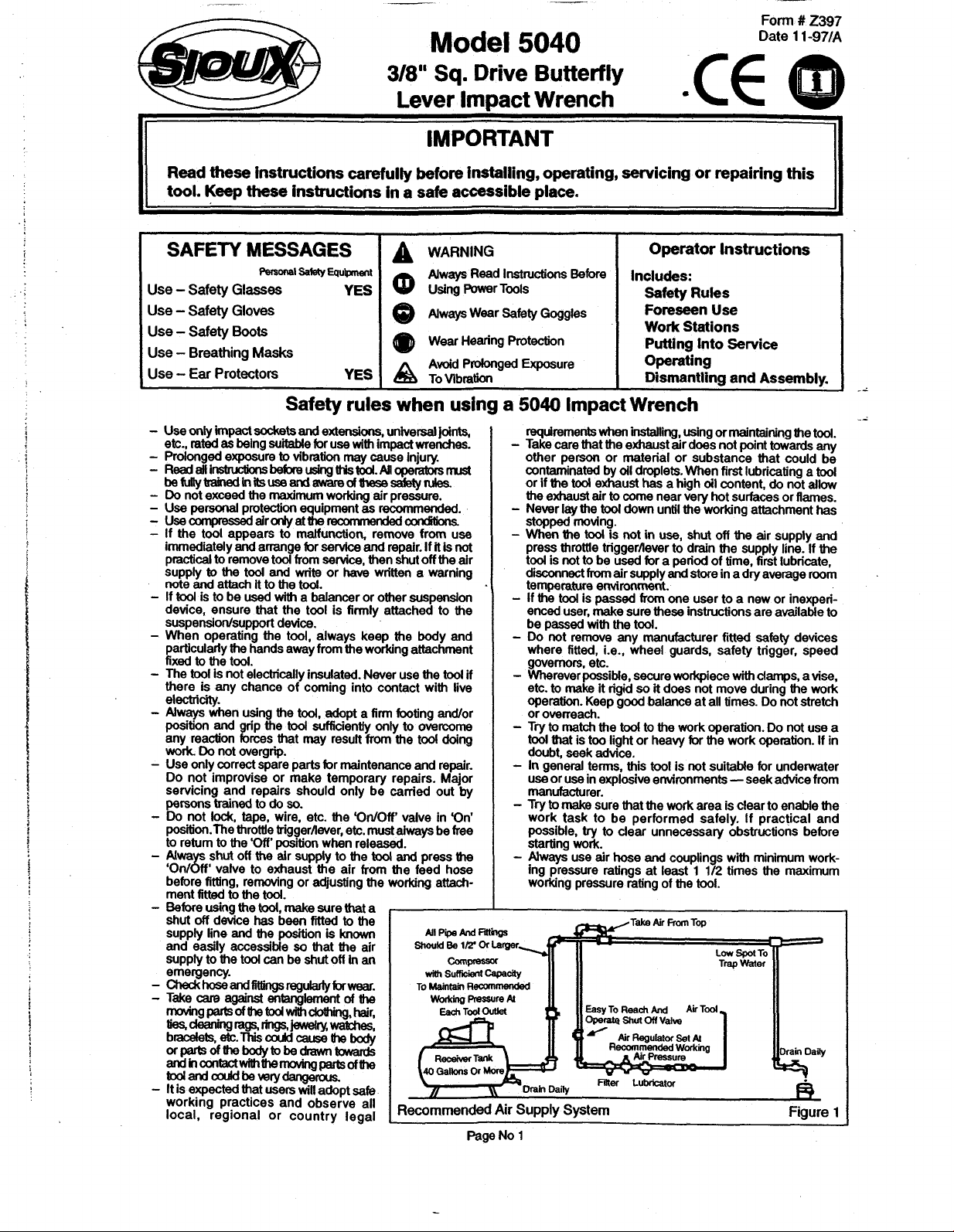
Model
-
5040
Form
Date
-
#
1 1 -97lA
Z397
318''
Sq.
Drive Butterfly
Lever Impact Wrench
IMPORTANT
Read
these instructions carefully before installing, operating, servicing or repairing this
tool. Keep these instructions in a safe accessible place.
2
SAFETY MESSAGES
Use - Safety Gloves
Use
-
Safety
Boots
Use - Breathing Masks
Use
-
Ear
Protectors
Safety rules when using
-
Use oniy impact sockets
etc., rated
-
Prolonged e-ure
-
RdAimbabWWW-Nmmd
b*Mhbmd6dm**
-
Do
-
Use
-
Use-drm&Wwm
-
If the tool appears to malfunction, remove from
immediately
practical
supply
note
-
If
device, ensure that the tool is firmly attached to the
suspension/support device.
-
When operating the tool, always keep the body and
particularly the hands away from the working attachment
fixed to the
-
The tool is not electrically insulated. Never use the
there is any chance of coming into contact with live
electricity.
-
Always when using the td,
position
any reaction forces that may result
work.
-
Use only correct $are parts for maintenance and rew'r.
Do not improvise or make temporary repairs. Maior
servicing and repairs should only be
wrsons trained to
-
Do not lock, tape, wire, etc. the 'On/0ff' valve in 'On'
position.The throttle triggerhever, etc.
to return to the
-
Awa
'0n/&' valve to exhaust the air from the feed hose
before fitting, removing or adjusting the
ment fitted
-
Eefore using the
shut
supply line
and easily accessible
supply to the td
emergency.
CheCk~and~reg~fGf~.
~&e
as
baing suitable for use with impact wrenches.
not exceed the maximum working air pressure.
personal
protection equipment & r&mended.
and
to
remove td from service, then shutoff the air
to
the td
and
attach it to the tool.
tool
is to be
used
td.
and
grip the tool sufficiently only
Do
not overgrb.
'Off'
shut off the air supply to the
to
the td.
off
device
and
care
against entang~ement of the
nmingpartsofthetcdwihdothing,hair,
*c+=lmra9ym%w%-,
b~ts,etc.Tlnscuddcause~body
orpartsofthcJbodytobedmwntuwa~~~
andin~~the~~ofthcJ
todandcculdbewty~
It is expected that users
working practices and observe all
local, regional or country legal
and
extensions, universal joints,
to
vibration
arrange for
and
with
do
tool,
has
the position
can
sew
write or have written a warning
a balancer or other suspension
adopt
so-
position when released.
make sure
been fitted to the
is
so
that the air
be shutoff
will
adopt
1
A
@
@
YES
may
that
known
,&I
cause injury.
atxi
repair. If
a firm footing and/or
to
from
must
tool
a
overcome
the td doing
cahed
always
and
woking
1-
in
an
To
sfe
1
Recommended
WARNING
Always Wear Safety Goggles
~arliearing Protection
Avoid Pmhged Exposure
T o Vibration
a
use
it
is
not
tool
if
out -by
be
free
press
the
attach-
Ail
Pi
And
Filtii
*W
wiul
suwi
Maintain
capacity
UmW
Air
Page No
@Câ
1
Operator Instructions
~ore&en Use
Work Stations
Putting Into
Operating
Dismantling
5040
-
-
-
-
-
-
-
-
-
-
Supply System
1
Impact Wrench
requirements
Take care that the exhaust air does not point towards any
other person or material or substance that could be
contaminated by
or if
the
the exhaust air to come near very hot surfaces or flames.
Never lay the tool down until the working attachment has
stopped moving.
When
press throttle triggerhever to drain the supply line. If the
td is
disconnect
temperature envirmnt.
If the td is passed from one user to a new or inexperienced user, make sure these instructions are available to
be passed with the td.
Do not remove any manufacturer fitted
where fitted, i.e., wheel guards, safety trigger, speed
governors, etc.
Wherever possible, secure workpiece with damps, a vise,
etc. to make it rigid
operation. Keep good balance at all
or overreach.
Try
to match the td to the work operation. Do not use a
tool !hat is too light or heavy for the work operation. If in
doubt,
In general terms, this tool is not suitable for underwater
use or use in explosive environments
manufacturer.
Try
to
work task to be performed safely, If practical and
possible,
starting work.
hays use air hose
ing pressure ratings at least
working pressure rating of the tool.
when
installing, using or maintaining the tool.
oil
tool exhaust has a high
the
td is not in
not
to
from
seek
make sure that the
try
Easy
droplets. When
use,
be
used
for a period of time, first lubricate,
air supply
advice.
to dear unnecessary obstructions before
To
and
.so it
does not move during the work
work
and
couplings with minimum work-
Take
Air
From
Reach
And
Service
and
first
oil
content, do not allow
shut off the air supply and
store in a dry average room
times.
-
area is dear to enable the
1
1/2
times the maximum
Top
Low
Spot
Trap
Water
Air
Td
@
Assembly.
lubricating a
safety
devices
Do not stretch
seek advice from
-
L.2
To
Figure
tool
-I
1
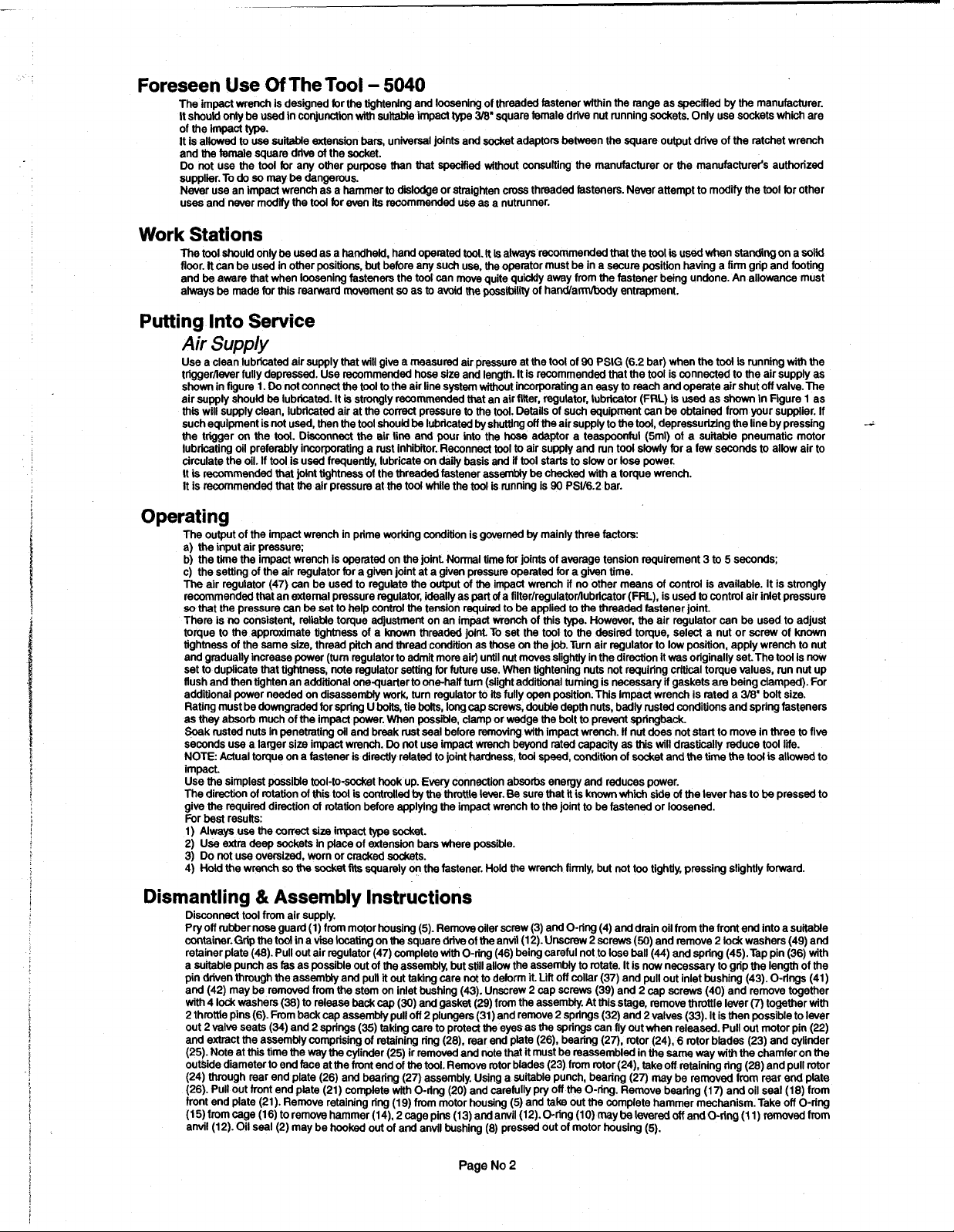
Foreseen Use
The impact
It should
of the impact
It is allwed to
and
the
female square drive
Do not use the tool for any other purpose than
supplier. To do
Never use an impact wrench as a hammer to dislodge or straighten cmss threaded fasteners. Never attempt to modify the tool for other
uses and never modify the td for
Of
The Tool
wrench
only
is designed for the tightening and Imning of threaded fastener within the range as specified by
be used in conjunction
type.
use
suitable extension bars, universal joints and socket adaptors beWn the square output drive of the ratchet wrench
$0
may
be
of
the socket.
dangemus.
even
-
5040
with
suitable impact type
that
its recommended use as a nutrunner.
3W
square female drive nut running sockets. Only use sockets
sptxified without consulting the manufacturer or the manufacturet's authorized
Work Stations
The
tool shoutd only be used as a handheld, hand operated tool.
floor.
It
can be used in other positions,
and be aware that when loosening fasteners the td can me quite quickly away from the fastener being undone. An allowance must
always
be
made for this rearward movement
but
before any such use, the operator must be in a secure position having a firm grip and footing
so
as to avoid
lt
is
always recommended that
the
possibility of hand'amhdy entrapment.
the
tool is used when stadng on a
Putting Into Service
Air
Supply
Use a clean iubtkated air supply that will give a measured air pressure at the tool of
tri~erflW8r fully depressed. Use recammended hose Size and lenath. It is recommended that the tool is connected to the air supply as
s&m in figure
air supply should
thii
will supply clean, lubricated air at the correct pressure to the tool. Details of such equipment can
such equipment is not used, then the tool shoukl be lubricated
the trigger on the td. Diinnect the air line and pour into the
lubricating oil preferably incorporating a rust inhibiior. Reconnect tool to air supply and run td slowly for a few seconds to albw air to
circulate the oil. If tool is used freauentlv. lubricate on
It
is
recommended that Wnt tight& &the threaded fasiener assembly be checked with a torque wrench.
It is recommended that
1.
Do
not connect the tool to the air line system withzut incorporating an easy to reach and operate air shut off valve.-he
be
lubricated. It
the
is
strongly recommended that an air filter, regulator, lubricator
by
shutting off
hose
adaptor a teaspoonful (5ml) of a suitable pneumatic motor
daii
basis and
air pressure at the tool while the tool is tunning is
if
tool starts to slow or lose mwer.
!XI
PSIG
(6.2
bar) when the tool is running with the
(FRL)
is
us&
as shown In Figure I as
be
the
air supply to the td, depressurizing the line by pressing
90
PSU6.2
bar.
obtained from your supplier. If
Operating
The output of the impact wrench in prime working condition is governed
a) the input air pressure;
b) the time the impact wrench is operated on the jomt. Normai time for joints of average tension requirement
c) the setting of the air regulator for a ghn joint at a given pressure operated for a given time.
The air regulator
recommended that an external pressure regulator, ideally as parl
so
that the pressure can
There is
tomue to the awmximate tiahtness of a
tightness of the &me size, t6read pitch and thread condiik as those on the job.Turn air regulatoito low position, apply wrench to nut
and gradually increase power (turn regulator to admit mom air) until nut moves slightly in the direction it was originally set. The td is now
set to duplicate that tightness, note regulator setting for future use. When tightening nuts not requiring critical toque values, run nut up
flush and then tighten an addiional onequarler to onehalf turn (&it additional turning is necessary if gaskets are being clamped). For
additional power needed on disassembly work, turn regulator to its fully open position. This impact wrench is rated a
Rating must be downgraded for spring U bolts, tie bolts, long cap screws, double depth nuts, badly rusted conditions and spring fasteners
as
they absorb much of the impact power. When posdtie, clamp or wedge the bolt to prevent springback.
Soak rusted nuts in penetrating oil and break rust seal before removing with impact wrench. If nut does not start to move in three to five
seconds use a larger size impact wrench. Do not use impact wrench beyond rated capacity as this will drastically reduce tool liie.
NOTE: Actual toque on a fastener is directly related to joint hardness, tool speed, condition of socket and the time the tool is allowed to
immct.
use the simplest possible tool-to-socket hook up. Every connection absoh energy and reduces paver.
The direction of mtation of
give the required direction of mtatiin before applying the impact wrench to the joint to be fastened or loosened.
For best resuns:
I)
Always
2)
Use extra
3)
Do not use oversized, worn
4)
Hold the wrench so
(47)
can be used to regulate the output of the impact wrench if no other means of control is available. It is strongly
be
no
consistent, reliable toque adjustment on an impact wrench of this
use
the correct
deep
set to help control the tension requid to be applied to the threaded fastener joint.
known
threaded
ioint.
thii
tool
Is
size
the
socket
impact
or
cracked sockets.
fits
sockets in place of
contmlled
squarely on the fastener. Hold the wrench firmly, but not too tightly, pressing slightly forward.
type
socket.
extension
by
the throttle lever.
bars where possible.
by
mainly three factors:
3
to 5 seconds;
of
a
filterlregulatorflubricator
To set the tool to the desired tome. select a nut or screw of known
Be
type.
sure that it is
(FRL), is used to control air inlet pressure
However, the air regulator can be used to adjust
known
whii
side
ol
the lever has to
the
manufacturer.
whii
3/8"
bolt size.
be
pressed to
are
solid
--
Dismantling & Assembly Instructions
Disconnect tool from air supply.
Pry off rubber nose guard
container. Grip the
retainer plate
a suitable punch as
pin driven through the assembly and pull it out taking care not to deform it.
and
with
2
throttie Pins
out
2
and extract the ayembly comprising
(25).
outside diameter to end face at the fmnt end of
(24)
(261,
front end plate
(15)
anvil
(48).
(42)
may be removed from the stem on inlet bushing
4
lock washers
(6).
valve seats
Note at this tlme the way the cylinder
through rear end plate
Pull out front end plate
from cage
(12).
oil
(21).
(16)
seal
(I)
tool in a vise locating on the square drive of
Pull out air regulator
Fmm back cap assembly pull off 2 plungers
(34)
(2)
from motor housing
fas
as possible out of the assembly, but still allow the assembly to mtate. It is now necessary to grip the length of the
(38)
to release
and 2 springs
Remove retaining ring
to remove hammer
may be
bat#
(35)
of
(26)
and bearing
(21)
complete with O-ring
(14).
hooked
out of and anvil bushing
(5).
Remove oiler screw
(47)
complete with O-ring
cap
(30)
taking care to protect
retaining ring
(25)
ir removed and note that it must be reassembled in the same way with the chamfer on the
the
(27)
(19)
2
cage pins
(43).
and gasket
(28).
tool. Remove mtor blades
assembly. Using a suitable punch, bearing
(20)
from motor housing
(13)
Page
(3)
the
anvil
(46)
Unscrew 2 cap screws
(29)
from the assembly. At this stage, remove throttle lever
(31)
and remove 2 Springs
the
rear end plate
and carefully pry off the O-ring, Remove bearing
and anvil
(8)
No
and O-ring
(12).
Unscrew 2 screws (50) and remove
being careful not to lose ball
Lift
eyes as the springs can fly out when released. Pull out mtor pin
(26).
(23)
(5)
and
take
(12).
O-ring
pressed out of motor housing
2
Off collar
bearing
from mtor
out
the
(10)
(4)
and drain oil from the front end into a suitable
(44)
(37)
and pull out inlet bushing
(39)
and 2 cap screws
(32)
and 2 valves
(27),
mtor
(24),6
(24),
take off retaining ring
(27)
may be removed from rear
complete hammer mechanism. Take off O-ring
may be levered
(5).
2
and spring
off
lock
(45).Tap
(40)
and remove together
(33).
It is then possible to lever
mtor blades
(1 7)
and oil seal
and O-ring
washers
pin
(43).
O-rings
(7)
together with
(23)
and cylinder
(28)
and pull mtor
(I
1)
removed from
(49)
(36)
end
(18)
and
with
(41)
(22)
plate
from