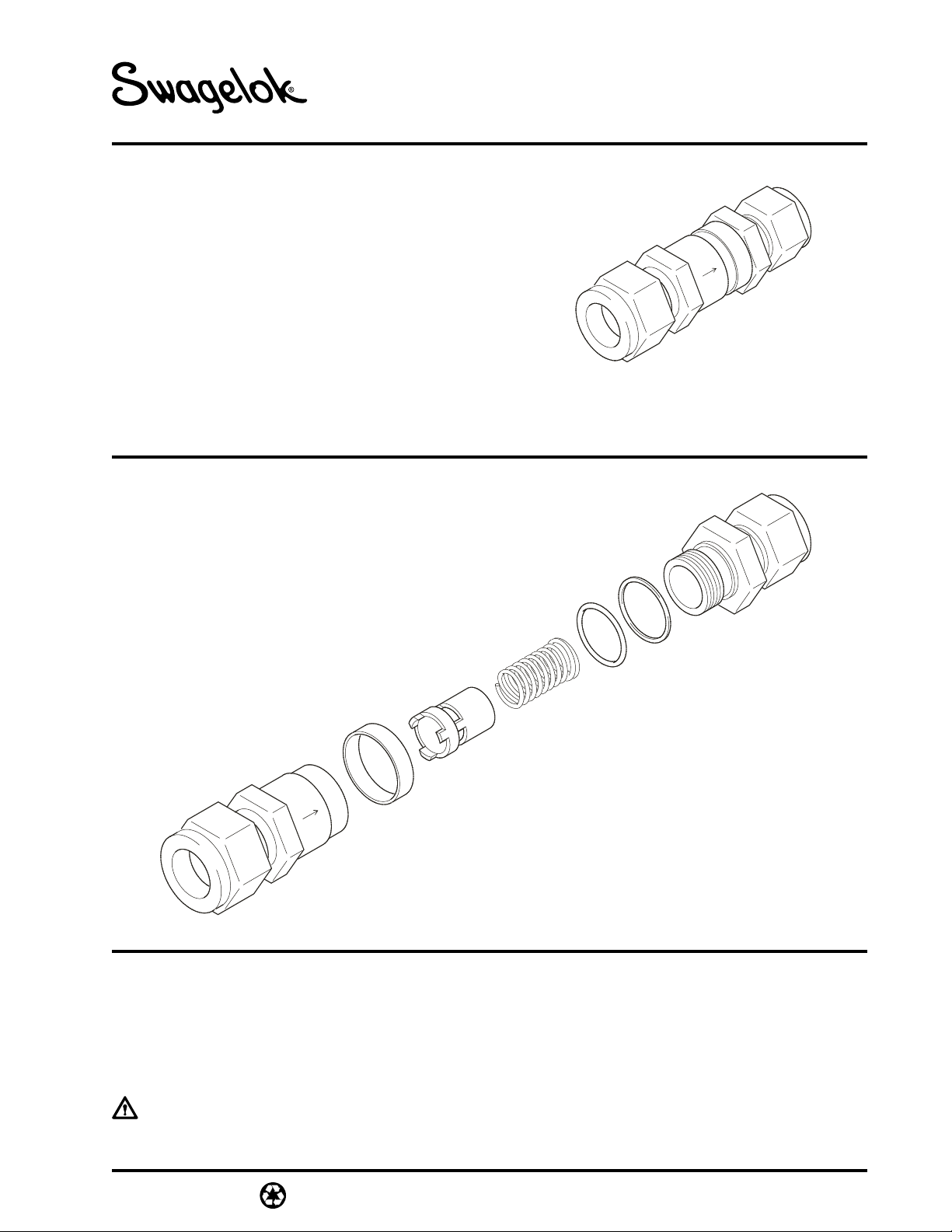
O-ring
Outlet Body
Backup Ring
Spring
Identification Ring
Poppet
Inlet Body
End Connection
End Connection
Body Hex
Body Hex
MS-CRD-0064
Revision 1 6-00-CP
XS Series Excess Flow Valve
Service Instructions
Contents
• Component Identification . . . . . . . . . . . . . . . 1
• Tool Requirements . . . . . . . . . . . . . . . . . . . . 2
• Installation . . . . . . . . . . . . . . . . . . . . . . . . . . 2
• Testing . . . . . . . . . . . . . . . . . . . . . . . . . . . . 2
• Kit Contents . . . . . . . . . . . . . . . . . . . . . . . . . 3
• Maintenance . . . . . . . . . . . . . . . . . . . . . . . . 3
• Troubleshooting . . . . . . . . . . . . . . . . . . . . . . 6
Valve is shown with Swagelok®tube fitting end connections. These instructions also apply to XS series
valves with pipe ends and with VCR®and VCO®face-seal fitting end connections.
Component Identification
Definitions
Statements and symbols are used in this document
to identify safety concerns. Read the definitions
below before performing the service instructions.
This symbol indicates cautionary
information.
Caution: Indicates a potentially hazardous
situation. It may also be used to
alert against unsafe practices.
Notice: Indicates a statement of company
policy directly or indirectly related to
the safety of personnel or protection
of property.
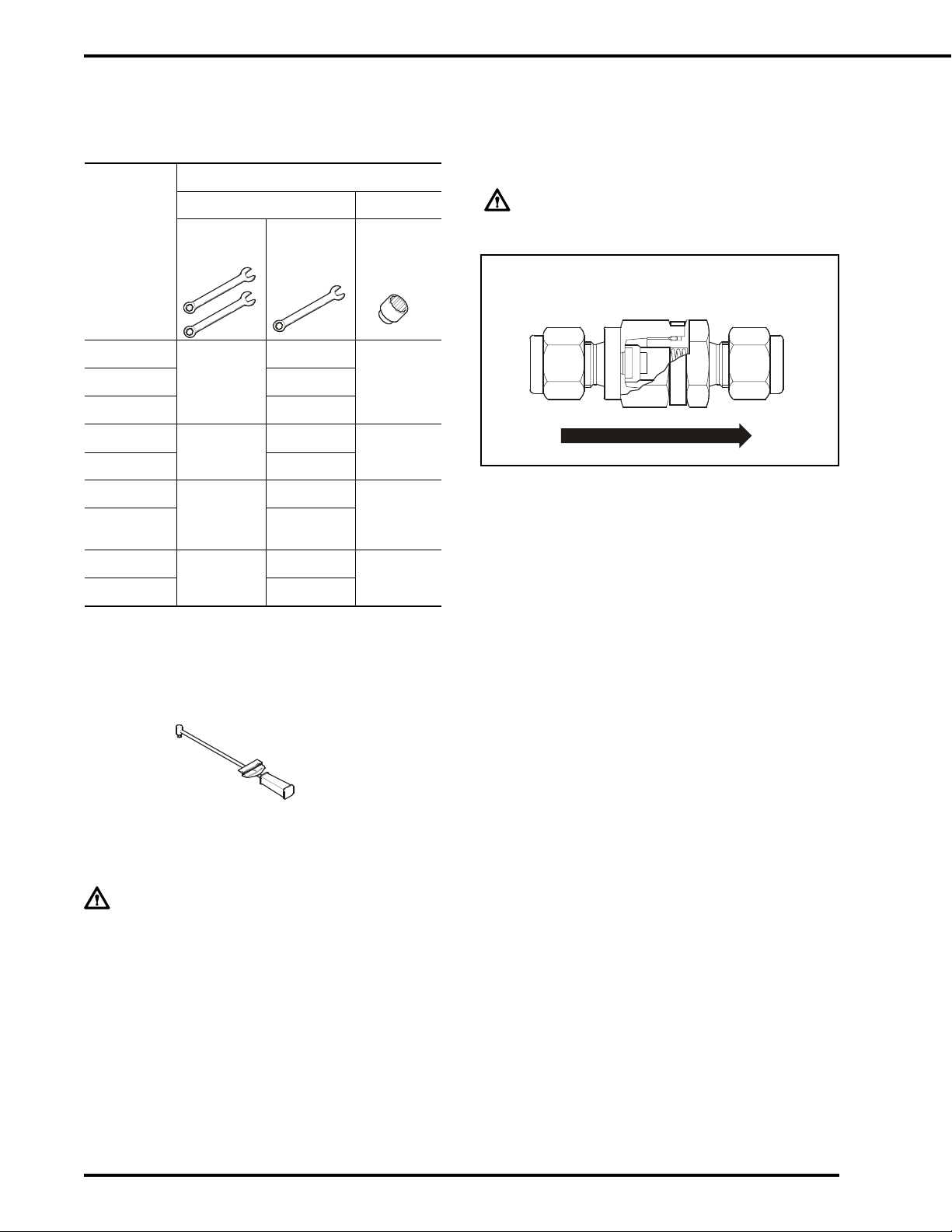
For Body
Hex
Qty. (1)
2
MS-CRD-0064
Revision 1 6-00-CP
Tool Requirements
Tool size depends on the nominal end connection
size and style. See the table below.
Other Tools
Torque wrench rated to 200 in·lb (22.6 N·m).
Installation
1. Refer to the flow direction arrow on the excess
flow valve and install the valve in the
correct orientation.
IMPORTANT:
Verify proper flow direction when installing.
Inlet
Outlet
2. For valves with Swagelok tube fittings or VCO
®
or VCR®fittings, following the specific fitting
assembly instructions.
3. For valves with pipe fittings or straight thread
fittings, follow standard industry practices.
The flow direction verification card included
with the valve shows the proper flow direction.
Testing
1. Operate at normal flow rate. Create maximum
flow surges. Valve must remain open in both
instances.
2. Vent system line to simulate a break. Valve
must trip (close).
• If valve trips closed, proceed to step 3.
• If valve does not trip closed, replace the
spring with one of the lower-flow springs.
Repeat the Testing procedure.
3. Perform reset test by venting system to trip
valve. Close upstream or downstream valve to
allow the valve to reset. Valve must open and
allow normal flow.
4. Test the valve to ensure there is no leakage to
the atmosphere.
Nominal
End
Connection
Size
Tool Size and Quantity
Wrenches Socket
For Body
Hex Qty. (2)
For End
Connection
Qty. (1)
1/8 in.
11/16 in.
7/16 in.
11/16 in.
1/4 in. 9/16 in.
6 mm 14 mm
3/8 in.
1 in.
11/16 in.
1 in.
1/2 in. 7/8 in.
1/2 in. FNPT
11⁄16 in.
11⁄16 in.
11⁄16 in.
1/2 in.
BSP/ISO
11⁄16
in.
8 mm
1 in.
16 mm
1 in.
12 mm 22 mm
Caution:
Before servicing any installed valve you
must:
• depressurize the system
• purge the valve.
Flow Direction Verification Card