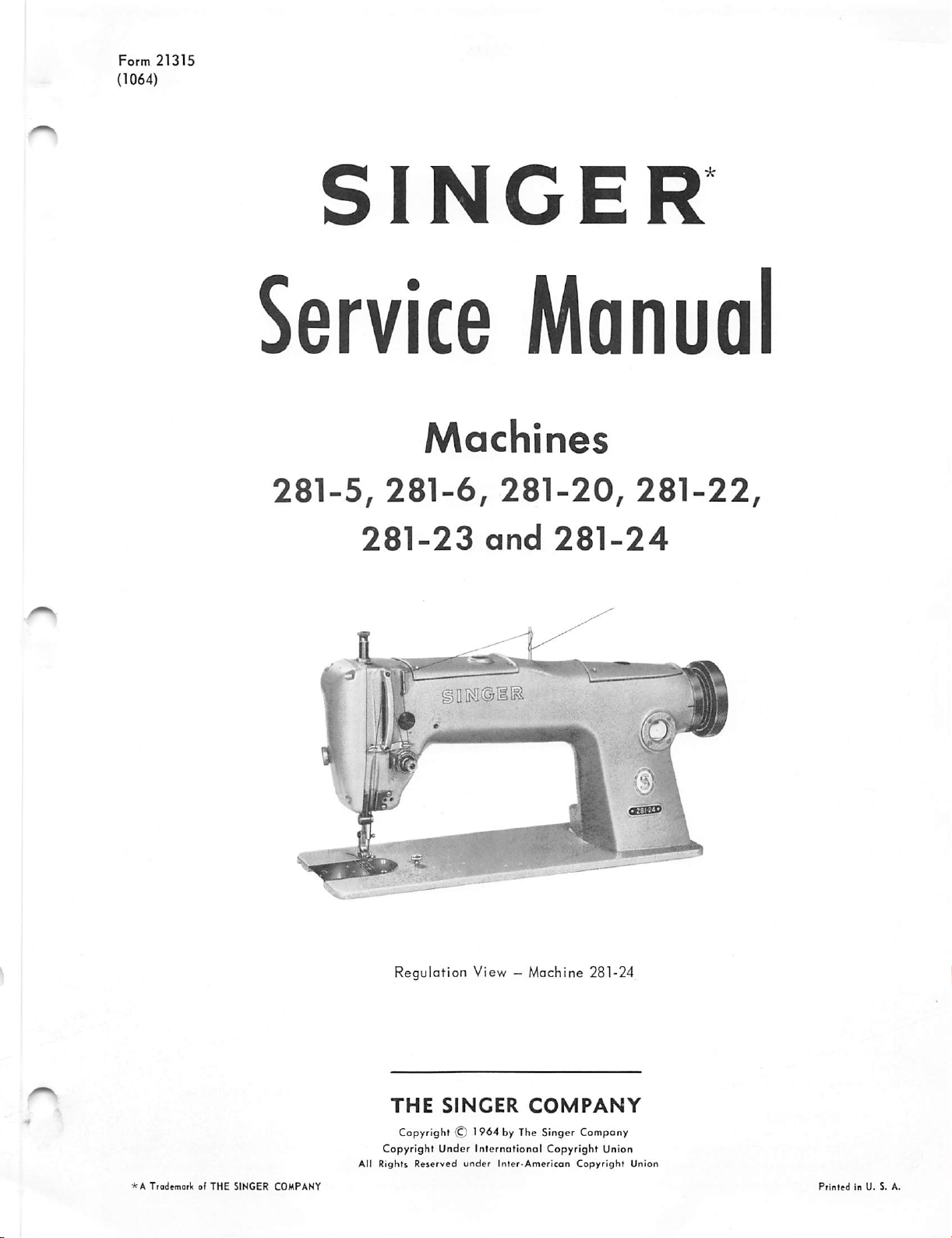
Form
(1064)
21315
SINGER
Service
Machines
281-5,
281-6,
281-23
and
Manual
281-20,
281-24
281-22,
Regulation View - Machine 281-24
*A
Trademarko(THE
SINGER
THE
Copyright Under International Copyright Union
All Rights
COMPANY
SINGER
Copyright ® hy The Singer
Reserved
under
COMPANY
Inter-American
Compony
Copyright
Union
Printed
In U. S. A.
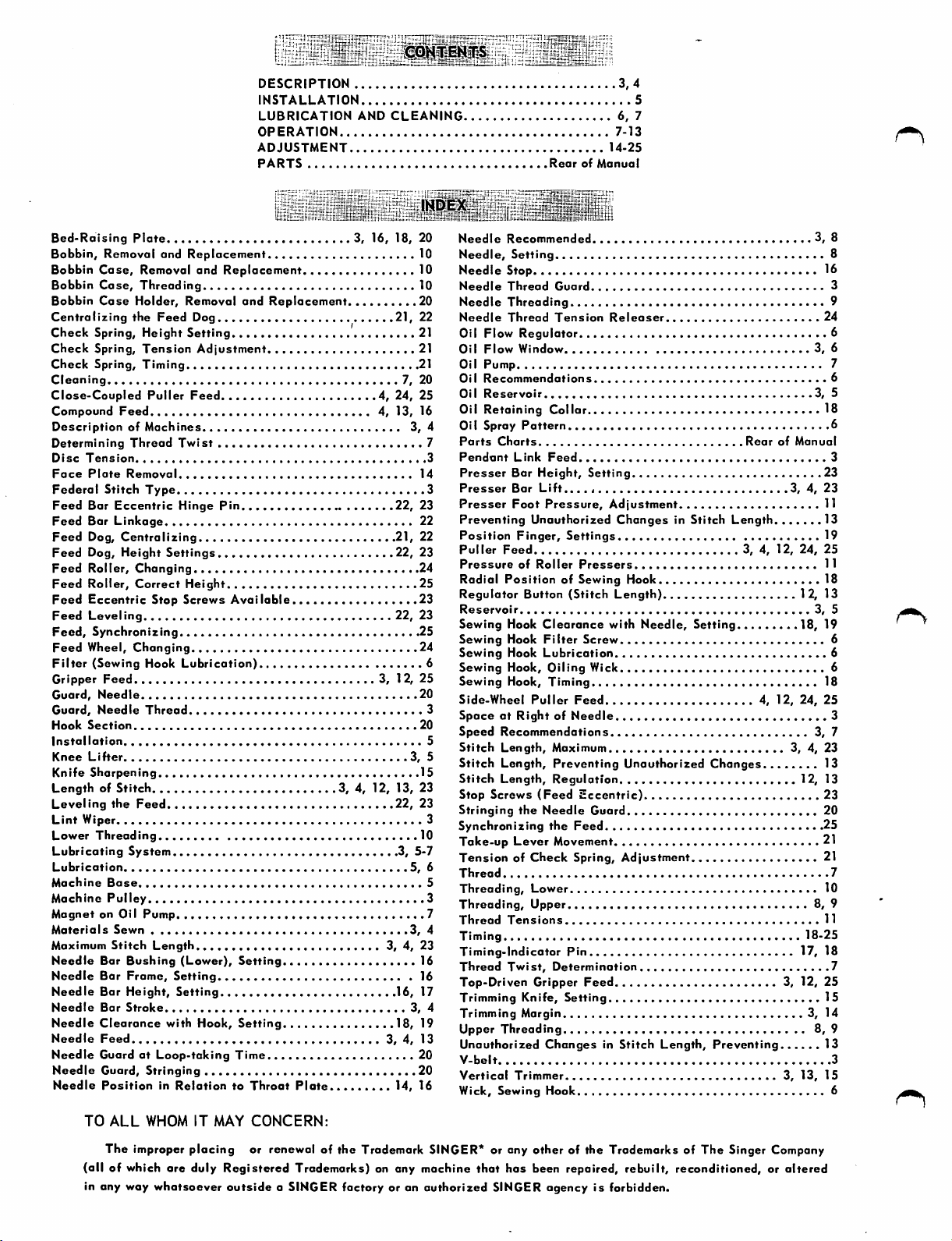
DESCRIPTION
INSTALLATION
LUBRICATION
OPERATION
ADJUSTMENT
PARTS
is
AND
CLEANING
3,4
6,
7-13
14-25
RearofManual
5
7
Bed-Raising
Bobbin,
Bobbin
Bobbin
Bobbin
Centralizing
Check
Check
Check
Cleaning
Close-Coupled
Compound
Description
Determining
Disc
Tension
Face
Federal
Feed
Feed
Feed
Feed
Feed
Feed
Feed
Feed
Feed,
Feed
Filter
Gripper
Guard,
Guard,
Hook
Installation
Knee
Knife
LengthofStitch
Leveling
Lint
Wiper 3
Lower
Lubricating
Lubrication
Machine
Machine
Magnet
Materials
Maximum
Needle
Needle
Needle
Needle
Needle
Needle
Needle
Needle
Needle
Plate
Removal and
Case,
Removal
Cose,
Threading
Case
Holder,
the
Spring,
Spring,
Height
Tension
Replacement
and
Replacement
Removal
Feed
Dog 21, 22
and
Replacement
Setting
Adjustment
3, 16, 18, 20
Spring, Timing 21
Puller
Feed
of
Thread
Plate
Removal
Stitch
Bar
Eccentric
Bar
Linkage
Dog,
Centralizing
Dog,
Height
Roller,
Roller,
Eccentric
Machines
Twist
Type
Hinge
Settings
Changing
Correct
Stop
Feed
Height
Screws
Pin
Available
....4,
Leveling
Synchronizing
Wheel,
Changing
(Sewing
Hook
Lubrication)
Feed
Needle
Needle
Section
Lifter
Sharpening
Thread
3, 4, 12, 13, 23
the
Feed
Threading
System
Base
Pulley
on Oil
Pump
Sewn
Stitch
Bar
Bar
Bar
Bar
Clearance
Feed
GuardatLoop-taking
Guard,
PositioninRelationtoThroat
Length
Bushing
Frame,
Height,
Stroke
Stringing
(Lower),
Setting
Setting
with
Hook,
Setting
Setting
Time
Plate
10
10
10
20
21
21
7, 20
24,
25
4, 13, 16
3, 4
14
22,
23
22
21,
22
22,
23
24
25
23
22, 23
25
24
3, 12, 25
20
20
3, 5
22, 23
10
3,
5-7
5, 6
3,
3, 4, 23
16
16, 17
3, 4
18, 19
3, 4, 13
20
20
14, 16
Needle
Needle,
Needle
Needle
Needle
Needle
Oil Flow
Oil
Recommended
Setting
Stop 16
Thread
Guard
Threading
Thread
Tension
Releaser
Regulator
Flow
Window
Oil Pump 7
Oil
Recommendations
Oil
Reservoir
Oil Retaining Collar 18
Oil Spray
Parts
7
Pendant
3
Presser
Presser
3
Presser
Preventing
Position
Puller
Pressure
Radial
Regulator
Reservoir
Sewing
Sewing
Sewing
6
Sewing
Sewing
Side-Wheel
3
SpaceatRightofNeedle
Speed
5
Stitch
Stitch
15
Stitch
Stop
Stringing
Synchronizing the
Take-up Lever
Tension
Thread
5
Threading,
3
Threading,
7
Thread
4
Timing 18-25
Timing-Indicator
16
Thread
Top-Driven
Trimming Knife,
Pattern
Charts
Link
Feed
Bar
Height,
Bar
Lift....
Foot
Pressure,
Unauthorized
Finger,
Feed
of
Settings
Roller
PositionofSewing
Button
(Stitch
Hook
Clearance
Hook
Filter
Hook
Lubrication
Hook,
Oiling
Hook,
Timing
Puller
Feed
Recommendations
Length,
Length,
Length,
Screws
Maximum 3, 4, 23
Preventing
Regulation
(Feed
the
Needle
Setting
Adjustment
ChangesinStitch
Pressers
Hook 18
Length)
with
Needle,
Setting
Screw
Wick 6
Unauthorized
Eccentric)
Guard 20
RearofManual
Length
3, 4,
Changes
Feed
Movement
of Check Spring, Adjustment 31
Lower 10
Upper 8, 9
Tensions
Pin
Twist,
Determination
Gripper
Feed
Setting
Trimming Margin 3, 14
Upper
Threading
Unauthorized
V-belt
Vertical
Wick,
Sewing
ChangesinStitch
Trimmer
Hook
Length,
Preventing
12,
4, 12,
3, 8
24
3,
3, 5
23
3, 4,
23
11
13
19
24,
25
11
12, 13
3,
18, 19
18
24,
25
3, 7
13
12, 13
23
35
31
11
17, 18
3, 12, 25
15
8, 9
13
3,
13,
15
8
3
9
6
6
6
6
3
5
6
6
3
7
7
3
6
TO
ALL
The improper
(all
of which
in any way
WHOM IT MAY
placing
ore
duly
whatsoever
CONCERN:
or renewal of the Trademark SINGER* or any other of the Trademarks of The Singer Company
Registered
outside
Trademarks)
a SINGER
factory
on any
or on
machine
authorized
that
SINGER
has
been
repaired,
agencyisforbidden.
rebuilt,
reconditioned,oraltered
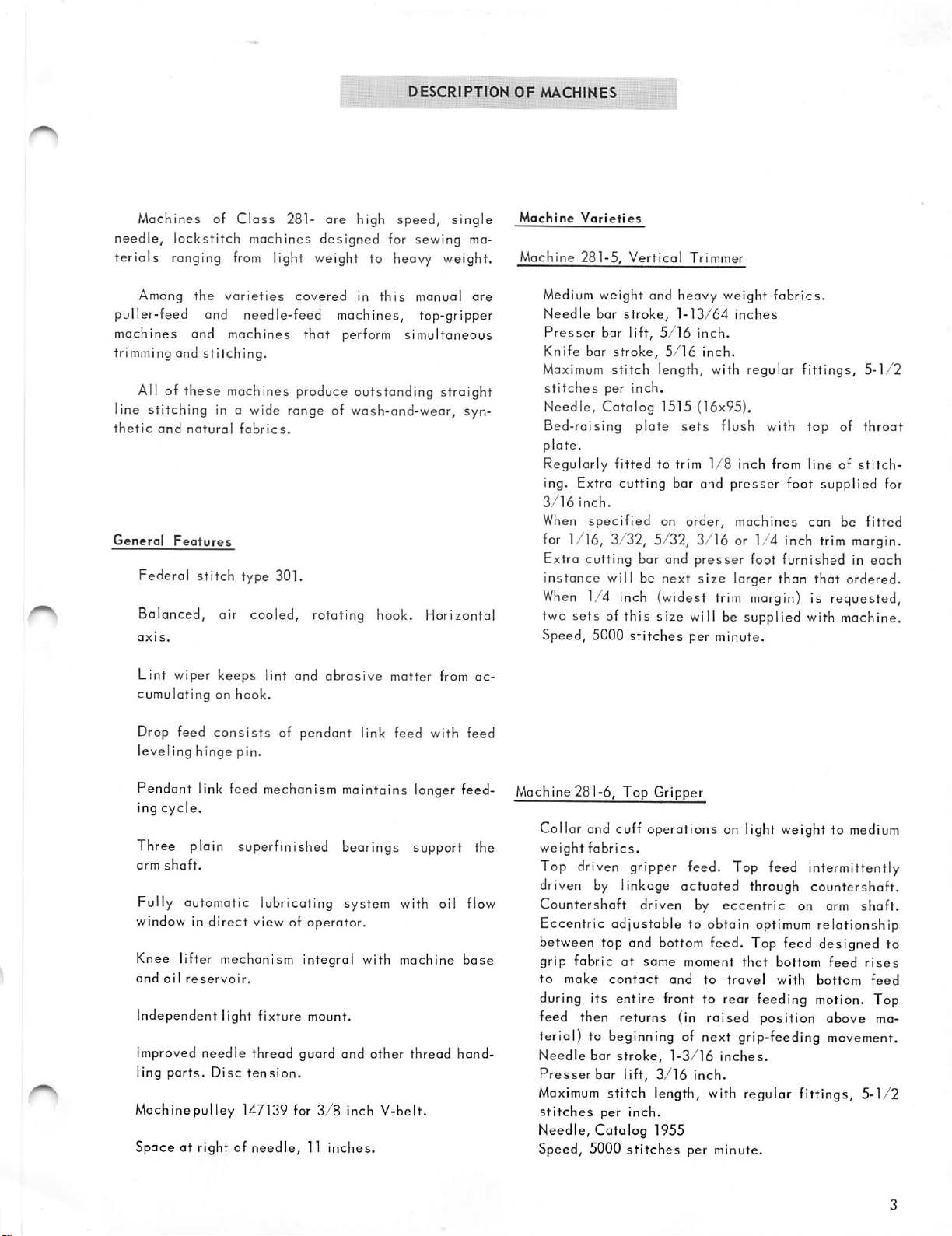
DESCRIPTION
OF
MACHINES
Machines of
Class
281- are high
speed,
single
needle, lockstitch machines designed for sewing ma
terials ranging
Among
the
from
varieties
light weight to heavy weight.
covered
in
this
manual
are
puller-feed and needle-feed machines, top-gripper
machines and machines that perform simultaneous
trimming and
stitching.
All of these machines produce outstanding straight
line stitching in a wide range of wash-and-wear, syn
thetic
and
natural
Generol
Features
Federal stitch type 301.
Balanced, air cooled, rotating hook. Horizontal
fabrics.
Machine
Machine
Varieties
281-5,
Vertical
Trimmer
Medium weight and heavy weight
Needle
Presser
Knife bar
Maximum
stitches
Needle,
Bed-raising
plate.
bar
stroke,
bar lift,
stroke,
stitch
per
Catalog
1-13/64
5/16
inch.
5/16
inch.
length, with regular
inch.
1515 {16x95).
plate
sets
Regularly fitted to trim
ing. Extra cutting bar and
3/16
inch.
When
specified
for
1/16, 3/32, 5/32, 3/16 or 1/4 inch
Extra cutting bar and
instance
When
two
will be next
1/4 inch (widest trim
setsofthis
Speed, 5000
on order,
size
stitches
presser
size
will be supplied with machine.
per minute.
fabrics.
inches
flush
with
1/8
inch from line of
presser
machines
foot furnished in
larger than
margin)
fittings,
top
of
5-1/2
throat
stitch
foot supplied for
can be
trim
fitted
margin.
each
that
ordered.
is requested,
Lint
wiper
keeps
lint and
abrasive
matter from ac
cumulating on hook.
Drop feed
consists
of pendant link feed with feed
leveling hinge pin.
Pendant link feed mechanism maintains longer feed
ing
cycle.
Three plain superfinished bearings support the
arm
shaft.
Fully automatic lubricating system with oil flow
window in
direct
view of
operator.
Knee lifter mechanism integral with machine base
and
oil
reservoir.
Independent light fixture mount.
Improved
ling
Machinepulley 147139 for
Space
needle
ports.
at right of
thread
Disc
tension.
needle,11inches.
guard
3/8
and
other
inch V-belt.
thread
hand
Mochine 281-6, Top Gripper
Collar and cuff operations on light weight to
weight
fabrics.
Top driven gripper feed. Top feed intermittently
driven by linkage actuated through countershaft.
Countershaft driven by eccentric on arm shaft.
Eccentric
adjustable
to obtain optimum
relationship
between top and bottom feed. Top feed designed to
grip fabricatsame
to
moke
contact
during
its entire
feed then returns (in
moment
and
to
front
to rear feeding
raised
that
travel
bottom feed
with
position
bottom
motion.
above ma
terial) to beginning of next grip-feeding movement.
Needle
Presser
Maximum
stitches
Needle,
Speed, 5000
bar
stroke,
bar lift,
1-3/16
3/16
inches.
inch.
stitch length, with regular fittings,
per
inch.
Catalog
1955
stitches
per minute.
medium
rises
feed
Top
5-1/2
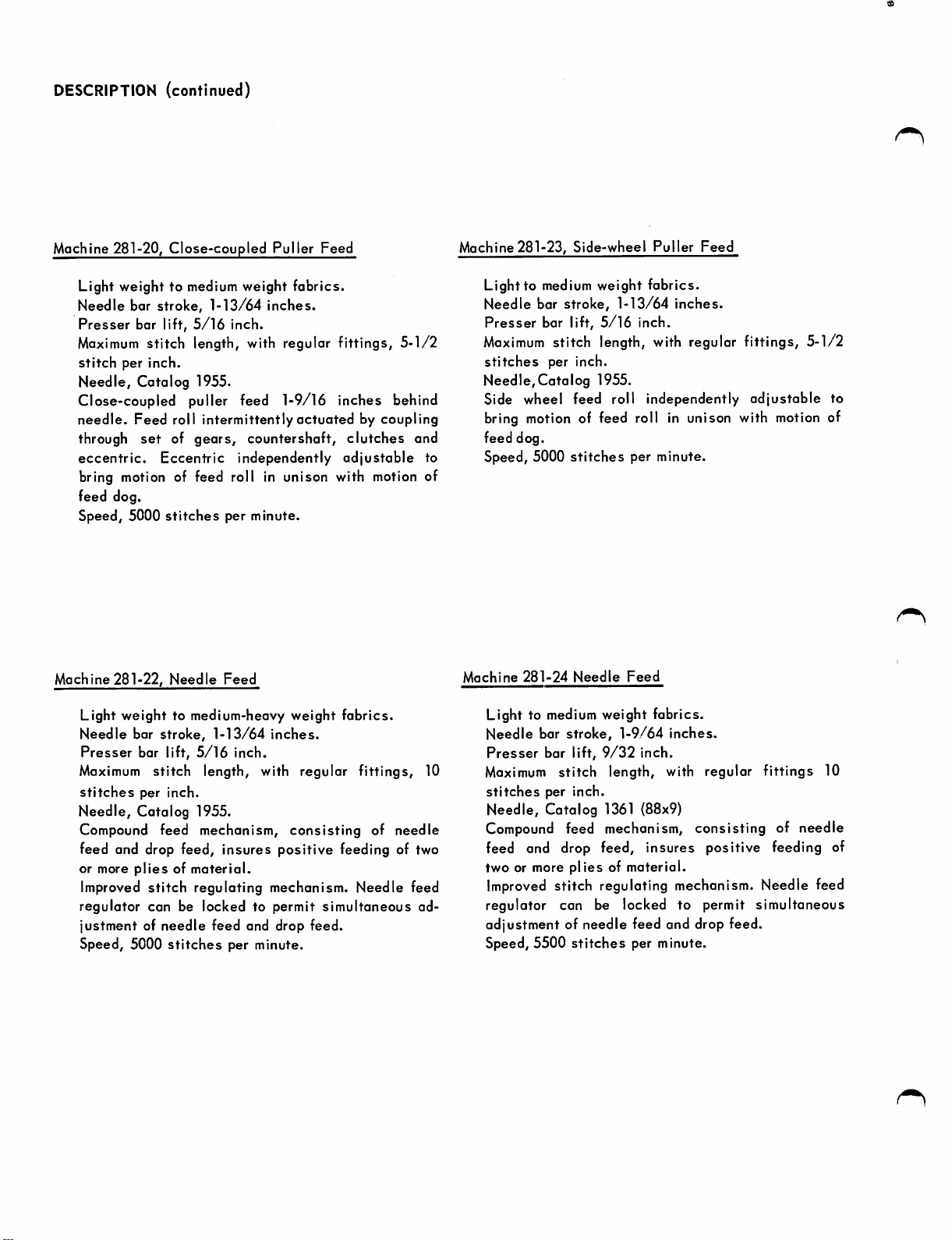
DESCRIPTION
(continued)
Machine 281-20,
Close-coupled
Puller
Feed
Light weight to medium weight fabrics.
Needle bar stroke, 1-13/64 inches.
Presser
Maximum
stitch
Needle, Catalog 1955.
bar lift,
5/16
inch.
stitch length, with regular fittings, 5-1/2
per
inch.
Close-coupled puller feed 1-9/16 inches behind
needle.
through
eccentric.
Feed roll intermittently actuated by coupling
set
of gears, countershaft, clutches and
Eccentric independently
adjustable
bring motion of feed roll in unison with motion of
feed dog.
Speed, 5000
Machine281-22,
stitches
Needle
per minute.
Feed
Machine 281-23,
Light to medium weight fabrics.
Needle bar stroke, 1-13/64 inches.
Presser
Maximum
stitches
Needle,Catalog 1955.
Side wheel feed roll independently
bring
feed dog.
to
Speed, 5000
Machine
Side-wheel
bar lift,
5/16
Puller
inch.
Feed
stitch length, with regular fittings, 5-1/2
per inch.
adjustable
motion
281-24
of feed roll in unison with
stitches
Needle
per minute.
Feed
motion
to
of
Light weight to medium-heavy weight
Needle bar stroke,
Presser
Maximum
stitches
bar lift,
stitch
per inch.
1-13/64
5/16
length, with regular
inches.
inch.
Needle, Catalog 1955.
Compound feed mechanism,
feed and drop feed, insures
or more
Improved
regulator
justmentofneedle
Speed, 5000
pliesofmaterial.
stitch
regulating mechanism. Needle feed
con be locked to permit
feed
stitches
per minute.
consisting
positive
and drop
feed.
fabrics.
fittings,
of
needle
feeding of two
simultaneous
ad
10
Light to medium weight fabrics.
Needle
Presser
Maximum
stitches
bar
stroke,
bar lift,
1-9/64
9/32
inches.
inch.
stitch length, with regular fittings 10
per inch.
Needle, Catalog 1361 (88x9)
Compound feed mechanism, consisting of needle
feed and drop feed, insures positive feeding of
two or more
pliesofmaterial.
Improved stitch regulating mechanism. Needle feed
regulator con be locked to permit simultaneous
adjustment of needle feed and drop feed.
Speed, 5500
stitches
per minute.
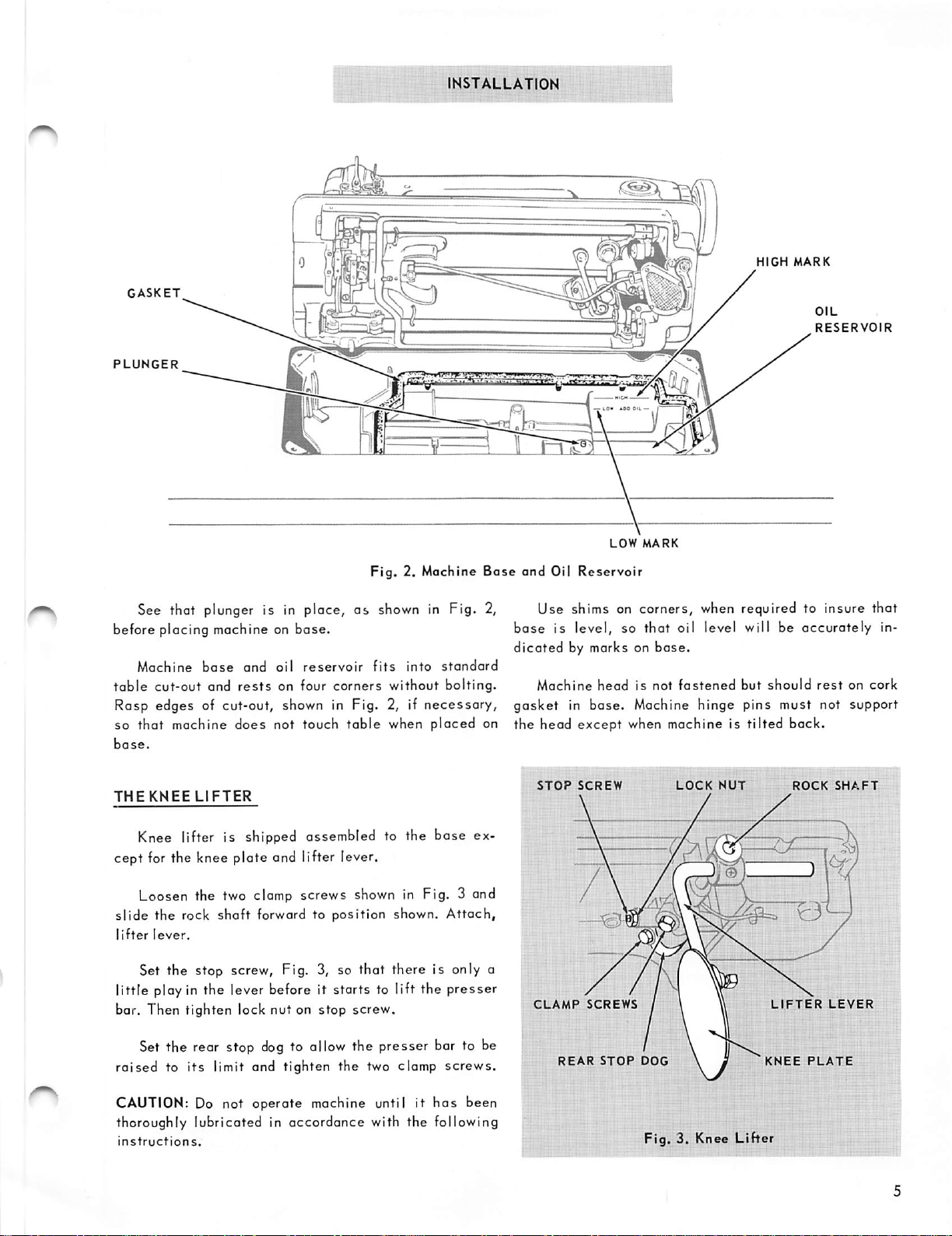
GASKET
PLUNGER
Fig.
2. Machine
Base
and Oil Reservoir
LOW
MARK
HIGH
MARK
OIL
RESERVOIR
See that plunger is in place, as
before placing
Machine
table
cut-out and
machine
base
on base. base is level, so that oil level will be accurately in
and
oil
reservoir
rests
on four corners without bolting. Machine head is not
shown
fits
in Fig. 2, Use shims on corners,
into
dicated
standard
by marks on
Rasp edges of cut-out, shown in Fig. 2, if necessary, gasket in base.
so
that
machine
base.
THEKNEE
LIFTER
does
not touch
table
when
placed
on the head
STOP
except
SCREW
Knee lifter is shipped assembled to the base ex
cept for the knee plate and lifter lever.
Loosen the two clamp screws shown in Fig. 3 and
slide
the rock shaft forward to position shown.
lifter
lever.
Attach,
Set the stop screw, Fig. 3, so that there is only a
little play in the lever before it starts to lift the
bar. Then
tighten
lock
nutonstop
screw.
presser
CLAMP
SCREWS
Set the rear stop dog to allow the presser bar to be
REAR
raised
to
its
limit and
tighten
the
two clamp
screws.
STOP
when
base.
fastened
Machine
when machine is
DOG
hinge pins must not support
LOCK
NUT
required to insure that
but should
tilted
KNEE
back,
ROCK
LIFTER
rest
SHAFT
LEVER
PLATE
on cork
I
CAUTION: Do not
thoroughly lubricated in
instructions.
operate
accordance
machine until it
with the following
has
been
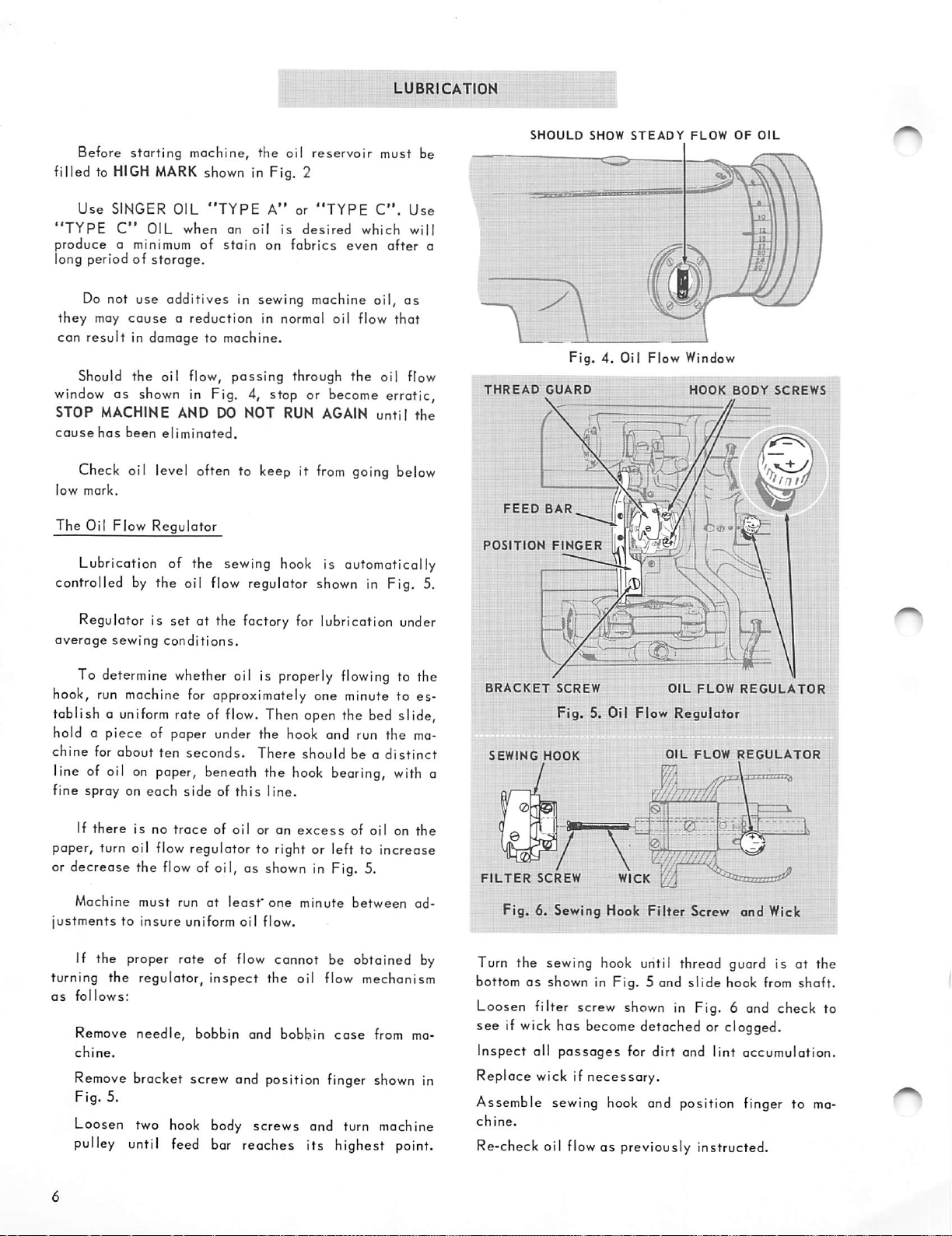
LUBRICATION
Before
filled to
Use
"TYPE
produce a minimum
starting
HIGH
SINGER
C"
machine,
MARK
shown in Fig. 2
OIL
OIL when an oil is
of
"TYPE
stain
the
A"
on
oil
reservoir
or
desired
fabrics
"TYPE
even
must be
C".
Use
which will
after
long period of storage.
Do not use
they
may
can
result
Should
window
as
STOP MACHINE AND DO NOT RUN AGAIN
cause
has
Check oil level often to keep it
low
mark.
The Oil Flow Regulator
additives
in sewing machine oil,
causeareduction
in damage to machine.
the
shown
been
oil flow,
eliminated.
passing
in Fig. 4, stop or
in normal oil flow
through
the
become
from
going below
as
that
oil flow
erratic,
until
the
Lubrication of the sewing hook is automatically
controlled by the oil flow regulator shown in Fig. 5.
SHOULD
SHOW
STEADY
FLOW
OF
OIL
a
Fig.
4. Oil Flow Window
THREAD
POSIT,OH
FEED
GUARD
BAR
HOOK
BODY
SCREWS
Regulator is set at the factory for lubrication under
average
hook,
tablish a
hold 0
chine for about ten
Iine of oil on paper, beneath the
fine spray on
paper, turn oil
or decrease the
justmentstoinsure
sewing
conditions.
To determine whether oil is properly
run
machine for approximately one minute to es
uniform
piece
rate of
flow.
Then open the bed slide,
of paper under the hook and run the ma
seconds.
There should be a
hook
each
If
there
Machine
is no
must
sideofthis
trace
of oil or an
flow
regulator to right or left to increase
flow
of oil, as shown in Fig. 5.
run
at
uniform oil flow.
least'
line.
one
excess
minute
flowing
to the
distinct
bearing, with a
of oil on
between
the
ad
If the proper rote of flow cannot be obtained by
turning the regulator, inspect the oil flow mechanism
as
follows:
Remove
chine.
Remove
Fig.
Loosen two
needle,
bobbin and bobbin
bracket screw and position finger
5.
hook
body screws and turn machine
case
from ma
shown
pulley until feed bar reaches its highest point.
in
BRACKET
SEWING
FILTER
Fig. 6. Sewing Hook
SCREW
Fig.
HOOK
SCREW
5. Oil Flow
a
WICK
Filter
OIL
FLOW
Regulator
OIL
FLOW
REGULATOR
U-
Screw and Wick
REGULATOR
Turn the sewing hook until thread guard is at the
from
bottom as shown in Fig. 5 and slide hook
shaft.
Loosen filter screw shown in Fig. 6 and check to
see if wick has becomedetached or clogged.
Inspect all
passages
for dirt and lint accumulation.
Reploce wick if necessary.
Assemble sewing
chine.
hook
and position finger to
ma
Re-check oil flowaspreviously instructed.
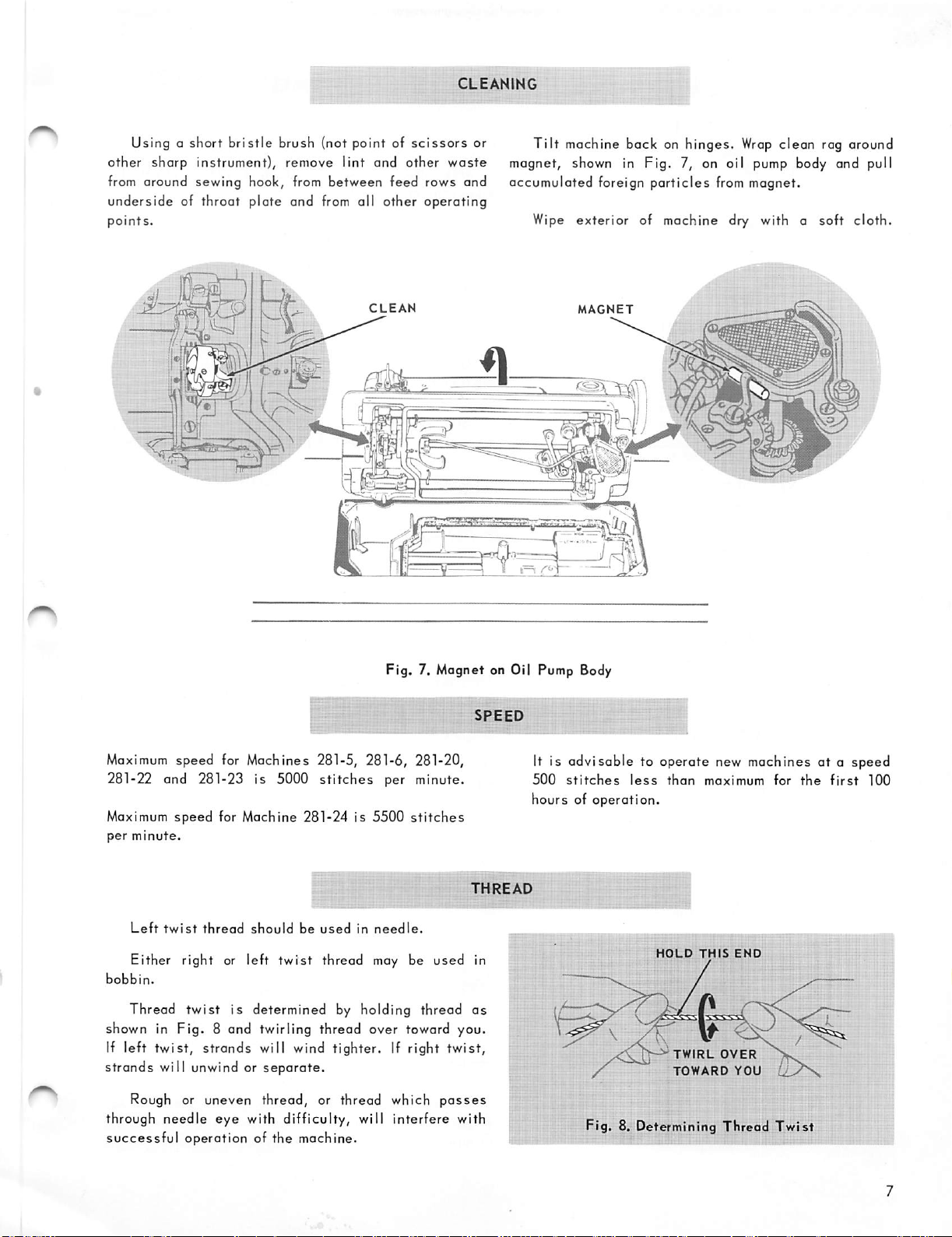
Sk^ING
Using a
other sharp instrument), remove lint and other
from around
underside of throat plate and from all other operating
points.
short
sewing
bristle
hook, from
brush (not point of
between
feed rows and
CLEAN
scissors
waste
or
Tilt
machine back on hinges.
Wrap
clean
magnet, shown in Fig. 7, on oil pump body and pull
from
accumulated foreign particles
Wipe exterior of machine dry with a soft
magnet.
rog around
cloth.
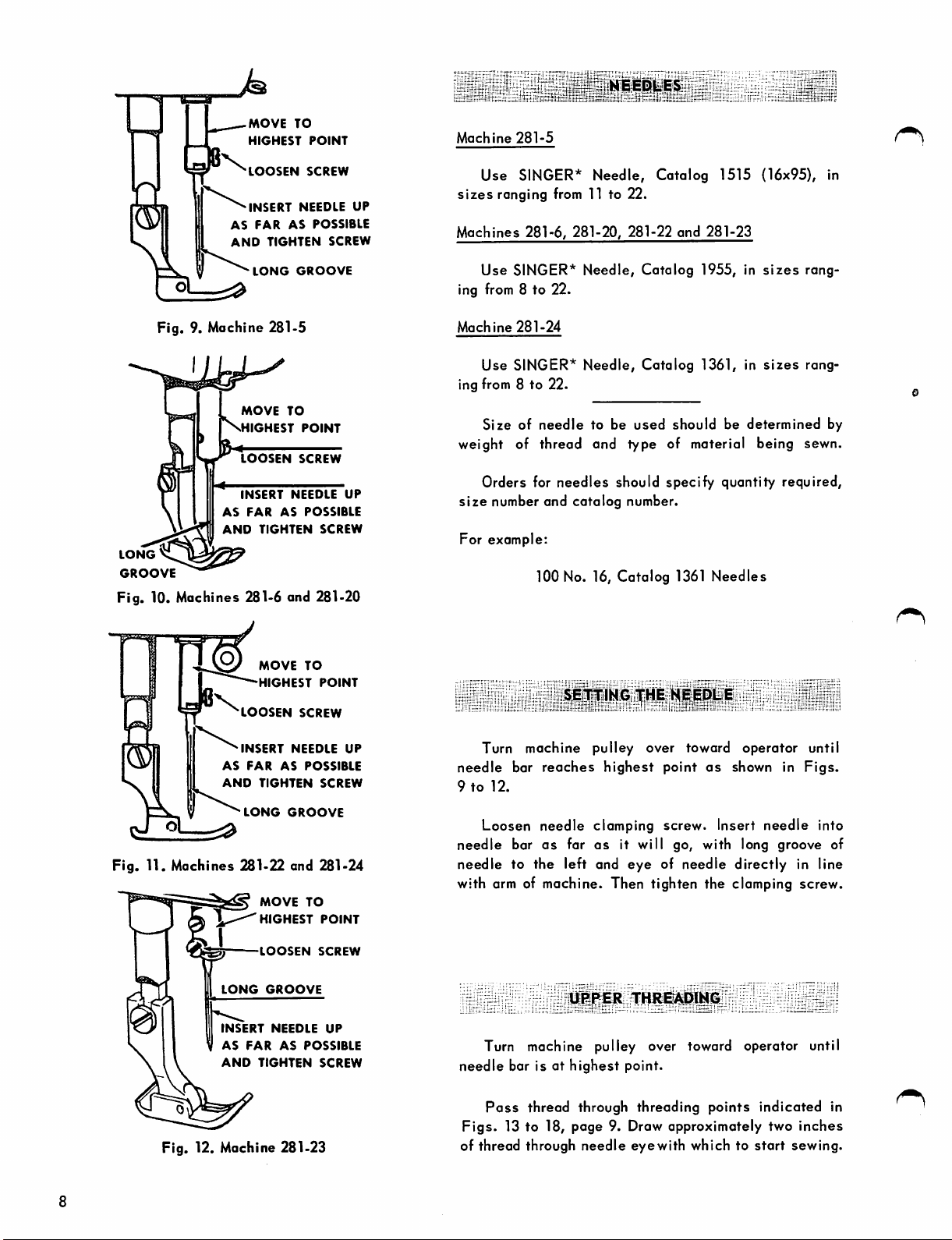
MOVE
HIGHEST
TO
POINT
Machine
281-5
AS
AND
LOOSEN
INSERT
FAR
LONG
NEEDLE
AS
TIGHTEN
GROOVE
SCREW
POSSIBLE
SCREW
Fig. 9. Machine 281-5
LONG
OOVE^^
GROOVE
MOVE
"^HIGHEST
LOOSEN
INSERT
AS
AND
FAR
TIGHTEN
TO
NEEDLE
AS
POINT
SCREW
UP
POSSIBLE
SCREW
Fig. 10. Machines 281-6 and 281-20
UP
Use SINGER* Needle, Catalog 1515 (16x95), in
sizes
ranging from 11 to 22.
Machines
281-6, 281-20, 281-22
Use
SINGER* Needle,
and
Catalog
281-23
1955, in
sizes
rang
ing from 8 to 22.
Machine
Use
281-24
SINGER*
Needle,
Catalog
1361, in
sizes
rang
ing from 8 to 22.
Size of
needle
to be
used
should be determined by
weight of thread and type of material being sewn.
Orders for needles should specify quantity required,
size
number and catalog number.
For
example:
100 No. 16, Catalog 1361 Needles
LOOSEN
INSERT
FAR
AND
LONG
LONG
INSERT
FAR
AND
MOVE
HIGHEST
AS
TIGHTEN
MOVE
HIGHEST
LOOSEN
GROOVE
NEEDLE
AS
TIGHTEN
TO
Fig.
11. Machines 281-22 and 281-24
Fig. 12. Machine 281-23
TO
SCREW
NEEDLE
POSSIBLE
GROOVE
TO
SCREW
POSSIBLE
POINT
SCREW
POINT
UP
SCREW
UP
SETTING
the
needle
Turn machine pulley over toward operator until
needle
9to12.
needle
needle to the left and
bar
reaches
highest
point
as
shown in
Loosen needle clamping screw. Insert
bar
as
far
as
it will go, with long groove of
eye
of needle directly in line
needle
Figs.
into
with arm of machine. Then tighten the clamping screw.
UPPER
THREADING
Turn machine pulley over toward operator until
needle
Figs.
of thread through needle
bar is at
Pass
highest
point.
thread through threading points indicated in
13 to 18, page 9. Draw approximately two
eye
with which to
start
inches
sewing.