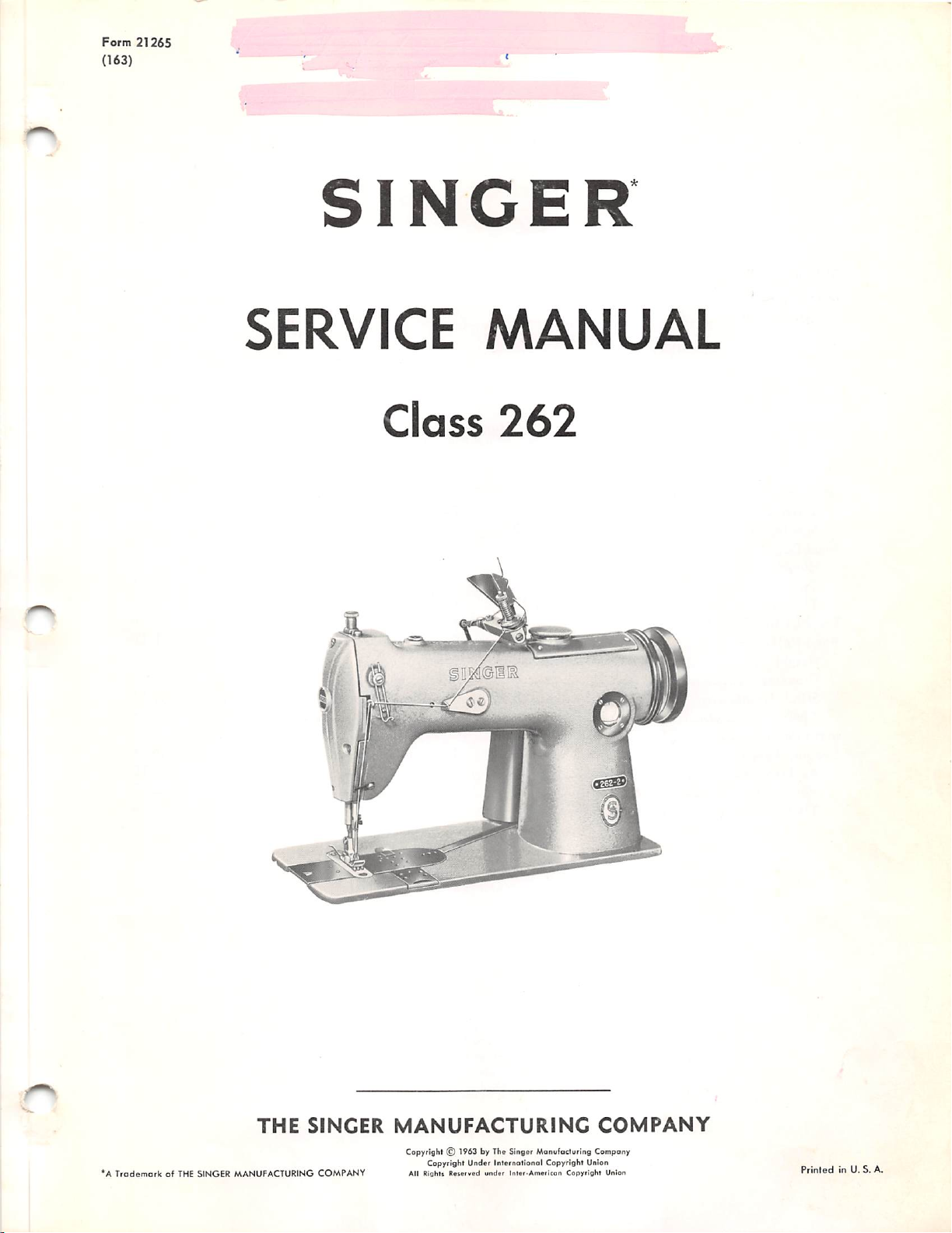
Form
(163)
21265
i
SINGER
SERVICE
Class
MANUAL
262
rs
•A
TfodemorkofTHE
SINGER
THE
MANUFACTURING
SINGER
COMPANY
MANUFACTURING
Copyright 1963 by The Singer
Copyright Under tnfernotionol Copyright Union
All Riflhti Reserved
under
Manufacturing
Inter-Americon Cepyrighl Union
COMPANY
Compony
Printed
In U. S. A.
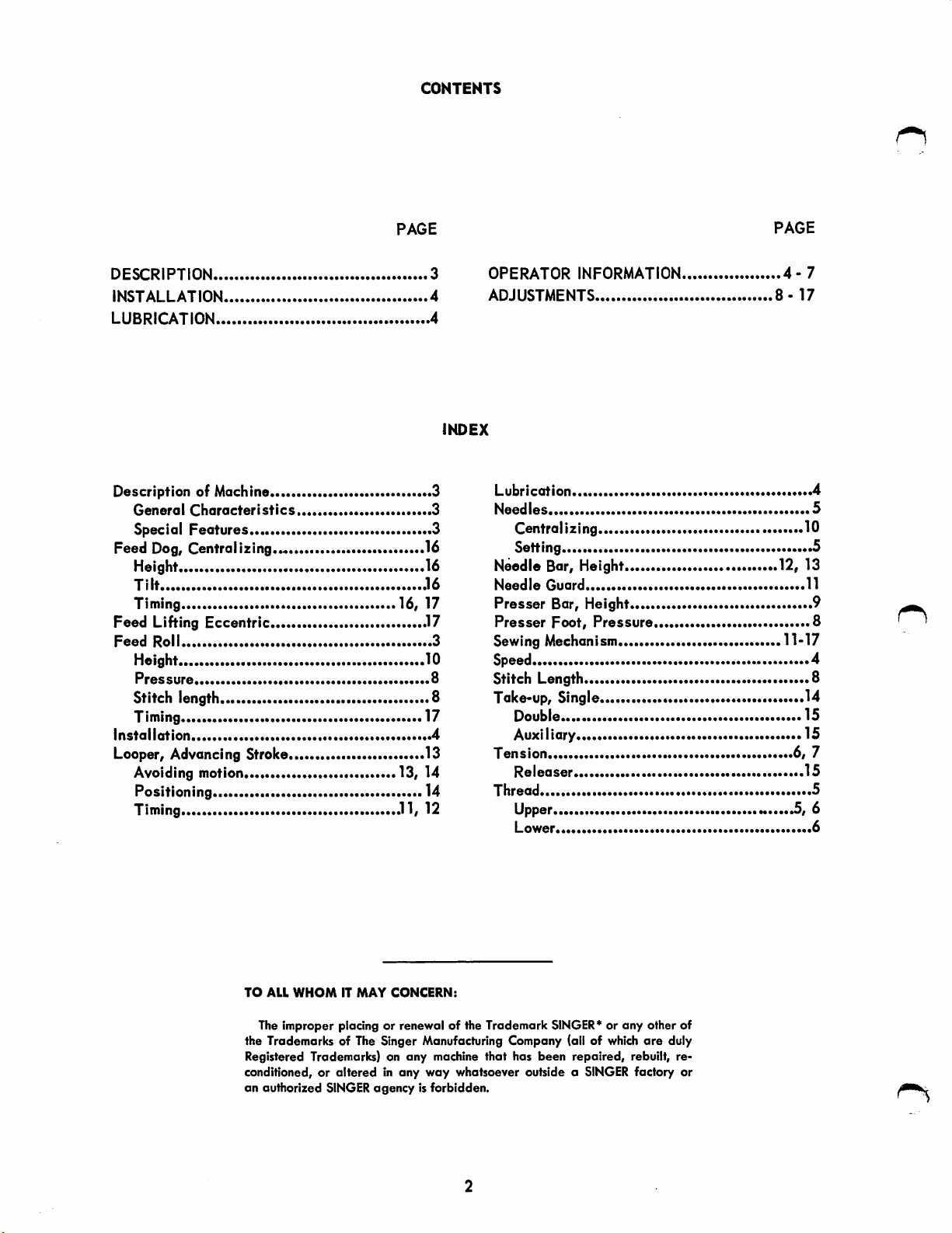
CONTENTS
PAGE
DESCRIPTION
INSTALLATION
LUBRICATION
Description of Machine 3
General
Special
Characteristics
Features
Feed Dog, Centralizing 16
Height 16
Tilt
.16
Timing 16, 17
Feed Lifting Eccentric .17
Feed
Roll
Height 10
Pressure
Stitch length 8
Timing 17
Installation
Looper, Advoncing Stroke 13
Avoiding motion 13, 14
Positioning 14
Timing .11, 12
3
4
4
INDEX
3
3
3
8
4
PAGE
OPERATOR
ADJUSTMENTS
Lubrication...
Needles
INFORMATION.
..4-7
,8-17
Centralizing 10
Setting 5
Needle Bar, Height 12, 13
Needle
Guard
Presser Bar, Height 9
Presser
Sewing
Foot,
Pressure
Mechanism
11-17
Speed 4
Stitch Length 8
Take-up, Single 14
Double
Auxiliary 15
Tension
Releoser
Thread
Upper
Lower
6,
5, 6
4
5
11
8
15
7
15
5
6
TO
ALL
WHOMITMAY
The improper placing or renewal of the Trademark SINGER*or
the Trademarks of The Singer Manufacturing Company (all of which
Registered Trademarks) on any machine that has
conditioned, or
on authorized SINGER
alteredinany
CONCERN:
way
agencyisforbidden.
whatsoever outside a SINGER factory or
been
repaired,
any
ore
rebuilt, re
other of
duly
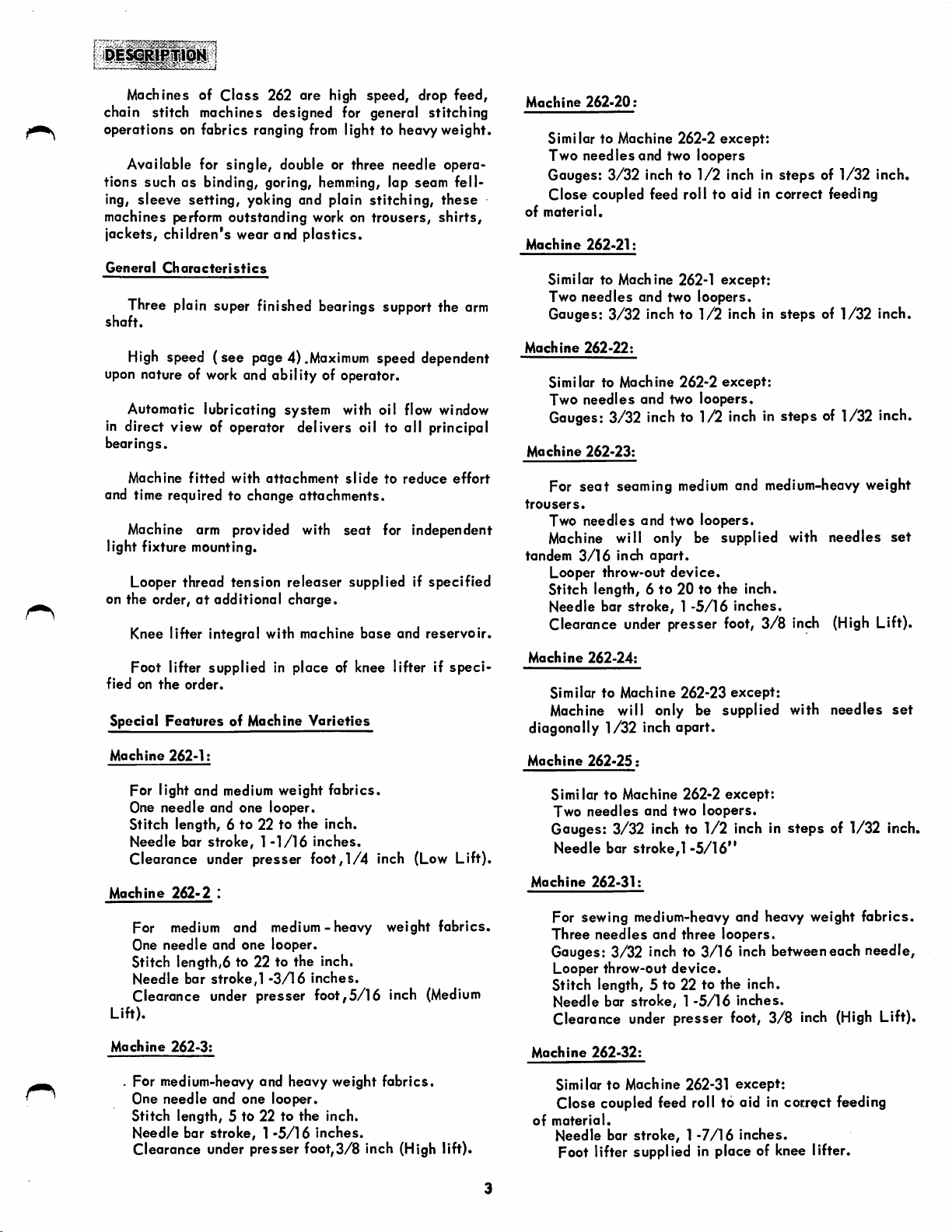
Machines of
Class
262 are high speed, drop feed,
chain stitch machines designed for general stitching
operations on fabrics ranging from light to
heavyweight.
Available for single, double or three needle opera
tions such as binding, goring, hemming, lop seam fell
ing, sleeve setting, yoking and plain stitching, these
machines perform outstanding work on trousers, shirts,
jackets, children's wear and
General
Characteristics
Three plain super finished bearings support the
shaft.
High
speed
(see
page 4)
plastics.
.Maximum
arm
speed dependent
upon nature of work and ability of operator.
Automatic lubricating system with oil flow window
in direct view of operator delivers oil to all principal
bearings.
Machine
262-20:
Similar to Machine 262-2
Two
needles
and two loopers
Gauges: 3/32 inch to
Close
coupled feed roll to aid in correct feeding
of
material.
Machine
Machine
Machine
262-21:
Similar to Machine 262-1
Two needles and two loopers.
Gauges:
Similar to Machine
3/32
262-22:
inch to
262-2
Two needles and two loopers.
Gauges:
3/32
262-23:
inch
to 1/2
except:
1/2
inch in steps of 1/32 inch.
except:
1/2
inch in steps of
except:
inch
in steps of 1/32 inch.
1/32
inch.
Machine
fitted
with
attachment
and time required to change attachments.
Machine arm provided with
light fixture mounting.
Looper thread tension releaser supplied if specified
_ on the order,atadditional charge.
Knee lifter integral with machine base and reservoir.
Foot lifter supplied in place of knee lifter if speci
fiedonthe
Special
Machine
For light and medium weight
order.
Features
262-1:
of Machine Varieties
One needle and one looper.
Stitch length, 6 to 22 to the inch.
Needle bar
stroke,1-1/16
inches.
Clearance under presser foot,
Machine
For
One
262-2
medium
needle
I
and medium-heavy weight fabrics.
and one looper.
Stitch length,6 to 22 to the inch.
Needle bar stroke,1
-3/16
inches.
Clearance under presser foot,5/16 inch
Lift).
slidetoreduce
seat
for independent
fabrics.
1/4
inch (Low Lift).
effort
(Medium
For
seat
seaming
trousers.
medium
and
medium-heavy
Two needles and two loopers.
Machine
tandem
Looper throw-out
will only be supplied with needles set
3/16
inch
apart.
device.
Stitch length, 6 to 20 to the inch.
Needle bar stroke, 1
Clearance under presser foot,
Machine
262-24:
Similar to Machine 262-23
Machine
will only be supplied with needles
-5/16
inches.
3/8
except:
inch
(High
diagonally 1/32 inch apart.
Machine
262-25:
SimilartoMachine 262-2
Two
needles
and two
loopers.
except:
Gauges: 3/32 inch to 1/2 inch in steps of 1/32 inch.
Needle bar stroke,1-5/16"
Machine
262-31:
For sewing medium-heavy and heavy weight
Three
needles
and
three
loopers.
Gauges: 3/32 inch to 3/16 inch betweeneach needle,
Looper throw-out
device.
Stitch length, 5 to 22 to the inch.
Needle bar
Clearance under presser foot,
stroke,1-5/16
inches.
3/8
inch
(High
weight
Lift).
set
fabrics.
Lift).
Machine
262-3:
For medium-heavy and heavy weight fabrics.
One needle and one looper.
Stitch length, 5 to 22 to the inch.
Needle bar
stroke,1-5/16
inches.
Clearance under presser foot,3/8 inch (High lift).
Machine
262-32:
SimilartoMachine 262-31
Close coupled feed roll to aid in correct feeding
of
material.
Needle bar stroke, 1
Foot lifter supplied in place of knee lifter.
-7/16
except:
inches.
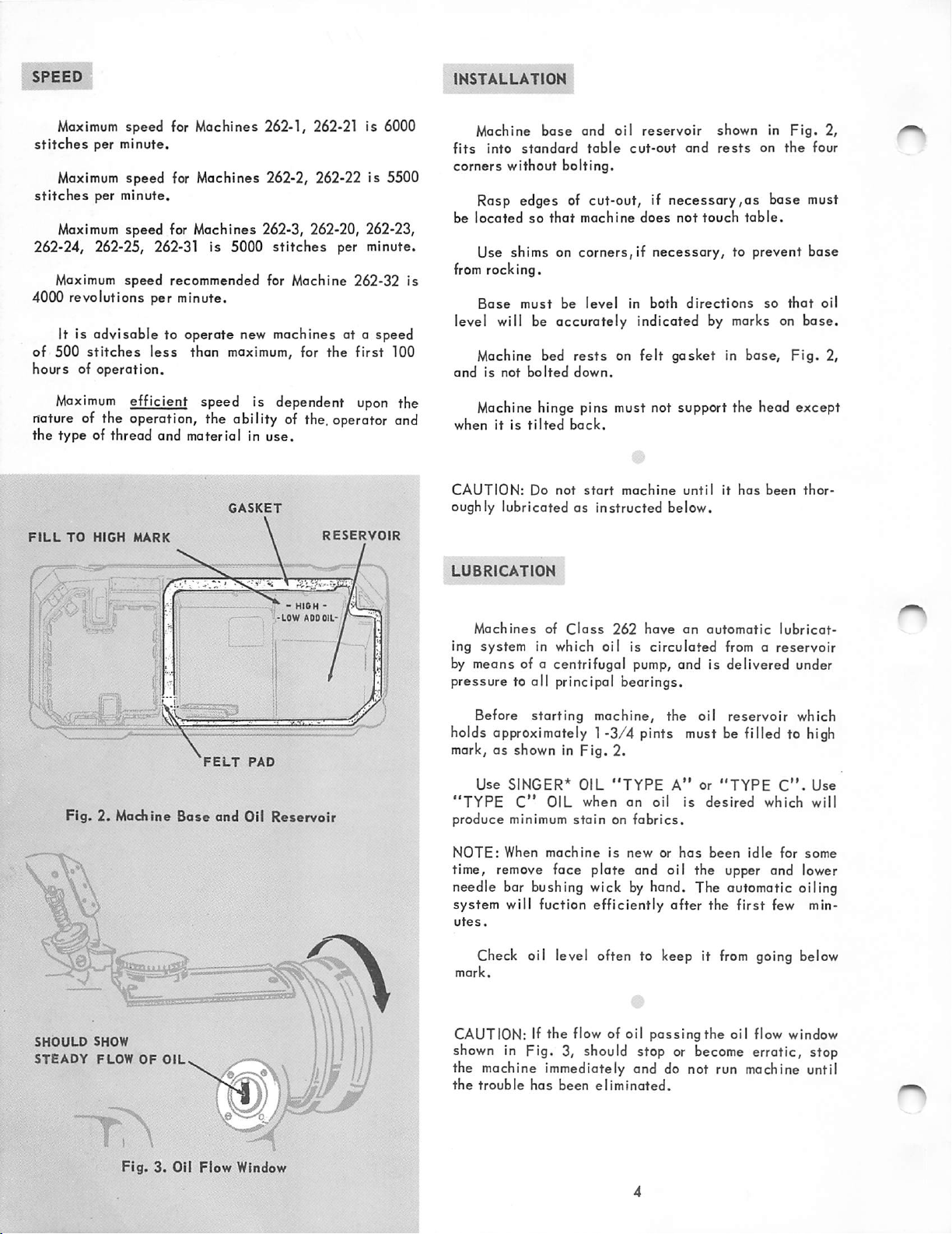
SPEED
INSTALLATION
Maximum
stitches
Maximum
stitches
Maximum
262-24, 262-25, 262-31 is 5000
Maximum
speed for Machines 262-1, 262-21 is 6000
per minute.
speed for Machines 262-2, 262-22 is 5500
per minute.
speed for Machines 262-3, 262-20, 262-23,
speed
recommended
stitches
for
per minute.
Machine
262-32
4000 revolutions per minute.
It is
of
500
advisable
stitches
to operate new machines at a speed
less
than
maximum, for
the
first
100
hours of operation.
Moximum
efficient speed is dependent upon the
nature of the operation, the ability of the, operator and
the type of thread and material in
FILL
TO
HIGH
MARK
use.
GASKET
RESERVOIR
ts
Machine
fits
into
corners
Rasp edges of cut-out, if
be
locatedsothot
Use shims on
from
rocking.
Base
base
standard
without
must
and oil reservoir shown in
table
cut-out
and
rests
bolting.
necessary,as
machine
corners,Ifnecessary,
be
level
in
does
both
not
touch
directions
on
the
base must
table.
to prevent
so
that
Fig.
four
base
level will be accurately indicated by marks on base.
Machine bed
andisnot
bolted
rests
down.
on
felt
gasketInbase.
Fig.
Machine hinge pins must not support the head except
whenitis
CAUTION:
oughly
LUBRICATION
tilted
back.
Do
not
start
machine
lubricatedasinstructed
untilithas
below.
been
thor
2,
oil
2,
Fig.2.Machine
SHOULD
STEADY
SHOW
FLOW
OF
li i
OIL
Base
'FELT
and
PAD
Oil
A\
-LOW
AODOIL-
Reservoir
.h.
Machines
ing system in which oil is
of
Class
262
have
an
circulated
automatic
from a reservoir
lubricat
by means of a centrifugal pump, and is delivered under
pressure to all principal bearings.
J
Before
holds approximately 1
starting
machine,
-3/4
the oil
reservoir
pints must be filled to high
which
mark, as shown in Fig. 2.
Use
SINGER*
"TYPE
C"
produce minimum
NOTE:
When
time, remove
OIL
OIL
"TYPE
when
an
A"
oil is
stainonfabrics.
machineisneworhas
face
plate
and oil the upper and lower
or
"TYPE
desired
been
idle
C".
which
for
Use
will
some
needle bar bushing wickbyhand. The outomatic oiling
system will fuction efficiently after the first few min
utes.
Check oil level often to keep it
mark.
CAUTION: If
the
flow of oil
passing
from
going below
the oil flow window
shown in Fig. 3, should stop or become erratic, stop
the machine immediately and do not run machine until
the
trouble
has
been
eliminated.
Fig.
3. Oil
Flow
Window
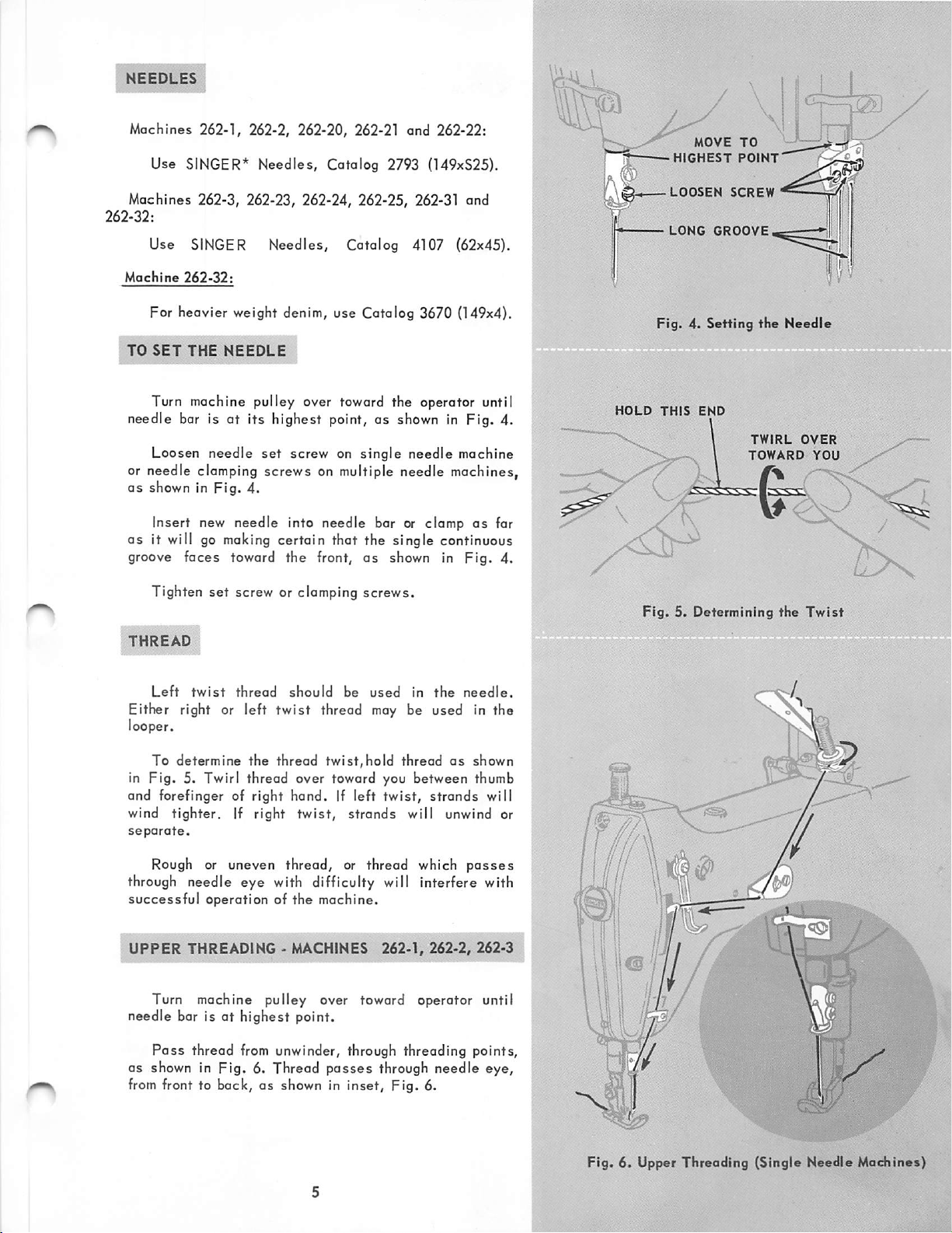
•NEEDLES
Machines 262-1, 262-2, 262-20, 262-21 and 262-22:
Use SINGER* Needles, Catalog 2793 (149x525).
Machines 262-3, 262-23, 262-24, 262-25, 262-31 and
262-32:
Use SINGER
Machine
TO
262-32:
For heavier weight denim, use Catalog 3670 (149x4).
SET
THE
NEEDLE
Needles,
Catalog 4107 (62x45).
Turn machine pulley over toward the operator until
needle bar is at its highest point, as shown in Fig. 4.
Loosen
needle
set
screw on
single
needle
machine
or needle clamping screws on multiple needle machines,
as
shown in Fig. 4.
Insert new needle into needle bar or clamp as far
as it will go making certain that the single continuous
groove faces toward the front, as shown in Fig. 4.
Fig. 4. Setting
HOLD
•
HIGHEST
LOOSEN
LONG
THIS
MOVE
GROOVE-
END
TO
POINT
SCREW
TWIRL
TOWARD
the
Needle
OVER
YOU
set
Tighten
THREAD
Left
screw or clamping screws.
twist
thread
should
be
usedinthe
needle.
Either right or left twist threod may be used in the
looper.
To
determine
the
thread
twist,hold
threadasshown
in Fig. 5. Twirl thread over toward you between thumb
and forefinger of right hand. If left
wind tighter. If right
separate.
twist,
Rough or uneven thread, or thread which
twist,
strands will unwind or
strands
will
passes
through needle eye with difficulty will interfere with
successful
UPPER
operation of the machine.
THREADING - MACHINES 262-1, 262-2, 262-3
Turn machine pulley over toward operator until
needle bar is at highest point.
).
Fig.
5. Determining
the
T\
^
m
m
dm
Pass
thread
as shown in Fig. 6. Thread
from front to bock, as shown in
from
unwinder, through threading points,
passes
through needle eye,
inset.
Fig.
6.
Fig.6.Upper Threading (Single Needle Machines)

UPPER
262-22, 262.23, 262-24, 262-25
THREADING • MACHINES 262.20, 262-21,
Turn machine pulley over toward operator until
needle
ing point indicated in
threading of
bar isathighest
Pass
each
these
point.
thread from unwinder through
Fig.
7. See
machines.
Fig.
each
8 for
thread
needle
/
Fig. 7. Upper Threoding (Two Needle Machines)
26^20l(.
262-21^fi262^22
i
11
262-25
4262.2.1
262-24
UPPER
needle
ing point indicated in
THREADING-MACHINES
Turn machine pulley over toward operator until
bar isathighest
Pass
each
thread from unwinder through
point.
Fig.
262-31,
9. See Inset,
262-32
each
Fig.
needle threading.
THREADING
(SINGLE
Pass
indicated in
threading on double take-up machines.
When
two inches of thread through looper eye to
THREADING
(MULTIPLE
THE
LOOPER
LOOPER
thread from unwinder through threading
MACHINES)
Fig.
10 and 11. Inset,
Fig.
11, shows
threading Is completed, draw approximately
start
THE
LOOPER
LOOPER
MACHINES)
thread
9, for
points
sewing.
Fig. 8. Threoding
the
Needles
%
• '
/•
•^ / • /
" r ^
!
Iff/
:w
Fig. 9. Upper Threading (Three Needle Machines)
Pass
each thread
points
release
right
two inches of thread through looper
indicatedinFig.12and
Before threading looper,
toward operator and swing looper carrier to the
as
shown In Fig. 13.
When
threading Is completed, draw approximately
Return looper carrier to sewing position.
ADJUSTING
THREAD
from
unwinder through threading
13.
press
eyetostart
TENSION
Regulate needle thread tension only when
footisdown.
Tension
while
To regulate, turn thumb nutatfront of
as shown in
on thread should be
still
sufficient
Fig.
14 and 15.
as
light
to
set
the
stitch
looper throw-out
sewing.
presser
as
possible
in
material.
tension
discs,
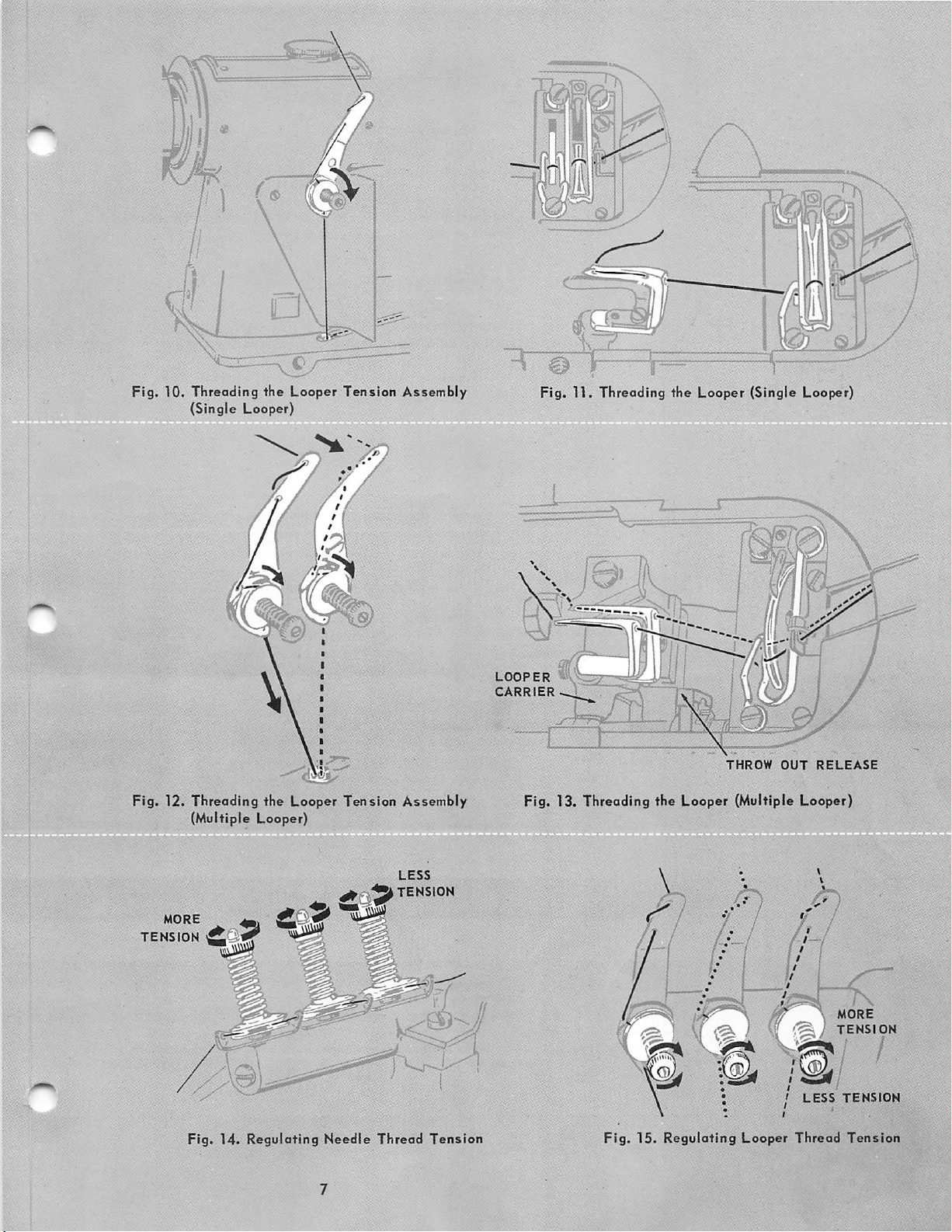
•K
.c..
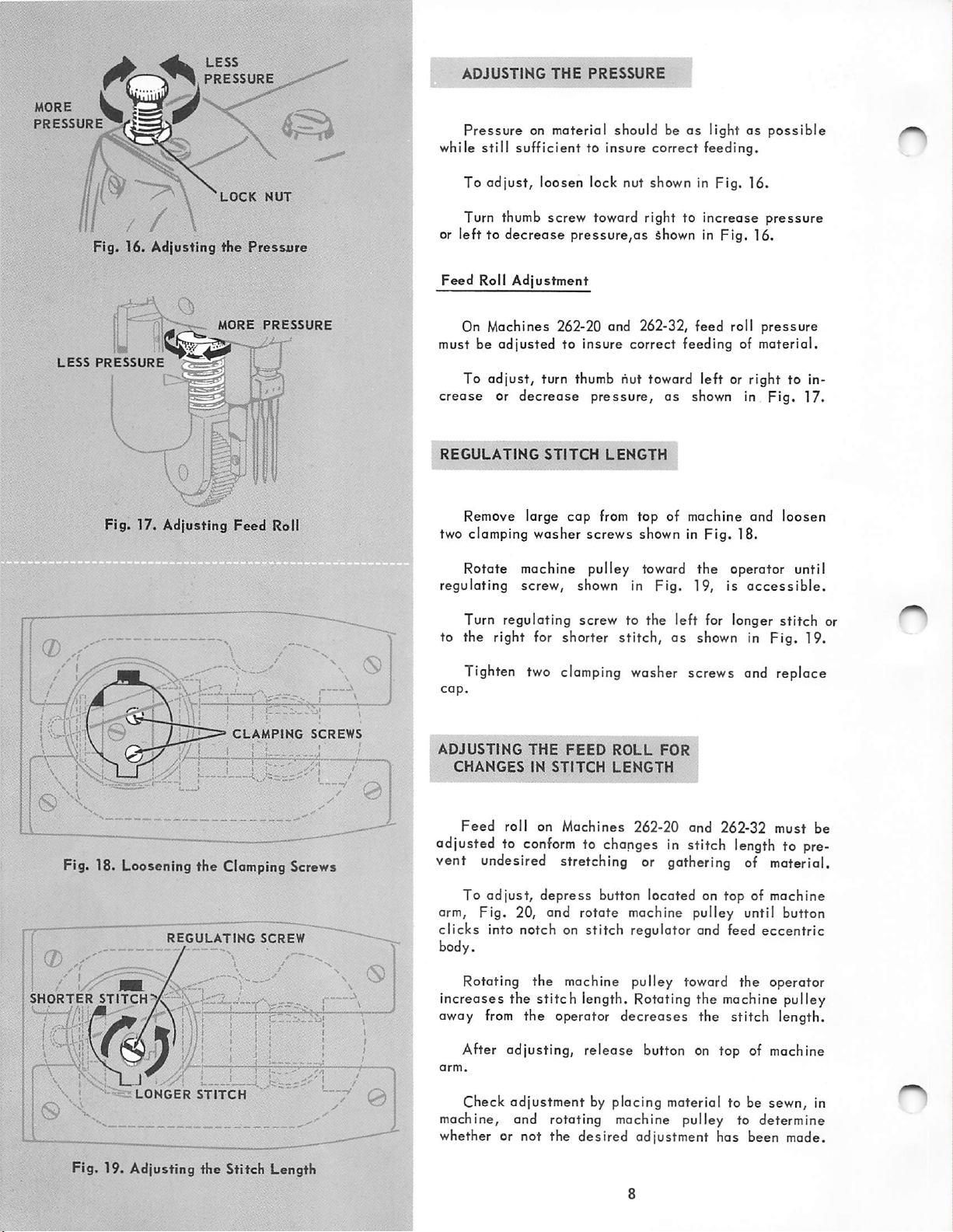
LESS
PRESSURE
ADJUSTING
THE
PRESSURE
MORE
^ I;
PRESSURE^vil
Fig. 16. Adjusting
LESS
PRESSURE
Fig. 17. Adjusting
LOCK
the
MORE
Feed
NUT
Pressure
PRESSURE
Roll
Pressure
on material should beaslightaspossible
while still sufficient to insure correct feeding.
To
adjust,
loosen lock nut shown in Fig. 16.
Turn thumb screw toward right to increase
Or
left to decrease pressure,as shown in Fig. 16.
Feed
Roll Adjustment
On Machines 262-20 and 262-32, feed roll
must be
adjusted
to insure correct feeding of material.
To adjust, turn thumb hut toward left or right to in
crease
REGULATING
two clamping
or
decrease
STITCH
Remove large
washer
pressure, as shown in Fig. 17.
LENGTH
cap
from
top
of machine and
screws
shown in Fig. 18.
pressure
pressure
loosen
/ » ^
CLAMPING
//
> '
Fig. 18. Loosening the ClampingScrews
REGULATiNG
SHORTER
(L:¥,
\\
STITCH
jiii
!);i »
1
^\{li
SCREW
SCREWS
•s
(5
Rotate machine pulley toward the operator until
regulating screw, shown in Fig. 19, is
Turn regulating screw to the left for longer
accessible.
stitch
to the right for shorter stitch, as shown in Fig. 19.
Tighten two clamping washer screws and replace
ADJUSTING
^g^ANGESINSTITCH
Feed
adjusted to
THE
roll on
conform
FEED
ROLL
FOR
LENGTH
Machines
to changes in stitch
262-20 and 262-32
length
must
to pre
be
vent undesired stretching or gathering of material.
To
adjust,
depress
button located on top of machine
arm. Fig. 20, and rotate machine pulley until button
clicks into notch on stitch regulator and feed eccentric
body.
Rotating the machine pulley toward the operator
Increases the stitch length. Rotating the machine pulley
from
away
the operator decreoses the stitch length.
After adjusting, release button on top of machine
or
..
1—I
. i J 1
LONGER
STITCH
Check adjustment by placing material to be sewn, in
machine, and rotating machine pulley to determine
whether or not the
desired
adjustment has been made.
Fig. 19. Adjusting the Stitch Length
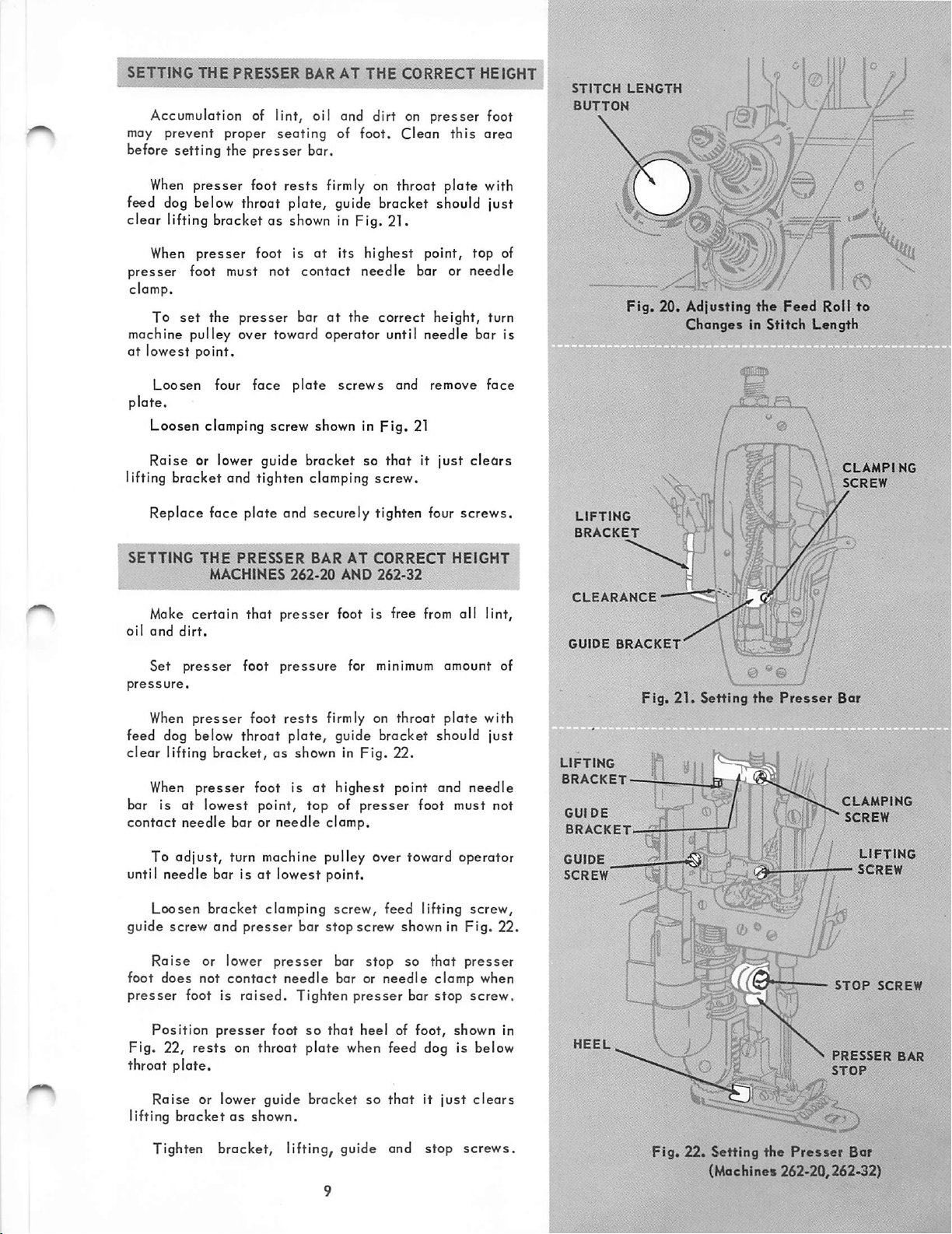
pETTING
THE
PRESSER
BARATTHE
CORRECT
HEIGHT
Accumulation of lint, oil and dirt on presser foot
may prevent proper
seating
of foot. Clean
this
area
before setting the presser bar.
When
presser foot
rests
firmly on throat plate with
feed dog below throat plate, guide bracket should just
clear lifting bracket as shown in Fig. 21.
When
presser
foot is
at
its
highest
point, top of
presser foot must not contact needle bar or needle
clamp.
To
set
the
presser
bar
at
the
correct
height, turn
machine pulley over toward operator until needle bar is
at
lowest point.
STITCH
BUTTON
LENGTH
Fig.
20. Adjusting
the
Feed
Roll
Changes in Stitch Length
to
Loosen
plate.
Loosen clamping screw shown in
four
face
plate
screws
and remove
Fig.
21
Raise or lower guide bracket so that it just
lifting bracket and tighten clamping screw.
Replace face
^SETTING
I
Make
certain
oil
and
dirt.
Set
presser
pressure.
When
presser
feed dog below throat
clear
lifting bracket,asshown In Fig. 22.
When
presser
bar is at
plate
and
THE
PRESSER
MACHINES
that
presser
foot
pressure
foot
rests
foot is
lowest
point, top of
securely
BAR
262-20
firmly on throat
plate,
at
tighten four
AT
CORRECT
AND
foot is free from all lint,
for minimum amount of
guide bracket should
highest
presser
262-32
point and
foot must not
contact needle bar or needle clamp.
To adjust, turn machine pulley Over toward operator
at
until needle bar is
lowest point.
clears
screws.
HEIGHT
plate
needle
face
with
just
LIFTING
BRACKET
CLEARANCE—
GUIDE
LIFTING
BRACKET
GUIDE
GUIDE
BRACKET-^g
BRACKET
BRACKET'
Fig.
If]
:iJ |
guide
SCREW'—g/
SCREW
21.
X-T
\ © /
Setting
/ I
mwAi
the
ri
Presser
i!i/
i
CLAMPING
\
SCREW
Bor
.
CLAMPING
SCREW
/
screw
Loosen bracket clamping screw, feed lifting screw,
guide
screw
and
presser
Raise
foot does not
presser
Position
Fig. 22,
throat
foot is
rests
plate.
or lower
contact
raised.
presser
on throat plate when feed dog is below
Raise or lower guide bracket so that it just
lifting bracketasshown.
bar
presser
needle
Tighten
foot
so
stop
screw shown in
bar stop so
bar or
that
needle
presser
heel of foot, shown in
that
bar stop
Fig.
22.
presser
clamp when
screw.
clears
HEEL
Tighten bracket, lifting, guide and stop screws.
Fig.
22.
Setting
(Machines
STOP
the
Presser
262-20,262-32)
STOP
PRESSER
Bar
SCREW
BAR
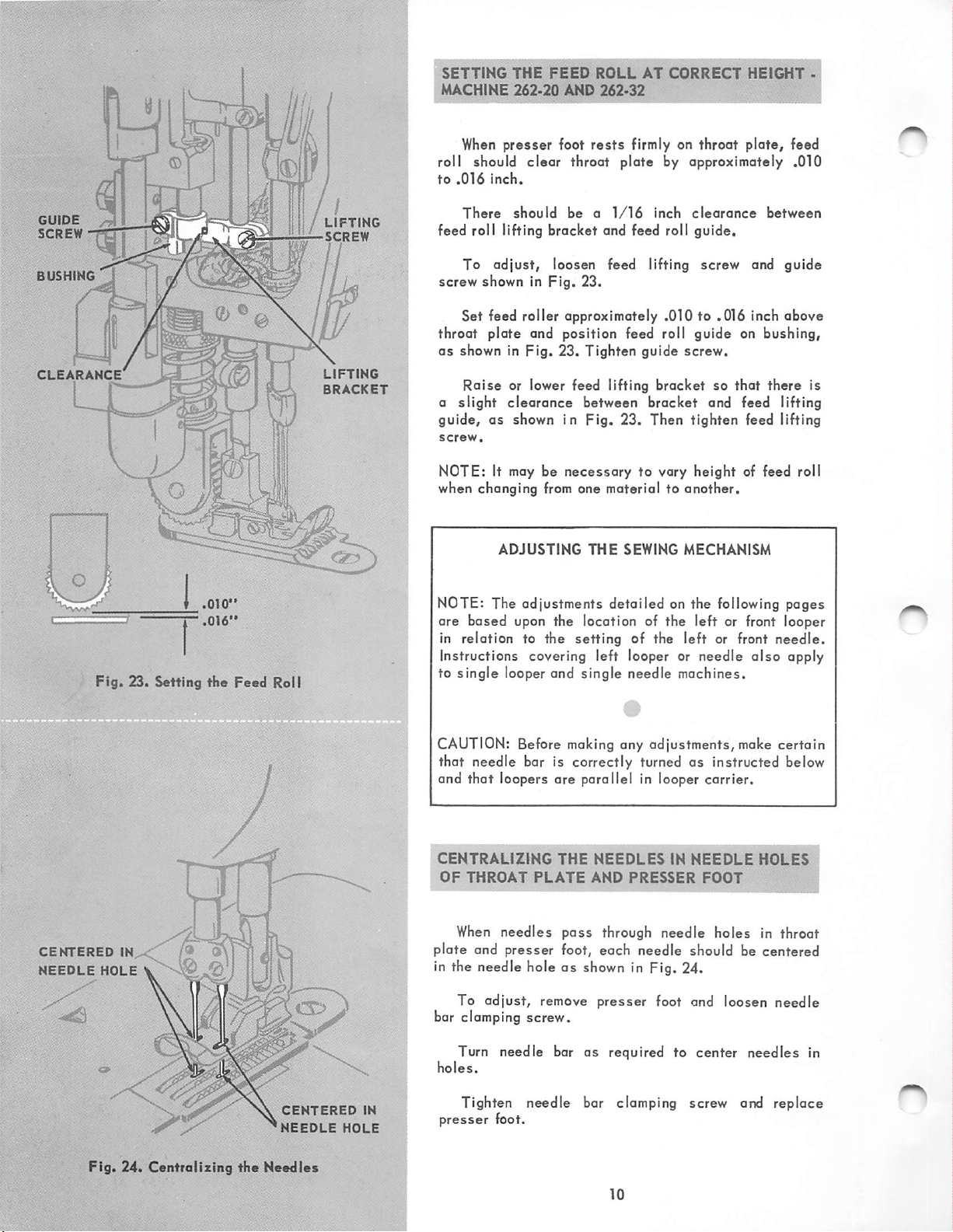
SETTING
;|IACHINE
When
THE
FEED
262.20
AND
presser foot
ROLL
AT
CORRECT
HEIGt
262-32^^^ggg^^^||
rests
firmly on throat plate, feed
roll should cleor throat plate by approximotely .010
to
.016
inch.
Fig.
23« Setting
the
Feed
Roll
LIFTING
SCREW
LIFTING
BRACKET
There
should
bea1/16
Inch
clearance
between
feed roll lifting bracket and feed roll guide.
To adjust, loosen feed lifting screw and guide
screw shown In Fig. 23.
Set feed roller approximately .010 to .016 inch above
throat plate and position feed roll guide on bushing,
as shown in Fig. 23. Tighten guide screw.
Raise
or lower feed lifting bracket so
that
there is
a slight clearonce between bracket and feed lifting
guide,
as
shown in
Fig.
23. Then
tighten
feed lifting
NOTE: it may be necessary to vary height of feed rol
when changing from one material to
ADJUSTING
THE
SEWING
another.
MECHANISM
NOTE: The adjustments detailed on the following pages
ore based upon the location of the left or front looper
in relation to the
Instructions covering left looper or needle
to
single
looper and
setting
single
of the left or front
needle machines.
also
needle.
apply
CEtfTERED
NEEDLE
HOLE
Fig.
•••.
•
IN.-.r"
0"""
24.
Centralizing
®
/®
4 -
I.//
/V
the
Needles
CENTERED IN
NEEDLE
HOLE
CAUTION: Before making any adjustments, make certain
that needle bar is correctly turned as Instructed below
and
that
ioopers
CENTRALIZING
OF
THROAT
When
needles pass through needle holes in throat
plate and
presser
are
THE
PLATE
foot,
parallel in looper carrier.
NEEDLES
AND
each
IN
NEEDLE
PRESSER
FOOT
needle should be
in the needle hole as shown in Fig. 24.
To
if
^
adjust,
bar clamping
Turn needle bar
holes.
Tighten needle bar clamping screw and replace
presser
foot.
remove
screw.
presser
as
required to
foot and loosen
center
HOLEI
centered
needle
needles
in
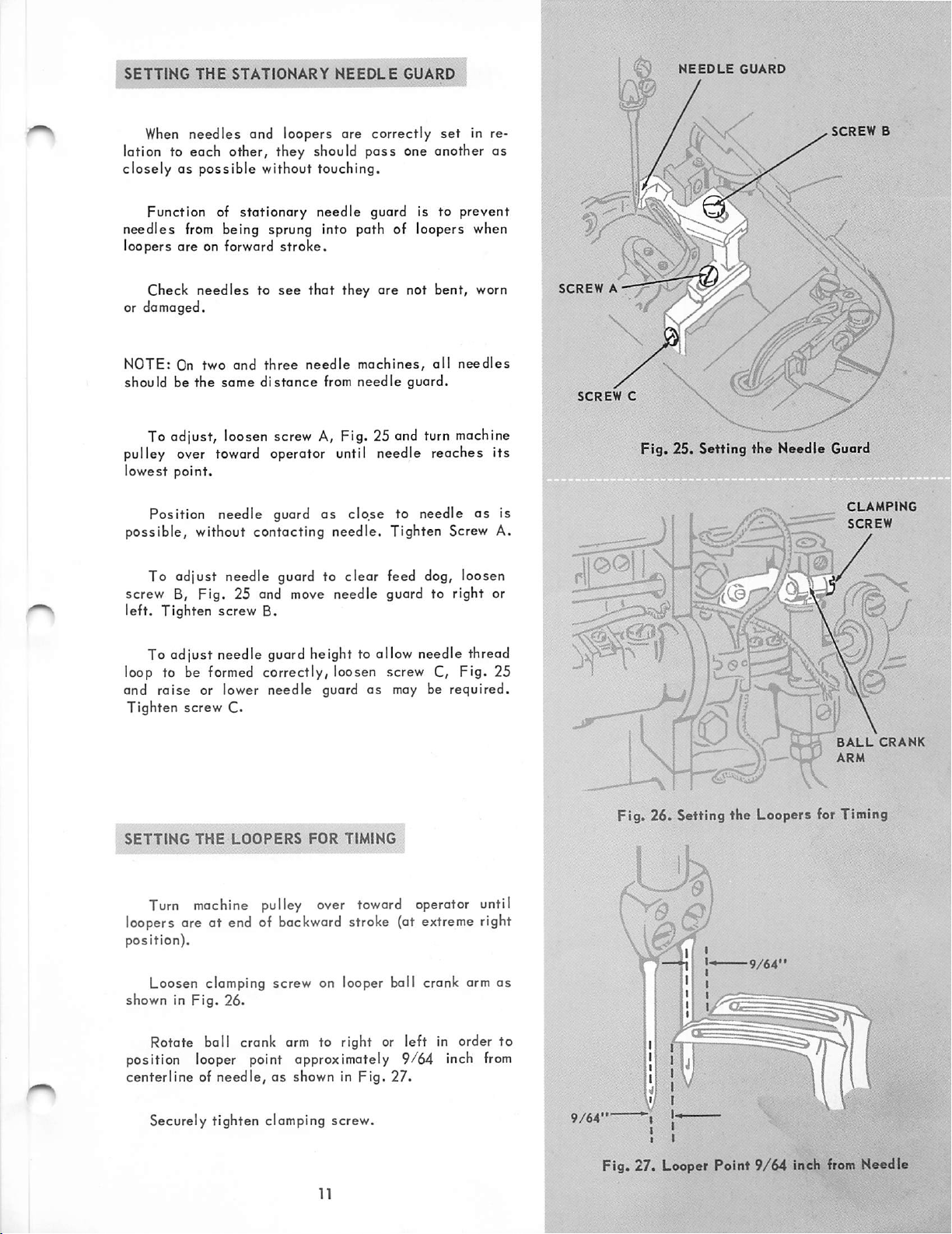
SETTING
THE
STATIONARY
NEEDLE
GUARD
NEEDLE
GUARD
When
needles
lation to each other, they should
and loopers ore correctly
pass
One
set
in re
another as
closely as possible without touching.
Function of
needles
loopers ore on forward
or damaged.
NOTE: On two
should be the same
from
Check
stationary
needle
guard Is to prevent
being sprung into path of loopers when
stroke.
needlestosee
and
distance
three
that
they are not bent, worn
needle
from
machines,
needle
guard.
all
needles
To adjust, loosen screw A, Fig. 25 and turn machine
pulley over toward operator until needle reaches Its
lowest point.
Position needle guard as
possible,
without
contacting
close
needle.
to needle as is
Tighten Screw A.
To adjust needle guard to clear feed dog, loosen
screw B, Fig. 25 and move
left. Tighten screw B.
needle
guard to right or
SCREW
A-7=7^
SCREW
f®©l
SCREW
mm.
C
Fig. 25. Setting the Needle Guard
B
CLAMPING
SCREW
To adjust needle guard height to allow needle thread
loop to be formed correctly, loosen screw C, Fig. 25
may
and raise or lower needle guard as
Tighten screw C.
SETTING
THE
LOOPERS
FOR
TIMING
be required.
Turn machine pulley over toward operator until
loopers are at end of backward stroke (at extreme right
position).
Loosen clamping screw on looper ball crank arm as
shown in
Fig.
26.
Rotate ball crank arm to right or left In order to
position looper point approximately 9/64 inch
centerlineofneedle,
as shown in
Fig.
27.
from
Fig.
1
IWJ-
©I
26*
Setting the Loopers for Timing
9/64"
BALL
ARM
CRANK
Securely tighten clamping screw.
Fig. 27. Looper Point 9/64 inch
from
Needle