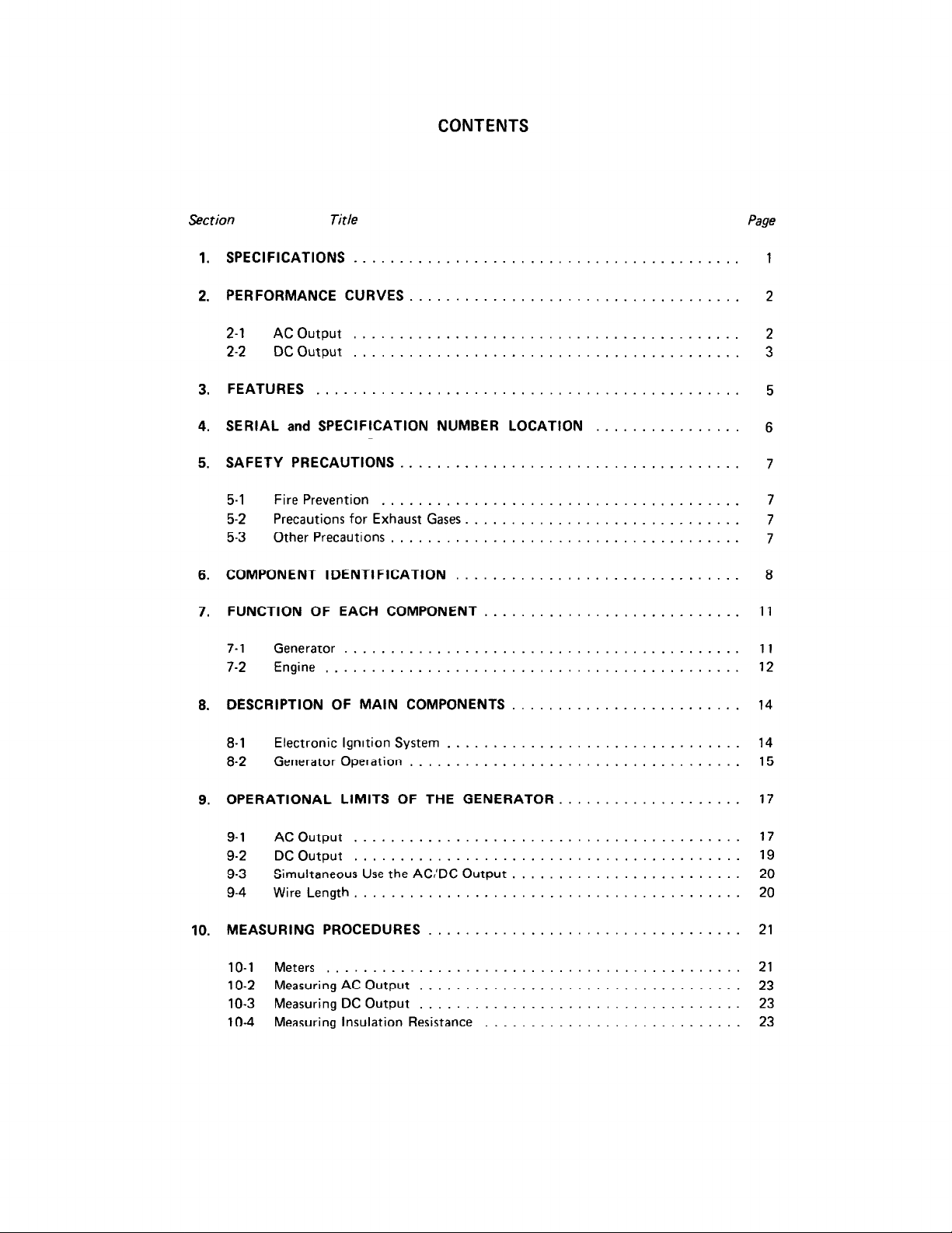
CONTENTS
Section
SPECIFICATIONS ..........................................
1.
PERFORMANCE CURVES
2.
2-1 AC Output ..........................................
2-2 DC Output ..........................................
FEATURES ..............................................
3.
SERIAL and SPECIFICATION NUMBER LOCATION
4.
SAFETY PRECAUTIONS
5.
5-1 Fire Prevention .......................................
5-2 Precautions for Exhaust Gases.
5-3 Other Precautions
COMPONENT IDENTIFICATION
6.
FUNCTION OF EACH COMPONENT
7.
7-1
7-2
Generator ...........................................
Engine .............................................
Title
....................................
.....................................
.............................
......................................
...............................
............................
................
Page
1
2
2
3
5
6
7
7
7
7
8
11
11
12
DESCRIPTION OF MAIN COMPONENTS
8.
8-1
8-2
OPERATIONAL LIMITS OF THE GENERATOR.
9.
9-1
9-2
9-3
9-4
MEASURING PROCEDURES
10.
Electronic lgnition System
Generator Operation
AC Output ..........................................
DC Output ..........................................
Simultaneous Use the AC/DC Output
Wire Length. .........................................
10-1 Meters .............................................
10-2 Measuring AC Output
10-3 Measuring DC Output
10-4 Measuring Insulation Resistance . . . . . . . . . . . . . . . . . . . . .
................................
....................................
..................................
...................................
...................................
.........................
...................
......................... 20
14
14
15
17
17
19
20
21
21
23
23
23
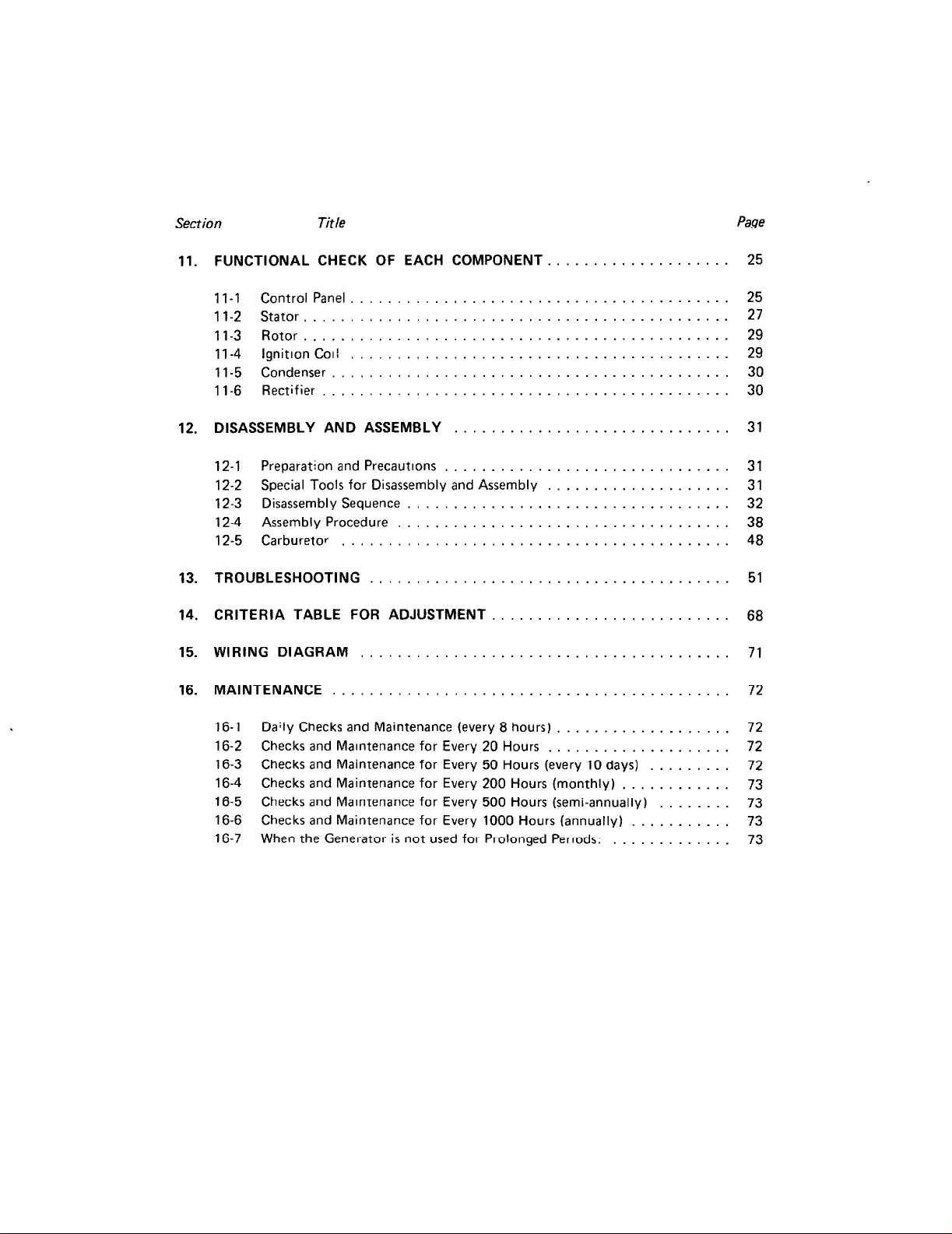
Section
Title
Page
11.
FUNCTIONAL CHECK OF EACH COMPONENT.. . . . . . . . . . . . . . . . . .
25
11-1 Control Panel
11-2 Stator.....
11-3 Rotor . . . . .
11-4
lgnition Coil
11-5 Condenser
11-6
Rectifier . .
. .
. . .
. . .
.
. .
. . .
.
. .
.
. .
.
.
. .
. . . .
. . .
. . . .
. . .
. . .
. . . .
. . . . .
. . . . . .
. . . .
. . .
......
......
......
......
. . . . .
. . .
25
. .
27
. . . 29
. .
29
. . 30
. . .
30
12.
DISASSEMBLY AND ASSEMBLY . . . . . . . . . . . . . . . . . . . . . . . . . . . . .
31
12-1
Preparation and Precautrons
...............................
31
12-2 Special Tools for Disassembly and Assembly ....................
31
12-3 Disassembly Sequence ...................................
32
12-4 Assembly Procedure ....................................
38
12-5 Carburetor ..........................................
48
13.
TROUBLESHOOTING . . . . . . . . . . . . . . . . . . . . . . . . . . . . . . . . . .
51
14.
CRITERIA TABLE FOR ADJUSTMENT . . . . . . . . . . . . . . . 68
15.
WIRING DIAGRAM . . . . . . . . . . . . . . . . . . . . . . . . . . . . . . . . .
71
16.
MAINTENANCE . . . . . . . . . . . . . . . . . . . . . . . . . . . . . . .
72
16-1 Daily Checks and Maintenance (every 8 hours)
................... 72
16-2 Checks and Maintenance for Every 20 Hours
....................
72
16-3 Checks and Maintenance for Every 50 Hours (every 10 days) ......... 72
16-4 Checks and Maintenance for Every 200 Hours (monthly) ............
73
16-5 Checks and Maintenance for Every 500 Hours (semi-annually) ........ 73
16-6 Checks and Maintenance for Every 1000 Hours (annually) ........... 73
16-7 When the Generator is not used for Prolonged Periods: ............. 73
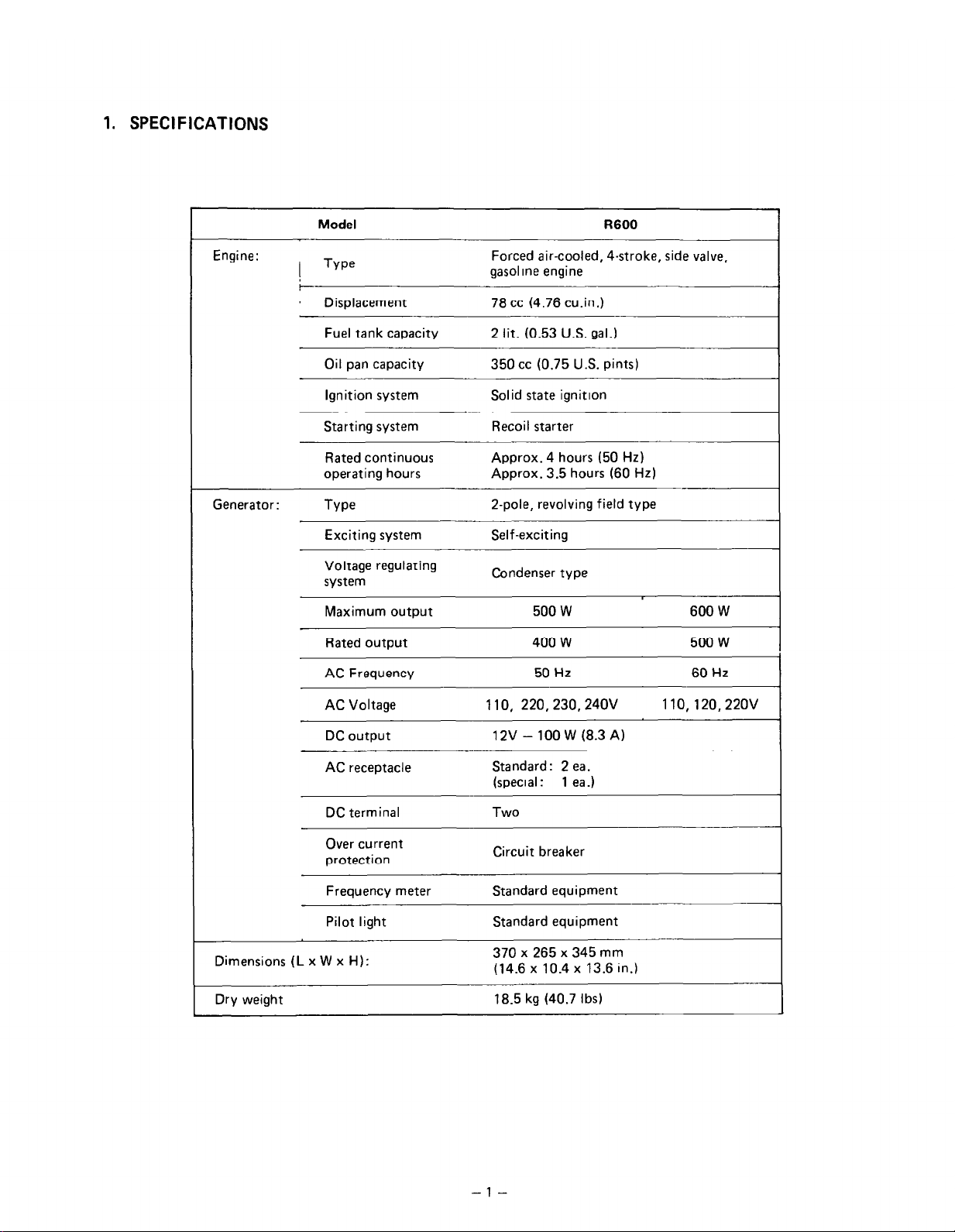
1. SPECIFICATIONS
Model
R600
Engine:
i Type
Forced air-cooled, 4-stroke, side valve,
gas01 ine engine
L--
Displacement
78 cc (4.76 cu.in.1
Fuel tank capacity
2 lit. (0.53 U.S. gal.)
Oil pan capacity
350 cc (0.75 U.S. pints)
Ignition system
Solid state ignition
~~
Starting system
Recoil starter
Rated continuous
Approx. 4 hours (50 Hz)
operating hours Approx. 3.5 hours (60 Hz)
Generator:
Type
2-pole, revolving field type
Exciting system
Self-exciting
Voltage regulating
system
Condenser type
Maximum output 500 w 600 W
Rated output 400 w 500w
AC Frequency
50 Hz 60 Hz
AC Voltage
110, 220,230,24OV
110, 120,220v
DC output 12V - 100 W (8.3 A)
AC receptacle
Standard: 2 ea.
(special: 1 ea.)
DC terminal Two
Over current
protection
Circuit breaker
Frequency meter
Standard equipment
Pilot light
Standard equipment
Dimensions (L x W x H):
370 x 265 x 345 mm
(14.6 x 10.4 x 13.6 in.)
Dry weight
18.5 kg (40.7 Ibs)
-1-
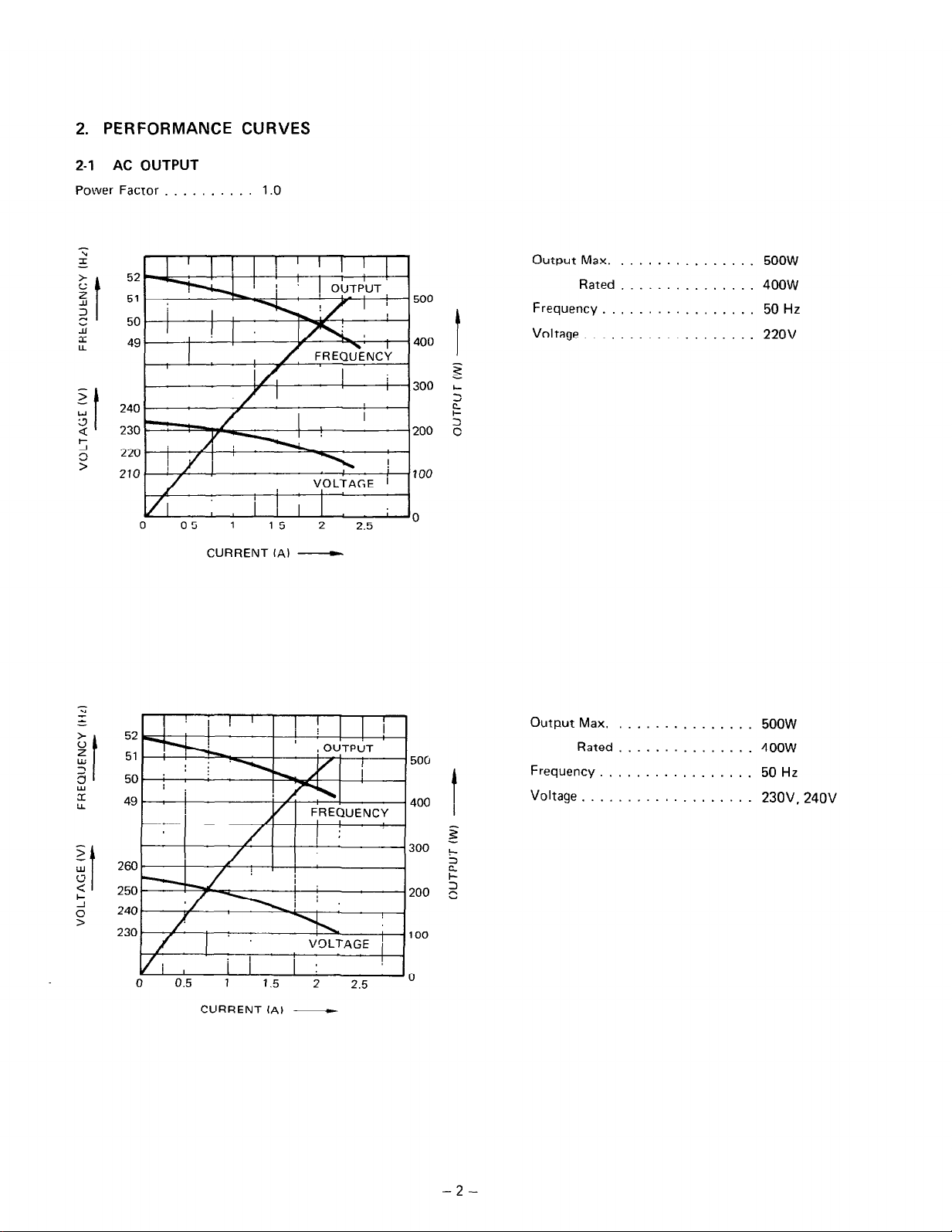
2. PERFORMANCE
2-1 AC OUTPUT
Power Factor . . .
CURVES
1
.o
3
-t
w
3
a
I I I I 1
! 1 I 1 1
I ’
I I
!
1 OUTPUT’
i ,
I
FRECiENC
i/: ‘1 I
1
Y I
i 300
t
240
/ I
/ I I $
CURRENT IA) -
1
I
, ,
I
1 I 1 1 i
, OUTPUT
1.1 j 500
: :
50
i I I
I II
-i----l
49-
/‘\I
// FREQUENCY
400
t
I
I
/
I 1 a
I , :
I
/ I I !
300
260
I
/ : I I
Output Max.
............... 500W
Rated
............... 400W
Frequency.
................
50 Hz
Voltage.
.................. 220V
Output Max.
............... 500W
Rated
............... 400W
Frequency.
................ 50 Hz
Voltage
................... 230V. 240V
vi : I 1
0 0.5 1 1.5 2 2.5 0
CURRENT
(Al -
-2-
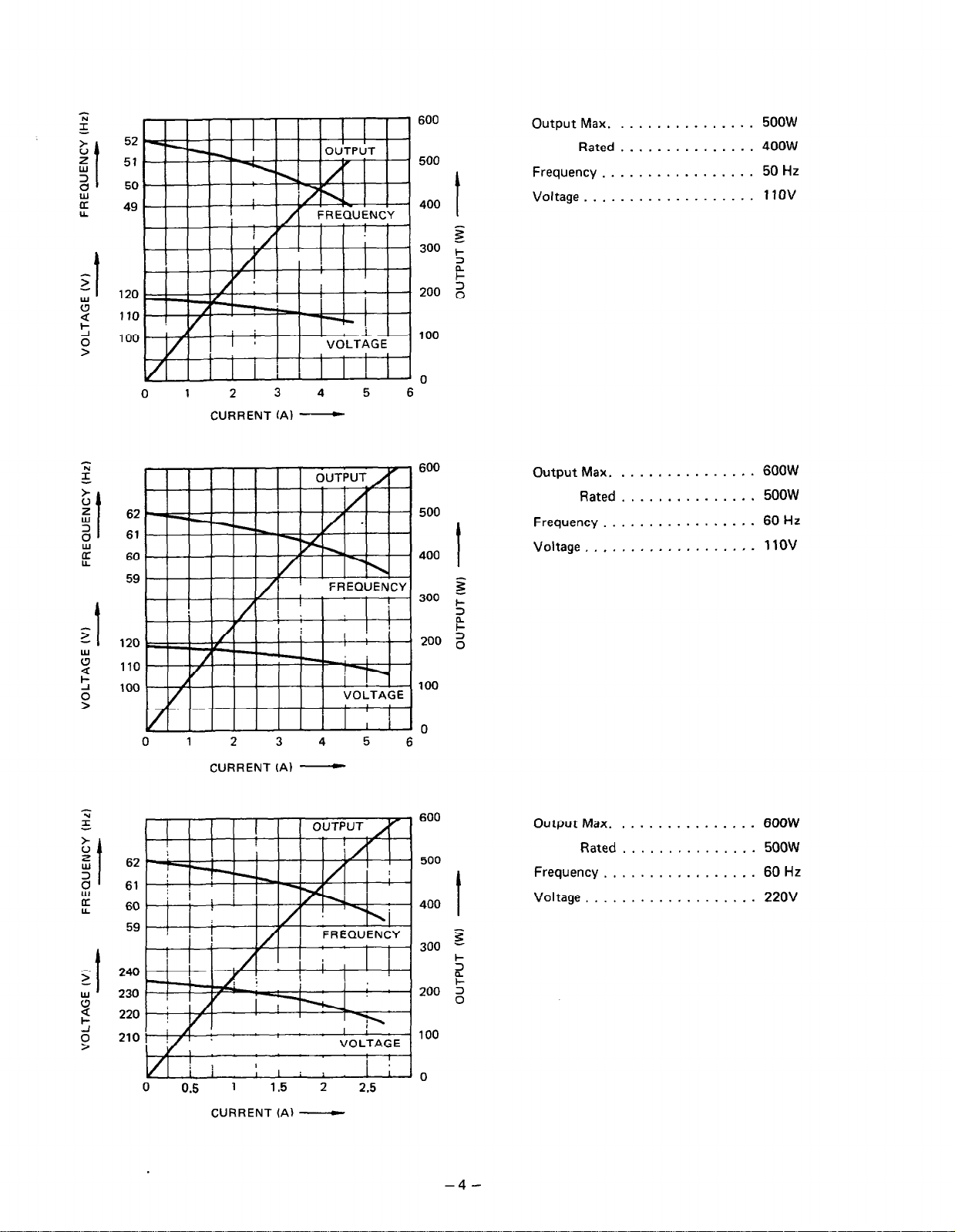
52
51
50
49
0
1 2 3
CURRENT IA)
4 5
-
600
500
400 t
300 +
200 2
6
Output Max. ...............
...............
Rated
Frequency .................
Voltage.
3
3
E
..................
500W
400W
50 Hz
11OV
I I I I I
62
61
60
59
120
110
100
0
1 2 3
CURRENT IA)
4 5
-
FREQUENCY
r
I
1
400
300
200 ‘0
100
0
6
I
3
f
k
Output Max. ...............
...............
Rated
Frequency .................
Voltage.
Output Max.
..................
...............
Rated ...............
Frequency
Voltage
.................
...................
600W
500W
60 HZ
11OV
600W
500W
60 Hz
220V
0 0.5
1 1.5
CURRENT (A)
2 2.5
-
-4-
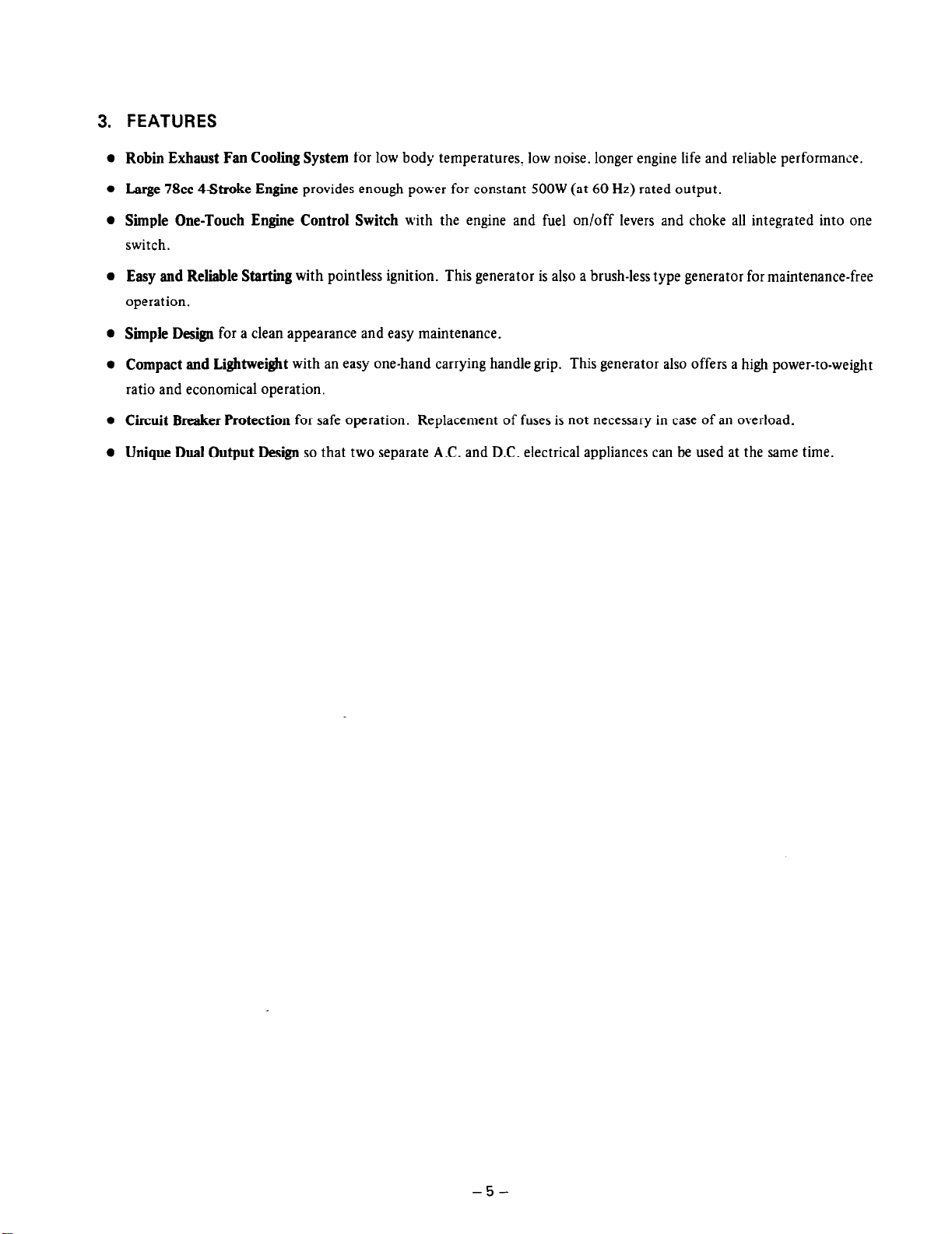
3. FEATURES
l
Robin Exhaust Fan Cooling System for low body temperatures, low noise. longer engine life and reliable performance.
l
Large 78cc
4Stroke
Engine provides enough power for constant 500W (at 60 Hz) rated output.
l
Simple One-Touch Engine Control Switch with the engine and fuel on/off levers and choke all integrated into one
switch.
l
Easy and Reliable Starting with pointless ignition. This generator is also a brush-less type generator for maintenance-free
operation.
l
Simple Design for a clean appearance and easy maintenance.
l
Compact and Lightweight with an easy one-hand carrying handle grip. This generator also offers a high power-to-weight
ratio and economical operation.
l
Circuit Breaker Protection for safe operation. Replacement of fuses is not necessary in case of an overload.
l
Unique Dual Output Design so that two separate A.C. and D.C. electrical appliances can be used at the same time.
-5-
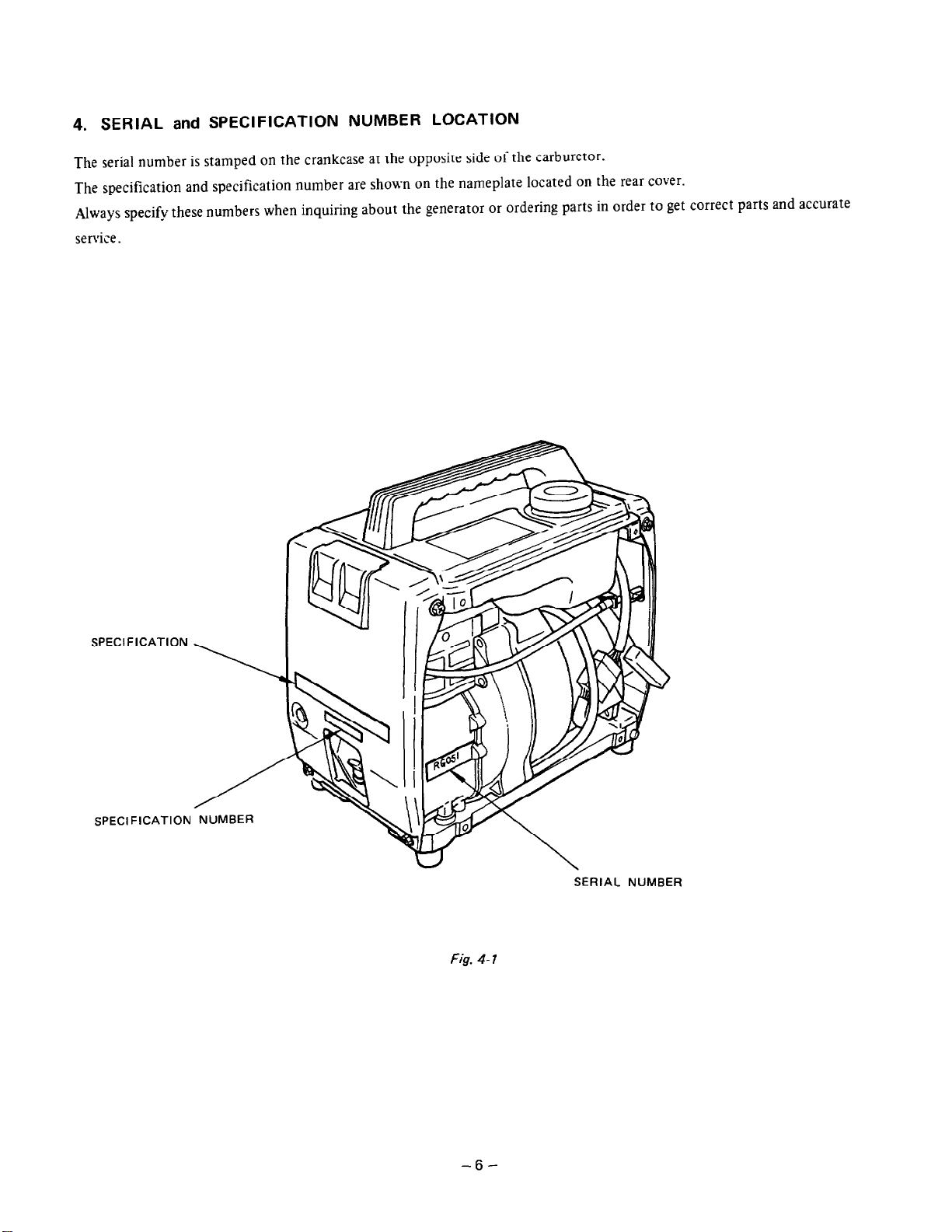
4. SERIAL and SPECIFICATION NUMBER LOCATION
The serial number is stamped on the crankcase at the opposite side of the carburetor.
The specification and specification number are shown on the nameplate located on the rear cover.
Always specify these numbers when inquiring about the e
oenerator or ordering parts in order to get correct parts and accurate
service.
SPECIFICATION
SPECIFICATION NUMBER
SERIAL NUMBER
Fig. 4-7
-6-
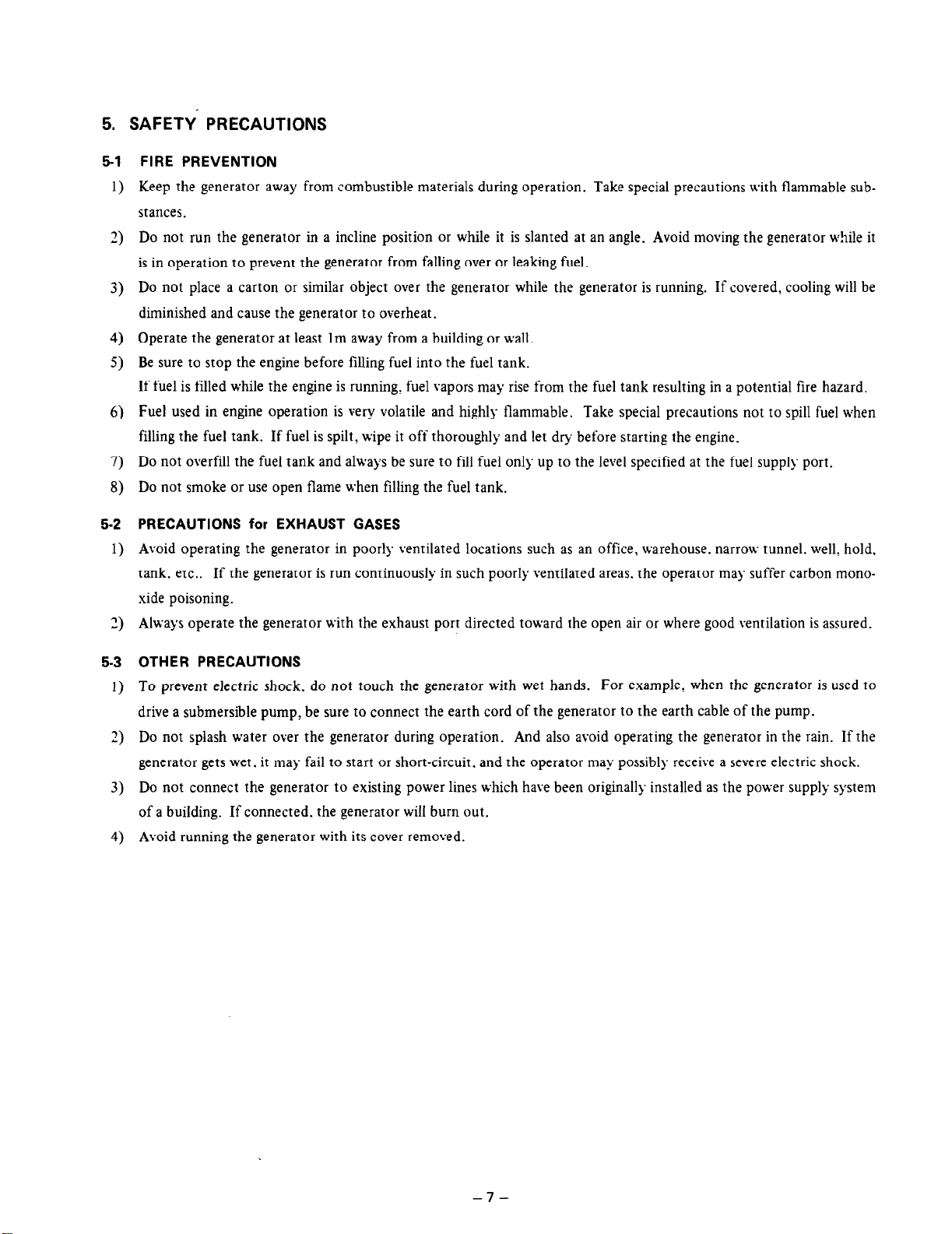
” - . . . - . . - -
5. SAFETY- PRECAUTIONS
51
1)
2)
3)
4)
5)
6)
7)
8)
5-2
1)
3
5-3
1)
2)
3)
4)
FIRE PREVENTION
Keep the generator away from combustible materials during operation. Take special precautions with flammable substances.
Do not run the generator in a incline position or while it is slanted at an angle. Avoid moving the generator while it
is in operation to prevent the generator from falling over or leaking fuel.
Do not place a carton or similar object over the generator while the generator is running. If covered, cooling will be
diminished and cause the generator to overheat.
Operate the generator at least lm away from a building or wall.
Be sure to stop the engine before filling fuel into the fuel tank.
If fuel is filled while the engine is running, fuel vapors may rise from the fuel tank resulting in a potential fire hazard.
Fuel used in engine operation is very volatile and highly flammable. Take special precautions not to spill fuel when
filling the fuel tank. If fuel is spilt, wipe it off thoroughly and let dry before starting the engine.
Do not overfill the fuel tank and always be sure to fill iuel only up to the level specified at the fuel supply- port.
Do not smoke or use open flame when filling the fuel tank.
PRECAUTIONS for EXHAUST GASES
Avoid operating the generator in poorly ventilated locations such as an office, warehouse. narrow tunnel. well, hold.
tank. etc..
If the generator is run continuously in such poorly ventilated areas. the operator may suffer carbon monoxide poisoning.
Always operate the generator with the exhaust port directed toward the open air or where good ventilation is assured.
OTHER PRECAUTtONS
To prevent electric shock. do not touch the generator with wet hands.
For example, when the generator is used to
drive a submersible pump, be sure to connect the earth cord of the generator to the earth cable of the pump.
Do not splash water over the generator during operation.
And also avoid operating the generator in the rain. If the
generator gets wet. it may fail to start or short-circuit. and the operator may possibly receive a severe electric shock.
Do not connect the generator to existing power lines which have been originally installed as the power supply system
of a building. If connected. the generator will burn out.
Avoid running the generator with its cover removed.
-7-
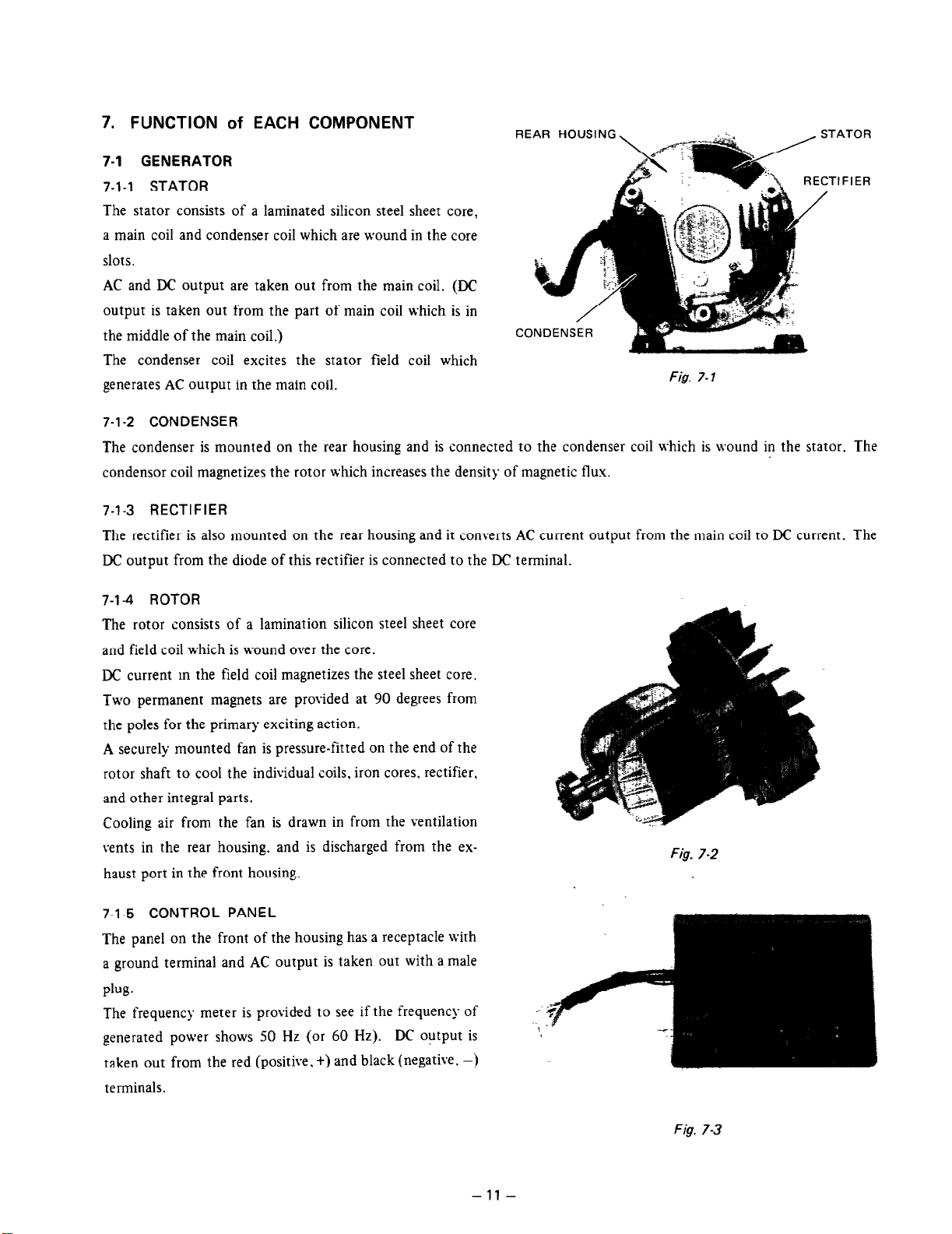
7. FUNCTION of EACH COMPONENT
7-1 GENERATOR
7-1-1 STATOR
The stator consists of a laminated silicon steel sheet core,
a main coil and condenser coil which are wound in the core
slots.
AC and DC output are taken out from the main coil. (DC
output is taken out from the part of main coil which is in
the middle of the main coil.)
The condenser coil excites the stator field coil which
generates AC output in the main coil.
7-1-2 CONDENSER
REAR HOUSING
RECTIFIER
Fig. 7- 7
The condenser is mounted on the rear housing and is connected to the condenser coil which is wound in the stator. The
condenser coil magnetizes the rotor which increases the density of magnetic flux.
7-1-3 RECTIFIER
The rectifier is also mounted on the rear housing and it converts AC current output from the main coil to DC current. The
DC output from the diode of this rectifier is connected to the DC terminal.
7-1-4 ROTOR
The rotor consists of a lamination silicon steel sheet core
and field coil which is wound over the core.
DC current m the field coil magnetizes the steel sheet core.
Two permanent magnets are provided at 90 degrees from
the poles for the primary exciting action.
A securely mounted fan is pressure-fitted on the end of the
rotor shaft to cool the individual coils. iron cores. rectifier.
and other integral parts.
Cooling air from the fan is drawn in from the ventilation
vents in the rear housing. and is discharged from the ex-
haust port in the front housing.
Fig. 7-2
7-l-5 CONTROL PANEL
The panel on the front of the housing has a receptacle with
a ground terminal and AC output is taken out with a male
Plug.
The frequency meter is provided to see if the frequency of
generated power shows 50 Hz (or 60 Hz). DC output is
taken out from the red (positive. +) and black (.negative. -)
terminals.
-11-
Fig. 7-3
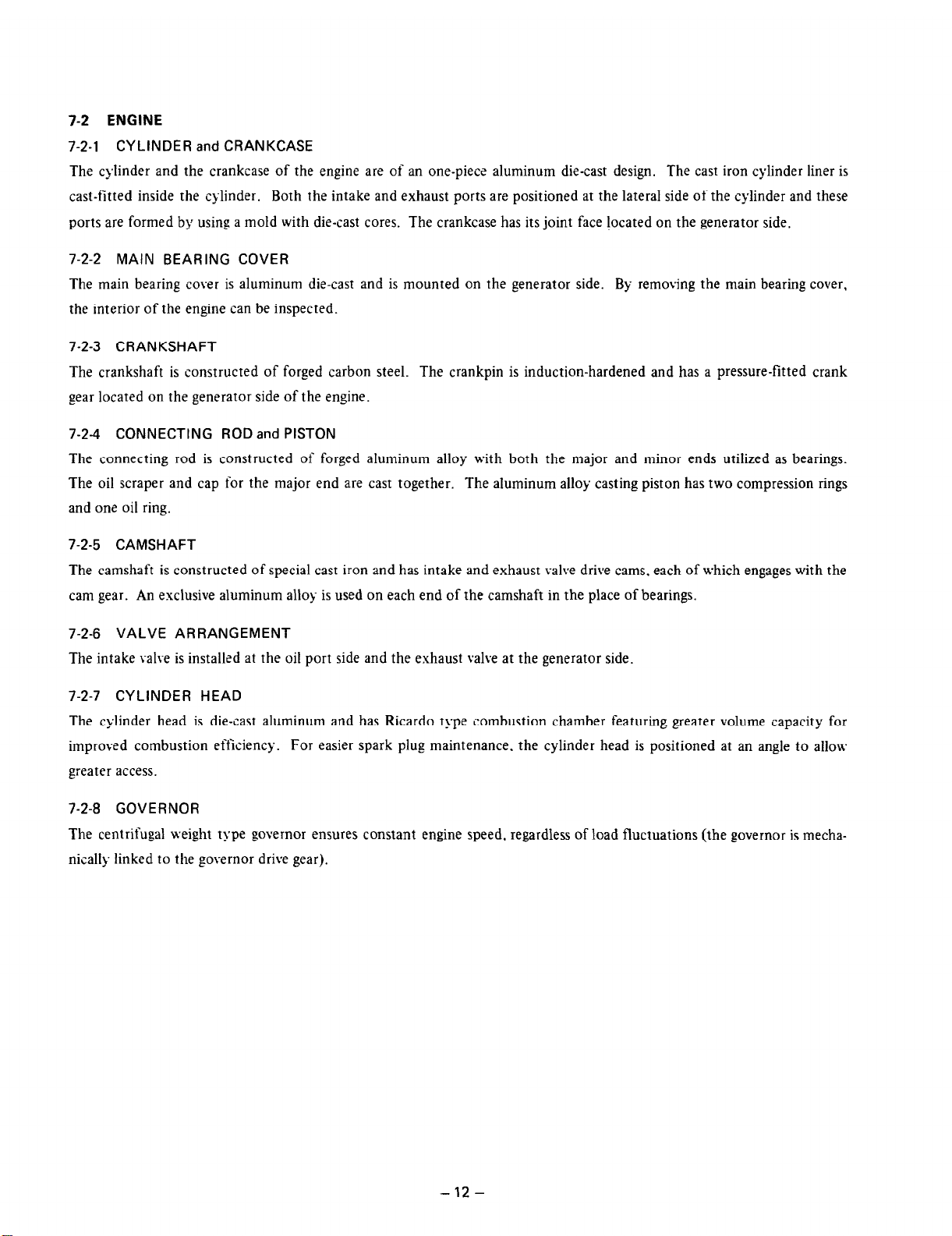
7-2 ENGINE
7-2-l CYLINDER and CRANKCASE
The cylinder and the crankcase of the engine are of an one-piece aluminum die-cast design. The cast iron cylinder liner is
cast-fitted inside the cylinder. Both the intake and exhaust ports are positioned at the lateral side of the cylinder and these
ports are formed by using a mold with die-cast cores. The crankcase has its joint face located on the generator side.
7-2-2 MAIN BEARING COVER
The
main bearing cover is aluminum die-cast and is mounted on the generator side. By removing the main bearing cover.
the interior of the engine can be inspected.
7-2-3 CRANKSHAFT
The crankshaft is constructed of forged carbon steel. The crankpin is induction-hardened and has a pressure-fitted crank
gear located on the generator side of the engine.
7-2-4 CONNECTING ROD and PISTON
The connecting rod is constructed of forged aluminum alloy with both the major and minor ends utilized as bearings.
The oil scraper and cap for the major end are cast together. The aluminum alloy casting piston has two compression rings
and one oil ring.
7-2-5 CAMSHAFT
The camshaft is constructed of special cast iron and has intake and exhaust valve drive cams. each of which engages with the
cam gear. An exclusive aluminum alloy is used on each end of the camshaft in the place of bearings.
7-2-6 VALVE ARRANGEMENT
The intake valve is installed at the oil port side and the exhaust valve at the generator side.
7-2-7 CYLINDER HEAD
The cylinder head is die-cast aluminum and has Ricardo type combustion chamber featuring greater volume capacity for
improved combustion efficiency. For easier spark plug maintenance. the cylinder head is positioned at an angle to allow
greater access.
7-2-8 GOVERNOR
The centrifugal weight type governor
ensures
constant engine speed, regardless of load fluctuations (the governor is mecha-
nically linked to the governor drive gear).
-12-
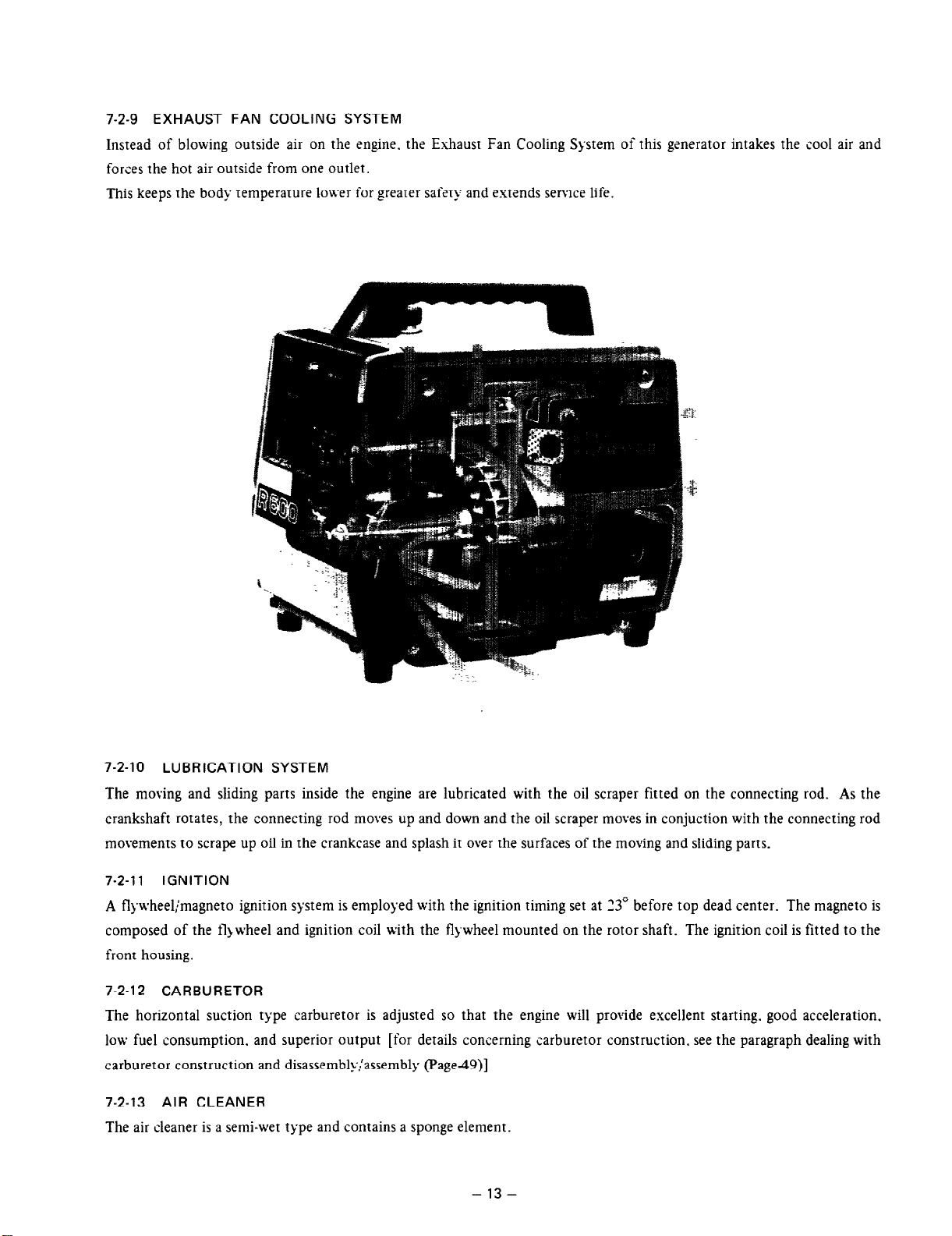
7-2-9 EXHAUST FAN COOLING SYSTEM
Instead of blowing outside air on the engine. the Exhaust Fan Cooling System of this generator intakes the cool air and
forces the hot air outside from one outlet.
This keeps the body temperature lower for greater safety and extends service life.
7-2-10 LUBRICATION SYSTEM
The moving and sliding parts inside the engine are lubricated with the oil scraper fitted on the connecting rod. As the
crankshaft rotates, the connecting rod moves up and down and the oil scraper moves in conjuction with the connecting rod
movements to scrape up oil in the crankcase and splash it over the surfaces of the moving and sliding parts.
7-2-l
1 IGNITION
A flywheeh’magneto ignition system is employed with the ignition timing set at 23” before top dead center. The magneto is
composed of the tl)wheel and ignition coil with the fll-wheel mounted on the rotor shaft. The ignition coil is fitted to the
front housing.
7-2-l 2 CARBURETOR
The horizontal suction type carburetor is adjusted so that the engine will provide excellent starting. good acceleration.
low fuel consumption. and superior output [for details concerning carburetor construction. see the paragraph dealing with
carburetor construction and disassembly/assembly (Page49)]
7-2-13 AIR CLEANER
The air cleaner is a semi-wet type and contains a sponge element.
- 13-
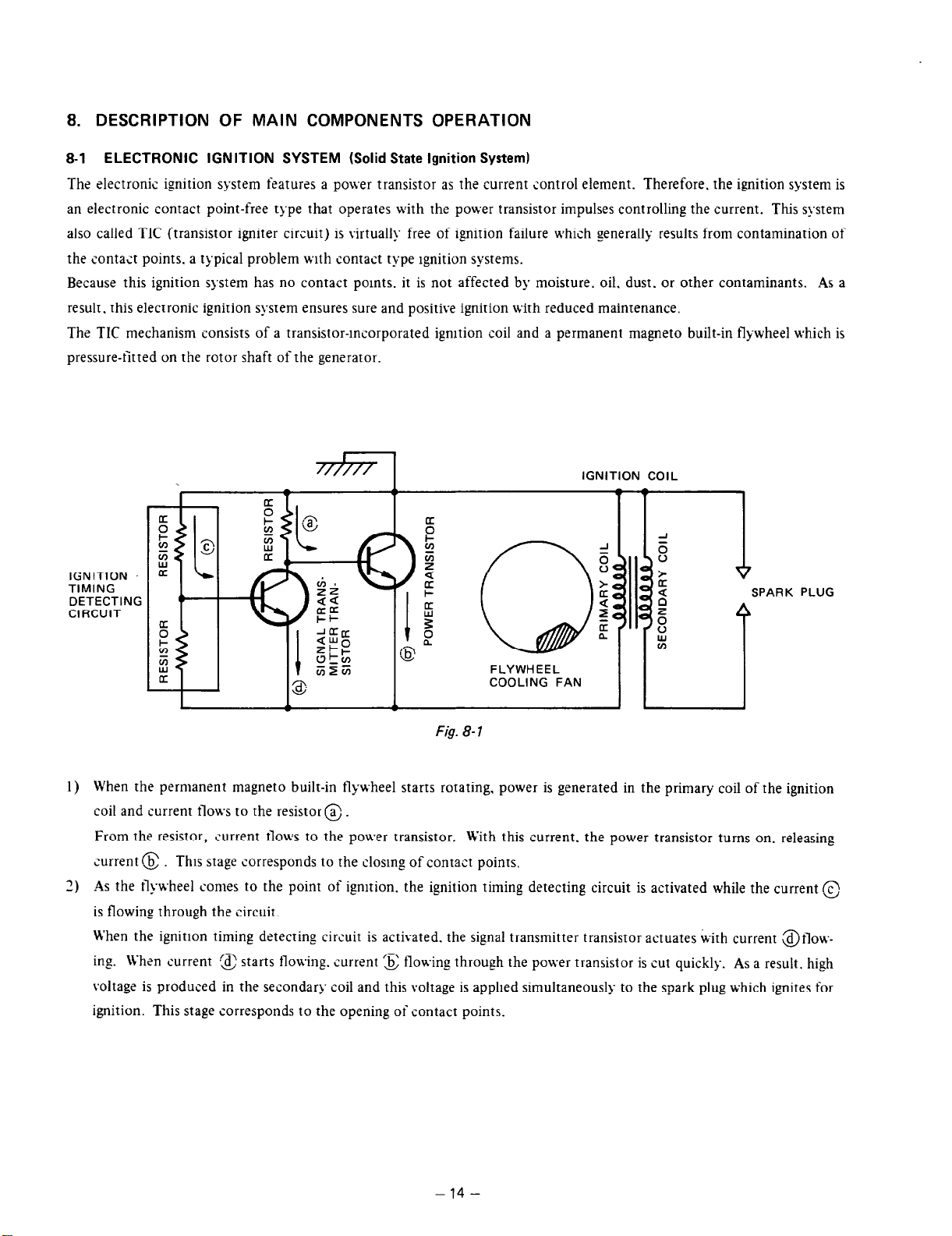
8. DESCRIPTION OF MAIN COMPONENTS OPERATION
8-1 ELECTRONIC IGNITION SYSTEM (Solid State Ignition System)
The electronic ignition system features a polver transistor as the current control element. Therefore. the ignition system is
an electronic contact point-free type that operates with the po\ver transistor impulses controlling the current. This system
also called TIC (transistor igniter circuit) is virtually free of ignition failure which generally results from contamination of
the contact points. a typical problem vvrth contact type ignition systems.
Because this ignition system has no contact points. it is not affected by moisture. oil. dust. or other contaminants. 4s a
result. this electronic ignition system ensures sure and positive ignition lvith reduced maintenance.
The TIC mechanism consists of a transistor-mcorporated ignition coil and a permanent magneto built-in flywheel which is
pressure-fitted on the rotor shaft of the generator.
I
//////
IGNITION COIL
IGNITION
TIMING
DETECTING
CIRCUIT
FLYWHEEL
COOLING FAN
PLUG
Fig. 8- 1
1) When the permanent magneto built-in flywheel starts rotating. power is generated in the primary coil of the ignition
coil and current tlows to the resistor @ _
From the resistor, current flows to the power transistor. RYth this current. the power transistor turns on. releasing
current I(@ Thrs stage corresponds to the closmg of contact points.
2) As the tlywheel comes to the point of ignition. the ignition timing detecting circuit is activated while the current @
is flowing through the circuit.
When the ignition timing detecting circuit is activated. the signal transmitter transistor actuates hzith current 8 flowing. \Vhen current ,$$ starts flovving.
current s flowing through the power transistor is cut quickly. As a result. high
voltage is produced in the secondary coil and this voltage is applied simultaneously to the spark plug which ignites for
ignition. This stage corresponds to the opening of contact points.
-14 -
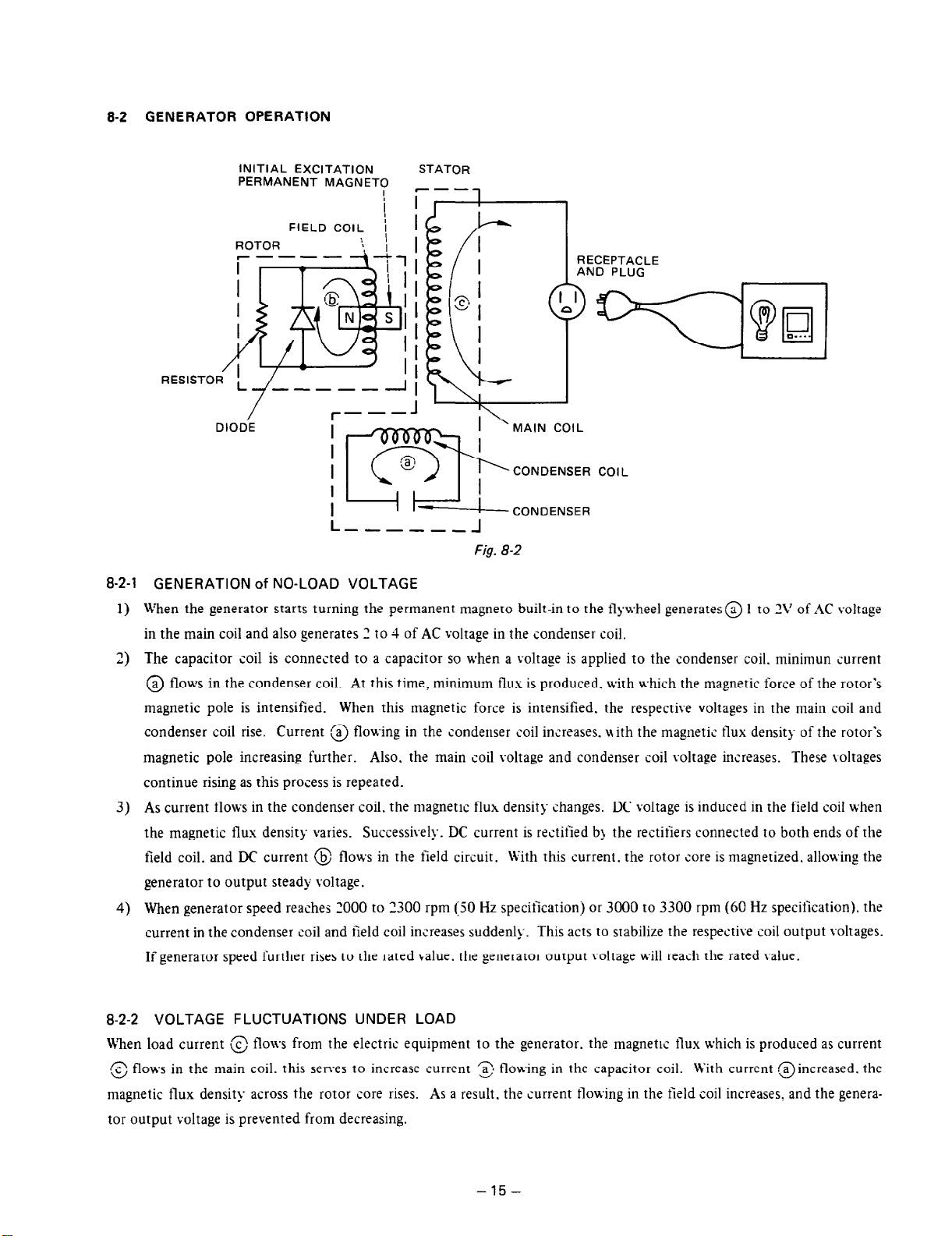
8-2
GENERATOR OPERATION
INITIAL EXCITATION
PERMANENT MAGNETO
FIELD COIL i
ROTOR
: I
RESIS
-----
DIODE
8-2-l
1)
GENERATION of NO-LOAD VOLTAGE
2)
3)
41
When the generator starts turning the permanent magneto built-in to the flywheel generates@ 1 to 2\’ of AC voltage
in the main coil and also generates 1 to 4 of AC voltage in the condenser coil.
The capacitor coil is connected to a capacitor so when a voltage is applied to the condenser coil. minimun current
@ flows in the condenser coil. At this time, minimum flus is produced. vvith which the magnetic force of the rotor’s
magnetic pole is intensified. When this magnetic force is intensified. the respective voltages in the main coil and
condenser coil rise. Current 1s flowing in the
condenser coil increases. with the magnetic tlux densit)- of the rotor’s
magnetic pole increasing further. Also. the main coil voltage and condenser coil voltage increases. These voltages
continue rising as this process is repeated.
As current flows in the condenser coil. the magnetic flux density changes. DC voltage is induced in the field coil when
the magnetic flus density varies. Successively. DC current is rectified bl the rectifiers connected to both ends of the
field coil. and DC current @ flows in the field circuit.
With this current. the rotor core is magnetized. allowing the
generator to output steady voltage.
When generator speed reaches 2000 to
2300 rpm (50 Hz specification) or 3000 to 3300 rpm (60 Hz specification). the
current in the condenser coil and field coil increases sudden&. This acts to stabilize the respective coil output voltages.
If generator speed further rises to the rated v-alue. the generator output voltage will reach the rated value.
STATOR
RECEPTACLE
MAIN COIL
CONDENSER
COIL
CONDENSER
L
------
A
Fig. 8-2
8-2-2 VOLTAGE FLUCTUATIONS UNDER LOAD
When load current -s flows from the electric equipment to the generator. the magnetic flux which is produced as current
.s flows in the main coil. this serves to increase current ‘$ flowing in the capacitor coil. With current @increased. the
magnetic flux density across the rotor core rises. As a result. the current flowing in the field coil increases, and the generator output voltage is prevented from decreasing.
-15-
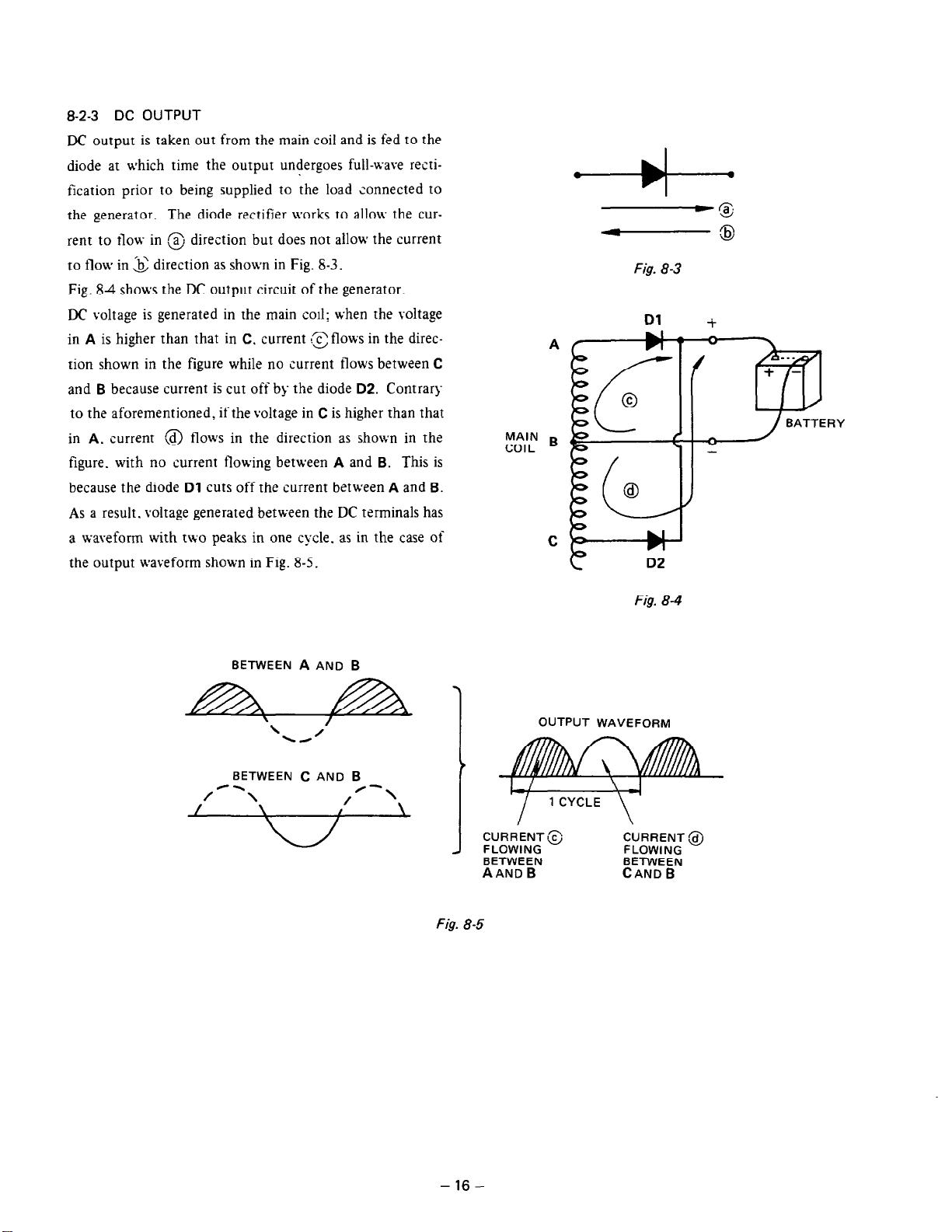
8-2-3 DC OUTPUT
DC output is taken out from the main coil and is fed to the
diode at which time the output undergoes full-wave rectification prior to being supplied to the load connected to
the generator. The diode rectifier works to allow the current to tlow in @ direction but does not allow the current
to flow in s direction as shown in Fig. S-3.
Fig. 84 shows the DC output circuit of the generator.
DC voltage is generated in the main coil; when the voltage
in A is higher than that in C. current !~flows in the direction shown in the figure while no current flows between C
and B because current is cut off by the diode
D2.
Contraq
to the aforementioned, if the voltage in C is higher than that
in
A,
current a flows in the direction as sholvn in the
figure. with no current flowing between A and B. This is
because the diode
Dl
cuts off the current between A and
B.
As a result. voltage generated between the DC terminals has
a waveform with t\vo peaks in one cycle. as in the case of
the output waveform shown in Fig. 8-5.
BETWEEN A AND
B
BETWEEN C AND
B
=w=
MAIN B
COIL
Fig. 8-3
Dl
+
Fig. 8-4
OUTPUT WAVEFORM
CURRENT 0
FLOWING
CURRENT @
FLOWING
BETWEEN
BETWEEN
AAND
B
CAND
B
Fig. 8-5
- 16 -
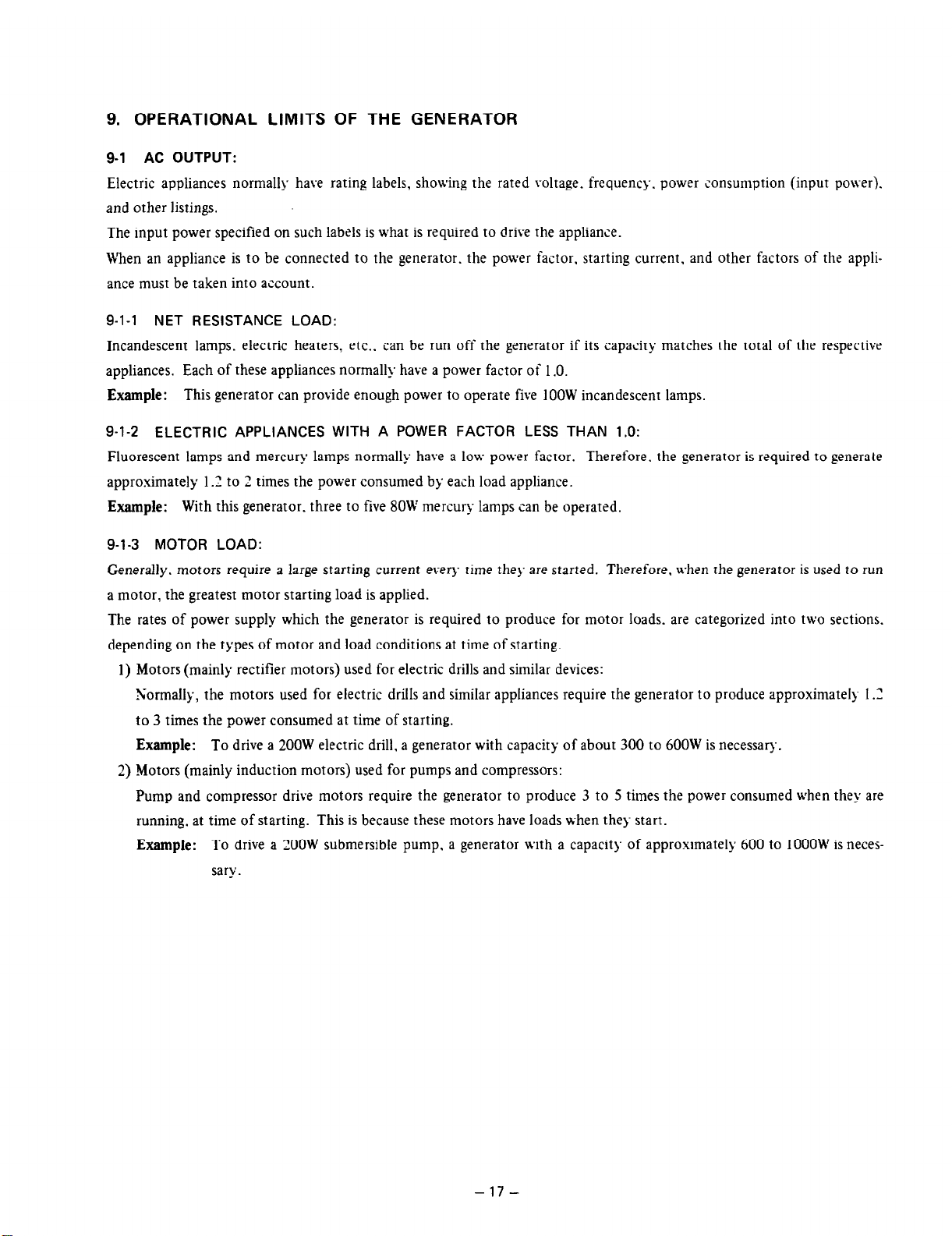
9. OPERATIONAL LIMITS OF THE GENERATOR
9-1 AC OUTPUT:
Electric appliances normally have rating labels, showing the rated voltage. frequency. power
consumption (input power).
and other listings.
The input power specified on such labels is what is required to drive the appliance.
When an appliance is to be connected to the generator. the power factor. starting current. and other factors of the appli-
ance must be taken into account.
9-l-l NET RESISTANCE LOAD:
Incandescent lamps. electric heaters, etc.. can be run off the generator if its capacity matches the total of the respective
appliances. Each of these appliances normally have a power factor of 1 .O.
Example :
This generator can provide enough power to operate five 1OOW incandescent lamps.
9-l-2 ELECTRIC APPLIANCES WITH A POWER FACTOR LESS THAN 1.0:
Fluorescent lamps and mercury lamps normally have a low po\ver factor. Therefore. the generator is required to generate
approximately 1.2 to 2 times the power consumed by each load appliance.
Example: With this generator. three to five 8OW mercury lamps can be operated.
9-l-3 MOTOR LOAD:
Generally. motors require a large starting current every time they are started. Therefore. when the generator is
used
to run
a motor, the greatest motor starting load is applied.
The rates of power supply which the generator is required to produce for motor loads. are categorized into two sections.
depending on the types of motor and load conditions at time of starting.
1) Motors (mainly rectifier motors) used for electric drills and similar devices:
Sormally, the motors used for electric drills and similar appliances require the generator to produce approximateI>- I.1
to 3 times the power consumed at time of starting.
Example: To drive a 2OOW electric drill. a generator with capacity of about 300 to 600W is necessary.
2) Motors (mainly induction motors) used for pumps and compressors:
Pump and compressor drive motors require the generator to produce 3 to 5 times the power consumed when they are
running. at time of starting. This is because these motors have loads w-hen the>- start.
Example: To drive a 2OOW submersible pump. a generator with a capacity of approximately 600 to IOOOW is neces-
sary.
-17 -
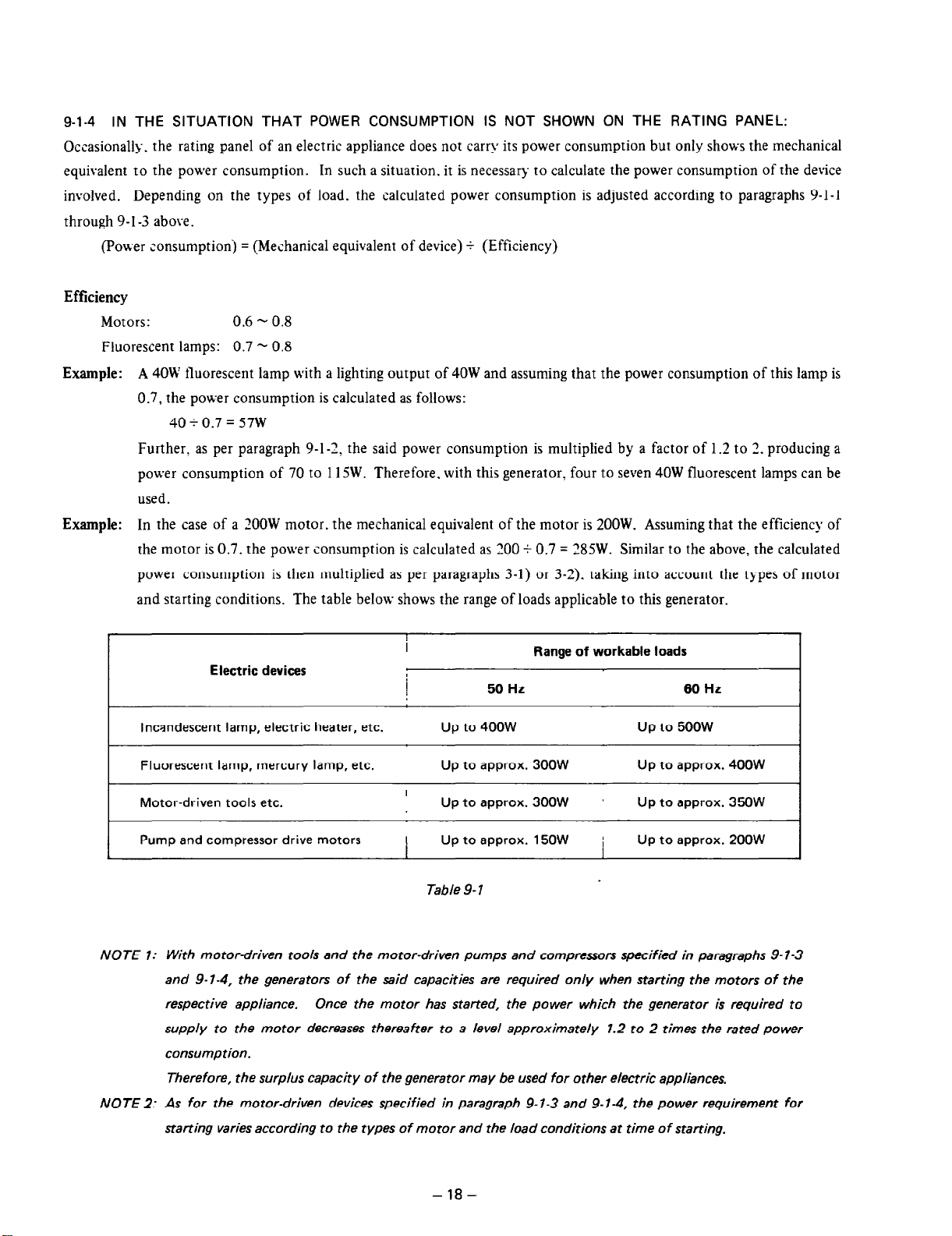
9-l-4 IN THE SITUATION THAT POWER CONSUMPTION IS NOT SHOWN ON THE RATING PANEL:
Occasionally. the rating panel of an electric appliance does not carry its power consumption but only shows the mechanical
equivalent to the power consumption. In such a situation. it is necessary to calculate the power consumption of the device
involved. Depending on the types of load. the calculated power consumption is adjusted according to paragraphs 9-l-l
through 9-I-3 above.
(Power consumption) = (Mechanical equivalent of device) + (Efficiency)
Efficiency
Motors:
0.6 - 0.8
Fluorescent lamps: 0.7 - 0.8
Example :
A
4OW fluorescent
lamp with a lighting output of 40W and assuming that the power consumption of this lamp is
0.7, the power consumption is calculated as follows:
40 + 0.7 = 57W
Further, as per paragraph 9-l-2, the said power consumption is multiplied by a factor of 1.2 to 2. producing a
power consumption of 70 to 11 SW. Therefore. with this generator, four to seven 40W fluorescent lamps can be
used.
Example: In the case of a 2OOW motor. the mechanical equivalent of the motor is 200W. Assuming that the efficiency of
the motor is 0.7. the power consumption is calculated as 200 f 0.7 = 285W. Similar to the above, the calculated
power consumption is then multiplied as per paragraphs 3-1) or 3-2). taking into account the types of motor
and starting conditions. The table below shows the range of loads applicable to this generator.
Electric devices
Range of workable loads
50 Hz 60
Hz
I
Incandescent lamp, electric heater,
etc.
up to 4oow
up to 5oow
I
Fluorescent lamp, mercury lamp, etc. Up to approx. 300W Up to approx. 400W
I
Motor-driven tools etc.
I
Up to approx. 300W Up to approx. 350W
Pump and compressor drive motors
I Up to approx. 150W /
Up to approx. 200W
Table 9- 7
NOTE 7: With motor-driven tools and the motor-driven pumps and compressors specified in paragraphs 9-7-3
and 9-l-4, the generators of the said capacities are required only when starting the motors of the
respective appliance. Once the motor has started, the power which the generator is required to
supply to the motor decreases thereafter to a level approximately 1.2 to 2 times the rated power
consumption .
Therefore, the surplus capacity of the generator may be used for other electric appliances.
NOTE 2: As for the motor-driven devices specified in paragraph 9- 7-3 and 9-l -4, the power requirement for
starting varies according to the types of motor and the load conditions at time of starting.
-
18-
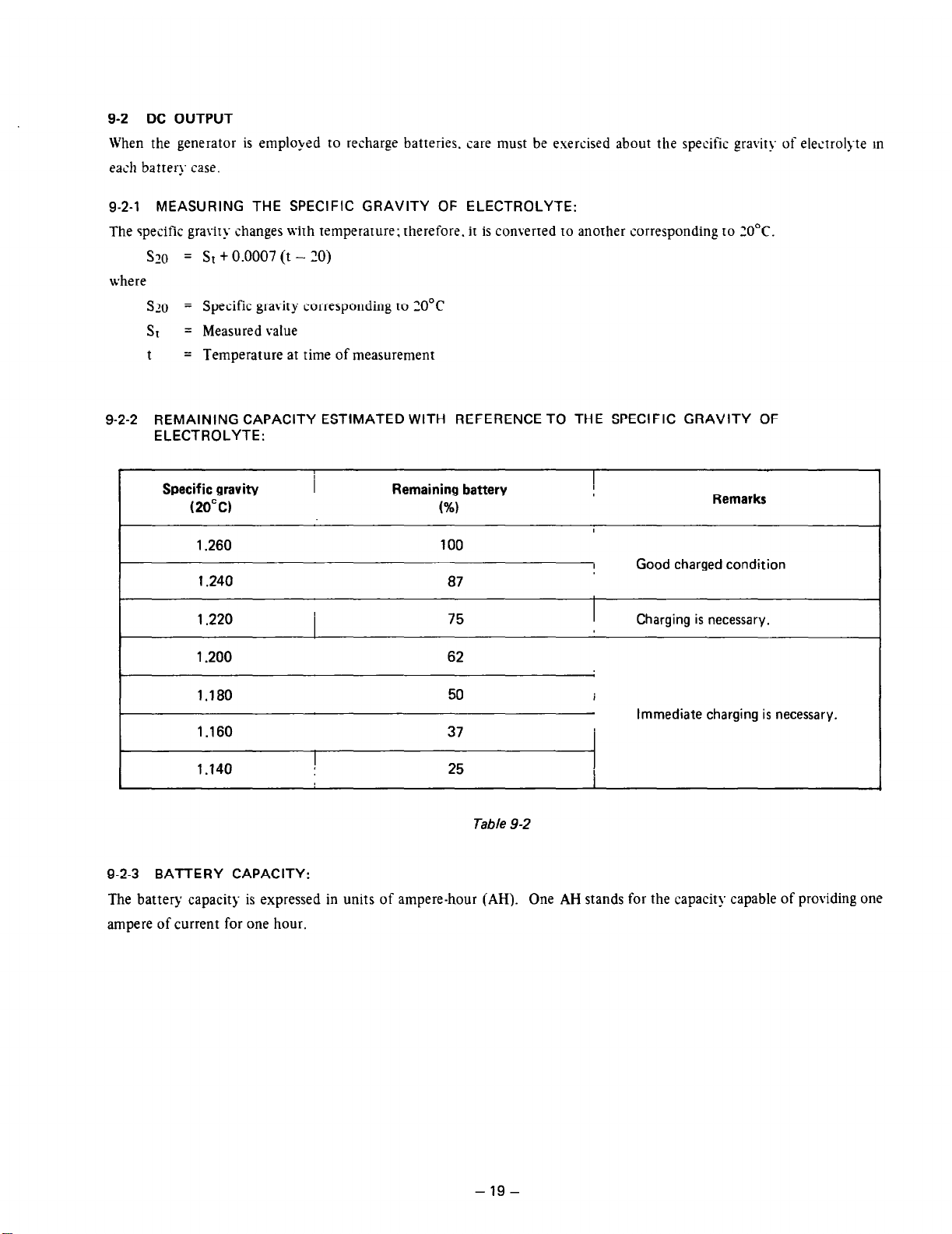
9-2 DC OUTPUT
When the generator is employed to recharge batteries. care must be exercised about the specific gravity of electrolk-te rn
each batter\. case.
9-2-l MEASURING THE SPECIFIC GRAVITY OF ELECTROLYTE:
The specific gravity changes with temperature; therefore. it is converted to another corresponding to 20°C.
S20
= St + 0.0007 (t - 10)
where
S~J = Specific gravity corresponding to 20°C
SI
= Measured value
t = Temperature at time of measurement
9-2-2 REMAINING CAPACITY ESTIMATED WITH REFERENCE TO THE SPECIFIC GRAVITY OF
ELECTROLYTE:
c
I
Specific gravity
Remaining battery
I
(20°C)
(%I
Remarks
1.260
100
1.240 87
I
I
Good charged condition
1.220
75
I
Charging is necessary.
1.200
1.180
1.160
1.140
62
50
,
Immediate charging
is
necessary.
37
25
Table 9-2
9-2-3 BATTERY CAPACITY:
The battery capacity is expressed in units of ampere-hour (AH). One AH stands for the capacity capable of providing one
ampere of current for one hour.
-19-
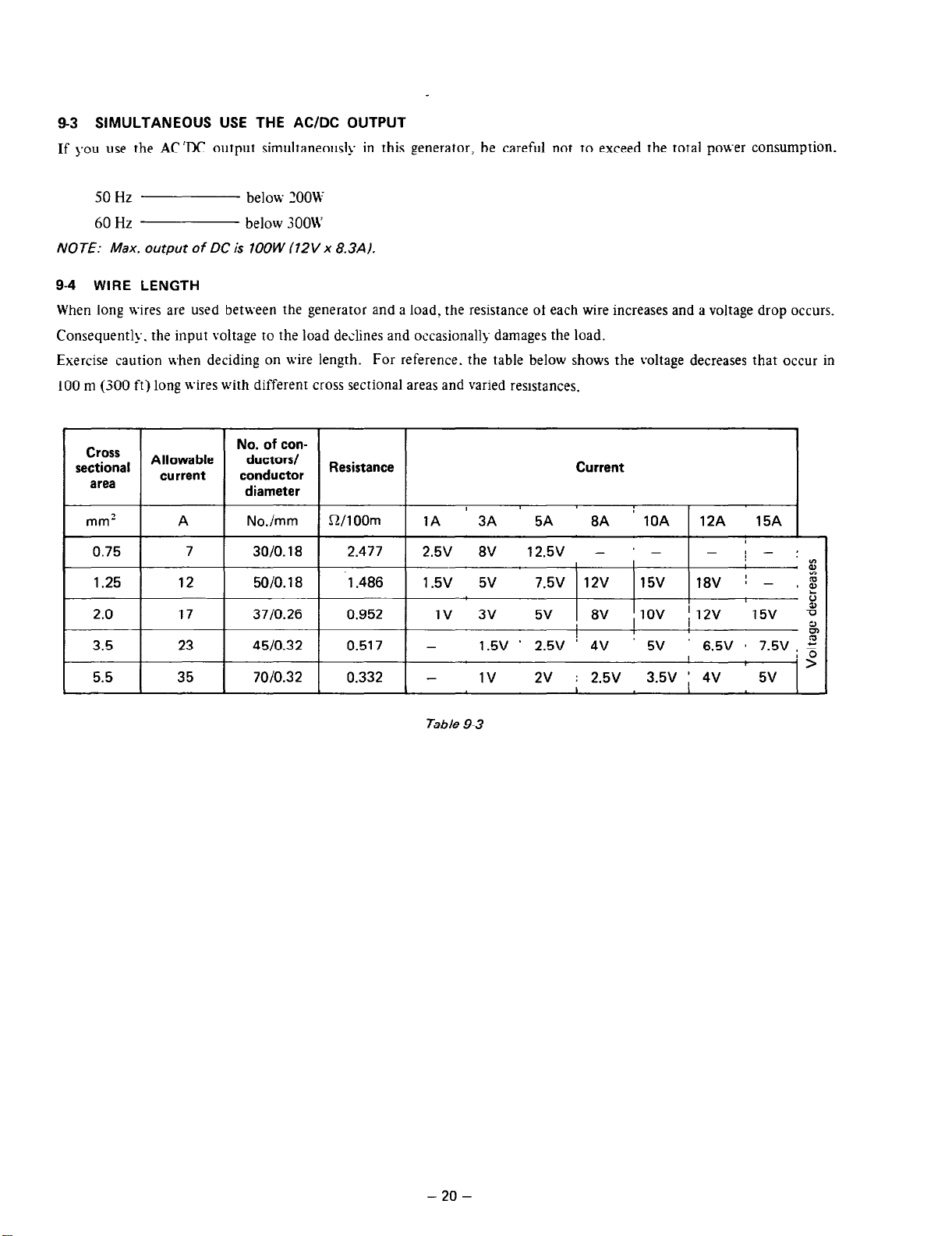
9-3 SIMULTANEOUS USE THE AC/DC OUTPUT
If you use the AC’DC output simultaneously in this generator, be careful not to exceed the total power consumption.
50 Hz
below 3OOW
60
Hz
below 3OOIV
NOTE: Max. output of DC is 1OOW /12V x 8.3A).
9-4 WIRE LENGTH
When long Lvires are used between the generator and a load, the resistance of each wire increases and a voltage drop occurs.
Consequently. the input voltage to the load declines and occasionall!- damages the load.
Exercise caution Lvhen deciding on wire length. For reference. the table below shows the voltage decreases that occur in
100 m (300 ftt) long wires with different cross sectional areas and varied resistances.
Cross
sectional
area
Allowable
current
No. of con-
ductorsl
conductor
Resistance Current
diameter
mm’
A
No./mm
,0,/l
OOm
1A ’ 3A 5A 8A ’ 10A 12A 15A
0.75
7
30/O. 18 2.477
2.5U 8U
12.5U - ‘- - ;-:
I
:
1.25 12 5OiO.18 1.486
l.5U 5u
7.5u l2U 15u
18U I -
, 8
t
2.0 17
3710.26
0,952 1u 3u
5U 8U
1 1ou
; l2U
15u 0”
8
3.5
23 4510.32 0.517 -
1.5U ’ 2.5U ’ 4U 5U 6.5U - 7.5U ; <
I
>
5.5 35 7OiO.32 0.332 -
1U 2U : 2.5U
3.5u ; 4u 5u
L I
Table 9-3
- 20 -
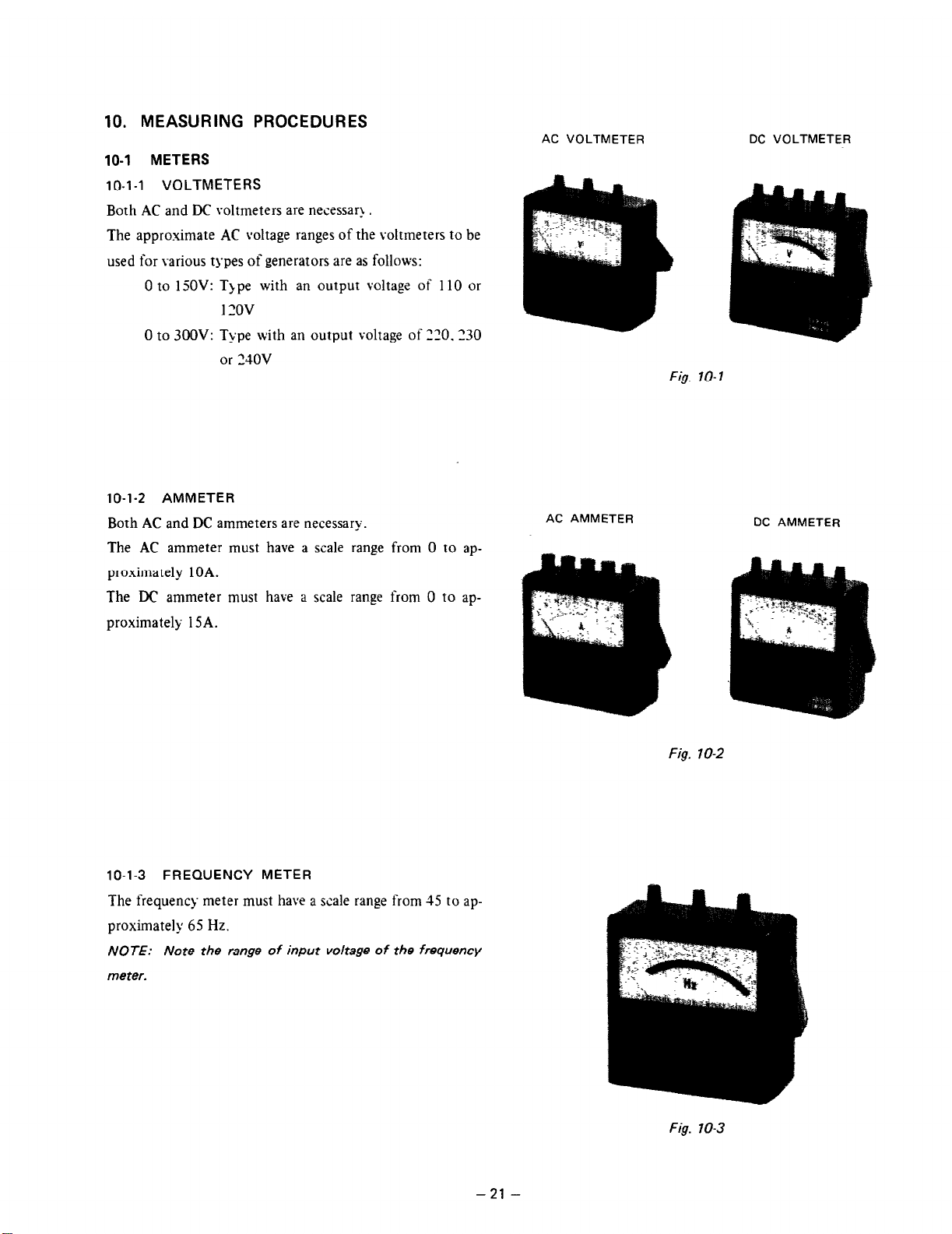
10. MEASURING PROCEDURES
AC VOLTMETER
DC VOLTMETER
10-l METERS
10-1-l VOLTMETERS
Both AC and DC voltmeters are nesessar! .
The approximate AC voltage ranges of the voltmeters to be
used for various types of generators are as follows:
0 to 1 SOV: Type with an output voltage of 110 or
12ov
0 to 300V: Type with an output voltage of 220.230
or 21OV
Fig. 70-l
10-l-2 AMMETER
Both AC and DC ammeters are necessary.
The AC ammeter must have a scale range from 0 to approximately 10A.
AC AMMETER
DC AMMETER
The DC ammeter must have a scale range from 0 to ap-
proximately 15A.
Fig. 10-2
10-l-3 FREQUENCY METER
The frequency meter must have a scale range from 45 to ap-
proximately 65 Hz.
NOTE: Note the range of input voltage of the frequency
meter.
Fig. 70-3
-2l-

10-l-4 CIRCUIT TESTER
A circuit tester is used for measuring resistances and others.
Fig. 104
10-l-5 MEGGER TESTER
To measure the insulation resistance of the generator. Use
voltage capacity of 5OOV.
Fig. 10-5
10-l-6 TACHOMETER
Use the contact-less tl pe tachometer.
Fig. 10-6
- 22 -

10-2 MEASURING AC OUTPUT
SWlTFf; LOAj
TOACd+)@ km77
With the circuit shown in Fig.lO-7.measurement 1s made of the AC output of the generator. An electric heater or an in-
candescent lamp with a power factor of 1 .O is suitable as a load for the generator.
When the measured AC output of the generator is confirmed to be wnhin the voltage range specified in the table belon.
over its voltage rating. the AC output is normal.
Measurement must
be
made under rated load and at rated speed; sometimes. load and speed adjustments are necessary-.
Voltage
I
rating
11ou
12ou
220u
230,240U
Range of
voltage
108% 12OU
118- 130U 218 - 240U
235 - 260U
10-3 MEASURING DC OUTPUT
Table 10-l
SWITCH
DC TERMINAL
Fig. 10-8
Measurement is made of the DC output of the generator with the witch shown in the abobe circuit turned on while the
generator is kept running at its rated speed. The DC output should be aithin 1 1 to 14V. Lvith the current regulated
at
8.3A
by adjusting the load connected to the generator.
NOTE: If a battery is connected as a load to the generator, the DC output voltage will increase by approximately 1 to 2V.
Therefore, carefully observe the electrolyte level and do not to overcharge the battery.
IO-4 MEASURING INSULATION RESISTANCE
To measure insulation resistance. connect the megger tester
across either one of the two output terminals of the socket
and the earth terminal. When the measured insulation
resistance of the generator is over lMI2. it is normal (over
1OMR at time of shipment).
(Be sure to turn on the circuit breaker when measuring
insulation resistance.)
If the insulation resistance is less than 1X19. drsassemble
the generator. and measure the respective resistances of the
stator.
rotor and control panel.
Fig. 10-9
- 23 -

10-4-1 STATOR
Measure the resistances
the stator and the core.
betlveen red coupler leading from
Fig. lo-10
1 O-4-2 ROTOR
d
Measure the insulation resistance across one of the soldered
terminals of the rotor and the core.
Fig. 10-11
10-4-3 CONTROL PANEL
Measure the insulation resistances between the live parts
and the grounded part.
If the measured resistance of a component is below 1MR.
the insulation is defective.
Promptly replace the defective component because there
may be leakage of current from the generator and a poten-
_
tial danger of electrical shock.
Fig. 10-12
- 24 -

11. FUNCTIONAL CHECK of EACH COMPONENT
11-l CONTROL PANEL
11-l-l ENGINE SWITCH
Using the circuit tester. check continuity across the black
and green top terminals of the 6P coupler.
When continuity between the termmals is confirmed with
the engine switch turn2d off. the switch is normal. It is also
normal if there is no continuity between thrse terminals,
when the engine switch is set at RUN or CHOKE position.
Fig. 11-l
1 l-l-2 FREQUENCY METER
Also check with the circuit tester. th2 continuity across the
yellow and blue top tsrminals of the 6P coupler. If continuity is confirmed between these terminals. the frequency
meter is normal.
Fig. 7 l-2
11-1-3 PILOT LIGHT
Using the circuit tester, check continuity between the red
and yellow top terminals of the 6P coupler.
Fig. 1 l-3
- 25 -

11-1-4 AC RECEPTACLES
Using the circuit tester. check continuity between the t\vo terminals at the rear of the XC receptacles while the receptacle is
mounted on the control panel. When continuity is confirmed between the output terminals of the receptacle Lvvlth a \vtre
connected across these terminals. the AC receptacle is normal. When the wire is removed and no continuity- is eonfirmed
between these terminals. the receptacles are also normal.
Fig. 7 7-4(A)
11-1-5 DC TERMINALS
Csmg the circuit tester. check continuity between the DC
terminals at the rear side of the control panel while they are
mounted on the panel.
Ben continuity- is confirmed bet\veen the DC terminals
Lvith a wire connected across these terminals. the DC
terminals are normal. When the wire is removed and no
continuity is <onfirmed between these terminals. the
terminals are also normal.
Fig. 1 l-4(81
Fig. 1 l-5
11-1-6 CIRCUIT BREAKER
Check continuity between each of two terminals at the rear of the circuit breaker while it is mounted on the control panel.
Normally. there is continuity between each of the two lvhen the circuit breaker is on while there is no continuiq when the
circuit breaker is
ofi.
16P coupler wiring]
DARK BLUE
YELLOW
RED
BLACK
BROWN
WHITE
Fig. 11-6
- 26 -

11-2 STATOR
Measure the resistance of each stator coil using the circuit tester.
Classified coil
I
Main coil : Condenser coil
I
!
I
I
Cord color of @
AC coil
For use with the I
frequency
meter /
DC coil : Condenser coil
Measurement
location
50Hz-110V
60Hz-110V
50Hz-120V
j
60Hz-120V
50 Hz - 220V
!
60
Hz - 220V
50
Hz - 230V
50
Hz - 240V
6P coupler j
3.4R ’
2.6
I
3.3 j
2.7 ’
13.9
11.4
15.2
15.2
I
6P coupler
0.2251
0.16
0.22
I
0.16 ,
0.22
0.16 ,
0.22
0.22
I
Rectifier 1
Between
connector j
connectors
I
1.1n I
8.9R : White/Green
I
:
0.9
7.6 White/Red
1.1
8.9 Brown
I
7.6 Blue
0.9
1
I
1.1
8.9 : Gray
0.9
i 7.6 Pink
1.1
8.9 i Orange
1.1 j
8.9 Orange
Table 11-l
(at 21cC)
NOTE: If the circuit tester is not sufficient/y accurate, it may not show the values given and may give erroneous readings.
Erroneous readings will also occur when there is a wide variation of resistance among coil windings or when measurement is
performed at ambient temperatures different from the values specified in the space directly upper the table.
[6P coupler wiring]
DARK BLUE
YELLOW
RED
BLACK
BROWN
- 27 -

Table 1 l-2
Fig. 11-11
NOTE 1: Measure the resistance of each coil winding while the diode and each resistor are disconnected with the/r solder
removed.
NOTE 2: If the circuit tester is not sufficiently accurate, it may not show the values given and may give erroneous readmngs.
Erroneous -eadings will also occur when there is a wide variation of resrstance among coil windings or v/hen measurement
is performed at ambient temperatures different from the values specified in the space directly below the table.
11-4 IGNITION COIL
[APPROX 162:
Resistance value
0.61’1
7.52
I
Measurement location
B~tl::ee? The con-e and the gree? cord
Betkseen the grew cord and the high-ttvsor cord
Table 7 7 -3
- 29 -

11-5 CONDENSER
Measurement of capacity substitutes for checking the condenser. The capacity of the condenser cannot be measured by
using the circuit tester. Therefore. the generator is run with a new condenser to see whether or not the generator performs
normally. If the generator performs normall>-. the condenser is normal.
Reference: If an instrument ii available for measuring the capacity of the condenser, the total capacity range should be 70
to 7 7pF fat 20°C).
When the condenser displays its total capacity within this range, it is normal.
11-6 RECTIFIER
Using the circuit tester. measure the resistance between
each of the two terminals of the rectifier. The rectifier is
considered normal when the respective resistances have the
values specified below.
NOTE: Each of the given values changes with the polarity
of the circuit tester.
Green Red
White@ [
01
3 :...16RI
.160 1
@
#3
. .
\
Y
,
The polarity of the circuit tester
Table 7 l-4
-30-

12. DISASSEMBLY and ASSEMBLY
12-1 PREPARATION and PRECAUTIONS
1) Be sure to remember the locations of individual parts when disassembling the generator so that the generator can be
reassembled correctly. Tie tags noted with the necessary information to facilitate easier and smoother reassembly.
2) For more convenience, divide the parts into several groups and store them in boxes.
3) To prevent bolts and nuts from being misplaced or installed incorrectly. place them temporarily back at their original
positions.
4) Handle disassembled parts with care; clean them before reassembly using a neutral cleansing fluid.
5)
Us2
all disassembly/assembly tools properly, and use the right tool for each specific job.
12-2 SPECIAL TOOLS for DISASSEMBLY and ASSEMBLY
-
Fig. 12- 1
b
\o
3
(D
No.
Tool No. ;
Name of tool
1
2309500107
Valve spring retainer
1
,
Description
For disassembling and assembling the intake
and exhaust valves
2
2309500207
Valve guide puller To pull out the valve guide
3
3589500107 :
Rotor puller To pull out the rotor
Table 12-l
-31-

12-3 DISASSEMBLY SEQUENCE
I
I
Sequence Part to remove I
Description
Precautions
Necessary tools
1
Side cover (Lj
(1 j Remove both the left and right
!
2 PlUj
screw-
and (Rj
co\-2rs. by taking out eight 31-C
driver
I
flang2 screws.
I
-I
Couplsrs (dis-
1 (1) Disconnect th2 (6Pj coupler
of
Pull them under
connection)
the generator from the other (6P) while pressing
extending from the control panel.
1 down the retainer
claws.
622
Fig. 1 Z-2.)
!
3 ’ Choke cab12
(1) Set the engine control to STOP.
rs Minus
I
and remove the screw from the
screw-driver
I
tip of the choke cable to disconnect the choke cable from
the dial plate.
I
(2)
Disconnect the outer cable of the
1 1Omm box spanner
choke cable from the fuel tank
bracket.
(3) Loosen the M4 screw of the
!
carburetor choke lever swivel to
13 Plus screw-
driver
pull out the inner Loire from the
choke cable.
4
Fuel line
(1) Hold thz fuel line clamp inserted
/
Be careful not to
Pliers
inside the felt strainer using pliers,
’
and pull it backward to remove
damage the hose. :
the fu21 line from inside the
I
strainsr.
I
5
’ Fuel tank
handle
(1) Push up the end of the cover
I
fitted to the handle with finger.
r (2) Pull out the rubber tube use; as
the air vent pipe.
a (3) Remove two bolts (tank). and
1Omm box
remove the handle.
I
I
I spanner
Fig. 12-2
-32-

Sequence
Part to remove Description
Precautions Necessary tools
6
Rear cover
( 1) Remove the rear :over at the 1Omm box
opposing sid2 of the control spannsr
pan21 by unscrewing th2 four
I
$16 flange bolts.
7
Fuel tank (.I) Loosen the set screw of th2 ,z Plus screw-
strainer shaft at th2 rear of the driver
engine control switch.
(2)
Remove two M5 flange bolts
, (,See Fig. 1 Z-3.) !
1Omm box
clamping the front cover and spanner
tank bracket together. and tank
bracket together. and then
remove the fuel tank.
8
Front cover (.l j Rsmove two MS tlange bolts
1Omm box
clamping the front cover to
spanner
the basr to rrmove the front
cover.
,
9
Fuel hose
(1) Using pliers. hold the fuel line
Be careful not
Electricians’
clamp at the fuel support joint to damage the
I
of the carburetor (L-joint
’ fuel line.
! pliers
directed downward) to pull it
aside. Then. pull out the line.
10
Choke cable
(1 j Insert the tip of a screwdriver
(.tlat-headed type) in the groove
of the choke cable bracket protruding from the head cover.
3 Minus
screwdriver
11
I Muffler cover
(1) Remove the out2r cover; this is
Take care not to
and muffler
-3 Plus screw-
done by removing seven M5 drop the removed
driver
!
tapping screws.
screws down into
(2) R2move one M6 x 1’ flange the cooling air
! IOmm box
bolt of the muffler bracket. and
1 channel.
two M6 nuts from the muffler
spanner
’ (See Fig. 11.4.)
tlange. Then. remov2 th2 flange.
I
(3) Remove four 315 x 8 lock screws
from inside the muffler t I remove
the inner cover.
3 Minus screw-
driver
I
flUFFI
Fig. 123
Fig. 124
- 33 -

Sequence
1 Part to remove
Description
Precautions
Necessary tools
12
Bas2 platz
(1) Remove one set screw of the
T Plus screw-
earth wire which grounds the
; u
driver
rear housing and base
plate
I
togethsr (Zr)OV system onlv).
I
(2) Rsmove four 5115 x 10 bolts from
j
under the base plate.
Starter pullek
(1
13
Recoil starter
(1) Remove the recoil starter from
the rear housing. by removing
three 516 x 8 flange bolts.
j
Turn the starter pulley b]- hand
to set the piston to the compression stroke limit (lvhere the pulle)
becomes heavy). Csing a hammer
strike the box wrench set ov2r the
I
head of the through bolt to remove
I
the bolt. Then remove the pulleb _
I
(See Fig. 12-S.)
(See Fig. 1 Z-6.)
Smm box spanner
1Omm box
spanner
1 ?mm box
spanner
Handle hammer
Fig. 12-5 Fig. 12-6
Sequence Part to remove
Description Precautions , Necessary tools
15
Stator assemblq- (1 j Remove three M6 x 85 bolts
clamping the rear housing of the
stator assembly. and the front
housing together.
(2j
Remove the stator assembly- from
the front housing. The stator and
rear housing are removed together
by using a plastic hammer to light11
strike the boss of the rzar housing.
(3)
Remove the lead from the clamp
I . .
b_~- taking out one M4 x 8 scre\v.
.
I
’ 1Omm box
spanner
Plastic hammer
(See Fig. 12-7.) j
3 Plus screw-
_ driver
1 (4) Kemove both the capacitor and
I
: Cd Plus screw-
I
diode from the rear housing by
driver
I removing three M5 x 30 scre\\s.
/ (5) Remove the wiring between the
stator and rear housing. Discon-
i
nest three terminals irom the
diode. t\vo terminals from the
capacitor. and the ground \vire
from the r2ar housing.
-34 -

Sequence
Part to remove
16
’ Rotor assembl)
Description
(1) Fit the rotor puller to th2 rotor
shaft. and drive it into place to
Precautions
! Necessary tools
’ Rotor puller
remove the rotor from the engine
shaft.
Plastic hammer
1; Plug cap (1 j Remove the plug cap from th2
spark plug in advance.
(3) Remove the clamp of the high-
voltage power cable.
18
Front housing
and center
baffle
(1 j Remove the front housing and 1 Omm box spanner
center baffle from the engine
main bearing. b) removmg thrze
I
j
M6 x Xmm bolts and one M5
x 55mm bolt. (See Fig. 11.8.) t
CENTER BAFFL
FRO
Fig. 12-7
Fig. 128
Sequence
Part to remove
Description
19
! ~
Air cleaner
(1) Remove the center screw of the
air cleaner cover to remove the
cleaner cover. filter element. and
element retainer.
(2) Remove the M5 screw at the lower
right inside the element chamber.
(3) Remove tvvo M6 flange nuts
clamping the air cleaner and the
carburetor together to remove the
air cleaner.
Precautions
Necessary tools
i?
;s Minus screw-
driver
A
\fi Plus screw-
driver
i 1Omm box
spanner
! (See Fig. 12-9.)
I
AIR CLEANER
ELEMENT & ELEMENT
*
RETAINER
ELEMEN/T
?
Al R ‘CLEANER
COVER
FIQ. 10-9
-35-

Sequence
20
Part to remove
Governor and
related parts
Description
(. 1) Remove the governor lever from
the governor shaft.
(~j
Remove the governor rod, rod
spring. and governor spring.
Precautions
/ Necessary tools
I
Loosen the bolt
1Omm box spanner
(unnecessary to
remove it)
‘1
Carburetor
(1 j Remove the carburetor from
the stud area of the intake side
flange of the crankcase.
I
7-3
--
Head cover , (1 j Remove two M5 screws from the
.B Plus screw-
lateral side of the head cover to driver
I
remove the head cover.
33
24
Qlinder baffle
(1 j Remove the M6 bolt from the
i 1Omm box
crankcase and the $15 bolt from
5 anner
the main bearing cover to remove
5
+ Plus screw-
!he cylinder baffle. driver
Spark plug
(1) Remove the spark plug from the
19mm box
cylinder head.
:
spanner
25
Cylinder head (1 j Remove sev2n M6 x 32 bolts to
remove the cl-linder head.
(3) Remove the head gasket.
; Mark the head
1Omm box
gasket with its
spanner
mounting position
accurately matching the cylinder
head, also mark
the gasket mounting face of the
, cylinder head.
i Intake valve
(1) Remove both the inner and outer
B2
sure to posi- t 1Omm box
tappet chamber covers from the
crankcase. by removing two Y6
tion the notch in spanner
x 1: bolts.
the spring retain-
: (3) Remove both the intake and
er’s outside periphery to the front
exhaust valves.
13 Minus screw-
and hook the
driver
(3) Remove the valve spring and
minus screw-
retainer.
I
i driver (medium
I
side) in the recess
/ (lower side) of
I
a the retainer.
I
Then pull the
spring retainer ’
backward to remove it.
I@
1
RETAINER
PULL BACK
(1) Remove the Woodruff key from
the crankshaft.
(2) Remove five M6 x 15 bolts locking
1 Omm box
the main bearing cover from the
crankcase.
spanner
’ Plastic hammer
(3) Using a plastic hammer or a
Be
careful not
similar tool. strike the mam
to damage the
bearing cover uniformly around
i lip of the oil seal.
its peripheq to remov-e the cover. ;
-36 -

Sequence Part to remove
Description
I
I
Precautions
Necessary tools
28 ’ Camshaft
(1) Pull out the camshaft from the
Set the crankcase
crankcase.
sideways so that
it will not fall
i and damage the
! tappets.
29 ; Tappets (1 j Remove the tappets from the
I
crankcase.
Be sure to mark
the tappets to
, distinguish them
; from each other;
i one for the intake
1 valve and the
other for the
exhaust valve.
30 Connecting rod ! (1) Scrape off the carbon deposits
i Confirm the 1 e Minus screw-
and piston from the cylinder and piston head. , mounting direc- i
driver
Push open the bend of the connect- tion of the oil
I
I
ing rod lock washer, and remove
two bolts.
scraper. Pliers
(2) Remove the lock washer and con- 1Omm box
netting rod cap from the crank-
spanner
shaft.
(3) Turn the crankshaft until the
piston comes to its top position.
and push the piston from the
upper part of the cylinder.
31
Piston and
piston rings
(1) Remove two clips from the piston
(1) Replace
pin and take out the piston pin. these clips
Remove the piston from the vvit h new
connecting rod. ones: do not
(2) Each of the piston rings can be reuse them.
removed from the piston by opening wide the ring joint.
: (2) Be careful
not to
I
1
damage the
minor rod ;
end.
I
(3) Be careful
not to open
the ring
joint exces-
sivelv .
32
Crankshaft (1 j Pull out the crankshaft from the
crankcase. If unable to pull it out
by hand, use a plastic hammer to
gently strike the main bearing
joint tace. and pull the crankshaft
pulled out.
33
Governor shaft
(1) Remove the clip of the governor
!
shaft. and pull out the governor
!
I
I
shaft from the crankcase.
I
I
-37-

12-4 ASSEMBLY PROCEDURE
0 Precautions in Assembly
1) Thoroughly clean each part. When cleaning. take special care for the piston. cylinder, crankshaft, connecting rod, and
bearings.
7) Be
sure to completely remove the carbon deposits on the cylinder head and piston head. Also, thoroughly clean and
remove carbon deposits from each piston ring groove.
3) Apply lubricating oil to the lip of each seal. Confirm that the lip of each oil seal is not damaged. If damaged, replace
with new one.
4)
Replace the gaskets and similar items with new ones; do not reuse old gaskets.
5) Replace the keys. pins, bolts, nuts. etc., with new ones if necessary.
6) Do not apply torque exceeding the specified value.
7) Apply lubricating oil to both moving and sliding parts when they are assembled.
8)
Prior to assembly, check the clearance of each part, and adjust it if necessary.
9) When each of the main components are assembled, turn it by hand to check for smoothness of rotation and unusual
noise.
l
Assembly Sequence and Precautions
12-4-l GOVERNOR SHAFT
Put the governor shaft into crankcase, then drive the clip into position to secure the governor shaft.
124-2 CRANKSHAFT
1) Insert the crankshaft into the ball bearings of the crankcase.
2)
Fig. 104-l shows the dimentional tolerance of the crankpin.
OUTSI DE
-DIAMETER
Fig. 72-10
-38-

l
Tolerances of Newly Installed Parts
Thrust directional tolerance between the cylinder and piston skirt
0.008L - 0.047L
I
I
Top ring
! 0.2L - 0.4L
Clearance of piston ring joint
Second ring 0.2L - 0.4L
’ Oil ring
! 0.05L - 0.25L 1
Spare rings
Top ring
0.09OL - 0.135L
Clearance between piston ring Second ring 1 0.06OL - 0.105L
I
Spare rings
Oil ring
O.OlOL-0.065L ,
Inside and
outslde diameter
Clearance between connecting clearance
0.037 L - 0.063L
rod major end and crankpin
I
Side clearance 0.1 L - 0.7L
Clearance between connecting rod minor end and piston pin
O.OlOL - 0.029L
Clearance between piston pin and piston pin hole
0.009T - 0.01 OL
L = Loose T = Tight
Table 12-2
NOTE: The clearance between the piston and cylinder is checked by measuring the clearance between the piston and
cylinder skirt.
124-3 PISTON and PISTON RINGS
1) If a ring expander is not available. set the ring joint at
OPEN ENDS OF
PISTON RINGS
the first land of the piston. as shown in Fig. 12-l 1 so
that the ring can be slided into its groove.
NOTE: Be careful not to twist or expand excessively each ring. The oil ring is fitted first on to the
piston, followed by the second ring and top ring-
The
top
and second rings must be fitted with their
marked sides kept upward.
Fig. 12-l 1
~j The connecting rod is joined to the piston by the piston pin.
NOTE: Before assembly, apply sufficient lubricating oil to the connecting rod minor end
NO JE: Be sure to fit the clips to both sides of the piston pin.
-39-

STD EQUIPMENT ! SPARE PARTS
- Top ring
’ Taper
\
Second ring
Taper
‘\
\
Oil ring
I
Fig. 72-72
Taper
I
. \ ‘,\
x.
Undercut :.
q \ . .
1244 INSTALLING THE CRANKCASE
1) The connecting rod is put into the cylinder while
holding it with the piston ring guide. as shown in Fig.
lo-13 (in the case that a piston ring guide is not
available, press rings inward with fingers and at the
same time. strike down the piston. using a wooden
block). The connecting rod must be mounted in
place with its @ and MA marks directed to the ball
bearing side of the crankcase.
NOTE: Apply a sufficient quantity of oil to the
piston rings, connecting rod surfaces, and cylinder.
NOTE: The top, second and oil rings are fitted to
the piston with their ring joints arranged 90’ off each
adjacent joint.
Fig. 72-73
12-4-5 INSTALLING THE CONNECTING ROD
MAJOR END CAP
1 j Manually turn the crankshaft until the piston reaches
top dead center. Gently strike down the piston head
until the connecting rod touches the crankpin to
install the connecting rod major end cap.
3) The cap is installed with the 011 scraper positioned
right-downward. (See Fig. 13-14.)
NOTE: Be sure to use a new lock washer; and carefully bend the washer correctly.
NOTE: When the cap has been installed, turn the
crankshaft to see if the connecting rod moves smooth-
Iv.
NOTE: The correct torque for installing the connect-
ing rod major end cap is 60 to 80 kg-cm.
NOTE: See Table 72-2 for details regarding the
clearances between the piston, piston rings, and
connecting rod and their counterparts.
Fig. 72-74
OIL SCI
GUIDE
RAPER
-40-

12-4-6 INSTALLING THE TAPPETS and CAMSHAFT
Install the tappets. and then the camshaft.
NOTE: Align the timing mark at the base of the cam gear
with the timing mark of the crank gear. If the valve timing
is set incorrectly, the engine will not run or operate proper-
ly. (See Fig. 72-75.)
NOTE: If the intake and exhaust valves are installed in
reverse order, tappet clearance will be incorrect.
Fig. 72-75
12-4-7 INSTALLING THE MAIN BEARING COVER
Install the main bearing cover to the crankcase.
NOTE:
The governor gear is already mounted to the bearing cover; therefore, it is necessary to confirm that the governor
gear is meshed with the cam gear. (See Fig. 72-76.)
If the oil seal requires replacement, pressure-fit the new oil seal in position before installing the main bearing cover.
NOTE: Prior to installation, apply oil to the bearing and oil seal.
Apply a small amount of oil to the cover fitting face,
as specified, in preparation for installing the bearing cover packing.
Place the oil seal guide over the crankshaft so that the
oil sea7 lip will not be damaged during installation.
Make sure that the side clearance of the crankshaft is within 0 to 0.2mm.
If necessary, adjust the clearance, using the adjusting collar.
(see Fig. 72- 7 7.)
NOTE:
Torque for the main bearing cover: 80 - 7 00 kg-cm.
MAIN BEARING COVER.
fY;ie;
GOVERNOR GEAR
‘-
Fig. 72-77
-41 -

*Shown in Fig. 12-18. is the method to measure the side
clearance of the crankshaft. According to this method,
measure the clearance between the machined face of the
crankcase and the adjusting collar. The machined face of
the crankcase is mounted with packing so it is necessary to
set the clearance properly by allowing for a packing thickness of O.??mm. -I
M6 x 25mm bolt . . . . . . . . . 8 PCS.
M6 x 55mm bolt . . . . . . . . . 1 pc.
Fig. 72-78
12-4-8 INSTALLING THE INTAKE and EXHAUST VALVES
Prior to installing. remove carbon and gum deposits, from the valve, valve seat, intake and exhaust ports, and valve guide.
NOTE: If the valve face is worn, replace the valve with a new one.
NOTE: If the clearance between the valve guide and valve stem is excessively large, replace the valve guide with a new one.
Replace the valve guide by using a pull block and pull bolt as shown in Fig.
72-20.
A
VALVE FACE
VALVE SEAT
- VALVE STEM
VALVE GUIDE
VALVE SPRING
E GUIDE
PULLER
Fig. 72-79
‘VALVE RETAINER
A:
Valve
face angle
B: Valve seat angle
C: Valve guide inside diameter
D: Valve stem outside diameter
Intake valve
Exhaust valve
Fig. 72-20
45”
45O
I
5 59 +0.018
I
0
I
-0.020
I
5’59 -0.032
I
-0.056
5.5@ -0.074
Clearance (clearance between C and D)
between valve guide and valve stem
Intake valve
0.02OL - 0.05OL
Exhaust valve
0.056L - 0.072L
Table 72-3
L: LOOSE
-42-

12-4-9 TAPPET ADJUSTMENT
Set
the tappet at
1112
loa-est position to depress the valve. Then measure the clearance
between
the valve and tappet stem.
using a clearance gauge inserted into the clearance. (See Fig. 12-21.)
NOTE: As with the intake and exhaust valves, the clearance between the valve and tappet stem must be within 0.1 f. 0.02.
INTAKE & EXHAUST VALVE
VALVE SPRING
NCE GAUGE
Fig. 12-27
Fig. 12-22
NOTE: If the clearance is smaller than that specified, slightly grind down the valve stem end using a grinder, then measure
the clearance.
If the clearance is larger than that specified, replace the valve with a new one.
Spot the valve seat and use some compound
to adjust the clearance.
NOTE: After completing adjustment of tapper clearance, install the valve spring retainers, and then recheck the tappet
clearance.
*Installing the valve spring retainer:
Using the special tool. place the retainer over the valve stem
with the notch in the outside periphery of the retainer kept
toward the front.
@
1
FRONT
12-4-10 INSTALLING THE CYLINDER HEAD
Fig. 12-23
Before reinstalling the cylinder head.
be
sure to remove carbon deposits from the combustion chamber. and clean between
the cooling fins. Also check the cylinder head for levelness.
NOTE: Replace the cylinder head gasket with a new one.
The cylinder head is installed using seven 516 x 32mm bolts.
NOTE: Torque for each cylinder head lock bolt: 90 - 7 70 kg-cm
12-4-11 INSTALLING THE SPARK PLUG
Torque for spark plug: 120 - 130 kg-cm
12-4-12 INSTALLING THE CYLINDER BAFFLE
The
cylinder baffle is installed to the crankcase, using the M6 x 20mm screw and to the main bearing cover. using the M5
x 1Omm screw.
The cylinder baftle and
fuel
line clamp are installed. together to the crankcase.
-43 -

12-4-13 INSTALLING THE HEAD COVER
The head cover is installed over each of the left and right parts of the c>-linder head. using the 345 x 1Omm screws.
124-14 INSTALLING THE GOVERNOR and RELATED PARTS
Model EYOSD has a centrifugal iveight type governor which is installed while engaged with the governor gear. With the
governor. the throttle valve of the carburetor is controlled automatically by using a lever link mechanism. Therefore. engine
speed is constantlq- maintained even under load variations.
1)
‘j
3)
Using two $16 x 1Omm bolts. install the speed control assembly to the crankcase.
Temporarily install the carburetor with two h-16 tlange nuts.
4)
5)
6)
Join the throttle lever of the carburetor to the governor rod and rod spring.
Insert the governor lever into the governor shaft.
Insert a minus screwdriver into the groove of the
governor shaft. and turn the screwdriver fully in the
counterclockwise direction. Push the governor lever
clockwise (at this time. the throttle valve is fully
opened) and fasten the governor lever with the lock
bolt.
Torque for the governor lever: 70 - 90 kg-cm
Link the governor lever and speed controller with the
governor spring. one end of which is inserted into the
center hole (of the three) of the governor lever and
Fig. 12-24
IING
the remaining end inserted into the hole of the speed controller.
Fig. 12-25
Fig. 12-26
12-4-15 INSTALLING THE CARBURETOR and AIR CLEANER
Place the carburetor gasket. insulator. gasket. and carburetor in the correct positions. Kest. fit the air cleaner gasket and air
cleaner case. and install them. using the hi6 flange nut and 315 x 1Omm screw. Set the element (small type). element retainer. element. and cleaner cover. and tighten them with screws (slot head tk-pej.
Torque for installing the carburetor and air cleaner:
50 - 60 kg-cm
NOTE: See page lo-26 for details concerning disassembly and assembly of the carburetor.
-44 -

124-16 INSTALLING THE CENTER BAFFLE and FRONT HOUSING
1 j Set the knock hole of the front housing to the knock of the main bearing cover and assemble them together. During
assembly. place the center baffle between the main bearing cover and front housing.
Torque for the front housing: 80 - 100 kg-cm
12-4-17 INSTALLING THE IGNITION COIL
1) Install the ignition coil and grommet (IG-COIL) to the front housing. Simultaneousl>-. temporarily set the generator
rotor in position.
-4nd assemble the ignition co11 and magnet together while adjusting the air gap between the two to
0.4 to 0.5 mm.
Firmly bond the grommet to the front ensuring that there is no residual clearance.
(use
CEMEDINE 575).
2) Fit the plug cap on the spark plug.
124-18 INSTALLING THE ROTOR ASSEMBLY
Install the rotor assembly to the taper of the crankshaft with their keyways in line.
NOTE: Thoroughly clean the tapers (both male and female tapers) of oily substances.
12-4-19 INSTALLING THE STATOR ASSEMBLY
1) Install the stator correctly into the recess of the rear housing. Sate the leads and their positions.
2) Install the wiring between the stator and rear housing.
Connect the wires from the stator IO the capacitor
(with these wires joined to two black top terminals).
Also connect the wires from the stator to the rectifier
(with these wires joined to three terminals).
GREEN RED
:EJ
Connect the ground cord to the rear housing. using
Refer to paragraph 9-2 for @.
one M6 x 8mm screw.
Install the stator assembly correctly into the recess of the front housing.
If necessary, softly strike the rear housing
with a plastic hammer (be careful not to strike the capacitor and diode).
Fasten the front housing to the rear housing of the stator assembly. using three M6 bolts, while the three bosses of the
front housing are set to their counterparts of the rear housing.
Torque for each bolt: 65 2 10 kg-cm
Clamp the lead of the 6P x coupler and the lead from the ignition coil to the bolts specified in paragraph d above.
using the wire bands.
124-20 INSTALLING RUBBER MOUNT (A)
1) Fit rubber mount (Aj to the bosses (two) at the lower center of the crankcase.
2) Also fit another rubber mount (A) to the bosses at the lower part of the stator assembly of the generator.
124-21 INSTALLING THE STARTER PULLEY
Install the starter pulle) to the rotor shaft using the rotor through bolt.
Torque for the through bolt: 100 - 150 kg-cm
124-22 INSTALLING THE RECOIL STARTER
Install the recoil starter to the rear housing using the M6 flange bolt.
-45-

12-4-23 RUBBER TUBES for USE as AIR VENTS
Connect two rubber tubes to the air vent connectors of the carburetor. Keep theje rubber tubes suspended downward from
the air vent connectors.
12-4-24 INSTALLING THE BASE FRAME
1)
Install the base frame with its rear side facing the
welded nut area of rubber mount (A). Match the
rubber mount (A) which is fitted to the lower part of
the engine and generator. Base frame is installed
using four MZ bolts.
3)
Insert each rubber tube from the air vent connector
of the carburetor into the hole in the base frame.
3)
Fasten the ground terminal of the ZOOV power
system to the rear housing using the $16 bolt.
-/
EASE PLATE
12-4-25 INSTALLING THE MUFFLER and MUFFLER COVER
Fig. 12-27
1) Fit the gasket (for the muffler cover) to the studs of the exhaust flange of the crankcase.
3) Using the 545 scre\vs, install the muffler cover in place.
NOTE: Be careful not to drop the screws into the cooling air channel.
3) Set the gasket (for the exhaust port) on the studs of the exhaust port flange. Then, mount the asbestos sheets to the
upper and lateral sides of the muffler. The muffler is installed while secured to the muffler flange using two M6 nuts,
and also to the muffler bracket by using one M6 bolt.
4)
Install the outer muffler cover place using seven MS tapping screws.
Torque: 70 - 90 kg-cm
124-26 INSTALLING THE CHOKE CABLE
1) insert the inner wire of the choke cable into the swivel of the choke lever.
2) Insert the outer 2nd of the choke cable into the wire bracket of the head cover; temporarily tighten the outer end so
that it will not slip out of the uzir2 bracket.
NOTE: The inner wire is installed later. Leave it loose in the swivel.
12-4-27 INSTALLING THE FUEL LINE
1) Connect the fuel line to the line connector at the fuel supply port of the carburetor. Then. fasten the line so that it
will not come
oii
the line c’onn2ctor.
2) Secure the
fuel
line with the clamp of the cylinder baffle.
124-28 INSTALLING THE FRONT COVER
Using two h16 x 8mm flange bolts. install the front cover installed with the control pan21 to the base plate. Keep the engine
switch set at STOP.
12-4-29 INSTALLING THE FUEL TANK
1 j Keep the strainer shaft at the lower part of th2 fuel tank m a position that will allow the setscrews to be tightened
from the opposite direction of the muffler.
2) Insert the flexible shaft extendmg from the rear side of the engine switch which is mounted on the control panel into
the square hole of thr strainer shaft.
-46-

3) Align the mounting holes at the lateral side of the front cover with those in the bracket which are bolted to the fuel
tank. Then. install the fuel tank. using t\vo $16 x Emm flange bolts.
4) hlake sure that the flexible shait on the control dial side is inserted in the square hole of the strainer shaft. then fasten
the flexible shait .
124-30 INSTALLING THE REAR COVER
Align the mounting holes at the lateral side of the rear co\-er urth those in the
fuel
tank bracket. Then install the rear cover-.
using two 516 x gmm Slang2 bolts.
Also align the holes at the lolver part of the rear cover s-ith those in the base plate. and
install the rear co\-er by two M6 x Smm flange bolts.
124-31 INSTALLING THE FUEL TANK HANDLE
1) Set the bolt (to secure the tank handle) in the handle and assemble the O-ring to this bolt from the opposite side.
Then. tighten the bolt to install the handle to the
fuel
tank.
NOTE:
Be sure to direct the less slanted part of the handle toward the front cover.
2) Insert the rubber tube end over the protrusion oi the bolt (for the
15121
tank)
and push it
down to the base of the pro-
trusion.
NOTE:
Be sure to keep the air bleed hole at the center of the rubber tube directed upward.
3) Place the handle cover over the handle.
12-4-32 INSTALLING THE FUEL LINE
Insert the fuel line end over the fuel strainer joint (be sure to push the line end down to the joint base). and secure it with
the clamp.
12-4-33 INSTALLING THE CHOKE CABLE
1 j Insert the choke cable adjusting screw in its hole on the fuel tank bracket.
2) Secure this adjusting screw with the M6 nut and tighten to the midway point of the threaded part.
3) Set the dial of the control panel to STOP. and connect the locknut of the choke cable end to the panel.
4) Pull the inner wire of the choke cable to clamp the wire to the choke lever. using the setscrew.
124-34 CONNECTING THE COUPLERS TOGETHER
Connect the coupler (6Pj from the generator to the coupler (6P) extending from the control panel.
Also connect the stop wire (green) as required.
12-435 INSTALLING THE LEFT and RIGHT SIDE COVERS
Using the MS flange screlvs. install the left and right side covers in place.
-47-

12-5 CABURETOR
12-5-1 FUNCTION
and
COMPONENTS (See
Fig. 12-28)
1) Float system
The
float chamber is located direct& under the carburetor. Flat and needle valves. maintain a constant
id
level
inside the float chamber.
The fuel in the tank tlo\vs into the float chamber from the needle valve. When a certain quantity of fuel enters the
chamber. the float rises. When the buoyax)-
oi
the flat \-alve balances with the fuel in-flow pressure of the needle
valves. the valves close to keep the fuel at the correct level.
Schematic diagram of the fuel system
CHOKE -
BY PASS;
THROTTLE
r VALVE
,-PILOT OUTLET
PILOT AIR JET
PILOT JETJ’
MAIN AIR JET?
FLOAT
L-d
.“.- MAIN NEEDLE
/.-NEEDLE VALVE
FLOAT i ‘MAIN JET
Fig. 72-28
-48-

2) Pilot jet nozzle system
The pilot jet nozzle system controls the fuel supply for engine speeds ranging from idle to low-speed running. The
sytem operatzs with the
fuel
flowng through the main jet nozzle and up to the pilot jet nozzle where the tuel is
measured. When the fuel is mixed with air. the volume of the air-me1 mixture is also measurzd by the pilot air jet.
From this stage. the mixture is supphed to the engine t‘rom the pilot outlet and bb-pass. During idle.
fuel
is supplied
mainly from the pilot
outlet.
3) Main
jet
nozzle system
The main jet nozzle system supplies
fuel
for middle and high speed operation. The fuel flows to the main jet nozzle
where the fuel quantit) is measured. and then flows to the main nozzle. Air volume. which is measured by the main
air jet ~ enters from the bleed hole of the main nozzle and miszs with fuel to form a gas mist.
The gas mist flows out of the main bore and is again mixed with air from the air cleaner. From this stage. the correct
air-fu21 mixture is supplied to the engine.
4)
Choke
The choke helps in starting the engine in cold weather.
When the engine is started with the choke valve closed. negative pressure applied to the main nozzle rises. allowing
most of fuel to flow through the main nozzle.
-4 mixture with a high gasoline concentration is fed to the engine resulting in easier engine starting.
12-5-2 DISASSEMBLY and ASSEMBLY of CARBURETOR
The most common trouble with the carburstor is failure to provide the correct air-fuel mixture. This is generally caused blblockage in the air and fuel channels. at other times it is caused by fuel level fluctuations in the float chamber. In order to
maintain the carburetor in normal operating condition. it is vital that the air and t‘uel channels be kept clean. The following
descriptions are the procedures for carburetor disassembly and assembly. (See Fig. 12-19.)
1) Throttle mechanism
a) Remove Philips-head screw (77): throttle valve
(~8),
and pull out the throttle shaft (39).
b) When removing the throttle stop screw. a spring (3 1 j will also come off. Be careful when handling the throttle
valve to prevent the valve edge from damage.
2) Choke
a) Remove Philips-head screw (12). choke valve (23). and pull out choke shaft (24’).
b) Be sure to keep the notch of the choke valve positioned forward the main air jet side when the choke shaft is
installed.
3) Pilot jet nozzle
a) Remove pilot jet nozzle (?I ). When removin,.
0 use a proper tool so that the nozzle will not be damaged.
b) Firmly secure the jet nozzle when the carburetor is assembled. Otherwise, fuel will leak from the nozzle and
cause engine trouble.
4) Main
jet
nozzle
a) Remove bolt (15). and float chamber bodl- ( 13).
b) Remove main jet nozzle ( 19) from carburetor bodk (9j.
c) Firmly secure the main jet nozzle when assembling. Othzrwise. air-fuel mixture will become excessiveIF rich and
the engine will not operate properly.
d) Torque for bolt (15) is 70 kg-cm.
-49-

5) Float system
Pull out tloat pin (13) and remove float (I 1 j and needle valve
(,30).
* Avoid using a drill or a wire to clean the fuel passages (they map damage the orifice of the pilot and main jet
nozzles’). Use compressed air.
* The float pin is peen-secured to the carburetor body; the needle valve and float can be removed out from the op-
posite side of the peen-secured part b>- lightly striking the float pin with a thin bar-like object.
27
/
28
24
1'
Fig. 72-29
- 50 -

13. TROUBLESHOOTING
DIAG: DIAGNOSIS
8
DIAGNOSIS BY THE CUSTOMER
0
DIAG. 01
Engine fails to start.
?-
-)
DIAG. 02
Electricity not generated.
If the generator doesn’t perform properI>- or fails to run after troubleshooring. ask a qualified service dealer to
check it.
n
DIAGNOSIS BY THE SHOP
A. Fails to start
3) DIAG.
11
4) DIAG.
1:
5) DIAG.
13
6) DIAG.
14
7) DIAG.
15
8) DIAG.
16
9)
DIAG. 1’
10) DIAG.
18
11) DIAG.
19
12) DIAG.
20
13) DIAG.
21
B. Engine defective
14)
DIAG. 3 I
15) DIAG.
32
16) DIAG.
33
17) DIAG.
34
18) DIAG.
35
C. Control Panel
19) DJAG.
36
20) DIAG.
37
The fuel tank is emptkContaminated by water or dirt
Spark is weak of wire harness
Spark is strong of wire harnzss
Compression is insufficient
Compression is nonexistent
Cloggsd fuel pipe
The fuel doesn’t enter into the carburetor (No flow from the pipe)
The fuel doesn‘t enter into the float chamber (Flow from the pipe)
The fuel doesn’t enter into the combustion chamber (Fuel exists in the float)
Carburetor flooded
Excessive noise (Improper maintenance) . . . . . Check oil element
Oil consumption increases (gets thin)
Excessive noise occurs and engine suddenly stops
Black exhaust fumes (Excessively large fuel consumption)
White fumes produced (Excessively large lubricating oil consumption)
Pilot light fails to light up
The frequency meter fails to show any reading, with the needle resting at zero
D. Engine operates but voltage is not normal
21) DIAG. 41
No AC voltage is output (Resistance load)
23) DIAG. 41
No DC voltage is output (Resistance load)
23) DIAG. 43
No DC voltage is output
14)
DIAG. 44
The DC output voltage is only 50% of the rated value
25) DIAG. 45
130% higher or more DC is output
26)
DIAG. 46
So AC voltage is generated
27) DIAG. 3:
AC output voltage is onl! 20% of the rated value
E. Power lacking and performance poor
28)
DIAG. 5 1
Poor operating condition
29) DIAG. 52
Engine speed does not increase
30)
DIAG. 53
Knocking. engine overheats
31)
DIAG. 54
Failure to generate output. no compression
32)
DIAG. 55
Poor performance (Backfire)
33)
DIAG. -6
Misfire or combustion outside the combustion chamber
-51 -

DIAG.
12
I
1
DIAG.
13
Engine
fails
to
stllrt
Check spat k
Engine fails
to
St;lrt
Check fuel
quality
Engine fails
lo
start
Check fuel
quentity
Spark is
too
weak
of
wire
harness
L1
Parts
I
Fuel tank
Fuel strainer
I
Plug cap
0
Spark plug
L
Rotor
High voltage
code
Coil is
shorted or
wire broken
I
High voltage
code and
conlacl
trouble
Coil
is
shorted or
wire broken
Air gap is
too
wide
Weak
magnet
I
Check
r"
1
v:
Check the air
ga
P
Searcher
Measure the
coil
resistance
Circuit tester
Items
to
check and
procedurc
Without
special equip-
ment,
it
doesn't work
Check
I
Check
Clean plug
lz:
cr
I
1
No
fuel
r-
I
=a:
Wire
broken
on:
Sl1ort
Standard
first
:
0.6
1
S2
second
:
7.5
ki2
I
r::1
Air gap
is
too
wide
Standard is
0.4-0.5
Plug cap
cot1tact
defective
Moisture
or
dust exists
Dirt present
Insulation
troublc
Checking
criteria
Weak
magnet
L
I
r-
Remedies
I
Fill
with fuel
El
Replace
Adjust and
reform
Replace the
rotor
Repair
or
replace
Replace fuel
Repair
or
replace
Clean
or
teplacc

--- -.
Sym(~lollls
_. . .-
P0ssil1lc
CilllSCS
___-. -_.
SI icky
I
8
I
_--.. I ,.
(Ilwck lllc
I
gaskcl
(‘heck
-r
- ] . .
--. .---
Lhlllil#Xi
gasket
OI
ovcrst poke
rmgc
-- 1
Mcasurc
dcglcc 111
lcvcl11css
. -_-
I -_ - ..-
Not level
Grmcl lhc
end ol' lhc
wlve
;1nd
F
atljllsl IllC
iappct Spa""
_ ..-_-
-. --
J
Ilclns 10
check and
proccdllt c
Oil
VillVe
SlClIl ilrld
n1ove
sm00111ly
(‘heck
-r
--
..,
I
.-
-. .I..
1
(‘I~ill~ltlCC
Narrow . . .
I.~iltljllSl
Wide . . .
WplilCe
Not SCCUI cd
lighlly
Gasket tlefec-
Over
Ilie
sclvicc liiiiil
(‘hccking
critcliil
._ . _.
ovet the
service liillil
SI Icky
I ivc
I- --
1

---.-
r
-.. -_ ,, .-
DIAC. 18 -1
-71
Ll
Syrnplorns
. .--
-- -,.
T I
PiIrIS
- .-
t-
-_ .- -
-I
No I’ucl t’lows OUI
CVCII wlwn
Ill0
I’IICI
t-tiigitic I’uils IO ~1211
pipe is diswrinccl-
Pucl
tlow II01 ClllCl
irllo llic ~;II~~III~~~I
cd' flOll1 the
c;lrhrelor
L-
?
-.,-
-I
-.. - - -,,..-
I 1
Fuel I’illcr
- --_ - -
L
--_ -_
Dcl’cclivc I’ucl
r 1
I’il~Cl
.--. --_ 1 --- --
.-- _
..- --- .-.
--.
i
--. --. -
- -1 . ._
Fuel sl rnincr :IWI
I’illcr
..- .__ --
- -.- L
-.,
The air hlectl is
cloggc1l
--.
1
..-
I
_-- -
I-...
r 1
Fuci slrniticr
_-.
I
-_-. -.
Fuel pipe
L _
-I
-.
-
-. ..- _
AlXllllllllilll1~l1 01’
ail
----.
I- -
-
-
1. --_
l’lic air bleed is
L I
clogged
1
..- ,-.- -..
-. -.
Possible
I
CiIIISCS
-.
_. ..-_ L- .-
(‘heck
-. .T- -
1
Chock IIN bolt 01
nihher pipe iri the
Ilanlllc
EXAM 3 I
Items IO
cllcck atld
[“‘occtlllrc
--
-. .-
Clhccking
crilerh
-_-- .-
Clwck
(‘llcck
-_. -1... ,-.-- -
-- _I _--.- .-
Air buhhlc exisls
- -. 7 -‘-
. -.._
I-- -
The ;lir tdcccl is
clogged
l)c~cclivc I’iiel I’illc~
Closed posilion
. . I -
L
__ .A--.
-,
Vent lllc
ilir
1
- L__ . ..- .- ._
1
(‘lci~r, llw I’illcl
Cl~lllCl~l OI’ lCi7lilW
IIIC
SllilillCl
L.. . ., _ ---
..A &..-,- .-.. .- .- --. A
r
.-. .- L-
VICi#Il
or
ICplilCe
1
I
Sel in lhe closed
posil ion
I
L
-- --._.
J

rl
Syl~lploms
-
(‘twk
(Tly lo 111ovc)
-._
I
--.
(‘heck
__ 1 ,_-. .,-
--.I.---
Measure the
tloar hcighl.
The stmit’icnt ion is IS 3
111111 t’l0111
body
(‘tlcck

!I
Synlplollls
Excessive noise
Possihtc
l r
CBUSCS
. .
..,.-
it2
.- ._- ..-. L -._
lJxcossivcly wortl
Li
sliding paris
(llsc ol’old oil)
-.
‘1
---
Cheek lhl!
COIll- I
prcssion
To 111 AC. t 5 or
lb
----- I
Excessively worn
sliding parts
((‘tlilllgC the
oil)
Check 1 tic COIUprcssioii
To DIAG. IS or
16
Lhn~agetl or
clogged
(Lack ol’ Iilainlc-
IlilIlCC)
Cltlcck
i._..I
Engine opcr;il ion
I
DIAC. 32
1
dmornial
l.nbric:iting oil
consunipt ion
increases (gels thin)
T' --."-
Check thcjel
(Jut number,
looseness)
-.
Dislalett
Wrong jet
illICe ol’ pislon ring
lirnil
._I.
L :
Fuel
---r
- ..I ,.-
_ .--..
I
-.
r
--
Kcplaco will1
m)rm11 1’ucI
:ind
check
-.,-
-I-
--

r:
Sylllt~IolnS
,, ._-. -
._
I’ossiblc
I.. 1
C'Il1sw
L
-.,...- ._-
C'tlccking
crileria
--
Noise protlucctl and
_-
I --
Scizurc 01 d;magc
ot' ltic piston 01
connecliiig
rod
__.. -.. I
.-
_ .,,.
(‘llcck
I
j
..- .-.. ‘,
Scizut
c OI' tlillllJlgC
01‘ I tic piston
01
connecling rod
--I
..-.
Lxccssivcly IillgC I’UCI
r-
--.
1. .--.
('ICillNZr ClClllClll
I
I
1 __.-
.-
(‘logging of’ It1e air
clcmcr clcnrcnl
,.- I .--.-
(‘heck
,.. .--
I-
I>ii I
I-
Rich rJJixlurc
- -. 1 --
Cheek IIIC main jcl
(i)r loosc~~css antI ,jct
nlllnhcl
To DIAG. 2 I
-I-
‘-- ‘-1
I)islorlctl . . .
Tighlel1
Wrongjel
To I)tA(;. 2 I
I -
Fuel
L 1
---.
I:ucl riiixctl wit I1
foreigli si~hsl;rnccs
.-
1
--
Repli\cc with normal
I’ucl ;III~I cheek
-.-- I-’ --

Hnginc
Ir011hlc
Ll
Excessively
Wtlilc t’~jlllcs Iqo luhri-
protlucctl
citlirig oil
co~~suriiption
--- _
-. _..-- I -.
WOlIl Ollf
III-
Sticky
1
.' I .--
.I-
(Ihcck
clcararicc of
pislon ring
-r
I
-. -
I -.-_.
r- -
---- -
Possihlc
c;Iuscs
r
I--
VillVC
WOrll
1Nll and
rctllln
valve
&,gglXl
Cheek
(‘orilnriiina-
I ion (mixed
with ot!iet
ll1illCriillS
like carbon’)
(‘heck
over tt,e
service
limit
C’hcck
(‘heck
1
--.- -
---
Checking
crilerio
Over ttic
slaiidard
qlltiIllily
ACctIlI\IIlillioii of’
carboll
Assclllt~lccl
upside
down
Over ltic
service liniil
Oil Icakage
____. ‘T. .._.... -

MAC.
36
I
- ----I
rncler I;lilS
IO StlOW
the needle res(ilig
(‘or~lrot /XlIlCt
Ttlc pilot light
I;lilS
10 light
Op.
-- . _ _.. _ ._ -7
I
I
-
Sylllptl~llls
.
._ .-
11
PiNlS
._
1
. .
The I’ilamcn~ is
-. -...- _ I-- --
-I
Wile broken
OI
stwrlctl
tkl’cclive
soltlcr,
and leutl broken
Wilt hlc~kcll
OI
‘lie diode is
ShCM 14
tlc(‘cct ive
I
‘W
I
1
__ _ L--
Mc;wrc
ltic
Icsislwlcc
. . L
(Across lhc Icr-
iliiii;ils)
c’ircuil Icslcf
I
___ _ .._ ___
1 ---.-
Mcasurc LIIC rcsisl-
illlO (LICIOSS 1 tie
t~l3l~ilMlS)
(‘ircuii lesler
Wl1cn 42 .*,
Wire hrokw
WhWl a2 . . .
Stlorlctl
%
I
1
_, .__
- I ..-... .-_
(‘lwk IIIC I’rcctucncy nictc~ I’or
clcclrical con-
lirluily
1 -,
1
MCLSIJIC
IIIO
rcsiul~~iicc
‘
(ACIOSS ltic Icrrni-
IlillS)
Circuil tester
I
I
When 42 . . .
Wire hrokcll
(‘lwck the sol&xcd
paI I
Circuil lcslc~
IlClllS lo
clwk and
ploccdurc
Mci\llSrc the
rcsislnncc
(hl’ coiiplcr)
L. I--
I-----
.I-__
Me;lsure I hc
rcsisl*lrlCC
. ‘
(ilCIl!SS lhc ICI’-
miii;lls)
c’itcuil lcslcr
Wilt hlokcn
-
When 42 . . . tt1e
rcatling ol’ Ilic’
7
circuil Icslcr mq Itic
ICiltl Zllld
SOldL!f
LIIC
ttefcc~ive
WllCll 41 . . .
Witc hlokw
wtlcll OS1 . . .
SIIOI lCll
!.
(‘lwcking
CI ilcl i;i
.-

Kerr1cdies
I I
To DlA(;. 40
I
Mcasurc AC outpul
EXAM I
AC voltage is low by
Vc~y low 01 rlotIIing?
hginc is opcr;rtirrg well
MCISIJW
AC output
Measure DC
OIII~UI
EXAM 1
.--- - _ _
_ .__-.. .,.- .
-ir
_. ,. _-. _I_
To DIAG 45
To INAG. 43
To I)IAC. 44
1

Sylllpllm
.--.. -
[_1,
I~eiiiedies
.-, L.
L 1
Slulor IX1 coil
I
--..
.-
I
Wire hrokcn OI
shor INi
Measure Ihc rcsisl-
cliodc terniinds of
Wllerl 42 . . .
Wire blokcn
WllCll OS2 . . .
Stlortcd
The diode is tlct’cctivc
-
--I... .
Measure ~IIC tesislance
(;wwis the lcrniinas)
Circuil leslcr
-_ ,.lI
.-. I
__ _--.
When
l hc rcsislnnce
differs 1’1om the
1
slandard value
-
-.-
1
. --._.
Stator main coil
I
--
1
Mcasurc
I~IC
resistance
(across the lcrminals
01’ tlw 61’ coupler)
(‘ircuil lcslcr
.._. ., I . -. .-
-I
___. _-
1
WllCll 42 . . .
Wilt broken
wl\cll OS2 . . .
Shorlcd
-
--.,. --.-
DIAC,. 44
-_... _1
-. __..-
The IX’ oulput
vollagc is only SCYj%
01’ lhc ralctl value
- -I
One diode is def’cctivc
;7
IXiltl
r -1
-
Tile soldered pilrt is Tile soldered pilrt is
dcl’cclivc,
;rd the
lead dcl’cclivc, ;rd the lead
is hrokcn is hrokcn
1
Measure 1 hc resistance
(xross lhe Icroiinals)
(‘iicuil lcslei
-.
1
----
-_ - ..-
---
Whcri tlic resistaucc
tlil’fcrs I’rom lhc
Stillld~lld
Villue
Mciisurc the iosislance Mciisurc the iosislance
(iICrOSS
lllc
Icrniin~ils) (iICrOSS
lllc
Icrniin~ils)
Circuil lcslci Circuil lcslci
..L .-

..-
r1
Symptoms
--
.
r]
PiirIS
.-. .
IN’%, higher or more
IX: is output
i
l+rigirie running speed
is high
..__
T
-.
A
. . -.. . -
1
-. -
.._-J-
! 1
SlillOr
coiidenser
coil
-.- ._,
T
L.- -.-.
r 1
Condenser
r
-,..-.
..,, .._-
-r
_I. .-
L 1
Staler
tllilill coil
-7’ ---
- _-_-
Wire broken
OI
shortctl
1 ,,
r I-z .-
Mcasure
LIIC rGst:lllcc
(bclwccn llic Icr-
riiimds)
Tlrc
circuit tester
When 42 ..,
Wire hroken
When OS2 . . .
Shorted
-.
I
.- -,.....-
---
I. Wire broken
shorlcd
2. Kotor resistor is
dcl’cct ivc
3.
Kotor tliotlc is
del’ccl ivc
1
-- ,.--
1
Mci\sure the resislancc
across
tlic
resistors,
with solilcr
imoved.
MCiISIJIC
tile resislawc
01’ the rolor rcsislor,
ilntl cllcck
111~
tliotlc
li)r
lll~lIllIilCy
I) When 42 . . .
Wire brokcll
WllCll t-Is2 . . .
Shorlcd
) TIIC
resisI:lrlcc
tliI’l’crs by
as tiiuch
as 10%~ from lhc
slarldard value
1--- .--
r-” 7
-. ._ .---
-_--
McilstJre
the capacily
(circuil tester c;~ii nol
hc used li)r this
Possible
CilllS~S
The cngille running
spcctl is higher lhan
nornd
Wire hrokcn or
shorled
- --I
1
I- -
MCilsurc
111~
resistance
(between the ter-
IlliJliJlS)
The
circuit A lcstcr
1 I-
When 42 . . .
Wire blokcn
WhCll u2 . . .
Shorlcil
-_
T
_-.-. --.. -
I lerris lo
check ;md
lmxedure
To DIAG. 52
C’hcck 111e
governor
~-_.-
(‘hecking
criteria
_ 11 __ _r ..-.- _-,x
-.--_
..-
I ‘1
. _ .._. _ .-_-
Kcnicdies
AI
L..-----I _-_-.--_ ___ 1
-
____
--l- _--
DilTcrcnl I’rwn
the
slilrltlad
WlilC
-_
I
- .--. -
L . . . _--.
-
Replace the condcnscr
1
I1
L
Keplilce the
rolor
_ - ..-__ ,_-.
-.- J
L. ---1
L., ._... . ___ ,- ..,,, ..A

A(: OUllW1 VOlliIgC
is only 20f% ol’ lhc
ralcti value
._ ._
,1
Rotor
c
(lonclenser
_._- --..-
u
Pitrls
hgine
The cnginc speed is
lower than norrrial
---I- -
-7
The coil is shortcd
- ----‘T’ _ --
Shorting 0I’Ihe coil
rotor resistor
. .-.- .L ..__.. --
Aged or broken
Possible
1
causes
The coil is shorted
--_-_.
1
_-
I
E
I
__
.-A-- -.-
- . ..- - -1.
. . -.. -. -
To DIAG. 53,
Cheek
fhe
governor
.-.
I
_ .., . . . .,
Measure the rcsist-
Circuit tester
Mcasurc the resist-
311Cl!
(6P coupler lerlninills)
Circuit lcsler
Mensurc the capacitance (Ihe circuit
lcster can not be
used for I his measurement)
Measure the resistiItlcC (hctwecn the
lerminals)
Circuil tester
llcn1s
lo
cheek and
procedure
Checking
criteria
---
- -.-. - ,...
IS%, lower than
I he
coil
ililllllilId . . .
Shorted
IO’%, tlit’ferciicc
tllilll
llje
resister
stillltl~lKl . . .
Old
Dil’Tcrcnt I’roiri Ihc
standard value
Aged
Broken
TIIC rcsislance is
l Sfjh
lower
1lli111
llle
Slillldilld VillUC . . .
Shorlccl
TIIC rcsist;lucc is
1.5% lower
iliaii
the
standard
vihe ..,
Shorled
El
Remedies

---
Sylllpll~llls
..-
I
I T”
-
Possible
!
C3IISCS
---- -
_- --
Iiems lo
CllCCk ;I1111
produie
._-
-.. _
C’hecking
CrilL’riil
-. -
J
Dcl’ective selliiig
ol’ the governw
lever
illld
level
shnl’t
I
.- --.-..
---
_..-- --
Check ihe set
posil ion
---
_-_.
_
1.
.-
Dc~cctivc wiling
Poor or clcl’cclive
perli)rmullcc
(‘lwck
ihc II~OVC-
1
._ _-.
Incorrecl
llilllg-
ing posiliorl .,.
Kcplacc
Dcl’cctivc govcrritri
spring . . .
KeplilCe
-_ _ -.
T
..-_ .-
Worn
0111 .,,
I
Keplacc
I---
L
I,eilll
nlixlurc
.._
r
-.,_ .I---.---
1
(‘llcck I hc I’ucl pipe
of cnburctor
-___. - ----,
_-,,-
L
.-
1
-_ 1
C‘0lllillTli~lilli1~ll . . .
ClCilll
T-j- --I
--
: .
‘I’0 I)IAG. I7
_., .._-...
.- -
T

._.-
Possible
r1
C’I 11 scs L
__ .-._
,,, ..--.
I
(‘hccking
crilcriil
. .- ..-.
Ikt’ecl ivc sell irig
-_. --- I -.-
Check the SCI t ing
I
EXAM 54
-7 A
- .- I ~-.-
The
goveinor is in-
correctly set, iulcrf’eriiig with lhc
lhrolllc valve’s
opciiing.
--I- -
--
_---
,n
Valve
..-,- -.-, -, I ---
. .
The liming ol’ ihe
valves is tlcl’ectivc.
Acljuslmcni ol’cleilr-
iIIlCL! is incorrecl
DIAC. 52
Kngiiic speed 110CS
no1
illcreils~
4
. .-..
_ .--_
I
C’ilrburclor and ilir
a
cleaner
---_- -1. _...- -.~
Mixture is incorrect.
-. .,,_,--.- -
Cheek the carburator.
t;XAM
(‘heck
lhc ;lirclenncr
owner’s iiianuil
- . ..- .-
i=:
I --.-
and iiiul’ller
ilre
(‘heck by eyes
ZIIY
1
I
t%?Clriciil load
---
/ Ovill~;iillil
Correct to the
Stilllcl~rd
hltl
AC ; To WAC; 46
DC; To DIAG 43
--, -_--
L
OWrlOilCi

- _ --. ..- ..---- --
.----
.-.-
l
I.
r 1
ldeclric lid
---I-- --
.__ L-.-.
i,
Spark plug
--
r--- l
.._ -I -.....-
L 1
Cnrburctor
___-_ .--
I
__I ._--
Cylinder
heiltl
I 1
hind cylinder
_. -. .-. _. ._ .-
1
,_______ -l.---.
I 1
(‘ylimler licad
rnul’fler
. .
I
1
PiIrIS
I’ossib lc
) I!
CiIlISCS
.
,-
---I. ._-
-. - -r
,, --.
. . __- ,... -._ 1 _- _.
1
1
AClXllllllliltil~ll Of
carhi
(‘ooling I’;llls
iIN!
clogged.
Overloading
Mcasurc I hc insula-
tion
resklilnc~ * .
* Adjust to the
standard
IWli
AC ; To 111 AC, 46
IX’; To DIAC; 43
_--_ ,.-
-
--. _. _..
J
--
3
wcii
I --.’ ”
8
I
--
___A
Cylinder
hcild
IrXAM SO
Mul‘llcr
I’XAM 65
I. ._.
1
-
llcrlls to
cl\cck
iIIIt1
proccdurc
Checking
critcriii
(‘llcck
Spccilj
ISM K4.A
(NGK)
I’XAM 5 I
OVCdlillll Lilltl
check IIIC corburc-
(or.
Air compressor
IJXAM
-_. 1
,_-.-_
--J
--
7
-I
Tllcrml ril t ing of’
tllc spilrk plug is
IlOt illlCX~ll~lt~.
Overlootl
Dirt
illld
clogging
I---- --
I--
,.. -L. .,.---
1
l----‘------l
I
IlSilgC Ol’ Sl~lrlliiIrd
IOild.
Replace
with the
spccificd plug.
Kc~tiove the carbun
dcposi I.
I- .-----I
I-.. __--I

I
No trutpu1
Poor
No comprcs-
pdorniancc
-. , ,
siou
Backl’irc
Poor
Misfire or
cond~~stion
performnnce ou,side the
L..- - .J L- .-,--J L_-+
Moisture in
fuel
1
Check
(Inside of
cilrhl~riltl~r
cliambcr)
Dcfccl ivc
soldel
7
--
T
Rich niixlure.
-r
-_
-- -
Possihlc
CilllSCS I ,
.- .-
-. -.
ltcrlls IO
check
and
procetlul c
Clhcckiug
criteria
Worn out
(‘onlacl
point is
dcl’cclivc
_ --
l --
!
C’hcck 1 hr
IappCl ClCilr-
ilncc.
-.-. -
Check the
,jet fol
llN,scl~ess
((‘heck the
$1 number)
Loscncss . . .
Tighten
Wrong,jel . . .
Keplncc
Replace with
11~2 correct
piIdS illld
chuck
Check the
tappet Ckiir-
ancc.
-,,
-r-- -
Narrow . . .
Adiusl to
COlllilCl
rhc ml of
Ill0
ViilVC
Wiilc . . .
Replace
C:lnltoct
point by
soil is fail
Moisture in
fuel

14. CRITERIA TABLE for ADJUSTMENT
I terns of adjustment
Criteria
, Limit of
application
Description
Tools
Remarks
Levelness of cylinder head
Below 0.1 0.15
Surface plate
and searcher
Repalr
I
Cylinder
lnslde dia.
Seat width of Intake and
exhaust valves
510+o.o19
0
0.5
5 1 .cl6Q
1 a
1 Cylinder gauge
Slide calipers ’ Repair
and cutter
1 lnstde dia. of valve guide
5,50A0.018
. 0
5.656
Center dia.
Cylinder gauge
Replacement
Piston skirt’s outs,de
dia. I” thrust dIrectIon
0
50.9920 -o,02
50.92
I
Micrometer Replacement
I
’ TOP
, ,5 +0.025
0
1.65
Slide calipers Replacement
I
’ Ring groove
width
Second
, ,5 ~0.025
0
1.65
Slide calipers Replacement
Piston
i Pin hole
011
2.5 ao.035
0
2.65
Slide calipers
Replacement
, ,O +0.002
-0.009
11 .O35 Cylinder gauge Replacement
Clearance between piston
skirt and cylmder wall
0.008 - 0.047 0.14
’ Cylinder gauge
and mxrometer ,
Replacement
’
Top 0.090 -0.135 0.26 Searcher Replacement
, Clearance be-
tween ring and Second 0.060 -0.105 0.23 Searcher Replacement
ring groove -
Spare rings
v
’ Oil 0.010 -0.065 0.19 Searcher Replacement
Clearance between piston
and piston pin
0.009T - O.OlOL 0.06L
Winder Saw ’ Replacement
and micrometer
I
Top
0.2 - 0.4
1.5
Searcher
Replacement
I
Joint
gap
Second 0.2 -0.4 1.5
I Oil
Spare rings
0.02 -0.25 1 .5
Piston
rings I Top
-0.09
1.5 -0.11 1.3 Micrometer Replacement
Width
A-
Second
011
’ .5 -0.06
-0.08
1.33
2,5 -0.010
-0.030
2.38
Spare rings
MIcrometer Replacement
!
MIcrometer Replacement
P!ston pin outside dia. “* 0
-0.008
10.060 ’ MIcrometer Replacement
’ lnstde d:a. of large end
20d+0 013
0
20.050
Cylinder gauge Replacement
I Clearance between mslde
dia of large end and crankpin
0.037
-0.063 0.13
1 Cylinder gauge
and mlcrometer
Replacement
Connecting
rod
lnslde dia. of small end
L-0 021
“O-0.01rJ
11.080 ’ Cylinder gauge Replacement
1 Clearance between instde
dla of small end and ptstonpln
0.01 - 0.029
0.12
Cylinder gauge
Replacement
I
and micrometer
Slide clearance of large
i rod end
1
0.1 -0.7
1 .o
Searcher ’ Replacement
I
-68-

Items of adjustment
I
I
I
Criteria
, limit of
application
Description
Tools Ramarks
I
1 Crankpm outside dia.
, 19.920 !
Mtcrometer Replacement
Crankshaft 1
Generator 20e, -0.003
!
Crankshaft
side
-0.012
19.950
I Micrometer Replacement
journal outside
dia.
Counter-
side
, 7. -0.003
-0.011
‘6.950
Micrometer Replacement
Cam crest
18.4%” 18.15 ! Micrometer ! Replacement
Camshaft
Camshaft
i &:erator
,O9-o.O’3
-0.028 :
9.950
Mtcrometer ( Replacement
journal
outside dia.
Counter- -0.01 3
I
side
log -0.028
9.959
Micrometer Replacement
Valve
spring
Free length
Squareness
25
24
1 .o
Slide calipers Replacement
I
Square
Replacement
I
’
Intake 5.50
-0.020
Outside dia.
-0.032
5.440 1
Mtcrometer
Replacement
I
of valve stem
I Exhaust 5.5@
-0.056
-0.074 5.409
Micrometer
Replacement
Clearance be-
Intake 0.02 0.05
-
0.2
tween valve
At valve guide
Cylinder gauge
Replacement
Intake and
stem and
center
exhaust valve guide Exhaust 0.056 - 0.092
0.2
Cylinder gauge
Replacement
valve
’
Intake
I
Tappet
0.08 -0.12
-
0.05 0.25,
i
Searcher
Replacement
l
clearance
I
Exhaust
0.08 -0.12 0.05 - 0.25
Searcher
Replacement
1
’ Clearance
I
I
8
between
Intake
0.1 -0.3 i 0.5
’
, Slide calipers
Replacement ’
groove and
Exhaust
retainer
0.1 -0.3 0.5
1 Slide calpers
Replacement
Valve stem
Intake
3.5
!
2.5 1
Slide caltpers
Replacement
end length
Exhaust /
3.5 2.5
Sltde calipers
Replacement
i Total length
j 20.8 +i.” 20.3 )
I
Slide calipers Replacement
I
Tappet
!
Clearance between stem
1 and guide
0.01 -0.03
I
Spark
Type
BMR-4A (NGKI
I
I
Plug
Electrode gap
0.6 -0.7 1.0
Searcher
Replacement
Fuel con-
’ 50 Hz rating
0.5
I
sumption
I
(l/hr) [ 60 Hz rating
I
0.6
I~- ~~
Lubricating 1 50
Hz rating
Oil consumption
(cc!hr) 60
Hz rating
I
4 20 :
I
5 20 1
I
Quantity of lubricating oil cc
350
I I
AutomotIve engine oil of class over SC
Lubricating oil replacement Interval
Compression pressure (kg/cm2/rpm)
I Inittal: 20 hours after start
Regular: Every 100 hours
I
I
I
I
41800
I
Pressure
I
I
1 guage ’
-69-

Items of adjustment
(Tightening torque)
Criteria
Limit of ’
application
Description ’
Tools
1 Connecting rod bolts
60 -80 kg-cm
I
Main bearing cover bolts
80-100
[ Cylinder head bolts
go-110
I
I
Spark plug
120 -150
I
1
I
Air cleaner nuts
Governor lever nuts
50 -60
I
70 -90
I
I
Front housing bolts
80-100
I
I
I
Rotor bolts
100-150
I
I
1 Muffler nuts
I
I
Front cover bolts
55 -75
I
I
I
-
70
-

16. MAINTENANCE
The following standard maintenarxe procedurss are necessary to ensure th
2 generator’s normal performance under normal
operating conditions. Therefore. the mstructions described below are for ref2rence only and varl- depending on how th2
generator is operated. For instance. if the gsnsrator is operated in a dusty ar2a the air cleaner must be cleaned daily- ah~h
diffsrs from the interval specified below.
16-l DAILY CHECKS and MAINTENANCE (every 8 hours)
Check and maintenance items
(I) Clean each component of dust
I
I
Description
I
’ (1) If th2 joint of the governor is left in a dust! condition.
the governor ma>- fail to function normally.
(2) Check the fuel piping system and related parts for
leakage. Should leakage be detected. tighten or
replace the defective part.
(2) Ii fuel leakage is not corrected. fuel economy will be
reduced and there is a potential of fire.
(3) Check each part for looseness. Tighten if (3) If the parts are 10052. vibrations will occur. and ma)
necessary. subject the generator to troublz.
(3) Check the quantity of oil inside the crankcase: fill (4) If the engine is run with an insufficient quantity of oil.
oil as necessary-. th2 piston and other moving parts will be damaged.
(5) Check equipments of control panel. when found
(5) Can’t obtain any output which is needed.
damages. replace them.
I
16-2 CHECKS and MAINTENANCE for EVERY 20 HOURS
I
Check and maintenance items
Description
( 1) Drain the oil from the crankcase.
( 1) Replace \vith n2w oil.
The oil used a&r the initial period of operation is
likely to be heavily contaminated with fine metal
I
powder and other foreign substances from various
engine parts.
16-3 CHECKS and MAINTENANCE for EVERY 50 HOURS (every 10 days)
Check and maintenance items
Description
(I ) Clean the air <Isaner at the prrscribed intsnal.
i (1) If th2 air cleaner is continually used in contaminated
condition. it may lead to engine trouble.
(2) Check the spark plug for carbon sontammation.
If found dirt!. clean rt with gasoline. followed
b>- sandpaper.
(2) Should the plug be left m contaminated condition.
an sngine output will decline or it ma! fail
- 72 -

16-4 CHECKS and MAINTENANCE for EVERY 200 HOURS (monthly)
Check and maintenance items
Description
(1 j Drain the oil from the crankcase and replace with
(1) The us2 of contaminated oil will subject parts to
new oil. (every 100 hours)
excessive wear.
(2) Clean the fuel strainer and the fuel tank interior.
I (2) If the contaminated fuel strainer and fuel tank are
used continually. engine performance will be lessened
I
and may led to engine trouble.
16-5 CHECKS and MAINTENANCE for EVERY 566 HOURS (semi-annually)
Check and maintenance items
(1) Remove the cylinder head, and remove carbon
deposits.
(2) Disassembly and cleaning of engine carburetor.
Description
’ (1) If the engine is run with the cylinder head contami-
nated with carbon. it may led to engine trouble.
(2) If the engine is run with the cylinder head contami-
nated with carbon. it may led to to engine trouble.
,
(3) Check the switch of engine and tlexible shaft. (3) If the engine is run with the cylinder head contami-
nated with carbon. it may led to engine trouble.
16-6 CHECKS and MAINTENANCE for EVERY 1660 HOURS (annually)
Check and maintenance items Description
(1) Overhaul the engine for cleaning. adjustment
and parts replacement.
(2) Replace the piston rings.
(1) If the engine is used continually without an annual
overhaul. it may led to engine trouble.
I
’ (2) If the engine is used continually without an annual
,
overhaul. it may led to engine trouble.
(3) Replace the fuel pipe.
j (3) An old fuel pipe is likely to leak.
(4) Check all the relative parts of the generator.
(4) Can’t obtain any output which is needed.
I
16-7 WHEN THE GENERATOR IS NOT USED for PROLONGED PERIODS:
Ij Be sure to check the generator daily as instructed in 16-1 aboLe and it is required that the generator receive the 20-
hour check and maintenance detailed in 16-Z.
~j
Drain the fuel from the tank and from the tloat chamber
of
the carburetor.
3j To prevent the cylinder wall from rusting. remove the spark plug and lubricate the interior at the cylinder. Then. pull
the recoil starter knob two or three times. and replace the spark plug.
4) Keep the piston stationary at the position where the piston stroke f22ls the heaviest.
5) Clean the engine exterior. using an oil impregnated cloth. and then place a vinyl cover or other cloth over the generator in a dry- place where it Lvill not be subject to high humidity.
- 73 -

R-America, Inc.
940livelyBlvd.QWoodDale,1160191● Phone:630-350-8200● Fax630-350-8212
e-mail: sales @robinamerica.com ● wwwrobinamerica. com
PRINTED IN THE USA