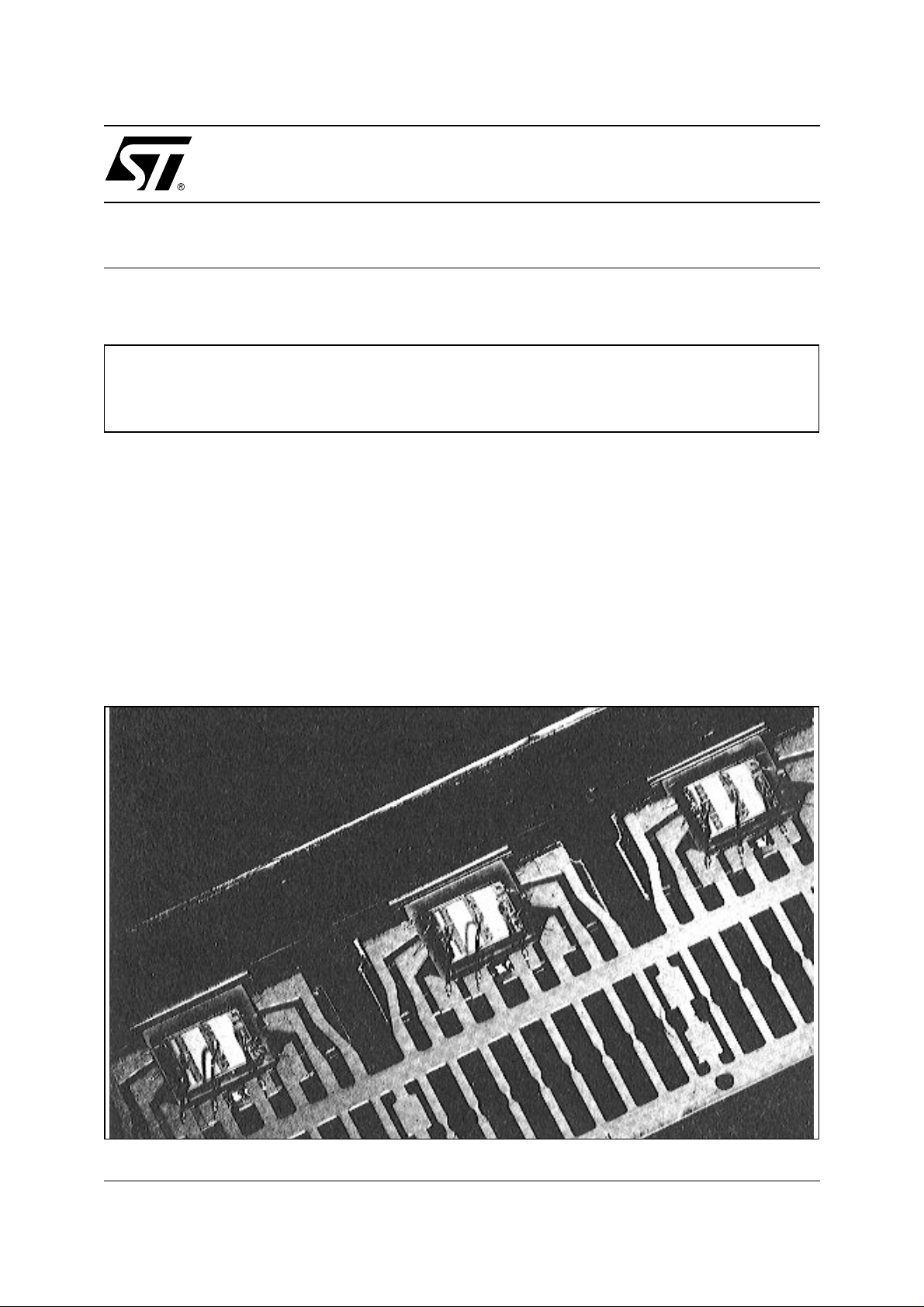
AN483
APPLICATION NOTE
MIXED WIRE BONDING TECHNOLOGY
FOR AUTOMOTIVE SMART POWER ICS
by R. Ferrari and A. Massironi
By using a mixture of gold and aluminum bonding wires in the same IC, STMicroelectronics has found
a reliable way to correct very high current ICs that avoids wasting die area.
One of the essential prerequisites for the largescale introduction of multiplex wiring systems for vehicles is the
availability of high power integrated circuits (ICs) capable of replacing relays, driving directly lamps, motors and
solenoids. These ICs must be rugged and highly reliable yet inexpensive. Many power ICs suitable for this market are already available but a gap was left at the high current — roughly 4A+ — end of the range; ICs delivering
20A or more are needed for loads like windowlift motors. One of the main problems in high current IC design
lies in the thin wires that connect the silicon chip itself to the external connecti ons of the IC package. These
bonding wires are typically fine gold wi res (up to 50um thi ck) which cannot carry more than a few amperes of
current. Increasing the thickness of the gold wires is ruled out partly because of cost, and also because they are
too rigid to weld to the surface of the chip without damaging it.
Figure 1. Part of an almost completed strip of integrated circuits utilizing the new mixed bonding technol-
ogy. The gold and aluminum wires connecting the silicon chip — the small gray rectangle — with
the gold-plated external connections can be clearly seen.
November 2003
1/3
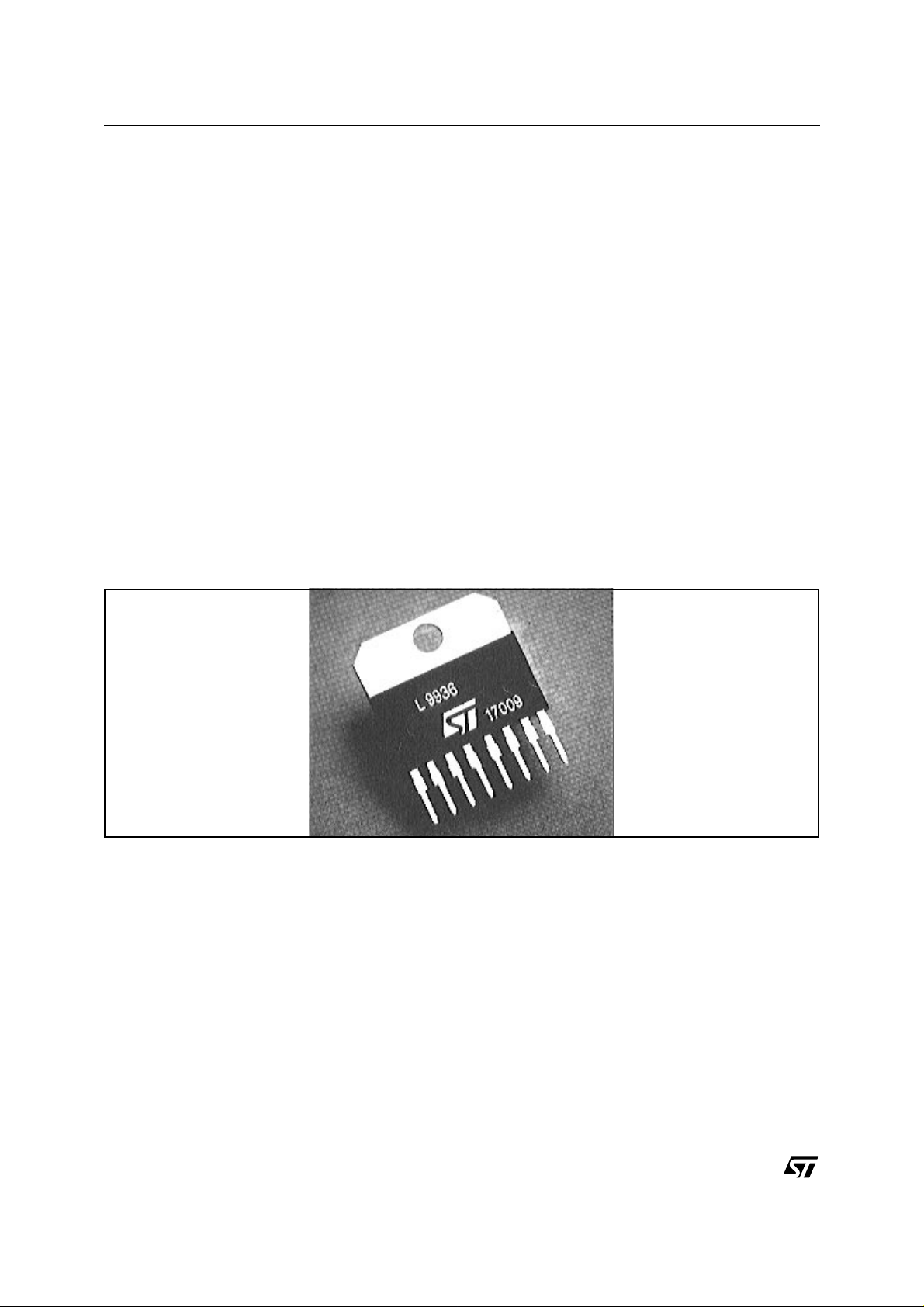
AN483 APPLICATION NO TE
It is possible in theory to use two or more gold wires in parallel for each connection but this solution is generally
impractical because the large number of bonding pads waste space on the chip (the cost of a silicon chip is
proportional to its area), the cost of the wire is excessive and because testing each bond is difficult.
One alternative, widely used in simple power ICs, is to use thick (250um) aluminum wires. However, a thick aluminum bonding wire needs a large bonding pad on the die. In a simple device like a 3-terminal voltage regulator
this is not a problem because there are few such pads, but for more complex ICs with eight or more connections
the w asted silicon area wo uld be excessive.
STMicroelectronics has developed and industrialized an effective and efficient solution to this problem: a mixed
bonding technology where thin gold wires are used for low current connections and thick aluminum wires used
for power connections.
Figure 1 shows a bonded frame of a 20A windowlift motor driver that uses this method; the two types of bonding
wire can be clearly seen. Figure 2 shows the same IC after encapsulation with black molding resin and removal
of the support elements of the frame. Because of the use of aluminum bonding wires a selective gold alloy plating of the leadframe is necessary; gold is one of the few metals that will weld reliably to aluminum. Apart from
reasons of cost, gold plating is used selectively — rather than the simpler overall plating — because of gold
were used on the external lead part of the frame it would contaminate the circuit board soldering bath, leading
to possible reliability problems.
Figure 2. After the wire bonding operation the completed frame assembly is encapsulated in black plastic
resin and the parts of the metal frame that served as a mechanical support are removed. The
finished parts are then tested and marked with the type number and lot tracing information.
Different bonding techniques are used to weld the two types of wire to the surface of the silicon chip.
For the thin gold wires the thermoso nic m ethod i s used where an electric discharge first creates a small ball on
the free end of the wire, this ball is then pressed on to the bonding pad and vibrated rapidly (in the ultrasonic
range), causing the gold ball and silicon su rfa c e to w el d t ogether. The thicker alum inum wires are bonded us ing
the impler ultrasonic method, where the wire is simply pressed onto the surface of the chip then vibrated rapidly
to weld the wire to the pad. Because more vigorous vibrations are used in this technique the aluminum wires
are bonded first, followed by the gold wires. On the production lines two separate machines are used in tandem.
Reliability is an important c onsideration in automotive ICs therefore i t is essential t hat wire bonds be secure
throughout the lifetime of the circuit. To ensure that bonds are correctly executed some parts are subjected to
a pull test, where the wires are pulled to determine their breaking strength.
Gold wires must resist a force of at least 15g; the thicker aluminum wires must resist a pull of 130g. In both cases
the wire must break; the bonds must not detach. These pull tests are also repeated on statistical samples after
accelerated life testing where parts are subjected to humidity, thermal cycling, and other stresses. Mixed bonding technology can be used in various different power IC packages, though the photos here show the Multiwatt-
2/3

AN483 APPLICATION NOTE
8 package. This type has eight leads in line at 0.1" centers — wider than is usual — to suit high current circuits
where wide circuit board tracks are used. The metal frame design of such packages reflects the care taken to
ensure reliability in line with the needs of the auto market. For example, the die-mounting zone of the frame is
isolated mechanically by notches and groove from the external mounting tab area. This ensures that deformation caused by overtightening the mounting screw will not subject to stress that could adversely affect reliability.
Figure 3.
Information furnished is believed to be accurate and reliable. However, STMicroelectronics assumes no responsibility for the consequences
of use of such information nor for any infringement of patents or other rights of third parties which may result from its use. No license is granted
by implic ation or o th erwise un der any pat ent or patent right s of STMi croelectr oni cs. Specifications menti oned in th i s publicati on are subj ect
to change without notice. This publication supersedes and replaces all information previously supplied. STMicroelectronics products are not
authorized for use as c ritical components in li fe support devices or syst em s without express wri t ten approval of STMic roelectronics.
The ST logo is a registered tradem ark of STMicroelectronics.
All other n am es are the property of their respective owners
© 2003 STMi croelectronics - All ri ghts reserved
Australi a - B elgium - B razil - Canada - China - C zech Republi c - Finlan d - F rance - Germ any - Hong Kong - India - Is rael - Italy - Japan -
Malaysia - Malta - Morocco - Singapore - Spain - Sweden - Switzerland - United Kingdom - United States
STMicroelectronics GROUP OF COMPANIES
www.st.com
3/3