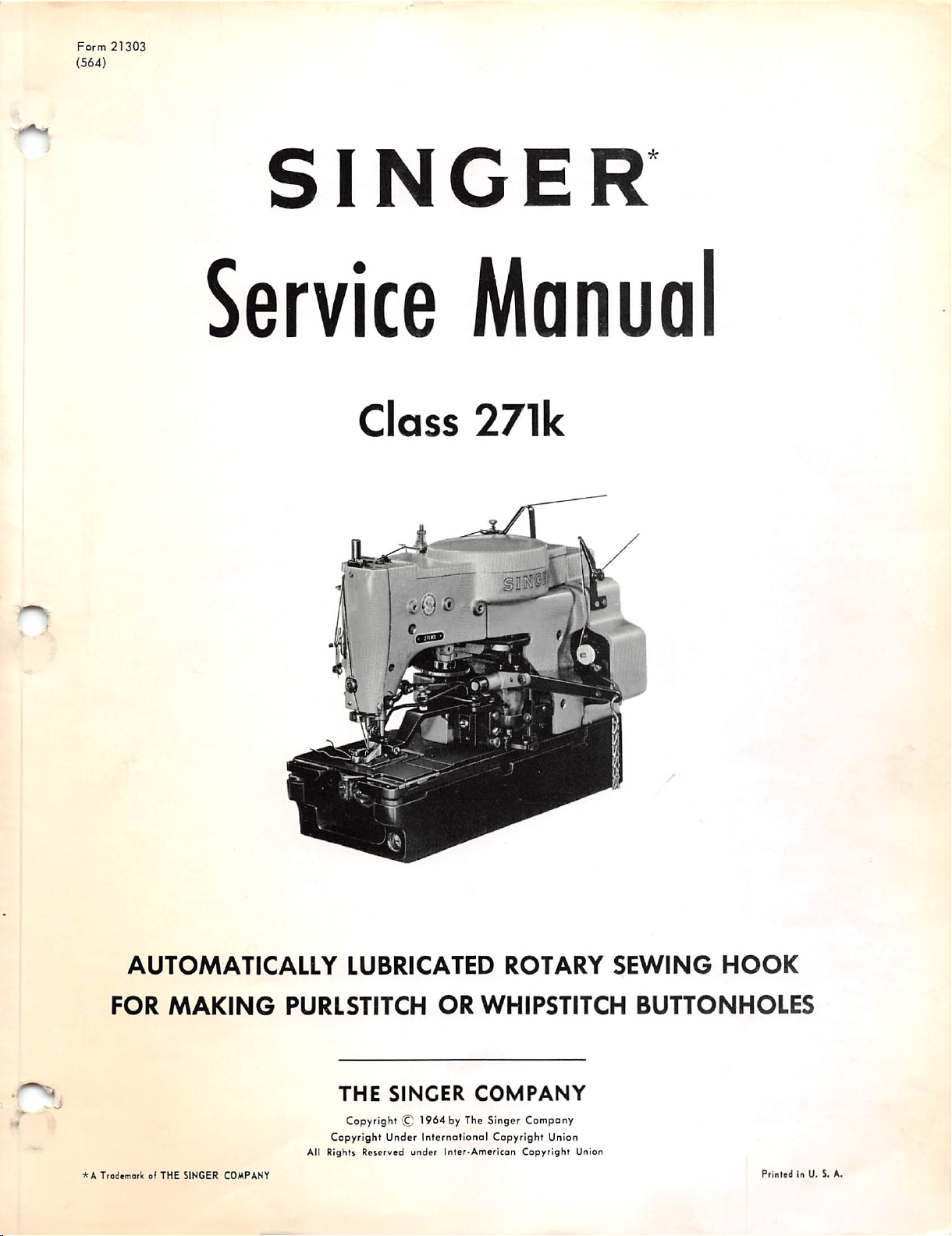
Form
(564)
21303
SINGER
Service
Class
0
>
Manual
271k
AUTOMATICALLY
FOR
*A
TrademerkofTHE
MAKING
SINGER
PURLSTITCH
COMPANY
LUBRICATED
OR
THE
Copyright Under International Copyright Union
Alt Rights Reserved
SINGER
Copyright ^ 1964 by TheSinger Company
under
Inler-American
ROTARY
WHIPSTITCH
COMPANY
Copyright
SEWING
BUTTONHOLES
Union
HOOK
Printed
In U. S. A.
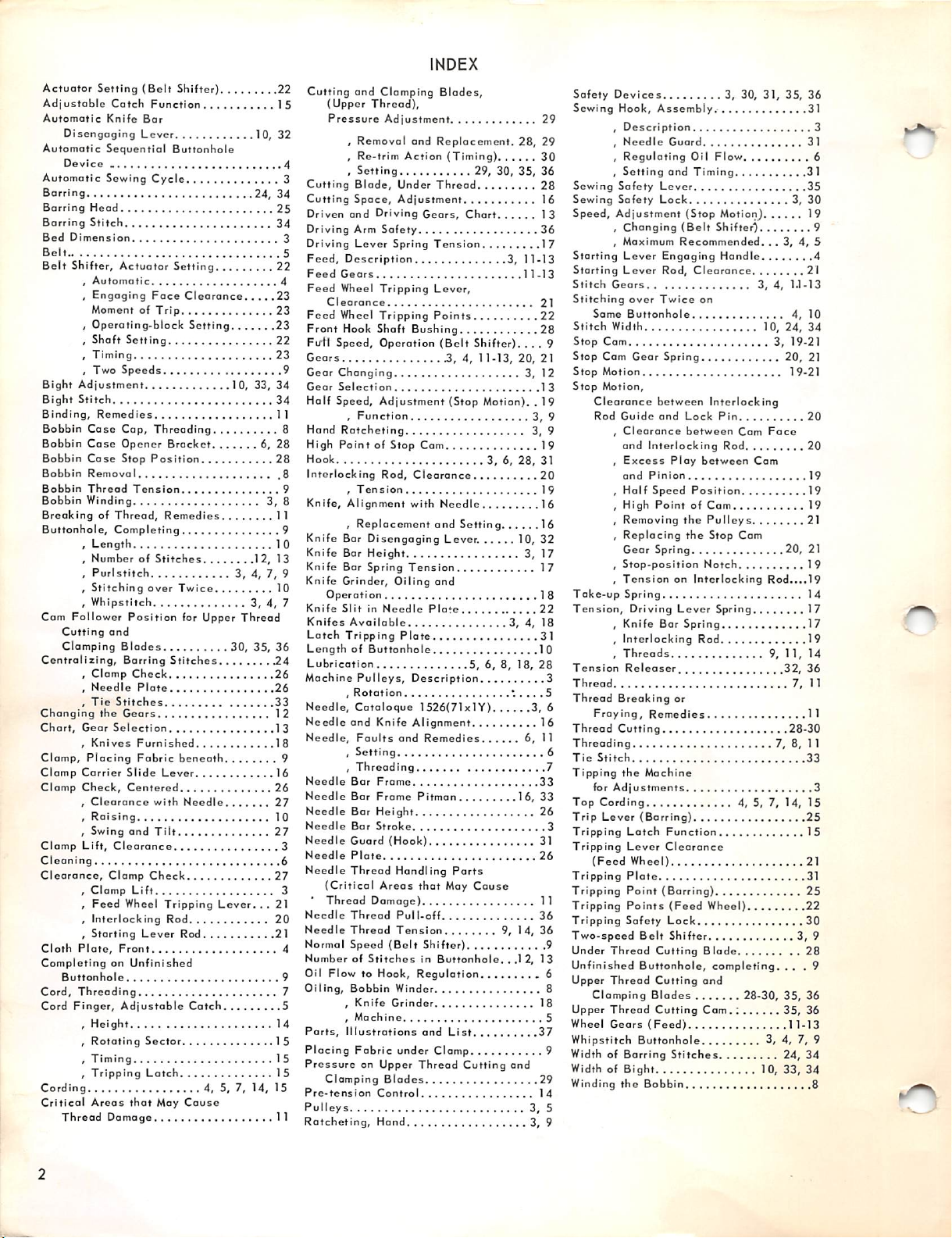
Actuator
Adjustable
Automatic
Automotic
Automatic
Barring
Barring
Barring
Bed
Belt
Setting
Catch
Knife
Disengaging
Sequential
Device
Sewing
Head
Stitch
Dimension
(Belt
Function
Bar
Lever
Cycle
Shifter)
10, 32
Buttonhole
24, 34
Belt Shifter, Actuator Setting 22
,
Automatic
,
Engaging
MomentofTrip
,
Operating-block
,
Shaft
,
Timing
, Two
Bight
Adjustment
Bight
Stitch
Binding,
Bobbin
Bobbin
Bobbin
Bobbin
Bobbin
Bobbin
Remedies
Cose
Case
Cose
Removal
Thread
Winding
BreokingofThread,
Buttonhole,
,
Length
,
NumberofStitches
,
Purl
Stitching
,
Whipstitch
,
Com
Follower
Cutting
Clamping
Centralizing,
,
Clamp
,
Needle
,
Changing
Chort,
Clamp,
Clamp
Clomp
Tie
the
Gear
,
Knives
Placing
Carrier
Check,
,
Clearance
,
Raising
, Swing
Clomp
Lift,
Cleaning
Clearance,
,
Clamp
,
Feed
,
Interlocking
,
Cloth
Starting
Plate,
CompletingonUnfinished
Buttonhole
Cord,
Threoding
Cord
Finger,
,
Height
,
Rotating
,
Timing
,
Tripping
Cording
Critical
Areas
Thread
Setting
Speeds
Cap,
Opener
Stop
Position
Tension
Completing
stitch
over
Position
and
Blodes
Barring
Check
Plate
Stitches
Gears
Selection
Furnished
Fabric
Slide
Centered
and
Clearance
Clamp
Check
Lift
Wheel
Lever
Front
Adjustable
Sector
Latch
that
Damage
Face
Clearance
Setting
10,
Threading
Bracket
Remedies
3, 4, 7, 9
Twice
for Upper
Thread
30, 35, 36
Stitches
beneath
Lever
with
Needle
Tilt
Tripping
Lever...21
Rod 20
Rod 21
Catch
4, 5, 7,
May
Cause
33,
6, 28
3,
12,
3, 4, 7
^4
14,
INDEX
22
Cutting
15
and Clamping
(Upper
Pressure
Thread),
Adjustment
, Removal and
,
Re-trim
Action
Under
Adjustment
Driving
Gears,
Safety
Spring
Tripping
Tripping
Shaft
Bushing
Operation
Adjustment
Cam 19
Rod,
Clearance
with
Disengaging
Height
Spring
Tension
Oiling
Plate
Tension
Lever,
Points
and
and
Plate
25
34
23
23
23
22
23
34
34
11
28
11
10
13
10
4
3
3
5
4
9
8
8
9
8
9
,
Cutting
Cutting
Driven
Driving
Driving
Feed,
Feed
Feed
Feed
Front
Fotl
Setting
Blade,
Space,
ond
Arm
Lever
Description
Gears
Wheel
Clearance
Wheel
Hook
Speed,
Gears
Gear
Changing
Gear
Selection
Half
Speed,
,
Hand
High
Function
Ratcheting
PointofStop
Hook 3, 6.
Interlocking
,
Knife,
Tension
Alignment
,
Replacement
Knife Bar
Knife
Bar
Knife
Bar
Knife
Grinder,
Operation
Knife
SlitinNeedle
Knifes
Available
Lotch
Tripping
LengthofButtonhole
Lubrication
26
Machine
26
33
Needle,
12
Needle
13
Needle,
18
9
16
Needle
26
Needle
27
Needle
10
Needle
27
Needle
3
Needle
6
Needle
27
3
Needle
Needle
Normal
4
NumberofStitchesinButtonhole.
Oil
9
Oiling,
7
5
14
Ports,
15
Placing
15
PressureonUpper
15
15
Pre-tension
Pulleys
11
Ratcheting,
Pulleys,
,
Rotation
Cataloque
and Knife
Faults
,
Setting
,
Threading
Bar
Bar
Bar
Bar
Guard
Plate
Threod
(Critical
•
Thread
Thread
Thread
Speed
FlowtoHook,
Bobbin
,
Knife
,
Machine
Illustrations
Fabric
Clamping
and
Frame
Frame
Height
Stroke
(Hook)
Handling
Areas
Damage)
Pull-off
Tension
(Belt
Winder
Grinder
under
Blades
Control
Hand
Description
1526(71xlY)
Alignment
Remedies
Pitman
that
Shifter)
Regulation
and
Clamp 9
Thread
Blades,
Replacement.
(Timin
Thread
29,
28,
g)
30,
35,
Chort
3,
11-13
11-13
(Belt
Shifter).
.3, 4,
11-13,
...
20, 21
3, 12
(Stop Motion). . 19
28,
Needle
Setting
Lever. 10, 32
3, 17
3, 4, 18
5, 6, 8, 18, 28
6,
16,
Ports
May
Couse
9,
14,
..12,
List
Cutting
and
Safety
Devices
Sewing
Hook,
Assembly.
Description
,
,
Needle
Regulating
Setting
Lever
Lock
Changing
Maximum
Lever
Engaging
Lever
Rod,
over
Twice
Buttonhole
Guard
Oil
Flow
and
Timing
(Stop Motion} 19
(Belt
Shifter}
Recommended...3, 4, 5
Handle
Clearance
on
,
,
Safety
Safety
Adjustment
,
,
Gears
Width 10, 24, 34
30
36
28
16
13
36
17
21
22
28
29
29
9
Sewing
Sewing
Speed,
Starting
Starting
Stitch
Stitching
Some
Stitch
Stop
Cam
Stop Com Geor Spring 20, 21
Stop
Motion 19-21
Stop
13
3, 9
3, 9
31
20
19
16
16
17
18
22
31
10
3
5
3, 6
16
11
6
7
33
33
26
3
31
26
11
36
36
9
13
6
8
18
5
37
29
14
Motion,
Clearance
Rod
,
,
,
,
,
,
,
,
Take-up
Tension,
,
,
,
Tension
Thread
Thread
Fraying,
Thread
Threading
Tie
Stitch
Tipping
for
Adjustments
Top
Cording
Trip
Lever
Tripping
Tripping
(Feed
Tripping
Tripping
Tripping
Tripping
Two-speed
Under
Thread
Unfinished
Upper
Thread
Clamping
Upper
Threod
Wheel
Gears
Whipstitch
Width of
Width of
Winding
between
Guide
and
CIcoronce
and
Interlocking
Excess
and
Pinion
Half
Speed
High
Point
Removing
Replacing
Gear
Spring 20, 21
Stop-position
Interlocking
Lock
Pin
between
Ploy
between
Position
of Com 19
the
Pulleys
the
Stop
Notch
TensiononInterlocking
Spring
Driving
Knife
Interlocking
Lever
Bar
Spring
Spring
Rod 19
Threads
Releaser
Breaking
Cutting
the
or
Remedies
Machine
(Barring)
Latch
Function
Lever
Clearance
Wheel)
Plote
Point
(Barring)
Points
(Feed
Safety
Belt
Cutting
Buttonhole,
Cutting
Wheel)
Lock
Shifter
Blade
completing.
and
Blades
Cutting
(Feed)
Com.;
Buttonhole
Borring
Stitches
Bight
the
Bobbin
3, 5
3, 9
3, 30, 31, 35,
3,
3, 4, 1.1-13
4, 10
3, 19-21
Com
Foce
Rod 20
Com
Cam
Rod....19
9,
11,
32,
36
7, 11
28-30
7, 8, 11
33
4, 5, 7, 14, 15
25
15
21
...31
25
22
30
3, 9
28
...
28-30,
35,
36
35,
36
11-13
3, 4, 7, 9
24,
34
10,
33,
34
36
31
3
31
6
31
35
30
9
4
21
20
19
19
21
19
14
17
17
14
11
3
9
8
o
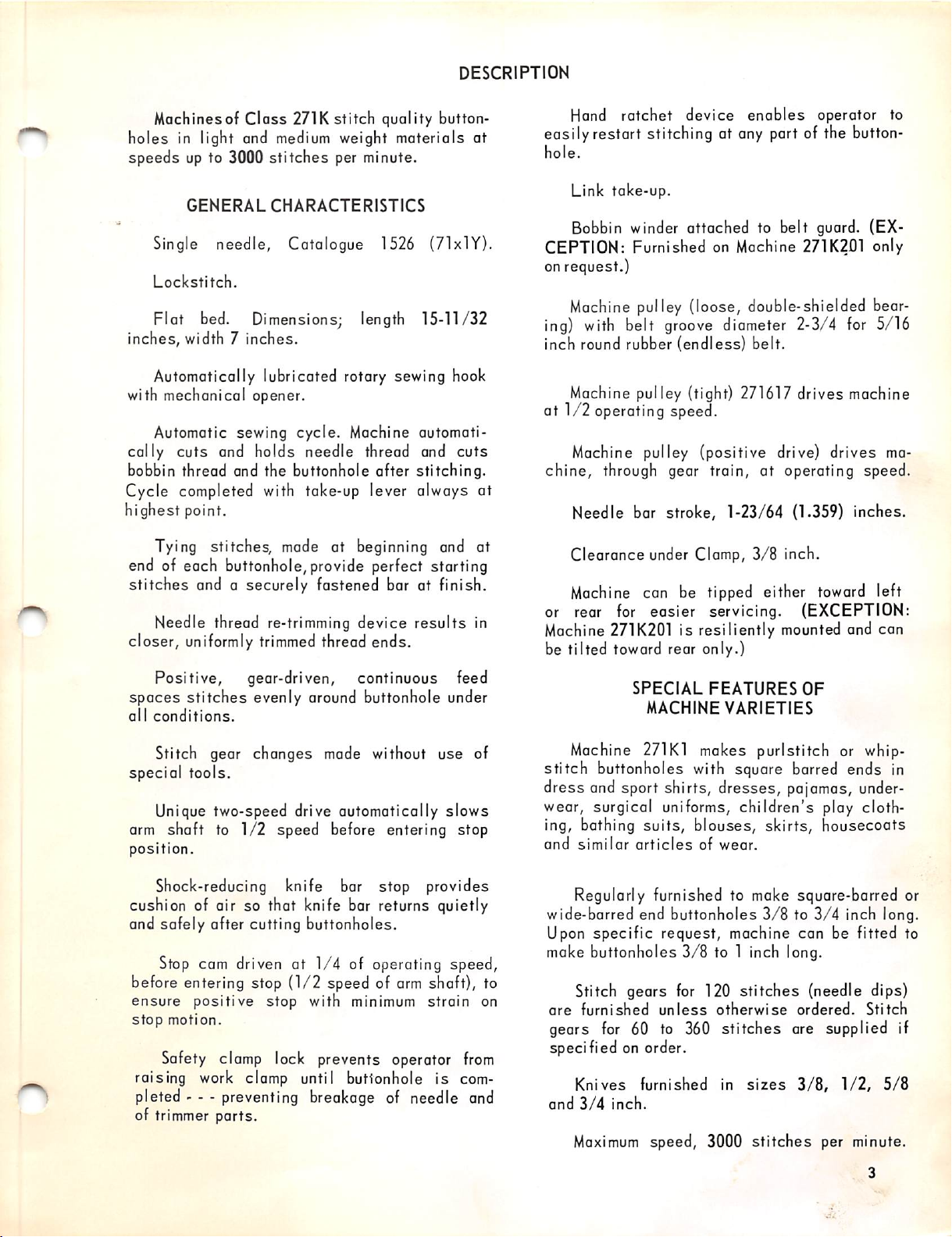
DESCRIPTION
Machinesof
holes in light end
speeds up to 3000
GENERAL
Class
271Kstitch quality button
medium
stitches
CHARACTERISTICS
weight materials at
per minute.
Single needle, Catalogue 1526 (71x1Y).
Lockstitch.
Fiat
inches, width 7 inches.
bed.
Dimensions;
length
15-11/32
Automatically lubricated rotary sewing hook
with mechanical opener.
Automatic sewing cycle. Machine automati
cally
cuts
and holds needle thread and
cuts
bobbin thread and the buttonhole after stitching.
Cycle completed with take-up lever always at
highest point.
Tying stitches,
made
at beginning and at
end of each buttonhole,provide perfect starting
stitches
and a securely fastened bar at finish.
Needle thread re-trimming device results in
closer, uniformly
trimmed
thread ends.
Hand ratchet device
easily restart stitching at any part of the
hole.
Link take-up.
Bobbin
CEPTION: Furnished on Machine
winder attached to belt guard. (EX
enables
operator to
button
271K201
only
onrequest.)
Machine pulley (loose, double-shielded bear
ing)
with
belt
groove
inch round rubber
diameter 2-3/4
(endless)
belt.
for
5/16
Machine pulley (tight) 271617 drives machine
at
1/2
operating speed.
Machine pulley (positive drive) drives ma
chine,
through gear train, at operating speed.
Needle bar stroke, 1-23/64 (1.359) inches.
Clearance under Clamp,
Machine
can be tipped either
3/8
inch.
toward
left
or rear for easier servicing. (EXCEPTION:
Machine
271K201
is resiliently mounted and can
be tilted toward rear only.)
Positive, gear-driven, continuous feed
spaces
all
stitches
conditions.
evenly around buttonhole under
Stitch gear changes made without use of
speciol tools.
Unique two-speed drive automatically
arm shaft to
position.
1/2
speed before entering stop
slows
Shock-reducing knife bar stop provides
cushion of air so that knife bar returns quietly
and safely after cutting buttonholes.
Stop com driven at 1/4 of operating speed,
before entering stop (1/2 speed of
ensure
stop
positive stop with
motion.
Safety clamp lock prevents operator
raising work clamp until buttonhole is com
arm
minimum
shaft), to
strain on
from
pleted - - - preventing breakage of needle and
of trimmer parts.
Machine
stitch
SPECIAL
MACHINE
271K1
buttonholes with square barred ends in
FEATURES
VARIETIES
OF
makes purlstitch or
whip
dress and sport shirts, dresses, pajamas, under
wear, surgical uniforms, children's play cloth
ing, bathing
and
similar
suits,
articles
blouses, skirts, housecoats
of
wear.
Regularly furnished to make square-barred or
wide-barred end buttonholes
3/8to3/4
inch long.
Upon specific request, machine can be fitted to
make buttonholes
Stitch gears for 120
are
furnished
gears
specified on order.
and
for
60 to 360 stitches are supplied if
Knives furnished in
3/4
inch.
Maximum
3/8
to 1 inch long.
unless
speed, 3000
otherwise
stitches
sizes
stitches
(needle dips)
ordered.
3/8,
Stitch
1/2,
per minute.
5/8
3
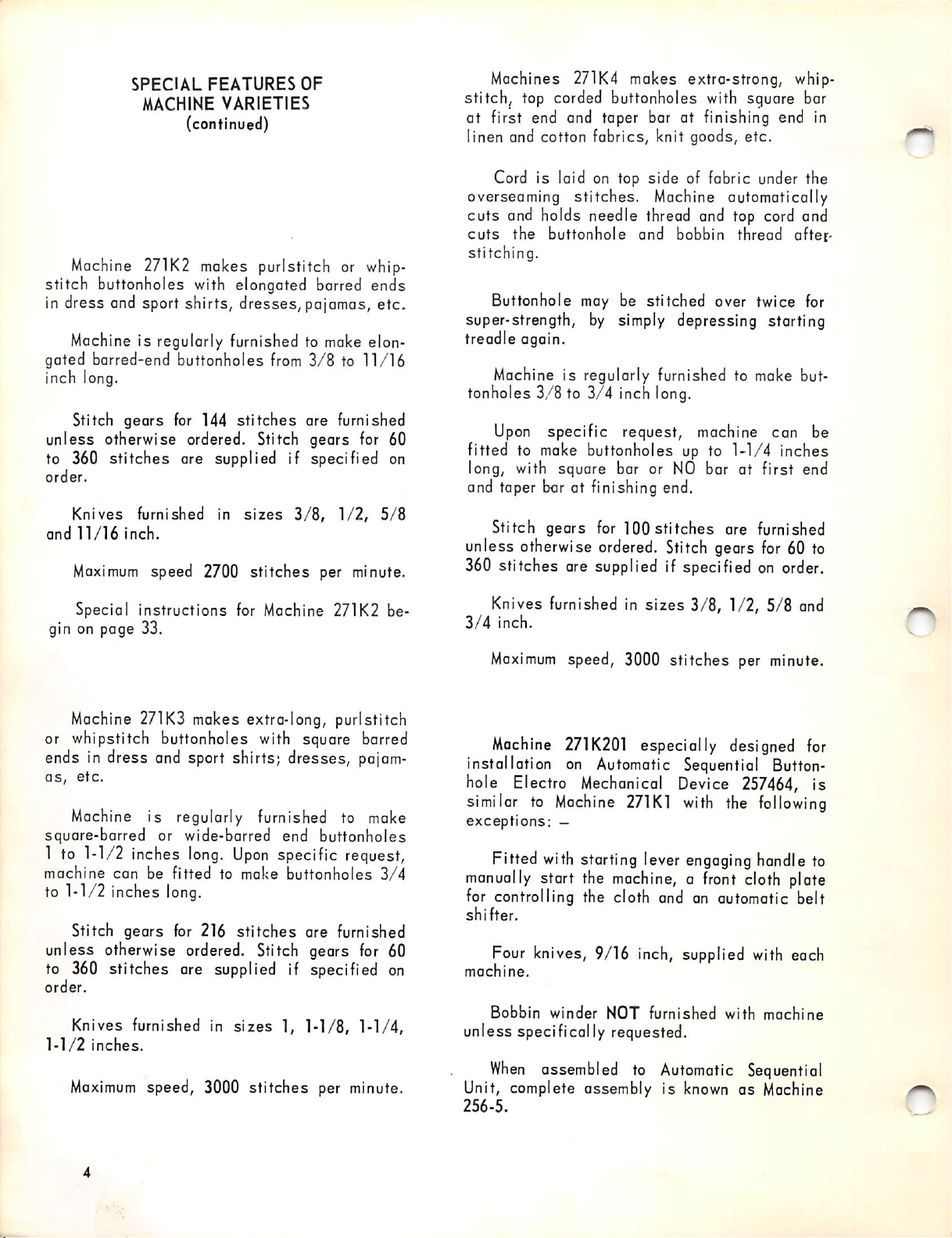
SPECIAL
MACHINE
FEATURES
VARIETIES
OF
(continued)
Machine
271K2
makes purlstitch or
whip
stitch buttonholes with elongated barred ends
in dress
gated bcrred-end buttonholes
inch long.
unless otherwise ordered. Stitch gears for 60
to 360
order.
and
sport shirts, dresses, pajamas, etc.
Machine is regularly furnished to
from
for
144
Stitch gears
stitches
are supplied if specified on
stitches
make
elon
3/8
to 11/16
are furnished
Machines
stitch,
at first end and taper bar at finishing end in
linen and cotton fabrics, knit goods, etc.
top
Cord is laid on top side of fabric under the
271K4
corded
makes extra-strong, whip
buttonholes
with
square bar
overseaming stitches. Machine automatically
cuts and holds needle thread and top cord and
cuts
the
buttonhole
stitching.
Buttonhole
super-strength,
treadle again.
Machine is regularly furnished to moke but
may
by
and
bobbin
be stitched over twice for
simply
depressing starting
thread
aftet-
tonholes 3/8 to 3/4 inch long.
Upon
fitted to
long, with square bar or
specific request, machine can be
moke
buttonholes up to 1-1/4 inches
NO
bar at first end
and taper bar at finishing end.
Knives furnished in
and
11/16
Maximum
Special instructions for Machine 271K2 be
gin on page 33.
Machine
inch.
speed 2700
271K3
makes extra-long, purlstitch
sizes
stitches
3/8,
1/2,
per minute.
5/8
or whipstitch buttonholes with square barred
ends in dress and sport shirts; dresses,
as,
etc.
Machine
square-barred or wide-barred end buttonholes
1 to 1-1/2 inches
machine
is regularly furnished to make
long.
Upon
specific request,
can
be
fitted
to moke
buttonholes
pajam
3/4
to 1-1/2 inches long.
Stitch gears
for
216
stitches
are furnished
unless otherwise ordered. Stitch gears for 60
to 360 stitches are supplied if specified on
order.
Knives furnished in
1-1/2
inches.
Maximum
speed, 3000 stitches per minute.
sizes
1, 1-1/8, 1-1/4,
Stitch gears
unless otherwise
360 stitches are supplied if specified
Knives furnished in
3/4
inch.
Maximum
Machine
installation
hole Electro
similar
exceptions:
manually
Fitted
to
with
start the
for
100
ordered.
stitches
Stitch
sizes
are furnished
gears
for
on
order.
3/8, 1/2, 5/8 and
speed, 3000 stitches per minute.
271K201
on
Mechanical
Machine
—
starting
especially designed
Automatic
Sequential
Device
271K1
lever
with
engaging
machine,afront
Button
257464,
the
following
handle
cloth plate
60 to
for controlling the cloth and an automatic belt
shifter.
Four knives, 9/16 inch, supplied
machine.
Bobbin winder NOT furnished with
with
machine
each
unless specifically requested.
When
Unit, complete assembly is
256-5.
assembled to
Automatic
known
Sequential
as Machine
o
for
is
to
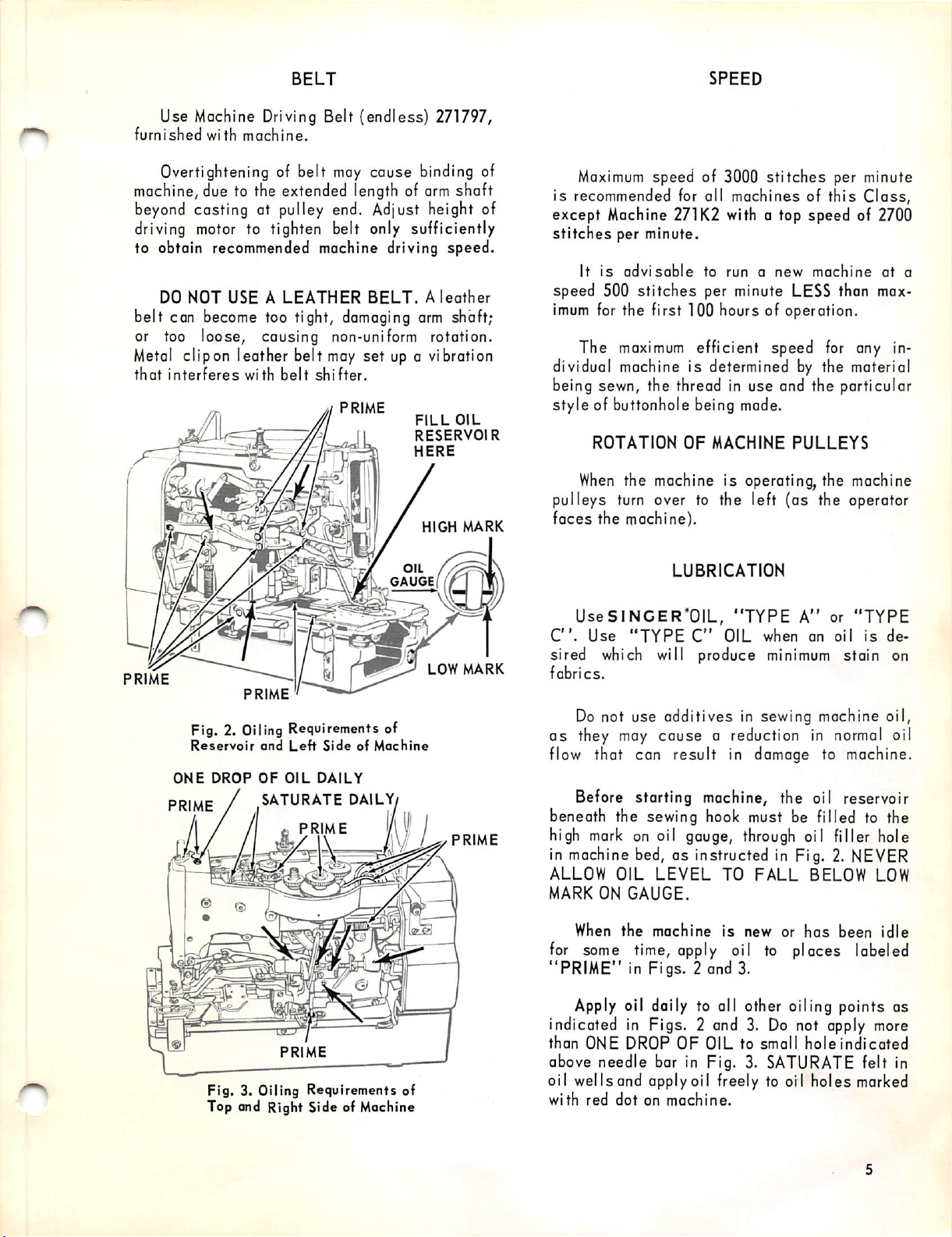
BELT
SPEED
Use Machine Driving Belt
furnished
with
machine.
Overtightening of belt
(endless)
may
cause binding of
2T\19I,
machine, due to the extended length of arm shaft
beyond
driving
casting at pulley end. Adjust height of
motor
to tighten belt only sufficiently
to obtain recommended machine driving speed.
DO
NOT
belt can
USEALEATHER
become
too tight, damaging
BELT.Aleather
arm
shaft;
or too loose, causing non-uniform rotation.
Metal
that
clipon leather belt
interferes
with
belt
may
shifter.
PRIME
set up a vibration
FILL
OIL
RESERVOIR
HERE
HIGH
MARK
OIL
GAUGE
Maximum
is recommended for all machines of
except
stitches
It
is
speed 500
imum
for the first 100 hours of operation.
The
dividual machine is determined
speed of 3000
Machine
per minute.
advisable
stitches
maximum
stitches
this
271K2
with
to run a
a top speed of 2700
new
machine
per minute LESS than max
efficient speed
for
by
the material
per minute
Class,
at
any in
being sewn, the thread in use and the particular
style of buttonhole being made.
ROTATION
When
the
OF
machine
MACHINE
PULLEYS
is operating, the machine
pulleys turn over to the left (as the operator
faces
the machine).
LUBRICATION
a
r\
PRIME
PRIME
Fig. 2. Oiling Requirements of
Reservoir
ONE
DROP
PRIME
Fig. 3. Oiling Requirements of
Top and Right Side of Mochine
and
Left
OF
OIL
SATURATE
PRIME
PRIME
SideofMachine
DAILY
DAILY
LOW
MARK
PRIME
UseSINCER'OIL,
C".
Use
"TYPE
sired which will produce
fabrics.
Do
not use additives in sewing machine oil,
as
they
may
cause a reduction in
C"
"TYPE
OIL
A" or "TYPE
when on
minimum
oil
is
stain on
normal
de
oil
flow that can result in damage to machine.
Before starting machine, the oil reservoir
beneath the sewing
high
markonoil gauge,
machine
in
ALLOW OIL
MARK ON
When
for
some time, apply oil to places labeled
bed,
LEVEL
GAUGE.
the
machine is new or
hook
must be filled to the
through
oil filler hole
as instructed in Fig. 2.
TO
FALL
BELOW LOW
has
NEVER
been
idle
"PRIME" in Figs. 2 and 3.
Apply
indicated in Figs. 2 and 3.
than
oil daily to all other oiling points as
Do
not
ONE
DROP
OF
OIL to
small
hole
apply
indicated
more
above needle bar in Fig. 3. SATURATE felt in
oiI
wel
with
Is and applyoiI freely to oiI holes
red
dot
on
machine.
marked
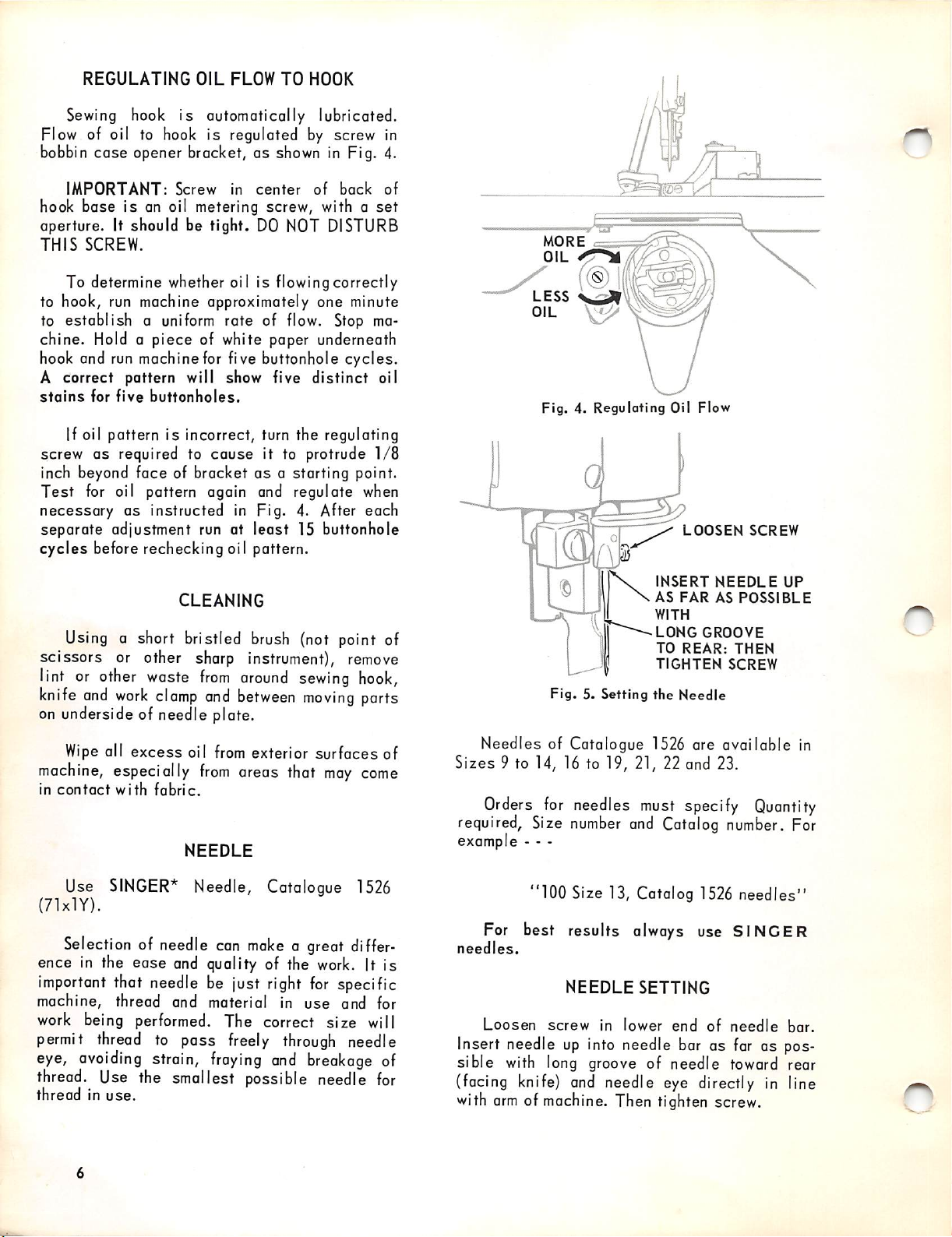
REGULATING
OIL
FLOW
TO
HOOK
Sewing hook
is
automatically lubricated.
Flow of oil to hook is regulated by screw in
case
bobbin
IMPORTANT:
hook base is an oil metering screw, with a
aperture. It should be tight.
THIS
SCREW.
opener bracket, as shown in Fig. 4.
Screw
in
center
of
back
of
set
DO
NOT
DISTURB
To determine whether oil is flowing correctly
to hook, run machine approximately one minute
to
establish
a uniform rate of flow. Stop ma
chine. Hold a piece of white paper underneath
hook and run machine for five buttonhole cycles.
A correct pattern will show five
stains
for
five
buttonholes.
distinct
oil
If oil pattern is incorrect, turn the regulating
screw
inch beyond face of bracketasa starting point.
Test
necessary
as
required to
cause
it to protrude
for oil pattern again and regulate
as
instructed in Fig. 4. After each
1/8
when
separate adjustment run at least 15 buttonhole
cycles
before rechecking oi I pattern.
ir^sr
MORE
OIL
Fig. 4. Regulating Oil Flow
LOOSEN
SCREW
CLEANING
Using a short bristled brush (not point of
scissors or other sharp instrument),
lint or
knife
and
other
work
waste
clamp
from
and
around
between
sewing
remove
moving
on underside of needle plate.
Wipe
all
excess
machine,
in
contact
Use
(71xlY).
especially
with
SINGER*
Selection of needle can
enceinthe ease and quality of the
important
machine, thread and material In
work being performed. The correct
permit
eye,
that needle be just
thread
avoiding
oil
from
from
areas that
fabric.
NEEDLE
Needle, Catalogue
to pass
strain,
freely
fraying
exterior
make
right
through
and
surfaces
may
a great
work.
for
use
size
breakage
differ
specific
and for
needle
thread. Use the smallest possible needle
threadinuse.
hook,
ports
come
1526
It is
will
for
of
of
Fig.5.Setting
INSERT
AS
WITH
LONG
TO
TIGHTEN
the
FAR
GROOVE
REAR:
Needle
NEEDLE
AS
POSSIBLE
THEN
SCREW
Needles of Catalogue 1526 are available in
Sizes 9 to 14, 16 to 19, 21, 22 and 23.
Orders
required.
example - - -
For best results always use
needles.
Loosen
Insert needle
sible
(facing
with
arm
for
needles
Size
number
"100 Size 13, Catalog
NEEDLE
screw
up
into
with
long groove of needle toward rear
knife)
and
must
specify
and
Catalog
1526
SETTING
in lower
end
of
needle bar as far as pos
needle eye directlyinline
of machine. Then tighten screw.
number.
needles"
SINGER
needle
UP
Quantity
For
bar.
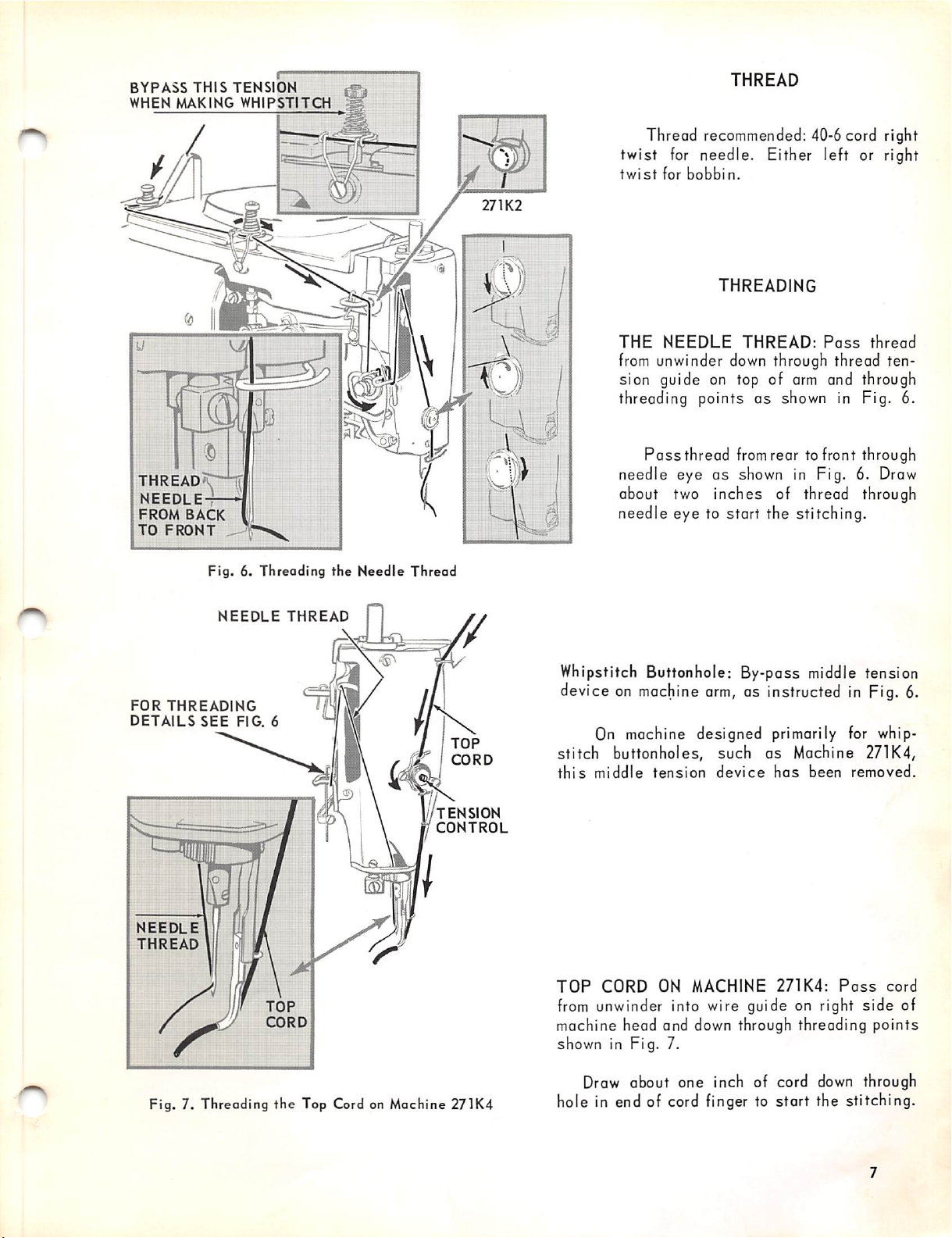
BYPASSTHIS
WHEN MAKING WHIPSTITCH M
THREADS
NEEDLEFROM
TO
FRONT
BACK
TENSION
^
271K2
THREAD
Thread recommended: 40-6 cord right
twist
twist
THE
from
sion guide on top of
for
needle. Either left or right
for
bobbin.
THREADING
NEEDLE
unwinder
THREAD:
down
through thread ten
arm
Pass
thread
and through
threading points as shown in Fig. 6.
Pass
thread
from
rear to front through
needle eye as shown in Fig. 6. Draw
about two inches of thread through
needle eye to start the stitching.
FOR
THREADING
DETAILS
NEEDLE
THREAD
Fig.
NEEDLE
SEE
6. Threading
THREAD
FIG.
6
TOP
CORD
the
Needle
Thread
TENSION
CONTROL
TOP
CORD
Whipstitch Buttonhole: By-pass middle tension
device on machine
arm,
as instructed in Fig. 6.
On machine designed primarily for whip
stitch buttonholes, such as Machine 271K4,
this
middle
TOP
CORD
from
unwinder into wire guide on right
tension
ON
device
MACHINE
has
271K4:
been
removed.
Pass
side
cord
of
machine head and down through threading points
shown in Fig. 7.
Draw about one inch of cord
Fig. 7. Threading
the
Top Cord on Machine 271K4
hole in end of cord finger to start the stitching.
down
through
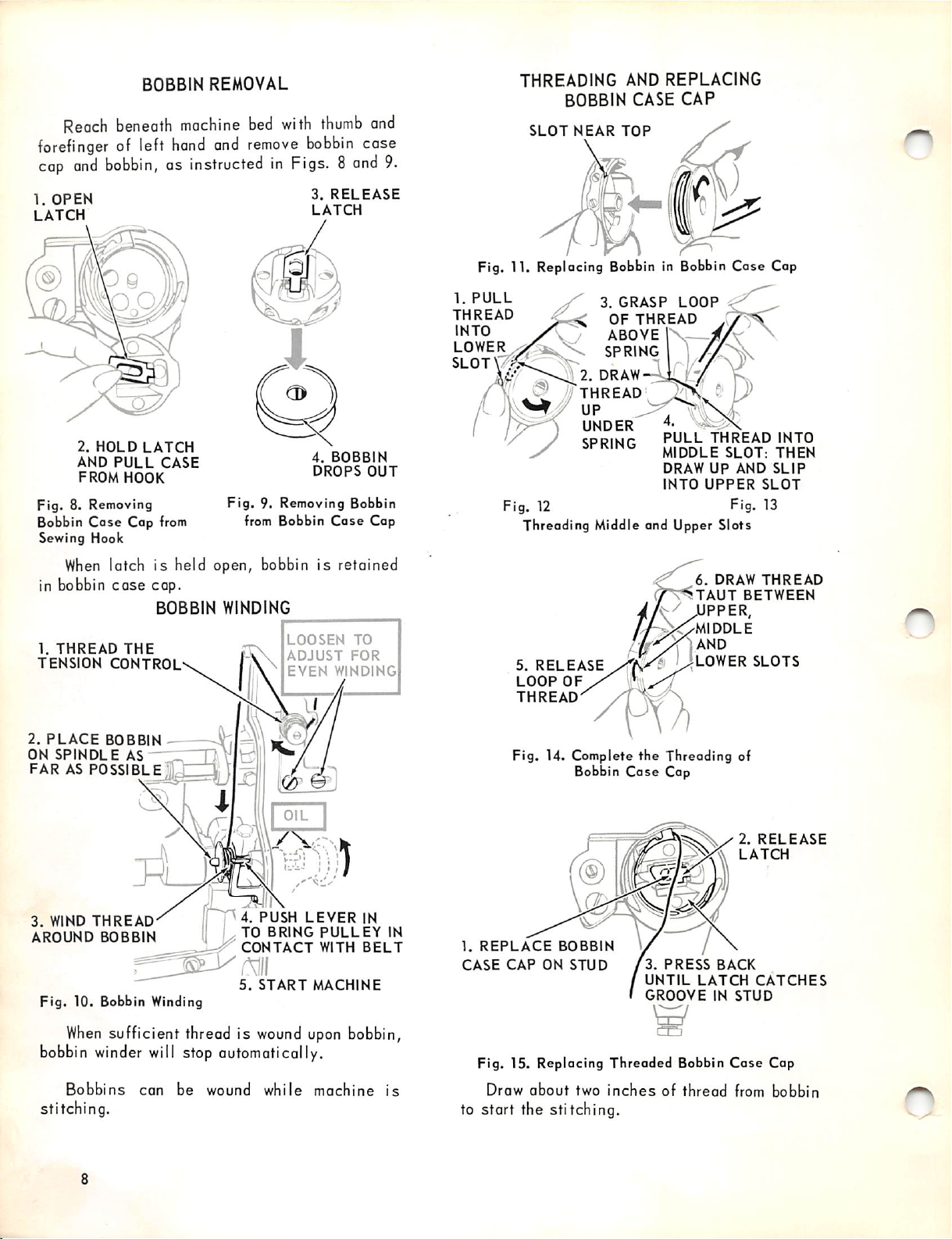
Reach
forefinger
cop
and
1.
OPEN
LATCH
BOBBIN REMOVAL
beneath
of left
machine
hand
and
bed
with
remove
thumb
bobbin
bobbin,asinstructedinFigs. 8
3.
RELEASE
LATCH
case
and
and
9.
THREADING
BOBBIN CASE
SLOT
NEAR
AND
TOP
REPLACING
CAP
2.
HOLD
AND
FROM
Fig.
8. Removing
Bobbin
Case
Sewing Hook
When
in bobbin
1.
THREAD
TENSION
LATCH
PULL
HOOK
Cop from
CASE
Fig.9.Removing
from Bobbin
4.
BOBBIN
DROPS
Case
OUT
Bobbin
Cap
latch is held open, bobbinisretained
case
cop.
BOBBIN
THE
CONTROL^
WINDING
LOOSEN
ADJUST
EVEN
TO
FOR
WINDING
Fig. 11. Replacing
1.
PULL
THREAD
INTO
LOWER
SLOT
Fig.
12
Threading
5.
RELEASE
LOOP
THREAD
BobbininBobbin
3.
GRASP
OF
THREAD
ABOVE
SPRING
DRAW
THREAD
UP
UNDER
SPRING
Middle and Upper
OF
LOOP
4.
PULL
MIDDLE
DRAW
INTO
6.
TAUT
.UPPER,
MIDDLE
lAND
LOWER
Cose Cop
THREAD
SLOT:
UP
UPPER
Fig. 13
Slots
DRAW
THEN
AND
SLIP
SLOT
THREAD
BETWEEN
SLOTS
INTO
o
2,
PLACE
ON
SPINDLE
FAR
AS
POSSIBLl
3.
WIND
THREAD
AROUND
Fig.
10. Bobbin Winding
When
bobbin
winder
Bobbins
stitching.
BOBBIN
AS
BOBBIN
sufficient thread is
will
stop automatically.
con be wound
4.
PUSH
TO
BRING
CONTACT
5.
START
wound
while
LEVER
PULLEY
WITH
MACHINE
upon
machine
IN
IN
BELT
bobbin,
is
Fig.
1.
REPLACE
CASE
CAP
ON
14. Complete
Bobbin
BOBBIN
STUD
the
Case
3.
UNTIL
GROOVE
Threading
Cap
PRESS
\:r7
Fig. 15. Replacing Threaded Bobbin
Draw
about
two
inchesofthread
to start the stitching.
BACK
LATCH
IN
Cose
of
2.
RELEASE
LATCH
CATCHES
STUD
Cap
from bobbin
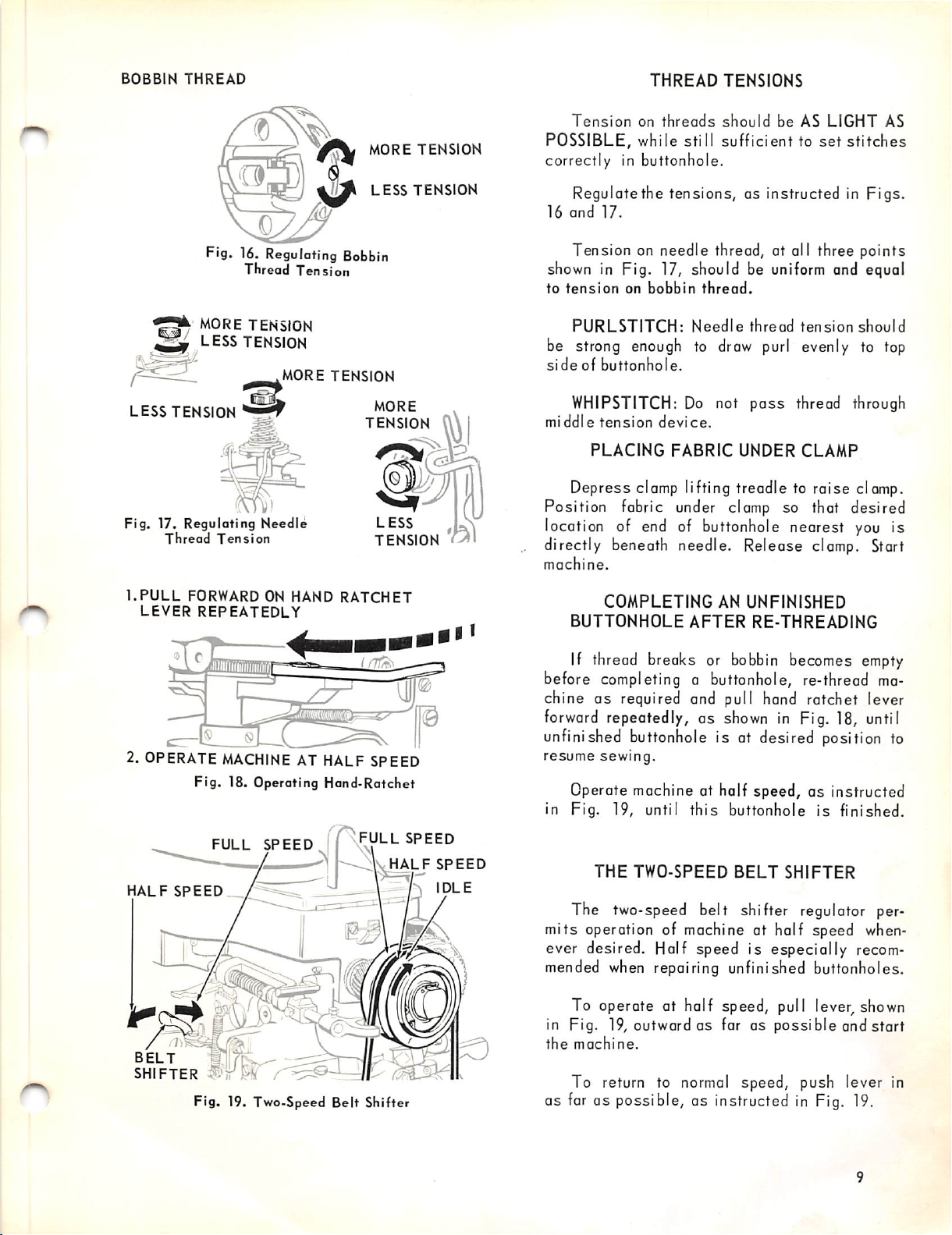
BOBBIN
THREAD
THREAD
TENSIONS
LESS
Fig.
TENSION
17.
Regulating
Thread
Fig. 16.
more
LESS
Tension
Regulating
Thread
tension
tension
.MORE
Needle
Tension
tension
MORE
LESS
Bobbin
MORE
TENSION
TENSION
TENSION
TENSION
Tension
POSSIBLE, while
on
threads
still
should
be
AS
sufficienttoset
LIGHT
stitches
AS
correctly in buttonhole.
Regulatethe tensions, as instructed in Figs.
16
and
17.
Tension on needle thread, at all three points
shown in Fig. 17, should be uniform and equal
to
tension
PURLSTITCH:
on
bobbin
thread.
Needle
thread
tension
should
be strong enough to draw purl evenly to top
sideofbuttonhole.
WHIPSTITCH: Do not
middle
tension
PLACING
device.
FABRIC
pass
UNDER
thread through
CLAMP
Depress clamp lifting treadle to raise clamp.
Position fabric under clamp so that desired
location of end of buttonhole nearest
you
is
directly beneath needle. Release clamp. Start
machine.
1.PULL
LEVER
FORWARD ON HAND
REPEATEDLY
2. OPERATE
Fig.
HALF
SPEED
RATCHET
MACHINE
18. Operating Hand-Ratchet
FULL
AT HALF SPEED
SPEED
'^FULL
SPEED
HALF
SPEED
COMPLETING
BUTTONHOLE
If thread breaks or
before completing a buttonhole, re-thread
AN
AFTER
UNFINISHED
RE-THREADING
bobbin
becomes
empty
ma
chine as required and pull hand ratchet lever
forward
repeatedly, as
showninFig.
18,
until
unfinished buttonhole is at desired position to
resume
in Fig. 19, until
sewing.
Operate machine at half speed, as instructed
this
buttonhole is finished.
THE
TWO-SPEED
BELT
SHIFTER
The two-speed belt shifter regulator per
mits operation of machine at half speed when
ever desired. Half speed is especially
mended
when
repairing unfinished buttonholes.
To operate at half speed, pull lever,
in Fig. 19, outward as far as
the
machine.
possible
recom
and
shown
start
SHIFTER
Fig. 19. Two-Speed Belt Shifter
To return to normal speed, push lever in
as far as possible, as instructed in Fig. 19.
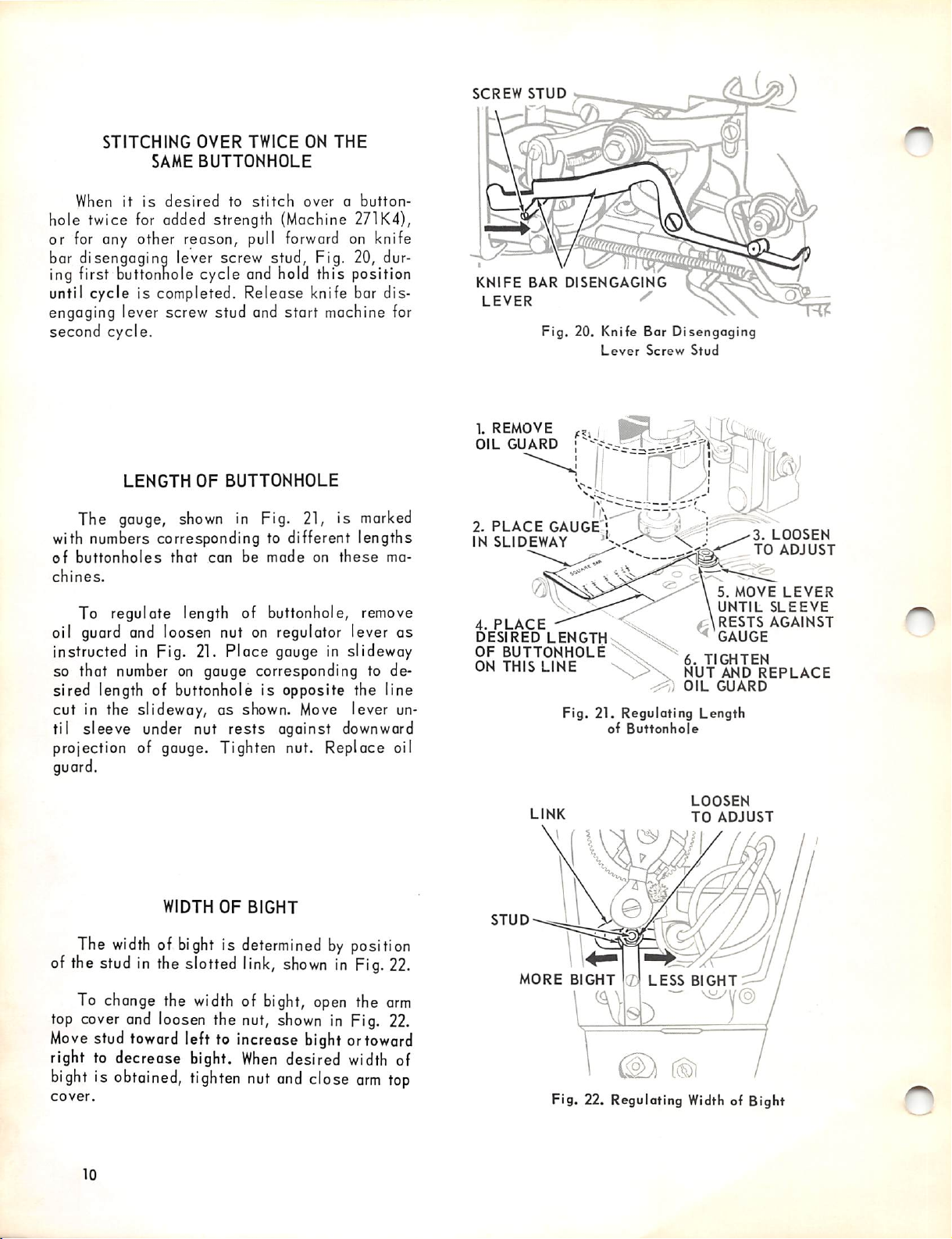
SCREW
STUD
STITCHING
When it
is
SAME
desired
OVER
BUTTONHOLE
to
TWICE
stitch
ON
THE
overabutton
hole twice for added strength (Mochine 271K4),
or for any other reason, pull
forward
on knife
bar disengaging lever screw stud, Fig. 20, dur
ing first buttonhole cycle and hold this position
until cycle is completed. Release knife bar dis
engaging lever screw stud and start machine for
second
cycle.
LENGTH
The gauge,
OF
BUTTONHOLE
shown
in Fig.
21,
is
marked
with numbers corresponding to different lengths
of
buttonholes
chines.
that
con
be
made
on
these
ma
To regulate length of buttonhole, remove
oil guard and loosen nut on regulator lever as
instructed in Fig. 21.
so that number
on
sired length of buttonhole
cut in the slideway, as
til
sleeve
under nut
Place
gauge in slideway
gauge corresponding to de
is
opposite the line
shown.
rests
Move
lever
against downward
un
projection of gauge. Tighten nut. Replace oil
guard.
KNIFE
LEVER
1.
REMOVE
OIL
GUARD
2.
PLACE
IN
SLIDEWAY
4.
PLACE
DESIRED
OF
BUTTONHOLE
ON
THIS
BAR
Fig.
GAUGE'5
LENGTH
LINE
DISENGAGING
20. Knife Bar
Lever
Fig.
21.
Regulating
of
Buttonhole
Disengaging
Screw
^
6.
NUT
OIL
Stud
5.
UNTIL
RESTS
GAUGE
TIGHTEN
AND
GUARD
Length
'3.
TO
MOVE
REPLACE
LOOSEN
ADJUST
LEVER
SLEEVE
AGAINST
WIDTH
The
widthofbightisdeterminedbyposition
of the stud in the slotted
To change the
top
cover
and loosen the nut,
Move
stud
toward
right to decrease bight.
bightisobtained,
cover.
10
OF
BIGHT
link,
width
showninFig.
of bight,
shown
open
in Fig.
the
22.
arm
22.
left to increase bight ortoward
When
tighten
nut
desired
and
close
width
arm
of
top
STUD
MORE
BIGHT
I'M
Fig. 22. Reguloting
LESS
'T
^ ' 1
—
LOOSEN
TO
ADJUST
BIGHT
Width
of Bight
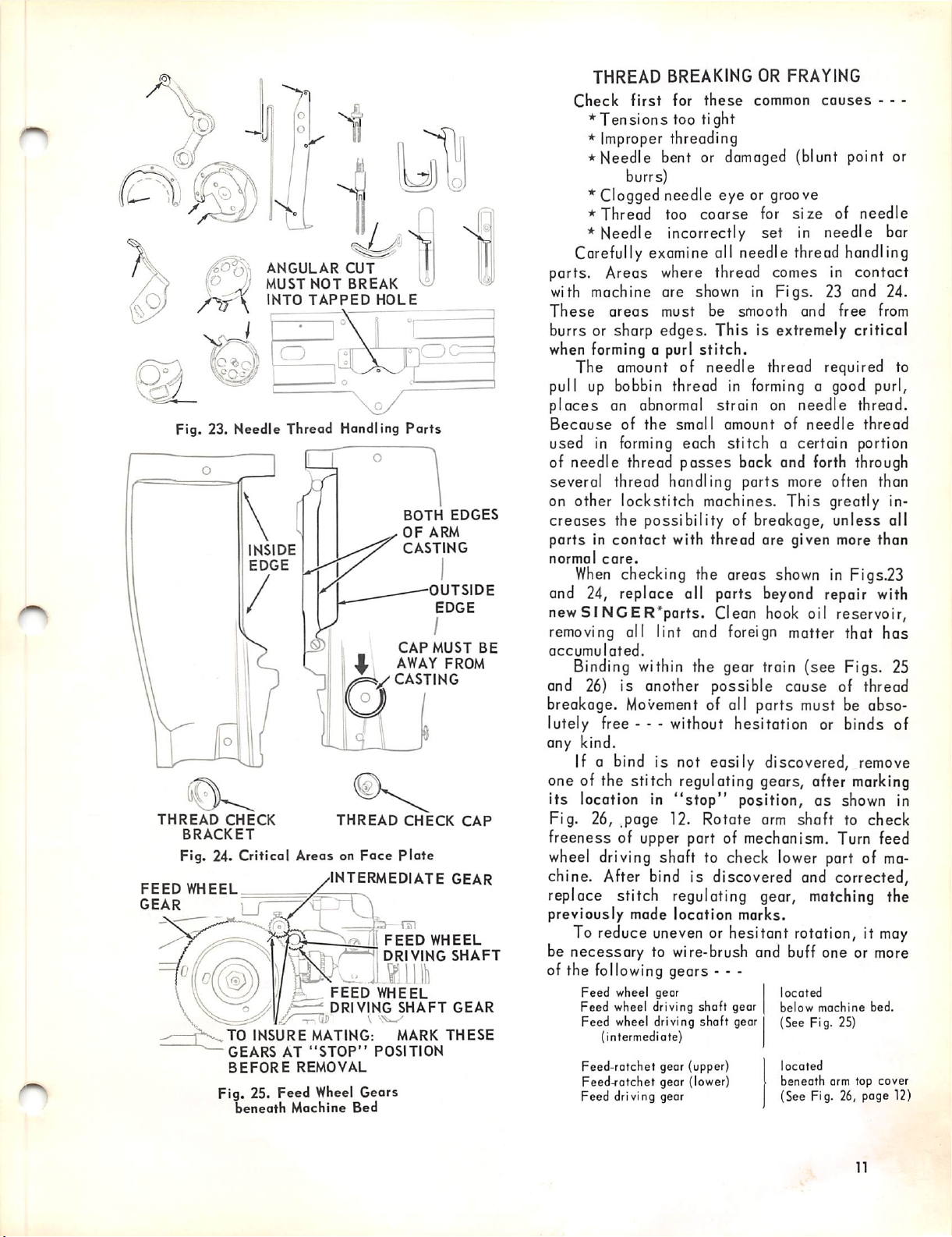
angular
r
Jj
MUST
NOT
/V\
into
TAPPED
/
C
Fig. 23. Needle Thread Handling
CT
INSIDE
EDGE
THREAD
FEED
GEAR
CHECK
BRACKET
Fig.
24.
Critical
WHEEL
TO
-GEARS
BEFORE
Fig. 25. Feed Wheel Gears
beneath
INSURE
AT
Areas on
"STOP"
REMOVAL
Machine
MATING;
cut
BREAK
^
HOL^
Parts
BOTH
OF
CASTING
CAP
X
AWAY
CASTING
O
"*
THREAD
INTERMEDIATE
FEED
DRIVING
Bed
Face
13-
FEED
DRIVING
WHEEL
\
'N-
POSITION
CHECK
Plate
rm
!Jih
SHAFT
•
MARK
EDGES
ARM
I
OUTSIDE
EDGE
/
MUST
FROM
CAP
GEAR
WHEEL
SHAFT
GEAR
THESE
BE
THREAD BREAKING OR FRAYING
Check
first
*Tensions
for
these
too tight
common
causes
- - -
* Improper threading
* Needle bent or damaged (blunt point or
burrs)
* Clogged needle
★Thread
too
eye
coarse
or groove
for
size
of
needle
* Needle incorrectly set in needle bar
Carefully examine all needle thread handling
parts. Areas where thread comes in contact
with machine are shown in Figs. 23 and 24.
These
areas
must
be
smooth
and
free
from
burrs or sharp edges. This is extremely critical
when
forming
a purl stitch.
The amount of needle thread required to
pull up bobbin thread in
places
Because
used in
of needle thread
an abnormal strain on needle thread.
of
the
small
forming
amount
each stitch a certain portion
passes
forming
bock and forth through
a good purl,
of
needle
thread
several thread handling parts more often than
on other lockstitch machines. This greatly in
creases
the
possibility
of breakage,
unless
oil
parts in contact with thread are given more than
normal
and 24, replace all parts
core.
When
checking the areas
shown
beyond
in Figs.23
repair with
newSiNC ER*parts. Clean hook oil reservoir,
removing all lint and foreign matter that
accumulated.
has
Binding within the gear train (see Figs. 25
and
26)
is another possible cause of thread
breakoge.
lutely
Movement
free---
of oil parts must be abso
without hesitation or binds of
any kind.
If a bind is not easily discovered,
one of the stitch regulating gears, after
its location in
"stop"
position, as
remove
marking
shown
Fig. 26, .page 12. Rotate arm shaft to check
freeness of upper port of mechanism. Turn feed
wheel driving shaft to check lower part of
ma
chine. After bind is discovered and corrected,
replace stitch regulating gear,
previously made location marks.
To reduce uneven or hesitant rotation, it
matching
the
may
be necessary to wire-brush and buff one or more
of the following gears - - •
Feed
wheel geor
Feed wheel driving shaft geor
Feed wheel driving shaft gear
(intermediote)
Feed-ratchet geor (upper)
Feed-rotchet gear (lower)
Feed
driving geor
located
belaw
machine
(See Fig. 25)
located
beneath orm top cover
(See Fig. 26, page 12)
bed.
in
11