
Aerospace 40 A - 200 V fast recovery rectifier
Features
■ Very small conduction losses
■ Negligible switching losses
■ High surge current capability
■ High avalanche energy capability
■ Hermetic package
■ Target radiation qualification:
– 150 krad (Si) low dose rate
– 1 Mrad high dose rate
■ Package mass: 10 g
■ ESCC qualified
BYV54HR
TO-254AA
Description
Figure 1. Device configuration
Packaged in a hermetic TO-254AA, this device is
intended for use in medium voltage, high
frequency switching mode power supplies, high
frequency DC to DC converters, and other
aerospace applications.
The complete ESCC specification for this device
Terminal 1:
Terminal 2:
Terminal 3:
is available from the European space agency web
site. ST guarantees full compliance of qualified
The case is not connected to any lead
parts with such ESCC detailed specifications.
Table 1. Device summary
Order code
ESCC detailed
BYV54S200FSY1 -
BYV54S200FSYHRB 5103/031/05 Flight part
1. Contact ST sales office for information about the specific conditions for products in die form and QML-Q versions.
(1)
specification
Quality level
Engineering
model
Lead
finish
Gold -
Solder
dip
Cathode
Anode
Anode
EPPL I
Y
V
F(AV)
40 A 200 V 150 °C 1.10 V
BYV54S200FSY1
2
3
T
RRM
j(max)VF (max)
HRBBYV54S200FSY
1
July 2010 Doc ID 17416 Rev 1 1/8
www.st.com
8
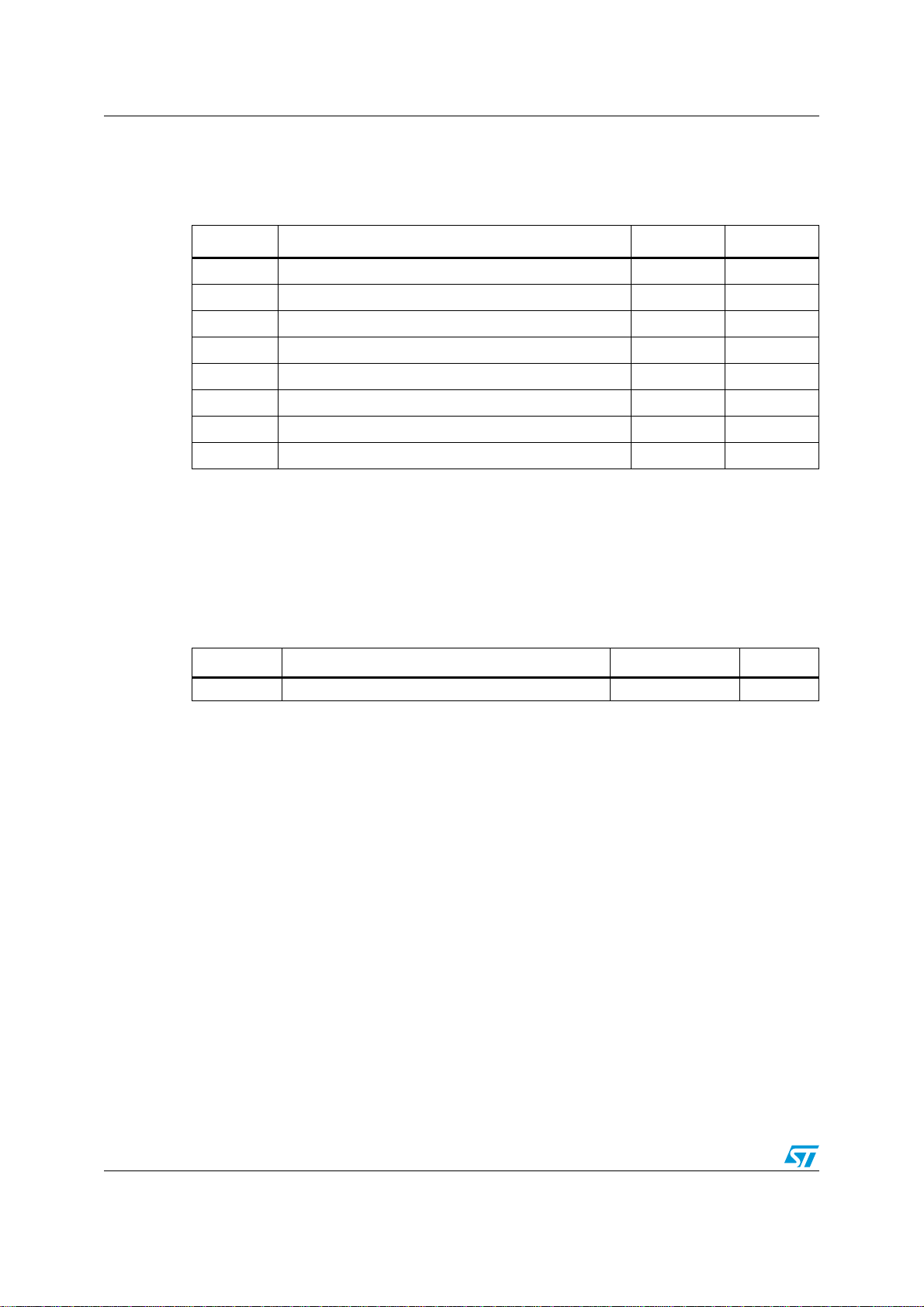
Characteristics BYV54HR
1 Characteristics
Table 2. Absolute maximum ratings
Symbol Characteristic Value Unit
I
FSM
V
RRM
I
O
I
F(RMS)
T
OP
T
T
STG
T
SOL
Forward surge current
Repetitive peak reverse voltage
Average output rectified current (50% duty cycle):
Forward rms current 60 A
Operating case temperature range
Junction temperature +150 °C
J
Storage temperature range
Soldering temperature
1. Sinusoidal pulse of 10 ms duration
2. Pulsed, duration 5 ms, F = 50 Hz
3. For T
4. For devices with hot solder dip lead finish all testing performed at T
inert atmosphere.
5. Duration 10 seconds maximum at a distance of not less than 1.5 mm from the device body and the same
lead shall not be resoldered until 3 minutes have elapsed.
> +99 °C, derate linearly to 0 A at +150°C.
case
(1)
(5)
(4)
(2)
(4)
400 A
200 V
(3)
40 A
-55 to +150 °C
-55 to +150 °C
+260 °C
> +125 °C are carried out in a 100%
amb
Table 3. Thermal resistance
Symbol Parameter Value Unit
R
Junction to case
th (j-c)
1. Package mounted on infinite heatsink.
(1)
1.0 °C/W
2/8 Doc ID 17416 Rev 1

BYV54HR Characteristics
Table 4. Electrical measurements at ambiant temperature (per diode), T
Symbol Characteristic
I
R
(2)
V
F1
(2)
V
F2
V
BR
C Capacitance 4001 V
t
rr
Z
th(j-c)
s
MIL-STD-750
test method
Test conditions
(1)
= 22 ±3 °C
amb
Limits
Min. Max.
Reverse current 4016 DC method, VR = 200 V - 50 µA
Forward voltage 4011
Pulse method, I
= 20 A - 0.95 V
F
Pulse method, IF = 30 A - 1.1 V
Breakdown voltage 4021 IR = 100 µA 200 - V
= 10 V, F = 1 MHz - 400 pF
R
= 1 A, VR = 30 V,
I
Reverse recovery time 4031
Relative thermal impedance,
(3)
junction to case
3101
F
/dt = -50 A/µs
dI
F
= 15 to 40 A, tH = 50 ms
I
H
= 50 mA, tmd = 100 µs
I
M
-60ns
Calculate ΔV
(4)
F
1. Testing performed with both anode terminals 2 and 3 tied ttogehter
2. Pulse width ≤ 680 µs, duty cycle ≤ 2%
3. Performed only during screening tests parameter drift values (initial measurements for HTRB), go-no-go.
4. The limits for ΔVF shall be defined by the manufacturer on every lot in accordance with MIL-STD-750 Method 3101 and
shall guarantee the R
Table 5. Electrical measurements at high and low temperatures (per diode)
limits specified in maximum ratings.
th(j-c)
Units
°C/W
Symbol Characteristic
I
Reverse current 4016
R
(2)
V
F1
Forward voltage 4011
(2)
V
F2
1. Read and record measurements shall be performed on a sample of 5 components with 0 failures allowed. Alternatively a
100% inspection may be performed.
MIL-STD-750
test method
Test conditions
T
= +125 (+0, -5) °C
case
DC method, V
= +125 (+0, -5) °C
T
case
pulse method, I
T
= -55 (+0, -5) °C
case
pulse method, I
T
= +125 (+0, -5) °C
case
pulse method, I
R
= 200 V
= 20 A
F
= 20 A
F
= 30 A
F
(1)
Limits
Min. Max.
-40mA
-0.85V
-1.15V
2. Pulse width ≤ 680 µs, duty cycle ≤ 2%
To evaluate the conduction losses use the following equation:
P = 0.74 x I
F(AV)
+ 1.00 x I
F2(RMS )
Units
1.0
Doc ID 17416 Rev 1 3/8