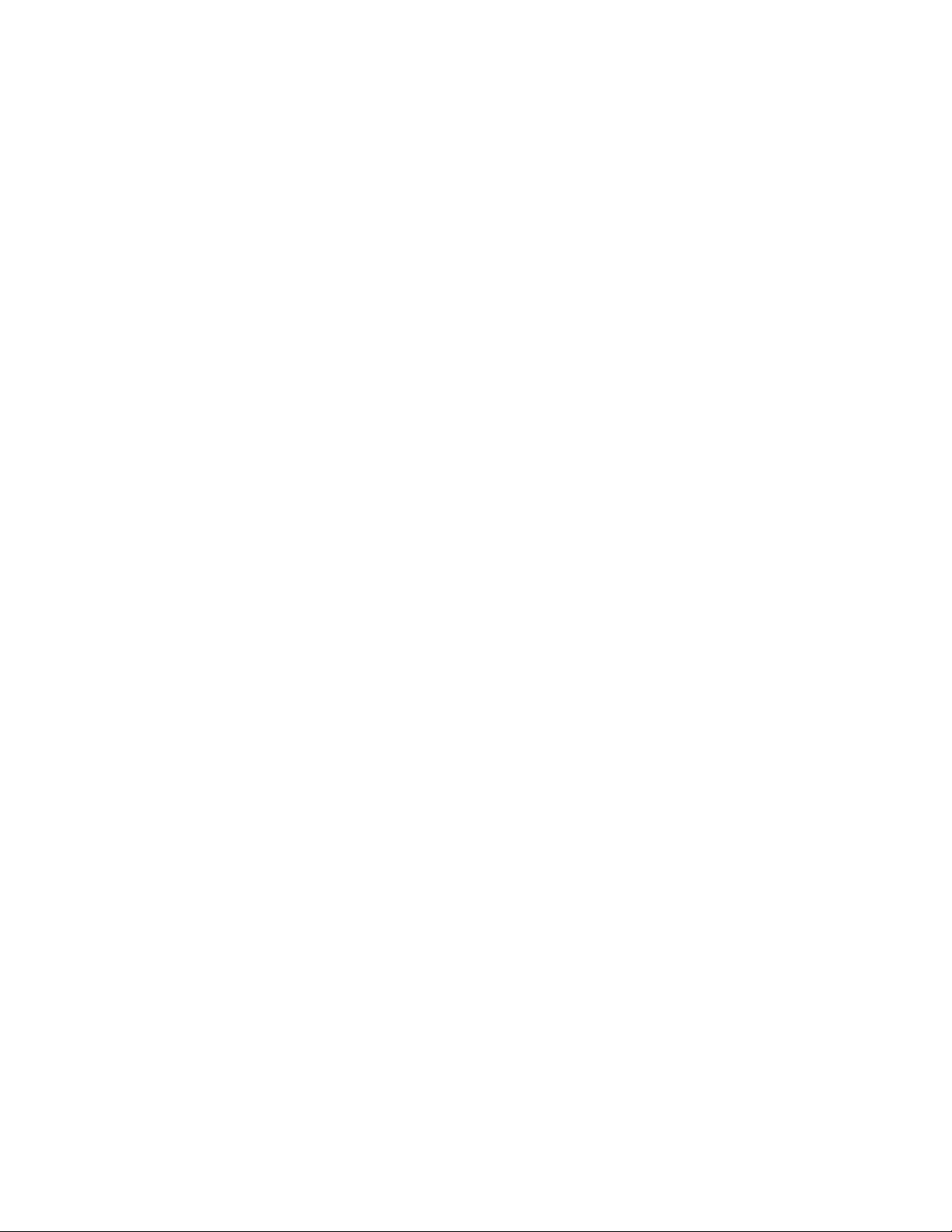
OPERATOR INSTRUCTIONS
This tapping attachment can be used on all types of manually operated
The tap will return to a forward rotation as soon as it is with-drawn
FOR REVERSIBLE TAPPING ATTACHMENT MODEL: HR 3 & 4
machines with rotating non-reversing spindles.
INSTALLING MORSE TAPER ARBOR
Clean the matching taper. Then with a twisting motion, insert the arbor
into the attachment. Strike the tang end of the arbor with a plastic
hammer to lock it firmly. The hex nuts are provided to remove the
arbor.
MOUNTING THE ATTACHMENT TO THE MACHINE
Mount the STOP ARM on the attachment. A circlip is provided to hold
the STOP ARM in place. Now mount the attachment on the machine
spindle. Ensuring that the taper is free of oil and grease. Extend strong
stop bar from machine spindle of machine table to engage short STOP
ARM. DO NOT HOLD STOP ARM BY HAND. DO NOT
LENGHTEN STOP ARM, DO NOT HOLD JOB BY HAND. Clamp
the job securely as full power of the machine is transmitted in reverse.
INSERTING THE TAP
A. MODEL : HR :
Insert the desire tap into the chuck of the attachment. The square
of the tap is fit and centered between adjustable square nuts &
further tighten Chuck Nut which forces the Collect to hold the tap
shank with a firm grip. Slacken adjustable square nut in order to
center the tap. Check that the adjustable square Nuts only grip the
square portion of the tap. Then firmly tighten the Adjustable
square nuts.
B. MODEL : HRF :
The Spindle of the attachment has a quick change device. Press
the bush of the adaptor (Model: QA) and insert the tap. Now
insert the adaptor with the tap into the spindle of the attachment.
To disengage the adaptor, push the bush of the adaptor again.
For each tap with varying shank dimension a different adaptor is
required.
TORQUE SETTING:
The torque adjustments are made by tightening or loosening the cup
nut (3) at the upper end of the attachment. When the desired torque
has been determined, the cup nut may be locked in place by a grub
screw (5). Proper procedure when beginning tapping operation in to
loosen the cup nut so that all the graduations on the body are visible.
Then tighten the cup nut progressively until the attachment will drive
a sharp tap. When the proper torque is determined for a specific job.
This reference point may be noted to save set up time in future. If later
during the operation the clutch slips it is evident that the tap is dull and
should be immediately exchanged for a sharp tap but the clutch should
not be tightened further.
THROUGH HOLE TAPPING:
Press the tap lightly against the mouth of the hole. The free axial float
is provided in the attachment which will automatically permit the tap
to follow its own lead. The operator merely moves the machine’s
spindle behind the lead of the tap until the desired, depth is reached.
To reduce the wear of the attachment it is recommended that a short,
quick upward movement of the machine spindle be made during
transition fro forward to reverse.
from the hole.
BOTTOM HOLE TAPPING
For accurate and efficient bottom hole tapping a machine feed stop
should be used to allow the attachment’s spindle to disengage in
neutral before the tap bottoms in the hole. To achieve this, set the
machine stop so that machine feed plus the attachment’s self feed
will equal the desired thread depth.
If clutch should slip before the tap reaches the desired depth,
check to see that the hole is of the correct size not packed with
chips, and that the tap is sharp and undamaged. The torque
control clutch is designed as a safety device to prevent tap
breakage in ease the tap accidentally hits to the bottom. We do
not recommend using the clutch for repetitive hole tapping unless
absolutely necessary.
TAPPING SPEED
The factors to be considered when trying to determine the best
tapping speed are :
* Material to be tapped.
* Pitch of the thread.
* Selection of tap :
● Length of chamfer on tap
● Rake Angle
● Standard, spiral or spiral point
* The percentage of full thread to be cut.
The tapping speed must be reduced as the Percentage
of full thread to be cut is increased.
* Drilled hole with respect to length of the hole to be tapped.
* Cutting fluid
* Straight or tapered thread to be tapped.
This tapping attachments have been designed to operate at max
800 R.P.M.
CUTTING FLUID :
The cutting fluid works two ways. Heat generated as the tap
proceeds into the hole both by the deformation of the material and
by friction. The fluid must discipate this heat. The fluid must also
lubricate so that the friction between the tap, the chips and the hold
is minimized.
Be sure to use large quantities of cutting fluid under pressure for
tapping. The higher the cutting speed, the deeper the hole and the
tougher the material, the more cutting fluid you will need.
LUBRICATION :
This attachment is prepacked at the factory and only needs periodic additions of grease to maintain proper lubrication. Approximately
every 600 Hrs partially disassemble the attachment and clean ball
bearing and gears. Add a small amount of grease and reassemble. Do
not over lubricate. Excess grease will create internal friction and overheating.
SERVICE OVERHAUL AND REPAIR
Since overhaul and repair are time consuming for someone not
familiar with the attachment, we recommend that they be sent to us.
We will be glad to get your tapping attachment operational again in
shortest possible time.

NOMENCLATURES
Lockring for Clutch Driver
15.
20. Pinion 20 HR3 (b) 3 Nos.
Driver
15 HR3© 15 HR3© 15HR4© 15HR4©
20HR4(b)3Nos 20HR4(b)3Nos
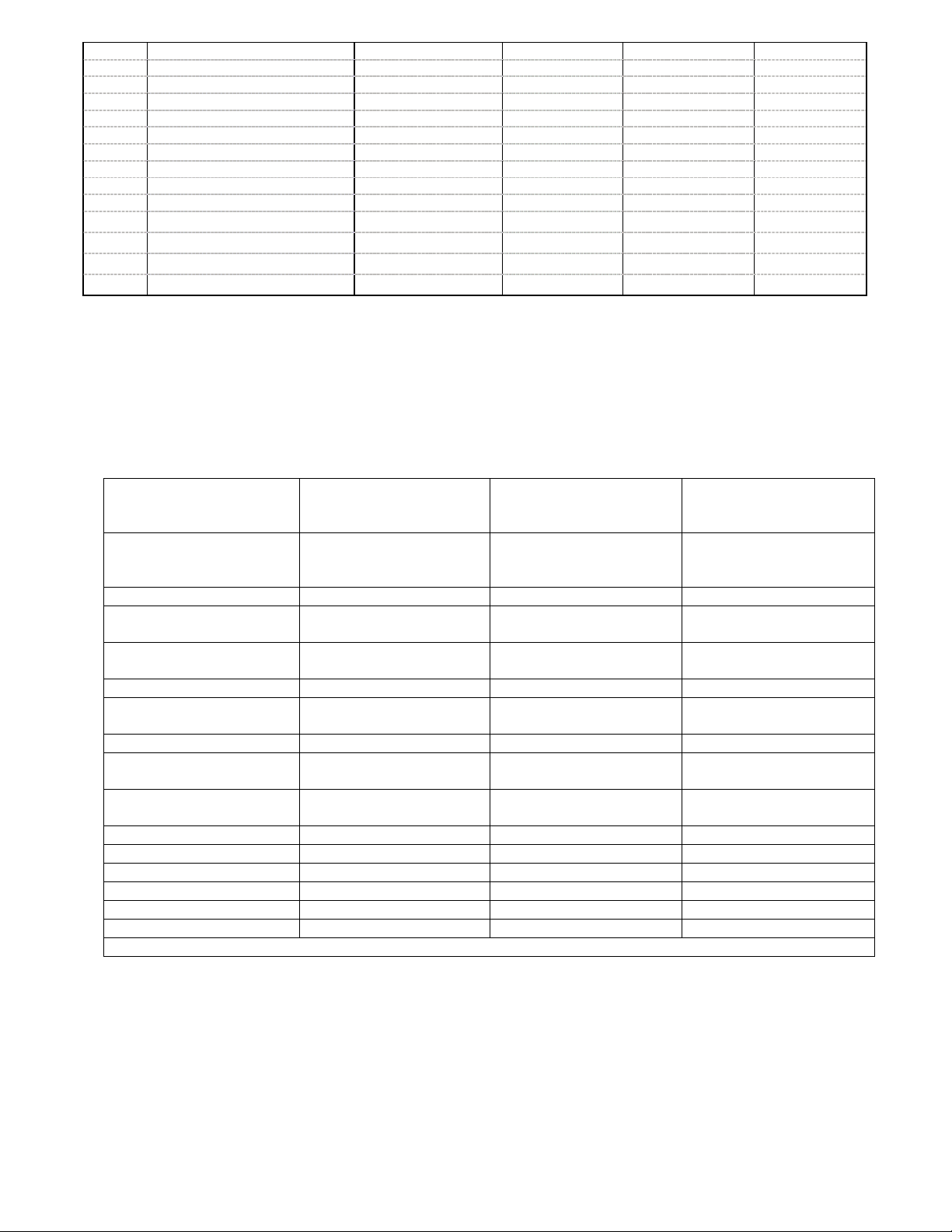
Heavy Chloride base oil
Sulphur-base oil
Soluble oil or light base
oil
Soluble oil or light base
oil
The above information are subject to Tapping Speed instructions
Spring for Pressure Block
Lockring for Pressure Block
55. Balls -- 55HRF3(3Nos) - 55HRF4(3Nos)
56. Knurling Sleeve -- 56 HRF3 - 56HRF4
57. Spring for Kn. Sleeve -- 57 HRF3 - 57HRF4
58. Lockring for Kn. Sleeve -- 58 HRF3 - 58HRF4
Note: - Following parts are only available as an assembly.
(a) Body (1) with Part No. (2) and (45).
(b) Carrier (24) with Part No. (20), (21), (24A), (24B), (24C), (25) and bearing (26).
(c) Bearing (15) with Part No. (13).
(d) Chuck Nut (41) with Part No. (41A) and (41B).
Recommended Cutting Speed
Material Rake Angle
0.10 – 0.50 % C
Molybdenum
10˚ - 15˚
10˚ - 15˚ 10 – 30 Heavy Sulphur-base oil
Speed feet/min
20 – 50
Steel-stainless 10˚ - 15˚ 10 – 23
Steel-cast 10˚ - 15˚ 15 – 50
Brass Drawn 10˚ - 15˚ 60 – 100
Brass Cast 0˚ - 5˚ 60 – 100
Cutting Fluid
Oil emulsion
base oil
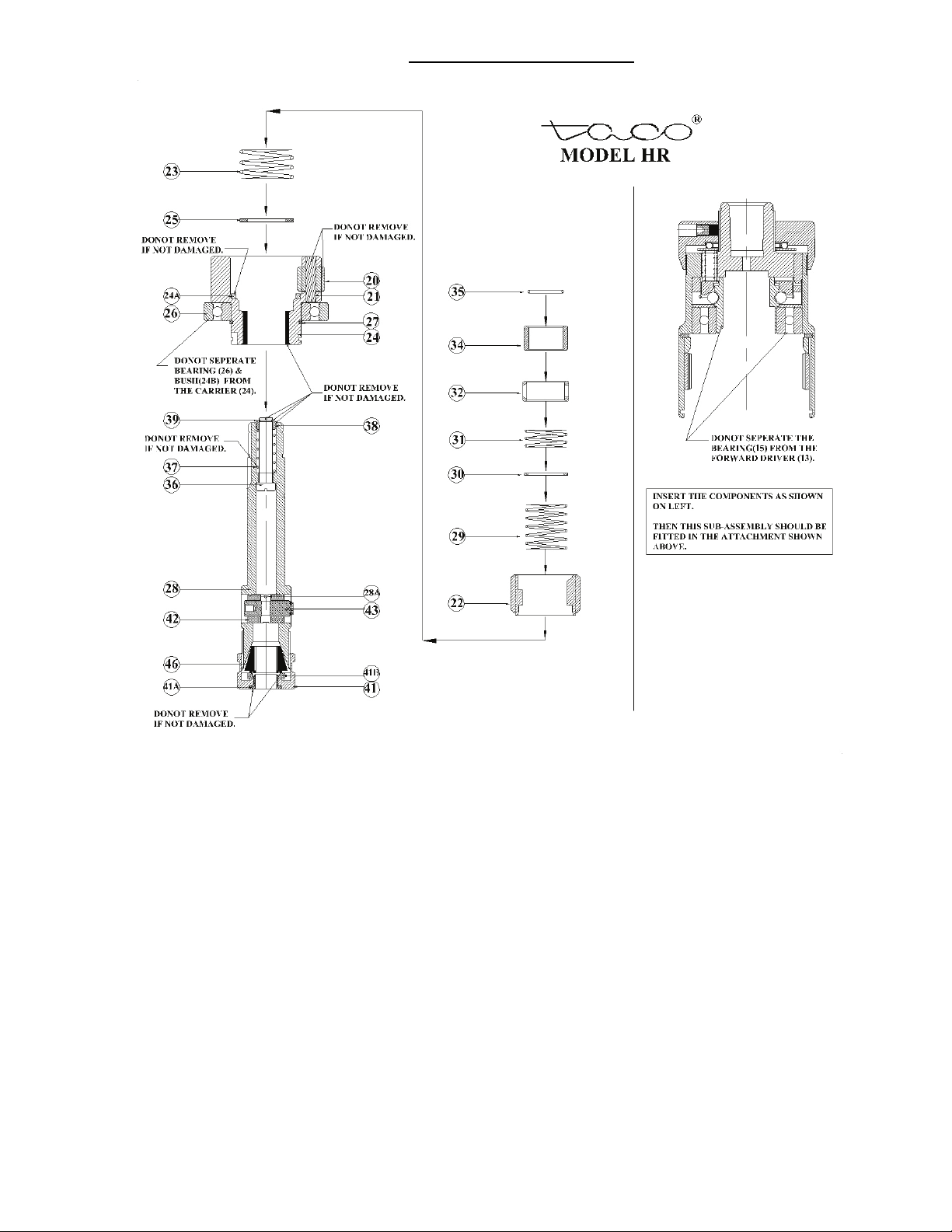
ASSEMBLY PROCEDURE
INSTRUCTIONS FOR DISASSEMBLY
1. Remove Lockring (6) and unscrew cup nut (3).
2. Hold unit in vertical position and remove thrust bearing (8), Washer (7) & Washer (7A).
3. Carefully invert unit over a clean receptable, pressure springs (9 & 10) will drop out.
4. From the lower end remove Chuck Nut (41),Collet (46) if necessary then remove E-Type Circlip (43A) and Loosen L-R stud (43) to remove Nuts(42)
(For Model HR).
5. Remove Circlip (27), Stop Arm (44), Circlip (16) and Bearing Cover (40).Do not remove Circlip (27) which holds bearing.
6. Lift out complete gear – carrier sub-assembly with spindle unit.
7. Remove Gear Ring (18), key (19) and Spacer (17).
8. Remove Lockring (35), Washer (34), Ball Carrier (32), Balls (33) and Spring (31).
9. Lift out Reverse Gear (22) and Spring (23).
10. Remove Lockring (30), Expansion Spring (29) and Washer (25) for relieving spindle unit from Carrier sub-assembly.
11. Remove Circlip (16) for disassembling clutch sub-assembly. Invert the Body over a clean receptable. Lift off pressure plate (11), Balls (14),
Clutch Driver (12). For reassembly pack grease in clutch sub-assembly, so Pressure Plate (11) will stay in place while reassembling Clutch
Bearing assembly.
12. Do not disassemble Ball bearings (15 & 26).
13. Do not disassemble pinion (20) – Carrier (24) sub assembly.
INSRTUCTIONS FOR ASSEMBLY
1. Clean and lubricate all parts requiring lubrication thoroughly.
2. Reverse procedure for assembly.

PROCEDURE FOR MOUNTING THE STOP-ARM