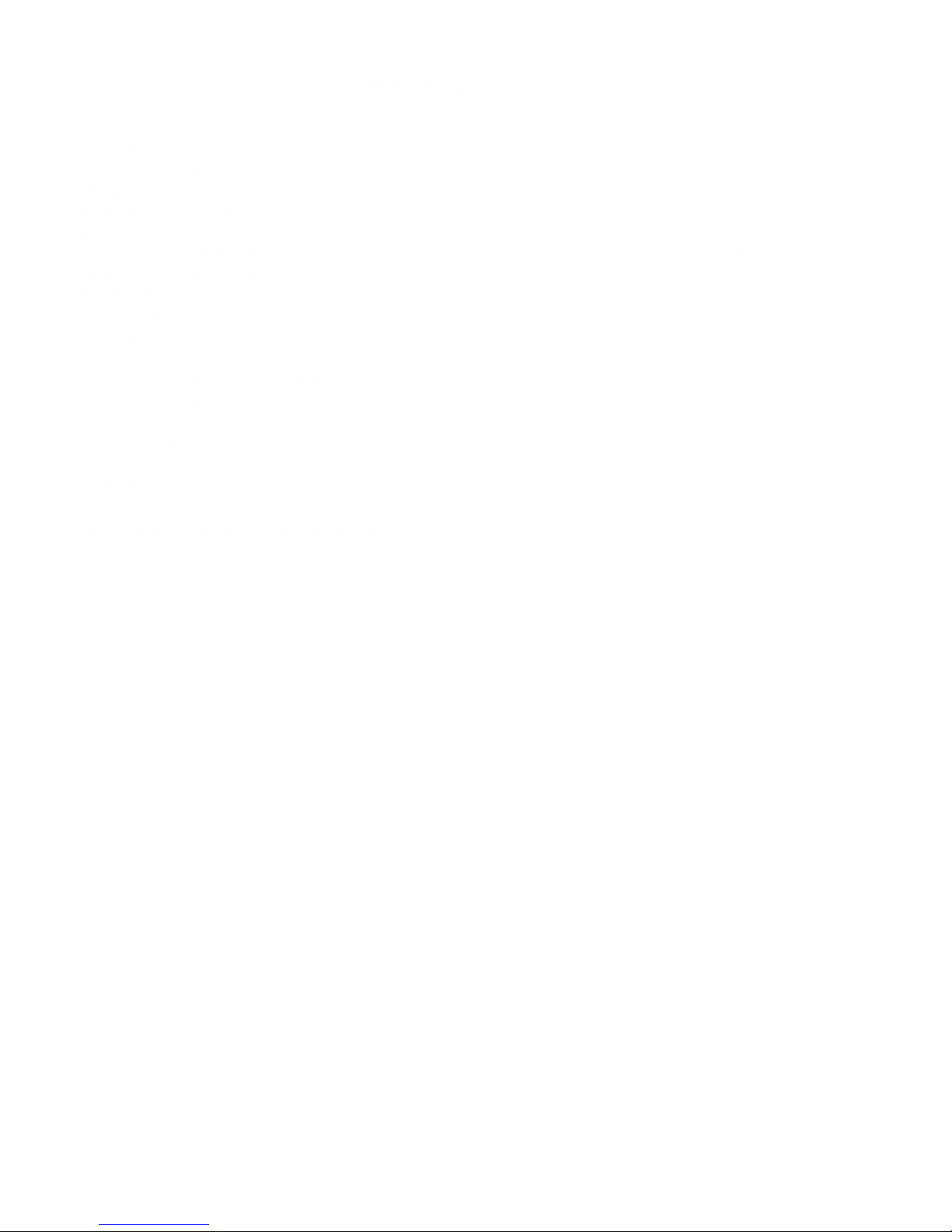
CONTENTS
Page
SPECIFICATIONS
3
IMPORTANT
SERVICE SAFETY
PRECAUTIONS 4
THEORY
OF
OPERATION 6
DISASSEMBLY INSTRUCTIONS
12
BLOCK
DIAGRAM 13
ALIGNMENT
INSTRUCTIONS
14
TROUBLESHOOTING
GUIDE
18
P.C. BOARD (Top and Bottom Views)
CRT Socket PCB
22
LED PCB
23
Main
PCB
23
WIRING
DIAGRAM
AND
PARTS
LOCATION
27
CABINET EXPLODED
VIEW/PARTS
LIST
1.
Cabinet
Exploded View
28
2.
Electrical
Parts List
29
3. Cabinet
Parts
List
39
SCHEMATIC
DIAGRAM
41
WAVEFORMS
44
SEMICONDUCTOR
LEAD
IDENTIFICATION
44
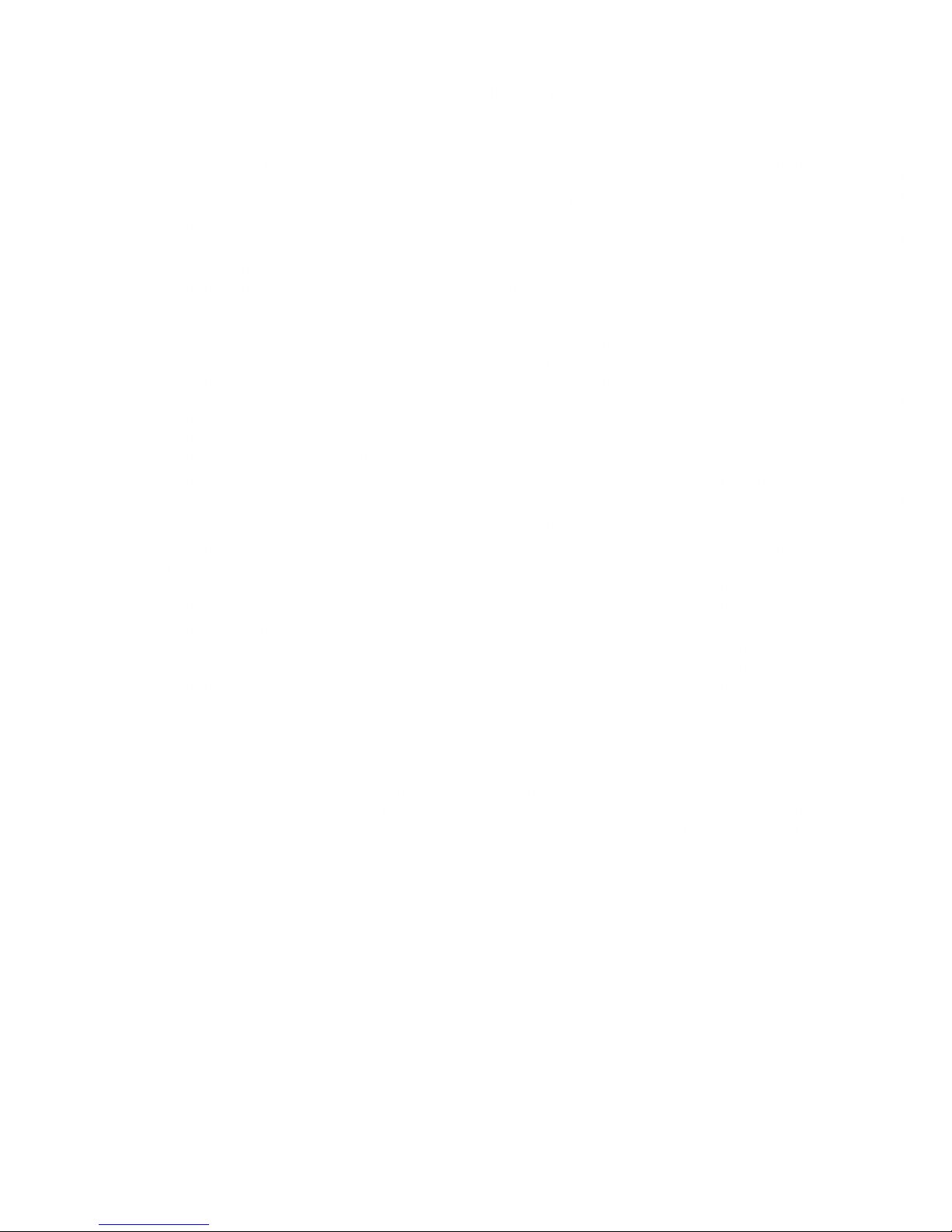
SPECIFICATIONS
Description
Nominal
Limit
1. Power input
AC 120V, 60Hz
2. AC input current 0.75A
+
10%
-30%
3. Input signal
a)
RGB Video RGB
separate
T.T.L.
Level, positive white
2.4
-
5.0Vp-p
~^"~
(default)
b)
Synchronous
"
"
T.T.L.
level,
positive going
(default)
c)
Intensity
T.T.L.
level, positive
going
(default)
4.
Resolution
a)
Horizontal
640 dots
b) Vertical
(non-interlaced)
225 lines
6.
Brightness
30
fl.
min.
(at
intensity
white)
8.
Display color
1
5
colors
9. High
voltage
23 kV/O^A
27.5 kV
maxJOfJK
10. Picture
linearity
a) Horizontal
10%
max.
b) Vertical
10%
max.
11.
Synchronous (Pull in
range)
a)
Horizontal
15.701 kHz
:i>
b)
Vertical
60 Hz
>
12.
Dot
Pitch
0.64 mm
NOTE:
Nominal
specs represent the
design
specs;
all units
should be
able
to
approximate these
—
some
will exceed
and
some
may drop
slightly
below these
specs. Limit
specs
represent the
absolute
worst condition
which still
might
be considered
acceptable; in
no case
should
a
unit
perform
to
less than within any
limit spec.
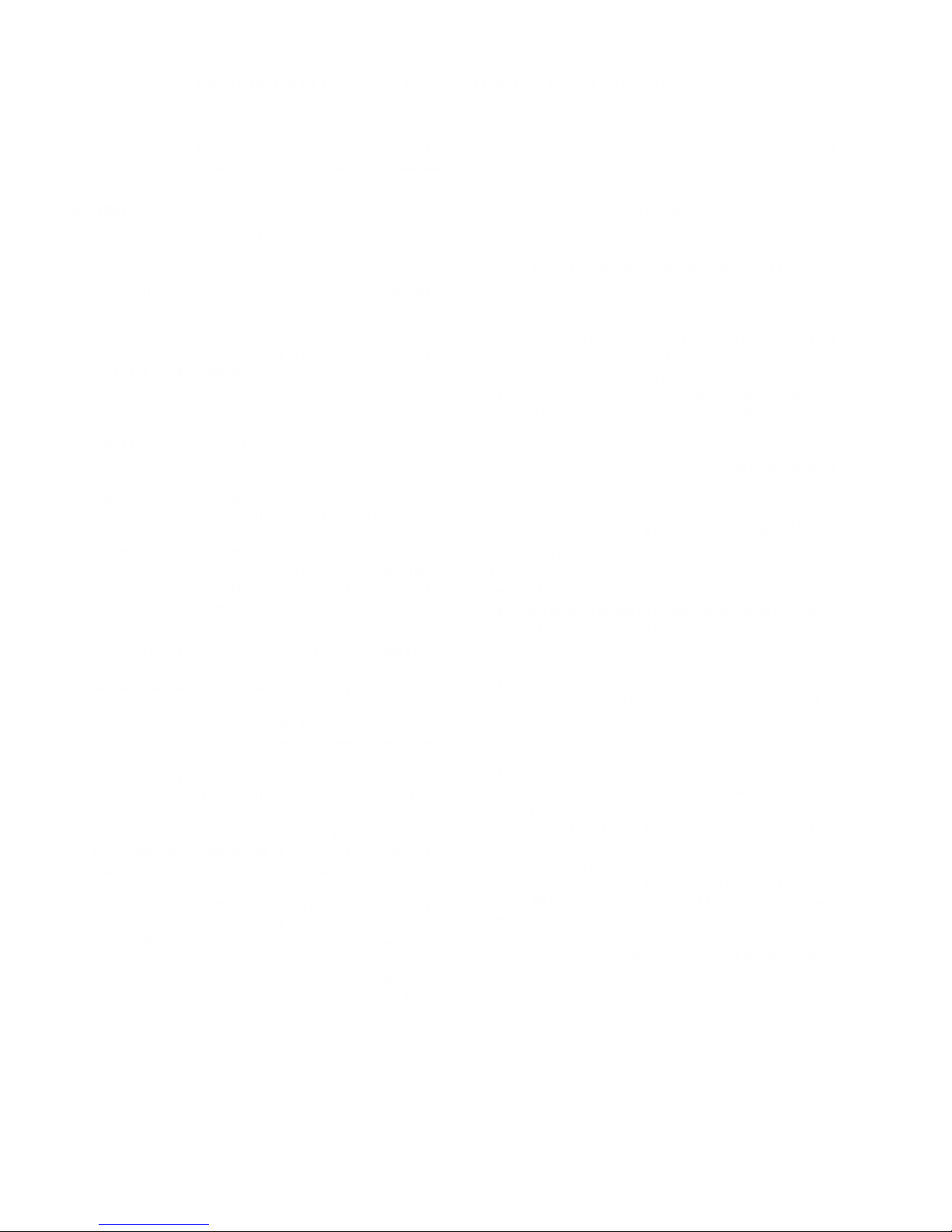
IMPORTANT
SERVICE
SAFETY PRECAUTIONS
Service
work should
be
performed
only
by
qualified
service technicians
who
are
thoroughly
familiar
with
all
of
the
following safety checks and
servicing
guidelines:
WARNING
1. For
continued
safety,
do
not
attempt
to
modify
the
circuit.
2.
Disconnect the
AC
power
before servicing.
3. Semiconductor
heat
sinks are
potential
shock haz-
ards when
the
chassis
is operating.
SERVICING
THE
HIGH
VOLTAGE
SYSTEM
AND PICTURE TUBE
When
servicing the high
voltage
system,
remove
the
static
charge by connecting a
10k
ohm
resistor
in
series
with
an insulated
wire
(such
as
a test probe)
between the chassis
and the
anode
lead.
(The
AC
line
cord should
be disconnected from
the
AC
outlet.)
1. The picture
tube
in this
display
monitor
employs
in-
tegral implosion
protection.
2. Replace with a
tube
of
the same
type
number
for
continued
safety.
3.
Do
not
lift
the
picture
tube
by the
neck.
4. Handle
the
picture
tube
only
when
wearing
shatter-
proof goggles
and after
discharging
the
high vol-
tage
anode completely.
X-RADIATION
AND
HIGH
VOLTAGE
LIMITS
1.
Be
sure
all
service
personnel are
aware
of the
procedures
and
instructions
covering
X-radiation.
The only
potential
source
of X-ray
in
a
current
solid-
state
display
monitor
is the picture
tube.
However,
the picture tube
does
not
emit
measurable
X-ray
radiation
if the high
voltage
is as
specified
in the
"high-voltage
check"
instructions.
It
is only when high
voltage
is
excessive
that
X-
radiation
is capable of
penetrating
the
shell
of
the
picture
tube, including
the
lead in
glass
material.
The
important
precaution
is
to keep
the
high vol-
tage below
the
maximum
level
specified.
2. It
is essential
that servicemen
have
available
at all
times
an
accurate
high
voltage
meter. The
calibra-
tion
of
this meter
should
be
checked
periodically.
3.
High
voltage
should
always
be kept
at the
rated
value
—
no higher.
Operation
at
higher
voltages
may cause
a failure of
the picture
tube or
high vol-
tage
circuitry
and, also,
under
certain conditions,
may
produce radiation
in excess of
desirable
levels.
4. When the high
voltage
regulator
is
operating proper-
ly
there
is
no
possibility
of
an X-radiation
problem.
Every
time
a
color
chassis
is serviced, the
bright-
ness
should
be
tested
while
monitoring the
high vol-
tage
with
a
meter
to be
certain
that
the high
voltage
does
not
exceed
the specified
value and
that it is
regulating
correctly.
5.
Do
not
use
a
picture
tube other
than that
specified
or make unrecommended
circuit
modifications to
the high
voltage
circuitry.
6.
When
troubleshooting
and taking test measure-
ments on
a
display monitor
with
excessive high vol-
tage, avoid
being
unnecessarily
close
to the
display
monitor. Do
not
operate
the display
monitor longer
than
is necessary
to locate
the
cause
of
excessive
voltage.
BEFORE RETURNING
THE DISPLAY MONITOR
Fire and
Shock
Hazard
Before
returning
the display
monitor
to the
user,
per-
form the
following
safety checks:
1.
Inspect
all
lead dress
to make
certain that
the
leads
are
not
pinched
or that
hardware
is
not
lodged be-
tween the
chassis and
other metal
parts
in the dis-
play
monitor.
2. Inspect
all
protective
devices
such as nonmetallic
control
knobs,
insulating
materials,
cabinet backs,
adjustment
and
compartment
covers
or
shield,
iso-
lation
resistor-capacitor
networks,
mechanical in-
sulators,
etc.
3. To be sure
that
no
shock hazard
exists,
check for
leakage
current in
the following
manner:
•
Plug
the
AC
line
cord
directly
into an 120 volt
AC
outlet. (Do
not
use
an isolation
transformer
for
this
test.)
•
Using two
clip
leads, connect
a 1.5k ohm,
10 watt
resistor paralleled
by a 0.15/iF
capacitor
in
series
with all exposed
metal
cabinet
parts
and a
known
earth
ground,
such
as
electrical
conduit
or electri-
cal ground
connected
to
earth
ground.
•
Use
a
SSVM or
VOM
with
1000 ohms
per-volt
or
higher
sensitivity
to
measure the
AC
voltage drop
across
the resistor.
(See
Figure
1.)
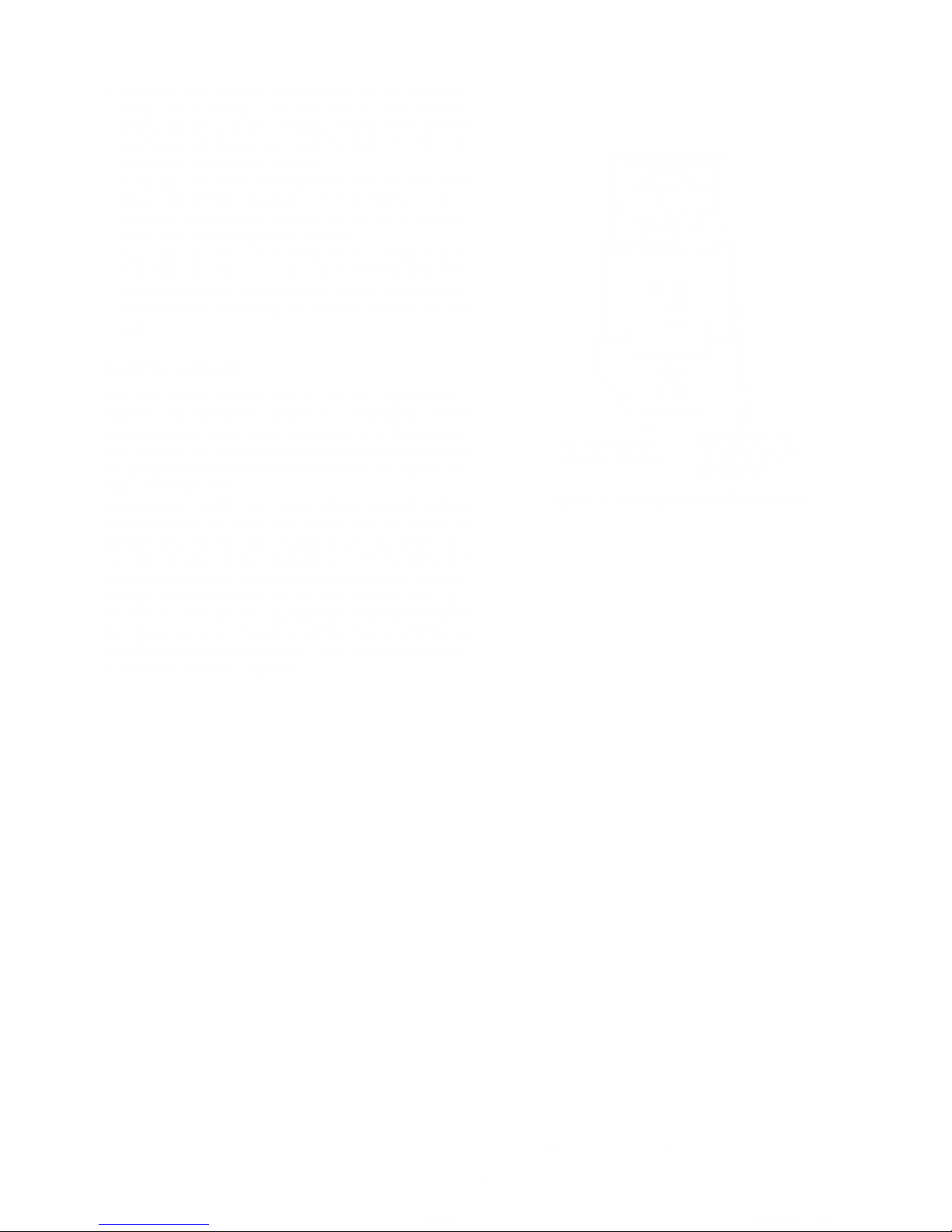
•
Connect
the
resistor connection
to
all
exposed
metal
parts
having
a return path to
the
chassis
(metal
cabinet,
screw
heads,
knobs
and
control
shafts,
escutcheon, etc.) and
measure
the
AC
vol-
tage
drop across
the resistor.
All
checks must
be repeated
with
the
AC line cord
plug
connection reversed.
(If
necessary, a non-
polarized adapter
plug
must
be
used
only for
the pur-
pose
of
completing
these
checks.)
Any
reading
of 0.3 volt
RMS
(this
corresponds
to
0.2
milliamp.
AC.) or
more
is
excessive
and indi-
cates a
potential shock
hazard which must
be cor-
rected
before
returning
the display
monitor to
the
user.
SAFETY
NOTICE
Many
electrical and
mechanical
parts in display
moni-
tors
have special safety-related characteristics.
These
characteristics often
pass
unnoticed and
the protec-
tion
afforded by them cannot necessarily
be
obtained
by
using
replacement
components rated for higher vol-
tage,
wattage,
etc.
Replacement
parts
that
have these
special
safety
characteristics are identified in
this manual; electrical
components
having
such
features
are
identified by a
A
and shaded
in
the Replacement Parts Lists and
Schematic
Diagram. For
continued protection, replace-
ment
parts must
be identicaltothose
used
in the
origi-
nal
circuit. The use
of
a
substitute replacement part
that
does not
have
the same safety characteristics
as
specified
in this service
manual, may create shock,
fire,
X-radiation or other hazards.
TO
EXPOSED
METAL PARTS
CONNECT
TO
KNOWN
EARTH
GROUND
Figure
1. Leakage Current
Test
Circuit
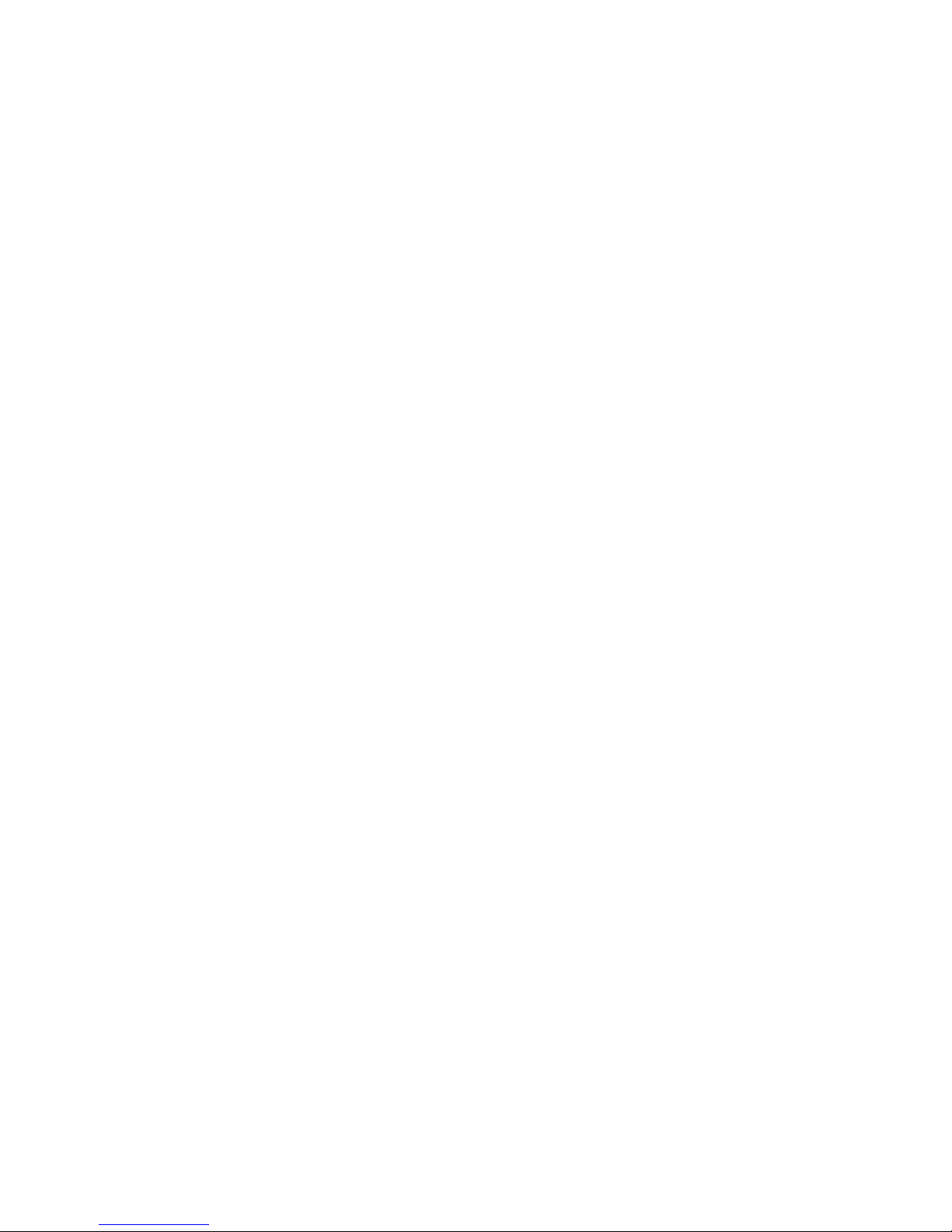
THEORY
OF
OPERATION
1.
RGB
Drive
Circuit
The
RGBI
signals
are applied to
HEX inverter
IC491
used
as
a
buffer). The
outputs of
IC491 are then
ap-
alied
to
IC492
which
is
an
open
collector HEX invert-
er.
The
resistors
tied
to
the
outputs of IC492 are
used
:o
set
the
appropriate
voltage
level
for the color
sig-
nals.
The
signals
are
then applied to
the base
of RGB-
Amp
transistors
Q451,
Q461 and Q471.
The
brightness
and
sub
brightness controls
(R41
7
and
341
6)
are used
to
adjust the
bias of
the
RGB-Amp
tran-
sistors.
These
controls are
connected
to the
base of
Q401
and
Q402.
When the intensity
signal
is
LOW,
transistor
Q421
is
turned
ON.
The
contrast
control
(R422) is used
to
adjust
the con-
trast
between
high
and low intensity color
signals.
2. Video
(RGB) Output {Fig.
2)
An RGB
drive system
is
utilized
in
the
video output
cir-
cuit of
this
unit.
The
function
of
this
circuit
is to
com-
oine
the
color signals and the brightness
signal,
and
amplify them
sufficiently
to
drive
the
cathodes. 1
45V
DC
must
be applied
to
the collectors
of the
output tran-
sistors
(Q851, Q861,
Q871).
When
the horizontal
output circuit is
operating, pulses are
developed
and
fedtothe
1
16V supply
where they are applied
to
a
winding
of the
horizontal output transformer (T602).
This pulsed
DC
voltage
is
then
taken
from terminal (s)
of
T602 and applied
through
D71
7,
and
R865
or
R866
or
R867 to
the
collectors of
Q851,
Q861
andQ871,
respectively.
The brightness
signal
from the
Blanking
(Q402)
is
ap-
plied
to
the emitters of
Q851,
Q861 and
Q871.
C853
and C855
are
peaking capacitors.
Color signals from
the
outputs
of
Q451,
Q461 and
Q471
are
applied
to
the bases of
Q851,
Q861 and
Q871 . The picture
tube
used
in
this
unit
is
a
precision,
inline
gun-type.
The control grid
(G1)
and the
screen
grid
(G2)
are common
with
respect to the red, green
and blue cathodes. Consequently, the
emitter circuits
of Q85
1
, Q86 1
and
Q87
1
are
provided
with bias con-
trols
(R862, R863 and
R864,
respectively)
for picture
tube
cut-off
adjustment. Drive
controls
(R856
and
R858) are provided
in
the emitter circuits
of Q851 and
Q871 for white balance
adjustment.
FROM
EMITTER
>
OF Q451
Q851
RED
OUTPUT
FROM
EMITTER
>
OFQ461
FROM
EMITTER
>
OFQ471
FROM
VIDEO
DRIVE
>
CIRCUIT
<
+145
Figure
2.
Video
Output
Circuit

3,
Vertical
Deflection
Circuit
The
vertical
sync,
signal
with
positive polarity
is ap-
plied
to
pin(7)of
the vertical
and
horizontal
IC
(IC601).
Pin
(8)of
IC601
is connected
to
the vertical oscillator
circuit.
The
frequency of the oscillator can
be
con-
trolled
by the
voltage
of pin
(8)
which
can be varied
by
V.HOLD
VR
(R514).
The
sawtooth signal is
ob-
tained by
the integrating
circuit which
is connected be-
tween
pin
(5)
and pin
Qj)
.
The
oscillator output
is
fed
to the vertical
drive circuit
through a
buffer
circuit.
Its
output, derived
from pin
(2)
,
is
applied to
the
vertical output.
The
sawtooth
wave
is
applied
to
pin
(3)
of
IC601 as
an AC
feedback
signal.
The
emitter circuit of Q501 is controlled by
V-SIZE VR
(R507)
to vary the vertical size of the raster.
The
vertical
linearity
control
(R526) is part of
an
in-
tegrating circuit
which controls the sawtooth
waveform.
4.
Horizontal
Oscillator, AFC
and
Drive Circuit
The
horizontal
sync,
signal
with
positive
polarity is ap-
plied to
pin
(15)
of IC601.
The output
from the fly-back
transformer (T602)
is
in-
tegrated
and
connected
to pin
(^3)
of
IC601 as part
of
the
automatic frequency control circuit.
H.
CENT
control
(R623)
determines
the relative posi-
tion
of
the raster and
picture.
The
horizontal
oscillation
frequency can
be controlled
by H.
HOLD VR
R607
connected
to
pin
(j~2).
The
horizontal frequency is
obtained from pin
\[Q)
of
IC601,
and is
fed
to
the
next
horizontal
drive circuit.
The
pulse-switching
mode of the
driver and
output
stage is a
reverse
polarity
type;
that
is,
when
the
driver
transistor
Q601 is
ON,
the
output
transistor
Q602
is
OFF.
5.
Horizontal Output
and
HV
Rectifier
(Figs.
3-5)
Horizontal drive voltage,
developed at
pin
^6)
of
the
deflection
processor integrated
circuit
(IC601
),
is
am-
plified
through
the horizontal drive
stage
(Q601)
and
coupled to the base
of
the horizontal output
circuit
via
the horizontal drive transformer
(T601 ).
Refer
to
Fig. 3.
The horizontal
output circuit generates the
horizontal
scan and
high voltage
to
be applied to
the picture tube.
The function
of the
horizontal output
stage
(Q602)
is
to
serve
as a
switch for the horizontal
output
circuit.
Refer
to
Fig. 4.
During
the horizontal
scanning
period, Q
operates
(S
1
is
closed,
S2 is open) and the current
is
applied
in
one
direction through the
horizontal coils
of the
deflection
yoke
(LY)
and the
capacitor
(C).
During retrace
time,
Q is inoperative (S 1
is
open, S2 is
closed)
and
the
cur-
rent is applied in the opposite
direction
through
the
damper
diode
(D),
the horizontal
coils of
the
deflection
yoke (LY)
and
the capacitor
(C).
The
high
voltage
required
to
be
applied
to
the
anode
of the picture tube is generated by
boosting
the
pulse
from the collector of Q602
through
T602
during
the
flyback
(retrace) period and applying
this
boosted
pulse
to
a
series of
silicon
rectifiers. Refer
to
Figure 5.
High voltage regulation is accomplished
internally
in
T602.
T601
HORIZ. DRIVE
From
Pin (TS)
^
of
IC601
^
C609
T
I
To
BASE
of
Q602
Q601
HORIZ.
DRIVE
^+12V
Figure
3.
Horizontal
Drive Circuit
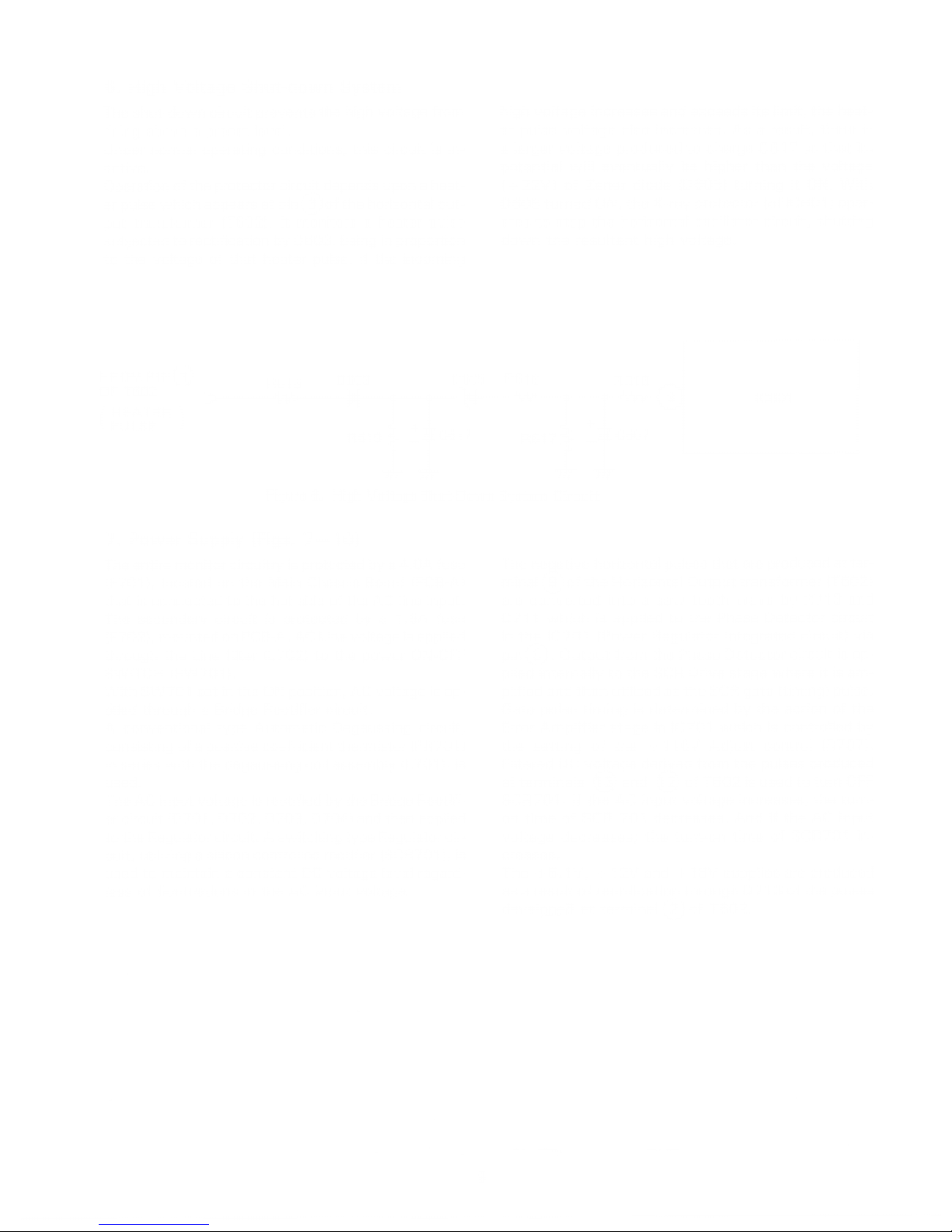
6.
High
Voltage Shut-down System
The
shut-down
circuit
prevents
the
high
voltage from
rising above a
preset
level.
Under normal
operating
conditions,
this circuit is
in-
active.
Operation
of
the
protector
circuit depends
upon
a heat-
er
pulse
which
appears at
pin
{3)
of
the horizontal out-
put
transformer
(T602).
It monitors
a
heater pulse
subjected
to
rectification by D603.
Being in
proportion
to
the
voltage of
that heater pulse,
if
the
incoming
high voltage
increases and exceeds its
limit,
the heat-
er pulse
voltage
also
increases. As
a
result,
there is
a
larger voltage
produced to
charge
C617
so
that
its
potential
will eventually
be higher
than
the
voltage
(
+ 22V) of
Zener
diode
(D605)
turning
it
ON.
With
D605
turned
ON,
the
X-ray
protector
(of
IC601
)
oper-
ates
to
stop
the
horizontal
oscillator circuit,
shutting
down the resultant
high
voltage.
FROM
PIN©
OF
T602
/ HEATER
\
\
pulse
;
>
R615
D603
-w
M—
D605
R618
—
^
VA-
R619?
±ZZC617
R6175
-^
77T
Figure
6. High
Voltage
Shut-Down
System
Circuit
R616
^
-AW-(V)
C607
7.
Power
Supply (Figs.
7
—
10)
The
entire
monitor
circuitry
is
protected
by
a
4.0A
fuse
(F701),
located
on the Main Chassis
Board (PCB-A)
that
is connected
to
the
hot side of
the
AC
line
input.
The
secondary
circuit
is
protected
by
a
1.5A
fuse
(F702),
mounted on
PCB-A.
AC
Line voltage
is applied
through
the Line
filter (L702)
to
the
power
ON-OFF
SWITCH
(SW701).
With SW701 set
in the ON position, AC
voltage
is ap-
plied
through
a
Bridge
Rectifier
circuit.
A
conventional type
Automatic Degaussing
circuit,
consisting
of
a
positive coefficient thermistor (PR701
)
in
series
with
the
degaussing coil assembly
(L701
),
is
used.
The
AC
input voltage
is rectified
by
the
Bridge
Rectifi-
er
circuit
(D701
,
D702,
D703,
D704) and then
applied
to the
Regulator
circuit.
A
switching
type
Regulator
cir-
cuit,
utilizing
a
silicon
controlled rectifier
(SCR701),
is
used to
maintain
a constant DC
voltage level
regard-
less
of
fluctuations \n the AC
input
voltage.
The negative
horizontal
pulses
that
are
produced
at
ter-
minal
@of
the
Horizontal Output
transformer
(T602)
are converted
into
a saw
tooth wave by
R713
and
C71 1 which
is
applied
to
the Phase
Detector
circuit
in
the
IC701 (Power Regulator
integrated
circuit)
via
pin
(5)
.
Output from the
Phase
Detector
circuit is
ap-
plied
internally
to
the
SCR
Drive stage
where
it is
am-
plified and
then
utilized as
the
SCR
gate
(timing)
pulse.
Gate
pulse timing is
determined by the
action
of the
Error Amplifier
stage
in
IC701
which is
controlled by
the setting of
the
+116V Adjust
control
(R707).
Filtered DC voltage
derived from the
pulses
produced
at terminals
@
and
@
of
T602
is
used to
turn
OFF
SCR701. If
the AC
input
voltage increases,
the
turn-
on time
of
SCR
701 decreases.
And
if the
AC
input
voltage decreases;
the turn-on
time
of SCR701
in-
creases.
The
+
5.
1
V,
+
1 2V
and
+
1
8V
supplies
are
produced
as
a
result
of rectification
through
D71
3
of the
pulses
developed
at
terminal @of
T602.

DISASSEMBLY
INSTRUCTIONS
Remove
the six
screws
(T) retaining the
rear
cabinet.
Remove
the rear cabinet.
(Figure 1 1A)
Note:
The CRT
must
be
discharged. Refer to
the
high
voltage discharge
procedure
on
page
4.
(1)
Remove the
CRT's
second
anode
cap(2)from
the CRT.
(2)
Remove
the
PCB--B
(CRT
PCS)
lead of
the CRT
grounding
strap.
(Figure
11B)
(3)
Remove the
PCB-B.
(4)
Loosen
the
wire
holder
on
the Flyback
trans-
bracket
and disconnect the connector K.
(Figure 11B)
(5)
Disconnect
the
connectors NA and M on the
PCB-A
(main
PCB-A)
(6)
Loosen
the
wire
holder
fixing
power switch
lead,
CRT
ground lead, RGB
output lead,
Degaussing lead
and
LED
lead. (Figure
1 1B)
(7)
Remove
the
PCB-A
(main PCB)
from the
front
cabinet.
3.
Remove
screw
(5)
for PCB-C the LED and
also
PCB-C
from the
front cabinet.
(Figure 1 1B)
Note: When
servicing,
be
sufficiently careful with
the
control door
because
it
may detach
from
the
cabinet if
it
touches
the
surface
while
the
set
is
inclined toward the front.
Figure
11A
Figure
11B
12

ALIGNMENT
INSTRUCTIONS
Mote:
This
adjustment
requires
the
connection of
a personal
computer
to
the Monitor.
Although
the
Monitor
is ad-
usted
before
it
Is
delivered, readjustment
may
be
re-
quired
when
the
setting
position
is
changed
or
when
i
component
is replaced.
1.
B+
Power Circuit
Adjustment
(Instrument
in use: a
20
kohm/V
tester)
1)
Be
sure that the
AC line
voltage is
above 1 14V.
2)
Rotate
the B
+ voltage
adjusting control
(R707)
to
provide a
DC
voltage of
1 16V
between
TP91
and
ground.
Mote
1
:
If the AC
line
voltage
is below
1
14V,
the
DC
voltage may
not increase
to 1
1
6V,
but
this
is
not a
problem
related
to
this
adjust-
ment.
If
the value
of
1
16V
DC
is almost
reached, the adjustment
is
enough.
-Mote
2:
Clockwise rotation
of the B+
voltage
ad-
justing control
will
increase
the
B +
power
supply
voltage.
2.
Horizontal Hold Adjustment
(1)
Operate
the computer in
such
a
way
that
the
let-
ters
"H"
cover
the
entire screen
(data display
peri-
od:
44.698
/*S
horizontal, 14.33
mS vertical).
(2)
Adjust the horizontal hold control
(R607) until
the
picture
on
the
screen becomes
still
(synchronized).
(3)
Turn the power
switch on
and off
several
times
to
check that
the
picture
does
not
fluctuate.
3.
Vertical Size Adjustment
(1
)
Operate
the computer in
such
a
way that the
let-
ters "H" cover the
entire screen
(data
display
peri-
od:
44.698
mS
horizontal,
14.33
mS
vertical).
(2)
Adjust the vertical size
control (R507)
so
that
the
heightofthe
displayed pattern
is 170
mm.
4.
Focusing
(1) Operate the
computer to
display
the
alphabetical
characters
on
the screen.
(2) Set
the
brightness control
at
the center
position.
(3)
Rotate
the focus
adjusting control (part
of
T602)
for
the best
focus.
(4)
Change
the
position
of the brightness
control
to
confirm
that
the
picture remains
focused.
5.
High
Voltage
Check
High
voltage
is
not
adjustable
but
must be checked
to
verify
that
the
Monitor
is
operating within
safe
and ef-
ficient
design
limitations
as
specified.
1
.
Operate the display
Monitor
for
at
least
1
5
minutes
at
1 20V
AC
line voltage
with
the computer
display-
ing
high intensity
white
pattern.
2.
Turn
off
Switch
SW851
on
PCB-B.
3. Rotate
the screen
control
(on T602)
to
the
maxi-
mum
(counterclockwise)
end
of
its rotation.
4. Connect
an
accurate,
high-voltage meter
to
the
CRT anode.
Check
that the
reading is approximate-
ly 22.0kV and
23.0kV
(at
beam current).
If a correct
reading
cannot
be
obtained, check
the cir-
cuitry for malfunctioning
components.
On
completion
of
the voltage check, readjust the screen control for
proper
operation as detailed in the "Black
and
White
Tracking"
procedures.
6. Vertical-Linearity
Adjustment
1
.
Operate
the
computer
in such a
way
that the
let-
ters "H" cover
the
entire screen (data display peri-
od: 44.698
/iS
horizontal,
14.33
mS vertical).
2. Adjust
the
V-Lin.
control
(R526)
until the height
of
a character varies
no more than 1
percent from
the
average
character size.
7. X-ray
Protector Circuit
Test
After service
has
been
performed
on
the
horizontal
deflection
system,
the
high
voltage system and
the X-
ray
protector
circuit must
be tested
for
proper
opera-
tion as
follows:
1
.
Apply
1
20VAC,
using
a variac transformer
for ac-
curate
input voltage.
2.
Operate
the
computer
in such
a way that
the
en-
tire
screen displays
a high
intensity
white
signal
(data
display
period:
44.698
/*S
horizontal,
1 4.33
mS
vertical).
3. Check
the voltage of
test
point TP601 .
(Its
voltage
should
be
about
17.5VDC.)
4.
Connect
the
cathode
of
diode D503 and
TP601
through
a 6.8K ohm, 1/2W resistor.
5.
To
start
operation,
remove the resistor
and
touch
the
IC601
(9)
pin-to-chassis ground
with
a short
clip
lead.
(Remove
the short clip
lead
as
soon
as
the
set
operates
again
with
a normal
picture).
6. Connect
the short-clip
lead
between TP602
and
chassis
ground. When
these
points are
connect-
ed,
the
operation
of
the horizontal
osc. must stop.
7.
To
start
operation,
remove
the short-clip
lead when
the set
begins
operating
again
with
a
normal
picture.
8.
If
the operation
of
the horizontal
osc.
does not
stop
in
steps
4
and
6,
the
circuit
must be repaired
be-
fore the
set
is
returned
to
the
customer.
14

11.
Dynamic
Convergence
(Figs.
17
—
19)
Dynamic
convergence
(convergence
of
the
three color
fields at the edges
of the CRT screen)
is accomplished
by proper
insertion
and positioning
of three
rubber
wedges
between
the edgeofthe deflection
yoke
and
the funnel
of
the CRT.
This
is accomplished
in the following
manner:
1
Switch the display
monitor
ON
and allow
it
to
warm
up
for 15 minutes.
2.
Apply the Crosshatch pattern (Fig.
14) from the
computer
to
the
display
monitor.
Observe
spacing
between
lines
around the
edges
of the CRT.
3.
Tilt the
deflection
yoke up
and down.
Insert
tilt
ad-
justment wedges
(T) and
(5)
between
the deflec-
tion
yoke and the CRT
until
the
misconvergence
illustrated
in Figure 17
has
been
corrected.
4.
Tilt the deflection
yoke right and
left.
Insert tilt
ad-
justment
wedge
(3)
between the
deflection
yoke
and
the
CRT
until
the
misconvergence
illustrated
in
Figure 18
has
been corrected.
5.
Alternately
change the
spacing
between,
and depth
of
insertion
of, the
three
wedges until
proper
dy-
namic
convergence
is obtained.
6.
Check purity
and
readjust,
if
necessary.
r
GREEN
^r
BLUE-
(RED)
7T"
l^
RED
I—
(BLUE)
/
BLUE(RED).
77
/
GREEN
RED
(BLUE)
Figure
17
/
/(RED)
GRE
RED
L_"
tu
|^_(BLUE)|
GREEN
BLUE
RED)
Figure
18
WEDGE
(2)
DEFLECTION
YOKE
REAR
VIEW
WEDGE(3)
Figure
19. Dynamic Convergence
17

TROUBLESHOOTING
GUIDE
Circuits
checked:
• Power
regulator
circuit
•
Protector
circuit
•
Horizontal
sync
circuit
NO
POWER
Does
150V
appear between
the
anode
of
SCR701 and
ground?
Yes
Connect a
zener
diode (60V)
between
the
gate
of
SCR701
and
T702-to-D716
junction:
connect
the
zener
diode anode to the gate of
SCR701
Is
the power
circuit
activated?
i-
— —
-*
—
—
«
J
»«! D705
1
1
1
Yes
D716
i
i
i
No
Connect
a
resistor
(15W,
50
ohms)
between
TP-91
and
T702-to-D7
16
junction.
Is the horizontal
sync circuit
activated?
No
Yes
Does
18V
appear
between pin(S)of
IC701
and ground?
—
No
Yes
Does
7.8V appear
between
pin(7)of
IC701
and
ground?
—
No
|
R615
D605
)
IC601
R613
t\
Q601
R620
i
Q602
D603
I
D602
JR717
R719
D714i
|R716
D713
|
i
i
i
IC701
R706
*
R707
R709
!
R711 C707
Yes
SCR701
R712
R705
C709
C710
I
J
18

2.
Electrical Parts
List
PRODUCT
SAFETY
NOTErComponents
marked
with
a
a
have special
characteristics
important
to safety.
Before
replacing
any
of
these
components,
read
carefully the
SAFETY
NOTICE
on
page
4
of
this
service manual. Do not
degrade the
safety
of
the product
through
improper servicing.
Components
marked
with
an
a
are
related
to
the X-ray protection
circuit.
REF.NO.
DESCRIPTION
RS
PART
NO.
MFR'S
PART NO.
P.C.B. Assembly.
Main (PCB-A) (U.S.A.)
AX9203 DUNTK4163RA0H
Consists of
the
following: (CANADA)
DUNTK4163RA1H
CAPACITORS
C401
Electrolytic,
22/xF, 16V,
±20%
CC226MDAP
VCEAAA1CW226M
C402 Ceramic,
0.0
VF, 50V,
+80-20%
CC103ZJCP
VCKZPA1HF103Z
C403 Electrolytic, 10/J=, 50V,
±20%
CC
106MJAP
VCEAGA1HW106M
C404
Electrolytic,
47^F,
16V, ±20%
CC476MDAP
VCEAGA1CW476M
C405 Electrolytic, 100
M
F,
25V,
±20%
CC107MFAP
VCEAGA1EW107M
C406
Electrolytic,
47/xF, 25V,
±20%
CC476MFAP
VCEAGA1EW476M
C407
Ceramic,
0.0
VF, 50V,
+80-20%
CC103ZJCP
VCKZPA1HF103Z
C408
Ceramic,
100pF,
500V,
±10%
CC104KJCP
VCKYPA2HB101K
C451 Ceramic,
15pF, 50V,
±5%
CC150JJCP
VCCSPA1HL150J
C461
Ceramic,
15pF,
50V,
±5%
CC150JJCP
VCCSPA1HL150J
C471 Ceramic,
15pF, 50V,
±5%
CC150JJCP
VCCSPA1HL150J
C481 Electrolytic,
220/xF,
16V, ±20%
CC227MDAP
VCEAGA1CW227M
C482
Ceramic,
0.0
VF, 50V, ±+80-20%
CC103ZJCP VCKZPA1HF103Z
C483 Ceramic,
820pF,
50V,
±10%
CC821KJCP
VCKZPA1HB821K
C484 Electrolytic,
VF,
50V, ±20%
CC105MJAP
VCEAAA1HW105M
C491
Ceramic,
0-VF,
25V,
+80-20%
CC104ZFCP
VCTYPU1EF104Z
C492 Electrolytic,
VF,
50V,
±20%
CC105MJAP
VCEAAA1HW105M
C493
Ceramic,
O.VF,
25V,
+80-20%
(U.S.A.
21988-)
CC104ZFCP
VCTYPU1EF104Z
C502
Ceramic,
180pF, 50V,
±5%
CC181JJCP
VCCSPA1HL181J
C503 Tantalum,
2.2^iF,
35V,
±10%
CC225KGTP
VCSATA1VE225K
C504 Electrolytic,
VF,
50V, ±20%
CC105MJAP
VCEAAA1HW105M
C505 Electrolytic,
1000/iF,
16V,
±20%
CC108MJAP
VCEAAA1CW108M
C506
Ceramic,
0.0047^F, 50V,
±10%
CC472KJCP
VCKZPA1HB472K
C507 Electrolytic, 33^F,
16V,
±10%
CC336KDAP
VCEACA1CC336K
C508 Electrolytic,
10/*F, 25V,
±20%
CC106MFAP
VCEAAA1EW106M
C509
Electrolytic,
470/iF,
25V,
±20%
CC477MFAP
VCEAAA1EW477M
C510
Electrolytic,
1000/iF, 50V,
±20%
CC108MJAP
VCEAAH1HW108M
C511 Ceramic,
39pF, 50V,
±5%
CC390JJCP
VCCSPA1HL390J
C512 Tantalum,
2.2/iF,
35V,
±10%
CC225KGTP
VCSATA1VE225K
C514 Electrolytic,
10/iF,
16V,
±20%
CC106MDAP
VCEAAA1CW106M
C515 Ceramic,
0.0
VF, 500V,
±10%
CC103KUCP
VCKYPB2HB103K
C601
Mylar*,
0.01
8/^F, 50V,
±10%
CC183KJMP
VCQYSH1HM183K
C603
Electrolytic,
VF,
50V,
±20%
CC105MJAP
VCEAAA1HW105M
C604 Polypro
Film,
0.0027/iF,
100V, ±2%
CC272GLHP
VCQPSA2AA272G
*Mylar
is
a
registered
trademark
of
E.I.Du
Pont de
Nemours and Company.
29

REF.NO.
DESCRIPTION RS
PART NO. MFR'S
PART
NO.
C605
Mylar,
0.0068/xF,
50V,
±10% CC682KJMP
VCQYSH1HM682K
C606
Mylar, 0.0022/^F, 50V,
±5% CC222KJMP VCQYSH1HM222J
C607 Electrolytic,
10/tF,
16V,
±20% CC106MDAP
VCEAAA1CW106M
C608
Electrolytic,
220jiF, 25V,
±20%
CC227MFAP
VCEAGA1EW227M
C609
Ceramic,
0.00
VF,
50V,
±10%
CC102KJCP VCKZPA1HB102K
C610 Mylar,
0.0047fiF,
50V, ±10% CC472KJMP
VCQYSH1HM472K
C611
Mylar,
0.015^F,
50V,
±10% CC
153KJMP
VCQYSH1HM153K
C612
Mylar,
0.056/tF,
50V,
±10% CC563KJCP
VCQYSH1HM563K
C613
Mylar, 0.027/tF, 50V,
±10% CC273KJMP
VCQYSH1HM273K
C614
Ceramic,
0.00
VF,
50V,
±10%
CC102KJCP
i
VCKZPA1HB102K
C615
Ceramic, 0.01/tF,
50V, ±10%
CC103KJCP
VCKZPA1HB103K
C616
Ceramic,
470pF, 50V, ±10%
CC471KJCP
VCKZPA1HB471K
C617
Electrolytic,
4.7/tF,
50V,
±20%
CC475MJAP VCEAGA1HW475M
C618
Ceramic,
0.00VF,
50V,
±10%
CC102KJCP
VCKZPA1HB102K
C619
Ceramic,
82pF,
50V,
±5%
CC820JJCP
VCCSPA1HL820J
C620 Electrolytic,
100jiF,
25V, ±20%
CC107MFAP VCEAGA1EW107M
C623
A
Metalized Polypro,
0.33/iF,
200V,
±5%
CC334JPGP VCFPPD2DB334J
C625AA Metalized Polypro,
0.0022/tF,
1.6kV,
±5%
CC222JYHP
VCFPPC3CA222J
C626
A A
Metalized
Polypro, 0.001 5/iF, 1.6kV,
±5%
CC152JYHP
VCFPPC3CA152J
C627
AA
Metalized
Polypro,
0.001
5/tF,
1.6kV,
±5% CC152JYHP
VCFPPC3CA152J
C628
AA
Metalized
Polypro, 0.001 5/tF, 1.6kV,
±5%
CC152JYHP VCFPPC3CA152J
C629 Not used
C630
A
Polypro
Film, 0.068^F, 200V,
±10%
CC683KPHP
VCQPSC2DA683K
C701 A
Across Line, 0.22/iF,
125V (AC), ±20%
AC-0091 RC-QZ019DCEZZ
C702
Ceramic, 0.0
VF,
250V
(AC)/1.4kV (DC),
±5%
CC103JYCP
RC-KZ007JCEZZ
C703 Ceramic,
0.0
VF,
250V
(AC)/1.4kV
(DC), ±5%
CC103JYCP RC-KZ007JCEZZ
C704
Ceramic,
0.0
VF,
500V, ±10%
CC103KUCP
VCKYPB2HB103K
C705
A
Electrolytic,
470/iF, 200V, ±20%
CC477MPAP
RC-EZ0164CEZZ
C706 A Electrolytic,
330/iF,
200V,
±20%
CC337MPAP RC-EZ0162CEZZ
C707
A
Electrolytic,
100/iF,
160V,
±20%
CC107MNAP
VCEAAH2CW107M
C708 Electrolytic,
47/iF,
50V,
±20%
CC476MJAP
VCEAGA1HW476M
C709
Polypro Film,
0.047nF,
200V, ±10%
CC473KPHP
VCQPSB2DA473K
C710 Ceramic, 0.0047^F, 500V,
±10%
CC472KUCP VCKYPA2HB472K
C711
AA
Ceramic,
0.0
VF, 50V,
±10%
CC103KJCP VCKZPA1HB103K
C712
A
Ceramic,
3300pF, 125V
AC,
±20%
CC332MXCP
RC-KZ0030CEZZ
C713 Electrolytic,
1000/iF,
35V,
±20%
CC108MGAP VCEAAH1VW108M
C714 Ceramic,
0.0
VF,
50V,
+80-20%
CC1032JCP VCKZPA1HF103Z
C715 Ceramic,
0.0
VF,
50V,
+80-20%
CC103ZJCP VCKZPA1HF103Z
C716 Ceramic,
0.0
VF, 50V,
+80-20%
CC103ZJCP VCKZPA1HF103Z
C717
Electrolytic, 100^F,
16V, ±20%
CC107MDAP
VCEAGA1CW107M
C718
Electrolytic,
470/tF,
16V,
±20%
CC477MDAP
VCEAGA1CW477M
C719
Electrolytic,
100/iF, 25V,
±20%
CC107MFAP
VCEAGA1EW107M
C720
A
Electrolytic,
470/tF,
25V,
±20%
CC477MFAP
VCEAAA1EW477M
C721
A Electrolytic 100^F,
25V,
±20%
CC107MFAP
VCEAGA1EW107M
C722
Ceramic,
0.00
VF, 500V,
±10%
CC102KUCP VCKYPA2HB102K
C723
Ceramic,
0.022/tF,
50V,
+80-20%
(U.S.A. Up to 66050/CANADA
Up
to
7004)
CC223ZJCP VCKZPA1HF223Z
C723
Mylar,
0.022/tF,
50V,
±10%
(U.S.A.
66051
-/CANADA
7005-)
VCQYSH1HM223K
30

REF.NO.
DESCRIPTION
RS
PART
NO. MFR'S
PART NO.
D701
A
1S1887 Silicon
DX2443
RH-DX0038CEZZ
D702
A
1S1887 Silicon
DX2443
RH-DX0038CEZZ
D703
A
1S1887
Silicon
DX2443
RH-DX0038CEZZ
D704
A
1S1887
Silicon
DX2443 RH-DX0038CEZZ
D705
A
Zener HZ60
Silicon
DX0237 RH-EX0086CEZZ
D706 1S2473
Silicon DX0230
RH-DX0048CEZZ
D707 1S2473
Silicon
DX0230
RH-DX0048CEZZ
D708
1D4B42
Silicon DX0235
RH-DX0200CEZZ
D709
1SS119
Silicon DX2272
VHD1SS119//-1
D710
Zener
RD 12E Silicon DX2311
RH-EX0047CEZZ
D711
S5277G
Silicon DX2276 RH-DX0110CEZZ
D712
RH1S
Silicon
DX2275 RH-DX0086TAZZ
D713
A
RG2
Silicon DX0236 RH-DX0181CEZZ
D714
AA
RF1
Silicon
DX2450
RH-DX0101CEZZ
D716
1S2473
Silicon
DX0230
RH-DX0048CEZZ
D717
A
RH1S
Silicon
DX2275
RH-DX0086TAZZ
SCR701A
Silicon
Controlled
Rectifier
S6192F
DX2454 VHSS6192FLB1E
FUSES
F701
a
4A,
Fast
Blow
HF-1193
QFS-B4021GEZZ
F702
A
1.5A, Fast Blow
AHF0010 QFS-B1521GEZZ
ICs
IC491 IC SN74S04N
HEX
Inverter AMX4945
VHISN74S04/-1
IC492
IC
HD7406
HEX Inverter
(Open
Collector) AMX3675
VHIHD7406//-1
IC493 IC HD7426
Quad
2-input Gate
MX4297
VHIHD7426/M
IC494
IC
SN74S11N
Tripple
3-lnput
AND
Gate
MX6406
VHISN74S11/-1
IC601AA
IC HA11235 SYNC.
AFC,
X-Ray Protector,
Bipolar Linear
MX6452
RH-IX0065CEZZ
IC701AA
IC
T2058
Povyer
Regulator,
Bipolar Linear
MX6092
RH-IX0137CEZZ
COILS
L491
Ferrite Bead
RBLN-0038CEZZ
L492
Ferrite Bead
RBLN-0038CEZZ
L493
Ferrite
Bead
RBLN-0038CEZZ
L494
Ferrite
Bead
RBLN-0038CEZZ
L495
Ferrite
Bead
RBLN-0018CEZZ
L496
Ferrite
Bead RBLN-0018CEZZ
L602
Linearity
Coil
ACA8373
RCILZ0213CEZZ
L702
A
Line
Filter
ACA8382
RCILF0087CEZZ
TRANSISTORS
Q401-
2SA1015(Y)
A.B.L.,
Silicon PNP
2SA1015
VS2SA1015Y/1E
32

REF.NO.
DESCRIPTION
RS
PART NO.
MFR'S
PART NO.
Q402 2SA854(Q)
Blanking, Silicon
PNP
2SA854Q
VS2SA854-Q/1E
Q421
2SC1815(Y) Contrast Circuit, Silicon
NPN 2SC1815Y VS2SC1815YW-1
Q422
2SC1815(Y)
Contrast
Circuit,
Silicon
NPN
2SC1815Y
VS2SC1815YW-1
Q423
2SC1815(Y) Horizontal
Sync. Silicon NPN 2SC1815Y
VS2SC1815YW-1
Q451
2SC1815(Y) Red Amp., Silicon NPN
2SC1815Y
VS2SC1815YW-1
Q461
2SC1815(Y) Green Amp.,
Silicon
NPN
2SC1815Y
VS2SC1815YW-1
Q471
2SC1815(Y) Blue Amp.,
Silicon NPN 2SC1815Y
VS2SC1815YW-1
Q501 2SC1826
(G)
Vertical Output,
Silicon
NPN
2SC1826
VS2SC1826GL2E
Q502 2SC1826
(G)
Vertical
Output, Silicon NPN
2SC1826
VS2SC1826GL2E
Q601
2SC1213A
(C)
Horizontal
Driver,
Silicon
NPN
2SC1213C VS2SC1213AC1A
Q602
a
2SD869 Horizontal
Output,
Silicon
NPN 2SD869 VS2SD869-//1E
Q701 2SD325
(F> B+
Regulator,
Silicon NPN 2SD325
VS2SD325-F/1E
RESIS
TORS: Unless
otherwise
specified,
resistors are 1/4W,
±5%,
carbon type.
R401
Oxide Film,
270
ohm, 1W,
±5%
N0155EGD
VRSA/V3AB271J
R402 330 ohm
N0189EEC VRD-RA2EE331J
R403 1 2k
ohm
N0288EEC
VRD-RA2EE123J
R404
5.6k ohm
N0257EEC VRD-RA2EE562J
R405 10k
ohm
N0281EEC VRD-RA2EE103J
R406
Oxide Film,
3.9k ohm, 1W,
±5%
N0237EGD
VRS-VV3AB392J
R407
1
0k
ohm
N0281EEC VRD-RA2EE103J
R408
1.2k ohm
N0199EEC
VRD-RA2EE122J
R409
820 ohm
N0187EEC VRD-RA2EE821J
R410 1 20
ohm
N0136EEC
VRD-RA2EE121J
R411
Carbon,
1.5k ohm,
1/8W, ±5%
N0206EBC
VRD-RA2BE152J
R412
Carbon,
1.8k
ohm,
1/8W,
±5%
N0210EBC
VRD-RA2BE182J
R413
Carbon,
470
ohm, 1/8W,
±5%
N0169EBC VRD-RA2BE471J
R414
Carbon,
330
ohm,
1/8W,
±5%
N0159EEC VRD-RA2BE331J
R415
330
ohm
N0189EEC
VRD-RA2EE331J
R416
See
Controls
(PCB-A)
R417
See
Controls
(PCB-A)
R421
1.2k ohm
N0199EEC
VRD-RA2EE122J
R422
See
Controls
(PCB-A)
R423
270
ohm
N0155EEC
VRD-RA2EE271J
R424
Oxide Film,
470
ohm,
1W,
±5%
N0169EGD
VRS-VV3AB471J
R425
Carbon,
270 ohm,
1/2W,
±5%
N0155EFC
VRD-RA2HD271J
R426
Carbon, 270
ohm,
1/2W,
±5%
N0155EFC
VRD-RA2HD271J
-R427
Carbon, 270
ohm,
1/2W,
±5%
N0155EFC
VRD-RA2HD271J
R451
Carbon,
680 ohm,
1/8W,
±5%
N0183EBC
VRD-RA2BE681J
R452
Carbon, 1.5k
ohm, 1/8W,
±5%
N0206EBC
VRD-RA2BE152J
R453
470
ohm
N0169EEC VRD-RA2EE471J
R454
Carbon,
820
ohm,
1/8W,
±5%
N0187EBC VRD-RA2BE821J
R455
1.2k ohm
N0199EEC
VRD-RA2EE122J
R456
8.2k
ohm
N0122EEC
VRD-RU2EE822J
R461
Carbon,
680
ohm,
1/8W, ±5%
N0183EBC
VRD-RA2BE681J
R462
Carbon,
1.5k
ohm,
1/8W,
±5%
N0206EBC
VRD-RA2BE152J
R463
470 ohm
N0169EEC
VRD-RA2EE471J
33

REF.NO.
DESCRIPTION
RS
PART
NO.
MFR'S PART
NO.
3464
3465
3466
3468
3471
3472
3473
3474
3475
3476
3481
3482
3483
3484
3485
3486
3491
3492
3493
3503
3504
3
505
3506
=
507
=
508
=
509
=
510
=
511
=
512
=
513
=
514
=
515
=
516
=
518
=
519
=
520
=
521
=
523
3524
=
525
3526
=
527
3528
=
550
=
551
3552
=
603
3604
A
A
Carbon,
820
ohm,
1/8W,
±5%
1.2k ohm
8.2k ohm
See
Controls
(PCB-A)
Carbon, 680
ohm,
1/8W,
±5%
Carbon,
1.5k ohm,
1/8W,
±5%
470 ohm
Carbon,
820 ohm,
1/8W, ±5%
1.2k
ohm
8.2k
ohm
Oxide
Film,
82
ohm,
3W, ±5%
Carbon,
330
ohm,
1/8W, ±5%
1
20k
ohm
10k
ohm
680 ohm
100 ohm
Carbon, 560 ohm,
1/8W,
±5%
56 ohm
5.6k ohm
390 ohm
Carbon,
2.7k
ohm,
1/8W,
±5%
10k
ohm
Oxide Film,
82 ohm,
1W,
±5%
See Controls
(PCB-A)
Carbon,
4.7
ohm,
1/2W,
±5%
Carbon, 4.7k
ohm,
1/8W,
±5%
470 ohm
Carbon, 12k
ohm,
1/8W,
±5%
Carbon, 47k
ohm,
1/8W,
±5%
3.3k
ohm
See
Controls
(PCB-A)
4.7k ohm
3.3k ohm
Carbon,
5.6 ohm,
1/2W,
±5%
Carbon,
390 ohm,
1/2W,
±5%
Oxide
Film,
390
ohm, 1W,
±5%
Oxide Film,
680
ohm, 2W,
±5%
Not
used
£xtde
Film,
15
ohm,
2W,
±5%
82
ohm
See
Controls (PCB-A)
Not
used
Not
used
Oxide
Film,
3.3k ohm, 1W,
±5%
Oxide Film,
2.2k ohm,
1W,
±5%
Oxide
Film,
270
ohm,
1W,
±5%
15k ohm
8.2k
ohm
N0187EBC
N0199EEC
N0122EEC
N0183EBC
N0206EBC
N0169EEC
N0187EBC
N0199EEC
N0122EEC
N0122EJD
N0189EEC
N0375EEC
N0281EEC
N0183EEC
N0132EEC
N0176EBC
N0107EEC
N0257EEC
N0162EEC
N0224EBC
N0281EEC
N0122EGD
N0040EFC
N0247EBC
N0169EEC
N0288EBC
N0340EBC
N0230EEC
N0247EEC
N0230EEC
N0052EFC
N0162EFC
N0162EGD
N0183EHD
N0074EHD
N0122EEC
N0230EGD
N0216EGD
N0155EGD
N0297EEC
N0271EEC
VRD-RA2BE821J
VRD-RA2EE122J
VRD-RU2EE822J
VRD-RA2BE681J
VRD-RA2BE152J
VRD-RA2EE471J
VRD-RA2BE821J
VRD-RA2EE122J
VRD-RU2EE822J
VRS-VV3LB820J
VRD-RA2BE331J
VRD-RA2EE124J
VRD-RA2EE103J
VRD-RA2EE681J
VRD-RA2EE101J
VRD-RA2BE561J
VRD-RA2EE560J
VRD-RA2EE562J
VRD-RA2EE391J
VRD-RA2BE272J
VRD-RA2EE103J
VRS-VV3AB820J
VRD
VRD
VRD
VRD-
VRD
VRD
RA2HD4R7J
RA2BE472J
RA2EE471J
RA2BE123J
RA2BE473J
RA2EE332J
VRD-RA2EE472J
VRD-RA2EE332J
VRD-RA2HD5R6J
VRD-RA2HD391J
VRS-VV3AB391J
VRS-VV3DB681J
VRS-VV3DB150J
VRD-RA2EE820J
VRS-VV3AB332J
VRS-VV3AB222J
VRS-VV3AB271J
VRD-RA2EE153J
VRD-RA2EE822J
34

REF.NO.
DESCRIPTION
RS PART NO. MFR'S
PART
NO.
R605
33k
ohm
N0324EEC VRD-RA2EE333J
R606
12k ohm N0288EEC VRD-RA2EE123J
R607 See
Controls
(PCB-A)
R608
680k
ohm N0433EEC VRD-RA2EE684J
R609 220
ohm
N0149EEC VRD-RA2EE221J
R612
220 ohm
N0149EEC
VRD-RA2EE221J
R613
A
Oxide
Film, 47
ohm,
3W, ±5% N0099EJD
VRS-VV3LB470J
R614 100
ohm
N0132EEC
VRD-RA2EE101J
R615
AA
Carbon,
47
ohm,
1/2W, ±5% N0099EFC VRD-RA2HD470J
R616
100 ohm N0132EEC
VRD-RA2EE101J
R617
3.9k
ohm N0237EEC
VRD-RA2EE392J
R618
AA
10k
ohm
N0281EEC
VRD-RA2EE103J
R619
AA
Carbon, 10k ohm,
1/8W,
±5% N0281EBC
VRD-RA2BE103J
R620 100
ohm
N0132EEC
VRD-RA2EE101J
R621
100 ohm
N0132EEC VRD-RA2EE101J
R622 4.7k ohm
N0247EEC
VRD-RA2EE472J
R623
See Controls
(PCB-A)
R624
15k ohm
N0297EEC
VRD-RA2EE153J
R626 Oxide Film, 560
ohm,
1W,
±5%
N0176EGD
VRS-VV3AB561J
R631
a
Oxide Film, 10
ohm, 1/2W,
±5%
N0063EFD
VRS-SV2HC100J
R632
A
Oxide Film,
3.3 ohm, 1W,
±5%
N0037EGD
VRN-VV3AB3R3J
R701
A
Cement,
1.8
ohm,
5W, ±10%
N0029FKF
VRW-KP3HC1R8K
R702
180k ohm
N0387EEC
VRD-RA2EE184J
R703
A
A
33k ohm
N0324EEC
VRD-RA2EE333J
R704
a
Oxide Film,
150
ohm, 1/2W,
±5%
N0142EFD
VRS-SV2HC151J
R705
a
Oxide
Film,
330 ohm,
3W, ±5%
N0159EJD
VRS-VV3LB331J
R706
AA
82k
ohm
N0360EEC
VRD-RA2EE823J
R707 See
Controls
(PCB-A)
R708
A
Cement, 2.7
ohm,
5W, ±10%
N0034FKF
RR-WZ0058CEZZ
R709
AA
Carbon,
3.9k ohm,
1/8W,
±5%
N0237EBC
VRD-RA2BE392J
R710
Carbon,
15k
ohm, 1/8W,
±5%
N0297EBC
VRD-RA2BE153J
R711 560 ohm
N0176EEC VRD-RA2EE561J
R712
56
ohm
N0107EEC VRD-RA2EE560J
R713
Carbon, 12k ohm,
1/2W,
±5%
N0288EFC VRD-RA2HD123J
R714 1k
ohm
N0196EEC
VRD-RA2EE102J
R715
A
Oxide Film,
39
ohm,
1/2W,
±5%
N0092EFD VRS-SV2HC390J
R716
A
Oxide Film,
0.68
ohm, 1W,
±5%
N0015EGD
VRN-VV3ABR68J
R717
A
1
ohm
N0022EEC VRD-RA2EE1R0J
R718
A
Carbon, 3.9M ohm,
1/2W,
±10%
N0460FFB
VRC-UA2HG395K
R719
AA
680k
ohm
N0433EEC
VRD-RA2EE684J
R720
1.5k ohm
N0206EEC
VRD-RA2EE152J
R721'
1.2k ohm
N0199EEC
VRD-RA2EE122J
TRANSFORMERS
T601
Horizontal
Driver
ATB0425
RTRNZ0217CEZZ
T602
AA
(Flyback)
ATB0428
RTRNF1545CEZZ
35

REF.NO.
DESCRIPTION
RS
PART
NO.
MFR'S PART
NO.
T701
Power (U.S.A.)
ATA001
RTRNP0361CEZZ
(CANADA)
RTRNP0372CEZZ
T702
Power
Choke
ATA 1062
RTRNC0028CEZZ
SWITCHES
SW501
V-Center
AS0020
QSW-B0006CEZZ
5W701
Power
AS0015
QSW-P0317CEZZ
CONTROLS
3416
Pot,
Sub-Brightness,
B-curve
10k ohm
AP7412
RVR-M7053TAZZ
=1417/
Pot, Brightness,
B-curve
10k
ohm
AP7003
RVR-Z4044CEZZ
3422/
Pot,
Contrast
B-curve 100
ohm
3507/ Pot, V-Size, B-curve
100
ohm
3514/ Pot,
V-Hold,
B-curve 5k
ohm
3623
Pot,
H-Center,
B-curve
50k
ohm
3468 Pot,
Brown AD
J,
B-Curve
5k
ohm
AP6690
RVR-M7198TAZZ
3526
Pot, V-Line,
B-curve
500
ohm
AP7416
RVR-B4456CEZZ
3607 Pot,
H-Hold, B-curve
5k ohm
AP7419
RVR-B4460CEZZ
3707
AA
Pot,
B + ADJ,
B-curve
1k ohm
P-7681
RVR-B4457CEZZ
MISCELLANEOUS
=R701
A
Posistor
T-1251
RMPTP0026CEZZ
Holder,
Fuse
F-1406
QFSHD1002CEZZ
REF.IMO.
DESCRIPTION
RS
PART
NO.
MFR'S PART
NO.
P.C.B.
Assembly,
CRT
Socket
(PCB-B)
AX
9204
DUNTK4164RA0H
Consists of
the following:
CAPACITORS
3850
Ceramic, 150pF,
50V,
db5%
CC151KJCP
VCCSPA1HL151J
3851
Ceramic, 150pF,
50V,
±5%
CC151KJCP
VCCSPA1HL151J
3852
Ceramic,
150pF, 50V,
±5%
CC151KJCP
VCCSPA1HL151J
C853
Ceramic,
150pF, 50V,
±5%
CC151KJCP
VCCSPA1HL151J
C854
Ceramic,
180pF,
50V,
±5%
CC181JJCP
VCCSPA1HL181J
3855
Ceramic,
180pF, 50V,
±5%
CC181JJCP
VCCSPA1HL181J
C856
See
Controls
C857
See
Controls
C858
See
Controls
C859
Ceramic,
0.0
VF,
1.4KV,
±20%
CC103MYCP
RC-KZ007JCEZZ
C860
Electrolytic,
22/JF,
250V,
+50-10%
CC226WRAP
VCEAAH2EW226Y
36

REF.NO.
DESCRIPTION
RS
PART
NO.
MFR'S PART
NO.
CONNECTOR
(Socket)
CRT
Socket,
8-pin
AJ6018
QSOCV0819CEZZ
TRANSISTORS
Q851
2SC2068 (LB)
Red output, Silicon,
NPN
2SC2068LB
VS2SC2068LB1E
Q861
2SC2068
(LB) Green output, Silicon,
NPN
2SC2068LB
VS2SC2068LB1E
Q871
2SC2068 (LB)
Blue output,
Silicon,
NPN
2SC2068LB
VS2SC2068LB1E
RESIS
TORS:
Unless
otherwise
specified,
resistors
are
1/8W,
±5%,
Carbon
type.
R850
47
ohm
N0099EBC
VRD-RA2BE470J
R851 47
ohm
N0099EBC
VRD-RA2BE470J
R852
47 ohm
N0099EBC
VRD-RA2BE470J
R853
1
50 ohm
N0142EBC
VRD-RA2BE151J
R854
270 ohm
N0155EBC
VRD-RA2BE271J
R855
1
50 ohm
N0142EBC
VRD-RA2BE151J
R856
See Controls
(PCB-B)
R857
1 50
ohm
N0142EBC
VRD-RA2BE151J
R858
See
Controls
(PCB-B)
R859
820 ohm
N0187EBC
VRD-RA2BE821J
R860
820
ohm
N0187EBC
VRD-RA2BE821J
R861 820
ohm
N0187EBC
VRD-RA2BE821J
R862
See
Controls
(PCB-B)
R863
See
Controls
(PCB-B)
R864
See
Controls
(PCB-B)
R865
A
Oxide Film,
5.6k
ohm,
2W
±5%
N0257EHD
VRS-VV3DB562J
R866
A
Oxide Film,
5.6k
ohm,
2W,
±5%
N0257EHD
VRS-VV3DB562J
R867
A
Oxide
Film,
5.6k
ohm,
2W,
±5%
N0257EHD
VRS-VV3DB562J
R868
Solid,
2.7k
ohm,
1/2W,
±10%
N0224EFB
VRC-MA2HG272K
R869
Solid,
2.7k
ohm,
1/2W, ±10%
N0224EFB
VRC-MA2HG272K
R870
Solid,
2.7k ohm,
1/2W,
±10%
N0224EFB
VRC-MA2HG272K
R871
Carbon,
220k
ohm,
1/4W,
±5%
N0396EEC
VRD-RA2EE224J
R872
Solid,
470k
ohm,
1/2W,
±10%
N0423FFB
VRC-MA2HG474K
SWITC
:h
SW851
Luminance
Video
Cut-off
AS0016
QSW-B0017CEZZ
CONTROLS
R856 Pot,
Red Drive,
B-curve
500
ohm
AP0002
RVR-B4563CEZZ
37

REF.NO.
DESCRIPTION RS
PART
NO.
MFR'S
PART NO.
R858
R862
R863
R864
Pot, Blue
Drive, B-curve 500
ohm
Pot, Red
Bias,
B-curve
5K
ohm
Pot, Green
Bias,
B-curve 5K ohm
Pot, Blue Bias,
B-curve
5K ohm
AP0002
AP0003
AP0003
AP0003
RVR-B4563CEZZ
RVR-B4567CEZZ
RVR-B4567CEZZ
RVR-B4567CEZZ
MISCELLANEOUS
SG850
A
SG851
A
SG852
A
SG853
A
Spark
Gap
Spark Gap
Spark Gap
Spark Gap
C-1615
C-1615
C-1615
C-1489
QSPGC0015CEZZ
QSPGC0015CEZZ
QSPGC0015CEZZ
QSPGC0011CEZZ
REF.NO. DESCRIPTION
RS
PART NO. MFR'S PART NO.
P.C.B. Assembly, LED (PCB-C)
Consists
of
the following:
AX9205
DUNTK4165RA0H
CONNECTOR
NA-NC
Socket
for
Main PCB,
2 pin
AJ-4028 CSOCN0230RA03
DIODE
D718
GL-9PR24
AL0010
RH-PX0161CEZZ
MISCELLANEOUS
(Parts
not
located
on
the
PCBs.)
A
L701
CRT
AA
DY601AA,
Cord,
AC
Coil, Automatic Degaussing
(U.S.A.)
(CANADA)
Magnet,
Purity and
Static
Convergence
Picture Tube (E8093B22(PD))
Yoke, Deflection
(U.S.A.)
(CANADA)
^»
Signal
Input
Cable Unit
(U.S.A.)
(CANADA)
AW1012
HC3479
AXX8018
ATB0429
AW
1023
QACCD5005CEZZ
RCILG0244CEZZ
RCILG0240CEZZ
PMAGF3006CEZZ
VBE8093B22/1Y
RCILH1477CEZZ
RCILH1482CEZZ
QCNW-0585CEZZ
QCNW-0602CEZZ
38

3. Cabinet Parts
List
REF.IMO.
DESCRIPTION
RS
PART
NO.
MFR'S
PART
NO.
101 Cabinet
Ass'y,
Front (U.S.A.)
AZ0043
CCABA1527TAKB
(CANADA)
CCABA1565TAKB
101-1
Cabinet, Front
(U.S.A.)
GCABA1527CEKB
(CANADA)
GCABA1565CEKB
101-2
Door,
Control
ADA-0242
GDORF1430CESA
101-3
Plate, Control
Door
HINDP2328CESA
101-4
Button, Power
Switch
AK0336 JBTN-1305CEKB
101-5
Spring, Button
ARB5023 MSPRC0072CEFW
104-6
Badge,
TANDY
AHC0049
HBDGZ3065CESA
101-7
Felt
Door
BK0337
GCOVH9182CE09
102 Cabinet Ass'y,
Rear
(U.S.A.)
A20031
CCABB1560TAKA
(CANADA)
CCABB1594TAKA
102-1
Cabinet, Rear
(U.S.A.)
GCABB1560CEKA
(CANADA)
GCABB1594CEKA
102-2
Label,
Warning (U.S.A.)
TCAUS3062CEZZ
(CANADA)
TCAUS3055CEZZ
102-3
Label, X-Ray Caution (U.S.A.)
TCAUH0092TAZZ
Warning (CANADA)
TCAUS3052CEZZ
102-4
Shield
PSLDM3588CEFW
102-5
Clip, Shield
LX-LZ0022TAZZ
103 Screw, 5 x 30mm,
Tapping-1,
Hexagon Head
LX-TZ3042CEFD
104
Screw, 3 x 6mm,
Machine, Bind Head
(U.S.A.
Up to
55000/CANADA
Up
to 7000)
XHBSD30P06000
Screw, 3 x
8mm,
Machine,
Binding Head
XHBSD30P08000
(U.S.A.
55001
-/CANADA
7001
~)
105 Knob, Control
AK0338
JKNBK1168CEKA
106 Bracket,
AC
Cord
(U.S.A.
Up to
21987,
55001
-)
LANGK0288CESA
(USA
21988-55000)
LANGK0298CESA
(CANADA)
LANGK0276CESA
107 Wire
Holder,
Black
LHLDW1033CE00
108
Label,
Model
NO.
(U.S.A.)
TLABM1692CEZZ
(CANADA)
TLABM1723CEZZ
109 Spring,
Grounding Strap
MSPRT0020CEZZ
110
Wedge, Yoke
PSPAG0028CEZZ
111
Wire, Grounding
Strap
QEARC1405CEZZ
112 Not used
HARDWARE
KIT
113
AHW2501021
DBNW-0001RA0H
Screw, 4 x 20mm,
Tapping-1,
Brazier Head
XTASD40P20000
114
Screw, 4 x 12mm,
Tapping-1,
Brazier Head
AHD3007
XTASD40P
12000
115
Wire Holder,
White
(U.S.A.)
LHLDW1037CEZZ
116
Shield
case,
FBT
PSLDM3614CEFW
117
Screw,
4 x
10mm,
Tapping-2,
Brazier
Head
XCASD40P
10000
118
Heat
Sink
(Q501,
Q502)
PRDAF0258TAFW
119
Screw, 3 x 8mm,
Machine, Pan Head
AHD-2915
LX-BZ3100CEFD
39

REF.NO.
DESCRIPTION
RS
PART
NO.
MFR'S
PART
NO.
120
Heat
Sink
(Q602)
PRDAR1156CEFW
121
Screw, 3 x
16mm,
Tapping-2,
Binding
Head
AHD3001
LX-CZ3004CEFU
122
Heat Sink
(SCR701)
PRDAR5043CEFW
123
Not used
124
Holder,
LED
ART0105
LHLDZ9055CEZZ
125
Wire
Holder,
White
LHLDW1047CEUZ
126
Wire
Holder,
Black
LHLDW1005GEZZ
127
Wire
Holder,
White
LHLDW1015TAZZ
128
Holder,
AC
Cord
Stopper
(U.S.A.)
LHLDW1001TA00
(CANADA)
LHLDK1010CEZZ
129
Wire
Holder,
White
LHLDW1019CEZZ
130
Label,
Model
NO. (CANADA)
TLABN0042CEZZ
131
Label, Address
(CANADA)
TLABZ0107CEZZ
132
Label,
Fuse
Caution
(CANADA)
TCAUS3111CEZZ
133
Label,
Fuse
Caution
(CANADA)
TCAUS3095CEZZ
134
Label,
CSA
(CANADA)
TLABS0003CEZZ
135
Screw,
4 x
8mm,
Machine, Pan Head
XBPBW40P08000
136
Spring
Washer
XWSPW42-10000
137
Nut,
4 x 3.2mm
XNEBW40-32000
138
Screw,
3 x
8mm,
Tapping-2, Brazier Head
XCASD30P08000
139
Wire
Holder
LHLDW1002GEZZ
140
Ferrite Core,
FB701 (U.S.A. 21
988-
RCORF0001CEZZ
141
Screw,
3 x
10mm, Machine, Pan Head (U.S.A.
21
988-
XBPSD30P10JS0
142
Ground
Plate (U.S.A.
21
988
~)
QEARP0018CEFW
143
Screw
(Ground)
(U.S.A.
21988-55000)
LX-BZ3125CEFN
40

SCHEMATIC
DIAGRAM
NOTES:
1
.
The
unit of resistance
"ohm"
is omitted
(K:1000 ohms. M:1 Meg ohm»
2. All resistors are
1/4
watt,
unless
otherwise
noted.
3
.
All capacitors
are
pF, unless
otherwise
noted
(PWiF)
4.
(G)
indicates ±2% tolerance
may
be
used.
VOLTAGE
MEASUREMENT
CONDITIONS:
1 . All
DC voltages
are
measured-
with
SSVM
connected
between
points indicated and
chassis
ground.
Line
voltage
is set
at
120V AC
and
all
contols are
set
for
a
normal
picture
unless
otherwise
indicated.
2.
All
voltages
are measured
with 1000//V
B&W
or
Color
signal.