns, an engine running on a stoichiometric mixture will produce the most power for the least fuel
when the spark is advanced to a point just short of where detonation or "knocking" occurs. Working at that opti-
mum value of spark advance, however, is fraught with dangers.
When combustion goes haywire and the entire contents of the cylinder" go off with a bang," power is lost and
fuel wasted because the violent turbulence that accompanies detonation scrubs the hot gasses against the interi-
or surfaces of the combustion chamber, so much of the heat energy winds up in the exhaust or cooling system.
.Far worse, the rapid "spike" in cylinder pressure from this explosive combustion is potentially crippling to an
engine. If knocking persists for long, piston crowns can-quite literally-have holes punched through them,
spark plugs can have their side electrodes knocked clean off the shell and/or have their porcelain bodies cracked,
rod and main bearings can be damaged, head gaskets can be eroded away.
In the days of mechanical distributors, the static setting of ignition timing had to be chosen conservatively,
because the additional advance arrived at by the combination of mechanical and vacuum advance controls was
approximate atbest, and changed with wear of the mechanical parts. (Ever installed a new set of points in an older
vehicle, had it tend to knock slightly, but then marveled that it seemed to "heal up" after a time? That's because
the rubbing block on the moveable half of the points wore down enough to retard the timing a few degrees.)
The higher precision of electronic triggering allowed engineers to work closer to the danger mark, but vari-
ability in climate, fuel quality, driving habits, and engine condition still meant that a safety margin had to be held
inhand.Whatwasneededwassomedevicethatcoulddetectthe incipientonsetofdetonation- plus,of course,
the ability to continuously and rapidly adjust the timing so that it was always at the ragged edge. The device is
the knock sensor.
While the internal working principle of knock sensors can have a variety of possible fonns, the one used by
Bosch (and many other manufacturers) depends on the piezoelectric principle. Some materials- in this case a
special ceramic-produce anelectrical voltage when they are strained, or defonned. Such devices have been used
for microphones and in inexpensive cartridges for LPrecord players.As applied to the knock sensor, a rigid, mas-
sive housing contains a lump of the piezoelectric ceramic, one face of which is attached to the housing, while the
other face is attached to a smaller weight. When the housing is shaken, the "free weight" tries to dance around
and so strains the ceramic, which accordingly produces a small electrical signal. We can arrange to shake the
housing by attaching it to the engine block.
Shaking of the outer housing, of course, occurs all the time the engine is running- notjust because the engine
is moving around on its mountings (that movement is too slow to excite any measurable signal, anyway), but
because the engine block is vibrating from the fury going on within it.The nature of the shake, however, changes
significantly when knocking occurs, so the electrical signal put out by the sensor changes too. If that signal is fed
to a device that can recognize the characteristic "sound" of knocking, then we have captured the infonnation we
need to control ignition timing so as to avoid the knock. (While Bosch categorizes its knock sensor as an
accelerometer, it is helpful, and not completely wrongful, to think of it as a microphone.)
The device that does the recognizing may be a separate electronic "blackbox," as on some early Motronics, or
can be integrated into the ECU, as on models ML3 and later. The characteristic frequencies the electronics are
looking for are in the range of 10,000-15,000 cycles per second-exactly the range offrequencies ofthe sounds
we hear as engine knock.


Preventative Maintenance
Beforeattributingsomeoperatingfaultto
the fuel injection system, be surethe remain-
der of the engine is in sound order. It is quite
pointless to start to troubleshoot the injec-
tion system if the spark plugs are years old,
the rubber intake ducting is cracked, or an
exhaust valve is burned.
Spark Plugs
As in the days of carburetors and point-
and-breaker ignition systems, the fIrst diag-
nostic test should be to remove the plugs and
examine them - the removed plugs can
reveal a great deal about engine condition.
The insulator should be a light gray-to-tan
color. An insulator that is bone-white-or
worse, blistered- indicates excessive lean-
ness, or perhaps a plug of the wrong heat
range; a blackened insulator may be the
result of a too-cold plug, or excessively rich
running, or may be a product of oil fouling,
because of worn rings or valve stems, a
plugged PCV valve, or even simply an over-
filled oil pan. To distinguish between carbon
(fuel) fouling and oil fouling, rub the plug
against the heel of your hand-oil fouling
will leave a greasy smudge; carbon fouling
will not.
Any mechanical damage to the plug- a
cracked insulator, a broken side electrode-
implies detonation, which may have dam-
aged much more than the plug. A plug that is
truly wet with gasoline implies a non-firing
cylinder that has continued to receive fuel.
Check Gap-Also, check the gap on
removed plugs. If the plugs have seen any
substantial amount of service, the gap is sure
to be larger than on a new, correctly gapped
one. This widening of the gap results from
erosion by the hot gasses within the cylinder.
An excessive plug gap can make unsustain-
able demands on the ignition system
- the
voltage required to jump the exaggerated
gap may cause the secondary (high-tension)
voltage to rise so high that the spark seeks
another path to ground, perhaps punching a
microscopic hole right through the insula-
tion on the plug or coil wires, leaving a leak
path to ground that remains even after the
plugs are replaced.
Replacing Plugs-The replacement inter-
val for spark plugs suggested by the factory
is likely to be highly optimistic; except for
platinum tipped plugs, they should be
replaced annually, as should the air and fuel
filters. Check the gap on new plugs before
installing them even if they come pre-
gapped, and take care when replacing the
fuel filter that the act of removal and
replacement does not allow dirt to enter the
system. High-tension wires should be
replaced every couple of years, likewise the
distributor cap and rotor, if applicable.
Routine Checks
Other routine service inspections that
should be taken care of before going further
are checking ignition timing and, on engines
without hydraulic lifters, the valve clear-
ances. Inspect all rubber air trunking for
cracks and other sources of air leaks.
75

76
Assuming all is in order so far, the next step
is a compression check. This will reveal
worn rings or leaking valves. Compression
that is uniformly down by even as much as
20-30psi relative to the factory figure is not
much to worry about,but variations between
cylinders of that much is cause for concern.
Gas Pains
Many fuel injection troubles can be avoid-
ed, or at least long postponed, simply by
paying attention to the quality of fuel used,
and where and when it is bought. While the
owner's manual may make clear that regular
gas of about 87 pump octane is suitable, and
while the engine may not be able to take
advantage of the higher octane (about 92) of
premium fuel, the premium fuel from most
national gasoline brands contains a more
aggressive detergent additive package than
does their regular fuel. Clogged injectors are
one of the more common causes of grief
with fuel injection systems-all systems,
notjust Bosch. Higher detergency of the fuel
helps prevent these faults. Even supplement-
ing a standard diet of regular with a tankful
of premium every few weeks helps.
Aftermarket detergent additives may also be
effective.
Running out of gas is a pain, argument
enough for following the advice implicit in
the old saw that "it costs no more to drive
around with a full tank than a near empty
one," but running most of the time with the
gauge showing 1/4 tank or less is especially
poor practice with fuel injection systems.
The larger the air space above the fuel in the
tank, the greater the amount of water that
condenses out of the air, and the greater the
susceptibility of steel and iron components
in the system to rusting. Apart from the
direct consequences of this corrosion, tiny
flakes of rust can play havoc if they get into
the system.
Note, too, that it is a good idea to keep an
eye on when your habitual gas station gets
its deliveries. The replenishment of the sta-
tion's underground storage tanks stirs up rust
and sediment in their tanks that may wind up
in yours. Better to fill up the day before or
the day after.
"No User Serviceable Parts Inside»
No matter what the results of the diagnos-
tic tests described below, bear in mind that
in most cases the only remedy for something
out of spec is component replacement. Parts
that cannot be repaired or adjusted include,
where applicable: pressure regulator; accu-
mulator; injectors; cold start injector; auxil-
iary air bypass (idle speed stabilizer); fuel
pump (except for the check valve, which is
replaceable); and all sensors.
Bear in mind, too, that without the highly
specialized equipment to which service
technicians in dealerships have access, there
is absolutely nothing you can do with any
electronic control modules; you cannot even
test them. All you can do if an electronic
controller is suspect is to systematically
eliminate all other components as potential
culprits and, as a final resort, replace the
controller.
Troubleshooting Tests
Despite the dismayingly long list of things
that cannot be done, there are nevertheless
some troubleshooting procedures that can be
helpful. These should be carried out in a log-
ical way, and with an understanding of how
the system is supposed to work and what
different components do in various circum-
stances. For example, if an engine starts
readily from cold and runs well while first
starting to warm up, but then runs progres-
sively richer as it reaches operating temper-
ature, guzzling gas and spewing black
smoke, one plausible culprit is a cold start
injector stuck open. In the same way, if the
idle speed is way too high when warm, or
too low when cold, one of the first places to
look might be the idle speed stabilizer/auxil-
iary air bypass. In general, if only one part of
the engine's operating regime is affected,

WARNING!
Gasolineis highlyflammableand potentiallyexplosive.It can be ignitedby an
electricalsparkor by contactwithhot engineparts.Useextremecarewhenwork-
ing on anyengine'sfuel system.Workonlyin a wellventilatedarea,ban smoking
oranyopenflamefromtheworkarea,andensurea fullychargedlargecapacityfIre
extinguisheris close to hand. Many fuel injectionsystem circuitsremain under
pressureevenwhenthe engineis stoppedandthefuelpumpis deactivated;before
looseninganyfuelfItting,wrap arag aroundit.
look first at components whose function is
directly related to operation in that regime.
Air Meter (vane type)
As noted, the airflow meter is not service-
able; all you can do is check for smooth
mechanical action and test the electrical out-
put of its potentiometer. Test for free,
smooth movement simply by moving the
vane with your fInger. After unplugging the
electrical connector, apply one probe of an
Ohmmeter (or multimeter set to "Ohms" or
"resistance" scale) to a clean chassis ground
and contact each terminal on the meter in
turn with the other probe. In every case, the
meter should read an open circuit (infInite
Ohms).
The "voltage-in" and "voltage-out" pins
differ from one model to another; the manu-
al for your vehicle may identify them. In
every case, however, there will be one pair
of pins that show a varying resistance as the
vane is moved. The exact numbers don't
matter much; what is important is that the
resistance should vary smoothly as the vane
is slowly deflected by hand.
Air Meter (Hot-WIre Type)
There is nothing serviceable or adjustable
in the hot-wire air mass sensor; all you can
do is confirm its functioning. If it doesn't
work, it must be replaced.
The wire in the sensor is so fIne that, with-
out ideal lighting, it is easy to mistakenly
suppose that it is broken or missing. Recall
that a "bum-off" cycle is provided, that feeds
a large amount of current to the wire to
vaporize any dirt deposits on it. The wire
glows red hot during this brief (about one
second) cycle, which makes it plainly visi-
ble.
With the engine running and the meter ori-
ented so it is possible to sight through it with
its wire harness and trunking to the throttle
body still connected (it is OK to detach the
housing and move it around, as long as you
don't damage the trunking or wiring), rev the
engine to at least 3000 rpm and shut it off.
(For safety reasons, the bum-off cycle is
cancelled if the engine has not exceeded
3000 rpm since the last time the ignition was
shut off). After three or four seconds, the
wire will glow for about one second. While
this doesn't confIrm that the meter is work-
ing correctly, it does prove the wire is OK.
There are fIve wires connected to the hot-
wire sensor.One is a ground; one is voltage-
in, one is voltage-out, and the other two are
involved only in the bum-off cycle. Which
is which depends on the specific model, and
should be specifIed in each vehicle's manu-
al. Failing that, the above test (you may
have to repeat it several times, working this
way) should identify those last two by plac-
ing the probes of a high-impedance digital
voltmeter/multimeter on pairs of terminals
(peel back the insulating boot on the con-
nector) until you fInd the pair that are "live"
and "ground" during the bum-off. DO NOT
USE AN ORDINARY ANALOG (NEE-
DLE-AND-DIAL) VOLTMETER; there is
severe risk of damage to theECU.
77

Bosch
intermittent
injection
Domestic
throttle-
body
inj ection
Typical
car buretor
Bosch
continuous
injection
system
One of the minor reasons why fuel injection is superior to carburetors is because forcing the fuel through small orifices at high pressure
does a better job of vaporizing it than sucking it through small orifices with a small pressure difference. A potential downside for servic-
ing is an increased fire risk. Many circuits contain fuel under residual pressure, even when the engine is stopped.
With one voltmeter probe grounded, the
voltage-in terminal will show battery volt-
age (nominally 12volts) when the ignition is
switched on. WITH THE IGNITION OFF,
the ground will show zero Ohms (no resis-
tance) to ground. (Never apply an
Ohmmeter to a powered circuit.) By elimi-
nation, the remaining terminal must be volt-
age-out.
The voltage between ground and the volt-
age-out terminal will typically vary from a
bit more than 2 volts with the engine idling
to a bit less than 3 volts at about 3000-
4000rpm. Again, the factory specs may be in
78
the manual for your vehicle, but the exact
numbers are less important than seeing a
smooth voltage increase pretty much in pro-
portion to engine speed.
Fuel Pressure Checks
Unless the engine has been stopped for a
very long time (hours), there is likely to be
residual pressure in the system. Before
breaking into the fuel plumbing to attach a
pressure gauge, this residual pressure must
be relieved. The simplest way to do this is to
pull the fuel pump fuse, thereby disabling it,
then run the engine until it stalls for lack of

fuel. For pressure tests, a pressure gauge
with a capacity of at least SOpsiis needed,
together with hoses and fittings to connect it.
Some engines have an extra port for con-
venient connection of a pressure gauge.
Failing that, the fuel line to the cold-start
injector can be pulled and the connection
made there. A specific figure for fuel system
pressure willbe listed in the manual for your
particular vehicle, usually about 3Spsi,
although some high powered engines may
run at about 44psi. Note, however, that this
"factory" figure is measured with the engine
stopped.
An alternative test procedure that permits
checking the functioning of both the fuel
pressure regulator and the pump is to gauge
the pressure with the engine idling. In that
case, the pressure should be somewhere in
the neighborhood of 30psi, or a bit less.
Again, this applies to most engines; high
horsepower ones that call for, say, 44psi
with the engine stopped will usually show a
bit less than 40psi when checked idling.
Recall from the previous chapter that the
fuel pressure regulator has a vacuum hose
running to the intake manifold, so manifold
vacuum can act on the diaphragm within the
regulator. This allows the regulator to main-
tain fuel pressure in the rail at some constant
amount higher than the pressure in the
intake manifold, no matter how manifold
vacuum may vary.If the vacuum hose is dis-
connected at the regulator (and plugged),
then with the engine idling the gauged pres-
sure should have risen to the "factory" fig-
ure.
High Pressure-If the system pressure is
too high, the problem is either a defective
pressure regulator or a restricted return line
from the regulator to the tank. This last can
be checked by disconnecting the return line
at the regulator and attaching a test line lead-
ing to a suitable container. If the pressure
returns to normal, the original line is
obstructed; if not, then the regulator is
defective. The pressure regulator on inter-
mittent systems-except for now somewhat
rare D-Jetronic-is not adjustable.
Low Pressure-If the pressure is too low,
on the other hand, there are numerous possi-
bilities. First there are the obvious things: Is
there fuel in the tank? Are there any visible
external leaks? Is any part of the supply line
from the tank to the fuel rail dented partly
shut? Less obviously, the tank vent may be
obstructed, forcing the pump to attempt to
"implode" the tank. This can be checked by
removing the gas cap. The fuel filter may be
clogged, as may the (usually fitted) in-tank
strainer-a kind of wire mesh "sock" that
filters out rust flakes and other large pieces
of debris.
Other possible causes for low pressure are
lowIno voltage at the pump and a defective
pressure regulator. Confirm that the pump is
running. In a reasonably quiet environment,
you should be able to hear it. If the pump is
not running, check the electrical supply to
the pump, starting with its fuse. If the fuse is
OK, check for electrical power at the pump.
A voltmeter with one probe appliedto one of
the fuel pump terminals and the other to a
good chassis ground should show battery
voltage (near 12 volts) at one pump termi-
nal, and zero at the other. (You will have to
fold the rubber boot around the connector
out of the way to gain access to the electri-
cal terminals.) Low voltage at the pump is
likely the result of corroded terminals or a
bad ground. Check the pump ground.
Pump Does Not Run-If there is ade-
quate power to the pump but it does not run,
the pump is defective and will have to be
replaced. If the pump seems to be in order,
pinch shut the return line from the pressure
regulator to the tank. If the pressure rises to
standard values, the regulator is defective; if
not, and the alternative faults listed above
are excluded, it is likely the pump after all.
Residual Pressure-Recall from the sys-
tem description in Chapter 3 that the pump
on intermittent systems is equipped with a
check valve that keeps the fuel lines full and
79

80
pressurized even when the engine is
stopped. This permits quicker restarts, and
helps to prevent vapor lock. With the pres-
sure gauge connected as described above,
run the engine briefly, then shut it off (or
energize the fuel pump with the engine
stopped). The pressure should not drop
below about 14 psi for at least 20 minutes
after shut-down. A loss of residual pressure
may be caused by an external leak, one or
more leaking injectors, a defective pressure
regulator, or the fuel pump check valve.
To check both these last two, repressurize
the system and, immediately after shutting
down the engine (or disabling the pump),
pinch shut the supply line from the pump to
the regulator. IT the residual pressure now
holds, the regulator is defective; if not, the
pump check valve is leaking.
ITall this fails to stem the drop in residual
pressure, about the only remaining candi-
dates are one or more defective injectors,
and the cold start valve.
Injector Leakage, Flow,Pattern
With system pressure relieved, remove the
cold start injector (cold start valve), but
leave its fuel supply connected. Place the
injector in a suitable container and repres-
surize the system; the injector should not
seep or drip fuel. ITit does, it is defective.
Remove the injectors and temporarily
plug the holes they came out of. Set each
injector into the mouth of a graduated ves-
sel.A reasonable degree of accuracy is need-
ed here, so graduated cylinders (available at
any laboratory supply outfit, or ask your
druggist) are preferable to domestic measur-
ing cups, etc. It should be pretty obvious that
plastic vessels are preferable to glass ones!
For safety's sake, disable the primary igni-
tion circuit by disconnecting the connection
from the battery to the coil. Now run the
pump; no fuel should flow from the injec-
tors. Look also for seepage around the
seams in the injector bodies.
Next, remove the spark plugs and crank
the engine for about one minute, allowing
the injectors to discharge into the graduated
cylinders. The amount of fuel discharged by
each injector should be the same, within 10
percent or less. Also, observe the spray pat-
tern from each. It should be cone shaped and
symmetrical. Partial clogging may result in
a spray pattern that is lopsided, or a dis-
charge that is hardly atomized at all- more
like a stream than a spray-or may simply
reduce the rate of delivery.A slight degree of
asymmetry in the spray pattern is accept-
able, as long as the delivery volumes match,
but pronounced lopsidedness or a stream
rather than a spray requires that the defective
injector(s) be replaced.
Basic Mixture Strength/CO Adjustment
After about 1987, LH-Jetronic and
Motronic systems make no provision for
adjusting the mixture strength/exhaust CO
level- none is needed. On earlier L-models,
those having a moving vane air meter, the
basic mixture strength can be adjusted by
turning a screw. This screw is accessible
through a small hole on the top of the air
meter housing, usually closed-off with an
"anti-tampering" plug. After the anti-tam-
pering plug is pried out, turning this screw
clockwise richens the mixture; counter-
clockwise leans it. On those LH-Jetronics
that have provision for adjustment, the
adjuster is located on the side of the air
meter, again under an anti-tampering plug
about 7/16" diameter. Note that while the
adjustment is always carried out at idle, its
effect is felt throughout the engine's operat-
ing envelope.
Note, too, that on systems with a lambda
sensor, the lambda sensor/electronic control
will attempt to bring the mixture back to the
stoichiometric value no matter what you do
with the COlbasic mixture adjustment. The
fix is simple-before carrying out the
adjustment, disconnect the lambda sensor,
obliging the electronic control to operate
open loop.

Engine exhalist
before convertor
NO
X
./'
""-
""-/
/""-
/
/
/
/
I
I
/
/
""-
""-
""
""- HC
""-
""
'----
""-
"-
"
\
'-.
Three-way catalytic conver-
tors are essential to meet
current emissions limits. But
convertors can only do their
jOb if the air:fuel mixture fed
to the engine is held very
close to stoichiometry-the
chemically correct ratio. And
to achieve that, a lambda
(oxygen) sensor is essential.
Its electrical output varies
very strongly right around the
point of stoichiometry.
I
0.90
13.2
0.95
14.0
Lamb da
control
limits
HC
----
1.00
14.7
1.05
15.5
1.10
16.2
Tailpipe exhaust
after three-way convertor
NOx
.........
'-
A
A/F ratio
0.90
13.2
0.95
14.0
1.00
14.7
1.05
15.5
--
1.10
16.2
A
A/F ratio
81

1000
>-
S
+J
+J
0
H
0
UJ
Q)
UJ
800
600
400
200
--
-----
0.98 0.99
--
--
--
\"
1.00 1.01
- New sensor
--- Aged sensor
\
\ I
\
\
\
\
\
\
\
\
"-
" '
"--
1.02
82
Air-fuel
Most folks don't have a CO meter, but many have a multi-meter. It is tempting to gauge exhaust CO on
the basis of the output of a lambda (oxygen) sensor, but beware that the sensor's output sags gradually
with age, so simply aiming for about 500 millivolts may not do the trick. The shape of the curve is reli-
able, however, so by adjusting the mixture both rich and lean, you can establish the upper and lower lim-
its of the sensor's output range. Aim for the middle.
An exhaust gas analyzer (CO meter) is
almost essential to perform this adjustment.
Before you start, however, set the idle speed
using the idle air bypass screw. Note, too,
that the CO meter has to "read" the exhaust
gas upstream of the catalytic converter-
remember, the converter is doing its best to
oxidize the CO to CO2' There is usually a
port or pipe or fitting on or near the exhaust
manifold for this purpose.
With the engine fully warm and an appro-
priate idle speed set, adjust the mixture until
the meter reports a CO value corresponding
to the figure on the EPA placard in the
engine compartment. If the placard is miss-
ing, aim for around 0.6 percent. Without a
ratio
CO meter, about all you can do is adjust for
the leanest setting that still provides a
smooth idle, then turn the adjuster 1/4 turn
clockwise (richer).
If a CO meter is available, then on lamb-
da-equipped engines both correct mixture
strength and correct functioning ofthe lamb-
da sensor and the electronic control is
absolutely confirmed if the CO reading is
the same with the lambda sensor connected
(closed loop) and disconnected (open loop).
Auxiliary AirValve
L-Jetronics and early LH-Jetronics use an
auxiliary air valve to provide the extra air a
cold engine needs to maintain an idle speed
(Lambda)

high enough that the engine will not stall.As
described in Chapter 3, this is simply a small
rotary disc valve that allows air to bleed.
around the nearly closed throttle (it is some-
times called the "auxiliary air bypass"). The
position of the disc is governed by a bi-
metallic coil. When the coil is warm, the
valve is completely closed; when very cold,
it is fully open, with a smooth and gradual
transition between the two as the engine
warms up. In very cold weather the auxiliary
air bypass valve can take eight or ten min-
utes to move from fully open to fully closed.
The valve is not serviceable, but its condi-
tion can be initially diagnosed by symptom:
An idle that is appropriate when cold but
excessively high when warm points to this
valve being stuck partly or fully open.
Conversely, if the warm idle seems right but
the engine requires some throttle opening to
avoid stalling when cold, then the valve may
be stuck closed.
If the valve is suspect, check, first, by
pinching shut the connecting hose. On a
cold engine, this should drop the idle speed;
on a hot one it should make no difference. If
the valve fails this test, sight through the
valve. Because the valve is powered as long
as the ignition is on, the heating element
should completely close the valve within ten
minutes. Ensure that 12 volts is getting to
the valve, allow time for it to warm up, then
look through to confirm the valve is closed.
To confirm the valve is opening when cold,
pop it into a freezer for ten minutes and
again sight through it- there should be a
clear, round passageway through it.
Idle Speed Regulator
Later LH-Jetronics and all subsequent
Bosch intermittent injection systems modu-
late the auxiliary idle air bypass in a differ-
ent way. It remains in principle a valve that
bypasses more or less air around the throttle
plates, and its effect is most significant dur-
ing warm up. However, because its more
sophisticated control enables it to maintain
an appropriate idle speed, irrespective of
temperature or engine age and condition, it
is renamed an "idle speed regulator," or
sometimes "rotary idle actuator."
In this device, the moveable valve that
varies the size of the air opening is driven by
a component that looks like an electric
motor. Indeed, in construction it essentially
is, but in action it never turns more than 90
degrees, its electrical components receiving
pulses from the ECD that cause it to "dither"
back and forth slightly around an average
position that gives the idle speed pro-
grammed into the ECD.
Analogous to the function of the electro-
magnetic injectors themselves, the position
of the valve, and thus the amount of air that
passes, depends on the ratio of on-time to
off-time- its "duty cycle," in other words. A
long duty cycle-more on-time than off-
drives the valve further open; a shorter duty
cycle closes it further.This duty cycle can be
measured with a dwell meter, set on the
four-cylinder scale.
The exact values under various circum-
stances vary considerably among different
vehicles, so check your vehicle's specs in its
manual. As a general guide, the duty cycle
with a warm, idling engine will read some-
where around 30 degrees on the dwell meter.
Adding a fair-sized load, such as by turning
on an electric rear window defroster, should
have little effect on the idle speed, but the
duty cycle should increase somewhat.
To simulate cold start operation, discon-
nect the engine temperature sensor. Disable
the fuel pump (pull the fuse), and crank the
starter. Dwell should be dramatically
increased; expect about twice the idling fig-
ure. A defective idle speed regulator cannot
be repaired; it must be replaced.
83


here are a great many reasons why
auto manufacturers may have been
T
reluctant to wholeheartedly em-
brace intermittent EFI after it first
appeared-in D-Jetronic form-in 1967/68.
One of them may have been cost. While it
is impossible to know what it costs Bosch
to manufacture an intermittent EFI system,
it is possible to gain some general indica-
tion of the OEM cost of the system to auto
manufacturers. As noted on Chapter 3, the
D-Jetronic intermittent EFI system first
appeared as standard equipment on certain
models of the Volkswagen type 3 1600.
Soon after, however, the system became
available as an option on some other models
at a cost of $250-$300. Considering that a
1968 VW 1600 was priced at less than
$2,500, this is a rather hefty premium.
Another reason may have been simply that
it was an essentially brand-new and
unproven technology. Although some auto
executives and engineers surely were umea-
sonably conservative (and someremain so!),
it is not necessary to assume they were all a
hidebound bunch of stuffed shirts in order to
understand why they might be reluctant to
gamble with their own reputation in order to
cement that of Bosch. The "mere" task of
training thousands of mechanics at dealer-
ships around the world in a new and myste-
rious technology is a daunting prospect in
itself, and an expensive one. (A colleague
experienced in such matters estimates that
the cost of merely translating a 100-page
service manual from one language to one
other could amount to $30,000, in today's
dollars, and VW, for example, deals world-
wide in more than 50 languages!)
K-Jetronic
Whatever the reason for reluctance, there
was evidently motivation in some quarters
to find an alternative to the carburetor. . .
and one that didn't have dozens of wires
coming out of it. Thus, despite the fact that
by eight years after its introduction the
Jetronic intermittent EFI system was well
developed and widely admired, Bosch intro-
duced a purely mechanical gasoline injec-
tion system, in 1973.First used on the 1973
Porsche 9UT, this "K-Jetronic" gained a
significant following, and wound up on
some vehicles such as the 6.9 liter Mercedes
Benz, where the cost of the alternative sys-
tem was, if not irrelevant, surely not the
overriding consideration.
Basic System Operation & Components
The "K" in K-Jetronic stands for kon-
tinuierlich, the German word for continu-
ous. This sets out the first obvious difference
between K-Jetronic and the systems we
have been describing so far: the injectors on
the K-system spraycontinuously, rather than
intermittently. The quantity of fuel delivered
per unit of time thus depends solely on the
rate of fuel delivery to the injectors.
The regulation of fuel delivery to the
injectors takes place in the mixture control
unit, which comprises two parts: an air
meter and a fuel distributor.The general pur-
85

Reduced cost could not have been a major reason that Mercedes Benz chose a K-Jetronic system for their 6.9 liter (425 cu in) V8! This
installation used the comparatively rare downdraft air meter; most K-systems have an updraft meter. (Daimler-Chrysler Archive)
86
pose of the air meter should be obvious: to
provide a suitable air/fuel ratio, the rate of
fuel delivery appropriate for the prevailing
conditions depends on the rate of airflow, so
it is necessary to measure that airflow. The
output from the air meter, in turn, acts on the
fuel distributor to modify the amount of fuel
fed to the injectors. All operations are pure-
ly mechanical.
Air Meter-Although the physical
arrangements are different, the air meter-
ing on K systems resembles that of the
L-Jetronic in that they use a moveable vane
or flap within a housing through which all
the engine's intake air is drawn. The flap
amounts to a circular plate on the end of a
lever and is positioned across a conical
opening-like a funnel- at the entrance to
the housing. According to the rate of airflow
through the funnel, the flap is deflected to a
greater or lesser degree. so the position of
the plate is a measure of the airflow.
The weight of the plate and the lever is
balanced by either a counterweight or, on

Components of the K-Jetronic system. (Robert Bosch Corporation)
some later versions, a light spring, so very
little force is required to lift the plate. As
increasing airflow raises the plate, it takes
up a new position within the funnel, so the
size of the gap around the perimeter of the
plate- the space through which the intake
airflows-depends on the details of the
multi-angled taper of the walls of the funnel.
(The "updraft" configuration just described
is most common, but some K-Jetronics, gen-
erally those used on V6 and V8 engines,
have the metering apparatus upside down, in
which case the plate is pushed downward by
the air.)
In the design of the K-Jetronic, the quanti-
ty of fuel injected is a direct, one-to-one
function of the travel of the plate-a dou-
bling of its movement from the rest (closed)
position will double the rate of fuel flow. If
the funnel had a simple, constant angle
taper, the quantity of fuel delivered would
also be directly proportional to the rate of
airflow,and the mixture strength would thus
be the same at all rates of airflow. We have
already seen, however, that this is not appro-
priate for all circumstances. Accordingly,
the funnel is shaped with multiple tapers so
that the relationship between the position of
the flap and the airflow space around it is
nonlinear. Usually, this means that the fun-
87

a.Sensorplatein zeroposition
b.Sensorplateinoperatingposi-
tion
1.Airfunnel
2.Sensorplate
3.Reliefcross-section
4.Idlemixtureadjustingscrew
5.Pivot
6.lever
7.leafspring
1
2 3 4 5
a
7 6
b
Updraft airflow sensor. (Robert Bosch Corporation)
Increasing airflow "floats"
the sensor flap upward (on
updraft systems), toward
the larger end of the intake
funnel. This opens up the
gap between the sensor
and the funnel.
88
nel tapers out slowly at fIrst, then grows
steeper, then the angle becomes more shal-
low again.
The effect of this is that a small change in
airflow at the low flow rates encountered at
idle (and just off idle) requires a compara-
tively large movement of the vane. Because
the rate of fuel flow depends directly on the
vane position, this provides the slight
enrichment needed for idling. As the rate of
airflow speeds up to a point that corresponds
to normal, light load driving, the vane
moves into the wider angled portion of the
funnel. Here the same amount of travel of
the vane will give a more rapid increase in
airflow area, so the vane moves less for a
given increase in airflow, and the mixture is
accordingly leaned out slightly. At maxi-
mum flow rates, the vane is pulled into the
mouth of the tunnel where the taper dimin-

The height (h) of sensor
plate lift needed to obtain
a certain flow area (g)
depends on the rate of
taper of the funnel.
g
A funnel with multiple tapers
allows a comparatively large
amount of sensor plate lift
around idle, which provides a
1
2
slight idle enrichment, and a
similar richening effect at
maximum flow rate, yet with
a taper in between the two
that gives more rapid vane lift
for a given airflow increase-
and so a slight leaning-
under light load, medium
speed operation.
ishes again, so the increase in flow area for
a given travel of the vane will be less, forc-
ing the vane to move further to provide
enough flow area, and so richening the mix-
ture for large loads and high speeds.
Acceleration Enrichment-As on
L-Jetronic systems, acceleration
en r ich men tis achieved automatically
by "overswing" of the metering vane.A sud-
den increase in airflow as occurs when the
driver rapidly opens the throttle will cause
3
the metering vane to quickly lift upward,
and assume some new position. The inertia
of the vane and lever assembly, however,
assures that it will initially "overshoot" that
final position. Because the rate of fuel deliv-
ery depends on the position of the vane,
there will be a momentary enrichment to
meet the needs of the accelerating engine.
To prevent damage tothe metering vane in
the event of a backfire, "wrong way" airflow
is allowed to push the vane past its rest
89

7
1.Intakeair
2.(antralpressure
3.Fuelinlet
4.Meteredquantityoffuel
5.(ontrolplunger
Within
the air meter, the sensor plate pushes upward on the control plunger through an intermediate lever. Plunger movement is always
upward for more fuel, so on downdraft sensors the pivots of the intermediate lever are reversed. (Robert Bosch Corporation)
(engine stopped) position, to a widening in
the funnel that provides enough flow area to
vent the backfire without hann. The final
limit of travel in this backwards direction is
established when the metering vane contacts
a rubber bumper.
Clearly,the shape of the funnel determines
the variation in mixture strength under dif-
ferent operating conditions. Because of the
different breathing characteristics of differ-
ent engines, the exact contours of the funnel
vary from one installation to another.
Indeed, the profile of the funnel is the
means by which the design engineers tailor
90
a K-Jetronic system for any particular instal-
lation. To learn just how the movement of
the vane affectsthe fuel flow rate we have to
look inside the fuel distributor.
Fuel Distributor-The regulation of fuel
quantity takes place in the fuel distributor.
The key component here is the control
plunger, which slides in a bore within the
cast iron housing of the fuel distributor.The
bottom of this plunger contacts the metering
vane lever, and is pushed upward by the
lever in proportion to the extent the air
metering vane is deflected by the intake air-
flow. (The control plunger movement is
6.Barrelw/meteringslits
7.Fueldistributor

a
b
c
1
2
3
4
... 5
.....
Barrelwith metering slits and control plunger (a) engine stopped (b) part throttle (c) fullthrottle. (1) control pressure; (2) control plunger;
(3) metering slit in barrel; (4) "control" edge of plunger; (5) fuel in from main pump; (6) barrel.
always upward for more fuel, no matter
whether the air meter is an updraft or down-
draft type. On downdraft versions, the ful-
crum for the air vane lever is moved to the
opposite side of the plunger to reverse the
internal action.)
The plunger looks a bit like the moveable
part of a "spool valve," such as you would
find in an automatic transmission- it is
dumbbell-shaped, with a thin section in the
middle and fat ends, with sharp shoulders at
the transitions. The bore that the plunger
slides in is lined with a precision-machined
sleeve (Bosch terms this sleeve the barrel)
that has a number of ports cut through the
upper part of its wall, in the form of very
narrow (about 0.008 inch) vertical slits.
With the plunger at the bottom limit of its
travel, corresponding to zero airflow- and
thus engine stopped-the "fat" upper por-
tion of the plunger completely blocks these
ports. As the airflow vane lever pushes the
plunger upward, the control edge of the
plunger- the sharp shoulder at the meeting
of the large and small diameters-progres-
sively uncovers an ever greater length of
........-
6
The position of the control plunger relative to the extremely narrow (about 0.008
in) slits in the metering barrel controls the rate of fuel flow in the K-Jetronic sys-
tem. (Robert Bosch Corporation)
these slits. With the plunger pushed all the
way up, corresponding to maximum lift of
the metering vane and thus full power oper-
ation, the metering slits are fully exposed.
Fuel Flow-Fuel enters the fuel distribu-
tor through a set of ports located so they are
always exposed by the reduced diameter
central section of the plunger. Raising the
91

to control-pressure
regulator
to fuel
injector
t
1.
differential-pressure
con trol
pressure
valve
flow
restrictor
fuel in D
from pump UJ .
system
pressure
Differential-pressure valves-one for each injector-maintain a constant pressure drop across the metering slits, even as the slit area
changes because of control plunger movement. The thin metal diaphragm separating the upper and lower halves of each valve "bulges"
in response to changes in the pressure difference between supply-side and delivery-side, tending to block or open up the open end of the
nearby tube feeding the injector. This does NOTvary fuel quantity; it just maintains a constant pressure drop.
92
plungerthusallowsfuelto flowoutthrough
themeteringslitsand on to the injectors,in
a quantitythat is proportionalto the height
oftheplunger.(Insomerespects,thisvague-
lyresemblesthefuelmeteringarrangements
oftheRochestercontinuousPImentionedin
Chapter 2, but note that fuel escaping
through the Rochester's spill ports is
returnedto the tank; it is the remainderof
the pump outputthat goes to the injectors,
oppositeto theK-Jetronic'ssystem.)
At fIrst glance it might seem that this
arrangementis all that is neededto provide
accurate fuel metering- the area of slit
exposedis linearlyproportionalto control
plungerlift,whichislinearlyproportionalto
meteringvanelift,which,in turn,is propor-
tionalto airflowrate,with mixturestrength
corrections for different operating regimes
provided by the varying taper of the air
intake funnel. Alas, it is not that simple.
Differential Pressure Valves-Fuel pass-
ing through the metering slits is propelled by
the pressure difference between the supply
side-below the control edge of the
plunger-and the delivery side, outboard of
the slits. For a given exposed area of slit, the
fuel flow rate will be proportional to this
pressure difference. At the same time, for a
given pressure difference, the fuel flow rate
will be proportional to the exposed slit area.
The awkward complication is that, with-
out some other mechanism to perform a cor-
rection, the pressure difference across the
slits varies according to how far open the
slits are! If only a small length of slit is

exposed, there will be a large pressure dif-
ference between supply and delivery sides; a
fully open slit will experience a lower pres-
sure difference. Thus, while there is a one-
to-one relationship between vane movement
and plunger lift, and between plunger lift
and exposed slit area, there will not be a
one-to-one relationship between exposed
slit area and fuel flow rate. The greater the
exposed slit area, the less the pressure dif-
ference, so while an increase in slit area will
flow more fuel simply because the hole is
bigger, the increase will be greater than pro-
portional because there is now less pressure
difference between the inside and the out-
side of the barrel to resist the flow, so the
mixture strength will tend to become richer
with every increase in airflow through the
meter. To correct for this nonlinearity, the
fuel distributor also contains a number of
differential pressure valves, whose function
is to maintain a constant pressure drop
across the slits, no matter what the rate of
fuel flow through them.
Valve Construction-Each differential
pressure valve comprises two chambers-
an upper and a lower-separated by a thin,
flexible metal diaphragm, backed by a
spring. There is one valve for each injector,
and thus one for each engine cylinder. The
upper chamber of each valve communicates
with one slit in the barrel (there is one barrel
slit for each injector), while each lower
chamber is connected to the annular space
surrounding the slim central part of the
plunger and thus is exposed to the same,
constant supply-side fuel pressure. Fuel
emerging from each slit flows through the
upper chamber of its dedicated differential
pressure valve on its way to the injector.
The outlet from the upper chamber of each
differential pressure valve is located just
above the diaphragm separating the two
halves of the valve, so upward deflection of
the diaphragm tends to restrict the outflow,
while downward deflection provides a
greater passage area. It is important to rec-
ognize that this apparent "throttling" of the
flow through the valve does not affect the
quantity of fuel delivered- that is estab-
lished by the exposed area of the metering
slits. All that the movement of the
diaphragm does is to maintain a constant
pressure drop across the metering slit it
serves. Fuel flows out from each differential
pressure valve to the injector associated with
it at system supply pressure minus, typical-
ly, about 1.5psi, the difference being a result
of the force of the spring acting on the valve
diaphragm.
Control Pressure and Its Regulation
In reading the description of the air meter,
above, it may have occurred to you that
there is a component missing. Without a
spring, or some other mechanism to return it
to its rest position, even the smallest rate of
airflow would immediately drive the meter-
ing vane to the limit of its travel, and it
would stay there, with the control plunger
shoved fully up into the maximum fuel flow
position. The force that tends to drive the
plunger- and thus the metering vane
- back
down is not a spring, but rather the closely
regulated pressure of fuel acting on the top
of the plunger.
This pressure is neither the full system
supply pressure, nor the very slightly lower
pressure prevailing in the upper chambers of
the differential pressure valves, but rather a
still lower pressure that Bosch terms the
control pressure. This control pressure act-
ing on the plunger top produces a downward
force that counteracts two upward acting
forces-a minor one is atmospheric pressure
acting on the exposed lower end of the
plunger; the major one is the force on the
plunger exerted by the metering vane, via its
lever.
The position of the plunger in its barrel is
thus the result of a sort of hydraulic balanc-
ing act between the force of the incoming air
acting on the metering vane and the control
pressure acting on the plunger. An increase
93

a.Withenginecold
b.Withengineat operatingtemperature
1.Valvediaphragm
2.Return
3. (ontrol pressurefrommixturecontrolunit
4.Valvespring
5. Bi-metalspring
6. Electricalheating
a
6
b
5 4
1
The control pressure regulator, previously termed the "warm-up" regulator (a) with the engine cold (b) with the engine warm. (Robert
Bosch Corporation)
in the control pressure will increase the force
acting on the top of the plunger, which
opposes movement of the air metering vane.
The vane will not move as far as it otherwise
might, the control plunger will not rise as
high, and so less of the metering slits will be
uncovered. Conversely, a reduction in con-
trol pressure will allow the vane and plunger
to rise higher, uncovering more of the slits.
Thus, a higher control pressure will lean the
mixture; a lower one will richen it.
Regulator-The control pressure, in turn,
is regulated by the control pressure regulator
(a reasonable name!). The regulator main-
tains a constant pressure downstream with a
spring loaded valve that opens at the set
pressure and allows fuel to recirculate back
to the tank. It should be clear from the above
description that, in a given installation, the
air/fuel ratio depends entirely on the control
pressure. Use is made of this fact for warm-
up enrichment,indeedthe originalnamefor
94

the control pressure regulator was wann up
regulator (WUR).
The control pressure/wann up regulator is
supplied with fuel from the fuel distributor;
a second fuel line leads from the regulator
back to the tank.Within the regulator, a flex-
ible metal diaphragm is held very close to
the port leading to the return line by a pair of
springs, one a coil, the other a leaf spring. If
the control pressure tends to drop for any
reason, the force of the springs forces the
diaphragm even closer to the return port,
obstructing the flow and so raising the pres-
sure again. Similarly, if the control pressure
attempts to rise, the diaphragm will bulge
away from the return port allowing more
flow and thus dropping the pressure.
To achieve the enrichment needed for
wann up, the leaf spring is made as a
bimetallic strip. When cold, it bends down-
ward, which opposes the coil spring and so
allows the diaphragm to move further from
the return port. That allows more fuel to
flow back tothe tank, thus dropping the con-
trol pressure. At Montana-in-February tem-
peratures, a typical control pressure might
be as low as 7-8 psi; on a fully wann engine,
the control pressure will be about 50-55psi.
The WUR is invariably mounted on the
engine block, or somewhere else that runs at
engine temperature, so the effect is sup-
pressed when the engine is wann.
With an engine started from stone cold,
the bimetallic leaf would gradually straight-
en out again as the engine wanns up, which
would raise the control pressure and so lean
the mixture back to the standard operating
air/fuel ratio. Trouble is, this would take too
long-maybe ten minutes or more-and the
engine would run excessively rich during
the later stages of wann up. To avoid this,
the bimetallic leaf has a heating coil wound
around it, very much like the thermo-time
switch that runs the cold start injector on the
L-Jetronic, as described in Chapter 3. This
heater is powered every time the ignition
switch is turned on; after just a couple of
minutes, even in freezing temperatures, it
will have bent so as to return the leaf to its
basic position, and so restore the control
pressure to the basic setting.
On some versions of K-Jetronic, the con-
trol pressure regulator is given the further
function of modulating control pressure
according to engine load, increasing mixture
strength under conditions of low
vacuumlhigh pressure in the intake mani-
fold. This additional function justified the
name of the device being changed from
"warm up regulator" to "control pressure
regulator." This modified form of control
pressure regulator is most often found on
turbocharged engines, but some normally
aspirated models use it, too.
This later, wider purpose control pressure
regulator can be recognized from its two-
piece construction, contrasted with the one-
piece WUR. The extra section contains a
second diaphragm within a separate sealed
chamber. One side of the diaphragm is vent-
ed to the atmosphere, while the other side
faces the "original" part of the control pres-
sure regulator, which is connected by a vac-
uum hose to the manifold. That second
diaphragm serves to support a second coil
spring nested within the main coil, like
"dual" valve springs. With high manifold
vacuum, corresponding to ordinary light
loads, the manifold vacuum pulls the
diaphragm to the "basic"position.
When manifold vacuum drops to near
atmospheric pressure, as during full throttle
running (or when turbo boost drives mani-
fold pressure above atmospheric), the
diaphragm is pushed down to the high-load
position. Because the supplementary coil
spring is supported by the diaphragm, it no
longer contributes to shoving on the other,
"original" diaphragm that restricts return
flow to the tank, so the return flow increas-
es. Accordingly, the control pressure drops,
the control plunger in the fuel distributor is
allowed to rise further from the force
applied by the metering vane, more slit area
95