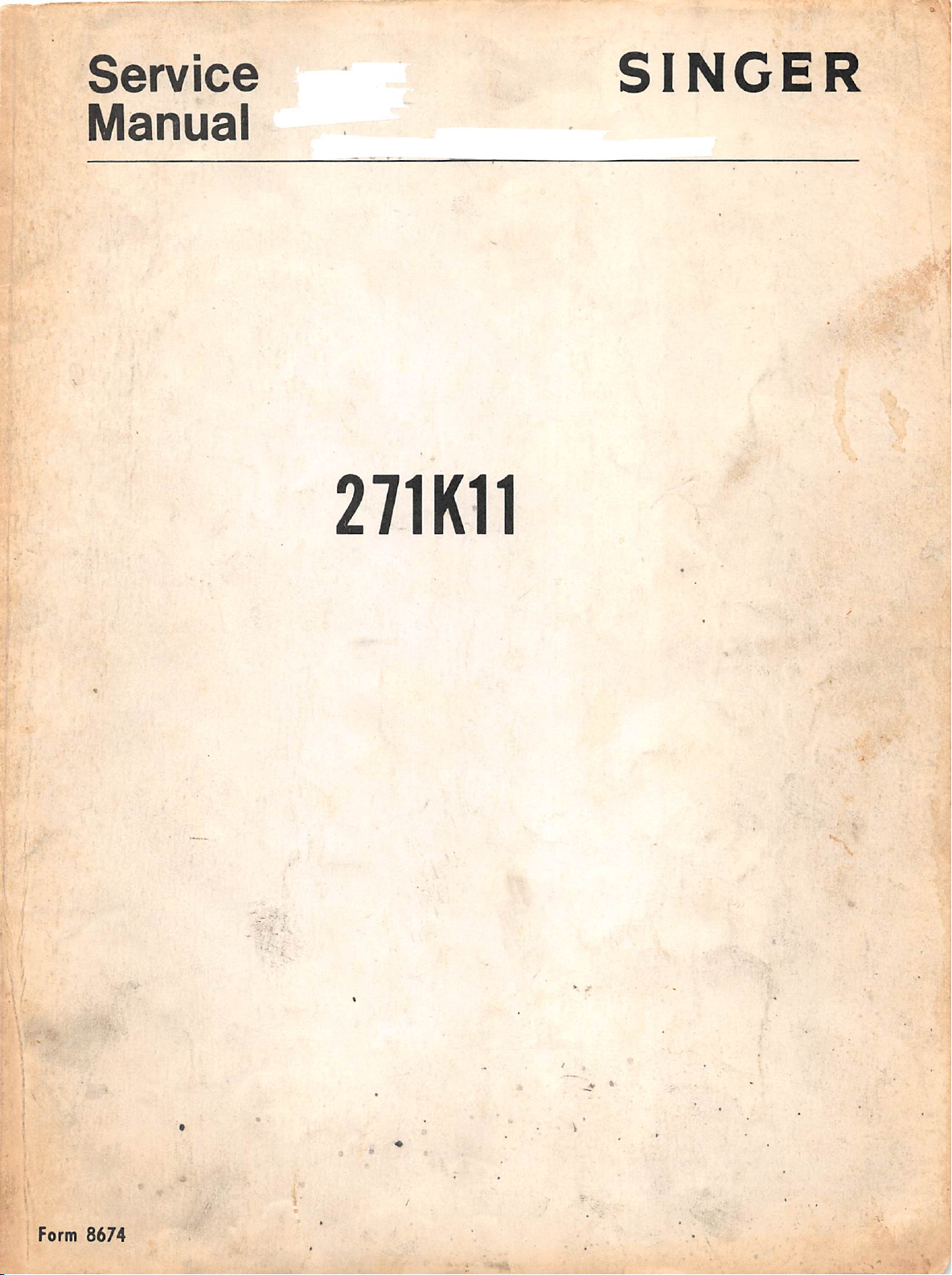
Service
Manual
SINGER
Mr
•lii:'<•.
'4y'"5\
n
;•'!
s
3-
|.r'
•
"X
5|r
<
•'
I ^
"
•-
'ru,
271K11
•
.-.w'i
.a-
'••V
i '
> • !'•-:
m
•1^6
I .i'
.i I l'
k
i V •
:\
.v.-v.
Form
-W
Jj.
8674
- !
•
"s-
.A
- '.I
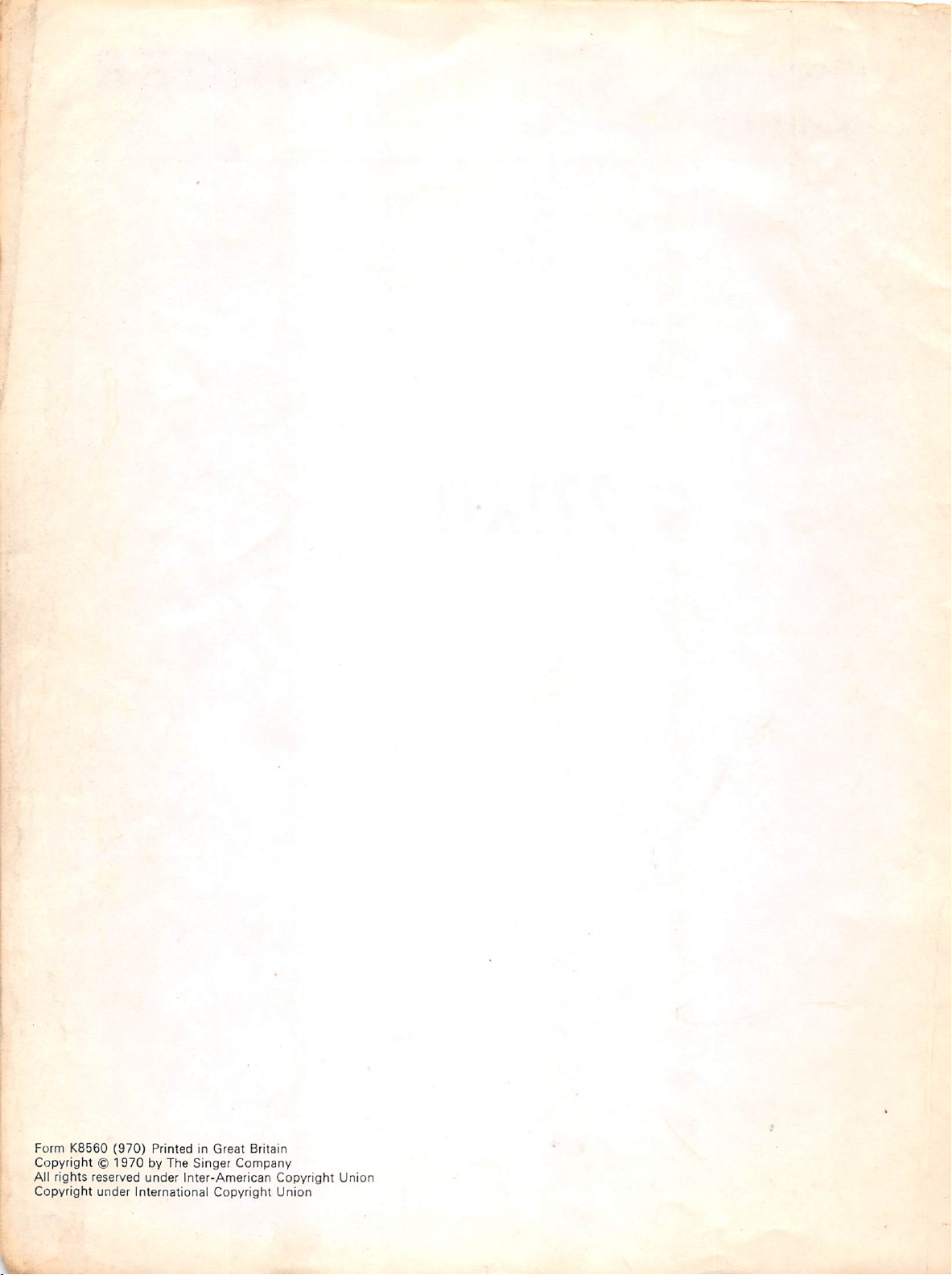
Form K8560
Copyright©1970byThe
All rights reserved under Inter-American Copyright Union
Copyright
(970)
under
Printed in
Singer
International
Great
Britain
Company
Copyright
Union
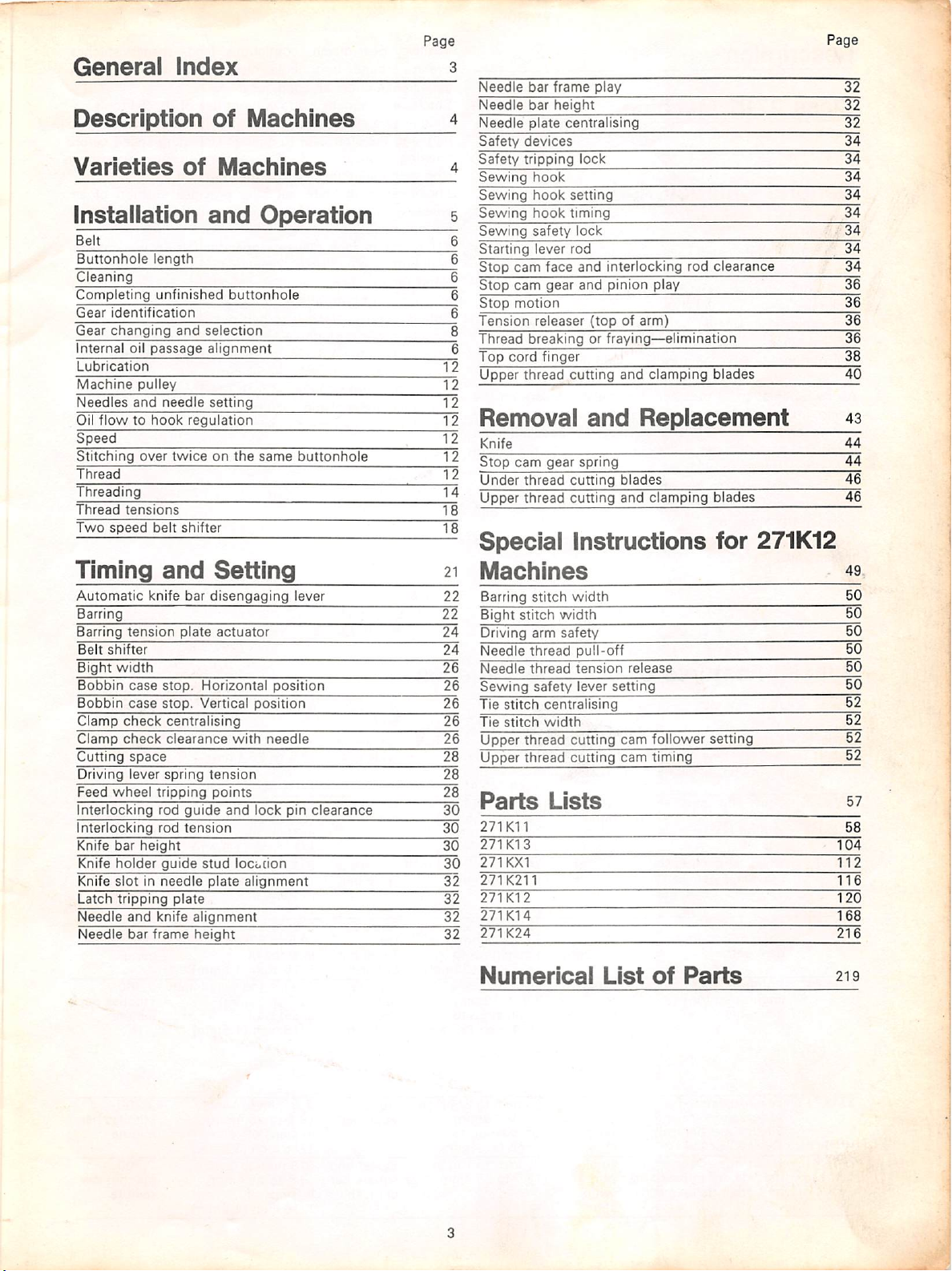
General
index
Description
Varieties
Instaiiation
Belt
Buttonhole
Cleaning
Completing
Gear
Gear
Internal
Lubrication
Machine
Needles
Oil
flowtohook
Speed
Stitching
Thread
Threading
Thread
Two
Timing
Automatic
Barring
Barring
Belt
Bight
Bobbin
Bobbin
Clamp
Clamp
Cutting
Driving
Feed
Interlocking
Interlocking
Knife
Knife
Knife
Latch
Needle
Needle
length
unfinished
identification
changing
oil
passage
pulley
and
needle
over
twiceonthe
tensions
speed
belt
and
knife bar
tension
shifter
width
case
stop.
case
stop.
check
centralising
check
clearance
space
lever
spring
wheel
tripping
rod
rod
bar
height
holder
guide
slotinneedle
tripping
and
knife
bar
frame
and
plate
of
of
Machines
and
selection
alignment
setting
regulation
shifter
Setting
disengaging
plate
actuator
Horizontal
Vertical
tension
points
guide
tension
stud
plate
alignment
height
Machines
Operation
buttonhole
same
position
position
with
needle
and
lock
pin
loct-tion
alignment
buttonhole
lever
clearance
Page
3
Needle
Needle
4
Needle
Safety
devices
Safety
4
tripping
Sewing
Sewing
Sewing
5
Sewing
6
Starting
6
Stop
6
6
6
8
6
12
12
12
12
12
12
12
14
18
18
cam
Stop
cam
Stop
motion
Tension
Thread
Top
cord
Upper
thread
Removal
Knife
Stop
cam
Under
thread
Upper
thread
opeciai
21
Machines
22
Barring
22
Bight
stitch
24
Driving
24
Needle
26
Needle
26
Sewing
26
Tie
stitch
26
Tie
stitch
26
Upper thread cutting
28
Upper
thread
28
28
Parts
30
271
30
30
30
32
32
32
32
K11
271
K13
271
KX1
271K211
271
K12
271K14
271K24
bar
frame
bar
height
plate
centralising
hook
hook
setting
hook
timing
safety
lever
rod
face
gear
releaser
breaking
finger
cutting
gear
cutting
cutting
stitch
width
arm
safety
thread
thread
safety
centralising
width
cutting
Lists
play
lock
lock
and
interlocking
and
pinion
(topofarm)
rod
play
or fraying—elimination
and
clamping
and
Replacement
spring
blades
and
clamping
insiruciions
width
pull-off
tension
lever
release
setting
cam
cam
follower
timing
clearance
blades
blades
jot
setting
Page
32
32
32
34
34
34
34
34
34
34
34
36
36
36
36
38
40
43
44
44
46
46
iivi^
49
50
50
50
50
50
50
52
52
52
52
57
58
104
112
116
120
168
216
Numerical
List
of
Parts
219
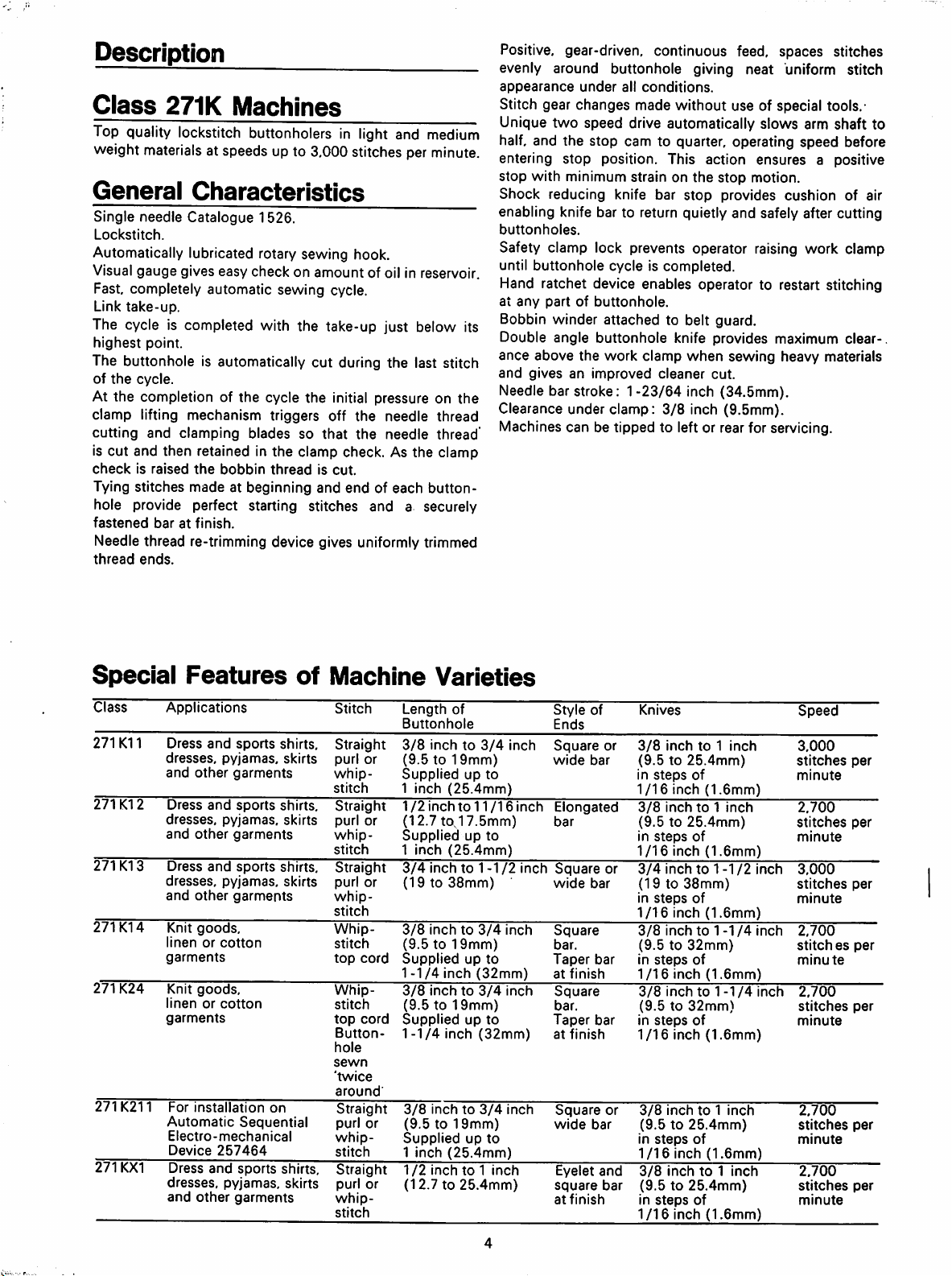
Description
Ciass
Top quality lockstitch buttonholers in light and
weight materials at speeds up to 3,000 stitches per
271K
Machines
medium
minute.
General Characteristics
Single needle Catalogue
Lockstitch.
Automatically lubricated rotary sewing hook.
Visual
gauge
gives easy check on
Fast, completely automatic sewing cycle.
Link
take-up.
The cycle is completed with the take-up just below its
highest
point.
The buttonhole is automatically cut during the last stitch
of
the
cycle.
At
the
completion of
clamp lifting mechanism triggers off the needle thread
cutting
and
clamping
is cut and then retained in the clamp check. As the clamp
checkisraised
the
Tying stitches made at beginning and
hole provide perfect starting stitches and a securely
fastened
baratfinish.
Needle thread re-trimming device gives uniformly trimmed
thread
ends.
the
bobbin
1526.
cycle
blades
threadiscut.
amount
the
so
of oil in reservoir.
initial pressure on
that
the
end
needle
thread'
of each button
the
Positive, gear-driven, continuous feed, spaces stitches
evenly around buttonhole giving neat uniform stitch
appearance
under
all
conditions.
Stitch gear changes made without use of special tools.Unique two speed drive automatically slows arm shaft to
half, and the stop cam to quarter, operating speed before
entering stop position. This action ensures a positive
stop
with minimum strain on
Shock
reducing knife bar
the
stop
stop
motion.
provides
cushion
of air
enabling knife bar to return quietly and safely after cutting
buttonholes.
Safety clamp lock prevents operator raising work clamp
until
buttonhole
cycle is completed.
Hand ratchet device enables operator to restart stitching
at
any
partofbuttonhole.
Bobbin winder attached to belt guard.
Double angle
ance
above
and
gives
Needle bar stroke:
Clearance under clamp:
buttonhole
the
work clamp
an improved
1-23/64
knife provides maximum
when
sewing heavy materials
cleaner
cut.
inch (34.5mm).
3/8
inch (9.5mm).
clear-.
Machines can be tipped to left or rear for servicing.
Special
Class
271
K11
271
K12
271
K13
271
K14
271
K211
271
KX1
Features
Applications
Dress
and
dresses,
and
Dress
dresses,
and
Dress
dresses,
and
Knit
linenorcotton
garments
linenorcotton
garments
For
Automatic
Electro-mechanical
Device
Dress
dresses,
and
sports
pyjamas,
other
garments
and
sports
pyjamas,
other
garments
and
sports
pyjamas,
other
garments
goods,
installation
Sequential
257464
and
sports
pyjamas,
other
garments
shirts,
skirts
shirts,
skirts
shirts,
skirts
on
shirts.
skirts
of
Machine
Stitch
Straight
purl
whip
stitch
Straight
purl or
whip
stitch
Straight
purl or
whip
stitch
Whip
stitch
top
stitch
top
Button
hole
sewn
'twice
around"
Straight
purl or
whip
stitch
Straight
purl
whip
stitch
Length
Buttonhole
3/8
or
(9.5to19mm)
Supplied
1 inch
1/2
(12.7
Suppliedupto
1
inch
3/4
(19to38mm)
3/8
(9.5to19mm)
cord
Suppliedupto
1 -1/4inch
(9.5to19mm)
cord
Suppliedupto
1
-1/4
3/8
(9.5to19mm)
Suppliedupto
1
inch
1/2
or
(12.7to25.4mm)
Varieties
of
inchto3/4
(25.4mm)
inchto11/16
toj
(25.4mm)
inch to 1 -1/2inch
inchto3/4
inch
inchto3/4
(25.4mm)
inchto1
inch
up to
inch
7.5mm)
inch
(32mm)
(32mm)
inch
inch
Style
of
Ends
Square
wide
bar
Elongated
bar
Square
wide
bar
Square
bar.
Taper
bar
at ifinish
bar.
Taper
bar
at finish
Square
wide
bar
Eyelet
square
at
finish
Knives
or
3/8
(9.5to25.4mm)
in
1/16
3/8
(9.5to25.4mm)
in
1/16
or
3/4
(19to38mm)
in
1/16
3/8
(9.5to32mm)
in
1/16
(9.5to32mm)
in
1/16
or
3/8
(9.5to25.4mm)
in
1/16
and
3/8
bar
(9.5to25.4mm)
in
1/16
inchto1
steps
inch
inchto1
steps
inch
inchto1
steps
inch
inchto1
steps
inch
steps
inch
inchto1
steps
inch
inchto1
steps
inch
of
(1.6mm)
of
(1.6mm)
of
(1.6mm)
of
(1.6mm)
of
(1.6mm)
of
(1.6mm)
of
(1.6mm)
inch
inch
-1/2
-1/4
•1/4
inch
inch
inch
inch
inch
Speed
3.000
stitches
minute
2.700
stitches
minute
3.000
stitches
minute
2.700
stitchesper
minute
2,700
stitches
per
per
per
per
minute
2.700
stitches
minute
2.700
stitches
minute
per
per
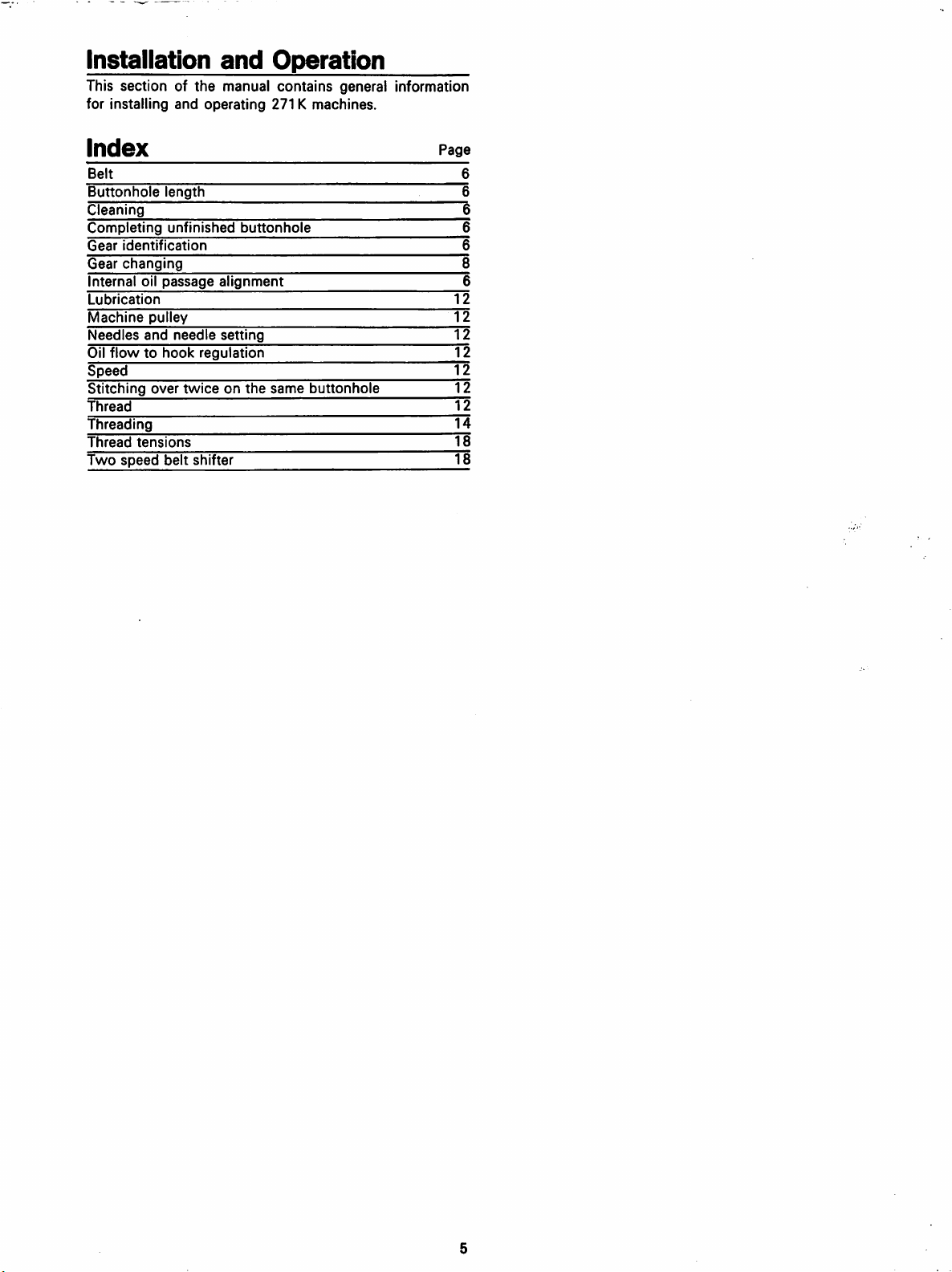
Installation
This section of
for installing
and
and
the
manual contains general
operating
Operation
271 K machines.
information
Index
Belt
Buttonhole
Cleaning
Completing
Gear
identification
Gear
changing
Internal oil
Lubrication
Machine
Needles
Oil
Speed
Stitching
Thread
Threading
Thread
Two
and
flowtohook
tensions
speed
length
unfinished
passage
pulley
needle
over
belt
buttonhole
alignment
setting
regulation
twiceonthe
shifter
same
buttonhole
Page
6
6
6
6
6
8
6
12
12
12
12
12
12
12
14
18
18
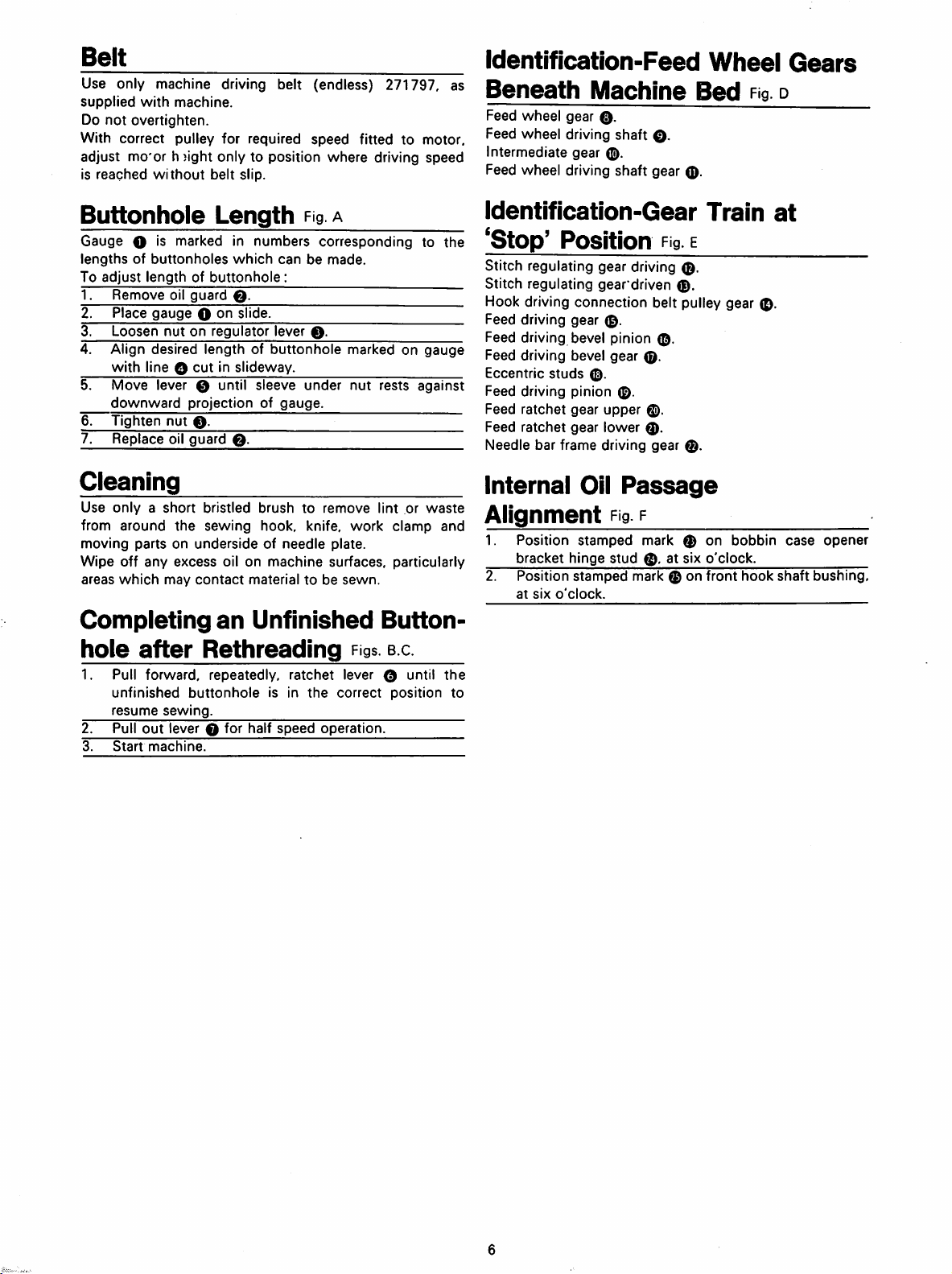
Belt
Use only machine driving belt (endless) 271797, as
supplied
Do
With correct pulley for required speed fitted to motor,
adjust
is
not
overtighten.
mo'or
reached
with
without
machine.
h)ight
belt
only to position
slip.
where
driving
speed
Identification-Feed
Beneath
Feed wheel gear
Feed wheel driving shaft
Intermediate gear
Feed wheel driving shaft gear
Machine
0.
Q.
®.
Wheel
Bed
0.
Fig,
d
Gears
Buttonhole Length
Gauge
lengthsofbuttonholes
Toadjust
1.
2.
3.
4. Align desired length of
5. Move lever 0 until sleeve
6.
7. Replace oil
Cleaning
Use
from around
moving
Wipe
areas
Completing
hole
1. Pull
2.
3.
O marked in
length
of buttonhole:
Remove
Place
Loosen
with
downward
Tighten
onlyashort
off
which
unfinished
oil
guard ®.
gauge
Q on slide.
nuton
line
Q cut in
projection
nut
0.
guard
bristled
the
sewing hook, knife, work clamp
partsonundersideofneedle
any
excess
may
contact
after
forward,
Rethreading
buttonhole
numbers
which
regulator
slideway.
of gauge.
0.
brushtoremove
oil on
materialtobe
an
Unfinished
repeatedly,
resumesewing.
Pull
out
lever
0 for
half
Start
machine.
canbemade.
lever
buttonhole
machine
is in
speed operation.
Fig,
a
corresponding
0.
under
plate.
surfaces,
ratchet
the
correct
marked on
nut
rests
against
lint or
particularly
sewn.
Button-
Figs.
B.C.
lever 0 until
position
to
the
gauge
waste
and
the
identification-Gear
'Stop'
Stitch regulating gear driving
Stitch regulating gear driven
Hook driving connection belt pulley gear ®.
Feed driving gear
Feed driving bevel pinion
Feed driving bevel
Eccentric
Feed driving pinion
Feed
Feed
Needle
internal
Alignment
1.
2. Position
to
studs
ratchet
ratchet
bar
Position
Position
®.
gear
0.
gear
upper
gear
lower
frame driving
Oil
Fig,
stamped
fiq
0.
®.
®.
0.
©.
0.
0.
gear
0.
Passage
f
mark 0 on
e
brackethingestud0,at sixo'clock.
stamped
at
six
o'clock.
mark 0 on front
Train
bobbin
hook
at
case
shaft
opener
bushing,
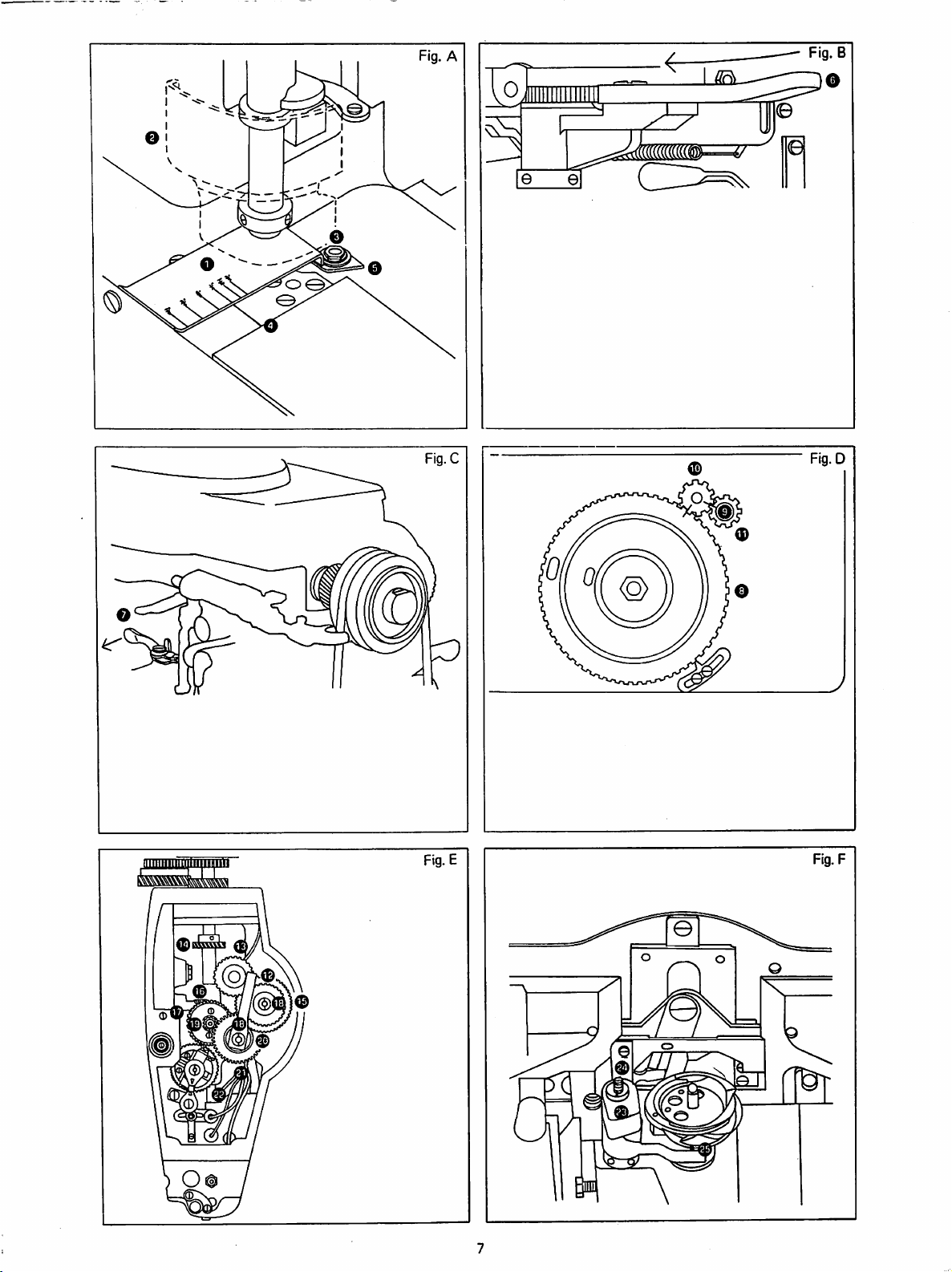
1®
\^Wp
Fig. E
fp-
\ o ^ /
'==^^/w
p
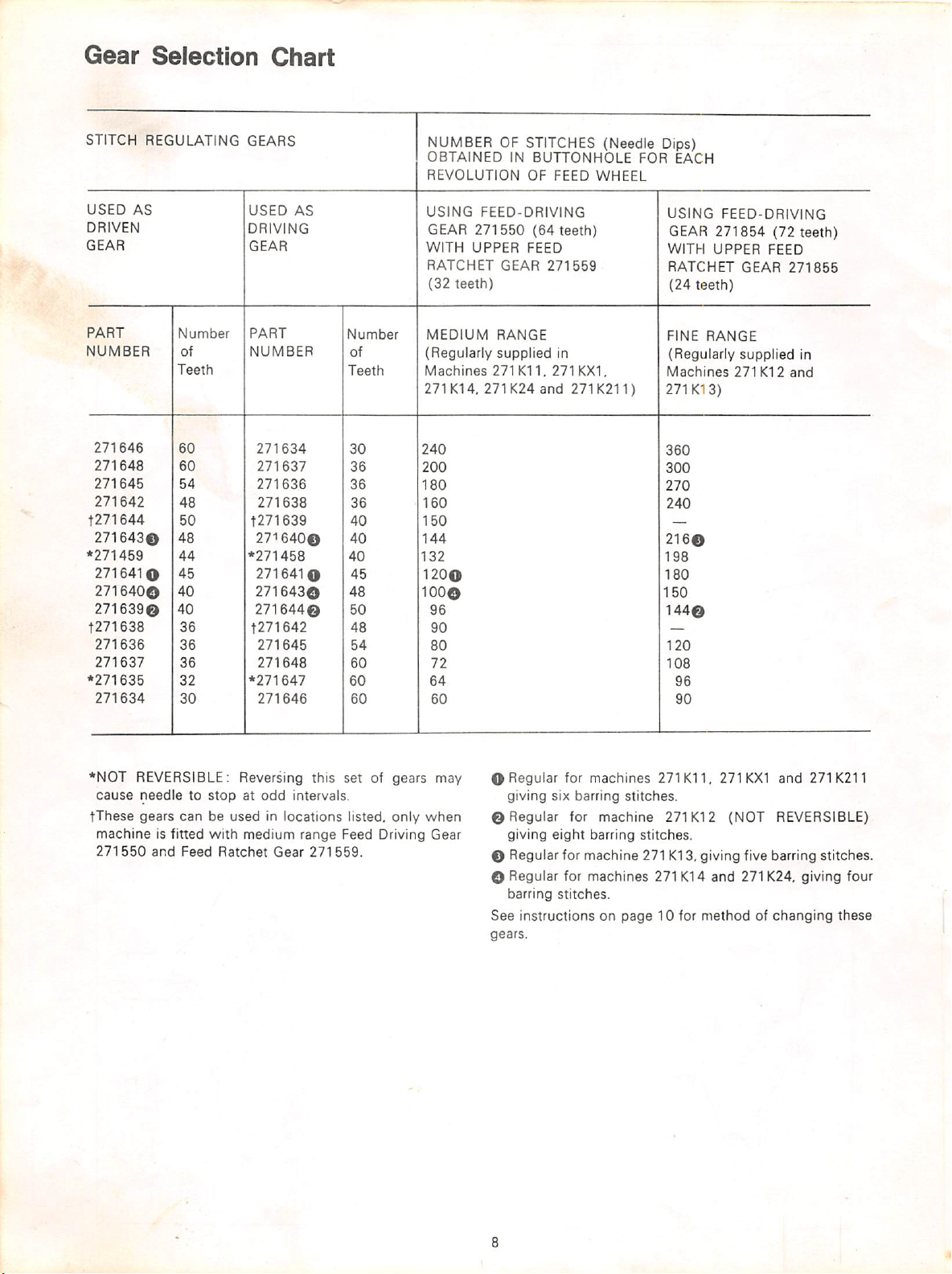
Gear
Selection
Chart
STITCH
USED
DRIVEN
GEAR
PART
NUMBER
271646
271648
271645
271642
1271644
271643©
*271459
271641©
271640©
271639©
t271638
271636
271637
*271635
271634
REGULATING
AS
Number
of
Teeth
60
60
54
48
50
48
44
45
40
40
36
36
36
32
30
GEARS
USED
AS
DRIVING
GEAR
PART
NUMBER
271634
271637
271636
271638
t271639
271640©
♦271458
271641©
271643©
271644©
t271642
271645
271648
*271647
271646
Number
of
Teeth
(Regularly
Machines
271 K14,
30
36
36
36
40
40
40
45
48
50
48
54
60
60 64
60 60
240
200
180
160
150
144
132
120©
100©
NUMBER OF STITCHES (Needle Dips)
OBTAINED
REVOLUTION
USING
GEAR
WITH
RATCHET
(32
teeth)
MEDIUM
96
90
80
72
IN
BUTTONHOLE
OF
FEED-DRIVING
271550
UPPER
(64
FEED
GEAR
RANGE
supplied
271 K11,
271K24and
FEED
teeth)
271559
in
271KX1,
271K211)
FOR EACH
WHEEL
USING
GEAR
WITH
RATCHET
(24
FINE
(Regularly
Machines
271 K13)
360
300
270
240
—
216©
198
180
150
144©
—
120
108
96
90
FEED-DRIVING
271854
UPPER
GEAR
teeth)
RANGE
supplied
271K12
(72 teeth)
FEED
271855
in
and
•NOT REVERSIBLE: Reversing this set of gears may
cause
tThese
machine
271550
needletostopatodd
gears
canbeusedinlocations
is fitted with medium
and
Feed
Ratchet
intervals.
Gear
listed,
range
Feed Driving Gear
271559.
only
when
©Regular
giving
for
six
©Regular
giving
eight
© Regular for
©Regular
barring
See
gears.
for
stitches.
instructions on
machines
barring
for
barring
machine
machines
271K11,
271KX1
stitches.
machine
271K12
(NOT
stitches.
271 K13,giving five barring stitches.
271 K14
page10for
and
271K24.
methodofchanging
and
271K211
REVERSIBLE)
giving four
these
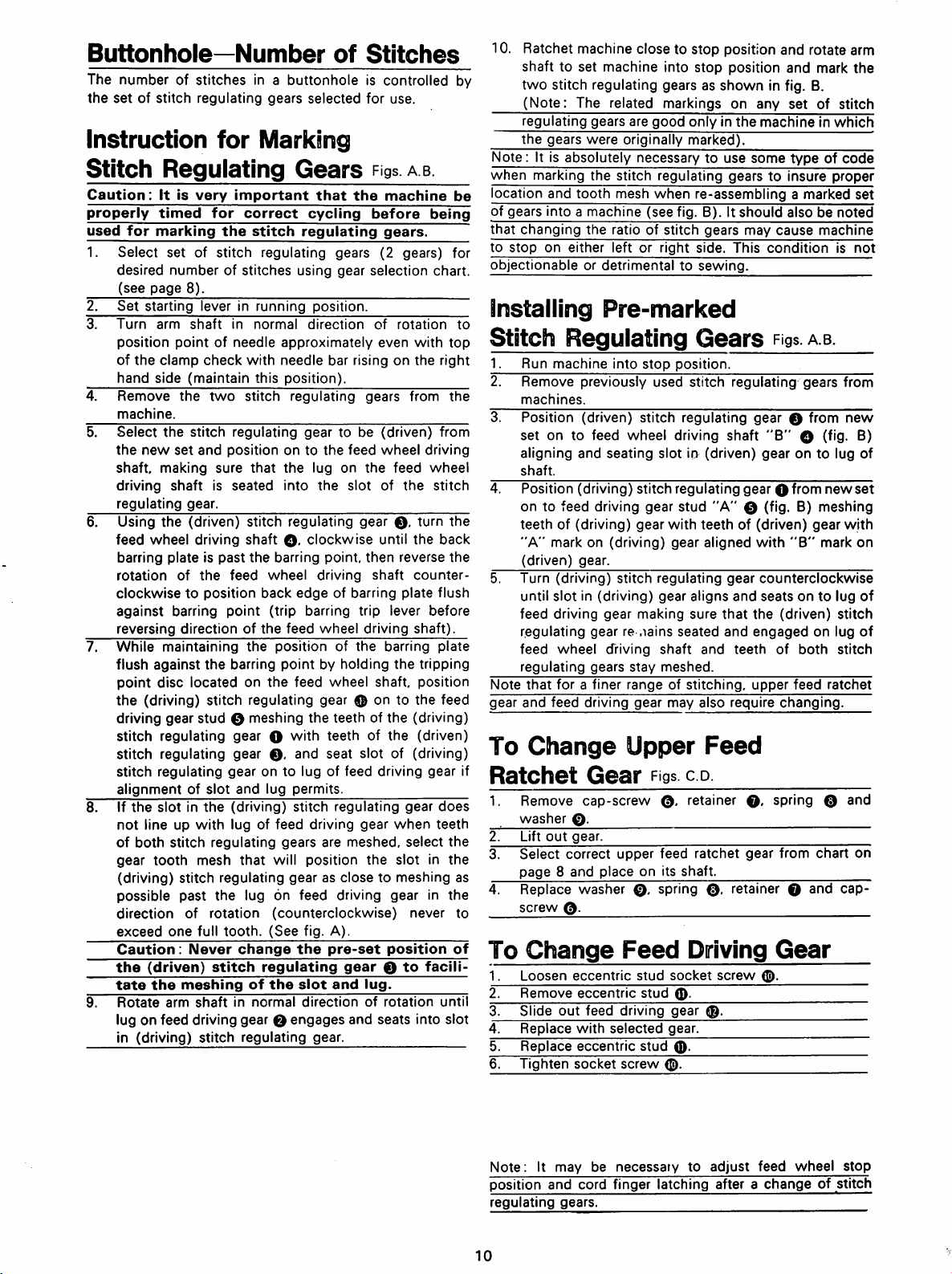
Buttonhole—Number
of
Stitches
The number of stitches in a buttonhole is controlled by
the
setofstitch
instruction
Stitch
Caution:
properly
used for marking
1.
Select
desired
regulating
for
Regulating
Itisvery
timed
setofstitch
numberofstitches
important
for
correct
the
stitch regulating gears.
gears
selected
Marking
Gears
that
cycling
regulating
using
the
gears
gear
for use.
Figs.
machine
before
(2
gears)
selection
A.B.
be
being
for
chart.
(see page 8).
2. Set starting
3.
Turn
position
of
the
leverinrunning
arm
shaft
pointofneedle
clamp
check
in
normal
approximately
with
needle
position.
direction
bar rising on
of
even
rotation
with
the
top
right
hand side (maintain this position).
4.
Remove
the
two
stitch
regulating
gears
from
the
machine.
5.
Select
the
stitch
the
new
shaft,
driving
regulating
set
and
positiononto
making
sure
shaftisseated
that
the
into
gear
lug on
the
the
to be
feed
slot
(driven)
wheel
the
of
feed
the
from
driving
wheel
stitch
regulating gear.
6.
Using
the
(driven)
feed
wheel
driving
barring
rotation
clockwisetoposition
against
reversing
plateispast
of
barring
directionofthe
stitch
shaftO'clockwise
the
the
feed
wheel
back
point
regulating
barring point,
edgeofbarring
(trip barring trip lever
feed
driving
wheel
gearQ.turn
until
then
reverse
shaft
plate
driving
the
back
counter
flush
before
shaft).
the
the
T. While maintaining the position of the barring plate
flush
against
point
the
(driving) stitch regulating
driving
stitch
stitch regulating
stitch
the
disc
locatedonthe
gear
stud
regulating
regulating
barring
0 meshing
gear
point
by holding
feed
wheel
gear
the
teethofthe
gearOwith
gear
0,
on to lug of feed driving
teethofthe
and
seat
the
shaft, position
^ on to
(driving)
slot
of (driving)
tripping
the
feed
(driven)
gear
alignment of slot and lug permits.
8. If
the
slotinthe
not
line up
of
both
stitch
gear
tooth
(driving) stitch regulating
possible
direction
exceed
past
one
Caution:
the
(driven)
tate
the
meshingofthe
Rotate
lugonfeed
in
arm
(driving)
(driving)
with
lug of
regulating
mesh
that
the
lug on
of
rotation
full
tooth.
Never
change
stitch
shaftinnormal
driving
gear0engages
stitch
regulating
stitch
regulating
feed
driving
gears
are
meshed,
will
position
gearasclose
feed
driving
(counterclockwise)
(See
fig.
A).
the
pre-set
regulating
slot
direction
gear.
gear0to
and
and
gear
gear
when
select
the
slotinthe
to meshing as
gearinthe
never
position
lug.
of
rotation
seats
into
does
teeth
the
of
facili
until
slot
10. Ratchet machine close to
shaft to
two
(Note:
regulating
the gears were
Note:
when
set
machine into
stitch regulating gears as
The related markings on any
gears
are
originally
It is absolutely
marking the stitch regulating gears to insure proper
necessarytouse
location and tooth mesh
of
gears
into a
machine
that
to
changing
stop
on
the
either
ratio of
left or
stop
position and rotate arm
stop
position
shown
good
only in
the
marked).
when
re-assembling a marked
(see
fig. B). It
stitch
right
gears
side.
should
This
and
in fig. B.
set
machineinwhich
some
typeofcode
alsobenoted
may
cause
conditionisnot
objectionable or detrimental to sewing.
Installing
to
Stitch
1.
Run
machine into stop position.
2. Remove previously used stitch regulating gears from
Pre-marked
Regulating
Gears
Figs.
machines.
3. Position (driven) stitch regulating
set
on to feed
aligning
shaft.
4. Position (driving) stitch regulating
on to feed driving
teeth
"A"
and
of (driving)
mark on (driving)
wheel
seating
gear
gear
driving
slot
let (driven)
stud
with
gear
teeth
aligned
shaft
gear
"A"
0 (fig. B)
of (driven)
gear
0 from
"B"
gearonto
O from
with
"B"
(driven) gear.
5. Turn (driving)
until
slot
feed
driving
regulating
feed
wheel
stitch
in (driving)
gear
making
gear
re .iains
driving
regulating
gear
aligns
sure
seated
shaft
and
gear
counterclockwise
and
seatsonto
that
the
and
engagedonlug
teeth
of
(driven)
regulating gears stay meshed.
Note
that
if
gear
and
To
Change
Ratchet
Remove
washer
2. Lift
Select
for a finer
feed
Q.
out
gear.
correct
rangeofstitching,
driving
gear
Upper
Gear
cap-screw
upper
may
Figs.
0,
feed
also
Feed
C.D.
retainer
ratchet
upper
require
0,
gear
changing.
spring
from
page 8 and place on its shaft.
0,
spring
0.
Replace
To
1.
screw
Change
Loosen
to
washer
0.
eccentric
Feed
stud
socket
retainer 0
Driving
screw
Gear
2. Remove eccentric stud^
3.
Slide
out
feed
4.
5.
6.
Replace
Replace
Tighten
with
selected
eccentric
socket
driving
screw
stud
gear
gear.
0.
0.
0.
mark
of stitch
machine
A.B.
new
O (fig. B)
lug of
new
meshing
gear
with
mark
lug
stitch
both
stitch
feed
ratchet
0
chart
and
cap-
the
set
set
on
of
of
and
on
Note:
position
It may be
and
necessarytoadjust
cord finger latching after a
regulating gears.
10
feed
change
wheel
of stitch
stop
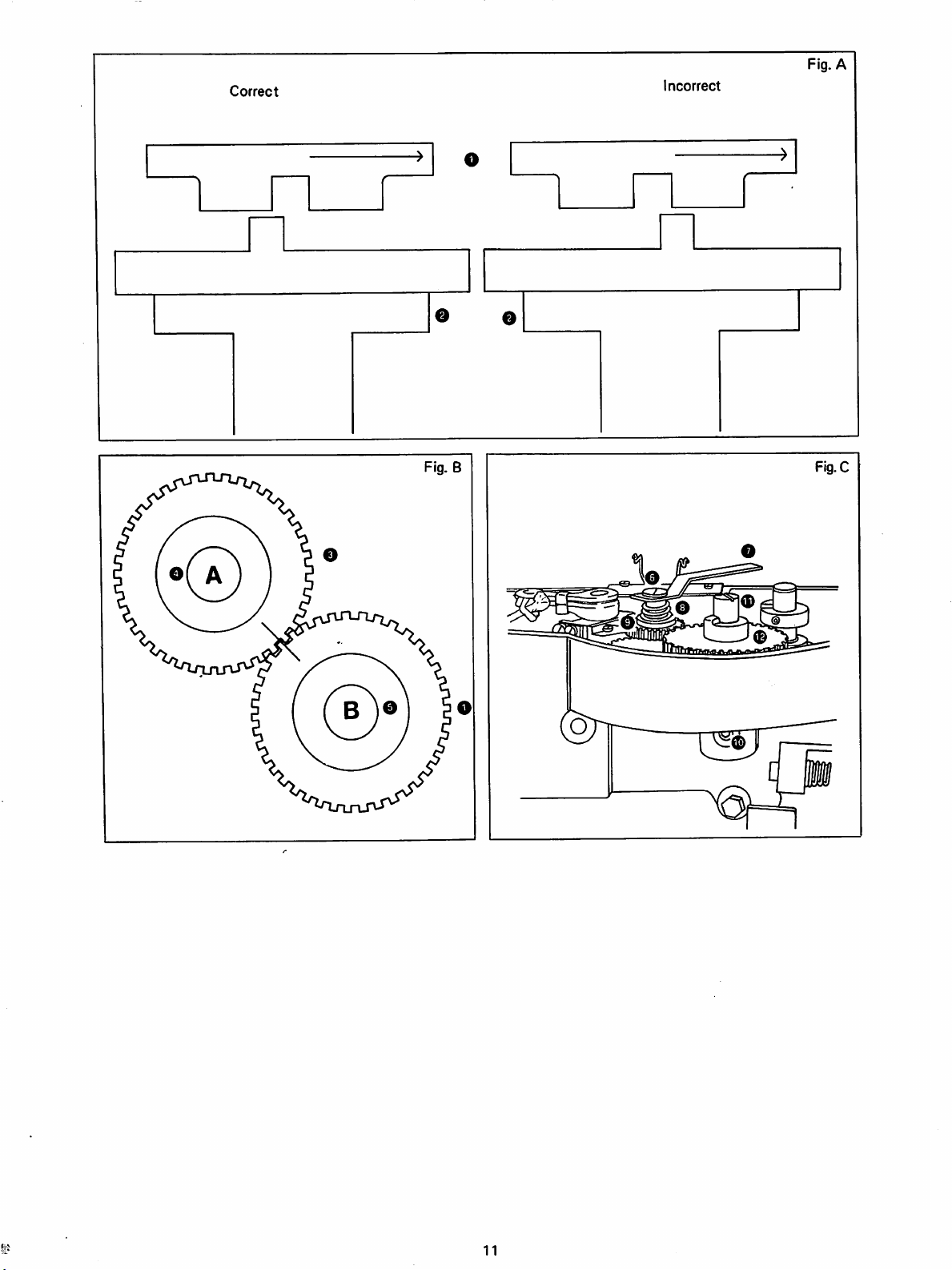
Correct
Fig. A
Incorrect
O o
Fig.B
11
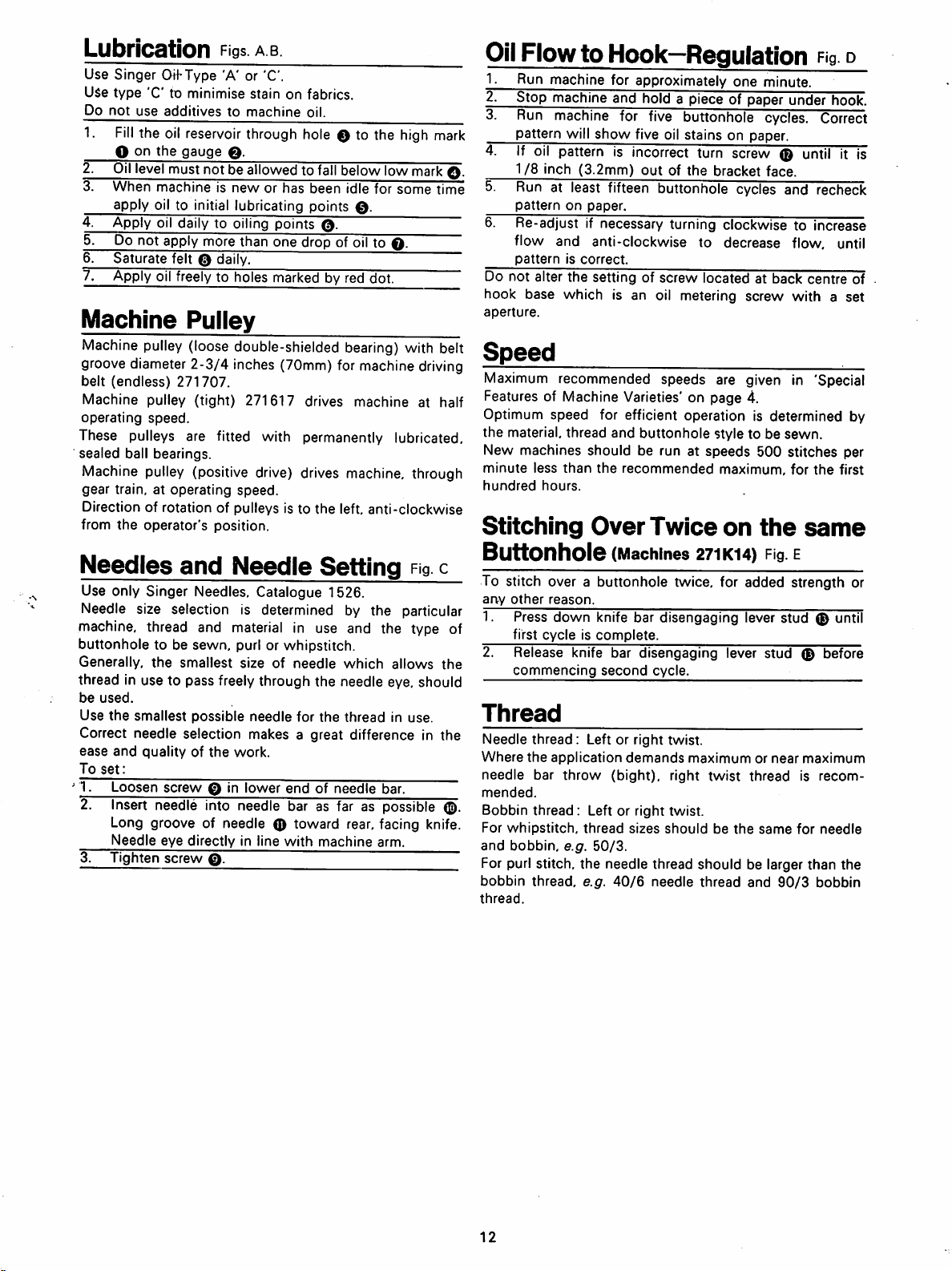
Lubrication
Use Singer OiFType 'A' or
Use
type'Cto
Do
1.
not use
Fill
additivestomachine
the oil reservoirthrough hole Q to the high mark
Figs.
minimise
A.B.
'C.
stainonfabrics.
oil.
O on the gauge Q.
2.
Oil
level
must
notbe
allowedtofall
3.
When
machineisneworhas
apply
oiltoinitial
4. Apply oil daily to oiling points
5.
Do
not
apply
6. Saturate felt Q daily.
7. Apply oil freely to holes marked by red doL
Machine
Machine
pulley
lubricating
more
than
one
Pulley
(loose double-shielded bearing) with belt
groove diameter 2-3/4 inches (70mm) for machine
belt
(endless)
Machine pulley (tight)
operating
These pulleys are fitted with permanently lubricated,
sealed
ball
Machine pulley (positive
gear train, at operating speed.
Direction of rotation of pulleys is to
from
the
Needles
Use only Singer Needles, Catalogue 1526.
Needle size selection is determined by the particular
machine, thread and material in use and the type of
buttonhole to be sewn, purl or whipstitch.
Generally,
thread in use to pass freely through the needle eye, should
be
used.
Use
the
Correct needle selection makes a great difference in the
ease
and
To
set:
' 1.
Loosen
271707.
speed.
bearings.
operator's
and
the
smallest
smallest
qualityofthe
possible
screwQInlower
271617
drive)
position.
Needle
size of
needle
work.
end of
belowlow
been
idle for
points
0.
0.
dropofoil
mark
some
to Q.
driving
drives machine at half
drives machine, through
the
left, anti-clockwise
Setting
needle
for
the
which
thread
needle
Fig,
allows
in use.
bar.
time
c
2. Insert needle into needle bar as far as possible ©.
Long groove of needle Q toward rear, facing knife.
Needle
3. Tighten
eye
directlyinline
screw
0.
with
machine
arm.
OilFlowtoHook—Regulation
1. Run machine for approximately one minute.
2. Stop machine and hold a piece of paper under hook.
3. Run machine for five buttonhole cycles. Correct
pattern
4^Ifoil
Q.
1/8
5^
Runatleast
pattern on paper.
6. Re-adjust if necessary turning clockwise to increase
flow
pattern is correct.
Do not alter
hook base which is an oil metering screw with a set
aperture.
Speed
Maximum recommended speeds are given In 'Special
Features of Machine Varieties' on page 4.
Optimum speed for efficient operation is determined by
the
material, thread
New machines should be run at speeds 500 stitches per
minute
hundred
Stitching
Buttonhole
To Stitch over a buttonhole twice, for added strength or
aay other reason.
1. Press down knife bar disengaging lever stud 0 until
first
2. Release knife bar disengaging lever stud 0 before
the
commencing second cycle.
Thread
Needle
Where
needle
mended.
Bobbin
For
whipstitch,
and
bobbin,
For purl stitch, the needle thread should be larger than the
bobbin
thread.
will
show
patternisincorrect
inch
(3.2mm)
fifteen
and
anti-clockwise to decrease flow, until
the
settingofscrew
and
less
than
the
hours.
Over
(Machines
cycle is complete.
thread:
the
bar
thread:
thread,
Left or right twist.
application
throw
(bight),
Left or right twist.
thread
e.g.
50/3.
e.g.
40/6
five
oil
stainsonpaper.
out of
the
buttonhole
buttonhole
recommended
Twice
demands
sizes
maximumornear
right
shouldbethe
needle
turn
screw0untilitis
bracket
face.
cycles
located at back
style to be
maximum,
on
the
271K14)
twist
thread
Fig.
thread
same
and
and
sewn.
for
E
is recom
for
90/3
Fig,
d
recheck
centre
the
first
same
maximum
needle
bobbin
of
12
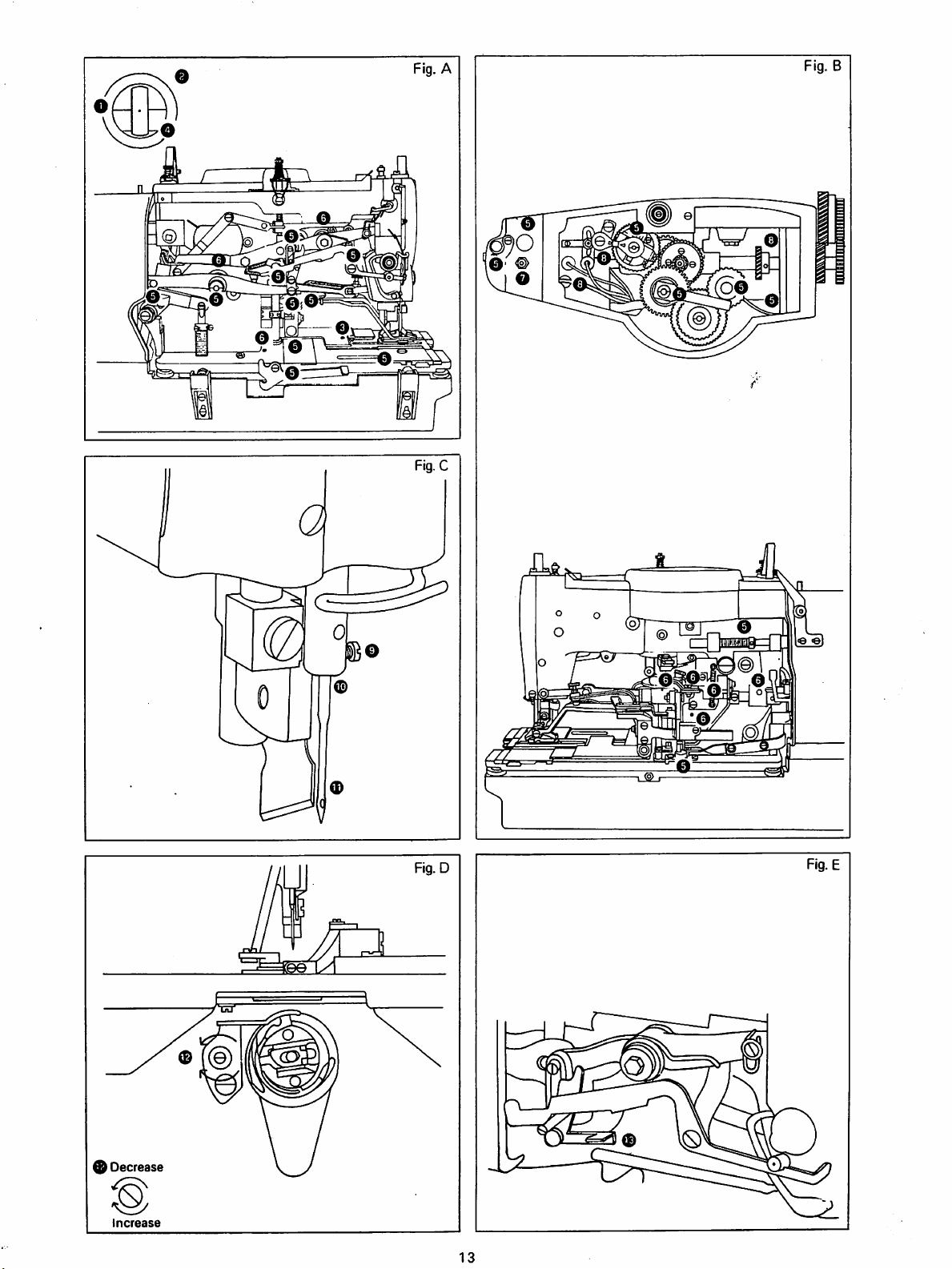
o
o
Q
m
0 Decrease
Increase
13
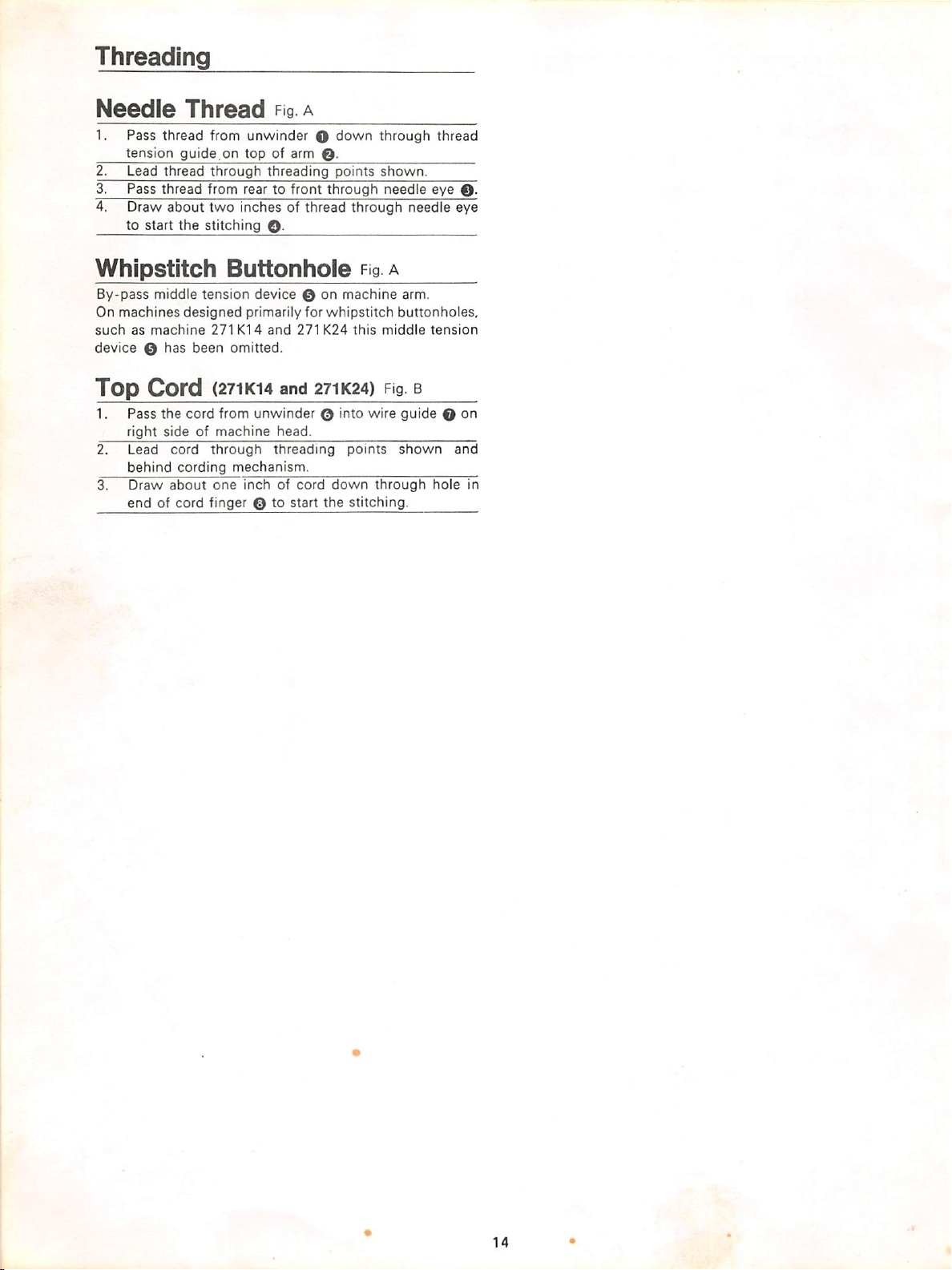
Threading
Needle
1.
Pass
tension guide.on top of
2.
Lead
3.
Pass
4. Draw
Thread
thread
from
Fg a
unwinderOdown
arm
thread
through threading
thread from rear to front
about
two
inches of
thread
Q.
points
through
to start the stitching Q.
Whipstitch Buttonhole
By-pass
On
such
device0has
Top
1.
2. Lead
3.
middle
machines
as
machine
Cord
Pass
the
tension
designed
been
cord
device
primarily for
271
K14
and
omitted.
(271K14
from
unwinder
and
right side of machine head.
cord
through
threading
behind cording mechanism.
Draw
about
one
inch of
endofcord
finger
O to
0 on
whipstitch
271
K24
271K24)
O into
cord
start
the
down
through
shown.
needle
through
Fig,
machine
this
middle
Fig.
wire
points
through
stitching.
thread
eye
needle
a
arm.
buttonholes,
tension
8
guide
shown
hole
Q.
eye
0 on
and
in
14
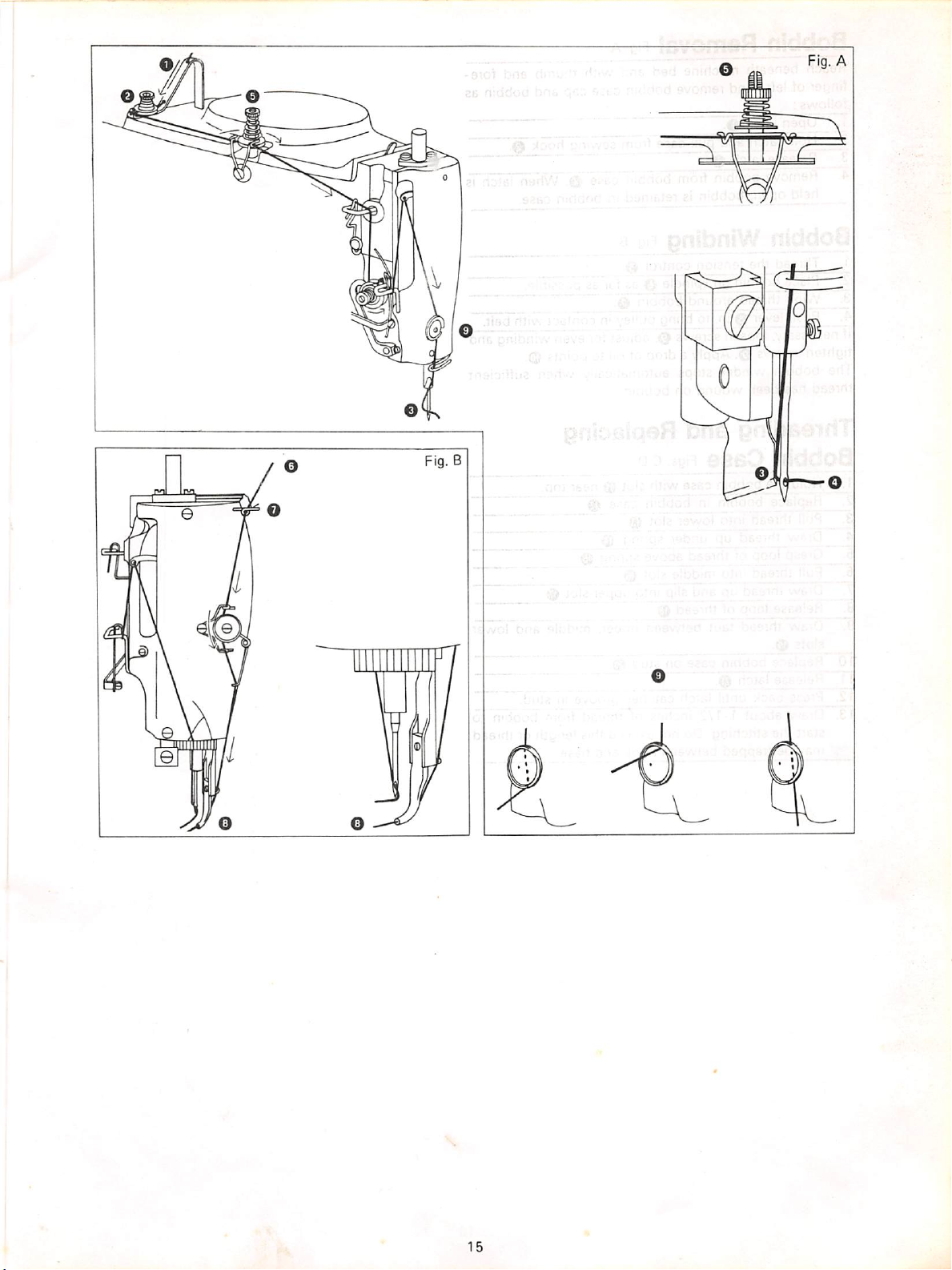
Fig. A
15
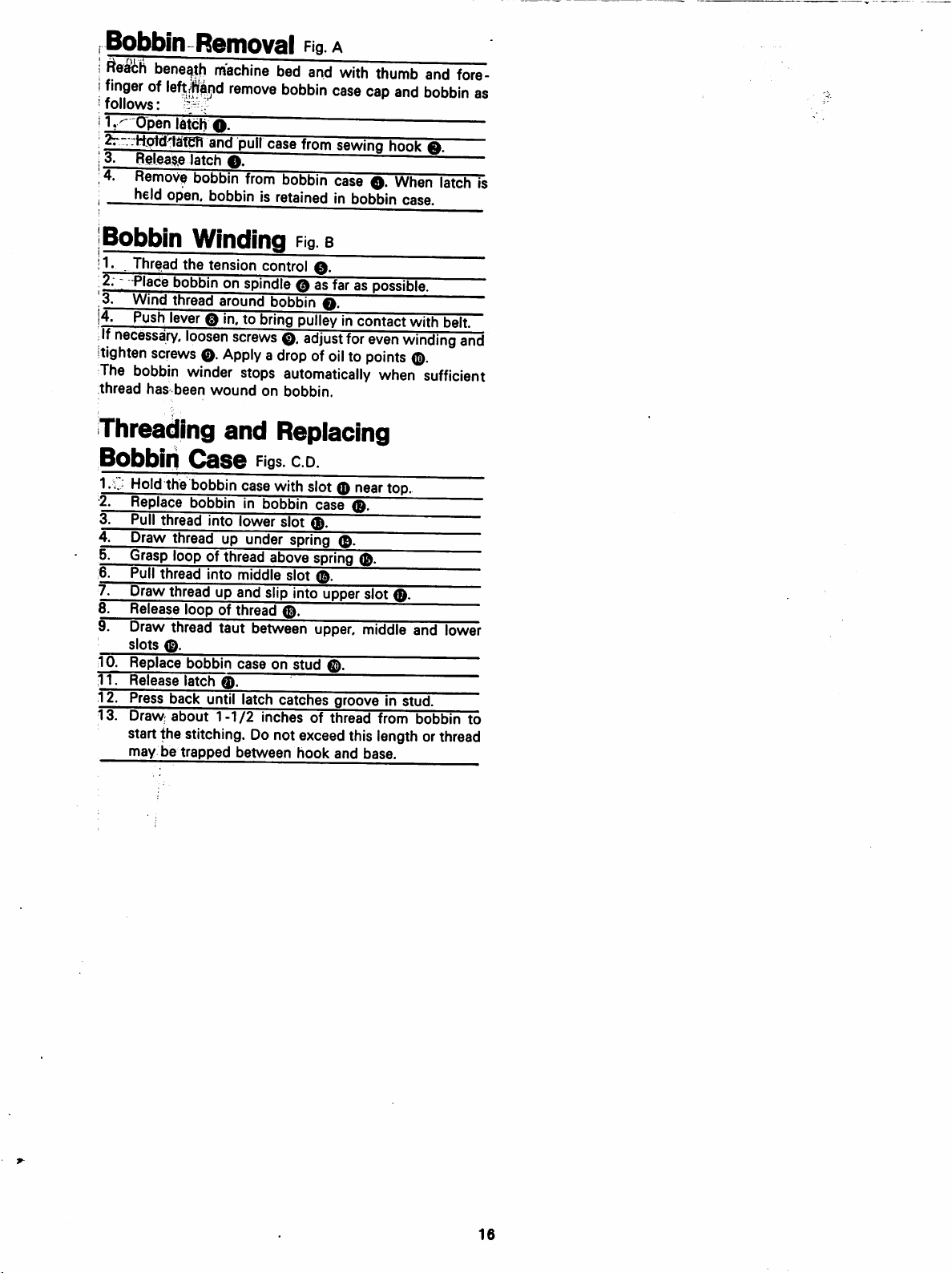
,
Bobbin
i
fteSih
!
fingeroflefj/njand
!
follows:
11.gpen
i
:H:ptddiStett
j3. Relea^
;4.Remove
i
held
1
Bobbin
!1..
Thread
f lace bobbinon spindle 0 as far as possible.
13.
Wind
!4.
Push
If
necessary,
itighten
The
bobbin
thread has been
Removal
bene^h
open,
machine
remove
latcb
O.
and
0.
bobbin
pull
from
latch
bobbinisretainedinbobbin
Winding
the
tension
thread
around
lever0in.tobring
loosen
screws0,adjust
screws0.Applyadropofoiltopoints
winder
stops
wound
Rg.
bed
and
bobbin
case
from
bobbin
Fig,
control
on bobbin.
0.
bobbin
pulleyIncontact
automatically
a
with
case
cap
sewing
caseO.When
b
Q.
for
even
Threading and Replacing
thumb
and
hook
case.
with
winding
0.
when
and
fore-
bobbin
as
0.
latch
belt.
and
sufficient
is
Bobbin
1.1
Hold
2.
Replace
3. Pull thread into lower slot
4. Draw thread up under spring
5. Grasp loop of thread above spring
6. Pull thread into middle
7. Draw thread up and slip into upper slot
8. Release loop of thread
9. Draw thread taut between upper,
slots
10. Replace bobbin case on stud @.
11.
Release latch
12.
Press
Draw
start the stitching. Do not exceedthis length orthread
maybetrapped
Case
the
bobbin
bobbininbobbin
0.
back
about
0.
until
1-1/2
case
latch
between
Figs.
C.D.
with
slot0
near
top.
case
0.
0.
0.
0.
slot"^
0.
middle
catches
inches of thread from bobbin to
grooveinstud.
hook
and
base.
and lower
16