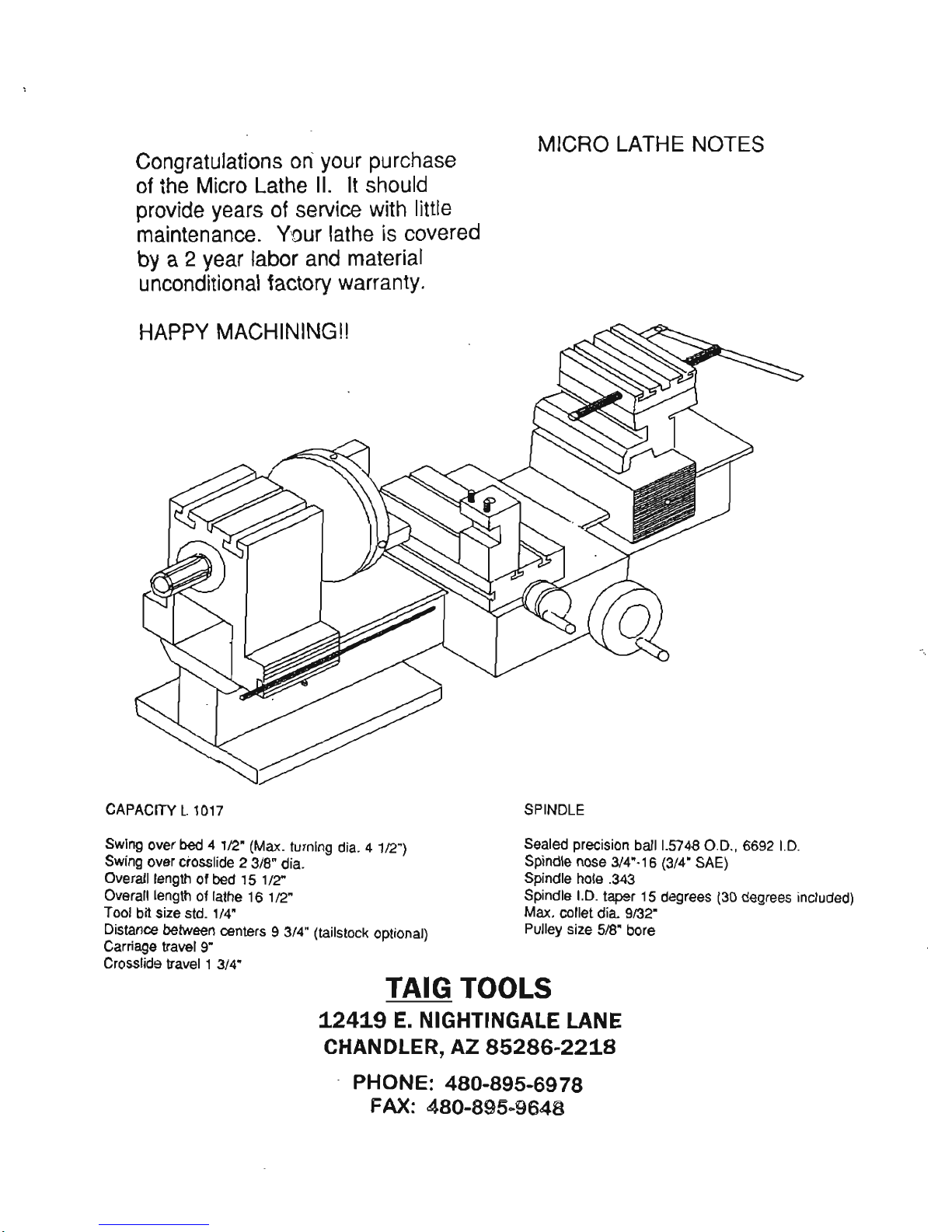
Congratulations
on
your
purchase
of the Micro Lathe II. It should
provide years of service with little
maintenance. Y'our lathe is covered
by a 2 year labor and material
unconditional fact9ry warranty-
HAPPY
MACHININGI!
CAPACITY L
1017
Swing
ov~r
bed 4 1/2" (Max. turning dia. 4 1/2")
Swing
over cross
fide23/S"
dia.
Overall length
of
bed 15 1/2"
Overall lengthoflathe 16 1/2" .
Tool bit size std. 1/4"
Distance between centers 9 3/4" (tailstock optional)
Carriage traver 9"
Crosslide travel 1 3/4"
MICRO LATHE NOTES
SPINDLE
Sealed precision ball
1.5748
0.0.,6692
1.0.
Spindle nose 3/4"..16 (3/4" SAE)
Spindle hole .343
Spindle
1.0.
taper15degrees (30 degrees included)
Max.
collet dia. 9/32"
Pulley size
5/8"
bore
TAIG TOOLS
12419
E.
NIGHTINGALE LANE
CHANDLER, AZ
85286-2218
PHONE: 480-895-6978
FAX: 480-8900.9648
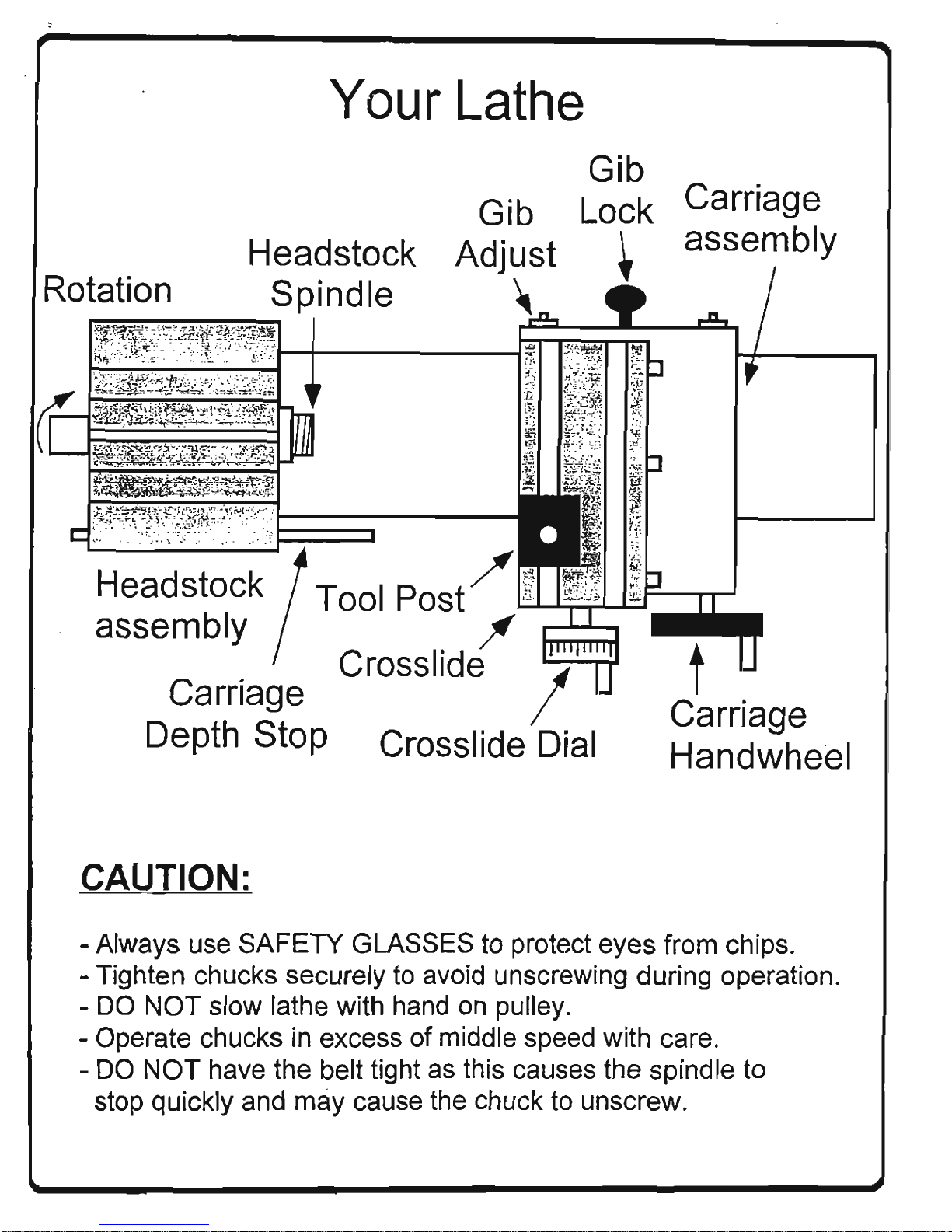
Your Lathe
t
Carriage
"Handwheel
Gib
Lock Carriage
~
assembly
Gib
Adjust
~
Headstock
Spindle
~;.
Headstock Tool Post/
......
~f
...........
--.......!i-----.
......
assembly
;t
Crosslide I
Carriage
Depth Stop Crosslide Dial
~~i~::'~~?:F~:Y~;:~lt~~~~::,;?;-:!;~::""::",I------
..
-.~
;.'
'."~-."::
.~::.~):
~_.,
'
.::/1--
....
Rotation
CAUTION:
- Always use SAFETY GLASSES to protect eyes from chips.
- Tighten chucks securely to avoid unscrewing during operation.
- DO
NOT
slow lathe with hand
on
pulley.
- Operate chucks in excess of middle speed with care.
-
DO
NOT
have the belt tight as this causes the spindle to
stop quickly and may cause the chuck to unscrew.
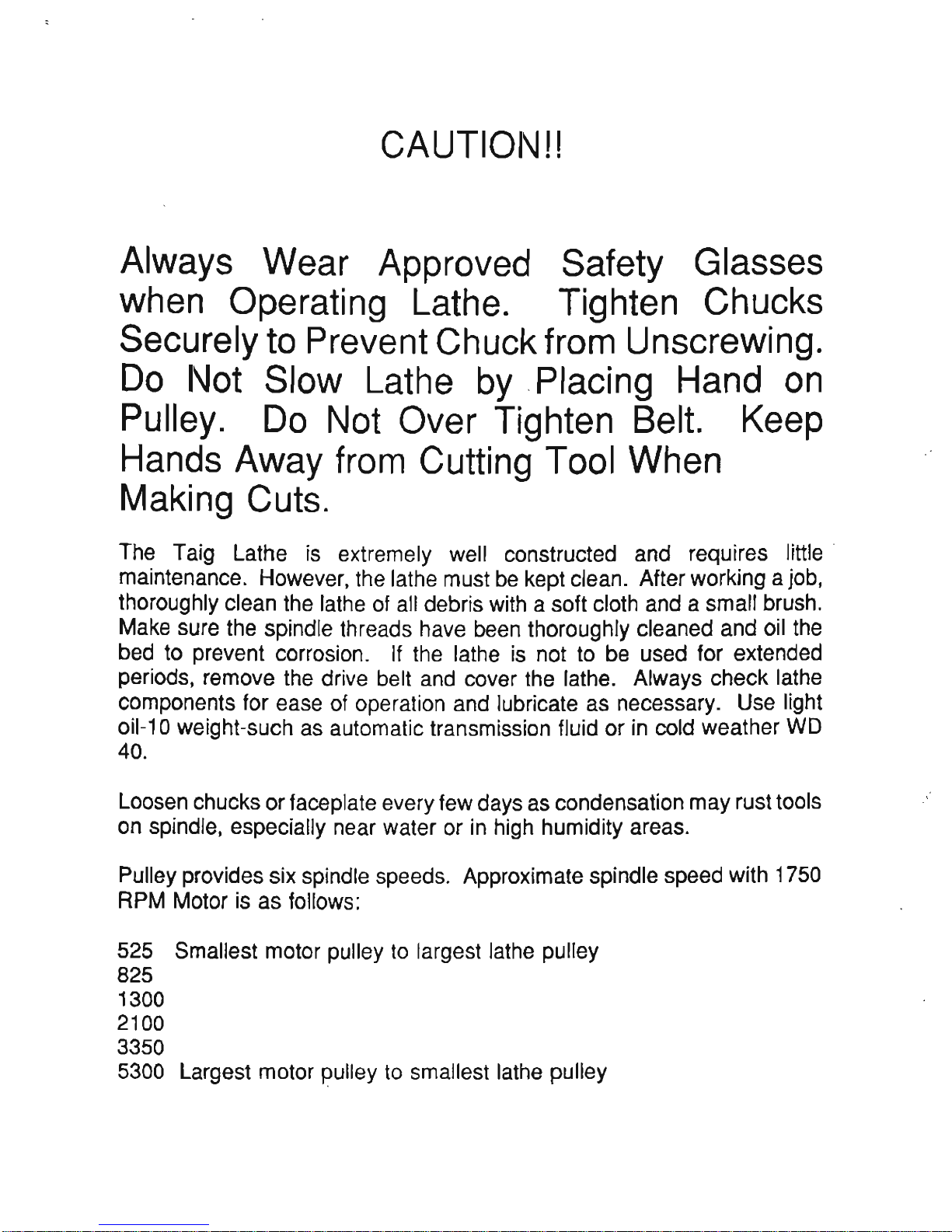
CAUTIONII
Always Wear Approved Safety Glasses
when Operating Lathe. Tighten Chucks
Securelyto Prevent Chuckfrom Unscrewing.
Do Not Slow Lathe
by.
Placing Hand on
Pulley. Do Not Over Tighten Belt. Keep
Hands Away from Cutting Tool When
Making Cuts.
The
Taig Lathe
is
extremely well constructed
and
requires little'
maintenance. However,
the
lathe must
be
kept clean. After working ajob,
thoroughly clean the
lathe
of
all
debris
with
a soft cloth
and
a small
brush.
Make
sure the spindle threads have
been
thoroughly cleaned
and
oil
the
bed
to prevent corrosion.
If
the
lathe
is
not
to
be
used for extended
periods, remove
the
drive belt
and
cover
the
lathe. Always check lathe
components for ease
of
operation
and
lubricate
as
necessary.
Use
light
oil-10 weight-such
as
automatic transmission fluid orincold weather
WD
40.
Loosen
chucks or faceplate every few days
as
condensation may rust tools
on
spindle, especially near water or
in
high
humidity areas.
Pulley provides six spindle speeds. Approximate spindle speed with
1750
RPM
Motorisas follows:
525 Smallest motor pulley
to
largest
lathe
pulley
825
1300
2100
3350
5300
largest motor pulley to smallest lathe pulley
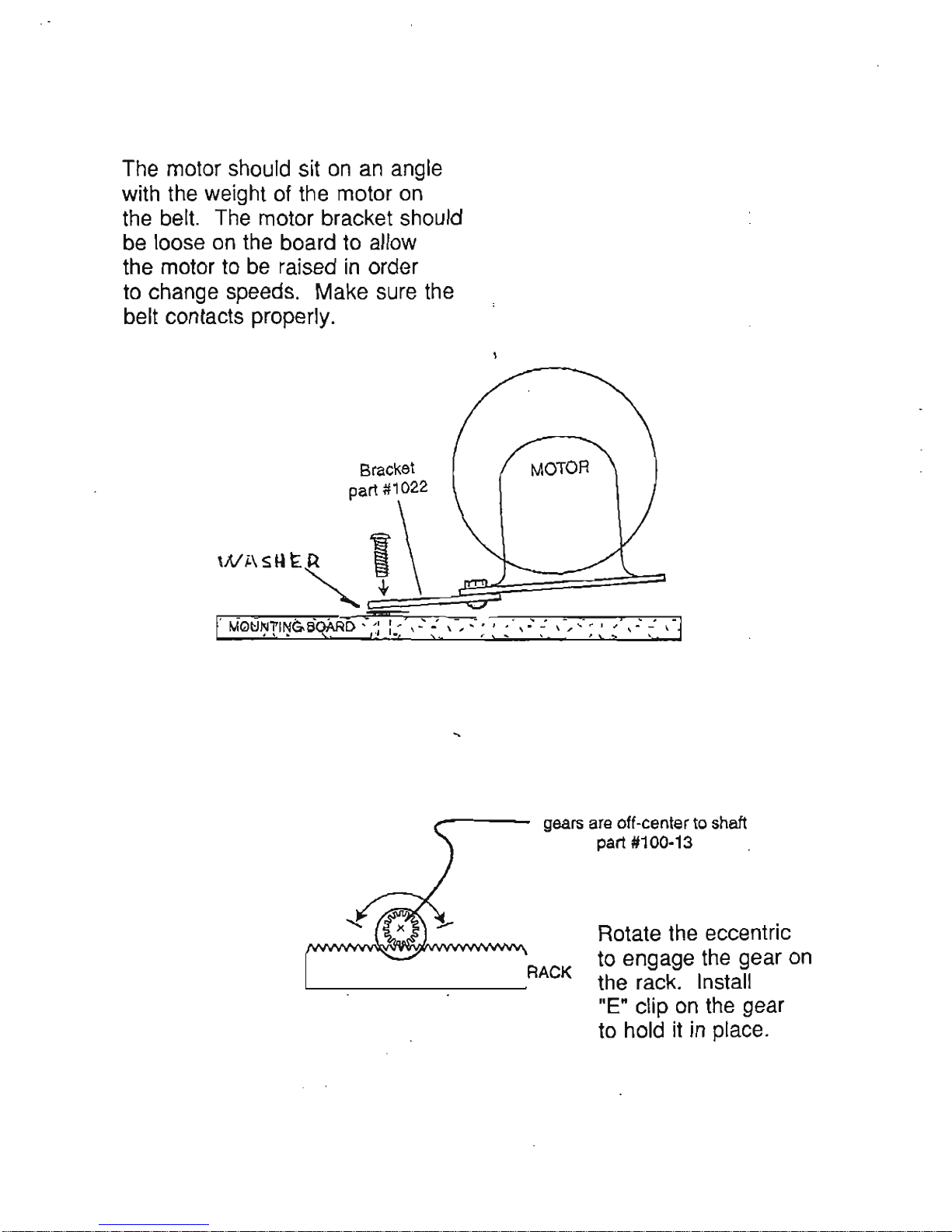
The motor should sit on an angle
with the weight of the motor
on
the
belt. The motor bracket should
be loose on the board to allow
the motor to be raised in order
to change speeds. Make
sure
the
belt contacts properly.
\A!j:\sll
t R 1
~
r.1~
:=hd~=~
rMG8N1'ING-BOARb'~'~:
,-,,,-.,
,',::':
,-,.:..,
,',::
\-1
~
"
~
" >
'-;1
;:;;
.-.
')
. "
)...
,
,)...
, J
gears
are
off-centertoshaft
part #100·13
RACK
Rotate the eccentric
to engage the gear on
the rack. Install
"E" clip
on
the gear
to hold it
in
place.
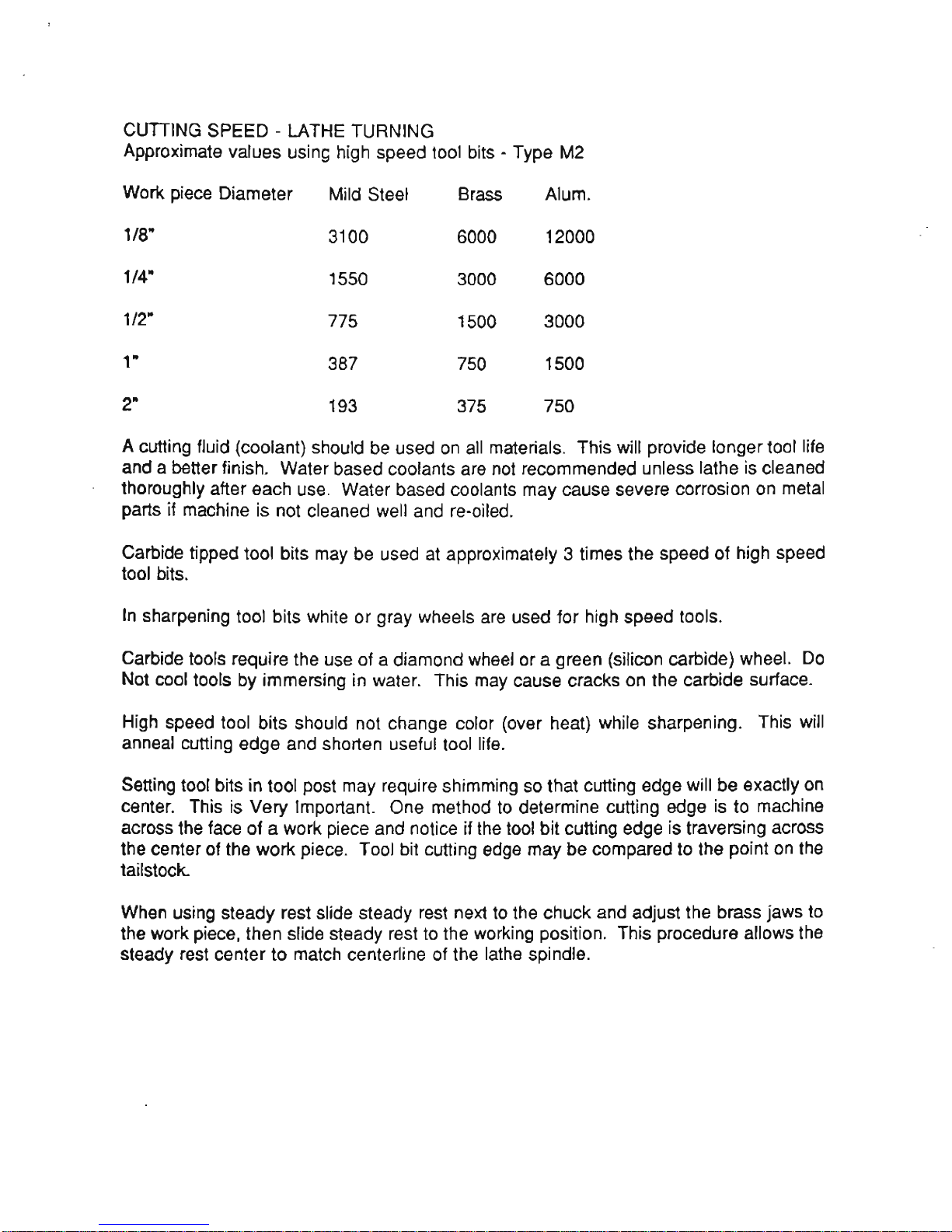
CUTIING
SPEED - LATHE TURNING
Approximate values using high speed tool bits - Type M2
Work piece Diameter
Mild Steel Brass Alum.
1/8"
3100
6000
12000
1/4"
1550
3000
6000
1/2"
775
1500
3000
1"
387
750
1500
2"
193
375 750
Acutting fluid (coolant) should be used on all materials. This will provide longer tool life
and a better finish. Water based coolants are not recommended unless lathe is cleaned
thoroughly after each use.
Water
based coolants
may
cause severe corrosion on metal
parts
if
machine is not cleaned well
and
re-oiled.
Carbide tipped tool bits may be used at approximately 3 times the speed of high speed
tool bits.
In sharpening tool bits white
or
gray wheels are used for high speed tools.
Carbide tools require the use of a diamond wheel or a green (silicon carbide) wheel. Do
Not cool tools by immersing in water. This may cause cracks on the carbide surface.
High speed tool bits should not change color (over heat) while sharpening. This will
anneal cutting edge and shorten useful tool life.
Setting tool bits in tool post may require shimming so that cutting edge will
be
exactly on
center. This is
Very Important. One method to determine cutting edge is to machine
across the face of a work piece and notice if the tool bit cutting edge is traversing across
the center of the
work
piece. Tool bit cutting edge may be compared to the point on the
tailstock.
When using steady rest slide steady rest next to the chuck and adjust the brass jaws to
the work piece,
then
slide steady rest to the working position. This procedure allows the
steady rest center
to
match centerline of the lathe spindle.

Micro
Lathe
Headsock
PART #1026
DEPTH
STOP
J
TIIf
«1J~l.6-1
---.-..ft
....
ulICJilrnB
Lathe
Chuck
DelJlll
Slop
I
Ilstal
I
ed
ill
SpiJldle
• Used to provide stop for workpiece held
in
chuck
• Parts held
in
chuck
Inay
be
I11achined
to
saine length
• Jaws are independently adjusted
in
pairs. Four-jaw chucks are by far
tile
ITIOst vesatile
of
all
Cllucks
• Parts Inay
be
machined to run very
true. This will require more time
to
center than a three-jaw. Setting a
workpiece off-center creates crankshaft and cam shapes
Adjust
In
paIrs
PART #1030 FOUR-JAW CHUCK
• Hardened steel with steps
Reversible range
1/8
- 3 1/4 ins.

Your options for workpiece mounting hardwareare as fonows:
Part
1030: 4
Jaw
Oluck
Part
1050: 3
Jaw
Chuck
-----
....

PART #1035·. FACE PLATES
Stop
• Faceplates are used to run shafts
between centers and to fixture spe-
cial
jobs
• Holes can
be
drilled and tapped
i1
needed in faceplate
Faceplate
\Vorkpiece
Special
Stops
Use of Clarnps
Faceplate
Angle
Bracket
PART #1036 1 X 1IN. SQUARE
ANGLE BRACKETS
(2 PIECES)

·
PART#1040
PARTffl042
COLLET
CLOSER
Collet is used
fOl·
sInaI
J
dialnetel· sllaft \vork alld
holding cutters for nlilJing.
Sizes are
1/8, 5/32, 3/16, 7/32,
1/4 &.9/32 iIlclles -- 5/16
illCll
is a stub c.ollet
of
3"/8
illclles
ill
depth.
• Advantages
of
collets are they are fast and accurate and spindle
nlay
be
run at
InaxinlUll1
speed on
altllninUITI
and brass.
• Collets will accept material
that
is
.001 over collet size to .004
under collet size. Bar stock
is
nonnaJly within this tolerance.
Blanl{ Collet #1043
Center
Mark
• Used to modify
staIldal·d screws
•
Ivtay
be
used to
l1lake
special sizes
Drill and tap so screw
will protrude
Macllille llead to
suit

~,
arbornut---
Part
1052: Full Circle
Jaw
Part
1040: Collet
Part
1042: Collet
Coser
Nut
Part
1026: Depth Stop
Part
1043: Blank Collet
collet (slotted, drilled and threaded)
depth stop (drilled and threaded)
blank collet (solid-not
~hined)
collet closer
nut
.~~~
/

PART
#1050
THREE-JAW
CHUCI( ·
To achieve best accuracy
soft
jaws
lTIllSt
be trued on
spindle chuck will be used
011
• Part
#1050
is 3 1/4 inches in
dialnetel·
• All steel scroll
chuck
with
alulninun top
jaws
(commonly
called soft
jaws)
• Three
jaw
chucks
are
used to
hold round and hex material.
•
The
self
centering ability
enables all three
jaws
to
move
at
tIle
same
ti
me.
Belt
~~-
Rotate ring to Inove
jaws
Close
jaws
on
washer
Washer
o
Set
depth Stop
rod to prevent
tool
bit frOll1 washer

1
051
Soft Jaws
( 3 pieces with 6
screws)
1
000
)
Spare Jaws same as supplied with chuck.
~_
Soft Jaws may be machined with steps
such
as
this.
Reverse Jaws as shown to cut steps.
Advantages
of
Soft Jaws
10 Will not damage work piece
as normal hard jaws
do.
2. Greater accuracy can be obtained when
machining jaws for a specific size and
used
on
the same
lathe.
Remember:
When using any chuck always mark workpiece and chuck
jaws so that the part is
in
the same relationshipifremoved
and replaced in chuck - A good idea is to paint one
jaw
with nail polish.

PART #1052 FULL CIRCLE
J~W
."
\ @
'1
Sho\vn \vith steps
• To bore
jaws,
place 1/4 inch
diameter pin
in
center
• Jaws
may
be
cut
with steps to
hold thin disks
or
clock gears
• Thin wall tubes that regular three-
jaws
would damage
may
be held by
machining
jaws
to
exact
size
of
tube so that almost 100% contact
on
tube
will be achieved

Part
1200: Top Slide (Compound)
A compound is used for angles and short tapers
on
the work piece. The
positive length may be achieved by having the compound
90 degrees to
the crosslide and by using the dial on the compound to control the length
of
the
cut.
The compound will attach to either "tee" slot of the crosslide and will rotate
and be clamped at any angle. The tool bit is clamped directly on the table
of
the
compound.

PART #1152.
DIE
HOLDER
•Threads Inay
be
put on a part \vith a button-die. This
is
a round
piece
of
tooled steel with thread-cutting grooves.
The
dialneters
of
small button-dies are 13/16 and 1.00 inches. In this size,
threads may be cutfrom 0-80 to 1/2 inch.
Die
The
purpose
of
a die holder is to align
alld allow the button-die to cut a
tl·ue and
untapered thread..When scre\ving the
button die on workpiece, always have a
45 degree chalnfer (edge brake) on end
of
shaft
to be threaded.
Die
I-Iolder
..---Slide
Button-Die
WORKPlECE I··{ELD
ON
CENTER
BY t-IEA DS
Toe
1\
CHUCK
OR
COLLET

Part
1220: Milling i\ttachment
Approximate
cutting
speed
using
high
speed
end
mills
in
RPM.
Alum.
Brass
Steel
3/16 dia. 2100 1300 525
1/8.dia. 3350 2100 825
1/16 dia. 5300 5300
2100
longer
tool
life
and
better
finishes
may.beobtained
using
a
cutting
fluid.
For
steel a
pipe
thread
cutting
oil
works
very
wen.
For
alum.orbrass
keroseneordiesel
fuel
may
be
used.
The·l220
Milling
Attachment
provides vertical
travelofapprox.13/4
inches.
The
crosslide dial
provides
travel
in·.001
increments
direct reading.
The
cutters
(end
mills)
are
heldinthe
spindle
with
the
colletstoprovide
maximum
ridgidty. Miniature
end
mills
c~me
with
3/16
dia.
bodies
and
various
size
cutting
diameters. The
end
mills
will cut
all
materials
steel,
alum.
t
brass
and
plastics.
o 0
o
o
Carbide
tipped
router
bits
with
1/4
inch
diameter
body
maybeused
·for
cutting
alum
.•
brass,
plastics
and
wood.
They
are
not
recommended
for
steel.
Carbide
tools
should
run
at least
4
times
faster
than
high
speed
end
mills
of comparable
size.