
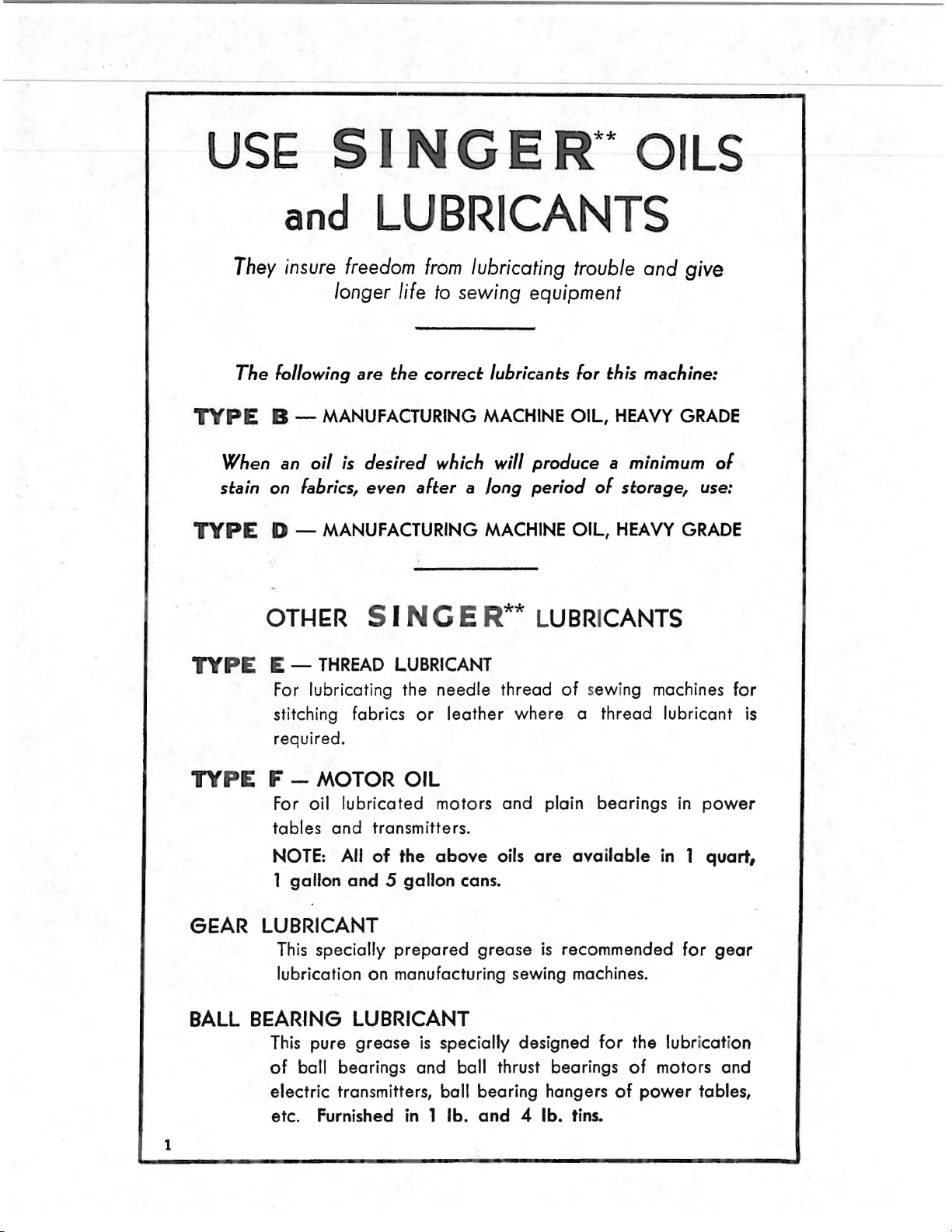
USE
SI
GER
**
OILS
and
They
The
TYPE
When
stain on fabrics,
TYPE
TYPE
insure
following are
B - MANUFACTURING MACHINE
an
D - MANUFACTURING MACHINE
OTI-I£:R
E -
For lubricating the needle thread
stitching fabrics
required.
freedom
longer
oil
is
THREAD
LUBRI
from
life
to
sewing equipment
the
correct lubricants lor this machine:
desired which will produce a minimum
even
5 I N
alter a long period
Ci
E R
LUBRICANT
or
leather where a thread lubricant
CAN
lubricating
**
L
UBRICANTS
trouble
OIL,
of
OIL,
of
sewi
TS
and give
HEAVY GRADE
storage, use:
HEAVY GRADE
ng
machines
of
for
is
TYPE
GEAR LUBRICANT
BALL BEARING LUBRICANT
1
F - MOTOR
For
oil
lubricated motors and plain bearings
tables and transmitters.
NOTE: All
1 gallon and 5 gallon cans.
This
specially prepared grease
lubrication on manufacturing sewing machines.
This
pure grease
of
ball bearings and ball thrust bearings
electric transmitters, ball bearing hangers
etc. Furnished in 1
of
OIL
the
above
is
specially designed
lb.
oils
and 4 lb.
are
is
recommended
available
for
the lubrication
of
of
tins.
in
power
in 1
quart,
for
motors and
power
tables,
gear
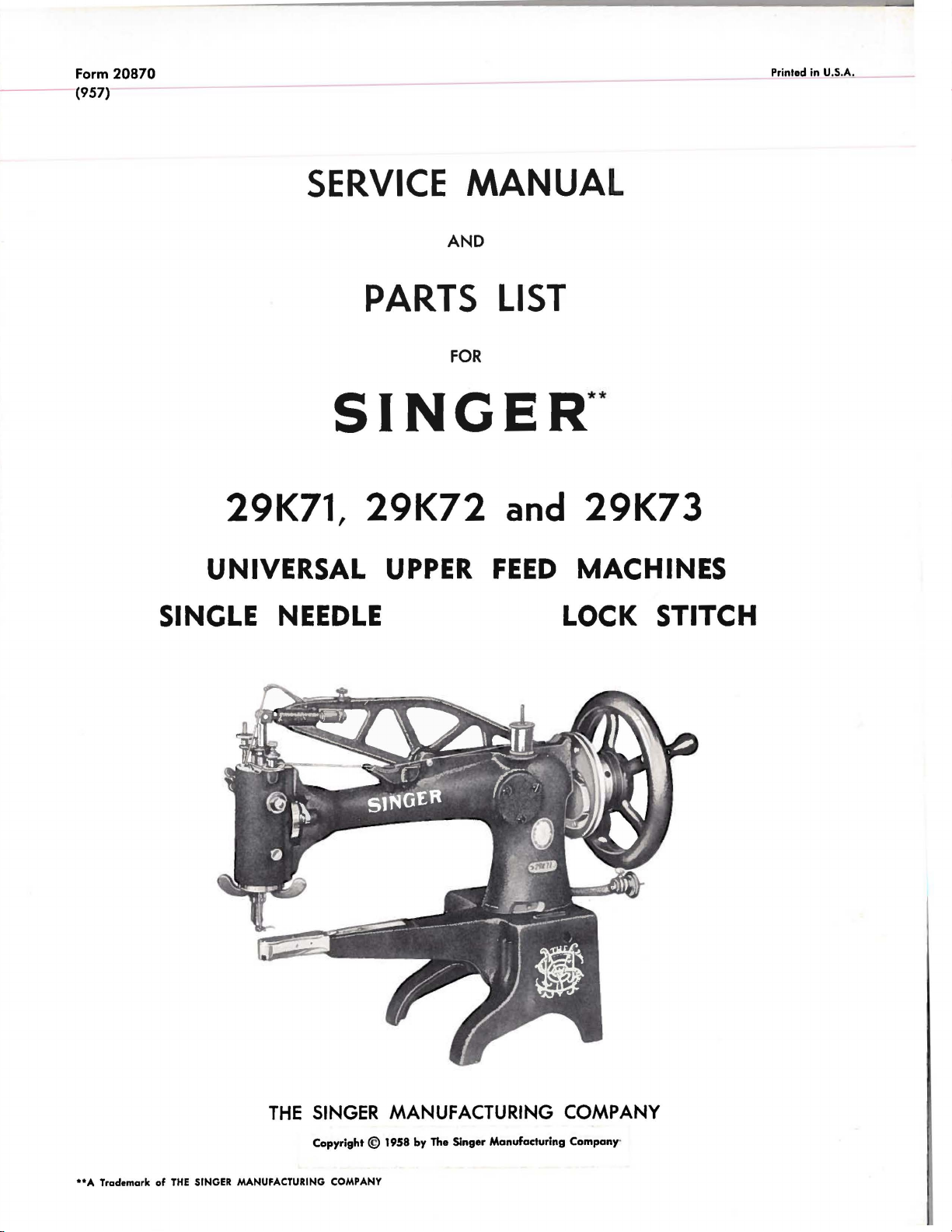
Form 20870
(957)
Printed in
U.~.S.A
"--
.
_
29K71, 29K72
UNIVERSAL
SINCLE
SERVICE
PARTS
MANUAL
AND
LIST
FOR
SINGER**
and
UPPER
NEEDLE LOCK STITCH
FEED
29K73
MACHINES
THE
**A
Trademark
of
THE
SINGER
SINGER
Copyright©
MANUFACTURING
COMPANY
MANUFACTURING
1958
by
The Singer Manufacturing Company·
COMPANY
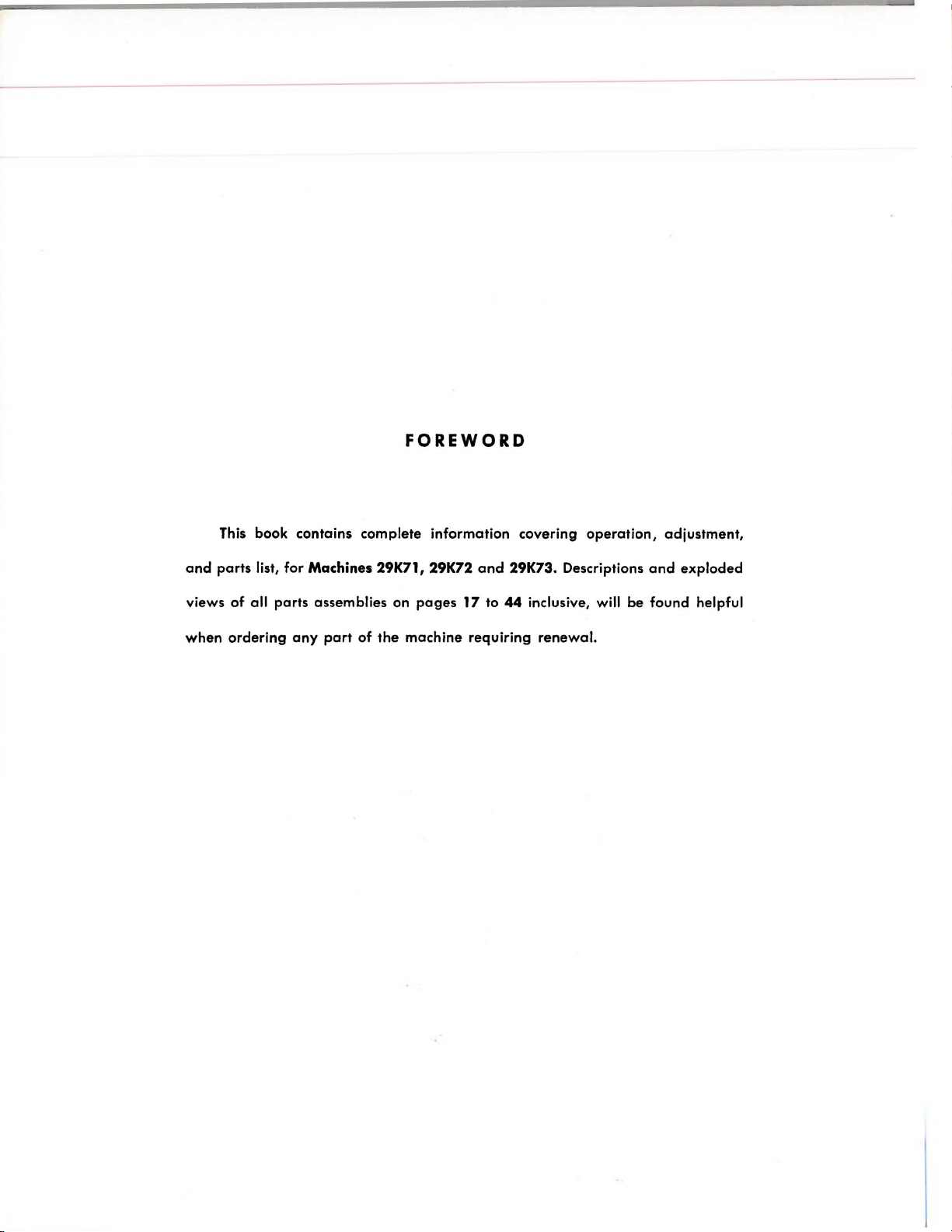
FOREWORD
This book contains complete information covering
and
parts
views
when
list, for Machines 29K71, 29K72
of
all
parts
assemblies on
ordering
any
part
of
the
machine
pages
and
17
to
requiring
operation,
29K73. Descriptions
44 inclusive, will
renewal.
be
and
found
adjustment,
exploded
helpful
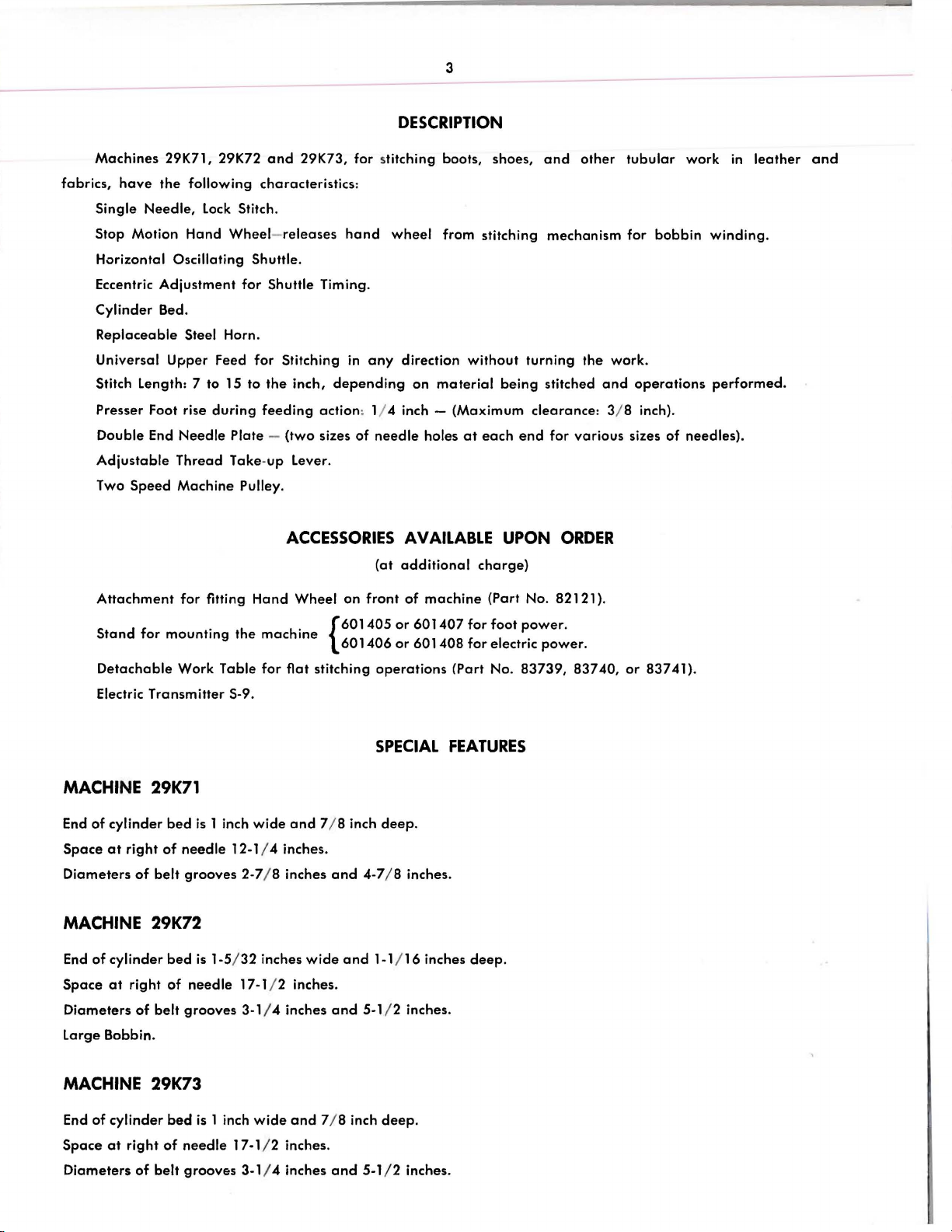
3
DESCRIPTION
Machines
fabrics,
Single
Stop Motion
Horizontal Oscillating Shuttle.
Eccentric
Cylinder
Replaceable
Universal
Stitch Length: 7 to 15 to
Presser Foot rise
Double End
Adjustable
Two
Attachment
have
Needle,
Speed
the
Adjustment
Bed.
29K71, 29K72
following characteristics:
Lock
Hand
Steel Horn.
Upper
Feed
during
Needle
Thread
Machine
for
fitting
and
29K73, for stitching boots, shoes,
Stitch .
Wheel-
Plate -(two
Take-
releases
for
Shuttle Timing.
for
Stitching
the
inch,
feeding
up
Lever.
Pulley.
ACCESSORIES
Hand
Wheel
hand
wheel
in
any
direction
depending
action
: 1 I 4 inch - (Maximum
sizes
of
needle
on
holes
AVAILABLE UPON
(at
additional
on
front
of
machine
from stitching
without
material
being
at
each
charge)
(Part No. 82121
and
mechanism
turning
stitched
clearance:
end
for
ORDER
other
the
work.
and
318 inch).
various
).
tubular
for
bobbin
operations
sizes
of
work
in
winding.
performed.
needles).
leather
and
Stand
for
Detachable
Electric
MACHINE
End
of
cylinder
Space
at
right
Diameters
of
MACHINE
End
of
cylinder
Space
at
right
Diameters
Large Bobbin.
of
. .
mountmg
Work Table
Transmitter
29K71
bed
is
1 inch
of
needle
belt
grooves
29K72
bed
is
1-51
of
needle
belt
grooves
the
mach
me
for
flat stitching
S-9.
wide
and
12-1 I 4 inches.
2-718 inches
32
inches
wide
17-1/ 2 inches.
3-1 I 4 inches
{601405
601406
7/ 8 inch
and
4-7
and
and
5-1
or
601407
601408
or
operations
SPECIAL
deep.
/ 8 inches.
1-1
I 16 inches
/ 2 inches.
for foot
f
1
ore
ectnc
(Part No.
FEATURES
deep.
power.
.
power.
83739,
83740,
or
83741).
MACHINE
End
of
Space
Diameters
29K73
cylinder
at
right
of
bed
of
belt
is
1 inch
needle
grooves
wide
and
7/ 8 inch
17-1 12 inches.
3-1 I 4 inches
and
5-11 2 inches.
deep.
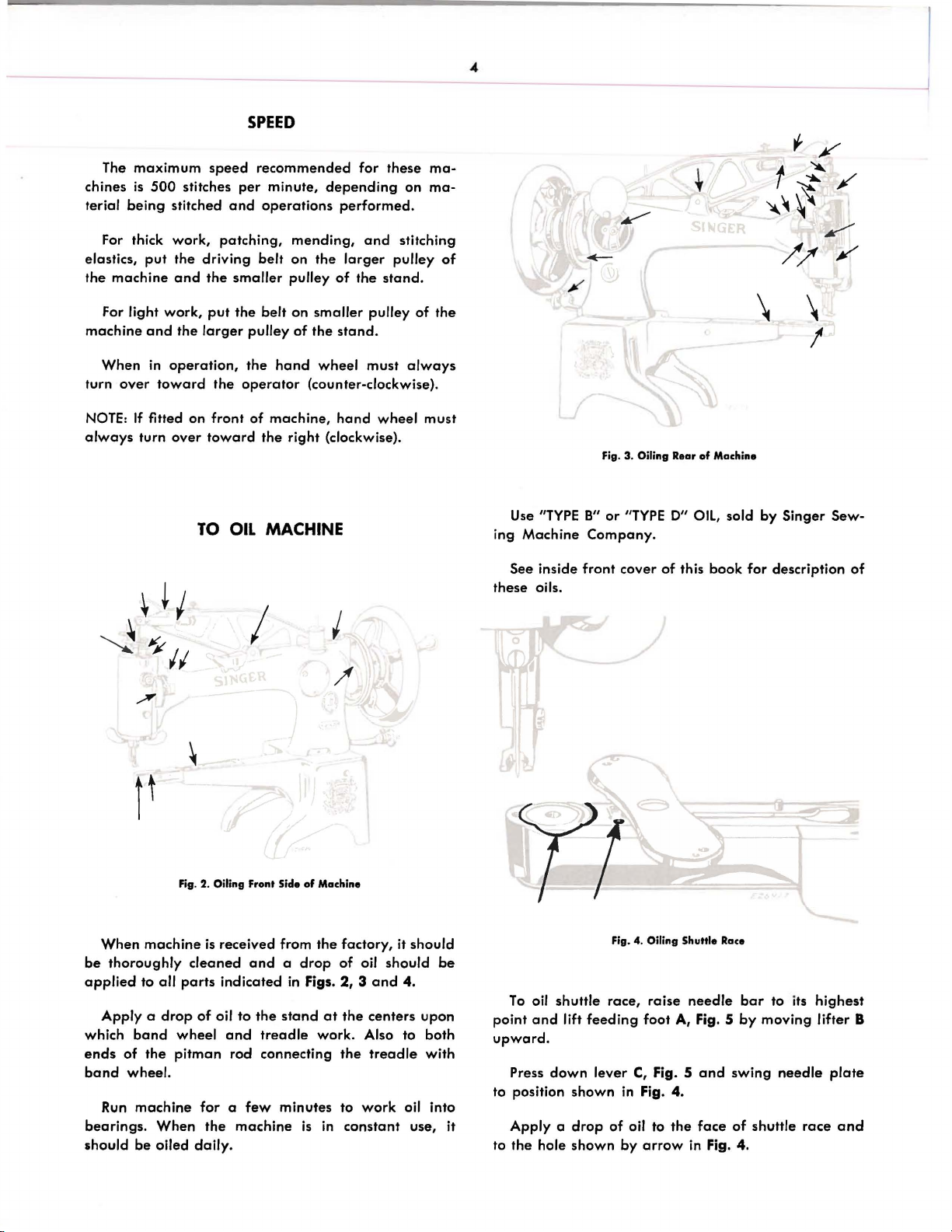
The
chines
terial
maximum
is
500
being
stitched
speed
stitches
SPEED
recommended
per
minute,
and
operations
for
depending
performed.
these
on
_j
mama-
For thick work,
elastics,
the
machine
turn
NOTE:
always
put
machine
For light work,
and
When
in
over
toward
If
fitted
turn
patching,
the
driving belt on
and
the
put
the
larger
operation,
the
on
front
over
toward
TO
OIL
mending,
the
smaller
the
operator
pulley
of
belt
on
smaller
pulley
of
the
the
hand
wheel
(counter-clockwise).
of
machine,
the right (clockwise).
MACHINE
I
and
larger
the
pulley
stand.
must
hand
stitching
pulley
stand.
always
wheel
of
must
of
the
Fig. 3. Oiling Rear
Use
"TYPE
B"
or
ing Machine
See inside front cover
these oils.
Company.
"TYPE
\
of
Machine
D"
Oil,
sold
by
Singer Sew-
of
this book for description
\
I
of
Fig.
2.
When
machine
be
thoroughly
applied
which
ends
band
bearings.
should
to all
Apply a drop
band
of
the
wheel.
Run
machine
be
parts
wheel
pitman
When
oiled
Oiling Front Side
is
received from
cleaned
indicated
of
oil
to
and
rod connecting
for a few
the
machine
daily.
and a drop
the
of
in
stand
treadle
minutes to
is
Machine
the
factory,
of
Figs. 2, 3
at
the
work. Also to both
the
in
constant
it
should
oil should
and
4.
centers
treadle
work
oil into
use,
upon
be
with
it
To
oil shuttle race,
point
and
upward.
Press
down
to position
Apply a
to
the
hole
lift
feeding
shown
drop
shown
Fig. 4. Oiling ShuHie Race
raise
needle
foot A, Fig. 5
lever
C,
Fig. 5
in
Fig. 4.
of
oil to
the
face
by
arrow
in
and
Fig. 4.
bar
to its
by
moving lifter B
swing
needle
of
shuttle
highest
plate
race
and
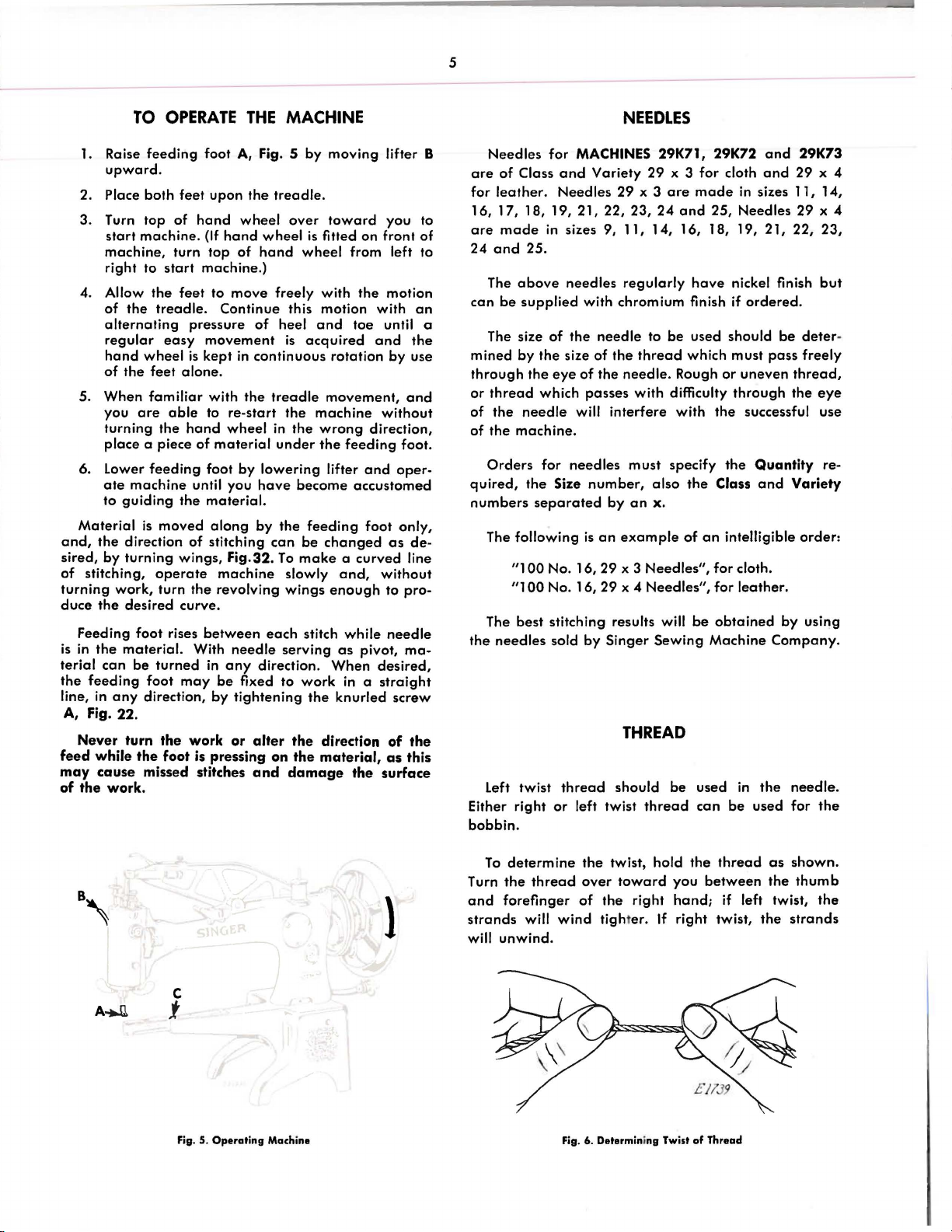
TO
OPERATE
THE
MACHINE
5
NEEDLES
1. Raise
2. Place
3. Turn
4.
5.
6. Lower
Material
and,
the
sired,
of
stitching,
turning
duce
the
Feeding foot rises
is
in
the
terial
the
feeding
line, in
A, Fig. 22.
Never
feed
while
may
cause
of
the
feeding
upward.
both
top
start
machine.
machine,
right
to
Allow
the
of
the
alternating
regular
hand
wheel
of
the
feet
When
familiar
you
are
turning the
place
a piece of
feeding
ate
machine
to
guiding
is
direction of stitching
by
turning
work,
desired
material.
can
be
foot
any
direction,
turn
the
missed stitches
work.
foot A, Fig. S by
feet
upon
of
hand
(If
turn
top
start
machine.)
feet
to
treadle.
pressure
easy
movement
is
kept
alone.
with the
able
to
hand
material
foot
until you
the
material.
moved
operate
turn
turned
the
foot
along
wings, Fig.32.
machine
the revolving
curve.
between
With
in
may
be
by
work
is
pressing
moving
the
treadle.
wheel
hand
of
move
Continue this motion with
in
re-start
wheel
by
needle
any
fixed to
tightening
or
over
wheel
is
hand
wheel
freely with
of
heel
and
is
acquired
continuous
treadle
the
machine
in
the
under
lowering
have
become
by
the
feeding
can
be
To
make a curved
slowly
wings
each
stitch
serving
direction.
work
the
alter
the
on
the
and
damage
toward
fitted on front of
rotation
movement,
wrong
the
lifter
changed
enough
as
When
knurled
direction
material,
lifter B
you to
from left to
the
motion
toe until a
and
by
without
direction,
feeding
and
oper-
accustomed
foot only,
as
and,
without
to pro-
while
needle
pivot,
desired,
in a straight
screw
of
as
the
surface
an
the
use
and
foot.
de-
line
ma-
the
this
Needles
are
of
for
leather.
16, 17, 18, 19, 21, 22, 23,
are
24
and
The
can
be
The size
mined
through
or
thread
of
the
of
the
Orders
quired,
numbers
The
The
the
needles
for
MACHINES 29K71, 29K72
Class
and
Variety
Needles
made
in sizes 9, 11, 14, 16, 18, 19, 21,
25.
above
by
machine.
following
"1
"1
best
needles
supplied
of
the
the
size
the
eye
which
needle
for
needles
the
Size
separated
00
No. 16,
00
No. 16,
stitching results will
sold
29
regularly
with chromium finish if
needle
of
the
of
the
needle.
passes
will
is
by
with difficulty
interfere
must
number,
by
an
an
example
29
x 3 Needles",
29
x 4 Needles", for
Singer
THREAD
Left twist
Either right
bobbin.
thread
or
left twist
should
29
x 3
are
24
to
be
thread
specify
also
x.
Sewing
be
thread
x 3
for
made
and
25, Needles
have
used
which must
Rough
or
with
the
the
Class
of
an
for
be
obtained
Machine
used
can
and
cloth
and
in
sizes 11,
nickel finish
ordered.
should
the
intelligible
be
be
pass
uneven
through
successful
Quantity
and
cloth.
leather.
Company.
in
the
used
by
29K73
29
x 4
14,
29
x 4
22, 23,
but
deter
freely
thread,
the
eye
use
re-
Variety
order:
using
needle.
for
the
-
To
determine
Turn
the
thread
and
forefinger
l
strands
will
will
unwind
wind
.
c
A....U
j
Fig. 5.
Operating
Machine
Fig. 6. Determining Twist
the
twist, hold
over
of
the
tight
toward
right
er.
the
you
hand;
If
right twist,
of
thread
between
if left twist,
the
Thread
as
the
shown.
thumb
the
strands
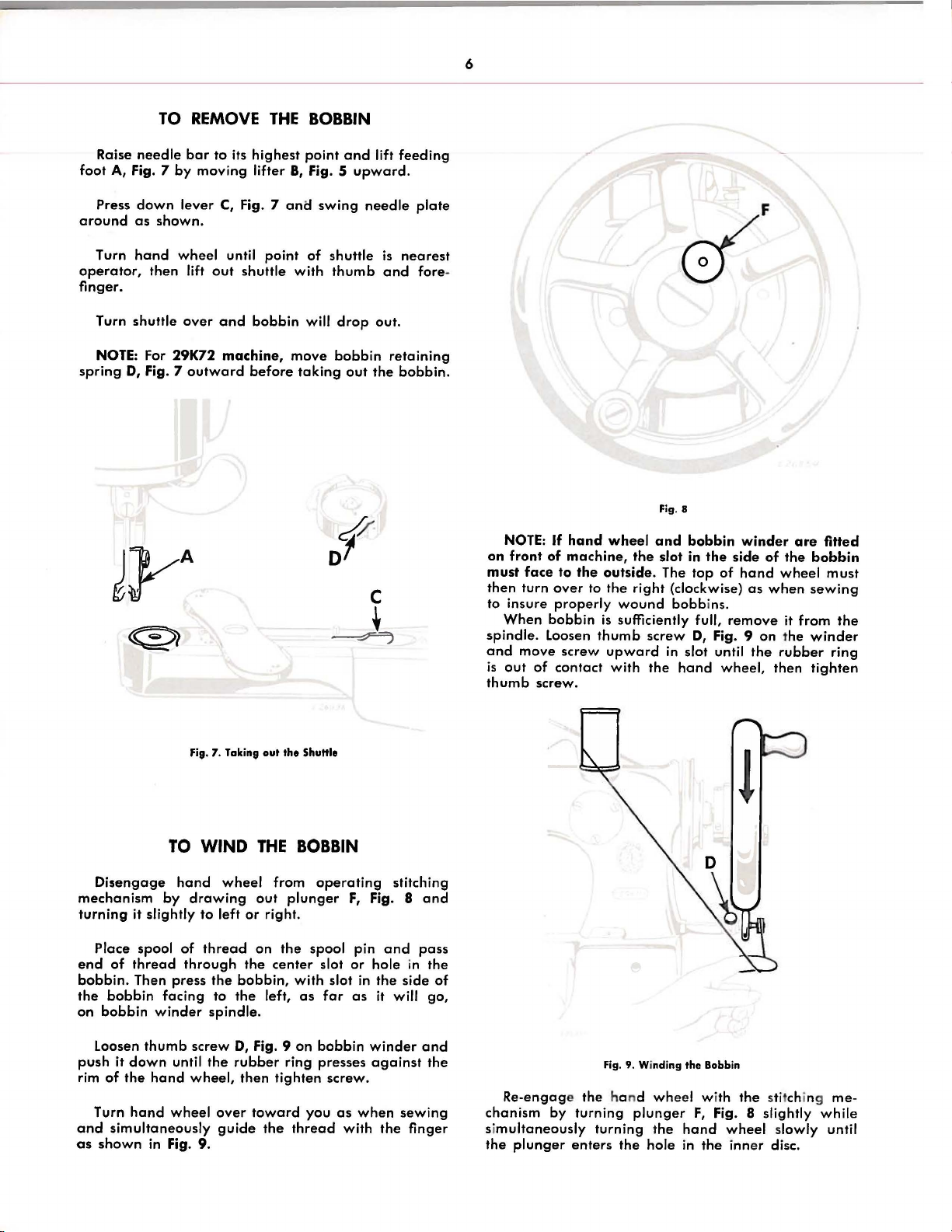
TO
Raise
needle
foot A, Fig. 7
Press
down
around
operator,
finger.
Turn
as
shown.
hand
then
REMOVE
bar
to its
by
moving
lever
C,
wheel
lift
out
Fig. 7
until
shuttle
THE
highest
lifter
B,
ana
point
BOBBIN
point
Fig. 5
swing
of
shuttle
with
thumb
and
lift
upward.
needle
feeding
is
nearest
and
plate
fore
6
if'F
-
Turn shuttle
NOTE:
spring
D,
over
For 29K72
Fig. 7
outward
Fie. 7. Takine
and
bobbin
machine,
before
out
move
taking
the
will
bobbin
of'
J,
Shuttle
drop
out
out.
retaining
the
bobbin.
c
NOTE:
on
front
must
face
then
turn
to insure
When
spindle.
and
move
is
out
thumb
of
If
hand
of
machine,
to
over
properly
bobbin
loosen
screw
contact
screw.
wheel
the
outside.
to
the
wound
is
sufficiently full,
thumb
upward
with
and
the
right
screw
the
Fig. 8
bobbin
slot in
the
The
top
(clockwise)
bobb
ins.
D,
in
slot until
hand
winder
side
of
hand
remove
Fig. 9
wheel,
of
as
when
on the
the
are
the
wheel
it
from
rubber
then
fitted
bobbin
must
sewing
the
winder
ring
tighten
TO
Disengage
mechanism
turning
end
bobbin.
the
on
push
rim
and
as
it slightly
Place spool
of
thread
Then
bobbin
bobbin
loosen
it
down
of
the
Turn
hand
simultaneously
shown
hand
by
press
facing
winder
thumb
until
hand
wheel
in
Fig.
WIND
drawing
to
of
thread
through
spindle.
screw
the
wheel,
9.
wheel
left
the
to
over
guide
THE
out
or
right.
on
the
bobbin,
the
left,
D,
Fig. 9
rubber
then
toward
the
BOBBIN
from
plunger
the
center
with
as
on
ring
tighten
you
thread
operating
F,
spool pin
slot
or
slot
in
far
as
bobbin
presses
screw.
as
when
with
stitching
Fig. 8
and
hole
the
side
it will
winder
against
sewing
the
and
pass
in
the
of
go,
and
the
finger
Re-engage the
chanism
si
multaneously
the
by
plunger
Fig.
ha nd whee
turning
turning the
enters
the
9. Winding the Bobbin
l w ith
plunger
hole
F,
Fig. 8 slightly
hand
wheel
in
the
the sti
tching me-
slowly until
inne r disc.
while
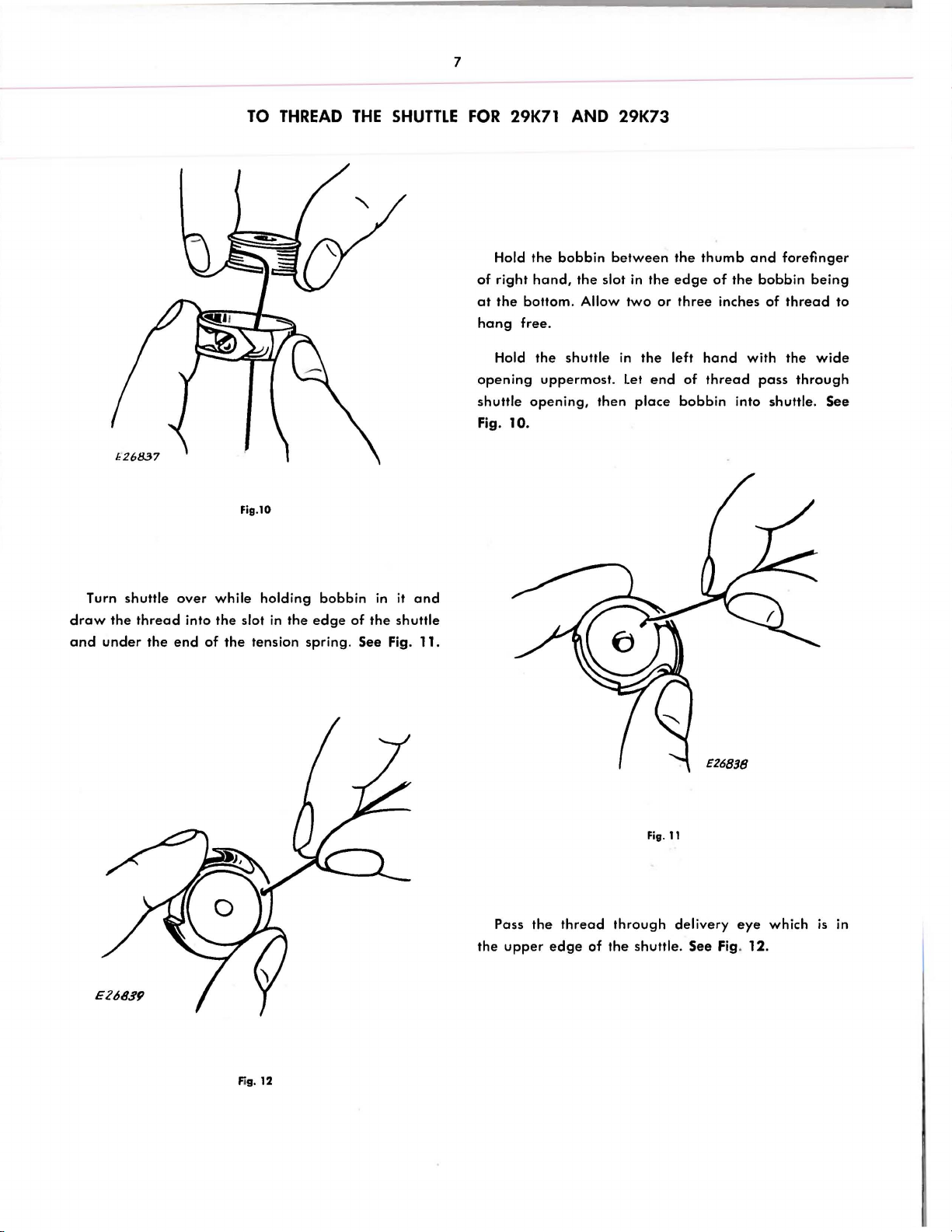
TO
Fig.10
THREAD
THE
7
SHUTTLE
FOR
Hold
of
right
at
the
hong
Hold
opening
shuttle
Fig.
29K71
the
hond,
bottom.
free
the
uppermost.
opening,
10.
AND
bobbin
.
shuttle
the
slot
Allow
then
29K73
between
in
the
two
in
the
Let
end
place
or
the
edge
three
left
of
bobbin
thumb
of
the
inches
hand
thread
into shuttle.
end
bobbin
of
with
pass
forefinger
being
thread
the
to
wide
through
See
Turn
drew
end
shuttle
the
under
thread
the
over while
into
the
end
of
the
holding
slot
tension
in
the
bobbin
edge
spring
in
it
of
the
shuttle
. See Fig.
end
11.
the
Poss
upper
the
thread
edge
of
through
the
shuttle
Fig.
11
delivery
. See Fig.
eye
12.
which
is
in
Fig. 12
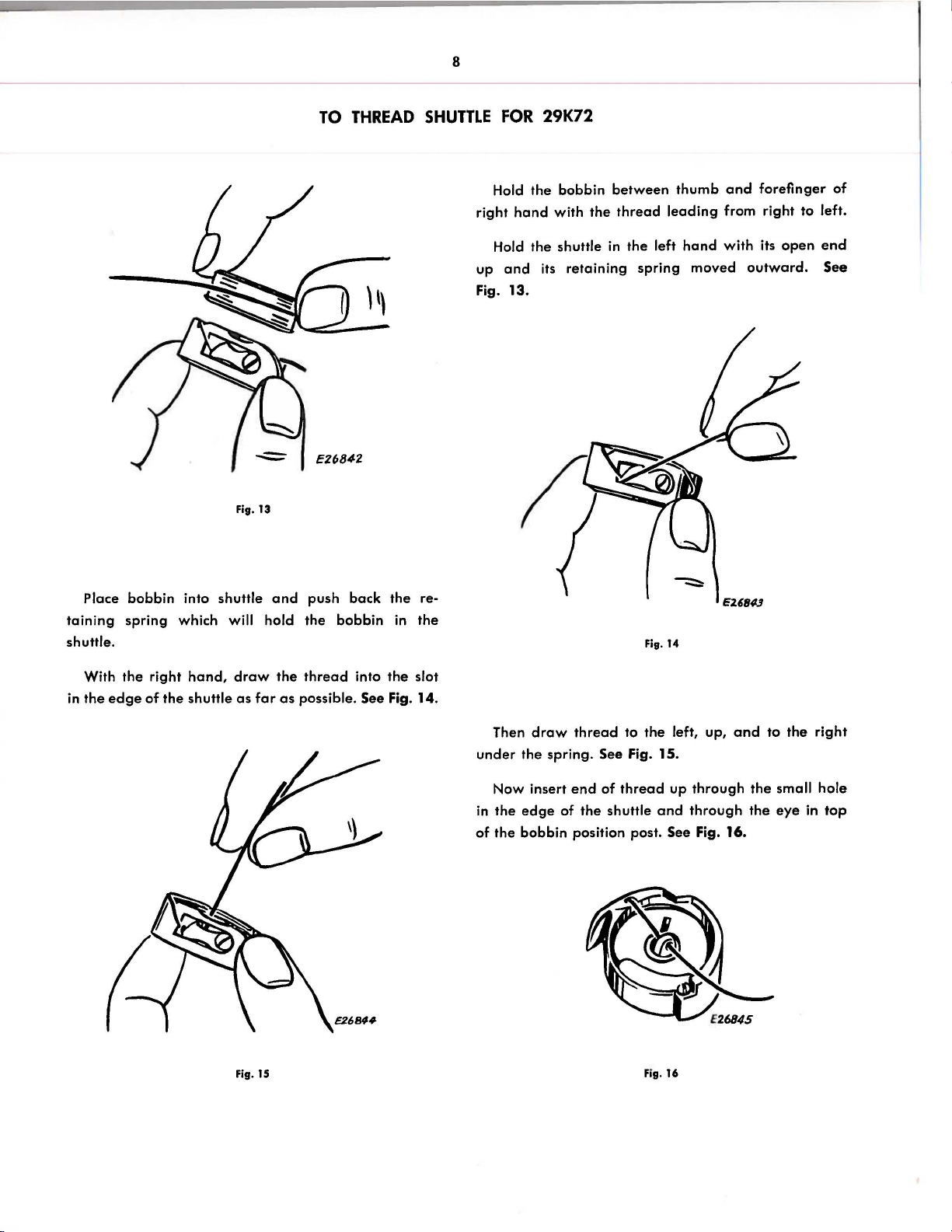
Fig. 13
TO
THREAD
8
SHUTTLE
right
up
Fig. 13.
FOR
Hold
Hold
and
the
hand
the
29K72
bobbin
with
shuttle
its
retaining
between
the
in
thread
the
spring
thumb
leading
left
hand
and
from right
with
moved
forefinger
its
open
outward.
to
of
left.
end
See
Place
taining
shuttle.
With
in
the
bobbin
spring
the
edge
into shuttle
which will hold
right
hand,
of
the
shuttle
draw
as
far
and
push back
the
bobbin
the
thread
as
possible. See Fig. 14.
into
the
in
the
re-
the
slot
Then
under
the
Now insert
in
the
edge
of
the
bobbin
Fig. 14
draw
thread
spring.
end
of
position post. See Fig. 16.
to
See Fig. 15.
of
thread
the
shuttle
the
and
left, up,
up
through
through
and
the
the
to
the
right
small hole
eye
in
top
Fig. 15
Fig. 16
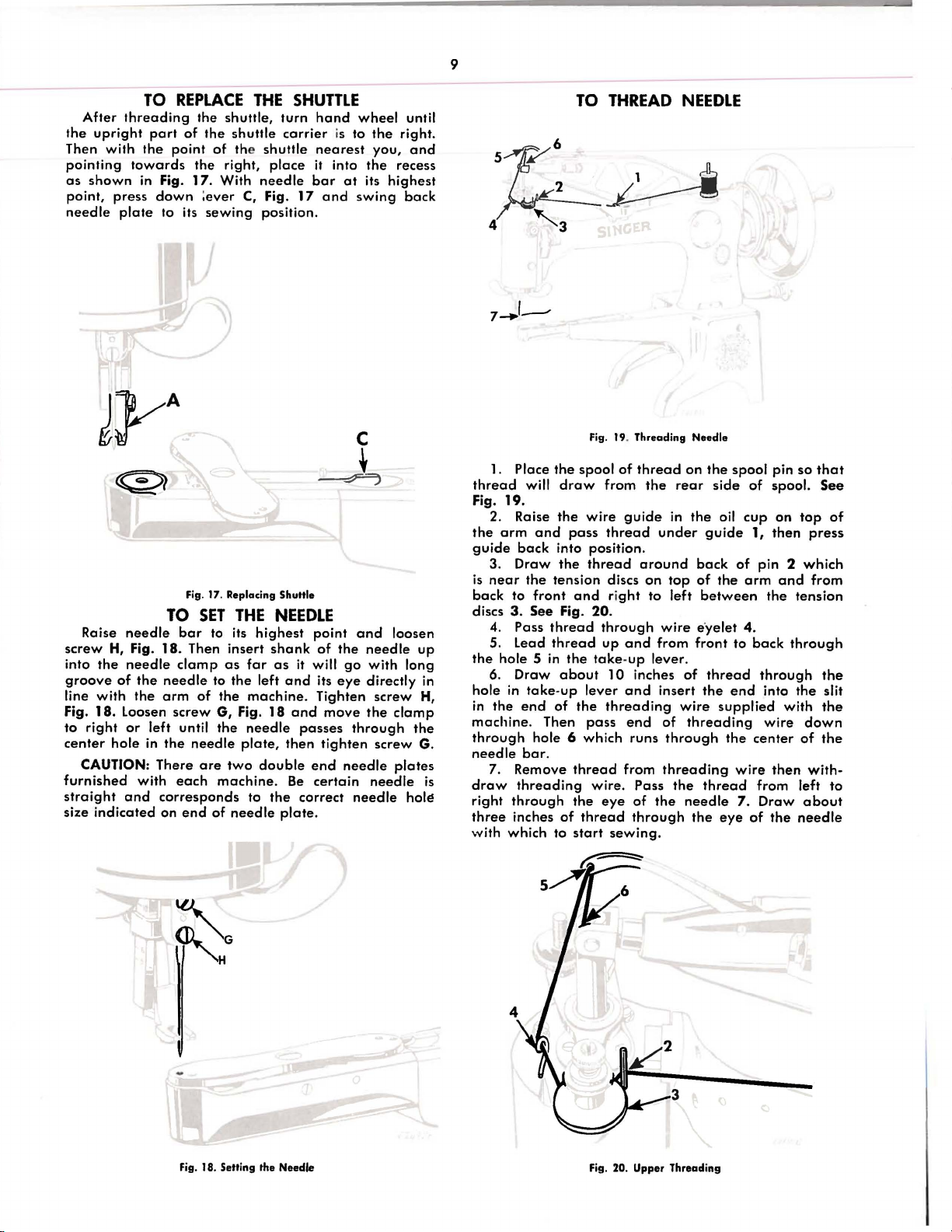
After
the
upright
with
Then
pointing
as
shown
point,
needle
TO
threading
part
the
towards
in Fig.
press
down :ever
plate
REPLACE
the shuttle, turn
of
the
point
of the
the right,
17.
With
to its
sewing
THE
shuttle
shuttle
needle
C,
Fig.
position.
SHUTTLE
carrier
place
bar
17
hand
is to
nearest
it
into
at
and
wheel
the
you,
the
its
swing
until
right.
and
recess
highest
back
9
TO
THREAD
NEEDLE
Raise
screw
H,
into
the
groove
line
with
18. loosen
Fig.
to
right
center
furnished
straight
size
hole
CAUTION:
indicated
needle
Fig.
needle
of
the
the
or
with
and
Fig. 17. Replacing Shuttle
TO
SET
bar
18.
needle
arm
left until
in
There
corresponds
on
to its
Then
clamp
to
of
screw
the
needle plate,
are
each
end
of
as
the
G, Fig.
the
two
machine.
THE
highest
insert
far
the
left
machine
needle
double
to
needle
_J,
NEEDLE
point
shank
18
the
as
and
and
then
Be
plate.
of
it will
its
. Tighten
passes
end
ce r
correct
c
and
the
go
eye
move
through
tighten
needle
tain
needle
loosen
needle
with
long
directly
screw
the
clamp
screw
plates
needle
holE!
up
in
H,
the
G.
is
1. Place
thread
Fig.
19.
2. Raise
the
arm
guide
back
Draw
3.
is
near
back
to
discs
3.
4. Pass
5.
lead
the
hole 5
Draw
6.
hole
in
in
the
end
machine
through
needle
draw
right
three
with
bar.
7. Remove
threading
through
inches
which
Fig. 19. Threading Needle
the
spool
will
draw
the
wire
and
pass
into position.
the
thread
the
tension
front
and right
See Fig.
take-up
. Then
hole 6 which
thread
thread
in
the
about
of
the
thread
the
of
to
start
20.
take-up
lever
pass
wire.
thread
of
thread
from
the
guide
thread
around
discs
on
through
up
and
10
inches
and
threading
end
runs
from
Pass
eye
of
through
sewing
on
rear
in
under
top
to
left
wire
from
lever.
of
insert
wire
of
threading
through
threading
the
the
needle
.
the
side
the
oil
guide
back
of
the
between
e'yelet
front
thread
the
supplied
the
thread
the
eye
spool
of
cup
1,
of
arm
4.
to
back
end
center
wire
from left
7.
of
pin
so
spool.
on
top
then
pin 2
and
the
tension
through
through
into
the
with
wire
of
then
Draw
the
needle
that
See
of
press
which
from
the
slit
the
down
the
with-
to
about
Fig
. 18. Setting the Needle
Fig
. 20. Upper Threading
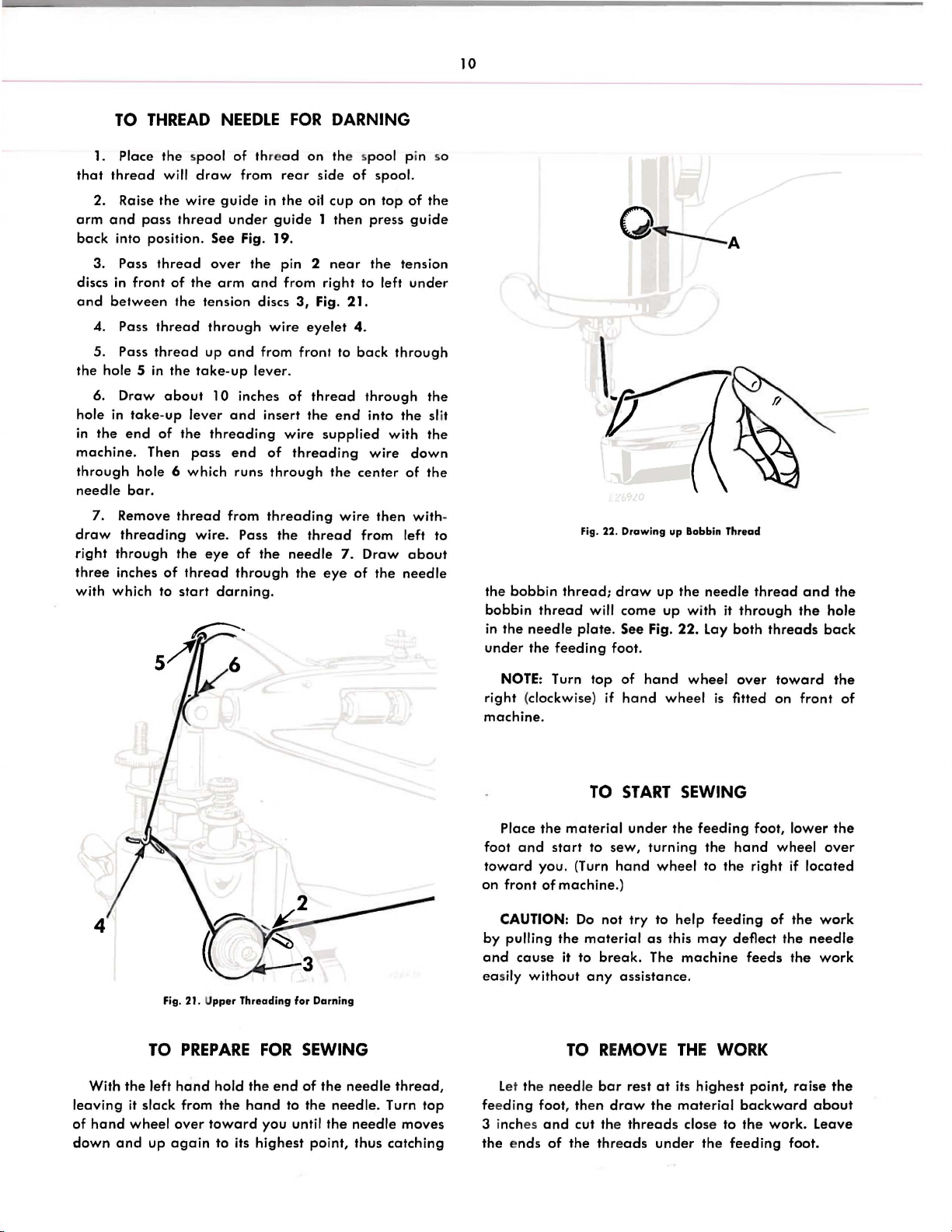
TO
THREAD
NEEDLE
FOR
10
DARNING
1. Place
that
thread
2. Raise
arm
and
back
into position.
3. Pass
discs in
and
between
4.
Pass
5. Pass
the
hole 5
Draw
6.
hole
in
in
the
end
machine.
through
needle
draw
right
three
with
bar.
7. Remove
threading
through
inches
which
the
will
the
pass
thread
front
of
thread
thread
in
the
about
take-up
of
Then
hole 6
of
to
spool
draw
wire
thread
the
the
tension
up
take-up
lever
the
pass
which
thread
wire.
the
eye
thread
start
of
thread
from
guide
under
See
Fig. 19.
over
the
arm
and
discs
through
and
lever.
10
inches
and
threading
end
runs
from
Pass
of
through
darning.
on
rear
side
in
the
oii
guide 1 then
pin 2
from
right
3,
Fig.
wire
eyelet
from
front
of
thread
insert
the
wire
supplied
of
threading
through
threading
the
thread
the
needle
the
eye
the
spool pin so
of
spool.
cup
on
press
near
the
to left
21.
4.
to
back
through
end
into
wire
the
center
wire
from
7.
Draw
of
the
top
through
with
then
of
the
guide
tension
under
the
the slit
the
down
of
the
with
left
to
about
needle
o~A
-
the
bobbin
bobbin
in
the
needle plate.
under
the
thread;
thread
feeding
Fig. 22.
will
Drawing
draw
come
See
foot.
up
up
Fig.
up
Bobbin
the
with
22.
Thread
needle
it
lay
both
thread
through
threads
and
the
the
hole
back
4
With
leaving
of
hand
down
the
it
slack from
wheel
and
Fig. 21.
TO
PREPARE
left
hand
over
up
again
Upper
hold
the
toward
to
its
Threading
FOR
the
end
hand
you
highest
for
Darning
SEWING
of
the
to
the
until
the
point,
needle
needle.
needle
thus
thread,
Turn
top
moves
catching
NOTE:
right
(clockwise) if
machine.
Place
foot
and
toward
on
front
CAUTION:
by
pulling
and
cause
easily
fee
3 inch
the
without
let the
ding
es
ends
Turn
the
material
start
you.
of
machine.)
the
it
TO
needle
foot,
and
of
the
top
TO
to
sew,
(Turn
Do
not
material
to
break.
any
REMOVE
bar
then
draw
cut
the
threads
of
hand
hand
wheel
START
under
the
turning
hand
wheel
try
to
as
this
The
assistance.
rest
at
the
threads
under
wheel
is
SEWING
feeding
the
to
the
help
feeding
may
machine
THE
WORK
its
highest
material
close
to
the
feeding
over
toward
fitted
on
foot,
hand
wheel
right
of
deflect
feeds
point,
backward
the
work.
front
lower
if
the
the
the
raise
foot.
the
of
the
over
located
work
needle
work
the
about
leave
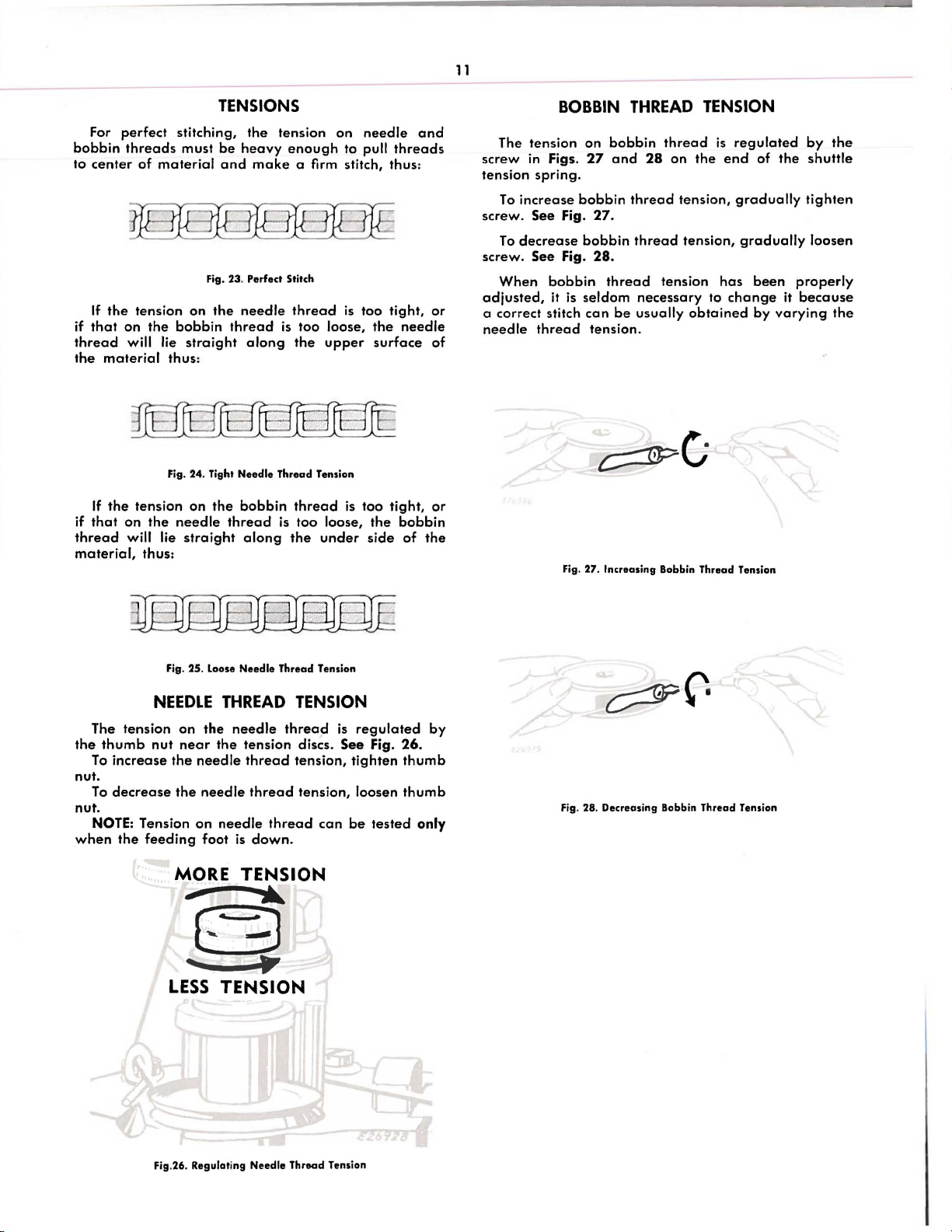
11
for
bobbin
to
center
If
the
if
that
thread
the
material
If
the
if
that
thread
material,
TENSIONS
perfect
threads
on
will lie
on
will lie
stitching,
must
of
material
tension
tension
thus:
on
the
bobbin
straight
thus
:
Fig. 24. Tight Needle Thread Tension
on
the
needle
straight
the
be
heavy
and
make
Fig
. 23. Perfect Stitch
the
needle
thread
along
the
bobbin
thread
along
tension
enough
is
is
on
a firm stitch,
thread
too
loose,
the
upper
thread
too
loose,
the
under
needle
to pull
is too tight,
is
thus
the
surface
too
tight,
the
side
threads
needle
bobbin
of
and
:
or
the
of
or
BOBBIN
The
tension
screw
in
Figs.
tension
screw.
screw
adjusted,
a correct stitch
needle
To
increase
To
decrease
. See Fig.
When
spring.
See
Fig.
bobbin
it
is
thread
Fig. 27. Increasing Bobbin Thread Tension
on
bobbin
27
and
bobbin
27.
bobbin
28.
thread
seldom
can
be
tension.
THREAD
thread
28
on
thread
tension,
thread
tension,
tension
necessary
usually
obtained
TENSION
is
regulated
the
end
gradually
gradually
has
to
change
of
been
by
varying
by
the
shuttle
tighten
properly
it
because
the
loosen
the
The
tension
the
thumb
To
increase
nut.
To
decrease
nut.
NOTE: Tension
when
the
feeding
Fig. 25. Loose Needle Thread Tension
NEEDLE
nut
the
on
near
the
THREAD
the
the
needle
needle
on
needle
foot is
needle
tension
thread
thread
down.
TENSION
thread
discs.
tension,
tension,
thread
can
is
regulated
See
Fig. 26.
tighten
loosen
be
tested
by
thumb
thumb
only
Fig
. 28. Decreasing Bobbin Thread Tension
Fig.26. Regulati
ng
Needle Thread Tension
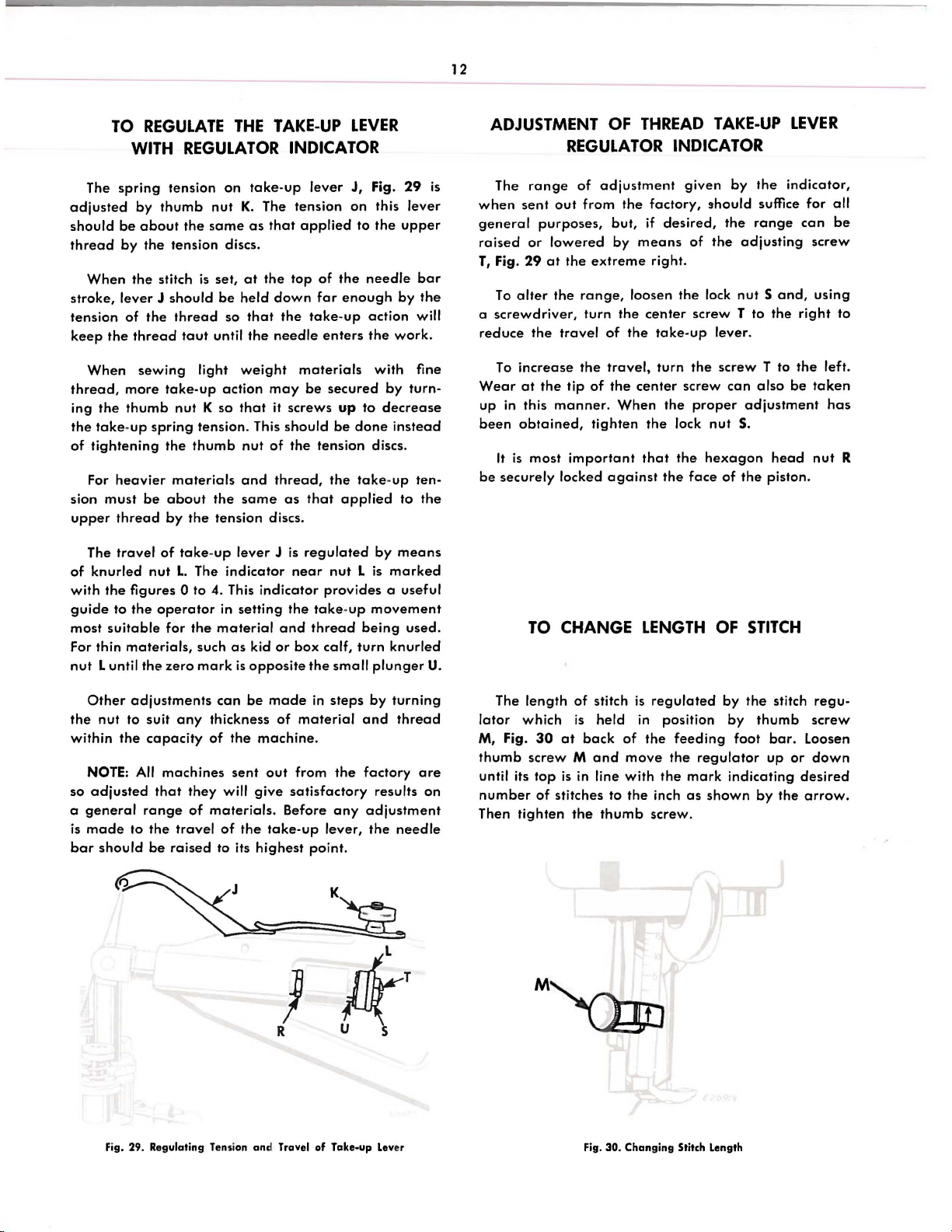
12
TO
The
adjusted
should
thread
When
stroke,
tension
keep
the
When
thread,
ing
the
the
take-up
of
tightening
For
heavier
sion
must
upper
The
of
knurled
with
the
guide
to
most
suitable
For thin
nut
L until
REGULATE
THE
TAKE-UP
WITH REGULATOR INDICATOR
spring
be
by
lever J should
thread
travel
by
about
the
the
tension
thumb
tension
stitch
the
nut
same
is
on
discs.
set,
be
of
the
thread
sewing
more
thumb
spring
thread
take-up
nut
the
taut
light
K so
tension.
thumb
so
until
action
materials
be
about
the
by
the
tension
of
take-up
nut
L.
The
indicator
figures 0 to 4. This
the
operator
for
materials,
the
zero
the
such
mark
in
material
as
take-up
K.
The
as
that
at
the
held
down
that
the
the
needle
weight
may
that
it
This
should
nut
of
and
thread,
same
as
discs.
lever J is
indicator
setting
and
kid
or
is
opposite
lever
tension
applied
top
of
the
far
enough
take-up
enters
materials
be
secured
screws
up
be
the
tension
the
that
applied
regulated
near
nut L is
provides a useful
the
take-up
thread
box
calf,
the
small
LEVER
J,
Fig.
on
this
to
the
needle
action
the
with
by
to
decrease
done
discs.
take-up
by
movement
being
turn
plunger
29
lever
upper
bar
by
the
will
work.
fine
turn-
instead
ten-
to
the
means
marked
used.
knurled
U.
ADJUSTMENT OF THREAD TAKE-UP
LEVER
REGULATOR INDICATOR
The
is
when
range
sent
general
raised
T,
a
or
Fig.
29
To
alter
screwdriver,
reduce
To
increase
Wear
at
up
in this
been
obtained,
It
is
most
be
securely
TO CHANGE LENGTH OF
of
out
purposes,
lowered
at
the
the
the
travel
the
tip
manner.
important
locked
adjustment
from
the
but,
by
extreme
range,
turn
the
of
the
travel,
of
the
When
tighten
against
factory,
if
means
right.
loosen
center
the
center
the
that
given
desired,
of
the
screw
take-up
turn
the
screw
the
proper
lock
the
the
face
by
the
!thould suffice
the
range
the
adjusting
lock
nut S and,
T to
the
lever.
screw
T to
can
also
adjustment
nut
S.
hexagon
of
the
head
piston.
STITCH
indicator,
for
all
can
be
screw
using
right
to
the
left.
be
taken
has
nut
R
Other
adjustments
the
nut
to
suit
within
so
a
is
bar
the
capacity
NOTE:
general
made
All
machines
adjusted
that
range
to
the
should
be
Fig. 29. Regulating Tensian
any
they
of
travel
raised
can
be
thickness
of
the
machine.
sent
will
give
materials.
of
the
to its
highest
and
made
in
steps
of
material
out
from
the
satisfactory
Before
take-up
any
lever,
point.
Travel of Take-up
by
turning
and
thread
factory
are
results
adjustment
the
needle
Lev
er
on
The
lator
M,
Fig.
thumb
until its
number
Then
length
which
30
at
of
is
back
screw M and
top
is
in line
of
stitches
tighten
the
Fig.
stitch
held
to
thumb
30.
is
regulated
in position
of
the
feeding
move
the
with
the
the
inch
screw.
Changing
by
by
regulator
mark
indicating
as
shown
Stitch Length
the
foot
stitch
thumb
bar.
up
by
the
regu-
screw
Loosen
or
down
desired
arrow.
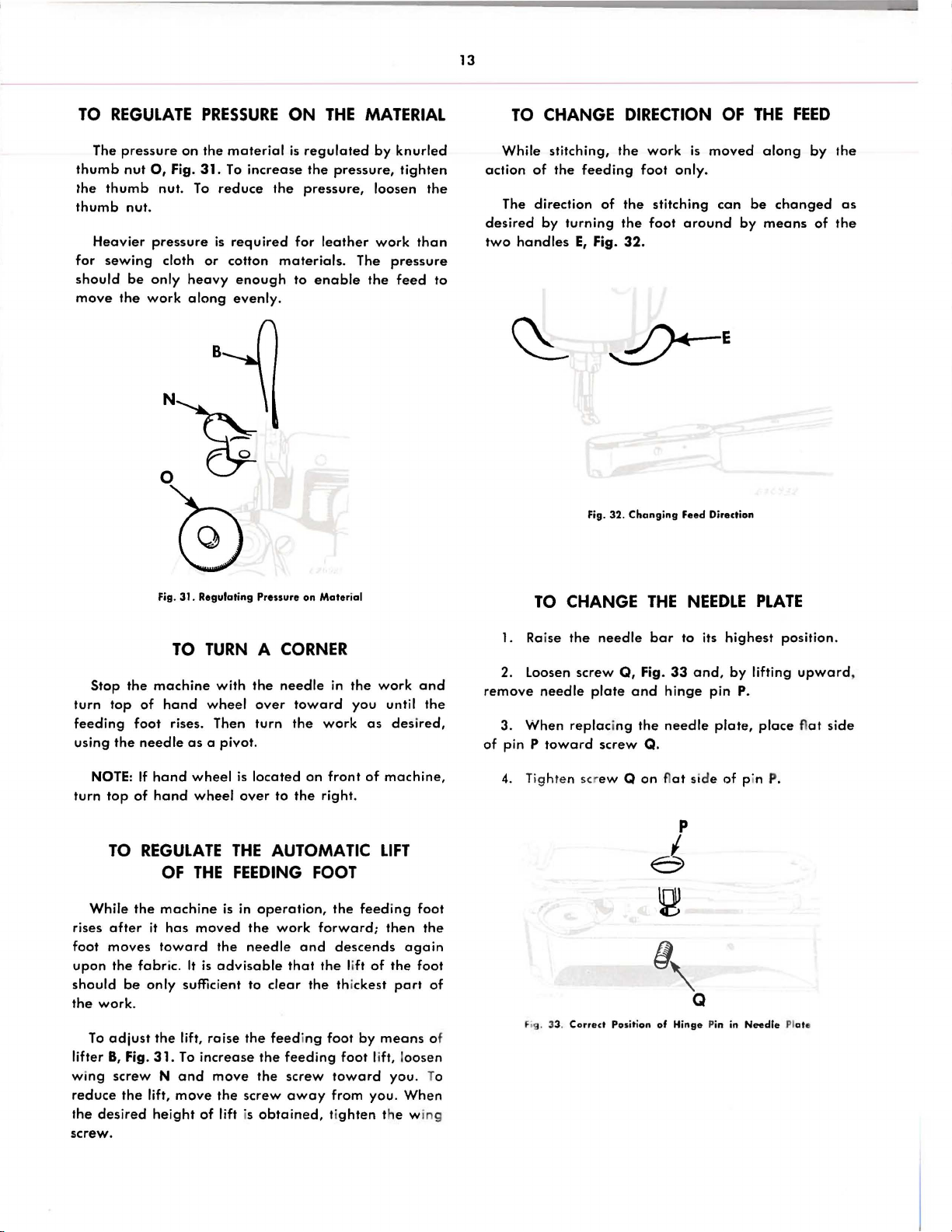
TO
REGULATE
The
thumb
lhe
thumb
thumb
Heavier
for
sewing
should
move
pressure
nut
0,
nut.
nut.
pressure
be
only
the
work
on
Fig.
To
cloth
heavy
along
PRESSURE
the
material
31.
To
increase
reduce
is
required
or
cotton
enough
evenly
ON
is
regulated
the
the
pressure,
for
leather
materials.
to
enable
.
THE
pressure,
The
MATERIAL
by
knurled
tighten
loosen
work
the
the
than
pressure
feed
to
13
TO CHANGE DIRECTION OF
While
action
The
desired
two
stitching,
of
the
direction
by
handles
feeding
of
turning
E,
Fig. 32.
the
the
the
work
foot
only.
stitching
foot
around
~E
is
moved
can
by
THE
along
be
means
FEED
by
changed
of
the
as
the
Stop
turn
feeding
using
NOTE:
turn
While
rises
foot
upon
should
the
work.
To
lifter
wing
reduce
the
desired
screw.
Fig.
31.
TO TURN A CORNER
the
machine
top
of
hand
foot
rises.
the
needle
If
hand
top
of
hand
TO
REGULATE
OF
the
machine
after
it
has
moves
the
adjust
8,
screw N and
fabric.
be
Fig.
the
toward
only
the
31.
lift,
height
lift,
To
move
sufficient to
Regulating
with
the
wheel
as a pivot.
wheel
wheel
Then
is
over
turn
located
over
THE
THE
FEEDING FOOT
is
in
moved
It
increase
of
the
is
advisable
raise
move
the
lift is
the
needle
the
screw
Pressure
on
Material
needle
to
toward
the
work
on
the
right.
in
the
front
you
AUTOMATIC
operation,
work
clear
feeding
the
feeding
the
screw
away
obtained, tighten
and
that
the
forward;
descends
the
the
th i
foot
foot
toward
from
feeding
lift
ckest
by
work
until
as
desired,
of
machine,
LIFT
then
of
the
part
means
lift, l
you
you.
the wing
and
the
foot
the
again
foot
of
of
oosen
. To
When
TO
1. Rai
se
2.
loosen
remove
of
needle
3.
When
pin P toward
4. Tighten
fig. 33. Correct Position
Fig. 32.
Changing
CHANGE
the
needle
screw
Q,
plate
replacing
screw
sc
ew Q on flat
THE
bar
Fig. 33
and
the
Q.
of
Feed Direction
NEEDLE
to its
and,
hinge
pin
needle
side
Hinge Pin in
highest
by
P.
plate,
of
PLATE
position.
lifting
place flat
pin P.
Needle Plat
upward
side
e
,

14
Oil
the
machine
The
top
of
If
located
Never
Do
The
See
Machine Working Heavily
To
The
run
not
run
foot
.
Belt
that
the
end,
shorten
If
the
machine
the
machine
Avoid Breaking Needles
feeding
material
See
page 5.
hand
the
the
belt
fool
regularly.
wheel
at
side
machine
machine
is
not
the
runs
hard
rapidly,
should
with
too fine a
of
too
belt
must
always
machine,
without
when
both
tight; it
and
rejoin.
after
standing
then
wipe
be
securely
needle. A large
HINTS
turn
the
material
shuttle
should
idle
clean
fastened
over
hand
between
and
be
for
and
FOR
wheel
needle
just
some
needle
PERFECT
toward
tight
oil.
by
the
must
turn
the
feeding
are
enough
time, use a little
the
thumb
and
thread
OPERATION
operator (counterclockwise)
over
fool
threaded
not to slip.
screw.
to
from left
and
unless
kerosene
Do
correspond
needle
there
If
too
or
not
toward
plate.
is
loose,
benzine
sew
should
.
right
material
remove
in
heavy
be
(clockwise).
under
the
the
oiling
seams
used
on
the
hook
places,
or
very
heavy
feeding
at
one
run
thick
work.
Avoid
Breaking of Upper Thread
Breaking of Under Thread
The
CAUTION:
Examine
pulling
Improper
Tension
thread
The
The
needle
Improper
Bobbin
Skipping of
needle
Remove
bar
the
by
feeding
the
material
threading
being
too
tight.
being
too
being
bent,
threading
Thread
Stitches
may
accumulation
working a piece
Do
not
not
bend
foot
tension
be
accurately
and
when
of
machine.
coarse
having a blunt
of
shuttle.
being
of
dirt
of
tape
spring
away
remove
stitching. This
for
the
size
point,
too tight.
set
into
the
or
lint
which
or
thread
from
needle
any
dirt
may
of
the
needle
might
back
or
lint
cause
needle.
or
bar
gather
and
bar
from
being
or
or
spring
the
set
the
behind
forth
the tee
needle
incorrectly.
needle
between
thread
may
th
to
may
become
to
insure
strike
be
retaining
spring
regular
on
the
needle
blunt
or
bent.
spring near
and
needle
permanently
feeding
plate
bottom
bar.
damaged.
of
material.
and
break
of
.
needle
Working
When
on
old, hard leather
working
a
long stitch to
on
old,
hard
prevent
leather,
needle
it
is
advisable
from splitting
to soft
the
en the le
leath
er.
ather
with
oil, use a
coar
se
needle
and
mak
e