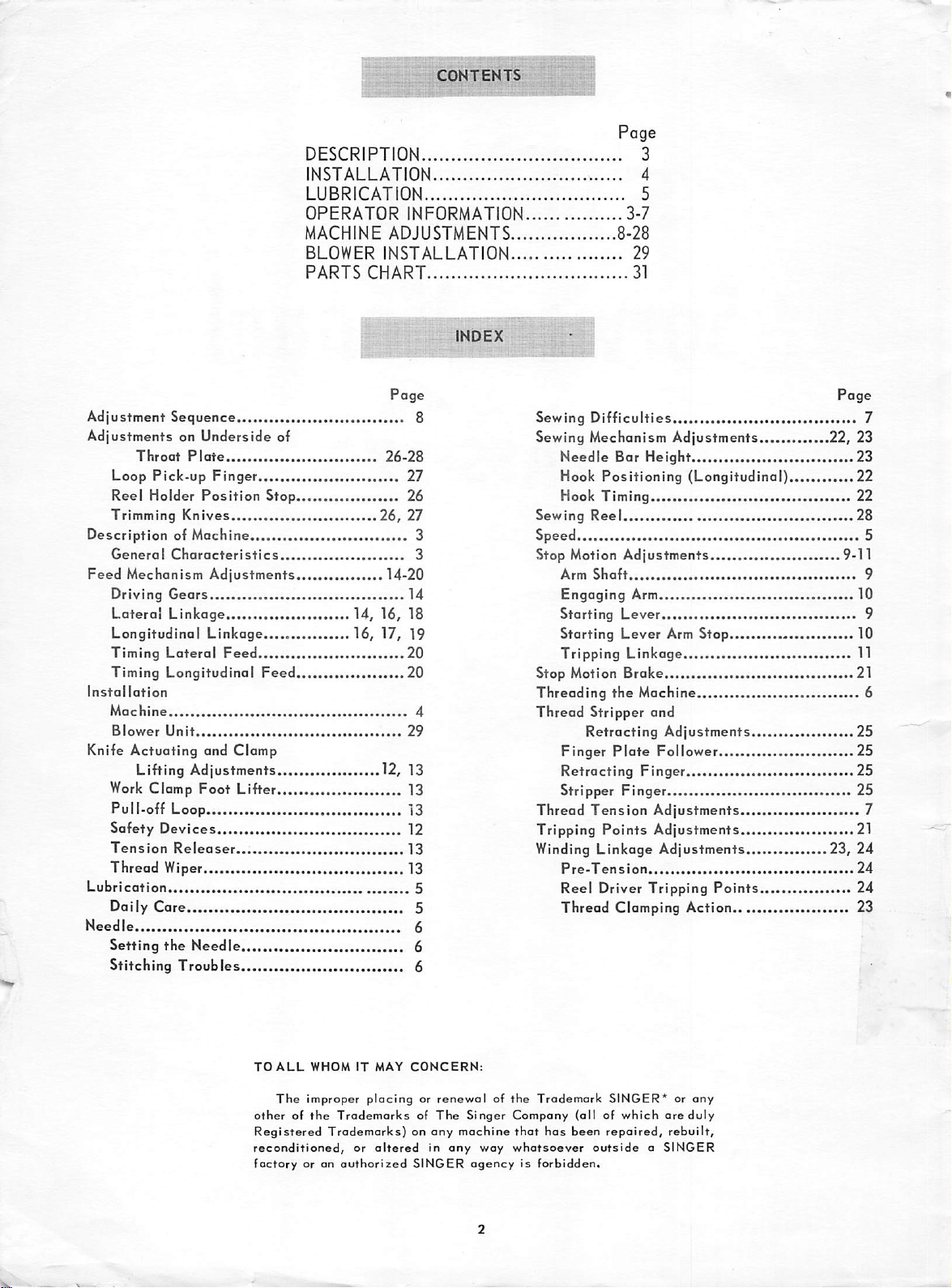
DESCRIPTION
INSTALLATION
LUBRICATION
OPERATOR
MACHINE
BLOWER
PARTS
INFORMATION
ADJUSTMENTS
INSTALLATION
CHART
CONTENTS
Page
3
4
5
3-7
8-28
29
31
INDEX
Adjustment
Adjustments
Loop
Reel
Trimming
Description
General
Feed
Driving
Lateral
Sequence
on
Throat
Pick-up
Holder
Knives
of
Characteristics.
Mechanism
Gears
Linkage....
Longitudinal
Timing
Timing
Installation
Machine
Blower
Knife
Lateral
Longitudinal
Unit
Actuating
Lifting
Work
Clamp
Pull-off
Safety
Tension
Thread
Loop.
Devices
Releaser...
Wiper
Lubrication
Daily
Care
Needle
Setting
Stitching
the
Troubles
Underside
Plate
of
Finger
Position
Stop
Machine..
Adjustments
Linkage
Feed
Feed
and
Clamp
Adjustments
Foot
Lifter....
Needle
8
26-28
27
26
....26,
27
3
3
.......14-20
14
14, 16,
16,
17,
18
19
20
....20
4
29
12,
13
13
13
12
13
13
5
5
6
6
6
Sewing
Sewing
Sewing
Difficulties
Mechanism
Needle
Hook
Hook
Bar
Positioning
Timing...
Reel
Height
Speed
Stop
Motion
Arm
Engaging
Starting
Starting
Tripping
Stop
Motion
Threading
Thread
Adjustments
Shaft........
Arm
Lever
Lever
Linkage
Brake
the
Machine
Stripper
Retracting
Finger
Retracting
Stripper
Thread
Tripping
Winding
Pre-Tension......
Reel
Thread
Plate
Finger
Finger
Tension
Points
Linkage
Driver
Clamping
Adjustments
(Longitudinal)
Arm
Stop
and
Adjustments.
Follower
Adjustments
Adjustments
Adjustments
Tripping
Points
Action..
7
....22,
23
23
22
22
....28
5
9-11
9
10
9
10
11
21
6
25
25
25
25
7
..21
23,
24
24
24
23
TOALL
other
Registered
reconditioned,
foctory
The
improper
of
or
WHOM
IT
placing
the
Trademarks
Trademarks)
or
an
authorized
MAY
CONCERN:
or
of
on
altered
SINGER
renewal
The
Singer
any
machine
in
any
agency
of
the
Compony
that
way
whatsoever
is
Trademork
(all
has
been
forbidden.
SINGER*
of
which
repaired,
outside a SINGER
or
any
are
duly
rebuilt,
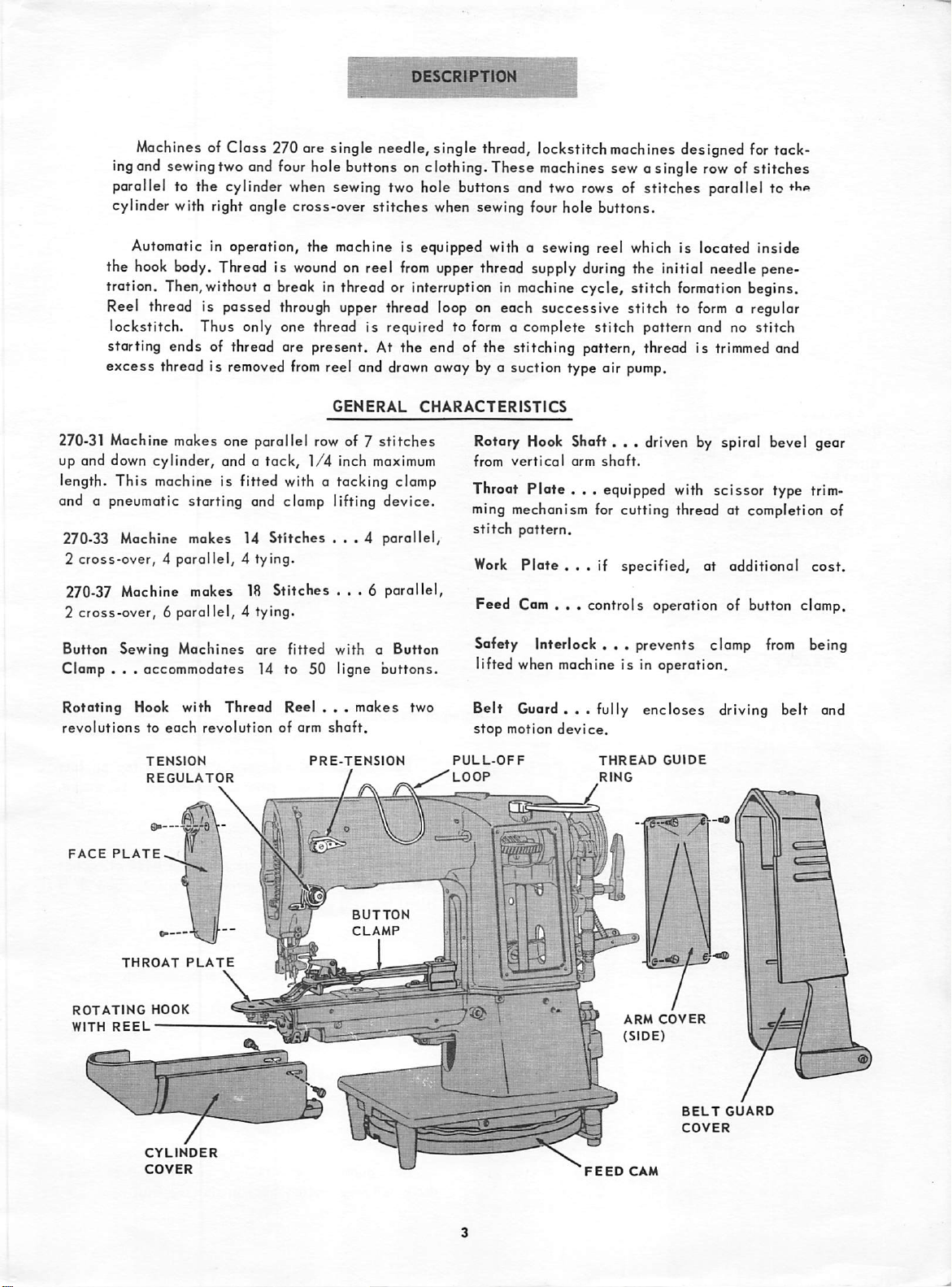
Machines
ing
and
sewing
parallel
cylinder
to
the
with
of
Class
two
and
cylinder
right
angle
270
ore
single
four
hole
buttons
when
sewing
cross-over
needle,
stitches
single
on
clothing.
two
hole
when
thread,
These
buttons
and
sewing
four
lockstitch
machines
two
machines
sew a single
rows
hole
buttons.
of
designed
row
stitches
parallel
for
tack
of
stitches
to
Automotic
the
hook
tration.
Reel
threod
lockstitch.
starting
excess
270-31
up
length.
and a pneumatic
Machine
and
down
270*33
2
cross-over, 4 parallel, 4 tying.
270-37
2
cross-over, 6 parallel, 4 tying.
Button
Clamp
. . .
Rotating
revolutions
thread
cylinder,
This
machine
Machine
Machine
Sewing
accommodates
Hook
to
in
operation,
body.
Threod
Then,
without a break
Is
passed
Thus
only
ends
of
thread
is
removed
makes
each
one
and a tack,
is
fitted
starting
makes
makes
Machines
with
14
Thread
revolution
parallel
and
18
are
14
the
machine
is
wound
on
in
thread
through
one
are
from
with a tacking
clamp
Stitches ... 4
Stitches ... 6 parallel,
fitted
to
Reel
of
upper
thread
present.
reel
GENERAL
row
of 7 stitches
1/4
inch
lifting
with a Button
50
llgne
. . .
arm
shaft.
reel
or
thread
is
required
At
and
drawn
maximum
clamp
device.
parallel,
buttons.
makes
is
equipped
from
upper
interruption
loop
the
end
away
CHARACTERISTICS
two
with o sewing
thread
on
to
form a complete
of
supply
in
machine
each
successive
the
stitching
by a suction
Rotary
from
Throat
ming
stitch
Work
Feed
Safety
lifted
Belt
stop
Hook
vertical
Plate
mechanism
pattern.
Plate
Cam
. . .
Interlock
when
machine
Guard
. . .
motion
device.
reel
which
during
the
initial
cycle,
type
Shaft.
arm
. . . equipped
...
stitch
stitch
stitch
pattern,
for
controls
pattern
thread
air
pump.
. .
driven
shaft.
cutting
if
specified,
operation
. . .
prevents
is
in
operation.
fully
encloses
formation
to
with
thread
is
located
Inside
needle
pene
begins.
form a regular
and
no
stitch
is
trimmed
by
spiral
scissor
at
clamp
and
bevel
type
at
completion
odditional
of
button
from
driving
gear
trim
cost.
clamp.
being
belt
of
and
FACE
PLATE
ROTATING
WITH
REEL
TENSION
REGULATOR
THROAT
HOOK
PLATE
PRE-TENSION
BUTTON
CLAMP
PULL-OFF
LOOP
-r")®
THREAD
RING
I
i
ARM
(SIDE)
GUIDE
COVER

I
STOP
A.
B.
C.
D.
II
KNIFE
ADJUSTMENTS
A.
B.
C.
D.
E.
III
FEED
A.
B.
C.
made
MOTION
Arm
Shaft
1.
Adjust
for
Starting
1.
2.
Engaging
1.
Tripping
1.
2.
Safety
1.
2.
3.
Tension
1.
2.
3.
Work
1.
Thread
1.
2.
Thread
1.
Feed
1.
2.
Feed
1.
2.
3.
4.
Feed
1.
2.
Lever
Set
clearance
machine
Adjust
arm
arm
Adjust
Linkage
Adjust
Set
clearance
ACTUATING
Devices
Set
Lifting
Adjust
surface
Set
Clamp
Releoser
Position
Set
lifting
Set
lifting
Clomp
Position
Wiper
Set
wiper
Position
Pull-off
Adjust
MECHANISM
Driving
Check
Eliminate
Linkage
Center
Increase
feed
bar
Center
age
Increase
ment
of
Timing
Time
longitudinal
Time
lateral
The
sequence
in
the
ADJUSTMENTS
end
ploy
between
pulley
stop
to
obtain
rock
correct
shaft
between
AND
Arm
Lug
lifting
lever
on
lifting
lifter
tension
link
arm
to
Foot
lifter
beneath
lever
stop
regulator
connection
release
Lifter
support
wiper
wire
Loop
tension
on
ADJUSTMENTS
Gears
alignment
play
of
in
gears
Adjustment
and
position
or
decrease
and
position
or
decrease
feed
bar
Adjustment
feed
of
adjustments
order
given
interlocking
"V**
belt
support
bell
crank
CLAMP
pawl
spring
timing
longitudinal
feed
movement
LIFTING
to
clear
tension
arm
hook
marks
lateral
laterol
feed
longitudinal
movement
to
avoid
arm
and
tension
for
binding
and
pawl
engaging
linkage
movement
feed
link
move
outlined
confusion
of
on
this
and
IV
V
STOP
VI
VII
VIII
IX
page
should
unnecessary
TRIPPING
A.
Set
timing
MOTION
A.
Obtain
B,
Adjust
SEWING
A,
B.
REEL
A.
B.
C.
A.
B.
C.
D.
ADJUSTMENTS
A.
B.
C.
MECHANISM
Sewing
1.
Set
2.
Time
Needle
1.
Set
WINDING
Winding
1.
Adjust
Reel
1.
Set
2.
Adjust
Pre-Tension
1.
Adjust
THREAD
ADJUSTMENTS
Finger
1.
Set
Stripper
1.
Adjust
Retracting
1.
Adjust
Tension
1.
Re-check
Reel
Trimming
1.
Set
2.
Time
3.
Adjust
Loop
1.
Position
2.
Set
repetition.
POINTS
to
BRAKE
brake
brake
Hook
longitudinal
hook
Bar
Needle
Linkage
thread
Driver
Tripping
tripping
Extension
to
STRIPPING
Plate
to
actuate
Finger
to
Finger
to
Releaser
Holder
Knives
movable
knives
knife
Pick-up
operating
loop
pick-up
be
checked
ADJUSTMENT
actuate
clearance
interlocking
ADJUSTMENTS
pressure
ADJUSTMENTS
position
Bar
Height
ADJUSTMENTS
clamping
Points
point
for
for
aid
in
reel
AND
Follower
stripper
remove
pick
UNDER
unused
up
reel
THROAT
Position
and
adjustable
pressure
Finger
lever
finger
and
action
"full
pinch"
duration
winding
RETRACTING
finger
reel
thread
Stop
arm
of
pinch
thread
PLATt
knives