
Manual
PROFIBUS Tester 4
BC-600-PB
FW version 1.13 (rev. 17)
Revision 2013-05-31

© Copyright 2013 Softing Industrial Automation GmbH
No part of this manual may be reproduced, photocopied, stored on a retrieval
system, transmitted, processed or translated without the express prior written
consent.

Contents
1
Introduction 6
1.1
General 6
1.2
Test Functions 6
1.2.1
Stand-alone mode of operation 6
1.2.2
PC mode of operation 7
2
Delivery Scope 8
3
Optional Accessories 9
3.1
D-sub adapter cable for testing live sy st ems 9
3.2
Adapter Set for M12 Connection Te chnology 9
3.3
Fieldbus Shield Digital Leakage Current Clamp 10
3.4
Portable Power Supply 10
3.5
Service Interface for PROFIBUS DP 11
3.5.1
Connection Type D-sub 11
3.5.2
Connection Type M12 12
4
Connectors and Controls 13
5
Power Supply and Auto Power On 14
5.1
Power-Up Behaviour without USB Connection 14
5.2
Power-Up Behaviour when USB Connected 15
6
Software Installation 16
6.1
Connection to a PC 16
7
Connection to PROFIBUS 16
7.1
Basics 16
7.1.1
Warning notice for testing a liv e bus 16
7.1.2
Connection types 17
7.1.3
Adapter cable 17
7.1.4
Strain relief 18
7.1.5
Test locations 18
7.2
Simple Connection for Tests During S ystem Shutdown 19
7.3
Connection for Testing a Live Bus 20
7.3.1
Connection via D-sub connector with service socket 21
7.3.2
Direct cable connection 22
7.3.3
Connection via M12 connector 23

7.4
Master Simulator and Topology S can 23
7.4.1
Special case: Active devices at both ends of the bus 25
8
Display and Control in Stand-Alone Mode 26
8.1
Main Display 26
8.2
Operating Concept 28
8.3
Functions 29
8.3.1
Live Status function 29
8.3.1.1
Bus status summary 29
8.3.1.2
Segment status 1 31
8.3.1.3
Segment status 2 32
8.3.1.4
Station status 33
8.3.2
Quick Test function 34
8.3.3
Trend function 35
8.3.4
Master Simulator function 36
8.3.5
Settings and help functions 36
9
Data Import into the PC 37
10
Firmware Update 38
11
Maintenance and Servicing 39
12
Troubleshooting 40
13
Specifications 41
14
General Notes 42
14.1
Lithium Battery 42
14.2
CE Conformity 42

Introduction Manual
Page 6 © 2013
1 Introduction
1.1 General
The PROFIBUS Tester 4 is a powerful tool that allows full testing of the bus
physics and bus communication on PROFIBUS DP segments.
Using the integrated master simulator, you can also test the bus physics if the
PLC is currently not in operation, or individually check “suspicious” bus
stations.
The tool is powered either through an external AC adapter, by direct
connection to 24 VDC or through an optional portable power supply unit .
1.2 Test Functions
The PROFIBUS Tester 4 automatically detects the baud rate or open circuit
voltage as soon as you connect it to a PROFIBUS DP segment.
You can then choose between two modes of operation for bus testing
depending on if you run it in stand-alone mode, or connect the PROFIBUS
Tester 4 to a PC or notebook. If required the master simulator can be enabled
in both modes if no other master is acti ve.
1.2.1 Stand-alone mode of operation
In the stand-alone mode three test functions with simultaneous analysis of bus
physics and bus communication are available:
1. The Live Stat us shows the bus status and the details of the analysis
in real-time on the display.
2. To evaluate the bus health up to ten Quick Tests can be executed,
stored internally and imported by the PC software then.
3. To locate the causes of sporadic bus faults the long-term Trend logs
data for up to 41 days and stores them internally for later import by the
PC software.

BC-600-PB Introduction
Softing Page 7
1.2.2 PC mode of operation
The PC software provides many additional features for performing, analyzing
and managing bus tests. Quick Tests and Trends stored in the tool can be
imported.
In the PC mode four main functions are available. Two of them provide
complex functionality that only experts need and that are accessed separately
from the standard functionality.
Standard functions:
1. The Network Status is a collection of information and test data
relating to a PROFIBUS network. It provides the basis for a
comprehensive evaluation of the bus health.
o Quick test and user-controlled test with simultaneous analysis
of bus physics and bus communication
o Topology scan
o Test report
o Master simulator
2. If sporadic faults occur in a PROFIBUS installation, the quality indexes
and critical protocol events should be monitored with the long-term
Trend over a prolonged period to locate the causes of bus problems.
Expert functions:
3. The function Frames enables the classic frame analysis.
4. The Oscilloscope permits the detail analysis of signal waveforms.

Delivery Scope Manual
Page 8 © 2013
2 Delivery Scope
The PROFIBUS Tester 4 comes in a carrying case comprising:
• Test tool with RS485 interface
• Wide-range power supply with European and US mains power cables
• Connecting cable for direct power supply wit h 24 VDC
• RS485 D-sub adapter cable BC-600-PB-CB-DSUB-2 “Standard”
(cable petrol blue, light connect or) for PROFIBUS DP
• USB cable, 3 m
• Terminal block for trigger input/output
• CD-ROM with driver software, PC softw are and detailed integrated
help system in English and German
• PROFIBUS Tester 4 user manual and Gett ing S tarted manual for the
PROFIBUS Diagnostics Suite PC software
Fig. 1: BC-600-PB with carrying case

BC-600-PB Optional Accessor ies
Softing Page 9
3 Opt i onal Accessories
3.1 D-sub adapter cable for testing live systems
This D-sub adapter cable is optimized for reduced influence on live
PROFIBUS DP segment operation. Thereby it is most suitable for testing of
running plants. The risk of critical influences on bus operation which can cause
a plant standstill is significantly reduced. Attention: Using this cable it is not
possible to use the both active functions master simulator and topology
detection (see page 23
).
Fig. 2: D-sub adapter cable with reduced influence on bus operation
Softing Order No.: BC-600-PB-CB-DSUB-1
3.2 Adapter Set for M12 Connection Technology
Using the M12 adapter set, you can connect the PROFIBUS Tester 4 to field
devices with M12 connectors. The set comprises an M12 adapter cable with
special pin layout and an M12 terminating resistor that you can screw on, if
required.
Fig. 3: Special adapter set for M12
Softing Order No.: BC-600-PB-CB-M12

Optional Accessories Manual
Page 10 © 2013
3.3 Fieldbus Shield Digital Leakage Current Clamp
When routing PROFIBUS cables in high-interference environments,
electromagnetic interference can affect the signal quality. By measuring the
shield currents with the digital leakage current clamp, you can locate EMC
problem areas and take appropriate countermeasures. The digital leakage
current clamp is supplied in a handy case, including measuring cables. There
is also an empty compartment for the fieldbus shield digital leakage current
clamp in the carrying case of the BC-600-PB.
Fig. 4: Fieldbus shield digital leakage current clamp
Softing Order No.: PB-LSZ-CHB3
3.4 Portable Power Supply
The portable power supply unit allows up to 4 hours of portable operation. The
power supply kit also includes a charger and a carrying case. Attention: Mains
connector type of charger station available for Europe only.
Fig. 5: Portable power supply
Softing Order No.: BC-MOST-PB
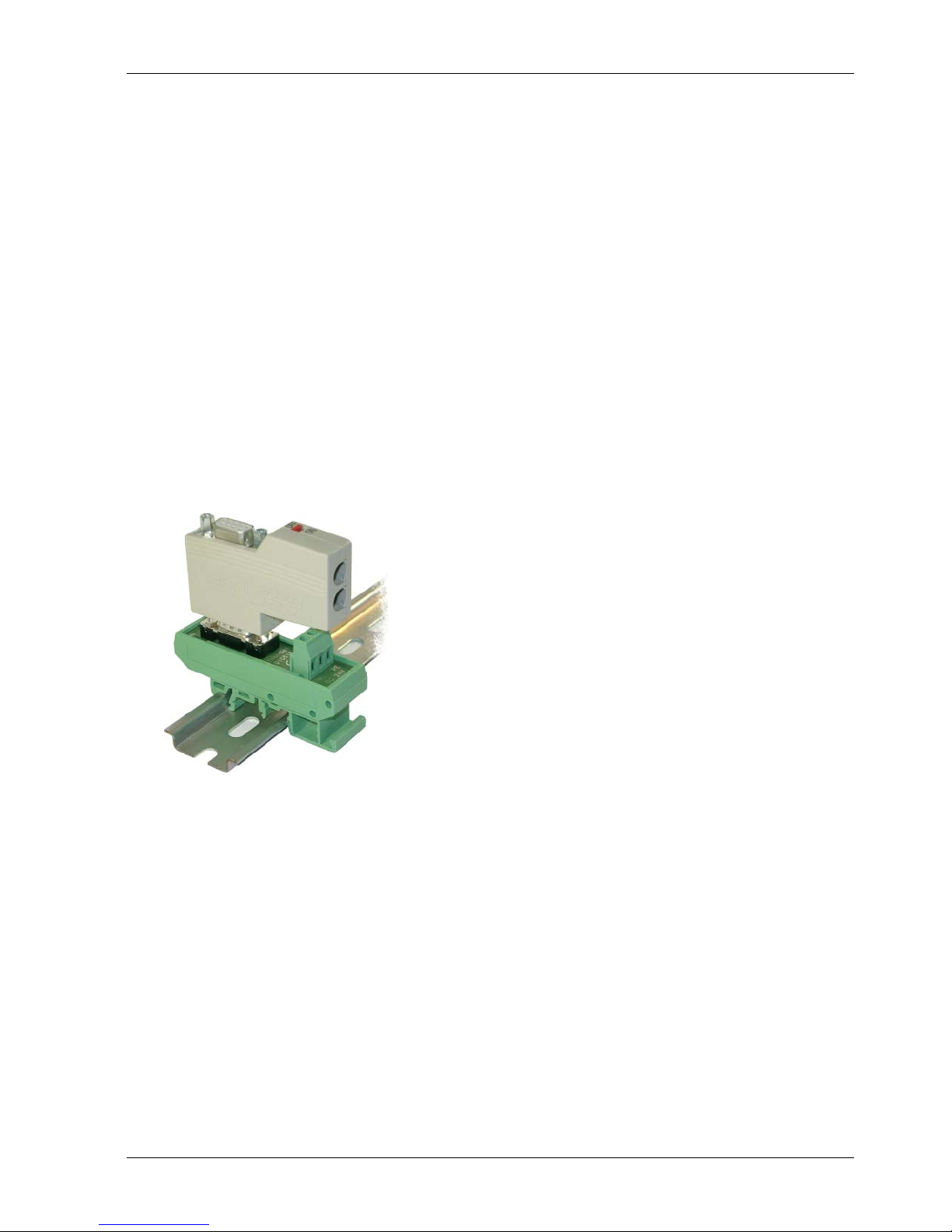
BC-600-PB Optional Accessor ies
Softing Page 11
3.5 Service Interface for PROFIBUS DP
3.5.1 Connection Type D-sub
The D-sub service interface provides a PROFIBUS access point for testing if
the existing D-sub connectors have no service socket or if the bus stations are
connected via a terminal block. The service interface can power the
terminating resistor of the D-sub connector. You can thus use it as an active
bus termination at the beginning o r end of the bus.
If the PLC allows dropping and adding bus stations on the live bus, you will
need this external bus termination to be able to exchange the first and last bus
stations without causing problems on the bus.
The compact unit is rail mounted like a terminal block and powered by an
external 24 VDC power supply. The package includes an 90° angled
PROFIBUS connector with a switchabl e terminating resistor.
Fig. 6: D-sub service interface for testing a live bus
Softing Order No.: BC-PBMB-PB-S
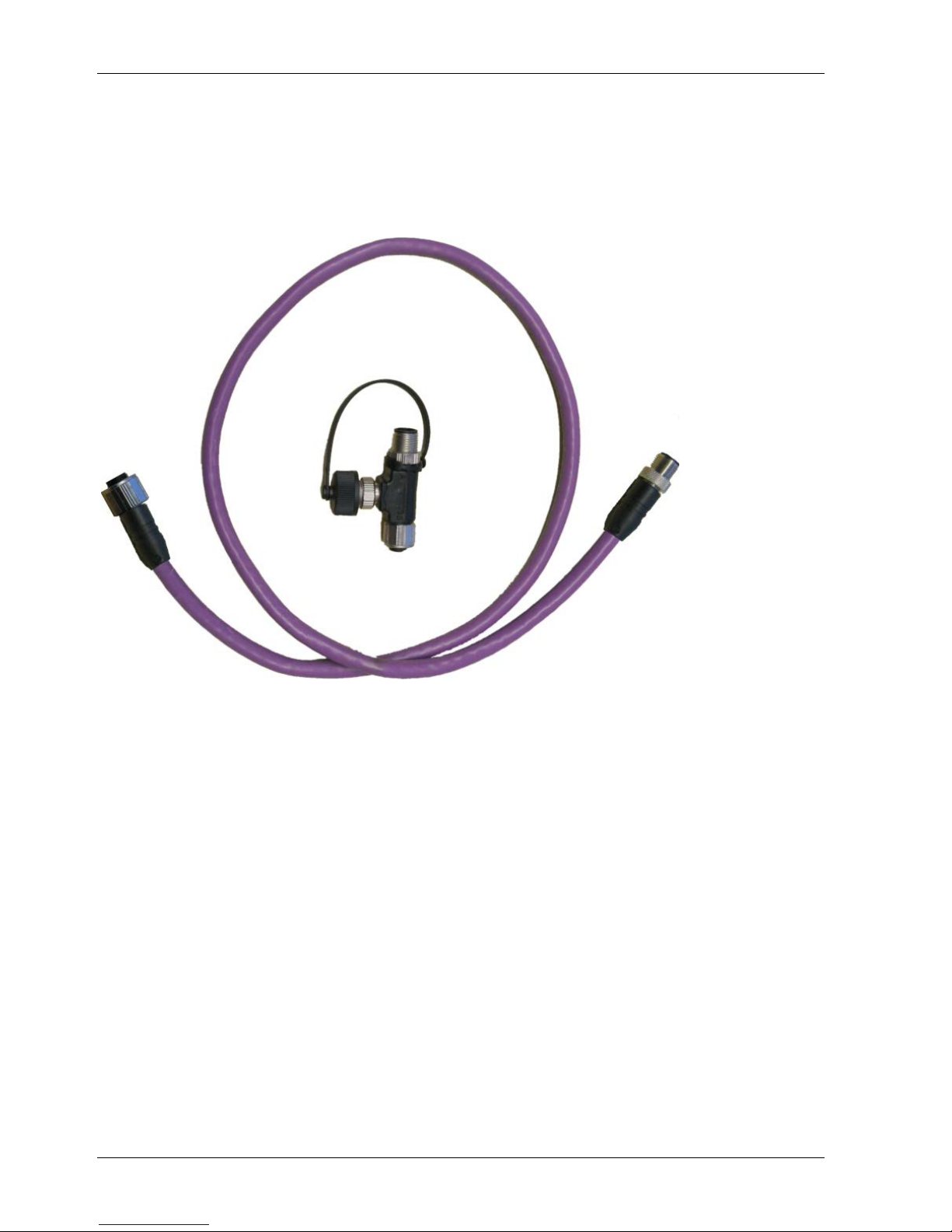
Optional Accessories Manual
Page 12 © 2013
3.5.2 Connection Type M12
The M12 service interface comprises an IP68 rated T piece, an end cap for the
service output of the T piece, and a 1m PROFIBUS DP cable fitted with a
male/female M12 connector on each end.
Fig. 7: M12 service interfac e for testing a live bus
Softing Order No.: BC-M12DP-PB

BC-600-PB Connectors and Controls
Softing Page 13
4 Connectors and Controls
RS485
Connection to PROFIBUS DP
Display
Status display & operation
Function key 2 Funktionstaste 3
Detail selection Start
Function key 1 Funktionstaste 4
Function selection Back/Cancel
Power USB
Connection to
Connection to notebook/PC
24 VDC Trigger input
Status LED
Trigger Output
Terminal block for
trigger input/output
Fig. 8: Connectors and status displays on the BC-600-PB

Power Supply and Auto Power On Manual
Page 14 © 2013
5 Pow er Suppl y and Auto Power On
The tool is powered with 24 VDC either through the external AC adapter or by
using the single-ended cable for direct 24 VDC power supply. Both are
included in delivery.
Attention: Before being connected to the AC mains power, the
PROFIBUS Tester 4 and the AC adapter must be acclimated to room
temperature to avoid condensati on. This may take up to 60 minutes.
The tool switches on automatically when you connect it to a power supply. The
display lights up and self-test starts.
Attention: When the tool is connected directly to 24 VDC, there is no
galvanic isolation to the external power supply. Insufficient potential
equalization between the power supply and the PROFIBUS will lead
to equalizing currents which can falsify the test results and, in the
worst case, even destroy the PROFIBUS Tester 4 and part of the bus
installation. In these cases, use of the supplied AC adapter is
mandatory for operating the PROFIB US Tester 4.
On completion of initial setup, the PROFIBUS Tester 4 displays the following
dialog in English:
You can now select the desired display language. The following languages are
available: German, English, Frenc h, Italian, Polish and Spanish.
5.1 Power-Up Behaviour without USB Connection
The PROFIBUS Tester 4 starts up in stand-alone mode in this case (see
page 26
) and is immediately ready for test i ng.

BC-600-PB Power Supply and Auto Power On
Softing Page 15
5.2 Power-Up Behaviour when USB Connected
Attention: The “PROFIBUS Diagnostics Suite” PC software also
includes the required USB driver. You therefore need to install the
software first before connecting the test tool to the PC or notebook.
On successful completion of the self-test, the PROFIBUS Tester 4 displays:
Fig. 9: Power-up display when USB connected
When you start the PROFIBUS Diagnostics Suite control and evaluation
software on your computer and select the PROFIBUS Tester and a network for
testing in its user interface, the test tool switches to PC mode. The display
shows:
Fig. 10: Display at testing with PC software
While in PC mode, you can only display readings and operate the tool by using
the control and evaluation software on the computer.
At this point, you can also start a firmware update instead of using the control
and evaluation software. See page 38
.

Software Installation Manual
Page 16 © 2013
6 Software Installation
The “PROFIBUS Diagnostics Suite” PC software is provided on the included
CD-ROM. You need administrator privileges to install the software. If the CDROM does not start automatically when inserted, please run the “start.exe” file
in the main directory.
Future updates can be downloaded from our web site at industrial.softing.com
.
Attention: The “PROFIBUS Diagnostic Suite” PC software also
includes the required USB driver. You therefore need to install the
software first before connecting the test tool to the PC or notebook.
The installation and basic use of the PC software is described in the separate
PROFIBUS Diagnostics Suite – Getting Started manual.
6.1 Connection to a PC
Use the included USB cable to connect the tool to a PC or notebook. Power is
also supplied from the USB interface.
Attention: It is recommended to connect the unit directly to a USB
port on the PC or notebook. When you use external USB hubs or
notebook docking stations for conne ct ion, problems can occur.
7 Connection to PROFIBUS
7.1 Basics
7.1.1 Warning notice for testing a live bus
Attention: When you connect a test tool, side effects on the
system under test are generally unavoidable. If the PROFIBUS is
already disturbed to a certain degree or if Simatic Diagnostic
Repeaters are used, the operation of the PROFIBUS might
nevertheless be affected occasionally. Compliance with the
connection notes is mandatory!

BC-600-PB Connection to PROFIBUS
Softing Page 17
7.1.2 Connection types
There are several ways to connect a bus station to a PROFIBUS network:
• Using connectors
o D-sub connectors, most of which have an integrated terminating
resistor and, optionally, an addi tional service socket
o M12 connectors fo r environments requiring increased IP ratings
o Special vendor-specific hybrid connectors; they are used in
combination with special cables t o supply power via the bus
• Using terminals for direct conne ct i on
Due to the typical daisy-chain topology, the connection points of the bus
stations are the only possible points for connecting the test tool in most cases.
7.1.3 Adapter cable
The PROFIBUS Tester 4 is supplied with the D-sub adapter cable BC-600-PBCB-DSUB-2 „Standard“ (light connector). For testing on live systems the
optional D-sub adapter cable BC-600-PB-CB-DSUB-2 is recommended. An
M12 adapter set is optionally av ai l abl e, see on page 9
.
Attention: Use only the short original cables with special pin layout to
connect the unit to a PROFIBUS network. Do not cascade more than
two D-sub connectors with service sockets at the same time:
Fig. 11: Unallowed cascading of D-sub connectors
Active connection cables with integrated repeaters, such as Softing's BC-131PB, cannot be used for testing.

Connection to PROFIBUS Manual
Page 18 © 2013
7.1.4 Strain relief
Attention: When you connect the PROFIBUS Tester 4, its weight can
place a high mechanical stress on the connectors and the bus
station. Ensure proper strain relief by using suitable supports, cable
ties, etc. When this is not possible, you need to select a different
connection point to avoid damage.
Fig. 12: Strain relief fitt i ngs
7.1.5 Test locations
The PROFIBUS Tester 4 can basically carry out tests anywhere on a physical
PROFIBUS segment. Please note that the use of repeaters creates separate
physical segments that each need to be measured individually.
For the best and most informative results, perform the tests at the beginni ng
and end of each physical segment. If these test results indicate pro bl em s t hat
cannot be clearly classified right away , you should carry out one or more
additional tests at the centre.

BC-600-PB Connection to PROFIBUS
Softing Page 19
7.2 Simple Connection for Tests During System Shutdown
If all bus stations provide D-sub connectors with an additional service socket,
you can simply plug in the PROFIBUS Tester 4 at that socket (see figure
below). If a D-sub connector does not provide a service socket, you can plug
in the D-sub adapter cable underneath. The only thing you need to keep in
mind is that you should never cascade more than two D-sub connectors (see
page 17
).
When using M12 connection technology, the M12 adapter cable is “looped”
into the bus. It is essential to ensure proper termination at the beginning and
end of the bus by using the terminating resistor provided with the M12 adapter
set.
Attention: All these simple connection types will divide the bus. You
therefore need to shut down the PLC and all the devices connected
to the PROFIBUS; in other words, you need to shut down the whole
installation.
D-sub
Connection points
PLC
Remote I/O Remote I/O
Remote I/O
M12
Termination
at begin and
end of bus!
or
Fig. 13: Connection point s at system shutdown

Connection to PROFIBUS Manual
Page 20 © 2013
7.3 Connection for Testing a Live Bus
To test a live PROFIBUS with the PROFIBUS Tester 4 during operation,
appropriate connection possibilities have to be provided. If no suitable
connection points are available in the existing installation, it is recommended
to install them during system shutdown. This will make future maintenance
work much easier.
Attention: When installing additional connection points, you divide the
bus. Before doing so, you therefore need to shut down the PLC and
all the devices connected to the PROFIBUS; in other words, you need
to shut down the whole installation.
Attention: For testing on live systems the optional D-sub adapter
cable BC-600-PB-CB-DSUB-1 with reduced influence on bus
operation is highly recommended! See page 9
.

BC-600-PB Connection to PROFIBUS
Softing Page 21
7.3.1 Connection via D-sub connector with service socket
If all bus stations provide D-sub connectors with an additional service socket,
you can simply plug in the PROFIBUS Tester 4 at that socket (see figure
below).
MPI Operator Panel
Remote I/O
Remote I/O
D-sub
Connection points
PLC
Fig. 14: Connection point s for the D-sub adapter cable

Connection to PROFIBUS Manual
Page 22 © 2013
7.3.2 Direct cable connection
To test a live PROFIBUS, you will need additional D-sub service interface of
the type BC-PBMB-PB-S (see page 11
).
PBMB
PBMB
PBMB
D-sub
Connection points
PLC
FC
FC
Diagnostic
repeater
Fig. 15: Service interfac e provide connection points at direct cable connec tion

BC-600-PB Connection to PROFIBUS
Softing Page 23
7.3.3 Connection via M12 connector
Tests on a live PROFIBUS are only allowed on bus segments providing D-sub
connection technology. Only D-sub connectors with service socket can be
used as connection points for the test tool. For this reason, tests can often only
be performed at a bus end.
D-sub
Connection point
PLC
Remote I/O
Remote I/O
Remote I/O
Fig. 16: Connection point s for the M12 adapter cable
7.4 Master Simulator and Topology Scan
The master simulator allows checking the bus cabling and the station
addresses during installation and commissioning, when the PLC (master) is
not in operation yet. In addition, you can use this mode to check individual
“suspicious” bus stations that have been disconnected from the bus.

Connection to PROFIBUS Manual
Page 24 © 2013
The topology scan determines the sequence and distances of all passive bus
stations (slaves). This feature requires correct bus cabling, a very good signal
quality, and a connection point located directly at the beginning or end of the
bus.
Both features can only be used during shutdown of the installation. The D-sub
cable BC-600-PB-CB-DSUB-2 which is included in the standard scope of
supply must be used. As long as communication is detected on the bus, i.e. at
least one device is an active master, the functions are disabled. If necessary,
disconnect every single active device (PLC, MPI and, if necessary, diagnostic
repeaters) from the power supply or the bus. If an active device is at the end of
the bus you want to test, its PROFIBUS connector needs to be unplugged and
connected directly to the PROFIBUS Tester 4. The bus termination in the
device connector will then be powered by the PROFIBUS Tester 4.
w/o
adaptor
cable
Connection points
MPI Operator Panel
Remote I/O
PLC
Disconnect from bus
Remote I/O
D-sub
D-sub cable „Standard“
BC-600-PB-CB-DSUB-2
Fig. 17: Connection point s for topology scan

BC-600-PB Connection to PROFIBUS
Softing Page 25
Attention: Bus stations must only be disconnected from the power
supply or the bus during shutdown of t he i nst al lation.
Attention: The two functions can be started also when the PROFIBUS
Tester 4 is disconnected from the bus. If you then connect the
PROFIBUS Tester 4 to a live bus despite the yellow bus status bar
indicated by the PC software, this can cause bus communication
problems or a shutdown of the installation.
7.4.1 Special case: Active devices at both ends of the bus
On the very rare occasion when there is an active device at each end of the
bus, do the following:
1. When using D-sub connection:
• Additionally switch on the terminating resistor in the D-sub
connector of the last slave. The outgoing cable to the active
device at the bus end has to be connected to the outgoing
connector (marked with “OUT”, an o utgoing arrow, or “A2/B2”).
Fig. 18: Checking the connect ion direction at the D-sub connector
2. When using M12 connection:
• The cable from the bus start or test tool has to be connected to
the incoming M12 connector of the last slave. A bus termination is
required at the outgoing M12 connector of the last slave.

Display and Control in Stand-Alone Mode Manual
Page 26 © 2013
8 Display and Control in Stand-Alone Mode
The PROFIBUS Tester 4 always starts in stand-alone mode unless it is USB
connected to a PC or notebook. The readings are shown on the display. You
can control the tool with the four funct i on key s.
When you establish a USB connection during stand-alone mode while a test is
running, the test will be aborted and the tool will be reset (restart). The display
briefly shows: “Changing operatin g m ode – Please wait …”.
8.1 Main Display
The baud rate of a connected PROFIBUS network is detected and displayed
automatically:
Fig. 19: Main display - exam ple of a live PROFIBUS at 1. 5 Mbit /s

BC-600-PB Display and Control in Stand-Alone Mode
Softing Page 27
The PROFIBUS status is shown in line 2. The following displays are possible:
3. The PROFIBUS is not connected:
• Display: “DP n/a”
4. The PROFIBUS is connected, but no master is active:
• Display of the static RS485 bus voltage,
e.g. “DP 1015 mV stat.”
5. The PROFIBUS is connected and one or more masters are active:
• Display of the detected baud rate, e.g. “DP 1.5 Mbit/s”
The status of the integrated master simulator is shown in line 3. The following
displays are possible:
1. The master simulator is disabled:
• The display remains blank.
2. The master simulator has been enabled manually (see page 36
):
• Display: “M.Sim. ON”
The only control on the main display is the down arrow key with which you can
select the individual functions.

Display and Control in Stand-Alone Mode Manual
Page 28 © 2013
8.2 Operating Concept
Fig. 20: Display control with the four function keys

BC-600-PB Display and Control in Stand-Alone Mode
Softing Page 29
8.3 Functions
8.3.1 Live Status function
The Live Status function very quickly gives you an overview of the bus status.
Even transient disturbances during the test are reliably detected. Once you
start the function, the tool determines and continuously updates the status for
the segment and for each bus station.
8.3.1.1 Bus status summary
Fig. 21: Live Status with bus status summary
Line 1 shows the overall bus status. It results from the substatus for bus
communication and the substatus for bus physics, which are displayed in lines
2 and 3.
Bus communication:
1. “Error”
• Bus stations were dropped or added during the test
• Configuration errors or parameter errors occurred
(the actual structure of modular slaves differs from the
configuration stored in the PLC, or an in correct GSD file was
used)
2. „Warning“
• Frame errors, retries or diagnostics occurred during the test
• One or more bus stations have not been configured in the PLC
3. „OK“
• No critical states or events
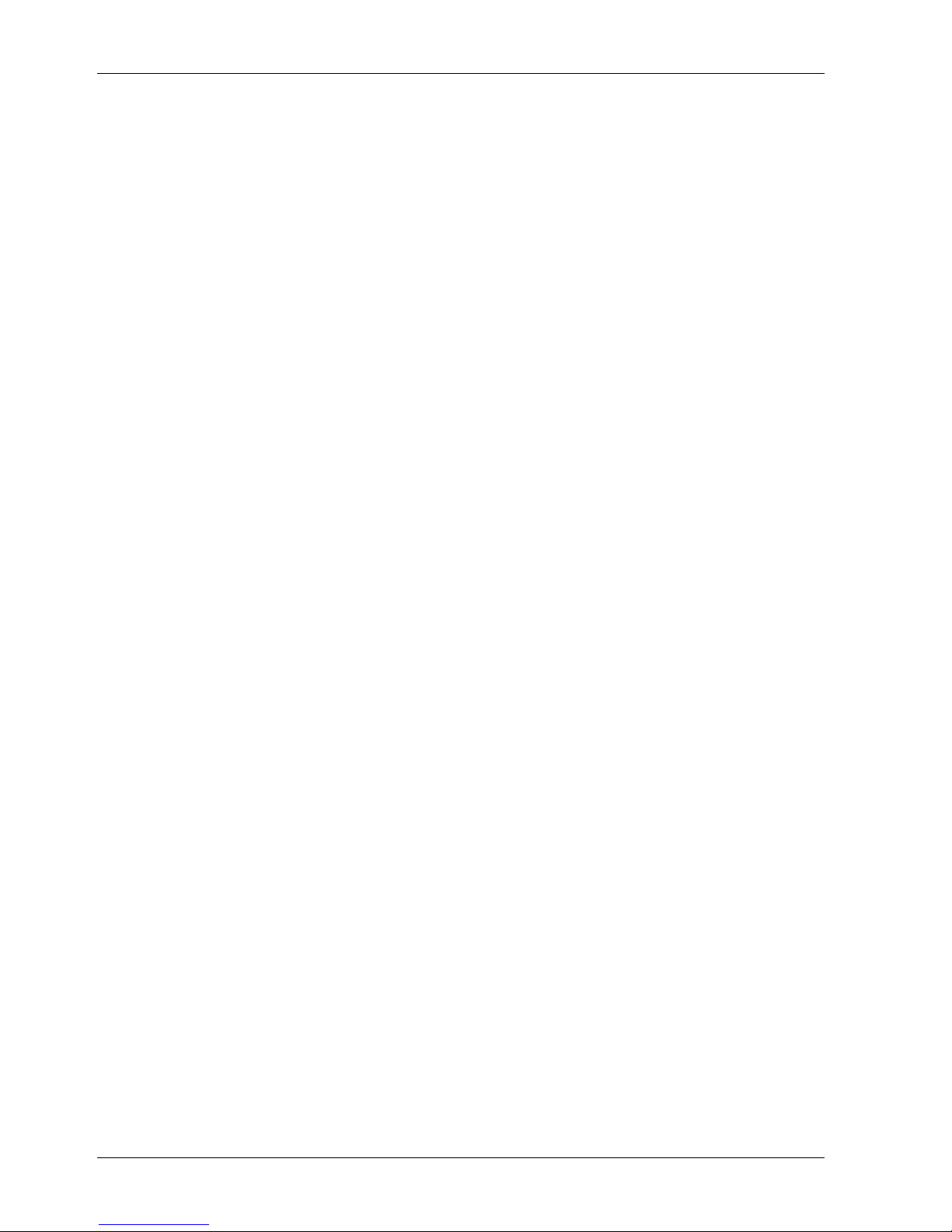
Display and Control in Stand-Alone Mode Manual
Page 30 © 2013
Bus physics:
1. “Error”
• One or more bus stations failed to respond during the last physical
test cycle
2. „Warning“
• One or more quality indexes* are below the user-defined limit
value (default: 2500)
3. „OK“
• All quality index* results are above the limit value
* .. See the “Interpretation of the signal quali ty test results” chapter
in the PROFIBUS Diagnostics Suite manual.

BC-600-PB Display and Control in Stand-Alone Mode
Softing Page 31
8.3.1.2 Segment status 1
Fig. 22: Live Status with segment status 1
To the right of “DP Segm.” in line 1, the display shows changes in the live list
(added and dropped bus stations). The following displays are possible:
1. The number of bus stations has not changed during the test:
• No display of live list changes
2. One or more bus stations have been added during the test:
• “+” display
3. One or more bus stations have been dropped during the test:
• “-” display
4. One or more bus stations have been added and one or more dropped
during the test:
• “+ -” display
The live list should usually not change when a PROFIBUS system is stable.
In line 2, you see the number of masters (M) and slaves (S). For the slaves,
the first figure indicates the number of slaves addressed by the master(s). If
not all slaves respond, the number of slaves that failed to respond is indicated
after a “-” sign.
Line 3 indicates the token rotation time. Note: The token rotation time does not
necessarily equal the bus cycle time.
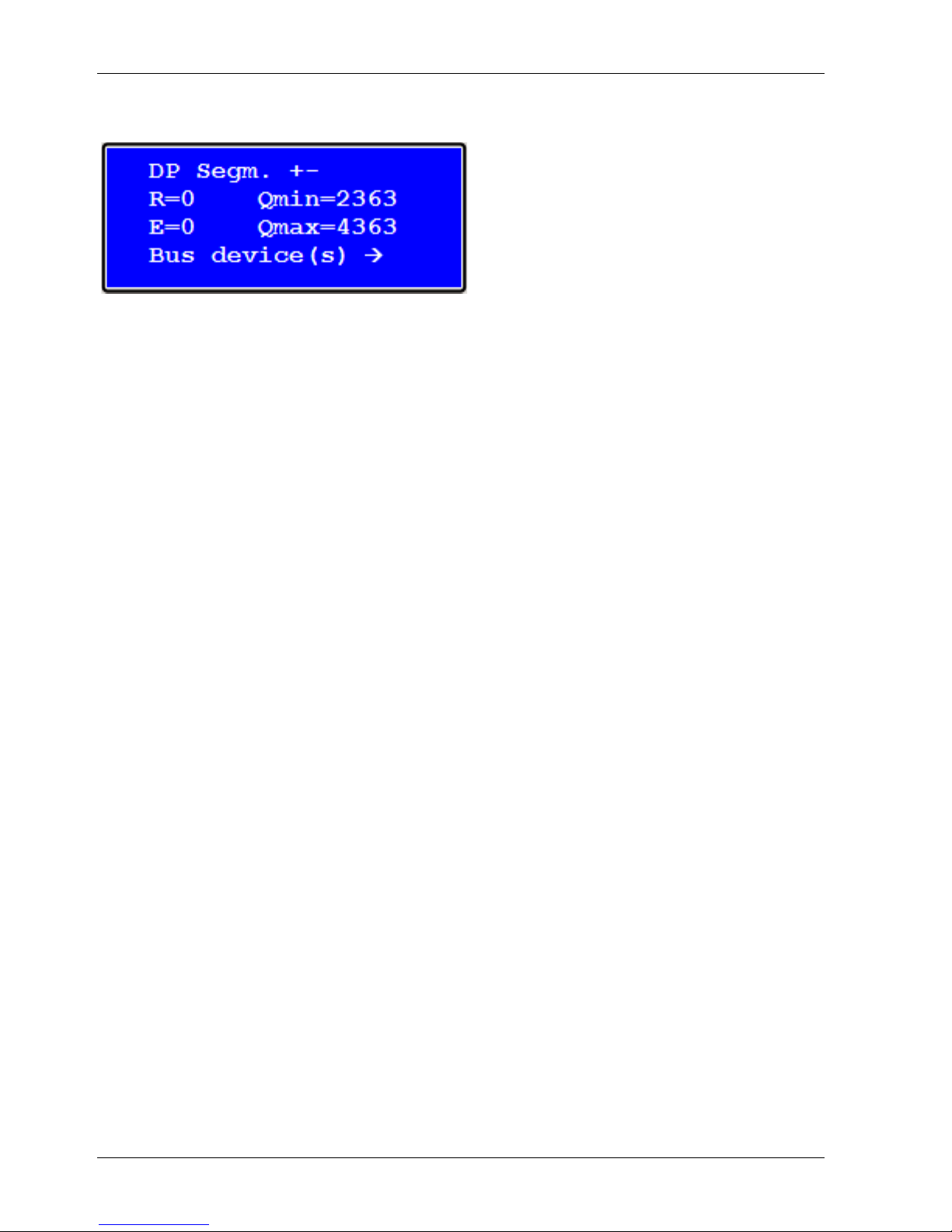
Display and Control in Stand-Alone Mode Manual
Page 32 © 2013
8.3.1.3 Segment status 2
Fig. 23: Live Status with segment status 2
Line 1 is the same as for segment status 1.
In line 2 you see, on the left, the number of retries on the entire segment and,
on the right, the worst quality index of all bus stations.
Line 3 shows, on the left, the number of frame errors on the entire segment
and, on the right, the best quality index of all bus stations.

BC-600-PB Display and Control in Stand-Alone Mode
Softing Page 33
8.3.1.4 Station status
This function displays the station status for each bus station, i.e. for all masters
and all slaves.
Fig. 24: Live Status with station status of a master
Fig. 25: Live Status with station status of a slave
The PROFIBUS address of the bus station is displayed right after “DP#” on the
left of line 1. The letter in the middle indicates whether the device is a mas ter
(M) or slave (S). If the letter is enclosed in square brackets, the BC-600-PB
was able to determine the address of the PROFIBUS device to which it is
connected. In the above example, the test tool is connected to the device with
the address 11 (see Fehler! Verweisquelle konnte nicht gefunden
werden.). On the right, you see the live list changes (see page 31
) for this bus
station.
Line 2 shows the number of retries on the left, and the worst quality index of
this bus station on the right.
Line 3 indicates the number of diagnostics on the left, and the best quality
index of this bus station on the right.
Note: The update rate for the live status substantially depends on the number
of bus stations and the signal quality.

Display and Control in Stand-Alone Mode Manual
Page 34 © 2013
8.3.2 Quick Test function
The Quick Test allows full testing of bus physics and bus communication. The
test data is stored in the tool. It can subsequently be imported by the
PROFIBUS Diagnostics Suite software application.
To start the function, choose one of 10 internal memory locations. The display
indicates if the selected memory location is allocated or free. If you select an
allocated memory location, t he prev i ous test data will be overwritten.
Fig. 26: Quick test complet ed
The duration of a Quick Test depends on the baud rate, the number of slaves
and the current bus communication. It can take only a few seconds or up to
three minutes.
On completion of the test, press the acknowledgment key to cancel the status
display.

BC-600-PB Display and Control in Stand-Alone Mode
Softing Page 35
8.3.3 Trend function
Trend logging is used for detecting rare or sporadic faults over a prolonged
period of time. The function monitors both the bus physics and critical events
in the bus communication. The PROFIBUS Tester 4 can automatically test the
bus in stand-alone mode from within the control cabinet for up to 41 days. The
test data is stored in the tool. It can subsequently be imported by the
PROFIBUS Diagnostics Suite software application.
Before you start the function, choose a test interval. When you select “Auto”
the tool automatically determines the optimum interval. The Trend Test runs
until manually stopped with the “x ” key .
Fig. 27: Trend running for 23 h and 52 min.
The test is aborted automatically when the power supply is interrupted (all data
logged so far is retained in memory) or when the maximum logging time of 999
hours and 59 minutes is reached.

Display and Control in Stand-Alone Mode Manual
Page 36 © 2013
8.3.4 Master Simulator function
The master simulator is disabled by default when you switch on the tool. You
can only select a baud rate on the display and thus start the master simulator if
no other master is active.
8.3.5 Settings and help functions
The following options are available:
• Settings/Delete all internal memory locations: Deletes all qui ck tests
and trend recordings
• Settings/Current language: Toggles between English, German,
French, Italian, Polish and Spanish (all w/o national specific
characters)
• Settings/Limit signal quality: Sets the limit value in increments of 100
(default: 2500)
• Settings/Time-out signal quality: Sets the time-out val ue in increments
of 5 (default: 5 seconds)
• HW Information: Displays on two screens the firmware and FPGA
versions and the date and time of the last factory calibration.
• Help: Briefly describes the functionality of the four function key s.

BC-600-PB Data Import into the PC
Softing Page 37
9 Data Im por t into the PC
Quick Tests and Trend logs stored in the test tool can be imported into the PC
software. To do this, start the PROFIBUS Diagnostics Suite. If a PROFIBUS
Tester is connected to the PC via USB and contains stored test data, an
additional “Import Test Data f rom T ool” dialog box appears automat icall y.
Fig. 28: Importing test data
For ALL the stored data, you need to fully select the action to be performed,
the network/project, and the test location to which you want to store the data.
The default action “Import & Delete“ deletes the test data in the tool after the
import is complete. This frees the allocated memory locations for new tests.
The imported Quick Tests and Trend logs are fully compatible with the test
data that can be acquired using the PC software.

Firmware Update Manual
Page 38 © 2013
10 Firmware Update
Firmware updates are made available as required. They are provided with the
updates to the PC software (see page 16
) and allow access to new or
improved functionality. How to update the firmware is described in detail in the
separate “PROFIBUS Diagnostics Suite – Getting Started” manual.
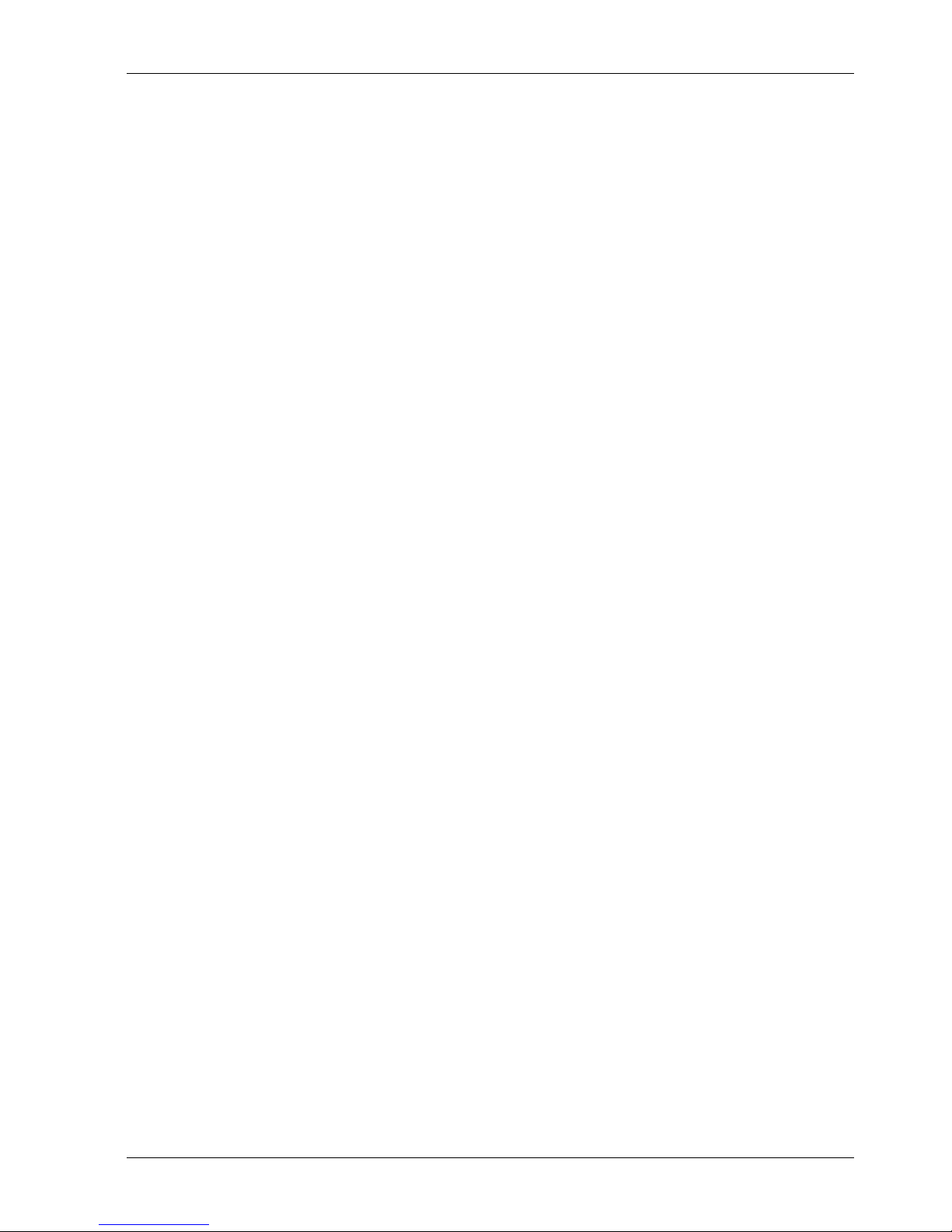
BC-600-PB Maintenance and Servicing
Softing Page 39
11 Maintenance and Servicing
The PROFIBUS Tester 4 is maintenance-free and does not require calibration.
Repairs may only be carried out by the device manufacturer. All returns must
be made in the supplied carrying case. Please also include a brief fault
description and a phone number at which we can contact you should we need
further details. In case of returns within the warranty period, please also
enclose a copy of the invoice or deliv ery note.

Troubleshooting Manual
Page 40 © 2013
12 Troubleshooting
The display of the
PROFIBUS Tester 4 remains
blank.
Possible cause:
• The PROFIBUS Tester 4 always needs an additional
external power supply.
Remedy:
• Use the supplied external AC adapter to connect the tool to
the mains power supply.
• When connected directly to a 24 VDC power supply: check
the voltage at the terminals
Alternative cause:
• The tool is defective.
Remedy:
•
Return the tool for servicing (see page 39)
following error message:
“USB ERROR - Refer to
manual or disconn. for standalone mode”.
• This error message can be caused by poor physical
connection via USB (“loose” contact).
Remedy:
•
Check the USB cable and connector.
The baud rate is not detected
automatically on a live
PROFIBUS.
• Massive disturbances in the bus physics.
Remedy:
•
Manually set the baud rate and repeat the test.
If you need to contact Softing's support team, you will find the contact data on
the back cover of the manual.

BC-600-PB Specifications
Softing Page 41
13 Specifications
Power supply
Via external AC adapter 100 V .. 240 VAC 50/60 Hz (galvanically
isolated) or direct connection to 24 VDC ±20%, approx. 0.5 A
(without galvanic isolation)
PROFIBUS D-sub connector (female), 9-pin,
switchable power supply for ext. bus termination
Protocol and frame analysis:
PROFIBUS DP and DPV1,
automatic baud rate detection 9.6 kbit/s .. 12 Mbit/s
Signal analysis:
PROFIBUS DP, DPV1, FMS and MPI;
signal quality index 0 .. 5000 determined from signal waveform
as well as signal/noise ratio and rise time;
signal sampling with 8/16 samples per bit
Oscillogram display:
Test range ±5V at 10mV resolution (differential), 0V…15V at
15mV resolution (A or B to DGND)
sampling rate: up to 384 MSamples/s,
for signal details: 2,400 sampled points,
for oscillogram analysis: 8,192 sampled points
Topology scan:
Active, maximum distance 230 m, accuracy ±2 m
V 2.0, high speed 480 Mbit/s, galvanically isolated
Trigger
IN : L=0 .. 0.8 V; H=2.4 .. 24 V; pulse > 10 μs, active high
OUT: approx. 5 V, active low (connection to storage oscilloscope)
10 memory locations for Quick Tests,
1 Trend log, max. 41 days
Test tool without cable: approx. 0.45 kg,
complete with carrying case, without accessories: approx. 3.9 kg
Permissible ambient
conditions
Operating temperature 0 .. 50 °C
Storage temperature -20 .. 70 °C,
Air humidity 10 .. 90% without condensation
Via four-line display and four function keys or via PC/notebook.
Localization of the display: DE+EN+FR+IT+PL+ES
(without national specific characters)
PROFIBUS Diagnostic Suite, see separate manual

General Notes Manual
Page 42 © 2013
14 General Notes
14.1 Lithium Battery
Warning! This product contains a lithi um backup battery.
The lithium content is not more than 1 g. The battery has been successfully
tested by the manufacturer in accordance with the UN Manual of Test and
Criteria (test procedures of P art II I, Sub-Section 38.3).
Improper handling of lithium batteries can cause the batteries to ignite or
explode and pose a burn hazard to users. If the product is properly handled,
this battery does not need to be replaced during the lifetime of the product.
Therefore, opening the product is unnecessary and not permitted. The product
must only be operated within the specified temperature range. Do not expose
to heat above this temperature range and keep away from open fire. Store in a
dry place.
14.2 CE Conformity
This product complies with the requirements of the EC Directives 2004/108/EC
Electromagnetic Compatibility (EMC directive)
Emission: EN 61000-6-4 Generic Emission Standard (industrial environments)
EN 55011 Group 1 Class A (ISM P roduct Standard)
EN 55022 Class A (ITE Product Standard)
Immunity: EN 61000-6-2 Generic Immunity S tandard (industrial environments)
EN 61326-1 (Measurement, Control and Laboratory Equipment
Product Standard)
A Declaration of Conformity in compliance with the above standards has been
made and can be inspected at Soft i ng AG on request.
NOTE:
For compliance with the legal EMC requirements, the other components
(PROFIBUS devices, AC adapter, etc.) must also meet these requirements. To
meet the EMC conditions, the product must be installed and connected in
accordance with the installation inst ructions.
Warning! This is a Class A product. In a domestic environment this product
may cause radio interference in which case the user may be required to take
adequate measures.

Industrial Automation GmbH
Tel. +49 89 45656-326 (Support)
Tel. +49 89 45656–340 (Sales)
Germany Email: support.automation@softing.com