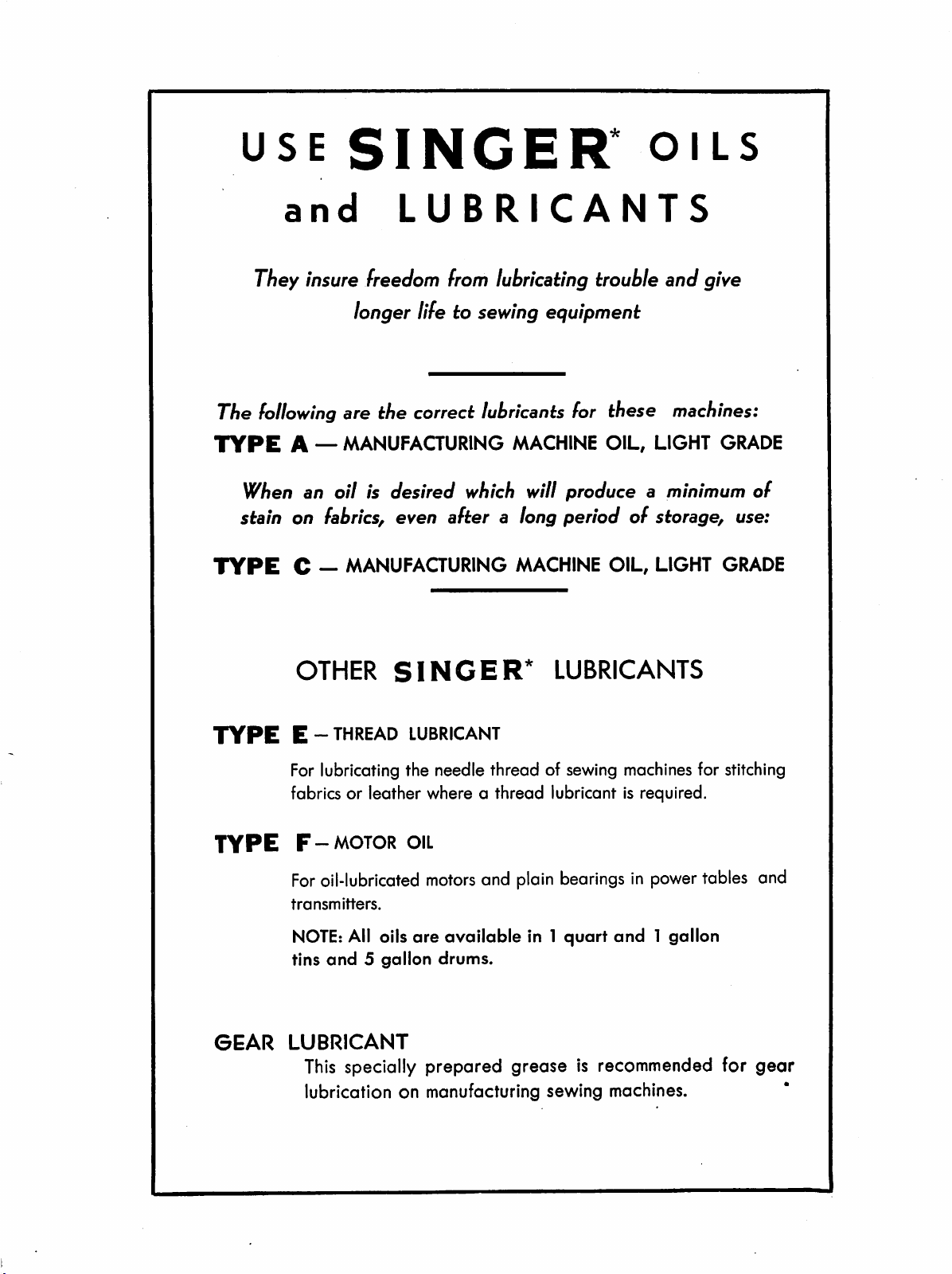
USE
SINGER
OILS
and
They insure freedom
The
following
TYPE
stain on fabrics, even after a long period of storage, use:
TYPE
A — MANUFACTURING MACHINE
When an oil is desired which will produce a minimum
C — MANUFACTURING MACHINE
are the correct lubricants for these
OTHER
LUBRICANTS
longer
SINGER*
from
life
lubricating trouble and give
to
sewing
equipment
OIL,
LIGHT GRADE
OIL,
LIGHT GRADE
LUBRICANTS
machines:
of
TYPE
type
GEAR
E -THREAD
For lubricating the needle thread of sewing machines for stitching
fabrics or leather where a thread lubricant is required.
F-motor
For
oil-lubricated
transmitters.
NOTE:
tins
LUBRICANT
All oils
and5gallon
This
specially prepared grease is recommended for
lubrication on manufacturing sewing machines.
LUBRICANT
oil
motors
are
and
available
drums.
plain
bearingsinpower
in 1
quart
and
tables and
1 gallon
gear
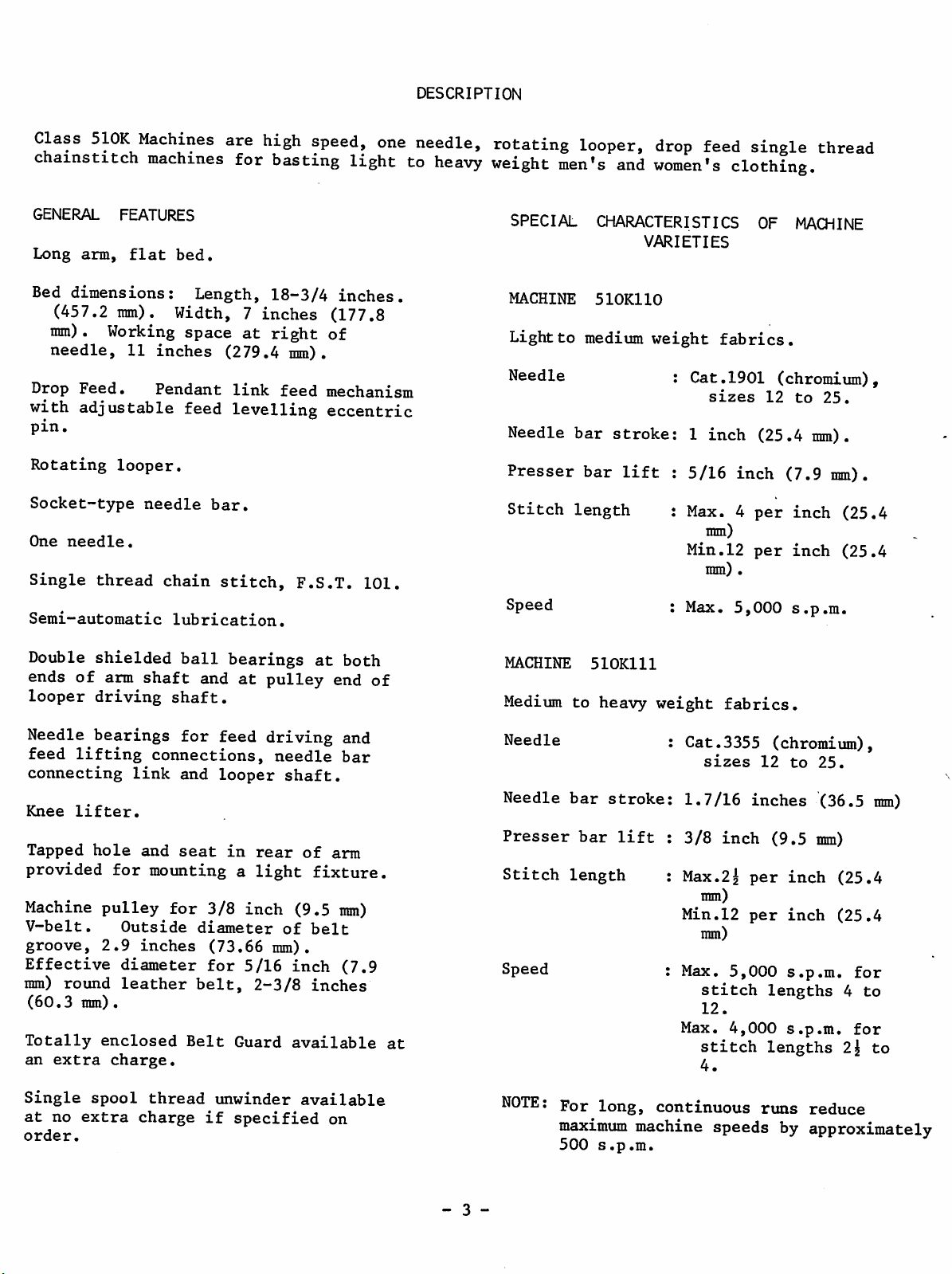
DESCRIPTION
Class
510K
chainstitch
GENERAL
Long
Bed
dimensions:
(457,2
mm),
needle,
Drop
with
pin.
Rotating
Socket-type
One
needle.
Single
Semi-automatic
FEATURES
arm,
mm).
Working space
11
Feed,
adjustable
looper.
thread
Machines
machines
flat
bed.
Length,
Width, 7
inches
Pendant
feed
needle
chain
lubrication.
are
high
speed,
for basting light to
at
(279,4
link
levelling
bar.
stitch,
18-3/4
inches
right
mm).
feed
(177,8
of
mechanism
eccentric
F.S.T,
inches,
101,
one
needle,
heavy
rotating
weight
SPECIAL CHARACTERISTICS OF
MACHINE
Lighttomedium
Needle
Needle
Presser
Stitch
Speed
looper,
men's
510K110
bar
bar
length
and
women's
VARIETIES
weight
stroke:
lift
drop
feed
:
Cat,1901
1
:
5/16
:
Max,4per
Min,12
:
Max,
fabrics.
sizes
inch
mm)
mm) ,
single
clothing.
MACHINE
(chromium),
12
to
(25,4
inch
5,000
per
(7,9
inch
inch
s.p.m.
thread
25,
mm),
mm).
(25,4
(25,4
Double
ends
of
looper
Needle
feed
lifting
connecting
Knee
Tapped
lifter.
hole
provided
Machine
V-belt,
groove,
Effective
mm)
round
(60,3
Totally
an
Single
at
order.
extra
no
mm),
spool
extra
shielded
arm
shaft
driving
bearings
link
and
for
mounting a
pulley
Outside
2,9
inches
diameter
leather
enclosed
charge.
thread
charge
ball
bearings
and
at
shaft.
for
feed
connections,
and
looper
seat
for
in
3/8
diameter
(73,66
for
belt,
Belt
Guard
unwinder
if
specified
pulley
driving
rear
light
inch
5/16
2-3/8
needle
shaft.
of
(9,5
of
mm).
inch
available
available
at
both
end
and
bar
arm
fixture.
mm)
belt
(7,9
inches
on
of
at
MACHINE
Medium
Needle
Needle
Presser
Stitch
510K111
to
heavy
bar
stroke:
bar
length
lift
weight
:
Cat,3355
sizes
1,7/16
:
3/8
: Max,2^
mm)
Min,12
mm)
Speed : Max,
stitch
12,
Max,
stitch
4.
NOTE:
For
long,
maximum
500
s.p.m.
continuous runs reduce
machine speeds by approximately
fabrics.
12
inches
inch
per
per
5,000
lengths
4,000
lengths
(chromium),
to
25,
(36,5
(9,5
mm)
inch
inch
s.p.m,
s.p.m,
(25,4
(25,4
for
4
for
2^
mm)
to
to
- 3 -